制动盘优化设计原稿
紧凑型轿车盘式制动器设计优化方案探究
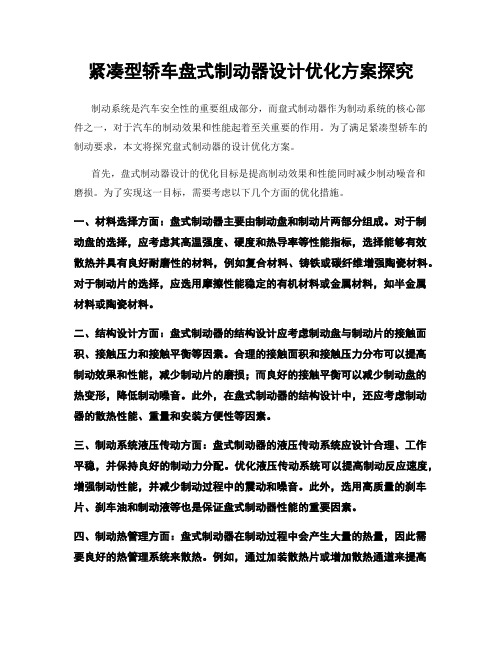
紧凑型轿车盘式制动器设计优化方案探究制动系统是汽车安全性的重要组成部分,而盘式制动器作为制动系统的核心部件之一,对于汽车的制动效果和性能起着至关重要的作用。
为了满足紧凑型轿车的制动要求,本文将探究盘式制动器的设计优化方案。
首先,盘式制动器设计的优化目标是提高制动效果和性能同时减少制动噪音和磨损。
为了实现这一目标,需要考虑以下几个方面的优化措施。
一、材料选择方面:盘式制动器主要由制动盘和制动片两部分组成。
对于制动盘的选择,应考虑其高温强度、硬度和热导率等性能指标,选择能够有效散热并具有良好耐磨性的材料,例如复合材料、铸铁或碳纤维增强陶瓷材料。
对于制动片的选择,应选用摩擦性能稳定的有机材料或金属材料,如半金属材料或陶瓷材料。
二、结构设计方面:盘式制动器的结构设计应考虑制动盘与制动片的接触面积、接触压力和接触平衡等因素。
合理的接触面积和接触压力分布可以提高制动效果和性能,减少制动片的磨损;而良好的接触平衡可以减少制动盘的热变形,降低制动噪音。
此外,在盘式制动器的结构设计中,还应考虑制动器的散热性能、重量和安装方便性等因素。
三、制动系统液压传动方面:盘式制动器的液压传动系统应设计合理、工作平稳,并保持良好的制动力分配。
优化液压传动系统可以提高制动反应速度,增强制动性能,并减少制动过程中的震动和噪音。
此外,选用高质量的刹车片、刹车油和制动液等也是保证盘式制动器性能的重要因素。
四、制动热管理方面:盘式制动器在制动过程中会产生大量的热量,因此需要良好的热管理系统来散热。
例如,通过加装散热片或增加散热通道来提高散热效果;同时,合理选择制动盘和制动片的材料,以提高其耐热性能,减少热膨胀和热衰减对制动性能的影响。
综上所述,紧凑型轿车盘式制动器的设计优化方案涉及材料选择、结构设计、液压传动和热管理等多个方面。
通过合理选择材料、改善结构设计、优化液压传动系统和加强热管理,可以提高制动效果和性能,减少制动噪音和磨损,进而提高紧凑型轿车的整体安全性和驾驶体验。
CRH380B动车组制动盘有限元分析与优化

CRH380B动车组制动盘有限元分析与优化摘要:动车组制动盘在列车制动过程中起到重要的作用,为了保证制动效果和制动安全性能,有限元分析和优化方法被广泛应用于制动盘结构设计中。
本文以CRH380B动车组为研究对象,采用有限元分析方法对制动盘进行了结构分析,并通过参数优化方法对其结构进行改进和优化,以提高制动性能和制动安全性。
1. 引言动车组制动盘是高速列车制动系统的重要组成部分,它负责将制动力通过摩擦将能量转化为热能,并将速度转化为制动力。
制动盘的结构与性能直接影响了列车的制动效果和制动安全性能。
因此,深入研究制动盘的结构和性能,并进行有限元分析与优化,对于提高动车组的制动效果和制动安全性能具有重要意义。
2. 有限元分析模型建立针对CRH380B动车组制动盘的结构特点,建立了有限元模型。
首先,采用三维建模软件对制动盘的几何形状进行建模,并根据实际情况给予适当的约束条件。
然后,将建模结果导入有限元分析软件,进行网格划分和材料属性设置。
最后,通过施加相应的载荷,得到制动盘在制动过程中的应力和变形分布。
3. 结果分析通过有限元分析,得到了CRH380B动车组制动盘在制动过程中的应力和变形分布。
结果表明,制动盘表面的应力集中区主要集中在制动盘的刹车面和孔洞周围,而变形较大的区域主要集中在制动盘的孔洞附近。
这些应力集中和变形较大的区域容易导致制动盘的疲劳破裂和变形失效,从而降低了制动效果和制动安全性能。
4. 优化方法探讨为了改善制动盘的结构和性能,采用了参数优化方法进行改进和优化。
首先,对制动盘的材料参数进行优化,选择具有较高抗疲劳性能和热稳定性的材料,以提高制动盘的耐久性和热稳定性。
其次,优化制动盘的几何形状参数,减小制动盘刹车面的应力集中区,降低变形区域的变形值,以提高制动性能和制动安全性能。
5. 优化结果分析通过参数优化方法,得到了改进后的制动盘结构。
与初始结构相比,改进后的制动盘表面应力集中区减小了约20%,变形区域的变形值降低了约15%。
基于安全与效能的紧凑型轿车盘式制动器设计优化

