LM27953TL中文资料
明基 LK952 LK953ST 投影机用户手册说明书

保修及版权信息有限保修在正常使用和存放情况下,BenQ 对本产品的任何材料和工艺缺陷提供保修。
要求保修时必须提供有效三包卡和有效发票。
如果在保修期内发现本产品有缺陷,BenQ 唯一的义务和针对您的独家补救办法是更换任何有缺陷的部件(包括劳务费)。
当您购买的产品有任何缺陷时应立即通知经销商,以获得保修服务。
重要事项:如果客户未按照 BenQ 的书面用法说明使用本产品,将不适用上述保修。
尤其是环境湿度必须介于 10% 和 90% 之间、温度介于 0°C 和 40°C 之间、海拔高度低于 3000 米(配合高海拔模式使用),以及避免在多灰尘的环境下操作本投影机。
本保修授予您特定的法律权利,您可能还享有其它权利,具体取决于您所在的国家。
有关其它信息,请访问。
版权明基电通股份有限公司 (BenQ) 版权 © 2018。
保留所有权利。
未经明基电通有限公司事先书面许可,不得以任何形式或方式,包括电子、机械、磁性、光学、化学、手写或其它方式,对本文的任何部分进行复制、传输、转译、储存于检索系统或翻译成任何文字或电脑语言。
免责声明对于本文之任何明示或默示内容,明基电通有限公司不做任何保证,亦拒绝对任何特殊目的之商用性或适用性目的予以保证。
此外,明基电通有限公司保留修订本手册和随时修改本手册内容的权利,无需通知任何人。
*DLP、Digital Micromirror Device 和 DMD 为 T exas Instruments 之商标。
其它则分别为其各自公司或组织的版权。
专利请进入/以了解 BenQ 投影机专利范围的详情。
2 保修及版权信息目录保修及版权信息 (2)重要安全说明 (4)简介 (6)物品清单 (6)投影机外观视图 (7)控制面板 (8)控制端子 (9)遥控器 (10)安装 (12)选择位置 (12)冷却注意事项 (12)获取首选的投影图像大小 (13)吊挂投影机 (15)调节投影机位置 (16)调节投影图像 (17)连接 (18)操作 (20)启动投影机 (20)使用菜单 (21)投影机安全 (22)切换输入信号 (23)关闭投影机 (23)菜单操作 (24)图片菜单 (24)显示菜单 (28)安装菜单 (29)系统设置:基本菜单 (31)系统设置:高级菜单 (31)信息菜单 (32)维护 (33)维护投影机 (33)光源信息 (34)LED 指示灯 (35)故障排除 (36)规格 (37)投影机规格 (37)外形尺寸 (38)时序表 (39)RS232 命令 (44)目录3重要安全说明您的投影机经过设计和测试,符合最新信息技术设备的安全标准。
CAT9532YI-T2;CAT9532HV6I-GT2;CAT9532WI-T1;中文规格书,Datasheet资料

CAT953216-bit Programmable LED Dimmer with I2C Interface DescriptionThe CAT9532 is a CMOS device that provides 16−bit parallel input/output port expander optimized for LED dimming control. The CAT9532 outputs can drive directly 16 LEDs in parallel. Each individual LED may be turned ON, OFF, or blinking at one of two programmable rates. The device provides a simple solution for dimming LEDs in 256 brightness steps for backlight and color mixing applications. The CAT9532 is suitable in I2C and SMBus compatible applications where it is necessary to limit the bus traffic or free−up the bus master’s timer.The CAT9532 contains an internal oscillator and two PWM signals that drive the LED outputs. The user can program the period and duty cycle for each individual PWM signal. After the initial set−up command to program the Blink Rate 1 and Blink Rate 2 (frequency and duty cycle), only one command from the bus master is required to turn each individual open drain output ON, OFF, or cycle at Blink Rate1 or Blink Rate 2. Each open drain LED output can provide a maximum output current of 25 mA. The total current sunk by all I/Os must not exceed 200 mA.Features•16 LED Drivers with Dimming Control•256 Brightness Steps•16 Open Drain Outputs Drive 25 mA Each•2 Selectable Programmable Blink Rates:– Frequency: 0.593 Hz to 152 Hz– Duty Cycle: 0% to 99.6%•I/Os can be Used as GPIOs•400 kHz I2C Bus Compatible•2.3 V to 5.5 V Operation•5 V Tolerant I/Os•Active Low Reset Input•24−Lead SOIC, TSSOP and 24−pad TQFN (4 x 4 mm) Packages •These Devices are Pb−Free, Halogen Free/BFR Free and are RoHS CompliantApplications•Backlighting•RGB Color Mixing•Sensors Control•Power Switches, Push−buttons•Alarm SystemsSOIC−24W SUFFIXCASE 751BKTSSOP−24Y SUFFIXCASE 948ARTQFN−24HV6 SUFFIXCASE 510AGTQFN−24HT6 SUFFIXCASE 510ANSee detailed ordering and shipping information in the package dimensions section on page 16 of this data sheet.ORDERING INFORMATIONMARKING DIAGRAMSA = Assembly LocationB = Product Revision (Fixed as “B”)CAT9532Y = Device Code I = Temperature Range 3= Matte-Tin Lead Finish Y = Production Year (Last Digit)M = Production Month (1−9, O, N, D)XXX = Last Three Digits ofAssembly Lot NumberA = Assembly Location 3= Matte −Tin Lead FinishB = Product Revision (Fixed as “B”)CAT9532W = Device Code I = Industrial Temperature Range Y = Production Year (Last Digit)M = Production Month (1−9, O, N, D)XXXX = Last Four Digits ofAssembly Lot NumberHHHH= Device Code LAAC = HV6 MAAC = HT6A = Assembly Location XXX = Last Three Digits of Assembly Lot NumberY = Production Year (Last Digit)M = Production Month (1−9, O, N, D)CC= Country Code TH = Thailand MY = MalaysiaABCAT9532YI 3YMXXXA3BCAT9532WI HHHH AXXX YMCC TQFN (HV6, HT6)TSSOP (Y)SOIC (W)3YMXXXFigure 1. Pin ConfigurationsRESET LED15LED14LED13LED12LED11LED0LED1LED2LED3LED4LED5A 2A 1A 0V C CS D AS C LL E D 6L E D 7V S SL E D 8L E D 9L E D 10SOIC (W), TSSOP (Y)(Top View)TQFN (HV6, HT6)(Top View)RESET LED15LED14LED13LED12LED11LED10LED9LED8SCL SDA V CC 1LED7V SSLED5LED6LED3LED4LED1LED2A2LED0A0A11Figure 2. Typical Application CircuitTable 1. PIN DESCRIPTIONDIP / SOIC / TSSOPTQFN Pin NameFunction122A0 Address Input 0223A1 Address Input 1324A2 Address Input 24−111−8LED0 − LED7LED Driver Output 0 to 7, I/O Port 0 to 7129V SSGround13−2010−17LED8 − LED15LED Driver Output 8 to 15, I/O Port 8 to 152118RESET Reset Input 2219SCL Serial Clock 2320SDASerial Data 2421V CCPower SupplyFigure 3. Block DiagramTable 2. ABSOLUTE MAXIMUM RATINGSParametersRatings Units V CC with Respect to Ground−2.0 to +7.0V Voltage on Any Pin with Respect to Ground −0.5 to +5.5V DC Current on I/Os ±25mA Supply Current200mA Package Power Dissipation Capability (T A = 25°C) 1.0W Junction Temperature +150°C Storage Temperature−65 to +150°C Lead Soldering Temperature (10 seconds)300°C Operating Ambient Temperature−40 to +85°CStresses exceeding Maximum Ratings may damage the device. Maximum Ratings are stress ratings only. Functional operation above the Recommended Operating Conditions is not implied. Extended exposure to stresses above the Recommended Operating Conditions may affect device reliability.Table 3. D.C. OPERATING CHARACTERISTICS (V CC = 2.3 to 5.5 V, V SS = 0 V; T A = −40°C to +85°C, unless otherwise specified) Symbol Parameter Conditions Min Typ Max Unit SUPPLIESV CC Supply Voltage 2.3− 5.5V−250550m AI CC Supply Current Operating mode; V CC = 5.5 V; no load;f SCL = 100 kHzI stb Standby Current Standby mode; V CC = 5.5 V; no load;− 2.1 5.0m AV I = V SS or V CC, f SCL = 0 kHz−−2mA ΔI stb Additional Standby Current Standby mode; V CC = 5.5 V; everyLED I/O = V IN = 4.3 V, f SCL = 0 kHz− 1.5 2.2VV POR (Note 1)Power−on Reset Voltage V CC = 3.3 V, No load;V I = V CC or V SSSCL, SDA, RESETV IL (Note 2)Low Level Input Voltage−0.5−0.3 V CC VV IH (Note 2)High Level Input Voltage0.7 V CC− 5.5VI OL Low Level Output Current V OL = 0.4 V3−−mAI IL Leakage Current V I = V CC = V SS−1−+1m AC I (Note 3)Input Capacitance V I = V SS−−6pFC O (Note 3)Output Capacitance V O = V SS−−8pFA0, A1, A2V IL (Note 2)Low Level Input Voltage−0.5−0.8VV IH (Note 2)High Level Input Voltage 2.0− 5.5VI IL Input Leakage Current−1−1m AI/OsV IL (Note 2)Low Level Input Voltage−0.5−0.8VV IH (Note 2)High Level Input Voltage 2.0− 5.5VI OL (Note 4)Low Level Output Current V OL = 0.4 V; V CC = 2.3 V9−−mAV OL = 0.4 V; V CC = 3.0 V12−−V OL = 0.4 V; V CC = 5.0 V15−−V OL = 0.7 V; V CC = 2.3 V15−−V OL = 0.7 V; V CC = 3.0 V20−−V OL = 0.7 V; V CC = 5.0 V25−−I IL Input Leakage Current V CC = 3.6 V; V I = V SS or V CC−1−1m AC I/O (Note 3)Input/Output Capacitance−−8pF1.V DD must be lowered to 0.2 V in order to reset the device.2.V IL min and V IH max are reference values only and are not tested.3.This parameter is characterized initially and after a design or process change that affects the parameter. Not 100% tested.4.The output current must be limited to a maximum 25 mA per each I/O; the total current sunk by all I/O must be limited to 200 mA (or 100mAfor eight I/Os)Table 4. A.C. CHARACTERISTICS (V CC = 2.3 V to 5.5 V, T A = −40°C to +85°C, unless otherwise specified) (Note 5)Symbol ParameterStandard I 2CFast I 2CUnits MinMax MinMax F SCL Clock Frequency100400kHz t HD:STA START Condition Hold Time 40.6m s t LOW Low Period of SCL Clock 4.7 1.3m s t HIGH High Period of SCL Clock 40.6m s t SU:STA START Condition Setup Time 4.70.6m s t HD:DAT Data In Hold Time 00m s t SU:DAT Data In Setup Time 250100ns t R (Note 6) SDA and SCL Rise Time 1000300ns t F (Note 6) SDA and SCL Fall Time 300300ns t SU:STO STOP Condition Setup Time40.6m s t BUF (Note 6)Bus Free Time Between STOP and START 4.71.3m s t AA SCL Low to Data Out Valid 3.50.9m s t DH Data Out Hold Time10050ns T i (Note 6) Noise Pulse Filtered at SCL and SDA Inputs100100nsPORT TIMINGt PV Output Data Valid 200ns t PS Input Data Setup Time 100ns t PHInput Data Hold Time1m sRESETt W (Note 6)Reset Pulse Width 10ns t RECReset Recovery Time 0ns t RESET (Note 7)Time to Reset400ns5.Test conditions according to “AC Test Conditions” table.6.This parameter is characterized initially and after a design or process change that affects the parameter. Not 100% tested.7.The full delay to reset the part will be the sum of t RESET and the RC time constant of the SDA line.Table 5. AC TEST CONDITIONSInput Pulse Voltage 0.2 V CC to 0.8 V CC Input Rise and Fall Times ≤5 nsInput Reference Voltage 0.3 V CC , 0.7 V CC Output Reference Voltage 0.5 V CCOutput LoadCurrent source: I OL = 3 mA; 400 pF for f SCL(max) = 400 kHz Figure 4. 2−Wire Serial Interface TimingSCLSDA INSDA OUTPin DescriptionSCL: Serial ClockThe serial clock input clocks all data transferred into or out of the device. The SCL line requires a pull −up resistor if it is driven by an open drain output.SDA: Serial Data/AddressThe bidirectional serial data/address pin is used to transfer all data into and out of the device. The SDA pin is an open drain output and can be wire −ORed with other open drain or open collector outputs. A pull −up resistor must be connected from SDA line to V CC .LED0 to LED15: LED Driver Outputs / General Purpose I/OsThe pins are open drain outputs used to drive directly LEDs. Any of these pins can be programmed to drive the LED ON, OFF, Blink Rate1 or Blink Rate2. When not used for controlling the LEDs, these pins may be used as general purpose parallel input/output.RESET: External Reset InputActive low Reset input is used to initialize the CAT9532internal registers and the I 2C state machine. The internal registers are held in their default state while Reset input is active. An external pull −up resistor of maximum 25 k W is required when this pin is not actively driven.Functional DescriptionThe CAT9532 is a 16−bit I/O bus expander that provides a programmable LED dimmer, controlled through an I 2C compatible serial interface.The CAT9532 supports the I 2C Bus data transmission protocol. This Inter −Integrated Circuit Bus protocol defines any device that sends data to the bus to be a transmitter and any device receiving data to be a receiver. The transfer is controlled by the Master device which generates the serial clock and all START and STOP conditions for bus access.The CAT9532 operates as a Slave device. Both the Master device and Slave device can operate as either transmitter orreceiver, but the Master device controls which mode is activated.I 2C Bus ProtocolThe features of the I 2C bus protocol are defined as follows:1.Data transfer may be initiated only when the bus is not busy.2.During a data transfer, the data line must remain stable whenever the clock line is high. Anychanges in the data line while the clock line is high will be interpreted as a START or STOP condition (Figure 5).START and STOP ConditionsThe START Condition precedes all commands to the device, and is defined as a HIGH to LOW transition of SDA when SCL is HIGH. The CAT9532 monitors the SDA and SCL lines and will not respond until this condition is met.A LOW to HIGH transition of SDA when SCL is HIGH determines the STOP condition. All operations must end with a STOP condition.Device AddressingAfter the bus Master sends a START condition, a slave address byte is required to enable the CA T9532 for a read or write operation. The four most significant bits of the slave address are fixed as binary 1100 (Figure 6). The CAT9532uses the next three bits as address bits.The address bits A2, A1 and A0 are used to select which device is accessed from maximum eight devices on the same bus. These bits must compare to their hardwired input pins.The 8th bit following the 7−bit slave address is the R/W bit that specifies whether a read or write operation is to be performed. When this bit is set to “1”, a read operation is initiated, and when set to “0”, a write operation is selected.Following the START condition and the slave address byte,the CA T9532 monitors the bus and responds with an acknowledge (on the SDA line) when its address matches the transmitted slave address. The CA T9532 then performs a read or a write operation depending on the state of the R/W bit.Figure 5. Start/Stop TimingSTART CONDITIONSDASTOP CONDITIONSCLFigure 6. CAT9532 Slave AddressHARDWARE SELECTABLEAcknowledgeAfter a successful data transfer, each receiving device is required to generate an acknowledge. The acknowledging device pulls down the SDA line during the ninth clock cycle,signaling that it received the 8 bits of data. The SDA line remains stable LOW during the HIGH period of the acknowledge related clock pulse (Figure 7).The CAT9532 responds with an acknowledge after receiving a START condition and its slave address. If the device has been selected along with a write operation, it responds with an acknowledge after receiving each 8− bit byte.When the CAT9532 begins a READ mode it transmits 8bits of data, releases the SDA line, and monitors the line for an acknowledge. Once it receives this acknowledge, the CAT9532 will continue to transmit data. If no acknowledge is sent by the Master, the device terminates data transmission and waits for a STOP condition. The master must then issuea stop condition to return the CA T9532 to the standby power mode and place the device in a known state.Registers and Bus TransactionsAfter the successful acknowledgement of the slave address, the bus master will send a command byte to the CAT9532 which will be stored in the Control Register. The format of the Control Register is shown in Figure 8.The Control Register acts as a pointer to determine which register will be written or read. The four least significant bits, B0, B1, B2, B3, are used to select which internal register is accessed, according to the Table 6.If the auto increment flag (AI) is set, the four least significant bits of the Control Register are automatically incremented after a read or write operation. This allows the user to access the CAT9532 internal registers sequentially.The content of these bits will rollover to “0000” after the last register is accessed.Table 6. INTERNAL REGISTERS SELECTIONB3B2B1B0Register NameType Register Function0000INPUT0READ Input Register 00001INPUT1READ Input Register 10010PSC0READ/WRITE Frequency Prescaler 00011PWM0READ/WRITE PWM Register 00100PSC1READ/WRITE Frequency Prescaler 10101PWM1READ/WRITE PWM Register 10110LS0READ/WRITE LED 0−3 Selector 0111LS1READ/WRITE LED 4−7 Selector 1000LS2READ/WRITE LED 8−11 Selector 11LS3READ/WRITELED 12−15 SelectorFigure 7. Acknowledge TimingACKNOWLEDGESTARTSCL FROM MASTERDATA OUTPUTFROM TRANSMITTERDATA OUTPUT FROM RECEIVERFigure 8. Control RegisterThe Input Register 0 and Input Register 1 reflect the incoming logic levels of the I/O pins, regardless of whether the pin is defined as an input or an output. These registers are read only ports. Writes to the input registers will be acknowledged but will have no effect.Table 7. INPUT REGISTER 0 AND INPUT REGISTER 1INPUT0LED 7LED 6LED 5LED 4LED 3LED 2LED 1LED 0 bit76543210 default X X X X X X X X INPUT1LED 15LED 14LED 13LED 12LED 11LED 10LED 9LED 8 bit76543210 default X X X X X X X XThe Frequency Prescaler 0 and Frequency Prescaler 1 registers (PSC0, PSC1) are used to program the period of the pulse width modulated signals BLINK0 and BLINK1 respectively:T_BLINK0 = (PSC0 + 1) / 152;T_BLINK1 = (PSC1 + 1) / 152Table 8. FREQUENCY PRESCALER 0 AND FREQUENCY PRESCALER 1 REGISTERSPSC0bit76543210 default00000000 PSC1bit76543210 default00000000 The PWM Register 0 and PWM Register 1 (PWM0, PWM1) are used to program the duty cycle of BLINK0 and BLINK1 respectively:Duty Cycle_BLINK0 = PWM0 / 256;Duty Cycle_BLINK1 = PWM1 / 256After writing to the PWM0/1 register an 8−bit internal counter starts to count from 0 to 255. The outputs are low (LED on) when the counter value is less than the value programmed into PWM register. The LED is off when the counter value is higher than the value written into PWM register.Table 9. PWM REGISTER 0 AND PWM REGISTER 1 PWM0bit76543210 default10000000 PWM1bit76543210 default10000000Every LED driver output can be programmed to one of four states, LED OFF, LED ON, LED blinks at BLINK0 rate and LED blinks at BLINK1 rate using the LED Selector Registers (Table 10).Table 10. LED SELECTOR REGISTERSLS0LED 3LED 2LED 1LED 0 bit76543210 default00000000 LS1LED 7LED 6LED 5LED 4 bit76543210 default00000000 LS2LED 11LED 10LED 9LED 8 bit76543210 default00000000 LS3LED 15LED 14LED 13LED 12 bit76543210 default00000000 The LED output (LED0 to LED15) is set by the 2 bits value from the corresponding LSx Register (x = 0 to 3):00 = LED Output set Hi−Z (LED Off – Default)01 = LED Output set LOW (LED On)10 = LED Output blinks at BLINK0 Rate11 = LED Output blinks at BLINK1 RateWrite OperationsData is transmitted to the CAT9532 registers using the write sequence shown in Figure 9.If the AI bit from the command byte is set to “1”, the CAT9532 internal registers can be written sequentially. After sending data to one register, the next data byte will be sent to the next register sequentially addressed.Read OperationsThe CAT9532 registers are read according to the timing diagrams shown in Figure 10 and Figure 11. Data from the register, defined by the command byte, will be sent serially on the SDA line.After the first byte is read, additional data bytes may be read when the auto−increment flag, AI, is set. The additional data byte will reflect the data read from the next register sequentially addressed by the (B3 B2 B1 B0) bits of the command byte.When reading Input Port Registers (Figure 11), data is clocked into the register on the failing edge of the acknowledge clock pulse. The transfer is stopped when the master will not acknowledge the data byte received and issue the STOP condition.LED Pins Used as General Purpose I/OAny LED pins not used to drive LEDs can be used as general purpose input/output, GPIO.When used as input, the user should program the corresponding LED pin to Hi−Z (“00” for the LSx register bits). The pin state can be read via the Input Register according to the sequence shown in Figure 11.For use as output, an external pull−up resistor should be connected to the pin. The value of the pull−up resistor is calculated according to the DC operating characteristics. To set the LED output high, the user has to program the output Hi−Z writing “00” into the corresponding LED Selector (LSx) register bits. The output pin is set low when the LED output is programmed low through the LSx register bits (“01” in LSx register bits).Figure 9. Write to Register Timing DiagramFigure 10. Read from Register Timing DiagramExternal Reset OperationThe CAT9532 registers and the I 2C state machine areinitialized to their default state when the RESET input is held low for a minimum of t W . The external Reset timing is shown in Figure 12.Power −On Reset OperationThe CAT9532 incorporates Power −On Reset (POR)circuitry which protects the internal logic against powering up in the wrong state. The device is in a reset state for V CC less than the internal POR threshold level (V POR ). When V CC exceeds the V POR level, the reset state is released and the CAT9532 internal state machine and registers are initialized to their default state.Figure 11. Read Input Port Register Timing DiagramFigure 12. RESET Timing DiagramSDASCLLEDxRESET分销商库存信息:ONSEMICAT9532YI-T2CAT9532HV6I-GT2CAT9532WI-T1。
LM27313
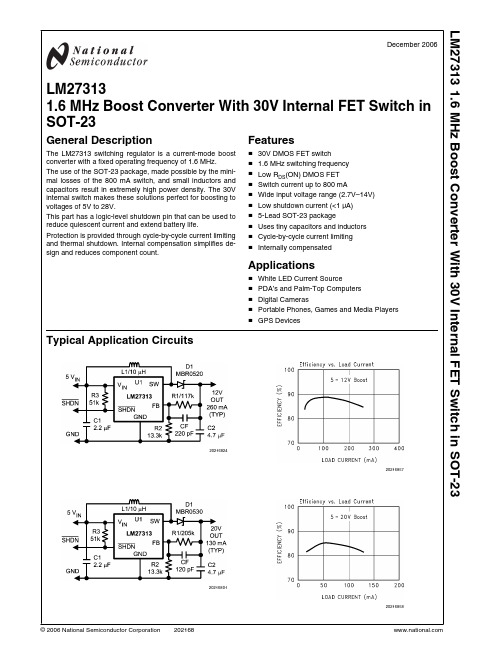
Not Switching, VSW = 5V
Min 2.7 0.80 1.5
1.205
1.15 80
Typical
1.25 500
0 0 1.230 60 2.1 400 0.024 0.02 1.6 88
Max 14
650 0.50
2 1.255
3.0 500
1
1.90
4
SHDN Shutdown control input. Connect to VIN if this feature is not used.
