SPS系统总装车间运行方式分析
G公司总装线混流式生产单台份部品配送模式(SPS)研究.doc

G公司总装线混流式生产单台份部品配送模式(SPS)研究
随着精益生产理念在中国各行业的研究以及推广,越来越多的企业尤其是汽车行业采用了混流生产模式,也就是均衡化的生产组织模式。
这种生产模式下,针对业内共同面临课题:如何以更低的物流、库存成本,实现高品质的车辆组装,本文重点对G公司混流式生产模式下,单台份部品配送(Set Parts Supply,简称SPS)模式的运作进行了案例研究,对均衡化生产模式下的部品供给方案的改善进行了探讨。
文章先对均衡化生产模式理论进行阐述,并结合G公司的生产组织模式,从均衡化生产计划的制定作为切入口,阐述了单台份部品配送模式的运作背景。
在此基础上,对部品准时、定量供给模式下订单系统的设定进行了研究,明确了混流生产中订单系统最关键的目标:车辆生产的均衡化与部品供给的均衡化。
随后进一步对单台份部品供给系统中部品分拣中的工程排程、人员配置、物流运输等如何实现均衡化作业进行了探讨。
接下来结合G公司生产中的实际案例,针对新车型导入后,单台份部品配送(SPS)系统工程排程不均衡问题,通过变更作业模式、改善拣货方式、工程优化组合等方式,对整体工程排程进行了改善,实现了工程设置、人员配置的低减。
最后的总结明确了均衡化生产中单台份部品配送(SPS)系统今后的改善方向,并对本文研究中的不足之处进行了总结。
浅析丰田SPS物料供应模式
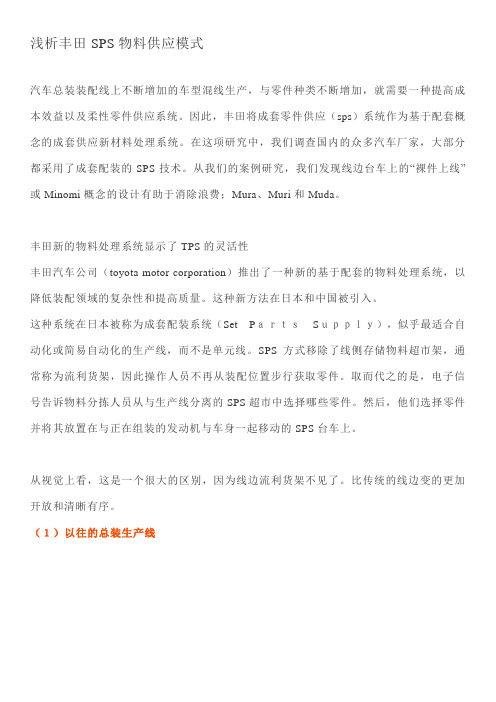
浅析丰田SPS物料供应模式汽车总装装配线上不断增加的车型混线生产,与零件种类不断增加,就需要一种提高成本效益以及柔性零件供应系统。
因此,丰田将成套零件供应(sps)系统作为基于配套概念的成套供应新材料处理系统。
在这项研究中,我们调查国内的众多汽车厂家,大部分都采用了成套配装的SPS技术。
从我们的案例研究,我们发现线边台车上的“裸件上线”或Minomi概念的设计有助于消除浪费;Mura、Muri和Muda。
丰田新的物料处理系统显示了TPS的灵活性丰田汽车公司(toyota motor corporation)推出了一种新的基于配套的物料处理系统,以降低装配领域的复杂性和提高质量。
这种新方法在日本和中国被引入。
这种系统在日本被称为成套配装系统(Set PartsSupply),似乎最适合自动化或简易自动化的生产线,而不是单元线。
SPS方式移除了线侧存储物料超市架,通常称为流利货架,因此操作人员不再从装配位置步行获取零件。
取而代之的是,电子信号告诉物料分拣人员从与生产线分离的SPS超市中选择哪些零件。
然后,他们选择零件并将其放置在与正在组装的发动机与车身一起移动的SPS台车上。
从视觉上看,这是一个很大的区别,因为线边流利货架不见了。
比传统的线边变的更加开放和清晰有序。
(1)以往的总装生产线(2)实施SPS的总装生产线由于零部件选择是在上游进行的,因此装配工可以“关注安装质量”。
随着向客户提供越来越多的功能,多样性和由此产生的复杂性不断增加。
例如,在新系统为当前一代凯美瑞和Avalon引入之前,物流拣货人员必须在24种遮阳板中进行选择。
这一变化意味着,装配作业人员现在将近100%的时间集中在安装部件的增值工作上,因为他们不再需要执行非增值任务,即走几步从流利货架上取回部件。
”装配作业人员保持在一个非常高效的作业步率,几乎100%的增值时间。
”该方式还消除了装配操作员对零件的步行、拉伸容器和搜索零件的浪费。
总装车间SPS系统的优化设计与实现方法

车辆工程技术111机械电子0 引言 在当今个性化的时代,汽车厂家生产的品类越来越多,专线生产单一规格车型的生产模式由于不具有经济性已经退出历史的舞台。
当今主流的汽车生产线,通常混线生产3种以上的车型。
为了解决生产线混流生产与操作工位边物流存储区域不足的矛盾,丰田公司最先在其精益生产模式中提出了有效解决该问题的方法——零部件成套供应(SPS),目前国内的大部分汽车厂也开始学习应用该方法用于总装混流生产中。
1 典型SPS 自动配送系统组成与原理介绍 在SPS 系统布局中,集配区的功能是实现物料的分拣,拣料员按照生产序列单,在集配区将同一台车的各种物料分拣并放置在同一台料车上。
满载的料车从拣料区出发,被送到装配区,装配区的功能是实现物料的装配,装配工按照安装工艺,从料车拿取物料并将其安装在车身上。
每台车的物料拿取装配完成后,空料车被从装配区送返回集配区,进行后续待装配车辆的分拣。
见附图1所示。
总装车间SPS 系统的优化设计与实现方法林 骥,王天生(上汽通用五菱汽车股份有限公司,广西 柳州 545007)摘 要:介绍了汽车制造业总装车间SPS(Set Parts Supply 零部件成套供应)自动实现配送、随行的原理、案例与运行过程中的问题,通过对存在的问题进行深入分析,文章提出了一种提高SPS 自动配送系统运行可靠性的优化设计方法。
关键词:SPS系统;设计;优化 料车从集配区到装配区的配送,随着生产智能化的发展,已由人工配送的方式转向采用AGV 全自动配送的模式,其流程描述如下: (1)AGV 牵引空料车进入集配区域,通过人工进行配料; (2)当人工配料完成后,工作人员通过按钮盒给AGV 发送所配物料上线点(在最后一个分拣工位装2键按钮盒,分别是车门右侧上线点和车门左侧上线点),AGV 牵引2台满料车至上线点缓存区; (3)当上线点行程开关检测到没料车,发送信号给缓存区的AGV,AGV 接到信号自动启动,运行至上线点,AGV 与料车自动脱钩分离; (4)分离后的AGV 单机自动启动,运行至下线处的AGV 等待点进行等待; (5)上线点通过自动上线机构把料车送上随行同步带,让料车跟着生产线同步运行,料车随随同步带运行至下线点,通过下线点自图1 SPS 系统布局动下线机构使料车与随行线分离; (6)料车下线后,通过自动下线机构使料车之间安全连接,发送信号给在等待点的AGV,使AGV 自动启动,AGV 运行至下线点,升降销自动启动与第一台空料车挂钩,挂钩完成,AGV 自动启动,牵引2台空料车沿既定的路线进入集配区,完成一个循环; (7)循环。
SPS物料台车规划

SPS物料台车规划面对当今消费者的日益个性化的趋势,成套配装的概念(Set Parts Supply)的概念日益深入人心,介绍SPS类的文章很多,如何设计SPS物料台车,简单的做个以下介绍!SPS 系统基本概念⌝一、对SPS的理解⌝二、SPS的优缺点⌝三、总装车间SPS箱体设计与构思⌝四、SPS小车设计与思路⌝五、SPS小车之人机标准一、SPS的理解1、SPS是一种成套供应方式,SPS是一个工序变成两部分:首先是分配零部件,将每辆车所需的所有零配件放置到与车辆对应的专用的物料架中,在生产线上物料架与待装配车身同步移动;生产线上的工人只需要把料盒内的零部件安装到对应的车辆上。
