唐钢超薄热轧带钢生产线的质量控制技术
热轧钢板内控质量技术要求

热轧钢板内控质量技术要求一、管理目的为提升产品实物质量,满足用户需求,确保不合格品得到有效的识别和控制,规范热轧钢板的检验、试验、判定、放行等环节控制,特制订热轧钢板内控质量技术要求。
二、适用范围本内控标准适用于公司热轧钢板的生产检验与内控质量判定。
三、引用标准国家标准GB/T 700-2006《碳素结构钢》、GB/T 711-2008《优质碳素结构钢热轧钢板和钢带》、GB/T 1591-2008《低合金高强度结构钢》、GB/T 3274-2007《碳素结构钢和低合金结构钢热轧厚钢板和钢带》、GB 712-2011《船舶及海洋工程用结构钢》、《CCS材料与焊接规范2012》等。
四、内控质量技术要求1、化学成分热轧钢板Q235B、Q345B、45、船体用结构钢板化学成分应分别符合下表的规定。
表1: Q235B主要化学成分注:钢中残余元素铬、镍、铜含量应各不大于0.30%。
表2: Q345B主要化学成分注:钢中残余元素铬、铜、镍含量应各不大于0.30%,铌含量应不大于0.07%,钒含量应不大于0.15%,钛含量应不大于0.20%,钼含量应不大于0.10%,氮含量应不大于0.012%。
表3:45钢主要化学成分注:钢中残余元素铬含量应不大于0.20%,镍含量应不大于0.30%,铜含量应不大于0.25%。
表4:船舶及海洋工程用钢板主要化学成分要求注:①所有等级的钢均应符合:C%+1/6Mn%≤0.40%。
②钢中残余铜含量应不大于0.35%,铬、镍的残余含量各应不大于0.30%。
2、外形、尺寸技术要求2.1热轧钢板尺寸及允许偏差应符合下表的规定。
表5:钢板的厚度允许偏差(N类)单位:mm表6:切边钢板的宽度允许偏差单位:mm注:不切边钢板宽度允许偏差由供需双方协商严格执行CCS49号通函船舶及海洋工程用钢板至少选两条线进行厚度测量,每条线至少选3个测量点,按规定的测量方法计算钢板的平均厚度,测量的平均厚度不得小于钢板名义厚度。
热轧钢板质量控制技术的研究

热轧钢板质量控制技术的研究随着工业化的普及,钢材的需求量不断增加,其产量也呈逐年上升的趋势。
钢材在应用中经常作为结构材料,承担着重要的力学性能,要求其稳定性、高精度和高强度等方面都能得到满足。
在制造过程的过程中,热轧钢板是钢材的重要组成部分,其质量对钢的整体质量有着重要的影响。
为了确保热轧钢板的质量,在生产制造时就需要采用一系列的质量控制技术与措施。
热轧钢板质量控制技术主要包括两方面的内容,即控制生产制造条件和应用热力学计算模型。
在生产制造条件方面,需要对各项参数进行控制和调整,如调整轧制温度、轧辊压力、轧制速度等等。
这些参数的细致调整与正确设置,对于提高热轧钢板质量有着至关重要的作用。
当然,这也需要在生产实践中不断摸索和积累经验,才能取得稳步的进步。
在应用热力学计算模型方面,主要以建立数学模型为主要手段,对热轧钢板的制造过程进行计算模拟。
这种方法已经在现代制造业得到广泛运用,并且取得了不错的效果。
通过模型计算分析,可以更加准确地预测热轧钢板的性能表现,进一步掌握制造生产的规律性和内在机理。
在这两种方法中,应用热力学计算模型的方法可能取得了更加显著的成果。
而且,随着现代计算模拟技术的不断完善,预测精度也在逐步提高。
此外,这种方法对于生产实践的指导也具有实质性的意义,能够更加准确地揭示热轧钢板质量不佳的根源并寻找到对立于之的方法。
不难看出,热力学计算模型的应用对质量控制的改进与提升有着重要的作用。