5
VIN
Analog and power input.
Package Marking
SRPB SRPB
2ቤተ መጻሕፍቲ ባይዱ
LM27313
Absolute Maximum Ratings (Note 1)
Features
■ 30V DMOS FET switch ■ 1.6 MHz switching frequency ■ Low RDS(ON) DMOS FET ■ Switch current up to 800 mA ■ Wide input voltage range (2.7V–14V) ■ Low shutdown current (<1 µA) ■ 5-Lead SOT-23 package ■ Uses tiny capacitors and inductors ■ Cycle-by-cycle current limiting ■ Internally compensated
General Description
The LM27313 switching regulator is a current-mode boost converter with a fixed operating frequency of 1.6 MHz.
LG LED监视器32UL950和32BL95U所有者指南说明书

* L G LED Monitor applies LCD screen with LED backlights.Please read this manual carefully before operating your set andretain it for future reference.32UL95032BL95UCopyright © 2018 LG Electronics Inc. All Rights Reserved.LICENSEEach model has different licenses. Visit for more information on the license.The terms HDMI and HDMI High-Definition Multimedia Interface,and the HDMI Logo are trademarks or registered trademarks ofHDMI Licensing Administrator, Inc. in the United States and othercountries.The SuperSpeed USB Trident logo is a registered trademark of USBImplementers Forum, Inc.Thunderbolt and the Thunderbolt logo are trademarks of IntelCorporation or its subsidiaries in the U.S. and/or other countries.*TABLE OF CONTENTSLICENSE (2)OPEN SOURCE SOFTWARE NOTICEINFORMATION (3)ASSEMBLING AND PREPARING (3)USING THE MONITOR (8)USER SETTINGS (11)TROUBLESHOOTING (23)PRODUCT SPECIFICATION (25)2OPEN SOURCE SOFTWARE NOTICE INFORMA-TIONTo obtain the source code under GPL, LGPL, MPL, and other open source licenses, that is contained in this product, please visit .In addition to the source code, all referred license terms, warranty disclaimers and copyright notices are available for download.LG Electronics will also provide open source code to you on CD-ROM for a charge covering the cost of performing such distribution (such as the cost of media, shipping, and handling) upon email request to ******************. This offer is valid for a period of three years after our last shipment of this product. This offer is valid to anyone in receipt of this information.ASSEMBLING AND PREPARINGCAUTION•Always use genuine LG components to ensure safety and product performance.•The product warranty will not cover damage or injury caused by the use of unauthorized components.•It is recommended to use the supplied components.•If you use generic cables not certified by LG, the screen may not display or there may be image problems.•Illustrations in this document represent typical procedures, so they may look different from the actual product.•Do not apply foreign substances (oils, lubricants, etc.) to the screw parts when assembling the product. (Doing so may damage the product.)•Applying excessive force when tightening screws may cause damage to the monitor. Damage caused in this way will not be covered by the product warranty.•Do not carry the monitor upside down by just holding the base. This may cause the monitor to fall off the stand and could result in personal injury.•When lifting or moving the monitor, do not touch the monitor screen. The force applied to the monitor screen may cause damage to it.NOTE•The components may look different from those illustrated here.•Without prior notice, all product information and specifications contained in this manual are subject to changeto improve the performance of the product.•To purchase optional accessories, visit an electronics store or an online shopping site, or contact the retailerfrom which you purchased the product.•The power cord provided may differ depending upon the region.Supported Drivers and Software).34How to Use the Joystick ButtonYou can easily control the functions of the monitor by pressing the joystick button or moving it left/right/up/down with your finger.Basic FunctionsNOTE•The joystick button is located at the bottom of the monitor.Moving and Lifting the MonitorWhen moving or lifting the monitor, follow these instructions to prevent the monitor from being scratched or damaged and to ensure safe transportation, regardless of its shape or size.•Place the monitor in the original box or packing material before attempting to move it. •Before moving or lifting the monitor, disconnect the power cord and all other cables. •Hold the bottom and side of the monitor frame firmly. Do not hold the panel itself.•When holding the monitor, the screen should face away from you to prevent it from being scratched. •When transporting the monitor, do not expose the monitor to shock or excessive vibration.•When moving the monitor, keep it upright and never turn the monitor on its side or tilt it sideways.CAUTION•Avoid touching the monitor screen as much as possible.-This may result in damage to the screen or some of the pixels used to create images.•If you use the monitor panel without the stand base, its joystick button may cause the monitor to become unstable and fall, resulting in damage to the monitor or human injury. In addition, this may cause the joystick button to malfunction.5ENGLISHInstalling on a Table•Lift the monitor and place it on the table in an upright position. Place the monitor at least 100 mm (3.9 inches) away from the wall to ensure sufficient ventilation.CAUTION•Unplug the power cord before moving or installing the monitor. There is risk of electric shock.•Make sure to use the power cord that is provided in the product package and connect it to a grounded power outlet.•If you need another power cord, please contact your local dealer or the nearest retail store.Adjusting the Stand Height1 Place the monitor mounted on the stand base in an upright position.2 Handle the monitor with both hands for safety.Max 110.0 mm(4.3 inches)WARNING•Adjusting the Angle1 2 experience. WARNING•To avoid injury to the fingers when adjusting the screen, do not hold the lower part of the monitor’s frame as illustrated below.•Be careful not to touch or press the screen area when adjusting the angle of the monitor.6Using the Kensington LockThe connector for the Kensington security system is located at the bottom of the monitor.For more information on installation and usage, refer to the Kensington lock owner’s manual or visit the website at .Connect the monitor to a table using the Kensington security system cable.NOTE•The Kensington security system is optional. You can obtain optional accessories from most electronics stores.Installing the Wall Mount PlateThis monitor meets the specifications for the wall mount plate or other compatible devices. NOTE•The wall mount plate is sold separately.•For more information on installation, refer to the wall mount plate’s installation guide.•Be careful not to apply too much force while mounting the wall mount plate as it may cause damage to the screen.•Remove the stand before installing the monitor on a wall mount by performing the stand attachment in reverse.Installing on the WallInstall the monitor at least 100 mm (3.9 inches) away from the wall and leave about 100 mm (3.9 inches) of space at each side of the monitor to ensure sufficient ventilation. Detailed installation instructions can be obtained from your local retail store. Alternatively, please refer to the manual for how to install and set up a tilting wall mounting bracket.7CAUTION•Unplug the power cord before moving or installing the monitor to avoid electric shock.•Installing the monitor on the ceiling or on a slanted wall may result in the monitor falling off, which could lead to injury. Use an authorized LG wall mount and contact the local dealer or qualified personnel.•Applying excessive force when tightening screws may cause damage to the monitor. Damage caused in this way will not be covered by the product warranty.•Use the wall mounting bracket and screws that conform to VESA standards. Damage caused by the use or misuse of inappropriate components will not be covered by the product warranty.•When measured from the back of the monitor, the length of each installed screw must be 8 mm (0.3 inches) or less.To install the monitor to a wall, attach a wall mounting bracket (optional) to the back of the monitor.Make sure that the wall mounting bracket is securely fixed to the monitor and to the wall.Wall Mount (mm)100 x 100Standard screw M4 x L10Number of screws4Wall Mount Plate (Optional)RW120NOTE•A non-VESA standard screw may damage the product and cause the monitor to fall. LG Electronics is not liable for any accidents relating to the use of non-standard screws.•The wall mount kit includes the installation guide and all necessary parts.•The wall mounting bracket is optional. You can obtain optional accessories from your local dealer.•The length of the screw may differ for each wall mounting bracket. If you use screws longer than the standard length, it may damage the inside of the product.•For more information, please refer to the user manual for the wall mounting bracket.USING THE MONITOR•Illustrations in this manual may differ from the actual product.Press the joystick button, go to [Settings] [Input], and then select the input option.CAUTION•Do not press the screen for a prolonged time. This may cause image distortion.•Do not display a still image on the screen for a prolonged time. This may cause image retention. Use a PC screensaver if possible.•When connecting the power cord to the outlet, use a grounded (3-hole) power strip or a grounded power outlet.•The monitor may flicker when turned on in an area where the temperature is low. This is normal.•Sometimes red, green, or blue spots may appear on the screen. This is normal. Connecting to a PC•This monitor supports the *Plug and Play feature.* Plug and Play: A feature that allows you to add a device to your computer without having to reconfigure anything or install any manual drivers.HDMI ConnectionTransmits digital video and audio signals from your PC to the monitor.CAUTION•Using a DVI to HDMI / DP (DisplayPort) to HDMI cable may cause compatibility issues.•Use a certified cable with the HDMI logo attached. If you do not use a certified HDMI cable, the screen may not display or a connection error may occur.•Recommended HDMI cable types-High-Speed HDMI®/TM cable-High-Speed HDMI®/TM cable with Ethernet DisplayPort ConnectionTransmits digital video and audio signals from your PC to the monitor.NOTE•There may be no video or audio output depending on the DP (DisplayPort) version of the PC.•Make sure to use the supplied DisplayPort cable of the product. Otherwise, this may cause the device to malfunction.•If you are using a Mini DisplayPort output graphics card, use a Mini DP to DP (Mini DisplayPort to DisplayPort) cable or gender that supports DisplayPort1.4. (Sold separately)Thunderbolt TM 3 () ConnectionYou can connect your high-resolution display or high-performance data device to the monitor via a Thunderbolt TM 3( ) port.NOTE•The maximum data transmission rate of each port is 40 Gb/s.•Make sure to use a Thunderbolt TM 3() certified cable. Otherwise, this may cause the device to malfunction.•Thunderbolt TM 3() is supported in such environments as Windows 10 and Mac product.•In accordance with Mac products may not support the recommended resolution or the some features. •The ability to set up dual monitors using the Thunderbolt TM 3() and daisy-chaining technology depends on the performance of your video card.89Connecting AV DevicesHDMI ConnectionHDMI transmits digital video and audio signals from your AV device to the monitor. NOTE•Using a DVI to HDMI / DP (DisplayPort) to HDMI cable may cause compatibility issues.•Use a certified cable with the HDMI logo attached. If you do not use a certified HDMI cable, the screen may not display or a connection error may occur. •Recommended HDMI cable types -High-Speed HDMI ®/TM cable-High-Speed HDMI ®/TM cable with EthernetConnecting PeripheralsUSB Device connectionThe USB port on the product functions as a USB hub. NOTE•It is recommended you install all Windows Updates to keep your Windows up-to-date before connecting to the product for use.•Peripheral devices are sold separately.•A keyboard, mouse, or USB device can be connected to the USB port. •The charging speed may vary depending on the device.CAUTIONCautions When Using a USB Device•A USB device with an automatic recognition program installed, or that uses its own driver, may not be recognized.•Some USB devices may not be supported or may not work properly.•It is recommended to use a USB hub or hard disk drive with power supplied. (If the power supply is not adequate, the USB device may not be recognized properly.)If you change the input on the menu while a device is in connection via the Thunderbolt TM 3 ( ) port, then the device in connection via the USB port may not work properly.[To use Thunderbolt cable]Please connect the Thunderbolt cable to the PC.To use USB 3.0, connect the Thunderbolt cable of the product to the PC.[PC][Monitor][PC][Monitor][PC][Monitor] Headphones ConnectionConnect peripherals to the monitor via the headphones port.NOTE•Peripheral devices are sold separately.•Depending on the audio settings of the PC and external device, headphones and speaker functions may belimited.•If you use angled earphones, it may cause a problem with connecting another external device to the monitor.Therefore, it is recommended to use straight earphones.(Recommend)10ENGLISHMain Menu FeaturesMenu Settings1 To view the OSD menu, press the joystick button at the bottom of the monitor and then enter the [Settings].2 Move the joystick up/down and left/right to set the options.3 To return to the upper menu or set other menu items, move the joystick to or pressing () it.4 If you want to exit the OSD menu, move the joystick tountil you exit.NOTE•: On•: OffENGLISHQuick SettingsInput[PBP]PictureNOTE•The [Picture Mode] that can be set depends on the Input signal. [[Picture Mode] on SDR (Non HDR) signal][[Picture Mode] on HDR signal]ENGLISHENGLISHGeneralENGLISH212223ENGLISHTROUBLESHOOTING2425ENGLISHPRODUCT SPECIFICATIONSpecifications are subject to change without notice.* The Operating Mode of Power Consumption is measured with LGE test standard. (Full White pattern, Maximum resolution) * The Power Consumption level can be different by operating condition and monitor setting.Factory Support Mode (Preset Mode, PC) DisplayPort/Thunderbolt TM 3/ USB-C2627ENGLISHHDMIHDMI Timing (Video)28This device can be used in all regions. Read the owner's manual (CD) carefully and keep it at hand. Please note that the label attached to the product provides information for technical support.ModelSerial No.Supplier`s Declaration of Conformity Trade Name: LGResponsible Party: LG Electronics USA, Inc. Address: 1000 Sylvan Ave Englewood Cliffs, NJ 07632 Telephon: (201) 266-2215。
稳压管大全)
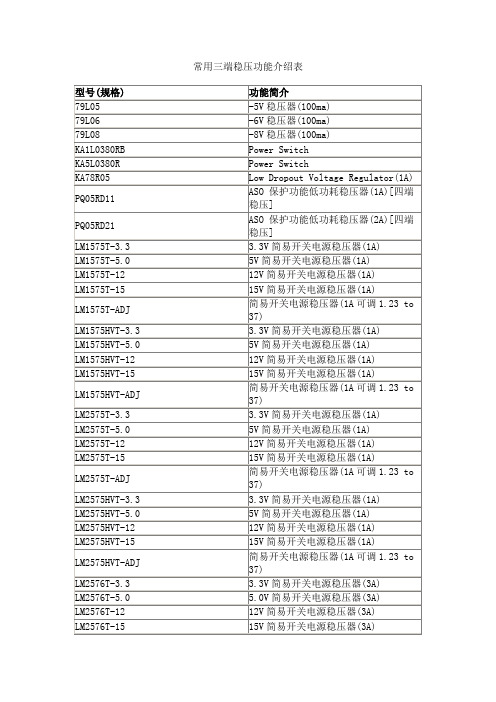
3.3V简易开关电源稳压器(1A)
LM1575T-5.0
5V简易开关电源稳压器(1A)
LM1575T-12
12V简易开关电源稳压器(1A)
LM1575T-15
15V简易开关电源稳压器(1A)
LM1575T-ADJ
简易开关电源稳压器(1A可调1.23 to 37)
LM1575HVT-3.3
LM2575HVT-ADJ
简易开关电源稳压器(1A可调1.23 to 37)
LM2576T-3.3
3.3V简易开关电源稳压器(3A)
LM2576T-5.0
5.0V简易开关电源稳压器(3A)
LM2576T-12
12V简易开关电源稳压器(3A)
LM2576T-15
15V简易开关电源稳压器(3A)
LM2576T-ADJ
79L08
-8V稳压器(100ma)
KA1L0380RB
Power Switch
KA5L0380R
Power Switch
KA78R05
Low Dropout Voltage Regulator(1A)
PQ05RD11
ASO保护功能低功耗稳压器(1A)[四端稳压]
PQ05RD21
ASO保护功能低功耗稳压器(2A)[四端稳压]
型号(规格)
功能简介
兼容型号
CA3130
高输入阻抗运算放大器
Intersil[DATA]
CA3140
高输入阻抗运算放大器
CD4573
四可编程运算放大器
MC14573
ICL7650
斩波稳零放大器
LF347(NS[DATA])
带宽四运算放大器
TLV271ID中文资料

TLV244x 2.7−10 300 † Typical values measured at 5 V, 25°C
Please be aware that an important notice concerning availability, standard warranty, and use in critical applications of Texas Instruments semiconductor products and disclaimers thereto appears at the end of this data sheet.
PRODUCTION DATA information is current as of publication date. Products conform to specifications per the terms of Texas Instruments standard warranty. Production processing does not necessarily include testing of all parameters.