这种方式将零部件挑拣工作与装配作业分离,使得工人更专注于转配作业,减少了人为失误。
2、采用SPS的工位,一般都为一些比较小的成套零件。
3、并不是所有的东西都能SPS的。
4、SPS零件和车辆是一一对应的,如果零件质量出现问题,并不能像kanban之类的模式继续使用容器中的零件,sps方式准备的零件数量和使用数是完全相等的,没有对零件质量问题的冗余,所以它对零件质量的要求很高.二、SPS的优缺点SPS的优点:λ上线点减少意味着流减少,冲突减少,浪费减少。
λ库存减少了,更加精益了。
λ节约线边空间。
λ减少物流配送,节约了人员。
λ减少装配员找件时间,专心装配,提高装配质量。
λ缩短线长,提高节拍。
λ由于是一对一的装配,避免了装配出错。
SPS的缺点:λ二次搬运造成工时的损耗。
λ零件品质在二次搬运后的质量问题。
λ对可疑零件后如应急不及时,可能造成停线。
三、总装车间SPS容器设计思路四、SPS小车设计与思路五、SPS小车之人机标准操作距离的人机标准内饰小车尺寸:1500*800*1500 mm⌝以数据参数为依据规范a、人机标准垂直高度<1500mmb、人机标准水平距离<640mmc、顶层多数零件取料高度为1300mmd、个别零件最高取料高度为1450mme、零件最低取料高度为420mm⌝以实际操作作为实践标准1、在以数据参数为参考依据的同时考虑零件的拿放料的操作性,安全性,空间结构性2、最底层移动料盒的取料高度为460mm 一次拿取一个移动料盒即取出了多种零件,减少了拿料次数,提高了工作效率人机学的操作舒适度和便捷度考虑到流水线的快速高频节奏须让物料的取放达到顺畅a.零件摆放的方向性、顺序性零件根据其零件特性(重心,表面材料,装料方向等因素)选择最合适的放置方向和顺序b.料盒的空间余量合理化根据零件在料盒中的最大高度设计料盒相对料车最合适的取放料高度余量c.对于移动料盒无抓手结构的料箱增加辅助扣手件使便于操作人机学的操作习惯性和准确度1.考虑到部分零件的装配的同步性,须让部分物料一起放置提高物料的装配速度2.考虑到部分零件的相似度,须让部分物料分开放置保证操作的准确度。
关于智能物流的应用——总装车间零件配送

车辆工程技术97机械电子1 行业背景 我国是世界上现今为数不多的汽车潜在需求巨大的地区,在过去的十年里,中国的汽车市场一直都是世界最大的汽车贸易市场。
但是我国国产汽车的占有率并不高,在培育了上百家本土汽车品牌的同时,国外各大汽车公司分别抢滩国内市场,通过合资建厂和进口贸易等形式与中国本土汽车企业进行竞争。
因此,我国汽车制造业面临着巨大挑战。
降低成本, 提高市场敏捷性就成为中国本土汽车企业获得市场竞争力的关键。
据有效数据显示, 欧洲汽车制造企业的物流成本占销售额的比例为8%左右;日本汽车厂商这一比例达到5%;而中国汽车生产企业物流成本占销售额的比例要达15%以上[1]。
可见,我国本土汽车企业物流成本是日本车企的3倍,在降低物流成本方面尚有很大提升空间。
2 智能物流的概念 智能物流是利用集成智能化技术,使物流系统能模仿人的智能,具有思维,感知,学习,推理判断和自行解决物流中某些问题的能力。
关于智能物流的应用——总装车间零件配送郭劲松,何长青(广汽乘用车有限公司,广州 511434)摘 要:近年来,随着中国工业的飞速发展和生产技术水平的不断提高,人们对汽车的需求日益扩大。
汽车制造企业得到空前发展的同时,同行之间的竞争越显激烈。
在保证产品品质的前提下,控制企业的成本变得越来越重要。
企业在可控的生产过程中降低成本的空间逐年减少,而在供应生产的零件运输、配送等物流环节却有很大潜力可挖。
所以,积极提升物流效率、采用智能化物流技术来降低物流成本成为又一重要经营手段。
本文主要分享总装车间的零件配送精益化管理及智能化的零件配送形式。
关键词:车间物流;零件配送;精益化管理;智能物流智能物流的未来发展将会体现出四个特点:智能化,一体化和层次化,柔性化与社会化。
在物流作业过程中的大量运筹与决策的智能化;以物流管理为核心,实现物流过程中运输,存储,包装,装卸等环节的一体化和智能物流系统的层次化;智能物流的发展会更加突出“以顾客为中心”的理念,根据消费者需求变化来灵活调节生产工艺;智能物流的发展将会促进区域经济的发展和世界资源优化配置,实现社会化。
三一重工SPS生产方式图解及降本路径分析
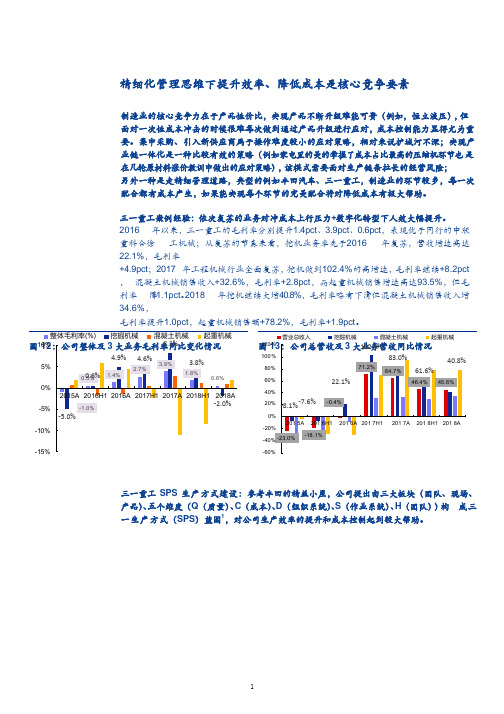
-23.0%
-0.4%
64.7%
45.6%
35.5%
毛利率
31.8%
26.2%
25.8%
24.8%
26.2%
30.1%
30.6%
32.7%
人均创收
134.2
131.4
132.7
145.0
169.2
270.9
321.1
410.1
yoy
37.0%
-2.1%
1.0%
9.3%
16.7%
60.1%
18.5%
27.7%
精细化管理思维下提升效率、降低成本是核心竞争要素
制造业的核心竞争力在于产品性价比,实现产品不断升级难能可贵(例如,恒立液压),但 面对一次性成本冲击的时候很难每次做到通过产品升级进行应对,成本控制能力显得尤为重 要。集中采购、引入新供应商属于操作难度较小的应对策略,相对来说护城河不深;实现产 业链一体化是一种比较有效的策略(例如家电里的美的掌握了成本占比最高的压缩机环节也 是 在几轮原材料涨价教训中做出的应对策略),该模式需要面对生产链条拉长的经营风险; 另外一种是走精细管理道路,典型的例如丰田汽车、三一重工,制造业的环节较多,每一次 配合都有成本产生,如果能实现每个环节的完美配合将对降低成本有极大帮助。
1.6%
3.0%
3.7%
其他 合计
1.7% 100.0%
1.6% 100.0%
2.0% 100.0%
2015A 84.1% 9.1% 4.4% 2.4% 100.0%
2016A 83.0% 8.6% 5.8% 2.6% 100.0%
2017A 83.3% 7.9% 6.0% 2.8% 100.0%
SGMW总装车间SPS运行分析
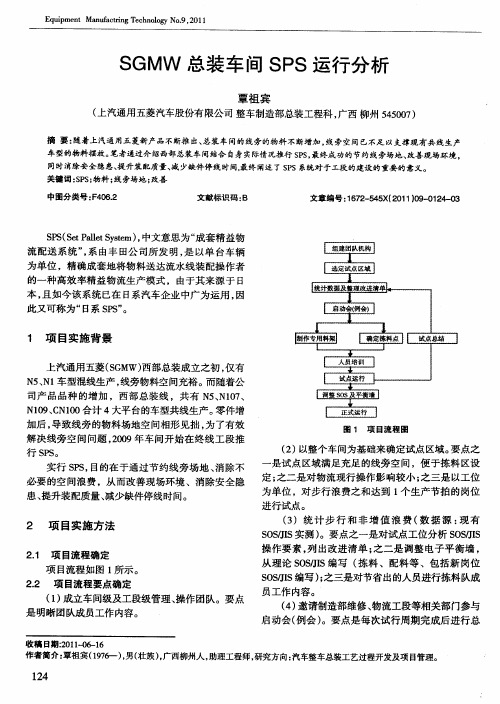
《 装备制造技术)0 1 ) 1 年第 9 2 期
结例会 , 为下次试行作准备 。 () 5 制作专用料架 。要点之一是确定试点物料 ; 同时 , 节约 出来 的空 间 , 建立起 了班组 园地 , 在 班组 园地内放 置了一些桌凳 ,让员工能在一些 短暂 0 n m 能够坐下休息 , 消除 之二是按试点物料形态制作专用料架及料盒 ( 注意 的停线和 2 i 停线休息时间 , 保护零件质量 ) ;之三是 由于线旁料架减少或取消 , 了坐在料架的安全隐患 。 需要为试点工位制作专用料架 、 工具盒 、 腰包等 。 32 提 升装 配品质 - () 6 确定 SS拣料点。 I 要点之一是规划拣料点料 在未实行 S 之前 , S I 每个 岗位都是 自己拿物料 、
