CAE-车轮轮辋强度强度分析报告
车轮CAE分析
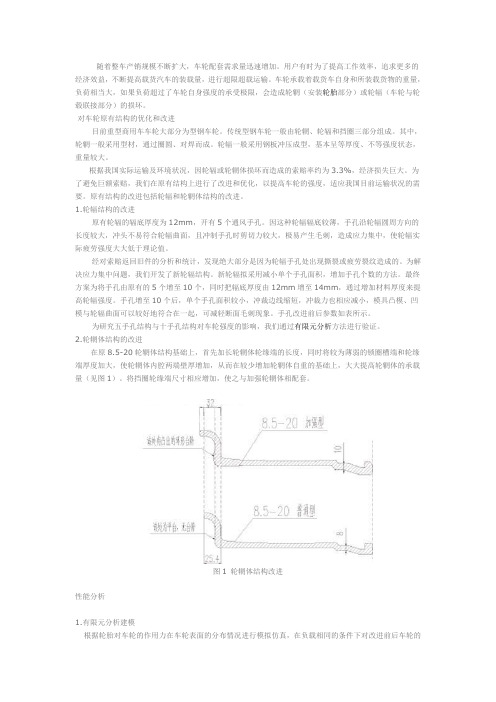
随着整车产销规模不断扩大,车轮配套需求量迅速增加。
用户有时为了提高工作效率,追求更多的经济效益,不断提高载货汽车的装载量,进行超限超载运输。
车轮承载着载货车自身和所装载货物的重量,负荷相当大,如果负荷超过了车轮自身强度的承受极限,会造成轮辋(安装轮胎部分)或轮辐(车轮与轮毂联接部分)的损坏。
对车轮原有结构的优化和改进目前重型商用车车轮大部分为型钢车轮。
传统型钢车轮一般由轮辋、轮辐和挡圈三部分组成。
其中,轮辋一般采用型材,通过圈圆、对焊而成。
轮辐一般采用钢板冲压成型,基本呈等厚度、不等强度状态,重量较大。
根据我国实际运输及环境状况,因轮辐或轮辋体损坏而造成的索赔率约为3.3%,经济损失巨大。
为了避免巨额索赔,我们在原有结构上进行了改进和优化,以提高车轮的强度,适应我国目前运输状况的需要。
原有结构的改进包括轮辐和轮辋体结构的改进。
1.轮辐结构的改进原有轮辐的辐底厚度为12mm,开有5个通风手孔。
因这种轮辐辐底较薄,手孔沿轮辐圆周方向的长度较大,冲头不易符合轮辐曲面,且冲制手孔时剪切力较大,极易产生毛刺,造成应力集中,使轮辐实际疲劳强度大大低于理论值。
经对索赔返回旧件的分析和统计,发现绝大部分是因为轮辐手孔处出现撕裂或疲劳裂纹造成的。
为解决应力集中问题,我们开发了新轮辐结构。
新轮辐拟采用减小单个手孔面积,增加手孔个数的方法。
最终方案为将手孔由原有的5个增至10个,同时把辐底厚度由12mm增至14mm,通过增加材料厚度来提高轮辐强度。
手孔增至10个后,单个手孔面积较小,冲裁边线缩短,冲裁力也相应减小,模具凸模、凹模与轮辐曲面可以较好地符合在一起,可减轻断面毛刺现象。
手孔改进前后参数如表所示。
为研究五手孔结构与十手孔结构对车轮强度的影响,我们通过有限元分析方法进行验证。
2.轮辋体结构的改进在原8.5-20轮辋体结构基础上,首先加长轮辋体轮缘端的长度,同时将较为薄弱的锁圈槽端和轮缘端厚度加大,使轮辋体内腔两端壁厚增加,从而在较少增加轮辋体自重的基础上,大大提高轮辋体的承载量(见图1)。
基于CAE的QX1060车轮结构性能分析

利 用三维 C D软件 U i rp i A nG a hc建立 车轮零 部 件 的实 体, 并进行 装 配得到 车轮 轮 圈如 图 I 所示 。
驶 安全 性 、 纵稳 定性 、 坐舒 适性 、 油经济 性等 诸 操 乘 燃 多方 面有重要 的作 用 ¨ 。传 统 的设 计 方法 是 以经 验 J
型, 轮辋 宽度 , 轮辋 标定 直 径, 轮辋 高度 等 。轮 辐 主要
是 确 定 其 厚 度 。 参 考 相 关 资料 后 J 通 过 参 照 对 比 , ,
图 2 轮 圈 有 限 元 模 型
图 3 车 轮 轮 圈 约 束
确定 轮辋代号 为 l 55 6— . F SC 轮 辐厚 度 为 6 D 。 mm。
( )胎压载荷增加后 , 2 轮辋承受的压力增加 , 变 形加大, 存在一定 的线性关系; 如图 l 0所示 ; 胎压载 荷对 轮辋 及轮辐 的影 响较小 。
所示 。径向力的分布规律近似余弦载荷: ) 2 0 c s =10 0 ox () 2 加载 时 , 以压强 的形 式 加 在轮 辋 的受力 面上 , 可 近似 模拟径 向载 荷 。如 图 1 示 。 2所
压传 递 到轮辋 上 。由前 面的计算 可知 : 胎压 载荷 对 车 轮 的影 响较 小 , 以 只研 究 通 过 胎 圈 传 递 的力 的 影 所
响。汽 车满载 时 , 由于 轮 胎 的变 形 , 向载 荷 分 布在 径 轮胎 接地 印迹上 , 约作用 在+ 5 的范 围 J 如 图 1 大 4。 , 1
=
来, 随着 计算 机技 术 的快 速 发展 , 成 了 以实 体 造 型 形 设计 、 构性 能分 析 、 拟 仿 真 加 工 相 结合 的设 计 方 结 模
基于CAE的QXl060车轮结构性能分析

基于CAE的QXl060车轮结构性能分析第一章:绪论(300字)QXl060车轮是一种重要的汽车零部件,它的性能直接关系到汽车行驶的安全和舒适性。
由于车轮在行驶过程中需要承受各种力的作用,因此必须对其结构进行全面的性能分析,以保证其良好的使用效果。
本文采用有限元仿真分析技术,通过建立QXl060车轮的CAE模型,对其结构的静力学、动力学和疲劳寿命等性能进行分析,为该车轮的设计和使用提供技术支撑。
第二章:QXl060车轮的结构分析(400字)本章主要介绍QXl060车轮的结构特点和材料选择。
在了解车轮的结构之后,本文采用有限元建模和仿真技术,对车轮进行了静力学和动力学分析。
静力学分析主要是对车轮的静态载荷进行计算和分析,以判断车轮在静态状态下的承载能力和变形情况。
动力学分析主要是对车轮的动态载荷进行计算和分析,以判断车轮在行驶状态下的受力情况和振动响应。
第三章:QXl060车轮的疲劳寿命分析(400字)本章主要介绍QXl060车轮的疲劳寿命分析。
通过有限元仿真技术,本文对车轮的疲劳寿命进行了预测和评估。
首先,本文采用应力-应变曲线来描述车轮的应力状态,然后采用疲劳分析方法来计算车轮的疲劳损伤程度和寿命。
最后,本文采用统计学方法来确定车轮的寿命分布,从而为车辆的使用和维护提供重要的参考依据。
第四章:QXl060车轮的优化设计(300字)本章主要介绍QXl060车轮的优化设计。