SELECTION OF SIGNAL AMPLIFIER PRODUCTS† DEVICE TLV27x TLC27x TLV237x TLC227x TLV246x TLV247x VDD (V) 2.7−16 3−16 2.7−16 4−16 2.7−6 2.7−6 VIO (µV) 500 1100 500 300 150 250 Iq/Ch (µA) 550 675 550 1100 550 600 725 IIB (pA) 1 1 1 1 1300 2 1 GBW (MHz) 3 1.7 3 2.2 6.4 2.8 1.8 SR (V/µs) 2.4 3.6 2.4 3.6 1.6 1.5 1.4 SHUTDOWN — — Yes — Yes Yes — RAILTORAIL O — I/O O I/O I/O O SINGLES/DUALS/QUADS S/D/Q S/D/Q S/D/Q D/Q S/D/Q S/D/Q D/Q
L9953XP;L9953XPTR;L9953TR;L9953;中文规格书,Datasheet资料
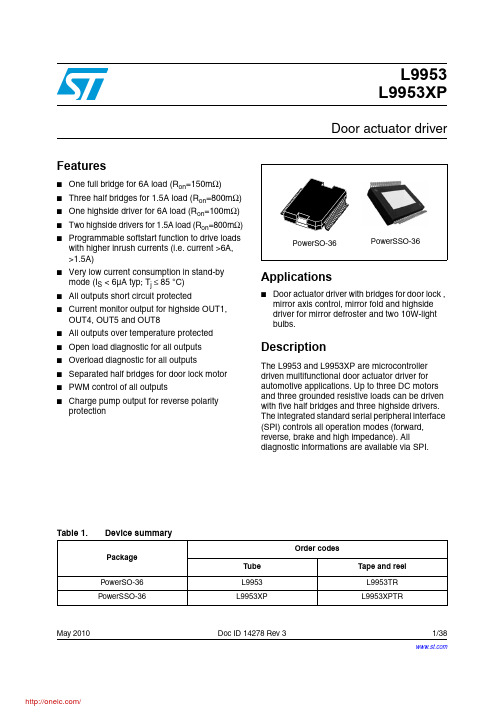
May 2010Doc ID 14278 Rev 31/38L9953L9953XPDoor actuator driverFeatures■One full bridge for 6A load (R on =150m Ω)■Three half bridges for 1.5A load (R on =800m Ω)■One highside driver for 6A load (R on =100m Ω)■Two highside drivers for 1.5A load (R on =800m Ω)■Programmable softstart function to drive loads with higher inrush currents (i.e. current >6A, >1.5A)■Very low current consumption in stand-by mode (I S < 6µA typ; T j ≤ 85 °C)■All outputs short circuit protected■Current monitor output for highside OUT1, OUT4, OUT5 and OUT8■All outputs over temperature protected ■Open load diagnostic for all outputs ■Overload diagnostic for all outputs ■Separated half bridges for door lock motor ■PWM control of all outputs■Charge pump output for reverse polarity protectionApplications■Door actuator driver with bridges for door lock , mirror axis control, mirror fold and highside driver for mirror defroster and two 10W-light bulbs.DescriptionThe L9953 and L9953XP are microcontroller driven multifunctional door actuator driver for automotive applications. Up to three DC motors and three grounded resistive loads can be driven with five half bridges and three highside drivers. The integrated standard serial peripheral interface (SPI) controls all operation modes (forward, reverse, brake and high impedance). All diagnostic informations are available via SPI.PowerSSO-36Table 1.Device summaryPackageOrder codesTubeTape and reel PowerSO-36L9953L9953TR PowerSSO-36L9953XPL9953XPTRContents L9953 / L9953XPContents1Block diagram and pin description . . . . . . . . . . . . . . . . . . . . . . . . . . . . . 62Electrical specifications . . . . . . . . . . . . . . . . . . . . . . . . . . . . . . . . . . . . . . 92.1Absolute maximum ratings . . . . . . . . . . . . . . . . . . . . . . . . . . . . . . . . . . . . . 92.2ESD protection . . . . . . . . . . . . . . . . . . . . . . . . . . . . . . . . . . . . . . . . . . . . . . 92.3Thermal data . . . . . . . . . . . . . . . . . . . . . . . . . . . . . . . . . . . . . . . . . . . . . . . 92.4Electrical characteristics . . . . . . . . . . . . . . . . . . . . . . . . . . . . . . . . . . . . . . 102.5SPI - electrical characteristics . . . . . . . . . . . . . . . . . . . . . . . . . . . . . . . . . 143Application information . . . . . . . . . . . . . . . . . . . . . . . . . . . . . . . . . . . . . 193.1Dual power supply: VS and VCC . . . . . . . . . . . . . . . . . . . . . . . . . . . . . . . 193.2Standby mode . . . . . . . . . . . . . . . . . . . . . . . . . . . . . . . . . . . . . . . . . . . . . 193.3Inductive loads . . . . . . . . . . . . . . . . . . . . . . . . . . . . . . . . . . . . . . . . . . . . . 193.4Diagnostic functions . . . . . . . . . . . . . . . . . . . . . . . . . . . . . . . . . . . . . . . . . 193.5Overvoltage and under voltage detection . . . . . . . . . . . . . . . . . . . . . . . . . 203.6Charge pump . . . . . . . . . . . . . . . . . . . . . . . . . . . . . . . . . . . . . . . . . . . . . . 203.7Temperature warning and thermal shutdown . . . . . . . . . . . . . . . . . . . . . . 203.8Open load detection . . . . . . . . . . . . . . . . . . . . . . . . . . . . . . . . . . . . . . . . . 203.9Over load detection . . . . . . . . . . . . . . . . . . . . . . . . . . . . . . . . . . . . . . . . . 203.10Current monitor . . . . . . . . . . . . . . . . . . . . . . . . . . . . . . . . . . . . . . . . . . . . 213.11PWM inputs . . . . . . . . . . . . . . . . . . . . . . . . . . . . . . . . . . . . . . . . . . . . . . . 213.12Cross-current protection . . . . . . . . . . . . . . . . . . . . . . . . . . . . . . . . . . . . . . 213.13Programmable softstart function to drive loads with higher inrush current 214Functional description of the SPI . . . . . . . . . . . . . . . . . . . . . . . . . . . . . 234.1Serial Peripheral Interface (SPI) . . . . . . . . . . . . . . . . . . . . . . . . . . . . . . . . 234.2Chip Select Not (CSN) . . . . . . . . . . . . . . . . . . . . . . . . . . . . . . . . . . . . . . . 234.3Serial Data In (DI) . . . . . . . . . . . . . . . . . . . . . . . . . . . . . . . . . . . . . . . . . . 234.4Serial Data Out (DO) . . . . . . . . . . . . . . . . . . . . . . . . . . . . . . . . . . . . . . . . 244.5Serial clock (CLK) . . . . . . . . . . . . . . . . . . . . . . . . . . . . . . . . . . . . . . . . . . . 244.6Input data register . . . . . . . . . . . . . . . . . . . . . . . . . . . . . . . . . . . . . . . . . . 244.7Status register . . . . . . . . . . . . . . . . . . . . . . . . . . . . . . . . . . . . . . . . . . . . . 24 2/38 Doc ID 14278 Rev 3L9953 / L9953XP Contents4.8Scan mode . . . . . . . . . . . . . . . . . . . . . . . . . . . . . . . . . . . . . . . . . . . . . . . . 244.9Test mode . . . . . . . . . . . . . . . . . . . . . . . . . . . . . . . . . . . . . . . . . . . . . . . . . 254.10SPI - input data and Status registers . . . . . . . . . . . . . . . . . . . . . . . . . . . . 265Packages thermal data . . . . . . . . . . . . . . . . . . . . . . . . . . . . . . . . . . . . . . 306Package and packing information . . . . . . . . . . . . . . . . . . . . . . . . . . . . . 316.1ECOP ACK® packages . . . . . . . . . . . . . . . . . . . . . . . . . . . . . . . . . . . . . . . 316.2PowerSO-36™ package information . . . . . . . . . . . . . . . . . . . . . . . . . . . . 316.3PowerSSO-36™ package information . . . . . . . . . . . . . . . . . . . . . . . . . . . 336.4PowerSO-36™ packing information . . . . . . . . . . . . . . . . . . . . . . . . . . . . . 346.5PowerSSO-36™ packing information . . . . . . . . . . . . . . . . . . . . . . . . . . . . 36 7Revision history . . . . . . . . . . . . . . . . . . . . . . . . . . . . . . . . . . . . . . . . . . . 37Doc ID 14278 Rev 33/38List of tables L9953 / L9953XP List of tablesTable 1.Device summary. . . . . . . . . . . . . . . . . . . . . . . . . . . . . . . . . . . . . . . . . . . . . . . . . . . . . . . . . . 1 Table 2.Pin definitions and functions. . . . . . . . . . . . . . . . . . . . . . . . . . . . . . . . . . . . . . . . . . . . . . . . . 6 Table 3.Absolute maximum ratings. . . . . . . . . . . . . . . . . . . . . . . . . . . . . . . . . . . . . . . . . . . . . . . . . . 9 Table 4.ESD protection . . . . . . . . . . . . . . . . . . . . . . . . . . . . . . . . . . . . . . . . . . . . . . . . . . . . . . . . . . . 9 Table 5.Operating junction temperature . . . . . . . . . . . . . . . . . . . . . . . . . . . . . . . . . . . . . . . . . . . . . . 9 Table 6.Temperature warning and thermal shutdown. . . . . . . . . . . . . . . . . . . . . . . . . . . . . . . . . . . 10 Table 7.Supply. . . . . . . . . . . . . . . . . . . . . . . . . . . . . . . . . . . . . . . . . . . . . . . . . . . . . . . . . . . . . . . . . 10 Table 8.Overvoltage and under voltage detection. . . . . . . . . . . . . . . . . . . . . . . . . . . . . . . . . . . . . . 11 Table 9.Current monitor output . . . . . . . . . . . . . . . . . . . . . . . . . . . . . . . . . . . . . . . . . . . . . . . . . . . . 11 Table 10.Charge pump output. . . . . . . . . . . . . . . . . . . . . . . . . . . . . . . . . . . . . . . . . . . . . . . . . . . . . . 11 Table 11.OUT1 - OUT8. . . . . . . . . . . . . . . . . . . . . . . . . . . . . . . . . . . . . . . . . . . . . . . . . . . . . . . . . . . 12 Table 12.Delay time from standby to active mode. . . . . . . . . . . . . . . . . . . . . . . . . . . . . . . . . . . . . . . 14 Table 13.Inputs: CSN, CLK, PWM1/2 and DI . . . . . . . . . . . . . . . . . . . . . . . . . . . . . . . . . . . . . . . . . . 14 Table 14.DI timing . . . . . . . . . . . . . . . . . . . . . . . . . . . . . . . . . . . . . . . . . . . . . . . . . . . . . . . . . . . . . . . 14 Table 15.DO . . . . . . . . . . . . . . . . . . . . . . . . . . . . . . . . . . . . . . . . . . . . . . . . . . . . . . . . . . . . . . . . . . . 15 Table 16.DO timing . . . . . . . . . . . . . . . . . . . . . . . . . . . . . . . . . . . . . . . . . . . . . . . . . . . . . . . . . . . . . . 15 Table 17.CSN timing . . . . . . . . . . . . . . . . . . . . . . . . . . . . . . . . . . . . . . . . . . . . . . . . . . . . . . . . . . . . . 15 Table 18.Test mode. . . . . . . . . . . . . . . . . . . . . . . . . . . . . . . . . . . . . . . . . . . . . . . . . . . . . . . . . . . . . . 25 Table 19.SPI - input data and Status registers 0. . . . . . . . . . . . . . . . . . . . . . . . . . . . . . . . . . . . . . . . 26 Table 20.SPI - input data and status registers 1 . . . . . . . . . . . . . . . . . . . . . . . . . . . . . . . . . . . . . . . . 28 Table 21.PowerSO-36™ mechanical data . . . . . . . . . . . . . . . . . . . . . . . . . . . . . . . . . . . . . . . . . . . . 32 Table 22.PowerSSO-36™ mechanical data . . . . . . . . . . . . . . . . . . . . . . . . . . . . . . . . . . . . . . . . . . . 33 Table 23.Document revision history . . . . . . . . . . . . . . . . . . . . . . . . . . . . . . . . . . . . . . . . . . . . . . . . . 37 4/38 Doc ID 14278 Rev 3L9953 / L9953XP List of figures List of figuresFigure 1.Block diagram. . . . . . . . . . . . . . . . . . . . . . . . . . . . . . . . . . . . . . . . . . . . . . . . . . . . . . . . . . . . 6 Figure 2.Configuration diagram (top view) . . . . . . . . . . . . . . . . . . . . . . . . . . . . . . . . . . . . . . . . . . . . . 8 Figure 3.SPI - transfer timing diagram . . . . . . . . . . . . . . . . . . . . . . . . . . . . . . . . . . . . . . . . . . . . . . . 16 Figure 4.SPI - input timing . . . . . . . . . . . . . . . . . . . . . . . . . . . . . . . . . . . . . . . . . . . . . . . . . . . . . . . . 16 Figure 5.SPI - DO valid data delay time and valid time . . . . . . . . . . . . . . . . . . . . . . . . . . . . . . . . . . 17 Figure 6.SPI - DO enable and disable time . . . . . . . . . . . . . . . . . . . . . . . . . . . . . . . . . . . . . . . . . . . 17 Figure 7.SPI - driver turn-on/off timing, minimum CSN hi time. . . . . . . . . . . . . . . . . . . . . . . . . . . . . 18 Figure 8.SPI - timing of status bit 0 (fault condition). . . . . . . . . . . . . . . . . . . . . . . . . . . . . . . . . . . . . 18 Figure 9.Example of programmable softstart function for inductive loads . . . . . . . . . . . . . . . . . . . . 22 Figure 10.Packages thermal data. . . . . . . . . . . . . . . . . . . . . . . . . . . . . . . . . . . . . . . . . . . . . . . . . . . . 30 Figure 11.PowerSO-36™ package dimensions . . . . . . . . . . . . . . . . . . . . . . . . . . . . . . . . . . . . . . . . . 31 Figure 12.PowerSSO-36™ package dimensions. . . . . . . . . . . . . . . . . . . . . . . . . . . . . . . . . . . . . . . . 33 Figure 13.PowerSO-36™tube shipment (no suffix). . . . . . . . . . . . . . . . . . . . . . . . . . . . . . . . . . . . . . 34 Figure 14.PowerSO-36™tape and reel shipment (suffix “TR”) . . . . . . . . . . . . . . . . . . . . . . . . . . . . . 35 Figure 15.PowerSSO-36™tube shipment (no suffix). . . . . . . . . . . . . . . . . . . . . . . . . . . . . . . . . . . . . 36 Figure 16.PowerSSO-36™tape and reel shipment (suffix “TR”) . . . . . . . . . . . . . . . . . . . . . . . . . . . . 36Doc ID 14278 Rev 35/38Block diagram and pin description L9953 / L9953XP6/38 Doc ID 14278 Rev 31 Block diagram and pin descriptionTable 2.Pin definitions and functionsPinSymbolFunction1, 18, 19, 36GNDGround:Reference potentialImportant: for the capability of driving the full current at the outputs all pins of GND must be externally connected.2, 35OUT8Highside driver output 8The output is built by a highside switch and is intended for resistive loads, hence the internal reverse diode from GND to the output is missing. For ESD reason a diode to GND is present but the energy which can be dissipated is limited. The highside driver is a power DMOS transistor with an internal parasitic reverse diode from the output to VS (bulk-drain-diode). The output is over-current and open load protected.Important: for the capability of driving the full current at the outputs both pins of OUT8 must be externally connected.345OUT1 OUT2OUT3Half-bridge-output 1,2,3The output is built by a highside and a lowside switch, which are internally connected. The output stage of both switches is a power DMOS transistor. Each driver has an internal parasitic reverse diode (bulk-drain-diode: highside driver from output to VS, lowside driver from GND to output). This output is over-current and open load protected.L9953 / L9953XPBlock diagram and pin descriptionDoc ID 14278 Rev 37/386, 7, 14, 15, 23, 25, 28, 32VSPower supply voltage (external reverse protection required)For this input a ceramic capacitor as close as possible to GND is recommended.Important: for the capability of driving the full current at the outputs all pins of VS must be externally connected.8DISerial data inputThe input requires CMOS logic levels and receives serial data from the microcontroller. The data is an 24bit control word and the least significant bit (LSB, bit 0) is transferred first.9CM/PWM2Current monitor output/PWM2 inputDepending on the selected multiplexer bits of Input Data Register thisoutput sources an image of the instant current through thecorresponding highside driver with a ratio of 1/10.000. This pin is bidirectional. The microcontroller can overdrive the current monitor signal to provide a second PWM input for the output OUT7.10CSNChip select not input / test modeThis input is low active and requires CMOS logic levels. The serial data transfer between L9953 and micro controller is enabled by pulling the input CSN to low level. If an input voltage of more than 7.5V is applied to CSN pin the L9953 will be switched into a test mode.11DOSerial data outputThe diagnosis data is available via the SPI and this tristate-output. The output will remain in tristate, if the chip is not selected by the input CSN (CSN = high)12VCCLogic supply voltageFor this input a ceramic capacitor as close as possible to GND is recommended.13CLKSerial clock inputThis input controls the internal shift register of the SPI and requires CMOS logic levels.16,17, 20,21,OUT4 OUT5Half-bridge-output 4,5: see OUT1 (pin 3).Important: for the capability of driving the full current at the outputs both pins of OUT4 (OUT5, respectively) must be externally connected.26CPCharge pump outputThis output is provided to drive the gate of an external n-channel power MOS used for reverse polarity protection27PWM1PWM1 input:This input signal can be used to control the drivers OUT1-OUT6 and OUT8 by an external PWM signal.Table 2.Pin definitions and functions (continued)PinSymbolFunctionBlock diagram and pin descriptionL9953 / L9953XP8/38 Doc ID 14278 Rev 33133OUT6, OUT7Highside driver output 6,7:Each output is built by a highside switch and is intended for resistive loads, hence the internal reverse diode from GND to the output is missing. For ESD reason a diode to GND is present but the energy which can be dissipated is limited. Each highside driver is a power DMOS transistor with an internal parasitic reverse diode from each output to VS (bulk-drain-diode). Each output is over-current and open load protected.22, 24, 29,30, 34NCNot connected pins.Table 2.Pin definitions and functions (continued)PinSymbolFunctionL9953 / L9953XP Electrical specificationsDoc ID 14278 Rev 39/382 Electrical specifications2.1Absolute maximum ratingsStressing the device above the rating listed in the “Absolute maximum ratings” table maycause permanent damage to the device. These are stress ratings only and operation of the device at these or any other conditions above those indicated in the operating sections of this specification is not implied. Exposure to absolute maximum rating conditions forextended periods may affect device reliability. Refer also to the STMicroelectronics SURE Program and other relevant quality document2.2 ESD protection2.3 Thermal dataTable 3.Absolute maximum ratingsSymbol ParameterValue Unit V S DC supply voltage -0.3 to28V Single pulse t max < 400ms40V V CCStabilized supply voltage, logic supply -0.3 to 5.5V V DI , V DO, V CLK , V CSN, V pwm1Digital input / output voltage -0.3 to V CC + 0.3V V CM Current monitor output -0.3 to V CC + 0.3V V CP Charge pump output -25 to V S + 11V I OUT1,2,3,6,7Output current ±5A I OUT4,5,8Output current±10ATable 4.ESD protectionParameterValue Unit All pins± 2(1)1.HBM according to MIL 883C, Method 3015.7 or EIA/JESD22-A114-A.kV Output pins: OUT1 - OUT8± 8(2)2.HBM with all unzapped pins grounded.kVTable 5.Operating junction temperatureSymbol ParameterValue Unit T jOperating junction temperature-40 to 150°CElectrical specificationsL9953 / L9953XP10/38 Doc ID 14278 Rev 32.4 Electrical characteristicsV S = 8 to 16V , V CC = 4.5 to 5.3V , T j = - 40 to 150°C, unless otherwise specified.The voltages are referred to GND and currents are assumed positive, when the currentflows into the pin.Table 6.Temperature warning and thermal shutdownSymbol ParameterMin.Typ.Max.Unit T jTW ON Temperature warning threshold junction temperatureT j 130150°C T jSD ON Thermal shutdown threshold junction temperatureT j increasing 170°C T jSD OFFThermal shutdown threshold junction temperatureT jdecreasing150°C T jSD HYS Thermal shutdown hysteresis5°KTable 7.SupplySymbol ParameterTest conditionMin.Typ.Max.Unit V SOperating supply voltage range728VI SV S DC supply currentV S = 16V , V CC = 5.3V active modeOUT1 - OUT8 floating 720mAV S quiescent supply currentV S = 16V , V CC = 0V standby modeOUT1 - OUT8 floating T test = -40°C, 25°C 412µAT test = 85°C (1)1.Guaranteed by design.625µA I CCV CC DC supply currentV S = 16V , V CC = 5.3V CSN = V CC , active mode 13mAV CC quiescent supply currentV S = 16V , V CC = 5.3V CSN = V CC standby mode OUT1 - OUT8 floating 2550µAI S + I CCSum quiescent supply currentV S = 16V , V CC = 5.3V CSN = V CC standby modeOUT1 - OUT8 floating T test = 130°C50100µA分销商库存信息:STML9953XP L9953XPTR L9953TR L9953。
LM系列芯片大全
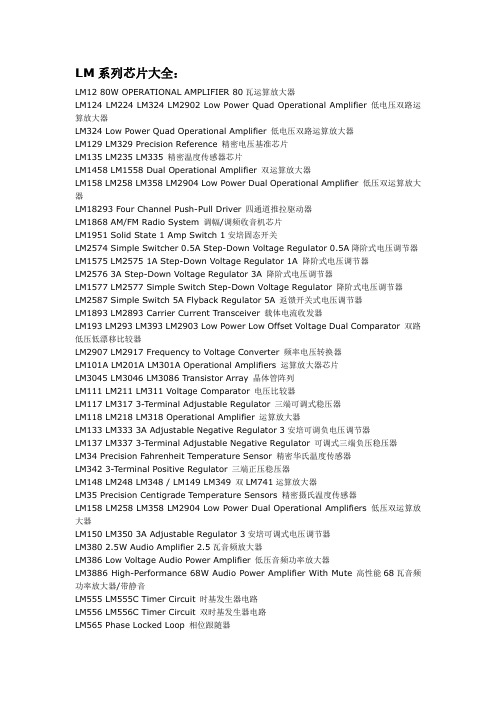
