制动器时间优化设计报告
汽车制动总结报告范文(3篇)

第1篇一、引言汽车制动系统是汽车安全行驶的重要组成部分,其性能直接影响着行车安全。
为了提高汽车制动系统的性能,我国汽车制动行业不断进行技术创新和优化。
本文通过对汽车制动系统的实验分析,总结其性能特点,为汽车制动系统的研发和应用提供参考。
二、实验目的1. 分析汽车制动系统的性能特点;2. 评估汽车制动系统的可靠性;3. 为汽车制动系统的改进提供依据。
三、实验方法1. 实验对象:选取某品牌汽车,车型为XX型;2. 实验设备:汽车制动性能测试台、制动踏板力传感器、速度传感器、制动距离传感器等;3. 实验内容:汽车制动性能试验,包括制动距离、制动减速度、制动协调时间等指标;4. 数据处理:采用统计学方法对实验数据进行处理和分析。
四、实验结果与分析1. 制动距离实验结果显示,该车型在高速行驶时,制动距离为100m,满足国家标准。
但在中低速行驶时,制动距离略大于标准值。
这可能是由于中低速行驶时,驾驶员对制动踏板的控制不够精准,导致制动距离增加。
2. 制动减速度实验结果显示,该车型在高速行驶时,制动减速度为10m/s²,满足国家标准。
在中低速行驶时,制动减速度为8m/s²,略低于标准值。
这可能是由于制动系统在低速行驶时,制动力分配不均,导致制动减速度下降。
3. 制动协调时间实验结果显示,该车型在高速行驶时,制动协调时间为0.8s,满足国家标准。
在中低速行驶时,制动协调时间为1.2s,略高于标准值。
这可能是由于制动系统在低速行驶时,制动力响应速度较慢,导致制动协调时间增加。
4. 制动系统可靠性通过对实验数据的分析,该车型在高速行驶时,制动系统可靠性较高,但在中低速行驶时,制动系统可靠性有所下降。
这可能是由于制动系统在低速行驶时,制动力分配不均,导致制动效果不稳定。
五、结论与建议1. 结论通过对汽车制动系统的实验分析,得出以下结论:(1)该车型在高速行驶时,制动性能较好,满足国家标准;(2)在中低速行驶时,制动性能略低于标准值,需要进一步优化;(3)制动系统在低速行驶时,可靠性有所下降,需要提高制动力分配均匀性。
汽车制动系统的性能分析和优化设计

汽车制动系统的性能分析和优化设计摘要:随着我国轿车工业的不断发展,有关部门对轿车的安全性越来越关注,轿车的安全性也越来越重要。
而在汽车行驶过程中,刹车系统起着非常关键的作用,刹车系统既能确保汽车行驶的平稳性,又能有效地提高汽车的使用寿命,提高汽车的安全性。
汽车刹车系统作为一种重要的交通工具,其作用在于对车速进行有效的控制,以保证车辆在行驶时的平稳性。
本文通过对汽车制动器性能的分析,提出了改善汽车制动器性能的几点建议。
关键词:汽车制动系统;电子制动;气动制动1 引言汽车制动系统的主要功能是保证刹车时的安全,并保证刹车时不会受到路面坡度的影响,从而保证车辆的平稳运行。
在汽车制动系统中,最常用的制动方式有电子制动和气动动力制动。
本论文以某型轿车为研究对象,对其制动系统进行了理论分析,对其主要性能进行了分析,并对其进行了优化设计。
2汽车制动影响因素2.1汽车轮胎气压轮胎压力对汽车制动性能的影响很大。
当轮胎气压较低时,刹车平台接触面积较大,在打滑过程中会出现迟滞损耗,进而增加打滑摩擦,使得轮胎摩擦系数增加。
在轮胎压力较大的情况下,由于轮胎与刹车台接触面积较小,使得滑移摩擦系数降低,使得轮胎摩擦系数降低。
相反,如果胎压不足,则会使胎面凹陷,使胎面半径改变,起到刹车作用。
由于轮胎压力的改变,使得轮胎与鼓轮之间的最大粘着系数也随之改变,使得轮胎与鼓轮之间的接触状态改变,使得轮胎与鼓轮之间的摩擦状态改变,使得轮胎的制动性能降低。
尤其是在轮胎压力过高的情况下,车轮动半径会显著增加,从而使制动功率的测量值进一步下降。
车辆在刹车过程中,往往会出现轮胎一侧被锁死的情况,这种情况不仅会对制动力平衡造成很大的影响,而且还会造成很大的后果。
2.2 轮胎与地面摩擦系数轮胎与路面的摩擦力是影响车辆刹车性能的主要因素之一。
增加轮胎与地面的接触面,在增加抓地力的同时,也增加了对制动力的需求。
当摩擦力较大时,刹车噪音较大,摩擦力较大,噪音较大,油耗较高。
关于汽车制动系统性能分析及优化设计探讨

关于汽车制动系统性能分析及优化设计探讨汽车制动系统是汽车安全行驶的关键部件之一,其性能的优劣直接影响车辆的制动距离和安全性。
本文将探讨汽车制动系统性能分析及优化设计的相关内容。
首先,我们来分析汽车制动系统的一般性能指标。
汽车制动系统的主要性能指标包括制动力、制动距离、制动响应时间和制动稳定性。
制动力是制动系统提供的制动能力,其大小取决于制动器的设计和材料选择。
制动距离是汽车从行驶状态到停止所需要的距离,该指标受到汽车质量、车速和路面摩擦系数的影响。
制动响应时间是指从驾驶员踩下制动踏板到制动器开始工作所需的时间。
制动稳定性是指制动系统在不同工况下的稳定性能,包括制动力分配的均衡性和制动器的温升控制等。
在优化设计方面,可以从以下几个方面进行改进。
首先是制动器的设计与优化。
制动器是传递制动力的关键部件,其设计包括制动盘、制动鼓、制动片和制动液等。
制动盘和制动鼓的材料和结构设计可以通过优化来提高制动器的散热性能和刹车效果。
制动片的材料选择和摩擦系数的调整也是提高制动力和稳定性的重要方面。
此外,制动液的选用和性能也会直接影响制动系统的响应速度和稳定性。
另一个重要的方面是制动力分配的均衡性。
在不同路面和工况下,前后轮的制动力分配应该能够实现均衡,避免制动不足或制动过度。
通过改进制动力分配的控制系统,可以实现制动力分配的实时调整,提高制动系统的稳定性和安全性。
此外,制动系统的热管理也是需要考虑的因素。
长时间制动会产生大量热量,如果不能及时散热,制动器的温度会升高,影响制动力和稳定性。
因此,可以通过使用散热片、风冷系统和制动风扇等热管理措施来提高制动系统的散热性能,保持制动器的稳定温度。
最后,还可以考虑将新的技术和材料应用于汽车制动系统的设计与制造中。
例如,利用电动化技术,可以实现电动制动系统,提高制动力和响应速度。
采用轻量化材料,如高强度钢、铝合金和复合材料,可以减轻车身质量,提高制动性能。
综上所述,对汽车制动系统的性能进行分析,并进行优化设计,可以提高制动力、减小制动距离、缩短制动响应时间和提高制动稳定性。
现代汽车盘式制动器的优化设计分析