基于安全与效能的紧凑型轿车盘式制动器设计优化设计优化紧凑型轿车盘式制动器,需要基于安全与效能的考虑因素。
重点在于提高制动器的性能、减小体积、降低制动距离,并确保驾驶员和乘客的安全。
首先,我们需要注意制动器的材料选择。
现代制动器常用的材料有钢、铸铁和碳陶瓷复合材料。
钢制制动器耐用,但重量较大;铸铁制动器相对较轻,但容易发生裂纹;碳陶瓷复合材料制动器具有良好的制动性能和耐久性,但成本较高。
因此,我们需要根据市场需求和成本效益考虑,选择最适合的材料。
其次,轿车盘式制动器的设计需要考虑制动盘的尺寸。
制动盘的直径越大,制动力矩也越大,因此制动效果更好。
然而,较大的制动盘也会增加重量和制动系统的体积。
因此,我们需要进行详细的分析和测试,找到适合的平衡点,以确保制动器既能提供足够的制动力,又能保持轻巧紧凑。
此外,制动蹄片是制动器的重要组成部分。
我们需要选择合适的制动蹄片材料,以确保制动蹄片具有良好的耐磨性和热稳定性。
同时,制动蹄片的设计应该充分考虑散热性能,以避免制动器过热导致失效。
通过使用适当的材料和设计方法,可以提高制动器的寿命和性能。
另外,制动器的制动液也需要特别注意。
制动液在制动系中起着传递压力、保持系统稳定的重要作用。
选择合适的制动液,可以提高制动系统的性能和快速响应。
同时,制动液的沸点和湿润性也是重要考虑因素。
沸点较高的制动液可以在高温环境下保持稳定,湿润性强的制动液能够有效防止脚气现象的发生。
最后,设计优化过程中应考虑到制动系统的整体效能。
可以通过优化制动系统的液压传动装置、制动踏板及主缸等部件,以提高制动效能和响应速度。
此外,完善的制动控制系统和防抱死系统也可增强制动器的安全性。
总结而言,基于安全与效能的考虑因素对紧凑型轿车盘式制动器的设计优化至关重要。
在选择材料时,需要权衡其重量、耐久性和成本等因素。
制动盘、蹄片和制动液的选材和设计应充分考虑制动性能、散热性能和稳定性。
通过优化整个制动系统,我们可以提高制动效能和安全性,同时减小制动器的重量和体积,以满足紧凑型轿车的需求。
基于紧凑型轿车需求的盘式制动器优化设计
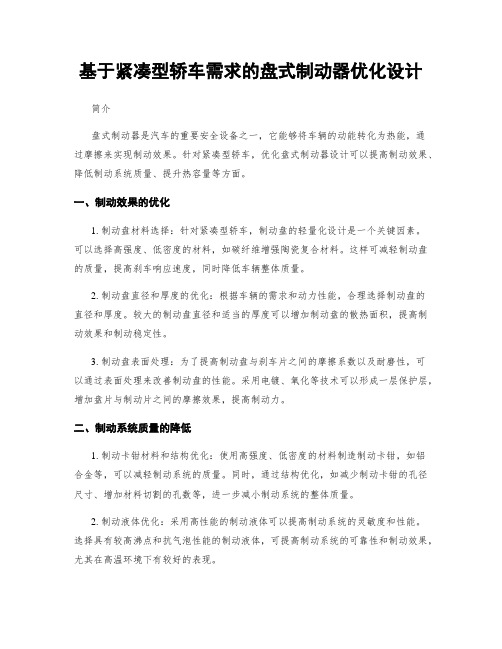
基于紧凑型轿车需求的盘式制动器优化设计简介盘式制动器是汽车的重要安全设备之一,它能够将车辆的动能转化为热能,通过摩擦来实现制动效果。
针对紧凑型轿车,优化盘式制动器设计可以提高制动效果、降低制动系统质量、提升热容量等方面。
一、制动效果的优化1. 制动盘材料选择:针对紧凑型轿车,制动盘的轻量化设计是一个关键因素。
可以选择高强度、低密度的材料,如碳纤维增强陶瓷复合材料。
这样可减轻制动盘的质量,提高刹车响应速度,同时降低车辆整体质量。
2. 制动盘直径和厚度的优化:根据车辆的需求和动力性能,合理选择制动盘的直径和厚度。
较大的制动盘直径和适当的厚度可以增加制动盘的散热面积,提高制动效果和制动稳定性。
3. 制动盘表面处理:为了提高制动盘与刹车片之间的摩擦系数以及耐磨性,可以通过表面处理来改善制动盘的性能。
采用电镀、氧化等技术可以形成一层保护层,增加盘片与制动片之间的摩擦效果,提高制动力。
二、制动系统质量的降低1. 制动卡钳材料和结构优化:使用高强度、低密度的材料制造制动卡钳,如铝合金等,可以减轻制动系统的质量。
同时,通过结构优化,如减少制动卡钳的孔径尺寸、增加材料切割的孔数等,进一步减小制动系统的整体质量。
2. 制动液体优化:采用高性能的制动液体可以提高制动系统的灵敏度和性能。
选择具有较高沸点和抗气泡性能的制动液体,可提高制动系统的可靠性和制动效果,尤其在高温环境下有较好的表现。
三、热容量的提升1. 制动系统散热设计:为了提高制动系统的热容量,可以在设计中合理设置散热片和通风孔,加强制动系统的散热效果。
通过增加散热片的面积和适当设置通风孔,能够快速散热,降低制动系统的温度,提高制动性能。
2. 制动盘内部通风片设计:在制动盘内部加入通风片,可以提高制动盘的内部空气流通性,增加散热效果。
通过通风片的设计,能够使热量更加迅速地从制动盘中散发出来,提高制动能力和稳定性。
结论基于紧凑型轿车需求的盘式制动器优化设计是为了提高制动效果、降低制动系统质量、提升热容量等方面。
基于工程性能的紧凑型轿车盘式制动器设计优化

基于工程性能的紧凑型轿车盘式制动器设计优化随着现代社会的快速发展和人们对个人交通工具的需求增加,轿车成为大多数家庭的必备之物。
作为轿车的重要组成部分,制动器在行车安全和性能方面起着至关重要的作用。
本文将介绍一种基于工程性能的紧凑型轿车盘式制动器设计优化方案。
首先,我们需要了解紧凑型轿车盘式制动器的基本构造和工作原理。
盘式制动器主要由制动盘、刹车钳和制动片组成。
当驾驶员踩下制动踏板时,制动油经由主缸传递给刹车钳,使得刹车钳内的制动片夹住制动盘,从而实现制动作用。
紧凑型轿车盘式制动器的设计要求通常包括制动力、制动距离、散热性能、重量和成本等方面。
优化紧凑型轿车盘式制动器的第一步是确定设计目标。
根据制动力和制动距离的要求,可以确定所需的刹车钳和制动盘的尺寸。
制动盘的直径和刹车钳的数量与制动力直接相关,需要根据车辆的重量和速度确定。
可以采用仿真软件进行盘式制动器的设计和分析。
该软件可以模拟不同工况下的制动效果和温度分布,从而帮助优化设计方案。
在设计过程中,需要考虑散热性能和制动效率的问题。
散热性能是指制动器在高速制动时能够有效散发热量,防止制动盘过热导致制动效果下降。
可以采用内部通风和外部散热片等散热设计,提高散热效果。
同时,制动片的材料选择和制动片的摩擦系数也会影响制动效率,需要平衡制动力和制动温度之间的关系。
另外,盘式制动器的重量和成本也是需要考虑的因素。
通过优化设计,可以减轻制动器的重量,提高车辆的燃油经济性和操控性。
同时,可以通过合理选择材料和制造工艺,降低制动器的成本,并提高制动器的可靠性和耐久性。
最后,进行测试和验证是优化设计方案的重要步骤。
可以借助实验室和道路试验等手段,对制动器的性能进行评估。
通过与实际使用情况的比较和分析,不断调整和改进设计方案,以达到最佳的综合性能。
综上所述,基于工程性能的紧凑型轿车盘式制动器的设计优化需要考虑制动力、制动距离、散热性能、重量和成本等方面。
通过合理的设计和分析,可以实现较好的制动效果和操控性,提高驾驶安全性和舒适性。
现代汽车盘式制动器的优化设计分析