通过对QXl060车轮结构的分析和疲劳寿命预测,本文确定了车轮结构的性能缺陷和优化方向。
基于此,本文提出了一系列优化措施,从车轮的材料、结构和加工工艺三个方面出发,对车轮的性能进行了改进和增强。
通过有限元仿真技术,本文对优化后的车轮进行了分析和验证,证明了优化设计的效果和优越性。
第五章:结论(200字)通过本文的研究,我们可以发现,QXl060车轮的结构特点和材料选择对其性能具有重要的影响。
通过有限元仿真技术,我们可以对车轮的静力学、动力学和疲劳寿命等性能进行准确的预测和分析。
关于CAE技术在自卸车车轮轻量化设计中的应用
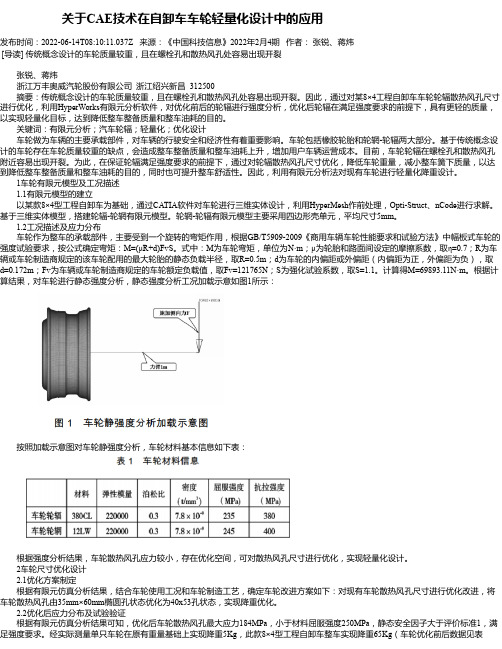
关于CAE技术在自卸车车轮轻量化设计中的应用发布时间:2022-06-14T08:10:11.037Z 来源:《中国科技信息》2022年2月4期作者:张锐、蒋炜[导读] 传统概念设计的车轮质量较重,且在螺栓孔和散热风孔处容易出现开裂张锐、蒋炜浙江万丰奥威汽轮股份有限公司浙江绍兴新昌 312500摘要:传统概念设计的车轮质量较重,且在螺栓孔和散热风孔处容易出现开裂。
因此,通过对某8×4工程自卸车车轮轮辐散热风孔尺寸进行优化,利用HyperWorks有限元分析软件,对优化前后的轮辐进行强度分析,优化后轮辐在满足强度要求的前提下,具有更轻的质量,以实现轻量化目标,达到降低整车整备质量和整车油耗的目的。
关键词:有限元分析;汽车轮辐;轻量化;优化设计车轮做为车辆的主要承载部件,对车辆的行驶安全和经济性有着重要影响。
车轮包括橡胶轮胎和轮辋-轮辐两大部分。
基于传统概念设计的车轮存在车轮质量较重的缺点,会造成整车整备质量和整车油耗上升,增加用户车辆运营成本。
目前,车轮轮辐在螺栓孔和散热风孔附近容易出现开裂。
为此,在保证轮辐满足强度要求的前提下,通过对轮辐散热风孔尺寸优化,降低车轮重量,减小整车簧下质量,以达到降低整车整备质量和整车油耗的目的,同时也可提升整车舒适性。
因此,利用有限元分析法对现有车轮进行轻量化降重设计。
1车轮有限元模型及工况描述1.1有限元模型的建立以某款8×4型工程自卸车为基础,通过CATIA软件对车轮进行三维实体设计,利用HyperMesh作前处理,Opti-Struct、nCode进行求解。
基于三维实体模型,搭建轮辐-轮辋有限元模型。
轮辋-轮辐有限元模型主要采用四边形壳单元,平均尺寸5mm。
1.2工况描述及应力分布车轮作为整车的承载部件,主要受到一个旋转的弯矩作用,根据GB/T5909-2009《商用车辆车轮性能要求和试验方法》中幅板式车轮的强度试验要求,按公式确定弯矩:M=(μR+d)FvS。
轮辋性能测试实验报告(3篇)

第1篇一、实验目的1. 了解轮辋的基本结构及工作原理;2. 研究轮辋在不同工况下的力学性能;3. 评估轮辋在实际应用中的可靠性和安全性;4. 为轮辋的设计与制造提供实验依据。
二、实验原理轮辋是连接轮胎与车轴的重要部件,其性能直接影响到车辆的行驶安全。
本实验通过模拟实际工况,对轮辋进行力学性能测试,包括拉伸、弯曲、扭转等试验,以评估轮辋的力学性能。
三、实验材料与设备1. 实验材料:某品牌轮辋样品;2. 实验设备:万能试验机、测力传感器、千分尺、卡尺等。
四、实验方法与步骤1. 样品准备:选取具有代表性的轮辋样品,对其表面进行打磨、清洗,确保样品表面平整、无损伤;2. 样品尺寸测量:使用千分尺和卡尺测量轮辋样品的直径、宽度、厚度等尺寸参数;3. 拉伸试验:将轮辋样品固定在万能试验机上,进行拉伸试验,记录最大拉伸载荷和断裂伸长率;4. 弯曲试验:将轮辋样品固定在万能试验机上,进行弯曲试验,记录最大弯曲载荷和弯曲角度;5. 扭转试验:将轮辋样品固定在万能试验机上,进行扭转试验,记录最大扭转载荷和扭转角度;6. 数据处理与分析:对实验数据进行统计分析,得出轮辋在不同工况下的力学性能指标。
五、实验结果与分析1. 拉伸试验结果:轮辋样品的最大拉伸载荷为XXX N,断裂伸长率为XXX %。
结果表明,该轮辋具有良好的抗拉伸性能,满足实际应用需求;2. 弯曲试验结果:轮辋样品的最大弯曲载荷为XXX N,弯曲角度为XXX °。
结果表明,该轮辋具有良好的抗弯曲性能,能够承受一定的弯曲载荷;3. 扭转试验结果:轮辋样品的最大扭转载荷为XXX N,扭转角度为XXX °。
结果表明,该轮辋具有良好的抗扭转性能,能够承受一定的扭转载荷。
六、实验结论1. 通过本实验,验证了该轮辋具有良好的抗拉伸、抗弯曲和抗扭转性能,满足实际应用需求;2. 实验结果为轮辋的设计与制造提供了实验依据,有助于提高轮辋的可靠性和安全性;3. 建议在轮辋设计和制造过程中,充分考虑实际工况,优化轮辋结构,提高轮辋性能。
CRH2型动车组轮轨接触计算及车轮强度CAE分析
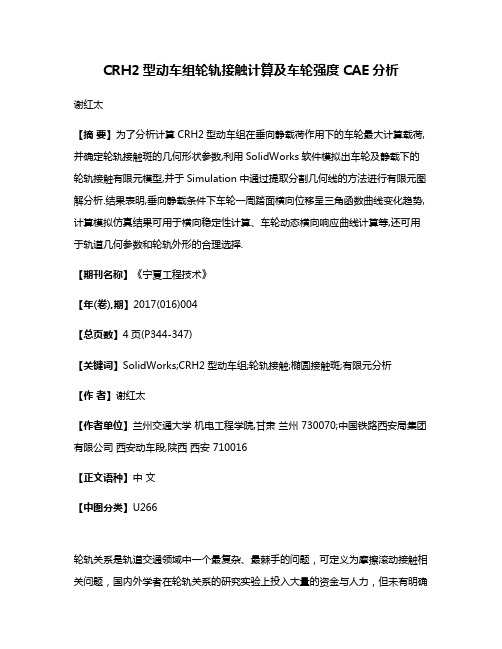