现代汽车盘式制动器的优化设计分析摘要盘式制动器具有热稳定性好、浸水性能减小少等多方面的优点,且其应用广,所以在汽车中得到推广。
文章对盘式制动器的效能进行了分析,并有针对性地对其进行了优化设计,以期能够促进盘式制动器的更优发展。
关键词汽车;盘式制动器;设计;优化1 盘式制动器基本特性分析1.1 盘式制动器制动力矩的分析与计算盘式制动器制动力矩对于整个制动器的稳定性能具有重要作用,所以在制动器的性能优化过程中,常常优先对其制动力矩进行分析。
根据现有公式:首先,制动器在制动过程中产生的制动力矩为:Mρ=2ρPR,其中ρ表示盘式制动器的摩擦系数,一般ρ=0.35,在理想条件下ρ可取0.3,使计算结果符合实际情况。
P表示单项制动片对制动盘的压紧力:P=1/4πd2p。
R表示受力半径,对于一些常见的摩擦片的表面,根据实际情况的反复检验,证明如果其具有相对较小的径向宽度,那么取R等于有效半径Re[1]。
平均半径:Rm=R1+R2/2。
其中R1和R2分别为摩擦衬片的内半径和外半径。
有效半径:Re=Mρ/2ρP。
T=2ρpπd2(R23-R13)/6(R22-R12)。
1.2 制动器摩擦片所受的压力制动器摩擦片所受的压力,是研究盘式制动器性能的重要参数。
计算其所受的压力,我们首先要知道摩擦片上的点与制动盘轴线的距离,假设这一段的距离为r,那么在这段距离范围内,摩擦片上的任意一点所受的压力我们都可以通过公式进行计算。
压力用P表示,那么:P=βR/r·πd2p/4A。
这个公式中,A代表摩擦片的摩擦面积,其单位一般选定mm2,β的值通过公式计算:β=4R1R2/(R1+R2)R+2R1R2,β一般表示比例函数。
其中在R1和R2处,P分别达到最大值和最小值。
摩擦片的最大的单位压力为:Pmax=βR/R1·πd2p/4A。
2 盘式制动器优化设计模型建立首先,对于盘式制动器的优化,是为了防止制动器的设计不合理、摩擦材料老化等原因引起的制动器的热能损耗,或者引起制动时的强烈震动等。
基于灵敏度分析的鼓式制动器时变可靠性优化设计
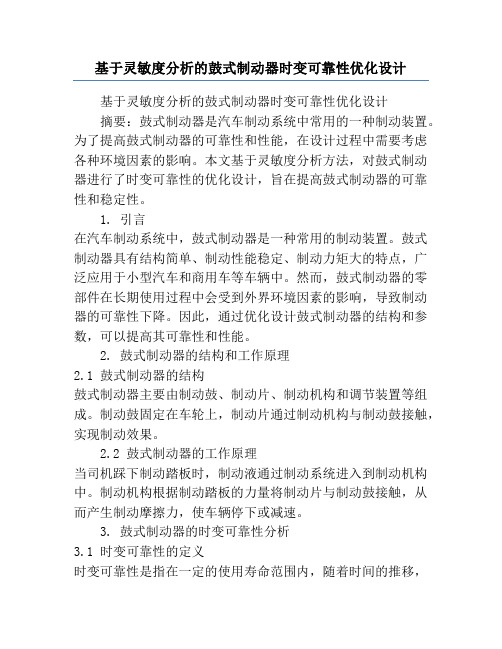
基于灵敏度分析的鼓式制动器时变可靠性优化设计基于灵敏度分析的鼓式制动器时变可靠性优化设计摘要:鼓式制动器是汽车制动系统中常用的一种制动装置。
为了提高鼓式制动器的可靠性和性能,在设计过程中需要考虑各种环境因素的影响。
本文基于灵敏度分析方法,对鼓式制动器进行了时变可靠性的优化设计,旨在提高鼓式制动器的可靠性和稳定性。
1. 引言在汽车制动系统中,鼓式制动器是一种常用的制动装置。
鼓式制动器具有结构简单、制动性能稳定、制动力矩大的特点,广泛应用于小型汽车和商用车等车辆中。
然而,鼓式制动器的零部件在长期使用过程中会受到外界环境因素的影响,导致制动器的可靠性下降。
因此,通过优化设计鼓式制动器的结构和参数,可以提高其可靠性和性能。
2. 鼓式制动器的结构和工作原理2.1 鼓式制动器的结构鼓式制动器主要由制动鼓、制动片、制动机构和调节装置等组成。
制动鼓固定在车轮上,制动片通过制动机构与制动鼓接触,实现制动效果。
2.2 鼓式制动器的工作原理当司机踩下制动踏板时,制动液通过制动系统进入到制动机构中。
制动机构根据制动踏板的力量将制动片与制动鼓接触,从而产生制动摩擦力,使车辆停下或减速。
3. 鼓式制动器的时变可靠性分析3.1 时变可靠性的定义时变可靠性是指在一定的使用寿命范围内,随着时间的推移,系统或设备的可靠性性能如何变化的问题。
鼓式制动器在长期使用过程中,由于外界环境因素的影响,其可靠性会发生变化。
3.2 时变可靠性的分析方法灵敏度分析是一种常用的时变可靠性分析方法,可以用于评价制动系统的鲁棒性和敏感度。
通过对制动系统关键参数的灵敏度分析,可以评估参数变化对制动性能和可靠性的影响程度,进而优化设计。
4. 鼓式制动器的时变可靠性优化设计4.1 系统参数的选择与确定鼓式制动器中各个零部件的参数选择和确定对时变可靠性具有重要影响。
需要考虑各个零部件的材料强度、摩擦系数和磨损寿命等因素,以及制动鼓和制动片的磨损、变形和热胀冷缩等因素。
毕业设计论文轿车盘式制动器设计及优化

行车制动装置和驻车制动装置,都由制动器和制动驱动机构两部分组成。
任何制动系都是由以下4个部分组成:
(1)供能装置。包括供给、调节制动所需能量以及改善传能介质的各个部件。
(3)制动稳定性好。由于盘式制动器的制动力矩与其制动油缸的活塞推力及摩擦系数成线性关系,还由于无自行增势作用,因此在制动过程中制动力矩增长较缓和,与鼓式制动器相比,能保证高的制动稳定性。
(4)制动力矩与汽车前进和后退的行驶状态无关。
(5)在输出同样大小的制动力矩条件下,盘式制动器的结构尺寸和质量比鼓式的要小。
摩擦式制动器按其旋转元件的形状又可分为鼓式和盘式两大类。
鼓式制动器又分为内张型鼓式制动器和外束型鼓式制动器。由于外束型鼓式制动器通常简称为带式制动器,而且在汽车上已很少采用,所以内张型鼓式制动器通常简称为鼓式制动器,而通常所说的鼓式制动器即是内张型鼓式结构。
盘式制动器的旋转元件是一个垂向安放且以两侧面为工作面的制动盘,其固定摩擦元件一般是位于制动盘两侧并带有摩擦片的制动块。当制动盘被两侧的制动块夹紧时,摩擦表面便产生作用于制动盘上的摩擦力矩。盘式制动器常用作轿车的车轮制动器,也可用作各种汽车的中央制动器。
(2)控制装置。包括产生制动作用和控制制动效能的各个部件。
(3)传动装置。包括将制动能量传到制动器的各个部件及管路,如制动主缸、轮缸及连接管路。
(4)制动器。产生阻碍车辆运动或运动趋势的力的部件。一般通过固定元件与旋转元件工作表面之间的摩擦作用来实现。
较完善的制动系还应具有制动力调节装置、报警装置、压力保护装置等附加装置。
基于动态刹车需求的紧凑型轿车盘式制动器设计优化方案