LM系列芯片大全:LM12 80W OPERATIONAL AMPLIFIER 80瓦运算放大器LM124 LM224 LM324 LM2902 Low Power Quad Operational Amplifier 低电压双路运算放大器LM324 Low Power Quad Operational Amplifier 低电压双路运算放大器LM129 LM329 Precision Reference 精密电压基准芯片LM135 LM235 LM335 精密温度传感器芯片LM1458 LM1558 Dual Operational Amplifier 双运算放大器LM158 LM258 LM358 LM2904 Low Power Dual Operational Amplifier 低压双运算放大器LM18293 Four Channel Push-Pull Driver 四通道推拉驱动器LM1868 AM/FM Radio System 调幅/调频收音机芯片LM1951 Solid State 1 Amp Switch 1安培固态开关LM2574 Simple Switcher 0.5A Step-Down Voltage Regulator 0.5A降阶式电压调节器LM1575 LM2575 1A Step-Down Voltage Regulator 1A 降阶式电压调节器LM2576 3A Step-Down Voltage Regulator 3A 降阶式电压调节器LM1577 LM2577 Simple Switch Step-Down Voltage Regulator 降阶式电压调节器LM2587 Simple Switch 5A Flyback Regulator 5A 返馈开关式电压调节器LM1893 LM2893 Carrier Current Transceiver 载体电流收发器LM193 LM293 LM393 LM2903 Low Power Low Offset Voltage Dual Comparator 双路低压低漂移比较器LM2907 LM2917 Frequency to Voltage Converter 频率电压转换器LM101A LM201A LM301A Operational Amplifiers 运算放大器芯片LM3045 LM3046 LM3086 Transistor Array 晶体管阵列LM111 LM211 LM311 Voltage Comparator 电压比较器LM117 LM317 3-Terminal Adjustable Regulator 三端可调式稳压器LM118 LM218 LM318 Operational Amplifier 运算放大器LM133 LM333 3A Adjustable Negative Regulator 3安培可调负电压调节器LM137 LM337 3-Terminal Adjustable Negative Regulator 可调式三端负压稳压器LM34 Precision Fahrenheit Temperature Sensor 精密华氏温度传感器LM342 3-Terminal Positive Regulator 三端正压稳压器LM148 LM248 LM348 / LM149 LM349 双LM741运算放大器LM35 Precision Centigrade Temperature Sensors 精密摄氏温度传感器LM158 LM258 LM358 LM2904 Low Power Dual Operational Amplifiers 低压双运算放大器LM150 LM350 3A Adjustable Regulator 3安培可调式电压调节器LM380 2.5W Audio Amplifier 2.5瓦音频放大器LM386 Low Voltage Audio Power Amplifier 低压音频功率放大器LM3886 High-Performance 68W Audio Power Amplifier With Mute 高性能68瓦音频功率放大器/带静音LM555 LM555C Timer Circuit 时基发生器电路LM556 LM556C Timer Circuit 双时基发生器电路LM565 Phase Locked Loop 相位跟随器LM567 Tone Decoder 音频译码器LM621 BrushLess Motor Commutator 无刷电机换向器LM628 LM629 Precision Motion Controller 精密位移控制器LM675 Power Operational Amplifier 功率运算放大器LM723 Voltage Regulator 电压调节器LM741 Operational Amplifier 运算放大器LM7805 LM78xx 系列稳压器LM7812 LM78xx 系列稳压器LM7815 LM78xx 系列稳压器LM78L00 3-Terminal Positive Voltage Regulator 三端正压调节器LM78L05 3-Terminal Positive Voltage Regulator 三端正压调节器LM78L09 3-Terminal Positive Voltage Regulator 三端正压调节器LM78L12 3-Terminal Positive Voltage Regulator 三端正压调节器LM78L15 3-Terminal Positive Voltage Regulator 三端正压调节器LM78L62 3-Terminal Positive Voltage Regulator 三端正压调节器LM78L82 3-Terminal Positive Voltage Regulator 三端正压调节器LM340 LM78Mxx Series 3-Terminal Positive Regulator 三端正压稳压器LM7905 3-Terminal Nagative Voltage Regulator 三端负压调节器LM7912 3-Terminal Nagative Voltage Regulator 三端负压调节器LM7915 3-Terminal Nagative Voltage Regulator 三端负压调节器LM79Mxx 3-Terminal Nagative Voltage Regulator 三端负压调节器LF147 LF347 Wide Bandwidth Quad JFET input operational amplifier 宽带J型场效应输入运算放大器LF351 Wide Bandwidth Quad JFET input operational amplifier 宽带J型场效应输入运算放大器LF353 Wide Bandwidth Quad JFET input operational amplifier 宽带J型场效应输入运算放大器LF444 Quad Low Power JFET input operational amplifier 双低压J型场效应输入运算放大器。
TLV27L1IDR中文资料

元器件交易网IMPORTANT NOTICETexas Instruments Incorporated and its subsidiaries (TI) reserve the right to make corrections, modifications,enhancements, improvements, and other changes to its products and services at any time and to discontinueany product or service without notice. Customers should obtain the latest relevant information before placingorders and should verify that such information is current and complete. All products are sold subject to TI’s termsand conditions of sale supplied at the time of order acknowledgment.TI warrants performance of its hardware products to the specifications applicable at the time of sale inaccordance with TI’s standard warranty. Testing and other quality control techniques are used to the extent TIdeems necessary to support this warranty. Except where mandated by government requirements, testing of allparameters of each product is not necessarily performed.TI assumes no liability for applications assistance or customer product design. Customers are responsible fortheir products and applications using TI components. To minimize the risks associated with customer productsand applications, customers should provide adequate design and operating safeguards.TI does not warrant or represent that any license, either express or implied, is granted under any TI patent right,copyright, mask work right, or other TI intellectual property right relating to any combination, machine, or processin which TI products or services are used. Information published by TI regarding third-party products or servicesdoes not constitute a license from TI to use such products or services or a warranty or endorsement thereof.Use of such information may require a license from a third party under the patents or other intellectual propertyof the third party, or a license from TI under the patents or other intellectual property of TI.Reproduction of information in TI data books or data sheets is permissible only if reproduction is withoutalteration and is accompanied by all associated warranties, conditions, limitations, and notices. Reproductionof this information with alteration is an unfair and deceptive business practice. TI is not responsible or liable forsuch altered documentation.Resale of TI products or services with statements different from or beyond the parameters stated by TI for thatproduct or service voids all express and any implied warranties for the associated TI product or service andis an unfair and deceptive business practice. TI is not responsible or liable for any such statements.Following are URLs where you can obtain information on other Texas Instruments products and applicationsolutions:Products ApplicationsAmplifiers Audio /audioData Converters Automotive /automotiveDSP Broadband /broadbandInterface Digital Control /digitalcontrolLogic Military /militaryPower Mgmt Optical Networking /opticalnetworkMicrocontrollers Security /securityTelephony /telephonyVideo & Imaging /videoWireless /wirelessMailing Address:Texas InstrumentsPost Office Box 655303 Dallas, Texas 75265Copyright 2003, Texas Instruments Incorporated。
L5973AD资料

1/14L5973ADDecember 20041GENERAL FEATURES■2A INTERNAL SWITCH■OPERATING INPUT VOLTAGE FROM 4.4V TO 36V ■3.3V / (±2%) REFERENCE VOLTAGE■OUTPUT VOLTAGE ADJUSTABLE FROM 1.235V TO 35V■LOW DROPOUT OPERATION: 100% DUTY CYCLE■500KHz INTERNALLY FIXED FREQUENCY ■VOLTAGE FEEDFORWARD■ZERO LOAD CURRENT OPERATION ■INTERNAL CURRENT LIMITING ■INHIBIT FOR ZERO CURRENT CONSUMPTION■SYNCHRONIZATION■PROTECTION AGAINST FEEDBACK DISCONNECTION■THERMAL SHUTDOWN1.1APPLICATIONS:■CONSUMER: STB, DVD, TV, VCR,CAR RADIO, LCD MONITORS■NETWORKING: XDSL, MODEMS,DC-DC MODULES■COMPUTER: PRINTERS, AUDIO/GRAPHIC CARDS, OPTICAL STORAGE, HARD DISK DRIVE■INDUSTRIAL: CHARGERS, CAR BATTERY DC-DC CONVERTERS2DESCRIPTIONThe L5973AD is a step down monolithic power switching regulator with a switch current limit of 2A so it is able to deliver more than 1.5A DC current to the load depending on the application conditions.The output voltage can be set from 1.235V to 35V. The high current level is also achieved thanks to an SO8 package with exposed frame, that allows to re-duce the R th(j-amb) down to approximately 40°C/W The device uses an internal P-Channel D-MOS tran-sistor (with a typical of 200m Ω) as switching element to avoid the use of bootstrap capacitor and guarantee high efficiency.An internal oscillator fixes the switching frequency at 500KHz to minimize the size of external components.Having a minimum input voltage of 4.4V only, it is particularly suitable for 5V bus, available in all com-puter related applications.Pulse by pulse current limit with the internal frequen-cy modulation offers an effective constant current short circuit protection.2A SWITCH STEP DOWN SWITCHING REGULATORFigure 2. Test and Application CircuitFigure 1. PackageTable 1. Order CodesPart Number Package L5973AD HSOP8L5973ADTRHSOP8 in Tape & ReelRev. 3L5973AD2/14Table 2. Thermal Data(*) Package mounted on boardFigure 3. Pin Connection (top view)Table 3. Pin DescriptionTable 4. Absolute Maximum RatingsSymbol ParameterValue Unit R th (j-amb)Thermal Resistance Junction to ambientMax.40 (*)°C/W Description1OUT Regulator Output.2SYNCMaster/Slave Synchronization. When it is open, a signal synchronous with the turn-off of the inter-nal power is present at the pin. When connected to an external signal at a frequency higher than the internal one, then the device is synchronized by the external signal.Connecting together the SYNC pin of two devices, the one with the higher frequency works as master and the other one, works as slave.3INHA logical signal (active high) disables the device. With IHN higher than 2.2V the device is OFF and with INH lower than 0.8V , the device is ON.If INH is not used the pin must be grounded. When it is open, an internal pull-up disables the device.4COMP E/A output to be used for frequency compensation.5FBStepdown feedback input. Connecting the output voltage directly to this pin results in an output voltage of 1.235V . An external resistor divider is required for higher output voltages (the typical value for the resistor connected between this pin and ground is 4.7K).6V REF Reference voltage of 3.3V . No filter capacitor is needed to stability.7GND Ground.8V CCUnregulated DC input voltage.Symbol ParameterValue Unit V 8Input Voltage40V V 1Output DC voltageOutput peak voltage at t = 0.1µs -1 to 40-5 to 40V VI 1Maximum output current int. limit.V 4, V 5Analog pins 4V V 3INH -0.3V to V CC V 2SYNC-0.3 to 4V P tot Power dissipation at T amb ≤ 60°C 2.25W T j Operating junction temperature range -40 to 150°C T stgStorage temperature range-55 to 150°C3/14L5973ADTable 5. Electrical Characteristics (T j = 25°C, V CC = 12V, unless otherwise specified.)Note: 1.Guaranteed by designSymbol ParameterTest ConditionMin.Typ.Max.Unit V CC Operating input voltage range V o = 1.235V; I o = 2A 4.436V R DSONMosfet on Resistance 0.2500.5ΩI l Maximum limiting current V CC = 4.4V to 36V2 2.3A f sSwitching frequency 500KHzDuty cycle100%DYNAMIC CHARACTERISTICS (see test circuit ).V 5Voltage feedback 4.4V < V CC < 36V 1.2201.235 1.25V ηEfficiencyV O = 5V, V CC = 12V90%DC CHARACTERISTICSI qop T otal Operating Quiescent Current 57mA I q Quiescent currentDuty Cycle = 0; V FB = 1.5V 2.7mA I qst-by T otal stand-by quiescent currentV inh > 2.2V 50100µA INHIBITINH Threshold VoltageDevice ON 0.8V Device OFF 2.2V ERROR AMPLIFIER V OH High level output voltage VFB = 1V 3.5VV OL Low level output voltage VFB = 1.5V0.4V I o source Source output current V COMP = 1.9V; V FB = 1V 200300µA I o sink Sink output current V COMP = 1.9V; V FB = 1.5V1 1.5mA I b Source bias current 2.54µA DC open loop gain R L = ∞5057dB gmT ransconductanceI comp = -0.1mA to 0.1mA V COMP = 1.9V 2.3mSSYNC FUNCTIONHigh Input Voltage V CC = 4.4V to 36V 2.5V REF V Low Input Voltage V CC = 4.4V to 36V 0.74V Slave Sink Current V sync = 0.74V (1)V sync = 2.33V 0.110.210.250.45mA mA Master Output Amplitude I source = 3mA2.753V Output Pulse Widthno load, V sync = 1.65V0.200.35µsREFERENCE SECTIONReference Voltage3.2343.3 3.366V I REF = 0 to 5mA V CC =4.4V to 36V3.2 3.3 3.399V Line Regulation I REF = 0mAV CC = 4.4V to 36V 510mV Load Regulation I REF = 0 to 5mA815mV Short Circuit Current101830mAL5973AD4/143FUNCTIONAL DESCRIPTIONThe main internal blocks are shown in Fig. 1, where is reported the device block diagram. They are:● A voltage regulator that supplies the internal circuitry. From this regulator, a 3.3V referencevoltage is externally available.● A voltage monitor circuit that checks the input and internal voltages.● A fully integrated sawtooth oscillator whose frequency is500KHz ●Two embedded current limitations circuitries which control the current that flows through thepower switch. The Pulse by Pulse Current Limit forces the power switch OFF cycle by cycle if the current reaches an internal threshold, while the Frequency Shifter reduces the switch-ing frequency in order to strongly reduce the duty cycle.● A transconductance error amplifier.● A pulse width modulator (PWM) comparator and the relative logic circuitry necessary to drivethe internal power.●An high side driver for the internal P-MOS switch.●An inhibit block for stand-by operation.● A circuit to realize the thermal protection function.Figure 4. Block Diagram3.1POWER SUPPLY & VOLTAGE REFERENCEThe internal regulator circuit (shown in Figure 2) consists of a start-up circuit, an internal voltage Prereg-ulator, the Bandgap voltage reference and the Bias block that provides current to all the blocks.The Starter gives the start-up currents to the whole device when the input voltage goes high and the de-vice is enabled (inhibit pin connected to ground).The Preregulator block supplies the Bandgap cell with a preregulated voltage V REG that has a very low supply voltage noise sensitivity.L5973AD3.2VOLTAGES MONITORAn internal block senses continuously the V cc, V ref and V bg. If the voltages go higher than their thresholds, the regulator starts to work. There is also an hysteresis on the V CC (UVLO).3.3OSCILLATOR & SYNCHRONIZATORFigure 6 shows the block diagram of the oscillator circuit.The Clock Generator provides the switching frequency of the device that is internally fixed at 500KHz. The frequency shifter block acts reducing the switching frequency in case of strong overcurrent or short circuit. The clock signal is then used in the internal logic circuitry and is the input of the Ramp Generator and Synchronizator blocks.The Ramp Generator circuit provides the sawtooth signal, used to realize the PWM control and the internal volt-age feed forward, while the Synchronizator circuit generates the synchronization signal. Infact the device has a synchronization pin that can works both as Master and Slave.As Master to synchronize external devices to the internal switching frequency.As Slave to synchronize itself by external signal.In particular, connecting together two devices, the one with the lower switching frequency works as Slave and the other one works as Master.To synchronize the device, the SYNC pin has to pass from a low level to a level higher than the synchronization threshold with a duty cycle that can vary approximately from 10% to 90%, depending also on the signal frequen-cy and amplitude.The frequency of the synchronization signal must be at least higher than the internal switching frequency of the device (500KHz).5/14L5973ADFigure 6. Oscillator Circuit3.4CURRENT PROTECTIONThe L5973AD has two current limit protections, pulse by pulse and frequency fold back.The schematic of the current limitation circuitry for the pulse by pulse protection is shown in figure 7.The output power PDMOS transistor is split in two parallel PDMOS. The smallest one has a resistor in series, R SENSE. The current is sensed through Rsense and if reaches the threshold, the mirror is unbalanced and the PDMOS is switched off until the next falling edge of the internal clock pulse.Due to this reduction of the ON time, the output voltage decreases.Since the minimum switch ON time (necessary to avoid false overcurrent signal) is not enough to obtain a suf-ficiently low duty cycle at 500KHz, the output current, in strong overcurrent or short circuit conditions, could in-crease again. For this reason the switching frequency is also reduced, so keeping the inductor current under its maximum threshold. The Frequency Shifter (see fig. 6) depends on the feedback voltage. As the feedback volt-age decreases (due to the reduced duty cycle), the switching frequency decreases too.6/14L5973AD3.5ERROR AMPLIFIERThe voltage error amplifier is the core of the loop regulation. It is a transconductance operational amplifier whose non inverting input is connected to the internal voltage reference (1.235V), while the inverting input (FB) is con-nected to the external divider or directly to the output voltage. The output (COMP) is connected to the external compensation network.The uncompensated error amplifier has the following characteristics:T ransconductance2300µSLow frequency gain65dBMinimum sink/source voltage1500µA/300µAOutput voltage swing0.4V/3.65VInput bias current 2.5µAThe error amplifier output is compared with the oscillator sawtooth to perform PWM control.3.6PWM COMPARATOR AND POWER STAGEThis block compares the oscillator sawtooth and the error amplifier output signals generating the PWM signal for the driving stage.The power stage is a very critical block cause it has to guarantee a correct turn on and turn off of the PD-MOS.The turn on of the power element, or better, the rise time of the current at turn on, is a very critical param-eter to compromise.At a first approach, it looks like the faster it is the rise time, the lower are the turn on losses.But there is a limit introduced by the recovery time of the recirculation diode.In fact when the current of the power element equals the inductor current, the diode turns off and the drain of the power is free to go high. But during its recovery time, the diode can be considered as an high value capacitor and this produces a very high peak current, responsible of many problems:Spikes on the device supply voltage that cause oscillations (and thus noise) due to the board parasitics. Turn on overcurrent causing a decrease of the efficiency and system reliability.Big EMI problems.Shorter freewheeling diode life.The fall time of the current during the turn off is also critical. In fact it produces voltage spikes (due to the parasitics elements of the board) that increase the voltage drop across the PDMOS.In order to minimize all these problems, a new topology of driving circuit has been used and its block dia-gram is shown in fig. 8.The basic idea is to change the current levels used to turn on and off the power switch, according with the PDMOS status and with the gate clamp status.This circuitry allow to turn off and on quickly the power switch and to manage the above question related to the freewheeling diode recovery time problem. The gate clamp is necessary to avoid that Vgs of the internal switch goes higher than Vgsmax. The ON/OFF Control block avoids any cross conduction be-tween the supply line and ground.7/14L5973AD8/143.7INHIBIT FUNCTIONThe inhibit feature allows to put in stand-by mode the device. With INH pin higher than 2.2V the device is dis-abled and the power consumption is reduced to less than 100µA. With INH pin lower than 0.8V, the device is enabled. If the INH pin is left floating, an internal pull up ensures that the voltage at the pin reaches the inhibit threshold and the device is disabled. The pin is also Vcc compatible.3.8THERMAL SHUTDOWNThe shutdown block generates a signal that turns off the power stage if the temperature of the chip goes higher than a fixed internal threshold (150°C). The sensing element of the chip is very close to the PDMOS area, so ensuring an accurate and fast temperature detection. An hysteresis of approximately 20°C avoids that the de-vices turns on and off continuously4ADDITIONAL FEATURES AND PROTECTIONS4.1FEEDBACK DISCONNECTIONIn case of feedback disconnection, the duty cycle increases versus the maximum allowed value, bringing the output voltage close to the input supply. This condition could destroy the load.To avoid this dangerous condition, the device is turned off if the feedback pin remains floating.4.2OUTPUT OVERVOLTAGE PROTECTIONThe overvoltage protection, OVP, is realized by using an internal comparator, which input is connected to the feedback, that turns off the power stage when the OVP threshold is reached. This threshold is typically 30%higher than the feedback voltage.When a voltage divider is requested for adjusting the output voltage (see test application circuit), the OVP inter-vention will be set at:Where R 1 is the resistor connected between the output voltage and the feedback pin, while R 2 is between the feedback pin and ground.V OVP 1.3R 1R 2+R 2--------------------V FB⋅⋅=L5973AD4.3ZERO LOADDue to the fact that the internal power is a PDMOS, no boostrap capacitor is required and so, the device works prop-erly also with no load at the output. In this condition it works in burst mode, with random repetition rate of the burst.4.4APPLICATION CIRCUITIn figure 9 is shown the demo board application circuit, where the input supply voltage, V cc, can range from 4.4V to 25V due to the rated voltage of the input capacitor and the output voltage is adjustable from 1.235V to V cc.Table 6. Component ListReference Part Number Description Manufacturer C110µF, 25V TOKINC2POSCAP 6TPB330M330µF, 6.3V SanyoC3C1206C221J5GAC220pF, 5%, 50V KEMETC4C1206C223K5RAC22nF, 10%, 50V KEMETR1 5.6K, 1%, 0.1W 0603NeohmR2 3.3K, 1%, 0.1W 0603NeohmR3 4.7K, 1%, 0.1W 0603NeohmD1STPS2L25U2A, 25V STL1DO3316P-15315µH, 3A COILCRAFT9/14L5973AD10/14Figure 10. Junction Temperature vs. OutputCurrentFigure 11. Junction Temperature vs Output CurrentFigure 12. Efficiency vs. Output CurrentFigure 13. Efficiency vs. Output Current5APPLICATION IDEASideas.L5973AD belongs to L597x family.Related part numbers are:●L5970D: 1.5A (I sw), 250KHz Step Down DC-DC Converter in SO8●L5972D: 2A (I sw), 250KHz Step Down DC-DC Converter in SO8●L5973D: 2.5A (I sw), 250KHz Step Down DC-DC Converter in HSOP8 In case higher current is needed, the nearest DC-DC Converter family is L497x.6PACKAGE INFORMATIONFigure 17. HSOP8 (Exposed Pad) Mechanical Data & Package Dimensions7REVISION HISTORYTable 7. Revision HistoryDate Revision Description of Changes December 20031First IssueJanuary 20042Migration to EDOCS dmsDecember 20043Added D1 & E1 dimensions in HSOP8 package information.Information furnished is believed to be accurate and reliable. However, STMicroelectronics assumes no responsibility for the consequences of use of such information nor for any infringement of patents or other rights of third parties which may result from its use. No license is granted by implication or otherwise under any patent or patent rights of STMicroelectronics. Specifications mentioned in this publication are subject to change without notice. This publication supersedes and replaces all information previously supplied. STMicroelectronics products are not authorized for use as critical components in life support devices or systems without express written approval of STMicroelectronics.The ST logo is a registered trademark of STMicroelectronics.All other names are the property of their respective owners© 2004 STMicroelectronics - All rights reservedSTMicroelectronics group of companiesAustralia - Belgium - Brazil - Canada - China - Czech Republic - Finland - France - Germany - Hong Kong - India - Israel - Italy - Japan - Malaysia - Malta - Morocco - Singapore - Spain - Sweden - Switzerland - United Kingdom - United States of America。
