利用子结构动态特性优化设计抑制制动器尖叫
制动器刹车噪音的控制研究
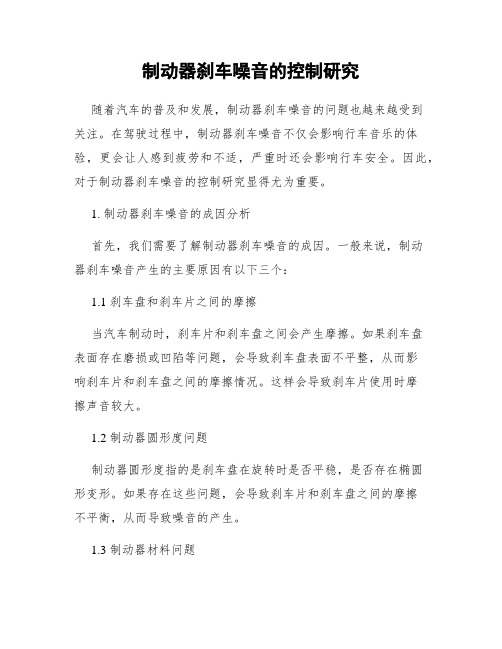
制动器刹车噪音的控制研究随着汽车的普及和发展,制动器刹车噪音的问题也越来越受到关注。
在驾驶过程中,制动器刹车噪音不仅会影响行车音乐的体验,更会让人感到疲劳和不适,严重时还会影响行车安全。
因此,对于制动器刹车噪音的控制研究显得尤为重要。
1. 制动器刹车噪音的成因分析首先,我们需要了解制动器刹车噪音的成因。
一般来说,制动器刹车噪音产生的主要原因有以下三个:1.1 刹车盘和刹车片之间的摩擦当汽车制动时,刹车片和刹车盘之间会产生摩擦。
如果刹车盘表面存在磨损或凹陷等问题,会导致刹车盘表面不平整,从而影响刹车片和刹车盘之间的摩擦情况。
这样会导致刹车片使用时摩擦声音较大。
1.2 制动器圆形度问题制动器圆形度指的是刹车盘在旋转时是否平稳,是否存在椭圆形变形。
如果存在这些问题,会导致刹车片和刹车盘之间的摩擦不平衡,从而导致噪音的产生。
1.3 制动器材料问题刹车片和刹车盘的材料会直接影响到刹车噪音的产生。
如果刹车片和刹车盘的材料不配合,会产生刹车噪音。
此外,如果刹车材料本身就是噪音较大的,也会导致制动器刹车噪音的产生。
2. 制动器刹车噪音的控制方法了解了制动器刹车噪音的产生原因,我们可以采取一些控制方法来降低制动器刹车噪音。
下面我们简单介绍一下几种常用的制动器刹车噪音的控制方法:2.1 制动器片材质优化首先,我们可以通过改善刹车盘和刹车片的摩擦性能来降低噪音的产生。
在选择刹车片和刹车盘的材料时,需要保证材料相互匹配,摩擦系数要适当。
此外,可以将含有噪音源的材料进行改进,例如添加特殊的填料和改变材料的结构,来降低刹车噪音。
2.2 制动器片形状优化通过优化制动器片的形状,可以减小刹车噪音。
例如,可以调整刹车片的形状和间距,来降低运动时的摩擦。
2.3 制动器减震优化针对一些轻质车辆和高速车辆,有时制动器产生刹车噪音也与车辆的共振有关。
在这种情况下,可以通过制动器减震来降低共振噪音。
2.4 制动器生产与安装优化生产过程和安装过程对于制动器刹车噪音的产生也有一定影响。
面向制动尖叫抑制的制动盘结构优化

2022年第46卷第12期Journal of Mechanical Transmission面向制动尖叫抑制的制动盘结构优化设计潘公宇1刘志康1徐旗钊2陈林2(1江苏大学汽车与交通工程学院,江苏镇江212013)(2江苏恒力制动器制造有限公司,江苏泰州214500)摘要针对汽车盘式制动器的制动尖叫问题,提出了一种基于加权制动尖叫倾向系数作为制动尖叫性能评价指标的方法。
在建立盘式制动器复模态有限元模型的基础上,通过噪声台架试验验证了模型的有效性;将中心复合试验设计、响应面(RSM)代理模型法和Pointer优化算法相结合,以加权制动尖叫倾向系数最小为优化目标,对制动盘的单侧盘面高度、散热筋高度、弹性模量和盘帽高度进行了结构优化设计。
结果表明,提出的优化设计方法能够显著提高优化求解的效率,有效降低盘式制动器在全频段内的尖叫倾向性,抑制制动尖叫噪声的产生。
关键词制动盘制动尖叫复特征值法RSM代理模型优化设计Optimization Design of Brake Disc Structure for Brake Squeal SuppressionPan Gongyu1Liu Zhikang1Xu Qizhao2Chen Lin2(1School of Vehicle and Transformation Engineering,Jiangsu University,Zhenjiang212013,China)(2Jiangsu Hengli Brake Manufacturing Co.,Ltd.,Taizhou214500,China)Abstract Aiming at the problem of brake squeal of automobile disc brake,a method based on weighted brake squeal tendency coefficient is proposed to evaluate the brake squeal performance.On the basis of estab⁃lishing a complex mode finite element model of the disc brake,the validity of the model is verified by the noise bench test.By combining the central composite test design,Response Surface Method(RSM)surrogate model method and the Pointer optimization algorithm,and taking the minimum weighted brake squeal tendency coeffi⁃cient as the optimization goal,the structural optimization design is carried out for the unilateral disc height,heat sink rib height,elastic modulus and disc cap height of the brake disc.The results show that the optimization de⁃sign method proposed can significantly improve the efficiency of the optimization solution,effectively reduce the squeal tendency of the disc brake in the full frequency band,and suppress the generation of brake squeal noise.Key words Brake disc Brake squeal Complex eigenvalue method RSM surrogate model Optimiza⁃tion design0引言制动尖叫,指车辆在制动时制动系统工作振动所产生的频率在1~16kHz的高频率噪声[1-2]。
鼓式制动器结构振动尖叫问题综述
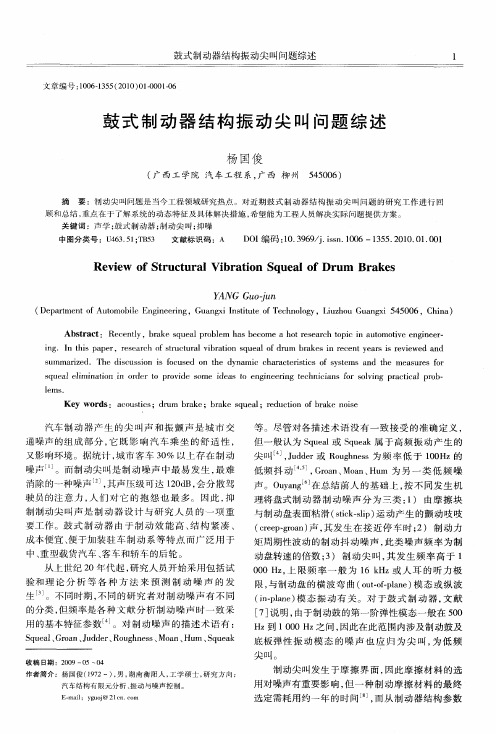
又影 响环 境 。据统 计 , 市 客 车 3 % 以上存 在 制 动 城 0 噪声 。而制动 尖 叫是 制 动 噪 声 中最 易 发 生 , 难 最 消除 的一 种 噪声 , 其声 压级 可 达 1 0 B, 分散 驾 2d 会
驶 员 的注 意力 , 们 对 它 的抱 怨 也 最 多 。 因此 , 人 抑 制制 动尖 叫声 是 制 动 器 设 计 与研 究 人 员 的 一 项 重
lm s e . Ke o d y w r s: a o sis;d u b a e;br k q a ; r d c in o r k o s c u tc r m r k a e s ue l e u to fb a e 叫声 和振 颤 声 是 城 市 交
低频 抖 动 J G o n Mon H m 为 另 一 类 低 频 噪 , ra 、 a 、 u
声 。O yn 。 在 总结 前 人 的基 础 上 , 不 同发 生 机 u ag。 按 理将 盘式 制 动 器 制 动 噪 声 分 为 三 类 : ) 由摩 擦 块 1
与制 动 盘表 面粘 滑 (t ksp 运 动产 生 的颤动 吱 吱 sc—i) i l ( re — on 声 , 发 生 在 接 近 停 车 时 ; 制 动 力 cepg a ) 其 r 2) 矩周 期性 波 动 的制 动抖 动 噪声 , 类 噪声 频 率 为 制 此 动 盘转 速 的倍 数 ; ) 制 动 尖 叫 , 发 生 频 率 高 于 1 3 其 0 0 H , 限 频 率 一 般 为 1 H 0 z上 6 k z或 人 耳 的 听 力 极
鼓式 制 动器 结构 振动 尖 叫 问题 综 述
文 章 编 号 :0 615 (0 0 0 -0 1 6 10 —35 2 1 ) 1 0 - 0 0
盘式制动器制动尖叫CAE分析及其解决方案
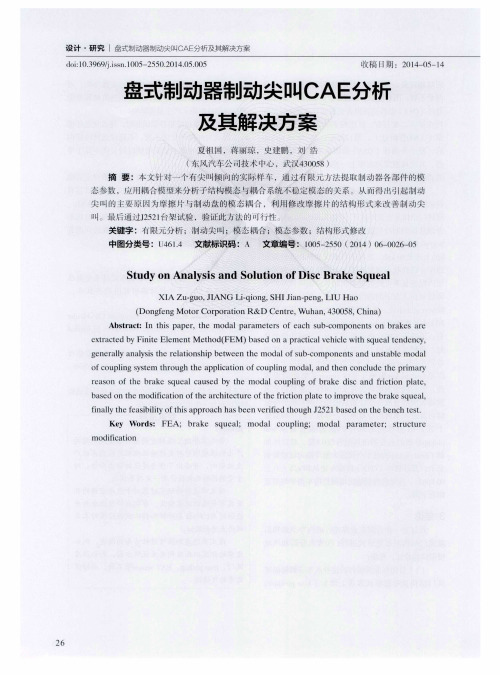
3 盘式 制动 器有 限元分 析
● ●
0
0
近。所以 ,为了研究8 5 8 0 H z 、7 5 7 7 H z 发生尖 叫的
8 8 8 8 8 8 8 8
z H 、 脚 葵
6 0 O
0 0
4
J, }
0 0
,-
利 有 限元法计 算 的尖 叫个 数往往 会多于 实
火 叫的 主要 原因为摩擦 片 与制 动黜 的模 态耦 合 ,利用 修改摩擦 片 的结 构形式 来改善制 动尖
