FMEA21
过程FMEA有关注意事项
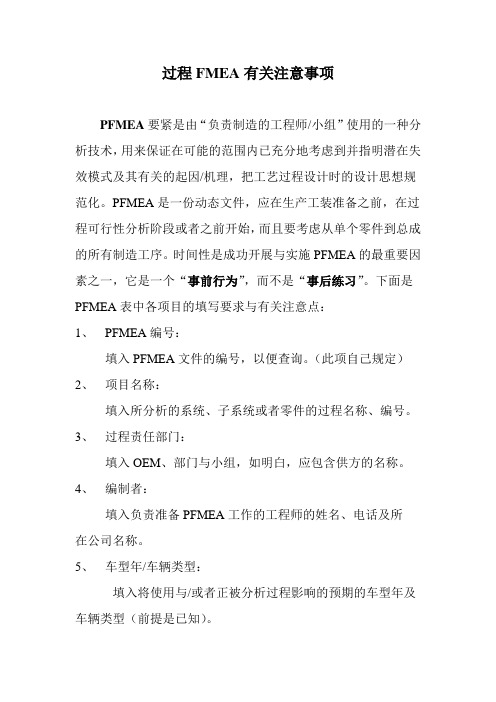
过程FMEA有关注意事项PFMEA要紧是由“负责制造的工程师/小组”使用的一种分析技术,用来保证在可能的范围内已充分地考虑到并指明潜在失效模式及其有关的起因/机理,把工艺过程设计时的设计思想规范化。
PFMEA是一份动态文件,应在生产工装准备之前,在过程可行性分析阶段或者之前开始,而且要考虑从单个零件到总成的所有制造工序。
时间性是成功开展与实施PFMEA的最重要因素之一,它是一个“事前行为”,而不是“事后练习”。
下面是PFMEA表中各项目的填写要求与有关注意点:1、PFMEA编号:填入PFMEA文件的编号,以便查询。
(此项自己规定)2、项目名称:填入所分析的系统、子系统或者零件的过程名称、编号。
3、过程责任部门:填入OEM、部门与小组,如明白,应包含供方的名称。
4、编制者:填入负责准备PFMEA工作的工程师的姓名、电话及所在公司名称。
5、车型年/车辆类型:填入将使用与/或者正被分析过程影响的预期的车型年及车辆类型(前提是已知)。
6、关键日期:填入初次FMEA预定完成的日期,该日期不应超过计划开始生产的日期。
7、PFMEA日期:填入编制PFMEA原始稿的日期及最新修订的日期。
8、核心小组:列出责任部门与个人姓名。
9、过程功能/要求:简单描述被分析的过程或者工序。
尽可能简单地说明该过程或者工序的目的,如过程(如装配)包含许多具有不一致潜在失效模式的工序,那么可把这些工序作为独立过程列出。
10、潜在失效模式:潜在失效模式是指过程可能发生的不满足过程要求与/或者设计意图的形式,是对某体工序不符合要求的描述。
它可能是引起下道工序的潜在失效模式的起因,也可能是上道工序潜在失效的后果。
根据零件或者过程特性,对应特定的工序,列出每一个潜在失效模式(前提是假设这种失效可能发生,但不一定必定发生)。
在此应注意两个问题:** 过程/零件怎么不能满足规范?** 假设不考虑工程规范,顾客会提出什么异议?11、潜在失效后果:潜在失效后果是指失效模式对顾客的影响。
五大手册之FMEA介绍
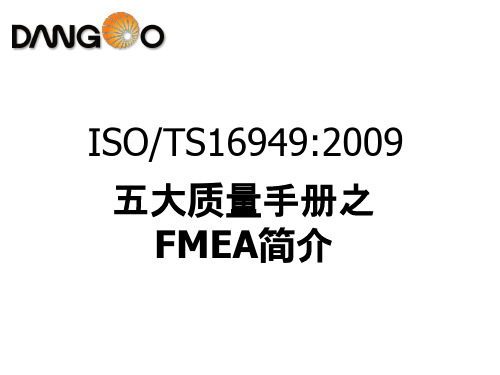
危险(没有征兆的)
危険(有征兆的) 非常高 高 还可以 低 非常低 轻微 非常轻微 没有
导致人身事故(破裂,发火,发热)
导致物品损害事故(破裂,发火,发热) 灯泡不可点亮,客户的产品无法使用. 灯泡可以点亮,但寿命低下。 大部分的顾客感到不满. 灯泡可以点亮,但配光或光通量达不到客户要求。 一部分的顾客感到不满. 安全性、电气特性正常。明显的外观问题。 没有明显外观问题,但是比轻微外观问题严重的 细小伤痕,污点等外观问题. 在工程内可能修正的 没有影响.没有人注意到
FMEA-参考手册
9
由北美三大汽车公司(克莱斯勒、福特和通用)FMEA工 作组编写;是一本设计FMEA和过程FMEA的开发指南; 目的不在于定义要求,而是在于阐明FMEA技术开发中的 问题;
1993年2月发布第一版;1995年2月发布第二版; 2001年7月发布第三版;2008年6月发布第四版; 2001年11月发布《设备和工装潜在失效模式及后果分析 (MFMEA )》第一版; 手册提供了应用 FMEA 技术的总体指南,但并没有给出 如何完成每一 FMEA 项目的具体说明,也不是综合性的 参考资料或培训资料。
A
B
C C C C
基准说明 不能测出结果或不检查 只通过间接或抽查来控制 只通过目视检查来控制
评 分 10 9 8
非常低
低 中等 中高等 高 非常高
控制方法测出的机会少
控制方法可能测出 控制方法可能测出 控制方法测出的机会高 控制方法测出的机会高 肯定能测出 A A A B B B B B
C
C
只通过双重目视检查来控制
DFMEA是产品设计和开发(第二阶段)的输出之一 PFMEA是过程设计和开发(第三阶段)的输出之一 PFMEA是CP的输入及指导依据 文件流程:特殊特性清单、过程流程图、特殊特性矩阵图、 FMEA、CP、PCM(如TRW要求)、SOP
FMEA新版手册
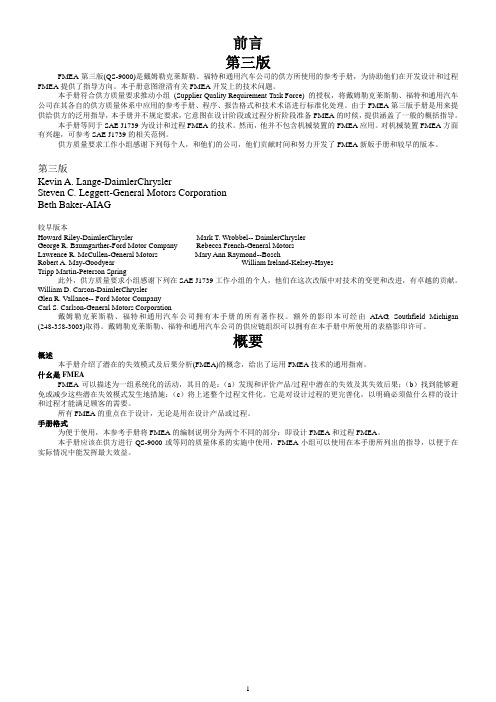
前言第三版FMEA第三版(QS-9000)是戴姆勒克莱斯勒、福特和通用汽车公司的供方所使用的参考手册,为协助他们在开发设计和过程FMEA提供了指导方向。
本手册意图澄清有关FMEA开发上的技术问题。
本手册符合供方质量要求推动小组(Supplier Quality Requirement Task Force) 的授权,将戴姆勒克莱斯勒、福特和通用汽车公司在其各自的供方质量体系中应用的参考手册、程序、报告格式和技术术语进行标准化处理。
