一种提高装载机前车架生产效率的工艺方法
机械制造效率提高措施方案

机械制造效率提高措施方案概述随着科技的不断发展,机械制造行业的竞争越来越激烈。
为了在市场中立于不败之地,提高生产效率变得至关重要。
本文将介绍一些机械制造效率提高的措施方案,包括优化生产流程、采用先进技术和设备、提高员工培训等。
优化生产流程生产流程的优化是提高机械制造效率的关键。
以下是一些可以考虑的优化措施:1. 建立并实施精益生产理念:通过减少浪费和提供持续改进,以提高生产效率。
2. 进行价值流分析:通过对生产流程进行分析,找出影响生产效率的瓶颈和问题,并提出相应的改进计划。
3. 实施自动化生产:引入自动化设备和系统,减少人工操作和人为错误,提高生产效率和产品质量。
4. 优化生产排程:合理安排生产任务和资源,避免资源浪费和生产延误。
采用先进技术和设备采用先进技术和设备是提高机械制造效率的另一个重要因素。
以下是一些可以考虑的措施:1. 引进数字化生产技术:借助工业物联网、云计算和大数据等技术,实现生产过程的数字化、信息化和智能化管理,提高生产效率和产品质量。
2. 使用3D打印技术:在一些适用的领域,采用3D打印技术可以缩短生产周期,减少生产成本。
3. 选用高效节能设备:替换老旧设备,选用具有高效能和节能特点的设备,提高生产效率的同时降低能源消耗。
4. 引进智能机器人:自动化和智能化的机器人可以加快生产速度,提高产品质量和一致性。
提高员工培训员工是机械制造企业的重要资产,提高员工的技能和知识水平对于提高生产效率至关重要。
以下是一些可以考虑的措施:1. 进行定期培训:为员工提供定期的培训,包括新技术、新设备的使用和操作、安全操作等方面的培训,以提高员工的技能水平。
2. 鼓励员工学习和创新:营造一个鼓励员工学习和创新的企业文化,激励员工积极参与工作改进和创新。
3. 提供职业发展机会:给予员工晋升和发展的机会,通过提升员工的职业发展和满足其个人成长的需要,提高员工的工作积极性和效率。
结论提高机械制造效率是机械制造企业保持竞争优势的重要手段。
导重准则法在装载机前车架结构优化中的应用

按照步长因子法,寻优迭代公式为
性 与实用 性在某 轮式装 载机 前车架 的优 化设计 实践 中得 到充分验 证 。
[ 关键词] 车架 ;优化设计 ;导重法 ;敏度分析 [ 中图分类号]U 9.5 24 2
Ap l a i n o pi t f c o
[ 文献标识码]B
[ 文章编号]10—5 X 20 )1 0 1 3 0154 (0 81- 9 — 0 0
目前 ,常用 的结构优 化 方法 主要有 两类 :数学
明 ,该方 法具 有表达 简洁 ,意义 明确 ,收 敛快 ,优 化效 果好 的优 点E 。
规划法和准则法。数学规划法的本质是根据设计点 的性态函数及其导数信息来决定寻优迭代方 向和步
长 ,但 随着设 计变 量与约 束条 件 的增加 ,求 解 问题 规模 的加大 ,采用 数学规 划法 需要 的结 构分 析次数
板 密度 ;
=W ( X) = ∑
W ;
2 应 用 实例
作为 国 内第 3代 装 载 机 的 代 表 产 品 ,Z 5G L0
W。 —— 结 构 总 重 量 ,
是 目前各生产厂主推的主力机型,其前车架是结构 = 一t ・ 复杂的承载构件 ,它由不同厚度钢板焊接成箱形结 构 ,是整 机结 构强度 、刚度 设计 的关键 件之 一 。对
外载随设计变量变化而变化的速率 , 故仍存在准则
不准 的缺 陷 ,且所 涉及 的结 构形 式和优 化 目标约束
具有很 大局 限l 。 _ 2 J
文献 E]创立的结构优化导重法 ,是从极值 3
条件和 刚度 方程 出发严 密推 导的理 性 准则 法 ,意义
情况 ,第 组板单元重量数学表达为
Hyper_Mega工法研究
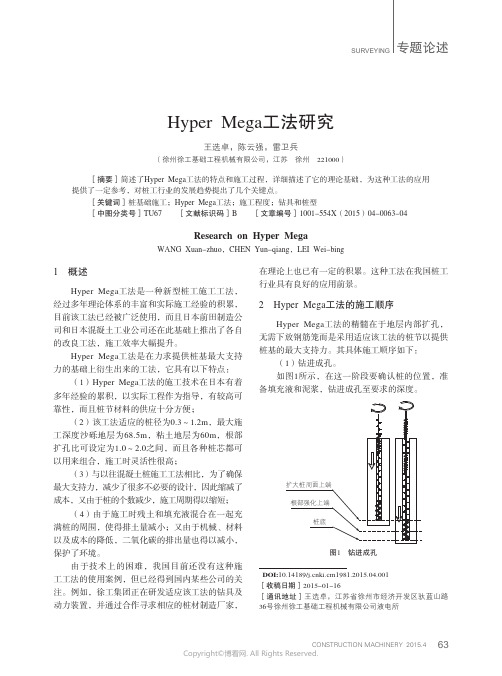
(4)由于施工时残土和填充液混合在一起充 满桩的周围,使得排土量减小;又由于机械、材料 以及成本的降低,二氧化碳的排出量也得以减小, 保护了环境。
由于技术上的困难,我国目前还没有这种施 工工法的使用案例,但已经得到国内某些公司的关 注。例如,徐工集团正在研发适应该工法的钻具及 动力装置,并通过合作寻求相应的桩材制造厂家,
γJNqqu—u —(粘对2JNq0qu 于土u 5直地.(52q型层0u )Z桩中5.5γ桩qu=的)Z0Jq周.;u7qu面,JNq摩对(u20擦于(2系节50.5数型q5u.),桩5Zqu )Z
qu
——桩周围粘土地层的第一节杆压强的 q平u 均值(kN/m2), qu 的数值在10
以上,大于200按200计算;
(5)提升钻杆。 钻孔根部强化成功后提出钻杆,如图5所示。
图2 扩大桩孔
(3)混合搅拌。 反复搅拌扩孔区间,使得填充液和残土充分 混合,如图3所示。
图3 混合搅拌
(4)根部强化。 根部强化过程根据地层不同其操作步骤也不 相同。对于砂砾地层要在注入强化液的同时反复提 升和加压钻具至少3次;对于粘土地层,至少要加 压和提升钻具1次,并在孔底保持钻头开翼状态下
Lc——桩 与 粘 土 地 层 相 接 触 的 总 长 度 (m);
φ——桩 的 周 长 ( m ) , φ = π D ( D 为 桩
径)。
扩孔比ω与桩底部支持力系数α的关系可按表
1确定。
CONSTRUCTION MACHINERY 2015.4 65
Copyright©博看网. All Rights Reserved.
