苯胺法高压搅拌合成2-巯基苯并噻唑反应器(3m3)的设计
2-巯基苯并噻唑反应器的选型、设计与

四、从VX03中向反应器RX01中进料 1、打开反应器RX01放空阀V12 2、打开进料泵PUMP1的前阀V10 3、打开进料泵PUMP1 4、打开进料泵PUMP1的后阀V11,向RX01 中进料(Na2Sn) 5、进料完毕(LI103为0.09m),关闭 PUMP1泵的后阀V11 6、停进料关泵PUMP1 7、关闭进料泵前阀V10 五、从VX01中向反应器RX01中进料(CS2) 1、检查放空阀V2开放 2、打开进料阀V4向RX01中进料 3、待进料完毕(LI101为0.00m),关闭V4 六、从VX02中向反应器RX01中进料 ( C6H4CLNO2) 1、检查放空阀V6开放 2、打开进料阀V8向RX01中进料 3、待进料完毕(LI102为0.00m)关闭V8 4、进料完毕后关闭放空阀V12
冷热源的选择
冷源:冷却水 反应温度达110~130℃,冷冻盐水冷却效果较好且 工业上应用比较广泛。
选择:压料 因为使用位差出料会使很多的产品留在釜 的内壁,上出料对于操作要求较高,出料 时通入增压蒸汽。出料时应该要注意不要 弄到皮肤上,因为该品低毒,对皮肤和粘 膜有刺激作用。
安全措施
பைடு நூலகம்
十、出料准备 1、打开放空阀V12 5~10s,放出可燃气体 2、关闭放空阀V12 3、打开阀门V13和v15,通入 增压气体 4、打开蒸汽出料预热阀V14,片刻后关闭 V14 十一、出料 1、打开出料阀V16 2、出料完毕(LI104为0.00m), 保持吹 扫10s,关闭V16 3、关闭蒸汽阀V15和V13
釜式反应器温度自动控制
TT
隔套
TT
调节阀
利用劣质苯胺合成2-巯基苯并噻唑的中试优化工艺

利用劣质苯胺合成2-巯基苯并噻唑的中试优化工艺尹志刚;罗雷鸣;张同艳;钱恒玉;张春霞;王全玲;费宗雷【摘要】以劣质苯胺作为原料,首先在低压下进行苯胺与二硫化碳的分子间亲核加成反应,然后采用闷罐型(无搅拌)高压反应釜进行分子内氧化脱氢合成了2-巯基苯并噻唑.经过单因素考察,得出优化中试工艺条件:n(PhNH2)∶n(CS2)∶n(S)=1.00∶1.10∶ 1.04,投料系数0.50,温度240℃,时间4h,收率约80%.该优化工艺将传统苯胺法中“溶硫过程”更改为低压反应过程,在不增加任何设备投入的情况下,使收率提高约10%,操作简便.【期刊名称】《精细石油化工》【年(卷),期】2013(030)003【总页数】5页(P38-42)【关键词】2-巯基苯并噻唑;劣质苯胺;优化合成工艺;中试【作者】尹志刚;罗雷鸣;张同艳;钱恒玉;张春霞;王全玲;费宗雷【作者单位】郑州轻工业学院,河南省表界面科学重点实验室,河南郑州450000;郑州轻工业学院,河南省表界面科学重点实验室,河南郑州450000;郑州轻工业学院,河南省表界面科学重点实验室,河南郑州450000;郑州轻工业学院,河南省表界面科学重点实验室,河南郑州450000;郑州轻工业学院,河南省表界面科学重点实验室,河南郑州450000;郑州轻工业学院,河南省表界面科学重点实验室,河南郑州450000;郑州轻工业学院,河南省表界面科学重点实验室,河南郑州450000【正文语种】中文【中图分类】O626.322-巯基苯并噻唑[1](促进剂M)是一种重要的化学中间体,主要用作橡胶硫化促进剂,也用作医药中间体和金属腐蚀抑制剂或金属减活剂[2-5]。
目前,工业上主要采用传统“苯胺法”来合成促进剂M,即先将硫磺溶解在二硫化碳中(称为“溶硫过程”),然后在190℃,用高压泵将硫磺的二硫化碳溶液与苯胺加入高压反应釜中,反应约5h[6-7],反应过程如下:传统苯胺法合成促进剂M 分为3个步骤:第一步,将硫磺溶解到二硫化碳中;第二步,使用物料泵将硫磺的二硫化碳溶液和苯胺加到高压反应釜中进行高温、高压反应;第三步,将粗产物进行分离得到合格的促进剂M。
2-巯基苯并噻唑的合成与固体吸附剂对合成反应的影响