架摆放 ; 之二是与物流确定料架上物料摆放 , 便于物
料 配送 。
自己装 配 、 自己检查 , 所有 的品质控制环节 , 全部 由 本 岗位的员工来执行 。而单纯依靠一个人员来 保障
一
道工序的品质 ,尤其对一些劳动强度 比较 大的岗 是 S 拣员工 S s I 操作培训 ; S I O ,S J 之三是各试点工位 位 , 在每天数 百次的重复操 作 中 , 相对而言 , 出错 的 s s I 操作培训。 o /S J 几率还是 比较高的。 () 8 试点运行。 要点之一是初次试点运行使用班 而通过进行 S , S I 将一些关键 岗位和十分消耗体
此又 可称 为 “ 日系 S s 。 P ”
1 项 目实施背景
上汽通用五菱(G w) s M 西部总装 成立之初 , 仅有
N 、1 5 N 车型混线生产 , 线旁物料空间充裕 。 而随着公 司产品品种 的增加 ,西部总装 线 ,共有 N 、 17 5N 0 、 Nl9 C 0 o 、 N10合计 4大平 台的车型 共 线生 产 。 件 增 零 加后 , 导致线旁 的物料场地空间相形见拙 , 了有效 为
汽车总装车间SPS实施运行探讨

1 ) 按 零部 件种 类摆 放 : 是在 S P S 集 配 区 内将 所 有车 型 的零 部 件 按 照种 类 进行 区分 , 比如 , 所 有车 型 的 C柱饰 板 都 在某 一 区域集 中放 置 。这种 布置 可 使得 部品放 置 比较 紧密 , 节 省空 间 , 但 作业 者选 取部 品时 的步 行距 离 比较 长。 2) 按 车 型摆 放 : 是在 S P S 集 配 区内将部 品按 车型摆 放 的方 式, 具体讲 , 就 是 把 某一 车 型 的所 有 零 部件 都 放 在 一 个 区 域 , 另外 车 型 的零 部 件 放置 在 另外 的区 域 。这种 置 方 式可 使 得 零部 件放 置 比较 宽松 , 浪费 空 间 , 但作 业 者选 取 零 部件 时 的步 行距 离较 短 。
一
种先进 的 物流输 送 方式 。
关键词
S P S ; 物料 ; 信 息化 : 防错 文 献标 识码 : A 文 章编 号 : 1 6 7 1 — 7 5 9 7( 2 0 1 3 )1 2 — 0 1 6 8 一 O 1
中图分 类号 : 0 4 6 8 . 2
S P S( S E T P A R T S S U P P L Y) 来 自于 日本 丰 田 , 是一 种 物料 单 辆 份 向生产 线 准 时化 配 送 的 方式 ,由于 S P S区临 近 生 产 线 , S P S区 的物 流 作 业人 员 按 照 生 产 指示 ( 该 指示 根 据 车辆 顺 序 生 成 并 按 下线 实绩 控 制 进度 )在 货架 上 拣 取 一套 零 部件 放 于专 用 的物 流 周转 台 车 中 , 并送 到线 边 , 实 现零 部 件 小批 量 多 频 次 的 输送 , 循 环流转 。
ห้องสมุดไป่ตู้
随行配料系统(SPS)布局方案设计
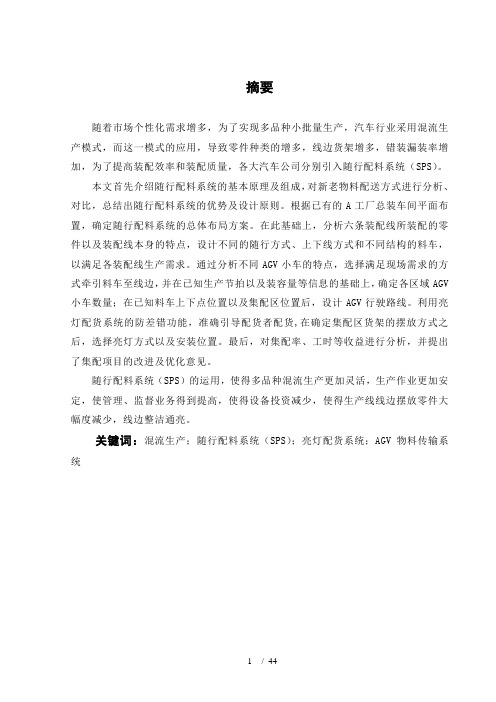
摘要随着市场个性化需求增多,为了实现多品种小批量生产,汽车行业采用混流生产模式,而这一模式的应用,导致零件种类的增多,线边货架增多,错装漏装率增加,为了提高装配效率和装配质量,各大汽车公司分别引入随行配料系统(SPS)。
本文首先介绍随行配料系统的基本原理及组成,对新老物料配送方式进行分析、对比,总结出随行配料系统的优势及设计原则。
根据已有的A工厂总装车间平面布置,确定随行配料系统的总体布局方案。
在此基础上,分析六条装配线所装配的零件以及装配线本身的特点,设计不同的随行方式、上下线方式和不同结构的料车,以满足各装配线生产需求。
通过分析不同AGV小车的特点,选择满足现场需求的方式牵引料车至线边,并在已知生产节拍以及装容量等信息的基础上,确定各区域AGV 小车数量;在已知料车上下点位置以及集配区位置后,设计AGV行驶路线。
利用亮灯配货系统的防差错功能,准确引导配货者配货,在确定集配区货架的摆放方式之后,选择亮灯方式以及安装位置。
最后,对集配率、工时等收益进行分析,并提出了集配项目的改进及优化意见。
随行配料系统(SPS)的运用,使得多品种混流生产更加灵活,生产作业更加安定,使管理、监督业务得到提高,使得设备投资减少,使得生产线线边摆放零件大幅度减少,线边整洁通亮。
关键词:混流生产;随行配料系统(SPS);亮灯配货系统;AGV物料传输系统AbstractWith the increasing market demand for personalized, in order to achieve more varieties of small batch production, the automotive industry using mixed production mode, and the application of this model, leading to an increase in types of parts, wire shelf edge increases, the wrong equipment installed leak rate increase, in order to improve assembly efficiency and assembly quality, the major car companies were introducing set part supply (SPS).This article introduces the basic principles of the set part supply (SPS) and its composition, comparing and analyzing the new and old material distribution methods, summarizing as well the advantages and design principles of the system (SPS). The overall layout of the set part supply (SPS) program is determined on the basis of the existing a factory assembly shop layout. Six assembly lines and their