普通圆柱蜗杆传动的多目标模糊优化设计
双锥面二次包络环面蜗杆传动多目标优化设计

双锥面二次包络环面蜗杆传动多目标优化设计邱清盈;舒勤业;冯培恩;朱肖虎;曹磊【摘要】The work introduced in this paper is based on the research of a dual-cone double enveloping hourglass worm gear pair,while taking the dual-line contact transmission performance of the dual-cone double enveloping hourglass worm into account.The optimization goal of this work is to enhance transmission efficiency and carrying capacity.This paper adopted the method of imitation of biological evolution to multi-objectively optimize the design parameter of the dual-cone double enveloping hourglass worm gear pair,thereby establishing a general optimization model which avoided worm undercutting and addendum pointing during the ing independently developed dual-cone double enveloping hourglass worm gear processing equipment and a test platform,an experiment was carried out.The result confirmed that the optimization model has practical performance.%针对环面蜗杆副优化设计不能兼顾传动性能与承载能力这2个性能指标的问题,建立了双锥面二次包络环面蜗杆通用的优化模型.该模型考虑双锥面二次包络环面蜗杆的双线接触传动性能,以传动效率和承载能力为优化目标,以避免在加工时产生根切和齿顶变尖为约束条件,利用仿生物进化法对设计参数进行多目标优化.结合自主研发的加工和检测设备进行了实验,结果显示,优化后的双锥面二次包络环面蜗杆副的接触线分布更广,传动效率更高,从而验证了该优化模型具有实际的效能.【期刊名称】《哈尔滨工程大学学报》【年(卷),期】2012(033)007【总页数】6页(P869-874)【关键词】环面蜗杆;双线接触;传动效率;承载能力;多目标优化设计【作者】邱清盈;舒勤业;冯培恩;朱肖虎;曹磊【作者单位】浙江大学机械工程学系,浙江杭州310027;浙江大学机械工程学系,浙江杭州310027;浙江大学机械工程学系,浙江杭州310027;浙江大学机械工程学系,浙江杭州310027;浙江大学机械工程学系,浙江杭州310027【正文语种】中文【中图分类】TH132.44环面蜗杆副传动相对于普通圆柱蜗杆传动,具有同时啮合齿数多、啮合时呈双线接触、接触点的法向速度大、综合曲率半径大、接触应力小、易形成油膜等优点,因此具有更高的传动效率和承载能力,更长的使用寿命.环面蜗杆副传动在冶金、采矿、军工、化工、造船等领域已得到了广泛的应用.环面蜗杆按产型面的不同可分为直廓环面蜗杆、平面包络环面蜗杆、锥面包络环面蜗杆以及双锥面包络环面蜗杆,根据是否以一次包络所得的滚刀产型面来加工蜗轮又可分为一次和二次包络环面蜗杆传动.国内外学者针对各种类型的蜗杆传动副,在模型建立、啮合性能分析、加工修型、优化设计等各方面开展了长期的研究[1-4].在环面蜗杆副的优化设计方面,学者也做了相关的研究[5-9],建立了各种不同类型,不同优化目标的优化设计模型. 双锥面二次包络环面蜗杆传动不仅具有环面蜗杆副的承载能力大、传动效率高及使用寿命长的优点,而且不易引起蜗杆边齿顶变尖和根切等加工问题.在加工时,由于其左右侧齿面同时进行磨削,在生产效率方面也有很大的优势.但国内外针对双锥面二次包络环面蜗杆副的研究却较少.本文以双锥面二次包络环面蜗杆作为研究对象,结合自主研发的加工和检测设备,对该种环面蜗杆传动进行多目标优化设计,以期获得一种比较通用的设计方法,使双锥面二次包络环面蜗杆副达到更优的性能.1 双锥面二次包络环面蜗杆副模型选择如图1所示的坐标系,建立蜗杆副的数学模型.其中σo1(O1;io1,jo1,ko1)为蜗杆静坐标系,σo2(O2;io2,jo2,ko2)为蜗轮静坐标系,σod(O d;iod,jod,kod)为刀座静坐标系.σo1、σo2、σod均与机架固连.σ1 (O1;i1,j1,k1)、σ2(O2;i2,j2,k2)、σd(Od;id,jd,kd)分别与蜗杆、蜗轮、刀座固连.k1=ko1,k2=ko2,kd= kod.蜗杆转角为φ1,蜗轮转角为φ2,φ2=i21φ1,i21为蜗轮蜗杆的传动比,初始位置φ1=φ2=0°,σ1与σo1重合,σ2与σo2重合.刀座转角为φd,蜗杆毛坯转角为φ,φd=id1φ,id1为刀座与蜗杆毛坯的速比,初始位置φ=φd=0°,σd与σod重合.图1 双锥面二次包络环面蜗杆副的坐标系Fig.1 Coordinate system for dual-cone double enveloping hourglass worm gear pair如图2所示,砂轮的齿形角为αd,齿顶宽为sa.取坐标系σa(Oa;ia,ja,ka)与砂轮固连.产形双锥面Σd在σa里的方程为式中:xa=-ucosαdcos θ+rdcos θ,ya=-ucosαdsin θ+ rdsin θ,za=±(usinαd+0.5sa).式中:za取正,表示砂轮右侧;za取负,表示砂轮左侧.在Σd任一点Q处的切平面上建立活动坐标系σd(Q;αξ,aη,n).对式(1)进行σa→σd坐标变换,可得到产形双锥面Σd在σd里的方程:式中:R[id,-(90°-β)]的意义是表示矢量绕id转过-(90°-β)角度的回转矩阵. 式(2)通过σd→σod→σo1→σ1的转换,最终可将产形面上的啮合点在刀座动坐标系中的位置表达,转换到蜗杆动坐标系:一次包络共轭条件方程为根据式(4),可求出砂轮上的啮合点,将求得的啮合点参数代入式(3),即可得到在σ1里蜗杆上的各个接触点.这些接触点就组成了在σ1里的蜗杆螺旋面Σ1.图2 双锥面砂轮在坐标系中的位置Fig.2 The position of dual-cone grinding wheel at the coordinate system双锥面二次包络蜗轮的加工过程,是以滚刀齿面作为成型面,进行二次包络对蜗轮齿面的成形.因此,建立蜗轮齿面模型即为求解二次包络过程中产出的蜗轮齿面啮合点.通过σ1→σo1→σo2→σ2的转换,可获得啮合点在蜗轮动坐标系中的位置表达:蜗杆副二次包络共轭条件方程为根据式(6),可求出滚刀上的啮合点,将求得的啮合点的参数代入式(5)中,即可得在σ2里蜗轮上的各个接触点.而所有的接触点就构成了在σ2里蜗轮齿面Σ2.2 优化模型的建立2.1 优化参数的选择设计开发一套新的蜗轮蜗杆减速器,首先应提出中心距a和传动比i这2个基本条件.蜗杆的头数z1和蜗轮的齿数z2根据传动比i的要求进行选择.此外,针对双锥面二次包络环面蜗杆传动,还需要确定其他3个重要的参数,分别是蜗杆分度圆直径系数k1、主基圆直径系数k2和产型面倾角β.如表1所示,这3个参数又影响到蜗杆副其他的几何参数,从而影响蜗轮蜗杆减速器的综合性能.常规设计时,k1、k2和β都是根据经验在推荐的一定的范围内选取的,为此,本文选择这3个参数作为所建立的优化模型的优化参数,即:表1 双锥面二次包络环面蜗杆副部分几何参数Table 1 The geometric parameters of the dual-cone double enveloping hourglass worm gear pair根据设计要求确定传动比i 根据设计要求确定蜗杆头数z1 选取蜗轮齿数z2z2=i21z1蜗杆分度圆直径d1/mm d1=k1a (0.33≤k1≤0.50)蜗轮分度圆直径d2/mm d2=2a-d1蜗轮端面模数mt/mm mt=d2/z2蜗杆齿根圆直径df1/mm df1=d1-1.8mt主基圆直径db/mm db=k2a(0.50≤k1≤0.67)蜗杆分度圆压力角α/(°) α=arcsin(db/d2)蜗杆喉部分度圆导程角γm/(°) γm=arctan[d2/(i21d1)]成形面倾角β/(°) β≥γ参数计算公式中心距a/mm m由第1节可知,蜗轮蜗杆副的齿面模型,与参数αd、sa、a0、β、a、rd有关.其中a根据设计要求确定,rd根据加工的条件决定,均可设为一定值;αd、sa与蜗杆副中的主基圆直径db、蜗杆分度圆压力角α等密切相关,受优化参数k2的影响;a0=a-0.5df1-rd,受优化参数k1的影响;而β即为优化参数之一.可见,蜗杆分度圆直径系数k1、主基圆直径系数k2和产型面倾角β这3个参数的选择,对蜗杆副的齿面模型有着直接的影响.2.2 优化目标在现有的平面环面蜗杆优化研究中,一般以提高润滑性能和减小传动副体积为优化目标,但只是以环面蜗杆的一次接触性能为基础进行分析,没有将环面蜗杆双线接触的传动特性进行综合分析,而且也没有考虑二次接触线的分布位置.本文对双锥面二次包络环面蜗杆优化设计的研究,基于优先提高性能的考虑,追求更高的传动效率和更优的承载能力2个方面性能.传动效率主要取决于润滑条件,可以蜗杆副传动时的油膜厚度为参考因素,承载能力则受接触线分布情况影响较大,因此选择油膜厚度最厚、一次和二次接触线分布范围最广作为优化目标.2.2.1 油膜厚度的几何系数根据弹性流体动压润滑理论,蜗杆副接触齿面间油膜厚度,可按道森(Dowson)公式进行计算:式中:κ12N表示蜗杆副沿瞬时接触线法向的诱导法曲率;W表示作用在单位齿宽上的载荷;Ch表示与润滑油的运动粘度、压粘系数及蜗杆蜗轮材料的弹性模量和泊松比有关的系数;vn表示相对卷吸速度.蜗杆副沿αξ和αη方向的诱导法曲率为式中:Nξ和Nη为蜗杆副瞬时接触线上任一点处的法矢量N沿αξ和αη方向的分量,Ψ为蜗杆副二次包络曲率干涉界限函数.根据式(9)、(10),可求出蜗杆副沿瞬时接触线法向的诱导法曲率为计算蜗杆副齿面间油膜厚度时,还需要求相对卷吸速度,即式中:v1和v2分别为蜗杆副啮合点处的蜗杆和蜗轮的线速度在不考虑润滑油和蜗轮蜗杆材料性质,以及具体载荷的情况下,可选择油膜厚度的几何系数作为油膜厚度的评定参数[5]:在蜗杆副不同的啮合角度和蜗杆齿面不同的啮合位置,油膜厚度的几何系数各不相同.为了获得最优的润滑条件,需要使接触面间的最小油膜厚度最大.由于蜗杆副啮入端蜗杆齿根处的油膜厚度最小,因此,以该位置处的油膜厚度几何系数建立优化目标模型,即2.2.2 接触线分布双锥面二次包络环面蜗杆具有双线接触的特性,包括一次接触线和二次接触线,其中一次接触线是产型面上接触线在蜗轮齿面上的再现,二次接触线是滚刀加工蜗轮的过程中产生的新接触线,传动过程中2类接触线同时作用.从工作起始角处开始,一次和二次接触线由蜗轮两侧面逐渐向蜗轮中心对称面附近移动.双锥面二次包络环面蜗杆副的一次和二次接触线在蜗轮齿面上的分布,不能过宽,也不能过窄.分布过宽时,工作起始角处的接触线在蜗轮齿面的外侧,这表示从工作起始角处开始的一定角度内,蜗轮外侧齿面未参与啮合,这将减少参与啮合的蜗轮齿数,从而降低了蜗杆副的承载能力.反之,当接触线在蜗轮齿面分布过窄时,接触线会集中于蜗轮齿面的中心对称面处,从而降低齿面强度,缩短了蜗杆副的使用寿命.为了获得较好的分布区域,即接触线分布范围和蜗轮齿面的重合度更高,需要使工作起始角处的接触线,即最外侧的接触线,与蜗轮侧面的距离越小越好.为了具有代表性,选择该接触线位于蜗轮分度圆处的接触点为参考点建立目标模型,即式中:zj表示接触线的位置方程,j=1表示一次接触线,j=2表示二次接触线,其计算见式(5);B表示蜗轮齿宽.2.3 约束条件如2.1节所述,与蜗杆分度圆直径系数k1、主基圆直径系数k2和产型面倾角β相关的约束主要考虑避免环面蜗杆根切和蜗杆齿顶变尖.2.3.1 避免环面蜗杆根切为了在加工环面蜗杆的过程中避免发生根切,需要保证一次包络的曲率干涉界线Ψd在蜗杆齿根环面之内.为建模方便,只需要保证根切曲线与蜗杆齿根环面之间的最小径向距离处不发生根切即可.经计算分析,可得一次包络曲率干涉界限在蜗轮齿面内的变化,如图3所示.