第38卷第3期河北工业大学学报2009年6月V ol.38No.3JOURNAL OF HEBEI UNIVERSITY OF TECHNOLOGY June2009文章编号:1007-2373(2009)03-0029-04Ïõ»ù±½»ìºÏ·¨´úÌæ´«Í³µÄ±½°··¨ºÏ³É2-巯基苯并噻唑(促进剂M),确定了最佳的合成条件:反应温度为240~260℃,反应时间为4h,产品收率大于80%.以活性氧化铝、二氧化硅和活性炭3种常见的固体吸附剂为催化剂,考察了固体吸附剂对合成反应的影响,催化效果明显:2-巯基苯并噻唑的收率由原来的80.6%提高到了85%以上,最高达到86.7%;反应时间由原来4h缩短为3h.关键词2-巯基苯并噻唑;促进剂M;合成;活性氧化铝;二氧化硅;活性炭中图分类号TQ251.2文献标识码ASynthesis of2-Mercaptobenzothiazole and Effects of SolidAdsorbents on the Synthetic ReactionHAN Jin-ping1,WANG Nong-yue2,FENG Xiao-gen2,PAN Ming-wang1(1.Institute of Polymer Science and Engineering,Hebei University of Technology,Tianjin300130,China; 2.Shanghai Sinorgchem(Group)Co.Ltd.,Shanghai200136,China)Abstract An improved process for the preparation of2-mercaptobenzothiazole(accelerator M)by reacting aniline,nit-robenzene,and carbon disulfide was disclosed.The reaction was optimal conducted at240℃to260℃for4hours withthe yield more than80percentage.Activated alumina,silica dioxide and activated carbon,which are three commonsolid adsorbents,were applied as catalyst,respectively.The yield of2-mercaptobenzothiazole was improved from theoriginal80.6%to more than85%,even up to86.7%.And the reaction time had been shortened from the original4hoursto3hours.Key words2-mercaptobenzothiazole;accelerator M;synthesis;activated alumina;silica dioxide;activated carbon2-巯基苯并噻唑在工业上简称促进剂M,它既是一种重要的硫化促进剂,是产量最大的促进剂品种,又是合成噻唑类和次磺酰胺类促进剂的中间体.2-巯基苯并噻唑的合成方法很多[1],其中工业生产上比较成熟的合成路线是苯胺法.苯胺法是以苯胺、二硫化碳和硫磺为原料,在200~300℃,9.0~10.0MPa条件下反应,生成的粗品再经精制得到成品2-巯基苯并噻唑的方法[2-4].Akzo等[5]发现某些酸、酸性物质或成酸物质可做催化剂.由于此法反应压力高,危险性大,反应后的副产物H2S又难以处理,因此寻找更可靠且废气排放量小的方法一直是助剂行业研讨的热门课题.苯胺法改进的硝基苯-苯胺混合法[6-8]是合成2-巯基苯并噻唑的一种新方法,也是近年来研究的热点.硝基苯与苯胺混合法不但成本低,而且副产物H2S的量比苯胺法降低1/3,但该法反应复杂、副产物多、产品纯度低,且对反应器的材料要求也较高.固体吸附剂是一些多孔、大比表面积、具有吸附活性的固体物质.本文采用硝基苯与苯胺混合法,以3种固体吸附剂活性氧化铝、二氧化硅和活性炭为催化剂合成2-巯基苯并噻唑,着重研究了它们对合成反应时间和产品收率的影响.1实验部分1.1主要原料与仪器设备原料:苯胺、硝基苯、二硫化碳(分析纯,国药集团化学试剂有限公司);活性氧化铝、二氧化硅、收稿日期:2009-03-10作者简介:韩金平(1984-),女(汉族),硕士生;导师简介:潘明旺(1964-),男(汉族),教授.30河北工业大学学报第38卷活性炭(化学纯,天津市天大化工试验厂);其他试剂均为国产化学纯.