基于ADAMS的伸缩臂叉装车工作装置运动学与动力学仿真
基于 ADAMS 的伸缩臂叉装车工作装置运动学与动力学仿真

Adams动力学仿真分析的详细步骤
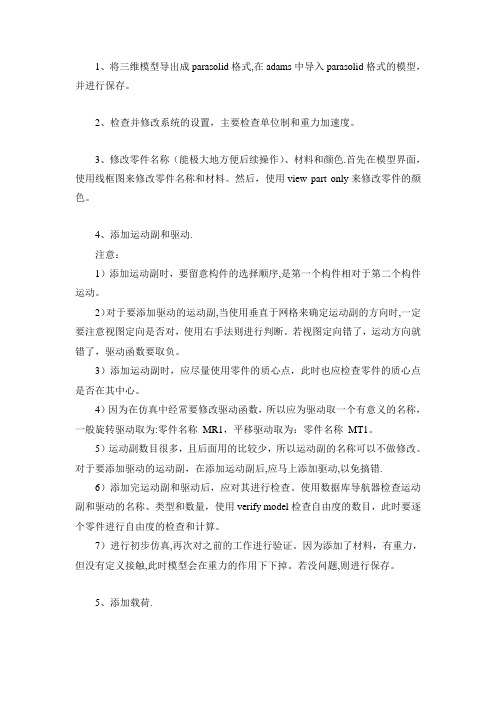
1、将三维模型导出成parasolid格式,在adams中导入parasolid格式的模型,并进行保存。
2、检查并修改系统的设置,主要检查单位制和重力加速度。
3、修改零件名称(能极大地方便后续操作)、材料和颜色.首先在模型界面,使用线框图来修改零件名称和材料。
然后,使用view part only来修改零件的颜色。
4、添加运动副和驱动.注意:1)添加运动副时,要留意构件的选择顺序,是第一个构件相对于第二个构件运动。
2)对于要添加驱动的运动副,当使用垂直于网格来确定运动副的方向时,一定要注意视图定向是否对,使用右手法则进行判断。
若视图定向错了,运动方向就错了,驱动函数要取负。
3)添加运动副时,应尽量使用零件的质心点,此时也应检查零件的质心点是否在其中心。
4)因为在仿真中经常要修改驱动函数,所以应为驱动取一个有意义的名称,一般旋转驱动取为:零件名称_MR1,平移驱动取为:零件名称_MT1。
5)运动副数目很多,且后面用的比较少,所以运动副的名称可以不做修改。
对于要添加驱动的运动副,在添加运动副后,应马上添加驱动,以免搞错.6)添加完运动副和驱动后,应对其进行检查。
使用数据库导航器检查运动副和驱动的名称、类型和数量,使用verify model检查自由度的数目,此时要逐个零件进行自由度的检查和计算。
7)进行初步仿真,再次对之前的工作进行验证。
因为添加了材料,有重力,但没有定义接触,此时模型会在重力的作用下下掉。
若没问题,则进行保存。
5、添加载荷.6、修改驱动函数.一般使用速度进行定义,旋转驱动记得加d。
7、仿真。
先进行静平衡计算,再进行动力学计算。
8、后处理。
具体步骤如下:1)新建图纸,选择data,添加曲线,修改legend。
一般需要线位移,线速度,垂直轮压和水平侧向力的曲线。
2)分析验证,判断仿真结果的正确性(变化规律是否对,关键数值是否对)。
3)截图保存,得出仿真分析结论.。
基于ADAMS折叠式动臂工作装置动态特性仿真分析
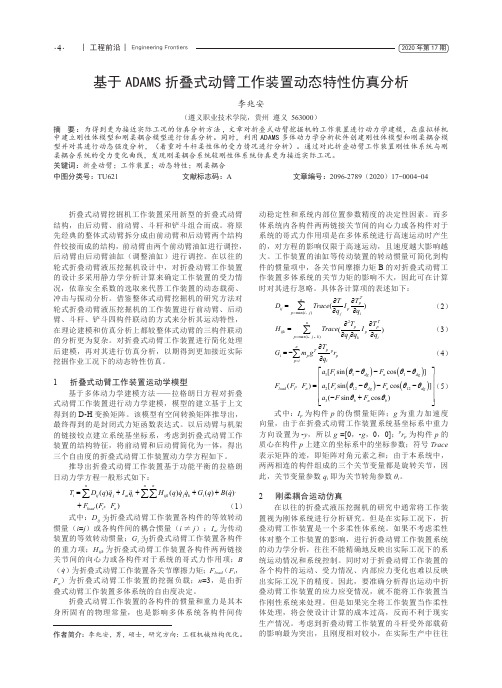
作者简介:李兆安,男,硕士,研究方向:工程机械结构优化。
基于ADAMS 折叠式动臂工作装置动态特性仿真分析李兆安(遵义职业技术学院,贵州 遵义 563000)摘 要:为得到更为接近实际工况的仿真分析方法,文章对折叠式动臂挖掘机的工作装置进行动力学建模,在虚拟样机中建立刚性体模型和刚柔耦合模型进行仿真分析。
同时,利用ADAMS 多体动力学分析软件创建刚性体模型和刚柔耦合模型并对其进行动态强度分析,(着重对斗杆柔性体的受力情况进行分析)。
通过对比折叠动臂工作装置刚性体系统与刚柔耦合系统的受力变化曲线,发现刚柔耦合系统较刚性体系统仿真更为接近实际工况。
关键词:折叠动臂;工作装置;动态特性;刚柔耦合中图分类号:TU621 文献标志码:A 文章编号:2096-2789(2020)17-0004-04折叠式动臂挖掘机工作装置采用新型的折叠式动臂结构,由后动臂、前动臂、斗杆和铲斗组合而成。
将原先经典的整体式动臂拆分成由前动臂和后动臂两个结构件铰接而成的结构,前动臂由两个前动臂油缸进行调控,后动臂由后动臂油缸(调整油缸)进行调控。
在以往的轮式折叠动臂液压挖掘机设计中,对折叠动臂工作装置的设计多采用静力学分析计算来确定工作装置的受力情况,依靠安全系数的选取来代替工作装置的动态载荷、冲击与振动分析。
借鉴整体式动臂挖掘机的研究方法对轮式折叠动臂液压挖掘机的工作装置进行前动臂、后动臂、斗杆、铲斗四构件联动的方式来分析其运动特性,在理论建模和仿真分析上都较整体式动臂的三构件联动的分析更为复杂。
对折叠式动臂工作装置进行简化处理后建模,再对其进行仿真分析,以期得到更加接近实际挖掘作业工况下的动态特性仿真。
1 折叠式动臂工作装置运动学模型基于多体动力学建模方法—拉格朗日方程对折叠式动臂工作装置进行动力学建模,模型的建立基于上文得到的D-H 变换矩阵。
该模型有空间转换矩阵推导出,最终得到的是封闭式力矩函数表达式。
以后动臂与机架的链接铰点建立系统基坐标系,考虑到折叠式动臂工作装置的结构特征,将前动臂和后动臂简化为一体,得出三个自由度的折叠式动臂工作装置动力学方程如下。
基于ADAMS的双叉臂悬架系统动力学研究
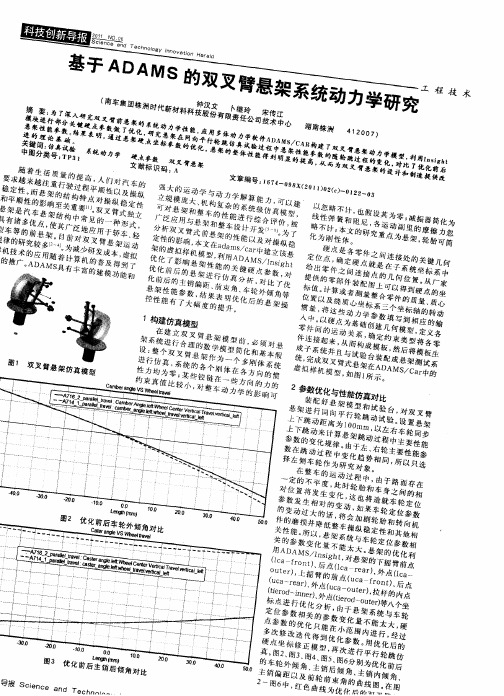
损 。 际 设 计 时 , 致 的 范 围 在7 l , 望 实 大 ~ 希 3 取 较 小 数 值t。 因此 设 计 要 求 丰销 内 倾 角不 从 中 双 定 性 变 差 。 是 如 果 太 大 会 使 车 轮 支 撑 处 能 太 大 , 图4 可 以 看 出 , 叉 臂 式 悬 架 但 优 化 前 、 的 丰 销 内 倾 角变 化 范 围分 别是 后 反 力 矩 过 大 , 成 车 轮 摆 振 或 者 转 向 盘 力 造 1 ~l . 。 4 2。 的 变 化 , 股 要 求 主 销 后 倾 角 在 3 ~6 之 9. 。 1 3 与7. 。~9. 。 不 仅变 化 区 间 一 。 。 最 提 间 。 3 图 中所 示 的 曲线 表 明 , 未优 化 的 恳 架 大 为 变 小 , 值 也大 幅 度 的 变 小 , 高 了汽 转 减 主销 后 倾 角 在 5. ~5. 。 间 , 化 后 的 车 的转 向能 力 , 向 操 作 更为 轻 便 , 小 了 4。 5之 优 在 3. 8 2 。~4. 6 之 间 , 图 3 见 , 化 后 轮 胎 的 磨 损 。 0。 由 可 优 () 销偏  ̄ (c u r d u ) 4主 .sr b a is。 主 销 后 倾 角 的 幅 值 大 大 减 小 , 利 于 抑 制 有
制 动 点 头 , 时 提 高 了 悬 架 系 统 的 直 线 行 同 驶稳定性 。 汽 车 转 向 时 , 向 轮 绕 主 销 转 动 , 面 转 地 对 转 向 的 阻力 力 矩 与 主 销 偏 距 的 大 小 成正