由于FMEA第三版手册是用来提供给供方的泛用指导,本手册并不规定要求,它意图在设计阶段或过程分析阶段准备FMEA的时候,提供涵盖了一般的概括指导。
本手册等同于SAE J1739为设计和过程FMEA的技术。
然而,他并不包含机械装置的FMEA应用。
对机械装置FMEA方面有兴趣,可参考SAE J1739的相关范例。
供方质量要求工作小组感谢下列每个人,和他们的公司,他们贡献时间和努力开发了FMEA新版手册和较早的版本。
第三版Kevin A. Lange-DaimlerChryslerSteven C. Leggett-General Motors CorporationBeth Baker-AIAG较早版本Howard Riley-DaimlerChrysler Mark T. Wrobbel-- DaimlerChryslerGeorge R. Baumgarther-Ford Motor Company Rebecca French-General MotorsLawrence R. McCullen-General Motors Mary Ann Raymond--BoschRobert A. May-Goodyear William Ireland-Kelsey-HayesTripp Martin-Peterson Spring此外,供方质量要求小组感谢下列在SAE J1739工作小组的个人,他们在这次改版中对技术的变更和改进,有卓越的贡献。
FMEA失效分析与失效模式分析全

擦伤或损坏)。 由于横向性能差而在锻件中出现分离线的失效现象。
11
在服役条件下由于质量恶化而产生失效的原因包括
过载或未预见的加载条件。 磨损(磨蚀、因过度磨损而咬住、粘住、擦伤、气蚀)。 腐蚀(包括化学接触、应力腐蚀、腐蚀疲劳、脱锌、铸铁石
找出被分析对象的“单点故障”。所谓单点故障是指这种故障单独发 生时,就会导致不可接受的或严重的影响后果。一般说来,如果单点 故障出现概率不是极低的话,则应在设计、工艺、管理等方面采取切 实有效的措施。产品发生单点故障的方式就是产品的单点故障模式。
为制定关键项目清单或关键项目可靠性控制计划提供依据。 为可靠性建模、设计、评定提供信息。 揭示安全性薄弱环节,为安全性设计(特别是载人飞船的应急措施、
16
什么是失效分析?
失效分析:考察失效的构件及失效的情景(模式), 以确定失效的原因。
失效分析的目的:在于明确失效的机理与原因。改 进设计、改进工艺过程、正确地使用维护。
失效分析的主要内容:包括明确分析对象,确定失 效模式,研究失效机理,判定失效原因,提出预防 措施(包括设计改进)。
17
失效分析的要点?
失效模式的判断分为定性和定量分析两个方面。在一般 情况下,对一级失效模式的判断采用定性分析即可。而 对二级甚至三级失效模式的判断,就要采用定性和定量、 宏观和微观相结合的方法。
19
一级失效模式的分类
20 主要失效模式的分类与分级
21
如某型涡轮叶片在第一榫齿处发生断裂,通过断口 的宏观特征可确定一级失效模式为疲劳失效。然后 通过对断口源区和扩展区特征分析和对比,并结合 有限元应力分析等,可作出该叶片的断裂模式为起 始应力较大的高周疲劳断裂的判断,即相当于作出 了三级失效模式的判断。
2019年新版FMEA手册(中文版)
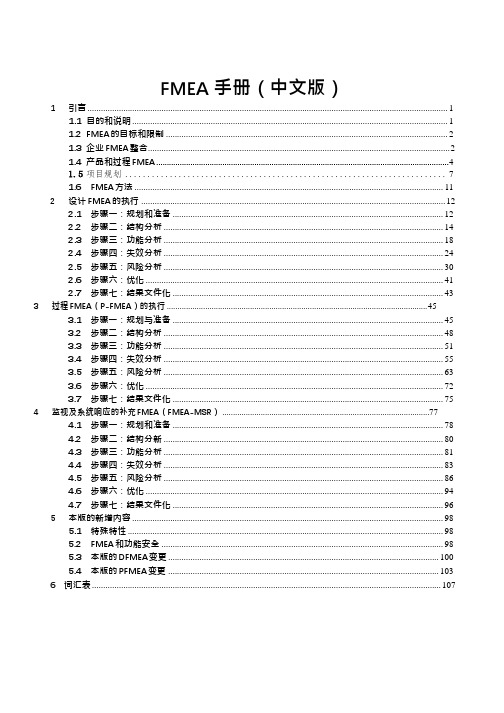
FMEA 手册(中文版)1引言 (1)1.1目的和说明 (1)1.2FMEA 的目标和限制 (2)1.3企业FMEA 整合 (2)1.4产品和过程FMEA (4)1.5项目规划 (7)1.6FMEA 方法 (11)2设计FMEA 的执行 (12)2.1步骤一:规划和准备 (12)2.2步骤二:结构分析 (14)2.3步骤三:功能分析 (18)2.4步骤四:失效分析 (24)2.5步骤五:风险分析 (30)2.6步骤六:优化 (41)2.7步骤七:结果文件化 (43)3过程FMEA(P-FMEA)的执行 (45)3.1步骤一:规划与准备 (45)3.2步骤二:结构分析 (48)3.3步骤三:功能分析 (51)3.4步骤四:失效分析 (55)3.5步骤五:风险分析 (63)3.6步骤六:优化 (72)3.7步骤七:结果文件化 (75)4监视及系统响应的补充F MEA(FMEA-MSR) (77)4.1步骤一:规划和准备 (78)4.2步骤二;结构分新 (80)4.3步骤三:功能分析 (81)4.4步骤四:失效分析 (83)4.5步骤五:风险分析 (86)4.6步骤六:优化 (94)4.7步骤七:结果文件化 (96)5本版的新增内容 (98)5.1特殊特性 (98)5.2FMEA 和功能安全 (98)5.3本版的DFMEA 变更 (100)5.4本版的PFMEA 变更 (103)6 词汇表 (107)1引言本联合出版物是美国汽车工业行动集团(AIAG)与德国汽车工业联合会(VDA)的整车厂(OEM)和一级供应商成员合作逾三年的成果。