现代汽车盘式制动器的优化设计分析摘要盘式制动器具有热稳定性好、浸水性能减小少等多方面的优点,且其应用广,所以在汽车中得到推广。
文章对盘式制动器的效能进行了分析,并有针对性地对其进行了优化设计,以期能够促进盘式制动器的更优发展。
关键词汽车;盘式制动器;设计;优化1 盘式制动器基本特性分析1.1 盘式制动器制动力矩的分析与计算盘式制动器制动力矩对于整个制动器的稳定性能具有重要作用,所以在制动器的性能优化过程中,常常优先对其制动力矩进行分析。
根据现有公式:首先,制动器在制动过程中产生的制动力矩为:Mρ=2ρPR,其中ρ表示盘式制动器的摩擦系数,一般ρ=0.35,在理想条件下ρ可取0.3,使计算结果符合实际情况。
P表示单项制动片对制动盘的压紧力:P=1/4πd2p。
R表示受力半径,对于一些常见的摩擦片的表面,根据实际情况的反复检验,证明如果其具有相对较小的径向宽度,那么取R等于有效半径Re[1]。
平均半径:Rm=R1+R2/2。
其中R1和R2分别为摩擦衬片的内半径和外半径。
有效半径:Re=Mρ/2ρP。
T=2ρpπd2(R23-R13)/6(R22-R12)。
1.2 制动器摩擦片所受的压力制动器摩擦片所受的压力,是研究盘式制动器性能的重要参数。
计算其所受的压力,我们首先要知道摩擦片上的点与制动盘轴线的距离,假设这一段的距离为r,那么在这段距离范围内,摩擦片上的任意一点所受的压力我们都可以通过公式进行计算。
压力用P表示,那么:P=βR/r·πd2p/4A。
这个公式中,A代表摩擦片的摩擦面积,其单位一般选定mm2,β的值通过公式计算:β=4R1R2/(R1+R2)R+2R1R2,β一般表示比例函数。
其中在R1和R2处,P分别达到最大值和最小值。
摩擦片的最大的单位压力为:Pmax=βR/R1·πd2p/4A。
2 盘式制动器优化设计模型建立首先,对于盘式制动器的优化,是为了防止制动器的设计不合理、摩擦材料老化等原因引起的制动器的热能损耗,或者引起制动时的强烈震动等。
基于性能和结构的紧凑型轿车盘式制动器优化设计

基于性能和结构的紧凑型轿车盘式制动器优化设计紧凑型轿车盘式制动器是现代汽车制动系统中的重要组成部分,对于车辆的制动性能和安全性起着关键作用。
优化设计可以提高制动器的性能和结构,从而提升整车的制动效果和驾驶体验。
本文将基于性能和结构的角度,对紧凑型轿车盘式制动器进行优化设计,并提出相应的方案。
一、性能优化1. 制动力的提升:通过优化摩擦材料和制动液的性能,可以改善制动器的刹车效果。
选用高性能摩擦片,提高摩擦系数和耐磨性,确保制动力的稳定输出;选用高质量制动液,提高油压传递效率,减少制动系统的延迟。
2. 散热性能的提升:制动器在制动过程中会产生大量的热量,如果散热不良会导致制动力下降甚至制动衰竭。
通过设计散热通道和增加散热片等方式,增强制动器的散热性能,降低温升,增加制动器的工作稳定性。
3. 制动系统的调校:制动器的性能与整车的悬挂、电子控制系统等因素密切相关。
通过对制动系统进行调校和优化,使其与整车的其他系统协调工作,提高制动器的响应速度和制动效果。
二、结构优化1. 材料的优化:选择高强度、低密度的材料,可以降低制动器的质量,提高整车的燃油经济性和操控性能。
同时,合理的材料选择还能够提高制动器的耐磨性和抗热性能。
2. 结构的优化:通过优化制动器的结构设计,如减小主缸和制动钳的尺寸,减少滑动阻力和摩擦损失,降低制动器的磨损和能量损失。
合理设计制动器的凸轮和制动片间隙,提高制动片的刹车效果。
3. 制动器的轻量化设计:通过减小制动器的质量,可以降低整车的非悬挂质量,提高悬挂系统的工作效率和车辆的燃油经济性。
轻量化设计还能够减小制动器的惯性质量,提高制动器的响应速度。
三、优化设计方案1. 采用高性能摩擦材料,如陶瓷复合材料,提高摩擦系数和耐磨性。
2. 优化制动液的性能,选用高质量制动液,提高油压传递效率。
3. 设计散热通道,增加散热片,提高制动器的散热性能。
4. 与整车的悬挂和电子控制系统协调工作,提高制动器的响应速度和制动效果。
家用车制动盘的多目标优化设计

家用车制动盘的多目标优化设计作者:王所国沈精虎石乐来源:《青岛大学学报(工程技术版)》2021年第04期摘要:針对某家用车制动盘的结构改进问题,本文对家用车制动盘进行多目标优化。
为避免优化的盲目性,提高设计效率,首先对建立的制动盘有限元模型进行灵敏度分析,得出制动盘各尺寸参数对制动性能的影响度。
以制动盘表面温度最低与最大等效应力值最小作为目标函数,建立优化数学模型,采用Ansys Workbench中的多目标遗传算法进行求解,优化后进行仿真验证。
优化结果表明,优化后最高温度降低了13.1%,最大应力降低了11.5%,既节省了优化时间又改进了制动盘的结构,实现了制动盘的多目标优化设计。
该研究为盘式制动器设计提供了参考。
关键词:制动盘; 优化设计; 多目标优化; 灵敏度分析; Ansys Workbench中图分类号: U463.51+2 文献标识码: A随着小型家用汽车的普及,交通事故的发生量逐年增加,汽车的行驶安全更加引起人们的重视。
作为制动系统关键部件的制动盘,其性能直接影响车辆的行驶安全[1]。
盘式制动器具有良好的制动性能,广泛用于家用车的制动系统[2],制动盘作为盘式制动器的关键部件直接决定制动性能的好坏。
针对盘式制动器的优化设计,不少学者进行了大量研究。
赵树国等人[3]利用Optistruct软件对汽车盘式制动器进行了拓扑优化,优化后的制动器质量减少了45%;华逢志等人[4]以小型轿车前轮盘式制动器为研究对象,基于Ansys Workbench软件对钳体和支架进行了优化设计;沙智华等人[5]通过分析制动盘沟槽的角度、宽度、密度之间的交互关系对制动盘最大温度值和最大等效应力值的影响完成了对制动盘的优化设计;吴家虎[6]以制动时的温升最小和制动盘尺寸最小为目标函数,利用多目标遗传算法对盘式制动器进行了优化设计;阚云峰[7]以制动过程中的最高制动温度以及允许出现的最大制动力矩为目标函数对盘式制动器进行优化并得到了试验验证;潘公宇等人[8]以散热筋尺寸为优化对象,对盘式制动器进行了有限元分析与优化。
汽车刹车制动盘形状优化设计

第2"卷第"期 2018年6月哈尔滨理工大学学报JOURNAL OF HARBI,^ UNIVERSITY OF SCIE:NCE AND TECHNOLOGYV ol.23 No. 3Jun. 2018汽车刹车制动盘形状优化设计陈再发(浙江国际海运职业技术学院,浙江舟山316021)摘要:针对摩擦热效应等因素引起汽车刹车制动器性能不足的问题,依据动力学原理的固有 频率理论,首先运用OptiStruct仿真软件对不同材料属性的盘式刹车片进行模态分析,其次是基于 HyperMorph对制动盘进行领变形定义并以此作为形状优化的设计变量,通过OptiStruct优化求解器计算出盘式制动盘的最佳结构形状,最后对设计变量灵敏度进行分析,给出对优化结果影响最大的设计变量并进行了针对性的改进。
设计方法对提高刹车制动系统的性能、降低制动噪音和减小振动有着重要意义。
关键词! OptiStruct软件;盘式制动系统;模态分析;形状优化DOI&10.15938/j. jhust. 2018.03.022中图分类号:TH164 文献标志码:A 文章编号!1007-2683(2018)03-0128-05 Shape Optimization Design of Brake System Based on Opti StructC H E N Z a i-fa(Zhejiang International Martime College,Zhoushan 316021,China)Abstract $Due to friction h eat effect or severe vibration and other factors,the performance of automobile brake is insufficient,according to natural frequency theory of tlie princijDle of dynamics,Firstly,the simulation software of OptiStruct is used to analyze the disc brake pads with different material properties,Secondly,t brake disc is defined based on HyperMorph and used as the design variable of OptStruct optimization solver to calculate the best shape of disc brake disc design variables is analyzed,and the design variables which have the greatest impact on the optimization results are given. The design results are significant to improve the performance of brake system,reduce braking noise and reduce vibration.Keywords :optistruct software;disc brake system %modal analysis;shape optimization〇引言刹车制动系统是汽车构造中的重要组成部分,刹车片和制动盘在行驶过程中通过接触摩擦作用可 使汽车减速及停止,复杂的路况需制动系统具有良好的动态性能,防止摩擦热效应或剧烈振动等因素 引起刹车制动器性能不足,甚至出现疲劳失效。
紧凑型轿车盘式制动器优化设计方案研究