( ) 销后倾 角(a tr n l) 2主 c se a g e。
詈 量
2 8 8. 5~2 . 6 9 9 mm之 间 , 值 和 范 围减 少 , 幅 使 得 悬 架 操 作 稳 定 性 能得 到 提 升 。 () 5 前轮前 束 角(o a g e。 t e n l) 车轮 前 束 角 的 怍 用 主 要 是 减 少汽 车 前
基于ADAMS的装车推拉器受力分析及仿真研究
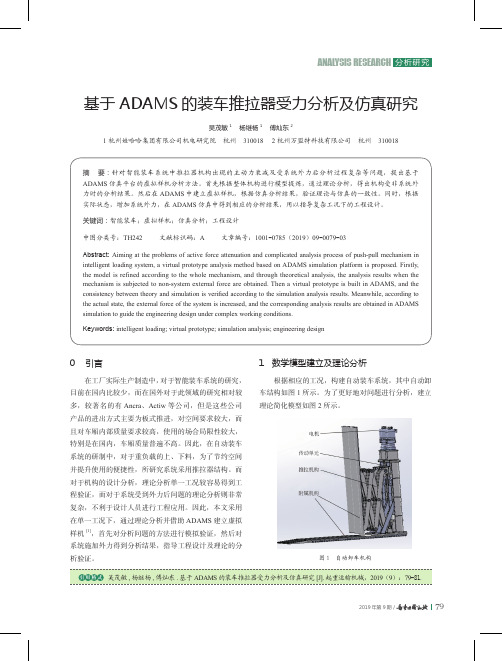
图1 自动卸车机构的装车推拉器受力分析及仿真研究[J].起重运输机械,2019(9):79-812019年第9期 /图2 理论简化模型根据虚位移原理,结构在外力作用下处于平衡状态如果给结构一个可能发生的位移即虚位移,虚功)等于结构因虚变形获得的虚应变能进行受力分析,其中T表示推拉货物水平阻力传动轴方向的施加力,φ表示力F与一级杆之间的夹角受力方向为X轴方向,且向右为正方向受力方向为Y轴方向,且向上为正方向。
其中表示相应方向的位移,有图3 简化模型由于ADAMS建模能力较差,一般常将三维软件设图4 虚拟样机模型3 虚拟仿真及结果输出分析根据理论分析及工况状态,对虚拟样机添加主动力阻力驱动设置为静止。
同时,设置主动力与=14.54°。
对系统进行仿真,图5 系统激励根据以上结果分析,虚拟仿真偏差与理论计算偏差在0.8%左右,在实际工程应用中结果精度可完全满足实际工况。
为了验证系统结果的有效性,设置主动力与/ 2019年第9期图6 系统激励图7 驱动阻力根据结果分析得到的实际结果偏差在0.2%左右。
对以上理论分析及系统仿真结果比较可知,仿真结果是有效的,但是由于系统环境为只有单一系统内力,并未考虑系统外力的影响。
当系统受到外力时,特别是受到多角度多个系统外力时,理论模型往往较为复杂,但是通过建立虚拟样机,可以更直接方便地得出接近实际状态的结果,见图8和图9,为实际工程应用设计提供了便利。
图8 理论模型图9 仿真结果4 结束语通过对推拉器结构受力分析及理想模型的理论推导,得到理论计算结果。
然后通过建立虚拟样机,对理想模型进行仿真,仿真结果与理论分析结果十分接近,误差满足实际工程要求,同时验证了虚拟样机模型的正确性。
在此基础之上,通过添加现实复杂工况条件,可更加真实地模拟实际工况。
所述理论分析及仿真验证方法,对于复杂状态下的工程应用及理论推导都具有很好的指导意义。
基于ADAMS的装载机工作装置机构优化仿真

4 2确定 1 变量。根据优化 目 标确定优化设
计 变 量 , 用 A AMS 计 点 参 数 化 功 能将 G( 利 D 设 G q、(F) E BB ) (q、 D、 (A、 H F r、 、(B、 C D ) A ) E( C A H( 和 M( 点在工况 I MM) 时的 x Y坐标值等 l Il
纪 玉 新
基于 A A D MS的装载机工作装置机构优化仿真
( 福建华橡 自控技术股份 有限公 司, 建 三明 35 0 ) 福 6 5 0
摘 要: 应用 A A / e D MSVi w模块提供的 O T E — Q P D S S P优化算法 , 对装载机 工作装置仿真优化 , 到优化后的模型。 化后铲斗 的平移性大为改 得 优 善, 举升过程 中铲斗的收斗角由原来的 1.。 62 降为 6 。自动放平性更好、 ., 7 卸载性也 大大改 变, 优化效果明显。 关键 词 : D A AMS 装 载 机 ; 化仿 真 ; 优 1 概述 AA D MS系列产 品的核心模块 之一。 表 1虚拟样机 中各传动角约束 优化 设计 ( t lds n 在 现 代计 算 机广 o i ei ) p ma g是 4工作装置的仿真优化 泛应用的基础上发展起来的—项新技术 , 是根据最 4l 确定 目标 函数 。 目标 函数 是用来 使‘ 计” 设 优化原理和方法综合各方面的因素, 以人机配合方 优 化的函数, 是设 计所追求 目标 的函数 表 达式 。对 式 或“ 自动探 索” 方式 I 机械 设 计与 数学 规划 理 装载 机工作装 置进 行优化 时 , 函数 的选择 有多 l l , 把 目标 论及方法相结合 , 借助电子计算机 , 寻求最优设计 种方案, 文中选用在动臂举升过程中铲斗的平移性 方案和最佳设计参数。 化问题的类型按有无约束 最好作为目标函数 ,即在转斗油缸闭锁, 吡 动臂 由工 可分为有约束和无约束两大类。 在优化设计 问题的 况 Ⅱ 上升到工况Ⅲ的过程中根据优化目标: 寻求铲 数学模型式(… 3若 I v 0, 。 2 3 ) 1 = 既无约束条件存 斗举升平动的最优方案。下面两种形式都可当作目 , = 在, 称这类问题为无约束优化没计问题 , 否则称这 标 函数 F , 即 类问题为有约束优t 崮 十 匕 问题。 优化问题的类型按 () m n l= - , x = _ q一 , l, k m i 2一 l 目 函 、 标 数 约束函数的性质 , 可以分为线性优化问 乳 ( = f ( —n ) J x) ’ n 题 和非线 问题 。所 谓线 陛优化 问题 , 就是 在 数学模型式0 2 3 3 v ) . 、 均为设计变 — ~—) e 、 h 中, x g ) 式 中 . 铲 斗从工 况 Ⅱ 升 到工 况 Ⅲ的过 广 举 量的线性函数; 否则,若其中有任— 为非线陛函 程中, 个瞬间位置的铲斗对地位置角。 k 利用最,二 J \ 数时, 就称为非线性优化问题。若—个优化设计问 乘法原理来建立优化目标函数, 即用举升过程中铲 题既是有约束的, 又是非线 陛 , 的 则称为非线性约 斗与水平面夹角的绝对值以及运输工况时铲斗与 束优化问题目 。 工程优化没计问题绝大多属于非线 水平面的收斗角之差的平方和的最小平均值作为 优化问题, 装载机工作装置就属于此类。 优化 目标 函数 ,利用主菜单 B ID中的 ME — UL A 2 用优化方法求解装载机工作装置优化设计 S RE选项 , U 建立测量 F C I N ME 一 1测量 { UN T O — A 2 , 。