8D分析报告模板(标)
8d报告完整版范文3篇
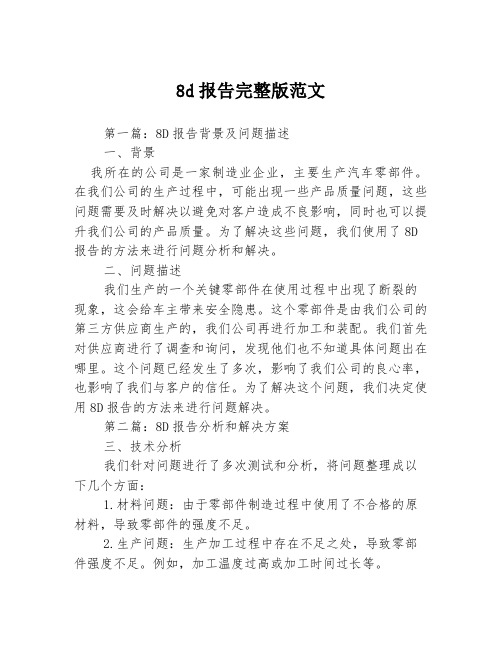
8d报告完整版范文第一篇:8D报告背景及问题描述一、背景我所在的公司是一家制造业企业,主要生产汽车零部件。
在我们公司的生产过程中,可能出现一些产品质量问题,这些问题需要及时解决以避免对客户造成不良影响,同时也可以提升我们公司的产品质量。
为了解决这些问题,我们使用了8D 报告的方法来进行问题分析和解决。
二、问题描述我们生产的一个关键零部件在使用过程中出现了断裂的现象,这会给车主带来安全隐患。
这个零部件是由我们公司的第三方供应商生产的,我们公司再进行加工和装配。
我们首先对供应商进行了调查和询问,发现他们也不知道具体问题出在哪里。
这个问题已经发生了多次,影响了我们公司的良心率,也影响了我们与客户的信任。
为了解决这个问题,我们决定使用8D报告的方法来进行问题解决。
第二篇:8D报告分析和解决方案三、技术分析我们针对问题进行了多次测试和分析,将问题整理成以下几个方面:1.材料问题:由于零部件制造过程中使用了不合格的原材料,导致零部件的强度不足。
2.生产问题:生产加工过程中存在不足之处,导致零部件强度不足。
例如,加工温度过高或加工时间过长等。
3.设计问题:设计过程中没有考虑到应力分布的均匀性,导致零部件在使用过程中容易产生应力过大的现象。
四、解决方案1.材料问题:我们将与供应商重新协商并重新规定原材料标准,以保证原材料的质量。
2.生产问题:我们将对生产过程进行检查和测试,改进加工温度和加工时间,并进一步探究生产中存在的不足之处,以最大程度地提高相关生产能力。
3.设计问题:我们会重新设计零部件,考虑应力分布的均匀性,并对原有零部件进行更加严格的测试和分析以验证新设计的可行性。
第三篇:8D报告措施计划和预防五、措施计划1.与供应商合作并重新规定原材料标准。
2.对生产过程进行检查和测试,并改进加工温度和加工时间。
3.重新设计零部件,考虑应力分布的均匀性,并进行严格的测试和分析。
4.对生产和供应链流程进行跟踪和监控,确保问题不再发生。
企业经典8D报告模板(精选)

Define the Problem明确问题
Root Cause根本原因
Why?为什么?
Why?为什么?
Why?为什么?
Why?为什么?
Therefore因此
Therefore因此
Therefore因此
Therefore因此
Root Cause Analysis - Cont’d (根本原因分析 - 续前页)
D4.8) 5-Why Analysis for the Verified Cause (对验证的原因进行5个为什么分析)
D4 – ROOT CAUSE ANALYSISD4 – 根本原因分析
Root Cause Analysis - Cont’d (根本原因分析 - 续前页)
D2 – PROBLEM STATEMENTD2 – 问题描述
D2.3) Pictures Showing the Defective & Acceptable Samples (好坏板照片)
Describe Problem - Cont’d (描述问题 - 续前页)
Defective Sample (坏板)
D4 – ROOT CAUSE ANALYSISD4 – 根本原因分析
D5 – IMPLEMENT CORRECTIVE ACTIOND5 – 执行改善行动
Implement Corrective Action (执行改善行动)
D5.1) Occurrence Permanent Corrective Action(s) (针对发生原因的永久性改善行动)
Containment Action - Cont’d (围堵行动 - 续前页)
8D报告(模板)

PREPARED BY:
(拟定)
Closedate:
(结案日期)
调查分析情况
Responsibility Dept.
(责任单位)
Guarantor
(担当人)
Completion Date
(完成日期)
5. Permanent C/Aplan:
(永久对策)根据4原因分析,从流程、管理制度以及人员能力方面提出预防同类问题发生的对策
Responsibility Dept.
8D改善对策报告
Customer:
(客戶)
Part Name:
(产品名称)
SalesOrderNo.:
(销售订单号)
QTYNo.:
(批量)
Defect Rate:
(不良ቤተ መጻሕፍቲ ባይዱ率)
PartNo:
(料号)
Open Date:
(开案日期)
Release Date:
(报告发行日期)
1. Use the team approach:
(成立处理团队)
Name(姓名)
Dept. (部門)
Name(姓名)
Dept. (部門)
Name(姓名)
Dept. (部門)
2. Problem Description(Definition):
(问题描述)如果是设计问题,问题描述应该包括技术上的原因
3. Containment plan:
(暂时(紧急)对策)紧急对策含对库存产品、其他型号同样问题的处理
(责任单位)
Guarantor
(担当人)
Completion Date
(完成日期)
6.Verification of effectiveness:
8D报告模板