粉末活性氧化铝是孔体积为300~800mm 3/g 、比表面积为100~300m 2/g的m、比表面积为200~400m 2/g ;活性炭比表面积为500~1000m 2/g (比表面积测试采用全自动F-Sorb2400比表面积分析仪,BET 法进行).反应设备:GCF-1型高压釜(威海祥威化工机械厂生产).1.2合成反应方程式2-巯基苯并噻唑合成的化学反应式如下主要副反应的反应式如下1.32-巯基苯并噻唑的合成与处理向高压釜中加入苯胺149.0g ,硝基苯98.5g ,二硫化碳292.4g 及适量吸附剂为催化剂,密闭,搅拌下加热升温,控制反应温度在设定温度范围内.待反应结束后,冷却降温,并用30%氢氧化钠溶液吸收反应产生的硫化氢气体,釜内固体物即为反应生成的粗产品2-巯基苯并噻唑.粗品2-巯基苯并噻唑经精制后得到成品.精制过程参照文献[8]方法进行,主要包括以下步骤:氢氧化钠碱液溶解、过滤、鼓风氧化、过滤、硫酸酸化、过滤、洗涤、真空干燥等.2结果与讨论2.1反应温度对产品收率的影响苯胺法合成2-巯基苯并噻唑的最低反应温度为200℃,最高温度为300℃[10].参考上述反应温度,以确定本合成路线的最佳反应温度,实验过程如1.3所述,反应时间拟定为4h .改变反应温度,考察不同反应温度对产品收率的影响,结果如图1所示.从图1可以看出:反应温度为240~260℃时,2-巯基苯并噻唑的收率较高,达到80%左右.从实验现象来看,反应温度越高,反应速度越快;温度越低,反应速度越慢.当反应温度过低时,反应速度较慢,副反应较多,生成的杂质较多,对产品的收率影响较大;而反应温度过高时,产物易碳化颜色发黑,产生较多的焦油副产物,从而使产品2-巯基苯并噻唑的含量降低;同时实验也发现:反应温度较高时,反应温度和压力较难控制,容易造成超压现象.因此,较佳的反应温度范围为240~260℃,最佳反应温度为250℃.2.2反应时间对产品收率的影响反应时间也是合成反应的重要影响因素,反应时间过长会引起副反应增多,反应时间过短则会导致反应不完全.按1.3所述的操作,设定反应温度为250℃,改变反应时间,考察不同反应时间对产品收率的影响,结果如图2所示.从图2中可以看出,在反应时间少于4h 范围内,随反应时间的增加,产品2-巯基苯并噻唑的收率逐步提高,原因可能是在此范围合成反应进行不够充分;当反应时间达到4h 左右时,2-巯基苯并噻唑的收率达到最大值;而后随反应时间延长,副产物增多,产品收率降低.因此,较佳的反应时间为4h .(1)++++(2)图1反应温度对2-巯基苯并噻唑收率的影响Fig.1Effect of reaction temperature on the yield of 2-mercaptobenzothiazole 2002202402602808278747068/h收率/%第3期韩金平,等:2-巯基苯并噻唑的合成与固体吸附剂对合成反应的影响31 2.3合成原理分析苯胺/min/min32河北工业大学学报第38卷面积,使反应迅速、充分发生,从而显著提高反应速率,减少副反应发生的机会.在这3种吸附剂中活性炭的比表面积最大,吸附效果最好,所以反应时间最短;二氧化硅表面存在活性硅羟基(Si-OH )[11],是质子酸性表面,有利于产品2-巯基苯并噻唑的合成[5],因此反应收率最高.2.5固体吸附剂用量对反应的影响固定其它反应条件,改变吸附剂用量,考察吸附剂用量对2-巯基苯并噻唑收率的影响,结果如图6所示.其中吸附剂活性氧化铝、二氧化硅、活性炭用量分别为反应物料总质量的0.5%、1%、1.5%、2%;添加活性氧化铝的合成反应时间为3.5h ,添加二氧化硅、活性炭的合成反应时间为3h .由图6可以看出,随着吸附剂用量的增加,2-巯基苯并噻唑的收率有先升高再降低的趋势.说明加入一定量的吸附剂有助于加快反应,提高反应产物的收率,但吸附剂加入量过多,不但会使原料成本增加,同时会导致反应的选择性下降,副产物含量增加,产品的收率降低.