本手册已进行改写,并在几个关键领域对 FMEA 方法进行了修订。
其目的是为这些组织所代表的汽车行业提供 FMEA 通用基础知识。
尽管我们尽了最大努力以达成共识,但可能仍有必要参考特定公司的出版物或顾客特定要求(CSR)。
一种新方法:本手册增加一个新的 FMEA 类别,即监视及系统响应 FMEA (FMEA-MSR)。
FMEA标准手册

FMEA标准⼿册FMEAPotential Failure Mode and Effect Analysis 潜在失效模式与后果分析概要概述本⼿册介绍了潜在失效模式及后果分析(FMEA)的概念,给出了运⽤FMEA技术的通⽤指南。
FMEA可以描述为⼀组系统化的活动,其⽬的是:1)发现、评价产品/过程中潜在的失效及其后果;2)找到能够避免或减少这些潜在失效发⽣的措施;3)将上述过程⽂件化。
它是对设计过程的完善,以明确什么样的设计才能满⾜顾客的需要。
历史虽然⼯程技术⼈员早已在其设计和制造过程中应⽤了类似FMEA形式的分析⽅法,但第⼀次正式地应⽤FMEA则是六⼗年代中期航天⼯业的⼀项⾰新。
⼿册格式为便于使⽤,本⼿册将FMEA的编制说明分为两个不同的部分,即设计FMEA和过程FMEA。
在同⼀⼿册中介绍两种FMEA,有助于对⽤于制定不同类型FMEA的技术进⾏⽐较,以便更清楚地说明它们的正确应⽤及其相互关系。
FMEA的实施由于尽可能持续改进产品质量应是⼀个企业的承诺,所以将FMEA作为专门的技术应⽤以识别并帮助消除潜在隐患⼀直是⾮常重要的。
对车辆回收的研究结果表明,全⾯实施FMEA 能够避免许多回收事件的发⽣。
虽然在FMEA的编制⼯作中,每项职责都必须明确到个⼈,但是要完成FMEA还得依靠⼩组努⼒。
⼩组应由知识丰富的⼈员组成,如设计、制造、装配、服务、质量及可靠性等⽅⾯有丰富经验的⼯程技术⼈员。
时间性是成功实施FMEA的最重要因素之⼀,它是⼀个“事前⾏为”,⽽不是“事后练习”。
为达到最佳效益,FMEA必须在设计或过程失效模式被⽆意地纳⼈设计产品之前进⾏。
事先花时间很好地进⾏综合的FMEA分析,能够容易、低成本地对产品或过程进⾏修改,从⽽减轻事后修改的危机。
FMEA能够减少或消除因修改⽽带采更⼤损失的机会。
适当地加以应⽤,FMEA是⼀个相互作⽤的过程,永⽆⽌境。
设计FMEA简介设计FMEA主要是由“负责设计的⼯程师/⼩组”采⽤的⼀种分析技术,⽤来保证在可能的范围内已充分地考虑到并指明各种潜在的失效模式及其相关的起因/机理。
MFMEA培训教材 - 设备FMEA
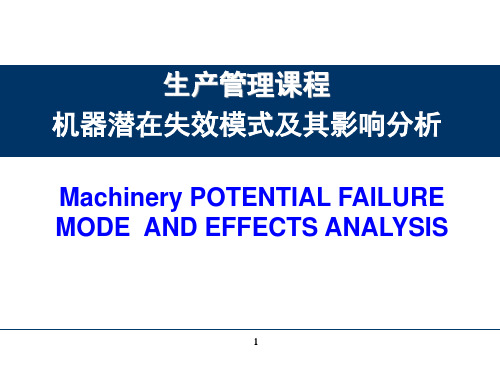
30
8.核心小组
•列出所有被授权识别和执行任务的负责人姓名及所在部门(建议包含 所有成员的姓名,部门,电话号码,地址等)。
9a.子系统名称
输入对被分析的子系统名称的描述。
自动装货设备,锭子,水力的,电子的,工作站-5-左边。
设备等级术语
24
MFMEA是一份动态的文件,应: •在一个设计概念最终形成之时或之前开始 •在设备开发的各个阶段,发生更改或获得更多的信息时,持续予
以更新 •在设备图样完工之前全部完成
考虑到制造/装配需求已经包容在内,MFMEA针对设计意 图并且假定该设计将按此意图进行生产/装配。制造或装配过程 中可能发生的潜在失效模式和/或其原因/机理不需、但也可能 包括在MFMEA 当中。
17
3. 先前的或相似的数据 •设备故障清单(故障现象、故障原因、发生的频次) •由于设备设计不良、设备故障的原因导致的产品缺陷的现象和频率 •发生人身伤害的现象和次数 •售后服务数据 4. 报告(由供应商准备) •服务调查报告(SIRS) •经销商问题报告 •售后服务报告 •实验室测试报告
18
•耐久性测试报告 •拆卸报告 5.其他FMEA •之前的/类似的设计FMEA •之前的/类似的过程FMEA
下前车管
下后车管
功能及性能要求 用尽可能简明的文字来说明被分析项目满足设计意图的功能。当
