陶瓷胶态注射成型技术
CIM(陶瓷注射成型)简介

Company Confidential
1.1 CIM工艺流程
陶瓷粉体 混炼 有机载体 后续加工 造粒 注射成型 脱脂
烧结
①注射喂料的制备,将合适的有机载体(具有不同性质和功能的有机物) 与陶 瓷粉末在一定温度下混炼、干燥、造粒,得到注射用喂料; ②注射成型,混炼后的注射混合料于注射成型机内被加热转变为粘稠性熔体, 在一定的温度和压力下高速注入金属模具内,冷却固化为所需形状的坯体, 然后脱模; ③脱脂,通过加热或其他方法,将注射成型坯体内的有机物排除; ④烧结,脱脂后的陶瓷素坯在高温下致密化烧结,获得所需外观形状、尺寸 精度和显微结构的致密陶瓷部件。
Company Confidential
1.4 CIM 应用展示
轴类/轴承类/轴承套
齿轮
Company Confidential
1.4 CIM 应用展示
手表配件
线嘴/喷嘴
表盘/手表配件
Company Confidential
纺织配件
1.4 CIM 应用展示
斜口钳
推剪
刀片
阀门
Company Confidential
生产效率
大量生产
技术要点
添加剂选择,脱
脂
粉末+ 有机材料( 4~ 8%)
粉末+ 有机材料( 3~ 8%) 粉末+ 各种材料+ 水 粉末+ 各种材料+ 有机溶剂 粉末+ 有机材料+ 水
间歇、自动 大量生产
颗粒调整
干式大流量 颗粒调整、磨具 生产 设计 间歇式 控制粒度、调整 粉浆
200~ 15
粒度分布,粉浆 自动大量生 调整,有机物选 产 择 添加剂选择
陶瓷原位凝固胶态成形基本原理及工艺过程
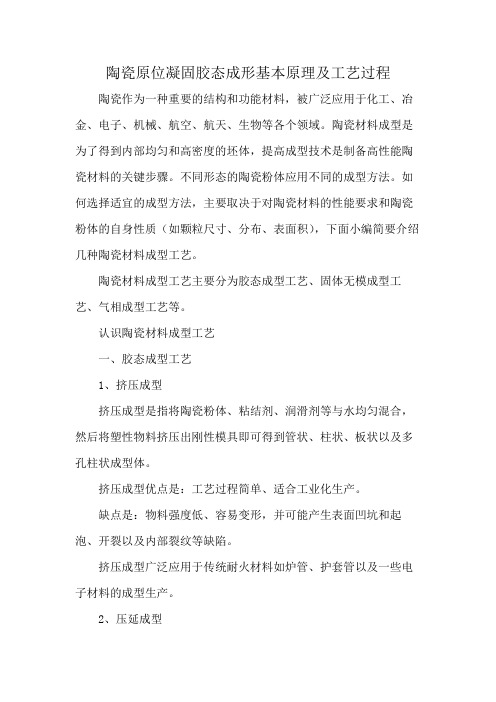
陶瓷原位凝固胶态成形基本原理及工艺过程陶瓷作为一种重要的结构和功能材料,被广泛应用于化工、冶金、电子、机械、航空、航天、生物等各个领域。
陶瓷材料成型是为了得到内部均匀和高密度的坯体,提高成型技术是制备高性能陶瓷材料的关键步骤。
不同形态的陶瓷粉体应用不同的成型方法。
如何选择适宜的成型方法,主要取决于对陶瓷材料的性能要求和陶瓷粉体的自身性质(如颗粒尺寸、分布、表面积),下面小编简要介绍几种陶瓷材料成型工艺。
陶瓷材料成型工艺主要分为胶态成型工艺、固体无模成型工艺、气相成型工艺等。
认识陶瓷材料成型工艺一、胶态成型工艺1、挤压成型挤压成型是指将陶瓷粉体、粘结剂、润滑剂等与水均匀混合,然后将塑性物料挤压出刚性模具即可得到管状、柱状、板状以及多孔柱状成型体。
挤压成型优点是:工艺过程简单、适合工业化生产。
缺点是:物料强度低、容易变形,并可能产生表面凹坑和起泡、开裂以及内部裂纹等缺陷。
挤压成型广泛应用于传统耐火材料如炉管、护套管以及一些电子材料的成型生产。
2、压延成型压延成型是指将陶瓷粉体、添加剂和水混合均匀,然后将塑性物料经两个相向转到滚柱压延,而成为板状素坯的成型方法。
压延法成型优点是:密度高,适于片状、板状物件的成型。
3、注射成型陶瓷注射成型是借助高分子聚合物在高温下熔融、低温下凝固的特性来进行成型的,成型之后再把高聚物脱除。
注射成型优点是:可成型形状复杂的部件,并且具有高的尺寸精度和均匀的显微结构。
缺点是:模具设计加工成本和有机物排除过程中的成本比较高。
目前,注射成型新技术主要有水溶液注射成型和气相辅助注射成型。
(1)水溶液注射成型水溶液注射成型采用水溶性的聚合物作为有机载体,很好的解决了脱脂问题。
水溶液注射成型技术优点是:自动化控制水平高,而且成本低。
(2)气体辅助注射成型气体辅助注射成型是把气体引入聚合物熔体中而使成型过程更容易进行。
适合于腐蚀性流体和高温高压下流体的陶瓷管道成型。
4、注浆成型注浆成型工艺是利用石膏模具的吸水性,将制得的陶瓷粉体浆料注入多孔质模具,由模具的气孔把浆料中的液体吸出,而在模具中留下坯体。
陶瓷注射成型技术
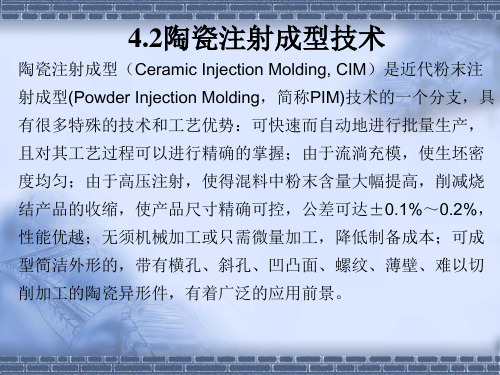
▪ 练泥时间:时间过短则练泥混合效果不好,时间过长则练泥混合效率不高
1) 粉末应专门配制,以求高的极限填充密度和低的成本; 2) 2) 粉末不结块团聚; 3) 3) 粉末外形主要为球形; 4) 4) 粉末间有足够的摩擦力以避开粘结剂脱出后坯件变
形或塌陷,在大多数情况下,自然坡度角应大于55°; 5) 5) 为利于快速烧结,应具有小的平均粒度,一般要