characteristics are analyzed with the aim of designing different patterns and structures to meet the demand of production lines. The characteristics of different AGV cars are analyzed, the AGV car with the pattern top traction is selected, sending the materials to the line by using the mode of tape navigation.Based on the known production rhythm and assembly capacity, the number of AGV cars is fixed. The AGV route is designed after confirming the position of the points on the material cars and the assembly location. The workers can accurately distribute the parts by making use of the light picking system. After fixing the mode of arrangement, the light-on pattern and installation position can be selected. Finally, the earnings such as assembly rates, working hours are calculated, and then some ideas and suggestions are proposed towards the assembly project.With the use of the set part supply (SPS), the multi-species mixed production becomes more flexible, the operation more stable, and the management and supervision business is improved. Meanwhile, reduce greatly the equipment investment and the number of the parts on the line side, which make the line side more clean and tidy.Keywords:mixed production; set part supply (SPS); the lights picking system; AGV cars目录第一章概论................................................... - 1 -1.1 论文研究的意义............................................. - 1 -1.2 随行配料系统(SPS)国内外现状.............................. - 1 -1.3 论文的主要内容............................................. - 2 - 第二章随行配料系统(SPS)介绍................................ - 3 -2.1 随行配料系统(SPS)组成.................................... - 4 -2.2 随行配料系统(SPS)原理.................................... - 4 -2.3 随行配料系统(SPS)优势分析................................ - 5 -2.4 随行配料系统(SPS)设计要求................................ - 5 -2.5 本章小结................................................... - 6 - 第三章随行配料系统(SPS)布局方案设计........................ - 6 -3.1 A工厂总装车间平面布置图.................................... - 7 -3.2 随行配料系统(SPS)布局设计方案............................ - 7 -3.3 本章小结................................................... - 8 - 第四章料车设计............................................... - 9 -4.1 料车的设计原则............................................. - 9 -4.2 六个区域料车设计........................................... - 9 -4.2.1 HC1料车.............................................. - 9 -4.2.2 HC2料车............................................. - 11 -4.2.3 PDB料车............................................. - 12 -4.2.4 POR料车............................................. - 13 -4.2.5 MV1料车............................................. - 15 -4.2.6 MV2料车............................................. - 16 -4.3 本章小结.................................................. - 17 - 第五章 AGV物料传输系统....................................... - 17 -5.1 AGV物料传输系统设计原则................................... - 17 -5.2 AGV小车设计............................................... - 18 -5.2.1 AGV小车选择......................................... - 18 -5.2.2 AGV数量确定......................................... - 18 -5.3 AGV行驶路线确定........................................... - 20 -5.4 本章小结.................................................. - 21 - 第六章亮灯配货系统.......................................... - 22 -6.1 亮灯配货系统应用背景及原理................................ - 22 -6.2 集配区零件布置............................................ - 23 -6.2.1 布置原则............................................. - 23 -6.2.2 布置信息............................................. - 23 -6.2.3 平面布置图确定....................................... - 24 -6.3 亮灯方式及安装位置........................................ - 26 -6.4 本章小结.................................................. - 28 - 第七章随行配料系统(SPS)成效............................... - 29 -7.1 XX公司A工厂总装车间集配信息.............................. - 29 -7.2 总体收益.................................................. - 30 - 第八章结论.................................................. - 31 -结束语....................................................... - 32 -致谢......................................................... - 33 -参考文献..................................................... - 34 -附录1 ....................................................... - 34 -第一章概论在现今汽车生产中,如何利用并不宽裕的物料存储区域,提高装配线的柔性和工作效率,这是现如今每一个汽车公司未来发展的方向。
车间sps运作流程
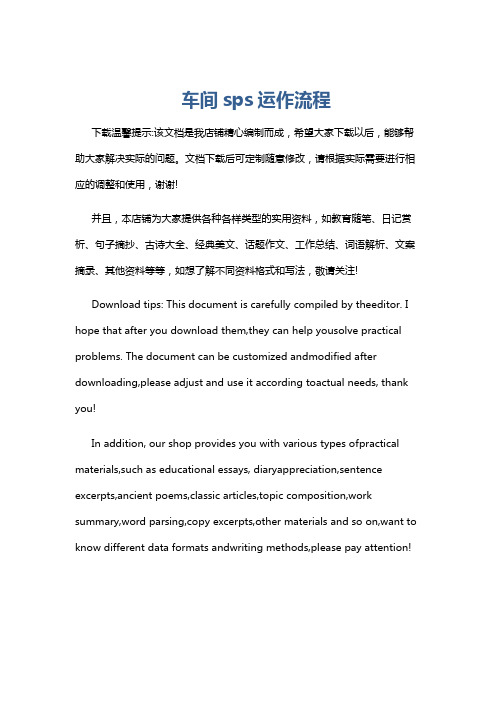
车间sps运作流程下载温馨提示:该文档是我店铺精心编制而成,希望大家下载以后,能够帮助大家解决实际的问题。
文档下载后可定制随意修改,请根据实际需要进行相应的调整和使用,谢谢!并且,本店铺为大家提供各种各样类型的实用资料,如教育随笔、日记赏析、句子摘抄、古诗大全、经典美文、话题作文、工作总结、词语解析、文案摘录、其他资料等等,如想了解不同资料格式和写法,敬请关注!Download tips: This document is carefully compiled by theeditor. I hope that after you download them,they can help yousolve practical problems. The document can be customized andmodified after downloading,please adjust and use it according toactual needs, thank you!In addition, our shop provides you with various types ofpractical materials,such as educational essays, diaryappreciation,sentence excerpts,ancient poems,classic articles,topic composition,work summary,word parsing,copy excerpts,other materials and so on,want to know different data formats andwriting methods,please pay attention!SPS(Set Parts Supply)是一种零部件供应方式,它将每个工位所需的零部件按照生产顺序放置在一个特定的容器中,然后将这些容器按照生产顺序送到各个工位。
SPS系统总装车间运行方式分析
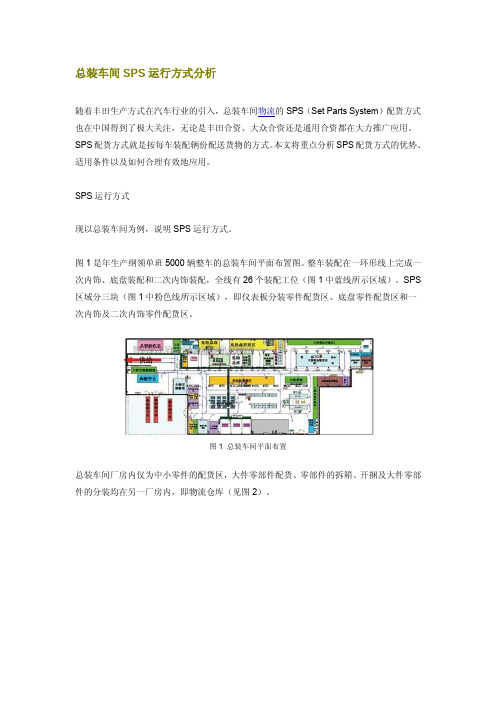
总装车间SPS运行方式分析随着丰田生产方式在汽车行业的引入,总装车间物流的SPS(Set Parts System)配货方式也在中国得到了极大关注,无论是丰田合资、大众合资还是通用合资都在大力推广应用。
SPS配货方式就是按每车装配辆份配送货物的方式。
本文将重点分析SPS配货方式的优势、适用条件以及如何合理有效地应用。
SPS运行方式现以总装车间为例,说明SPS运行方式。
图1是年生产纲领单班5000辆整车的总装车间平面布置图。
整车装配在一环形线上完成一次内饰、底盘装配和二次内饰装配,全线有26个装配工位(图1中蓝线所示区域)。
SPS 区域分三块(图1中粉色线所示区域),即仪表板分装零件配货区、底盘零件配货区和一次内饰及二次内饰零件配货区。
图1 总装车间平面布置总装车间厂房内仅为中小零件的配货区,大件零部件配货、零部件的拆箱、开捆及大件零部件的分装均在另一厂房内,即物流仓库(见图2)。
图2 物流仓库平面布置1.配货顺序总装车间的物流系统在信息控制系统指导下,有条不紊地从仓库货架取出所需零件,按SPS 配货方式送到指定工位,配货顺序如下:(1)中央控制室(CCR)根据市场分析及订单情况安排生产计划,并将生产计划的车辆顺序信息向总装车间情报中心传递。
(2)车辆顺序信息传到总装车间情报中心,由情报信息员根据实际工位查找相应信息指示卡。