子系统必须在特定条件下运行时,对条件的描述是有益的。条件可以 包含环境参数,工程要求和/或设备功能规范(例如:运行温度,性 能,周期时间,平均故障时间,平均维修时间和其他可度量的工程属 性)。如果该项目有多种功能,且有不同的失效模式,应把所有的功 能单独列出。 例如: 切削加工外径 :外径尺寸符合图纸要求;表面粗糙度符合要 求 。 印刷图案:图案清晰、 位置正确 吸除灰尘:除尘彻底 清洗玻璃表面:表面清洗无灰尘和印迹
FMEA教材-正版.pdf

一、产品风险与可靠度
汽车工业的质量管理系统: TS16949,QS9000为汽车工业的品质管理系统,其以持续改 进为目标,强调缺点预防,降低品质差异,减少生产过程的 浪费与废弃物。
面对市场开放与日本的竞争压力,美国福特、克莱斯勒、通 用汽车等三大汽车厂共同主导制定QS9000品质系统,并结 合美国品管学会(ASCQ)与车辆工程学会(SAE),开始研究 如何将可靠度之失效预防观念工程技术导入汽车业。
改善现有之可靠度工程分析工具(如FMEA、FTA等)作为 前端工程作业,以提高开发产品过程中之工程决策支援,并 发展新的前端工程分析工具。
3
一、产品风险与可靠度
汽车工业的质量管理系统之各种作业程序与参考手册,成为美国 汽车工业共同的作业准则,其将被TS16949替代并已成为全世界 汽车行业共同规范。 工程人员普遍缺乏整体系统开发观念,前端工程分析作业无法连 贯,分析工作变成多余而无效的,造成许多在研发初期就应该作 好的预防工作,却要等到进入原型生产才能提出修改建议进行矫 正。如此,不仅浪费时间,而且浪费资源、金钱。 必须有整体性的规划,并且循序渐进地逐步改善企业的研发环境
有些 我先 是必需的!有些 所以没有 是可预期避免的
核电厂、水库、卫星、飞机、十大召回事件… …
有效运用 FMEA 可减少事后追悔
8
二、FMEA的基本概念
及时性是成功实施FMEA的最重要因素之一。 它是“事前的预防”而不是“事后的追悔”。 事先花时间进行FMEA分析,能够容易且低成本地对产品设计或 制程进行修改,从而减轻事后修改的危机。 FMEA能够减少或消除因修改而带来更大损失的机会,它是一个 相互作用的过程,永无止境的改善活动。
10
二、FMEA的基本概念
5大工具《FMEA失效分析(最新教材)》
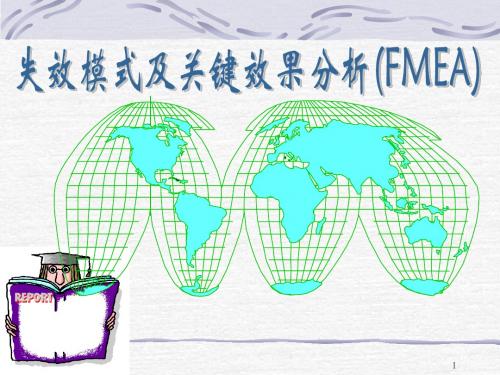
潛在失效模式及後果分析
嚴重度(S) 嚴重度(S) – (續) 很高(8) 生產線嚴重破壞,可能100%的產品需報廢, 系統無法運行,喪失基本功能,顧客不滿意 高(7) 生產線破壞不嚴重,產品需篩選部分(低於 100%)報廢,系統能夠運行,但性能下降, 顧客不滿意
24
潛在失效模式及後果分析
嚴重度(S) 嚴重度(S) – (續) 中等(6) 生產線破壞不嚴重,部分(低於100%)產品報廢 (不篩選),系統能夠運行,但舒適性或方便性 項目性能失效,顧客有些不滿意 低(5) 生產線破壞不嚴重,產品需要100%返工,系統能 夠運行,但有些舒適性或方便性項目性能下降, 顧客有些滿意
15
6.失效的分类 失效的分类应根据失效原因、危害程度、失效 程度与产生的频率加以分类,一般的分类原则如下:
失效类别 1 致命失效 2 严重失效 3 一般失效 分 类 原 则 危及产品安全,可能导致人身伤亡,或引起重要总成报废,造成 重大经济损失或对周围环境造成重大危害。 影响产品安全,可能导致主要总成、零部件损坏或性能显著下降 且不能用简易工具和备件在短时间(约30min)内修复。 不影响产品安全,造成性能下降,但一般不会导致主要总成及零 部件损坏,并可用简易工具和备件在短时间内(30min)修复。 4 轻微失效 一般不会导致性能下降,不需要更换零件,用简易工具在短时间 (5min)内能轻易排除。
13
一、基本概念 (续)
典型的失效链: 典型的失效链: 路面不平 (不是内在原 因是环境条件) 产生异响 (伴生模式) 水箱支架断裂 水箱后倾 水箱与风扇皮带碰 中间模式 水箱水管断 水箱水泄漏 发动机损坏 冷却系过热 停车 最终模式 …… 根源模式
14
一、基本概念 (续)
FMEA管理规范

1.目的通过分析、预测设计、过程中潜在的失效,研究失效的原因及其后果,并采取必要的预防措施,避免或减少这些潜在的失效,从而提高产品、过程的可靠性。
2.适用范围适用于公司设计FMEA、过程FMEA活动的控制。
3.职责3.1 产品研发部(R&D)负责组织成立DFMEA(设计FMEA)小组,负责DFMEA活动的管理。
3.2 生产技术部(PE)负责组织成立PFMEA(过程FMEA)小组,负责PFMEA活动的管理。
3.3 产品研发部、生产技术部、品管部、生产部、营销部、采购部等部门指定人员参加DFMEA小组、PFMEA小组。