求小于1μm; 6) 6) 粉末本身致密,无内孔隙; 7) 7) 粉末的表面清洁,不会与粘结剂发生化学反应。
立式注射成型机
注射成型机构组成
▪ 可塑化机构(注射机构) ▪ 合模机构(包括模具) ▪ 油压机构 ▪ 电气掌握机构
注射成型模具
注射成型制备氧化锆坯体
注射成型制备氧化锆坯体
注射成型过程中缺陷的掌握
▪ 在注射成型过程中缺陷的掌握基本可从两个方面考 虑:一方面是成型温度、压力和时间三者关系设定; 另一方面是填充时喂料在模腔中的流淌。由于CIM 产品大多数是外形简洁、精度要求高的小尺寸零件, 混料在模腔的流淌就牵涉到模具设计问题,包括进 料口位置、流道的长度、排气孔的位置等,都需对 混料流淌性质、模腔内温度和残余应力分布等参数 有清楚了解。现行计算机充模过程动态模拟,正为 注射成型这一步供应理论指导。
孔洞缺陷
▪ 孔洞,指在生坯的横截面上可以发现的孔隙。 有的是一个近圆形的小孔,有的就进展为几 乎贯穿生坯坯体的中心通孔,这是常见的缺 陷.
陶瓷注射成型技术教学课件ppt
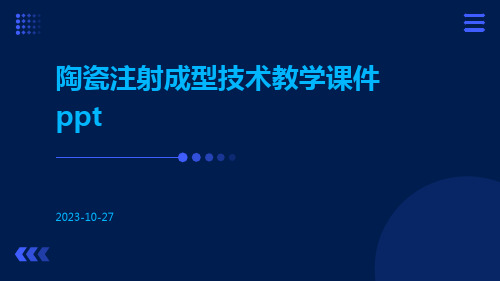
陶瓷注射成型技术的优缺点及与其他成型技术的比较 最新研究进展和未来发展趋势
02
陶瓷注射成型技术概述
陶瓷注射成型技术的定义
陶瓷注射成型技术是一种将陶瓷粉末、粘结剂、增塑剂等原 料混合,通过注射机注入模具,经干燥、烧结后获得致密陶 瓷成品的工艺方法。
陶瓷注射成型技术结合了塑料注射成型技术和传统陶瓷成型 技术的优点,具有成型复杂形状、高精度、高一致性等优势 。
注射机
将混合好的原料注射到模具中 ,形成所需形状的坯体。
模具
用于确定坯体的形状和尺寸, 通常由金属或陶瓷制成。
压机
用于将注射好的坯体进行压缩 ,以提高其密度和强度。
烧结设备
烧结炉
用于将坯体进行高温烧结,使其成为具有足够强 度的成品。
烧结助剂
为了促进烧结过程的进行,通常需要添加一些烧 结助剂。
冷却装置
高技术陶瓷领域
如电子、通讯、能源、环保等 领域的零部件制造。
精密陶瓷领域
如光学、机械、航空航天等领域 的零部件制造。
功能陶瓷领域
如压电、热敏、磁性等领域的电子 元器件制造。
03
陶瓷注射成型技术工艺流程
原料制备
原料储存
配料计算
保证原料的化学性质稳定,避免吸潮、氧化 等。
根据所需制备的陶瓷部件的尺寸和性能要求 ,计算所需原料的种类和数量。
球磨混合
干燥与除气
将原料加入球磨机中,加入适量的水或其他 溶剂,混合均匀,以保证原料的分散性。
通过干燥和除气处理,去除原料中的水分和 气泡,保证注射成型的质量。
模具设计
01
02
03
模具材料选择
根据陶瓷部件的形状和尺 寸要求,选择合适的模具 材料,如金属、塑料等。
胶态成型的工艺和原理

胶态成型的工艺和原理
胶态成型是一种材料加工技术,其工艺和原理如下:
1. 工艺:将陶瓷粉体、溶剂、粘接剂、增塑剂的混合浆料通过刮刀浇筑在一个平面基体上,均匀铺展、溶剂挥发后,形成具有一定强度和柔韧性的陶瓷坯片(生片)。
2. 原理:胶态成型利用浆料的流变学性质,在一定条件下使浆料形成稳定的悬浮体系或黏弹性胶体,再通过固化或干燥过程实现成型。
这种工艺可以使材料在分子尺度上重新排列,以达到制备高性能、高精度、高一致性产品的目的。
在胶态成型中,浆料的流变特性对成型过程和产品质量有重要影响。
了解和控制这些因素,可以提高产品性能和减少生产成本。
以上内容仅供参考,建议查阅胶态成型相关书籍获取更多专业信息。
陶瓷高压注浆成型工艺

陶瓷高压注浆成型工艺
陶瓷高压注浆成型工艺是一种将陶瓷粉末和粘合剂混合后,通过高压
注射机将混合物注入模具中进行成型的工艺。
具体工艺流程如下:
1.准备原料:将陶瓷粉末和粘合剂按一定比例混合。
2.注浆:将混合物倒入高压注射机中,通过高压将混合物注入模具中。
在注入过程中,需要控制注入速度和压力,以保证成型品的质量。
3.固化:注浆完成后,待陶瓷材料固化后,即可将成型品取出。
4.烧结:成型品经过固化后需要进行烧结,以使其获得更高的密度和
硬度。
5.加工处理:烧结后的陶瓷成型品需要进行加工处理,如磨光、抛光等,以使其表面光滑。
陶瓷高压注浆成型工艺具有成品的尺寸精度高、表面光滑、强度高、
耐磨性好等优点,广泛应用于电子、机械、化工等领域的制造。
陶瓷的注射成型技术.

