建模及强度分析报告
大摆锤游乐设备有限元强度分析报告
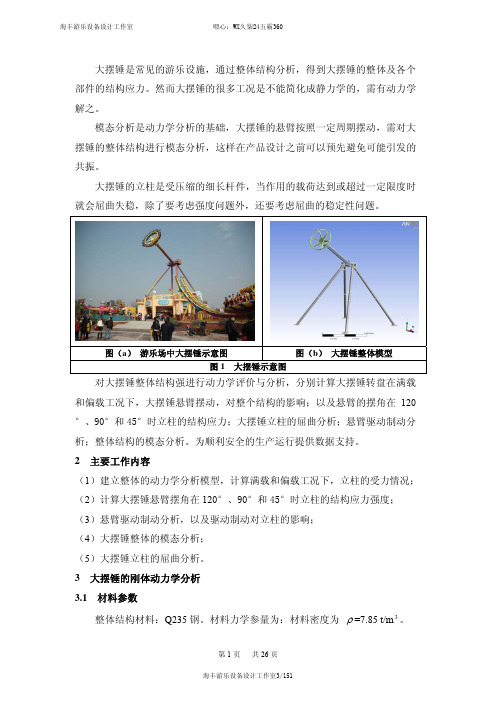
大摆锤是常见的游乐设施,通过整体结构分析,得到大摆锤的整体及各个部件的结构应力。
然而大摆锤的很多工况是不能简化成静力学的,需有动力学解之。
模态分析是动力学分析的基础,大摆锤的悬臂按照一定周期摆动,需对大摆锤的整体结构进行模态分析,这样在产品设计之前可以预先避免可能引发的共振。
大摆锤的立柱是受压缩的细长杆件,当作用的载荷达到或超过一定限度时就会屈曲失稳,除了要考虑强度问题外,还要考虑屈曲的稳定性问题。
图(a)游乐场中大摆锤示意图图(b)大摆锤整体模型图1 大摆锤示意图对大摆锤整体结构强进行动力学评价与分析,分别计算大摆锤转盘在满载和偏载工况下,大摆锤悬臂摆动,对整个结构的影响;以及悬臂的摆角在120°、90°和45°时立柱的结构应力;大摆锤立柱的屈曲分析;悬臂驱动制动分析;整体结构的模态分析。
为顺利安全的生产运行提供数据支持。
2 主要工作内容(1)建立整体的动力学分析模型,计算满载和偏载工况下,立柱的受力情况;(2)计算大摆锤悬臂摆角在120°、90°和45°时立柱的结构应力强度;(3)悬臂驱动制动分析,以及驱动制动对立柱的影响;(4)大摆锤整体的模态分析;(5)大摆锤立柱的屈曲分析。
3 大摆锤的刚体动力学分析3.1 材料参数整体结构材料:Q235钢。
材料力学参量为:材料密度为 =7.85 t/m3。
3.2 几何模型使用通用结构分析软件ANSYS Workbench Environment(AWE)14.0多物理场协同CAE仿真软件,对大摆锤的整体进行建模,分别建立立柱、悬臂、大转盘建,并在软件中进行装配,如图3所示。
(a)大摆锤整体结构(b)转盘局部结构(c) 大摆锤悬臂(d)大摆锤立柱图2 大摆锤整体装配模型3.3载荷与约束立柱的底板固定在地方面,因此在立柱底板与地面之间,施加固定(Fixed)约束,模拟底板与地面之间的紧固连接。
在重力作用下,悬臂绕转筒中心轴转动,在悬臂的横臂的内表面和立柱固定筒之间,施加旋转幅(Revolute),模拟悬臂绕横梁转动。
3dmax建模实验报告内容

3dmax建模实验报告内容1. 实验目的本实验旨在通过使用3DMax软件进行建模,学习和掌握3D建模的基本原理和操作技巧。
2. 实验环境- 操作系统:Windows 10- 软件工具:3DMax 20213. 实验内容3.1 建立场景首先,在3DMax中创建一个新的场景。
选择一个适合的场景背景,例如户外环境或室内空间,以便后续的建模工作。
3.2 添加基本模型在场景中添加基本的模型,例如立方体、球体、圆柱体等。
通过调整这些基本模型的尺寸、位置和旋转角度等属性,来构建所需的物体形状。
3.3 进行模型细化通过进一步细化模型,添加细节和特征,使其更加真实和逼真。
可以使用3DMax提供的模型库,或自行绘制模型并导入。
3.4 材质和纹理处理为模型添加材质和纹理,使其表面具有不同的颜色、纹理、光泽等特征。
可以通过调整材质属性,如色彩、透明度、反射率等,来实现所需的渲染效果。
3.5 光照和渲染设置通过添加光源来照亮场景,并设置不同种类的光照效果,如方向光、点光源和聚光灯等。
进一步调整光照属性,如颜色、强度和阴影设置等,以达到所需的渲染效果。
3.6 动画和渲染输出在模型中添加动画效果,如旋转、平移或变形等。
通过调整关键帧设置和动画路径,使模型产生动态效果。
最后,设置渲染参数,选择合适的渲染引擎,生成最终的渲染效果图或动画。
4. 实验结果与分析经过实验,我们成功完成了一个3D建模的过程,并生成了一个具有逼真效果的渲染图。
在实验过程中,我们学习和掌握了3DMax软件的基本操作,包括添加模型、调整属性、细化模型、处理材质和纹理、设置光照和动画等方面的技巧。
通过实验,我们发现3DMax软件具有强大的建模和渲染功能,能够满足不同需求的建模任务。
同时,我们也发现了一些问题,如材质调整不够细致、光照设置不够逼真等,这些问题需要进一步学习和研究,以便提高建模的质量和效果。
5. 实验总结通过本次实验,我们初步了解了3DMax建模的基本原理和操作技巧,掌握了建立场景、添加基本模型、模型细化、材质和纹理处理、光照和渲染设置以及动画生成等方面的基本方法。
汽车变速器齿轮的强度分析【毕业作品】
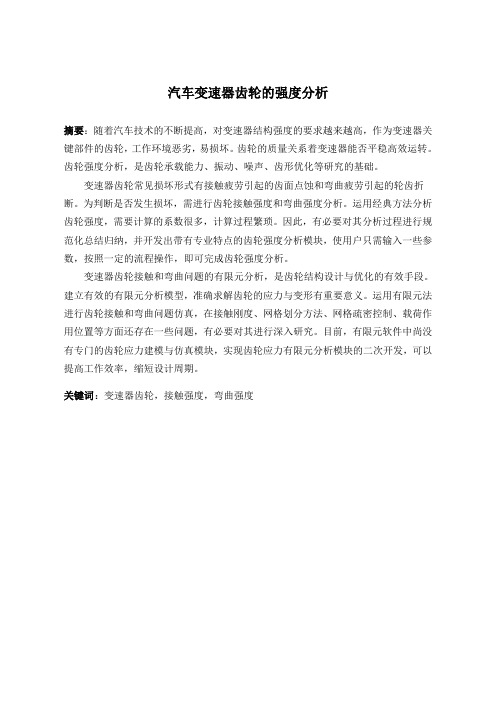
汽车变速器齿轮的强度分析摘要:随着汽车技术的不断提高,对变速器结构强度的要求越来越高,作为变速器关键部件的齿轮,工作环境恶劣,易损坏。
齿轮的质量关系着变速器能否平稳高效运转。
齿轮强度分析,是齿轮承载能力、振动、噪声、齿形优化等研究的基础。
变速器齿轮常见损坏形式有接触疲劳引起的齿面点蚀和弯曲疲劳引起的轮齿折断。
为判断是否发生损坏,需进行齿轮接触强度和弯曲强度分析。
运用经典方法分析齿轮强度,需要计算的系数很多,计算过程繁琐。
因此,有必要对其分析过程进行规范化总结归纳,并开发出带有专业特点的齿轮强度分析模块,使用户只需输入一些参数,按照一定的流程操作,即可完成齿轮强度分析。
变速器齿轮接触和弯曲问题的有限元分析,是齿轮结构设计与优化的有效手段。
建立有效的有限元分析模型,准确求解齿轮的应力与变形有重要意义。
运用有限元法进行齿轮接触和弯曲问题仿真,在接触刚度、网格划分方法、网格疏密控制、载荷作用位置等方面还存在一些问题,有必要对其进行深入研究。
目前,有限元软件中尚没有专门的齿轮应力建模与仿真模块,实现齿轮应力有限元分析模块的二次开发,可以提高工作效率,缩短设计周期。