必要时,由品管部邀请供应商、客户参加。
3.4 DFMEA小组负责制定《DFMEA潜在失效后果严重程度(S)评价标准》、《DFMEA潜在失效模式发生概率(O)评价标准》、《DFMEA潜在失效模式发现难度(D)评价标准》。
3.5 PFMEA小组负责制定《PFMEA潜在失效后果严重程度(S)评价标准》、《PFMEA潜在失效模式发生频度(O)评价标准》、《PFMEA潜在失效模式发现难度(D)评价标准》。
4.工作程序4.1 设计FMEA的开发实施4.1.1 DFMEA实施的时机4.1.1.1 按APQP的计划进行DFMEA。
4.1.1.2 在出现下列情况时,DFMEA小组应在产品零件图纸设计之前进行DFMEA活动:①开发新产品/产品更改;②产品应用的环境发生变化;③材料或零部件发生变化。
4.1.2 DFMEA实施前的准备工作①产品研发部(R&D)牵头成立DFMEA(设计FMEA)小组,生产技术部、品管部、生产部、营销部、采购部等部门指定人员参加DFMEA小组,必要时,由品管部邀请供应商、客户参加。
②在DFMEA活动实施前,DFMEA小组应制定出《DFMEA潜在失效后果严重程度(S)评价标准》、《DFMEA潜在失效模式发生概率(O)评价标准》、《DFMEA潜在失效模式发现难度(D)评价标准》。
FMEA全套教程
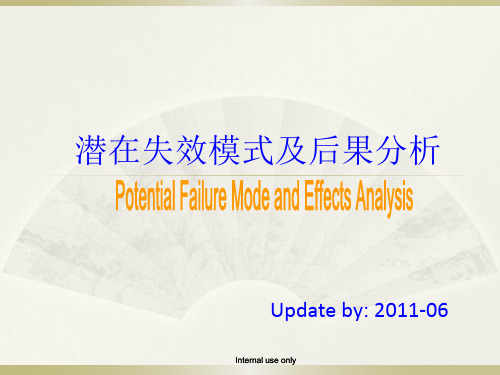
产品可靠性 不好,客户 抱怨
Internal use only
最终模式
1.9 失效链实例(续)
跌落时发生 震动 环境条件
焊锡脱落
根源模式
锡渣碰到线路板
线路板短路
中间模式
电池发热 伴生模式
充电时不能限压
电池发生过充
电池损坏
Internal use only
最终模式
2.0 FMEA工作模式
• 第一步 准备工作 • 第二步 确定失效模式及影响分析 • 第三步 针对失效模式分析原因 • 第四步 确认控制方法
核电厂,水库,卫星,飞机,十大召回事件……
有效运用FMEA可减少事后追悔
Internal use only
早知道….就不会
我先 看了气象预报 我先 评估金融大楼高度 我先 设计电脑防火墙 我先 做好桥梁设计 桥倒塌
所以没有 所以没有 所以没有 所以没有
淋成落汤鸡 影响飞机安全 被黑客入侵 造成重庆彩虹大
Measure
Understand the Process
Analyze
Analyze the Data
Improve
Change the Process
Control
Ensure Performance
Charter
Thought Process Map SIPOC QFD
Process Map
C&E Matrix
2.1.3 DFMEA与PFMEA的联系
● 既有明确分工又有紧密的联系: ● 产品设计部门的下一道工序是过程设计,产品设计应充分考虑可制造与可装配性问题, 由于产品设计中没有适当考虑制造中技术与操作者体力的限制,可能造成失效模式的发 生。 ● 产品设计FMEA不能依靠过程检测作为控制措施 ● PFMEA应将DFMEA作为重要的输入。对DFMEA中表明的特殊特性也必须在PFMEA中作 为重点分析的内容。 PFMEA原则上是在设计能够满足顾客需要的前提下,对过程中的潜在失效模式进行分析。 ● DFMEA的工作不包含在PFMEA中。 ● PFMEA有可能成为设计FMEA中对可制造性和装配性问题的补充,应该反馈到DEMEA中 去.
FMEA基础知识简介

Failure Mode and Effect Analysis
课程内容
• 何为FMEA失效模式与效应分析
• FMEA起源与发展
• FMEA在质量系统上的意义与范畴
• 一般执行FMEA分析方法
• 如何执行FMEA
• FMEA流程展开
• 执行FMEA最大的困难点
•结语
FMEA
2
Failure Mode and Effect Analysis
FMEA项目小组包括:
设计工程人员
RD单位
品管工程人员
QC单位
品保工程人员
QA单位
制程工程人员
ME单位
工艺工程人员
PE
客户服务工程师 CQE
FMEA
22
导入FMEA之先期规划
设计阶段由设计单位主导DFMEA之进行,制造阶段由生产单位主 导PFMEA之进行,没有必要要求每个项目小组人员参加会议,但 是必须提出各阶段之FMEA意见,以免内容失之偏颇。
严重度 难检度 发生率 失效效应 失效模式
改善措施找寻 措施确定
改善前与改善后比较
FMEA
12
FMEA範疇
可靠度预估
可靠度试验
可靠度成长
可靠度配置
客服FMEA
维修FMEA
制造FMEA