装载机的生产工艺

提高装载机工艺效率
1、推土机的推煤方式、形成的煤堆的形状和底部是否平整等方面严格要求,为前装载机有利条件
2、推土机在推煤过程中,要根据现场实际情况确定最优推送距离,提高时间利用系数,降低运送中的漏损(缩短推土机作业时的循环时间(6-10米);提高时间利用效率;降低运送中的漏损,尽量创造下坡运铲的条件(13%)。
)
3、配备的自卸车不但车箱高度要满足装在要求,而且装载斗数为整数
4、改善前装载机作业场地,压缩不必要处理场地时间,提高设备作业效率。
导重准则法在前车架结构优化设计中的应用

基金项目广西柳州市科学研究与技术开发计划资助项目()作者简介石光林(6),男,高级工程师23@63导重准则法在前车架结构优化设计中的应用石光林1,2,陈树勋2,梁光明3(1.广西工学院机械系,广西柳州 545006;2.广西大学机械工程学院,广西南宁 530004;3.广西柳工机械股份有限公司,广西柳州 545007)摘要:提出了一种实用高效的机械结构优化设计方法———导重准则法,该方法既能充分利用结构分析软件AN 2SYS 有限元建模、分析求解与结果输出方便的优势,又能发挥导重法优化效果好、收敛快的优越性,一般只需约5~7次优化迭代计算,即可得到十分显著的优化效果,大大提高了设计效率与设计质量.其优越性与实用性在某轮式装载机前车架的优化设计实践中得到充分验证.关键词:前车架;结构优化;导重法;灵敏度分析中图分类号:TH123.4 文献标识码:A 文章编号:1672-5581(2008)02-0139-05Weight 2guidedcriterionmethoda ppliedforstructuraloptimizationdesi gnoffrontframesSHI Guan g 2lin1,2,CHEN Shu 2xun 2,LIA NGGuan g 2m in g3(1.De partmentofMechanicalEngineering,Guan gxi Universit yofTechnolo gy,Liuzhou545006,China;2.Colle geofMechanicalEngineering,Guan gxiUni versit y,Nannin g530004,China;3.Guan gxiLiu gongMachiner yCo.Ltd.,Liuzhou545007,C hina)Abstract :Inthisstud y,ahi gh pragmaticandefficientstructuraloptimizationdesi gnmethodolo gy,i.e.theweight 2guidedcriterionmethod,is proposed.Inthisregard,thefiniteelementmodelingisconductedusingsuchastructuralanal ysissoftware,i.e.ANYSTM,thatthesolutionandout putcanbeaccordin gly produced.Meanwhile,theo ptimizationresultsaresatisfactoril yattainedbecauseofthefastconver genceofwei ght 2guided criterionmethodwith5-7iterations.Therefore,thisa pproachsi gnificantl yenhancesthedesi gnefficienc yand qualit y.Tothisend,acasestud yonfrontframedesignforawheel2typeloaderisusedtoverifyitssu periorit yand practicalit y.Keywords :frontframe;optimizationdesi gn;wei ght 2guidedcriterionmethod;sensitivit yanal ysis. 目前,常用的结构优化方法主要有2类:数学规划法和准则法[1].数学规划法的本质是根据设计点的性态函数及其导数信息来决定寻优迭代方向和步长,其优点是具有较强的数学基础,通用性好,可处理不同性质的优化问题.但由于结构优化问题往往是涉及高次非线性隐函数的非线性规划,随着设计变量与约束条件的增加,求解问题规模的加大,采用数学规划法需要的结构分析次数即迭代计算次数迅速增加,故优化效率低,尤其是优化迭代的前几步优化效果不明显,因而难以满足实际工程复杂结构优化设计的需要,影响其在工程结构优化实践中的推广和应用.准则法由于有预先给定的衡量结构最优的准则,把寻找最优结构问题转化为寻求满足某一准则的结构问题,使优化迭代“定向”进行,因而具有意义明确、收敛快和计算量少的优点,早期的准则法如满应力法、满约束准则及满应变能准则等属感性准则法,虽有一定优化效果,但由于数学上不严密,一般不能找到最优解.基于极值条件和位移虚功表达的虚功准则法属于理第6卷第2期2008年6月中 国 工 程 机 械 学 报CHINESEJOURNALOFCONSTRUCTIONMACHINERY Vol.6No.2 Jun.2008:2007010102:197-.E mail:s gl .性准则法,但虚功准则法无法考虑外载随设计变量变化而变化的速率,故仍具有准则不准的缺陷,且所涉及的结构形式和优化目标约束具有很大局限[2].文献[3,4]创立的结构优化导重法,是从极值条件和刚度方程出发严密推导的理性准则法,意义明确、形式简洁,在不少方面改进了原有的结构优化准则法,提高了优化效果,拓宽了应用范围,克服了满应力准则法与虚功准则法的缺陷,融合了理性准则法与数学规划法的优点.大量工程应用表明,该方法具有表达简洁,意义明确,优化效果好,收敛快,尤其是优化迭代的前几步优化效果就很明显的优点[5~7].通用分析软件ANSYS 具有很强的结构分析能力,但结构优化功能却相对薄弱,其优化方法大多采用一般的数学规划法.在大型复杂工程结构优化计算中,其迭代次数过多、效果并不理想.为了既能充分发挥ANSYS 软件在有限元建模、分析求解和结果输出方便等方面的优势,又能利用导重准则法优化效果好、收敛快的特点,现提出了一种ANSYS 与导重准则法相结合的结构优化设计方法:利用ANSYS 的分析模块进行结构特性分析,并利用其优化模块中梯度法的设计参数独立变动再分析功能,求得结构特性对设计变量的差分灵敏度,然后利用导重准则法进行优化迭代计算,得到新的设计方案,如此反复进行分析优化迭代,最终使结构趋于最优.文中将该方法应用于某型号轮式装载机前车架的结构优化设计实践,取得了十分显著的优化效果,大大提高了优化效率和设计质量,充分验证了该方法的优越性与实用性.1 结构优化导重准则法简介1.1 质量约束结构优化设计其数学模型为find X =[x 1,x 2,…,x N ]T ∈R N (1)min f (X)(2)s.t. m (X )-m 0≤0(3)x Li ≤x i ≤x Ui ,i =1~N(4)式(1)~(4)中:X =[x i ,x 2,…,x n ,…,x N ]T ∈R N 为N 维实数设计变量组成的设计向量,它可包括截面积、板厚等构件尺寸变量、结构形状几何尺寸变量、拓扑变量等多种设计变量;f (X )可为任意结构性态函数,如挠度、精度、应力储备安全度和自振基频等;m ,m 0分别为结构质量和质量约束上限,x L i ,x U i 分别为x i 的下,上限值.根据文献[4],对于上述数学模型,由不等式约束极值条件推导出结构最优的导重准则基本表述为:最优结构应按各组构件的导重正比分配结构质量.例如,对于设计变量x i 为板单元(平面应力板)板厚t i 的情况,第i 组板单元质量数学表达为m i =a i ρi t i =m 0(G ti /G )(5)式中:m i 为第i 组板单元质量;a i 为板厚为t i 的第i 组板单元总面积;ρi 为板厚t i 的线密度;m 0为结构总质量,m 0=m (X )=∑m i ;G ti 为第i 组板构件导重,G ti =-t i9f (X )9t i;G 为结构总导重,G =∑Gti .