关键词:变速器齿轮,接触强度,弯曲强度Auto ransmission gear strength analysisAbstract:With the continuous improvement of automotive technology,the demand of the transmission structural strength has become more and more increasingly.As a key component of the transmission,the working conditions of gears are poor and the gears are easy to damage.The quality of gears decides whether the transmission can operate smoothly and efficiently or not.The analysis of gear strength is the basis for the research of the gears carrying capacity,vibration,noise,profile optimization.The common forms of damage are tooth surface pitting caused by contact and tooth broken caused by bending fatigue.As to determine whether the damage occurred,the gear contact and bending strength need to ing classical method to calculate gear strength, many factors need to calculate,the process is very trouble.It is necessary to normalize and summarize the analysis process,and to develop the gear strength analysis professional module.The complete gear strength can be finished the certain input parameters are only provided.The finite element analysis of transmission gear contact and bending is an effective means of gear structural design and optimization.To establish the efficient and precise analysis of the gear contact and bending stress,there are some problems in the contact rigidity,mesh method,mesh density control,load lines.It is necessary to conduct in-depth study.There are so many gear pairs in transmission that it is difficult to analyze and calculate.At present, there is no application software having special module for gear stress simulation analysis.To develop professional modules of parametric modeling and simulation for gear stress analysis can greatly improve efficiency and shorten the design cycle.目录1绪论------------------------------------------------------------------ 1 1.1变速器齿轮强度分析的研究背景---------------------------------------- 1 1.1.1变速器齿轮失效形式------------------------------------------------ 1 1.1.2变速器齿轮强度分析方法-------------------------------------------- 1 1.2变速器齿轮强度分析与评价的研究现状---------------------------------- 2 1.2.1变速器齿轮强度分析的经典方法-------------------------------------- 2 1.2.2变速器齿轮强度分析的有限元法-------------------------------------- 3 1.2.3变速器齿轮强度评价方法-------------------------------------------- 4 1.3有限元软件ANSYS概述------------------------------------------------ 5 1.3.1 ANSYS简介-------------------------------------------------------- 5 1.3.2 ANSYS内部语言简介------------------------------------------------ 5 1.3.3 ANSYS二次开发功能------------------------------------------------ 5 1.4本文主要研究工作---------------------------------------------------- 6 2齿轮强度经典分析方法-------------------------------------------------- 7 2.1齿轮接触应力和齿根应力分析的经典方法-------------------------------- 7 2.1.1齿轮接触应力分析经典方法------------------------------------------ 7 2.1.2齿根应力分析经典方法---------------------------------------------- 7 2.2齿轮许用接触应力分析经典方法---------------------------------------- 8 2.2.1齿轮许用接触应力-------------------------------------------------- 8 2. 2. 