LM27中文资料

LM27SOT-23,±3˚C Accurate,120˚C-150˚C Factory Preset ThermostatGeneral DescriptionThe LM27is a precision,single digital-output,low-power thermostat comprised of an internal reference,DAC,tem-perature sensor and comparator.Utilizing factory program-ming,it can be manufactured with different trip points as well as different digital output functionality.The trip point (T OS )can be preset at the factory to any temperature in the range of +120˚C to +150˚C in 1˚C increments.The LM27has one digital output (OS/OS/US/US),one digital input (HYST)and one analog output (V TEMP ).The digital output stage can be preset as either open-drain or push-pull.In addition,it can be factory programmed to be active HIGH or LOW.The digital output can be factory programmed to indicate an over tem-perature shutdown event (OS or OS)or an under tempera-ture shutdown event (US or US).When preset as an over-temperature shutdown (OS)it will go LOW to indicate that the die temperature is over the internally preset T OS and go HIGH when the temperature goes below (T OS –T HYST ).Simi-larly,when preprogrammed as an undertemperature shut-down (US)it will go HIGH to indicate that the temperature is below T US and go LOW when the temperature is above (T US +T HYST ).The typical hysteresis,T HYST ,can be set to 2˚C or 10˚C and is controlled by the state of the HYST pin.A V TEMP analog output provides a voltage that is proportional to temperature and has a −10.7mV/˚C output slope.Currently,there are several standard parts available,see ordering information for details.For other part options,con-tact a National Semiconductor Distributor or Sales Repre-sentative for information on minimum order qualification.The LM27is currently available in a 5-lead SOT-23package.Applicationsn Microprocessor Thermal Management n Appliancesn Portable Battery Powered Systems n Fan Controln Industrial Process Control n HVAC SystemsnElectronic System ProtectionFeaturesn Internal comparator with pin selectable 2˚C or 10˚C hysteresisn No external components requiredn Open-drain or push-pull digital output;supports CMOS logic levelsn Internal temperature sensor with V TEMP output pin n V TEMP output allows after-assembly system testingn Internal voltage reference and DAC for trip-point setting n Currently available in 5-pin SOT-23plastic package n Excellent power supply noise rejectionKey Specificationsj Power Supply Voltage 2.7V to 5.5V j Power Supply Current 40µA(max)15µA(typ)j Hysteresis Temperature2˚C or 10˚C(typ)j Temperature Trip Point Accuracy±3˚C (max)LM27CIM5-2HJ Simplified Block Diagram and Connection Diagram20030701The LM27CIM5-2HJ has a fixed trip point of 140˚C.For other trip point and output function availability,please see ordering information or contact National Semiconductor.August 2002LM27SOT-23,±3˚C Accurate,120˚C-150˚C Factory Preset Thermostat©2002National Semiconductor Corporation Ordering InformationFor more detailed information on the suffix meaning see the part number template at the end of the Electrical Characteris-tics Section.Contact National Semiconductor for other set points and output options.Order NumberTop Mark NS Package Number Trip Point SettingOutput Function Bulk Rail 3000Units in Tape &Reel LM27CIM5-1HJ LM27CIM5X-1HJ T1HJ MA05B 130˚C Open Drain OS LM27CIM5-2HJLM27CIM5X-2HJT2HJMA05B140˚COpen Drain OSConnection Diagram20030702Pin DescriptionPin NumberPin Name FunctionConnection1HYST Hysteresis control,digital inputGND for 10˚C or V +for 2˚C 2GNDGround,connected to the back side of the die through lead frame.System GND3V TEMP Analog output voltageproportional to temperature Leave floating or connect to a high impedance node.4V +Supply input2.7V to 5.5V with a 0.1µF bypass capacitor.For PSRR information see Section Titled NOISE CONSIDERATIONS .5OSOvertemperature Shutdown open-drain active low thermostat digital output Controller interrupt,system or power supply shutdown;pull-up resistor ≥10k ΩOSOvertemperature Shutdown totem-pull active high thermostat digital output Controller interrupt,system or power supply shutdownUSUndertemperature Shutdown open-drain active low thermostat digital output System or power supply shutdown;pull-up resistor ≥10k ΩUSUndertemperature Shutdown totem-pull active high thermostat digital outputSystem or power supply shutdownNote:pin 5functionality and trip point setting are programmed during LM27manufacture.L M 27 2Absolute Maximum Ratings(Note1) Input Voltage 6.0V Input Current at any pin(Note2)5mA Package Input Current(Note2)20mA Package Dissipation at T A=25˚C(Note3)500mW Soldering InformationSOT23PackageVapor Phase(60seconds) Infrared(15seconds)215˚C220˚CStorage Temperature−65˚C to+150˚CESD Susceptibility(Note4)Human Body ModelMachine Model2500V250V Operating Ratings(Note1)Specified Temperature Range T MIN≤T A≤T MAXLM27CIM−40˚C≤T A≤+150˚CPositive Supply Voltage(V+)+2.7V to+5.5VMaximum V OUT+5.5VLM27Electrical CharacteristicsThe following specifications apply for V+=2.7V DC to5.5V DC,and V TEMP load current=0µA unless otherwise specified.Bold-face limits apply for T A=T J=T MIN to T MAX;all other limits T A=T J=25˚C unless otherwise specified.Typical LM27CIM Units Symbol Parameter Conditions(Note6)Limits(Limits)(Note7)Temperature SensorTrip Point Accuracy(IncludesV REF,DAC,Comparator Offset,and Temperature Sensitivityerrors)+120˚C<T A<+150˚C±3˚C(max)Trip Point Hysteresis HYST=GND10˚CHYST=V+2˚C V TEMP Output TemperatureSensitivity−10.82mV/˚CV TEMP Temperature Sensitivity Error to Equation:V O=(−3.552x10−6x(T−30)2+ (−10.695x10−3x(T−30))+1.8386V −30˚C≤T A≤150˚C,2.7V≤V+≤5.5V±3˚C(max)−55˚C≤T A≤150˚C,4.5V≤V+≤5.5V±3˚C(max) T A=25˚C±2.5˚C(max)V TEMP Load Regulation−1µA≤I L≤00.070mV0≤I L≤+40µA0.7mV(max) V TEMP Line Regulation+2.7V≤V+≤+5.5V,−30˚C≤T A≤+120˚C−0.2mV/VI S Supply Current152240µA(max)µA(max)Digital Output and InputI OUT(“1”)Logical“1”Output LeakageCurrent(Note9)V+=+5.0V0.0011µA(max)V OUT(“0”)Logical“0”Output Voltage I OUT=+1.2mA andV+≥2.7V;I OUT=+3.2mA andV+≥4.5V;(Note8)0.4V(max)V OUT(“1”)Logical“1”Push-Pull OutputVoltage I SOURCE=500µA,V+≥2.7V0.8x V+V(min)I SOURCE=800µA,V+≥4.5VV+−1.5V(min)V IH HYST Input Logical”1“ThresholdVoltage0.8x V+V(min)V IL HYST Input Logical”0“ThresholdVoltage0.2x V+V(max)LM273Note 1:Absolute Maximum Ratings indicate limits beyond which damage to the device may occur.Operating Ratings indicate conditions for which the device is functional,but do not guarantee specific performance limits.For guaranteed specifications and test conditions,see the Electrical Characteristics.The guaranteed specifications apply only for the test conditions listed.Some performance characteristics may degrade when the device is not operated under the listed test conditions.Note 2:When the input voltage (V I )at any pin exceeds the power supply (V I <GND or V I >V +),the current at that pin should be limited to 5mA.The 20mA maximum package input current rating limits the number of pins that can safely exceed the power supplies with an input current of 5mA to four.Under normal operating conditions the maximum current that pins 2,4or 5can handle is limited to 5mA each.Note 3:The maximum power dissipation must be derated at elevated temperatures and is dictated by T Jmax (maximum junction temperature),θJA (junction to ambient thermal resistance)and T A (ambient temperature).The maximum allowable power dissipation at any temperature is P D =(T Jmax –T A )/θJA or the number given in the Absolute Maximum Ratings,whichever is lower.For this device,T Jmax =150˚C.For this device the typical thermal resistance (θJA )of the different package types when board mounted follow:Package Type θJA SOT23-5,MA05B250˚C/WNote 4:The human body model is a 100pF capacitor discharge through a 1.5k Ωresistor into each pin.The machine model is a 200pF capacitor discharged directly into each pin.Note 5:See the URL ”/packaging/“for other recommendations and methods of soldering surface mount devices.Note 6:Typicals are at T J =T A =25˚C and represent most likely parametric norm.Note 7:Limits are guaranteed to National’s AOQL (Average Outgoing Quality Level).Note 8:Care should be taken to include the effects of self heating when setting the maximum output load current.The power dissipation of the LM27would increase by 1.28mW when I OUT =3.2mA and V OUT =0.4V.With a thermal resistance of 250˚C/W,this power dissipation would cause an increase in the die temperature of about 0.32˚C due to self heating.Self heating is not included in the trip point accuracy specification.Note 9:The 1µA limit is based on a testing limitation and does not reflect the actual performance of the part.Expect to see a doubling of the current for every 15˚C increase in temperature.For example,the 1nA typical current at 25˚C would increase to 16nA at 85˚C.Part Number TemplateThe series of digits labeled xyz in the part number LM27CIM-xyz,describe the set point value and the function of the output as follows:The place holders xy describe the set point temperature as shown in the following table.x (10x)y (1x)Temperature (˚C)-H 0-J 1-K 2-L 3-N 4-P 5-R6x (10x)y (1x)Temperature (˚C)-S 7-T 8-V 9Z -121-132-143-15The value of z describes the assignment/function of the output as shown in the following table:Active-Low/HighOpen-Drain/Push-PullOS/US Value of zDigital Output Function000J Active-Low,Open-Drain,OS output 001K Active-Low,Open-Drain,US output 110L Active-High,Push-Pull,OS output 111NActive-High,Push-Pull,US outputFor example:•the part number LM27CIM5-2SJ has T OS =147˚C,and programmed as an active-low open-drain overtemperature shutdown output.•the part number LM27CIM5-ZLN has T US =123˚C,and programmed as an active-high,push-pull undertemperature shutdown output.Active-high open-drain and active-low push-pull options are available,please contact National Semiconductor for more informa-tion.L M 27 4Functional DescriptionLM27OPTIONSThe LM27can be factory programmed to have a trip point anywhere in-between 120˚C to 150˚C.Applications HintsAFTER-ASSEMBLY PCB TESTINGThe LM27’s V TEMP output allows after-assembly PCB testing by following a simple test procedure.Simply measuring the V TEMP output voltage will verify that the LM27has been assembled properly and that its temperature sensing cir-cuitry is functional.The V TEMP output has very weak drive capability that can be overdriven by 1.5mA.Therefore,one can simply force the V TEMP voltage to cause the digital output to change state,thereby verifying that the comparator and output circuitry function after assembly.Here is a sample test procedure that can be used to test the LM27CIM5X-2HJ which has a 140˚C trip point.1.Turn on V +and measure V TEMP .Then calculate thetemperature reading of the LM27using the equation:V O =(−3.552x10−6x(T−30)2)+(−10.69576x10−3x(T−30))+1.8386V(1)or(2)2.Verify that the temperature measured in step one iswithin (±3˚C +error of reference temperature sensor)of the ambient/board temperature.The ambient/board tem-perature (reference temperature)should be measured using an extremely accurate calibrated temperature sen-sor,which is in close proximity to and mounted on the same PCB as the LM27perhaps even touching the GND lead of the LM27if possible.The LM27will sence theboard temperature not the ambient temperature (see Section Titled Mounting Considerations )3.A.Observe that OS is high.B.Drive V TEMP to ground.C.Observe that OS is now low.D.Release the V TEMP pin.E.Observe that OS is now high.4.A.Observe that OS is high.B.Drive V TEMP voltage down gradually.C.When OS goes low,note the V TEMP voltage.D.V TEMP Trig =V TEMP at OS trigger (HIGH->LOW)E.Calculate Ttrig using Equation (2).5.A.Gradually raise V TEMP until OS goes HIGH.NoteV TEMP .B.Calculate T HYST using Equation (2).V TEMP LOADINGThe V TEMP output has very weak drive capability (40µA source,1µA sink).So care should be taken when attaching circuitry to this pin.Capacitive loading may cause the V TEMP output to oscillate.Simply adding a resistor in series as shown in Figure 2will prevent oscillations from occurring.To determine the value of the resistor follow the guidelines given in Table 1.The same value resistor will work for either placement of the resistor.If an additional capacitive load is placed directly on the LM27output,rather than across C LOAD ,it should be at least a factor of 10smaller than C LOAD .20030712LM27-__J 20030713LM27-__K20030714LM27-__L20030715LM27-__NFIGURE 1.Output Pin Options Block DiagramsLM275Applications Hints(Continued)TABLE 1.Resistive compensation for capacitiveloading of V TEMPC LOAD R (Ω)≤100pF 01nF 820010nF 3000100nF 1000≥1µF430NOISE CONSIDERATIONSThe LM27has excellent power supply noise rejection.Listed below is a variety of signals used to test the LM27power supply rejection.False triggering of the output was not ob-served when these signals where coupled into the V+pin of the LM27.•square wave 400kHz,1Vp-p •square wave 2kHz,200mVp-p•sine wave 100Hz to 1MHz,200mVp-pTesting was done while maintaining the temperature of the LM27one degree centigrade way from the trip point with the output not activated.MOUNTING CONSIDERATIONSThe LM27can be applied easily in the same way as other integrated-circuit temperature sensors.It can be glued or cemented to a surface.The temperature that the LM27is sensing will be within about +0.06˚C of the surface tempera-ture to which the LM27’s leads are attached to.This presumes that the ambient air temperature is almost the same as the surface temperature;if the air temperature were much higher or lower than the surface temperature,the actual temperature measured would be at an intermediate temperature between the surface temperature and the air temperature.To ensure good thermal conductivity,the backside of the LM27die is directly attached to the GND pin (pin 2).The temperatures of the lands and traces to the other leads of the LM27will also affect the temperature that is being sensed.Alternatively,the LM27can be mounted inside a sealed-end metal tube,and can then be dipped into a bath or screwed into a threaded hole in a tank.As with any IC,the LM27and accompanying wiring and circuits must be kept insulated and dry,to avoid leakage and corrosion.This is especially true if the circuit may operate at cold temperatures where conden-sation can occur.Printed-circuit coatings and varnishes such as Humiseal and epoxy paints or dips are often used to ensure that moisture cannot corrode the LM27or its connec-tions.The junction to ambient thermal resistance (θJA )is the pa-rameter used to calculate the rise of a part’s junction tem-perature due to its power dissipation.For the LM27the equation used to calculate the rise in the die junction tem-perature is as follows:(3)where T A is the ambient temperature,V +is the power supply voltage,I Q is the quiescent current,I L_TEMP is the load current on the V TEMP output,V DO is the voltage on the digital output,and I DO is the load current on the digital output.Since the LM27’s junction temperature is the actual temperature being measured,care should be taken to minimize the load current that the LM27is required to drive.The tables shown in Figure 3summarize the thermal resis-tance for different conditions and the rise in die temperature of the LM27without any loading on V TEMP and a 10k pull-up resistor on an open-drain digital output with a 5.5V power supply.20030717a)R in series with capacitor20030718b)R in series with signal pathFIGURE 2.Resistor placement for capacitive loadingcompensation of V TEMPSOT23-5no heat sink SOT23-5small heat sink θJA (˚C/W)T J −T A (˚C)θJA (˚C/W)T J −T A (˚C)Still Air 2500.11TBD TBD Moving AirTBDTBDTBDTBDFIGURE 3.Thermal resistance (θJA )and temperaturerise due to self heating (T J −T A )L M 27 6Typical Applications20030703Note:The fan’s control pin has internal pull-up.The 10k pull-down sets a slow fan speed.When the output of the LM27goes low,the fan will speed up.FIGURE 4.Two Speed Fan Speed Control20030720FIGURE 5.Fan High Side Drive20030721FIGURE 6.Fan Low Side DriveLM277Typical Applications(Continued)20030722FIGURE 7.Audio Power Amplifier Thermal Protection20030723FIGURE 8.Simple ThermostatL M 27 8Physical Dimensionsinches (millimeters)unless otherwise noted5-Lead Molded SOT-23Plastic Package,JEDECOrder Number LM27CIM5or LM27CIM5XNS Package Number MA05BLIFE SUPPORT POLICYNATIONAL’S PRODUCTS ARE NOT AUTHORIZED FOR USE AS CRITICAL COMPONENTS IN LIFE SUPPORT DEVICES OR SYSTEMS WITHOUT THE EXPRESS WRITTEN APPROVAL OF THE PRESIDENT AND GENERAL COUNSEL OF NATIONAL SEMICONDUCTOR CORPORATION.As used herein:1.Life support devices or systems are devices or systems which,(a)are intended for surgical implant into the body,or (b)support or sustain life,and whose failure to perform when properly used in accordance with instructions for use provided in the labeling,can be reasonably expected to result in a significant injury to the user.2.A critical component is any component of a life support device or system whose failure to perform can be reasonably expected to cause the failure of the life support device or system,or to affect its safety or effectiveness.National Semiconductor Corporation AmericasEmail:support@National Semiconductor EuropeFax:+49(0)180-5308586Email:europe.support@Deutsch Tel:+49(0)6995086208English Tel:+44(0)8702402171Français Tel:+33(0)141918790National Semiconductor Asia Pacific Customer Response Group Tel:65-2544466Fax:65-2504466Email:ap.support@National Semiconductor Japan Ltd.Tel:81-3-5639-7560Fax:81-3-5639-7507LM27SOT-23,±3˚C Accurate,120˚C-150˚C Factory Preset ThermostatNational does not assume any responsibility for use of any circuitry described,no circuit patent licenses are implied and National reserves the right at any time without notice to change said circuitry and specifications.。
TLP3526中文资料

1.0
1.4
1.8
2.2
2.6
Pulse forward voltage VFP (V)
4
2002-09-25
元器件交易网
Trigger LED current IFT (arbitrary unit)
Peak off-state current IDRM (arbitrary unit)
元器件交易网
TL(Ta = 25°C)
Characteristic
Symbol
Rating
Unit
Forward current
Forward current derating (Ta ≥ 53°C)
LE D
Peak forward current (100µs pulse, 100pps)
Characteristic Trigger LED current Capacitance (input to output) Isolation resistance
Isolation voltage
Fig.1: dv / dt test circuit
Symbol IFT CS RS
BVS
Test Condition
VT = 6V VS = 0, f = 1MHz VS = 500V AC, 1 minute AC, 1 second, in oil DC, 1 minute, in oil
Min.
―
― 5×1010 2500
― ―
Typ.