需要指出的是,热轧钢板质量控制技术要想发挥出最好的效益,离不开必要的设备与机械改进,如轧机设备的升级和改进、轧辊的设计与制造改进等等。
只有这些设备得到不断优化和升级,才能配合使用热力学计算模型和人工控制措施来实现对热轧钢板质量的优化与提升。
因此,在研究热轧钢板质量控制技术时,需要将制造过程、设备与机械改进和理论分析结合起来,形成一个有机的整体。
总而言之,针对热轧钢板的质量控制技术研究需要在各个方面进行着手,比如从实际生产操作中理论模拟、机械设备改进和人工控制措施等方面出发,积极摸索、提高和完善。
热轧薄板生产线设备功能精度管理

二级 单 位 (生产 厂 )的设 备 管 理 部 门 、点检 中心 、工 艺管 理 部 门 、公 司设 备 管理 部 门及 工 艺 管理 部 门 , 管理 流 程见 图 1。
(5)定检测 日期 :按照检测周期要求确定设备 功能 、精 度项 目的检 测 日期 。
5 设 备 功 能 、精 度项 目的管控 (1)设 备功能 、精 度项 目的 日常管理 :日常管
理 主要 包括功能 、精度项 目的 日常检查和恢复两 个方 面。二级单位和公 司设备功能 、精度管理部 门按照“五定”要求 ,对纳入管理 的设备功能 、精度 项 目进行检查 ,对 于设备功能不投入 和设备功能 、 精度超标项 目,在设备 日常维护和周 期性检修期 间安 排 恢 复 。对 于 精度 管 理 不达 标 的单 位 由主 管
生 产 线 生 产 的热 轧 薄 板 目前 有 几 十个 品 种 , 涵 盖 了 SPCC、SPHC等 普 通 板 材 以及 工具 钢 、汽 车 大 梁 钢等 特 殊用 途 的板 材 。薄规 格 产 品是 1810线 的 主导 产 品 。设 备 功 能 、精 度 管 理 是 设 备 管 理 的 重 要 组 成 部 分 和 预 防性 维 修 体 系 的 重 要 内容 ,设 备 功 能投 入 和保 持 对 1810线 产 品质 量 有 较 大 的影 响 ,因此 ,必须确定生产线 的设备功能、精度项 目, 对 其进 行 重点 管理 。
(2)精度 :是指设备原设计或经修复 、改造 、改
善后 必 须 达 到 的精 确程 度 。凡 纳 入管 理 的设 备 精 度 管 理 项 目 ,因 1项 或 几 项 未 达 到 原 设 计 标 准 ,而 影 响 产 品 的质 量 、品种 、成 材 率 、产 量 等 主要 生 产 技术 指 标 ,称 为 精度 超标 。
超薄规格热轧板卷稳定轧制及板形控制技术

超薄规格热轧板卷稳定轧制及板形控制技术栗建辉;田亚强【摘要】唐钢UTSP生产线通过对板坯温度控制、压下分配、轧制速度、板形控制等进行研究和实践,开发了薄板坯连铸连轧生产线辊底式加热炉蓄热式燃烧技术与超薄规格板卷稳定轧制技术,提升了板形控制能力,提高了超薄规格板卷轧制稳定性和板形质量,实现了薄板坯连铸连轧生产线1.0 mm超薄规格热轧板卷的大批量稳定生产。
通过技术升级和改造,目前1.0 mm超薄规格单轧程产量可达555 t,规格比例达到60%以上,且带钢板形及表面质量满足品种开发和产品质量要求。
【期刊名称】《金属世界》【年(卷),期】2014(000)004【总页数】6页(P56-61)【作者】栗建辉;田亚强【作者单位】河北联合大学河北省现代冶金技术重点实验室,河北唐山063009; 河北钢铁股份有限公司唐山分公司,河北唐山063009;河北联合大学河北省现代冶金技术重点实验室,河北唐山063009【正文语种】中文薄板坯连铸连轧生产线具有超薄规格产品生产的技术优势,但由于超薄规格热轧板卷生产技术难度高,国内薄板坯连铸连轧生产线的产品规格主要集中在1.6 mm以上,韩国东部制铁公司薄板坯连铸连轧生产线(FTSR)的产品规格集中在1.4 mm 以上,也未实现超薄规格热轧板卷的大批量稳定生产。