2接触寿命系数---------------------------------------------------- 9 2.2.3润滑剂系数------------------------------------------------------- 10 2.2.4速度系数--------------------------------------------------------- 10 2.2.5粗糙度系数------------------------------------------------------- 11 2.2.6工作硬化系数----------------------------------------------------- 11 2.2.7接触尺寸系数----------------------------------------------------- 12 2.3齿轮许用齿根应力分析经典方法--------------------------------------- 12 2.3.1齿轮许用齿根应力------------------------------------------------- 122.3.2弯曲寿命系数----------------------------------------------------- 12 2.3.3相对齿根圆角敏感系数--------------------------------------------- 14 2.3.4相对齿根表面状况系数--------------------------------------------- 15 2.3.5弯曲尺寸系数----------------------------------------------------- 16 2.4本章小结----------------------------------------------------------- 16 3齿轮应力分析有限元法------------------------------------------------- 16 3.1面-面接触有限元分析关键问题---------------------------------------- 17 3.1.1接触面和目标面确定----------------------------------------------- 17 3.1.2单元类型选择----------------------------------------------------- 17 3.1.3接触协调条件----------------------------------------------------- 19 3.2斜齿轮接触应力分析有限元法----------------------------------------- 20 3.2.1单元属性定义----------------------------------------------------- 20 3.2.2网格划分方法研究与应用------------------------------------------- 21 3.2.3接触单元和目标单元生成------------------------------------------- 25 3.2.4接触应力求解与结果分析------------------------------------------- 26 3.2.5接触应力仿真影响因素分析----------------------------------------- 27 3.3斜齿轮弯曲应力分析有限元法----------------------------------------- 30 3.3.2整体单元尺寸对仿真影响分析--------------------------------------- 32 3.3.3线网格细化对仿真影响分析----------------------------------------- 34 3.3.4面网格细化对仿真影响分析----------------------------------------- 37 3.3.5网格划分控制确定------------------------------------------------- 42 3.3.6不同载荷作用位置对仿真影响分析----------------------------------- 43 3.4本章小结-------------------------------------------- 错误!未定义书签。
挖掘机工作装置运动和疲劳强度分析

设计计算DESIGN & CALCULATION挖掘机工作装置运动和疲劳强度分析武慧杰1,杨建伟1,张志强2(1. 北京建筑大学 机电与车辆学院,北京 100044;2. 中交路桥北方工程有限公司,北京 100024)[摘要]针对挖掘机工作装置的疲劳损伤,利用Pro/E 及ANSYS 进行三维建模及有限元分析。
通过Pro/E 平台中的机构模块分析工作装置的极限位姿以及运动参数,然后利用工作装置位姿转换,基于力矩平衡关系,对斗杆挖掘和铲斗挖掘工况下的铰点进行受力分析,获取工作装置各铰点的最大载荷。
在此基础上,利用ANSYS 疲劳强度分析得出挖掘机最小疲劳全寿命。
研究结果可为挖掘机工作装置结构设计提供理论参考。
[关键词]挖掘机;运动分析;疲劳强度;全寿命[中图分类号]TU621 [文献标识码]B [文章编号]1001-554X (2015)06-0089-05Kinematics and fatigue strength analysis of excavator working deviceWU Hui -jie ,YANG Jian -wei ,ZHANG Zhi -qiang本文在Pro/E 软件中对挖掘机整机进行实体三维建模,并运用Pro/E 的机构运动分析模块对挖掘机工作装置的包络图及铲斗齿尖的位移、速度和加速度进行仿真模拟。
然后基于ANSYS 软件,结合工作装置位姿关系计算工作装置各铰点承受的最大载荷,在此基础上对挖掘机动臂、斗杆进行应力和全寿命分析,得到挖掘机工作强度和使用寿命的校核结果,为挖掘机工作装置强度和可靠性分析提供了高效的解决办法。