报告日期:
报告编号:
年月日
Page 1
D1:Use Team Approach 团队组成
团队 组长:
姓名
部门
职位
成员:
Page 2
D2:Describe the Problem异常问题描述
1) 异常发生/客户投诉时间: 2) 异常发生工序: 3) 异常发现部门(及人员)/客户: 4) 异常缺陷描述: 5) 异常影响范围: 6) 其他描述:
序号 1
针对根本原因的行动措施
负责人 完成期限 完成状态
2 3 4
Page 7
D6:Action(s) 纠正措施效果验证
序号 1 2 3 4 5
行动措施
验证情况(需附相关证据)
验证人
Page 8
D7:Recurrence Prevention 预防再发生
原因调查分析
2
3
4 5
6
注:可附页
Page 5
涉及因素
D4:Root Cause Definition 根本原因分析
D4-2 分析结论: 序号 1
原因分析结果
责任工序 主要原因或 或人员 次要原因
2
3
4
5
备注:主要原因列举在前,次要原因列举在后。
Page 6
D5:Permanent Corrective Action(s) 永久性纠正措施
Page 3
D3:Containment And Short Term Corrective Action(s) 围堵措施及短期行动计划
序号
行动措施
负责人 完成期限 完成状态
行动结果
1
2
完整8D报告模板

版本:产品名称Product Name 客户名称Customer Name客户型号Customer model工厂产品型号Positec model 客户订单号Order no.日期码Date code合同编号Contract No. 合同数量Quantity异常发生日期Complaint date发文部门Dispatched by 异常信息来源Message from要求完成时间Required complete dateDISCIPLINE 1: Use Team Approach (建立解决问题小组)质量改进小组组长:质量改进小组成员:□产品工程师_______________________ □研发工程师______________ □品质工程师_______________________ □制程工程师______________ □采购工程师/SQE___________________ □生产主管________________ □其他_____________________________填写人:日期:DISCIPLINE 2: Describe The Problem (问题描述)问题等级______类(填写A or B or C)□图片说明及详细信息描述:填写人:日期:DISCIPLINE 3: Implement And Verify Containment Action (执行暂时对策)□返工/补充加工(QE/PE)□质量问题通知供应商(SQE或采购)□生产计划调整(QE)□(在线/在途/库存)零部件库存处理(PE)□通知客户/QA (公司QA或工厂QE)□国外产品处理(项目主管or品质经理)□其它相应措施说明:填写人:日期:版本:DISCIPLINE 4: Define and Verify Root Cause (找出问题的真正原因)原因分析(责任部门填写)□设计缺陷/Design defects □规格、标准缺陷/criterion defects□工装设备缺陷/Equipment defects □检查判定缺陷(误判、错判)/Wrong verdict□制程及作业上缺陷(含料件)/Parts or assembling defects□模具、夹具缺陷/Fixture defects □其他/Others具体说明/Described in detail:□失效模式再现验证说明□改进失效验证说明附原因分析报告《》(插入附件, 空白表单在下面连接内)填写人:日期:DISCIPLINE 5:Choose and Verify Permanent Corrective Action (选择永久对策)相应措施进度及说明:具体内容责任人计划完成时间样品采购样品确认工程样机装配实验申请实验结果判断工装申请小批验证□ECR:(连接到文管中心下文件)□修模单:(连接到文管中心下文件)□其它填写人:日期:DISCIPLINE 6: Implement Permanent Corrective Action (执行及验证永久对策)□品质标准(品质人员提供,需明确清晰):□正向模式验证:□反向失效模式验证:实际完成情况确认人实际完成时间样品采购样品确认工程样机装配实验申请实验结果判断工装申请小批验证(工程人员提供正/反验证需包含详细数据,如实验申请号,验证结果等.)(品质)填写人:日期:(工程)填写人:日期:DISCIPLINE 7: Prevent Recurrence & Standardization (防止再发生措施及标准化)版本:产品工程师PE:□ECN□BOM□PQC检指/培训□IQC检指/培训制程工程师:□总装工艺卡/装配人员培训品质工程师QE:□FQC检指/培训采购部SQE:□供应商培训□供应商检指□供应商检具□供应商工艺□供应商库存处理其它填写人:日期:DISCIPLINE 8: Congratulate Our Team (批量验证/团队激励)改善情况的追踪:□ECN□BOM□供应商培训□供应商检指□供应商检具□供应商工艺□供应商库存处理□IQC检指/检验结果□PQC检指/检验结果□FQC检指/检验结果□总装工艺卡□试验/检验考核结果填写人:日期:经办/drafted by: 部门审核/checked by: 品质经理审核: 批准/Approved by:一、QC培训记录二、QC检指记录三、供应商方面培训、检(插入相关支持文件)指、检具、工艺、协议记录四、工艺文件备注:1.对异常问题或改进状态的描述要尽量有图片说明或详细的信息记录。
8D报告模板_6