唐钢UTSP生产线在原有设备、工艺基础上,通过应用对板坯温度控制、压下分配、轧制速度、板形控制等进行研究,开发了薄板坯连铸连轧生产线辊底式加热炉蓄热式燃烧技术与超薄规格板卷稳定轧制等先进技术,提高了超薄规格板卷轧制稳定性和板形质量,实现了1.0 mm超薄规格热轧板卷的大批量稳定生产,适应了当前市场的需求。
UTSP生产线工艺流程及关键装备、技术唐钢1810线于2001年引进的UTSP薄板坯连铸连轧生产线,是国内第一条应用半无头轧制工艺的热轧带钢生产线,生产线的布置如图1所示,其连铸采用意大利DANIELI公司的FTSC连铸机,生产厚度65~90 mm铸坯;加热炉采用美国BRICMONT公司的辊底式均热炉,炉长230.195 m;轧机采用2RM+5FM布置,粗轧机由意大利DANIELI公司设计,精轧机由日本三菱重工设计,具有动态PC和ORG功能;卷取区采用了IHI株式会社设计制造的高速飞剪、双地下卷取机。
热轧薄规格带钢塔形产生原因及控制措施
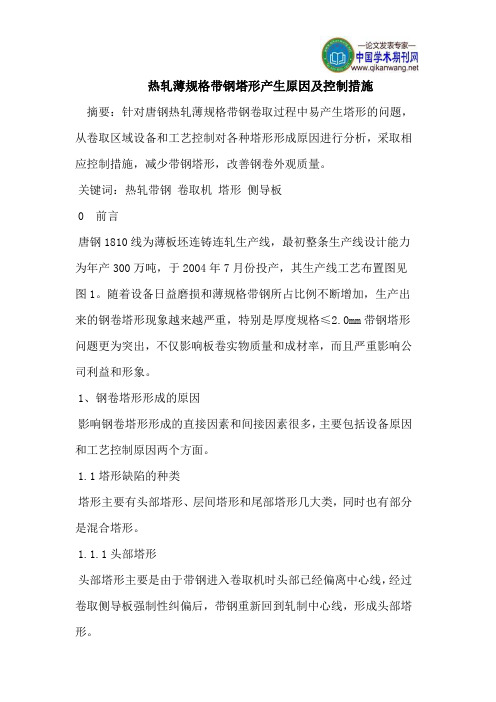
热轧薄规格带钢塔形产生原因及控制措施摘要:针对唐钢热轧薄规格带钢卷取过程中易产生塔形的问题,从卷取区域设备和工艺控制对各种塔形形成原因进行分析,采取相应控制措施,减少带钢塔形,改善钢卷外观质量。
关键词:热轧带钢卷取机塔形侧导板0 前言唐钢1810线为薄板坯连铸连轧生产线,最初整条生产线设计能力为年产300万吨,于2004年7月份投产,其生产线工艺布置图见图1。
随着设备日益磨损和薄规格带钢所占比例不断增加,生产出来的钢卷塔形现象越来越严重,特别是厚度规格≤2.0mm带钢塔形问题更为突出,不仅影响板卷实物质量和成材率,而且严重影响公司利益和形象。
1、钢卷塔形形成的原因影响钢卷塔形形成的直接因素和间接因素很多,主要包括设备原因和工艺控制原因两个方面。
1.1塔形缺陷的种类塔形主要有头部塔形、层间塔形和尾部塔形几大类,同时也有部分是混合塔形。
1.1.1头部塔形头部塔形主要是由于带钢进入卷取机时头部已经偏离中心线,经过卷取侧导板强制性纠偏后,带钢重新回到轧制中心线,形成头部塔形。
1.1.2层间塔形层间塔形主要是由于末架精轧机与卷取之间建立的张力不稳定,造成带钢在辊道上左右摆动。
1.1.3尾部塔形尾部塔形主要是由于在轧制过程中钢带跑偏严重,侧导板强制纠偏,形成弧形路径,在轧制过程中钢带未回到中心线上,末架精轧机抛钢张力消失后,带钢在辊道上左右摆动。
1.2设备原因1.2.1夹送辊上下辊之间不水平夹送辊上下辊之间不水平分为两种情况。
第一,安装新夹送辊时,由于上下辊之间轴线不平行,造成在卷钢过程中容易形成塔形。
第二,使用一段时间后,沿辊身长度方向磨损不均匀,造成上下辊面不水平,在卷钢过程中极易形成塔形。
1.2.2芯轴与助卷辊之间不水平当带钢头部进入卷取机时,头部几圈在助卷辊压力下紧紧缠绕在芯轴上,如果助卷辊与芯轴之间不水平,带钢受到助卷辊压力不一致,造成带钢头部发生横向移动形成塔形[1]。
1.2.3侧导板控制异常侧导板运行速度过快或者运行速度过慢,均会导致带钢对中难以控制,容易出现塔形。
唐钢薄板坯热轧带钢轧制工艺特点及质量控制分析

冶舭
全一QUALr Y ONTRoL FHoT—RoI 皿 r C o J