紧凑型轿车盘式制动器优化设计方案研究引言:随着汽车工业的发展,紧凑型轿车在市场上的需求与日俱增。
为了满足消费者对安全性能和驾驶舒适性的要求,盘式制动器的设计方案变得尤为重要。
本文将研究紧凑型轿车盘式制动器优化设计方案,通过对设计参数的优化和材料的选择,提高制动器的性能和可靠性。
一、制动器的工作原理和发展趋势1. 制动器的工作原理:盘式制动器通过制动盘和制动片的摩擦力来减速车辆。
2. 制动器的发展趋势:随着车辆速度的提高和制动性能要求的增加,制动器的发展趋势主要包括以下几个方面:a. 提高制动器的制动力和散热性能;b. 减小制动器的尺寸和重量;c. 降低制动噪音和振动。
二、紧凑型轿车盘式制动器设计参数的优化紧凑型轿车盘式制动器的设计参数优化可以从以下几个方面进行研究:1. 制动片材料的选择:a. 优化制动片材料的摩擦系数和稳定性,以提高制动效果;b. 选择具有良好散热性和耐磨性的制动片材料,延长制动器的使用寿命。
2. 制动盘的设计和优化:a. 选择适当的制动盘材料,提高制动盘的强度和刚度;b. 优化制动盘的散热效果,降低制动盘的温度;c. 通过减少制动盘的质量和减小制动盘直径,降低制动器的重量。
3. 制动器液压系统的设计:a. 优化制动系统的液压传动比和制动启动压力,提高制动力的实时可调性;b. 选择高效的液压制动泵和制动器液压油,提高制动系统的快速响应性能。
4. 制动片和制动盘的接触过程模拟:a. 借助计算机仿真软件,对制动片和制动盘的接触过程进行模拟和分析;b. 通过优化制动片和制动盘的表面形状和接触压力分布,提高制动器的摩擦效果和制动性能。
三、制动器的性能测试和评估为了验证优化设计方案的效果,需要进行制动器的性能测试和评估。
测试项目包括:1. 制动力和制动距离的测试;2. 制动噪音和振动的测试;3. 制动器的散热性能测试。
测试结果将用于评估设计方案的有效性,并指导后续的改进和优化。
结论:通过对紧凑型轿车盘式制动器的优化设计方案的研究,可以提高制动器的性能和可靠性。
紧凑型轿车盘式制动器设计优化方案研究

紧凑型轿车盘式制动器设计优化方案研究1. 紧凑型轿车盘式制动器介绍紧凑型轿车盘式制动器是一种常见的汽车制动系统,用于将车轮的动能转化为热能,从而实现汽车的减速和停车功能。
它由制动盘、制动钳和制动片等主要部件组成,具有结构简单、制动效果好、制动力平稳等特点。
2. 目前存在的问题然而,在使用过程中,紧凑型轿车盘式制动器也存在一些问题。
首先,制动盘和制动片之间的磨损会导致制动效果下降和噪音增加,需要定期更换制动片和研磨制动盘。
其次,制动片与制动盘之间的接触面积有限,对制动力的传递效率有一定的限制。
此外,制动器的散热性能也较差,长时间高速行驶时易出现制动力下降现象。
3. 设计优化方案为了解决上述问题并进一步提高紧凑型轿车盘式制动器的性能,设计优化方案如下:3.1 制动片材料优化首先,可以通过优化制动片材料来提高制动效果和耐磨性。
选择耐高温、低磨损的复合材料作为制动片的制造材料,可以延长制动片的使用寿命,降低更换频率,提高制动性能。
此外,还可以进行材料表面处理,如使用专门的涂层或纳米材料,以减少与制动盘的磨损和摩擦。
3.2 制动盘结构优化同时,可以对制动盘的结构进行优化设计。
采用更加均匀的通风孔设计,增强制动盘的散热性能,减少长时间高速行驶时的制动力下降情况。
此外,通过优化制动盘的形状和尺寸,可以增加制动盘与制动片之间的接触面积,提高制动力的传递效率。
3.3 制动钳结构优化制动钳作为制动器的核心部件之一,其结构也可以进行优化。
采用更轻量化的材料制造制动钳,可以减轻整个制动系统的重量,提高车辆的燃油经济性。
此外,通过优化制动钳的刚度和几何形状,可以提高制动器的响应速度,使制动效果更加平稳和可控。
3.4 制动系统控制策略优化最后,对于紧凑型轿车盘式制动器来说,制动系统的控制策略也是非常重要的。
采用先进的传感器和电子控制单元,实现对制动器工作状态的实时监测和控制,可以根据不同的行驶条件调整制动力和制动盘温度,以提供更加精确和可靠的制动效果,同时减少制动器的磨损和能量损失。
制动盘优化设计原稿

交通与汽车工程学院课程论文说明书课程名称: 车辆工程专业科技创新实践活动课程代码: 3510429 题目: 制动盘优化设计年级/专业/班: 2011级/车辆工程/汽设一班学生姓名:学号: 6117开始时间: 2014 年 03 月 18 日完成时间: 2014 年 05 月 25 日课程论文成绩:学习态度及平时成绩(30)技术水平与实际能力(20)创新(5)说明书(计算书、图纸、分析报告)撰写质量(45)总分(100)指导教师签名:年月日前言 01汽车刹车盘国外研究现状与目标 01.1国外研究现状 01.2国研究现状 (2)2制动盘组织分析与性能要求 (2)3制动盘温升对摩擦系数的影响 (2)4制动盘直径D (3)5制动盘厚度h (3)6 制动盘常存在的问题 (3)6.1气孔 (3)6.2缩松 (4)6.3砂眼缺陷 (4)7制动盘catia图形 (4)结论 (7)致 (8)参考文献 (8)前言汽车的设计与生产涉及到许多领域,其独有的安全性、经济性、舒适性等众多指标,也对设计提出了更高的要求。
汽车制动系统是汽车行驶的一个重要主动安全系统,其性能的好坏对汽车的行驶安全有着重要影响。
本次设计的主要容就是运输车辆中的制动器,目前广泛使用的是摩擦式制动器,摩擦式制动器就其摩擦副的结构形式可分成鼓式、盘式和带式三种。
其中盘式制动器较为广泛。
盘式制动器有着制动效果更好,不易受外界条件影响,且制动较平稳等优势。
1汽车刹车盘国外研究现状与目标制动盘在汽车的制动系统中发挥着至关重要的作用,性能优良的制动盘是汽车安全行驶的前提条件之一。
虽然经过多年的应用与发展,但是从早期的石棉制动盘到目前广泛使用的铸铁制动盘,在环保、质量等方面都存在一些缺陷,并不能完全满足市场需求。
汽车产业的迅猛发展,汽车产量的大幅度增加,降低能源消耗、加强环境保护对汽车用材料轻量化的要求,迫使人们不停的开展对汽车制动盘的研究。
1.1国外研究现状国外早期的制动盘是用石棉纤维填充酚醛树脂制造而成的,其中石棉由硅酸盐矿物质得,含有一定数量的结晶水。
汽车盘式制动器优化设计