其他
3.供应商内部流出原因(或汽车厂家处未识别出)的初步分析
不合格零件应当在何处被发现?
N
在制造工序中
在制造后(如最终检验)
出货前/汽车厂家入库时
没有被发现的原因
对不良产生原因初步判断/流出原因的分析:
D3-第三步骤:执行临时对策
4.临时对策–立即的
组织相关人员针对此问题开现场分析会。
考虑事项
防止再发生对策报告书―8D
编号:
D1-第一步骤:建立解决问题小组
组长:
组员:
D2-第二步骤: 描述问题
减振器在新车交验过程中损坏:弹簧弹出,减震器失效。
1 问题详情
受影响的数量(或追溯)
2. 向类似零件的展开
该问题在其他零件上发生过吗?
考慮事項
Y
N
备注/ 結果
其他车型零件
同一不良现象覆盖的所有车型。
D8-第八步骤: 团队激励。
处置
OK数
NG数
在制品
中间在库品(半成品)
仓库存品
服务备件
其他
首批交付合格部品如何特殊标识/标记 ?
标牌
D4-第四步骤: 找出问题真正原因
5最终分析
时间
原因
责任部门
生产管理部
生产管理部
D5-第五步骤: 选择永久对策
6.永久対策
措施
负责人
部门
实施时间
D6-第六步骤:执行及验证永久对策
7. 对策确认
Y
N
Y
N
D7-第七步骤: 防止再发。
8.跟踪措施
考慮事项
Yes/No
实施时间
实施部门
工序作业/检查指导书
完整8D报告模板

说明:D1第一步调: 建立解决问题小组由品质部召集相关人员若问题无法独立解决,通知你认为有关的人员组成团队。
团队的成员必须有能力执行,例如调整机器或懂得改变制程条件,或能指挥作筛选等。
备注:执行者不列入。
D2第二步调: 描述问题由品质部收集,并向小组人员传达向团队说明何时、何地、发生了什么事、严重程度、目前状态、如何紧急处理、以及展示照片和收集到的证物。
想象你是FBI的办案人员,将证物、细节描述越清楚,团队解决问题将越快。
D3第三步调: 执行暂时对策由小组人员负责执行若真正原因还未找到,暂时用什么方法可以最快地防止问题?如全检、筛选、将自动改为手动、库存清查等。
暂时对策决定后,即立刻交由团队成员带回执行。
备注:为了防止遗漏,纠正措施五要→客户仓库、在途、客户生产线、工厂生产线 & 工厂仓库。
D4第四步调: 找出问题真正原因由小组人员讨论后确定找问题真正原因时,最好不要盲目地动手改变目前的生产状态,先动动脑。
您第一件事是要先观察、分析、比较。
列出您所知道的所有生产条件(即鱼骨图),逐一观察,看看是否有些条件走样,还是最近有些什么异动?换了夹具吗?换了作业员?换了供应商?换了运输商?修过电源供应器?流程改过?或比较良品与不良品的检查结果,看看哪个数据有很大的差别?尺寸?重量?电压值?CPK?耐电压?等等不良的发生,总是有原因,资料分析经常可以看出蛛丝马迹。
这样的分析,可以帮忙您缩小范围,越来越接近问题核心。
当分析完成,列出您认为最有可能的几项,再逐一动手作些调整改变,而且观察哪些改变可使品质回复正常及影响变异的程度,进而找到问题真正的原因。
这就是著名田口式方法最简单而实际的运用。
D5第五步调: 选择永久对策由小组人员讨论后确定找到造成问题的主要原因后,即可开始拟出对策的方法。
对策的方法也许有好几种,例如修理或更新模具。
试试对可能的选择列出其优缺点,要花多少钱?多少人力?能持续多久? 再对可能的方法作一最佳的选择,而且确认这样的对策方法不会发生其它副作用。
完整8D报告模板

版本:产品名称客户名称客户型号Product Name Customer Name Customer model工厂产品型号客户订单号日期码Positec model Order no.Date code合同编号合同数量异常发生日期Contract No.Quantity Complaint date发文部门异常信息来源要求完成时间Dispatched by Message from Required complete date DISCIPLINE 1:Use Team Approach (建立解决问题小组)质量改进小组组长:质量改进小组成员:□产品工程师 _______________________□品质工程师 _______________________□采购工程师 /SQE___________________□其他 _____________________________□研发工程师 ______________□制程工程师 ______________□生产主管 ________________填写人:日期:DISCIPLINE 2:Describe The Problem (问题等级______类 (填写 A or B or C)问题描述)□图片说明及详细信息描述:填写人:日期:DISCIPLINE 3:Implement And Verify Containment Action (□返工 /补充加工 (QE/PE)执行暂时对策)□质量问题通知供应商(SQE或采购 )□生产计划调整(QE)□(在线 /在途 / 库存 )零部件库存处理 (PE)□通知客户 /QA ( 公司 QA 或工厂 QE)□国外产品处理 (项目主管 or 品质经理 )□其它相应措施说明:填写人:日期:管理部门:品质部第1页;共 4 页保存期限:三年【中PTA-0807-04-04 】版本:DISCIPLINE 4:Define and Verify Root Cause (找出问题的真正原因)原因分析(责任部门填写)□设计缺陷 /Design defects□ 规格、标准缺陷/criterion defects□工装设备缺陷 /Equipment defects□ 检查判定缺陷(误判、错判)/Wrong verdict□制程及作业上缺陷(含料件)/Parts or assembling defects□模具、夹具缺陷/Fixture defects□ 其他/Others具体说明 /Described in detail:□ 失效模式再现验证说明□ 改进失效验证说明附原因分析报告《》(插入附件 , 空白表单在下面连接内 )填写人:日期:DISCIPLINE 5 :Choose and Verify Permanent Corrective Action (选择永久对策 )相应措施进度及说明:具体内容责任人计划完成时间样品采购样品确认工程样机装配实验申请实验结果判断工装申请小批验证□ECR:( 连接到文管中心下文件)□ 修模单:( 连接到文管中心下文件)□ 其它填写人:日期:DISCIPLINE 6:Implement Permanent Corrective Action (执行及验证永久对策 )□品质标准 (品质人员提供 ,需明确清晰 ):□ 正向模式验证:□ 反向失效模式验证:实际完成情况确认人实际完成时间样品采购样品确认工程样机装配实验申请实验结果判断工装申请小批验证(工程人员提供正 /反验证需包含详细数据 ,如实验申请号 , 验证结果等 .)(品质 ) 填写人:日期:(工程 ) 填写人:日期:DISCIPLINE 7:Prevent Recurrence & Standardization (防止再发生措施及标准化 )第2页;共 4 页管理部门:品质部保存期限:三年【中 PTA-0807-04-04 】版本:产品工程师 PE:□ECN□BOM□PQC检指 /培训□IQC检指 / 培训制程工程师:□总装工艺卡 /装配人员培训品质工程师 QE :□FQC检指 /培训采购部 SQE :□ 供应商培训□ 供应商检指□ 供应商检具□ 供应商工艺□ 供应商库存处理其它填写人:日期:DISCIPLINE 8: Congratulate Our Team (批量验证/团队激励)改善情况的追踪:□ ECN□ BOM□ 供应商培训□ 供应商检指□ 供应商检具□ 供应商工艺□ 供应商库存处理□ IQC检指 / 检验结果□ PQC检指 /检验结果□ FQC检指 /检验结果□ 总装工艺卡□试验 /检验考核结果经办 /drafted by:部门审核/checked by:填写人:品质经理审核 :日期:批准 /Approved by:一、 QC 培训记录二、 QC检指记录三、供应商方面培训、检( 插入相关支持文件)指、检具、工艺、协议记录四、工艺文件备注: 1.对异常问题或改进状态的描述要尽量有图片说明或详细的信息记录。
8D报告格式模板