―
1.5 1014 ― 5000 5000
Max. 10 ―
― ― ― ―
1 5 125 600 1.0 0.7 -14.3
853控制柜调试指导书
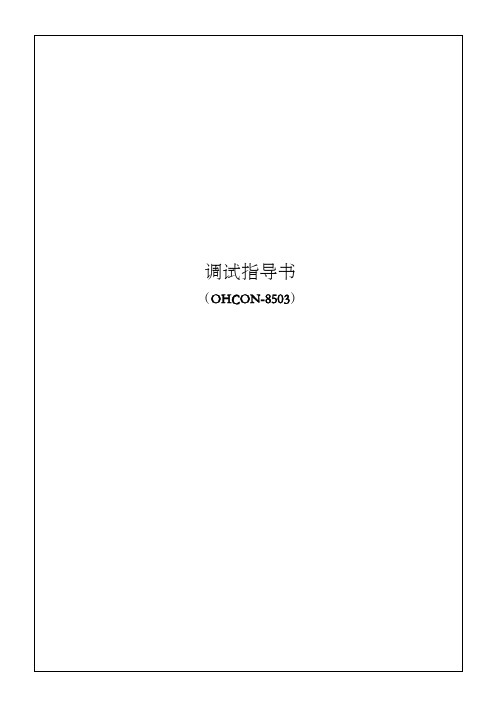
为099-100。
6.6.5. 再将载重量增加至额定载荷就可达到超载报警。
称重装置的插头端子对照表见下面表格。
6.7、舒适感调整一般情况下调整3319中的加速度、减速度及其jerk0-jerk3进行调整。
根据现场的实际情况而定,一般不调。
6.8、试外招和消防a用万用表量H4插键是否有短路,正常后插好,拨好地址码。
外召地址从21开始,一个地址一层,以此类推,按下按钮能呼到指定楼层,完毕。
b按下消防开关,电梯能返回指定楼层,且轿厢显示紧急退出,轿门一直打开,则正常。
以上结束后电梯上下反复运行几次,正常则调试完毕。
七、故障排除3.9编码器定位出厂时主机已经与控制柜进行配对试验,定位角度已经存在变频器中,如果发现主机运行异常或驱动器内参数与主机实际参数不符,则需要重新定位。
断电,将钢丝绳拨离曳引轮,短接SW-A1和BY-A1到AC110V,上电使接触器吸合,设置好驱动器参数和电机铭牌参数,将RUN SOURCE设成“0”,RUN ENABLE设成“0”。
用服务器插入SVT2,并按“M-3-3-2”并按“ENTER”键进行确认主机定位,注意:定位过程中主机将旋转(在此过程中要确认抱闸已经打开);等待服务器出现“Learning finished”表示定位完成;注意:如果电机相位更换,则需要进行重新定位,或更改成原来相位;3.10点动运行时,BY、SW不能正常吸合检查安全信号输入、输出(IO)信号是否正常,如不正常应根据原理图检查线路;如信号正常,请检查驱动器参数,参见驱动器参数表。
3.11点动运行时,接触器、抱闸继电器及抱闸正常打开,电机不转,电流很大“Drive Overload”。
可能是变频器到主机三相相序不对,应按照正确方法连接主机动力线,参见“2.6 动力线检查”。
3.12自学习运行到顶层后,电梯不能正常运行检查run enable值,应该设置成“1”,另外请检查井道信号是否正常。
3.13常见驱动器故障3.13.1驱动器“Over current”信息电流过大。
LM395T;中文规格书,Datasheet资料

LM195,LM395LM195/LM395 Ultra Reliable Power TransistorsLiterature Number: SNOSBO4BLM195/LM395Ultra Reliable Power TransistorsGeneral DescriptionThe LM195/LM395are fast,monolithic power integrated circuits with complete overload protection.These devices,which act as high gain power transistors,have included on the chip,current limiting,power limiting,and thermal over-load protection making them virtually impossible to destroy from any type of overload.In the standard TO-3transistor power package,the LM195will deliver load currents in ex-cess of 1.0A and can switch 40V in 500ns.The inclusion of thermal limiting,a feature not easily avail-able in discrete designs,provides virtually absolute protec-tion against overload.Excessive power dissipation or inad-equate heat sinking causes the thermal limiting circuitry to turn off the device preventing excessive heating.The LM195offers a significant increase in reliability as well as simplifying power circuitry.In some applications,where protection is unusually difficult,such as switching regulators,lamp or solenoid drivers where normal power dissipation is low,the LM195is especially advantageous.The LM195is easy to use and only a few precautions need be observed.Excessive collector to emitter voltage can de-stroy the LM195as with any power transistor.When the device is used as an emitter follower with low source imped-ance,it is necessary to insert a 5.0k resistor in series with the base lead to prevent possible emitter follower oscilla-tions.Although the device is usually stable as an emitter follower,the resistor eliminates the possibility of trouble with-out degrading performance.Finally,since it has good high frequency response,supply bypassing is recommended.For low-power applications (under 100mA),refer to the LP395Ultra Reliable Power Transistor.The LM195/LM395are available in the standard TO-3,Kovar TO-5,and TO-220packages.The LM195is rated for opera-tion from −55˚C to +150˚C and the LM395from 0˚C to +125˚C.Featuresn Internal thermal limitingn Greater than 1.0A output current n 3.0µA typical base current n 500ns switching time n 2.0V saturationn Base can be driven up to 40V without damage n Directly interfaces with CMOS or TTL n100%electrical burn-inSimplified Circuit006009011.0Amp Lamp Flasher00600916©2004National Semiconductor Corporation TO-3Metal Can Package 00600902Bottom ViewOrder Number LM195K/883See NS Package Number K02A(Note 5)TO-220Plastic Package00600903Case is EmitterTop ViewOrder Number LM395T See NS Package Number T03BTO-5Metal Can Package00600904Bottom ViewOrder Number LM195H/883See NS Package Number H03B(Note 5)L M 19 2please contact the National Semiconductor Sales Office/ Distributors for availability and specifications. Collector to Emitter VoltageLM19542V LM39536V Collector to Base VoltageLM19542V LM39536V Base to Emitter Voltage(Forward)LM195 LM39542V36VPower Dissipation Internally LimitedOperating Temperature RangeLM195−55˚C to+150˚CLM3950˚C to+125˚CStorage Temperature Range−65˚C to+150˚CLead Temperature(Soldering,10sec.)260˚CPreconditioning100%Burn-In In Thermal LimitElectrical Characteristics(Note2)Parameter Conditions LM195LM395UnitsMin Typ Max Min Typ MaxCollector-Emitter Operating Voltage I Q≤I C≤I MAX4236V (Note4)Base to Emitter Breakdown Voltage0≤V CE≤V CEMAX423660V Collector CurrentTO-3,TO-220V CE≤15V 1.2 2.2 1.0 2.2ATO-5V CE≤7.0V 1.2 1.8 1.0 1.8A Saturation Voltage I C≤1.0A,T A=25˚C 1.8 2.0 1.8 2.2V Base Current0≤I C≤I MAX3.0 5.0 3.010µA0≤V CE≤V CEMAXQuiescent Current(I Q)V be=02.0 5.0 2.010mA0≤V CE≤V CEMAXBase to Emitter Voltage I C=1.0A,T A=+25˚C0.90.9V Switching Time V CE=36V,R L=36Ω,500500nsT A=25˚CThermal Resistance Junction to TO-3Package(K) 2.3 3.0 2.3 3.0˚C/W Case(Note3)TO-5Package(H)12151215˚C/WTO-220Package(T)46˚C/WNote1:“Absolute Maximum Ratings”indicate limits beyond which damage to the device may occur.Operating Ratings indicate conditions for which the device is functional,but do not guarantee specific performance limits.Note2:Unless otherwise specified,these specifications apply for−55˚C≤T j≤+150˚C for the LM195and0˚C≤+125˚C for the LM395.Note3:Without a heat sink,the thermal resistance of the TO-5package is about+150˚C/W,while that of the TO-3package is+35˚C/W.Note4:Selected devices with higher breakdown available.Note5:Refer to RETS195H and RETS195K drawings of military LM195H and LM195K versions for specifications.3Collector Characteristics Short Circuit Current0060093300600934Bias Current Quiescent Current0060093500600936Base Emitter Voltage Base Current0060093700600938L M 19 4Saturation Voltage Response Time0060093900600940 Response Time10V Transfer Function006009410060090736V Transfer Function Transconductance00600908006009095Small Signal FrequencyResponse00600910Schematic Diagram0060091L M 19 61.0Amp Voltage Follower00600912*Solid TantalumPower PNP Time Delay00600913*Protects against excessive base drive**Needed for stability006009141.0MHz Oscillator0060091571.0Amp Negative Regulator00600917†Solid Tantalum1.0Amp Positive Voltage Regulator00600918†Solid TantalumL M 19 8Fast Optically Isolated Switch Optically Isolated Power Transistor0060091900600920CMOS or TTL Lamp Interface Two Terminal Current Limiter006009210060092240V Switch00600923*Drive Voltage 0V to ≥10V ≤42V6.0V Shunt Regulator with Crowbar Two Terminal 100mA Current Regulator00600924006009259分销商库存信息: NATIONAL-SEMICONDUCTOR LM395T。
lg 27mp38vq lcd 显示器 说明书

1 Adjusting the screen resolutionAdjusting the screen resolutionDue to the nature of liquid crystal display (LCD) technology, the picture resolution is always fixed. For the best display performance, please set the display to its maximum resolution that is the same with the monitor aspect ratio. This is called “Native Resolution” or maximal resolution – that is, the clearest picture. Please refer to the table below for the native resolution of your LCD. Lower resolutions are displayed on a full screen through an interpolation circuit. Image blurring across pixel boundaries can occur with the interpolated resolution depending upon the image type and its initial resolution.1. Open Display Properties and select the Settings tab.Y ou can open Display Properties by right-clicking on the Windows desktop and selecting Properties from the pop-up menu.2. Use the slider in the Screen area section to adjust the screen resolution.Select the recommended resolution (maximum resolution) then click Apply .3. Click OK then Yes .4. Close the Display Properties window.If your input source does not provide an image which is the same with the monitor aspect ratio, the displayed image may appear stretched or distorted. T o maintain the original aspect ratio, image scaling options can be found in the Display Mode adjustment. See the user manual formore information.• T o take full advantage of LCD technology you should select the native resolution setting of your PC screen as described below. Be aware that not all PC video cards provide this resolution value. If yours doesn't, check with the video card manufacturer's website for an updated driver for your particular model PC video cardwhich supports this resolution. Software video drivers are often updated and available for new hardware video resolutions. If necessary, you may need to replace and update the PC video card hardware to be able to support the native resolution of the monitor.• Depending on the operating system on your PC, different procedures should be followed to adjust the screen resolution. Refer to the help document of your operating system for details.If you select some other resolution, be aware that this other resolution is interpolated and may not accurately display the screen image as well as it could do at the native resolution setting.2Adjusting the screen refresh rate Adjusting the screen refresh rateY ou don’t have to choose the highest possible refresh rate on an LCD display, because it is not technically possible for an LCD display to flicker. The best results are obtained by using the factory modes already set in your computer. Check next chapter to see the factory modes: Preset display models on page 3.1. Double click the Display icon in Control Panel .2. From the Display Properties window, select the Settings tab and click the Advancedbutton.3. Select the Adapter tab, and select an appropriate refresh rate to match one of theapplicable factory modes as listed in the specification table.4. Click Change , OK , then Yes . 5. Close the Display Propertieswindow.Depending on the operating system on your PC, different procedures should be followed to adjust the screen resolution. Refer to the help document of your operating system for details.3 Preset display modelsPreset display models640x48060v vv vv v640x48075v v v 720x40070vvv720x48060v v v 720x57650vvv800x60060v v v 800x60075v v v 832x62475v v v 1024x76860v v v 1024x76875v v v 1152x87075vvv1280x72050vv v 1280x72060v vv vv v1280x80060v v v 1280x102460v v v 1280x102475v v v 1680x105060v v v 1600x90060vvv1920x108024v v v 1920x108025v v v 1920x108030v v v 1920x108050vv v 1920x108060v v v v v v 1920x1080100v v v v v v 1920x1080120vv vv vv 2560x144060v v v 2560x1440120vvv2560x1440144vv v • T o make sure the above timing works, check the compatibility and specifications of your graphic card first.• T o obtain the best image quality, refer to the above table to set the timing and the resolution of the input source.4Preset display modelsWQHD (2560x1440) video inputImage disruption may occur as a result of signal frequency differences from graphic cards whichdo not correspond with the usual standard. This is not, however, an error. Y ou may improve this situation by altering an automatic setting or by manually changing the phase setting and the pixel frequency from the DISPLAY menu.100120144100120144HDMI v v v v v v v v v v DisplayPort v v v v v v v v v v USB-C™ (DP Alt mode)vvvvvvvvvv100120144100120144HDMI v v v v v v v v DisplayPort v v v v v v v v v USB-C™(DP Alt mode)vvvvvvvvv100120144100120144HDMIvvvvvvvvvv100120144HDMIv (*)v (*)v (*)v (*)v (*)*: The monitor receives 12-bit data and displays 10-bit colors.6/21/19 EX2780Q。
低噪声、精密运算放大器 CBM27 数据手册说明书
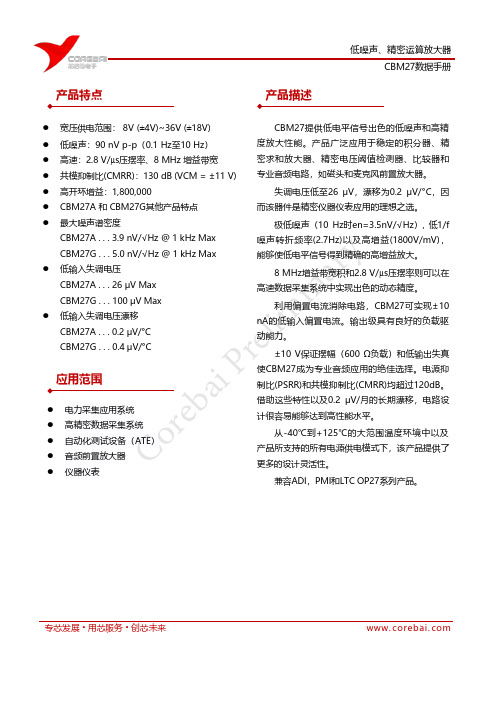
CBM27数据手册专芯发展 • 用芯服务 • 创芯未来www. corebai. com● 宽压供电范围: 8V (±4V)~36V (±18V) ● 低噪声:90 nV p-p (0.1 Hz 至10 Hz ) ● 高速:2.8 V/µs 压摆率、8 MHz 增益带宽 ● 共模抑制比(CMRR):130 dB (VCM = ±11 V) ● 高开环增益:1,800,000● CBM27A 和 CBM27G 其他产品特点 ● 最大噪声谱密度CBM27A . . . 3.9 nV/√Hz @ 1 kHz Max CBM27G . . . 5.0 nV/√Hz @ 1 kHz Max ● 低输入失调电压CBM27A . . . 26 μV Max CBM27G . . . 100 μV Max ● 低输入失调电压漂移CBM27A . . . 0.2 μV/°C CBM27G . . . 0.4 μV/°C● 电力采集应用系统● 高精密数据采集系统 ● 自动化测试设备(ATE )● 音频前置放大器 ● 仪器仪表CBM27提供低电平信号出色的低噪声和高精度放大性能。
产品广泛应用于稳定的积分器、精密求和放大器、精密电压阈值检测器、比较器和专业音频电路,如磁头和麦克风前置放大器。
失调电压低至26 μV ,漂移为0.2 μV/°C ,因而该器件是精密仪器仪表应用的理想之选。
极低噪声(10 Hz 时en=3.5nV/√Hz ), 低1/f 噪声转折频率(2.7Hz)以及高增益(1800V/mV),能够使低电平信号得到精确的高增益放大。
8 MHz 增益带宽积和2.8 V/µs 压摆率则可以在高速数据采集系统中实现出色的动态精度。
利用偏置电流消除电路,CBM27可实现±10nA 的低输入偏置电流。
输出级具有良好的负载驱动能力。
27寸屏WF2Q的规格书

CC 이기형 ( Monitor R&D 기획그룹 / 선임연구원 )손경조 ( HE 규격2그룹 / 선임연구원 )최찬용 ( Monitor 양산그룹 / 대리 )송성호 ( Monitor 회로개발그룹 / 선임연구원 )김경진 ( LCD TV 부품품질보증계 / 기사 )이상훈 ( Monitor 회로개발그룹 / 책임연구원 )김철회 ( LGEND R&D.MNT MECHANIC GROUP / 선임연구원 )허희준 ( Monitor R&D 기획그룹 / 선임연구원 )류동우 ( Monitor Module 구매그룹 / 과장 )이송화 ( Monitor Module 구매그룹 / 대리 )김영주 ( Monitor R&D 기획그룹 / 연구원 )이지수 ( Monitor Module 구매그룹 / 사원 )이연정 ( Monitor 회로개발그룹 / 연구원 )윤석재 ( Monitor 양산그룹 / 과장 )이상기 ( Monitor 기구개발그룹 / 선임연구원 )정성준 ( Monitor Module 구매그룹 / 사원 )이종수 ( Monitor 양산그룹 / 대리 )엄정훈 ( Monitor 양산그룹 / 과장 )남유조 ( Monitor Module 구매그룹 / 사원 )박경열 ( Monitor 양산그룹 / 과장 )이동규 ( Monitor Module 구매그룹 / 사원 )이재민 ( Monitor 회로개발그룹 / 수석연구원 )황동선 ( LGEND R&D.MNT S/W GROUP / 수석연구원 )김종태 ( Monitor 회로개발그룹 / 수석연구원 ) 김주만 ( Monitor NCP 회로그룹 / 수석연구원 )박일준 ( LGEIN R&D DISPLAY MECH GROUP / 수석연구원 )이명규 ( HE 규격2그룹 / 수석연구원 )배권일 ( Monitor 양산그룹 / 부장 )차상호 ( HE 규격2그룹 / 책임연구원 )윤성욱 ( HE 규격2그룹 / 책임연구원 )김명욱 ( Monitor 회로개발그룹 / 수석연구원 )박강식 ( LCD TV 부품품질보증계 / 기정 )이규호 ( LCD TV 부품품질보증계 / 기정 )박철진 ( LCD TV 부품품질보증계 / 기정 )SARWO SOVIANDY SIJABAT ( LGEIN R&D DISPLAY LCD MNT PART / sr. supervisor )pinquan zhou ( LGEND R&D.MNT MASS PRODUCTION GROUP / senior manager B )xiaodong li ( LGEND R&PONENT DEVELOPMENT GROUP / manager a )qiu Yu ( LGEND R&D.Power GROUP / manager b )xiaoyong zhang ( LGEND R&D.MNT DEVELOPMENT GROUP / manager a )jian dong ( SQA GROUP / Operator3 )ke zhu ( LGEND R&D.MNT MECHANIC GROUP / assist manager )wenxue li ( LGEND R&D.MNT PLANNING GROUP / assist manager )guozhe zheng ( LGEND PRODUCTION.Mechanical Supply Gr / manager b )jie sun ( LGEND R&D.MNT MASS PRODUCTION GROUP / officer 2 )li zhao ( LGEND R&D.MNT MASS PRODUCTION GROUP / officer 3 )hui kang ( LGEND R&PONENT DEVELOPMENT GROUP / assist manager )su yuan ( LGEND R&D.MNT PLANNING GROUP / officer 1 )yong qing ( LGEND R&D.MNT PLANNING GROUP / assist manager )fei sun ( LGEND PRODUCTION.MATERIAL GROUP / Operator2 )EDMS Doc LinkAttached Local FilesCAS_LM270WF2-TLA5.pdfIIS_LM270WF2-TLA5.pdfCAS_LM270WF2-TLA6.pdf IIS_LM270WF2-TLA6.pdfSafety.zipTest report.zipKPL & MCS.zip LM270WF2-TLA5 3D Drawing.zipProduct Specification 1/ 31Liquid Crystal Display Ver 1.0Dec. 13. 2010SPECIFICATIONFORAPPROVAL( ) Preliminary Specification(●) Final Specification27”Full HD TFT LCD TitleMODEL BUYERLM270WF2*MODELTLA5SUFFIX LG Display Co., Ltd.SUPPLIER *When you obtain standard approval,please use the above model name without suffixLG Electronics Please return 1 copy for your confirmation with your signature and comments.///SIGNATURE DATE APPROVED BYJ.H PARK / G.ManagerMNT Products Engineering Dept.LG Display Co., Ltd.APPROVED BY SIGNATURE DATE REVIEWED BYPREPARED BYJ.H. SONG / Manager [C]H.C. JUNG / EngineerD.H. Kang / Manager [P]S.Y. AN / Manager [M]Liquid Crystal DisplayContents 28ENVIRONMENT 7-319VLCD POWER DIP CONDITION 3-7179INTERFACE CONNECTIONS 3-2COLOR INPUT DATA REFERNECE 3-529DESIGNATION OF LOT MARK 8-129PACKING FORM 8-229PACKING 830PRECAUTIONS 928EMC 7-21COVER2CONTENTS3RECORD OF REVISIONS4GENERAL DESCRIPTION 15ABSOLUTE MAXIMUM RATINGS 26ELECTRICAL SPECIFICATIONS 36ELECTRICAL CHARACTREISTICS 3-115SIGNAL TIMING SPECIFICATIONS 3-316SIGNAL TIMING WAVEFORMS 3-418POWER SEQUENCE 3-620OPTICAL SFECIFICATIONS 424MECHANICAL CHARACTERISTICS 527RELIABLITY 628INTERNATIONAL STANDARDS 728SAFETY 7-1Page ITEM NoLiquid Crystal DisplayRECORD OF REVISIONS Update words of the safety and environment28Update the calculation formula of LED power consumption 8Modify the color coordinates of By and add I BL spec 20Update the Mechanical drawing 25, 26Update the LED String Voltage (Min/Max) and power consumption 8Modify the weight information of LCD Module 4, 24Dec. 13. 20101.0First Draft(Preliminary)-Sep. 7. 20100.0Description Page Revision Date RevisionNoLiquid Crystal Display1. General DescriptionFigure 1. Block diagramLM270WF2-TLA5 is a Color Active Matrix Liquid Crystal Display with an integral Light Emitting Diode (White LED) backlight system. The matrix employs a-Si Thin Film Transistor as the active element. It is a transmissive type display operating in the normally white mode. It has a 27 inch diagonally measured active display area with Full HD resolution (1080 vertical by 1920 horizontal pixel array) Each pixel is divided into Red, Green and Blue sub-pixels or dots which are arranged in vertical stripes. Gray scale or the brightness of the sub-pixel color isdetermined with a 8-bit gray scale signal for each dot, thus, presenting a palette of more than 16,7M colors with Advanced-FRC(Frame Rate Control). It has been designed to apply the interface method that enables low power, high speed, low EMI. FPD Link or compatible must be used as a LVDS(Low Voltage Differential Signaling) chip. It is intended to support applications where thin thickness, wide viewing angle, low power are critical factors and graphic displays are important. It is intended to support displays where high brightness, super wide viewing angle,high color saturation, and high color are important.Liquid Crystal Display2. Absolute Maximum RatingsThe following are maximum values which, if exceeded, may cause faulty operation or damage to the unit.Note : 1. Temperature and relative humidity range are shown in the figure below.Wet bulb temperature should be 39 °C Max, and no condensation of water.2. Storage condition is guaranteed under packing condition.Table 1. ABSOLUTE MAXIMUM RATINGS90%10203040506070800-2001020304050Dry Bulb Temperature [C]Wet Bulb Temperature [C]Storage Operation H u m i d i t y [(%)R H ]10%40%60%60Figure 2. Temperature and relative humidityLiquid Crystal Display3. Electrical Specifications3-1. Electrical CharacteristicsTable 2-1. ELECTRICAL CHARACTERISTICSNote :1. Permissive power ripple should be measured under V LCD =5.0V, 25°C, fV(frame frequency)=60Hzcondition and At that time, we recommend the bandwidth configuration of oscilloscope is to be under 20Mhz. See the next page.2. The specified current and power consumption are under the V LCD =5.0V, 25 ±2°C,f V =60Hz conditionwhereas Mosaic pattern(8 X 6) is displayed and fv is frame frequency.3. The specified current and power consumption are under the V LCD =5.0V, 25 ±2°C,fV=60Hz condition whereas Full Black pattern is displayed and fv is frame frequency.4. Maximum Condition of Inrush current :The duration of rush current is about 2ms and rising time of Input Voltage is 1ms(min.).At any rising time of Input voltage, Keep the I2T Value by below ConditionCondition : I2T < 32*2msIt requires two power inputs. One is employed to power the LCD electronics and to drive the TFT array and liquid crystal. The second input power for the LED/Backlight, is typically generated by a LED Driver.The LED Driver is an external unit to the LCDs.Liquid Crystal DisplayWhite pattern Black pattern•Permissive Power input ripple (V LCD =5.0V, 25°C, fV(frame frequency)=60Hz condition )•Power consumption (V LCD =5.0V, 25°C, fV (frame frequency=60Hz condition )Figure 3. Mosaic pattern & Black Pattern for power consumption measurementTypical power PatternBlack PatternLiquid Crystal DisplayTable 2_2. LED Bar ELECTRICAL CHARACTERISTICS 4,6,7Watt 23.9422.5321.12P BarPower Consumption 5,7Hrs --30,000LED_LT LED Life Time3,7V 54.451.248.0VsLED String Voltage 1,7LED :2,7mA 120110-Is LED String CurrentNotes Max.Typ.Min.Unit ValuesCondition Symbol ParameterLED driver design guide:The design of the LED driver must have specifications for the LED in LCD Assembly .The performance of the LED in LCM, for example life time or brightness, is extremely influenced bythe characteristics of the LED driver.So all the parameters of a LED driver should be carefully designed and output current should beConstant current control.Please control feedback current of each string individually to compensate the current variationamong the strings of LEDs.When you design or order the LED driver, please make sure unwanted lighting caused bythe mismatch of the LED and the LED driver (no lighting, flicker, etc) never occurs.When you confirm it, the LCD module should be operated in the same condition as installed inyour instrument.Notes :1. Specified values are for a single LED bar.2. The specified current is input LED chip 100% duty current.3. The specified voltage is input LED string and Bar voltage at typical 110mA 100% duty current.4. The specified power consumption is input LED bar power consumption at typical 110mA 100% duty current.5. The life is determined as the time at which luminance of the LED is 50% compared to that of initial value at the typical LED current on condition of continuous operating at 25 ±2°C.6. The LED bar power consumption shown above does not include loss of external driver.The used LED bar current is the LED typical current.Min Power Consumption