基于动态刹车需求的紧凑型轿车盘式制动器设计优化方案根据动态刹车需求的紧凑型轿车盘式制动器设计优化方案紧凑型轿车是现代交通中常见的汽车类型之一,其刹车系统的设计和性能对驾驶安全至关重要。
动态刹车需求是指在汽车行驶过程中的实际刹车需求,包括刹车力、刹车距离、刹车响应时间等方面的要求。
盘式制动器作为轿车常见的刹车系统之一,其设计优化将直接影响刹车性能和安全性。
在设计紧凑型轿车盘式制动器时,应考虑以下几个方面的优化方案。
首先,优化盘式制动器的材料选择。
材料的选择将直接影响刹车器的性能,包括刹车的稳定性和耐久性。
对于紧凑型轿车盘式制动器来说,常见的刹车盘材料有铸铁、碳陶瓷和复合材料等。
铸铁刹车盘具有制造成本低、刹车性能稳定等优点,但其重量相对较大,容易导致车辆重心向前移动,影响悬挂系统的稳定性。
碳陶瓷刹车盘由于其材料特性,具有优异的刹车性能和耐久性,但成本较高。
复合材料刹车盘是目前较为新兴的刹车盘材料,它的重量轻、刹车性能优良,但制造成本较高。
因此,在设计紧凑型轿车盘式制动器时,应综合考虑车辆重量、刹车性能和制造成本,在这三种材料之间做出权衡。
其次,优化盘式制动器的结构设计。
紧凑型轿车盘式制动器的结构设计应尽可能减小刹车器占用的空间,以适应车辆整体设计的紧凑要求。
优化设计主要包括刹车盘的直径、刹车片的数量和制动器的散热设计等方面。
刹车盘的直径直接影响到刹车力的传递效果,一般来说,直径越大,刹车力越大。
但过大的刹车盘直径会增加盘式制动器的重量和成本,还可能对悬挂系统产生负面影响。
刹车片的数量应根据车辆的制动需求来确定,过少会影响刹车性能,过多则可能影响磨损均衡。
制动器的散热设计应保证刹车系统在高温工况下的正常工作,可以通过增加散热片数量和改进散热通道设计等方式来实现。
再次,优化盘式制动器的刹车力分配。
在紧凑型轿车中,为了保证刹车性能和驾驶稳定性,前轮和后轮的刹车力分配需要合理调整。
传统的刹车力分配方式是根据车辆前后轴负荷比例来分配刹车力,但这种方式有时会导致刹车过早或过晚,影响刹车效果。
紧凑型轿车盘式制动器优化设计方案研究

紧凑型轿车盘式制动器优化设计方案研究引言:随着汽车工业的发展,紧凑型轿车在市场上的需求与日俱增。
为了满足消费者对安全性能和驾驶舒适性的要求,盘式制动器的设计方案变得尤为重要。
本文将研究紧凑型轿车盘式制动器优化设计方案,通过对设计参数的优化和材料的选择,提高制动器的性能和可靠性。
一、制动器的工作原理和发展趋势1. 制动器的工作原理:盘式制动器通过制动盘和制动片的摩擦力来减速车辆。
2. 制动器的发展趋势:随着车辆速度的提高和制动性能要求的增加,制动器的发展趋势主要包括以下几个方面:a. 提高制动器的制动力和散热性能;b. 减小制动器的尺寸和重量;c. 降低制动噪音和振动。
二、紧凑型轿车盘式制动器设计参数的优化紧凑型轿车盘式制动器的设计参数优化可以从以下几个方面进行研究:1. 制动片材料的选择:a. 优化制动片材料的摩擦系数和稳定性,以提高制动效果;b. 选择具有良好散热性和耐磨性的制动片材料,延长制动器的使用寿命。
2. 制动盘的设计和优化:a. 选择适当的制动盘材料,提高制动盘的强度和刚度;b. 优化制动盘的散热效果,降低制动盘的温度;c. 通过减少制动盘的质量和减小制动盘直径,降低制动器的重量。
3. 制动器液压系统的设计:a. 优化制动系统的液压传动比和制动启动压力,提高制动力的实时可调性;b. 选择高效的液压制动泵和制动器液压油,提高制动系统的快速响应性能。
4. 制动片和制动盘的接触过程模拟:a. 借助计算机仿真软件,对制动片和制动盘的接触过程进行模拟和分析;b. 通过优化制动片和制动盘的表面形状和接触压力分布,提高制动器的摩擦效果和制动性能。
三、制动器的性能测试和评估为了验证优化设计方案的效果,需要进行制动器的性能测试和评估。
测试项目包括:1. 制动力和制动距离的测试;2. 制动噪音和振动的测试;3. 制动器的散热性能测试。
测试结果将用于评估设计方案的有效性,并指导后续的改进和优化。
结论:通过对紧凑型轿车盘式制动器的优化设计方案的研究,可以提高制动器的性能和可靠性。
纯电动汽车制动器的设计优化与性能改进