图3 一次包络曲率干涉界线Fig.3 Once-enveloping curvature interference limit line曲率干涉界限径向距离变化趋势,如图4所示.可见,在工作起始角处,对应根切曲线的最右侧位置,其径向距离最小.所以选择约束条件:式中:L表示根切曲线与蜗杆齿根环面之间的最小径向距离.图4 L随φd的变化趋势F ig.4 The curve of L and φd2.3.2 避免蜗杆齿顶变尖环面蜗杆与普通圆柱蜗杆相比,成型面在蜗杆齿面上的啮合点随着刀座转角的变动而变动,所以蜗杆的齿顶宽度随着刀座转角变化.利用蜗杆左右两侧的齿面方程对蜗杆齿顶宽进行计算[10],可知蜗杆边齿顶宽最小.为了避免蜗杆齿顶变尖,则需要保证:式中:ks表示边齿顶宽度系数;sb表示边齿顶宽;mt表示蜗轮端面模数.2.4 模型的建立与求解通过以上优化模型建立各要素的讨论,可确定双锥面二次包络环面蜗杆副多目标优化模型:利用浙江大学机械设计研究所开发的柔性优化软件FlxOpt,建立上述优化模型.设定油膜厚度的几何系数和接触线分布的权重各为0.5,而在油膜厚度几何系数和接触线分布中,又分别设定一次接触线二次接触线的权重为0.5,如图5所示.图5 柔性优化软件FlxOpt界面Fig.5 Interface of the flexible optimization designing software FlxOpt3 双锥面二次包络环面蜗杆副优化设计实例设计的双锥面二次包络环面蜗杆传动的中心距为a=75 mm,传动比i=40,采用单头蜗杆,蜗轮齿数为40.加工时,取砂轮半径rd=100 mm.取原始优化参数X=[0.35,0.63,10°],经优化之后所得参数为X=[0.37,0.62,10.5°].模型目标经优化后结果如表2所示.表2 优化结果对照表Table 2 Comparison of optimization results目标及约束参数优化前优化后油膜厚度几何系数 kh 12.26 13.80接触线分布0.55 0.42 0.01 1.87根切 L 4.02 5.76齿顶 sb/mt ||z1|-B/2| ||z2|-B/2| 1.99 3.94根据双锥面二次包络环面蜗杆副的数学模型,选取u=0的位置,即蜗轮齿根处,对其油膜厚度几何系数kh进行计算分析,结果如图6.对双锥面二次包络环面蜗杆副的接触线进行计算分析,结果如图7、8.图7中,线1及1'为工作起始角处(φ2=-17.7°)的一次接触线和二次接触线,线2~9和线2'~8'对应的φ2从-14°以4°的增量递增,最后线10为工作结束角处(φ2=17.7°)的一次接触线.图8中表示了蜗杆副的双线接触性能.经计算可知,优化前当φ2=-15.1°时,蜗轮齿面上开始出现二次接触线,蜗杆副开始具有双线接触的性能,而当φ2=13.2°时,齿面上的二次接触线消失;而优化后,当φ2=-16.8°时,蜗轮齿面上开始出现二次接触线,当φ2=14.6°时,齿面上的二次接触线消失.由表2及图6~8可见,经过优化后,双锥面二次包络环面蜗杆副在约束的范围内,油膜厚度几何系数有所提高,其接触线分布范围与蜗轮齿面的重合度也有所提高,并且还具有了更长的双线接触区域.为了从实验中对优化模型的效用进行分析,本文设计并搭建了用于实际数据测试的试验平台和数据处理系统.其中试验平台设计方案如图9所示.利用自主研制的双锥面二次包络环面蜗杆副加工设备,根据优化前后的设计参数,加工了2套用于对比实验的环面蜗杆减速器.对这2套环面蜗杆减速器,采用相同的装配和安装方式,并且使用同种润滑油.最后,利用搭建的蜗杆减速器试验平台对转速、转矩和传动效率进行了测试.经过测试可以得到,双锥面二次包络环面蜗杆副减速器在优化前最高传动效率为57.39%,而优化后的最高传动效率能够达到62.56%.通过上述实验数据可知,利用上述多目标优化模型,对双锥面二次包络环面蜗杆副进行优化后,其传动性能有了一定的提高,从而证明该优化模型具有实际的效能.图6 优化前后的油膜厚度几何系数Fig.6 The geometrical coefficient of the oil film thickness before and after optimization图7 优化前、后接触线在齿面上的分布情况Fig.7 The distribution of the contact lines before and after optimization图8 优化前、后蜗杆副双线接触性能分析Fig.8 Analysis of dual-line contact performance before and after optimization图9 试验平台设计方案Fig.9 Design of the test platform4 结论1)与普通圆柱蜗杆副相比,润滑性能和双线接触体现了双锥面二次包络环面蜗杆副优越的传动和承载性能,本文集中这2个方面的内容为优化目标,建立了多目标优化模型.2)在考虑润滑性能这一优化目标时,选取油膜厚度的几何系数作为油膜厚度的评定参数.而在考虑承载能力这一优化目标时,不仅考虑了一次接触线的分布,而且同时考虑了二次接触线的分布情况.3)通过理论分析和实验测试对优化前后的双锥面二次包络环面蜗杆副进行了对比,验证了该模型的有效性,为后续深入研究的开展提供了参考的方向.参考文献:【相关文献】[1]SIMON V.The influence of gear hobbing on worm gear characteristics[J].Journalof Manufacturing Science and Engineering,2007,129(5):919-925.[2]LITVIN F L,PEREZ I G,YUKISHIMA K,et al.Design, simulation of meshing,and contact stresses for an improved worm gear drive[J].Mechanism and Machine Theory,2007,42(8):940-959.[3]HILTCHER Y,GUINGAN M,VAUIANY J P.Numerical simulation and optimisation of worm gear cutting[J].Mechanism and Machine Theory,2006,41(9):1090-1110.[4]SU Daizhong,QIN Datong.Integration of numerical analysis,virtual simulation and finite element analysis for the optimum design of worm gearing[J].Journal of Materials Processing Technology,2003,138(1-3):429-435[5]黄安贻,夏江敬,张仲甫.平面二次包络环面蜗杆传动多目标优化设计[J].机械设计,2003,20(9):40-45.HUANG Anyi,XIA Jiangjing,ZHANG Zhongfu.Design of multi-target optimization for planar quadratic ring enveloped worm gear drive[J].Journal of Machine Design,2003,20 (9):40-45.[6]谭昕,徐林红,周红.基于润滑性能优先的平面二次包络环面蜗杆副参数优化设计[J].机械设计与制造,2005,42(10):21-23.TAN Xin,XU Linhong,ZHOU Hong.Parameter optimization design for planar double enveloping hourglass worm gear drive based on the lubricating property[J].Machinery Design&Manufacture,2005,42(10):21-23.[7]张光辉,张太萍,罗文军.准平面二次包络环面蜗杆传动参数选择及优化[J].机械传动,2007,31(2):4-8.ZHANG Guanghui,ZHANG Taiping,LUO Wenjun.Selecting and optimizing of the parameters on quasi-plane double enveloping hourglass worm drive[J].Journal of Mechanical Transmission,2007,31(2):4-8.[8]王进戈,张均富,邓星桥,等.无侧隙双滚子包络环面蜗杆传动的参数优[J].机械工程学报,2010,46(21):7-12.WANG Jinge,ZHANG Junfu,DENG Xingqiao,et al.Parameter optimization of the non-backlash double-roller enveloping hourglass worm gearing[J].Chinese Journal of Mechanical Engineering,2010,46(21):7-12.[9]邓星桥,王进戈,张均富,等.基于遗传算法的无侧隙双滚子包络环面蜗杆传动的参数优化设计[J].四川大学学报:工程科学版,2010,42(2):250-254.DENG Xingqiao,WANG Jinge,ZHANG Junfu,et al.Optimization design of the non-backlash double-roller enveloping hourglass worm's parameters based on genetic algorithm[J].Journal of Sichuan University:Engineering Science E-dition,2010,42(2):250-254.[10]董学朱.环面蜗杆传动设计和修形[M].北京:机械工业出版社,2004:70-84.DONG Xuezhu.Design and modification of hourglass worm gearing[M].Beijing:China Machine Press,2004:70-84.。
蜗杆传动的模糊优化设计
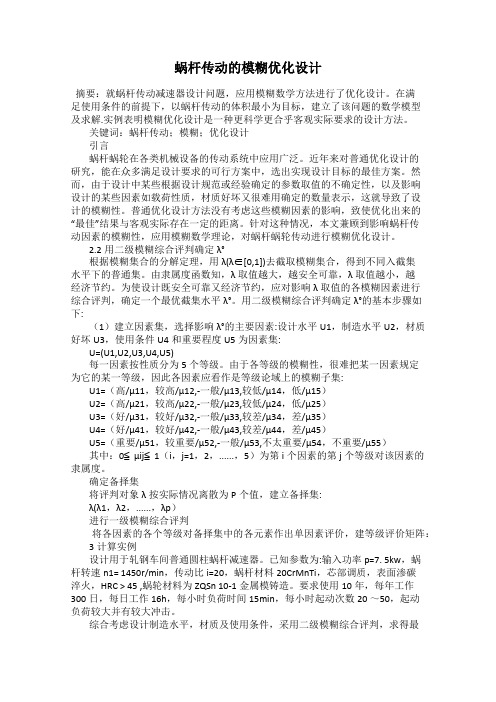
蜗杆传动的模糊优化设计摘要:就蜗杆传动减速器设计问题,应用模糊数学方法进行了优化设计。
在满足使用条件的前提下,以蜗杆传动的体积最小为目标,建立了该问题的数学模型及求解.实例表明模糊优化设计是一种更科学更合乎客观实际要求的设计方法。
关键词:蜗杆传动;模糊;优化设计引言蜗杆蜗轮在各类机械设备的传动系统中应用广泛。
近年来对普通优化设计的研究,能在众多满足设计要求的可行方案中,选出实现设计目标的最佳方案。
然而,由于设计中某些根据设计规范或经验确定的参数取值的不确定性,以及影响设计的某些因素如载荷性质,材质好坏又很难用确定的数量表示,这就导致了设计的模糊性。
普通优化设计方法没有考虑这些模糊因素的影响,致使优化出来的“最佳”结果与客观实际存在一定的距离。
针对这种情况,本文兼顾到影响蜗杆传动因素的模糊性,应用模糊数学理论,对蜗杆蜗轮传动进行模糊优化设计。
2.2用二级模糊综合评判确定λ°根据模糊集合的分解定理,用λ(λ∈[0,1])去截取模糊集合,得到不同入截集水平下的普通集。
由隶属度函数知,λ取值越大,越安全可靠,λ取值越小,越经济节约。
为使设计既安全可靠又经济节约,应对影响λ取值的各模糊因素进行综合评判,确定一个最优截集水平λ°。
用二级模糊综合评判确定λ°的基本步骤如下:(1)建立因素集,选择影响λ°的主要因素:设计水平U1,制造水平U2,材质好坏U3,使用条件U4和重要程度U5为因素集:U=(U1,U2,U3,U4,U5)每一因素按性质分为5个等级。
由于各等级的模糊性,很难把某一因素规定为它的某一等级,因此各因素应看作是等级论域上的模糊子集:U1=(高/μ11,较高/μ12,-一般/μ13,较低/μ14,低/μ15)U2=(高/μ21,较高/μ22,-一般/μ23,较低/μ24,低/μ25)U3=(好/μ31,较好/μ32,-一般/μ33,较差/μ34,差/μ35)U4=(好/μ41,较好/μ42,-一般/μ43,较差/μ44,差/μ45)U5=(重要/μ51,较重要/μ52,-一般/μ53,不太重要/μ54,不重要/μ55)其中:0≦μij≦1(i,j=1,2,......,5)为第i个因素的第j个等级对该因素的隶属度。
多目标优化与层次分析法相结合的滚齿机立柱改进设计