(3)情报信息员将信息指示卡投递到SPS供应管理板处。
(4)物流配货人员从SPS供给管理板处获取信息选取配货指示票,配货指示票上标有某个车型在某个工程装配零件的种类和数量。
(5)物流人员按照配货指示票到SPS区配货,放在相应的台车上,物流人员将部品放到运输台车上。
(6)配完后放在供给待发区,物流人员将零件供给到生产线的起始位置。
(7)物流人员将空台车返回到零件供给待发区,通过SPS方式配货完成。
2. 物料配送的四个步骤在图3的SPS物料及信息流程图中我们可以看到,所有的物料都是经过四个步骤完成运送的:接收物料需求信息(图3中①);按需求信息进行配货(图3中②);将配货送到装配线的接收端(图3中③);随装配线完成装配工序(图3中④)。
车间sps运作流程
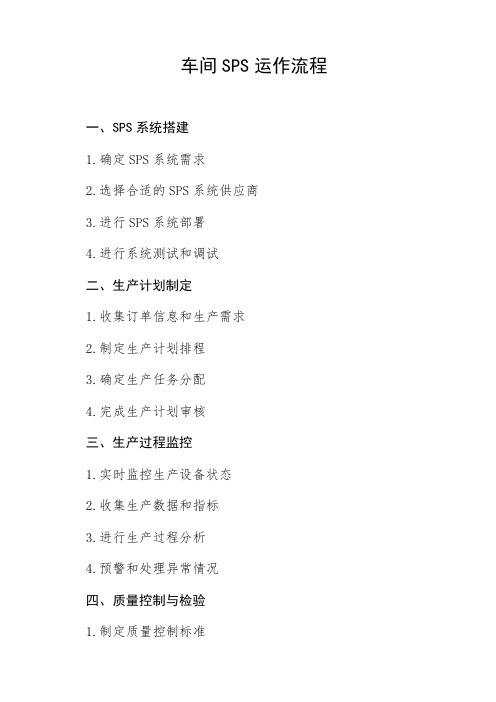
车间SPS运作流程
一、SPS系统搭建
1.确定SPS系统需求
2.选择合适的SPS系统供应商
3.进行SPS系统部署
4.进行系统测试和调试
二、生产计划制定
1.收集订单信息和生产需求
2.制定生产计划排程
3.确定生产任务分配
4.完成生产计划审核
三、生产过程监控
1.实时监控生产设备状态
2.收集生产数据和指标
3.进行生产过程分析
4.预警和处理异常情况
四、质量控制与检验
1.制定质量控制标准
2.进行生产过程质量监控
3.进行产品质量检验
4.处理质量异常问题
五、故障排除与维护
1.实施设备故障排查
2.进行设备维护保养
3.制定设备维护计划
4.处理设备故障和修复
六、数据分析与优化
1.收集生产数据
2.进行数据分析和挖掘
3.发现生产优化机会
4.实施生产流程优化措施。
总装车间SPS运行方式分析

总装车间SPS运行方式分析
肖伶俐
【期刊名称】《汽车制造业》
【年(卷),期】2009(000)19X
【摘要】本文通过分析SPS配货方式的运行方式.优势和适用条件.得出SPS运行方式并不适用于所有总装车间的结论:SPS运行方式最适用的是批量小、品种多且差异件多的整车试制线.或一些零件比较小.而零件在运送过程中不易受到损伤的总成件分装。
【总页数】3页(P40-40,42,43)
【作者】肖伶俐
【作者单位】机械工业第九设计研究院
【正文语种】中文
【中图分类】U468.1
【相关文献】
1.spss教学中相关分析的实例探究——基于spss分析的科研项目申报政策导引功能实证研究 [J], 周宇剑
2.SGMW总装车间SPS运行分析 [J], 覃祖宾
3.总装车间SPS系统的优化设计与实现方法 [J], 林骥;王天生;
4.浅谈某总装车间机械化输送分析 [J], 胡丽军
5.浅谈某总装车间机械化输送分析 [J], 胡丽军
因版权原因,仅展示原文概要,查看原文内容请购买。
SPS在发动机装配线的应用效果浅析
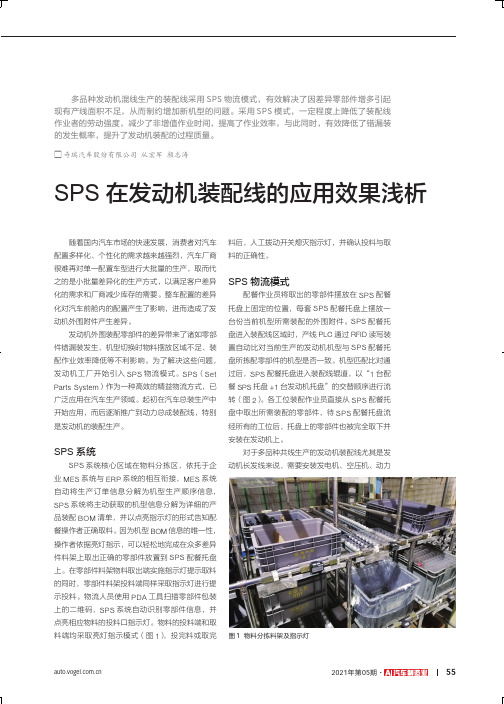
图1 物料分拣料架及指示灯
55
2021年第05期・
转向泵、装饰罩支架及皮带等众多外围附件,同一种外围附件根据机型不同存在不同型号或装与不装的差异。
在未实施SPS物流模式之前,采用多品种料架的方式来规避时有发生的错装零部件、漏装零部件的问题。
但随着差异零部件逐渐增多,现有产线的线边面积已经无法满足新增多品种料架的需要。
实施SPS模式后,线边不再摆放任何零部件料架,线边面积不再成为产线增加差异机型混线生产的制约因素。
同时,干净、整洁的作业环境也影响着作业者产生更多的积极情绪,有益于团队士气提升和产品装配质量的提升。
图2 SPS配餐托
盘与发动机托盘
交替流转
图3 每个SPS配餐托盘摆放一台份发动机外围装配零部件
05期。
浅析丰田SPS物料供应模式
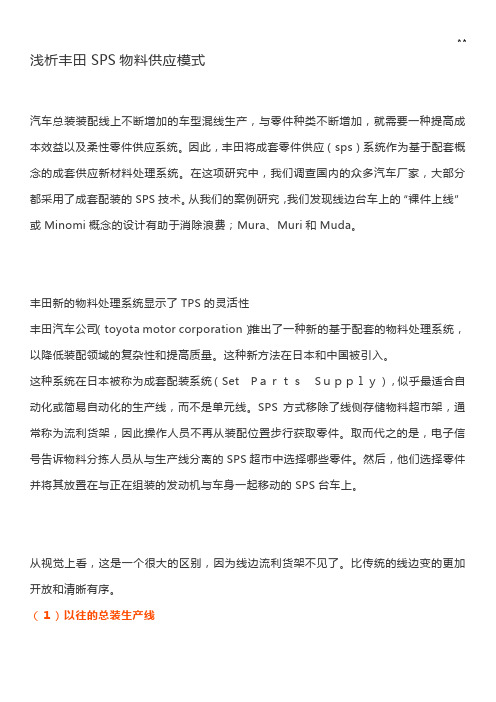
浅析丰田SPS物料供应模式汽车总装装配线上不断增加的车型混线生产,与零件种类不断增加,就需要一种提高成本效益以及柔性零件供应系统。
因此,丰田将成套零件供应(sps)系统作为基于配套概念的成套供应新材料处理系统。
在这项研究中,我们调查国内的众多汽车厂家,大部分都采用了成套配装的SPS技术。
从我们的案例研究,我们发现线边台车上的“裸件上线”或Minomi概念的设计有助于消除浪费;Mura、Muri和Muda。
丰田新的物料处理系统显示了TPS的灵活性丰田汽车公司(toyota motor corporation)推出了一种新的基于配套的物料处理系统,以降低装配领域的复杂性和提高质量。
这种新方法在日本和中国被引入。
这种系统在日本被称为成套配装系统(Set PartsSupply),似乎最适合自动化或简易自动化的生产线,而不是单元线。
SPS方式移除了线侧存储物料超市架,通常称为流利货架,因此操作人员不再从装配位置步行获取零件。
取而代之的是,电子信号告诉物料分拣人员从与生产线分离的SPS超市中选择哪些零件。
然后,他们选择零件并将其放置在与正在组装的发动机与车身一起移动的SPS台车上。
从视觉上看,这是一个很大的区别,因为线边流利货架不见了。
比传统的线边变的更加开放和清晰有序。
(1)以往的总装生产线(2)实施SPS的总装生产线由于零部件选择是在上游进行的,因此装配工可以“关注安装质量”。
随着向客户提供越来越多的功能,多样性和由此产生的复杂性不断增加。
例如,在新系统为当前一代凯美瑞和Avalon引入之前,物流拣货人员必须在24种遮阳板中进行选择。
这一变化意味着,装配作业人员现在将近100%的时间集中在安装部件的增值工作上,因为他们不再需要执行非增值任务,即走几步从流利货架上取回部件。
”装配作业人员保持在一个非常高效的作业步率,几乎100%的增值时间。
”该方式还消除了装配操作员对零件的步行、拉伸容器和搜索零件的浪费。
总装车间SPS运行方式分析
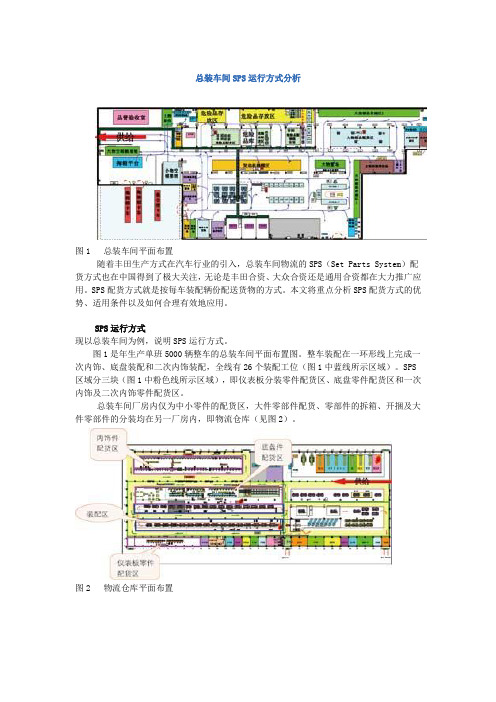
总装车间SPS运行方式分析图1 总装车间平面布置随着丰田生产方式在汽车行业的引入,总装车间物流的SPS(Set Parts System)配货方式也在中国得到了极大关注,无论是丰田合资、大众合资还是通用合资都在大力推广应用。
SPS配货方式就是按每车装配辆份配送货物的方式。
本文将重点分析SPS配货方式的优势、适用条件以及如何合理有效地应用。
SPS运行方式现以总装车间为例,说明SPS运行方式。
图1是年生产单班5000辆整车的总装车间平面布置图。
整车装配在一环形线上完成一次内饰、底盘装配和二次内饰装配,全线有26个装配工位(图1中蓝线所示区域)。
SPS 区域分三块(图1中粉色线所示区域),即仪表板分装零件配货区、底盘零件配货区和一次内饰及二次内饰零件配货区。