CRH2型动车组轮轨接触计算及车轮强度CAE分析谢红太【摘要】为了分析计算CRH2型动车组在垂向静载荷作用下的车轮最大计算载荷,并确定轮轨接触斑的几何形状参数,利用SolidWorks软件模拟出车轮及静载下的轮轨接触有限元模型,并于Simulation中通过提取分割几何线的方法进行有限元图解分析.结果表明,垂向静载条件下车轮一周踏面横向位移呈三角函数曲线变化趋势,计算模拟仿真结果可用于横向稳定性计算、车轮动态横向响应曲线计算等,还可用于轨道几何参数和轮轨外形的合理选择.【期刊名称】《宁夏工程技术》【年(卷),期】2017(016)004【总页数】4页(P344-347)【关键词】SolidWorks;CRH2型动车组;轮轨接触;椭圆接触斑;有限元分析【作者】谢红太【作者单位】兰州交通大学机电工程学院,甘肃兰州 730070;中国铁路西安局集团有限公司西安动车段,陕西西安 710016【正文语种】中文【中图分类】U266轮轨关系是轨道交通领域中一个最复杂、最棘手的问题,可定义为摩擦滚动接触相关问题,国内外学者在轮轨关系的研究实验上投入大量的资金与人力,但未有明确的定论,这与轮轨接触应力分析及车轮结构强度模拟仿真条件苛刻以及外界影响因素复杂繁多有关[1—3]。
随着有限元技术的兴起,很多现实中投入资金量大、计算复杂的问题可利用有限元技术加以解决。
SolidWorks Simulation有限元技术被广泛用于计算机辅助制造中。
目前轨道交通领域中对重载下车轮辐板、踏面、轮缘表面应力变化情况及分布规律普遍采用寻找粘贴应变斑的方法来讨论[4—5],整个实验分析过程极为复杂,同时也得不出定性结论,只是限定大范围内的描述性推测。
鉴于此,本文利用SolidWorks公司推出的有限元分析模块Simulation对车轮的受力情况给出一种简化分析模型与应力分布表述。
1 轮轨接触分析1.1CRH2型动车组LMA型踏面随着高速动车组的投运,对车轮轮型和精度都有了更高的要求,只有通过数控改造才能更好地满足高速动车组车轮加工的需要,其中最为困难和重要的是与钢轨接触的踏面形状控制。
《2024年铝合金轮毂的有限元分析》范文

《铝合金轮毂的有限元分析》篇一一、引言铝合金轮毂是现代汽车工业中广泛应用的重要部件之一。
随着汽车行业的飞速发展,对于车辆轻量化、耐用性和安全性的要求也日益提升。
因此,铝合金轮毂以其优良的物理性能和经济性得到了广大制造商的青睐。
然而,在实际使用中,铝合金轮毂的设计和生产需要充分考虑其复杂的工作环境和各种潜在风险。
因此,采用有限元分析(FEA)对铝合金轮毂进行性能分析和优化显得尤为重要。
二、铝合金轮毂的有限元模型建立1. 材料属性定义在有限元分析中,首先需要定义铝合金轮毂的材料属性。
这包括弹性模量、屈服强度、抗拉强度等关键参数。
这些参数将直接影响模型的力学性能和应力分布。
2. 几何模型建立根据铝合金轮毂的实际几何形状和尺寸,建立精确的几何模型。
在建模过程中,应充分考虑轮毂的复杂结构和细节特征,以确保分析的准确性。
3. 网格划分将几何模型划分为适当的网格是有限元分析的关键步骤。
网格的划分应考虑到计算精度和计算效率的平衡,确保在关键区域有足够的网格密度。
三、铝合金轮毂的有限元分析1. 载荷和边界条件设置在有限元分析中,需要设置载荷和边界条件。
载荷包括车辆行驶过程中的惯性力、摩擦力等;边界条件则涉及到轮毂与轮胎的连接方式、约束等。
这些条件的设置将直接影响分析结果的准确性。
2. 应力分析通过有限元分析,可以获得铝合金轮毂在各种工况下的应力分布情况。
这包括静态应力、动态应力以及交变应力等。
分析结果将有助于评估轮毂的强度、刚度和耐久性。
3. 模态分析模态分析可以获取铝合金轮毂的振动特性,如各阶模态频率和振型。
这对于评估轮毂在复杂工作环境下的动态性能具有重要意义。
四、结果与讨论通过对铝合金轮毂的有限元分析,可以得到以下结论:1. 铝合金轮毂在各种工况下的应力分布情况,为优化设计提供依据;2. 模态分析结果有助于了解轮毂的动态性能,为降低振动和噪声提供参考;3. 通过对比不同设计方案的有限元分析结果,可以找到最优的设计方案,提高轮毂的性能和寿命;4. 有限元分析还可以用于评估铝合金轮毂在复杂工作环境中的潜在风险,为生产制造提供有力支持。
汽车车轮的结构强度分析
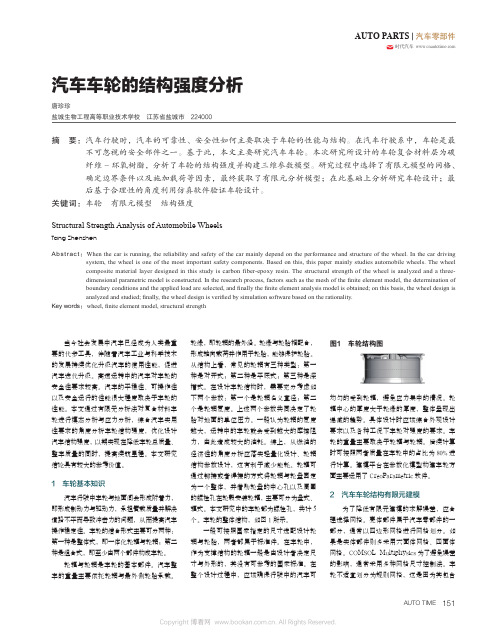
AUTO PARTS | 汽车零部件时代汽车 汽车车轮的结构强度分析当今社会发展中汽车已经成为人类最重要的代步工具,伴随着汽车工业与科学技术的发展持续优化升级汽车的使用性能,促进汽车迭代升级。
高速运转中的汽车对车轮的安全性要求较高。
汽车的平稳性、可操作性以及安全运行的性能很大程度取决于车轮的性能。
本文通过有限元分析法对复合材料车轮进行模态分析与应力分析,综合汽车实用性要求的角度分析车轮结构强度,优化设计汽车结构强度,以期实现在降低车轮总质量、整车质量的同时,提高续航里程。
本文研究结论具有较大的参考价值。
1 车轮基本知识汽车行驶中车轮与地面间会形成附着力,即形成制动力与驱动力,承担簧载质量并解决道路不平而导致冲击力的问题,从而提高汽车操作稳定性。
车轮的结合形式主要可分两种:第一种是整体式,即一体化轮辐与轮辋;第二种是组合式,即至少由两个部件构成车轮。
轮辐与轮辋是车轮的基本部件。
汽车整车的重量主要依托轮辋与最外侧轮胎承载。
轮缘,即轮辋的最外沿。
轮缘与轮胎相配合,形成轴向载荷并作用于轮胎,能够保护轮胎。
从结构上看,常见的轮辋有三种类型:第一种是对开式;第二种是平底式;第三种是深槽式。
在设计车轮结构时,需要充分考虑如下两个参数:第一个是轮辋名义直径;第二个是轮辋宽度。
上述两个参数共同决定了轮胎对地面的单位压力。
一般认为轮辋的宽度越大,运转中的车轮就会受到越大的摩擦阻力,由此造成较大的油耗。
综上,从燃油的经济性的角度分析应落实轻量化设计、轮辋结构参数设计,这有利于减少能耗。
轮辐可通过铆接或者焊接的方式将轮辋与轮盘固定为一个整体,并借助轮盘的中心孔以及周围的螺栓孔在轮毂安装轮辐,主要可分为盘式、辐式。