∞ ) 一 问题的—般步 骤 : 的表 达 式 为 : (m 一 3 q (B A AR — I t e7: F i A S fZ K 景一 。 2 根据装载机工作装置的谢 — 1 r 要求,应用相 ER 4 2 一4 妒 '. 1 SGN1 1. ie* 3 ) 0 2 0 ( I ( 9一t ) ) 5 + ,1 m) 关专业的基啦哩论与 技术规范, 建立起工作装 (B z A K R 4 2 一 0 ), 后 确定 优 A s R E _ 3 ) 4妒 2 最 ) 图 2 优 化 后 转 斗 在 工 作 过程 中 的转 角 ( 斗 铲 置各种参数之间的相互关系, 并进行工作装置的运 化设计的 目标 函数为测量 F N TO — A 2 U C I N ME 一 1 斗 底 与 水 平 面 夹 角) 变化 曲 线 图 (o ) FF 一 3 , B (Z A K R 4 2- 0) ga : (i 7 .( S R E _ 3)4 d 1 I me 0 A A ) 动学和动力学分析。 model z 5 I0 2 2在工作装置运动学与动力学分析的基础 , I I N 1 t ) A S AZ 2 5 ( SG ( 一i ) (B ( AR — O + 3 me* K 上, 按照实际 要, 建立工作装置优化设计的 ER 4 2 一 0 ) 2 其 中 A A K R 4  ̄是举 3) 4d , ) 木 z R E _3 数学模型 , 包括优化设计变量、 目标函数和约束条 升过程中铲斗底部与水平面夹角的瞬时值, 也是利 UL A UR 件, 并依据优化设计数学模型的特点, 选择优化算 用主菜单 B ID中的 ME S E选项建立的测
Adams运动仿真例子起重机的建模和仿真

1起重机的建模和仿真,如下图所示。
1)启动ADAMS1。
运行ADAMS,选择create a new model;2。
modal name 中命名为lift_mecha;3。
确认gravity 文本框中是earth normal (—global Y),units文本框中是MKS;ok4. 选择setting-—working grid,在打开的参数设置中,设置size在X和Y方向均为20 m,spacing在X和Y方向均为1m;ok5. 通过缩放按钮,使窗口显示所有栅格,单击F4打开坐标窗口.2)建模1. 查看左下角的坐标系为XY平面2. 选择setting——icons下的new size图标单位为13. 在工具图标中,选择实体建模按钮中的box按钮4。
设置实体参数;On groundLength :12Height:4Depth:85。
鼠标点击屏幕上中心坐标处,建立基座部分6. 继续box建立Mount座架部件,设置参数:New partLength :3Height:3Depth: 3.5设置完毕,在基座右上角建立座架Mount部件7。
左键点击立体视角按钮,查看模型,座架Mount不在基座中间,调整座架到基座中间部位:①右键选择主工具箱中的position按钮图标中的move按钮②在打开的参数设置对话框中选择Vector,Distance项中输入3m,实现Mount移至基座中间位置③设置完毕,选择座架实体,移动方向箭头按Z轴方向,Distance项中输入2。
25m,完成座架的移动右键选择座架,在快捷菜单中选择rename,命名为Mount8. 选择setting-working grid 打开栅格设置对话框,在set location中,选择pick 选择Mount。
cm座架质心,并选择X轴和Y轴方向,选择完毕,栅格位于座架中心选择主工具箱中的视角按钮,观察视图将spacing-working grid ,设置spacing中X和Y均为0。
基于ADAMS的装载机工作装置动力学分析

基于ADAMS的装载机工作装置动力学分析ADAMS(Advanced Dynamic Analysis of Mechanical Systems)是一种广泛应用于机械系统设计和分析中的动力学仿真软件。
装载机是一种常见的工程机械设备,用于搬运和装载各种物料。
本文将利用ADAMS软件对装载机的工作装置进行动力学分析,以探讨其运动规律和性能特点。
首先,我们需要建立装载机的运动学模型。
在ADAMS软件中,可以通过建立连接杆、关节等模型元素来描述装载机的结构,然后设置运动参数和约束条件。
特别是对于装载机的工作装置,需要考虑到各种关闭与打开装置的动作以及与装载机主体的协调运动。
接着,我们进行动力学仿真分析。
通过在ADAMS中添加质量、惯性力、弹簧、阻尼等物理特性模型元素来描述工作装置的动力学特性。
然后通过设定力学学习模型的参数,如质量、摩擦系数等,以模拟不同工作条件下的装载机运动行为。
在动力学仿真过程中,我们可以对工作装置的运动轨迹、速度、加速度等参数进行监测和分析。
通过观察工作装置在装载过程中的受力情况,可以评估其受载能力和运动稳定性。
同时,我们还可以根据仿真结果对工作装置的结构和工艺进行优化设计,以提高其工作效率和操作性。
另外,我们还可以利用ADAMS软件进行多体动力学分析,通过建立装载机和工作装置的多体模型,细化系统的结构和运动特性。
在多体动力学仿真中,我们可以模拟装载机在复杂道路条件下的运动行为,进一步评估其动态稳定性和操控性。
综上所述,基于ADAMS的装载机工作装置动力学分析可以帮助工程师深入理解装载机的运动规律和性能特点,为装载机的设计和优化提供有力支持。
通过仿真分析,可以有效减少实验测试的时间和费用,提高装载机的设计效率和性能表现。
希望本文的内容能够为相关领域的研究和应用人员提供参考和启发。
《2024年度伸缩臂叉装车行走系统优化分析与实验研究》范文

《伸缩臂叉装车行走系统优化分析与实验研究》篇一摘要:本文旨在探讨伸缩臂叉装车行走系统的优化设计及其实际应用效果。
首先,通过对行走系统的工作原理和现有问题进行深入分析,提出优化方案。
其次,通过理论建模和仿真分析,验证优化方案的可行性。
最后,通过实验研究,对优化后的行走系统进行性能评估,并得出结论。
一、引言随着工程机械的不断发展,伸缩臂叉装车作为一种重要的装载设备,其行走系统的性能直接影响到作业效率和安全性。