由图6可以看出,吸附剂的选用量分别为:活性氧化铝3.1~4.7g ,约为反应物料总质量的1%~1.5%;二氧化硅3.1~6.3g ,约为反应物料总质量的1%~2%;活性炭1.5~4.7g ,约为反应物料总质量的0.5%~1.5%,合成的2-巯基苯并噻唑收率可达到85%左右.3结论采用苯胺-硝基苯混合法合成2-巯基苯并噻唑工艺,本文分别考察了反应温度和时间对产品收率的影响,确定了较佳反应温度为240~260℃(最佳250℃),反应时间为4h ,产品收率能达到80%左右.通过加入活性氧化铝、二氧化硅或活性炭固体吸附剂,获得了良好的催化效果:首先提高了产品2-巯基苯并噻唑的收率,由不加吸附剂时的80.6%提高到了85%以上,其中加入二氧化硅的反应收率最高,达到86.7%.其次缩短了反应时间,分别加入这3种吸附剂反应3h ,产品收率即能达到或超过不加吸附剂反应4h 的收率.由于活性氧化铝、二氧化硅、活性炭是3种常用的固体吸附剂,价廉易得,这将有利于苯胺-硝基苯混合法制备2-巯基苯并噻唑在工业生产中的推广应用.参考文献:[1]尹志刚,陈培同,钱恒玉.促进剂M 的合成及其应用进展[J ].合成橡胶工业,2007,30(5):398-402.[2]Makoto S ,Kenjiro M ,Morisue N .Process for the rapid production of 2-mercaptobenzothiazole [P ].US Patent :3818025,1974-06-18.[3]Shaw C K .Purification of mercaptobenzothiazole [P ].US Patent :4515957,1985-05-07.[4]奚国辉,王晓华.2-巯基苯并噻唑合成反应工艺研究[J ].石化技术与应用,2003,21(4):259-261.[5]Cobb A ,Peemans R ,Coenegrachts P ,et al .Acid catalysed process for preparing 2-mercaptobenzothiazole and derivatives thereof [P ].WO :1997/046544,1997-12-11.[6]Reynolds ,Malz .Method for the production of 2-mercaptobenzothiazole [P ].US :6222041,2001-04-24.[7]吴举祥.连续化合成粗品硫化促进剂M 工艺的改进[J ].江苏化工,2007,35(1):49-51.[8]李薇,吴凯涛.正交试验研究生产促进剂M 的主反应工艺条件[J ].内蒙古石油化工,2005,9:12-13.[9]兰毅浩,李建州.高压M 后处理工艺分析[J ].甘肃科技,2007,23(5):76-77,80.[10]金福盛,甄中华.2-巯基苯并噻唑制造技术的进步[J ].精细化工,1995,8(1):39-41,52.[11]谢海安,戴宏程.超微细二氧化硅的改性研究及其应用[J ].湖北化工,2001(5):23-25.[责任编辑田丰]图5不同反应时间下吸附剂对2-巯基苯并噻唑收率的影响Fig.5Effects of adsorbent on the yield of 2-mercaptobenzothiazole at different reaction time Al 2O 3SiO 2活性C 对照9080706050收率/% 2.5h 3h 3.5h 4h 图6吸附剂用量对2-巯基苯并噻唑收率的影响Fig.6Effects of amount of adsorbents on the yield of2-mercaptobenzothiazole Al 2O 3SiO 2活性C 8880706050收率/%00.5%1%1.5%2%。
2-巯基苯并噻唑类衍生物的合成方法改进[发明专利]
![2-巯基苯并噻唑类衍生物的合成方法改进[发明专利]](https://img.taocdn.com/s3/m/0f23a4d1a32d7375a41780ef.png)
专利名称:2-巯基苯并噻唑类衍生物的合成方法改进专利类型:发明专利
发明人:邹小毛,刘殿甲,傅翠蓉,李伟,丁会娟,臧福坤申请号:CN201110191939.7
申请日:20110711
公开号:CN102304099A
公开日:
20120104
专利内容由知识产权出版社提供