纯电动汽车制动器的设计优化与性能改进随着电动汽车的快速发展,制动系统对于纯电动汽车的安全性和性能至关重要。
为了不仅满足行车安全的要求,还要提高纯电动汽车的制动效果和驾驶体验,制动器的设计优化和性能改进变得尤为重要。
以下是对纯电动汽车制动器设计优化和性能改进的探讨。
首先,根据纯电动汽车的特点,制动器设计需要考虑到电动汽车独特的能量回收和再利用机制。
由于电动汽车可以通过回收制动能量来充电电池,制动器的设计需要与动力电池系统紧密结合,使得制动能量可以高效地转化为电能进行储存和再利用。
其次,为了提高纯电动汽车的制动效果和驾驶体验,制动器的响应速度和制动力平衡是关键。
传统的液压制动系统通常存在延迟响应的问题,而采用电子制动系统可以实现更快的制动响应时间。
同时,通过精确控制每个车轮的制动力分配,可以提高制动力的平衡性,避免车轮的打滑和制动不均衡现象,从而提高制动效果和驾驶稳定性。
另外,制动器设计优化还应考虑到纯电动汽车的重量和能耗。
由于电池组的重量较大,制动器需要承受更大的停车制动力和长时间湿制动磨损,因此制动器的材料选择和结构设计需要更加耐磨和耐高温。
同时,制动器的能耗也需要尽量减少,以降低纯电动汽车的能量消耗,延长续航里程。
除了上述方面的改进,纯电动汽车制动器还需要进行智能化设计,以更好地适应未来智能交通的发展趋势。
通过车辆感知系统和主动安全技术,可以实现智能制动控制,根据车辆的装载情况、道路状况和驾驶行为实时调整制动力的分配和制动响应,提高制动的安全性和精确性。
在制动器性能改进方面,可以通过提高制动器的散热性能,降低制动片和刹车盘的温度。
通过改进制动片和刹车盘的材料和结构,减少刹车过程中的热量累积和传导,可以大大提高制动器的工作效率和耐久性。
此外,纯电动汽车制动器的舒适性也需要考虑。
通过减少刹车时的噪音和振动,可以提高乘坐舒适性和驾驶体验。
采用减振材料、优化制动器结构和控制算法,可以有效减少制动时的噪音和振动幅度。
针对紧凑型轿车的盘式制动器设计优化研究
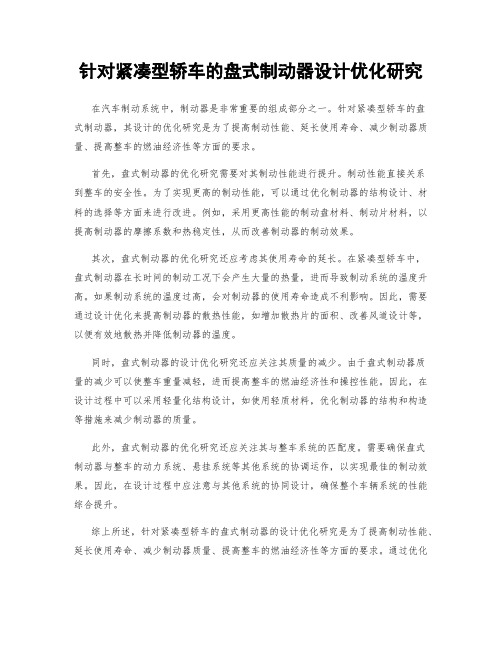
针对紧凑型轿车的盘式制动器设计优化研究在汽车制动系统中,制动器是非常重要的组成部分之一。
针对紧凑型轿车的盘式制动器,其设计的优化研究是为了提高制动性能、延长使用寿命、减少制动器质量、提高整车的燃油经济性等方面的要求。
首先,盘式制动器的优化研究需要对其制动性能进行提升。
制动性能直接关系到整车的安全性。
为了实现更高的制动性能,可以通过优化制动器的结构设计、材料的选择等方面来进行改进。
例如,采用更高性能的制动盘材料、制动片材料,以提高制动器的摩擦系数和热稳定性,从而改善制动器的制动效果。
其次,盘式制动器的优化研究还应考虑其使用寿命的延长。
在紧凑型轿车中,盘式制动器在长时间的制动工况下会产生大量的热量,进而导致制动系统的温度升高。
如果制动系统的温度过高,会对制动器的使用寿命造成不利影响。
因此,需要通过设计优化来提高制动器的散热性能,如增加散热片的面积、改善风道设计等,以便有效地散热并降低制动器的温度。
同时,盘式制动器的设计优化研究还应关注其质量的减少。
由于盘式制动器质量的减少可以使整车重量减轻,进而提高整车的燃油经济性和操控性能。
因此,在设计过程中可以采用轻量化结构设计,如使用轻质材料,优化制动器的结构和构造等措施来减少制动器的质量。
此外,盘式制动器的优化研究还应关注其与整车系统的匹配度。
需要确保盘式制动器与整车的动力系统、悬挂系统等其他系统的协调运作,以实现最佳的制动效果。
因此,在设计过程中应注意与其他系统的协同设计,确保整个车辆系统的性能综合提升。
综上所述,针对紧凑型轿车的盘式制动器的设计优化研究是为了提高制动性能、延长使用寿命、减少制动器质量、提高整车的燃油经济性等方面的要求。
通过优化制动器的结构设计、材料的选择等方面的改进,可以提升制动器的性能,并确保其与整车系统的匹配度,从而实现更安全、更高效的行车体验。
汽车制动性能的优化设计

3 制动力分配 比的确定
·一 + ≤ p≤ +
(12
式 中 Znl,_一 整车应 达 到的最小 制动 强度 利用 此式 ,可 以确定 ‘p=0.2—0.8之 间 的各种
为 :
在 轮胎 周缘 为 了克服 制动 器摩 擦力 矩 所需 的 力称 为 制动 器制 动力 ,以符 号 F 表示 。行 车制 动
EFr Z=一 若
(10)
采 用 Ⅱ型 双 回路气 压 制 动 系 。制 动 器 制 动 力 F 为 :
F :—pSK  ̄ 1 BFir — ]
(5)
式中 p一 制动器气室气压 ,可由试验测得
··--———--··——-一 m y
图 1 制 动 时 的汽 车 受 力 图
图 1中忽略了汽车的滚动阻力偶矩 、空气阻 力 以及旋 转质 量减 速时产 生 的惯性力 偶 矩 ,分别 对 前后轮 接地 点取力矩 ,得 :
NIL=Gb+m hs
oI 。
(1)
N2L=Ga—m hs
本 文 在设 计制 动 力分 配 比时,综合 考 虑到 满 载 与空载 两 种工 况,给 出了满 载 与空 载在 不 同 的 使用概率下,整车具有 良好 的制动稳定性和较高 制动效 能 的一 种优 化设计 方法 。另外 ,本文还介 绍 了当前使用 的几种典型的制动技术的原理 、构成 及功能 ,指出制动技术的进步显著提高了制动性 能 ,提 高 了汽 车 的安 全性 。
(2)
式 中 N,、N厂—玢 别 为地 面对前 轮和后 轮 的法 向反作用 力 汽车 重力
汽车盘式制动器优化设计2
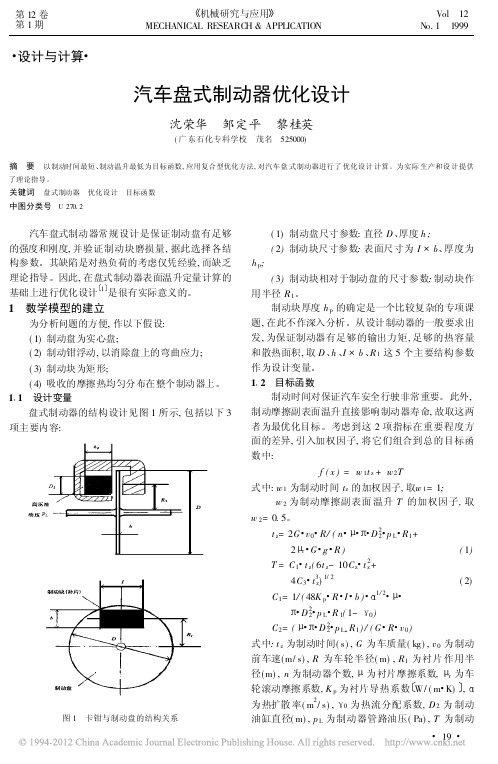
#设计与计算#汽车盘式制动器优化设计沈荣华 邹定平 黎桂英(广东石化专科学校 茂名 525000)摘 要 以制动时间最短、制动温升最低为目标函数,应用复合型优化方法,对汽车盘式制动器进行了优化设计计算。
为实际生产和设计提供了理论指导。
关键词 盘式制动器 优化设计 目标函数中图分类号 U 27012汽车盘式制动器常规设计是保证制动盘有足够的强度和刚度,并验证制动块磨损量,据此选择各结构参数。
其缺陷是对热负荷的考虑仅凭经验,而缺乏理论指导。
因此,在盘式制动器表面温升定量计算的基础上进行优化设计112是很有实际意义的。
1 数学模型的建立为分析问题的方便,作以下假设:(1)制动盘为实心盘;(2)制动钳浮动,以消除盘上的弯曲应力;(3)制动块为矩形;(4)吸收的摩擦热均匀分布在整个制动器上。
111 设计变量盘式制动器的结构设计见图1所示,包括以下3项主要内容:图1 卡钳与制动盘的结构关系(1)制动盘尺寸参数:直径D 、厚度h ;(2)制动块尺寸参数:表面尺寸为I @b 、厚度为h p ;(3)制动块相对于制动盘的尺寸参数:制动块作用半径R 1。
制动块厚度h p 的确定是一个比较复杂的专项课题,在此不作深入分析。
从设计制动器的一般要求出发,为保证制动器有足够的输出力矩,足够的热容量和散热面积,取D 、h 、I @b 、R 1这5个主要结构参数作为设计变量。
112 目标函数制动时间对保证汽车安全行驶非常重要。
此外,制动摩擦副表面温升直接影响制动器寿命,故取这两者为最优化目标。
考虑到这2项指标在重要程度方面的差异,引入加权因子,将它们组合到总的目标函数中:f (x )=w 1t z +w 2T式中:w 1为制动时间t z 的加权因子,取w 1=1;w 2为制动摩擦副表面温升T 的加权因子,取w 2=0.5。
t z =2G #v 0#R/(n #L #P #D 22#p L #R 1+ 2L r #G #g #R )(1)T =C 1#t z (6t z -10C z #t 2z +4C 3#t 3z )1/2(2)C 1=1/(48K p #R #I #b )#A 1/2#L #P #D 22#p L #R 1(1-C 0)C 2=(L #P #D 22#p L #R 1)/(G #R #v 0)式中:t z 为制动时间(s),G 为车质量(kg ),v 0为制动前车速(m/s),R 为车轮半径(m),R 1为衬片作用半径(m),n 为制动器个数,L 为衬片摩擦系数,L r 为车轮滚动摩擦系数,K p 为衬片导热系数1W/(m #K)2,A为热扩散率(m 2/s),C 0为热流分配系数,D 2为制动油缸直径(m),p L 为制动器管路油压(Pa),T 为制动#19#第12卷第1期5机械研究与应用6MECHANICAL RESE ARC H &APPLICATIONVol 12No.1 1999温升(e )。
制动系统优化设计开题报告