本文研究中的车轮都为螺栓孔,共计5个。
车轮的整体结构,如图1所示。
一般可按照国家指定的尺寸选配设计轮辋与轮胎,两者都属于标准件。
在车轮中,作为支撑结构的轮辐一般是由设计者决定尺寸与外形的,其没有可参考的国家标准。
CAE分析报告(2024)
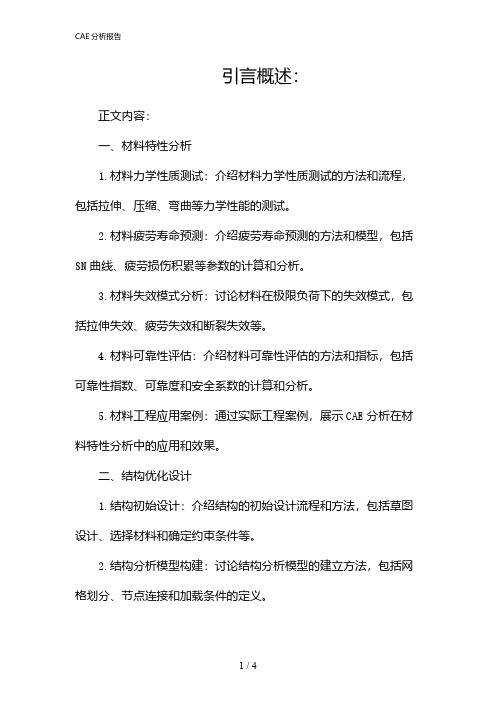
引言概述:正文内容:一、材料特性分析1.材料力学性质测试:介绍材料力学性质测试的方法和流程,包括拉伸、压缩、弯曲等力学性能的测试。
2.材料疲劳寿命预测:介绍疲劳寿命预测的方法和模型,包括SN曲线、疲劳损伤积累等参数的计算和分析。
3.材料失效模式分析:讨论材料在极限负荷下的失效模式,包括拉伸失效、疲劳失效和断裂失效等。
4.材料可靠性评估:介绍材料可靠性评估的方法和指标,包括可靠性指数、可靠度和安全系数的计算和分析。
5.材料工程应用案例:通过实际工程案例,展示CAE分析在材料特性分析中的应用和效果。
二、结构优化设计1.结构初始设计:介绍结构的初始设计流程和方法,包括草图设计、选择材料和确定约束条件等。
2.结构分析模型构建:讨论结构分析模型的建立方法,包括网格划分、节点连接和加载条件的定义。
3.结构优化算法:介绍结构优化算法的原理和分类,包括形状优化、拓扑优化和参数优化等方法。
4.结构优化效果评估:针对不同的优化目标,介绍效果评估指标的选取和考虑因素的分析。
5.结构优化设计案例:通过实际工程案例,展示CAE分析在结构优化设计中的应用和效果。
三、热仿真分析1.热传导分析:介绍热传导分析的原理和计算方法,包括热传导方程和传热边界条件的建立。
2.热应力分析:讨论热应力分析的方法和模型,包括线性热弹性模型和非线性热弹性模型。
3.温度场分布分析:展示CAE分析在温度场分布分析中的应用,包括温度梯度和温度均匀性等指标的计算和评价。
4.热仿真优化设计:介绍热仿真优化设计的原理和流程,包括热网格优化和热传导路径优化等方法。
5.热仿真分析案例:通过实际工程案例,展示CAE分析在热仿真分析中的应用和效果。
四、流体力学分析1.流体流动模拟:介绍流体流动模拟的原理和方法,包括NavierStokes方程和控制方程的求解。
2.流场数值计算:讨论流场数值计算的过程和方法,包括网格划分、边界条件设置和求解器选择等。
3.流场压力分析:分析流体流动中的压力场分布和压力梯度的计算和分析。
轮毂模拟分析报告模板

轮毂模拟分析报告模板一、引言轮毂模拟分析是对车辆轮毂的性能和设计进行评估的一种方法。
通过计算机辅助设计软件,可以对轮毂的结构、强度、刚度以及动力学性能进行模拟和分析。
本报告旨在对轮毂模拟分析的结果进行总结和评述,以提供轮毂设计改进的方向和建议。
二、轮毂结构模拟分析结果1. 结构强度分析:通过有限元分析方法,模拟轮毂在不同载荷条件下的应力和变形情况。
结果显示,在设计载荷范围内,轮毂结构具有足够的强度和刚度,不存在严重的应力集中和变形问题。
2. 质量分析:通过轮毂模拟分析,可以对轮毂的质量进行预测和评估。
分析结果显示,轮毂的质量分布均匀,能够满足车辆的性能和安全要求。
3. 动力学性能分析:通过模拟分析轮毂的滚动、扭转等运动情况,可以评估轮毂对整车动力学性能的影响。
分析结果显示,轮毂具有良好的运动稳定性和响应性,不会对整车的操控性和驾驶感受产生负面影响。
三、轮毂设计改进建议1. 结构优化:根据轮毂模拟分析结果,可以进一步优化轮毂的结构,减少材料使用量。
例如,通过局部加强结构,可以提高轮毂的强度,并同时减轻轮毂的重量。
2. 材料选择:根据模拟分析结果,选择合适的材料可以进一步提高轮毂的性能。
例如,选择高强度材料可以提高轮毂的强度和刚度,同时能够减轻整个车辆的重量。
3. 表面处理:轮毂在使用过程中会受到腐蚀和磨损的影响,因此可以考虑对轮毂表面进行特殊处理,以提高其耐腐蚀性和耐磨性。
四、结论通过轮毂模拟分析,可以对轮毂的结构、性能和设计进行准确评估。
本报告总结了轮毂模拟分析的结果,并提出了轮毂设计改进的建议。
这些建议将有助于提高轮毂的强度、刚度和整车的动力学性能,从而提升整个车辆的性能和安全性。
轮毂强度、刚度仿真分析方法
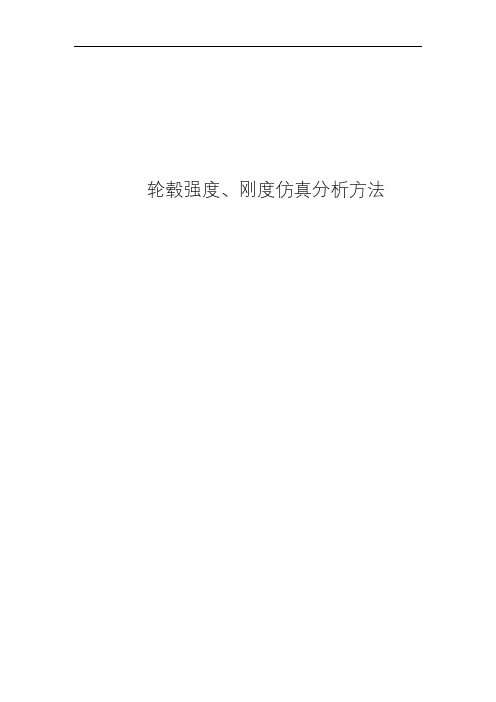
轮毂强度、刚度仿真分析方法1.概述1.1轮毂铝合金车轮是汽车上的重要部件,它承受着车身重力、驱动力、制动力以及汽车转弯时的横向载荷。
在汽车的行驶过程中,特别是在高速公路上行驶时,如果车轮裂开会造成严重的交通事故。
需要对车轮的强度进行分析以确保其具有足够的强度以满足车辆行驶的安全要求。
在铝合金车轮产品的设计开发中,新产品通常要进行标准的强度实验,包括冲击实验、弯曲疲劳实验和径向滚动疲劳实验,只有达到一系列强度实验的指标要求才能进行产品的批量生产。
1.2使用软件说明ANSYS软件是美国ANSYS公司研制的大型通用有限元分析(FEA)软件,是世界范围内增长最快的计算机辅助工程(CAE)软件,能与多数计算机辅助设计(CAD,computer Aided design)软件接口,实现数据的共享和交换,如NASTRAN, I-DEAS, AutoCAD等。
是融结构、流体、电场、磁场、声场分析于一体的大型通用有限元分析软件。
在核工业、铁道、石油化工、航空航天、机械制造、能源、汽车交通、国防军工、电子、土木工程、造船、生物医学、轻工、地矿、水利、日用家电等领域有着广泛的应用。