因此,对行走系统进行优化设计具有重要意义。
本文将重点分析伸缩臂叉装车行走系统的优化设计、理论建模、仿真分析以及实验研究等方面。
二、伸缩臂叉装车行走系统现状分析(一)工作原理伸缩臂叉装车行走系统主要由驱动系统、转向系统、制动系统和悬挂系统等组成。
驱动系统提供动力,转向系统控制行驶方向,制动系统保证安全停车,悬挂系统则起到减震作用。
(二)存在问题当前伸缩臂叉装车行走系统存在能耗高、稳定性差、操作不便等问题,影响了设备的整体性能和使用寿命。
三、行走系统优化设计(一)设计思路针对现有问题,从驱动系统、转向系统和悬挂系统等方面提出优化设计方案。
通过降低能耗、提高稳定性、优化操作等手段,提升行走系统的整体性能。
(二)具体措施1. 驱动系统:采用高效能电机和合理的传动比,降低能耗;2. 转向系统:优化转向控制策略,提高转向稳定性和灵活性;3. 悬挂系统:采用减震性能更好的悬挂装置,提高行驶平稳性。
四、理论建模与仿真分析(一)理论建模根据优化设计方案,建立行走系统的数学模型和物理模型,为后续的仿真分析提供基础。
(二)仿真分析利用仿真软件对优化后的行走系统进行仿真分析,验证其可行性和性能表现。
通过模拟实际工况,对能耗、稳定性、操作性能等指标进行评估。
五、实验研究(一)实验方法与步骤在实验场地进行实际测试,对比优化前后的行走系统在能耗、稳定性、操作性能等方面的表现。
通过数据采集和分析,评估优化效果。
(二)实验结果与分析实验结果表明,优化后的行走系统在能耗、稳定性和操作性能等方面均有显著提升。
基于ADAMS软件轿车前悬架动态模拟与仿真本科生毕业论文 精品
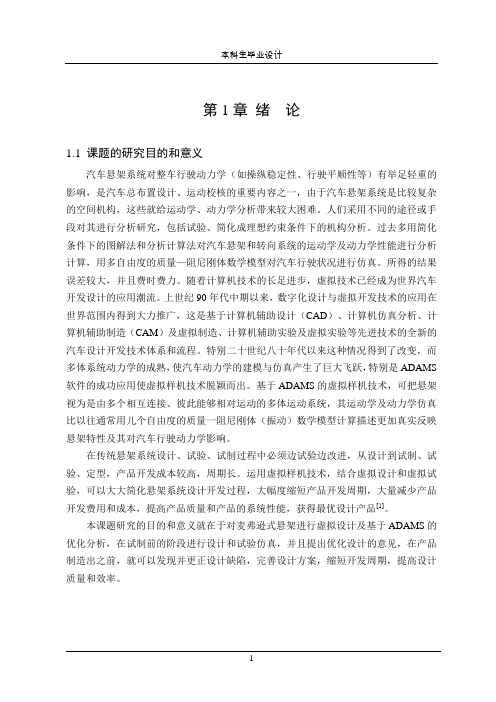
第1章绪论1.1 课题的研究目的和意义汽车悬架系统对整车行驶动力学(如操纵稳定性、行驶平顺性等)有举足轻重的影响,是汽车总布置设计、运动校核的重要内容之一,由于汽车悬架系统是比较复杂的空间机构,这些就给运动学、动力学分析带来较大困难。
人们采用不同的途径或手段对其进行分析研究,包括试验、简化成理想约束条件下的机构分析。
过去多用简化条件下的图解法和分析计算法对汽车悬架和转向系统的运动学及动力学性能进行分析计算,用多自由度的质量—阻尼刚体数学模型对汽车行驶状况进行仿真。
所得的结果误差较大,并且费时费力。
随着计算机技术的长足进步,虚拟技术已经成为世界汽车开发设计的应用潮流。
上世纪90年代中期以来,数字化设计与虚拟开发技术的应用在世界范围内得到大力推广,这是基于计算机辅助设计(CAD)、计算机仿真分析、计算机辅助制造(CAM)及虚拟制造、计算机辅助实验及虚拟实验等先进技术的全新的汽车设计开发技术体系和流程。
特别二十世纪八十年代以来这种情况得到了改变,而多体系统动力学的成熟,使汽车动力学的建模与仿真产生了巨大飞跃,特别是ADAMS 软件的成功应用使虚拟样机技术脱颖而出。
基于ADAMS的虚拟样机技术,可把悬架视为是由多个相互连接、彼此能够相对运动的多体运动系统,其运动学及动力学仿真比以往通常用儿个自由度的质量一阻尼刚体(振动)数学模型计算描述更加真实反映悬架特性及其对汽车行驶动力学影响。
在传统悬架系统设计、试验、试制过程中必须边试验边改进,从设计到试制、试验、定型,产品开发成本较高,周期长。
运用虚拟样机技术,结合虚拟设计和虚拟试验,可以大大简化悬架系统设计开发过程,大幅度缩短产品开发周期,大量减少产品开发费用和成本,提高产品质量和产品的系统性能,获得最优设计产品[1]。
本课题研究的目的和意义就在于对麦弗逊式悬架进行虚拟设计及基于ADAMS的优化分析,在试制前的阶段进行设计和试验仿真,并且提出优化设计的意见,在产品制造出之前,就可以发现并更正设计缺陷,完善设计方案,缩短开发周期,提高设计质量和效率。
基于ADAMS的装载机工作装置运动学仿真分析

[ 摘要]采用虚拟样机分析软件 A D A MS对装载机工作装置的三维模 型添加 了运动副、 负载与驱 动力, 编写了运
动过程控制函数 , 模拟 了工作装置在 工作 中的动作过程 , 从 而得到 了各主要执行部件的位移 、 速度 、 加速度及受 力曲线图, 对各个执行部件 的运动变化情况进行 了分析 。
[ Ab s t r a c t ]K i n e m a t i c p a i r ,l o a d a n d d r i v i n g f o r c e a r e a d d e d o n t h r e e — d i me n s i o n a l m o d e l o f t h e l o a d ma n i p u l a t o r b y v i r t u a l
p r o t o t y p e a n a l y s i s s o f t wa r e i n t h i s p a p e r ,c o n t r o l f u n c t i o n a b o u t mo v e me n t p r o c e s s i s c o mp i l e d ,a c t i o n p r o c e s s o f ma n i p u l a t o r i s e mu l a t e d,a n d g r a p h a b o u t d i s p l a c e me n t ,s p e e d a n d a c c e l e r a t i o n o f t h e p r i ma r y e x e c u t i o n u n i t a r e o b t a i n e d . T h u s c h a n g e o f t h e
基于ADAMS的42吨集装箱叉车转向机构的仿真与优化设计_毕业论文设计
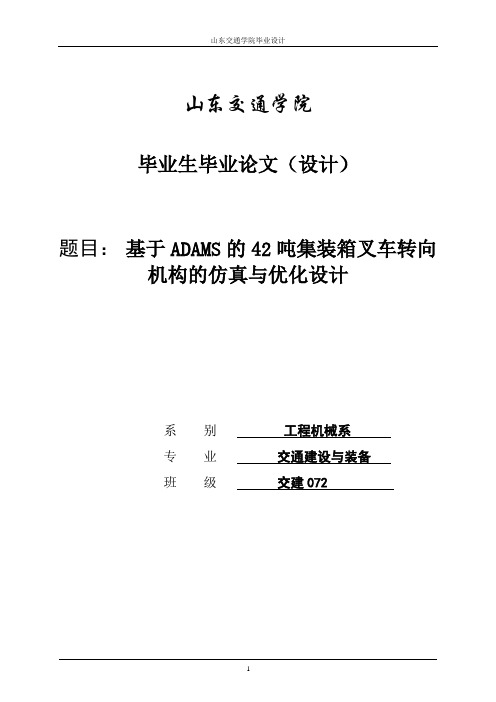
山东交通学院毕业生毕业论文(设计)题目:基于ADAMS的42吨集装箱叉车转向机构的仿真与优化设计系别工程机械系专业交通建设与装备班级交建072本文介绍了42t集装箱叉车的转向机构采用由横置液压缸组成的一组六连杆机构,为了保证车轮转向时作纯滚动,需对六连杆机构优化设计。