Continuous Improvement Plan持续改善计划 No.:Eight (8) Step Problem Solving(8个解决问题之步骤)类别:A() B()CUSTOMER NAME:(客户名称)PART NUMBER:(零件编号)PART DESCRIPTION:(零件名称)QUANTITY:(数量)DEPARTMENT:(部门)DATE:(日期)1. TEAM CHAMPION:(专案领队人)TEAM MEMBERS(团队成员):2. DESCRIBE THE PROBLEM: (WHAT'S WHEN'S, and WHERE'S - include samples when possible)(不良现象描述:为何、何时、何处-如有可能包含样本)3. SHORT TERM FIX: (What you will do immediately)(暂定对策措施:应急措施)Target Date:(预计完成日期)Effective Date:(实际完成日期)4. ROOT CAUSE OF PROBLEM(问题的根本原因):Indicate problem solving tools used, i.e.,Pareto-Cause/Effect Process.(说明解决问题所使用之工具:如柏拉图分析、特性要因分析等)5. LONG-TERM PERMANENT CORRECTIVE ACTION(永久对策矫正措施):Target Date:(预计完成日期)Effective Date:(实际完成日期)*6. PREVENT REOCCURENCE(预防再发对策):Modify Systems Procedures as required.Document the new procedures, removeobsolete procedures, revise standards.提示:如有必要修改系统程序、建立新程序移除、淘汰旧的程序,修订标准。
8D报告(通用模板)