表 2 优化前后 QY- P 型盘式制动器结构参数的对比
D( mm) H ( mm) A p( mm2) R1 ( mm)
优化前 295
12
29. 76
124
优化后 295
10
35. 52
119
注: A p= I b( 衬片表面积)
结果表明, 现有盘式制动器除衬片面积略小了点 外, 其余基本上 接近最优值。按最优值设计 的制动 器, 其制动性能在不同制动情况下都有改善, 高速下 制动尤为明显。
机械研究与应用 MECHANICAL RESEARCH & APPLICATION
Vol 12 No. 1 1999
化设计出的制动器尺寸大致不变, 故取下列值作为优 化设计综合结果: D = 295 mm, h= 10 mm, I = 75 mm, b= 47 mm, R 1= 119 mm。 3 2 优化前后结果对比分析( 表 2、表 3)
0. 2930 17 105( W/ m2)
( 3)
式中: s 为滑移率( s = 1. 0) , a 为制动减速度( m/ s2) , A R 为制动盘摩擦环表面积( m2) , ( A R= 2 R1 b) 。
( 2) 制动器不应出现严重的热衰退, 衬片吸收的
热流密度:
qp = 1. 41 0. 25 ( 1- s) G v0 a/ ( 2 778I b ) 0. 2930 1. 3 105( W/ m2) ( 4)
19
Vol 12 No. 1 1999
机械研究与应用 MECHANICAL RESEARCH & APPLICATION
第 12 卷 第1期
温升( ) 。 1 3 约束条件 1
毕业设计论文轿车盘式制动器设计及优化

轿车盘式制动器设计及优化摘要盘式制动器主要用于行车制动,其制动效能稳定,在汽车中得到广泛的应用。
首先通过了解制动器的设计要求,对盘式制动器进展初始设计;然后再对盘式制动器进展优化设计。
本设计通过对摩擦片的中心圆半径、摩擦片直径、制动盘的直径、活塞直径、制动盘厚度、油缸的油压等参数的优化设计,以制动时间、制动盘的厚度、制动盘的温升作为优化设计目标,建立盘式制动器的优化设计数学模型。
选用合理的优化设计方法,编写MATALB程序,通过优化程序的运行,得到最终优化结果,从而得出盘式制动器较合理的尺寸。
关键词:盘式制动器;轿车;设计;优化Design and Optimization of Disk Brake on CarABSTRACTDisc brakesare mainly used to brake when vehicle is steering.Due to stability of disk brakes, they are widely used on vehicles. First through understanding the design requirements of brake, do the initial design of disk brake;second doing the optimal design for disk brake. In this design, it optimizes the design through the optimal design of the radius of center circle of friction sheet, the diameter of friction sheet, the diameter of disc drake, the diameter of piston, the deep of dish brake, the oil pressure in oil jar and so on, andtaking the time of braking, the deep of disc brake,the temperature of disk brake as the aim of optimization, then establish the disk brake optimal design’s mathematical function model. selectinga reasonable optimal design’s tools and raddle program by MATLAB.Passing the optimal program’s operation, get the eventually optimal result, so we can conclude the reasonable dimension of disc brake.Keyboard:Disc brake; Car; Design; Optimization目录前言11 汽车制动系概述21.1 汽车制动器21.2 浮动钳式盘式制动器31.3 盘式制动器的优缺点及应用42 盘式制动器的设计52.1 制动器主要零部件的设计52.2 盘式制动器工作间隙的调整62.3 摩擦衬片〔衬块〕的磨损特性计算73 钳盘式制动器的优化设计83.1 概述83.2 建立盘式制动器优化设计的数学模型9 3.2.1 选取设计变量113.2.2 确立目标函数113.2.3 确立约束条件113.3选用适宜的算法求解123.4优化结果比拟124 完毕语125 辞13参考文献13附录A外文翻译—原文局部14附录B外文翻译—译文局部17附录C优化设计程序20前言2006年我国汽车产销量双双突破700万辆,分别到达727.97万辆和721.6万辆,同比增长27.32%和25.13%。
优化紧凑型轿车盘式制动器结构设计方案

优化紧凑型轿车盘式制动器结构设计方案紧凑型轿车盘式制动器是汽车制动系统中的重要零部件之一,在保证安全性和可靠性的基础上,优化盘式制动器的结构设计方案,可以提升制动性能、减轻重量、降低成本等方面带来一定的好处。
首先,我们可以从盘式制动器的材料选择和制造工艺方面来进行优化设计。
目前常用的盘式制动器材料有铸铁和复合材料两种。
铸铁材料制作的盘式制动器具有成本低、制造工艺简单等优势,但其刹车性能和散热性能相对较差。
相比之下,复合材料制作的盘式制动器具有重量轻、散热性能好等优点,但制造工艺较为复杂,成本较高。
因此,在优化盘式制动器结构设计方案时,可以根据车辆的使用情况和需求选择合适材料,并结合先进的制造工艺进行制作,使其既能满足制动要求,又能降低制造成本。
其次,我们可以从盘式制动器的组成部分进行优化设计。
盘式制动器主要由刹车盘、刹车夹和刹车片等组成。
刹车盘是承受刹车力的部件,在设计时需要考虑到刹车盘的厚度、直径、材料选择等因素。
优化设计可以选择合适的材料,如高强度合金材料,以提高刹车盘的耐热性和耐磨性。
同时,通过改变刹车盘的厚度和直径,可以提升制动力矩和散热能力。
刹车夹是将刹车片夹紧在刹车盘上的部件,优化设计可以优化刹车夹的结构,使其更加紧凑、轻量化,并考虑到刹车片的易更换性和维修性。
此外,在盘式制动器的结构设计中,还需要考虑到盘式制动器的散热性能。
制动时,刹车盘会受到较大的摩擦热量,如果不能及时散热,会导致刹车性能下降甚至制动失效。
因此,在优化设计过程中,应合理设计散热通道和散热片,以增加散热面积和散热能力,确保盘式制动器在高温工况下的正常工作。
可以通过优化刹车盘的内部结构,增加散热通道的数量和尺寸,进一步提升盘式制动器的散热性能。
最后,在盘式制动器的结构设计中,还需要考虑到制动力的传递和分配。
优化设计可以选择合适的刹车片材料和结构,以提高制动力的传递效果。
同时,合理设计刹车系统的衬垫和活塞等部件,以均匀地分配制动力,避免因部分区域受压不均衡导致刹车不稳定的问题。
盘式制动装置制动盘的有限元分析及优化
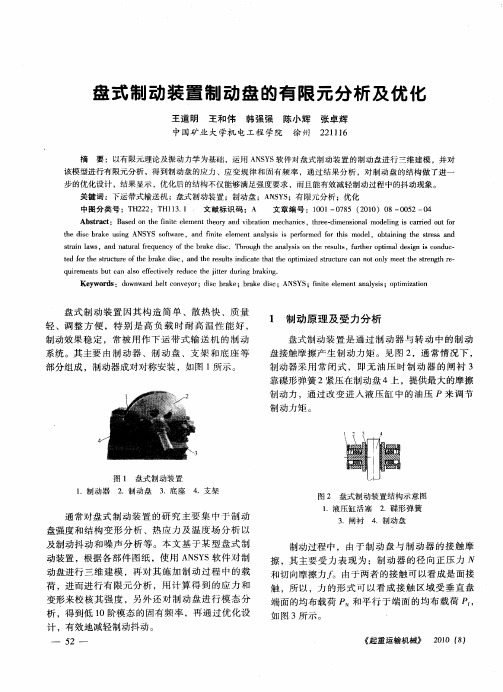
盘 式 制 动 装 置 因其 构 造 简 单 、散 热 快 、质 量
轻 、调 整 方 便 ,特 别 是 高 负 载 时 耐 高 温 性 能 好 ,
制 动效 果 稳 定 ,常 被 用 作 下 运 带 式 输 送 机 的制 动 系统 。其 主要 由制 动 器 、制 动 盘 、支 架 和 底 座 等 部 分组 成 ,制动 器成 对对 称安装 ,如 图 1所示 。
t e d s r k sn S ot a e n i i lme t a ay i i p r r d f r ti d l b an n h t s n h ic b a e u i g AN YS s f r ,a d f t ee n n lss s ef me o h s mo e ,o ti i g t e sr s a d w ne o e
和切 向摩擦 力 . 由于两 者 的接触 可 以看 成 是 面接 厂 。 触 ,所 以 ,力 的形 式 可 以看 成 接 触 区域 受 垂 直 盘
td frt esr c u eo e b a e d s ,a d t e r s l n i ae ta h p i z d sr cu ec n n to l e esr n t e e o t t r f h r k ic n h e u t i d c t t e o t h u t s h t mie t t r a o ny me t h t gh r — u t e
q i m nsb t a l f c v l rd c e ie uigba i . ur e t u c nas e et e u et t r r rkn e o f i ye h jt d n g
Ke wo d :d wn a d b l c n e o ;d s r k ;b a e d s y rs o w r e t o v y r icb a e r k ic;ANS YS;f i lme t n l ss p i z t n i t ee n ay i ;o t ne a miai o
刹车盘毕业设计范文