导重G ti 的物理意义就是在优化迭代中起到引导各组构件质量m i 重新合理分配从而使结构趋于最优的作用.由导重准则式(5)得t i =m 0(G ti /Ga i ρi )(6)按照步长因子法,寻优迭代公式为t (k +1)i =αm 0(G t i /Ga i ρi )(k )+(1-α)t (k)i (7)式中为迭代次数;α为步长因子,α取值控制收敛的原理与方法,见文献[5] 一般性的多性态约束质量最小化问题其优化设计数学模型为041 中 国 工 程 机 械 学 报第6卷 :k .1.2find X ∈D <R N(8)min m (X )(9)s.t. g j (X)≤0,j =1~J(10)式中:D ={X |X L ≤X ≤X U },X L ,X U 分别为X 的下,上限值;g j (X )为位移、应力、基频及安全度等多种结构性态函数.根据文献[4],有:m x i =x i H x i =∑Jj =1λjG jx i(11)式中:H x i为x i 的密度,H x i=9m (X)9x i ;G j x i为x i 的j 需求约束导重,G jx i=-x i 9g j (X )9x i.将式(11)的m i 视为x i 的广义质量,则式(11)即为推广的导重准则,即最优结构各设计变量的广义质量与其各约束导重成线性齐次组合关系.由式(11)得x i =∑Jj =1λjG jx i /H x i(12)式中:λj 为各约束的乘子,可通过线性互补问题的Lemker 算法求得.为保证收敛,采用步长因子迭代寻优的公式为x (k +1)i =α(∑Jj =1λjG jx i /H x i )(k)+(1-α)x (k)i , i =1~N (13) 采用导重法进行结构优化设计最后归结为一组非线性准则方程组的求解,采用直接迭代步长因子法,只要适当选取“步长”,即保证迭收敛[8].2 用ANSYS 求结构响应的差分灵敏度结构性态的灵敏度即结构性态对设计变量的偏导数计算是结构优化设计的重要内容,它直接影响优化效率甚至关系到能否收敛.通常,结构性态的灵敏度计算方法有2种:解析法和差分法.解析法是求准确导数,其特点是物理概念明确,计算效率高,结果准确,但对于工程实际问题,解析灵敏度求解十分困难.而差分法的优点是简单可靠,不足是计算工作量比解析法大,且每个设计变量的差分灵敏度都需要进行一次性能重分析.由前面的导重法简介可以看出,优化迭代计算的关键是要求出9f (X )/9x i ,9g (X )/9x i 和9m (X )/9x i ,即计算结构位移、应力、质量等动静力特性对设计变量的导数即灵敏度.准确的灵敏度计算要涉及结构刚阵求导等复杂计算,但ANSYS 并未提供解析灵敏度计算,故仅能利用ANSYS 软件的现有功能求结构响应的差分灵敏度,然后结合导重准则法进行结构优化设计,这样既不必进行复杂的程序改造和灵敏度计算,又能很好地满足工程结构优化设计的需要.具体作法如下.首先利用ANSYS 软件进行结构造型的参数化建模,将结构中可以变化的构件和外形尺寸等设为参数,进行结构动静力分析计算.然后利用优化模块中的梯度法,将构件和外形尺寸等设为设计变量,结构位移、应力、质量等动静力特性设为目标或约束.由于在ANSYS 软件的梯度法计算中,可以求出任一设计变量单独发生小比例变化而其他设计变量不变时,对结构进行重分析的动静力特性计算结果,这种动静力特性变化量除以该设计变量的变化量,就是结构动静力特性对该设计变量的差分灵敏度.利用ANSYS 的梯度法,进行N 次结构有限元重分析,即可求出结构动静力特性对所有设计变量的差分灵敏度.将这种差分灵敏度作为9f (X )/9x i ,9g (X )/9x i 和9m (X )/9x i 等灵敏度的近似值,代入式(7)或式(13),即可完成导重法的一次迭代计算,得到更优的新设计方案,然后再进行新一轮结构分析———差分灵敏度计算及优化迭代计算等,直至实现结构设计方案的最优化.3 应用实例装载机前车架是结构复杂的承载构件,是整机结构强度、刚度设计的关键件之一它由不同厚度钢板141 第2期石光林,等:导重准则法在前车架结构优化设计中的应用 .焊接而成一个箱形结构,在作业和行走过程中承受工作装置传来的力和力矩载荷.笔者利用ANSYS 与导重准则法,对某型号的轮式装载机前车架结构进行了优化设计,在保证车架的强度和刚度前提下,合理设计各板厚度,使车架的总重量最小化,从而达到企业要求的减重降成本目的.图1 前车架的有限元模型Fig.1 FEAm odelofthefr ontfr ame前车架的有限元分析模型如图1所示,左下角的三棱柱模拟与前车架相连的前桥结构;E ,F 两个轴销处模拟后车架对前车架的约束;在A ,B ,C 轴销处施加工作载荷.为保证分析计算符合实际,所有轴销与前车架间均以接触副相连.将15种工况的结构姿态、载荷值和相应的约束施加于该有限元模型上,即可分别求得各工况结构变形与应力,再根据分析结果对其进行结构优化设计.3.1 前车架结构尺寸优化的数学模型为find X =[x 1,x 2,…,x N ]∈R N min m (X )s.t. m (X )≤[σ],x min ≤x i ≤x max , i =1,2,…,N 式中,x i ,x 2,…,x N 为构件钢板厚度;m (X )是结构总质量;σ(X )是所有构件特征应力的包络函数[9];[σ]是材料的许用应力.3.2 优化迭代结果取前车架不同构件的钢板厚度作为优化设计变量x 1~x 20,其中仅x 5为过渡半径.按工程实际要求,钢板厚度优化结果应圆整为钢材厂供应的钢板厚度序列数值,优化约束为最大复合应力小于钢材许用应力220MPa.优化结果见表1.表1 前车架优化结果Tab.1 Resultsofo ptimizationofthefrontfr am e 设计变量初始值优化结果x 1/mm 3022x 2/mm 1113x 3/mm 1415x 4/mm 2024x 5/mm 100150x 6/mm 1612x 7/mm 1612x 8/mm 1412x 9/mm 1411x 10/m m 1413m(X)/k g15371361设计变量初始值优化结果x 11/mm 16 18x 12/mm 2015x 13/mm 1411x 14/mm 1211x 15/mm 1411x 16/mm 1411x 17/mm 1414x 18/mm 1613x 19/mm 1616x 20/mm2436σmax /MPa399218 构件尺寸优化后再次进行有限元分析,得到15种工况下的变形与应力分布,限于篇幅,仅给出应力最大的水平插入偏载工况在优化前后的复合应力云图(图2).从表1可以看出:通过采用导重法进行结构优化,在各工况最大应力从399.427MPa 下降到218.027MPa 不超过许用应力220MPa 的前提下,前车架整体结构受力更趋合理,自重从1.537t 下降到1.361t ,减轻质量176k g ,降重11.45%,圆满完成了厂方提出的优化降重5%以上的任务.4 结论(1)结构优化设计的实质是合理分配设计资源,对于质量最小化问题,其实质是材料质量在结构空间及构件间的合理分配.本文的优化过程与优化结果证明,以ANSYS 为分析器,利用导重准则法进行结构优化设计是一种很实用的工程结构高效优化设计方法.其优越性在于:充分发挥了ANSYS 软件建模、求解、输出方便和导重准则法收敛快、优化效率高的优点,一般只需约5~7次迭代,即可求得工程实际足够满意的优化设计方案,大大提高了优化效率和设计质量.()只有数学理论意义上的最优设计,实际工程中并不存在设计最优这是因为实际工程中要考虑多种目标和各种客观条件限制,这些目标和限制往往是相互制约的,导致在实际的工程结构设计中不存在绝对的“最优解”,给出的最优设计方案具有理论指导意义实际工程结构设计中应当按照结构软设计理论与241 中 国 工 程 机 械 学 报第6卷 2..结构模糊优化的理论方法寻求“满足满意解”.图2 前车架水平插入偏载工况优化前后的复合应力云图对比Fig.2 Complexstr ess pr ofileunder theNo.2wor kingcondition参考文献:[1] 王光远,董明耀.结构优化设计[M].