叫. . 最后通过J 2 5 2 1 台架试验 ,验证此方法 的可行性
关键字 :有限元分析 ;制动尖叫 ;模态耦 合 ;模 态参数 ;结构形式修改
中图分类号 :U 4 6 1 . 4 文献标识码 :A 文章编号 :1 0 0 5 — 2 5 5 0 f 2 0 1 4) 0 6 — 0 0 2 6 — 0 5
St ud y o n Ana l y s i s a nd S o l ut i o n o f Di s c Br a k e S que a l
XI A Zu ・ g uo , J I A N G Li - q i o ng , S HI J i a n — pe n g , LI U Ha o
( Do n g  ̄n g Mo t o r C o r p o r a t i o n R &D C e n t r e , Wu h a n , 4 3 0 0 5 8 , C h i n a )
Abs t r a c t :I n t h i s p a p e r ,t he mo da l p a r a me t e r s o f e a c h s ub — c o mp on e n t s on br a k e s a r e
某车型盘式制动器尖叫噪声分析及改进

10.16638/ki.1671-7988.2019.01.018某车型盘式制动器尖叫噪声分析及改进*李小珊,韦进光,秦再武,纪浩(上汽通用五菱汽车股份有限公司技术中心,广西柳州545007)摘要:文章针对某车型在后盘式制动器的尖叫噪声问题,在Abaqus中建立汽车低速状态制动的有限元模型进行复模态分析,得到与测试接近、特征根实部为正值的不稳定模态。
在此基础上探究不稳定模态的影响因素来指导改进工作。
结果表明:系统摩擦系数、摩擦块的弹性模量、制动盘刚度对制动尖叫噪声有重要影响,改进后结构无不稳定模态,经实车验证无尖叫噪声出现。
关键词:制动尖叫;制动器;复模态;噪声中图分类号:U463.5 文献标识码:A 文章编号:1671-7988(2019)01-56-03Brake-squeal Noise Analysis and Improvement of a Certain Vehicle*Li Xiaoshan, Wei Jinguang, Qin Zaiwu, Ji Hao( TDC, SAIC GM Wuling Automobile Co., Ltd, Guangxi Liuzhou 545007 )Abstract: This paper studied on brake-squeal Noise of a certain vehicle’s rear brake system. The finite element model of this system was established, and the complex eigenvalue was carried out by Abaqus software. A unstable dynamic response with positive value of eigenvlue’s real part that was calculated by simulation. It’s frequency was consistent with test results. On this basis, the influencing factors of unstable frequency were researched that could be use to improve this brake-squeal issue. The results showed that system friction coefficient, brake pad’s elastic modulus, and brake disc’s stiffness have important influence on brake-squeal noise. And there was no positive value of real part in improved brake system, which shows that the optimization analysis was effective.Keywords: brake-squeal; brake system; complex eigenvalue; noiseCLC NO.: U463.5 Document Code: A Article ID: 1671-7988(2019)01-56-03前言当前绝大部分乘用车都采用前后盘式制动器通过摩擦的方式进行制动,由此产生的噪声,本质是摩擦引起,这种由于摩擦引起的振动和噪声,是机械工程领域重大的科学问题[1],具有较大学科深度与难度。
汽车制动器的应用现状及发展趋势4700字

汽车制动器的应用现状及发展趋势4700字刘军(农业部南京农业机械化研究所,江苏南京210014)摘要:制动器是汽车制动系统中重要的组成部件,其优良的性能是人们的出行安全的重要保障。
随着我国高速公路网的快速发展以及路况复杂程度的增加,人们对于制动系统工作可靠性的需要也日益迫切。
论述了现有汽车制动器的发展现状,分析各自的特点并对汽车制动器的发展趋势进行了展望。
关键词:制动器;发展现状;展望0 引言近年来,我国的高速公路网迅速发展,车流密度和行车速度逐渐增加,路况也变得更加复杂,这使得我国高速交通事故频频发生。
为了保障汽车行车的安全性,研制优良的行车制动系统已然成为了当今汽车设计的热点。
汽车制动系统要求具有足够的制动力,良好的制动可靠性,制动器是制动系统中最重要的一个部件,其好坏决定了汽车是否具有优良的制动性能。
目前用途最广泛的制动器有鼓式制动器和盘式制动器这两类。
鼓式制动器又名块式制动器,是较早出现的制动器,主要依靠制动块压紧制动轮来实现刹车。
盘式制动器刹车作用过程与鼓式比较相似,利用制动盘与静止摩擦片接触来产生摩擦从而使车轮减速实现刹车的目的[1-4]。
1 国内外研究现状1.1 鼓式制动器国内外研究现状鼓式制动器一般由制动底板、制动蹄片、制动分泵、制动鼓以及连杆弹簧等组成,它首先通过液压装置将液压力传递到制动分泵上,然后再通过连杆弹簧将制动蹄片向外推出使其与制动鼓产生相对摩擦而阻止汽车前进。
从汽车诞生至今己有百年的历史,国内外许多专家学者对制动器都做出了大量的、开拓性的研究,涉及到摩擦学、动力学、振动理论和接触力学等多个研究领域。
国内也有很多学者对汽车制动器进行了相关研究。
韩文明等[5]分析单双自由度制动蹄效能因数与摩擦片上的径向合力作用点位置和摩擦系数变化间的关系,后将制动效能因数分解为摩擦自增势或自减势和杠杆增力作用两部分,进而分析每部分制动效能因数的变化特性,并得出提高制动效能稳定性的有效方法,为鼓式制动的改进提供了理论依据。
基于制动尖叫倾向性的盘式制动器优化设计

38机械设计与制造MachineryDesign&Manufacture第11期2008年11月文章编号:1001—3997(2008)l1-0038--02基于制动尖叫倾向性的盘式制动器优化设计王朝阳郭永进(上海交通大学车辆工程,上海200240)TheoptimizationdesignofthediscbrakesystembasedonthebrakesquealpropensityWANGZhao-yang,GUOYong-jin(ShanghaiJiaotongUniversity,AutomobileEngineering,Shanghai200240,China)中图分类号:THl2,U463文献标识码:A1引言随着人们对车辆舒适性和环保要求的不断提高,制动噪声问题越来越突出,受到r仓qp界的广泛关注。
现在通常的解决方法是从试验和仿真分析人手,对制动尖叫问题研究从而提出抑制制动尖叫方案。
然而由于是事后诊断,产品的结构形状、尺寸、丁艺已确定,修改没计空I'开J的自由度已大大减少,这大大限制了T程人员的发挥。
理想的方法是在制动器的早期设汁巾考虑制动噪声问题使得噪声抑制在甲.期设计阶段。
本文将就这一问题进行探讨,使制动器的制动尖叫倾向性在产品的‘}期设计中纳入考虑范围,通过CAE结构优化技术指导产品的设计,从而实现在产品早期没计阶段抑制噪声的发生。
AndrzejBajer,VladimirBelsky等考虑制动器的摩擦阻尼、非线性因素等,通过复特征值分析对制动尖叫进行了预测,预测结果与试验结果有很好的一致性【l】。
手登封、王玉为等则针对一个有制动尖叫的钳盘式制动器,在半消声室内制动器试验台L进行制动尖叫声试验,fEd时建立了基于接触摩擦耦合的有限元模刑进行了仿真,测最统计结果与仿真预测结果基本吻合,也证明r利用有限元仿真技术能够较好的预测制动器发生制动尖叫的倾向闭。
这些研究成果使得通过有限元技术在产品开发初期将制动器的制动尖叫倾向性纳入考虑范围从而指导产品设计成为可能。
汽车盘制动器优化设计热和机械特性的研究(一)