n ∈[ 30 , 300 ] , Z k = 12 , 对于该滚齿机而言, 经计 15 , 150 ] 。 由仿真分 算可得切削时的激振频率 p ∈[ 析结果可知, 一阶固有频率大于切削产生的激振频 , 率 避开了滚刀主轴的共振区。 通过对前四阶振型的分析, 前两阶主要是摆动, 后两阶出现扭动, 说明立柱的壁厚以及内壁筋板的 须对其进行优化设计。 厚度使得立柱的动刚度不足,
2013 年 1 月
徐
君, 等: 多目标优化与层次分析法相结合的滚齿机立柱改进设计
· 33·
柱导轨所承受的梯度载荷。 机床立柱底部用 8 个螺栓与床身固定连接, 故 在底部螺栓孔处要限制所有的自由度, 施加固定约 , , 束 立柱底部要防止发生扭转和滑移 因此在底面施 加位移约束。图 4 、 图 5 分别为立柱在静力分析后得 到的立柱位移和应力等值线图。 由图 4 可知, 沿着 且最大变形发生 立柱高度自上而下变形逐渐减小, 在立柱顶面与导轨相交处, 最大变形接近 0. 029mm ( 小于允许值 0. 03mm ) 。 图 5 表明, 最大主应力为 9. 02Mpa 远小于灰铸铁的抗拉强度, 由此立柱满足 [6 ] 具有很高的安全性 。 强度设计要求,
· 32·
组合机床与自动化加工技术
第1 期
种多目标决策分析方法。 它把复杂的决策系统层次 通过逐层比较多种关联因素的重要性, 为分析、 化, 决策提供定量的依据。 其基本原理是根据问题的性 将其分解为不同的组成因 质和所要达到的总目标, 素, 依照因素间的隶属关系和相互影响, 按不同层次 聚集组合后形成的一个多层次分析结构模型, 利用 确定每一层的 人的经验对决策方案优劣进行排序, 全部因素 相 对 重 要 的 权 重 值, 进 而 提 出 解 决 方 案。 [4 ] 刘世豪 等将层次分析法与模糊综合评判法结合, [5 ] 快速有效地评价了机床的整机性能指标 ; Z. Aya 运用层次分析法与仿真技术相结合, 通过 AHP 缩小 市场上对机床产品影响因子不大的因素比例, 运用 仿真技术得到几组可替代的方案, 通过单元选择投 资成本比例得出最优方案, 进而降低生产成本。 本文在分析滚齿机立柱改进前动静态特性的基础 上, 将多目标优化设计与层次分析法相结合, 充分利用 二者在结构设计上的优点对滚齿机立柱进行改进设计, 将立柱改进设计前后的动静态特性进行比较, 比较结果 验证了本文所采用设计方法的可靠性与合理性。
直齿圆柱齿轮的模糊优化设计