北京:高等教育出版社,1987. WAMGGuan gyuan,DONGMin gyao.Structuralo ptimizationdesi gn[M].Be jing:Hi ghEducationPress ,1987.[2] 王光远.工程软设计理论[M].北京:科学出版社,1992. WANGGuan gyuan.Theor yofs oftdesi gni nen gineering[M].Be j ing:SciencePress,1992.[3] CHENShuxun,YEShanghui.A guide 2weight cri terionmethodfortheopti m aldesi gnofantennastructures[J].EngineeringO pti m i zati on,1986,10(3):199-216.[4] 陈树勋.精密复杂结构的几种现代设计方法[M].北京:北京航空航天大学出版社,1992. CHENShuxun.Somemoderndesignmethodsof preciseandcom plexstructures[M].Be ji ng:Bei jingUniversit yofAeronauticsandAstronau 2ticsPress,1992.[5] 陈树勋,李威龙.一种实用的机械结构优化方法[J].机械设计,2003,20(1):41-44. CHENShuxun,LIWeilong.A practi caldesi gningmethodfortheo ptimizationofmechanicalstructure[J].JournalofMachineDes i gn,2003,20(1):41-43.[6] 陈树勋,孙建熙,裴少帅.半挂式散装水泥车结构分析与优化设计[J ].机械设计,2005,22(7):31-33. CHENShuxun,SUNJianxi,PEIShaoshuai.Structuralanalysisando ptimizationdesi gnofhalfhan gingt ypedbulk 2cementtruck[J].JournalofMachineDesi gn,2005,22(7):31-33.[7] 胡迎春,李尚平,陈树勋.甘蔗收割机机架虚拟样机的模态分析与优化设计[J].计算机辅助设计与图形学学报,2006,18(8):1282-1285. HUYin gchun,LIShan gpin g,CHENShuxun.Modalanalysisanddesi gno ptimizationforvirtual protot ypingofu pl iftdeviceofasu garcaneharvester[J].JournalofComputer 2AidedDesi gn&Com puterGra phics,2006,18(8):1282-1285.[8] 陈树勋,王素暖.一种新型线性化迭代算法及其在结构优化准则方程组求解中的应用[J].工程设计学报,2005,12(5):270-272. CHENShuxun,WANGSunuan.Newlineariterat ivealgorithmanditsa pplicationinseekin gsolutionofcriterione quationsofstructural opti 2mization[J].J ournalofEngineeringDesi gn,2005,(12)5:270-272.[9] 陈树勋,裴少帅.一种简明易用的结构优化的包络函数[J].现代制造工程,2004(7):89-92. CHENShuxun,PEIShaoshuai.Aconci s eandwidelyenvelo pefunctionofstructuralo ptimization[J].JournalofModernManufacturin gEn gi 2neering,2004(7):89-92.341 第2期石光林,等:导重准则法在前车架结构优化设计中的应用。
提高装载机工作效率的建议方法
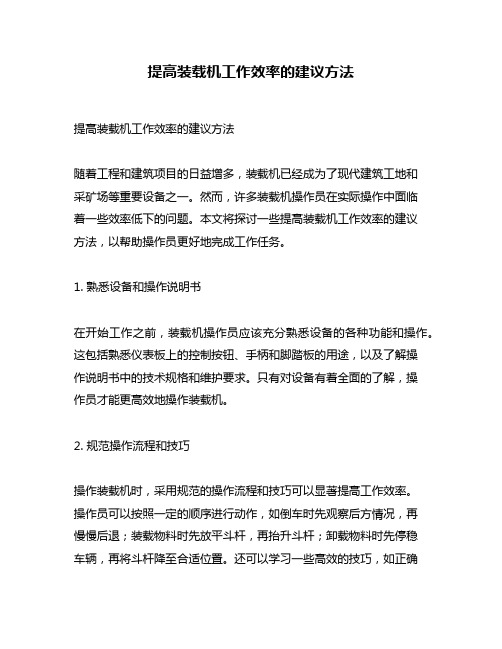
提高装载机工作效率的建议方法提高装载机工作效率的建议方法随着工程和建筑项目的日益增多,装载机已经成为了现代建筑工地和采矿场等重要设备之一。
然而,许多装载机操作员在实际操作中面临着一些效率低下的问题。
本文将探讨一些提高装载机工作效率的建议方法,以帮助操作员更好地完成工作任务。
1. 熟悉设备和操作说明书在开始工作之前,装载机操作员应该充分熟悉设备的各种功能和操作。
这包括熟悉仪表板上的控制按钮、手柄和脚踏板的用途,以及了解操作说明书中的技术规格和维护要求。
只有对设备有着全面的了解,操作员才能更高效地操作装载机。
2. 规范操作流程和技巧操作装载机时,采用规范的操作流程和技巧可以显著提高工作效率。
操作员可以按照一定的顺序进行动作,如倒车时先观察后方情况,再慢慢后退;装载物料时先放平斗杆,再抬升斗杆;卸载物料时先停稳车辆,再将斗杆降至合适位置。
还可以学习一些高效的技巧,如正确使用控制杆和换挡杆,合理调整行走速度和转向角度等,以提高操作的流畅度和准确性。
3. 配备合适的附件和工具装载机的附件和工具是提高工作效率的重要因素之一。
挑选适合不同工作任务的不同型号和尺寸的斗杆和斗形,可以提高装载和卸载的速度和效率。
根据实际需要,还可以配备其他附件如抓斗、推土板等,以满足不同工作场景的需求。
确保合适的附件和工具可以提高装载机的多功能性和适用性,进而提高工作效率。
4. 定期维护和检修设备装载机是一个复杂的机械设备,需要定期进行维护和检修,以保证其正常运行和工作效率。
操作员应该充分了解维护保养的方法和周期,如更换液压油、清洗空滤器、加注润滑油等。
定期进行设备检查,如检查液压系统、电气系统和制动系统等,可以及时发现和解决潜在的问题,减少停机时间,提高工作效率。
5. 加强沟通和协作装载机操作往往需要与其他设备操作员和工地人员进行紧密的沟通和协作。
强化沟通和协作可以减少误解和重复劳动,提高工作效率。
操作员应该与施工队和工地管理人员保持密切联系,及时了解工作计划和要求,以便更好地安排自己的工作。
提高铲运机生产效率的方法
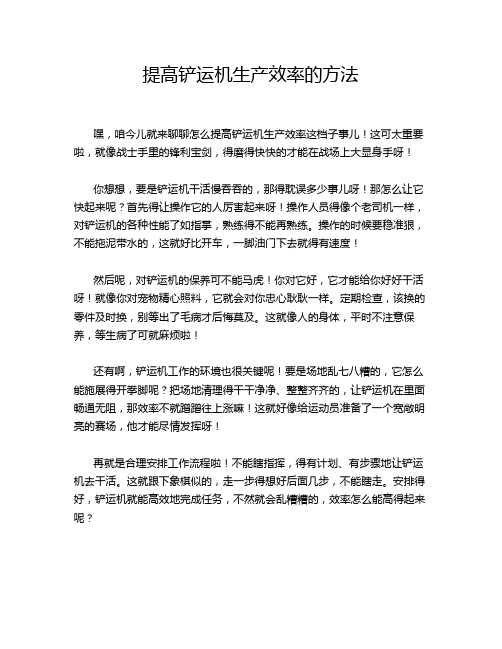
提高铲运机生产效率的方法
嘿,咱今儿就来聊聊怎么提高铲运机生产效率这档子事儿!这可太重要啦,就像战士手里的锋利宝剑,得磨得快快的才能在战场上大显身手呀!
你想想,要是铲运机干活慢吞吞的,那得耽误多少事儿呀!那怎么让它快起来呢?首先得让操作它的人厉害起来呀!操作人员得像个老司机一样,对铲运机的各种性能了如指掌,熟练得不能再熟练。
操作的时候要稳准狠,不能拖泥带水的,这就好比开车,一脚油门下去就得有速度!
然后呢,对铲运机的保养可不能马虎!你对它好,它才能给你好好干活呀!就像你对宠物精心照料,它就会对你忠心耿耿一样。
定期检查,该换的零件及时换,别等出了毛病才后悔莫及。
这就像人的身体,平时不注意保养,等生病了可就麻烦啦!
还有啊,铲运机工作的环境也很关键呢!要是场地乱七八糟的,它怎么能施展得开拳脚呢?把场地清理得干干净净、整整齐齐的,让铲运机在里面畅通无阻,那效率不就蹭蹭往上涨嘛!这就好像给运动员准备了一个宽敞明亮的赛场,他才能尽情发挥呀!
再就是合理安排工作流程啦!不能瞎指挥,得有计划、有步骤地让铲运机去干活。
这就跟下象棋似的,走一步得想好后面几步,不能瞎走。
安排得好,铲运机就能高效地完成任务,不然就会乱糟糟的,效率怎么能高得起来呢?
提高铲运机生产效率可不是一朝一夕的事儿,得靠大家的努力呀!操作人员用心,保养人员精心,管理人员上心,大家齐心协力,还怕铲运机的效率不高吗?这就好像一艘大船,只有大家一起用力划桨,才能在大海中乘风破浪呀!所以呀,大家都行动起来吧,让铲运机成为我们的得力助手,为我们创造更大的价值!。
如何提高木材装载机的工作效率和生产能力
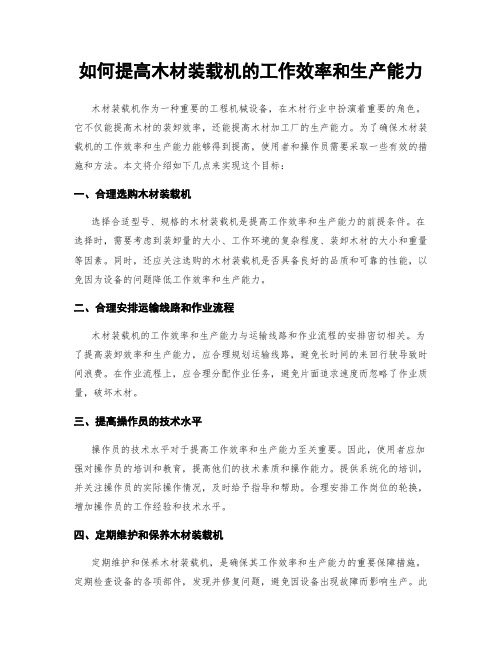
如何提高木材装载机的工作效率和生产能力木材装载机作为一种重要的工程机械设备,在木材行业中扮演着重要的角色。
它不仅能提高木材的装卸效率,还能提高木材加工厂的生产能力。