为了分析叉车的转向性能,采用ADAMS 软件对叉车的转向机构进行了建模仿真,测量了该转向机构的转角误差;实现了转向机构的参数化建模,以转向机构的累计转角误差最小为目标函数对转向机构进行了优化设计,并建立了叉车的整车模型,测量了叉车的外转向轮误差和整车模型的转向半径变化曲线,为分析叉车的转向性能提供了依据。
并且以优化设计的结果为参数在ADAMS中建立叉车的整车模型,仿真结果证明优化设计的有效。
关键字:ADAMS;转向机构;仿真;优化设计This article describes the 42t container forklift steering hydraulic cylinder used by the tap of a group composed of six-bar linkage, in order to ensure the steering wheel, made of pure rolling, the need for optimization of six-bar linkage design. To analyze the forklift's steering performance, the use of ADAMS, the steering mechanism on the truck the modeling and simulation, measuring the angle of the steering error; to achieve a steering mechanism of the parametric modeling, the steering angle error of the cumulative goal of minimizing function of the steering mechanism was optimized, and the establishment of a forklift vehicle model, measured outside the steering wheel forklift model error and the vehicle turning radius curve, analysis of the forklift's steering provided. And the results to optimize the design parameters to create the forklift vehicle ADAMS model, simulation results show that the effective optimal design.Key words: ADAMS;Steering system; simulation; Optimization design目录前言 (1)1绪论 (2)1.1本文研究的背景 (2)1.2虚拟样机技术 (2)1.2.1虚拟样机技术 (3)1.2.2 虚拟产品的开发流程 (3)1.3ADAMS软件的介绍 (5)1.3.1 ADAMS软件的概述 (5)1.3.2 ADAMS软件基本模块 (7)1.3.3 ADAMS 仿真分析步骤 (10)1.4平面连杆机构 (11)1.4.1 连杆机构的特点 (11)1.4.2 42吨集装箱叉车转向机构的连杆机构 (12)1.4.3横置液压缸式转向桥的结构形式 (12)2利用ADAMS对叉车转向机构进行建模 (14)2.1叉车转向机构的建模 (14)2.2应用ADAMS创建转向机构模型 (14)2.2.1启动ADAMS (14)2.2.2设置工作环境 (15)2.2.3创建设计点 (16)2.2.4创建机构的各个部件 (16)2.2.5创建车轮和地面 (17)2.2.6 保存模型 (21)3转向机构的仿真 (22)3.1叉车转向系统动力学仿真分析系统前处理模块 (23)3.2叉车转向系统动力学仿真分析系统分析计算模块 (23)3.3叉车转向系统动力学仿真分析系统后处理模块 (25)4叉车转向机构的优化设计 (26)4.1定义设计变量 (27)4.2定义目标函数 (29)4.3确定约束条件 (30)4.4优化模型 (30)5创建整车模型,仿真叉车的转向运动轨迹 (32)结论 (34)致谢 (35)参考文献 (36)前言叉车是指对成件托盘货物进行装卸、堆垛和短距离运输作业的各种轮式搬运车辆。
基于ADAMS的双叉臂悬架系统动力学研究

随着生活质量的提高,人们对汽车的要求越来越注重行驶过程平顺性以及操纵稳定性。
而悬架的结构特点对操纵稳定性和平顺性的影响至关重要[1]。
双叉臂式独立悬架是汽车悬架结构中常见的一种形式,具有诸多优点,使其广泛地应用于轿车、轻型车等的前悬架。
目前对双叉臂悬架运动规律的研究较多[2~4]。
为减少研发成本,虚拟样机技术的应用随着计算机的普及得到了大的推广。
ADA MS具有丰富的建模功能和强大的运动学与动力学解算能力,可以建立规模庞大、机构复杂的系统级仿真模型,可对悬架和整车的性能进行综合评价,被广泛应用与悬架和整车设计开发[5~8]。
为了分析双叉臂式前悬架的性能以及对操纵稳定性的影响,本文在adams/car中建立该悬架的虚拟样机模型,利用ADAMS/Insight 优化了影响悬架性能的关键硬点参数,对优化前后的悬架进行仿真分析,对比了优化前后的主销偏距、前束角、车轮外倾角等悬架性能参数,结果表明优化后的悬架操控性能有了大幅度的提升。
1 构建仿真模型在建立双叉臂悬架模型前,必须对悬架系统进行合理的数学模型简化和基本假设:整个双叉臂悬架作为一个多刚体系统进行仿真,系统的各个刚体在各方向的惯性力均为零;某些铰链在一些方向的力的约束真值比较小,对整车动力学的影响可以忽略不计,也假设其为零;减振器简化为线性弹簧和阻尼,各运动副里的摩擦力忽略不计;本文的研究重点为悬架,轮胎可简化为刚性体。
硬点是各零件之间连接处的关键几何定位点,确定硬点就是在子系统坐标系中给出零件之间连接点的几何位置。
从厂家提供的零部件装配图上可以得到硬点的坐标值。