+O1 8 × 3 )x 3 ×( ( ) ( )) 一[ ≤O ( ) . 5 ()/ ( ) 1 × 2 )) d ] 6 4
小 齿 轮
1 2 2齿 根 弯 曲 疲 劳 强 度 约 柬 ..
1 模 糊 优 化 设 计 的 数 学 模 型
1 1目标 函 数 和 设 计 变 量 .
摘 要 : 用模 糊 优 化 理 论 对 直 齿 圆柱 齿 轮 进 行 模 糊 优 化 设 计 , 运 用二 级 模 糊 综 合 评 判 法 对 设 计 中诸 多影 响 因 素 的 模 糊 性 进 行 了定 量描 述 和 处理 , 获 得 了 比常 规 优 化 设 计 更 紧凑 的 结 构 , 明 模 糊 优 化 设 计 是 一 种 更 符 合 客 观 实 际 的 科 学 设 计 方 并 说
。” 。
一u + : 『 ( + ) , ) l I 1 1 7
文 章 编 号 :0 2 8 6 2 0 ) 1 0 4 —0 1 0 —6 8 ( 0 8 0 — 0 7 2
直 齿 圆柱 齿 轮 的 模 糊 优 化 设 计
陈远 伟
( 四川 达 州职 业 技 术 学 院 , 川 达 州 6 5 0 四 3 0 0)
方 法未 考虑 齿轮传 动 中许用应 力 的界 限等各 种 模糊 凶素 , 致使设计 结果 难 以符 合 客 观 实 际 。本 文 以直 齿 圆 柱 齿 轮
传 动 为 例 , 齿 轮 传 动 的模 糊 优 化 设 计 进 行 了 探 索 。 对
已 知 一 由 电 机 驱 动 , 于 矿 山 机 械 的 闭 式 直 齿 圆 柱 齿 用
A b tac :Spurg ard ie r e i ed b s d o u z tm ia in t or T h u zn s a o plx fc or n d sg sr t e rv s a e d sgn a e n f z yop i z to he y. e f z i e sofm ny c m e a t si e i— n n p e r d ie sde c i d a oc s e ua ia i ey wih t e t — t ge f z y c pr he i v l a i e h i g s urg a rv s i s rbe nd pr e s d q ntt tv l t h wo s a u z om e nsve e a u ton m t od, nd a a m u h m o e c m p c t u t r a e n a h e e ha n c nv nton tm ia in d sgn c r o a tsr c u e h s b e c i v d t n i o e i al op i z to e i .T hs s ows t a h u z i h h tt e f z yoptm ia in i z to d sg s am or a tc lan ce ii sgn m e h . e in i e pr c ia d s intfc de i t od Ke r s t u z y wo d : he f z y optm ia i sgn;uz y c m p eh nsv v l a i n; sgn o pu — a i s i z ton de i f z o r e ie e a u to de i fs rge rdrve
机械优化设计题目

机械优化设计题目1、一直园杆,用锻铝制造,其强度极限δB=490Mpa,屈服极限δS=380Mpa,杆的直径d=25mm,承受轴向载荷P=45000N,弯矩M=17.5N.m,扭矩T=46.1N.m。
试用第三强度、第四强度理论计算杆的安全系数的最大值。
2、某一设备中的非变位普通圆柱蜗杆传动,蜗杆由电动机驱动,n1=1440r/min,传动比i=21。
由于结构限制,应使蜗杆传动的中心距a≤200mm。
蜗杆用45号钢淬火(HRC>45),蜗轮采用ZQ19-4砂模铸造,滚刀加工,Z2<80。
折合一班制工作,使用寿命7年,单向传动,工作稳定。
试按传递最大功率的要求确定主要参数。
3、某一设备中的非变位普通圆柱蜗杆传动,蜗杆由电动机驱动,n1=1440r/min,传动比i=21。
由于结构限制,应使蜗杆传动的中心距a≤200mm。
蜗杆用45号钢淬火(HRC>45),蜗轮采用ZQ19-4砂模铸造,滚刀加工,Z2<80。
折合一班制工作,使用寿命7年,单向传动,工作稳定。
试按具有最大啮合效率的要求确定主要参数。
4、设计一压缩圆柱螺旋弹簧,要求其质量最小。
最大工作载荷P max=450(N),最小工作载荷P min=200(N),弹簧工作行程要求不少于10(mm),弹簧材料为65Mn,III类载荷弹簧,弹簧端部结构为YIII型,疲劳强度设计安全系数S F=1.2。
(三维14约束)5、已知直齿圆柱齿轮传动的参数如下:法面压力角αn=20º,法面齿顶高系数h an*=1.0,法面径向间隙系数c n*=0.25,齿数Z1=50,Z2=80,许用齿顶厚系数[S a*]=0.25,重合度许用值[ε]=1.2,节点进入双齿啮合区深度系数δ=0.6,求该齿轮副的最优法面变位系数X n1、X n2的和。
(参考机械原理课本,二维七个不等式一个等式约束)6、一受静载荷圆柱螺旋压缩弹簧,已知工作压力F=700N,弹簧材料选用50C r V A,其密度ρ=7.8g/cm3,切变模量G=8.1Χ10-4Mpa,许用剪应力[τ]=444Mpa,设弹簧中径为D,弹簧丝直径为d,弹簧总圈数为n,有效圈数为n1(n1=n-n2,n2为弹簧支承圈数),要求最大变形量10mm,压并高度不大于50mm,弹簧内径不小于16mm,以重量最轻为目标函数优化设计该弹簧。
基于LINGO的蜗杆传动多目标优化设计

Kew rs y o d:mu ioj t e p mztnds n W r v; IG f ae l- b ci t i i ei ; O d e LN Os t r t e v oi ao g m r i ow
随着现代 工业 和技术 的发展 , 传统 的设计方
法 已越 来 越 不 能 满 足 现代 化 工 业 的需 求 , 优 化 而
Байду номын сангаас
W o m ie l- b et e t z t nD s nB sdo Go S f a e r Dr t O jci i ai ei ae nL v Mu i v Op mi o g ot r w
CAIYu -h a e u
( e ate tfMeh n a nier g H nnU w  ̄t A t adSi c, hn d, 1 0 0C ia D p r n m o c ai l gnei , u a n e i o r n c n e C age 4 5 0 hn ) c E n yf s e
设计 在现代化设计 和生产 中显 得相 当重要 .蜗 杆传动同时啮合 的齿数多 , 传动平稳 , 噪声低 , 且 传动 比大 , 件数少等一 系列优 点 , 蜗轮齿 圈 零 但 为铜合金材料 , 价格高 , 且传动效率低 , 为此 , 本
文 建立 蜗 杆 传 动 的 多 目标 优 化模 型 . 线 性 加 权 用 转 化 为单 目标 优 化 问题 , 使用 LN O软件 编 制 了 IG 通 用 程 序 , 用 时 只修 改 相 应 语 句 即可 , 用 简 使 使 单, 值得 推 广应 用 .
,
蜗轮 齿 数 z =11u为 齿数 比 )齿 宽6 g 2 2 . ( 1 , Z , = +) ,
基于粒子群算法的蜗杆传动多目标优化设计

mn( =∑ ( i ) f )
』= 1
() 8
式 中 : 为 最 小 油 膜 厚 度 , m; c 润 滑 油 的 黏 压 系 h 0为 。 数 , 2 2X1 P ; 为 环 境 黏 度 , 7 5X 1 P / 取 . 0 a 伽 取 . 0 a s 为 接 触 点 处 润 滑 油 的 卷 吸 速 度 , ; m/s P 为 接 触 点 ;
mn ( ) 号 i X = i f
卷 吸 速 度 可 按 下 式 计 算 】 :
1 一
() 2
13 1 强 度 约 束 ..
蜗 轮齿 面接 触 疲劳 强度 条 件约 束 :
M
言( i + 。 ) n s 亩 mls A A z。 eA
( 3 )
g ( )= 1 ・ Kr ( 1 06  ̄
h =2 6 8 (7M 。 E ”( /L) ” ( ) . 5 * ) P o 1
对 于 多 目标 优 化 问 题 , 般 不 能 保 证 所 有 的 目标 一 同 时 达 到 最 优 , 根 据 各 目标 的 重 要 程 度 , 别 乘 以 权 需 分
重 系 数 , 后 相 加 作 为 总 目标 函 数 。 然
14 0r mi 传 动 比 i 0, 荷 平 稳 , 杆 材 料 为 4 5 / n, =2 载 蜗 5 钢 ,表 面 淬 火 ,硬 度 为 4 5~5 HRC, 轮 材 料 为 5 蜗 Z u n0 1砂模 铸 造 。 C S lP ,
1 1 目 标 函 数 的 建 立 .
=
) m 一 g
( 0) 1
式 中 : 、 为 蜗杆 、 轮 的 圆周速 度 ; : 蜗 A为 蜗 杆 导 程 角 ;
基于MATLAB的多级齿轮传动多目标可靠性优化设计研究