刹车盘毕业设计范文刹车盘是车辆刹停的重要组成部件,其设计和制造质量直接影响到汽车的制动性能、安全性和舒适性。
因此,在毕业设计中选择刹车盘为研究对象,对其进行设计和优化是非常有意义的。
刹车盘的主要功能是将车辆动能转化为热能,通过磨擦消耗掉,从而实现刹车效果。
因此,刹车盘的设计需要满足以下几个关键要求:1.热传导性能:刹车盘在长时间制动过程中会产生大量的热量,所以需要具备良好的热传导性能,能够将热量迅速传导到刹车盘整体,并通过刹车盘的表面散热出去,以保证刹车盘的温度不过高,避免热膨胀引起的失效问题。
2.抗变形性能:刹车盘在制动过程中会受到较大的负荷,因此需要具备良好的抗变形性能,能够承受大负荷下的压力和扭矩,避免产生变形导致制动效果下降。
3.制动效果:刹车盘的设计应该能够提供理想的制动效果,即能够在车辆需要紧急制动时,能够达到较短的制动距离和稳定的制动效果,确保车辆能够在最短的时间内停下来,确保驾驶者和乘客的安全。
4.安全性和舒适性:刹车盘的设计需要考虑到安全性和舒适性的需求,在制动过程中,刹车盘应该具备良好的抗褪色性能和耐久性,能够在长时间的使用中保持刹车效果不变,并且不造成刹车卡滞、噪音过大等驾驶不舒适的现象。
综上所述,在刹车盘的毕业设计中,可以从材料的选择、结构的设计和制造工艺的优化等方面展开研究。
材料的选择可以基于实验室测试和材料力学性能分析,结构的设计可以基于有限元分析和计算机模拟,制造工艺的优化可以通过优化切割工艺和热处理工艺等来提高刹车盘的性能。
最后,设计师还可以考虑发展一种刹车盘,该刹车盘可以通过传感器实时监测刹车盘的温度、压力和变形等参数,并与车辆的制动系统相连,实现自适应的制动效果。
这样的设计将进一步提高刹车盘的性能和智能化水平。
同时,设计师还可以对不同车型和用途的车辆,基于刹车盘的研究结果,开展针对性的刹车系统的设计和优化,以满足不同车型和用途需求。
基于工程原理的紧凑型轿车盘式制动器优化设计探讨

基于工程原理的紧凑型轿车盘式制动器优化设计探讨在设计紧凑型轿车盘式制动器时,工程原理是关键因素之一。
本文将探讨基于工程原理的紧凑型轿车盘式制动器的优化设计。
首先,我们应该了解盘式制动器的工作原理。
盘式制动器由刹车盘、刹车片、刹车卡钳和刹车液组成。
当驾驶员踩下制动踏板时,刹车液被推动到刹车卡钳中,使刹车片夹紧刹车盘,从而产生摩擦力,使车辆减速或停止。
在设计优化过程中,我们需要考虑以下几个方面。
首先是刹车盘材料的选择。
优质的刹车盘材料应具有良好的耐磨性、热稳定性和抗褪色性能。
常见的刹车盘材料包括铸铁、钢铁、复合材料等。
根据车辆类型和使用条件,选择合适的刹车盘材料可以提高刹车性能和寿命。
其次是刹车片材料的选择。
刹车片是刹车系统中负责产生摩擦力的部分,因此材料的选择至关重要。
常用的刹车片材料包括无机非金属材料、金属基复合材料等。
在优化设计中,应根据车辆质量、车辆类型和行驶条件等因素,选择适当的刹车片材料,以保证制动力的稳定性和耐磨性。
另外,刹车卡钳的设计也是优化过程中需要考虑的因素之一。
刹车卡钳负责夹紧刹车盘和刹车片,需要具备足够的力量和稳定性。
在优化设计中,我们可以采用轻质化设计和结构优化,以降低刹车卡钳的质量和提高其刚性。
此外,采用防尘密封设计可以减少灰尘和水分的进入,进而保护刹车片和刹车盘的使用寿命。
最后,刹车系统的液压系统也需要进行优化设计。
液压系统负责将驾驶员踩下的制动踏板力量转化为刹车盘和刹车片之间的夹紧力。
为了提高刹车性能,我们可以优化液压系统的结构,提高液压液的流量和压力,以提高刹车盘和刹车片之间的接触质量和可靠性。
总之,基于工程原理的紧凑型轿车盘式制动器的优化设计,需要考虑刹车盘材料、刹车片材料、刹车卡钳设计和液压系统结构等因素。
在优化设计过程中,我们应根据车辆类型、行驶条件和使用需求等因素,选择合适的材料和结构,以提高刹车性能和使用寿命。
通过不断的优化设计,我们可以实现紧凑型轿车盘式制动器在安全性、舒适性和可靠性等方面的全面提升。
基于制动尖叫倾向性的盘式制动器优化设计