总装车间厂房内仅为中小零件的配货区,大件零部件配货、零部件的拆箱、开捆及大件零部件的分装均在另一厂房内,即物流仓库(见图2)。
图2 物流仓库平面布置1.配货顺序总装车间的物流系统在信息控制系统指导下,有条不紊地从仓库货架取出所需零件,按SPS配货方式送到指定工位,配货顺序如下:(1)中央控制室(CCR)根据市场分析及订单情况安排生产计划,并将生产计划的车辆顺序信息向总装车间情报中心传递。
(2)车辆顺序信息传到总装车间情报中心,由情报信息员根据实际工位查找相应信息指示卡。
(3)情报信息员将信息指示卡投递到SPS供应管理板处。
(4)物流配货人员从SPS供给管理板处获取信息选取配货指示票,配货指示票上标有某个车型在某个工程装配零件的种类和数量。
(5)物流人员按照配货指示票到SPS区配货(KITTTING),放在相应的台车上,物流人员将部品放到运输台车上。
(6)配完后放在供给待发区,物流人员将零件供给到生产线的起始位置。
(更先进的方式是AGV 自动输送至相应工位。
(7)物流人员将空台车返回到零件供给待发区,通过SPS方式配货完成。
2. 物料配送的四个步骤在图3的SPS物料及信息流程图中我们可以看到,所有的物料都是经过四个步骤完成运送的:接收物料需求信息(图3中①);按需求信息进行配货(图3中②);将配货送到装配线的接收端(图3中③);随装配线完成装配工序(图3中④)。
总装车间SPS系统的优化设计与实现方法
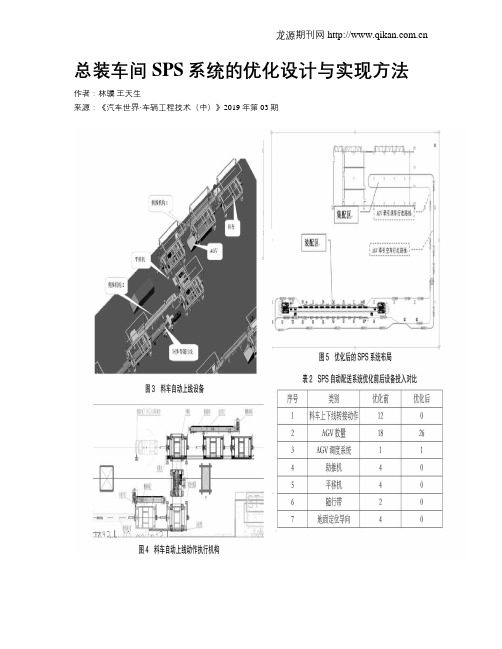
总装车间SPS系统的优化设计与实现方法作者:林骥王天生来源:《汽车世界·车辆工程技术(中)》2019年第03期摘要:介绍了汽车制造业总装车间SPS(Set Parts Supply 零部件成套供应)自动实现配送、随行的原理、案例与运行过程中的问题,通过对存在的问题进行深入分析,文章提出了一种提高SPS自动配送系统运行可靠性的优化设计方法。
关键词:SPS系统;设计;优化0 引言在当今个性化的时代,汽车厂家生产的品类越来越多,专线生产单一规格车型的生产模式由于不具有经济性已经退出历史的舞台。
当今主流的汽车生产线,通常混线生产3种以上的车型。
为了解决生产线混流生产与操作工位边物流存储区域不足的矛盾,丰田公司最先在其精益生产模式中提出了有效解决该问题的方法——零部件成套供应(SPS),目前国内的大部分汽车厂也开始学习应用该方法用于总装混流生产中。
1 典型SPS自动配送系统组成与原理介绍在SPS系统布局中,集配区的功能是实现物料的分拣,拣料员按照生产序列单,在集配区将同一台车的各种物料分拣并放置在同一台料车上。
满载的料车从拣料区出发,被送到装配区,装配区的功能是实现物料的装配,装配工按照安装工艺,从料车拿取物料并将其安装在车身上。
每台车的物料拿取装配完成后,空料车被从装配区送返回集配区,进行后续待装配车辆的分拣。
见附图1所示。
料车从集配区到装配区的配送,随着生产智能化的发展,已由人工配送的方式转向采用AGV全自动配送的模式,其流程描述如下:(1)AGV牵引空料车进入集配区域,通过人工进行配料;(2)当人工配料完成后,工作人員通过按钮盒给AGV发送所配物料上线点(在最后一个分拣工位装2键按钮盒,分别是车门右侧上线点和车门左侧上线点),AGV牵引2台满料车至上线点缓存区;(3)当上线点行程开关检测到没料车,发送信号给缓存区的AGV,AGV接到信号自动启动,运行至上线点,AGV与料车自动脱钩分离;(4)分离后的AGV单机自动启动,运行至下线处的AGV等待点进行等待;(5)上线点通过自动上线机构把料车送上随行同步带,让料车跟着生产线同步运行,料车随随同步带运行至下线点,通过下线点自动下线机构使料车与随行线分离;(6)料车下线后,通过自动下线机构使料车之间安全连接,发送信号给在等待点的AGV,使AGV自动启动,AGV运行至下线点,升降销自动启动与第一台空料车挂钩,挂钩完成,AGV自动启动,牵引2台空料车沿既定的路线进入集配区,完成一个循环;(7)循环。
汽车行业SPS简述

汽车总装线旁边一般都有线边库,线边库会存放半小时、一小时或两小时左右的零部件。
汽车总装是混线生产,多种车型轮流总装,这样线边库就需要存放多种车型的零部件。
这是个个性化的时代,汽车也是这样,汽车型号、规格越多,线边库管理越复杂。
线边库遇到了挑战,所以改变思路。
是要改变存放方法吗?不全是,更重要的是改变物料上线方式。
对于专用大件,采用JIS同步顺序供应方式,不在线边设库存。
对于中小专用件,可以采用这种同步顺序供应吗?可以,只是更复杂,而且走得更远,不仅同步上线,而且还与生产线同步随行,这种方式就是SPS。
SPS,Set Parts Supply,零部件成套供应。
SPS这个词最先是丰田公司用的,部分其他汽车公司现在也用SPS这种叫法,另外一些公司将这种单辆份成套供应、物料与生产线同步随行的方式称之为为“Kitting”等。
SPS是向生产线单辆份成套供料的一种零部件配送方式。
这种方式取消了线边的物料存储料架,改为与生产线同步随行的台车料架。
刚开始,SPS成套供应主要应用在在内饰线和车门线等,因为这两条线的零部件具有体积大、重量轻、配置多、颜色件多等特点,线边存放占用面积较大,操作人员拣选麻烦。
随着对SPS的应用越来越熟悉,慢慢就扩展到底盘线、发动机装配线等。
为什么SPS这种方式越来越多地被汽车企业采用呢?首先,由于SPS是单辆份成套供应,所以,降低了取料错误的可能性,提高了装配质量和装配效率。
中国汽车行业增长较快,车间新手较多,这种降低拣料、装配复杂度的方法能有效减少新手的学习时间。
其次,SPS单辆份成套供应还降低了生产线操作人员拣选物料的时间。
同时,由于零部件是与生产线同步随行,物料箱可以放在操作人员身边,不需要走出装配区域去取物料,这同样提升了装配效率。
装配效率的提升会导致装配节拍的降低,这对生产线资源紧缺的汽车总装来讲非常重要,因为同样的生产线在不扩产的情况下可以生产出更多的车辆了。
再次,由于SPS采用同步顺序上线和物料随行方式,所以节省了线边库的占用。
- 1、下载文档前请自行甄别文档内容的完整性,平台不提供额外的编辑、内容补充、找答案等附加服务。
- 2、"仅部分预览"的文档,不可在线预览部分如存在完整性等问题,可反馈申请退款(可完整预览的文档不适用该条件!)。
- 3、如文档侵犯您的权益,请联系客服反馈,我们会尽快为您处理(人工客服工作时间:9:00-18:30)。
总装车间SPS运行方式分析
随着丰田生产方式在汽车行业的引入,总装车间物流的SPS(Set Parts System)配货方式也在中国得到了极大关注,无论是丰田合资、大众合资还是通用合资都在大力推广应用。
SPS配货方式就是按每车装配辆份配送货物的方式。
本文将重点分析SPS配货方式的优势、适用条件以及如何合理有效地应用。