1 挖掘机三维建模与虚拟仿真1.1 工作装置原理与结构液压挖掘机的作业过程包括铲土挖掘、满载回转、举升卸载、空斗返回等,其中反铲作业设备是液压挖掘机的主要工作装置[1],由动臂、斗杆、铲斗、动臂油缸、斗杆油缸、铲斗油缸、连杆等组成,其结构如图1所示。
土方机械工作装置整体结构的强度分析方法

土方机械工作装置整体结构的强度分析方法摘要:基于工作土方机械设备的结构特征,结合有限元方法计算结果提高分析的准确性的问题,以一个小型挖掘机工作装置结构为研究对象,整体结构使用有限元分析方法,提出了工作装置动臂,铲斗,斗杆,油缸和连接销轴系统组成进行整体建模、加载和有限元强度分析,并结合实际的产品开发进行验证。
结果表明,该方法对土方机械及同类产品的设计和分析具有一定的指导意义,为解决类似问题提供了一种可行的分析方法。
关键词:土方机械;工作装置;整体机构;有限元;强度分析1前言在工程土工的机械使用中,其工作效率在很大程度上取决于工作装置,特别是设备的结构强度直接影响到土方机械的可靠性和性能的使用。
土方机械,如挖掘机、装载机等,其工作装置通常由动臂、连杆、斗杆、斗链机构等组成。
有限元法在土方机械结构分析中得到了广泛的应用。
目前,大多数研究只进行有限元分析的连接销轴套筒的铰链点的工作设备,并且经常忽视的联系和协调问题的影响轴和轴套的计算结果。
2工作装置有限元模型及计算工况2.1工作装置整体结构有限元模型的建立小型液压挖掘机的工作装置主要由活动臂、斗杆、桶和油缸组成。
利用UG软件,建立了框架的三维几何模型、动臂、斗杆、桶形和连接盖。
在建模过程中,去掉了螺杆孔,不影响计算结果的倒角,消除了运输吊耳等因素。
在实际模型中,对焊缝进行连续处理,将材料作为母材处理。
利用有限元方法对有限元软件ANSYS有限元模型进行了有限元分析。
由于移动臂、臂等设备的各个部分主要由薄板焊接构成,几何模型非常复杂,所以在有限元模型的划分中,Solid45单元类型选择三维实体单元。
油缸是由Link8单元建模的[1]。
最后的工作装置由活动臂、斗杆和其他部件组装而成,在活动臂与斗杆之间、铲斗之间通过连接套筒和销轴连接。
利用接触针表面的三维接触元件和连接套管的表面,建立了整体工作装置的更精确的有限元模型。
工作装置整体结构的有限元模型。
2.2计算工况的确定挖掘机的挖掘工况由动臂油缸、斗杆油缸,铲斗油缸的变化可以组合成成千上万的工作条件,因此如何确定工作装置,在外载荷作用下的一种或几种最不利条件下,针对强度计算的工作条件,强度的准确是非常重要的。
不规则球形封头的逆向建模应力分析和强度评估
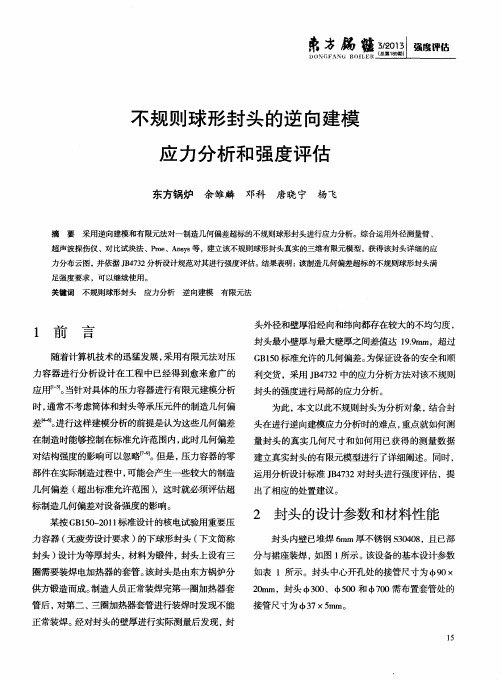
逆向建模 有 限元法
1 日 J I 吾
随着计 算机技 术 的迅猛 发展 , 采用 有限元法 对压
头外径和壁厚沿经向和纬向都存在较大的不均匀度,
封 头最小壁厚 与最大壁厚之 间差值达 1 9 . 9 m m,超过
G B 1 5 0 标准允许的几何偏差。 为保证设备的安全和顺
利交 货 ,采用 J B 4 7 3 2中的应 力分析方法对 该不规则 封头 的强度进行 局部 的应力 分析 。 3 3 5测量封 头的外半径 , 采用 U S N 6 0 数 字超声波探
工作温度( ℃) 设计温度( ℃) 腐蚀裕量( m m) 简体名义尺寸( m m)
封头名义尺寸 mm )
伤仪和对比试块法来测量封头母材的厚度( 不包括堆 焊层厚度 ) 。封头具体的测试方案如图 2 所示。在封
图1 已部 分装 焊 的下球 形封头 组件
封头和与其相焊的筒身的材料均为 2 0 M n M o I V ,
电加热器套管的材料为 0 C r l 8 N i l 0 T i ,封头中心开孔 处的接管材料为 s 3 2 1 6 8 Ⅲ,它们的泊松 比1 J 、设计 温度下的弹性模量 E t 、 设计温度下的许用应力 S m ( 按
头 外表面按 图 2中要 求每 1 0 。 画经 纬线 ,经纬线 交
点即为测量点。 此外, 为了保证封头与筒身连接部位 的可测量性 , 对封头和裙座的焊接部分进行了切除处 理, 并根据超声波探伤仪的测量要求对封头外表面进
行 抛光处理 ,抛光 后的表面粗糙 度不大于 6 _ 3 m。
加 姗 姗 o 一 矾
封头 ) 设计为等厚封头, 材料为锻件, 封头上设有三
圈需要 装焊 电加 热器 的套 管 。 该封头 是 由东方 锅炉分
ansys实验强度分析报告
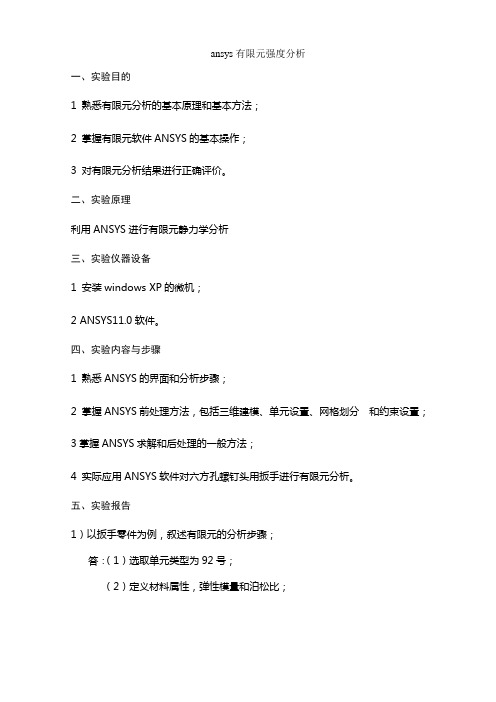
ansys有限元强度分析一、实验目的1 熟悉有限元分析的基本原理和基本方法;2 掌握有限元软件ANSYS的基本操作;3 对有限元分析结果进行正确评价。
二、实验原理利用ANSYS进行有限元静力学分析三、实验仪器设备1 安装windows XP的微机;2 ANSYS11.0软件。
四、实验内容与步骤1 熟悉ANSYS的界面和分析步骤;2 掌握ANSYS前处理方法,包括三维建模、单元设置、网格划分和约束设置;3掌握ANSYS求解和后处理的一般方法;4 实际应用ANSYS软件对六方孔螺钉头用扳手进行有限元分析。
五、实验报告1)以扳手零件为例,叙述有限元的分析步骤;答:(1)选取单元类型为92号;(2)定义材料属性,弹性模量和泊松比;建立模型。
先生成一个边长为0.0058的六边形平面,再创建三条线,其中z向长度为0.19,x向长度0.075,中间一段0.01的圆弧,然后把面沿着三条线方向拉伸,生成三维实体1如题中所给形状,只是手柄短了0.01;把坐标系沿z轴方向平移0.01,再重复作六边形面,拉伸成沿z轴相反方向的长为0.01的实体2;利用布尔运算处理把实体1和2粘接成整体。
(4)划分网格。
利用智能网格划分工具划分网格,网格等级为4级。
(5)施加约束。
在扳手底部面上施加完全约束;(6)施加作用力。
在实体2的上部面上施加344828pa(20/(0.01*0.0058))的压强,在实体2的下部面的临面上施加1724138pa(100/0.01/0.0058)的压强;(7)求解,进入后处理器查看求解结果,显示应力图。
2)对扳手零件有限元分析结果进行评价;答:结果如图所示:正确的显示出了受力的最大位置及变形量,同时给出了各处受力的值,分析结果基本正确,具有一定的参考意义。