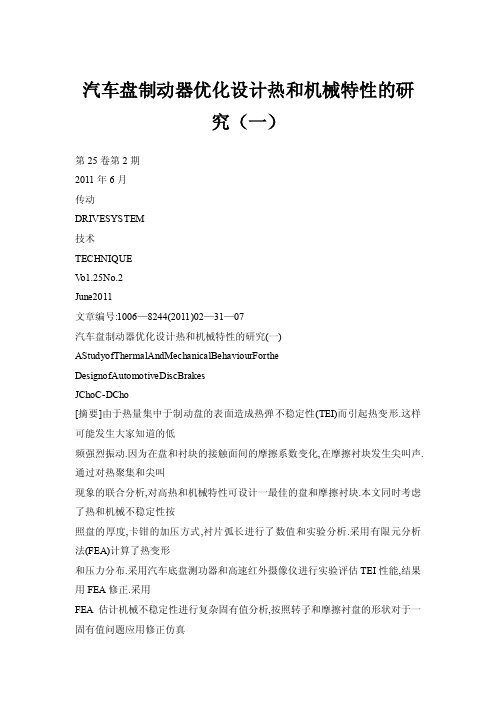
汽车盘制动器优化设计热和机械特性的研究(一)第25卷第2期2011年6月传动DRIVESYSTEM技术TECHNIQUEV o1.25No.2June2011文章编号:1006—8244(2011)02—31—07汽车盘制动器优化设计热和机械特性的研究(一) AStudyofThermalAndMechanicalBehaviourForthe DesignofAutomotiveDiscBrakesJChoC-DCho[摘要]由于热量集中于制动盘的表面造成热弹不稳定性(TEI)而引起热变形.这样可能发生大家知道的低频强烈振动.因为在盘和衬块的接触面间的摩擦系数变化,在摩擦衬块发生尖叫声.通过对热聚集和尖叫现象的联合分析,对高热和机械特性可设计一最佳的盘和摩擦衬块.本文同时考虑了热和机械不稳定性按照盘的厚度,卡钳的加压方式,衬片弧长进行了数值和实验分析.采用有限元分析法(FEA)计算了热变形和压力分布.采用汽车底盘测功器和高速红外摄像仪进行实验评估TEI性能,结果用FEA修正.采用FEA估计机械不稳定性进行复杂固有值分析,按照转子和摩擦衬盘的形状对于一固有值问题应用修正仿真结果分析接合形式.在热聚集和尖叫问题期间,讨论因考虑盘制动器性能盘和摩擦衬块的设计.[Abstract]Thethermaldistortioninducedbythermoelasticinstabi1ity(TEI)resultsinhotspo tsonthesur-faceofthebrakedisc.Thiscanincurlow-frequencyvibrationknownasjudder.Inpad—inducedsquealnoise,modecouplingoccursowingtothevariationinthefrictioncoefficientbetweenthedisca ndpad,indu—cinghigh-frequencynoise.Throughacoupledanalysisofhotspotsandsquealphenomena,an optimumdisc andpaddesigncanbedesignedforhigherthermalandmechanicalperformance.Inthisstudy,n umerical andexperimentalanalysesareperformedinaccordancewithdiscthickness,pressurizationty peofcaliper,andliningarc1ength,consideringthermalandmechanicalinstabilitysimultaneously.Therm aldeformation andpressuredistributionarecalculatedusingafiniteelementanalysis(FEA).Forevaluating TEIperform—ance,experimentsareperformedusingachassisdynamometerandahigh—speedinfraredcamera,andthere—sultsarecorrelatedwithFEAresults.Acomplexeigenvalueanalysisisconductedtoevaluate mechanicalin—stabilityusinganFEA.Modaltestingandsimulationsareconductedtocorrelatedarealmodel andanFEmodel,andthecorrectedsimulationresultsareappliedforacomplexeigenvalueproblemtoan alysecoupledmodesaccordingtorotorandpadshapes.Theresultsondiscbrakeperformancesconsideringt hediscand paddesignarediscussedintermsofhotspotsandsquealproblems.关键词:热弹不稳定性热点强烈振动摩擦衬块发生尖叫声热不稳定性机械不稳定性复杂固有值分析Keywords:thermoelasticinstabilityhotspots,juddervibrationpad—inducedsquealnoisethermal instabilitymechanicalinstabilitycomplexeigenvalueanalysis中图分类号:U463.512文献标识码:B1前言因为车辆制动有严重的热负荷和机械负荷作用,故摩擦盘式制动装置将有噪声和振动出现的倾向.这种噪声,振动和车身跳动(NVH)现象不仅不舒适而且危险.此外,热变化是因摩擦热产生的,由于旋转部件和摩擦衬盘衬材料间摩擦系数改变使盘与衬块间机械压力发生变化.该压力变化是非线性现象,如摩擦现象一般是非线性偶合问题.特别在汽车盘制动装置内,热的强烈振动和尖叫声是非线性的组合现象.这些现象分担的核心设计系数如转子和衬之间的压力分布,转子和衬块(刚度)的形状,排气口的数目,冷却性能和摩擦力变化,因此,为盘制动器的优化设计,在考虑强烈振动的同时分析尖作者简介:H—JCho和C-DCho:DepartmentofMechanicalEngineering,InhaUniversity,Iheheon,RepublicofKo rea一31—H—JCho等:汽车盘制动器优化设计热和机械特性的研究(一)叫声.当转子和衬块间超过某确定的滑动速度(临界速度)产生严重的摩擦热,则发生热弹性变形[1].一些临界因数如临界速度,外界温度,径向振摆和盘厚度变化(DTV)都可造成制动盘的热变形.此外,频繁制动也会在制动盘内引起大的热变形.这些工况造成相对大的热变形和热聚集,它是热强烈振动的原因之一].热强烈振动是一个大振幅但低频率(10—30Hz)的一种振动,它是盘制动装置经过轴套, 悬架,转向盘制动踏板和底板传给驾驶员[4],而且伴生常见的高温热聚集.它很容易导致材料损坏,包括形成盘表面热裂开.该热聚集现象,也理解为摩擦引起的热弹性不稳定性(TEI)首先是由Barber[3] 对含摩擦热的滑动装置检测和表述的.Lee和Bar—berL5假定温度波动和应力场随时间指数性地增大解TEI问题.他们表明不稳定的开始常常具有不对称的波动特征,相应于圆周边弯曲变形模式,导致热聚集于盘两边交替位置.而且,采取汽车盘的模型实验表明用两半空间模型计算临界速度估计过高.Y eo和Barber[6j导出一紊动方法的有限元(FE)方程式,其中利用线性控制方程求得以时间指数变化紊动的各个可变的解.Yi等I7采用有限元分析(FEA)对盘制动器和离合器的几何学解TEI 问题.他们表明要素波长(热点空间)和I临界速度用二维(2D)分析包括弯曲模式很好预测,达到三维(3D)效果没有实质性影响.Yi等I8]通过FEA分析和实验论证了制动盘的TEI问题.在TEl理论基础上,对承受热强烈振动的制动器系统建立了一个标准的设计准则.尽管努力去降低和消除发生尖叫声,但大多数制动器的NVH问题始终存在于汽车工业中.当驾驶减速或以低速制动车辆时,将产生高频噪声.因为结合到制动器系统尖叫声不能很容易解决,因此尖叫声应仔细评估.采用有限元(FEA)方法有二个主要方面可以仿真和分析制动器的尖叫声:一种是非线性瞬态仿真或动态瞬变分析和另一种是线性或非线性稳态分析,采用复杂模式估算[9.两种方法均各有其优点和限制;分析和预测尖叫声的精度,按照转子和其他制动部件的典型特性,两者在仿真和试验间必须具有好的修正[9].已经有很多通过研究仿真和实验方法的研究,Dessouki等[1]表明尖叫声特征为卡钳托架引起的为(2—6.5kHz)级,衬块引起为(4-1lkHz)级和转子引起为(7—16kHz)级. Junior等口采用FEA研究了一些工作参数如摩擦一32一系数,材料特性,磨损和隔离物对盘制动装置的影响.Fieldhousel_1研究了一些与衬块形状一致的噪声频率,并表明用一种方法可以预测和开发卡钳工作如单盘或双盘形式的动态不稳定性.Kung等I1] 采用复数固有值方法研究了低频尖叫声问题,并指出该方法对尖叫声分析是有效的.Dihau和JiangL1用有限元rFE]方法研究了形式耦合解复数固有值问题.Triches等[1采用典型的分析技术选择合适的制动器阻尼器降低尖叫声.Kung等I2叩采用新的复数固有值能在ABAQUS标准内对前盘制动器分析尖叫声问题.他们从预载荷考虑用公式阐明复数固有值的基本状态表明接触条件和其他非线性的影响.Giannini和Seslieri[2妇采用复数固有值分析和实验研究了模型的稳定性,他们讨论了盘和衬块动力学的关键作用.本文按照三个旋转部件试件研究了TEl和机械不稳定性:单盘加压和二卡钳加压型式(单盘和双盘型式)的衬片弧长.