制动系统优化设计开题报告制动系统优化设计开题报告一、研究背景随着汽车工业的快速发展,制动系统作为汽车安全的重要组成部分,对车辆的制动性能和驾驶者的安全起着至关重要的作用。
然而,随着汽车的不断升级和发展,制动系统面临着新的挑战和需求。
因此,对制动系统进行优化设计,提高其性能和安全性,成为当前汽车工程领域的研究热点之一。
二、研究目的本研究旨在通过优化设计制动系统,提高汽车的制动性能和安全性。
具体目标包括:1. 分析当前制动系统存在的问题和不足之处;2. 探索制动系统的优化设计方法和技术;3. 提出一种针对特定车辆类型的制动系统优化设计方案;4. 通过试验和仿真验证优化设计方案的有效性和可行性。
三、研究内容1. 制动系统性能分析通过对当前市场上常见的制动系统进行性能测试和分析,了解其制动力、制动距离、制动稳定性等方面的表现,明确现有制动系统存在的问题和不足。
2. 制动系统优化设计方法研究研究和探索制动系统的优化设计方法和技术,包括但不限于材料选择、结构设计、液压系统优化等方面。
通过对相关文献的调研和实验研究,总结出一套适用于制动系统优化设计的方法论。
3. 制动系统优化设计方案提出根据研究成果,提出一种针对特定车辆类型的制动系统优化设计方案。
该方案应考虑车辆的动力性能、负载情况、操控要求等因素,以提高制动系统的性能和安全性为目标。
4. 试验和仿真验证通过试验和仿真验证优化设计方案的有效性和可行性。
利用现有的试验设备和仿真软件,对优化设计方案进行性能测试和模拟分析,以验证其在实际应用中的效果。
四、研究意义制动系统的优化设计对汽车的性能和安全性具有重要影响。
本研究的成果有以下几方面的意义:1. 提高汽车的制动性能,缩短制动距离,提高制动稳定性,增强驾驶者的安全感;2. 降低制动系统的磨损和故障率,延长制动系统的使用寿命,减少维修和更换成本;3. 推动汽车工程领域的技术创新和发展,提高我国汽车工业的竞争力。
五、研究方法本研究采用综合研究方法,包括实验研究、文献调研和数值仿真等。
毕业设计(论文)-汽车电磁制动器优化设计[管理资料]
![毕业设计(论文)-汽车电磁制动器优化设计[管理资料]](https://img.taocdn.com/s3/m/1d8a6cbde518964bce847c5d.png)
汽车电磁制动器优化设计序言随着社会生产力水平的提高,科学技术的不断发展,汽车的制造工艺也在不断的提升。
人们在满足了日常出行便利的情况下,对汽车的安全性能越来越注重。
能源危机作为当前社会的主要矛盾之一却不能阻止人们对速度的追求,因此车辆制动系统性能的好坏直接关系到人们的生命安全和财产安全。
一直以来国内外汽车生产企业和科研部门都非常重视汽车新型制动系统的研发。
伴随着第一辆汽车的诞生,汽车制动器的研究就已经开始,从一开始的简单的机械装置制动到气压制动、液压助力制动和如今的电子控制液压制动器先后出现在汽车上面。
电磁制动器是一种新型制动器,国外己用到拖车尤其是房车的制动上,而国内在这方面的研究还处于起步阶段。
和传统的气压式、液压式制动器相比,电磁制动器有其突出的优点,正受到越来越多的重视。
首先用电缆代替管路,提高了制动器的灵敏度,冗余电路的加入也很方便,可靠性高,安装方便,尤其是主、挂车的制动系统连接更简单可靠,并永远避免了泄漏和气阻现象;其次,控制器设计方便,易于实现ABS,因此代表了制动器的发展趋势,为汽车线控操纵实现车辆自动化、智能化提供了必备部件。
本说明书共分为4章,第一章课题分析与方案论证;第二章对制动系统进行历史的回顾和未来的展望;第三章对制动器的增力机构进行分析和设计;第四章对制动器的核心部件电磁铁进行分析设计。
其中重点是机械增力机构和电磁铁的设计。
设计的最终成果是能满足轿车常规制动的性能要求。
第1章课题分析与方案论证课题任务分析本课题的主要任务是对汽车电磁制动器进行优化设计,完成电磁制动器的书面设计使之能满足轿车常规制动的性能要求。
首先需要了解的是汽车电磁制动器的使用性能和设计要求。
如今马路上的汽车越来越多,速度也越来越快,如何能在各种突发情况下对汽车进行有效的制动一直是人们关注的话题,因此本次设计的电磁制动器必须满足这一基本要求,只有立足在这一点上才能有目的地去完成这个课题。
在明确了课题的目标之后,就需要熟悉汽车电磁制动器的设计方法和流程。
紧凑型轿车盘式制动器设计的优化与性能分析