为了确保木材装载机的工作效率和生产能力能够得到提高,使用者和操作员需要采取一些有效的措施和方法。
本文将介绍如下几点来实现这个目标:一、合理选购木材装载机选择合适型号、规格的木材装载机是提高工作效率和生产能力的前提条件。
在选择时,需要考虑到装卸量的大小、工作环境的复杂程度、装卸木材的大小和重量等因素。
同时,还应关注选购的木材装载机是否具备良好的品质和可靠的性能,以免因为设备的问题降低工作效率和生产能力。
二、合理安排运输线路和作业流程木材装载机的工作效率和生产能力与运输线路和作业流程的安排密切相关。
为了提高装卸效率和生产能力,应合理规划运输线路,避免长时间的来回行驶导致时间浪费。
在作业流程上,应合理分配作业任务,避免片面追求速度而忽略了作业质量,破坏木材。
三、提高操作员的技术水平操作员的技术水平对于提高工作效率和生产能力至关重要。
因此,使用者应加强对操作员的培训和教育,提高他们的技术素质和操作能力。
提供系统化的培训,并关注操作员的实际操作情况,及时给予指导和帮助。
合理安排工作岗位的轮换,增加操作员的工作经验和技术水平。
四、定期维护和保养木材装载机定期维护和保养木材装载机,是确保其工作效率和生产能力的重要保障措施。
定期检查设备的各项部件,发现并修复问题,避免因设备出现故障而影响生产。
此外,保持设备的清洁和润滑,有效减少摩擦,延长使用寿命。
定期维护和保养木材装载机可以提高工作效率和生产能力,降低设备故障率和维修成本。
五、使用先进的技术和设备随着科技的不断进步,木材装载机的工作效率和生产能力也在不断提高。
使用先进的技术和设备,可以有效提高装卸速度和运输效率。
例如,采用自动化控制系统可以提高操作的准确性和稳定性,使用高效的木材装卸工具可以提高木材装卸效率。
提高铲运机生产率措施的研究
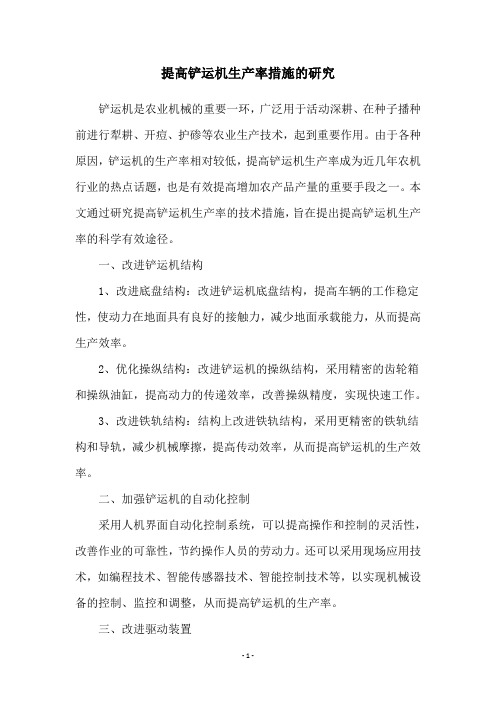
提高铲运机生产率措施的研究铲运机是农业机械的重要一环,广泛用于活动深耕、在种子播种前进行犁耕、开痘、护碜等农业生产技术,起到重要作用。
由于各种原因,铲运机的生产率相对较低,提高铲运机生产率成为近几年农机行业的热点话题,也是有效提高增加农产品产量的重要手段之一。
本文通过研究提高铲运机生产率的技术措施,旨在提出提高铲运机生产率的科学有效途径。
一、改进铲运机结构1、改进底盘结构:改进铲运机底盘结构,提高车辆的工作稳定性,使动力在地面具有良好的接触力,减少地面承载能力,从而提高生产效率。
2、优化操纵结构:改进铲运机的操纵结构,采用精密的齿轮箱和操纵油缸,提高动力的传递效率,改善操纵精度,实现快速工作。
3、改进铁轨结构:结构上改进铁轨结构,采用更精密的铁轨结构和导轨,减少机械摩擦,提高传动效率,从而提高铲运机的生产效率。
二、加强铲运机的自动化控制采用人机界面自动化控制系统,可以提高操作和控制的灵活性,改善作业的可靠性,节约操作人员的劳动力。
还可以采用现场应用技术,如编程技术、智能传感器技术、智能控制技术等,以实现机械设备的控制、监控和调整,从而提高铲运机的生产率。
三、改进驱动装置1、改进发动机:发动机是铲运机最重要的驱动装置,采用先进的技术,可以提高发动机的效率,提高铲运机的性能。
2、优化传动装置:改进铲运机的传动装置,优化传动装置结构,采用特殊材料,增加精密加工技术,从而提高传动效率,有效提升铲运机生产率。
3、改进换向装置:改进铲运机的换向装置,采用先进的换向技术,实现快速、准确、无缝的换向,来提高机械的工作效率,以期达到提高铲运机的生产率。
四、创新存储装置采用现代技术,建立起自动化的存储装置,实现智能化的存储管理,提高商品的及时交付效率,加快铲运机的生产率。
上述是改善铲运机生产率的技术措施,改进铲运机的结构结构、改善驱动装置和创新存储装置有助于提高铲运机的性能,从而大幅度提高其生产率。
因此,从现有的工作状态出发,实施有效的技术改进方案,通过合理地设计和组合,改进铲运机的性能,有助于提高铲运机的生产率。
提高装载机工作效率的建议

提高装载机工作效率的建议一、引言装载机是工地上必不可少的重型机械设备之一。
它能够快速、高效地完成各种物料的装卸作业,为工地建设提供了强有力的支持。
然而,在实际工作中,很多装载机操作员会遇到一些效率低下的问题,这些问题不仅影响了工作质量和效率,还可能增加安全隐患。
提高装载机工作效率是非常重要的。
二、优化操作流程1.合理规划施工场地布局在施工场地进行规划时,应该考虑到装载机的行驶路线和卸货点位置。
在场地规划中应尽量减少转弯和倒车次数,并将卸货点设置在距离行驶路线较近的位置,以减少时间浪费。
2.合理调整装载机工作方式对于同一批物料,在装卸时可以采用“批量处理”的方式。
即先将所有物料集中起来,再统一进行装卸作业。
这样可以减少车辆来回运输次数和等待时间。
3.科学制定施工计划在施工计划中应根据实际情况合理安排各项任务的优先级,确保装载机在最短时间内完成任务。
同时,应根据天气预报等信息,合理安排工作时间和任务量。
三、提高操作技能1.加强培训装载机操作员需要具备一定的技能和经验才能胜任工作。
企业应该定期组织培训和考核,提高操作员的技术水平和工作质量。
2.掌握正确的操作方法装载机的操作方法有很多种,但是只有掌握正确的方法才能提高效率。
在装卸物料时应该采用适当的角度和速度,并避免过度倾斜或过快运动造成物料损坏。
3.保持设备状态良好及时对装载机进行维护和保养是提高效率的重要保证。
检查油液、轮胎、制动器等设备部件是否正常运转,及时更换损坏部件,可以减少故障发生率并延长设备寿命。
四、加强管理监督1.建立健全制度企业应该建立完善的管理制度和规章制度,并加强对操作员的监督和考核。
可以对操作员进行定期检查和评估,并根据评估结果给予奖惩。
2.加强沟通协调装载机操作需要与其他工作人员密切配合,应该加强沟通协调,确保各项任务的顺利进行。
在装卸物料时需要与司机沟通好车辆位置和时间等信息。
3.推广先进技术随着科技的不断发展,装载机也在不断更新换代。
提高装载机机械加工精度的有效措施

提高装载机机械加工精度的有效措施1直接减少误差法直接减少误差法是一种思路最为清晰的方法,也是在一般解决误差过程中最常用的方法之一,即在找出误差产生原因之后直接就误差问题提出解决方案。
例如,由于受热而变形的长轴车削,在解决由于车削的弯曲带来的误差时,直接利用反切削法,再为其施加一个弹簧后顶尖,将直接解决车削由于热变形而产生的误差问题。
2误差补偿法误差补偿法是一种极为巧妙的消除误差的方法,在实践中可以有效解决众多误差问题。
误差补偿法即在原本的误差基础上有意制造出另一种新的误差,通过两种误差的综合将原来的误差抵消掉。
误差补偿法追求正负相消的原理,即若原本产生的误差为负值时,我们可以制造出另一种值为正的误差,且使两个正负误差的.绝对值相等,从而抵消掉原本的误差,使加工精度更高。
3均化原始误差误差均化法主要是通过试切加工过程对原始误差进行均化,这种解决误差的方法主要针对于对加工工件表面精确度的提高,或者针对需要完美配合的轴和孔的精确化加工。
误差均化法主要使用研磨工艺,通过反复的摩擦和磨损对工件表面进行不断均化。
其消除误差的基本原理就是通过两个表面之间的互相磨合以达到减小相互之间误差,提高精确度的目的,也是一个相互检查,相互修正,相互均化的过程。
这种通过均化来消除原始误差的方法适用于大部分精密基准件的加工过程,能最大程度地避免分度转位误差对加工精度带来的不利影响。
3.4实行实时补偿控制在装载机机械加工过程中,有些加工件对机床的转动精度相当高,此时我们需要使用补偿控制技术。
补偿控制技术主要通过校正尺和接收附加运动的螺母来完成补偿控制,其中校正尺的精度直接决定了补偿控制技术的精度,因此补偿控制的技术难点就在于对校正尺的调整。
实践中,一般通过数控机床进行软件补偿,在加工过程中,实时采集去加数据,同时反馈在数据表中,供数控系统在完成精插补后查询误差补偿值,从而达到控制坐标轴附加运动的目的。
控制装置根据实时采集的误差数据的方向和大小进行微量调整。
木材装载机的过程优化和效能提升方法
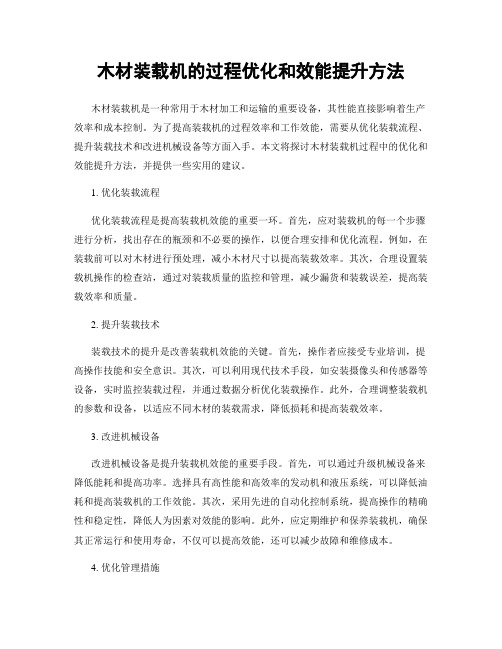
木材装载机的过程优化和效能提升方法木材装载机是一种常用于木材加工和运输的重要设备,其性能直接影响着生产效率和成本控制。
为了提高装载机的过程效率和工作效能,需要从优化装载流程、提升装载技术和改进机械设备等方面入手。