对于AE1分析采用一制动器测功仪和一高速红外摄像仪.按照制动器盘的形状如盖和环槽槽形成锥角,该角改变盘和衬块间的接触压力分布[2_29],而衬片的压力分布改变是一主要因数,该压力分布大大影响了热和机械的不稳定性以及热的性能.首先采用一有限元(FE)商业编码ABAQ056.6考虑转子几何学计算在常温下热变形和锥角,按照卡钳加压形式计算衬块的压力分布,分析结果并与TEI实验结果相比较.该分析结果采用TEl基本商业软件HOTSPOTTE仅TM求得临界速度.比较和分析由实验和分析方法求得的结果.用盘和衬块的典型试验和FEA确定处理一复数固有值分析,固有频率和模式,采用有限元(FEA)方法,按照盘厚度,衬片弧长和加压方式解复数固有值问题,为评估机械性能确定不稳定的配对模式和机械不稳定性的差异.最后,采用这些结果,评估和分析优化设计的热和机械性能.图1示盘制动装置优化设计的诸要素,本文考虑的最佳盘制动器设计要素如图点线框内所示.2热变形和结构有限元分析(FEA)盘制动器旋转部件由盖部分,环槽部分,排气口,外和内片组成(图2(a)).由于内及外片与制动器衬块接触而产生摩擦热,这是旋转部件假定的主要热源.发热过程如热传导,对流和辐射在旋转部件产生温度梯度并造成热变形.此外,内及外片的厚度由于厚度方向热传导速度不同,不仅控制了接H—JCho等:汽车盘制动器优化设计热和机械特性的研究(一)触表面热局部集中,而且还影响了旋转部件的刚度(特别是片外面).图2(b)和(c)示本文采用的按照旋转部件厚度和卡钳加压方式的几何学.该三个采用的几何模型是一个基本模型,2t—Ot模型和2t-2t图1盘制动装置最佳设计要素示意图点线框内为本文考虑的优化设计要素Fig.1Schematicdiagramoftheoptimaldesignfactorsforthediscbrakesystemthedotted boxshowsoptimaldesignfactorsthatwereconsideredinthisstudy熟(外一热)ljat(outer-hat颈Neck'外平面';0mboardplate排气口Airv平面Inboardplate(b)(c)图2旋转部件和卡钳加压方式的几何学:(a)制动盘横截面图;(b)旋转部件对应盘厚度的几何学;(c)卡钳加压方式(单盘和双盘)该模型为一个基本,2t-Ot和2t-2tFig.2Geometryofrotorandcaliperpressurizationtypes:(a)Cross-sectionviewofthebrakedi sc;(b)geometryoftherotorinaccordancewithdiscthicknesses;(c)Caliperpressurizationtype(one-potandtwo-pot).Themodelsareb ase,2t-Ot,and2t-2t.H—JCho等:汽车盘制动器优化设计热和机械特性的研究(--)模型,所有三个旋转部件有相同的直径254mm.在2t-0t旋转部件模型内,外片厚度减至2mm.同样,在2t-2t旋转部件内,内及外片两者厚度均为2mm.2.1有限元(FEA)模型和边界条件旋转部件由于摩擦热的热变形在盘和衬块间,产生不均匀的压力分布.旋转部件和衬块间的接触压力大大影响TEI和机械的不稳定性.该摩擦热源是法向力,摩擦系数和相对速度的函数.因为锥角,径向偏振,DTV,和卡钳加压方式使盘和衬块之间发生偏心的压力分布,并导致很快产生不均匀的热,在这些因数中,采用合理的旋转部件形状设计可减小锥角,为此,可构成热变形+和压力分布FEA.图3(a),(b),(c)示盘制动器热变形和结构分析用的3D有限元(FE)模型.图3(b)中示黑灰色表面是在后片上加压位置.一一(c)图3盘制动器的FEA:(a)在相应卡钳加压方式热变形和结构分析的3DFE模型;(b)内及外衬块(双盘卡钳)的3DFE模型;(c)锥角;(b)示黑灰表面示在背片上加压位置Fig.3FEAofthediscbrake:(a)3DFEmodelforthermal deformationandstructuralanalysisinaccordancewith caliperpressurizationtype;(b)3DFEmodelofthein—boardandoutboardpad(two—potcaliper);(c)coningangle.Thedarkgreysurfacein(b)showthelocation ofappliedpressuresonthebackplate因为运转时旋转部件的温度分布是变化的,故锥角大小不固定.通常有限元分析和实验中通过调整制动状况可以获得某个需要的锥角,热应力和一34一热容量口..但在本研究中,假定平均温度分布为100.C,在热FEA中,对应于旋转部件的厚度求出相对的锥角.通过仿真结果,相应于不同的内及外片厚度,评估和分析其热特性.采用非线性压力分布FEA对应于加压状况和衬块形状进行分析FEI和机械不稳性.为了在衬块上产生一压力分布,相应于单盘和双盘加压卡钳加压力状况应反映卡钳位置形状.采用静态和动态两状况.在静态状况,转速为零和加一1.5MPa的静态压力.在动态状况,旋转部件的转速,加压大小和摩擦系数分别为10r/rain,1.5MPa和0.4.在TE1分析中,衬块的压力分布可采用预定的有效压力和有效衬片弧长.它可控制热点数目和临界速度[3...而该热点数和临界速度密切与衬片弧长有关[5].因此,利用有效压力和有效衬片弧长概念可使TEI仿真更精确.采用ABAQUS6.6一个商业FEA包进行热变形和结构分析,计算锥角和压力分布.2.2仿真结果2.2.1热变形分析用热结构FEA相应于制动器盘的厚度计算锥角.表1示内片在100.C的锥角和变形仿真结果. 锥角的相对比值是旋转部件试样的锥角和基本旋转部件之间的比,结果表明,锥角有一个相对低的绝对值.但是因为常温的边界条件必须按旋转部件形状达到一相对热变形差,故相对锥角差比绝对锥角更重要.该结果指出环槽部分的几何差异大大起到几何约束作用,它造成变形差异.因此,内和外片厚度不仅对结构特性而且还对热变形性质有显着影响.在实际汽车中,在剧热和机械负荷下,旋转部件边缘变形比不均匀压力的作用由DTV和径向偏振产生的具有相对大的数值.因此,它是不可忽略的.虽然径向偏振和DTV也增加盘和衬块之间的局部压力,它们与旋转部件横截面形状无关.因此,对于盘的优化设计,必须考虑热变形和旋转部件的锥角以及热容量.表1旋转部件边缘锥角和变形的仿真结果Table1Simulationresultsforconinganglesand deflectionsoftherotoredgeH—JCho等;汽车盘制动器优化设计热和机械特性的研究(一) 2.2.2结构分析旋转部件和衬片间一种均匀的压力分布是在优化设计方向一个最重要的因数.一个均匀的压力分布意谓着有较大的接触区,较宽接触带产生热和较硬的衬片,在制动器内可能造成热点和更大的噪声.一种均匀的压力分布也可能造成NVH问题.然而为获得高效的在稳态下的制动力,均匀压力分布相对比非均匀压力分布更稳定.此外,它有助于获得相对的热和机械特性以及磨损性能,因为与非均匀压力分布相比较它的压力幅值较低.卡钳加压方式和衬片弧长的不同在制动时可改变压力分布,接触区和衬片刚度.因此,为优化设计应该按照加压方式和衬块长度来分析盘和衬块之间的压力分布,特别关系到热点现象.图4示外衬块在单盘卡钳为100,909/6和80衬片弧长的压力分布,仿真条件如下:在停车情况旋转部件的转动聋宅0趸璺衬块弧长比RatioofPadarclenth,L/Lmax一制动状态衬块压力比Padpressureratioatstopstatus.一一转动状态衬块压力比Padpressureratioatrot撕onstatus(co=10rpm)……有效衬块压力比EffectivePadpressureratio裔宅.殳盏璺速度和压力大小分别为0和1.5MPa在运转状态, 旋转部件的转速,压力大小和摩擦系数分别为10r/ min,1.5MPa和0.4.表2为分析压力分布和复数固有值列出仿真条件.如图4所示,按照衬片中心轨迹的应力分布由点画曲线表示.该垂直轴是压力比P/P…,水平轴是衬片弧长比L/L,黑实曲线,破折曲线,点画曲线是制动状态衬块的压力比, 转动状态衬块的压力比和旋转部件转动状态(∞一10r/rain)衬块的压力比,它们的合成值和黑曲线一致.结果表明如衬片弧长减小,有效衬块压力比增大.对于单盘加压型式,因一较短的有效衬片弧长造成衬片的不灵敏区,该不灵敏区表明一相对低压力分布位置,该结果相对高于TE1分析,因为临界速度明显与衬片弧长有关.在转动状态,应力分析沿转动方向移动.此外,压力分布内周边和外周边发生差异,由于圆周方向相对速度不同.衬块弧长比蓉g专.垒蒸1.O0.80.60.40.2}单盘卡钳,80%衬块弧长lll-potcaliper,80%padarclengthf.