ANSYS功能强大,操作简单方便,现在已成为国际最流行的有限元分析软件,在历年的FEA评比中都名列第一。
目前,中国100多所理工院校采用ANSYS软件进行有限元分析或者作为标准教学软件。
ANSYS Mechanical是利用ANSYS的求解器进行结构和热分析的。
其可进行结构、动态特性、热传递、磁场及形状优化的有限元分析。
1.3相关力学理论刚度是指材料或结构在受力时抵抗弹性变形的能力。
是材料或结构弹性变形难易程度的表征。
材料的刚度通常用弹性模量E来衡量。
在宏观弹性范围内,刚度是零件荷载与位移成正比的比例系数,即引起单位位移所需的力。
它的倒数称为柔度,即单位力引起的位移。
刚度可分为静刚度和动刚度。
刚度是使物体产生单位变形所需的外力值。
刚度与物体的材料性质、几何形状、边界支持情况以及外力作用形式有关。
CRH2动车组CADCAE分析
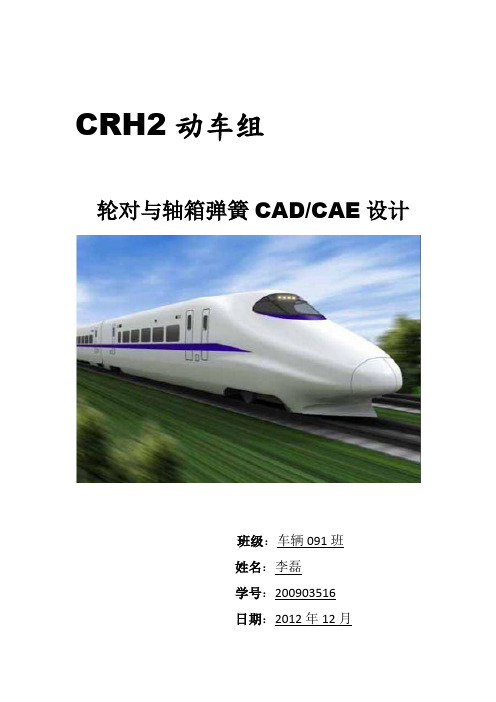
CRH2动车组轮对与轴箱弹簧CAD/CAE设计班级:车辆091班姓名:李磊学号:200903516日期:2012年12月一、问题描述CRH2型动车组以日本新干线E2-1000型动车组为原型,通过引进-消化-吸收-再创新,初步实现了国内制造。
1-1日本新干线E2-1000在国产化中,车轮踏面的适应性改造如下图1-2所示:图.1-2(左为日本新干线E2-1000,右为CRH2)为适应更高速速度与我国线路状况需要,在转向架的轴箱定位方式上改为转臂式轴箱定位(如图1-3所示),对构架、空气簧和轮对悬挂参数进行了优化。
图.1-3(左为E2-1000拉板式定位)众所周知,新干线自开通以来以它的优越性能,精准的正点率,非自然灾害之外的零伤亡事故赢得世界瞩目,长期的运营也证明了其出色的性能,但是在国内引进消化吸收再创新过程中,所采取的适应性改造是否合理,究竟是提升了其运行安全性和运行品质使得更加适应国内线路条件和车速需求,还是仅仅为了创新而创新需要经过理论和实践的双重检验。
由于我国高铁投入运营时间尚短,设计理念、设计方法不能与德国、法国、日本这些高铁大国同日而语,而通过试验运行来检验其设计合理性势必会有风险而且会增加设计周期减少经济效益,因而必要的计算机辅助分析与仿真是必不可少的。
下面就针对我国在对日本新干线动车组E2-1000引进国产化过程中的适应性改造进行CAE分析:即轴箱弹簧(悬挂参数优化)、轮对(踏面适应性改造)。
本文以CRH2动车组轮对与轴箱弹簧为研究对象,建立其有限元模型。
按照相关标准,应用solidworks2012对其进行CAD/CAE设计分析附:CRH2动车组拖车转向架基本参数二、 CAD设计1、轴箱弹簧CRH2型动车组轴箱弹簧的参数如下表2-1-1所示:(表2-1-1)CRH2轴箱弹簧外簧圈建模过程如图2-1-1所示:建模过程仿真在实际加工中的工艺流程:修正下料-端部加热-锻尖-加热-卷绕-淬火-回火-强化处理-磨平端部-试验或验收(使用三段直线法进行仿真)2、拖车空心车轴CRH2转向架车轴按照JIS E 4501(铁道车辆-车轴强度设计)进行设计,按JIS E 4502标准进行生产。
车轮轮辐结构强度分析
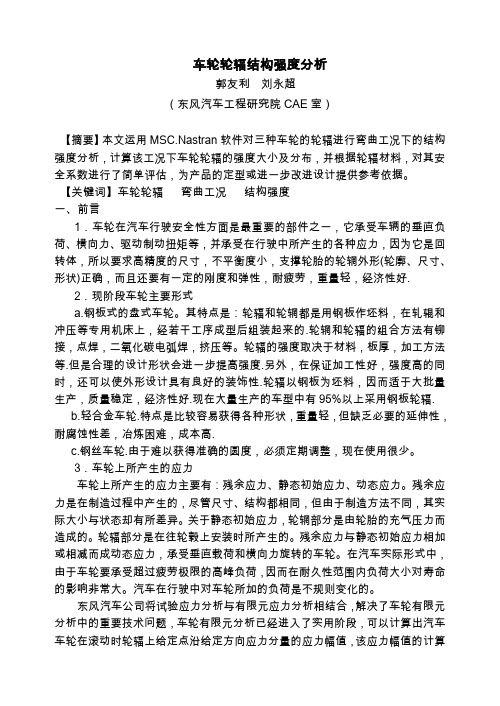
车轮轮辐结构强度分析郭友利刘永超(东风汽车工程研究院CAE室)【摘要】本文运用MSC.Nastran软件对三种车轮的轮辐进行弯曲工况下的结构强度分析,计算该工况下车轮轮辐的强度大小及分布,并根据轮辐材料,对其安全系数进行了简单评估,为产品的定型或进一步改进设计提供参考依据。
【关键词】车轮轮辐弯曲工况结构强度一、前言1.车轮在汽车行驶安全性方面是最重要的部件之一,它承受车辆的垂直负荷、横向力、驱动制动扭矩等,并承受在行驶中所产生的各种应力,因为它是回转体,所以要求高精度的尺寸,不平衡度小,支撑轮胎的轮辋外形(轮廓、尺寸、形状)正确,而且还要有一定的刚度和弹性,耐疲劳,重量轻,经济性好.2.现阶段车轮主要形式a.钢板式的盘式车轮。
其特点是:轮辐和轮辋都是用钢板作坯料,在轧辊和冲压等专用机床上,经若干工序成型后组装起来的.轮辋和轮辐的组合方法有铆接,点焊,二氧化碳电弧焊,挤压等。
轮辐的强度取决于材料,板厚,加工方法等.但是合理的设计形状会进一步提高强度.另外,在保证加工性好,强度高的同时,还可以使外形设计具有良好的装饰性.轮辐以钢板为坯料,因而适于大批量生产,质量稳定,经济性好.现在大量生产的车型中有95%以上采用钢板轮辐.b.轻合金车轮.特点是比较容易获得各种形状,重量轻,但缺乏必要的延伸性,耐腐蚀性差,冶炼困难,成本高.c.钢丝车轮.由于难以获得准确的圆度,必须定期调整,现在使用很少。
3.车轮上所产生的应力车轮上所产生的应力主要有:残余应力、静态初始应力、动态应力。
残余应力是在制造过程中产生的,尽管尺寸、结构都相同,但由于制造方法不同,其实际大小与状态却有所差异。
关于静态初始应力,轮辋部分是由轮胎的充气压力而造成的。
轮辐部分是在往轮毂上安装时所产生的。
残余应力与静态初始应力相加或相减而成动态应力,承受垂直载荷和横向力旋转的车轮。
在汽车实际形式中,由于车轮要承受超过疲劳极限的高峰负荷,因而在耐久性范围内负荷大小对寿命的影响非常大。
CAE-车轮轮辋强度强度分析报告
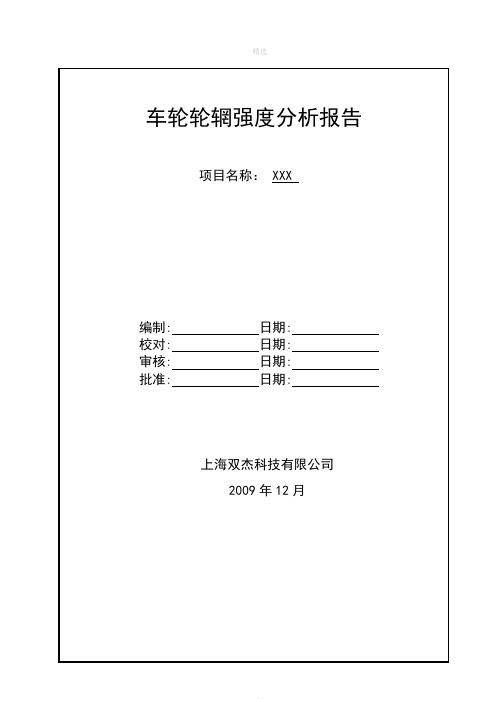