本文将探讨木材装载机过程中的优化和效能提升方法,并提供一些实用的建议。
1. 优化装载流程优化装载流程是提高装载机效能的重要一环。
首先,应对装载机的每一个步骤进行分析,找出存在的瓶颈和不必要的操作,以便合理安排和优化流程。
例如,在装载前可以对木材进行预处理,减小木材尺寸以提高装载效率。
其次,合理设置装载机操作的检查站,通过对装载质量的监控和管理,减少漏货和装载误差,提高装载效率和质量。
2. 提升装载技术装载技术的提升是改善装载机效能的关键。
首先,操作者应接受专业培训,提高操作技能和安全意识。
其次,可以利用现代技术手段,如安装摄像头和传感器等设备,实时监控装载过程,并通过数据分析优化装载操作。
此外,合理调整装载机的参数和设备,以适应不同木材的装载需求,降低损耗和提高装载效率。
3. 改进机械设备改进机械设备是提升装载机效能的重要手段。
首先,可以通过升级机械设备来降低能耗和提高功率。
选择具有高性能和高效率的发动机和液压系统,可以降低油耗和提高装载机的工作效能。
其次,采用先进的自动化控制系统,提高操作的精确性和稳定性,降低人为因素对效能的影响。
此外,应定期维护和保养装载机,确保其正常运行和使用寿命,不仅可以提高效能,还可以减少故障和维修成本。
4. 优化管理措施优化管理措施是提高装载机效能的重要环节。
首先,建立全面严格的作业规范和操作标准,确保每个环节都按照规定的程序和要求进行操作。
其次,加强装载机的绩效评估和考核,激励操作者积极工作,提高整体效能。
此外,注重装载机的定期检修和维护,及时识别问题和隐患,采取相应的措施,确保装载机的长期稳定运行。
总结起来,木材装载机的过程优化和效能提升可以通过优化装载流程、提升装载技术、改进机械设备和优化管理措施等方面来实现。
一种提高装载机前车架生产效率的工艺方法

一种提高装载机前车架生产效率的工艺方法我公司是装载机、推土机、压路机、旋挖钻机、专用车等工程、建设机械及国家军用工程机械产品的专业制造企业。
3吨、5吨系列轮式装载机品种多、市场需求大,但存在产能与市场需求的矛盾。
在产品试制及小批生产阶段,因产品图纸、结构不定型、产量少等原因,应按照在符合图纸要求的情况下尽量减少工装投入的原则来进行工艺流程及工艺、工装设计,而当产品结构定型并批量生产时,应在保证产品质量并满足使用要求前提下,通过采用新工艺、新技术设计并制定适合批量生产的上艺方法、最大限度地提高生产效率,并有效地降低制造成本。
1、一种5吨装载机前车架结构图1图1是一种5吨装载机前车架,由5个部件构成,按序号各部件的名称、作用及使用技术要求如下:(1)桥板(左、右各1件):下端向与装载机前桥总成的桥板面相贴,并通过螺栓紧密相联,应保证左、右两桥板面等高,并与前铰架孔D1、D2、D3中心连线垂直度0.20。
(2)转向油缸耳座(左、右各1件):通过在铰接孔穿销轴,与转向油缸相联,为保证转向油缸动作时不出现别劲的现象,左右两铰接孔位置应对称且等高。
(3)前铰接架:上、下铰接孔与后午架铰接孔之间通过销轴、轴承等件铰接相连,要求上、下铰接孔D1、D2、D3同轴度0.15。
(4)左侧板组件(序号4)及右侧板组件(序号6):应对称分布于前铰架及中间油缸支座两端,通过上端铰接孔D4与动臂相联,下端铰接孔D6与动臂油缸相联。
左、右侧板两组铰接孔相对前铰架及中问油缸支座铰接孔对称分布、并有0.15的同轴度要求,同侧上、下两组孔内开档大小及位置应一致,小允许出现动臂升降时左、右动作不同步及别劲的情况。
(5)中间油缸支座:铰接孔D5与翻斗油缸相联,要求组装后,油缸扁头左、右两端与油缸支座孔内开档均布间隙1mm左右。
2、改进前工艺情况2.1工艺流程该阶段采取工艺流程为:下料——焊前予加工——第一次对接与焊接——划线——镗孔、铣面——钻孔与攻丝——第二次对接与焊接——喷漆——入库(待装)。
装载机_前车架资料(最新整理)

目前我公司生产的ZL30F装载机,因焊接结构件的变形超差造成的失效已占相当大的比率。
本文主要针对ZL30F装载机前车架焊后变形超差率较高的问题,通过分析该前车架的具体结构形式,制定并采用了合理的焊接工艺,使前车架的焊后变形得到了有效控制。
ZL30F轮式装载机前车架是装载机的重要承载部件,属于空间半箱型的对称焊接结构,其主要组成部件有左、右翼箱,翻斗缸座,前板,上横梁,铰接架,下梁和桥安装板等。
用Solidege 三维软件建立的三维实体模型及其组成部件如图1所示。
前车架所有部件之间的连接均为连续角焊缝连接。
右翼箱1和左翼箱2主要由与前板和上横梁及铰接架相连接的翼板、外翼板、筋板、贴盘等组成。
翼板和外翼板的厚度均为16 mm。
翻斗缸座3主要组成件的厚度为24 mm。
前板4的厚度为10 mm。
上横梁5为折弯件,板厚为24 mm。
铰接架6主要组成件上、下铰接板的厚度为36 mm,4块筋板的厚度为20 mm。
下梁7的厚度为12 mm。
桥安装板8的厚度为30 mm。
材质均为焊接性能良好的低碳合金高强度钢Q345A。
图2所示为前车架主要结构尺寸。
其中宽度方向的3个尺寸810 mm、1015 mm±1.3 mm、 1 244 mm为结构关键尺寸。
1 焊接方法的选择CO2气体保护焊作为一种高效、高质量、低消耗的焊接方法,在国内工程机械行业车架等结构件的焊接中得到广泛应用,我公司装载机前后车架的焊接也采用CO2气体保护焊工艺。
2 ZL30F装载机前车架焊接工艺参数对于ZL30F装载机前车架,其组成工件的板厚大多为12~24 mm,只有上下铰板和桥安装板厚度达到30 mm以上。
由于颗粒过渡焊接的电弧穿透能力强,熔深大,焊接效率高,适合于12~50 mm中厚板焊接,因此该车架的焊接采用颗粒过渡焊接,焊接工艺参数见表1。
3 前车架焊接变形的预防措施据统计,在采用本文介绍的工艺改进措施之前,前车架的最大变形量达到4.5~5.5 mm,集中反映在前车架上部左右翼箱上面两铰接孔横向尺寸的收缩变形上,变形超差率达到20%以上,其中85%的变形量达到4 mm。
小型装载机前车架加工工艺研究

小型装载机前车架加工工艺研究摘要:前车架是轮式装载机的关键结构件之一,它将后车架、动臂和前驱动桥联接起来,承担整机静态载荷、铲运工作载荷和转向等关键功能。
它的结构比较复杂,由左/右箱、支座、上下铰链等下级部件拼装焊接,然后通过机械加工,把前铰接孔和相应的定位面加工成尺寸。
其中,关键尺寸用于连接前驱动桥总成和后车架。
关键词:装载机;前车架;内端面加工针对实际的生产要求,采用了一种新型、高效的数控工具,以提高工作效率和减少工人的劳动量为目的,有效地克服了针孔内部的自动切削问题,减少了工人的工作量,并使其工作效率得到了明显的改善。
1小型装载机前车架结构1.1翻斗缸支座两个筒耳对称焊接在上铰链本体和前盖后,形成一个翻桶支撑,并由铰链孔D3连接到翻斗液压缸;为确保汽缸平头安装后的间隙符合规定,两个汽缸缸盖的开口尺寸允许偏差为±0.5 mm。
1.2上下铰接体两个上部铰链板(每一个尺寸)与竖板、筋板等组合成一个上铰链主体,该上铰链孔D4具有上铰链孔D4;两个下部铰链板(每一个尺寸)与竖板、筋板等组合成一个下部铰链主体,该下部铰链孔D5具有下铰链孔D5;上、下铰链孔的共轴度是0.15毫米,每个铰链板的开口尺寸公差是±0.5毫米,从而使前框架通过上下铰链主体上的铰链孔与后框架通过销轴、铰链轴承铰链连接时,不会出现由于上下轴的不同而造成的“别劲”。
1.3转向缸支座左、右转向缸支架在前后框架上是对称的,它们由铰链孔D6穿过销轴与转向缸相连,左右两套铰链孔D6必须是对称的,高度是等高的,这样才能确保在操纵时不会出现“别劲”的情况。
1.4前桥连接板为了确保装载机的移动过程的稳定性,两个前轴连接板是与前传动轴连接的零件,它的要求是对称的,并且具有0.1毫米的平面度,并且与铰链孔D4和D5的垂直度是0.15mm。
1.5左右箱体左侧弯曲件和左侧弯曲件组成左侧箱体,右侧弯曲件和右侧面板形成右侧箱体,上部铰链孔D1由销轴连接于动臂油缸,下部铰链孔D2由销轴连接于动臂油缸,因此,需要在上下铰接孔D4、D5和翻斗筒铰接孔D3的两侧对称布置,每一套铰接孔的共轴度为0.12毫米,以确保起重臂在操作过程中左右协调,不会产生“别劲”的情况。
装载机的工作效率如何提升?