与客户_________联系,确认此批出货产品有/无以上不良现象。 与客户_________联系,确认此批出货产品有/无以上不良现象。 与客户_________联系,确认此批出货产品有/无以上不良现象。
备注(Memo)
表单编号:TZJD/QJL03-072
保存期限:三年
第2页
NO.
效果验证(Verification of Effectiveness)
1
2
3
4
确认人
日期
审核 Approved By:
审核日期 Approved Date:
7、预防措施(Discipline 7.Prevent Recurrence)
NO.
预防措施(Prevent Recurrence)
1
2
3
4
负责人
日期
审核 Approved:
审核日期 Approved Date:
8、客户确认及评价(Discipline 8.Customer satisfaction degree)
第一批产品满意程度:yes( ) 第二批产品满意程度:yes( ) 第三批产品满意程度:yes( )
no( ) no( ) no( )
主题 (Subject)
发生地点 (Occurred
Site)
客户 (Customer)
发生时间 (Occurred
Time)
产品编号 (Part Number)
1、成立小组(Discipline 1.Team Members)
部门 (Dept):
姓名(Name):
8D报告
(CA report in 8D format)
完成日期Completed Date:
(完整word版)完整8D报告模板
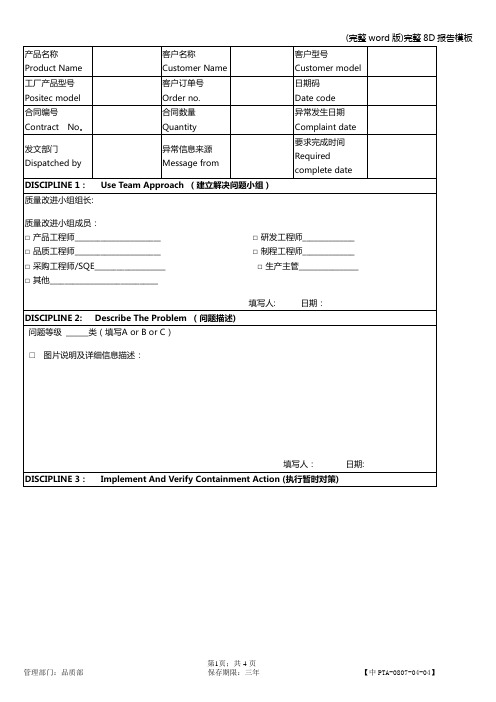
□返工/补充加工(QE/PE)□质量问题通知供应商(SQE或采购)□生产计划调整(QE)□(在线/在途/库存)零部件库存处理(PE)□通知客户/QA (公司QA或工厂QE)□国外产品处理(项目主管or品质经理)□其它相应措施说明:填写人: 日期:DISCIPLINE 4:Define and Verify Root Cause (找出问题的真正原因)原因分析(责任部门填写)□设计缺陷/Design defects □规格、标准缺陷/criterion defects□工装设备缺陷/Equipment defects □检查判定缺陷(误判、错判)/Wrong verdict □制程及作业上缺陷(含料件)/Parts or assembling defects□模具、夹具缺陷/Fixture defects □其他/Others具体说明/Described in detail:□失效模式再现验证说明□改进失效验证说明附原因分析报告《》(插入附件,空白表单在下面连接内)填写人:日期:DISCIPLINE 5:Choose and Verify Permanent Corrective Action (选择永久对策)备注:1。
对异常问题或改进状态的描述要尽量有图片说明或详细的信息记录.2。
□表示一个项目工作点;■表示项目已完成,后面要有支持文件;不涉及项目在后面写N/A。
3.问题等级按《产品质量问题等级判定规则》划分A、B、C类;A类问题须开“停产通知单”。
4。
质量改进报告单开立原则:以退货和日常的重大项目改进为主,料件的外观问题不列为此项改进内容.5.质量改进报告单填写细则:相关问题分析及验证性报告插入此改进单,能够使用超连接的选用连接形式(确认路径不变并能连接到改进的文件),支持文件不必打印。
6.此份报告前3页为改进项目进度的目录表,第4页是说明页,不必打印.7。
表单编号:a。
日常改进和退货的项目按照SGxx—yyyy—zzzz, 其中xx表示年份,yyyy是流水号,zzzz是工厂产品型号;b客户投诉按照CCxx—yy—zz—-mm,其中xx表示年份,yy是客户名称,zz表示产品型号,mm表示流水号。
8D报告范例

Responsible(负责人)
StandardiБайду номын сангаасation(标准化)
D8 Problem Close (问题关闭)
Responsible(负责人)
Prepared By/Date:
Approved By/Date:
备注:正常情况下,外协厂商请在3个工作日内完成,除非得到许可。 Remark:Normally,Please complete this report within 3 working days for local supplier,unless HT QE agreed。
Name(姓名)
Emergency Response Action(紧急应变行动)
D3 Emergency Response Action Effectiveness(有效性) (紧急应变行动)
Division(部门) Responsible(负责人) Responsible(负责人)
Escape cause investigation(流出原因分析)
Responsible(负责人)
Rootcause Analysis(产生原因分析) D4 Failure Analysis (失效分析)
Systemic cause Analysis(系统面原因分析)
Responsible(负责人) Responsible(负责人)
Corrective action(纠正行动)
D5 Corrective action
(纠正行动)
Responsible(负责人)
Preventive action(预防措施)
D6 Preventive action
(预防措施)
8D报告模板及实例

完成时间:2014-6-13
完成情况:已完成 完成情况:进行中
什
对
发现此问题前,产品成品检验方式为检具测量,由于产品不良问题点基本在产品冲扁部位中段,而检具检
验不能够保证100%测量到中段部位。中间不良,两头尺寸合格的不良品,照样能通过检具检验,所以无法 对包装检验人员进行测量指导,减少检具厚度,使检具能够测量到产品冲扁部位中段,有效的检验出中段尺寸不合格的不良品,另
备注
发现时间 XXX 发现人员 客户IQC 发现地点 客户进料区
类别 普通□ 较重□ 严重□ 缺陷图片:
说 --48小时无结果 72小时无结果
明 首次发生 重复发生
三次以上发生
管理层支持
部门经理
厂长 总/副总经
理
顾客现场
2400
现场挑选不良品
XXX
已完成
成品库
1955
调出库存,返工卡尺全检
XXX
已完成
2.冲边:改前:3.2 ,改后:3.2+0.08/-0.05 ;
3.冲孔:改前:3.2 ,改后:3.2±0.08
; 更改冲边,冲孔公差,弥补产品在冲边,冲孔过程中减少的厚度差,对产品
生
签
XXX
加工过程进行监督测量,避免不良影响,减少不良品的产生。 责任人:XXX 完成时间:2014-6-13 完成情况:进行中
XXX
货,并在外箱标示“已全检”
XXX
2014/6/6 进行中
XXX
D4.
(4 D5.
(4
根为 什
8小 1.为保证提升检具通过率,减少冲边模损耗故首件尺生产时调机按照为公差的中下限进行调整,下限公差 在生产过程中出现偏差。
确 针
8D报告-模板