紧凑型轿车盘式制动器设计的优化与性能分析轿车盘式制动器是汽车制动系统的核心部件之一,用于实现车辆的制动功能。
随着汽车工业的不断发展和人们对车辆性能和安全性要求的提高,紧凑型轿车盘式制动器的设计优化和性能分析变得尤为重要。
首先,紧凑型轿车盘式制动器设计的优化应注重以下几个方面:1. 制动盘与刹车片的材料选择:制动盘与刹车片的材料选择对制动器的性能有直接影响。
一方面,制动盘应选择高热导率和高热容量的材料,以提高散热效果,降低制动盘温度。
另一方面,刹车片应选择具有良好的摩擦性能和耐磨性的材料,以提高制动器的制动效果和寿命。
2. 刹车片的设计优化:刹车片的形状和结构对制动器的性能有重要影响。
应通过优化刹车片的形状和结构,提高刹车片与制动盘的接触面积和摩擦系数,以增强制动器的制动力和稳定性。
3. 刹车油路的优化设计:刹车油路的设计也是制动器性能优化的关键。
要选择合适的刹车主缸、刹车油管和刹车油储存器,以保证刹车系统的压力和流量稳定,提高制动器的制动响应速度和准确性。
其次,对紧凑型轿车盘式制动器的性能进行分析也是非常重要的。
对于制动器性能的分析可以从以下几个方面入手:1. 制动力和制动距离:通过实验测试和仿真模拟,评估制动器在不同工况下的制动力和制动距离。
同时,还可以分析制动力的分布情况,以确定制动器是否均匀工作。
2. 制动器的热性能:制动器在制动过程中会产生大量的热量,需要通过散热来保持制动器的性能稳定。
通过热传导和热辐射的分析,评估制动器的散热性能,以防止制动器因过热而失效。
3. 制动器的稳定性和可靠性:制动器在不同工况下的工作稳定性和可靠性是评价其性能的重要指标。
通过实验和模拟分析,评估制动器在急刹和长时间连续制动等特殊工况下的稳定性和可靠性。
最后,优化紧凑型轿车盘式制动器设计和提升其性能不仅依靠理论分析和仿真模拟,还需结合实际制造和测试。
通过实验测试,可以验证设计的优化方案和性能分析,为制动器的实际应用提供可靠的依据。
纯电动汽车制动器参数优化设计研究

纯电动汽车制动器参数优化设计研究随着电动汽车的普及,纯电动汽车制动器的设计与优化变得尤为重要。
制动器作为保证车辆安全的关键部件之一,其性能参数的优化设计对于提升制动效能、减少制动器磨损、延长制动器寿命具有重要意义。
本文将从制动器参数的优化设计出发,探讨如何提高纯电动汽车制动器的性能和可靠性。
首先,制动器参数的优化设计应考虑纯电动汽车的特点。
纯电动汽车具有短途驾驶、能量回收等特点,因此对制动器的需求可能与传统内燃车辆有所不同。
在选择制动器类型方面,电动汽车通常采用电子控制制动系统(EBS),其中包括电子制动力分配系统(EBD)、制动力增幅器(BBA)等部分。
选用适当的电子控制系统能够实现对制动力分配的精细调节,提高制动的安全性和舒适性。
其次,制动器参数的优化设计涉及到制动器的材料选择和结构设计。
对于电动汽车制动器而言,制动器的重量和占用空间都是重要的考虑因素。
因此,在材料选择方面,应优先选择轻质高强度材料,以减轻整车质量,提高能效。
在结构设计方面,应采用紧凑型设计,以最大程度地减少制动器占用空间。
此外,还应考虑电动汽车的能量回收系统,通过制动能量回收来减少制动器的使用频率,降低制动器的磨损。
第三,制动器参数的优化设计需要充分考虑纯电动汽车的动态特性。
电动汽车的加速性能通常较强,因此制动器的制动力水平应与电机输出相匹配。
过低的制动力将影响制动器的制动效能,而过高的制动力可能导致轮胎抱死现象,影响操控稳定性。
因此,在制动力的设定上应综合考虑车辆的动态特性以及驾驶员的操作反馈,实现制动力的平稳调节。
最后,制动器参数的优化设计还需要借助仿真模拟和试验验证。
通过建立电动汽车制动系统的数学模型,并结合实际道路情况和车辆运行状态,可以对制动器的性能预测与优化。
同时,应进行标准化的试验验证,以验证设计方案的可行性和有效性。
通过仿真模拟和试验验证,可以在较短的时间内评估和改进不同参数设计方案的制动性能,从而加快纯电动汽车制动器的优化设计过程。
纯电动汽车制动器设计与优化研究

纯电动汽车制动器设计与优化研究随着对环境保护和气候变化问题的关注日益增加,纯电动汽车作为一种低碳、环保的交通工具逐渐受到人们的青睐。
然而,纯电动汽车在制动系统设计上面临一系列的挑战和问题。
本文将围绕纯电动汽车制动器的设计与优化展开研究,旨在提出解决方案,改进纯电动汽车的制动性能和安全性。
首先,纯电动汽车的能量回收制动系统(Regenerative Braking System)是一项重要的技术,它能将制动时产生的动能转换为电能储存起来,以供之后的加速使用。
在制动器设计与优化的研究中,需要关注能量回收制动系统的优化,以提高能量的回收效率。
为了实现高效的能量回收,可以采用双模式制动器设计。
双模式制动器能在不同的驾驶工况下实现能量回收的最大化,提高纯电动汽车的续航里程。
其次,纯电动汽车的制动系统设计在安全性和制动性能方面面临一些挑战。
由于电动汽车具有高扭矩、瞬间加速的特点,在高速行驶或急刹车时容易出现制动距离过长的问题,因此需要对制动器进行更加精确和灵敏的控制。
制动系统的设计应考虑纯电动汽车的特殊性质,确保在不同路况下能够提供稳定的制动性能和安全性。
在纯电动汽车制动器的优化研究中,还需要考虑与车辆动力系统之间的协调和集成。
车辆的动力系统和制动系统紧密相连,两者之间需要进行协调工作,以实现高效的能量转换和安全的行驶。
制动器的设计和优化需要与电池管理系统、电控系统等其他车辆部件进行无缝集成,从而提高整体系统的性能。
除了设计和优化制动器本身,纯电动汽车制动器的材料选择也是一个重要的研究方向。
传统汽车制动器通常采用金属材料,但对于纯电动汽车来说,可能需要考虑轻量化和电磁兼容性等因素。
因此,可以研究发展新型的轻质材料,如复合材料或聚合物材料,以满足纯电动汽车制动器的特殊要求。
最后,纯电动汽车制动器的可靠性和耐久性也需要得到充分考虑。
电动汽车的制动系统在长时间使用和频繁制动的情况下会受到较大的应力,因此需要设计出能够承受这些应力的制动器。
纯电动汽车制动器设计与优化策略分析

纯电动汽车制动器设计与优化策略分析随着环境污染问题的日益严重和能源消耗压力的增加,纯电动汽车作为一种环保和可持续的出行方式逐渐崭露头角。
而作为纯电动汽车关键的安全性能部件之一,制动器在保证车辆行驶安全的同时也需要考虑低能耗和高效率的要求。
本文将就纯电动汽车制动器的设计与优化策略进行分析和讨论。
首先,纯电动汽车制动器的设计需要考虑到其特殊的动力系统和能量回收系统。
与传统汽车不同,纯电动汽车不会产生空气污染,但其驱动电动机的反向转换在制动过程中将产生较大的能量,需要通过制动器将多余的能量回收。
因此,在设计制动器时需要考虑与能量回收系统的配合,以提高能源利用效率。
在设计和优化纯电动汽车制动器时,还需要充分考虑其与车辆动力系统的协同性。
由于纯电动汽车通常采用无级变速传动系统,其制动器需要与传动系统配合,通过调整变速器齿轮比和转速等参数来实现优化制动效果。
此外,纯电动汽车特有的高扭矩和高功率特性对制动器的热耐受性和输出能力提出了更高的要求,需要选择能够适应高温和高负荷工作条件的制动材料和结构。
另外,纯电动汽车制动器的设计还需要兼顾驾驶者的用车感受和安全性能。
制动器的灵敏度、响应时间和制动力平衡等指标对驾驶者的驾驶体验有重要影响。
因此,制动器的优化策略应该考虑到不同驾驶模式下的制动感受和实际制动需求,通过合理的参数调节和系统控制来实现最佳的制动性能。
在纯电动汽车制动器的优化策略中,还需要考虑到降低制动器的能耗和减少制动器对车辆的负荷。
由于电动汽车的驱动系统对能源的高度敏感,制动能耗的降低对于续航里程的增加具有重要意义。
因此,制动器的设计和优化应该注重降低制动能耗,通过减小摩擦噪音、优化能量回收系统等方式来提高能源利用效率。
此外,在纯电动汽车制动器的设计和优化中,还可以考虑采用新的材料和制造工艺来提高制动器的性能。
例如,采用碳纤维材料可以降低制动器的重量和惯性,提高制动器的响应速度和稳定性;采用先进的制造工艺可以提高制动器的制造精度和一致性,进一步提升制动器的性能和可靠性。
电动机动车制动器的设计与优化