陶瓷的注射成型技朮随着现代陶瓷越来越多地被应用在先进热机组件上,注射成型以其适于大批量生产复杂形状陶瓷制品而倍受重视。
现代陶瓷在高温强度和耐磨性等方面具有优异的性能,但其硬度很大,采用机械加工成本极高,而采用注射成型技朮,由于坯体的成型形状接近制品的最终形状,使得这一问题得到了解决。
尽管许多工艺都可用来制造陶瓷,但对于高尺寸精度、复杂形状陶瓷制品的大批量生产,仅可通过粉浆浇注和注射成型来实现,而后者更快。
陶瓷的注射成型技朮有着诸多优点,用它制备复杂形状陶瓷组件,不仅产品尺寸精度高、表面条件好,而且省去了后加工操作,降低了生产成本,缩短了生产周期,还具有自动化程度高,适合于大规模生产的特点。
该工艺一般包括下列步骤:陶瓷粉的选取﹔粘结剂的选取﹔陶瓷粉与粘结剂的均匀混合﹔注射成型﹔脱脂(脱粘结剂)﹔烧结。
其中,脱脂是成功的关键。
1原料1.1陶瓷粉的选取陶瓷粉的特性如颗粒形貌、粒度分布、平均粒径、比表面以及表面自由能等对整个工艺的其它环节都有很大的影响﹝6~8﹞。
理想的陶瓷粉应该具有如下特点:(1)粒度分布宽,平均粒径小,适于快速烧结。
(2)以球形(或等轴)为主,填充密度高,有足够的粒间摩擦,以避免变形。
(3)表面洁净,无团聚。
(4)无毒害,低成本。
1.2粘结剂的选取粘结剂能使粉末填充成预期形状,它对整个工艺有重要的影响。
理想的粘结剂应具备下列特点:(1)在成型温度下纯粘结剂的粘度在0.1Pa.s以下,流动时不发生与粉体的分离,冷却后有足够的强度和硬度。
(2)为惰性物质,与粉体无反应。
(3)在成型和混合温度以上才分解,分解产物无毒性、腐蚀性且残余灰分少。
(4)膨胀系数低,由热膨胀或结晶引起的残余应力低。
(5)符合环保要求,价廉,安全﹔不吸湿,无易挥发组分,贮藏寿命长。
目前使用的大多数粘结剂可分为3类:蜡基或油基粘结剂、水基粘结剂和固体聚合物溶液。
表1列出了各类粘结剂的典型成分。
表1陶瓷注射成型用粘结剂的成分蜡基粘结剂通常含3、4种组分。
Al2O3陶瓷注射成型工艺实验研究

Al2O3陶瓷注射成型工艺实验研究摘要:采用注射成型的方法制备出了Al2O3陶瓷,根据实验结果分析了陶瓷粉末装载量、混炼温度高低、加料的先后顺序等因素对氧化铝陶瓷喂料性能的影响。
并使用热重分析仪分析了粘结剂物料体系的热特性,用扫描电镜分析了成型后的各种胚料的显微结构。
关键词:氧化铝;注射成型;喂料陶瓷注射成型(CeramicInjectionMolding,简称CIM)是一种制备陶瓷零部件的新型工艺,是在聚合物注射成型工艺的基础上并与陶瓷制备工艺相结合发展而来的,尤其适于制作尺寸精度高、批量大、形状复杂的陶瓷制品[1-2]。
陶瓷制品由于其较高的硬度和固有的脆性,这使得其机械加工具有很高的成本,在传统的生产工艺中约占整个陶瓷成品成本的30%~50%。
而用CIM技术制造的陶瓷产品极大地降低了加工成本,因此陶瓷注射成型技术被认为是当前最热门的精密陶瓷零部件成型技术之一,有广泛的应用前景。
陶瓷注射成型主要包括四个方面,配料及混炼、注射成型、脱脂和烧结[6]。
本文采用注射成型的方法制备Al2O3陶瓷,重点研究了在含有石蜡-聚烯烃粘结剂体系的情况下氧化铝陶瓷注射成型喂料的配方及对制备工艺的影响,期望制备出混料均匀,缺陷少的Al2O3陶瓷试样。
1实验1.1实验材料注射成型用氧化铝粉为高纯超细氧化铝粉,其平均粒径为0.56μm,αAl2O3,纯度为99.99%。
粘结剂体系选用醋酸乙烯-乙烯共聚物(EVA,分析纯),聚丙烯(PP,化学纯),硬脂酸(SA,分析纯),石蜡(PW,分析纯),邻苯二甲酸二丁酯(DBP,分析纯)。
1.2实验过程按一定的配比将粉末和有机粘结剂称量好,混炼设备采用双辊炼胶机,先将辊筒升温到170℃,加入聚丙烯和醋酸乙烯-乙烯共聚物,待融化后,再逐渐加入氧化铝粉末,然后依次加入石蜡、硬脂酸和邻苯二甲酸二丁酯,待物料充分分散与混炼后,进行造粒。
实验采用的JPH10型注射成型机由广东泓利公司生产,脱脂在电阻炉上进行,于空气气氛中脱脂,采用的是热脱脂工艺。
陶瓷凝胶注模成型技术

智能化