dton lpr c s ii a o e s,te m an q l y c tolw a s ito c d. h i uai onr y n r du e t
由于薄板 坯 连铸 连 轧 具 有 的 多种 技 术 、能 源 、
效益 上 的优势 ,现 已投 入生产 的项 目多 达 5 0余 个 ,
中国建成 或在 建 的 已达 l 0个 以上 。该 技 术 突 破 了
度制 度首先 是 薄板 坯不 经冷却 到室温再 升温 ,薄 板
坯 出连铸 机 后 , 内部 温 度 通 常 在 10 o 00 C以上 ,表
Ab t c :Th h n sa o t u u a t g a d r l n r d ci n l e i n te s c mp r d wi h r — sr t a e t i lb c n i o sc si n o l g p o u t i n Ta g S e li o a e t te ta n n i o n h
响 ,保 证产 品具 有均 一 的尺 寸 、板形 、金 相组 织 和
每 一相 邻炉 底辊 的辊 环交错 布 置 ,板坯 在炉 内保 温
时并 不 固定 在一 个位 置 ,而是 往 复运动 ,这 都保 证
了板 坯不会 有 “ 印” 产 生 。 黑
22 变 彩控 制 .
性 能 ,所 以生产 中的 保温 和调温 技术非 常重 要 。
热轧带钢生产工艺及常见质量问题探讨
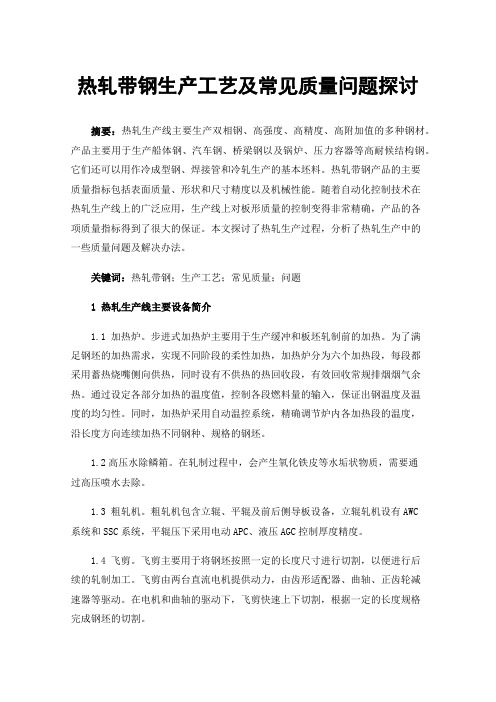
热轧带钢生产工艺及常见质量问题探讨摘要:热轧生产线主要生产双相钢、高强度、高精度、高附加值的多种钢材。
产品主要用于生产船体钢、汽车钢、桥梁钢以及锅炉、压力容器等高耐候结构钢。
它们还可以用作冷成型钢、焊接管和冷轧生产的基本坯料。
热轧带钢产品的主要质量指标包括表面质量、形状和尺寸精度以及机械性能。
随着自动化控制技术在热轧生产线上的广泛应用,生产线上对板形质量的控制变得非常精确,产品的各项质量指标得到了很大的保证。
本文探讨了热轧生产过程,分析了热轧生产中的一些质量问题及解决办法。
关键词:热轧带钢;生产工艺;常见质量;问题1热轧生产线主要设备简介1.1 加热炉。
步进式加热炉主要用于生产缓冲和板坯轧制前的加热。
为了满足钢坯的加热需求,实现不同阶段的柔性加热,加热炉分为六个加热段,每段都采用蓄热烧嘴侧向供热,同时设有不供热的热回收段,有效回收常规排烟烟气余热。
通过设定各部分加热的温度值,控制各段燃料量的输入,保证出钢温度及温度的均匀性。
同时,加热炉采用自动温控系统,精确调节炉内各加热段的温度,沿长度方向连续加热不同钢种、规格的钢坯。
1.2高压水除鳞箱。
在轧制过程中,会产生氧化铁皮等水垢状物质,需要通过高压喷水去除。
1.3 粗轧机。
粗轧机包含立辊、平辊及前后侧导板设备,立辊轧机设有AWC系统和SSC系统,平辊压下采用电动APC、液压AGC控制厚度精度。
1.4 飞剪。
飞剪主要用于将钢坯按照一定的长度尺寸进行切割,以便进行后续的轧制加工。
飞剪由两台直流电机提供动力,由齿形适配器、曲轴、正齿轮减速器等驱动。
在电机和曲轴的驱动下,飞剪快速上下切割,根据一定的长度规格完成钢坯的切割。
1.5 精轧机。
精轧机是一种高精度轧制工艺,利用液压AGC等自动控制和补偿系统,通过液压系统和轧辊轧制板坯。
它主要由电动机、联轴器、减速器等驱动和传动,以获得高精度的轧制件外观和尺寸。
1.6卷取机。
采用全液压三助卷辊强力卷取机,采用了无极涨缩试卷筒和自动踏步控制AJC系统。
唐钢超薄热带生产线板形控制

2 唐钢超薄 热带板形控制工艺方 法 .