摘要:本发明公开了一种合成2-巯基苯并噻唑衍生物的改进方法,将较为简单的原料——苯胺衍生物,二硫化碳和硫磺在反应釜中,充N至反应的压力保持在6~15MPa范围内,升温至200~260℃下反应2~5h。
用碱溶解产品,过滤除去副反应杂质,酸化析出产品含量在99%以上,通过优化反应条件可以使反应收率提高到90~100%。
本发明的优点在于:不仅节约了反应原料的成本,缩短了反应时间;而且提高了反应纯度和收率,可以推广至大规模工业生产。
申请人:南开大学
地址:300071 天津市南开区卫津路94号
国籍:CN
更多信息请下载全文后查看。
苯胺法高压搅拌合成2-巯基苯并噻唑反应器(3m3)的设计
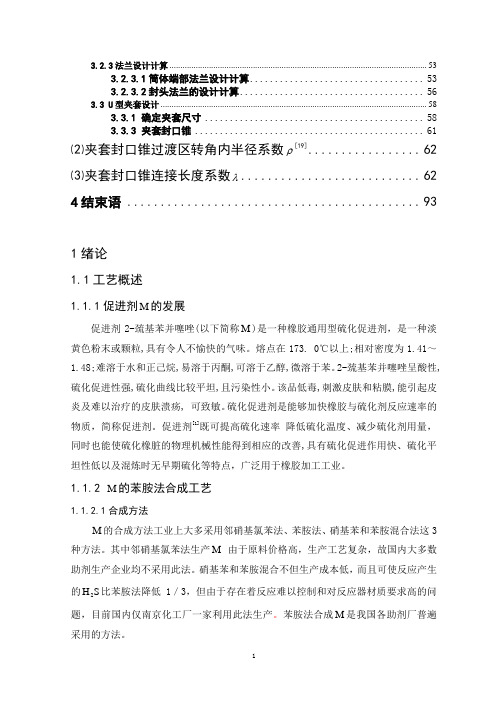
3.2.3法兰设计计算 (53)3.2.3.1筒体端部法兰设计计算 ................................... 53 3.2.3.2封头法兰的设计计算 . (56)3.3 U 型夹套设计 (58)3.3.1 确定夹套尺寸 ............................................ 58 3.3.3 夹套封口锥 . (61)⑵夹套封口锥过渡区转角内半径系数ρ[19] (62)⑶夹套封口锥连接长度系数λ ........................... 62 4结束语 ............................................ 93 1绪论1.1工艺概述1.1.1促进剂M 的发展促进剂2-巯基苯并噻唑(以下简称M )是一种橡胶通用型硫化促进剂,是一种淡黄色粉末或颗粒,具有令人不愉快的气味。
熔点在173. 0℃以上;相对密度为1.41~1.48;难溶于水和正己烷,易溶于丙酮,可溶于乙醇,微溶于苯。
2-巯基苯并噻唑呈酸性,硫化促进性强,硫化曲线比较平坦,且污染性小。
该品低毒,刺激皮肤和粘膜,能引起皮炎及难以治疗的皮肤溃疡, 可致敏。
硫化促进剂是能够加快橡胶与硫化剂反应速率的物质,简称促进剂。
促进剂[1]既可提高硫化速率 降低硫化温度、减少硫化剂用量,同时也能使硫化橡脏的物理机械性能得到相应的改善,具有硫化促进作用快、硫化平坦性低以及混炼时无早期硫化等特点,广泛用于橡胶加工工业。
1.1.2 M 的苯胺法合成工艺1.1.2.1合成方法M 的合成方法工业上大多采用邻硝基氯苯法、苯胺法、硝基苯和苯胺混合法这3种方法。
其中邻硝基氯苯法生产M 由于原料价格高,生产工艺复杂,故国内大多数助剂生产企业均不采用此法。
硝基苯和苯胺混合不但生产成本低,而且可使反应产生的S H 2比苯胺法降低1/3,但由于存在着反应难以控制和对反应器材质要求高的问题,目前国内仅南京化工厂一家利用此法生产。
橡胶硫化促进剂2-巯基苯并噻唑的合成进展
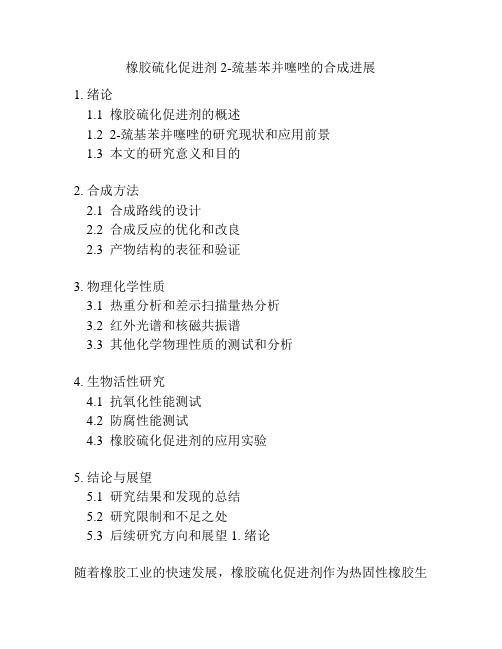
橡胶硫化促进剂2-巯基苯并噻唑的合成进展1. 绪论1.1 橡胶硫化促进剂的概述1.2 2-巯基苯并噻唑的研究现状和应用前景1.3 本文的研究意义和目的2. 合成方法2.1 合成路线的设计2.2 合成反应的优化和改良2.3 产物结构的表征和验证3. 物理化学性质3.1 热重分析和差示扫描量热分析3.2 红外光谱和核磁共振谱3.3 其他化学物理性质的测试和分析4. 生物活性研究4.1 抗氧化性能测试4.2 防腐性能测试4.3 橡胶硫化促进剂的应用实验5. 结论与展望5.1 研究结果和发现的总结5.2 研究限制和不足之处5.3 后续研究方向和展望1. 绪论随着橡胶工业的快速发展,橡胶硫化促进剂作为热固性橡胶生产中最为重要的辅助剂之一,具有极其重要的应用价值。
橡胶硫化促进剂是指在加速硫化反应中,起到促进硫化速度、改善运动性能和物理性能的化合物。
它们具有优越的加工性能,可使橡胶在快速硫化的同时,保持较好的物理性质。
因此,橡胶硫化促进剂已成为橡胶制品工业发展的重要支撑。
而2-巯基苯并噻唑(MBT)是一种重要的橡胶硫化促进剂,也被广泛应用于橡胶生产中。
MBT的分子结构中包含噻唑环和苯环,通过2-巯基相连,这种结构能与橡胶分子中的双键进行反应,加速橡胶硫化反应。
除此之外,MBT还具有较好的抗氧化性能和耐热性能,以及防腐性能。
在实际应用中经常与其他橡胶硫化促进剂混合使用,以达到更好的增塑效果。
然而,传统的MBT合成方法存在着一些不足之处。