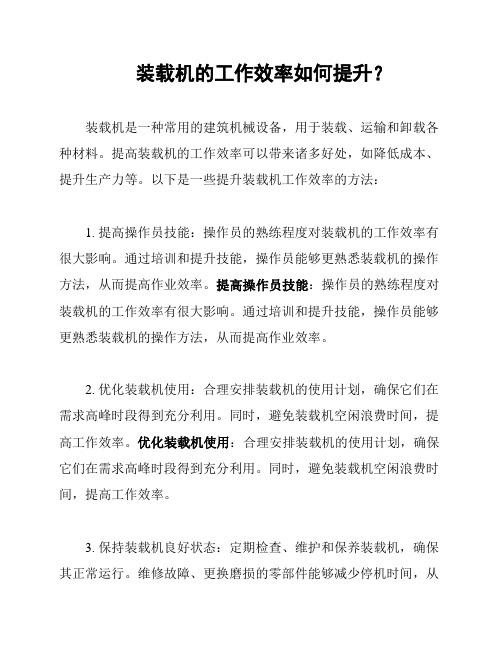
装载机的工作效率如何提升?装载机是一种常用的建筑机械设备,用于装载、运输和卸载各种材料。
提高装载机的工作效率可以带来诸多好处,如降低成本、提升生产力等。
以下是一些提升装载机工作效率的方法:1. 提高操作员技能:操作员的熟练程度对装载机的工作效率有很大影响。
通过培训和提升技能,操作员能够更熟悉装载机的操作方法,从而提高作业效率。
提高操作员技能:操作员的熟练程度对装载机的工作效率有很大影响。
通过培训和提升技能,操作员能够更熟悉装载机的操作方法,从而提高作业效率。
2. 优化装载机使用:合理安排装载机的使用计划,确保它们在需求高峰时段得到充分利用。
同时,避免装载机空闲浪费时间,提高工作效率。
优化装载机使用:合理安排装载机的使用计划,确保它们在需求高峰时段得到充分利用。
同时,避免装载机空闲浪费时间,提高工作效率。
3. 保持装载机良好状态:定期检查、维护和保养装载机,确保其正常运行。
维修故障、更换磨损的零部件能够减少停机时间,从而提高工作效率。
保持装载机良好状态:定期检查、维护和保养装载机,确保其正常运行。
维修故障、更换磨损的零部件能够减少停机时间,从而提高工作效率。
4. 合理管理装载区域:将装载区域规划为合理的布局,便于装载机操作员进行装载和卸载作业。
合理配置储存区、装载台和卸载区,减少装载机移动距离,提高工作效率。
合理管理装载区域:将装载区域规划为合理的布局,便于装载机操作员进行装载和卸载作业。
合理配置储存区、装载台和卸载区,减少装载机移动距离,提高工作效率。
5. 使用先进技术:采用先进的装载机技术,如自动化控制系统、传感器技术等,可以提高装载机的准确性和响应速度,进而提升工作效率。
使用先进技术:采用先进的装载机技术,如自动化控制系统、传感器技术等,可以提高装载机的准确性和响应速度,进而提升工作效率。
6. 优化运输路线:规划合理的运输路线,减少装载机移动时间和距离。
避免多余的转弯或绕行,提高装载机的工作效率。
提高机械加工生产率的工艺措施

提高机械加工生产率的工艺措施
提高劳动生产率不单纯是一个工艺技术问题,而是一个综合性问题,涉及到产品设计、制造工艺和生产组织管理等方面的问题。
这里仅就通过缩短单件时间来提高机械加工生产率的工艺途径作一简要说明。
缩短基本时间
大批大量生产中,基本时间在单件时间中占有较大比重。
缩短基本时间的主要途径有以下几种:(1)提高切削用量增大切削速度、进给量和背吃刀量都可缩短基本时间。
但切削用量的提高,受到刀具耐用度和机床刚度的制约,随着新型刀具材料的出现,切削速度得到了迅速的提高。
目前硬质合金刀具的切削速度可达200m/min,近年来出现的聚晶人造金刚石和聚晶立方氮化硼新型刀具材料,其切削速度可达900m/min。
采用高速磨削和强力磨削可大大提高磨削生产率,目前,国内生产的高速磨削磨床的砂轮磨削速度已达67m/s,国外已达90~120 m/min。
强力切削的切入深度可达6~12mm, 最高可达37mm。
(2)减少或重合切削行程长度减少切削行程长度也可以缩减基本时间。
例如,用几把刀同时加工同一表面或几个表面,或采用切入法加工,如图所示。
若采用切入法加工时,要求工艺系统具有足够的刚性和抗振性,横向进给量要适当减少以防止振动,同时要求增大主电动机的功率。
a)合并工步;b)多刀车削;c)横向切入法车削
(3)采用多件加工这种方法是通过减少刀具的切入、切出时间或使基本时间重合,从而缩短每个零件加工的基本时间,来提高生产率的,如图所示。
其中图a为多件顺序加工;图b为多件平行加工;图c 为平行顺序加工。
怎么提高车辆生产率方案

怎么提高车辆生产率方案在车辆制造行业,提高生产率是一直以来的目标。
随着技术的发展和市场形势的变化,企业需要不断寻求创新和优化,以提高生产力和降低成本,保持竞争力。
以下是几种可行的提高车辆生产率的方案:1. 加快工艺流程工艺流程是车辆生产的关键环节。
在这个环节中,每一道工序的改进都能提高车辆生产效率。
因此,企业应该不断地进行工艺流程优化,尽量简化交接工序,减少人力操作等,从而提高生产效率。
2. 采用智能化制造车辆制造业需要进行协调和管理,这需要一个实施智能化制造系统的过程。
智能化生产中心和职业技能教育等系统能帮助设备实现自动化生产,提升生产力和品质。
随着Artificial Intelligence (AI) 的快速发展,即将进入颠覆性创新的智能制造,企业也可以考虑在自动驾驶,电池技术和信息管理系统等方面进行开发和应用。
因此,企业可以考虑加大智能化制造的投入,以提高生产力和降低成本。
3. 建立多品种多批量生产现在的汽车市场需求多样化和生产需求快速变化,因此建立多品种多批量生产具有重要的意义。
这种模式可以有效地降低单一产品生产成本,随时调整生产制造计划,提供更快速,更有效的交付。
因此,企业可以考虑采用这种生产模式以提高生产率和满足市场需求。
4. 优化产能规划产能规划是企业中一个重要的环节,也是优化生产力的关键因素之一。
如果优化不好,可能会导致低估项目的产能或需要额外工作,导致生产成本增加。
因此,企业应该对产能进行规划,确定合理的产能规模,避免过量生产和产能不足的情况发生。
5. 加强供应链管理快速和有效的供应链也是提高生产力的必要条件。
制造商需要与供应商密切合作,优化供应链,减少生产流程中的错误和损失,提高生产效率,保证制造商以最小的成本来实现最大的产出效益。
总结:提高车辆生产率是一个复杂而持续性的过程。
企业需要根据自身生产环境和市场需求制定适合的方案,加强管理和优化,以提高生产力和降低成本,保持市场竞争力。
物理提高装载机工作效率的建议
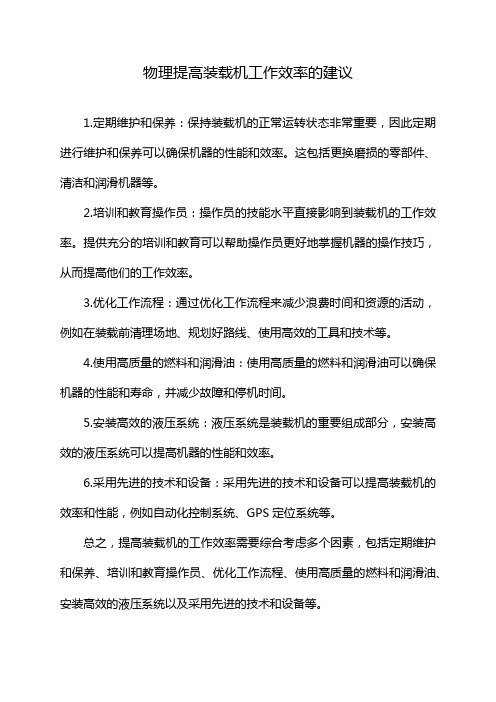
物理提高装载机工作效率的建议
1.定期维护和保养:保持装载机的正常运转状态非常重要,因此定期进行维护和保养可以确保机器的性能和效率。
这包括更换磨损的零部件、清洁和润滑机器等。
2.培训和教育操作员:操作员的技能水平直接影响到装载机的工作效率。
提供充分的培训和教育可以帮助操作员更好地掌握机器的操作技巧,从而提高他们的工作效率。
3.优化工作流程:通过优化工作流程来减少浪费时间和资源的活动,例如在装载前清理场地、规划好路线、使用高效的工具和技术等。
4.使用高质量的燃料和润滑油:使用高质量的燃料和润滑油可以确保机器的性能和寿命,并减少故障和停机时间。
5.安装高效的液压系统:液压系统是装载机的重要组成部分,安装高效的液压系统可以提高机器的性能和效率。
6.采用先进的技术和设备:采用先进的技术和设备可以提高装载机的效率和性能,例如自动化控制系统、GPS定位系统等。
总之,提高装载机的工作效率需要综合考虑多个因素,包括定期维护和保养、培训和教育操作员、优化工作流程、使用高质量的燃料和润滑油、安装高效的液压系统以及采用先进的技术和设备等。
- 1、下载文档前请自行甄别文档内容的完整性,平台不提供额外的编辑、内容补充、找答案等附加服务。
- 2、"仅部分预览"的文档,不可在线预览部分如存在完整性等问题,可反馈申请退款(可完整预览的文档不适用该条件!)。
- 3、如文档侵犯您的权益,请联系客服反馈,我们会尽快为您处理(人工客服工作时间:9:00-18:30)。
2 改进前工艺情况
21 工艺 流程 .