目次前言 (II)1 范围 (1)2 分析目的 (1)3 有限元模型的建立 (1)3.1 有限元模型建立流程 (1)3.2 有限元建立标准及方法 (2)3.3轮辋有限元模型 (2)3.4 材料及边界条件 (4)4 分析结果 (7)5 分析结论 (9)I前言为了校核新开发车型的轮辋强度是否符合国标要求,本报告对XXX项目轮辋进行强度分析。
本分析报告主要起草人:汪霞II1范围本报告规定了分析目的、有限元模型的建立、分析结果和分析结论。
本分析报告适用于XXX项目175-80R14轮辋总成的强度计算分析。
2 分析目的为了校核新开发车型的轮辋强度是否符合国标要求,本报告对XXX项目轮辋进行强度分析。
3 有限元模型的建立3.1 有限元模型建立流程CAE仿真计算的精度及准确性除了与有限元核心计算理论有关外,还在很大程度上依赖于仿真模型建立的精度,轮辋总成有限元模型建立流程见图1。
图1 有限元模型建立流程3.2 有限元建立方法根据设计部门提供的CAD数模,建立轮辋总成的有限元模型。
轮辋主要采用四面体二次单元进行离散,基准尺寸3.0mm。
3.3 轮辋总成有限元模型对轮辋进行有限元划分,轮辋有限元模型见图2。
轮辋总成有限元模型单元325545个。
图2 轮辋有限元模型3.4 材料及边界条件模型材料见材料特性表2。
表2 有限元模型的材料特性弹性模量(N/mm2)泊松比密度(T/mm3)101A 6.2E40.33 2.68E-93.4.1 强度分析边界条件(说明:边界条件中提到的自由度123分别为XYZ方向的平动自由度,自由度456分别为XYZ方向的转动自由度。
)按照QC/T 259-1998要求,轮辋、轮辐板料厚度的较小值大于3.5mm的车轮轮辋,在实验载荷294kN 作用下对应于车轮的轮辋/轮辐的焊接部位不应出现撕裂或可见的裂纹。
试验装置图见图3。
图3试验装置图模拟实验装置建立有限元模型,对下模处约束123自由对 在轮辋内侧加载294kN 集中力,强度计算边界条件见图4。
cae分析报告

cae分析报告CAE分析报告是一种基于数值模拟、力学分析和材料力学等方法,对于产品的性能进行评估和优化的工程分析方法。
本报告将对某个产品的CAE分析结果进行详细介绍和分析。
经过CAE分析,建议在产品的设计和制造过程中采用合适的材料和结构,以确保产品的性能和质量。
首先,对于材料的选择,通过CAE分析发现,目前使用的材料具有较高的强度和刚度,能够满足应力和振动的要求,但是存在一定的开裂和断裂的风险。
因此,建议在材料选择时,考虑使用更具韧性的材料,以增加产品的抗拉伸能力和耐磨性,同时降低开裂和断裂的风险。
其次,在产品设计和制造过程中,需要考虑到产品的结构强度和刚度。
通过CAE分析,发现当前产品在受力部位存在一定的应力集中,可能导致局部的破坏和失效。
因此,建议在产品的设计过程中,增加受力部位的支撑和加强结构,以分散应力和提高产品的强度。
另外,还可以考虑使用增加刚度的结构设计,以降低振动和共振的影响,提高产品的稳定性和寿命。
此外,在产品的制造过程中,需要注意制造工艺和表面处理的影响。
通过CAE分析,发现产品的表面粗糙度对于摩擦和磨损的影响较大。
因此,建议在制造过程中,采用适当的加工工艺,以提高表面的光洁度和平整度,降低表面粗糙度,从而减少摩擦和磨损。
最后,在产品的使用和维护过程中,需要进行适当的检测和修复。
通过CAE分析,发现产品的应力和变形会随着使用时间的增加而逐渐积累,可能导致材料疲劳和失效。
因此,建议在产品的使用过程中,定期进行检测和维修,以及时发现和修复产品的疲劳和损伤。
综上所述,CAE分析报告提供了一种全面的工程分析方法,可以评估产品的性能和质量,并提供优化的建议。
通过合理选择材料和结构设计,控制制造工艺和维护过程,可以提高产品的性能和寿命,降低故障和失效的风险。
因此,在产品的设计和制造过程中,需要充分应用CAE分析方法,以确保产品的安全性和可靠性。
汽车轮毂冲击的 CAE与实验分析

构设 计 中 , 首先 要 使其满 足 强度要求 , 一 般在 车轮 批量 生产 之前 , 必 须通过 冲击 试验 、 径 向滚动 疲劳 试验 和弯 曲疲 劳试 验 。即便是 在批 量生 产之 前进
行试 验可 避免 大批 量 的报 废 , 要 得 到试 验 用 车 轮
通过 实验 结果 与分 析 结 果 的 比较 , 提 出对 有 限元 分析模 型 的修正 系 数 , 从 而可 用 车 轮 冲击 试 验 有 限元分 析指 导新产 品设计 , 缩 短其开 发周期 。
仍需付出高昂代价 , 从车轮设计 、 模具设计 、 模具 开制 、 上模 具 、 小 批 生产 、 下模具 , 无论 是 时间还 是
成本 , 都是 一个 不 小 的支 出。而 小批 量 生 产 的车 轮又不 能保 证必 然 通 过 试验 , 就 有可 能 会 造 成更
大的 时间 和成 本 的浪 费 。随着 F E A技 术 的 不 断
摘
要 :针 对 汽 车 车 轮 冲 击 试验 , 通 过 动 态 响应 有 限元 分 析 , 确定车轮 结构中的最大应 力及危险 位置, 并通过实验
心 力 分析 , 利 用 动态 电阻 应 变 仪 等 , 测定 并计 算 车轮 结 构 中关 键 点 的 应 力 响应 , 利 用 MA T L A B计 算 并 绘 制 V o n Mi s e s应 力 响 应 曲线 。通 过 对 比有 限 元 分 析 与 实 测 结 果 , 提 出修 正 系数 , 对有 限元分析模 型进行修正 , 该结 果可用 于企业的车轮设 计, 提 高 产 品结 构 设 汁 的一 次 合 格 率 。 关 键 词 : 冲击 试 验 ; C A E分 析 ; 动态响应 ; 实验应力分析 ; 动 态 电 阻 应 变 仪 中 图 分 类 号 :U 4 6 3 . 3 4, 0 3 1 3 , 0 3 4 8 文献 标 识 码 :A 文 章 编 号 :1 0 0 7— 4 2 6 0( 2 0 1 3 ) 0 4— 0 0 7 6— 0 3