引入自动化和智能化的技 术手段,实现陶瓷凝胶注 模成型的远程监控和智能 化控制。
绿色化
发展环保型的陶瓷凝胶注 模成型材料和工艺,降低 生产过程中的环境污染。
未来研究方向
新材料体系
研究新型的陶瓷凝胶注模成型材 料,拓展其应用领域和应用范围。
工艺优化
探索更高效的陶瓷凝胶注模成型工 艺,提高产品的性能和降低生产成 本。
对未来的展望1Fra bibliotek随着科技的不断发展,陶瓷凝胶注模成型技术有 望在更多领域得到应用,如生物医疗、环保等。
2
未来,该技术的研究重点将放在提高陶瓷部件的 性能、降低生产成本、优化工艺参数等方面,以 更好地满足市场需求。
3
同时,随着环保意识的提高,开发环保型高分子 凝胶和绿色生产工艺将是未来的重要研究方向。
陶瓷凝胶注模成型技术
contents
目录
• 引言 • 陶瓷凝胶注模成型技术原理 • 陶瓷凝胶注模成型技术应用 • 陶瓷凝胶注模成型技术发展前景 • 结论
01 引言
背景介绍
01
陶瓷材料在工业领域的应用广泛 ,如高温炉、电子设备、航空航 天等。
02
传统陶瓷成型技术存在一些局限 性,如生产效率低、成本高、产 品性能不稳定等。
技术概述
陶瓷凝胶注模成型技术是一种新型的陶瓷成型技术,利用有机高分子凝胶作为载 体,将陶瓷粉体均匀分散在凝胶中,通过注模、固化、脱模等工序制备出形状复 杂的陶瓷部件。
该技术具有操作简便、生产效率高、成本低、产品性能优异等优点,在陶瓷领域 具有广阔的应用前景。
02 陶瓷凝胶注模成型技术原 理
凝胶注模成型原理
高经济效益。
05 结论
技术总结
陶瓷凝胶注模成型技术是一种先进的陶瓷成型技术,它利用高分子凝胶作为载体,将陶瓷浆料注入模 具中,通过固化、干燥和烧成等工艺过程,制备出高性能的陶瓷部件。
4.2陶瓷注射成型技术解析

的应用等 ▪ 在国内中南工业大学粉末冶金国家重点实验室开发出精密双
螺旋混练机陶瓷内衬和具有双螺纹的陶瓷喷嘴等 ;而华中科 技大学材料学院应用CIM技术成功开发出氧化锆氧传感器.
陶瓷粉末注射成型基本工艺流程图
注射成型技术对陶瓷粉末的要求
注射成型粘结剂体系
▪ 注射成型中的粘结剂有两个基本的功能。首先在注 射成型阶段能够和粉末均匀混合,加热后能够使得 粉末具有良好的流动性;其次,粘结剂能够在注射 成型后和脱脂期间起到维持坯体形状的作用。可以 说,粘结剂是粉末注射成型技术中的核心和关键, 每次注射成型工艺的提高和突破都伴随着新粘结体 系的诞生。在CIM中,由于粉末粒度比金属粉末注 射成型中的细小,粉末本身的流动性差,粉末和粘 结剂混合后粉末之间的间隙极小,造成脱脂困难, 这就对粘结剂提出了更苛刻的要求。因此,作为陶 瓷注射成型粘结剂,必须具备以下条件:
立式注射成型机ຫໍສະໝຸດ 注射成型机构组成▪ 可塑化机构(注射机构) ▪ 合模机构(包括模具) ▪ 油压机构 ▪ 电气控制机构
注射成型模具
注射成型制备氧化锆坯体
注射成型制备氧化锆坯体
注射成型过程中缺陷的控制
▪ 在注射成型过程中缺陷的控制基本可从两个方面考 虑:一方面是成型温度、压力和时间三者关系设定; 另一方面是填充时喂料在模腔中的流动。因为CIM 产品大多数是形状复杂、精度要求高的小尺寸零件, 混料在模腔的流动就牵涉到模具设计问题,包括进 料口位置、流道的长度、排气孔的位置等,都需对 混料流动性质、模腔内温度和残余应力分布等参数 有清楚了解。现行计算机充模过程动态模拟,正为 注射成型这一步提供理论指导。
系
【精品文章】一分钟了解陶瓷材料胶态成型方法
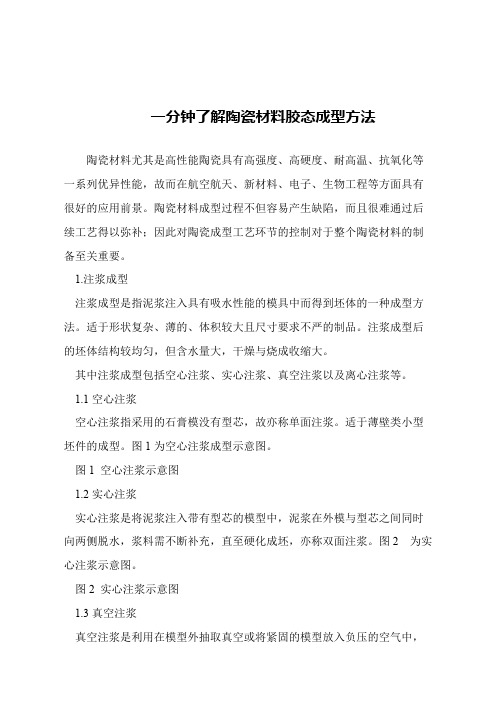
一分钟了解陶瓷材料胶态成型方法
陶瓷材料尤其是高性能陶瓷具有高强度、高硬度、耐高温、抗氧化等一系列优异性能,故而在航空航天、新材料、电子、生物工程等方面具有很好的应用前景。
陶瓷材料成型过程不但容易产生缺陷,而且很难通过后续工艺得以弥补;因此对陶瓷成型工艺环节的控制对于整个陶瓷材料的制备至关重要。
1.注浆成型
注浆成型是指泥浆注入具有吸水性能的模具中而得到坯体的一种成型方法。
适于形状复杂、薄的、体积较大且尺寸要求不严的制品。