六、回答下列思考题1.什么是CAE技术?答:CAE是包括产品设计、工程分析、数据管理、试验、仿真和制造的一个综合过程,关键是在三维实体建模的基础上,从产品的设计阶段开始,按实际条件进行仿真和结构分析,按性能要求进行设计和综合评价,以便从多个方案中选择最佳方案,或者直接进行设计优化。
电动汽车声品质的评价分析及建模

电动汽车声品质的评价分析及建模随着人们对环境保护意识的提高以及新能源技术的不断进步,电动汽车已经成为了人们日常生活中越来越常见的一种出行方式。
然而,与传统燃油车相比,电动汽车的声品质一直是广大消费者关注的焦点。
因此,本文将从声品质的角度对电动汽车进行评价分析,并建立一种声品质评价的数学模型。
电动汽车的声品质主要包括以下几个方面:1. 噪音:电动汽车在行驶过程中产生的运动噪音和驱动系统噪音相对较小,但电动机咆哮、轮胎与路面的摩擦噪音、车内舱噪音等在低速行驶时仍然较为明显,影响驾驶者的驾驶体验。
2. 振动:电动汽车的振动相对于传统燃油车会更小,但同时也会受到驱动系统和制动系统的影响,如轮胎与路面间的摩擦力等。
3. 声音:电动汽车的声音比传统燃油车要小,但具有独特的声音特征,如电动机的高频噪音、电子设备的电磁干扰噪音等。
对于电动汽车的声品质评价,首先需要确定评价指标。
本文选取了以下五个指标来评估电动汽车的声品质:1. 噪音级别:使用噪音仪器测得电动汽车在不同速度下的噪音大小。
2. 振动级别:使用振动仪器测得电动汽车在不同路况下的振动大小。
3. 安静度:使用环境噪音仪器测得车内环境下的噪音大小。
4. 低频音质:使用360度环境声场仪器测得电动汽车在不同速度下低频音的情况。
5. 高频音质:使用频谱分析仪器测得电动汽车在不同速度下高频音的情况。
在确定了评价指标后,我们需要对电动汽车的声品质进行建模,以定量化地评价汽车的声音质量。
1. 噪音级别模型:噪音级别模型使用如下公式计算:Lp = 10 log10 (p2/p1) + K其中,Lp表示声级,p2表示被测物体产生的声压级,p1表示参考级别(一般取10^-12 Pa),K为常数。
通过该公式可以计算出电动汽车在不同速度下的噪音级别。
2. 振动级别模型:振动级别模型使用如下公式计算:V = (1/N) ∑ (v^2)其中,V表示振动级别,N为采样点数,v表示每个采样点的振动大小。
轻量化不锈钢车体静强度仿真分析
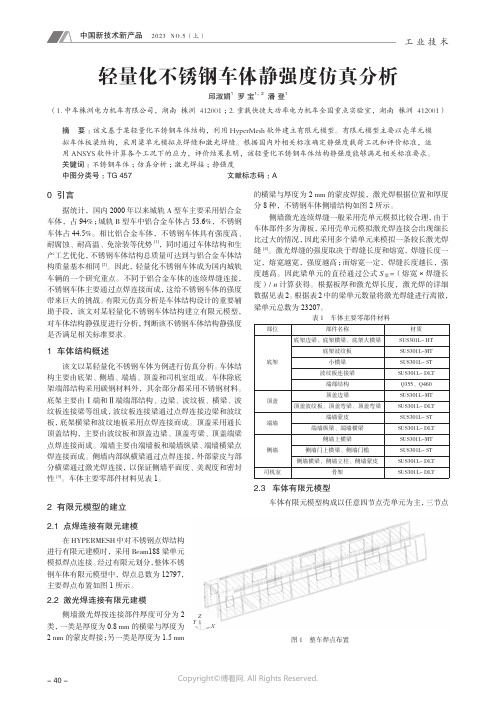
许用剪切力,其中 AW3 状态下 800 kN 纵向压缩工况,2 种
板厚最大的前 5 个焊点的计算结果见表 5。
表 5 AW3+ 纵向压缩工况作用下焊点剪切力
侧墙0.8mm
侧墙1.5mm
单元号 合成剪切力(N)
单元号
合成剪切力(N)
2524321
1453.23
1398863
1640.26
2524320
拟车体板梁结构,采用梁单元模拟点焊缝和激光焊缝。根据国内外相关标准确定静强度载荷工况和评价标准,运
用 ANSYS 软件计算各个工况下的应力,评价结果表明,该轻量化不锈钢车体结构静强度能够满足相关标准要求。
关键词 :不锈钢车体 ;仿真分析 ;激光焊接 ;静强度
中图分类号 :TG 457
抗拉 强度/MPa
510~620 510~620 510~620 510~620 510~620 510~620 510~620 510~620
最低剪切 拉力/kN
6 12 12 17 12 17 12 17
梁单元剪切力 =(焊缝长度 /30mm)×(30mm 拉伸剪切
力)/ 梁单元数量
(1)
经评价侧墙模拟激光焊的梁单元合成剪切力均小于其
3.2 点焊静强度
不锈钢车体焊点静强度可根据 BS EN 15085-3 中焊点的 最小剪切力与金属板的强度、板厚及焊核直径的关系来评价。 按照静强度载荷工况,进行整体有限元分析计算,从得到的 结果文件中提取各个工况下,焊点模拟梁单元轴向的两个剪 切力 SFy 和 SFz,并计算出合成剪切拉力 S 合,合成剪切拉力 S合 SFy2 SFz2 [5] ;再根据 BS EN 15085-3 所提供的电阻点 焊钢接头的最低剪切拉力表,按照不同金属强度、不同板厚 和焊核直径所对应的最低剪切拉力进行对比评价 [6]。偏安全考 虑,不同板厚和焊核直径选取较低的等级计算原则,本车各部 位点焊最低剪切拉力见表 3。经评价,车体焊点的合成剪切力 均小于其许用剪切力,其中,AW3 状态下,800 kN 纵向压缩 工况各部件最大的前 5 个焊点的计算结果见表 4。
矿用汽车车架建模与结构强度分析
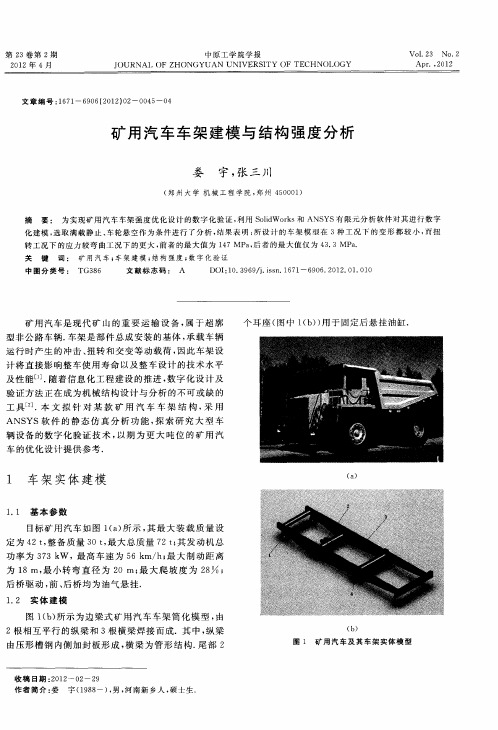
21 0 2年 4月
中原 工 学 院 学 报
J OURNAI OF Z ONGYUAN H UNI VERS TY I OF TECHNOI OGY
Vo . 3 No 2 12 .
Apr 201 ., 2
文 章 编 号 : 6 1—6 0 2 1 ) 2 0 4 —0 17 9 6( 0 2 0 — 0 5 4
收 稿 日期 :0 2 2 9 2 1 ~0 —2
作者简 介 : 娄 字 (9 8 ) 男 , 南 新 乡人 , 士 生 18一 , 河 硕
中原 工 学 院 学报
21 0 2年
第 2 3卷
为 方便 求 解 , 分析 中忽 略焊 接 等 因 素. 型 中 , 在 模
车 架 中梁与后 桥 上 的 A形 架 的前端 连接 ( 1 图 b中 2 ; )
图 1 b 所示 为 边梁式 矿 用 汽 车车 架简 化 模 型 , () 由 2根 相互 平行 的纵 梁 和 3根 横梁 焊接 而成 .其 中 , 梁 纵 由压形槽 钢 内侧 加封 板形 成 , 梁 为管 形 结 构. 横 尾部 2
( b)
图 1 矿 用 汽 车及 其 车 架 实体 模 型
根 据 车 架 结 构 特 点 及 其 受 载 后 的 变 形 特 性 , 用 采 S) I 9 离 散有 限元模 型 , 车车 架 共 有 1 80 2个 ( D 5 I 整 0 8
矿用 汽 车是 现代 矿 山 的重要 运 输 设 备 , 于超 廓 属 型非 公路 车 辆. 架是 部件 总成 安装 的基 体 , 车 承载 车辆
运行 时 产生 的 冲击 、 转 和交变 等 动载荷 , 扭 因此车 架设
个耳 座 ( 中 1 b ) 图 ( ) 用于 固定后 悬 挂油缸 .