~∥\\\=,,,,....OO.20.40.60.81.0村块弧长比RatioofPadarClenth,L/LmaxRatioofPadarclenth,L/Lm 一制动状态村块压力比Padpressureratioatstopstatus一—转动状态衬块压力比Padpressureratioatrotationstatus(co=10rpm)……有效村块压力比Effectivepadpressureratio一制动状态衬块压力比Padpress~eratioatstopstatus.一转动状态衬块压力比Padpressureratioatrotationstatus(co10rpm)…一有效村块压力比Effectivepadpressureratio图4外衬块的压力分布:(a)在100%衬片弧长压应力(b)在90%衬片弧长的压应力}(c)在8o%衬片弧长的压应力全为单盘型卡钳Fig.4Pressuredistributionofoutboardpad:(a)Compressivestressat100percentliningarele ngth,(b)Compressivestressat90percentliningarclength,and(c)Compressivestressat8Opercentliningarclength,allinaone-pot-typecaliper一35—H—JCho等:汽车盘制动器优化设计热和机械特性的研究(一)表2分析压力分布和复数固有值仿真条件Table2Simulationconditionsforpressuredistribution andcomplexeigenvalueanalysis旋转部件样件基本的,2t一0t,2t-2tRotorspecimensBase,2t-Ot,2t一2t100,9O,和8O在单盘卡钳内衬片弧长衬块样件∞,..,and.ini"garc."ghin——.one-potcahperPadspeclmens双盘卡钳内1OO衬片弧长100liningarclengthinatwo-potcaliper卡钳型式Calipertypes转速Rotationspeed作用压力Appliedpressure摩擦系数Frictioncoefficient单盘和双盘one-potandtwo~pot0.1Or/min1.5MPa0.4图5示双盘型卡钳内衬片的压力分布.其有效衬块压力和有效衬片弧长在中心迹线高于单盘型情况.关于TEI,较高的有效衬片弧长或有效压力意谓着临界速度较低I3...压力分布比单盘型相对均匀,然而上迹线的应力分布稍不均匀,它可能形成不灵敏区.该上迹线比下迹线有较高的相对速双盘卡钳,60*--2对角线减短衬块(上面)2-potcaliper,60degree2-diagonal—reducedpad(Upper)衬块弧长比RatioofPadarclenth,L/Lmax制动状态衬块压力比Padpressureratioatstopstatus一一转动状态衬块压比Padpressureratioatrotationstatus(co10rpm)……制动状态有效衬块压力比Effectivepadpressureratioatstopstatus…'转动状态有效衬块压力比Effectivepadpressureratioatrotationstatus(co=10rpm)度,该速度差在旋转部件的接触区形成压力差.在转动状况下,其结果与单盘型压力分布有相同趋向.特别,由于相对速度使压力集中于径向,内周边和外周边压力分布与圆周方向.由于在双盘型卡钳内周边和外周边的圆周方向之间的相对速度差,为降低不均匀热量介人的解决方法之一是减小径向加压位置的尺寸.当制动时相同加压力的情况下,与单盘型相比较,衬片刚度可增大.该结果结合到不稳定模式导致尖叫现象.均匀的接触压力分布也影响到制动的稳定性.因此,对于衬块形状的优化设计,不仅要考虑在径向和周向的相对速度和压力差,同时应当还要考虑卡钳的加压形状. 双盘卡钳,60*-2对角线减短衬块(中心)2-potcaliper,60degree衬块弧长比RatioofPadarclenth.L/Lmax制动状态衬块压力比Padpressureratioatstopstatus一一一转动状态衬块压比Padpressureratioatrotationstatus(colOrpm)…一制动状态有效衬块压力比EffectivepadpressureratioatstODstatus …?转动状态有效衬块压力比EffectivePadpressureratioat rotationstatus(o)=10wm)(b)双盘卡钳,60*2对角线减短衬块(下面) 2-potcaliper,60degree衬块弧长比RatioofPadarclenth,L/Lmax一制动状态衬块压力比Padpressureratioatstopstatus-一转动状态衬块压比Padpressureratioatrotationstatus(colOrpm)……制动状态有效衬块压力比Effectivepadpressureratioatstopstatus转动状态有效衬块压力比Effectivepadpressureratioatrotationstatus@=10rpm)图5衬片的压力分布:(a)在制动和转动情况下的压应力分布;(b)上,中心和下迹线的压应力分布Fig.5Pressuredistributionofthelining:(a)Compressivestressdistributionsatstoprotationc onditions;(b)Compressivestressdistributionsandtheupper,centre,andlowerpath一36~OOOOxeums∞害J00OOOO苍2T1ss2.0一葛:HH—JCho等:汽车盘制动器优化设计热和机械特性的研究(一)3热弹性不稳定性3.1实验评估TEI性能的基本标准是临界速度,高于临界速度的速度可导致发热点.热点分布在盘表面,不仅造成热强烈振动而且还引起磨损,材料损坏和热裂纹.因此,TEI性能的评估实质上是为了优化.临界速度分别按照旋转部件厚度,加压形式和主气缸压力确定的.实验中采用三种不同厚度的盘和二种不同的衬块,采用一制动器测功器用于制动,该主气缸压力为1.5和2.0bar,为检测热点,采用了高速红外线摄像仪.评估的样件为基本,2t-0t和2t一2t.采用单盘加压型整个衬片弧长即46.4.的衬块.还采用双盘加压型整个衬片弧长(49.8.)和8O(39.2.)的衬块样件.表3列出按照衬块样件和主气缸压力临界速度的实验条件.表3按照衬块样件和主气缸压力测量临界速度的实验条件Table3Experimentalconditionsformeasuringthecritical speedsaccordingtothepadspecimenandthepressure ofthemastercylinder旋转部件样件Rotorspecimens基本的,2t-0t,2t-2tBase,2t-0t,2t一2t46.4.(100衬片弧长;单盘卡钳型)46.4.(100liningarclength;one-potcalipertype)衬块弧长49.8.(i00衬片弧长;双盘卡钳型) Padarelengths49.8.(100liningarclength;two—potcalipertype) 39.2.(80衬片弧长}双盘卡钳型)39.2.(80liningarclength;two-potcalipertype)压力Pressures求得临界速度的实验步骤如下:第一步.建立底盘测功器的初始转速(在本实验中叫il为800r/min).第二步.加压力并测量旋转部件表面的温度分布.第三步.增加或减小最低速度由100r/rain并重复第二步直到热点产生.第四步.由100r/min减小转速,使其热点产生.并再由10r/rain增加转速.第五步.加压并测量旋转部件表面温度分布.第六步.由10r/min增大转速,并重复第五步直到热点发生.第七步.达到临界速度.18次试验采用不同的旋转部件厚度12次试验采用不同的衬块样件,每个设定压力进行三次试验,加压采取手动.对于所有试验的初始温度均为15.C,径向偏振小于10m.实验装置如图6所示.(b)图6实验装置:底盘测功器和高速红外线摄像仪.该高速红外线摄像仪装于盘表面垂直位置Fig.6Experimentalequipment:chassis—dynamometerand high-speedinfradcamera.Theinfraredcamerais placedperpendiculartothediscsurface.3.2预测TEI有限元分析(FEA)3.2.1理论方程式采用汽车盘制动器制动表明热传导和热弹性组合问题.两层(图7)的轴对称(3D)热传导方程式,在制动系统中可缩减为2D方程式.对于一盘制动装置,假定温度场的解超时间指数增长,按照T(x,Y,£)一To(z,.),)+[e+J0(z)](1)式中b为复数指数增长率,m为波动数,表示为复数值的实验部分.波动数是波动在2丌m和1TI的长度内波动的数目确定的,可以为任意正实数值.(,)是稳态下温度并总满足热方程式.要解热弹性接触问题,压力分布p(x,Y,)必须确定为瞬时温度场T(x,Y,)函数.Yi等口1]提出了确定这种关系的不同方法.以一矩阵形式离散化该热方程式,采用标准GalerkinFE公式和应用热弹性关系求得(下转第三期)一37—。