is calculated with PBar = Vs(Min.) x Is(Typ.) x NstringMax Power Consumption is calculated with PBar = Vbar(Max.) x Is(Typ) x Nstring7.LED operating DC Forward Current must not exceed LED Max Ratings at 25 ±2°C.Liquid Crystal Display3-2. Interface ConnectionsTable 3 MODULE CONNECTOR(CN1) PIN CONFIGURATIONThis LCD employs Two interface connections, a 30 pin connector is used for the module electronics and a 10Pin Connector is used for the integral backlight system.3-2-1. LCD ModuleNote: 1. All GND(ground) pins should be connected together and to Vss which should also be connected tothe LCD’s metal frame.2. All VLCD (power input) pins should be connected together.3. Input Level of LVDS signal is based on the EIA 664 Standard.4. PWM is a reference signal for inverter control. This PWM signal is synchronized with vertical frequency. Its frequency is 3 times of vertical frequency, and its duty ratio is 50%.If the system don’t use this pin, do not connect.V LCDV LCD V LCD PWM NC NC GND SR3P SR3MSCLKINPSCLKINM SR2P SR2M GND SR1P Symbol302928272625242322212019181716NoPower Supply +5.0VPower Supply +5.0V Power Supply +5.0V Reference signal for LED Driver control No ConnectionNo Connection Ground Plus signal of even channel 3 (LVDS)Minus signal of even channel 3 (LVDS)Plus signal of even clock channel (LVDS)Minus signal of even clock channel (LVDS)Plus signal of even channel 2 (LVDS)Minus signal of even channel 2 (LVDS)GroundPlus signal of even channel 1 (LVDS)SymbolMinus signal of even channel 1 (LVDS)GroundPlus signal of even channel 0 (LVDS)Minus signal of even channel 0 (LVDS)Plus signal of odd channel 3 (LVDS)Minus signal of odd channel 3 (LVDS)Plus signal of odd clock channel (LVDS)Minus signal of odd clock channel (LVDS)GroundPlus signal of odd channel 2 (LVDS)Minus signal of odd channel 2 (LVDS)Plus signal of odd channel 1 (LVDS)Minus signal of odd channel 1 (LVDS)Plus signal of odd channel 0 (LVDS)Minus signal of odd channel 0 (LVDS)DescriptionSR1M15GND 14SR0P 13SR0M 12FR3P 11FR3M 10FCLKINP 9FCLKINM 8GND7FR2P 6FR2M 5FR1P 4FR1M 3FR0P 2FR0M 1SymbolNo -LCD Connector(CN1): GT103-30S-HF15-E2500 (Manufactured by LSC ) or Equivalent -Mating Connector : FI-X30H and FI-X30HL (Manufactured by JAE) or Equivalent [ Figure 4 ] Connector diagramLiquid Crystal DisplayTable 4. REQUIRED SIGNAL ASSIGNMENT FOR Flat Link (TI:SN75LVDS83) Transmitter Notes : Refer to LVDS Transmitter Data Sheet for detail descriptions.Pin #Require SignalPin NamePin #Require SignalPin Name1Power Supply for TTL Input V CC 29Ground pin for TTL GND 2TTL Input (R7)D530TTL Input (DE)D263TTL Input (R5)D631TTL Level clock Input T X CLKIN 4TTL Input (G0)D732Power Down Input PWR DWN 5Ground pin for TTL GND 33Ground pin for PLL PLL GND 6TTL Input (G1)D834Power Supply for PLL PLL V CC 7TTL Input (G2)D935Ground pin for PLL PLL GND 8TTL Input (G6)D1036Ground pin for LVDSLVDS GND 9Power Supply for TTL Input V CC 37Positive LVDS differential data output 3TxOUT3+10TTL Input (G7)D1138Negative LVDS differential data output 3TxOUT3-11TTL Input (G3)D1239Positive LVDS differential clock output T X CLKOUT +12TTL Input (G4)D1340Negative LVDS differential clock output T X CLKOUT -13Ground pin for TTL GND 41Positive LVDS differential data output 2T X OUT2+14TTL Input (G5)D1442Negative LVDS differential data output 2T X OUT2-15TTL Input (B0)D1543Ground pin for LVDS LVDS GND 16TTL Input (B6)D1644Power Supply for LVDSLVDS V CC 17Power Supply for TTL Input V CC 45Positive LVDS differential data output 1T X OUT1+46Negative LVDS differential data output 1T X OUT1-18TTL Input (B7)D1747Positive LVDS differential data output 0T X OUT0+48Negative LVDS differential data output 0T X OUT0-19TTL Input (B1)D1820TTL Input (B2)D1949Ground pin for LVDS LVDS GND21Ground pin for TTL Input GND 22TTL Input (B3)D2023TTL Input (B4)D2150TTL Input (R6)D2751TTL Input (R0)D024TTL Input (B5)D2225TTL Input (RSVD)D2352TTL Input (R1)D153Ground pin for TTL GND 26Power Supply for TTL Input V CC 54TTL Input (R2)D255TTL Input (R3)D327TTL Input (HSYNC)D2456TTL Input (R4)D428TTL Input (VSYNC)D25Liquid Crystal DisplayLVDS Input characteristicsV V LVDS Common mode Voltage 600|V ID LVDS Differential Voltage Max Symbol Description1. DC Specification2. AC SpecificationLiquid Crystal DisplayVer 1.0Dec. 13. 2010< Clock skew margin between channel >< LVDS Data Format >3. Data Format 1) LVDS 2 Port< Spread Spectrum >Freq.Liquid Crystal Display2) LVDS 1 PortLiquid Crystal Display3-2-2. LED InterfaceThe LED interface connector is a model 10019HR-H06B manufactured by Yeonho.The pin configuration for the connector is shown in the table below.Table 5. LED connector pin configurationFIG. 5 Backlight connector viewLiquid Crystal Display3-3. Signal Timing SpecificationsThis is signal timing required at the input of the TMDS transmitter. All of the interface signal timing should be satisfied with the following specifications for it’s proper operation.Table 6. TIMING TABLE Note: Hsync period and Hsync width-active should be even number times of t CLK . If the value is odd numbertimes of t CLK , display control signal can be asynchronous.In order to operate this LCM a Hsync, Vsyn, and DE(data enable) signals should be used.1. The performance of the electro-optical characteristics may be influenced by variance of the verticalrefresh rates.2. Vsync and Hsync should be keep the above specification.3. Hsync Period, Hsync Width, and Horizontal Back Porch should be any times of of characternumber(8).4. The polarity of Hsync, Vsync is not restricted.16012858tHB Horizontal Blank960960960tHV Horizontal Valid 802010tVB Vertical Blank108010801080tVV Vertical Valid tHP1642tWV WidthHz756050fV Frequency tHP116011001090tVP Period 644820tHBP Horizontal Back Porch 484820tHFP Horizontal Front Porch tCLK483218tWH WidthKHz3285tVBP Vertical Back Porch 3283tVFPVertical Front Porch82.56664.3fH Frequency tCLK112010881018tHP PeriodHsyncVsyncMHz87.571.860.0-Frequency ns 15.3813.9311.42tCLKPeriodDCLKNoteUnit Max Typ Min SymbolITEMLiquid Crystal Display3-4. Signal Timing WaveformsLiquid Crystal Display3-5. Color Data ReferenceTable 7. COLOR DATA REFERENCEThe Brightness of each primary color(red,green,blue) is based on the 8-bit gray scale data input for the color;the higher the binary input, the brighter the color. The table below provides a reference for color versus data input.0 0 0 0 0 0 0 00 0 0 0 0 0 0 00 0 0 0 0 0 0 0GREEN (000) Dark GREEN0 0 0 0 0 0 0 00 0 0 0 0 0 0 10 0 0 0 0 0 0 0GREEN (001)............0 0 0 0 0 0 0 01 1 1 1 1 1 1 00 0 0 0 0 0 0 0GREEN (254)0 0 0 0 0 0 0 01 1 1 1 1 1 1 10 0 0 0 0 0 0 0GREEN (255)0 0 0 0 0 0 0 00 0 0 0 0 0 0 00 0 0 0 0 0 0 0RED (000) Dark RED 0 0 0 0 0 0 0 00 0 0 0 0 0 0 00 0 0 0 0 0 0 1RED (001)............0 0 0 0 0 0 0 00 0 0 0 0 0 0 01 1 1 1 1 1 1 0RED (254)0 0 0 0 0 0 0 00 0 0 0 0 0 0 01 1 1 1 1 1 1 1RED (255)0 0 0 0 0 0 0 10 0 0 0 0 0 0 00 0 0 0 0 0 0 0BLUE (001)............1 1 1 1 1 1 1 00 0 0 0 0 0 0 00 0 0 0 0 0 0 0BLUE (254)1 1 1 1 1 1 1 10 0 0 0 0 0 0 00 0 0 0 0 0 0 0BLUE (255)BLUE (000) Dark WhiteYellow Magenta Cyan Blue (255)Green (255)Red (255)Black 0 0 0 0 0 0 0 00 0 0 0 0 0 0 00 0 0 0 0 0 0 0Basic Color0 0 0 0 0 0 0 00 0 0 0 0 0 0 01 1 1 1 1 1 1 10 0 0 0 0 0 0 01 1 1 1 1 1 1 10 0 0 0 0 0 0 01 1 1 1 1 1 1 10 0 0 0 0 0 0 00 0 0 0 0 0 0 01 1 1 1 1 1 1 11 1 1 1 1 1 1 10 0 0 0 0 0 0 01 1 1 1 1 1 1 10 0 0 0 0 0 0 01 1 1 1 1 1 1 10 0 0 0 0 0 0 01 1 1 1 1 1 1 11 1 1 1 1 1 1 11 1 1 1 1 1 1 11 1 1 1 1 1 1 11 1 1 1 1 1 1 1BLUEMSB LSBGREEN MSB LSB RED MSB LSB B7 B6 B5 B4 B3 B2 B1 B0G7 G6 G5 G4 G3 G2 G1 G0R7 R6 R5 R4 R3 R2 R1 R00 0 0 0 0 0 0 00 0 0 0 0 0 0 00 0 0 0 0 0 0 0BLUE ColorInput Color DataLiquid Crystal Display3-6. Power SequenceNotes : 1. Please avoid floating state of interface signal at invalid period.2. When the interface signal is invalid, be sure to pull down the power supply for LCD V LCD to 0V.3. B/L power must be turn on after power supply for LCD and interface signal are valid.ms -1000T7ms 50-0.01T2ms ms --500T3--200T4ms 50-0.01T5ms 10-0.5T1Max Typ MinUnitsValuesParameterTable 8. POWER SEQUENCEPower supply for LCDVccInterface signalV IPower Supply for LEDLiquid Crystal Display3-7. VLCD Power Dip condition1) Dip condition3.5V ≤V LCD <4.5V , t d ≤20ms2) V LCD <3.5VV LCD -dip conditions should also follow the Power On/Off conditions for supply voltage.Liquid Crystal DisplayOptical characteristics are determined after the unit has been ‘ON’for approximately 30 minutes in a dark environment at 25±2°C. The values specified are at an approximate distance 50cm from the LCD surface at a viewing angle of Φand θequal to 0 °and aperture 1 degree.FIG. 6 presents additional information concerning the measurement equipment and method.FIG. 6 Optical Characteristic Measurement Equipment and Method4. Optical Specifications50cmOptical Stage(x,y)LCD ModulePritchard 880 or equivalentLiquid Crystal DisplayNotes 1.Contrast Ratio(CR)is defined mathematically as :Surface Luminance with all white pixelsContrast Ratio =Surface Luminance with all black pixels2. Surface luminance is luminance value at No.1 point across the LCD surface 50cm from the surface with all pixels displaying white. For more information see FIG 6.3. The variation in surface luminance , δWHITE is defined as :Measuring point for surface luminance & measuring point for luminance variation(%)100)L .... ,L ,(L Maximum )L .. ,L ,Minimum(L on9on2on1on9on2on1×…=WHITE δVActive AreaA : H/4 mmB : V/4 mm@ H,V : Active Area[ FIGURE 7 ] Measure Point for LuminanceBy PR880By PR880Liquid Crystal Display4. The response time is defined as the following figure and shall be measured by switching the input signal for “black”and “white”.Response time is the time required for the display to transition from white to black (Rise Time,T rR) and from black to white (Decay Time, T rD ).10090100%Optical responseTr R Tr D[ FIGURE 8] Response TimeLiquid Crystal Display7. Viewing angle is the angle at which the contrast ratio is greater than 10 or 5. The angles are determined for the horizontal or x axis and the vertical or y axis with respect to the z axis which is normal to the LCD surface. For more information see FIG. 9 .<Dimension of viewing angle range>[ FIGURE 9 ] Viewing angleTable 10. Gray Scale Specification8, Gray scale specificationGamma Value is approximately 2.2. For more information see Table 100.10010076.0054.5537.3023.4512.254.831.10255223191159127956331Relative Luminance [%] (Typ.)Gray LevelLiquid Crystal Display5. Mechanical CharacteristicsThe contents provide general mechanical characteristics. In addition the figures in the next page are detailed mechanical drawing of the LCD.Notes : Please refer to a mechanic drawing in terms of tolerance at the next page.336.31mm VerticalHard coating(3H)Anti-glare treatment of the front polarizerSurface TreatmentTyp : 2930g, Max : 3066gWeight 340.4mm Vertical 368.2mm Vertical 14.5mm Depth 597.89mm HorizontalActive Display Area602mmHorizontalBezel Area630mm HorizontalOutline DimensionLiquid Crystal Display<FRONT VIEW>Liquid Crystal Display<REAR VIEW>Liquid Crystal Display6. ReliabilityEnvironment test conditionMax 70%RH , Ta=40℃Maximum Storage Humidity for 4 corner light leakage Mura.90 -40,000 feet(12192m)Altitudestorage / shipment8Ta= 40 °C ,90%RHHumidity condition Operation7Shock level : 100GWaveform : half sine wave, 2ms Direction :±X, ±Y, ±ZOne time each direction Shock test(non-operating)6Wave form : random Vibration level : 1.0Grms Bandwidth : 10-300Hz Duration : X,Y,Z, 10minOne time each direction Vibration test(non-operating)5Ta= 0°C 240hLow temperature operation test4Ta= 50°C 50%RH 240h High temperature operation test 3Ta= -20°C 240hLow temperature storage test 2Ta= 60°C 240h High temperature storage test 1ConditionTest ItemNoLiquid Crystal Display7. International Standards 7-2. EMC7-3. Environment7-1. Safetyc) EN 60950-1:2006 + A11:2009, European Committee for Electrotechnical Standardization(CENELEC).Information Technology Equipment -Safety -Part 1 : General Requirements.a) UL 60950-1, Second Edition, Underwriters Laboratories Inc.Information Technology Equipment -Safety -Part 1 : General Requirements.b) CAN/CSA C22.2 No.60950-1-07, Second Edition, Canadian Standards rmation Technology Equipment -Safety -Part 1 : General Requirements.d) IEC 60950-1:2005, Second Edition,The International Electrotechnical Commission (IEC).Information Technology Equipment -Safety -Part 1 : General Requirements.(Including report of IEC60825-1:2001 clause 8 and clause 9)Notes1. Laser (LED Backlight) InformationClass 1M LED Product IEC60825-1 : 2001Embedded LED Power (Class 1M)2. Caution : LED inside.Class 1M laser (LEDs) radiation when open.Do not open while operating.a) ANSI C63.4 “American National Standard for Methods of Measurement of Radio-NoiseEmissions from Low-Voltage Electrical and Electronic Equipment in the Range of 9 kHz to 40 GHz.”American National Standards Institute (ANSI), 2003.b) CISPR 22 “Information technology equipment –Radio disturbance characteristics –Limit and methods of measurement." International Special Committee on Radio Interference (CISPR), 2005.c) CISPR 13 “Sound and television broadcast receivers and associated equipment –Radio disturbance characteristics –Limits and method of measurement." International Special Committee on Radio Interference (CISPR), 2006.a) RoHS, Directive 2002/95/EC of the European Parliament and of the council of 27 January 2003Liquid Crystal Display8-2. Packing Forma) Package quantity in one box : 10ea b) Box Size : 747 X 335 X 4668. Packing8-1. Designation of Lot Marka) Lot MarkABCDEFGHIJKLMA,B,C : SIZE(INCH) D : YEARE : MONTHF ~ M : SERIAL NO.Note1. YEAR2. MONTHMarkYear 02010620067200782008920094200452005321200320022001BNov MarkMonth AOct 6Jun 7Jul 8Aug 9Sep 4Apr 5May C321Dec Mar Feb Jan b) Location of Lot MarkSerial No. is printed on the label. The label is attached to the backside of the LCD module.This is subject to change without prior notice.Liquid Crystal Display9. PRECAUTIONSPlease pay attention to the followings when you use this TFT LCD module.9-1. MOUNTING PRECAUTIONS(1) You must mount a module using holes arranged in four corners or four sides.(2) You should consider the mounting structure so that uneven force (ex. Twisted stress) is not applied to themodule. And the case on which a module is mounted should have sufficient strength so that external force is not transmitted directly to the module.(3) Please attach the surface transparent protective plate to the surface in order to protect the polarizer.Transparent protective plate should have sufficient strength in order to the resist external force.(4) You should adopt radiation structure to satisfy the temperature specification.(5) Acetic acid type and chlorine type materials for the cover case are not desirable because the formergenerates corrosive gas of attacking the polarizer at high temperature and the latter causes circuit break by electro-chemical reaction.(6) Do not touch, push or rub the exposed polarizers with glass, tweezers or anything harder than HBpencil lead. And please do not rub with dust clothes with chemical treatment.Do not touch the surface of polarizer for bare hand or greasy cloth.(Some cosmetics are detrimental to the polarizer.)(7) When the surface becomes dusty, please wipe gently with absorbent cotton or other soft materials likechamois soaks with petroleum benzene. Normal-hexane is recommended for cleaning the adhesives used to attach front / rear polarizers. Do not use acetone, toluene and alcohol because they cause chemical damage to the polarizer.(8) Wipe off saliva or water drops as soon as possible. Their long time contact with polarizer causesdeformations and color fading.(9) Do not open the case because inside circuits do not have sufficient strength.9-2. OPERATING PRECAUTIONS(1) The spike noise causes the mis-operation of circuits. It should be lower than following voltage :V=±200mV(Over and under shoot voltage)(2) Response time depends on the temperature.(In lower temperature, it becomes longer.)(3) Brightness depends on the temperature. (In lower temperature, it becomes lower.)And in lower temperature, response time(required time that brightness is stable after turned on) becomes longer.(4) Be careful for condensation at sudden temperature change. Condensation makes damage to polarizer orelectrical contacted parts. And after fading condensation, smear or spot will occur.(5) When fixed patterns are displayed for a long time, remnant image is likely to occur.(6) Module has high frequency circuits. Sufficient suppression to the electromagnetic interference shall bedone by system manufacturers. Grounding and shielding methods may be important to minimized the interference.(7) Please do not give any mechanical and/or acoustical impact to LCM. Otherwise, LCM can’t be operatedits full characteristics perfectly.(8) A screw which is fastened up the steels should be a machine screw.(if not, it causes metallic foreign material and deal LCM a fatal blow)(9)Please do not set LCD on its edge.。
953-L规格书

试 验 方 法(JIS C5202) 按照 5.7 (1)安装条件为 A;V 形块法。 (2)试验电压按照本标准书表 2 之耐电压。
4
耐电压
无飞弧、烧损、绝缘 破坏等的异常现象。
5
按照 5.8 断续过负 (1)最高断续过负荷电压,按照条件 A,并在本 荷(适用 阻值的容许变化率 标准书表 2 的电压以下; 100 Ω 以 ± (5%+0.1Ω) 以内。 (2)试验次数 条件 A。 上) 于印刷基板上插入电阻器在锡焊好的状态下如下 图箭头的 3 个方向加以负载。加上去的力为:d 尺 寸 0.65 以下为 3N,其它的为:5 N 在加负载的方向不 能有 1.0 mm 以上摆 动。
-55 100 额 定 功 耗 的 百 分 比 ( ) % 80 60 40 20 0 -60 -40 -20 0 20 40 60 80 100 120 140 155 160 180 200 235 220 240 70
图2Leabharlann 环境温度 (℃)5.质量一致性检验 表3
编号 1 项 阻值 按照 5.1 规定要求 按照 5.2 (1) 试验温度 室温及比室温高约 100℃; 电阻温度 (2)电阻温度特性的表示方法按照 系数 5.2.2(2)(a)。 规定的阻值允许差以内 目 试 验 方 法(JIS C5202) 性 能
图3
备注:W1 是印刷线路板孔的直径,W2 是端子加工部的宽。 表4
种类及规格 P1 RS1/2FS-L RS1FS-L RS2FS-L RS3FS-L RS5FS-L 10.0±0.5 12.5±0.5 15.0±0.5 20.0±0.5 30.0±0.5 P2 10.0 15.0 20.0
+2.0 −1.0
- 1、下载文档前请自行甄别文档内容的完整性,平台不提供额外的编辑、内容补充、找答案等附加服务。
- 2、"仅部分预览"的文档,不可在线预览部分如存在完整性等问题,可反馈申请退款(可完整预览的文档不适用该条件!)。
- 3、如文档侵犯您的权益,请联系客服反馈,我们会尽快为您处理(人工客服工作时间:9:00-18:30)。