注浆成型后的坯体结构较均匀,但含水量大,干燥与烧成收缩大。
其中注浆成型包括空心注浆、实心注浆、真空注浆以及离心注浆等。
1.1空心注浆
空心注浆指采用的石膏模没有型芯,故亦称单面注浆。
适于薄壁类小型坯件的成型。
图1为空心注浆成型示意图。
图1 空心注浆示意图
1.2实心注浆
实心注浆是将泥浆注入带有型芯的模型中,泥浆在外模与型芯之间同时向两侧脱水,浆料需不断补充,直至硬化成坯,亦称双面注浆。
图2 为实心注浆示意图。
图2 实心注浆示意图
1.3真空注浆
真空注浆是利用在模型外抽取真空或将紧固的模型放入负压的空气中,。
陶瓷注塑成型工艺介绍

陶瓷注塑成型工艺介绍引言:陶瓷注塑成型工艺是一种常用于制造复杂形状陶瓷制品的方法。
它结合了注塑成型和陶瓷材料的特性,能够生产出高精度、高强度的陶瓷制品。
本文将介绍陶瓷注塑成型的原理、工艺流程以及应用领域。
一、原理:陶瓷注塑成型是将陶瓷粉末与有机物质(如聚乙烯醇)混合,形成可塑性较好的糊状物料。
然后,将糊状物料注入注塑机的料斗中,通过高温高压的作用,使其在模具中形成所需的形状。
最后,通过烧结过程,将有机物质燃尽,使陶瓷粉末结合成致密的陶瓷制品。
二、工艺流程:1. 原料准备:选择适合的陶瓷粉末和有机物质,并按照一定比例混合均匀。
2. 糊化:将混合后的原料与适量的水混合,形成糊状物料。
3. 注塑成型:将糊状物料注入注塑机的料斗中,通过高温高压的作用,使其在模具中形成所需的形状。
4. 烧结:将注塑成型后的陶瓷制品放入烧结炉中,进行高温烧结,使陶瓷粉末结合成致密的陶瓷制品。
5. 表面处理:根据需要,对陶瓷制品进行抛光、喷涂等表面处理工艺。
三、应用领域:陶瓷注塑成型工艺广泛应用于以下领域:1. 电子器件:陶瓷注塑成型可以制造出高精度、高绝缘性能的电子器件,如陶瓷基板、陶瓷封装等。
2. 汽车工业:陶瓷注塑成型可以制造出高强度、高耐磨性的汽车零部件,如陶瓷刹车片、陶瓷活塞环等。
3. 医疗器械:陶瓷注塑成型可以制造出生物相容性好、耐腐蚀性能强的医疗器械,如人工关节、牙科种植体等。
4. 能源领域:陶瓷注塑成型可以制造出高温、耐腐蚀的能源设备,如陶瓷燃烧器、陶瓷热交换器等。
结论:陶瓷注塑成型工艺是一种重要的陶瓷制造方法,它能够满足复杂形状、高精度、高强度的陶瓷制品需求。
随着技术的不断进步,陶瓷注塑成型工艺在各个领域的应用将会越来越广泛。
相信在不久的将来,陶瓷注塑成型将为我们带来更多的惊喜和突破。
陶瓷注射成型技术

烧结后的尺寸收缩远远大于模压制品,尺寸难以控制,烧结坯体中也容易产生内应力,影 响烧结体性能.为了防止因大量收缩引起的变形和精度下降,试验中在不影响成型性的条 件下,要求尽可能高的粉末含量.随着石蜡含量的减少,烧结后试样的体积密度和抗弯强 度都降低.这主要是由于降低石蜡含量将使喂料黏度增加,流动性变差,在相同的混料工 艺和时间内混料相对困难,黏结剂不能很好地均匀包裹粉末颗粒,脱脂后生坯密度不均匀, 更易形成内部缺陷,而这在后续的烧结中是无法弥补的.
双辊式混炼机的主要结构是以不同速度相对回转的2个辊筒.浆料在辊 隙中由于机械力和相对速度的作用受到强烈的碾压、剪切和撕裂作用,经过多 次反复碾压剪切作用使浆料的各组分分散均匀,达到混合的目的.在混合初期, 浆料在碾压和剪切力作用下,高分子链发生断裂生成部分相对分子质量较小的 有机物并且发生形变,形成片状或带状物结构.
不同的混料工艺对氧化铝注射成型制品的脱脂质量 也有较大的影响.
图7 采用2种混料工艺的试样在脱脂后的直观图
图7为脱脂后试样的直观图,可以看出,搅拌式 混料工艺有利于脱脂的进行,脱脂后试样无裂纹、变 形、孔洞、塌陷等缺陷,而采用双辊式混料工艺的试 样在脱脂后表面出现了严重的裂纹和中心凹陷,内部 有较大孔洞.
过程中会有少量碳生成,导致浆料颜色变深,而游离碳在后续脱脂工艺中很难 完全脱除,从而严重影响试样性能.当温度控制在低于170℃时,聚丙烯不能很 好地熔化,使得浆料黏度增加,与辊筒之间的摩擦阻力增大,不利于混料的进
行.摩擦热不是一个定值,而是随着浆料体积、室内温度、通风条件等的改变 而变化,因此双辊式混料的温度不易控制.