制动系统动力学特性及优化设计研究

制动系统动力学特性及优化设计研究制动系统是现代车辆安全性能不可或缺的一部分。
随着汽车制造技术的不断发展,制动系统的动力学特性和优化设计成为了汽车工程师和研究人员关注的焦点。
本文将探讨制动系统的动力学特性以及优化设计的研究。
首先,制动系统的动力学特性是指在制动过程中所表现出的运动学和动力学现象。
制动系统的主要目标是实现快速、稳定的制动,并确保车辆在紧急情况下能够迅速停车。
为了达到这一目标,制动系统必须具备以下重要特性:1. 制动力和制动效率:制动力是指制动系统提供的制动力矩大小,直接影响到车辆制动性能。
而制动效率则是指制动力与应用制动力时所用能量的比值,是衡量制动系统能效的重要指标。
2. 制动系统的响应时间:制动系统的响应时间必须足够快,以确保在紧急制动情况下能够迅速减速。
响应时间过长可能导致制动延迟,从而增加事故风险。
3. 制动系统的稳定性:制动过程中,稳定性是保证车辆行驶方向和质心稳定的重要特性。
制动系统应减小车辆在制动时的抖动和侧滑现象,确保驾驶员的操控稳定性。
为了优化制动系统的动力学特性,研究人员和工程师采取了多种技术手段和策略。
以下是一些常见的优化设计方法:1. 制动系统设计参数的优化:通过对制动系统的设计参数进行优化,可以提高制动力和制动效率。
例如,优化制动盘和刹车片的材料和结构,可以降低制动过程中的热衰减,提高制动力和制动效率。
2. 制动系统的液压传动优化:液压传动是现代汽车制动系统中常用的传动形式,优化液压传动系统的结构和工作状态,可以提高制动力的输出和响应速度。
例如,采用高性能的制动泵和优化的刹车油路系统,可以提高液压传动的效率和响应性能。
3. 利用电子控制技术:现代汽车制动系统中广泛采用了电子控制技术,通过电子控制单元(ECU)对制动系统进行监测和控制。
通过优化ECU的算法和参数,可以提高制动系统的响应速度和稳定性。
例如,采用主动制动力分配(ABD)和防抱死制动系统(ABS)等技术,可以减少制动延迟和减速不稳定现象,提高车辆制动性能和安全性。
电动汽车制动器的设计与优化方法探究

电动汽车制动器的设计与优化方法探究电动汽车作为新型的环保交通工具,越来越受到人们的关注和青睐。
制动器作为汽车中的重要安全系统之一,对电动汽车的制动性能和行车安全至关重要。
因此,电动汽车制动器的设计与优化方法成为了研究的热点之一。
本文将探究电动汽车制动器的设计与优化方法,以提高电动汽车的刹车性能和行车安全。
首先,我们需要了解电动汽车制动器的基本原理和分类。
电动汽车制动器主要通过将动能转化为热能来实现制动效果。
常见的电动汽车制动器分类包括机械制动器、电子制动器和液压制动器。
机械制动器包括盘式刹车器和鼓式刹车器,通过刹车盘或刹车鼓上的摩擦力实现制动。
电子制动器主要依靠电子控制单元控制电机反向工作,实现制动效果。
液压制动器利用液压力将制动力传递给制动器,实现制动效果。
然后,我们需要关注电动汽车制动器的设计要素和优化方法。
制动器的设计要素包括制动系统的结构、材料的选择和制动力的分配等。
优化制动器的方法包括改进刹车盘或刹车鼓的散热性能、优化制动液的性能、提高电子控制单元的精确度等。
此外,还可以通过减轻制动器的负荷、提高电机反向工作的效率等方法来优化制动器。
制动器的设计与优化方法还可以从以下几个方面展开研究:1. 制动系统的结构设计:包括刹车盘或刹车鼓的材料选择、形状设计以及刹车片的布置等。
合理的结构设计可以提高制动器的散热性能,减少制动时的能量损耗。
2. 制动力的分配:电动汽车通常采用四轮独立驱动,因此制动器需要实现前后轮的制动力分配。
合理的制动力分配可以保证车辆在制动时的稳定性和平衡性。
3. 制动液的性能优化:制动液在制动过程中需要承受高温和高压的条件,因此液体的性能至关重要。
优化制动液的性能可以提高制动的效果,并延长制动器的使用寿命。
4. 电子控制单元的精确度优化:电子制动器依赖于电子控制单元对电机进行精确的控制。
提高电子控制单元的精确度可以提高制动的响应速度和稳定性。
5. 制动器负载的减轻:减轻制动器负载可以减少制动器的磨损和能耗,延长其使用寿命。
机械结构的动态特性响应与优化

机械结构的动态特性响应与优化一、引言机械结构是现代工程领域中不可或缺的重要组成部分,其动态特性响应和优化是设计和制造过程中必须考虑的关键因素。
本文旨在探讨机械结构的动态特性响应和优化方法,为相关研究和工程实践提供参考。
二、机械结构的动态特性响应机械结构的动态特性是指在外部力作用下,结构产生的振动响应。
了解和预测结构的动态特性是设计优化和工程应用的基础。
在机械系统中,动态特性主要包括固有频率、模态形态和振型等。
1. 固有频率固有频率是机械结构在自由振动状态下的特征频率,它决定了结构的振动频率范围。
通过测量和分析结构的固有频率,可以了解结构的刚度和振动特性。
固有频率可以通过有限元分析等方法进行计算和优化,以满足设计要求。
2. 模态形态模态形态是机械结构在固有频率下的振动模式。
每个固有频率对应一个唯一的模态形态,它描述了结构各个部分的振动特性和振动形式。
通过分析模态形态,可以了解结构的固有振动特性和可能存在的问题。
3. 振型振型是机械结构在给定激励力下的振动形态。
通过对结构振动的测量和分析,可以得到结构在不同激励力下的振动响应曲线。
振型可以用于判断结构的耦合特性和共振问题,并为结构的优化提供参考。
三、机械结构的动态特性优化机械结构的动态特性优化旨在减小结构的振动响应和提高结构的动态性能。
在实际工程中,动态特性优化通常包括材料选择、结构设计和控制方法等方面。
1. 材料选择材料的选择对机械结构的动态特性有着重要影响。
合适的材料可以提高结构的刚度和耐久性,从而减小结构的振动响应。
同时,材料的密度和弹性模量等特性也会影响结构的固有频率。
因此,在设计过程中,需要选择合适的材料来满足结构的动态要求。
2. 结构设计结构设计是机械结构动态特性优化的核心环节。
在结构设计中,需要考虑结构的刚度、减震、降噪和模态等特性。
通过合理设计结构的形状、尺寸和连接方式等参数,可以减小结构的共振现象和振动响应。
同时,还可以采用缓冲、隔振和减振等措施来优化结构的动态性能。
制动系统的性能优化研究
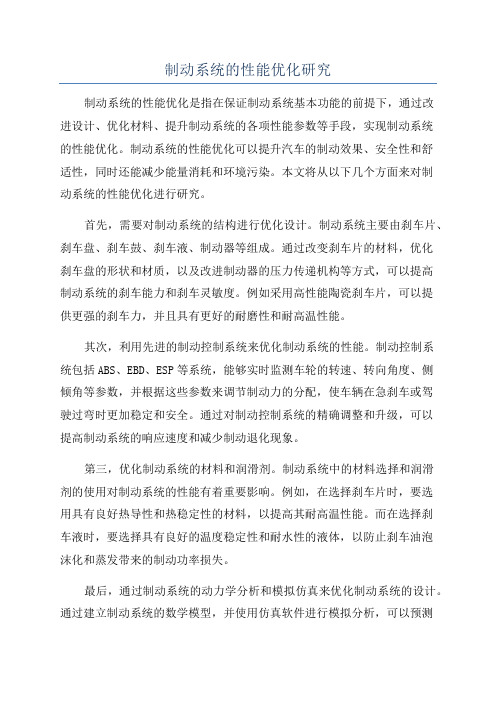
制动系统的性能优化研究制动系统的性能优化是指在保证制动系统基本功能的前提下,通过改进设计、优化材料、提升制动系统的各项性能参数等手段,实现制动系统的性能优化。
制动系统的性能优化可以提升汽车的制动效果、安全性和舒适性,同时还能减少能量消耗和环境污染。
本文将从以下几个方面来对制动系统的性能优化进行研究。
首先,需要对制动系统的结构进行优化设计。
制动系统主要由刹车片、刹车盘、刹车鼓、刹车液、制动器等组成。
通过改变刹车片的材料,优化刹车盘的形状和材质,以及改进制动器的压力传递机构等方式,可以提高制动系统的刹车能力和刹车灵敏度。
例如采用高性能陶瓷刹车片,可以提供更强的刹车力,并且具有更好的耐磨性和耐高温性能。
其次,利用先进的制动控制系统来优化制动系统的性能。
制动控制系统包括ABS、EBD、ESP等系统,能够实时监测车轮的转速、转向角度、侧倾角等参数,并根据这些参数来调节制动力的分配,使车辆在急刹车或驾驶过弯时更加稳定和安全。
通过对制动控制系统的精确调整和升级,可以提高制动系统的响应速度和减少制动退化现象。
第三,优化制动系统的材料和润滑剂。
制动系统中的材料选择和润滑剂的使用对制动系统的性能有着重要影响。
例如,在选择刹车片时,要选用具有良好热导性和热稳定性的材料,以提高其耐高温性能。
而在选择刹车液时,要选择具有良好的温度稳定性和耐水性的液体,以防止刹车油泡沫化和蒸发带来的制动功率损失。
最后,通过制动系统的动力学分析和模拟仿真来优化制动系统的设计。
通过建立制动系统的数学模型,并使用仿真软件进行模拟分析,可以预测制动系统的性能指标,如制动力、刹车距离和刹车温升等,从而指导制动系统的优化设计。
例如,通过优化刹车盘和刹车片的材料和形状,可以减少刹车片与刹车盘之间的热量传递,降低刹车温升,提高制动系统的制动效率和使用寿命。
综上所述,制动系统的性能优化是一个复杂而综合的工程问题。
它需要涉及到制动系统的结构设计、控制系统的优化、材料与润滑剂的选择以及动力学分析等多个方面。
论从车辆动态特性角度优化制动系统设计
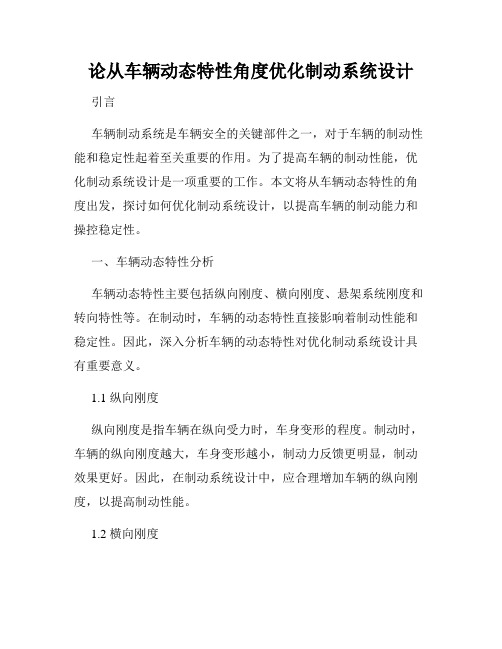
论从车辆动态特性角度优化制动系统设计引言车辆制动系统是车辆安全的关键部件之一,对于车辆的制动性能和稳定性起着至关重要的作用。