车轮强度疲劳分析
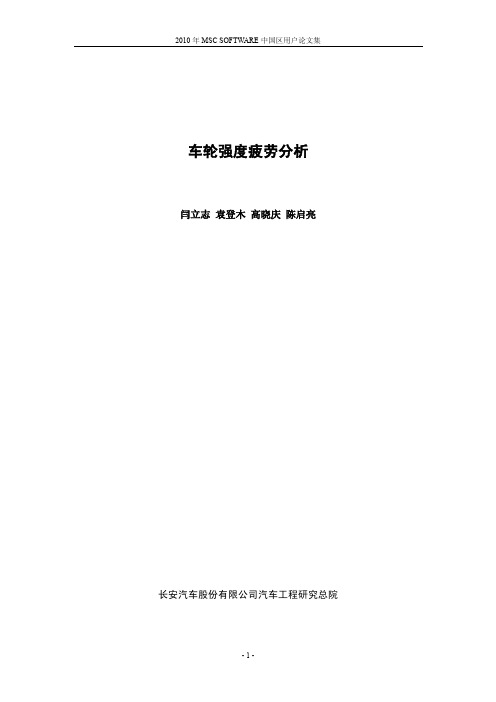
车轮强度疲劳分析闫立志袁登木高晓庆陈启亮长安汽车股份有限公司汽车工程研究总院车轮强度疲劳分析闫立志袁登木高晓庆陈启亮(长安汽车股份有限公司汽车工程研究总院CAE所,重庆,401120)【摘要】:汽车车轮主要承受循环载荷,借助MD.Nastran及MSC.Fatigue模拟车轮在循环对称载荷作用下的强度和疲劳,可以有效地指导车轮的设计。
【关键词】:车轮;强度;疲劳;MD.Nastran;MSC.FatigueStrength and Fatigue Analysis for the WheelYan Lizhi, Yuan Dengmu, Gao Xiaoqing, Cheng QiliangChangan Automotive Engineering Institute, Chongqing, 401120Abstract: The wheel of a vehicle is mostly supported by circular ing MD.Nastran and MSC.Fatigue,we can analysis it’s strength and fatigue,in order to guiding the designing.Key words:Wheel; Strength; Fatigue; MD.Nastran;MSC.Fatigue1引言汽车车轮的功用是支持全车的重量,承受驱动力、制动力、以及地面对车轮的各种力,并通过轮胎与地面的接触而实现汽车的运动。
因此车轮的强度疲劳对于整车的正常使用有非常重要的作用,而实际使用中,车轮主要承受径向载荷,也是车轮破坏的主要载荷形式,因此本论文针对车轮在滚动过程中承受径向载荷作用下,车轮强度疲劳分析并进行结构优化。
2 基于Nastran的汽车车轮循环对称响应分析(SOL109)本文以某项目开发为例,利用MD.Nastran分析车轮,并对危险部位通风孔进行结构改进及优化,得到较优方案,为设计提供参考意见。
轮辋强度分析报告
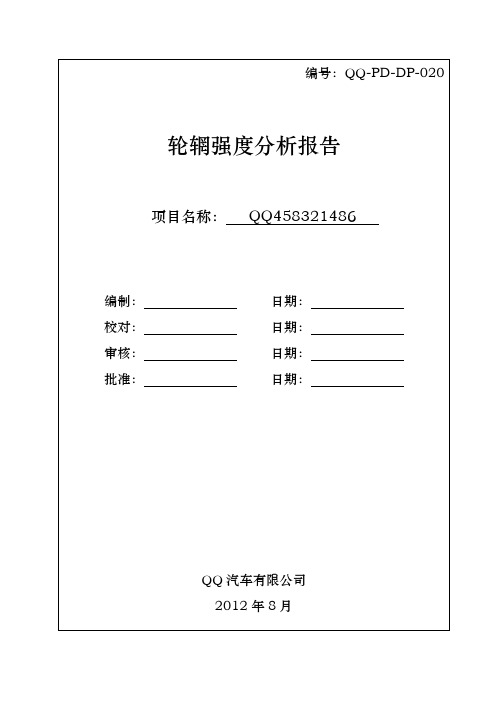
目录1分析目的 (1)2使用软件说明 (1)3有限元模型建立 (1)4边界条件 (1)5强度计算结果 (3)5.1车轮最大垂直静负荷462KG (3)5.2车轮最大垂直静负荷515KG (4)6分析结论 (5)1 分析目的参照国家标准GB/T 5334—2005《乘用车车轮性能要求和实验方法》对车轮进行强度分析,得到车轮在弯曲载荷作用下的应力分布,验证车轮设计的合理性,并为车轮结构优化、提高轮辐强度和降低生产成本提供支持。
2 使用软件说明本次分析采用Hypermesh作前处理,Altair optistruct求解。
HyperMesh是世界领先的、功能强大的CAE应用软件包,也是一个创新、开放的企业级CAE平台,它集成了设计与分析所需的各种工具,具有无与伦比的性能以及高度的开放性、灵活性和友好的用户界面,与多种CAD和CAE软件有良好的接口并具有高效的网格划分功能;Altair Optistruct是一个综和隐式和显示求解器于一体的大规模有限元计算软件,几乎所有的线性和非线性问题都可以通过其进行求解。
Altair Optistruct最强大的功能是其友好的CAO接口,通过Altair Optistruct可以进行任何形状、尺寸、拓扑结构的优化,采用固定的内存分配技术,具有很高的计算精度和效率。
3 有限元模型建立根据设计部门提供的CAD数模,建立轮辐—轮辋总成的有限元模型。
轮辐—轮辋总成主要采用四面体单元进行离散,基准尺寸5mm。
加载轴采用四面体单元进行离散,因不需要关注加载轴的应力分布和大小,结合其尺寸与结构,其基本尺寸取5mm。
轮辐—轮辋总成的有限元模型见图1。
图1 轮辐—轮辋总成有限元模型4 边界条件按照国家标准GB/T 5334—2005《乘用车车轮性能要求和实验方法》,规定将车轮牢固地夹紧在试验夹具上,加载力臂和连接件用无润滑的双头螺栓和螺母(或螺栓)连接到车轮的安装平面上,安装情况应与装于车辆上的实际使用工况相当。
轮毂强度、刚度试验报告

轮毂强度、刚度试验报告
一、试验内容
测量车辆轮毂刚度及强度。
二、试验目的
确定轮毂的各工况下的刚度及强度。
三、试验仪器
白车身及局部刚度实验台包括机械部分和电气部分两大部分。
1.机械部分
✓加载装置
✓摆角装置
✓锁紧装置
✓移动装置
✓机架
2.电控部分
✓测力单元、显示器、计算机:测力单元接受力传感器的输出,在液晶显示器显示出来,根据满意程度选择保存或打印。
✓控制:开环和闭环控制。
✓6个采集箱:根据需要分别独立工作,一个采集箱采集10路变形。
四、试验数据采集
1.试验步骤
✓试验前检查设备情况,加润滑油
✓将轮毂固定在试验台上
✓确定测点位置,布置传感器
✓连接各信号电源线、驱动器线、传感器线
✓检测传感器与采集箱,确认连线均已正确连接