主
题
2012.4.2
陶瓷注射成形技术及其研究进展

(综述)2018年09月陶瓷Ceramics陶瓷汪削成形技术及貝研究进展胡鹏程(中国科学院上海光学精密机械研究所上海2(18000)摘要陶瓷注射成形(C IM )是一种近净尺寸成形工艺,适用于体积小、形状复杂、成形精度高的陶瓷结构件。
笔者介绍 了 C I M 的基本工艺过程,包括陶瓷粉体和粘结剂的选择、喂料制备、注射工艺和脱脂工艺。
重点阐述了粘结剂的性能及 分类、脱脂工艺研究进展以及微注射成形和低压注射成形新技术。
最后对陶瓷注射成形的发展趋势进行了展望。
关键词陶瓷注射成形粘结剂脱脂工艺微注射成形中图分类号:T Q 17462文献标识码:A文章编号:1002 — 2872(2018)09 — 0009 — 05Injection Molding Technology and Research Progress of CeramicsHu Pcngchcng(Shanghai Institute of Optics and Fine Mechanics,the Chinese Academy of Sciences,Shanghai,2018000) Abstract :Ceramic injection miolding (CIM) is a technology of net size miolding. It is especially s uitable w ithsm all volum e,comiplcx shape and high precision. T'his paper introduces the basic technological process of CIM , including the selection of ccramiic powder and binder, miixing preparation,injection process and degreas ties and classification of the binder,the research progress of degreasing technology,and the new technology of miicro injection miolding and low pressure injection miolding are miainly elaborated. Finally,the development trend of ceramic injection miolding is prospected.Key words :C I M; Binder; Debinding process; Microinjcction miolding前言陶瓷注射成形(C IM )是一种新型的陶瓷成形技 术,其基本工艺过程可分为4个阶段:喂料制备、注射 成形、脱脂和烧结[1]。
一种氧化锆陶瓷的注射成型制备方法

一种氧化锆陶瓷的注射成型制备方法注射成型是一种常用的陶瓷制备方法,可以制备出复杂形状和高精度的陶瓷产品。
下面是一种氧化锆陶瓷的注射成型制备方法,包括以下50条步骤,并附有详细描述:1. 准备原料:氧化锆陶瓷的主要成分是氧化锆粉末,需要准备高纯度的氧化锆粉末材料。
2. 通过研磨和筛分处理氧化锆粉末,以确保粒径均一。
3. 往氧化锆粉末中添加适量的有机增塑剂,以增加其可塑性和流动性。
4. 在加入增塑剂的氧化锆粉末中加入一定量的有机溶剂,使用超声或机械搅拌的方法将其混合均匀,形成可注射的糊状物料。
5. 放置混合后的糊状物料静置,以使其中的泡沫自行消除,提高糊状物料的流动性。
6. 将糊状物料装入注射机的料筒中。
7. 在注射机的注射头中装配适当的模具,以便注射成型时可以形成所需形状的陶瓷产品。
8. 将注射机的料筒与模具连接,确保糊状物料能够流入模具中。
9. 启动注射机,并调整注射速度和注射压力,以确保糊状物料能够均匀地填充整个模具。
10. 注射完成后,等待糊状物料在模具中发生固化反应。
11. 取出固化后的陶瓷产品,可选择进行表面处理和调整尺寸。
12. 将固化后的陶瓷产品进行烘烤,以去除其中的有机成分。
13. 烘烤完成后,将陶瓷产品进行烧结处理,以提高其密度和力学性能。
14. 根据需要,可以进行陶瓷产品的磨削、抛光和涂层处理,以提高其表面光滑度和耐磨性。
15. 进一步测试和检验陶瓷产品的物理和化学性能,以确保其符合设计要求。
16. 针对不合格的陶瓷产品,可以选择进行返工或重新制备。
17. 对合格的陶瓷产品进行包装和储存,以便运输和使用。
18. 根据需要,可以进行陶瓷产品的装配和组装,以形成成品。
19. 在注射成型过程中,可以添加一定量的增塑剂,以提高糊状物料的可塑性和流动性。
20. 同样,也可以加入适量的抗结团剂,以防止糊状物料在注射成型过程中过度固化和凝胶化。
21. 注射成型的糊状物料常常需要在一定的温度范围内进行处理,以保持其流动性和可塑性。
陶瓷注射成型
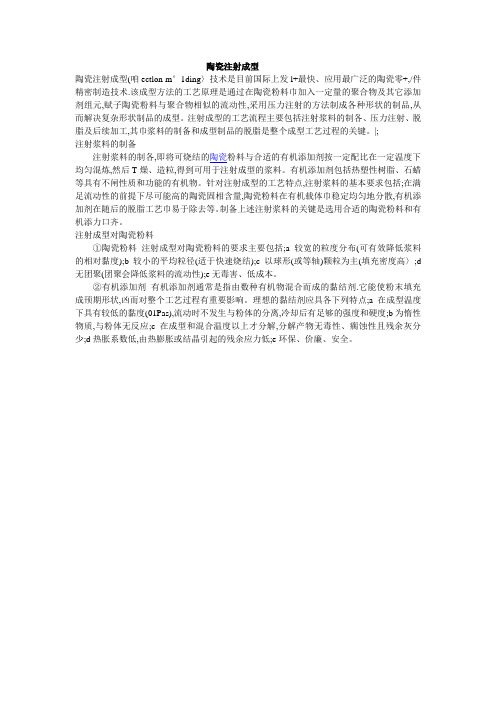
陶瓷注射成型陶瓷注射成型(咱ectlon m°1ding〉技术是目前国际上发l+最快、应用最广泛的陶瓷零+,/件精密制造技术.该成型方法的工艺原理是通过在陶瓷粉料巾加入一定量的聚合物及其它添加剂组元,赋子陶瓷粉料与聚合物相似的流动性,采用压力注射的方法制成各种形状的制品,从而解决复杂形状制品的成型。
注射成型的工艺流程主要包括注射浆料的制各、压力注射、脱脂及后续加工,其巾浆料的制备和成型制品的脱脂是整个成型工艺过程的关键。
|;注射浆料的制备注射浆料的制各,即将可烧结的陶瓷粉料与合适的有机添加剂按一定配比在一定温度下均匀混炼,然后T燥、造粒,得到可用于注射成型的浆料。
有机添加剂包括热塑性树脂、石蜡等具有不闸性质和功能的有机物。
针对注射成型的工艺特点,注射浆料的基本要求包括;在满足流动性的前提下尽可能高的陶瓷固相含量,陶瓷粉料在有机载体巾稳定均匀地分散,有机添加剂在随后的脱脂工艺巾易于除去等。