计算或者测量整合零件的质量、质心位置以及绕质心坐标系三个坐标轴的转动惯量,将这些动力学参数填写到相应的输入中。
以硬点为基础创建几何模型,定义各零件间的运动关系,确定约束类型将各零件连接起来,从而构成模板,然后将模板生成子系统并且与试验台装配成悬架测试系统,完成双叉臂式悬架在ADA MS/C ar中的虚拟样机模型,如图1所示。
adams机械系统动力学仿真实例
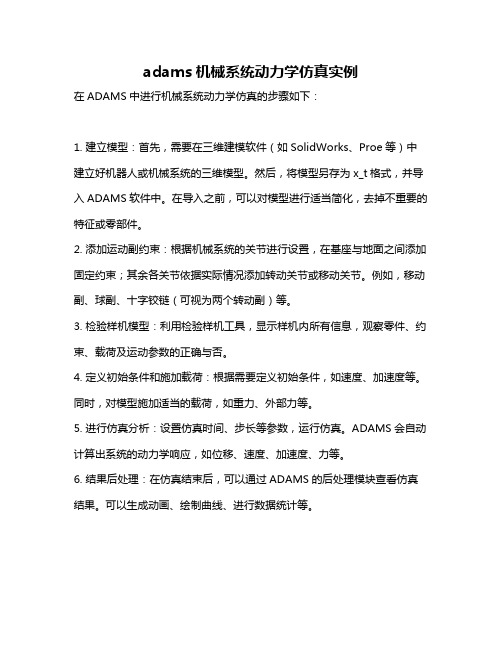
adams机械系统动力学仿真实例
在ADAMS中进行机械系统动力学仿真的步骤如下:
1. 建立模型:首先,需要在三维建模软件(如SolidWorks、Proe等)中建立好机器人或机械系统的三维模型。
然后,将模型另存为x_t格式,并导入ADAMS软件中。
在导入之前,可以对模型进行适当简化,去掉不重要的特征或零部件。
2. 添加运动副约束:根据机械系统的关节进行设置,在基座与地面之间添加固定约束;其余各关节依据实际情况添加转动关节或移动关节。
例如,移动副、球副、十字铰链(可视为两个转动副)等。
3. 检验样机模型:利用检验样机工具,显示样机内所有信息,观察零件、约束、载荷及运动参数的正确与否。
4. 定义初始条件和施加载荷:根据需要定义初始条件,如速度、加速度等。
同时,对模型施加适当的载荷,如重力、外部力等。
5. 进行仿真分析:设置仿真时间、步长等参数,运行仿真。
ADAMS会自动计算出系统的动力学响应,如位移、速度、加速度、力等。
6. 结果后处理:在仿真结束后,可以通过ADAMS的后处理模块查看仿真结果。
可以生成动画、绘制曲线、进行数据统计等。
通过以上步骤,就可以在ADAMS中进行机械系统动力学仿真了。
需要注意的是,具体的步骤可能会根据不同的机械系统和仿真需求有所不同。
因此,在进行仿真时,需要根据实际情况进行调整和修改。
基于ADAMS的货叉机构运动学仿真分析
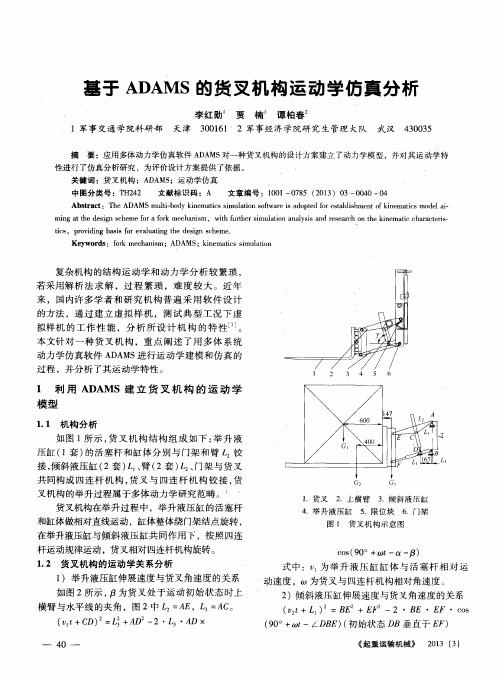
性进行 了仿 真分 析研究 ,为评价设计方 案提供 了依据 。 关键 词 :货叉 机构 ;A D A M S ;运动学仿 真
中 图 分 类 号 :T H 2 4 2 文 献 标 识 码 :A 文 章 编 号 :1 0 0 1— 0 7 8 5( 2 0 1 3 )0 3— 0 0 4 0— 0 4
1 )举升液压缸伸展速度与货叉角速度的关系 如图 2 所示 , 为货叉处于运动初始状态时上
横臂 与水 平线 的夹角 ,图 2中 L = A E,L , = A C 。
( V l t +C D) = L ; + A D 一 2・ L 3 ・ A D X
----— —
4 0. . . . — —
取货 叉 重 力 G = 1 1 7 6 N,额 定 载 荷 G : = 9 8 0 0 N。运 动 初 始状 态 四连 杆 机 构参 数 :倾 斜 液 压缸 L l =6 4 0 mm,摇 臂 L 2=6 4 0 m m,L 3=A C= 3 0 3 m m,举 升 液压 缸 两 固定 结 点之 间 的距 离 L =
接, 倾 斜 液压 缸 ( 2套 ) L 、 臂( 2套 ) L 、 门架 与 货 叉 共 同构 成 四 连 杆 机 构 , 货 叉 与 四连 杆 机 构 铰 接 , 货 叉 机构 的举 升 过程属 于 多体 动力 学研 究 范 畴 。 货叉 机构在举 升 过程 中 ,举 升液 压 缸 的活塞 杆 和缸体做 相对 直线运 动 ,缸体整 体绕 门架 结点 旋转 , 在举 升液压缸 与倾 斜 液压 缸 共 同作 用下 ,按 照 四连
基于 A D A MS的货 叉机 构 运 动 学 仿 真 分 析
李 红 勋 贾 楠 谭 柏春
1军事 交通 学院科研 部 天 津
ADAMS在汽车动力学仿真中的应用研究
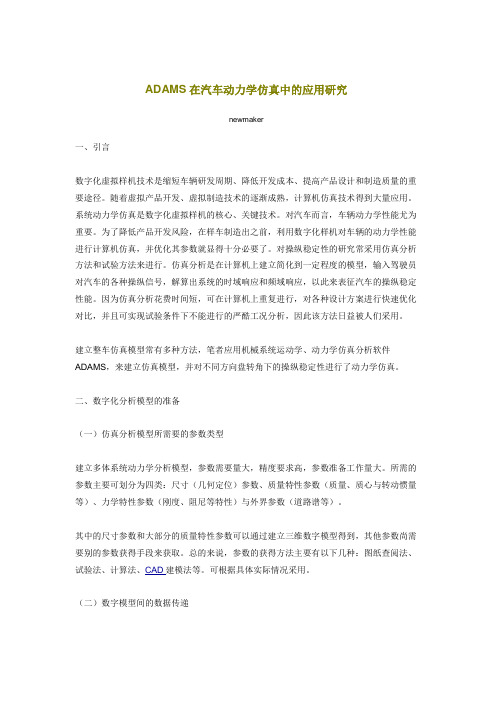
ADAMS在汽车动力学仿真中的应用研究newmaker一、引言数字化虚拟样机技术是缩短车辆研发周期、降低开发成本、提高产品设计和制造质量的重要途径。
随着虚拟产品开发、虚拟制造技术的逐渐成熟,计算机仿真技术得到大量应用。
系统动力学仿真是数字化虚拟样机的核心、关键技术。
对汽车而言,车辆动力学性能尤为重要。
为了降低产品开发风险,在样车制造出之前,利用数字化样机对车辆的动力学性能进行计算机仿真,并优化其参数就显得十分必要了。
对操纵稳定性的研究常采用仿真分析方法和试验方法来进行。
仿真分析是在计算机上建立简化到一定程度的模型,输入驾驶员对汽车的各种操纵信号,解算出系统的时域响应和频域响应,以此来表征汽车的操纵稳定性能。
因为仿真分析花费时间短,可在计算机上重复进行,对各种设计方案进行快速优化对比,并且可实现试验条件下不能进行的严酷工况分析,因此该方法日益被人们采用。
建立整车仿真模型常有多种方法,笔者应用机械系统运动学、动力学仿真分析软件ADAMS,来建立仿真模型,并对不同方向盘转角下的操纵稳定性进行了动力学仿真。
二、数字化分析模型的准备(一)仿真分析模型所需要的参数类型建立多体系统动力学分析模型,参数需要量大,精度要求高,参数准备工作量大。
所需的参数主要可划分为四类:尺寸(几何定位)参数、质量特性参数(质量、质心与转动惯量等)、力学特性参数(刚度、阻尼等特性)与外界参数(道路谱等)。
其中的尺寸参数和大部分的质量特性参数可以通过建立三维数字模型得到,其他参数尚需要别的参数获得手段来获取。
总的来说,参数的获得方法主要有以下几种:图纸查阅法、试验法、计算法、CAD建模法等。
可根据具体实际情况采用。
(二)数字模型间的数据传递基于CAD/CAM软件建立三维数字模型是建立数字化分析模型的基础。
使用CAD/CAM软件建立系统的三维实体数字模型,并以各个运动部件的形式先将零部件合并,装配好;将模型存为ADAMS软件可调用的特定格式的数据文件;然后利用CAD/CAM软件与ADAMS 软件之间的数据接口文件将三维模型传递到ADAMS软件中去;之后输入各运动部件的密度等必要参数,就可以直接得到各运动部件的质量、质心与转动惯量等质量参数。
- 1、下载文档前请自行甄别文档内容的完整性,平台不提供额外的编辑、内容补充、找答案等附加服务。