设计FMEA
FMEA为可靠度工程的一环,辅助取得可靠度之信息,包括失效模式、寿 命预估等。可区分为设计FMEA、制造FMEA、维修FMEA、客服FMEA等 ,其中以设计FMEA与制造FMEA为主,这两者也是许多客户诉求的重点
必须之模具草图
表面精度之限制
组装空间/加工之进出路径
钢材硬度之限制
FMEA知识测试题目汇总(1)教案资料

1:设计FMEA可以被用于:○清除设计缺陷(倾向于这个)○明确根本原因○识别精益生产的可能性○解决工程问题2:以下哪种情况中,过程FMEA更有效○由过程工程师编辑○由跨功能小组编辑○由管理者代表编辑○由独立的专家编辑3:以下哪项适用于启动FMEA?○供货给OEM的组织○原始设备制造商(比如:制造最终产品)○组织的供应商○Any of the above could initiate an FMEA4:以下哪项描述是正确的○FMEA在整个产品寿命周期进行更新○当开发了控制计划,可以放弃FMEAs○FMEA仅作为产品批准过程的一部分使用○FMEA仅对设计功能重要5:FMEA用来○优化行动的潜在失效○计划测试○分析被退产品○在生产中的不符合之后制定出纠正措施计划6:控制计划中识别的控制是:○至少是那些有设计FMEA决定的○独立于那些过程FMEA识别的○仅那些由过程FMEA决定的○至少是那些由过程FMEA决定的7:过程FMEA假设○根据设计的产品将满足设计意图○在过程FMEA开发期间,设计意图被完全忽略○所有潜在失效模式,包括那些由于设计失效导致的○设计FMEA是完全独立于过程FMEA的8:以下那些描述是正确的?○“分析”一词指对FMEA导致的行动的确认○“模式”一词指起因和失效之间所发生的○“影响”指过程或产品设计的影响○“失效”一词指过程或产品设计期间产生的潜在错误这个有点别扭,需要讨论9:PFMEA开始于○当评审过程流程图的时候,第一个被小组认为“高风险”的过程步骤○第一个生产过程步骤○第一个关键过程步骤○提出的过程流程图的第一个步骤10:所有的FMEAs关注于○仅产品设计○潜在后果可能影响作为最终使用者的顾客○产品开发的设计和顾客希望需要的●产品或过程的设计11:过程FMEA○为组织提供工具以获取产品设计的失效○不考虑设计FMEA,如果可用,作为其分析的一部分●从降低失效的风险方面支持生产过程的开发○在过程方法中是可选的需要查书证实!12:过程FMEA○依靠产品设计更改,克服过程中的缺陷○不应利用流程图建立,流程图用于确认与每个操作关联的产品/过程特性●由开发过程希望做什么和不希望做什么开始,比如:过程的意图○在过程方法中是可选的13:在准备生产过程的过程FMEA的时候,FMEA小组需要○不要考虑没有符合的输入零件/材料的可能性○仅考虑在常规的操作条件下产生的那些失效的失效模式○忽略设计FMEA,以预防可能对过程有害的偏倚或限制○假设出入零件/材料是正确的14:当材料由于现有产品发生更改,FMEA小组需要对以下哪些情况的新的潜在失效模式进行分析:○当前FMEA中的所有项目○新材料,以及可能被影响的产品实现系统的任何等级○新材料,以及任何其他装配或完工变更○仅对新材料15:如果可能的话,在过程FMEA中,更倾向于以下哪种行动作为过程控制的方法?○预防失效模式的起因/机制的发生。
FMEA-编制方法
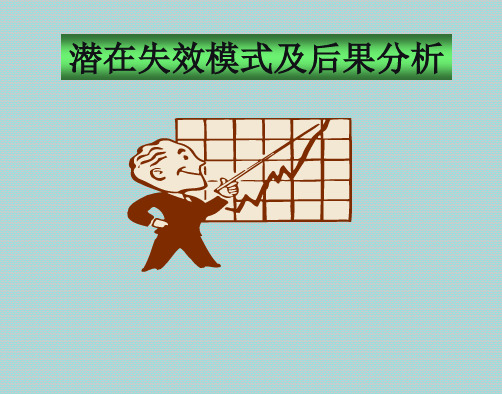
部件FMEA
设计FMEA 过程FMEA
整理课件
21
系统FMEA – 实 施 步 骤
第一步 第二步 第三步 第四步 第五步
系统单元 与
功系能统与结功构 能结构
缺陷分 析
风险评 价
优化
整理课件
分解
输入、输出、 内部功能 失效模式
RPN值
采取措施
22
产 品 系 统 FMEA
确定产品系统的结构 :
底盘系 统
– 确定系统单元并说明其功 能关系(结构树/功能树)。
整车
– 每一系统单元可能的失效
失效
模式。
发动机 驱动轴
失效 – 确定不同系统单元失效模
动力系统 传动器
失效
失效
齿轮
式间的逻辑关系
离合器
失效
整理课件
23
过 程 系 统 FMEA
过程1
整个过程 失效
过程 2 失效
分过程2.1
分过程 2.2失效
分过程2.3
•活塞 尺寸和材料是否 满足间隙的需求?
Herstellung betrachtet
•活塞 活塞销能否 被装错?
•Pleul Ist das Pleul in jeder Lage im Package genügend Freigang
•连杆 Ist die Pleulform den Anforderungen entsprechend konzipiert?