电动机动车制动器的设计与优化随着电动汽车的逐渐普及,电动机动车制动器的设计与优化成为了一个重要的研究方向。
与传统汽车相比,电动汽车的制动系统在设计上存在一些特殊要求和挑战。
本文将从设计原理、优化方法和挑战等几个方面探讨电动机动车制动器的设计与优化。
首先,我们来了解一下电动机动车制动器的基本原理。
电动机动车制动器主要通过提供制动力矩来减速或停止车辆的运动。
传统的汽车制动系统通常是通过摩擦制动原理来实现的,而电动车则可以利用电动机的逆变换特性来实现电能回馈制动。
电能回馈制动是指将电动机转换为发电机,把产生的电能由电池储存或返回电网。
这种制动方式不仅可以实现制动效果,还可以提高能源利用效率。
其次,针对电动机动车制动器的设计,优化方法至关重要。
在设计过程中,需要考虑到多个因素,包括制动力矩的大小、制动力的平稳性、节能性和可靠性等。
一种常见的优化方法是使用系统仿真软件,通过模拟不同设计参数和工况下的制动性能,找到最佳的设计方案。
同时,可以采用仿真实验相结合的方法,利用实验测试数据进行参数调整和优化。
另外,电动机动车制动器的设计也需要考虑制动力与制动距离的关系。
制动距离是指从刹车开始到车辆完全停下来所经过的距离。
制动距离的长短直接影响到行车安全性能。
因此,在设计过程中,需要根据电动车的质量、速度和道路条件等因素,合理确定制动力的大小和施加时间。
此外,电动机动车制动器的优化还需要考虑到能量回收和节能性。
在传统的摩擦制动中,制动时产生的能量通常是以热的形式散失掉的。
而电能回馈制动可以将制动时产生的电能回馈到电池中,从而提高能源利用效率。
因此,在设计过程中,需要合理设计制动系统的电能回馈装置,并优化其控制策略。
最后,电动机动车制动器的设计和优化也面临一些挑战。
首先,由于电动车的动力系统与传统汽车有很大的差异,制动器的设计需要考虑到电池系统的特性和安全性。
其次,电动车的制动器在高速制动时可能产生严重的磨损和热问题,需要采用耐高温和耐磨损材料来解决。
- 1、下载文档前请自行甄别文档内容的完整性,平台不提供额外的编辑、内容补充、找答案等附加服务。
- 2、"仅部分预览"的文档,不可在线预览部分如存在完整性等问题,可反馈申请退款(可完整预览的文档不适用该条件!)。
- 3、如文档侵犯您的权益,请联系客服反馈,我们会尽快为您处理(人工客服工作时间:9:00-18:30)。
汽车盘式制动器的制动时间优化设计摘要:利用matlab编程及工程优化的算法,建立以制动的最短时间为目标函数的数学模型,对汽车的制动时间进行科学的优化设计。
有效减少汽车盘式制动器的制动时间,从而提高汽车的制动与安全性能。
关键词:盘式制动器、最短制动时间、优化设计、单目标优化盘式制动器以其结构简单、尺寸紧凑,制动性能好,在同样大小的制动力矩条件下,其结构尺寸和质量都比鼓式制动器小,热稳定性和水稳定性好,无机械衰退问题,制动盘高温下形成热裂和热点的可能性小,不会如制动鼓那样的热膨胀引起制动踏板行程损失以及具有安全可靠,迅速平稳,摩擦衬片使用寿命长,重量轻,维修方便等一系列优点,被广泛应用于工程机械和各种汽车上。
但除了在一些高性能轿车上用于全部车轮以外,大都只用作前轮制动器,而与后轮的鼓式制动器配合,以期汽车有较高的制动时的方向稳定性。
1.目标函数与设计变量的确定盘式制动器的设计本质上是一个多目标优化问题。
在在制动器设计中有效提高制动效果、缩短制动时间是工程上普遍关注的问题。
缩短制动时间是缩短制动距离的有效措施之一,能够有效提高汽车的制动效能,提高汽车的制动性及安全性能。
汽车制动时间是重要的技术指标。
相同类型、级别的汽车,制动时间较短则汽车的安全性较高以制动时间最短为目标函数,2.建立盘式制动器优化设计的数学模型为分析问题的方便,作如下假设引入几个简化条件:1)制动盘为实体的2)制动钳或盘是浮动的,一边消除盘上的弯曲应力。
3)所有吸收的热量均匀分布在整个制动器上。
盘式制动器的结构剖面图如图所示。
如果将制动器的摩擦衬片的圆形摩擦面划分为无数个与盘心同心的圆弧单元,则该单元的摩摄与该处的压力p与线速度v成正比。
虽然摩擦衬片上的压力开始是均匀的,但是随着单元所在半径r的加大,其滑动线速度也会加大而导致单元磨损的加重。
这样的不均匀磨损过程使得远离盘心的地方压力越小,而使pv 在整个摩擦面上趋于相等,即pv=C,即常数。
采用辛普森积分法来进行计算。
因此制动盘所受压力F :F = pdA = C R +d/2R−d/2R +d/2R−d/2dA = C R +d/2R−d/2l dr式中l 为阴影部分小单元弧长,由图的几何关系可得: l =r •2α=2r •cos −1[R 2+r 2﹛d 2﹜2Rr ]由此可得常数C 为:C =F I 1 其中I 1= l r R +d/2R−d/2dr 可得:p =F I 1r制动时摩擦力矩为T f =2 μprdA =2μF I 2R +d/2R−d/2其中I 2= l I 1R +d/2R−d/2dr ,μ为制动盘与衬片间的摩擦系数由此可知格式中l 、I 2、I 2均为r 的函数 制动时,制动盘每转一圈时摩擦力矩T f 所小号的功为:H=T f •2π=4πF μI 2若n 0为开始时制动时制动盘或车轮的转速(r/min ),t 为从开始制动到完全停车所需要时间,即制动时间(min ),制动过程中制动盘或车轮转的总圈速为n s =n 02t 因此在制动过程中衬片与制动盘消耗的总的功为E =n s H = 2πF μn 0t t I 2而摩擦力所消耗的是汽车的动能,故又有E =1n W a •v 22g (N •m)根据能量守恒原理,制动过程中衬片与制动盘间所小号的总功与汽车动能相等。
t=W a•V24πFμI2•n0•mg(min)其中n0=V2πRr式中,W a为汽车总重,(N)V为汽车制动时的初速n为汽车车轮或制动器数,(r/min);g为重力加速度,(m/s2)F为高压油缸活塞推力F=π4D p2•p0D p为活塞直径(mm)p0为油缸内的油压(MPa)3.选取设计变量盘式制动器设计变量有4个,即: X = ( R, d , D,Dp,p0) = (x1, x2,x3,x4,x5) 。
其中, R 为衬垫中心线处的半径, mm; d 为衬垫的直径, mm; Dp为活塞直径, mm; p0为油压,MPa。
4.目标函数的确定以制动时间作为最优化的目标函数minf(x)=t5.建立约束条件参数约束条件根据以下关系建立1)衬片与轮毂不得发生干涉−x1+12x2+12D ≤0式中D 为给定的轮毂直径2)衬片的安装位置不应超出制动盘之外x1+12x2-12x3≤03)油缸与轮毂不应发生干涉−x1+12x4+t c+12D ≤0式中t c为压力油缸的壁厚4)制动盘的直径D应在其规定的范围[D max]内x3−[D max]≤05)油缸油压P0max不应超过其规定范围[P0max]x5−[P0max]≤06)衬片压力不应超过其规定范围[P max]πx42•x54I1(x1−x22)−[P max]≤07)制动摩擦力矩T f不应超过车轮与地面的附着力矩2μFI2−Wrφ≤0式中W为汽车满载时一个车轮的称重;φ为车轮与地面的附着系数;r为车轮半径F,I2为设计变量的函数6.选择算法采用改进粒子群算法,传统的粒子群优化算法早期收敛速度快,但是容易陷入局部最优解而发生“早熟”现象。