是否
不合
是否1问题
有NA
234567123456
123456
8D报告
零件号(内部)问题说明零件号(客户)零件名称发现时间发现地点来源/发现人问题零件数量零件追溯信息是否发布质量警示?
发布位置:
2.解决小组姓名
部门
职责
起始日期:
1.问题描述
责任人/组长问题解决目标&目标时间:小组成员1小组成员2小组成员3目标时间小组成员4小组成员5小组成员6
目标时间3. 遏制结果汇总(详细遏制信息见附件遏制表)总数
比例
遏制起止日期:遏制零件信息
4.根本原因分析
不适用
说明、再确认或验证结果
原因分析工具
操作是否正确?
鱼刺图工装夹具防错装置有效?矩阵表零件是否用错?5WHY
过程中是否有更改?产品设计是否有更改?分零件是否合格?5.纠正措施 (25%-已识别;50%-有效性确认;75%-执行;100%-完成)责任人
计划日期
实际日期
状态
顾客端内部草图或图片(失效+合格)
对失效测量/评估方法(包括能力)发生原因流出原因
问题严重性
作业
检验防错&
是否是否是否是否是
否
批准
6.效果验证文件更新与验证记录
过程流程图PFMEA 控制计划分层审核
培训
过程能力
其他(请注明):
7.横向展开&经验教训
8. 问题关闭
职能姓名
同意关闭批准日期
质量部经理生产部经理技术部经理商务部经理工厂经理。
中文8D报告模板

XT
(1)
(2)原始缺陷照片
是否具体
责任2.遏
分类
可能存在的数
量
区域确认人可疑品发现的数量可疑品处置确认人
供应商
原料在制品完成品在途公司内部
原材料库实验室现场在制品返工区待入库区成品库装箱区已出库
在途
纠正/预防措施表(8D报告) A/0
1.不合格现象/趋势描述:产品名称(产品代码)缺陷现象发现时间?缺陷数量/比例?
缺陷产品批次号谁发现此缺陷?哪里发现?(具体工位)是否
责任部门/责任人:
完成日期:
责任
部
门
/
责
任
人:
完成日期:责任部门/责任人:完成日期:
8.水平展开情况:
责任部门/责任人:
完成日期:
SQ E :
6. 涉及需更改的文件:
7. 效果验证(包括措施有效性、文件化等,按限制时间进行效果验证,如有,后附证明资料):
同类产品排查
相关文件/台帐更新
其它
建立/进入经验教训库工艺流程图
FMEA 控制计划工艺单
订货技术要求标准作业指导书设备文件产品标识方法搬运操作规程检验计划
包装作业指导书检具操作说明
其它文件及记录。
8D报告格式

8D报告格式8D报告模板一:1.问题描述:1.1.客户投诉或内部发现的问题;1.2.问题具体描述,包括具体现象和影响。
2.团队成员:2.1.参与问题解决的团队成员及其职责。
3.问题分析:3.1.问题发生的原因分析,采用鱼骨图或5W1H等工具进行分析;3.2.原因分析的结果,确认问题的根本原因。
4.校正措施:4.1.提出解决问题的校正措施;4.2.校正措施的具体步骤和实施计划。
5.短期纠正措施:5.1.通过临时措施或短期措施,解决当下的问题;5.2.短期纠正措施的实施过程和效果。
6.根本原因分析及长期纠正措施:6.1.对根本原因的深入分析,找出问题的真正原因;6.2.提出长期纠正措施,预防问题再次发生;6.3.长期纠正措施的实施过程和效果。
7.预防措施:7.1.针对类似问题的预防措施,提出改善建议;7.2.预防措施的实施计划和跟踪。
8.效果评估:8.1.对校正措施和纠正措施的效果进行评估;8.2.统计数据和客户反馈等证据支持。
9.改进机会:9.1.在问题解决过程中发现的改进机会;9.2.提出改进机会的可行性分析和实施计划。
10.结论:10.1.总结报告的最终结果和影响;8D报告模板二:1.问题描述:1.1客户投诉或内部发现的问题;1.2问题的具体描述,包括具体现象和影响。
2.团队成员:2.1参与问题解决的团队成员及其职责。
3.问题分析:3.1问题发生的原因分析,采用鱼骨图或5W1H等工具进行分析;3.2确认问题的根本原因。
4.纠正措施:4.1提出纠正措施,解决当下的问题;4.2纠正措施的具体步骤和实施计划。
5.短期纠正措施:5.1通过临时措施或短期措施,解决当下的问题;5.2短期纠正措施的实施过程和效果。
6.根本原因分析及长期纠正措施:6.1对根本原因的深入分析,找出问题的真正原因;6.2提出长期纠正措施,预防问题再次发生;6.3长期纠正措施的实施过程和效果。
7.效果评估:7.1对纠正措施和长期纠正措施的效果进行评估;7.2统计数据和客户反馈等证据支持。
8D报告经典模板