基于Solidworks Simulation的悬臂吊强度分析
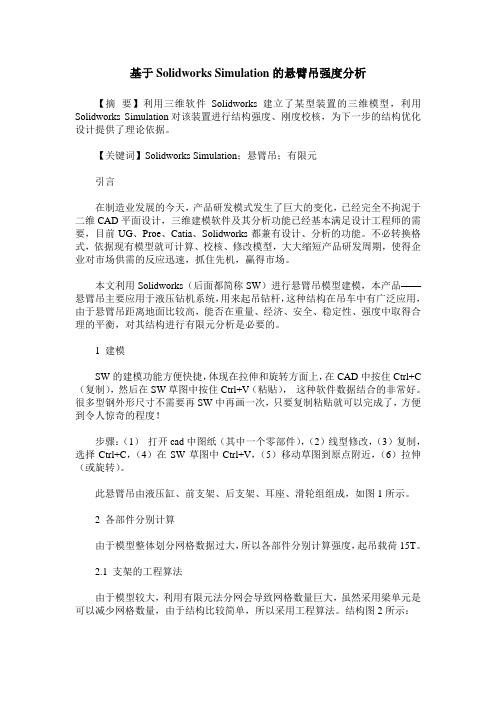
基于Solidworks Simulation的悬臂吊强度分析【摘要】利用三维软件Solidworks建立了某型装置的三维模型,利用Solidworks Simulation对该装置进行结构强度、刚度校核,为下一步的结构优化设计提供了理论依据。
【关键词】Solidworks Simulation;悬臂吊;有限元引言在制造业发展的今天,产品研发模式发生了巨大的变化,已经完全不拘泥于二维CAD平面设计,三维建模软件及其分析功能已经基本满足设计工程师的需要,目前UG、Proe、Catia、Solidworks都兼有设计、分析的功能。
不必转换格式,依据现有模型就可计算、校核、修改模型,大大缩短产品研发周期,使得企业对市场供需的反应迅速,抓住先机,赢得市场。
本文利用Solidworks(后面都简称SW)进行悬臂吊模型建模,本产品——悬臂吊主要应用于液压钻机系统,用来起吊钻杆,这种结构在吊车中有广泛应用,由于悬臂吊距离地面比较高,能否在重量、经济、安全、稳定性、强度中取得合理的平衡,对其结构进行有限元分析是必要的。
1 建模SW的建模功能方便快捷,体现在拉伸和旋转方面上,在CAD中按住Ctrl+C (复制),然后在SW草图中按住Ctrl+V(粘贴),这种软件数据结合的非常好。
很多型钢外形尺寸不需要再SW中再画一次,只要复制粘贴就可以完成了,方便到令人惊奇的程度!步骤:(1)打开cad中图纸(其中一个零部件),(2)线型修改,(3)复制,选择Ctrl+C,(4)在SW草图中Ctrl+V,(5)移动草图到原点附近,(6)拉伸(或旋转)。
此悬臂吊由液压缸、前支架、后支架、耳座、滑轮组组成,如图1所示。
2 各部件分别计算由于模型整体划分网格数据过大,所以各部件分别计算强度,起吊载荷15T。
2.1 支架的工程算法由于模型较大,利用有限元法分网会导致网格数量巨大,虽然采用梁单元是可以减少网格数量,由于结构比较简单,所以采用工程算法。
半承载式大客车车身有限元建模及强度分析
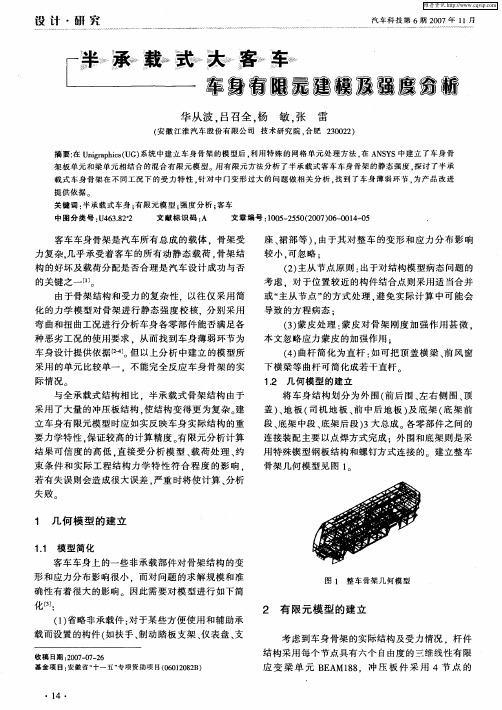
客车 车身骨 架是汽 车所有 总成 的载 体 .骨架 受 力 复 杂. 几乎 承受 着客 车的所 有 动静 态 载荷 , 骨架 结 构 的好 坏及 载荷分 配是 否合理 是汽 车设 计成 功与 否 的关键 之一 [。 1 I 由于骨 架结 构和 受力 的复杂 性 .以往 仅 采用 简 化 的 力学模 型对 骨架进 行 静态 强度 校 核.分别 采 用 弯 曲和扭 曲工 况进行 分析 车身 各零部 件 能否 满足各
按 照相 邻 线 共 点 。 邻 面 共 线 的要 求 . 板 梁 相 在
结 合 处 , 梁 中线 和板 中 面 的接 触 点 强 制 生 成 一 取 个 关 键 点 。这 样 骨 架 有 限元 模 型 在 受 力 的时 候 会 通 过 相 关 的点 、 、 线 面传 递 各 种 载 荷 。
种 恶劣 工况 的使用要 求 .从 而 找到 车身 薄弱 环节 为
车 身设 计提供 依据 ] 但 以上 分析 中建 立 的模 型所 。 采 用 的单元 比较单一 .不 能完 全反应 车 身骨 架 的实 际情 况 。 与全 承载式 结构相 比 .半 承 载式 骨架 结构 由于
下 横梁 等 曲杆 可简 化成若 干直杆
2 有 限 元 模 型 的 建 立
考虑 到车 身骨 架的实 际结 构及 受力情 况 .杆件 结 构采用 每个 节点 具有六个 自由度 的 三维线性 有 限 应 变 梁 单 元 B A 8 .冲 压 板 件 采 用 4节 点 的 E M18
・
1 ・ 4
维普资讯
有限元计算与强度分析-(二)几何建模及网格划分
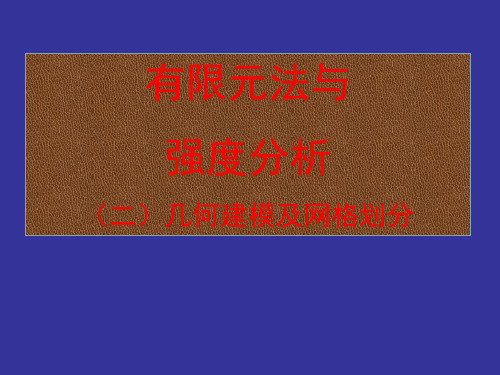
1.2 ANSYS Workbench建模技术
1.2.10 激活新平面
• New Sketch :在激活平面上新建草图。 • 新草图放在树形目录中,且在相关平面的下方。 • 通过树形目录或下拉列表操作草图(激活)。 • 注意:下拉列表仅显示以当前激活平面为参照的草图(示例如下)。
激活XY平面
下拉列表中仅显示XY平面内 的草图
关注于一个点
“Sphere of Influence” (红色 显示) 已经定义。球体内所关 注实体的单元大小是给定的平 均单元大小。
关注于两个面
1.4 划分网格
1.4.2.2 局部网格控制
刷新单元)。 • 需要更新:数据一改变单元的输出也要相应的更新。 • 最新的。 • 发生输入变动: 单元是局部时新的,但上行数据发生变
化也可能导致其发生改变。
1.2 ANSYS Workbench建模技术