LM27953White LED Driver with Four LED Current Sinks and 3/2x Switched Capacitor BoostGeneral DescriptionThe LM27953is a charge-pump-based white-LED driver that is ideal for mobile phone display backlighting.It is intended to drive 4LEDs for a main phone display backlight.Regu-lated internal current sources deliver excellent current and brightness matching in all LEDs.The LED driver current sinks can be used to backlight a main phone display with up to 4LEDs.The low-side current drivers accommodate common-anode-type LEDs.The cur-rent sinks can also drive standard two-terminal LEDs,and provide other general lighting functions (keypad lighting,fun lighting,etc).The brightness of the LEDs can be adjusted independently with an external resistor.The LM27953works off an extended Li-Ion input voltage range (2.7V to 5.5V).Voltage boost is achieved with a high-efficiency 3/2x-gain charge pump.The LM27953is available in National’s chip-scale 18-bump micro SMD package.Featuresn Drives 4Individual Common-Anode LEDs with up to 20mA each for a Main Display Backlightn Independent Resistor-Programmable Current Setting n Excellent Current and Brightness Matching n High-Efficiency 3/2x Charge Pump n Extended Li-Ion Input:2.7V to 5.5V n PWM Brightness Control:100Hz -1kHz n 18-bump Thin Micro SMD Package:(2.1mm x 2.4mm x 0.6mm)Applicationsn Mobile Phone Display Lighting n Mobile Phone Keypad Lighting n PDAsnGeneral LED LightingTypical Application Circuit20128001November 2004LM27953White LED Driver with Four LED Current Sinks and 3/2x Switched Capacitor Boost©2004National Semiconductor Corporation Connection Diagram18-Bump Thin Micro SMD Package,Large BumpNS Package Number TLA1820128002Pin DescriptionPin #s Pin NamesPin DescriptionsC1V IN Input voltage.Input range:2.7V to 5.5V.D2PWR GND Power GroundA3PWR P OUT Charge pump output.Approximately 1.5xV IN A1,B2,A5,E1C1+,C1-,C2+,C2-Flying capacitor connections.D6,E5,D4,E3D1,D2,D3,D4LED Outputs -Group AC5,B4,C3SIG P OUTSignal P OUT :Tie pins externally to PWR P OUTB6ENEnable for Charge Pump and LEDs (current outputs).Logic input.High =LEDs ON.Low =LEDs OFF.Pulsing this pin with a PWM signal (100Hz-1kHz)can be used to dim LEDs.A7SIG GND Signal Ground.Tie pin externally to PWR GNDE7I SET Placing a resistor (R SET )between this pin and GND sets the LED current.LED Current =100x (1.25V ÷R SET ).C7NCNo ConnectOperational StatesEN Mode of OperationL ShutdownHCharge Pump Enabled.LEDs ON.Ordering InformationOrder Information PackageSupplied AsLM27953TL TLA18Micro SMD250Units,Tape &Reel LM27953TLX3000Units,Tape &ReelL M 27953 2Absolute Maximum Ratings(Notes1,2) If Military/Aerospace specified devices are required, please contact the National Semiconductor Sales Office/ Distributors for availability and specifications.V IN pin voltage-0.3V to7.1V EN pin voltages-0.3V to(V IN+0.3V)w/6.0V max I Dx Pin Voltages-0.3V to(V POUT+0.3V)w/6.0V max Continuous Power Dissipation(Note3)Internally Limited Junction Temperature(T J-MAX)150o C Storage Temperature Range-65o C to+150o C Maximum Lead Temperature(Soldering,10sec.)265o C ESD Rating(Note4)Human Body Model-I Dx Pins: Human Body Model-All other Pins: Machine Model-I Dx Pins: Machine Model-All Other Pins:1.0kV2.0kV100V200VOperating Rating(Notes1,2)Input Voltage Range 2.7V to5.5VJunction Temperature(T J)Range-30˚C to+125˚CAmbient Temperature(T A)Range(Note5)-30˚C to+85˚C Thermal PropertiesJuntion-to-Ambient ThermalResistance(θJA),(Note6)100˚C/WElectrical Characteristics(Notes2,7)Limits in standard typeface are for T J=25˚C,and limits in boldface type apply over the full operating temperature range.Un-less otherwise specified:V IN=3.6V;V Dx=0.6V;EN=1.5V;R SET=8.35kΩ;C IN,C1,C2,and C POUT=1µF.(Note8)Symbol Parameter Condition Min Typ Max UnitsI Dx Output Current Regulation 3.0V≤V IN≤4.2V,and V IN=5.5V0.45V≤V Dx≤3.8VR SET=8.35kΩ13.5(-10%)1516.5(+10%)mA(%) 3.0V≤V IN≤5.5V;0.6V≤V Dx≤3.8VR SET=6.25kΩ20mA3.0V≤V IN≤5.5V;0.3V≤V Dx≤3.8VR SET=12.5kΩ10mA2.7V≤V IN≤3.0V;0.45V≤V Dx≤3.8VR SET=8.35kΩ15mAI Dx-MATCH Current Matching BetweenOutputsV IN=3.0V(Note9)0.6%I Q Quiescent Supply Current 2.7V≤V IN≤4.2V;No Load Current,EN=ON4.4 6.75mAI SD Shutdown Supply Current 2.7V≤V IN≤5.5V,ENA OFF2.35µA V SET I SET Pin Voltage 2.7V≤V IN≤5.5V 1.25V I Dx/I SET Output Current to Current SetRatio100R OUT Charge Pump Output Resistance(Note10)V IN=3.0V 2.7ΩV HR Current Source HeadroomVoltage Requirement(Note11)I Dx=95%X I Dx(nom)R SET=8.35kΩ(I Dx(nom)≈15mA)320mVf SW Switching Frequency 3.0V≤V IN≤4.2V375500625kHzLM279533Electrical Characteristics (Notes 2,7)(Continued)Limits in standard typeface are for T J =25˚C,and limits in boldface type apply over the full operating temperature range.Un-less otherwise specified:V IN =3.6V;V Dx =0.6V;EN =1.5V;R SET =8.35k Ω;C IN ,C 1,C 2,and C POUT =1µF.(Note 8)Symbol ParameterConditionMinTyp MaxUnits t START Start-up TimeI Dx =90%steady state 350µs 1.5x/1xCharge pump gain cross-over:Gain =1.5when V IN is below threshold.Gain =1when V IN is above threshold. 1.5x to 1x Threshold 4.75V 1x to 1.5x Threshold4.55VLogic Pin Specifications:EN V IL Input Logic Low 2.7V ≤V IN ≤5.5V 00.5V V IH Input Logic High 2.7V ≤V IN ≤5.5V 1.1V INV I LEAKInput Leakage CurrentV EN =0V0.1µAV EN =3V (Note 12)10Note 1:Absolute Maximum Ratings indicate limits beyond which damage to the component may occur.Operating Ratings are conditions under which operation of the device is guaranteed.Operating Ratings do not imply guaranteed performance limits.For guaranteed performance limits and associated test conditions,see the Electrical Characteristics tables.Note 2:All voltages are with respect to the potential at the GND pin.Note 3:Internal thermal shutdown circuitry protects the device from permanent damage.Thermal shutdown engages at T J =160˚C (typ.)and disengages at T J =120˚C (typ.).The thermal shutdown function is guaranteed by design.Note 4:The Human body model is a 100pF capacitor discharged through a 1.5k Ωresistor into each pin.The machine model is a 200pF capacitor discharged directly into each -STD-8833015.7Note 5:In applications where high power dissipation and/or poor package thermal resistance is present,the maximum ambient temperature may have to be derated.Maximum ambient temperature (T A-MAX )is dependent on the maximum operating junction temperature (T J-MAX-OP =125˚C),the maximum power dissipation of the device in the application (P D-MAX ),and the junction-to ambient thermal resistance of the part/package in the application (θJA ),as given by the following equation:T A-MAX =T J-MAX-OP –(θJA x P D-MAX ).Note 6:Junction-to-ambient thermal resistance is highly dependent on application and board layout.In applications where high maximum power dissipation exists,special care must be paid to thermal dissipation issues in board design.Note 7:Min and Max limits are guaranteed by design,test,or statistical analysis.Typical numbers are not guaranteed,but do represent the most likely norm.Note 8:C IN ,C POUT ,C 1,and C 2:Low-ESR Surface-Mount Ceramic Capacitors (MLCCs)used in setting electrical characteristicsNote 9:For the group of outputs on a part,the following are determined:the maximum output current in the group (MAX),the minimum output current in the group (MIN),and the average output current of the group (AVG).For the group,two matching numbers are calculated:(MAX-AVG)/AVG and (AVG-MIN)/AVG.The largest number of the two (worst case)is considered the matching figure for the group.The typical specification provided is the most likely norm of the matching figure for all parts.Note 10:Output resistance (R OUT )models all voltage losses in the charge pump.R OUT can be used to estimate the voltage at the charge pump output (P OUT ):V Pout =(1.5x V IN )–(R OUT x I OUT ).In the equation,I OUT is the total output current:the sum of all active Dxx output currents and all current drawn from P OUT .The equation applies when the charge pump is operating with a gain of 3/2(V IN ≤4.75V typ.).Note 11:Headroom voltage:V HR =V Pout –V LEDx .If headroom voltage requirement is not met,LED current regulation will be compromised.Note 12:There is a 300k Ω(typ.)pull-down resistor connected internally between the enable pin (EN)and GND.L M 27953 4Typical Performance CharacteristicsUnless otherwise specified:V IN =3.6V;V LED =3.6V;EN =V IN ;R SET =8.35k Ω;C IN ,C 1,C 2,and C POUT =1µF.LED Current (D1,D2,D3,D4)vs.Input VoltageLED Current (Dx)vs.Input Voltage2012800420128005Quiescent Current vs.Input Voltage,Charge Pump Output Voltagevs.Output Current2012800620128007LM279535Typical Performance Characteristics Unless otherwise specified:V IN =3.6V;V LED =3.6V;EN =V IN ;R SET =8.35k Ω;C IN ,C 1,C 2,and C POUT =1µF.(Continued)Charge Pump Output Voltagevs.Output CurrentCharge Pump Output Voltage vs.Input Voltage (No Load Current)2012801020128008Input Current vs.Input VoltageCharge Pump Output Resistancevs Output Current2012800920128011L M 27953 6Typical Performance Characteristics Unless otherwise specified:VIN=3.6V;V LED=3.6V;EN=V IN; R SET=8.35kΩ;C IN,C1,C2,and C POUT=1µF.(Continued)Charge Pump Switching Frequencyvs.Input VoltageDiode Current(Dx) vs.Headroom Voltage(Dx)2012801220128013Diode Current(Dx) vs.PWM Duty Cycle(EN)Diode Current(Dx)vs.R SET2012801520128016Input Voltage(Top)and Output Voltage(Bottom)WaveformsEN Signal(Top)and Charge Pump Start-Up(Bottom)Waveforms20128017 Vertical Scale=(100mV/div), Horizontal Scale=1µs/div)20128018Vertical Scale=(2V/div),Horizontal Scale=100µs/div)LM279537Block Diagram20128003Circuit DescriptionOVERVIEWThe LM27953is primarily intended for Lithium-Ion battery driven white-LED drive applications,and is well suited to drive white LEDs that are used for backlighting small-format displays.The part has four matched constant-current out-puts,each capable of driving up to 20mA (or more)through white LEDs.The well-matched current sources ensure the current through all the LEDs is virtually identical.This keeps brightness of all LEDs matched to near perfection so that they can provide a consistent backlight over the entire dis-play.CHARGE PUMPThe core of the LM27953is a 1.5x/1x dual-mode charge pump.The input of the charge pump is connected to the V IN pin.The recommended input voltage range of the LM27953is 2.7V to 5.5V.The output of the charge pump is the P OUT pin (“Pump OUTput”).The output voltage of the charge pump is unregulated and varies with input voltage and load current.The charge pump operates in the 1.5x mode when the input voltage is below 4.75V (typ.).In this mode,the input-to-output voltage gain of the charge pump is 1.5,and the voltage at the output of the charge pump will be approxi-mately 1.5x the input voltage (V(P OUT )≈1.5*V IN ).When in the 1.5x mode,the charge pump provides the voltage boost that is required to drive white LEDs from a Li-Ion battery.(White LEDs typically have a forward voltage in the range of 3.3V to 4.0V.A Li-Ion battery typically is not considered to be fully discharged until the battery voltage falls to 3.0V (ap-prox.))The charge pump operates in the 1x mode when the input voltage is above 4.75V (typ.).In these conditions,voltage boost is not required to drive the LEDs,so the charge pump merely passes the input voltage to P OUT (V(P OUT )≈V IN ).This reduces the input current and the power dissipation of the LM27953when the input voltage is high.REGULATED CURRENT OUTPUTSThe matched current outputs are generated with a precision current mirror that is biased off the charge pump output.Matched currents are ensured with the use of tightly matched internal devices and internal mismatch cancellation circuitry.There are four regulated common anode current outputs.There is an ON/OFF control pin for the group (EN).The DC current through the LEDs is programmed with an external resistor.Changing currents on-the-fly can be achieved with the use of digital pulse (PWM)signals.ENABLE PIN:ENThe LM27953has an enable pin that has active-high logic (HIGH =ON).There is an internal pull-down resistor (300k Ωtyp.)that is connected internally between the enable pin and GND.L M 279538Circuit Description(Continued)When the voltage on the EN pin is low(<0.5V),the part is in shutdown mode.All internal circuitry is OFF and the part consumes very little supply current when the LM27953is shutdown.When the voltage on the EN pin is high(>1.1V), the part is active.The charge pump is ON,and the corre-sponding output current drivers are active.EN is also used to turn the output currents ON and OFF. SETTING LED CURRENTSThe output currents of the LM27953can be set to a desired value simply by connecting an appropriately sized resistor (R SET)between the I SET pin of the LM27953and GND.The output currents(LED currents)are proportional to the current that flows out of the I SET pin.The output currents are a factor of100greater than the I SET current.The feedback loop of an internal amplifier sets the voltage of the I SET pin to1.25V (typ.).Placing a resistor between I SET and GND programs the I SET current,and thus the LED currents.The statements above are simplified in the equations below:I Dx=100x(V SET/R SET)R SET=100x(1.25V/I Dx)MAXIMUM OUTPUT CURRENT,MAXIMUM LED VOLTAGE,MINIMUM INPUT VOLTAGEThe LM27953can drive4LEDs at15mA each from an input voltage as low as2.7V,so long as the LEDs have a forward voltage of3.5V or less(room temperature).The statement above is a simple example of the LED drive capabilities of the LM27953.The statement contains the key application parameters that are required to validate an LED-drive design using the LM27953:LED current(I LEDx),num-ber of active LEDs(N),LED forward voltage(V LED),and minimum input voltage(V IN-MIN).The equation below can be used to estimate the total output current capability of the LM27953:I LED_MAX=((1.5x V IN)-V LED)/((N x R OUT)+k HR)(eq.1) I LED_MAX=((1.5x V IN)-V LED)/((N x2.7Ω)+22mV/mA) R OUT–Output resistance.This parameter models the inter-nal losses of the charge pump that result in voltage droop at the pump output P OUT.Since the magnitude of the voltage droop is proportional to the total output current of the charge pump,the loss parameter is modeled as a resistance.The output resistance of the LM27953is typically2.7Ω(V IN= 3.0V,T A=25˚C).In equation form:V POUT=1.5xV IN–NxI LED xR OUT(eq.2)k HR–Headroom constant.This parameter models the mini-mum voltage required to be present across the current sources for them to regulate properly.This minimum voltage is proportional to the programmed LED current,so the con-stant has units of mV/mA.The typical k HR of the LM27953is 22mV/mA.In equation form:(V POUT–V LED)>k HR xI LED(eq.3)The"I LED-MAX"equation(eq.1)is obtained from combining the R OUT equation(eq.2)with the k HR equation(eq.3)and solving for I LED.Maximum LED current is highly dependent on minimum input voltage and LED forward voltage.Output current capability can be increased by raising the minimum input voltage of the application,or by selecting an LED with a lower forward voltage.Excessive power dissipation may also limit output current capability of an application.PARALLEL Dx OUTPUTS FOR INCREASED CURRENTCAPABILITYOutputs D1through D4may be connected together in anycombination to drive higher currents through fewer LEDs.For example in Figure1,outputs D1A and D2A are con-nected together to drive one LED.D3A and D4A are con-nected to drive a second LED.With this configuration,two parallel current sources of equalvalue provide current to one of the LEDs.R SET shouldtherefore be chosen so that the current through each outputis programmed to50%of the desired current through theparallel connected LED.For example,if40mA is the desireddrive current for the parallel connected LED,R SET should beselected so that the current through each of the outputs is20mA.Other combinations of parallel outputs may be imple-mented in similar fashions,such as in Figure2.Connecting outputs in parallel does not affect internal opera-tion of the LM27953and has no impact on the ElectricalCharacteristics and limits previously presented.The avail-able diode output current,maximum diode voltage,and allother specifications provided in the Electrical Characteristicstable apply to parallel output configurations,just as they doto the standard application circuit on pg1of the datasheet.SOFT STARTThe LM27953contains internal soft-start circuitry to limitinput inrush currents when the part is enabled.Soft start isimplemented with a controlled turn-on of the internal voltagereference.During soft start,the current through the LED20128019FIGURE1.Two Parallel Connected LEDs20128020FIGURE2.One Parallel Connected LEDLM279539Circuit Description(Continued)outputs rise at the rate of the reference voltage ramp.Due to the soft-start circuitry,turn-on time of the LM27953is ap-proximately 350µs (typ.).THERMAL PROTECTIONInternal thermal protection circuitry disables the LM27953when the junction temperature exceeds 160˚C (typ.).This feature protects the device from being damaged by high die temperatures that might otherwise result from excessive power dissipation.The device will recover and operate nor-mally when the junction temperature falls below 120˚C (typ.).It is important that the board layout provides good thermal conduction.This will help to keep the junction temperature within specified operating ratings.Applications InformationPOWER EFFICIENCYEfficiency of LED drivers is commonly taken to be the ratio of power consumed by the LEDs (P LED )to the power drawn at the input of the part (P IN ).With a 1.5x charge pump,the input current is approximately 1.5x the output current (total LED current).For a simple approximation,the current consumed by internal circuitry can be neglected and the efficiency of the LM27953can be predicted as follows:Neglecting I Q will result in a slightly higher efficiency predic-tion,but this impact will be no more than a few percentage points when several LEDs are driven at full power.ADJUSTING LED BRIGHTNESS (PWM control)Perceived LED brightness can be adjusted using a PWM control signal to turn the LM27953current sources ON and OFF at a rate faster than perceptible by the eye.When this is done,the total brightness perceived is proportional to the duty cycle (D)of the PWM signal (D =the percentage of time that the LED is on in every PWM cycle).A simple example:if the LEDs are driven at 15mA each with a PWM signal that has a 50%duty cycle,perceived LED brightness will be about half as bright as compared to when the LEDs are driven continuously with 15mA.A PWM signal thus provides brightness (dimming)control for the solution.The minimum recommended PWM frequency is 100Hz.Fre-quencies below this may be visibly noticeable as flicker or blinking.The maximum recommended PWM frequency is 1kHz.Frequencies above this may cause interference with internal current driver circuitry.In cases where a PWM signal must be connected to the EN pin,measures can be taken to reduce the magnitude of thecharge-pump turn-on voltage spikes.More input capaci-tance,series resistors and/or ferrite beads may provide ben-efits.If the current and voltage spikes can be tolerated,connect-ing the PWM signal to the EN pin does provide a benefit:lower supply current when the PWM signal is active.When the PWM signal is low,the LM27953will be shutdown and input current will only be a few micro-amps.This results in a lower time-averaged input current.CAPACITOR SELECTIONThe LM27953requires 4external capacitors for proper op-eration.Surface-mount multi-layer ceramic capacitors are recommended.These capacitors are small,inexpensive and have very low equivalent series resistance (ESR <20mW typ.).Tantalum capacitors,OS-CON capacitors,and alumi-num electrolytic capacitors are not recommended for use with the LM27953due to their high ESR,as compared to ceramic capacitors.For most applications,ceramic capacitors with X7R or X5R temperature characteristic are preferred for use with the LM27953.These capacitors have tight capacitance toler-ance (as good as ±10%)and hold their value over tempera-ture (X7R:±15%over -55˚C to 125˚C;X5R:±15%over -55˚C to 85˚C).Capacitors with Y5V or Z5U temperature characteristic are generally not recommended for use with the LM27953.Ca-pacitors with these temperature characteristics typically have wide capacitance tolerance (+80%,-20%)and vary significantly over temperature (Y5V:+22%,-82%over -30˚C to +85˚C range;Z5U:+22%,-56%over +10˚C to +85˚C range).Under some conditions,a nominal 1µF Y5V or Z5U capacitor could have a capacitance of only 0.1µF.Such detrimental deviation is likely to cause Y5V and Z5U capaci-tors to fail to meet the minimum capacitance requirements of the LM27953.The voltage rating of the output capacitor should be 10V or more.All other capacitors should have a voltage rating at or above the maximum input voltage of the application.CIRCUIT BOARD LAYOUTFor optimal,low-noise performance,all capacitors (C IN ,C POUT ,C1,C2)should be placed very close to the LM27953.A solid ground plane should be used for IC and component GND connections.Refer to the LM27953Evaluation Board for an example layout.MICRO SMD MOUNTINGThe LM27953is an 18-bump micro SMD with a bump size of approximately 300micron diameter.The micro SMD pack-age requires specific mounting techniques detailed in Na-tional Semiconductor Application Note 1112(AN-1112).L M 27953 10Physical Dimensionsinches (millimeters)unless otherwise notedTLA18EHA:18-Bump Thin Micro SMD,Large BumpX1=2.098±0.030mm X2=2.403mm ±0.030X3=0.600mm ±0.075mmNational does not assume any responsibility for use of any circuitry described,no circuit patent licenses are implied and National reserves the right at any time without notice to change said circuitry and specifications.For the most current product information visit us at .LIFE SUPPORT POLICYNATIONAL’S PRODUCTS ARE NOT AUTHORIZED FOR USE AS CRITICAL COMPONENTS IN LIFE SUPPORT DEVICES OR SYSTEMS WITHOUT THE EXPRESS WRITTEN APPROVAL OF THE PRESIDENT AND GENERAL COUNSEL OF NATIONAL SEMICONDUCTOR CORPORATION.As used herein:1.Life support devices or systems are devices or systems which,(a)are intended for surgical implant into the body,or (b)support or sustain life,and whose failure to perform when properly used in accordance with instructions for use provided in the labeling,can be reasonably expected to result in a significant injury to the user.2.A critical component is any component of a life support device or system whose failure to perform can be reasonably expected to cause the failure of the life support device or system,or to affect its safety or effectiveness.BANNED SUBSTANCE COMPLIANCENational Semiconductor certifies that the products and packing materials meet the provisions of the Customer Products Stewardship Specification (CSP-9-111C2)and the Banned Substances and Materials of Interest Specification (CSP-9-111S2)and contain no ‘‘Banned Substances’’as defined in CSP-9-111S2.National Semiconductor Americas Customer Support CenterEmail:new.feedback@ Tel:1-800-272-9959National SemiconductorEurope Customer Support CenterFax:+49(0)180-5308586Email:europe.support@Deutsch Tel:+49(0)6995086208English Tel:+44(0)8702402171Français Tel:+33(0)141918790National Semiconductor Asia Pacific Customer Support CenterEmail:ap.support@National SemiconductorJapan Customer Support Center Fax:81-3-5639-7507Email:jpn.feedback@ Tel:81-3-5639-7560LM27953White LED Driver with Four LED Current Sinks and 3/2x Switched Capacitor Boost元器件交易网。