8D报告经典模板8D报告经典模板第一部分:问题描述(约200字)1. 问题简述:对问题进行概括性说明。
2. 问题细节:对问题的具体情况进行详述。
3. 问题影响:对问题可能产生的影响进行描述,如对产品质量、客户满意度、生产效率的影响等。
第二部分:立即采取的临时措施(约200字)1. 立即采取的措施:对于问题出现后,立即采取的缓解措施,如停机检查、切换备件、调整生产计划等。
2. 控制措施效果:对采取的措施进行分析,效果是否达到预期?第三部分:问题原因分析(约700字)1. 问题根本原因:对问题发生的根本原因进行分析。
可以采用五问法等方法来确定根本原因。
2. 问题追溯:对问题产生过程进行回放,并追溯问题的出现原因,以分析问题的发生及演变过程。
3. 原因分析工具:对常见原因分析工具进行描述,如Pareto 图、鱼骨图等,并举例说明如何运用工具进行分析。
第四部分:解决方案的提出(约700字)1. 解决思路:对问题进行思路的梳理和总结,梳理可能的解决方案。
2. 方案评估:对各个解决方案进行评估,考虑实施难度,成本,效果等因素,结合实际情况,选出可行的解决方案。
3. 实施计划:对选定的方案进行具体实施计划的制定,包括时间、流程、责任人等。
第五部分:解决方案的实施与效果(约700字)1. 方案实施:对解决方案的实施情况进行详细讲述,考虑实施过程中可能遇到的问题,如何解决等。
2. 效果评估:通过数据分析、对客户满意度、产品质量等的评估来判断实施效果是否达到预期。
如果未达到预期,需要进行调整,重新实施,直到达到预期效果为止。
第六部分:预防措施(约200字)1. 预防措施的提出:通过对问题解决的总结,结合以往类似问题的经验,对预防措施提出建议和方案。
2. 预防措施的实施:对预防措施的实际实施进行具体详细的讲述,考虑如何防止问题再次出现,减少可能发生的影响。
第七部分:经验教训(约300字)1. 案例分析:通过对本次问题的分析,总结出经验和教训。
8D报告模板

3. Revise FMEA?
Yes:
Document No.:
No :
Statement:
4. Revise Control Plan?
Yes:
Document No.:
No :
Statement:
5. Revise SOP?
Yes
Document No.:
No :
D8)Congratulate the Team and estimate the beneficial result if necessary. (效益评估)
(Note: Recognize the collective efforts of the team.)
1.CoPQ (total cost):暂无
D5)Corrective Action Verification(驗證改善對策)
(Note: Be make sure the corrective actions is effective in process as well as able to fix the customer complaint problem)
(Note: Internal / external containment action effectiveness and date.)
1.
D4)Define and Verify Root Causes(詳細說明與驗證根本原因)
(Note: Identify and verify all suspect causes, which needs explain why the problem occurred.)
D6)Implement Permanent Corrective Actions(執行永久對策)
品质8D报告标准模板