SPS运行方式
现以总装车间为例,说明SPS运行方式。
图1是年生产纲领单班5000辆整车的总装车间平面布置图。
整车装配在一环形线上完成一次内饰、底盘装配和二次内饰装配,全线有26个装配工位(图1中蓝线所示区域)。
SPS 区域分三块(图1中粉色线所示区域),即仪表板分装零件配货区、底盘零件配货区和一次内饰及二次内饰零件配货区。
图1 总装车间平面布置
总装车间厂房内仅为中小零件的配货区,大件零部件配货、零部件的拆箱、开捆及大件零部件的分装均在另一厂房内,即物流仓库(见图2)。
图2 物流仓库平面布置
1.配货顺序
总装车间的物流系统在信息控制系统指导下,有条不紊地从仓库货架取出所需零件,按SPS 配货方式送到指定工位,配货顺序如下:
(1)中央控制室(CCR)根据市场分析及订单情况安排生产计划,并将生产计划的车辆顺序信息向总装车间情报中心传递。
(2)车辆顺序信息传到总装车间情报中心,由情报信息员根据实际工位查找相应信息指示卡。
(3)情报信息员将信息指示卡投递到SPS供应管理板处。
(4)物流配货人员从SPS供给管理板处获取信息选取配货指示票,配货指示票上标有某个车型在某个工程装配零件的种类和数量。
(5)物流人员按照配货指示票到SPS区配货,放在相应的台车上,物流人员将部品放到运输台车上。
(6)配完后放在供给待发区,物流人员将零件供给到生产线的起始位置。
(7)物流人员将空台车返回到零件供给待发区,通过SPS方式配货完成。
2. 物料配送的四个步骤
在图3的SPS物料及信息流程图中我们可以看到,所有的物料都是经过四个步骤完成运送的:接收物料需求信息(图3中①);按需求信息进行配货(图3中②);将配货送到装配线的接收端(图3中③);随装配线完成装配工序(图3中④)。
图3 SPS物料及信息流程图
SPS运行方式的优势
1.上线点减少
一辆份零件被分成有限的几部份,分别在几个上线点与整车随行。
上线点的减少意味着在线旁的物流线路变得简单、清晰了。
简单的物流线路意味着交叉点的减少、冲突点的降低。
2.线旁物料面积减少
由于整车所需装配的零件均按辆份与车身随行,线旁的物料面积就不需要了。
以往由于生产纲领提高所造成的线旁物料面积的矛盾也就不存在了。
3.通道面积可能削减
如果能够整线实现SPS配货方式,SPS配货的上线点均设在线的端部,那么在整线中部工位没有物料需求,通道也就可以削减或取消了。
4.防错功能
装配线上操作工人的工作内容由原来的挑捡零件和装配零件两道工序变为只有装配零件,而且由于所装配零件有明显差异,操作工人不会出现错装;由于每个随行的料架均是按辆份配送的,所以如果装配后料架上有剩余零件,则为漏装,操作工人可及时发现和纠正错误。
5.减轻操作工人的劳动强度
操作工人不需要去线边的料架去取零件。
由于料架是随行的,操作工人可以就近取件,减少了操作工人频繁走动所增加的劳动强度。
6.提高了劳动生产率
由于操作工人减少了取件及挑捡零件的用时,减少了每个装配零件所需的工时,使得整线提高节拍成为可能。
SPS运行方式的局限
1.节省面积问题
无庸置疑,在SPS配货方式中,最大限度地节省了装配线旁的物料面积,但是它增加了配货面积,这部分面积是采用传统送货方式时所不需要的。
从整个车间角度上看,总面积没有节省反倒是增加了。
以前面所提厂项为例,16?000m2的总面积中,装配车间生产面积为4?880 m2,物流配货面积为7?186 m2,通道面积为2?926 m2,其他辅助面积为1?008 m2。
从上面的数据可以看出物流配货面积约是装配生产面积的1.47倍(不包括通道面积)。
在另两个丰田厂项中,一个厂总装车间装配生产面积约为13?600 m2,而物流面积达到24?600 m2,装配与物流面积之比约为1 : 1.8;另一个厂总装车间装配生产面积约为41?000 m2,而物流面积达61?200 m2,装配与物流面积之比约为1 : 1.49。
而我们以往采用送货制生产方式时,设计的装配生产面积与物流面积之比是按1 : (0.6~0.8)考虑的。
物流面积是非生产面积,是不创造价值的面积。
物流面积的增加大大地增加了新厂建设投资和生产厂的场地占用成本,实际上最终增加了产品的成本。
这与丰田的精益思想是相悖的。
2.防错功能问题
这里的防错功能包括两个方面,一方面是防装错,即防止差异较小的零件装错车;另一方面是防漏装。
在同一条生产线上生产的车型,既使是多品种,也都是一个系列的车型,也就是说,在同一条生产线上生产的车型中的大部分零件及总成件都是一样的。
为了少量差异零件的防错装而把所有零件都放在料车上,从成本和操作难度上综合考虑,是否必要,值得我们探究。
3.配送零件质量保证问题
由于配送零件是按辆份送到每个车旁的,也就是说没有备份,当装配过程中出现质量问题(如零件不合格、损坏或遗失)时,由于没有备份零件,没有线旁的物料供给,那么这辆车只能随其他车一起下线,再到返修区进行装配了。
这样大大就增加了返修区的工作量,增加了返
修面积。
因此,SPS运行方式对入库零件质量要求非常高,要求配送的零件合格率为100%,并且保证在运送过程中,无质量事故。
这对于同种零件成批送货相对容易保证,而对于按辆份配送的方式,由于要将结构各异的零件都放在同一配送小车上,保证起来会有一定的困难。
4.提高生产效率问题
这个问题应该从两个方面讨论:
一个方面是零件搬运问题。
SPS运行方式造成了零件的“二次搬运”,将零件取出送到配送区,再从配送区取出零件放到随行料架上,比传统的送货方式增加了一次零件配送,是属于丰田生产方式所说的“7种浪费”之一,可见其是影响生产效率的。
另一个方面是人在装配过程中的取件用时问题。
SPS运行方式一直强调操作工人从随行料架上取件比线旁取件所走的距离短。
事实上,笔者在实行SPS运行方式的总装车间看到的是随行料架放在两工位之间,操作工人到随行料架取件至少要走出1m远,与到线边料架相比并不近。
因此,通过随行料架取件和到线旁料架取件对工人装配效率的影响区别是微乎其微的。
5.SPS运行方式适用的零件问题
SPS运行方式是将整车零部件按辆份放在随行料架上,但我们很难想象大型总成件,如保险杠、座椅和轮胎等也放在随行料架上,这些零件会使随行料架变得很大;另外还有一些有分装内容的总成件,如仪表板、车门、动力总成和风挡玻璃等也不会采用随行料架送到装配工位的。
由此可见,SPS运行方式适用的是中小型的零件,如成套锁、门把手和内护板等件。
SPS的适用条件
SPS运行方式最大的优势体现在不同种类车型的差异件的取用和判断上,最大限度地减少了操作工人的判断失误。
SPS运行方式并不适用于大批量的整车生产方式。
SPS运行方式更适用的是批量小、品种多且差异件多的整车试制线,或一些零件比较小,而零件在运送过程中不易受到损伤的总成件分装。