潜在失效模式及后果分析
课程内容
一、FMEA概 述
FMEA的定义、起源 FMEA的实施、跟踪 FMEA的分类
二、设计 FMEA
三、过程 FMEA
设计FMEA简介 设计FMEA的实施
FEMA分析
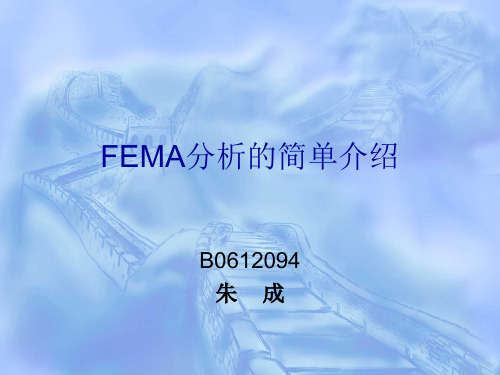
使输出结果失真
生产设计不符合
6
规格
5
3
63
4
84
1
21
1
20
3
72
2
56
2
56
3
90
FEMA分析的简单介绍
B0612094 朱成
什么是FEMA分析
故障模式影响分析(Failure Mode and Effects Analysis,简记为FEMA)是分析系统中每一产品所有 可能产生的故障模式及其对系统造成的所有可能影响, 并按每一个故障模式的严重程度、检测难易程度以及 发生频度予以分类的一种归纳分析方法
▪ 通过RPN可对各故障模式进行相对的危害性进行评定。那些 故障发生可能性高、故障严重程度高,又难以检出的故障模 式,其RPN值较高,从而危害性较大。而那些故障发生可能 性低、故障严重程度低,较容易检出的故障模式,其RPN值 较低
FMEA 工作表及填写方法
FMEA 分析举例
心电图机产品风险水平的 FEMA 分析
严重度评价准则
发生度评价准则
探测度评价准则
风险顺序数
▪ 某一产品的故障模式的风险顺序数RPN由故障模式的发生度 (Occurrence Probability Ranking, OPR)、严重度 (Effect Severity Ranking,ESR)和探测度(Detection Difficulty Ranking,DDR)的乘积计算得出,即: RPN=OPR×ESR×DDR
▪ 下表中列出了常见的一些典型故障模式
故障原因分析
▪ 故障模式分析只说明了产品将以什么模式发生故障,并未说 明产品为何发生故障的问题。因此,为了提高产品的可靠性, 还必须分析产生每一故障模式的所有可能原因。分析故障原 因一般从两个方面着手,一方面是导致产品功能故障或潜在 故障的产品自身的那些物理、化学或生物变化过程等直接原 因;另一方面是由于其他产品的故障、环境因素和人为因素 等引起的间接故障原因
PFMEA的评分标准

备注:
1项目:根据过程所属的系统、子系统或零部件进行分类,包括名称和编号。
2年型/车型:汽车的年型或车型(非汽车零件时用产品替代)
3核心小组:过程评估小组名称、部门和电话。
4过程责任:供应商生产部门和责任小组。
5关键日期:过程FMEA完成日期。
6过程的标识:用于追溯过程FMEA的内部编号。
7编制人:过程FMEA编制人的姓名、电话及所属公司。
8日期:原始稿编制日期、修改号和日期。
9过程功能/要求:与工艺流程中的作业编号和说明相同,简明指出过程目的(如:焊接,钻孔等)
10产品特性编号/说明:此栏所需填入的内容与工艺流程文件一致。
11潜在失效模式:所谓潜在失效模式是指过程可能发生的不能满足过程或设计要求的状况。
是对某一作业可能发生的不符合性的描述。
如,太长、太松等。
12潜在失效影响:潜在影响是指失效模式对客户的影响。
客户泛指下步作业、后续作业、组装厂和最终用户。
如,影响美观、不可显示等。
13严重度:是指潜在失效模式对客户影响的严重程度评价。
14级别:分为关键级别、重要级别、一般级别
15潜在失效原因/机理:列出失效模式的潜在原因,如:装备不当、轴承故障、设定不当等。
16频度:是指失效原因/机理预计发生频度,分1到10级。
- 1、下载文档前请自行甄别文档内容的完整性,平台不提供额外的编辑、内容补充、找答案等附加服务。
- 2、"仅部分预览"的文档,不可在线预览部分如存在完整性等问题,可反馈申请退款(可完整预览的文档不适用该条件!)。
- 3、如文档侵犯您的权益,请联系客服反馈,我们会尽快为您处理(人工客服工作时间:9:00-18:30)。
能与失效功能之间关系的系统的描述。
6
产品和过程系统FMEA基础
系统FMEA定义
将研究的系统结构化,并分成系统单元,说明各
单元间的功能关系。
从已描述的功能中导出每一系统单元的可想象的
失效功能(潜在缺陷)。
确定不同系统单元失效功能间的逻辑关系,以便
能在系统FMEA中分析潜在的缺陷、缺陷后果和 缺陷原因。
100 50
1
非常轻微 很低 对整车的功能影响非常轻 缺陷原因不可 微,只有专业人员才能察 能发生 觉
1
很高 肯定能发现已发生 的缺陷原因
30
实施系统FMEA的五个步骤
第五步
优化
1. 设计更改,以消除缺陷原因或降低缺陷后果的
严重度;
2. 提高设计的可靠性,以降低缺陷原因的发生频
度;
3. 采用有效的发现缺陷原因的措施(尽可能避免
支持信息的收集
决策采取措施 批准系统FMEA 演示系统FMEA 验证措施的实施
5,000 1,000 500
3 2
轻微 低 对整车的功能影响较小, 缺陷原因很少 必须按计划送修排除, 发生,可靠的 操纵系统与舒适性系统 设计 的功能受到限制
非常轻微 对整车的功能影响非常 轻微,只有专业人员才 能察觉 很低 缺陷原因不可 能发生
100 50
高 已发生的缺陷原因 被发现的概率很高, 通过许多相互独立 的试验方法来证明
各个系统FMEA的评价标准可能不同。
32
系统FMEA的表格
缺陷可能性及影响分析
□产品系统FMEA 类型/型号/生产/批号:零件号: 更改状态: 系统编号/系统单元: 零件号: 功能/任务: 更改状态: 潜在缺 陷后果 S 潜在 缺陷 潜在 缺陷 原因 预防 措施 频度 □过程系统FMEA 责任人: 公司: 责任人: 公司: 发现缺 陷措施 编号: 第 共 页 页
很高 肯定能发现已发生 的缺陷原因 28
1
1
过程系统FMEA评分判据
评 分 严重度S 频度P
非常高 缺陷原因发生 的频率很高, 不能使用或不 合适的过程 高 缺陷原因重复 发生,不精确 的过程
缺陷率 (ppm)
不可探测度D
非常低 不可能发现已发生的缺 陷原因, 无或不可能检验过程的 缺陷原因 低 已发生的缺陷原因的发 现率很低, 可能不被发现,检验不 可靠
潜在缺陷原因:下一级系统单元及通过交接点所涉
及的系统单元的所有可以想象的失效功能。
潜在缺陷后果:对上一级系统单元及通过交接点所