基于MATLAB的多级齿轮传动多目标可靠性优化设计研究I. 内容概述随着工业自动化的发展,多级齿轮传动系统在各个领域得到了广泛的应用。
然而由于其复杂的结构和工作条件,齿轮传动系统的可靠性一直是设计者关注的重点。
为了提高齿轮传动系统的可靠性,本文提出了一种基于MATLAB的多级齿轮传动多目标可靠性优化设计方法。
首先本文对多级齿轮传动系统的工作原理进行了详细的阐述,包括齿轮啮合、齿面接触、磨损和疲劳等方面的问题。
在此基础上,分析了齿轮传动系统的可靠性评价指标体系,包括寿命、失效率、维修性等关键性能指标。
其次针对多级齿轮传动系统的可靠性优化设计问题,本文提出了一种基于遗传算法和粒子群优化算法的多目标优化设计方法。
通过对比分析不同优化算法的优缺点,最终确定了基于MATLAB的遗传算法作为本研究的主要优化方法。
本文以某型号齿轮传动系统为例,运用所提方法对其进行了多目标可靠性优化设计。
实验结果表明,所提方法能够有效地提高齿轮传动系统的可靠性指标,为实际工程应用提供了有力的理论支持。
A. 研究背景和意义随着科学技术的不断发展,齿轮传动技术在各个领域的应用越来越广泛。
齿轮传动具有传动效率高、承载能力大、传动精度高等优点,因此在工业生产中得到了广泛的应用。
然而齿轮传动系统的可靠性一直是制约其性能的重要因素,为了提高齿轮传动系统的可靠性,降低故障率,保证设备的正常运行,需要对齿轮传动系统进行多目标可靠性优化设计。
目前基于数值计算的可靠性优化设计方法已经成为齿轮传动系统研究的主要手段。
MATLAB作为一种广泛应用于工程领域的数值计算软件,具有强大的数学运算能力和图形化编程功能,为齿轮传动系统的可靠性优化设计提供了有力的支持。
因此基于MATLAB的多级齿轮传动多目标可靠性优化设计研究具有重要的理论和实际意义。
首先研究基于MATLAB的多级齿轮传动多目标可靠性优化设计方法有助于提高齿轮传动系统的可靠性。
通过合理的参数设置和优化策略选择,可以有效地提高齿轮传动系统的可靠性指标,降低故障率,延长设备使用寿命。
基于模糊理论的机械多目标优化设计

收稿日期:2008-09-09基金项目:陕西省自然科学基金资助项目(6);西安理工大学科学研究基金资助项目()作者简介:魏锋涛(6),男,陕西合阳人,讲师,博士研究生,主要研究方向为结构优化设计。
工程中常常遇到期望一个设计方案的多项设计指标均达到最优的问题。
例如,设计一种机械传动装置,希望它的重量最轻、承载能力最高,同时它的性能又最可靠;设计一种高速凸轮机构,不仅要求体积最小,而且还要求其柔性误差最小,动力学性能最好等。
使多于一个设计指标达到最优的问题,就是多目标优化问题。
在多目标优化问题中,各分目标之间常常是互相矛盾的,一个分目标值的最优往往会导致另一个或几个分目标值的最劣。
要使几个分目标同时达到最优,一般来说是非常困难的,有时甚至是不可能的。
因此,用常规的方法求解多目标优化问题,得到的是问题的若干个有效解。
如何从这些有效解中选择出最有效解作为最优设计方案,是实际2010年工程图学学报2010第2期J OURNAL OF ENG INEERING GRAPHICSNo.2基于模糊理论的机械多目标优化设计魏锋涛,宋俐,李言,石坤,赵建峰(西安理工大学机械与精密仪器工程学院,陕西西安710048)摘要:多目标优化设计各分目标间的矛盾性和不可公度性增加了解决问题的难度,常规求解多目标优化设计方法一般只能求出问题的有效解,而得不到设计的最优结果。
该文以蜗杆传动多目标优化设计为例,采用改进的遗传算法求得若干有效解后,根据模糊理论中的相似优先比法从中确定出最有效解,即最优解,并可排出它们的优劣顺序。
关键词:机械设计;多目标优化设计;模糊理论;相似优先比法中图分类号:TH 122文献标识码:A文章编号:1003-0158(2010)02-0009-04Mechanical Multi-Object Optimization Design Based on Fuzzy TheoryWEI Feng-tao,SONG Li,LI Yan,SHI Kun,ZHAO Jian-feng(School of Mechanical and Instrumental Engineering ,Xi ’an University of Technology ,Xi ’an Shaanxi 710048,China )Abstr act:It is difficult to solve multi-objective optimization for inconsistency and incomparability among each single object.Multi-objective mathematical model of worm transmission is established.Effective solutions are obtained by general optimal arithmetic,such as improved genetic algorithm.The optimal solution is chosen from these available effective solutions and then ranked by the similarity priority ratio method of fuzzy theory .K ey words:machine design;multi-objective optimization design;fuzzy theory;similarity priority ratio method200E 108102-210710197-应用必须解决的问题[1]。
ZC蜗杆传动的多目标可靠性优化设计

作者简介 g 莫才颂 ( 7 )男 , 1 3 , 广东茂名人 , 9 一 硕士 , 讲师 , 从事 机电工 程的教 学与研究工作 。
维普资讯
3 2
茂 名 学院 学报
2c 年 0r 7
2 可靠性优化设计的数 学建模
为使 z C蜗杆传动优化设计能取得技术经济效益显著的最优结构设计方案 , 根据 z C蜗杆传动的工作 特点和结构要求 , 可将 z 蜗杆传动在满足承载能力和疲劳强度条件下 , C 其蜗杆齿冠体积最小 , 动效率 传 最高, 中心距最小作为优化 目 函数 , 标 分别记为 A( )A( , 。 , ) ( )
2 1 目标 函数 .
1蜗轮齿冠体积最小分 目 函数 ( ) ) 标 戈 。为节省较贵重的有色金属材料 , 降低生产成本 , 以蜗轮有色 合金齿冠体积最小建立 目标 函数[ 。将有关参数代入整理后得 2 】
mI = = mq2 ++ ) (-6)=(,, i ) - (+) -2 一.2 fm - I (  ̄ [ 一 4] g
莫才颂 林伟 明 , 学明 , 千
(. 1茂名 学院 机 电工程学 院, 东 茂名 55 0 ; 广 20 0 2 九江学 院 机械 工程 学院, . 江西 九江 320 ; . 300 3 西安 工业大学 机 电工程学 院, 陕西 西安 70 3 ) 102
摘要: 将可靠性设计理论与 多 目标优化设 计方法应用于 z C蜗杆传 动设 计 , 考虑约 束条件 的离散性 , 立了 z 建 C蜗杆传 动多 目标 可靠性 优化 设计的数学模型 , 通过用 优化方法求解 , 得到 了比常规设计更 为合理 的结构设 计方案 。给出了具体设 计实 例 , 果表明 , 结 该设计 方法是一种更具有工程实用价值 的综合设计方法 。 关键 词 :C蜗杆传动 ; 目标 ; Z 多 可靠性 ; 优化设计
基于Matlab的圆柱蜗杆传动多目标模糊优化设计

基于Matlab的圆柱蜗杆传动多目标模糊优化设计
吴广益
【期刊名称】《机械制造与自动化》
【年(卷),期】2016(000)006
【摘要】为了解决普通圆柱蜗杆传动成本高、效率低的缺点,利用模糊优化理论建立蜗轮轮缘部分体积最小和传动效率的倒数最小两个目标函数,构建了约束条件和隶属函数,并进行非模糊化处理,最终通过Matlab编程和优化工具箱完成具体优化,达到了体积明显减小和效率提高的目的,可供应用参考。
【总页数】4页(P149-151,219)
【作者】吴广益
【作者单位】德州职业技术学院山东德州253034
【正文语种】中文
【中图分类】TP391.9
【相关文献】
1.普通圆柱蜗杆传动的多目标模糊优化设计 [J], 陈健
2.普通圆柱圆蜗杆传动的多目标模糊优化设计 [J], 黄乾贵;周广林
3.基于混合退火遗传算法的圆柱蜗杆传动模糊优化设计 [J], 马景槐;王江涛
4.基于Matlab的圆柱齿轮模糊优化设计 [J], 张晓红
5.基于模糊概率约束的ZK蜗杆传动参数的多目标模糊优化设计 [J], 林国湘;罗金良;刘迪荣
因版权原因,仅展示原文概要,查看原文内容请购买。
钳工试题单项选择题(800题,包含答案)