2 1P . C角度控 制
少、 生产周期短 、 成本低及 自动化程度高等一系列
显著优 势 。唐钢考 虑 到调整 自己的产 品结构 , 意 与
P c轧机通过工作辊和支撑辊成对交叉形成的
交角 来保 证 良好 的辊缝 ,通 过 改变 交 叉 角度 来 控
口布置 M ( G 多功能仪表 , 用于检测精轧机出 口板形
和 板 凸度) P 与 C角 结合 使 用 。 当带钢头 部 到达 № (G的布 置位 置 见 图 1 时 ,G将 检测 的板 凸度 反 M ) M 馈 到 二 级控 制 ,二 级根 据 轧 制力 和 温 度 动态 调 节
⑧^
呈皇! 蔓塑_
1 .前言
薄 板坯 连 铸 连 轧 是 2 纪 8 代 中期 国外 0世 0年 开 发 成 功 的 当今 世 界 最 先 进 的带 钢 生 产 技 术 , 与 传 统 热轧 带 钢 生产 工 艺相 比 ,具有 流 程 短 、投 资
中 F  ̄F 用 P 1 3采 C控 制 ,2 3采 用 正弯辊 ,4 R  ̄F F ~ F 用正 、 5采 负弯 辊 ,4 F 用 OG 在线 磨辊) F 、5采 R( 。
田 回 回 回 回
图 1唐钢热轧薄板厂精 轧机组和 检测 示意图
的 原 因
影 响带 钢板 形 的因 素很 多 , 也很 复杂 , 根 本 其 原 因 是 由于 金属 在 发生 塑 性变 形 时变 形 物体 内变
2 2弯 辊 BN E . ED R控制 唐钢 热 轧 薄 板厂 R ~F 用 正 弯 辊 ,4 5 2 3采 F  ̄F 采用正、 负弯辊 。弯辊 力 如下 :
是保 证板 形 良好 的基本 条件 。唐钢 热板 厂在 F M出
唐钢热轧板带成形技术及控制措施

【 关键词 】 板形控制 ;热轧带钢 ;在线监测
1 引 言
随着我 国冶金 行业 的进 步与发展 ,对带钢 热连轧机组生产产品 的质量要求 也越来越 高,如何控制 热轧板带钢 板形,现己成为了当 前冶金行业 急需解 决的问题之 一。板 凸度、平直度、局部高点 以及 边 部减 薄组 成了板形,同时它也是有轧辊的弹性变形、原料形状等 决定的。对 冷轧后的凸度 和平 直度有关键影响的是热轧后的带材凸 度 ,由于 目前需求客户对冷轧薄板的平直度 以及凸度都有很高的要 求 ,所 以热轧板 带钢板形控制技术逐步得到重视 。传统的总轧制压 力控 制 阀 、 轧辊 的 局 部 冷 却 法 以及 变 压 下 量 法 等 等 这 些 虽 然 能 对 控 制板形起到一定的作用,但是他的随动性不好,所 以,这就要研究 人员再进 行更深 一步的探 究。 随着近几年冶金行业 国外 因素 的影响 , 我 国 的 武 钢 和 宝钢 已经 在 板 形 控 制 技 术 上 达 到 了 国 际水 平 。 