- 2、"仅部分预览"的文档,不可在线预览部分如存在完整性等问题,可反馈申请退款(可完整预览的文档不适用该条件!)。
- 3、如文档侵犯您的权益,请联系客服反馈,我们会尽快为您处理(人工客服工作时间:9:00-18:30)。
图5
变幅液压缸伸缩位移变化曲线
伸缩臂变幅过程中, 货叉属具水平方向移动 速度和位移变化曲线如图 6 和图 7 ,伸缩臂与水平 面夹角为 1. 1° 时, 货叉属具沿 X 轴正向最大速度 为 54. 46 mm / s; 与水平面夹角为 10. 48° 时, 货叉 属具沿 X 轴正向最大速度为 0 ; 与水平面夹角为 52. 42° 时, 货 叉 属 具 沿 X 轴 负 方 向 最 大 速 度 为 386. 68 mm / s。货叉属具垂直方向移动速度和位移 变化曲线如图 8 和图 9 , 伸缩臂与水平面夹角为 22. 7° 时, 货 叉 属 具 沿 X 轴 正 向 最 大 速 度 为 609 mm / s。 — 59 —
2013 ( 9 )
— 57 —
于多刚体系统动力学分析。 为了研究在作业过程 中叉装车 工 作 装 置 的 运 动 与 作 用 力 之 间 的 关 系 , 进而展开工作装置作业性能方面的研究, 需要建 立合理的叉装车工作装置动力学模型 。
表1 序号 1 2 3 4 5 6 7 8 9 10 11 12 13
二级臂与货叉属具 伸缩液压缸筒与基本臂 伸缩液压缸杆与二级臂 伸缩液压缸筒与液压缸杆 变幅液压缸筒与车架 变幅液压缸杆与基本臂 变幅液压缸筒与液压缸杆 货叉倾翻液压缸筒与二级臂 倾翻液压缸杆与货叉属具 货叉倾翻液压缸筒与液压缸杆 货叉与地面
图1
伸缩臂叉装车工作装置 CAD 模型
14
1. 1
环境设置 首先设置坐标系统为 Cartesian,设定全局坐标
1. 4
模型校验
利用模型检验工具对所建模型 ( 如图 2 ) 是否 存在错误进行检验, 如模型运动副对齐不准或零 件约束不当等。 在 Tools 菜单中选择 Model Verify, 通过命令显示信息窗口可以得到模型的重要信息, 包括移动的零件和运动副的数量及模型的自由度 数,并说明模型是否合理。 此外, 还可以用对象 测量和交互式仿真对模型进行检验, 同时, 仿真
系的原点位于伸缩臂与车架铰接点 ,X 轴为沿伸缩 臂向前的方向,Y 轴为垂直于伸缩臂叉装车车架向 上,Z 轴为垂直于 X 、 Y 轴方向向外; 单位设置为 mm、kg、N、s; 设置重力加速度方向沿 Y 轴负方
2 向,加速度大小为 9 806. 65 mm / s 。
零部件名称 一级臂 二级臂 货叉属具 变幅液压缸 伸缩液压缸 属具调平液压缸
图4
变幅液压缸伸缩速度变化曲线
2
2. 1
伸缩臂变幅运动学与动力学特性仿真
伸缩臂全缩、空载状态 在伸缩臂全缩、 空载状态, 设定伸缩液压缸 step( time, 0, 0, 15 , 905 )
驱动函数: 仿真时间 15 s,运行 200 步,伸缩臂在驱动函 数作 用 下 变 幅 至 最 大 位 置, 得 出 该 状 态 下 仿 真 结果。 伸缩臂全缩、 空载状态, 变幅液压缸由初始 位置变幅至最高位置过程中, 伸缩臂与车架铰接 点受力和变幅液压缸受力变化曲线如图 3 所 示。 伸缩臂从 最 低 位 置 变 幅 至 角 度 最 大 位 置 过 程 中 , 铰接点受力和变幅液压缸受力逐渐减小, 最大受 力点为伸缩 臂 在 最 低 位 置 ( 水 平 面 以 下 3. 14° ) , 铰接点受力最大值为 83. 35 kN, 变幅液压缸受力 最大值为 105 kN; 最小受力点为伸缩臂在最高位 置 ( 与水平面夹角为 66. 5° ) , 铰接点受力最小值 为 49. 37 kN,变幅液压缸受力最小值为 68. 48 kN。
伸缩臂由最低位置变幅至角度最大位置过程 中,变幅液压缸的伸缩速度变化曲线如图 4 所示, 最高速度为伸缩臂与水平面夹角为 35. 33° , 伸缩 速度为 94. 35 mm / s。 变幅液压缸的伸缩位移变化 曲线如图 5 所示, 变幅范围为 1 340 ~ 2 245 mm, 液压缸行程 905 mm。
辆,它将轮式起重机的伸缩臂式结构与传统叉装 车的装卸功能有机地结合, 充分利用了伸缩臂式 结构伸得高、 伸得远的特点, 在底盘不动的情况
[ 3] 张质 文,虞 和 谦,王 金 诺,等 . 起 重 机 设 计 手 册 面尺寸既合理也满足要求, 与用强度条件计算出 来的主梁截面尺寸相比要小, 同时主梁整体自重 减小 5% 左右,节约了大量成本。另外,对于主梁 受载差别很大时, 为设计者提供了一种新的设计 思路。
1. 2
添加约束 约束是指两构件之间的联接关系, 它限制两
构件在某个方向上的相对运动, 相对运动的方向 由约束的类型决定。 ADAMS 具有十分丰富的约束 库,包括 低 副 ( Joints ) 、 高 副 ( Higher Pair Constraints) 、基本副 ( Joint Primitives ) 3 类。 约束施 加的正确与否将直接影响动力学分析的准确性和 样机虚拟试验结果的有效性。 本文主要采用低副 和基本副。 表 1 列出了伸缩臂叉装车工作装置仿 真模型的约束副类型。 1. 3 施加载荷 作用于伸缩臂上的载荷分为动态载荷和附加 载荷,其中动态载荷包括伸缩臂总成质量、 工作 载荷及 惯 性 力; 附 加 载 荷 包 括 侧 向 力 和 风 载 荷。 — —伸缩臂系统的仿真,主要考虑伸 对于工作装置— — 58 —
参考文献 [ 1] 王金诺,于兰峰 . 起重运输机械金属结构[ M] . 北京: 中国铁道出版社,2002. [ 2] GB / T 3811 —2008 《起重运输机械》 S] . 起重机设计规范[ [ M] . 北京: 中国铁道出版社,1998. [ 4] 浦 广 益 . Ansys Workbench 12 基 础 教 程 与 实 例 详 解 [ M] . 北京: 中国水利水电出版社,2010. 作 地 邮 者: 路光远 址: 山西省太原市万柏林区窊流路 66 号太原科技大 学研究生学院 47 号信箱 编: 030024 收稿日期: 2013 - 04 - 05