二、单项选择题1. 在表面粗糙度的评定参数中,微观不平度+点高度符号是(D)。
A、RgB、RaC、RxD、Rz2. 国标规定螺纹的牙底用(B)。
A、粗实线B、细实线C、虚线D、点划线3. 对于加工精度要求(C)的沟槽尺寸,要用内径千分尺来测量。
A、一般B、较低C、较高D、最高4. 属位置公差项目的符号是(D)。
A、-B、○C、=D、⊥5. Ra在代号中仅用数值表示,单位为(A)。
A、μmB、CmmC、dmmD、mm6. 液压系统中的执行部分是指(B)。
A、液压泵B、液压缸C、各种控制阀D、输油管、油箱等7. 国产液压油的使用寿命一般都在(D)。
A、三年B、二年C、一年D、一年以上8. (B)是靠刀具和工件之间作相对运动来完成的。
A、焊接B、金属切削加工C、锻造D、切割9. 钻床夹具有:固定式、移动式、盖板式、翻转式和(A)。
A、回转式B、流动式C、摇臂式D、立式10. 扁錾正握,其头部伸出约(C)mm。
A、5B、10C、20D、3011. 锉削速度一般为每分钟(B)左右。
A、20~30次B、30~60次C、40~70次D、50~80次12. 锯条在制造时,使锯齿按一定的规律左右错开,排列成一定形状,称为(B)。
A、锯齿的切削角度B、锯路C、锯齿的粗细D、锯割13. 标准群钻的形状特点是三尖七刃(A)。
A、两槽B、三槽C、四槽D、五槽14. 为减少振动,用麻花钻改制的锥形锪钻一般磨成双重后角为(B)。
A、&ο=0°~5°B、&ο=6°~10°C、&ο=10°~15°D、&ο=15°~20°15. 在套丝过程中,材料受(B)作用而变形。
使牙顶变高。
A、弯曲B、挤压C、剪切D、扭转16. 刮削后的工件表面,形成了比较均匀的微浅凹坑,创造了良好的存油条件,改善了相对运动件之间的(A)情况。
A、润滑B、运动C、磨擦D、机械17. 精刮时,刮刀的顶端角度应磨成(C)。
基于遗传算法的圆柱齿轮传动模糊优化

基于遗传算法的圆柱齿轮传动模糊优化刘舜尧1,万正喜1,肖业恒2(1中南大学机电工程学院,长沙410083;2长沙重型机器制造有限责任公司,长沙410014)摘要:根据模糊数学的基本原理,建立斗轮堆取料机行走机构圆柱齿轮传动模糊优化设计的数学模型。
给出了模糊优化设计的方法及遗传算法,并结合M ATLAB的遗传算法工具箱进行寻优计算,通过求解圆柱齿轮优化设计表明使用该方法可提高效率且实用性强。
关键词:圆柱齿轮;齿轮传动;模糊数学;遗传算法;优化设计;MAT LAB软件中图分类号:TH137文献标识码:A文章编号:1671)3133(2010)12)0040)05Fuzzy optim izati on desi gn of cyli nder gear based on genetic al gorith mLIU Shun-yao1,WAN Zheng-x i1,XI A O Ye-heng2(1Schoo l ofM echan ica l and E lectr i c al Eng i n eer i n g,Central South Un i v ersity,Changsha410083,Ch i n a;2Changsha H eavy M ach i n ery M anu facturing Co.Ltd.,Changsha410014,Ch i n a)Abstrac t:Based on t he pr i nc i ple o f the fuzzing m athe m atics,establishes a fuzzy opti m iza ti onm a t he m aticalm ode l o f trav elli ng cy-l i nder gear.Spec ifica ll y descr i bes the design m ethod of f uzzy opti m ization and gene tic a l gor ith m,co m b i ned w ith MATLAB geneti c a lgo rith m t oo l box f o r opti m izati on ca l culati on,by so l v ing t he opti m al desi gn of cy li ndrical gear show that the m ethod can i m prove the e fficiency and practicab ilit y.K ey word s:cy linder g ea r;gear dr i ve;fuzzi ng ma t hema ti cs;genetic a l gor it hm;opti m u m desi gn;M ATLA B0引言机械设计领域中存在着许多不确定的因素,诸如设计参数、许用应力的取值界限、设计、制造水平、材质和零/部件的重要程度等都具有一定的模糊性。
蜗杆传动模糊优化设计

行 了非模糊化处理 , 最后借助复合形法对主要参数进行优化 , 达到 了提高设计质量、 降低成本、 延长
使用寿命的 目的。 关键词 : 模糊优化设计 ; 最优水平截集法 ; 复合形法; 蜗杆传动机构 中图分类号 :H 3 .4 T 12 4 文献标识码 : B 文章编号 : 0 — 84 20 )6— 0 3— 3 1 1 0 7 (0 6 0 0 1 0 0
( )目标函数 2
传动 比;
1 )啮合面相对滑动速度
O 一 法 向压力 角 , = 0 。 t 2。
4 结语
是否有火花产生以及起动的可靠性 。
参考 文献 :
( )本试验装置是通过盘式恒扭矩加载装置中 1
[ ] 陈伯时主编. 1 电力拖动 自动控制 系统 [ . 京 y Op i z t n De in o o m a s s in uz t mia i sg fW r Tr n miso o
C NG Zh o HE a ,WA —h n NG De s e g,WA u NG Y
(c ol f c ai l Pw rE g er g ea oy cncU i r t, iou 5 0 0 hn ) Sh o o hnc & o e n i ei ,H nnP lt h i nv sy Jazo 4 0 ,C ia Me a n n e ei 4
维普资讯
20 年第 6 06 期
煤
矿 机
电
・ 3 1・
蜗杆 传动模糊 优化设计
程钊 , 王得 胜 , 玉 王
( 河南理工大 学 机械与动力工程 学院 , 南 焦作 440 ) 河 500
摘
要 : 本文建立 了蜗杆传动模糊优化设计的数学模型, 运用最优水平截集法对模糊约束条件进
机械毕业设计1393凸轮机构的模糊优化设计论文正文

1引言近几年来,对摆动滚子从动件平面凸轮机构进行普通优化设计的较多,并能从众多满足设计要求的可行方案中,选出实现设计目标的最佳方案。
但由于设计中根据设计规范或经验确定的某些参数取值的不确定性,以及影响设计的某些因素如载荷性质、材质好坏又很难用确定的数值表示,这就导致了设计的模糊性。
而普通优化设计均未对这些模糊因素进行分析,致使设计方案难以更好地符合客观实际,为此需建立模糊优化设计的数学模型。
1.1本课题的研究意义凸轮机构广泛用于各种自动机中。
例如,自动包装机、自动成形机、自动装配机、自动机床纺织机械、农业机械印刷机械、自动办公设备、自动售货机陶瓷、机械加工中心换刀机构、高速压力机械、自动送料机械、食品机械、物流机械电子机械、自动化仪表服装加工机械、制革机械、玻璃机械、弹簧机械和汽车等。
凸轮机构之所以能够得到广泛的应用,是因为它具有传动、导向和控制等功能。
当它作为传动机构时,可以产生复杂的运动规律;当它作为导向机构时,可使工作机械的动作端产生复杂的运动轨迹;当它作为控制机构时,可控制执行机构的工作循环。
凸轮机构还具有以下优点:高速时平稳性好,重复精度高,运动特性良好,机构的构件少,体积小,刚性大,周期控制简单,运动特性良好,机构的构件少,体积小,刚性大,周期控制简单,可靠性好,寿命长。
1.2本课题国内外研究现状、水平和发展趋势随着社会发展和科技进步,各种自动机正朝着高效率、高精度、自动化程度高、优良的性能价格比、寿命长、操作简单和维修方便等方向发展。
为适应这种发展形式,满足自动机的要求,作为自动机核心部件的分度凸轮机构必须具有特性优良的凸轮曲线和高速、高精度性能。
由于计算机软件和数控技术的日益普及,凸轮CAD/CAM软件的问世,为高速高精度凸轮机构的设计、制造和检测提供了有利条件。
凸轮曲线特性优良与否直接影响凸轮机构的精度、效率和寿命。
多年来,世界上许多凸轮专家创造了数十种特性优良的凸轮曲线。
这些凸轮曲线完全能够满足各种自动机的要求。
基于粒子群算法的汽车传动系参数多目标优化