1.2.1 DesignModeler概述 – DesignModeler (DM) 是ANSYS Workbench的一个组成, 类似CAD的建模器,具有参数建模能力:
1.1.1启动Workbench
• 两种方式启动Workbench:
– 从windows开始菜单启动:
– 从其支持的CAD系统中启动
1.1 ANSYS Workbench概述
1.1.2Workbench的图形用户界面
• Workbench 的图形用户界面主要分成工具箱和项目概图 两部分:
工具箱
项目概图
1.4 划分网格
1.4.2.1 网格划分方法
• Sweep(扫掠划分):
– 扫掠划分单元(六面体,也可能是楔形体),否则就是四面体。 – 在mesh上点击鼠标右键选择Show Sweepable Bodies。 – Type :扫掠方向上的划分数目或单元大小。 – Sweep Bias Type: 扫掠方向上的间隔比例 – Src/Trg Selection:
机械结构的有限元分析

机械结构的有限元分析引言在现代工程设计与制造领域中,机械结构的设计是不可或缺的。
为了保证机械结构的稳定性、安全性以及耐用性,工程师们经常需要进行有限元分析。
有限元分析是一种利用计算机模拟材料力学行为的方法,能够帮助工程师们预测机械结构在实际工作条件下的性能。
第一部分:有限元分析的基本原理和步骤有限元分析的基本原理是将机械结构离散成许多小的有限元,然后通过求解有限元间的相互作用来模拟整个结构的行为。
这种离散的方法使得计算变得可行,同时还能提供关于结构应力分布、变形情况以及破坏点等有用信息。
有限元分析的步骤可以概括为以下几个方面:1. 建模:将机械结构根据实际几何形状、材料属性以及约束条件等进行建模。
这一步通常需要使用CAD软件来帮助创建结构模型。
2. 离散化:将机械结构划分成小的有限元,并为每个有限元分配材料属性和初始条件。
这一步可以通过网格生成工具来实现。
3. 定义边界条件:根据实际工作条件定义结构的边界条件,如约束和加载情况。
这些边界条件将影响结构的响应。
4. 计算求解:使用数值方法(如有限元算法)对有限元模型进行求解,得到结构的应力、变形等信息。
5. 分析结果:根据求解结果进行后处理分析,如应力云图、变形图以及破坏点的预测等。
第二部分:有限元分析在机械结构设计中的应用有限元分析在机械结构设计中具有广泛的应用。
下面将针对几个典型的应用领域进行介绍。
1. 振动分析在机械结构设计中,振动是一个重要的考虑因素。
通过有限元分析,可以预测机械结构在不同频率下的振动响应,并找到导致振动问题的原因。
进一步优化结构几何形状、选择合适的材料以及调整约束条件等,可以有效减少振动问题。
2. 疲劳分析机械结构在长期工作中容易受到疲劳损伤。
通过有限元分析可以模拟结构在不同工作条件下的疲劳寿命,并预测可能出现的疲劳破坏位置。
这有助于进行结构的寿命评估和优化设计。
3. 强度分析机械结构的强度是制定设计决策的重要因素。
通过有限元分析,可以预测结构在不同加载情况下的应力分布,并评估结构是否满足强度要求。
ug_强度分析
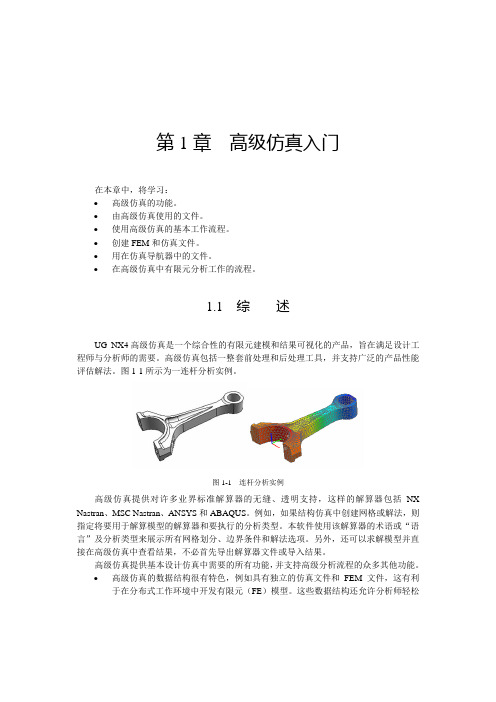
第1章高级仿真入门在本章中,将学习:•高级仿真的功能。
•由高级仿真使用的文件。
•使用高级仿真的基本工作流程。
•创建FEM和仿真文件。
•用在仿真导航器中的文件。
•在高级仿真中有限元分析工作的流程。
1.1综述UG NX4高级仿真是一个综合性的有限元建模和结果可视化的产品,旨在满足设计工程师与分析师的需要。
高级仿真包括一整套前处理和后处理工具,并支持广泛的产品性能评估解法。
图1-1所示为一连杆分析实例。
图1-1 连杆分析实例高级仿真提供对许多业界标准解算器的无缝、透明支持,这样的解算器包括NX Nastran、MSC Nastran、ANSYS和ABAQUS。
例如,如果结构仿真中创建网格或解法,则指定将要用于解算模型的解算器和要执行的分析类型。
本软件使用该解算器的术语或“语言”及分析类型来展示所有网格划分、边界条件和解法选项。
另外,还可以求解模型并直接在高级仿真中查看结果,不必首先导出解算器文件或导入结果。
高级仿真提供基本设计仿真中需要的所有功能,并支持高级分析流程的众多其他功能。
•高级仿真的数据结构很有特色,例如具有独立的仿真文件和FEM 文件,这有利于在分布式工作环境中开发有限元(FE)模型。
这些数据结构还允许分析师轻松UG NX4高级仿真培训教程2地共享FE 数据去执行多种类型分析。
•高级仿真提供世界级的网格划分功能。
本软件旨在使用经济的单元计数来产生高质量网格。
结构仿真支持完整的单元类型(1D、2D和3D)。
另外,结构级仿真使分析师能够控制特定网格公差。
例如,这些公差控制着软件如何对复杂几何体(例如圆角)划分网格。