品质8D 报告标准模板
小组负责人:管理者代表:8D 报告对象:
客户 供应商 公司内部报告编号:品质严重性: 非常严重 严重 轻微
报告日期: 客户/ 供应商名称:
涉及报告或文件:D1:成立改善
小组
D2:问题描述问题描述问题图片
1.
2.
3.
4.
D3:临时措施序号
临时措施要点及描述责任人完成日期结果确认
12
3
4
D4:根本原因
分析序号根本原因描述与分析责任人完成日期结果确认12
3
4
D5:永久性纠正措施序号永久性纠正措施描述责任人完成日期结果确认1
2
3
4
D6:纠正措施验证
序号纠正措施实际验证情况责任人完成日期结果确认1
2
3
4
D7:预防措施序号
预防措施具体描述责任人完成日期结果确认12
3
4
D8:批量验证/
团队激励
此项目原因分析准确,制定的永久性纠正措施验证可行有效。
承认小组的集体努力,对小组工作进行总结并祝贺,同时给予必要的物质和精神奖励。
- 1、下载文档前请自行甄别文档内容的完整性,平台不提供额外的编辑、内容补充、找答案等附加服务。
- 2、"仅部分预览"的文档,不可在线预览部分如存在完整性等问题,可反馈申请退款(可完整预览的文档不适用该条件!)。
- 3、如文档侵犯您的权益,请联系客服反馈,我们会尽快为您处理(人工客服工作时间:9:00-18:30)。
当事人:问题发生时间:年月日设备和生产所属部门: 4D截止日期:年月日□管理问题地点: 8D截止日期:年月日□市场及销售问题编号:问题关闭日期:年月日□声誉及法律1.
组建团队倡导者:
姓名所属部门及职位电话
其他小
组成员:
2.问题描述(定义)
负责人:
日期:问题描述(是什么、何时、何地、多少、严重程度等方面描述问题)
什么何时何地出现什么状况,数量频率(量化数字),正常状况应该是什么,现状离正常状况差距有多少,处于什么样的严重程度。
影响(识别潜在的对设备及生产、技术及工艺、经济及效益、管理、公司声
誉形象、法律纠纷等的影响)
该问题直接影响什么,将导致什么后果,受其牵连,什么将会怎么样,问题
如果继续扩大或恶化,将会导致什么样的后果。
涉及的对象(客户、政府部门、公司部门和供应商)
该问题涉及哪些部门,其中问题当事部门,问题参与部门,问题影响部门。
3.临时措施
负责人:实施日期:采取了什么临时处置措施(包括应急措施)。
为了避免问题的进一步发展扩大及恶化,根据初步掌握的状况采取哪些措施。
采取临时措施依据及标准实施临时措施的时间采取这些措施的依据,运行指标应控制在什么样的
范围(标准)。
何时开始实施。
其他地方是否存在类似问题?正常状况标识?
其他地方存在的类似问题。
那些地方的正常状况应该是什么。
4.根本原因为何产生该问题?怎样验证?(人机料法环测,5W法,脑力激荡法,三现法)
8D问题分析报告
负责人:日期:根据问题状况(图象分析、指标数据等),导致该问题发生的原因为什么(可以用鱼骨图法表示),根本原因应该是什么。
根据推断,应该或可能是先发
生什么,接着发生什么,在什么情况下进一步发生什么,最终导致问题的
发生。
问题是否及时被发现?为什么未能及时发现?
问题发展到什么阶段才被发现(隐患阶段、未遂先兆阶段、轻微阶段、严重
阶段),是何原因导致没有在未遂先兆阶段之前发现。
5.解决方案负责人:日期:对问题采取的纠正措施
针对导致问题发生的每个原因,制定以下一系列措施:……
特别是针对主要原因制定以下措施:
……
对问题未能及时发现采取的纠正措施
针对问题未能及时发现采取什么措施。
6.解决方案验证
负责人:
日期:验证已实施的措施是否将问题彻底消除
根据解决方案运行过程的各个环节的定期检查,现状指标为多少,问题解决前为多少,正常状况为多少。
该方案对问题的解决程度为多少。
结果验证日期如何标识正常状况?
方案运行结果验证日
期
正常状况各指标为多少。
7.预防问题再次发生(制度化)将来如何避免此类问题?
为防止此类问题再次发生应该制定什么措施,应该形成什么制度(制定新制度、对现有制度进行补充或修订)来确保措施的执行效果。
其他存在此类问题的地方/产品
名称追踪及解决方法最终期限
存在此类问题的地
方/产品
谁追踪及解决,采用什么方法。
类似问题解决期
限
制度化(分析报告后面附上制度化内容详细资料)
制度化内容负责人完成时间作业流程改善:制度标题
技术及工艺改善:制度标题
其他: 制度标题
8.问题关闭关闭声明(总结经验,表扬&解散团队)
经验:XX。
教训:XX。
本问题解决过程中团队小组成员付出了很多,特别是XXX表现最突出,在关
键问题的发现及解决方面起到了关键作用。
填写人:核实人:
8D问题详细分析报告
一、问题及团队
1、问题
问题名称。
2、团队
解决问题的团队成员:
具体分工
倡导者(负责8D程序进程跟踪及控制、会议召集):
文员(负责会议记录、材料汇总及整理):
其他成员分工……
二、问题描述
1、问题的产生
是什么、何时、何地、多少、严重程度等方面描述问题。
2、问题的影响
详细剖析问题对设备生产、技术工艺、经济效益、管理、公司声誉形象、法
律纠纷等的影响。
3、问题涉及的对象
和问题的发生有关联或将受到问题的影响的对象,如:客户、政府部门、公
司部门和供应商。
三、临时措施
为了防止问题的负面影响扩大或者是问题进一步恶化,采取什么临时处置
措施(包括应急措施),采取临时措施的依据及标准,何时开始实施临时措施。
及时调查其他地方是否存在类似问题?正常状况应该如何?
四、根本原因
1、原因查找
采用脑力激荡法查找可能原因:团队成员分头去调查问题相关人员,在规定
时间汇总可能原因。
相关检测数据及资料收集。
2、原因分析
针对汇总的可能原因进行关联分类,并采用鱼骨图法将分类的可能原因表示
出来,并针对这些可能原因进行分析验证(查找产生原因的依据数据及资料),去除伪原因,对确定的原因采取5W法(5问法:原因、原因的原因、原因的原因的原因、……)揭示更深层次的原因。
最后用鱼骨图法将分类的真原因表示
出来。
生产类问题原因寻找及分析鱼骨图:
管理类问题原因寻找及分析鱼骨图:3、问题发生过程推断模拟
根据推断,应该或可能是先发生什么,接着发生什么,在什么情况下进一步发生什么,最终导致问题的发生。
2大要因
1大要因
4大要因
3大要因
2.1中要因
4.1中要因
1.1中要因
3.1中要因
2.1.1小要因
问题
2.2中要因
问题人
原因
原因
原因
机器
原因
原因
原因材料
原因
原因
原因测量
原因
原因
原因
环境
原因原因
原因
方法
原因原因
原因
问题
执行原因原因
原因
合作方原因原因
原因
沟通协调原因原因
原因
制度标准
原因
原因
原因
工作流程
原因
原因
原因
个人主观
原因
原因
原因
4、问题发现机制
说明问题是如何发现的,处于什么阶段(隐患阶段、未遂先兆阶段、轻微阶段、严重阶段),分析这种发现方法是否合理?问题是否及时被发现?为什么未能及时发现?
五、解决方案
1、对问题采取的纠正措施
针对每个原因制定解决办法,最后综合成解决问题的方案。
2、问题发现机制的完善对问题未能及时发现采取的纠正措施。
六、解决方案验证
确定问题各个环节的正常状况,解决方案试行过程中定期检查各个环节的
指标和正常状况的差距,判断问题的解决程度,进而确定是否再次寻找新原因
和制定新解决方案。
七、预防问题再次发生(制度化)1、防止类似问题再次发生
根据原因分析及解决方案的验证结果,确定防止此类问题再次发生的方法,制定(或修改、补充)相关制度确保解决方案能够常态化运行(明确制度制定负责人及完成时间),相关制度见附件。
2、其他存在此类问题的地方或产品的解决
将本问题的解决方案应用到其他存在此类问题的地方或产品的解决,确定追踪及解决方法,设定问题解决的期限。
八、问题关闭1、总结
宣布8D 流程的结束。
针对8D 程序运行过程中的经验和教训进行分析总结,即对8D 程序运行过程中哪些环节和方法做得好,哪些做得不好,为什么?下次应该如何进行?2、表彰
针对问题解决过程中团队成员的努力和付出进行表彰,特别是解决问题过程中涌现出来的能人,要重点表彰和培养。
制度附件:
2大办法
1大办法
4大办法3大办法 2.1中办法
4.1中办法
1.1中办法
3.1中办法 2.1.1小办法
如
何
去
做
2.2中办法
关于XXX的管理办法
……
关于YYY的管理办法。