例如,合成过程中需要高温和高压,操作条件苛刻,且溶剂多为有机溶剂,对环境会造成一定影响。
为解决这些问题,近年来研究人员开始相继开发新的MBT合成方法,以提高合成效率和经济效益。
本文旨在系统总结2-巯基苯并噻唑的合成进展,并对其应用前景进行展望。
为此,将从以下三个方面进行探讨:第一,在综述橡胶硫化促进剂的概念及其应用基础上,简要介绍2-巯基苯并噻唑的物理化学性质以及其在橡胶生产中的应用场景。
2-巯基苯并噻唑

2-巯基苯并噻唑的合成工艺
五组:杨俊芳、孙传梅、任秀 云、李科、唐基恩
工艺概述 促进剂的发展
促进剂2-巯基苯并噻唑(以下简称)是一种橡胶通用 型硫化促进剂,是一种淡黄色粉末或颗粒,具有令 人不愉快的气味。熔点在173. 0℃以上;相对密度 为1.41~1.48;难溶于水和正己烷,易溶于丙酮,可溶 于乙醇,微溶于苯。2-巯基苯并噻唑呈酸性,硫化促 进性强,硫化曲线比较平坦,且污染性小。
降很慢。 处理:开出料预热蒸汽阀V14吹扫5分钟以上 (仿真中采用)。拆下出料管用火烧化硫磺, 或更换管段及阀门。
5、测温电阻连线故障
原因:测温电阻连线断。 现象:温度显示置零。 处理:改用压力显示对反应进行调节(调节 冷却水用量)。 升温至压力为0.3~0.75atm就停止加热。 升温至压力为1.0~1.6atm开始通冷却水。
苯胺法合成工艺
M的合成方法工业上大多采用邻硝基氯苯法
苯胺法、硝基苯和苯胺混合法这3种方法 。 苯胺合成M各助剂厂普遍采用的方法。 苯胺法生产M的特点是原料来源稳定,操作 难度小。对反应器材质要求低,其缺点是 由于法生产的粗M中M含量较低(85%), 焦油量大,收率较低,因此如何完善高压M 合成生产工艺,提高产品收率一直是国内 生产企业研究的重要课题。
变化缓慢。 处理:停止操作,出料维修。
3、冷却水阀V22、V23卡住(堵塞)
原因:蛇管冷却水阀V22卡。 现象:开大冷却水阀对控制反应釜温度无作
用,且出口温度稳步上升。 处理:开冷却水旁路阀V17调节。
4、出料管堵塞
- 1、下载文档前请自行甄别文档内容的完整性,平台不提供额外的编辑、内容补充、找答案等附加服务。
- 2、"仅部分预览"的文档,不可在线预览部分如存在完整性等问题,可反馈申请退款(可完整预览的文档不适用该条件!)。
- 3、如文档侵犯您的权益,请联系客服反馈,我们会尽快为您处理(人工客服工作时间:9:00-18:30)。
3.2.3法兰设计计算 (53)3.2.3.1筒体端部法兰设计计算 ................................... 53 3.2.3.2封头法兰的设计计算 . (56)3.3 U 型夹套设计 (58)3.3.1 确定夹套尺寸 ............................................ 58 3.3.3 夹套封口锥 . (61)⑵夹套封口锥过渡区转角内半径系数ρ[19] (62)⑶夹套封口锥连接长度系数λ ........................... 62 4结束语 ............................................ 93 1绪论1.1工艺概述1.1.1促进剂M 的发展促进剂2-巯基苯并噻唑(以下简称M )是一种橡胶通用型硫化促进剂,是一种淡黄色粉末或颗粒,具有令人不愉快的气味。
熔点在173. 0℃以上;相对密度为1.41~1.48;难溶于水和正己烷,易溶于丙酮,可溶于乙醇,微溶于苯。
2-巯基苯并噻唑呈酸性,硫化促进性强,硫化曲线比较平坦,且污染性小。
该品低毒,刺激皮肤和粘膜,能引起皮炎及难以治疗的皮肤溃疡, 可致敏。
硫化促进剂是能够加快橡胶与硫化剂反应速率的物质,简称促进剂。
促进剂[1]既可提高硫化速率 降低硫化温度、减少硫化剂用量,同时也能使硫化橡脏的物理机械性能得到相应的改善,具有硫化促进作用快、硫化平坦性低以及混炼时无早期硫化等特点,广泛用于橡胶加工工业。
1.1.2 M 的苯胺法合成工艺1.1.2.1合成方法M 的合成方法工业上大多采用邻硝基氯苯法、苯胺法、硝基苯和苯胺混合法这3种方法。
其中邻硝基氯苯法生产M 由于原料价格高,生产工艺复杂,故国内大多数助剂生产企业均不采用此法。
硝基苯和苯胺混合不但生产成本低,而且可使反应产生的S H 2比苯胺法降低1/3,但由于存在着反应难以控制和对反应器材质要求高的问题,目前国内仅南京化工厂一家利用此法生产。