涉及的系统单元所造成的失效功能。
20
实施系统FMEA的五个步骤
第三步
缺陷分析
SE1.1的失效功能 SE1的失效功能 SE1.2的失效功能
系统 失效功能1
SE2的失效功能
7
产品和过程系统FMEA基础
产品系统FMEA
设计FMEA的缺陷分析内容:
构件缺陷
缺陷原因 缺陷后果
8
产品和过程系统FMEA基础
产品系统FMEA
考虑整个产品钳子的失效功能,需要时 才考虑到构件的故障类型。
系统缺陷 系统缺陷原因 缺陷(在系统中造成的)后果
9
产品和过程系统FMEA基础
第 共
页 页
部门: 日期 部门: 日期
责任人/ 完成状态(%) 备注/ 完成日 状态 20 40 60 80 100 期
34
实施系统FMEA的组织流程
在跨部门工作组中制定系统FMEA
可以利用许多人知识和经验;
增加系统FMEA结果的认知度;
促进跨部门的联系和合作; 通过方法专家的支持保证系统化、有效的工作。
产品和过程的系统FMEA的基础 实施系统FMEA的五个步骤 系统FMEA的表格 系统FMEA的组织流程 与其他方法之间的关系
3
FMEA及系统FMEA概述 FMEA的发展过程
最初是在美国的航天工业界率先使用。 随着FMEA的成功使用,逐渐被其他行业接受,
并在全球推广实施。
批量投产前的质量保证 系统FMEA
1
系统FMEA
是D-FMEA和P-FMEA的进一步发展。
揭示了在项目的所有关键部位按项目进度如 何通过经验、计算、试验和检验降低已有的 风险或将来的风险。 是一种重要的支持跨部门合作的管理方法。
结构化的记录可以被后续活动所使用。
2
系统FMEA
FMEA及系统FMEA概述
部门: 日期 部门: 日期 探 RPN 责任人/ 测 完成日 度 期
33
系统FMEA的表格
措施跟踪
FMEA
类型/型号/生产/批号:零件号: 更改状态: 系统编号/系统单元: 零件号: 功能/任务: 更改状态: 潜在缺陷原 因及其缺陷 与缺陷后果 R P N 预防 措施 发现缺 陷措施 责任人: 公司: 责任人: 公司: FMEA编号:
实施系统FMEA的五个步骤
第四步
风险评价
风险评价的尺度:风险顺序数RPN
要素组成:
严重度S 频度P 用来评价缺陷后果的严重性 用来评价缺陷原因发生的概率
不可探测度D 用来评价缺陷原因、缺陷或缺陷后果 发生后被发现的概率
RPN=S×P ×D
23
实施系统FMEA的五个步骤
第四步
风险评价
严重度S
根据缺陷后果对整个系统以及外部顾客所
描述功能与 功能结构 实施 缺陷分析 实施 风险评价
实施优化措施
13
第五步
实施系统FMEA的五个步骤
准备
图纸
搜集
法律条文 官方规定
实验报告
产品建议书 质量规定
安全规章
标准化资料 过程计划
可比较的系统单元的
缺陷表
装配计划
检验计划等
14
售后市场经验
实施系统FMEA的五个步骤
29
特别严重 10 安全风险,未满足 法律要求,整车不 9 能运行
500,000 100,000
8 7
严重 整车功能受到很大 限制,必须立即强 制性送修,重要子 系统功能受到限制
50,000 10,000
过程系统FMEA评分判据
评 分 严重度S
中等严重 整车功能受到限制, 不需要立即强制性送修, 重要的操纵系统与舒适性 系统的功能受到限制
美国福特、通用和克莱斯勒三大汽车公司将
FMEA纳入QS-9000体系中,逐步成为行业标准。
4
FMEA及系统FMEA概述
系统FMEA的目的
提高产品的功能保证和可靠性 降低担保费用与折扣费用
缩短开发过程
减少批量投产时的问题 提高准时供货信誉 实现更经济的生产 改进服务
改善内部信息流
50,000 10,000
27
产品系统FMEA评分判据
评 分 严重度S 频度P 缺陷率 (ppm) 不可探测度D
中等 可能发现已发生的 缺陷原因,也许能 验证设计的可靠性, 验证方法相对不可 靠
6 5 4
中等严重 中等 整车功能受到限制, 缺陷原因偶尔 不需要立即强制性送修, 发生,合适的 重要的操纵系统与舒适 设计,比较成 性系统的功能受到限制 熟
频度P
中等 缺陷原因偶尔 发生, 不太精确的过 程
缺陷率 (ppm)
不可探测度D
中等 可能发现已发生的 缺陷原因, 检验相对可靠 高 已发生的缺陷原因 被发现的概率很高, 检验可靠,如多种 相互独立的检验
6 5 4
5,000 1,000 500
3 2
轻微 低 对整车的功能影响较小, 缺陷原因很少 必须按计划送修排除,操 发生,精确的 纵系统与舒适性系统的功 过程 能受到限制
产生的影响来确定S值的大小
也可以从内部顾客的观点出发按相似的评
价准则确定
24
实施系统FMEA的五个步骤
第四步
风险评价
频度P
应考虑所制订的所有的预防措施; 可以根据经验值来推测; 如果在一个新系统中包含有已评价的子系
统,应根据可能已改变的边界条件来验证 评价结果。
25
实施系统FMEA的五个步骤
按逻辑关系彼此相连。
功能结构
18
实施系统FMEA的五个步骤
第二步
功能与功能结构
SE1的功能贡献
系统功能1
SE2的功能贡献
SE3.5的功能贡献 SE2.1的功能贡献 SE2.2的功能贡献
功能结构
19
实施系统FMEA的五个步骤
第三步
缺陷分析
所考虑的系统单元的潜在缺陷是指:从已知功能中
导出和描述的失效功能,如没有完成功能或功能受 到限制。
35
实施系统FMEA的组织流程
开发员、设计员、 系统FMEA工作组的组成策划员、营销员
专业部门 开发员、设计员、实验工程 师、策划员、生产人员、实 项目责任人 验员、工装策划员、检验策 划员、工长、工人等
技术专家
方法专家
36
实施系统FMEA的组织流程
工作组的任务分配
专业部门(项目总负责)
决定实施
设备的设计数据中去。
11
产品和过程系统FMEA基础
过程系统FMEA
分过程1.1
过程1
分过程1.2
总过程 有缺陷 分过程2.1
人 机 料 法
过程2 有缺陷
分过程2.2
分过程2.3
有失效功能的整个过程的系统结构
环
12
实施系统FMEA的五个步骤
准备 确定系统单元 与系统结构
第一步
第二步 第三步 第四步
5
FMEA及系统FMEA概述
FMEA方法的进一步发展
进行设计FMEA时,只考虑各个构件的缺陷,而