38机械设计与制造MachineryDesign&Manufacture第11期2008年11月文章编号:1001—3997(2008)l1-0038--02基于制动尖叫倾向性的盘式制动器优化设计王朝阳郭永进(上海交通大学车辆工程,上海200240)TheoptimizationdesignofthediscbrakesystembasedonthebrakesquealpropensityWANGZhao-yang,GUOYong-jin(ShanghaiJiaotongUniversity,AutomobileEngineering,Shanghai200240,China)中图分类号:THl2,U463文献标识码:A1引言随着人们对车辆舒适性和环保要求的不断提高,制动噪声问题越来越突出,受到r仓qp界的广泛关注。
现在通常的解决方法是从试验和仿真分析人手,对制动尖叫问题研究从而提出抑制制动尖叫方案。
然而由于是事后诊断,产品的结构形状、尺寸、丁艺已确定,修改没计空I'开J的自由度已大大减少,这大大限制了T程人员的发挥。
理想的方法是在制动器的早期设汁巾考虑制动噪声问题使得噪声抑制在甲.期设计阶段。
本文将就这一问题进行探讨,使制动器的制动尖叫倾向性在产品的‘}期设计中纳入考虑范围,通过CAE结构优化技术指导产品的设计,从而实现在产品早期没计阶段抑制噪声的发生。
AndrzejBajer,VladimirBelsky等考虑制动器的摩擦阻尼、非线性因素等,通过复特征值分析对制动尖叫进行了预测,预测结果与试验结果有很好的一致性【l】。
手登封、王玉为等则针对一个有制动尖叫的钳盘式制动器,在半消声室内制动器试验台L进行制动尖叫声试验,fEd时建立了基于接触摩擦耦合的有限元模刑进行了仿真,测最统计结果与仿真预测结果基本吻合,也证明r利用有限元仿真技术能够较好的预测制动器发生制动尖叫的倾向闭。
这些研究成果使得通过有限元技术在产品开发初期将制动器的制动尖叫倾向性纳入考虑范围从而指导产品设计成为可能。
- 1、下载文档前请自行甄别文档内容的完整性,平台不提供额外的编辑、内容补充、找答案等附加服务。
- 2、"仅部分预览"的文档,不可在线预览部分如存在完整性等问题,可反馈申请退款(可完整预览的文档不适用该条件!)。
- 3、如文档侵犯您的权益,请联系客服反馈,我们会尽快为您处理(人工客服工作时间:9:00-18:30)。
交通与汽车工程学院课程论文说明书课程名称: 车辆工程专业科技创新实践活动课程代码: 3510429 题目: 制动盘优化设计年级/专业/班: 2011级/车辆工程/汽设一班学生姓名: 刘陈学号: 312011********* 开始时间: 2014 年 03 月 18 日完成时间: 2014 年 05 月 25 日课程论文成绩:学习态度及平时成绩(30)技术水平与实际能力(20)创新(5)说明书(计算书、图纸、分析报告)撰写质量(45)总分(100)指导教师签名:年月日前言 (1)1汽车刹车盘国内外研究现状与目标 (1)1.1国外研究现状 (1)1.2国内研究现状 (2)2制动盘组织分析与性能要求 (2)3制动盘温升对摩擦系数的影响 (3)4制动盘直径D (3)5制动盘厚度h (3)6 制动盘常存在的问题 (4)6.1气孔 (4)6.2缩松 (4)6.3砂眼缺陷 (4)7制动盘catia图形 (4)结论 (7)致谢 (7)参考文献 (8)前言汽车的设计与生产涉及到许多领域,其独有的安全性、经济性、舒适性等众多指标,也对设计提出了更高的要求。
汽车制动系统是汽车行驶的一个重要主动安全系统,其性能的好坏对汽车的行驶安全有着重要影响。
本次设计的主要内容就是运输车辆中的制动器,目前广泛使用的是摩擦式制动器,摩擦式制动器就其摩擦副的结构形式可分成鼓式、盘式和带式三种。
其中盘式制动器较为广泛。
盘式制动器有着制动效果更好,不易受外界条件影响,且制动较平稳等优势。
1汽车刹车盘国内外研究现状与目标制动盘在汽车的制动系统中发挥着至关重要的作用,性能优良的制动盘是汽车安全行驶的前提条件之一。
虽然经过多年的应用与发展,但是从早期的石棉制动盘到目前广泛使用的铸铁制动盘,在环保、质量等方面都存在一些缺陷,并不能完全满足市场需求。
汽车产业的迅猛发展,汽车产量的大幅度增加,降低能源消耗、加强环境保护对汽车用材料轻量化的要求,迫使人们不停的开展对汽车制动盘的研究。
1.1国外研究现状国外早期的制动盘是用石棉纤维填充酚醛树脂制造而成的,其中石棉由硅酸盐矿物质得,含有一定数量的结晶水。
由于强制制动时制动盘表面瞬间温度可达到500到600摄氏度,所含的结晶水快速遗失,往往造成制动盘制动性能发生热衰退,同时制动盘自身磨损,再加上石棉在加工、使用中其粉尘具有致癌作用,因此石棉制动盘渐渐被禁用。
从20世纪60年代开始,美、欧、日等国家大面积推广使用的第二代刹车盘是半金属石墨复合材料制造的一。
其主要成分是钢纤维、石墨、金属粉及其辅料,用改性酚醛树腊粘结成型。
半金属刹车盘比石棉刹车盘耐磨性提高25%以上,摩擦系数高、导热性好加工易成型。
同时,这种刹车盘也出现钢纤维在潮湿环境中易生锈、刹车时噪音大等缺点。
后来,由于铸铁具有一定的强度和良好的耐磨性,材料和制造成本都较低,长期以来一直是汽车刹车盘使用的材料。
为了提高铸铁的强度和耐热性,避免使用过程中的“热裂”,在铸铁中加入Ni、Cu、Mo、Cr等合金元素。
世界各国所采用刹车盘铸铁材料各有不同。
英、美等国主要用高碳低合金铸铁(C>7.36%,Si<1.5%,含Mo、Cu或Ni等元素);前苏联则采用Cr、Ni、Mo的合金铸铁,其碳含量为3.2%~3.5%,硅含量为1.9%~2.5%。
蠕墨铸铁具有良好的热疲劳抗力,因此国外在80年代中后期对其在制动器上的应用开始了研究。
近十多年来,用金属基复合材料制造汽车刹车盘的报道很多。
在材料方面,1986年开始用真空搅拌混合专利技术生产可重熔的颗粒增强铝基复合材料铸锭,铸锭重熔后,采用砂型、金属型、熔模、消失模、压铸、挤压铸造等工艺生产形状复杂、表面光洁、尺寸精确的高质量铸件。
研究表明,含25%SiC的铝基复合材料,其模量、强度、导热性都明显优于HT200,而重量减轻50%~60%。
SiC颗粒能明显提高基体的耐磨性能。
相比研究,复合材料的耐磨性明显优于基体合金,也优于铸铁。
研究“表明颗粒增强铝基复合材料刹车盘的主要优点是可使重量比铸铁件减少50%~60%,减小了惯性力,增加了制动的加速度,以致减少刹车距离。
1.2国内研究现状由于国内汽车发展较晚,对制动盘的着手程度也比不上国外,其中对铸铁的研究比较多,而有关铝基复合材料刹车盘的报道很少见到。