苯胺法合成M 是我国各助剂厂普遍采用的方法。
苯胺法生产M 的特点是原料来源稳定,操作难度小,对反应器材质要求低,其缺点是由于该法生产的粗M 中的M 含量较低(85%),焦油量大,收率较低。
因此,如何完善高压M 合成生产工艺,提高产品收率,综合利用轻组分(主要是苯并噻唑)一直是国内生产企业研究的重要课题。
[1] 1.1.2.2合成原理苯胺法合成M 是以苯胺、2CS 和硫磺为原料,在 200~300 ℃,9.0~10.0 MPa 条件下反应,生成的粗M 再经精制得到成品M 的生产方法。
其原理[2]是苯胺和硫磺先反应生成2,2′-二氨基二苯基二硫,再经2CS 酰化作用生成2, 2′- 二巯基二苯硫脲,最后转化为M 。
也就是反应方程式:原料规格:苯胺含量不小于 99.3%,水分含量不大于0.5%。
硝基苯含量不大于 0.015%, 2CS 含量不小于98.5%。
H 2S 含量不大于0.9%,残渣含量不大于0.02%。
硫磺含量不小于98.5%,水分含量不大于0.3%,灰分含量不大于0.1%。
1.2机械设计方案对比1.2.1材料选用针对促进剂M 的生产,对反应釜的设计,材料选择上应考虑其物料性质对釜体的影响。
在反应过程中有S H 2生成,同时反应过程压力较大,温度较高,对其进行综合性的考虑。
1.2.2 搅拌装置选用1.2.2.1 驱动方案对比磁力驱动是把机械能转变成磁能, 再由磁能转变为机械能的过程, 是利用磁体与磁体之间能通过空气或非磁性材料的磁力作用,可非接触地进行力传递。
使轴在被密封介质和大气之阀不用连接而形成无密封的搅拌,以达到绝对无泄漏。
目前国内已定型的标准釜用机械密封产品,由于其设计压力等参数的限制, 已远远不能满足要求;从防止污染及安全、节能等角度出发,对轴封装置的可靠性、寿命、泄漏量和经济性等方面的要求也越来越高。
[3]主要技术难点有:1)由于反应器的工艺特点,压力、温度、物料的形态等都随时间而变化, 在压力循环和冷热循环的作用下,密封端面易变形,导致密封失效;2)由于反应器操作温度较高,机械密封在运转时,摩擦面发热及釜内的热传导,将使密封腔内温度进一步上升,从而引起摩擦面液膜汽化,产生“干运转”,并加速腐蚀、磨损,加快密封圈老化,致使密封很快失效;3)该反应器操作压力接近10MPa , 密封介质压力是引起密封环变形的主要作用力, 其变形也是密封失效的主要因素之一;4)反应器搅拌轴的摆动量和振动必然较大, 因而容易使摩擦副间隙内流体液膜厚度产生变化, 摩擦副之间不能很好地贴合,有时还会将石墨环撞坏;5)间歇操作、频繁启动造成端面比压、摩擦力矩反复变化,易使密封失效,寿命降低。
另外,由于用户的维修技术水平不高,安装不良也很容易造成釜用机械密封的失效。
所以设计时应从便于安装、检修方面加以考虑。
对传统的填料密封[4],虽然可以通过改进各种填料和填料函的结构提高其密封性能,但泄漏是不可避免的。
因为搅拌轴都存在一定量的径向跳动和偏心,而起密封作用的润滑油膜不总是处在理想的粘着状态,所以填料只能对泄漏起节流作用而不能完全杜绝泄漏。
反应釜使用机械密封可使通过动、静环接触面的泄漏减小到最小,但其制造技术复杂,安装要求高,检修工作量大,影响了釜用机械密封在危险介质中的应用。
无泄漏釜用磁力传动就是为实现零泄漏而设计、制造的。
其最大特点就是把搅拌轴的动密封改成隔离套的静密封,从而达到不泄漏的目的。
内磁钢衬在钢套上,钢套与搅拌轴相连,搅拌轴由2个轴承进行轴向固定。
在内磁钢外面是隔离套,隔离套与容器相连承受容器内压力。
隔离套外是外磁钢,外磁钢与减速机输出轴相连,支承轴的两轴承固定在釜盖上。
由于取消了填料函轴封,所以可节能约10 %。
磁力传动部分使用状况良好, 减少了环境污染, 保证了安全。
由于空气被隔绝于釜外, 这对于空气氧化敏感的物料具有特殊意义, 可以因此提高产品收率和其它理化指标。
由于磁力传动的特殊优点,可在条件适合的反应釜上应用,但不是所有反应釜上都能使用。
如在反应过程中有较多固体产物时则不能应用,因为固体产物可能对搅拌产生较大的负载而使内磁钢滑脱。
在介质温度太高时也不能使用,此时会产生退磁现象。
1.2.2.2 搅拌器设计方案搅拌过程有赖于搅拌器的正常运转,当然搅拌器的结构,强度液是不容忽视的问题。