制备上述注射浆料的关键是选用合适的陶瓷粉料和有机添力口齐。
注射成型对陶瓷粉料①陶瓷粉料注射成型对陶瓷粉料的要求主要包括;a较宽的粒度分布(可有效降低浆料的相对黏度);b较小的平均粒径(适于快速烧结);c以球形(或等轴)颗粒为主(填充密度高〉;d 无团聚(团聚会降低浆料的流动性);e无毒害、低成本。
②有机添加剂有机添加剂通常是指由数种有机物混合而成的黏结剂.它能使粉末填充成顸期形状,凶而对整个工艺过程有重要影响。
理想的黏结剂应具各下列特点;a在成型温度下具有较低的黏度(01Pas),流动时不发生与粉体的分离,冷却后有足够的强度和硬度;b为惰性物质,与粉体无反应;c在成型和混合温度以上才分解,分解产物无毒性、瘸蚀性且残余灰分少;d热胀系数低,由热膨胀或结晶引起的残余应力低;e环保、价廉、安全。
- 1、下载文档前请自行甄别文档内容的完整性,平台不提供额外的编辑、内容补充、找答案等附加服务。
- 2、"仅部分预览"的文档,不可在线预览部分如存在完整性等问题,可反馈申请退款(可完整预览的文档不适用该条件!)。
- 3、如文档侵犯您的权益,请联系客服反馈,我们会尽快为您处理(人工客服工作时间:9:00-18:30)。
陶瓷胶态注射成型技术摘要:结合注射成型和凝胶注模成型技术的优点,发明了陶瓷胶态注射成型技术,实现了水基非塑性浆料的注射成型。
经过研究表明:通过调节工艺中的各项参数和添加适当的助剂,可以实现陶瓷浆料的可控固化;加入应力缓释剂调节高分子网络结构,能有效降低坯体中的内应力,制备出大尺寸陶瓷部件;利用胶态注射成型技术与设备,不仅能实现规模化大批量生产,而且产品具有较高的可靠性,具有广阔的应用前景。
关键词:胶态注射成型;水基非塑性浆料;可控固化;内应力;应力缓释剂Colloidal Injection Molding of CeramicsAbstract:Colloidal injection molding of ceramics(CIMC) is a new ceramic forming technique,which combines the advantages of gel-casting and injection molding, to achieve a non-plastic water-based slurry injection.After the study show that;all kinds of lectors which effect solidification of slurry is studied and then we can control solidification course.Internal stress of green body is also studied and large-size ceramic component can be got by adding moderator.So high performance ceramics with complex shape is manufactured by CIMC technique with high reliability,high automation and low cost.Key words:colloidal injection molding;injection molding;controllable solidification;stress;stress release agent引言随着技术的进步,高性能陶瓷以其优异的耐高温、高强度、耐磨损、耐腐蚀等性能和优点被广泛地应用于工业、国防、机械、石油、汽车、家用电器等各个领域的候选材料。
高性能陶瓷产业化关键在于提高产品性能可靠性和降低其制造成本,而陶瓷材料可靠性及其制造成本与制备工艺密切相关,围绕这两个关键问题,近二三十年来,新的陶瓷粉体制备工艺、成型工艺及烧结工艺的研究逐渐成为陶瓷材料研究领域的新热点。
其中成型工艺作为制备高性能陶瓷材料及部件的关键技术,它不仅是材料设计和材料配方实现的前提,而且是降低陶瓷制造成本,提高材料可靠性尤为重要的环节,已逐渐成为陶瓷材料制备科学研究的主流。
1 高性能陶瓷产业化应用的困局目前高性能陶瓷的应用面临的两大问题是陶瓷的制造成本高和使用性能的可靠性差。
由于陶瓷的制造成本高,从而导致产品的价格高,无法与金属及其复合材料竞争,因此目前只能用于一些特殊领域。
高技术陶瓷由于硬度高质脆,不像金属那样可以加工成各种各样的形状,其中陶瓷机加工的成本几乎占到陶瓷制造成本的1/3— 2/3,主要是因为陶瓷部件的成型很难达到近净尺寸成型。
原因在于传统的陶瓷注射成型技术来源于高分子材料的注塑成型,将大量的高分子粘结剂与陶瓷粉体混练在一起,然通过注射成型机制备各种复杂形状的陶瓷零部件。
因此,采用传统陶瓷制备工艺和装备很难获得显微结构均匀、无缺陷和近净尺寸陶瓷部件。
另外,陶瓷材料的性能分散性大,即陶瓷材料的可靠性差,特别是结构陶瓷又硬又脆既难加工又容易产生突发性的断裂,因而导致高技术陶瓷的制造成本高、性能离散性大、产品生产再现性和使用性能可靠性差等。
使许多领域不敢涉足陶瓷产品。
如果上述两个问题不解决,高性能陶瓷的市场就很难打开局面。
2 陶瓷注射成型技术的发展陶瓷注射成型技术来源于高分子材料的注塑成型,借助高分子聚合物在高温下熔融、低温下凝固的特性来进行成型的,成型之后再把高聚物脱除。
比传统的陶瓷加工工艺要简单的多,能制造出各种复杂形状的高精度陶瓷零部件,且易于规模化和自动化生产。
起初的陶瓷成型注射技术是将大量的高分子树脂与陶瓷粉体混在一起后得到混合料,然后装入注射机于一定温度注入模具,迅速冷凝后脱模而制成坯体[1~3]。
该技术适合制备湿坯强度大,尺寸精度高,机械加工量少,坯体均一的产品,适于大规模生产。
对形状复杂、厚度较薄产品的制备有着明显的优越性。