•高级仿真包括许多几何体简化工具,使分析师能够根据其分析需要来量身定制CAD几何体。
例如,分析师可以使用这些工具提高其网格的整体质量,方法是消除有问题的几何体(例如微小的边)。
•高级仿真中专门包含有新的NX传热解算器和NX流体解算器。
➢NX传热解算器是一种完全集成的有限差分解算器。
它允许热工程师预测承受热载荷系统中的热流和温度。
复合材料加筋壁板结构强度分析方法研究

Technological Innovation18《华东科技》复合材料加筋壁板结构强度分析方法研究宋波涛,付友波,白艳洁(航空工业西安飞机工业(集团)有限责任公司,陕西 西安 710089)摘要:复合材料设计技术日益成熟,其在航空产品上的应用越来越多,更多的主承力结构开始选用复合材料,其强度设计至关重要,关系飞机安全。
本文以某飞机复合材料机身壁板为例,详细介绍了加筋壁板有限元建模及强度分析方法,给出了详细的校核公式及分析过程,可用于指导飞机强度设计及校核工作。
关键词:复合材料;强度校核;加筋壁板;稳定性近年来高性能增强纤维的先进复合材料在航空领域得到了快速发展。
先进复合材料具有比强度、比模量高,性能可设计和易于整体成形等诸多优异特性,不仅可实现结构减重,并能够明显改善飞机气动弹性特性、降低油耗、减少维修费用从而提高飞机性能,这是其他材料无法或难以实现的。
本文基于飞机复合材料机身壁板为例,介绍了复合材料加筋壁板设计过程中所面临的强度问题,并给出了有限元建模过程及其强度校核分析方法。
1 有限元建模计算 在壁板有限元建模过程中,将蒙皮单元简化为板壳单元,蒙皮单元定义为复合材料单元,材料铺层与实际结构铺层定义一致,将单向带定义为二维各项异性材料,建立材料坐标系,将材料坐标系X 轴定义为0°方向;由于长桁主要承受拉压载荷,建模时将长桁单元简化为一维杆单元,单元横截面积定义为长桁实际截面积,材料属性定义为其实际铺层等效属性。
当长桁缘条与腹板铺层不同时,假设腹板等效弹性模量为E1,截面积为A1,缘条等效弹性模量为E2,截面积为A2,则在长桁单元属性定义中,要求长桁单元截面拉压刚度保持不变,一般定义长桁弹性模量为腹板弹性模量E1,则其等效面积为:12211E A E A E A e += 复合材料结构设计中,一般为了降低结构重量,提高经济效益,蒙皮铺层及长桁铺层会不断变化,这导致建模过程比较复杂,需要对单元属性进行分段定义。
- 1、下载文档前请自行甄别文档内容的完整性,平台不提供额外的编辑、内容补充、找答案等附加服务。
- 2、"仅部分预览"的文档,不可在线预览部分如存在完整性等问题,可反馈申请退款(可完整预览的文档不适用该条件!)。
- 3、如文档侵犯您的权益,请联系客服反馈,我们会尽快为您处理(人工客服工作时间:9:00-18:30)。
1.建模及强度分析目的
1)正确将三维CAD图导入分析软件;
2)修改不必要的细节,使网格剖分更均匀;
3)根据计算机的计算能力,选取适当的单元剖分网格;
4)正确施加载荷和边界条件;
5)完成强度分析;
2.模型参数
1)平衡块参数
2)曲轴材料
3)曲轴载荷--连杆对曲轴的作用力
4)载荷及其作用方向,如图
5)曲轴上载荷的分布
沿曲柄销轴线为抛物线分布 沿轴颈径向为余弦分布
3.具体操作过程:
1)首先将三维CAD 图导入ANSYS 分析软件,进行相关参数的设置;
2)其次进行网格的划分,由于电脑配置问题,本次划分的网格较为稀疏,划分
后网格数量为27009个;
3)在模型上加相应质量块,目的是用来平衡模型,降低模型旋转惯性,根据需求,本次施加了12个质量为10.44kg 的质量块;
)
11(1692
2x L LR Q q c y -=)2/3cos(θθx
x q q =
6060≤≤-θ
4)对模型进行静态分析,根据计算结果找出最大应力位置,与考核标准进行对比分析;
5)进行模态分析。
4.静力分析结果
1)静力分析整体如图:
2)最大应力处于主轴颈处,如图:
3)其他主轴颈处应力如图:
5.模态分析结果
1)曲轴的前6阶模态的固有频率
2)前6阶模态振型如图
(a)一阶模态振型
(b)二阶模态振型
(c)三阶模态振型
(d)四阶模态振型
(e)五阶模态振型
(f)六阶模态振型
6.总结
本次实验综合运用了CAD与ANSYS软件对曲轴进行了静力分析与模态分析。
通过静力分析与计算,得出曲轴的许用应力最大值;通过模态分析计算求得了
曲轴的自由振动模态的固有频率和振型,前6阶模态的固有频率从 146.13到587.66,随着频率的增大,通过曲轴的模态振型图可知,在曲轴的振动过程中,曲轴的变形越来越大。
预计在变形达到一定程度时,曲轴将出现破坏现象。
同时,通过模态分析,得到曲轴变形最大的位置和最可能出现破坏的地方,为以
后的优化设计奠定了基础。
建模及强度分析报告
2016.10。