由于搅拌操作的多样性,使搅拌器存在着多种型式。
各种搅拌器在配备各种可控制流动状态的附件后,能使流动状态以及供给能量的情况出现多种变化,更有利于强化不同的搅拌过程。
典型的搅拌器型式有桨式,涡轮式,推进式,锚式,框式,螺带式,螺杆式等。
下面对几种搅拌器进行简单的介绍: [5]⑪桨式搅拌器桨式搅拌器又可分为平直叶和折叶搅拌器两种。
这类搅拌器的结构和加工都比较简单。
搅拌器直径d 与釜径D 之比d/ D 为0.35~0.8 , 其运转速度为10 ~ 100r/ min , 为大型低速搅拌器,适用于低、中等粘度物料的混合及促进传热, 可溶固体的混合与溶解等场合。
运转时以剪切力为主。
就平直叶和折叶两种相比较而言, 由于折叶桨式搅拌器的叶片与旋转平面形成夹角, 因此在旋转时产生的轴向流要大于平直式, 其宏观混合效果更好些。
在实际生产中, 会遇到釜深液高的情况, 此时单层桨式搅拌器难以搅拌均匀, 通常采用的方法是装几层桨叶, 相邻二层桨叶间成90°角交错安装。
由于桨式搅拌器制造和更换方便, 因此常用于化工生产中有防腐蚀和金属污染要求的工况。
⑫涡轮式搅拌器涡轮式搅拌器又可分为开启涡轮式和圆盘涡轮式两类, 每类又可分为平直叶、折叶、后弯叶三种。
涡轮式搅拌器外形结构上与桨式搅拌器类似, 只是叶片较多。
搅拌器直径d 与釜径D 之比d/ D 为0117~015 , 转速为30~500r/ min。
旋转时有较高的局部剪切作用, 能得到高分散度微团, 适用于气液混合及液液混合或强烈搅拌的场合, 常用于低中等粘度物料(μ< 5 ×104cP) 。
就开启式和圆盘式相比较而言, 其构造上差异造成开启式比圆盘式循环流量更大, 轴向混合效果更好。
涡轮式搅拌器的叶片形状除了有平直叶和折叶外, 还有一种弯叶, 在搅拌中, 此种叶片受损程度、消耗功率都低, 适用于固体悬浮、固体溶解等搅拌场合。
⑬推进式搅拌器推进式搅拌器也常被称为旋桨式搅拌器。
顾名思义, 其叶片形式类似于轮船上的螺旋桨。
搅拌器直径d 与釜径D 之比d/ D 为012~015 , 转速较高, 为100~800r/ min。
运转时产生较大的轴向循环流量, 宏观混合效果较好, 适用于均相液体混合等搅拌不是非常强烈的以宏观混合为目的的搅拌场合, 常用于低粘度料液(μ<2000cP)的混合。
在搅拌器的选用时, 可按需搅拌的料液粘度及搅拌目的来选型。
就搅拌料液的物性来看, 粘度对搅拌效果的好坏是一个很重要的因素。
低粘度料液混合时的流动形式是湍流, 运动时高速旋转的旋涡尺寸越小, 对液体微团的破碎作用越大, 混合效果就越好。
由此看来应选用直径小, 高转速搅拌器。
性能优劣依次为: 推进式> 涡轮式> 桨式。
反之, 高粘度料液混合时的流动形式通常是层流。
由于料液高粘度这一特性, 使得搅拌时不能象低粘度料液那样依靠惯性力, 因此搅拌叶轮直径d 与釜径D 之比d/ D 尽量大, 所以应先选择锚式和框式搅拌器, 也可选螺带式。
搅拌目的:①均相液体混合均相低粘度液体混合流动状态为湍流, 即循环流量起决定性因素。
按此特点选择的搅拌器依次为: 推进式> 涡轮式> 桨式。
②非均相液体混合为了使其中一相以尽可能小的液滴状均匀分散到另一相中去, 就要求液体被搅拌时有较大的剪切力和循环流量, 以此来选择的优劣依次为:涡轮式> 推进式> 桨式。
③固液混合固液混合要求让固体悬浮于液体中需要容积循环好。
如固体比重与液体比重差小时, 可选用推进式搅拌器。
因为此类搅拌器为轴流型, 循环速率高。
当固体比重与液体比重差大时, 则应选用开启式涡轮搅拌器, 此类搅拌器工作时会把沉降的固体颗粒浮起来而推进式则正好相反。
④气液混合与液液互不相溶混合相似, 在剪切力作用下尽可能将大气泡打碎成小气泡以增大接触面积,使之均匀分散至液相, 剪切力起决定作用, 应优先选用涡轮式搅拌器, 又以平直叶圆盘涡轮搅拌器最为合适。
因为此搅拌器中间的圆盘可将气泡(一般由容器底部通入) 压至其下, 而后均匀分散至液相, 避免了气泡直接由搅拌轴短路。
⑤强化液体与器壁的传热此类操作的总体循环流量和换热面积上的高速流动起主要作用, 可优先选用涡轮式搅拌器1.2.3加热方案的对比⑪水蒸汽加热方式水蒸汽加热包括直接加热(与反应物混合) 和间接加热(预热器预热) 两种方式。