为了提高车辆的制动性能,优化制动系统设计是一项重要的工作。
本文将从车辆动态特性的角度出发,探讨如何优化制动系统设计,以提高车辆的制动能力和操控稳定性。
一、车辆动态特性分析车辆动态特性主要包括纵向刚度、横向刚度、悬架系统刚度和转向特性等。
在制动时,车辆的动态特性直接影响着制动性能和稳定性。
因此,深入分析车辆的动态特性对优化制动系统设计具有重要意义。
1.1 纵向刚度纵向刚度是指车辆在纵向受力时,车身变形的程度。
制动时,车辆的纵向刚度越大,车身变形越小,制动力反馈更明显,制动效果更好。
因此,在制动系统设计中,应合理增加车辆的纵向刚度,以提高制动性能。
1.2 横向刚度横向刚度是指车辆在横向受力时,车身侧倾的程度。
制动时,车辆的横向刚度越大,侧倾越小,侧向稳定性越高。
为了提高制动过程中的操控稳定性,应适当增加车辆的横向刚度。
1.3 悬架系统刚度悬架系统刚度对车辆的制动性能和稳定性有着重要影响。
在制动时,悬架系统刚度越大,车轮的垂直位移越小,制动效果越好。
因此,在制动系统设计中,应注意优化悬架系统刚度,以提高制动性能和稳定性。
1.4 转向特性转向特性是指车辆在制动时的转向响应性能。
良好的转向特性可以提高车辆的操控性,减少制动时的不稳定因素。
因此,在制动系统设计中,应考虑车辆的转向特性,并通过合理设计制动系统,提高转向的响应速度和精确度。
二、制动系统设计优化方案2.1 制动力分配制动力分配是指将制动力合理地分配给各个车轮,以实现最佳的制动效果。
根据车辆的动态特性和操控需求,可以采取前轮制动优先、后轮制动优先或前后轮同时制动的分配方式。
根据车辆的重心位置、所载荷物的位置以及制动时的车辆姿态等因素,确定最佳的制动力分配策略,以提高车辆的制动能力和操控稳定性。
2.2 制动系统的可调性为了适应不同驾驶条件下的制动需求,制动系统应具备一定的可调性。
面向制动尖叫抑制的制动盘稳健性设计

面向制动尖叫抑制的制动盘稳健性设计张立军;庞明;唐传骏;孟德健;余卓平【摘要】在建立盘式制动器复模态有限元模型并通过台架试验验证模型正确性的基础上,提出了一种以加权尖叫倾向性作为稳健性设计指标的方法,以摩擦系数的波动为干扰因素,采用田口方法进行了制动盘弹性模量、帽部高度、帽部直径和通风散热筋数量的尖叫稳健性设计.分析表明,制动盘的弹性模量对制动尖叫稳健性的影响最大且采用所建立的方法能够获得可有效控制试验制动尖叫的稳健的制动盘设计参数组合.【期刊名称】《汽车工程学报》【年(卷),期】2015(005)002【总页数】7页(P101-107)【关键词】制动尖叫;制动盘;田口方法;稳健性设计【作者】张立军;庞明;唐传骏;孟德健;余卓平【作者单位】同济大学新能源汽车工程中心,上海201804;同济大学汽车学院,上海201804;同济大学新能源汽车工程中心,上海201804;同济大学汽车学院,上海201804;同济大学新能源汽车工程中心,上海201804;同济大学汽车学院,上海201804;同济大学新能源汽车工程中心,上海201804;同济大学汽车学院,上海201804;同济大学新能源汽车工程中心,上海201804;同济大学汽车学院,上海201804【正文语种】中文【中图分类】U463.51+制动尖叫又称制动啸叫,是指汽车在制动过程中由于制动器工作时的振动而产生的频率在1~16 kHz的高频噪声,具有频率高、强度大的特点,如何减弱或消除汽车制动时的制动尖叫现象是汽车制动器行业的重要技术难题[1-2]。
因此,寻求切实有效的制动尖叫控制措施一直倍受关注。
前期研究表明,制动器材料、结构、运行工况和环境条件等是制动尖叫的关键因素[3]。
由于生产制造过程、运行条件和人类认知能力等的影响,这些因素都具有离散性、随机性和时变性的特点。
从系统稳健性角度出发,必须降低制动尖叫对各种因素的敏感性[4]。
因此,通过稳健性设计方法,合理进行参数设计,提高制动器尖叫的稳健性,成为重要的研究方向。
结构改进降低制动噪声:数值和试验的性能鉴定(二)

结构改进降低制动噪声:数值和试验的性能鉴定(二) Francesco Massi;Laurent Baillet;Antonio Culla【摘要】噪声是摩擦力引起振动造成音响的一个实例,最近十年多来已经开展了许多研究,这些研究确定集中于简单的制动系统和鉴别‘锁止’的不稳定是造成制动噪声的原因.本文介绍了过去研究的简短文献目录和最近的研究成果.由于锁止对系统动力学的敏感性,制动器设计不能避免模态上的耦合,高的模态不透明度和不确定性与自然频率有关.本文推荐了一种为避免振动滋生的改进方法,它是用集成结构修正转子.【期刊名称】《传动技术》【年(卷),期】2012(026)004【总页数】7页(P42-48)【关键词】制动器噪声;接触;不稳定性;锁止;结构改进;数值;实验【作者】Francesco Massi;Laurent Baillet;Antonio Culla【作者单位】【正文语种】中文【中图分类】U463.5另一方面,质量分离噪声继续变化(6.5秒后对10 g质量测量示于图7),并且噪声再开始在其初始的振幅和频率。
5.3 盘速度的影响质量值增加的影响涉及频率范围增大,用盘模块在相同周期结果锁止时间缩短。
另一方面,在锁止时(用集总块改进)对增加振动减少时间,增加盘的转动速度,即减小频率波动周期(Td/2m)。
图8(a)示在噪声阶段当盘附加5g质量时摩擦衬板的速度,盘速度由6r/m(盘速度A)增加到12 r/m(盘速度B)而最后到50r/m(盘速度C)。
图示由速度A到速度B时,锁止/脱开周期降低;此外,注意到噪声振动振幅降低。
当盘在高速转动时,发出的噪声几乎消失,并且摩擦衬板得到速度较低(图8(a),21s <t<27s)。
当质量脱开时(图8箭头所指),噪声振动回到初始振幅和频率。
图8(b)示用附加质量7.5g的相同的试验,显然特征相同,但对于盘的速度值为c的噪声完全消失(图8(b),13s<t<20s)。
基于ABAQUS的盘式制动尖叫分析

基于ABAQUS的盘式制动尖叫分析韦健;孙跃东;王书文;周萍【摘要】盘式制动啸叫问题依然是车辆领域的一大难题.针对盘式制动尖叫发生的普遍性,简化盘式制动器的模型,基于ABAQUS进行复特征值分析计算,预测出盘式制动器的尖叫频率,并通过结构参数的方法分别分析了制动转速、制动压力、摩擦系数、以及制动盘刚度对制动尖叫的影响.再通过结构优化,通过仿真对比验证这种方法的可行性.最后,通过制动台架试验,得到实验中的啸叫频率,从而验证仿真的可行性.本研究的工作有助于理解和揭示汽车盘式制动器制动尖叫的产生机理.【期刊名称】《机械设计与制造》【年(卷),期】2016(000)006【总页数】4页(P151-154)【关键词】ABAQUS;盘式制动器;制动尖叫;复特征值分析【作者】韦健;孙跃东;王书文;周萍【作者单位】上海理工大学机械工程学院,上海200093;上海理工大学机械工程学院,上海200093;上海理工大学机械工程学院,上海200093;上海理工大学机械工程学院,上海200093【正文语种】中文【中图分类】TH16;U467.5+23复特征值的实部表明系统的不稳定程度,也被认为和啸叫的产生的有关。
这是复特征值分析的原理[1]。
最早将复特征值分析应用到有限元方法中的是Liles。
Liles从分析中发现,更薄的摩擦片、阻尼的引入、较软的制动盘和刚度更大的背板能抑制啸叫;相反,高摩擦系数、高磨损率的摩擦材料有助于啸叫的产生[2]。
国内这方面起步比较晚,管迪华,张立军等做了很多相关的研究[3-9]。
很多实验和案例表明基于ABAQUS建立在复特征值分析基础上的频域分析方法是解决产品问题非常行之有效的方法。
复特征值问题是用子空间投影法求解的。
因此,须首先进行本征频率分析,以得到投影子空间。
复模态问题可以描述如式(1):弹性结构使刚度矩阵[K]可以包含预应力和载荷刚度效应。
特征值和特征向量都可以是复数。
这时的系统是因为丢失阻尼矩阵[C]和刚度矩阵[K]的不对称因素而被对称化了。
- 1、下载文档前请自行甄别文档内容的完整性,平台不提供额外的编辑、内容补充、找答案等附加服务。
- 2、"仅部分预览"的文档,不可在线预览部分如存在完整性等问题,可反馈申请退款(可完整预览的文档不适用该条件!)。
- 3、如文档侵犯您的权益,请联系客服反馈,我们会尽快为您处理(人工客服工作时间:9:00-18:30)。
( 7)
[ M] ){ xi
k} /
(
i-
k)
xi F F/ F = xi/ x i F xi
( 2)
对于设计变量一般还要根据实际情况确定其变化范 围作为等式或不等式约束条件。 2 3 优化方法的选择 上述子结构的动态特性设计问题转化为在一定 的约束条件下, 给定设计变量空间范围内, 对目标函 数寻优的问题。此类目标函数涉及计算子结构的动 态特征 , 是复杂的非二次函数。对于此类带约束的 非线性规划问题, 可以采用惩罚函数法。其基本原 理是将约束优化问题中的等式约束和不等式约束经 过加权转化后, 和原目标函数结合成新的目标函数 即惩罚函数。通过求解一系列惩罚函数的无约束极 小值问题 , 可得到原目标函数的最优解。 在将约束问题转化为无约束问题后 , 即可求解 无约束非线性极小化问题。由于目标函数为高度非 线性函数, 采用计算效率和稳定性比较高的变尺度 BFGS 法。变尺度 BFGS 法是 一种拟牛顿法, 其设 计向量 x 的迭代过程如下 [ 5] : x 式中