从国内外汽车刹车盘的研究与使用现状及发展趋势来看,铝基复合材料汽车刹车盘是今后的主要发展方向,同时,国内的研究与国外的研究相比,差距较大。
很有必要开展这项研究工作。
2制动盘组织分析与性能要求制动盘及其材料不仅要求高的安全可靠性,即足够的强度和刚度、好的耐磨性能和耐热疲劳性能,还要求一定的摩擦制动性能,即摩擦系数高而稳定,受速度和环境变化的影响小,保证列车在任何条件下以一定的减速度并在规定的制动距离内停车。
此外,特别是随着高速列车的发展,减轻列车重量,尤其是减少列车的簧下质量(如制动盘的重量),改善列车的运行品质,降低运营成本,已经成为高速列车的重要技术问题之一。
3制动盘温升对摩擦系数的影响在轿车高速运行或较长坡路的制动情况下,铸铁制动盘因制动摩擦发热而使其表面温度高达700℃,这一温度远远高于一般铝合金的熔点。
然而,大量试验数据表明,SiC颗粒增强铝基复合材料的导热系数约为HT250铸铁的四倍,比热约为HT250铸铁的2倍,因而在制动过程中复合材料制动盘的表面温升低于铸铁制动盘。
当然这还与制动盘的大小尺寸,实心、空心有关。
4制动盘直径D制动盘直径D应尽可能取大些,这时制动盘的有效半径得到增加,可以降低制动钳的夹紧力,减少衬块的单位压力和工作温度。
受轮辋直径的限制,制动盘的直径通常选择为轮辋直径的70%一79%。
总质量大于2t的汽车应取上限。
根据汽车设计老师和本人查阅的资料,本次设计制动盘的直径定为320mm。
5制动盘厚度h制动盘厚度对制动盘质量和工作时的温升有影响。
为使质量小些,制动盘厚度不宜取得很大;为了降低温度,制动盘厚度又不宜取得过小。
制动盘可以做成实心的,或者为了散热通风的需要在制动盘中间铸出通风孔道。
一般实心制动盘厚度可取为10—20mm,通风式制动盘厚度取为20~50mm,采用较多的是20—30mm。
在高速运动下紧急制动, 制动盘会形成热变形, 产生颤抖。
为提高制动盘摩擦面的散热性能, 大多把制动盘做成中间空洞的通风式制动盘, 这样可使制动盘温度降低20 %~30 %。
本次设计考虑到安全可靠性,采用实心,厚度为20mm,并带有部分对称性散热小孔以达到缓解成热变形状况。
6 制动盘常存在的问题6.1气孔气孔是刹车盘铸件最常见的缺陷之一,刹车盘铸件小而壁薄,冷却、凝固速度快,发生析出性气孔和反应性气孔的可能性不大。
而合脂油粘结剂砂芯的发气量大,如果铸型水分含量高,这两个因素常常会导致铸件产生侵入性气孔。
6.2缩松缩松缺陷在有些刹车盘生产厂家表现得比较严重。
对比不同厂家的不同生产条件发现,配料中废钢加入量大,铸件化学成分中的C、Si含量偏低,力学性能达350MPa以上),则缩松缺陷在总废品率中所占的控制得过高(个别情况下σb比例较高,组织致密度的控制难度较大。
刹车盘铸件为薄壁小件,可适当提高含量,增加石墨析出量,充分利用自补缩。
也可采用二次孕育措施,即在小包内加入0.1%-0.2%的75Si~Fe孕育剂进行瞬时孕育,提高孕育效果,促进石墨形核长大,孕育剂粒度以2-5mm为宜。
6.3砂眼缺陷个别厂家铸件砂眼缺陷较多,调研分析认为主要原因是型砂湿强度低。
由于缺少型砂检测仪器,凭经验掌握,粘土或膨润土、水等不定量,型砂的性能(水分、含泥量、透气性、湿强度、紧实率等)不稳定或不能保证。
而型砂的性能是控制刹车盘铸件的重要措施之一,这一点应该引起生产厂家的重视并设法改进完善。
在只混制面砂的情况下,控制混砂质量更为重要。
另外,采用手工模板造型时,浇注系统处的紧实度和均匀性也应得到保证,否则可能因冲砂、掉砂而造成砂眼缺陷。
7制动盘catia图形制动盘外径为320mm,凸台外径为160mm,凸台内径64mm,凸台上孔直径为20mm,制动盘上小孔的直径为6mm。
具体图形如下:图1图2图3图4图5结论汽车制动器是汽车一个重要部件,是车辆不可或缺的一部分,其中制动器设计发展到今天,其技术已经成熟,但对于我们还没有踏出校门的学生来说,其中的设计理念还是很值得我们去探讨、学习的。
盘式制动器的主要优点是:1、热稳定性较好。
因为制动摩擦衬块的尺寸不长,其工作表面的面积仅为制动盘面积的12%~6%,故散热性较好。
2、水稳定性较好。
因为制动衬块对盘的单位压力高,易将水挤出,同时在离心力的作用下沾水后也易于甩掉,再加上衬块对盘的擦拭作用,因而,出水后只需经一、二次制动即能恢复正常;而鼓式制动器则需经过十余次制动方能恢复正常制动效能。
3、制动力矩与汽车前进和后退行驶无关。
4、在输出同样大小的制动力矩的条件下,盘式制动器的质量和尺寸比鼓式要小。
5、盘式的摩擦衬块比鼓式的摩擦衬片在磨损后更易更换,结构也较简单,维修保养容易。
6、制动盘与摩擦衬块间的间隙小(0.05~0.15mm),这就缩短了油缸活塞的操作时间,并使制动驱动机构的力传动比有增大的可能。
7、制动盘的热膨胀不会像制动鼓热膨胀那样引起制动踏板行程损失,这也使间隙自动调整装置的设计可以简化。
盘式制动器的主要缺点是:制动比较粗暴。
两个粘有摩擦衬面的摩擦盘能在花键轴上来回滑动,是制动器的旋转部分。
当制动时,能在极短时间使车辆停止。
再加上压盘上球槽的倾斜角不可能无限大,所以制动不平顺。
致谢本次制动盘的优化设计主要从制动盘的材料,尺寸等方面进行优化考虑的,在制作的过程中遇到很多困难,好在学校的资源还丰富,图书馆的资料也很齐全,结合老师讲过的知识才完成了这次设计。
在此谢谢我的老师和我的学校,是他们给了我这次机会。
当然这次设计存在的问题还很多,不足之处比比皆是,我一定会再接再厉,好好学习专业知识,丰富自己,争取下次取得更好的成绩。
参考文献[1] 刘惟信.汽车设计.北京:清华大学出版社,2001:158~200[2] 张洪欣.汽车设计.北京:机械工业出版社,1981:106~126[3] 陈家瑞.汽车构造.第二版.北京:机械工业出版社,2005:40~61[4] 张文春.汽车理论.北京:机械工业出版社,2005:70~83[5] 彭文生,张志明,黄华梁.机械设计.北京:高等教育出版社,2002:96~138[6] 董宝承.汽车底盘.北京:机械工业出版社,2004:32~81[7] 陈焕江,徐双应.交通运输专业英语.北京:机械工业出版社,2002:20~30[8] 刘鸿文.简明材料力学.北京:高等教育出版社,1997:254~259[9] 陈殿云,张淑芬,杨民献.工程力学.兰州:兰州大学出版设, 2003:182~196[10] 葛志祺.简明机械零件设计手册.北京:冶金工业出版社,1985:14~16,113~115[11] 濮良贵,纪名刚.机械设计.第七版.北京:高等教育出版社,2005:109~111 387~406。