基于粒子群算法的汽车传动系参数多目标优化基于粒子群算法的汽车传动系参数多目标优化说起汽车,大家都知道它的动力系统由发动机和传动系统两部分组成。
而传动系统中的传动系则是决定汽车性能和油耗的重要组成部分。
然而,如何确定传动系的参数却是一项艰巨的任务。
在传动系统中,参数的数值对于车辆性能和油耗都至关重要。
随着科技的发展,汽车工程师正在探求新的优化方法,以便通过正确调整传动系参数来提高汽车的性能和经济性。
粒子群算法(Particle Swarm Optimization,PSO)是一种近年来被广泛应用于车辆设计优化的算法。
他的工作原理是利用数学模型,通过计算数值来达到优化的目标。
然而,由于传动系参数的多维特性和多目标性,传统的单目标优化方法并不能很好地完成任务。
PSO算法由于可以同时考虑多个优化目标,因此具有一定的优势。
按照PSO算法的工作原理,首先我们要为粒子设定初始参数。
然后,将粒子带入系统进行模拟,逐步调整粒子的初始参数,以尽可能地满足多个预设优化目标。
最终,算法将给出最佳的传动系参数取值,这是使得所有优化目标达到最优值的最佳解。
与传统的优化方法相比,基于PSO算法的传动系参数优化具有多个优点。
它可以同时考虑多个因素,减少了单目标优化方法因局部最优解而导致的误判。
同时,在进行参数优化时,它可以帮助汽车工程师更好地确定每个参数的重要性以及影响。
这些优势使得PSO算法,在汽车优化领域的应用趋于广泛。
基于粒子群算法的汽车传动系参数多目标优化,可以为汽车工程师提供更好的指导方案,同时也使得汽车的性能和经济性都有了极大的提升。
未来,这项技术将继续得到准确和精确的优化,以满足消费者对汽车性能和经济性的不断增长的需求。
以体积最小为目标函数的圆柱齿轮传动优化设计_何克祥

4 计算实例
设计某减速器中的渐开线斜齿圆柱齿轮传动, 其 输人功率 P = 45kW, 输人转速 n1 = 960r/m in, 传动比 u = 3, 工作寿命要求达到 Lh = 72000h; 原动机采用电 动机、工作状态均匀平稳, 大、小齿轮材料均为 40C r调 质后表面淬火, 齿轮精度采用 8 7 7。要求在满足正常 工作的条件下体积最小。
( 7) 轮齿弯曲应力应不大于许用应力 由齿轮传动
受力分析及实践证明, 轮齿可看作一悬臂梁, 按悬臂梁
计算齿轮传动中轮齿所受的最大弯曲应力。其最大弯
曲强度为
F
=
1 6KT 1 YFS bd01m n
由此得约束条件:
[ F]
g8 (x) = [ ] F1 - F1 0
g9 (x) = [ ] F2 - F2 0
中图分类号: TH 16; TG65
文献标识码: A
The Optim al D esign of Cylindrical G ear w ith the Objective Fun ction of the Sm a llest Volum e H E K e x iang
( Shaanx i Po lytechn ic Institu te, Shaanx i X ianyang 712000, Ch ina) Abstract: Cy lindrical gearmechan ical tran smission are most w idely u sed in one dev ice, in order to enable the cyl indrical gear tran smission structure is more compact, the design of amore reasonab le size, bu t also in order to improve transm ission performance and serv ice life, enhance the smooth transmission, and need to be Op timal D esign of reasonable。 th is text aims at to invo lute cyl indrical gear drive design, use ofmodern de sign methods to op timize the design, to the ob jective function of the smal lest volume of the gear drive, ex p ectation s by op timizing the design was the smallest volume of gear to reduce th e size of the entire trans mission case, to make up for the shortcomings of manual calcu lation. the estab lishmen tmathematical model and the choice of op timization method w as explored. the examples Combined w ith actual are given. K ey w ord s: invo lute cyl indrical gear; op timal design; vo lume; objective function
机械装备优化设计三级项目汇报 基于MATLAB的蜗轮蜗杆减速传动的优化设计

T2表示蜗轮输出转矩,大小为 1.5 10 N mm ; m为蜗轮蜗杆模数;Z1为蜗杆头数;Z2为蜗轮齿数;d1为蜗杆分 度圆直径;K为载荷系数取值, K K A K K 1.5111.05 1.21; [ H]为蜗轮齿面许用接触应力,单位为 MPa。代入相应参数化 2 为: 520 5 2
优化设计问题分析
在各类机械产品和装备中,蜗轮蜗杆减速传动是在交错轴 之间传递转矩和运动,具有传动比大、连续啮合、工作平 稳、低振动、噪声小、冲击载荷小及具有自锁性等优点; 而且其传动比大,体积小、重量轻、结构紧凑,蜗杆轮齿呈 螺旋形,蜗轮轮齿呈短而宽的环形悬臂梁,故蜗轮蜗杆传动 具有很高的抗弯强度,在数控回转工作台减速中有着广泛 的应用。在设计过程中如何确定最优的蜗轮蜗杆的模数、 齿数、直径、传动比以及中心距等基本参数,从而减小其 体积和质量、提高其承载能力和延长其使用寿命,具有重 要的经济价值和实用意义。本报告以数控回转工作台蜗轮 蜗杆减速装置为研究对象,目的使其达到体积最小、材料 最轻的设计目标。
优化设计方案选择
设计优化目的旨在寻找最优解,本报告是 通过机械设计的相关知识进行模型分析, 建立其优化设计的数学模型,以MATLAB强 大的矩阵处理功能为平台,进行MATLAB 程序语言的编写,最后利用软件自带的优 化工具箱进行优化求解,从而得到目标的 最优解,并且实现蜗轮蜗杆减速传动的优 化设计。
π 6 2 2 minF(x) 0.75x2 ( x3 2 x2 )50x1 2 (50x1 6.4) 4 x1 2
X [ x1, x2 , x3 ] [ z1, m, d1 ]
T
T
s .t Gi ( x) 0 i 1,2,3,,9
基于Pareto解模糊优化的汽车动力传动系匹配