置变幅至最高位置的过程中, 伸缩臂与车架铰接 点受力和变幅液压缸受力变化曲线如图 10 所示。 伸缩臂从最低位置变幅至角度最大位置的过程中, 铰接点受力和变幅液压缸受力逐渐减小, 最大受 力点为伸缩 臂 在 最 低 位 置 ( 水 平 面 以 下 3. 14° ) , 铰接点受力最大值为 348. 5 kN, 变幅液压有多种作业功能的车
下,对离前轮较远的物资进行装卸作业, 如对集 装箱内物资的装箱、 掏箱作业, 使作业效率大为 提高。叉装车底盘具备四轮驱动、 四轮转向、 蟹 行以及整车调平等功能,特别适合野外作业。 伸缩臂叉装车是一个多变量、 本质非线性的 复杂动力学系统, 因此工作装置的动力学分析属
《起重运输机械》 2013 ( 9 )
分析前进行装配也有助于纠正错误的约束 。
图2
伸缩臂叉装车工作装置动力学仿真模型 1. 变幅液压缸受力 2. 铰接点受力 图3 伸缩臂全缩、空载状态变幅液压缸 和车架铰接点受力变化曲线
1. 5
施加驱动
伸缩臂的变幅运动、 伸缩运动以及货叉的俯 仰运动分别是由变幅液压缸、 伸缩液压缸和属具 调平液压缸的伸缩运动实现的。 对模型进行仿真, 首先需要在各驱动液压缸上施加驱动, 本文采用 step 函 数 来 实 现。 step 函 数 是 阶 跃 函 数, 形 式 如下: step( A, x0 , h0 , x1 , h1 ) 其中,A 为 X 轴的变量名或一系列的 z 值, x0 为开始出现阶跃情况时的 x 值, h0 为当 x 小于或 等于 x0 时所对应的 y 值, x1 为阶跃情况结束时的 x 值,h1 为当 x 大于或等于 x1 时所对应的 y 值。 伸缩臂实际工作时, 具体的工况是多种多样 的,因此在仿真过程中, 无法对各种实际工况进 行一一模拟。 本文分别对伸缩臂变幅、 伸缩、 货 叉俯仰动作依次进行仿真分析。
缩臂总成质量和工作载荷, 伸缩臂在运动过程中 受到的惯性力、 侧向力及风载荷暂不考虑。 伸缩 臂质量是指伸缩臂总成所有的固定部分和活动部 分构件的质量,工作装置零部件材料及质量如表 2 所示。
表2 序号 1 2 3 4 5 6 工作装置零部件材料及质量 材料 质量 / kg 920 700 钢 550 90 260 80
工作装置模型约束副类型 配合零件 车架与大地 基本臂与车架 基本臂与二级臂 约束副类型 固定副 旋转副 滑移副 旋转副 旋转副 圆柱副 圆柱副 旋转副 圆柱副 圆柱副 旋转福 圆柱副 圆柱副 平行副
1
工作装置 ADAMS 仿真模型的建立
在 SolidWorks 中建立工作装置的几何模型,由 — —伸缩臂总成, 车架只 于研究对象为工作装置— 是作为 固 定 基 座, 故 对 车 架 模 型 结 构 进 行 简 化, 所建立的工作装置 CAD 模型如图 1 所示。 将其保 存为 . x _ t 格式的模型文件, 然后导入 ADAMS / View ,建立其动力学仿真模型。
基于 ADAMS 的伸缩臂叉装车工作装置 运动学与动力学仿真
闫洪峰 王伟平 王 志 中国农业机械化科学研究院 齐向阳 北京 100083
摘
— —伸缩臂为研究对象,建立了其 ADAMS 仿真模型。 在不同伸缩长 要: 以伸缩臂叉装车的工作装置 —
度、不同承载条件下,对变幅机构进行了运动学与动力学特性仿真 。 在最大负载、 吊臂处于不同变幅角度条件 下,对属具调平机构进行了动力学特性仿真 。在吊臂处于水平、 承载 1 500 kg 负载状态下进行了伸缩机构动力 学仿真。得出了伸缩臂叉装车工作装置各部件的运动规律以及关键部件和关键受力位置的受力变化规律,对伸 缩臂叉车的设计和优化具有重要的参考价值 。 关键词: 伸缩臂叉装车; 工作装置; 运动学; 动力学; 仿真 中图分类号: TP242 文献标识码: A 文章编号: 1001 - 0785 ( 2013 ) 09 - 0057 - 06 Abstract: With the working device of telescopic boom fork truck - telescopic boom as a study object,ADAMS simulation model is built. Under the condition of different expansions and different loads,the kinematics and dynamics simulation is performed for the luffing mechanism. In case of maximum load, when the suspended arm is in different luffing angles,the dynamic characteristic simulation is performed for the luffing mechanism; under the condition of the suspended arm in horizontal condition,the dynamic simulation is performed for expansion mechanism under 1500 kgloading state. The movement rules of each part of working device of telescopic boom fork truck, and force change rules of critical parts and forced positions are worked out, which can provide significant value for design and optimization of telescopic boom fork truck. Keywords: telescopic boom fork loading device; working device; kinematics; dynamics; simulation