叙词 : 制动器尖叫, 结构修改, 优化
Reduction of Brake Squeal U sing Substructure Dynamic Characteristics Optimization
Su Xindong & Guan Dihua
T si nghua U niv ersit y, St ate K ey L aborat ory of A ut omobi le S af ety and Energy, Beiji ng 100084
支架子结构的振型幅值优化
目标函数对设计变量灵敏度 ( F F F , , ) / mm - 1 t w h 迭代搜索方向(- H kgk ) ( 0 0280, 1 0000, 0 1138) ( - 0 1161, - 1 0000, - 0 0217)
( - 0 1240, - 0 2140, 0 1277 ( 0 0936, 0 6307, 0 0618)
k k+ 1
k i [ M ] - 0 5{ } T { }i k = i i xj 这种方法只有在已知系统完备模态集情况下才可得 到精确解 , 在一般有模态截断而仅知系统的有限个 低阶模态情况下, 用此法仅可以得到近似结果。 将特征向量导数表示为 n { }i x j = k = 1 ck { } k + { S r }
( 4)
( 5)
2 4 度
灵敏度分析的方法 在变尺度 BFGS 法中要计算惩罚函数 P 的梯 P( x , r ) = F( x ) + p(x, r ) ( 6) 上式第二项为惩罚函数障碍项的梯度, 可由约
k k
束函数的解析表达式求得。关键在于第一项中计算 子结构目标函数关于设计参数的灵敏度, 需要计算
T T H ky kST k - Sky kH k ] / S ky k
统一个振动周期内摩擦副各对应节点对系统产生的 能量馈入 , 发现馈入能量可以表征制动器的尖叫倾 向。对影响制动尖叫的各部件子结构动态特性进行 的分析表明, 制动振动噪声发生时的能量馈入主要 是通过内外制动块的刚体振动引起的, 而直接影响 制动块振动的关键子结构 是制动钳支架。分析表 明 , 支承内外制动块的制动钳支架关键节点的第 11 阶模态振型幅值是对系统振动产生不稳定的主要因 素 , 且其中的内制动块的振动对系统能量的馈入起 决定作用。为此, 针对支架子结构的关键节点模态 振型幅值进行了改进设计的分析优化。该支架子结 构是较复杂的三维结构 , 在原支架结构的有限元模 型中引入了设计参数, 其参数化模型如图 1。要求 通过优化设计减小关键节点处第 11 阶振型幅值。
表3
节点号 优化前节点振型值 优化后节点振型值
优化前后节点振型值
节点 1317 0 8914 1 9470 节点 1469 - 1 0190 - 0 5080 节点 1477 - 1 5132 - 0 00076
节点 1309 - 0 4911 0 1110
4
子结构修改结果验证
按文献[ 2] 的建模计算方法, 将结构设计参数变 化前后的制动器支架与制动器内外制动块、 制动盘、 制动钳进行各子结构的模态分析 , 然后用模态综合 技术对各个子结构进行模态综合。 图 2 为支架修改前耦合系统的复特征根分布 , 其虚部( 横坐标 ) 表示频率 , 实部( 纵坐标 ) 表示阻尼。 其不稳定模态( 特征根实部大于零 ) 要多于实际尖叫 频率数 , 这可能出于以下几方面的原因。系统模态 综合中摩擦界面上的摩擦系数简化为一个常量 ; 综 合系统中未计入任何形式的阻尼 , 而阻尼的存在有 利于系统的稳定 ; 制动尖叫为非线性的自激振动系 统, 建模中将其线性化了 ; 模态综合中各子结构的模 态的上截断频率约为 10~ 15kHz, 耦合系统中高阶
2003 年 ( 第 25 卷 ) 第 2 期
汽 车 工 程 Automotive Engineer ing
2003 ( Vol. 25) No. 2
2003039
利用子结构动态特性优化设计抑制制动器尖叫
宿新东 管迪华
100084) ( 清华大学 , 汽车安全与节能国家重点试验室 , 北京
[ 摘要 ]
N
( 8)
式中 { S r } =
k= n+ 1
ck { } k , n 为低阶保留模态阶数。
模态叠加法求特征向量导数的关键是如何计入高阶 截断模态的影响 { S r } 。 文献 [ 7 ] 利用其所定义的静 态模态提出了 { S r } 的计算方法。当每次迭代只计 算较少几个特征导数时 , 可采用 Nelson 法[ 8] 。另外 还可用有限差分法计算目标函数的导数。 F ( x k) / x j ( F ( x k+ x j )- F ( x k ) ) / x j ( 9)
i
子结构特征灵 敏度。对于式 ( 1) 表示的系统 , 文献 [ 6] 给出了质量矩阵和刚度矩阵为对称时的特征导 数表达式, 其中特征向量 ( 振型) 的导数可用系统所 有特征向量的线性组合来表达, 即 n { }i = a ik { } k xj k= 1 式中 { }T k( a ik = [K] xj
[ Abstract]
Aiming at t he t arget of substructure modificat ion for reducing brake squeal, t he modif icat ion
met hod in opt imal design is invest ig at ed On the basis of model simulation for brake squeal and det ermination of dynamic charact erist ic modif icat ion of key subst ruct ure, t he design paramet ers are incorporat ed into the substruc t ure FE model, and opt im ization is adopted to modify substructure dynamic charact eristics according t o the speci f ied objective f unction T he verif icat ion by model simulat ion shows t hat there is no unst able mode at t he frequen cy band, during w hich brake squeal has occurred, for t he brake syst em w it h modified subst ruct ure Keywords: Brake squeal, Structural modification, Optimization 尖叫的影响。
2003 年 ( 第 25 卷 ) 第 2 期
汽
车
工
程
169
表1
设计变量 下限值 上限值 横梁高度 h / mm 13 5 17
变量上下限
横梁宽度 w / mm 4 0 9 0 两侧支撑板 厚度 t / mm 10 5 15 0
果表明收敛性较好。 表 2 为优化迭代过程中设计变量、 目标函数、 目 标函数对设计变量的灵敏度值和迭代搜索方向, 其
[ 3]
2
子结构动态特性优化设计方法
2 1 目标函数 设一个 N 自由度子结构系统, 其振动特征方程 为 K = M ( 1)
பைடு நூலகம்
原稿收到日期为 2002 年 8 月 19 日 , 修改稿收到日期为 2002 年 9 月 23 日。
168
汽
车
工
程
2003 年 ( 第 25 卷 ) 第 2 期
式中 K 、 M 为系统的刚度阵、 质量阵, 是子结构物理 参数设计向量 x 的函数, 、 分别为系统振型矩阵 和特征对角阵。目标函数可取为要改变的动态特性 参数与目标值差的平方和或绝对值之和。 2 2 设计变量的选取 如果设计参数较多, 可取对目标函数敏感的参 数来作为设计变量。为了度量目标函数对各设计参 数的敏感度, 可以采用目标函数 F 对各设计变量 x i 的相时灵敏度公式 ( F / x i ) = lim x 0
针对制动器噪声分析研究所提出的对子结构修改以抑制噪声发生的 目标 , 探 讨了优化 设计的修改 方
法。在对有制 动尖叫倾向的制动器进行建模分析并确定其关键子结构动态特性修 改方向的基 础上 , 在部件子结 构 中引 入设计参数 , 用最优化的方法按照设定的目标 函数对 结构动 态特性 进行修 改。最后通 过模型 验证 , 表明部 件 子结构动态特性修改后制动器系统在原来尖叫频率的不稳定模态不再出现。