基于Pareto解模糊优化的汽车动力传动系匹配
王艺;叶欢月;宋小文;王耘;胡树根
【期刊名称】《机械科学与技术》
【年(卷),期】2011(030)009
【摘要】采用基于Pareto解的交互式模糊优化算法,提出了以汽车动力性、经济性与排放性为评价指标的评价体系,以3个指标为优化目标建立了多目标模糊优化模型。
优化过程中对多目标引进协同灵敏度分析,多目标耦合情况给予考虑。
利用Matlab编写了实现此算法的动力传动系统优化程序。
并以某型号农用车传动系参数作为实例进行了验证,验证了此方法的有效性。
【总页数】5页(P1413-1417)
【作者】王艺;叶欢月;宋小文;王耘;胡树根
【作者单位】浙江大学能源工程学系,杭州310027;浙江交通技师学院,金华321015;浙江大学能源工程学系,杭州310027;浙江大学能源工程学系,杭州310027;浙江大学能源工程学系,杭州310027
【正文语种】中文
【中图分类】TP391.7
【相关文献】
1.基于遗传算法的汽车动力传动系匹配设计变量优化 [J], 文孝霞;杜子学
2.基于复合形法的汽车动力传动系参数优化匹配分析 [J], 刘涛;郭源科
3.基于燃油经济性的汽车动力传动系匹配优化 [J], 杜子学;刘记君
4.基于燃油经济性的汽车动力传动系匹配优化 [J], 杜子学;刘记君
5.基于惩罚函数法的汽车动力传动系参数优化匹配分析 [J], 王薇;谷正气;董继征因版权原因,仅展示原文概要,查看原文内容请购买。
- 1、下载文档前请自行甄别文档内容的完整性,平台不提供额外的编辑、内容补充、找答案等附加服务。
- 2、"仅部分预览"的文档,不可在线预览部分如存在完整性等问题,可反馈申请退款(可完整预览的文档不适用该条件!)。
- 3、如文档侵犯您的权益,请联系客服反馈,我们会尽快为您处理(人工客服工作时间:9:00-18:30)。
— 蜗杆材料的弹性模量 ,N/ mm ; J — 蜗杆危险断面处的惯性矩 , mm , J =
mm. 2. 4 蜗杆特性系数约束
2
4
πd4 f1
64
; df 1 — 蜗杆齿根圆直径 ,
Байду номын сангаас
设计手册一般推荐使用 8 ≤ q ≤16 ,化成模糊约束为
[ q] ≤
~
≤ [ q ]. ~ tgα
Z1
-
2. 5 蜗杆螺旋升角约束
Abstract : This t hesis applies rague t heory to rague optimum design and evaluation of common cylinder worm drive ,which takes nodule ,spiral angle and worm number as variables and mini2 mal corona sixe ,maximal drive efficency and best lubrication condition as target f unction. Key words : Worm ;Optimum design ;rague t heory
表2 寻优结果与原始方案比较 设计变量 原始方案 模糊优化方案
Z1 ( x) m ( x 2)
图3 优化过程程序框图
,蜗杆材料 45 # 钢 ,淬火 HRC45 ~ 54 ,蜗轮齿冠材料 ZQSn10 - 1. 要求设计的蜗杆传动尽量作到在满足
正常运行条件下 , 节约锡青铜 , 创造良好的润滑条件 , 同 时使蜗杆传动效率最大 . 综合考虑设计与制造水平、 使用材料 、 重要程度 、 使 用条件 、 维修使用费用因素 ,采用一级模糊综合评判法求 解最优截集水平 λ3 = 0 . 494 . 优化方法采用内点罚函 数法 ,惩罚因子初始值 0 = 20 ,递减函数 C = 0 . 5 . 其 优化过程是通过罚函数将有约束的问题转化为无约束的 问题求解 . 求解方法采用鲍威尔法 ,将无约束的多维问题 转化为一维问题求解 . 再通过莫余分割法确定最优步长 搜索 ,最后采用进退法在确定的搜索区间内进行计算 . 将 结果返回主程序进行判断 ,满足精度后要进行参数圆整 , 按实际要求 ,齿数按自然整数序列进行圆整 ,螺旋角按标 准的蜗杆特性系数进行圆整 ,3 个设计变量 ,共有 8 种方 案 ,将方案代入目标函数式 , 并判断是否为可行点 , 从而 确定最优点 . 程序框图如图 3 所示 . 在最优截集水平下 , 得出计算结果如表 2 所示 .
对于传递动力蜗杆 ,设计手册推荐 12°≤α ≤27°,化为模糊约束为
[α] ≤α[α].
~ ~
-
2. 6 蜗轮齿数约束
普通圆柱蜗杆传动 ,一般取 Z2 = 27 ~ 80 ,化为模糊约束为
[ Z2 ] ≤ i Z1 ≤ [ Z2 ].
~ ~
-
2. 7 模数 、 蜗杆头数的限制
对于这类边界约束 ,一般按普通常规约束处理 :
收稿日期 :2001 - 04 - 13 作者简介 : 陈健 (1954 - ) ,女 ,辽宁鞍山人 ,济源高等职业技术学院机电系高级讲师 .
第3期
陈 健 : 普通圆柱蜗杆传动的多目标模糊优化设计
67
( 3)
F2 ( x ) =
m n1
19100
( z 1 / tgα ) 2 + z2 1 ,
式中 : n 1 — 蜗杆转速 , r/ min .
经化简得
F1 ( x ) = V = 0 . 51 ( m z1
图1 蜗轮齿冠体积
tgα
+ 2 m ) [ ( iz 1 m + 3 m ) 2 - ( iz 1 m - 6 . 4 m ) 2 ].
( 2)
1. 2 效率目标
要使蜗杆传动效率最大 ,即发热量 、 摩损量最小 ,就应使齿面相对滑动速度最小 .
q K T2 m
3 2 qz 2
-
σH = Z E
≤ [σ] H ,
~
( 7)
式中 : σH — 蜗轮的计算接触应力 ,N/ mm2 ; Z E — 材料系数 , Z E = 159 . 8 ; K — 载荷系数 ; T 2 — 蜗轮所 受扭矩 ,Nmm ; [σ] 模糊许用接触强度 ,Nmm2 .
V = ( 1)
轮齿数 ; i — 速比 , i = z 2 / z 1 ; m — 模数 ; e — 齿冠最小厚度 , e = 2 m , mm ; B — 蜗轮宽度 , mm , B = 0 . 65 d a1 ; d a1 — 蜗杆齿顶圆直径 , mm ,
d a1 = m q + 2 m ; q — 蜗杆特性系数 , q = z 1 / tgα ; α螺旋升角 .
[ m ] ≤ m ≤ [ m ] , [ Z1 ] ≤ Z1 ≤ [ Z1 ].
-
3 模糊约束的非模糊处理
模糊约束的隶属函数 ,工程上多采用线性隶属函数 . 约束条件不外乎有三种 .
( 1) 当常规约束为 g ≤ [ g ] 时 ,隶属函数图应为图 2 ( a ) 所示 ,得截集水平的上界为
1. 3 润滑条件目标
为了改善润滑条件 ,由流体弹性动压润滑线接触油膜厚度计算公式 ( 道枕公式 ) [ 2 ] 可知 , 为建立弹 性流体动压润滑状态创造有利条件 ,需使蜗杆蜗轮齿面接触点处的诱导法曲率半径趋于最大 ,即其曲率 趋于最小 ,
R = R1 R2 . R1 + R2
式中 : R — 诱导法曲率半径 ,mm ; R 1 , R 2 — 分别表示蜗杆与蜗轮在接触点法面上的曲率半径 ; 1/ R — 诱导法曲率 . 经推导
-
第3期
陈 健 : 普通圆柱蜗杆传动的多目标模糊优化设计
-
69
模糊过度区间的上下限 ,现在最常用扩增系数法来确定[3 ] ,即若普通设计规定 [ g ] ≤ g ≤ [ g ] ,则取
-
g
-
L
-
-
= [ g] , g
u
-
-
= a [ g] , g
u
-
= [ g] , g
-
L
= a [ g] ,
-
a , a 分别为上 、 下限扩增系数 ,一般取 1 . 05 ~ 1 . 30 ,根据约束的性质 、 重要性具体确定 . 确定上下界之
后 ,就将模糊优化模型转化为截集水平为 λ 非模糊优化模型 . 隶属函数图及模糊约束向非模糊约束转 化如表 1 所示 .
( a) ( b) ( c)
~
-
2. 2 蜗轮弯曲强度约束
σF =
1 . 62 K T 2
m qz 2
-
3
Y F Yβ ≤ [σ] F ,
~
-
( 8)
式中 : σF —蜗轮齿根的计算弯曲应力 ,N/ mm2 ; [σ] F —模糊许用弯曲应力上限 ,N/ mm2 ; Y F — 蜗轮的
~
α ° 齿形系数 ; Yβ — 螺旋角系数 , Yβ = 1 . 140° 2. 3 蜗杆刚度约束 蜗杆工作时最大挠度不应大于
图2 隶属函数图形
70
-
鞍山师范学院学报
-
第3卷
( 8) 、 ( 9) 、 ( 10) 、 ( 11 ) 、 将表 1 中的 [σ] H 、 [σ] F 、 [ y ]、 [ q ][ q ] 、 [λ] [λ] 、 [ Z2 ] [ Z2 ] 分别代入式 ( 7) 、
~ ~ ~ ~ ~ ~ ~ ~
2 约束条件
考虑到工程上实际的边界约束常呈模糊性 ,应存在一个从完全允许到完全不允许的一个过渡区间 , 这里将以蜗轮齿面接触应力 、 蜗杆齿面的弯曲力 、 蜗杆刚度等性能来约束蜗杆头数 ( 蜗轮齿数) ,模数 、 螺 旋升角的取值范围 ,均视为设计空间上的模糊子集 .
2 . 1 蜗轮齿面接触强度约束
F3 ( x ) =
1
R
=
= m iz 1 sinα ′
2cosα
5 . 85cosα
m iz 1
,
( 4)
式中 : α ′— 标准压力角 , α ′= 20° . 对于蜗杆传动 ,一般传动速比是确定的 . 由式 ( 2) ( 3) ( 4 ) , z 1 , m 和α 为三个独立变量 ,所以取设计 变量为
~
-
g λ = g u - λ( g u - g L ) ,
-
-
-
-
即
g ≤g
u u L - λ( g - g ) ,
式中 : λ — 截集水平 , λ ∈ [ 0 , 1 ]. ( 2) 当约束为 [ g ] ≤ g ≤ [ g ] 时 ,隶属函数图形如图 2 ( b) 所示 ,得其约束为
~ ~
g ≥g
X = [ x 1 , x 2 , x 3 ] T = [ z 1 , m ,α] T , ( 5) ( 6)
采用加权系数法 ,得总的目标函数为
F ( x ) = W 1 F1 ( x ) + W 2 F2 ( x ) + W 3 F3 ( x ) ,
式中 : W 1 , W 2 , W 3 — 加权因子 ,要求 W 1 + W 2 + W 3 = 1 .
鞍山师范学院学报
J ournal of Ansha n Teachers College
2 0 0 1 20 9 , 3 ( 3 ) : 6 6 - 7 0
普通圆柱蜗杆传动的多目标模糊优化设计
陈 健
( 济源高等职业技术学院 机电系 ,河南 济源 471000)
摘 要 : 以普通圆柱蜗杆传动的蜗杆头数 、 模数 、 螺旋升角为设计变量 ,以蜗轮齿冠体积最小 、 传动效率最 大、 润滑条件最好为目标函数 ,应用模糊理论对普通圆柱蜗杆传动进行模糊优化设计与实例验算 . 关键词 : 蜗杆 ; 优化设计 ; 模糊理论 中图分类号 : TH122 文献标识码 :A 文章篇号 :100822441 ( 2001) 0320066205