✓接通电源,启动计算机,开始试验
✓试验机可以正向或反向加载
✓试验结束,退出程序,关闭计算机及其电源
2.轮毂试验:
✓固定8个螺栓孔,施加径向力500N以及力矩100N·m
✓按照一定间距布置传感器,预加载消除间隙,考虑减去预加载时的位移或力读数
✓得到测点数据
五、试验数据分析
力与变形量数据采集
最大形变量出现在轮辋处,为0.16mm,强度最大为26MPa,符合要求。
基于CATIA V5的汽车车轮钢圈结构强度分析
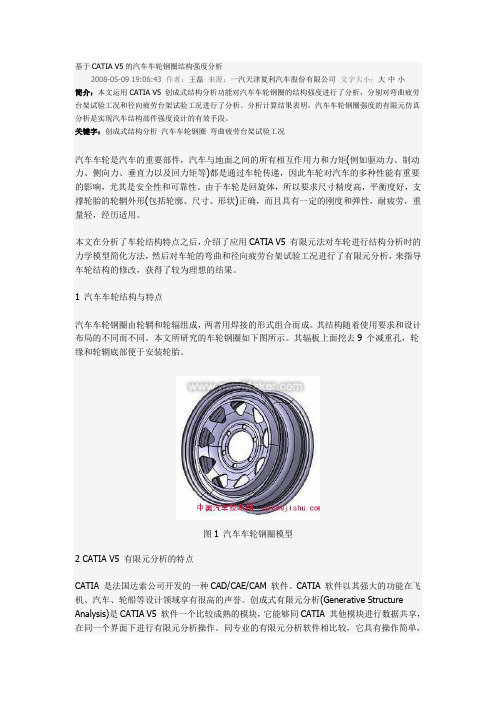
基于CATIA V5的汽车车轮钢圈结构强度分析2008-05-09 19:06:43 作者:王磊来源:一汽天津夏利汽车股份有限公司文字大小:大中小简介:本文运用CATIA V5 创成式结构分析功能对汽车车轮钢圈的结构强度进行了分析,分别对弯曲疲劳台架试验工况和径向疲劳台架试验工况进行了分析。
分析计算结果表明,汽车车轮钢圈强度的有限元仿真分析是实现汽车结构部件强度设计的有效手段。
关键字:创成式结构分析汽车车轮钢圈弯曲疲劳台架试验工况汽车车轮是汽车的重要部件,汽车与地面之间的所有相互作用力和力矩(例如驱动力、制动力、侧向力、垂直力以及回力矩等)都是通过车轮传递,因此车轮对汽车的多种性能有重要的影响,尤其是安全性和可靠性。
由于车轮是回旋体,所以要求尺寸精度高,平衡度好,支撑轮胎的轮辋外形(包括轮廓、尺寸、形状)正确,而且具有一定的刚度和弹性,耐疲劳,重量轻,经历适用。
本文在分析了车轮结构特点之后,介绍了应用CATIA V5 有限元法对车轮进行结构分析时的力学模型简化方法,然后对车轮的弯曲和径向疲劳台架试验工况进行了有限元分析,来指导车轮结构的修改,获得了较为理想的结果。
1 汽车车轮结构与特点汽车车轮钢圈由轮辋和轮辐组成,两者用焊接的形式组合而成。
其结构随着使用要求和设计布局的不同而不同。
本文所研究的车轮钢圈如下图所示。
其辐板上面挖去9 个减重孔,轮缘和轮辋底部便于安装轮胎。
图1 汽车车轮钢圈模型2 CATIA V5 有限元分析的特点CATIA 是法国达索公司开发的一种CAD/CAE/CAM 软件。
CATIA 软件以其强大的功能在飞机、汽车、轮船等设计领域享有很高的声誉。
创成式有限元分析(Generative Structure Analysis)是CATIA V5 软件一个比较成熟的模块,它能够同CATIA 其他模块进行数据共享,在同一个界面下进行有限元分析操作。
同专业的有限元分析软件相比较,它具有操作简单,分析结果可靠性好,同时不需要对分析模型进行数据转化,因而受到越来越广泛的关注和应用。
- 1、下载文档前请自行甄别文档内容的完整性,平台不提供额外的编辑、内容补充、找答案等附加服务。
- 2、"仅部分预览"的文档,不可在线预览部分如存在完整性等问题,可反馈申请退款(可完整预览的文档不适用该条件!)。
- 3、如文档侵犯您的权益,请联系客服反馈,我们会尽快为您处理(人工客服工作时间:9:00-18:30)。
目次
前言 (II)
1 范围 (1)
2 分析目的 (1)
3 有限元模型的建立 (1)
3.1 有限元模型建立流程 (1)
3.2 有限元建立标准及方法 (2)
3.3轮辋有限元模型 (2)
3.4 材料及边界条件 (4)
4 分析结果 (7)
5 分析结论 (9)
前言
为了校核新开发车型的轮辋强度是否符合国标要求,本报告对XXX项目轮辋进行强度分析。
本分析报告主要起草人:汪霞
1范围
本报告规定了分析目的、有限元模型的建立、分析结果和分析结论。
本分析报告适用于XXX项目175-80R14轮辋总成的强度计算分析。
2 分析目的
为了校核新开发车型的轮辋强度是否符合国标要求,本报告对XXX项目轮辋进行强度分析。
3 有限元模型的建立
3.1 有限元模型建立流程
CAE仿真计算的精度及准确性除了与有限元核心计算理论有关外,还在很大程度上依赖于仿真模型建立的精度,轮辋总成有限元模型建立流程见图1。
图1 有限元模型建立流程
3.2 有限元建立方法
根据设计部门提供的CAD数模,建立轮辋总成的有限元模型。
轮辋主要采用四面体二次单元进行离散,基准尺寸3.0mm。
3.3 轮辋总成有限元模型
对轮辋进行有限元划分,轮辋有限元模型见图2。
轮辋总成有限元模型单元325545个。
图 2 轮辋有限元模型
3.4 材料及边界条件
模型材料见材料特性表2。
表2 有限元模型的材料特性
3.4.1 强度分析边界条件
(说明:边界条件中提到的自由度123分别为XYZ方向的平动自由度,自由度456分别为XYZ方向的转动自由度。
)
按照QC/T 259-1998要求,轮辋、轮辐板料厚度的较小值大于3.5mm的车轮轮辋,在实验载荷294kN 作用下对应于车轮的轮辋/轮辐的焊接部位不应出现撕裂或可见的裂纹。
试验装置图见图3。
图3试验装置图
模拟实验装置建立有限元模型,对下模处约束123自由对 在轮辋内侧加载294kN 集中力,强度计算边界条件见图4。
图4 边界条件
4 强度计算结果
在上述边界条件及载荷作用下得到轮辋应力云图见图5。
SPC 123
图5轮辋应力云图
从轮辋应力云图可以观察到最大应力为259.7Mpa,小于GB101A材料抗拉极限(2760MPa)
轮辋在上述载荷作用下的位移云图见图6,最大位移0.127mm。
图6 轮辋位移云图
5.分析结论
通过模拟轮辋强度实验,最大应力为257.9Mpa,小于材料抗拉极限,满足国标强度设计要求。