了增加粒子群的多样性,防止粒子集中过快,本文引入基于浓度概念的竞争排挤机制。
其基本思想是每间隔数代按照式计算每个粒子的浓度,并以此为依据,按照式计算每个粒子的竞争排挤的概率,对所有粒子应用竞争排挤算子更新其位置与速度。
竞争排挤算子:在(0—1)内生成一个随机数对粒子不进行任何改变,粒子按照PSO算法的基本速度位受到竞争排挤,粒子的位置与速度都将由竞争排挤算子重新随机给定,其关于过去所经历个体最优点的相关记忆也将被重置。
该算法的基本流程图如图算法改进的结果是在高浓度区域以较高概率抑制粒子的过渡集中,而在浓度较低的区域大部分粒子仍然可以按照粒子群算法的迭代过程寻找最优解,从而提高了粒子群的多样性,增强了粒子群的全局搜索能力,有效的避免“早熟”现象。
PSO 算法属于进化算法的一种,和遗传算法相似,它也是从随机解出发,通过迭代寻找最优解,它也是通过适应度来评价解的品质,但它比遗传算法规则更为简单,它没有遗传算法的“交叉”(Crossover) 和“变异”(Mutation) 操作,它通过追随当前搜索到的最优值来寻找全局最优。
这种算法以其实现容易、精度高、收敛快等优点引起了学术界的重视,并且在解决实际问题中展示了其优越性。
7.优化结果的比较设初始值制动时间tt为11.4138s。
其中车轮半径r为350mm,摩擦系数μ为0.5,汽车总重Wa为3400N,汽车的制动初速度为44.4444m/s、汽车车轮数m为4.制动时间单目标优化时,制动时间最优值为9.0703s。
通过优化制动时间减少了两秒多,时间减少明显。
通过优化过程使制动时间能够有效地缩短,从而影响制动距离,改变制动距离的大小。
制动时间是影响制动距离的一个重要的因素。
因此该优化过程可以明显改变制动时汽车的制动距离,从而能够有效地提高汽车制动盘的制动性能,有利于缩短汽车制动时的制动距离,提高汽车的安全性能。
制动距离越小,汽车的制动性能就越好。
由于它比较直观,因此成为广泛采用的评价制动效能的指标。
正确掌握汽车制动距离对保障行车安全起着十分重要的作用。
附录1:运行程序(1)求制动力矩Tf,制动时间tt(初始设计值)r=30;u=0.5;fai=1;W=3400;v=44.4444;m=4;tc=6.5;Dh=75;Wa=W*m;g=9.8;n0=500*v/(pi*r);R=105;d=40;D=256;Dp=48;a=12;p0=2.5;F=pi/4*Dp*Dp*p0;syms tl=2*t*acos((R*R+t*t-(d/2)*(d/2)/(2*R*t));y=l/t;I1=int(y,t,R-d/2,R+d/2);I1=double(I1);I1=real(I1)I2=int(1,t,R-d/2,R+d/2);I2=double(I2)/I1Tf=2*u*F*I2;tt=W*v*v*1000/(4*pi*F*u*I2*n0*g)T=4*3.4265e+005/(4180*pi*0.113*7.8e-6*D*D*a)+35通过程序运行得到:Tf=4.7283eTt=11.4138即制动力矩Tf为472830N•m;制动时间tt为11.4138s(2)制动时间单目标优化%优化时间function y=F1X_tideal(x)global I1 I2 Fr=350;u=0.5;fai=1;W=3400;v=44.4444;m=4;tc=6.5;Dh=75;Wa=W*m;g=9.8; Dmax=300;Tmax=260;Ti=35;Pmax=3;P0max=7;J=4180;c=0.113;rou=7.8*10^(-6);E=Wa*v*v/(2*m*g);n0=500*v/(pi*r);F=pi/4*x(3)*x(3)*x(4);I1=0;I11=0;I12=0;I13=0;I2=0;I21=0;I22=0;I23=0;n=100;delt=x(2)/n;t=x(1)-x(2)/2;for k=1;(n+1)l(k)=2*t*acos((x(1)*x(1)+t*t-(x(2)/2)*(x(2)/2))/(2*x(1)*t));yI1(k)=l(k)/t;if (k-1)==0|(k-1)==nI11=l11+1/3*yll(k);elself rem(k-1,2)~=0I12=I12+4/3*yI1(k);elseI13=I13+2/3*yI1(k);endt=t+delt;endI1=(I11+I12+I13)*delt;I1=real(I1);t=x(1)-x(2)/2;for k=1:(n+1)l(k)=2*t*acos((x(1)*x(1)+t*t-(x(2)/2)*(x(2)/2))/2(2*x(1)*t));yI2(k)=l(k)/I1;if(k-1)==0|(k-1)==nI21=I21+1/3*yI2(k);else if rem(k-1,2)~=0I22=I22+4/3*yI2(k);elseI23=I23+2/3*yI2(k);endt=t+delt;endI2=(I21+I22+I23)*delt;I2=real(I2);y=W*v*v*1000/(4*pi*F*u*I2*n0*g);%优化约束function [c,cep]=F1X_tconstrideal(x)global I1 I2 Fc=[pi*x(3)*x(3)*x(4)/(4*I1*(x(1)-x(2)/2))-3;2*F*12-1190000];ceq=[];x0=[105;40;48;3;256];lb=[85;30;40;1;250];ub=[120;60;70;7;280];A=[-1,1/2,0,0,0;1,1/2,0,0,-1/2;-1,0,1/2,0,0];b=[-37.5;0;-44];options=optimset(‘largescal’ ,‘off’);[x,fval]=fmincon(@F1X_tideal,x0,A,b,[],[],1b,ub, ‘F1X_tconstrideal’,options)通过程序运行得到:X=104.0014 59.5322 59.1736 2.1023 268.1551fval=9.0703即摩擦衬片中心园半径为104.0014mm、摩擦衬片直径为59.5322mm、活塞直径为59.1736mm、油缸内的油压为2.1.23MPa、制动盘直径为268.1551mm时得到最短制动时间为9.0703s。