但是由于含有大量的高分子粘结剂,使陶瓷坯体的脱脂成为不可逾越难题,并且有毛坯易变形,容易形成气孔等缺点。
陶瓷注射成型使用的有机载体包括粘接剂、增塑剂、润滑剂等。
有机载体的选择重点考虑:体系内的相容性;注射悬浮体的流变特性;脱模特性与生坯强度。
通常有机载体与陶瓷粉体混合后的结合强度主要取决于热塑性树脂高聚物;脱脂特性亦可由耐热性好的高聚物调节;可塑剂和润滑剂可改善体系流动性及脱模性能;表面活性剂具有综合调节作用。
在熔体注射充模冷凝形成坯体的过程中,坯体内产生的应力有两种,即温度应力和成型应力。
对异型、大尺寸坯体的注射参数和充模过程的研究表明,过高的注射压力和注射温度使坯体内产生较大的成型应力和温度应力,增大了坯体变形和开裂的危险性。
由于注射成型加入大量有机载体,烧结前必须将其排除,即进行脱脂。
脱脂耗时较长,容易使坯体产生缺陷。
因此,脱脂是注射成型工艺的关键。
影响脱脂过程的因素主要有:气氛、压力和温度制度。
惰性气氛可避免有机物的氧化分解。
一定的气氛压力,可缩小有机物挥发及分解产生的有效体积,从而减少由于体积膨胀引起的坯体开裂。
另外,脱脂速率也直接受温度影响。
在坯体软化,内部尚未形成气孔通道的温度段l50~300℃,升温速率必须严格控制。
否则,坯体易发生变形、产生鼓泡及开裂等缺陷[4]。
为了避开陶瓷注射成型技术使用大量高分子粘结剂的缺点,九十年代后陶瓷成型技术的研究逐渐转向含有少量有机物的水基胶态成型技术的研究,新的成型技术不断涌现,如美国橡树里国家实验室发明的凝胶注模成型工艺、瑞士联邦理工大学发明的直接凝固注模成型技术等等。
总之,2l世纪在非塑性水基浆料的胶态成型方面取得了很大进展。
3 陶瓷胶态注射成型技术新工艺陶瓷胶态注射成型新工艺是把胶态成型和注射成型结合起来的“陶瓷胶态注射成型新工艺”,即水基非塑性浆料的注射成型。
它是将低粘度、高固相体积分数的水基陶瓷浓悬浮体注射到非孔模具中,并使之原位快速固化,再经烧结,制得显微结构均匀、无缺陷和近净尺寸的高性能、高可靠性的陶瓷部件。
该系由美国Allied Signal公司的研究人员发明,然后又经过一些研究中心的改进,得到了发展和推广[5]。
琼脂和琼脂糖常被用作水溶性有机载体,它能通过温度的变化而固定成型。
琼脂糖由2种不同的糖分子交替组成,聚合物骨架上的羟基和水分子之间能形成氢键。
水溶性浆料包括下列组分:陶瓷粉体、水、琼脂或琼脂糖、分散剂、润滑剂。
最重要的步骤是注射成型前陶瓷悬浮体的分散,这一步通常是由加入分散剂进行球磨而实现。
琼脂的用量被限制在质量分数1%~2%。
再多的用量会增加陶瓷悬浮体的粘度。
陶瓷悬浮体的固相体积分数不超过50%。
注射后,有机体在模具中转变为胶态,提供给产品一定的强度。
水在一般的炉子中会很容易地除去,也可用微波进行干燥。
干燥后的坯体不用进行脱脂而能直接进行烧结。
AIM技术可以很容易的实现自动控制,比起传统的注射成型来降低了成本。
陶瓷的胶态注射成型新工艺实现了水基瘠性料浆的注射成型。
此前,胶态成型制备高性能陶瓷复杂部件主要经历了以下几个发展阶段:注浆成型、注射成型、胶态原位凝固成型。
注浆成型利用瘠性料浆在石膏模中失水固化的机理来制备复杂陶瓷部件,这就使得操作时间比较长,而且坯体密度低、强度差,不适合制备高性能的陶瓷材料。
注射成型可成型尺寸精度高、形状复杂的陶瓷部件,且易于自动化和规模化生产。
但是该工艺需要添加大量有机物,使得排胶始终是制约其应用的一个关键环节,至今尚未完全突破。
旨在提高陶瓷坯体均匀性和解决陶瓷材料可靠性,胶态原位凝固成型工艺应运而生,如凝胶注模成型和直接凝固成型。
这些新工艺虽然避免了注射成型有机物含量高的缺点,但是仍然属于手工操作的范畴,自动化程度低,还不能满足高性能陶瓷大规模生产的要求。
陶瓷的注射成型与胶态成型的主要差别在于前者属于塑性成型的范畴,后者属于浆料成型,即浆料没有可塑性,是瘠性料。
胶态成型由于浆料没有塑性,无法采用传统的陶瓷注射成型的思路。
如果胶态成型同注射成型相结合,即利用专有的注射设备与胶态原位成型工艺所提供的新型固化技术,实现陶瓷材料的胶态注射成型。
这一新工艺,既区别于一般的胶态成型,又区别于传统的注射成型,将既具有胶态原位凝固成型坯体均匀性好,有机物含量低的特色,又具有注射成型自动化程度高的优点,是胶态成型工艺的一种质的升华,将成为高技术陶瓷走向产业化最有潜在前景的途径之一,如图1[6]图 14 陶瓷浆料的可控固化陶瓷胶态注射成型必须解决以下两个重要的关键技术:陶瓷浓悬浮体的快速原位固化和注射过程的可控性。
通俗而言即浆料在注射之前不能固化,流动性和稳定性良好,注射充模之后要实现快速原位固化,其关键之处是陶瓷浆料的可控固化,能够找到一个很容易控制因素,如浆料的成分、压力、温度等。
这就要求我们仔细研究影响浆料固化的各种因素,以达到可控固化的目的。
4.1 影响固化过程的内部因素陶瓷浆料是一个复杂的多相体系,包括陶瓷粉体、分散剂、有机单体、交联剂、无机离子等成分,它们对聚合过程都有一定的影响。
可以通过调节陶瓷浆料中这些化学物质,对固化过程进行调控,故而称它们为影响固化的内部因素。
通常陶瓷粉体都含有不同程度的可溶性杂质离子。
其中还原性离子,如Fe2+,SO2-;与引发剂发生氧化还原反应,会显著加速引发剂的分解,缩短聚合诱导期。
而Fe3+,Cu2+等高价离子,则会对聚合反应起到阻聚作用,延长诱导期。
4.2 影响固化过程的外部因素在胶态注射工艺中,为了实现陶瓷浆料的可控固化,必须调整各项工艺参数和助剂。
引发剂、催化剂的加入量,固化温度和压力,盛装浆料的容器材料和加入的阻聚剂都会影响浆料的固化过程。
同时通过它们可以实现浆料的可控固化,因此将它们称为影响固化的外部因素。
引发剂和催化剂的加入量是控制浆料固化过程的主要因素之一。
随着加入的引发剂浓度的升高,引发速率加快,聚合诱导期随之缩短,二者大致呈线性关系。
当引发剂加入量过少(小于0.25 mmol/L时),由于溶于浆料中的氧阻聚,聚合反应不完全,坯体质量很差。