唐钢 1 4 5 0 m m热带钢半连轧机与 1 9 9 2年年底 己基本建成 ,轧机 的装备水平较低 , 其 中F 卜F 6精轧机组没有增 设任何板形控制系统 。 为使热轧板厂的年产量达到 1 0 0万 t的设 计水平 ,产 品的板形达到 标准要求 ,为将来冷轧厂的生产打好基础 ,在唐钢现有 的热轧机条 件下选择合适的板形控制方法十分必要 。本文介绍 了国内外的热轧 板、带钢板形控制技术的状况,并结合唐钢 实际提 出了建 议。 2 国外热轧板 带钢板形控制技术现状 由于近来对板带钢 的横 向厚度精度 的要求更严 ,为 此,世 界工 业发达 国家在不 断地研 究开发新设备 、新工 艺,以改善板 带材 的板 形。 特别是 进入 8 O年代 以来 , 开发 了各种新型轧机和 新的控 制技术 , 几种有效 的方法 正在扩大推广应用 ,在这方 面 日本 和德 国均处在领 先地位 。国外板形控制最有效的方法有以下几种: 2 . 1 弯 辊 法 在 改善板 形的一切 措施 中,液压弯辊是最基本的方法,而且其 他方法也 离不开液压弯辊的配合 。 液压弯辊大体上可分为三种类型,
超薄热带连铸连轧生产线钢水质量控制
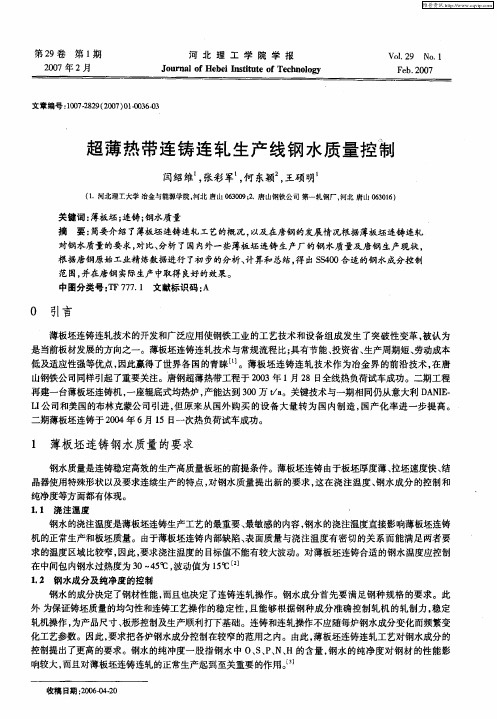
维普资讯
第1 期
闫绍维, 超薄热带连铸连轧生产线钢水质量控制 等:
3 7
Hale Waihona Puke 121 有:元素含量的控制 .. 葺 众所周知 钢中 sP元素含量对铸坯 的裂纹敏感性有 明显影响。P元素在结晶过程中偏析倾 向大 , 、 也使 钢 的晶界脆化 , 从而增大钢 的裂纹倾 向。此外 , 薄板坯中发生的碳化物 、 硫化物 和氮化物的沉淀析 出与普通
关键词: 薄板坯 ; 连铸 ; 钢水质量
摘 要: 简要介绍 了薄板坯连铸连轧工艺的概况, 以及在唐钢的发展情况根据薄板坯连铸连轧
对钢水质量的要求, 对比、 了国内外一些薄板坯连铸生产厂的钢水质量及唐钢生产现状 , 分析 根据唐钢原始工业精炼数据进行 了初步的分析、 计算和总结, 出S 40 得 S0 合适的钢水成分控制
性能, 特别是对作 汽车面板和高压容器板的薄板影响尤为显著。表 1 显示出了 c 、 jc、n等有色金属元 u N 、 rS 素对超低碳钢表面质量的影响 , 由此表可见, 随着有色金属元素含量的增加 ; 陷增多。钢中的 A、 、 b 缺 lN N 等 元素在钢 中形成 AN N C 1 、b N等氮化物 , 固时氮化物析出 , 凝 可引起板坯表面裂纹 。此外 , 氮含量高 , 钢材抗时 效性能差 , 冷加工性能也受影响。因此薄板坯连铸工艺要求钢中微量元素含量小于表 2给定的数值。
1 薄板坯连铸钢水质量 的要求
钢水质量是连铸稳定高效的生产高质量板坯的前提条件。薄板坯连铸由于板坯厚度薄、 拉坯速度快 、 结 晶器使用特殊形状 以及要求连续生产的特点 , 对钢水质量提出新的要求 , 这在浇注温度 、 钢水成分 的控制和