该 阶段 采取工艺 流程 为 :下料一 焊 前予加 工一第
一
次对 接与焊 接一 划线一 镗孑 、铣面 L
钻孔与 攻丝~
图l
第 二 次对 接 与焊 接一 喷漆一 入库 ( 装 ) 待 。
2 0 . 0建设 机械技 术与 管理 1 0 81 29
转 向油 缸 、后 车 架 、前 车 桥 等 的 关 键部 件 。因 其组 成 零 件 多 、结 构 复 杂 、各 铰 接 孔 的尺 、精 度 、表 面 粗糙 度 及 空 间 形 』 ‘
位误差要求高 、制造工序多、生产周期长 、大型镗床、铣床、钻床等加工设备 占用量大等 ,一直是影响装载机产能的
图 1 是一 种 5吨装 载机前车 架 , 由 5个部 件构成 联 。左 、右侧 板两组铰 接孔相 对前铰 架及 中间 油缸支
升 降时左 、右动 作不 同步 及别劲 的情 况 () 5 中间油缸支座:铰接 孔 D 与翻斗油缸相联 ,要 5
求组装 后 ,油缸扁 头左 、右两 端与油缸 支座 孔 内开档
用车 等工程 、建设 机械 及 国家军 用工程机 械产 品 的专 成的桥板面相贴 ,并通过螺栓紧密相联 ,应保证左 、右 业制造企 、 。3吨 、5吨系列 轮式 装载机品种 多、市场 两桥板 面等高 ,并与前铰架 孔 D】 2 j j , 、D 、D3中心连线 需求 大 ,但 存在 产能 与市场需 求的 矛盾 。在产 品试制 垂直 度 02 .0 及小批 生产 阶段 ,困产 品图纸 、结构 不定 型 、产量 少
满足 使用要 求前提 下 ,通 过采 用新工 艺 、新技术 设计 通过销轴 、轴承等件铰接相连 ,要求上 、下铰接孑 、 L Dl
并制 定适 合批量 生产 的工 艺方法 、最 大 限度地 提 高生 D 、D3同轴度 0 1 , 2 .5 产效率 ,并有 效地 降 低制造 成本 。 () 4 左侧板组件 ( 序号 4 及右侧板组 件 ( ) 序号 6 : )
的垂直度丰要 靠找正 的精确程度保 证,工件找正极为耗
费时间很长 ,而加工过程 中由于孔距远 、 刀杆刚性太差
() 3 第一次对接 与焊接 :利 用简易对接平 台等工装
在上述 予加工 过的 饺接孔 中穿轴 对接 各部什 ( 不带 转
的划线 ,而对 于镗床加l工序来说 ,需要加工各铰接孔 _ [
易出现孑 镗 圆的 问题 ,因此应在焊 至车 架前 在 个 L 零 或小 部什上子 加工 前铰接 架 、左 、台 侧板 、中间
油缸 支座上 D1 D6各铰接孑 一 般根据焊 接变形 情 Lf 况 ,单边 可 留l】 』上量 5 75 m) J I ~ .r ,此 步 可在 单个零件 a 或 小部 什上在 小型镗 床 、车 床或钻 床完 成
( ) 前予加 工 :因待镗各 铰接 孔仗予割而不予加 2焊
工 孔径 7 支位置误 差较大 、再 J 上焊 接 后的孔位 变化极 J 【 】
232 生产效 率低 : .. 主要表现在 如下几个 方面
() 1 焊接 :两次对接 与焊接. 吊装及转运 费事。 () 2 机加工 :因车架各铰接孔均 为焊 后加工 ,不仅 造成需 3 吊装 、翻转才能完成各加工孔及必要找正线 次
酪 零冀 瓣
毒
瓣 誓颡
22 各 工序主 要 内容 .
() 1 下料 :各组成零 什的型 、板件下料 及大型板 件
校 平
一
关系很大 。对于象前车架这 样的大型结构件 ,划线误差 般在 0 左右, . 5 相应按 线镗床加工上述各处铰接 孔前找 正误差大 ,因此加工的位置精度误差大 ,甚至影响使用。
主 要 因 素 ,本 文 介绍 丁… 种 可 有 效提 高 装 载 机 前车 架 生 产效 率 的 工 艺方 法 。
关键词 :装载机
前车架 铰接孔
精确定位镗孔 1装 =
我公司是装载机 、推土机 、压路 机 、旋挖钻机 、专
() 1桥板 ( 、右各 1 ) 左 件 :下端 面与装载机前桥总
应对 称分 布于 前铰架 及 中间油 缸 支座两端 ,通过 上端
l 一种 5 吨装载机前车架结构
按 序号各部 件的名 称 、怍用及 使用技 术要求如 下 :
铰接 孔 D4与动臂相联 ,下端铰接 孔 D 6与动臂油缸相 座铰接孔对称分布 、并有 01 . 5的同轴度要 求 ,同侧上 、 下两 组孔 内开档 大小 及位置 应一致 ,不允许 出现动 臂
一
种 提 高装 载 机 前 车 架 生 产 效 率 的 工 艺 方 法
On n f c n co mp o i gPr d c i eEf ce c f eKi d o h i fI r v n o u t f in yo Te v i
Fr ntBo a eo a e o dy Fr m fLo d r
■郑州字通 重工有限公 司 张丙文 / H NG B n we 王建 全 / NG J n u n Z A ig n WA i q a a
董
摘
学 /O u 李 D NG X e
瑛 /I ig 尚俊鹏 /HA G Jn e g L n Y S N u p n
要 :前车架作为装载机大型关键核心结 构什之 …,是连接工作装置动臂 2 转向油缸耳座 ( 左 右各 1 ) 件 :通过在铰接孑 L
等原 因 ,应按 照在符 合 图纸要 求的情 况下尽 量 减少工 穿 销轴 ,与转 向油缸 相联 ,为保证 转 向油 缸动 作时不
装投 入的原 则来进 行工艺 流程 及工艺 、工 装设计 ,而 出现别劲 的现象 ,左 右两铰接 孔位置 应对称且 等高 当产 品结构 定型并批 量生 产时 ,应在 保证产 品质 量井 () 3 前铰接架 :上 、下铰接 孔与后车架铰接孑 之间 L