热轧带钢表面质量控制要点及其前沿技术

热轧带钢表面质量控制要点及其前沿技术通过对热轧带钢表面质量缺陷的分析研究发现,由于热轧板带材生产工艺的特殊性,以及加上大的轧制力和低温轧制技术,这些特点使得板形缺陷-氧化皮压入成为板带材的主要表面缺陷。
因此除板形及尺寸方面的问题外,防止出现氧化皮成为压入板带钢表面质量控制的重点。
1、控制热轧板带氧化铁皮压入的主要技术措施保证和提高热轧板带面质量应当从钢铁生产的全流程着手。
首先必须保证钢质,避免大块非金属夹杂物的出现和充分脱气,对于薄规格产品,这点尤为重要。
为防止氧化皮压下,目前采用的方法主要有以下几个方面:①控制好轧制温度,包括板带坯料出炉温度、进入精轧前的温度以及轧辊表面温度等;②增加除鳞次数,即在精轧机组内也安装除鳞设备;③适当增加换辊次数及在线磨辊,保证工作辊的表面光洁度。
2、热轧带钢表面质量检测系统的研制及实践热轧带钢表面质量检测通常只对带钢尾部一段采用目视检查方式。
这种只对带钢尾部很短的一段区域进行表面质量抽检的检测方式,不能及时反映带钢表面质量的全貌,给下道工序生产带来困难,造成用户质量异议。
另外,由于缺乏有效的带钢表面质量检测手段,无法提供轧辊更换优化指导,不能进行准确的产品质量等级判定,造成不必要的产品降级。
近年来国内外一些研究机构都致力于热轧带钢表面质量在线检测系统的研制,比较有代表性的是以VAISIAS为代表的线扫描摄像机检测系统和以Parsytec为代表的面扫描摄像机检测系统。
宝钢分公司热轧厂为了保证热轧产品表面质量,满足下道工序生产和市场对高质量产品的需求,于2003年在2050mm热轧线上安装了一套Parsytec公司的带钢表面质量在线检测装置,取得了良好的使用效果。
2004年又在1580mm热轧成功投入运行一套带钢表面质量检测装置,为热轧厂产品质量控制提供了高效的控制手段。
①表面检测系统原理与构成Parsytec公司的带钢表面质量在线检测装置采用CCD高速摄像系统,其主要设备包括上、下表面检测单元,图像数据转换单元,图像数据处理单元,图像数据记录单元,网络设备,配电系统,操作终端,系统调整终端,打印设备及开发维护设备,辅助设备等。
唐钢1810线热轧薄规格产品的开发与生产实践
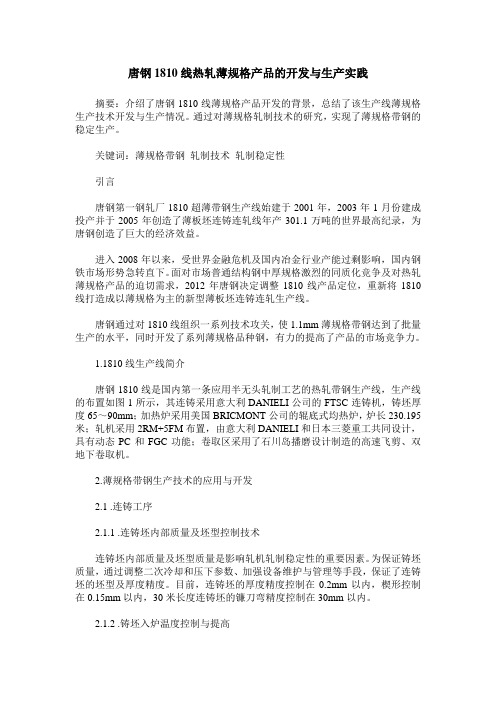
唐钢1810线热轧薄规格产品的开发与生产实践摘要:介绍了唐钢1810线薄规格产品开发的背景,总结了该生产线薄规格生产技术开发与生产情况。
通过对薄规格轧制技术的研究,实现了薄规格带钢的稳定生产。
关键词:薄规格带钢轧制技术轧制稳定性引言唐钢第一钢轧厂1810超薄带钢生产线始建于2001年,2003年1月份建成投产并于2005年创造了薄板坯连铸连轧线年产301.1万吨的世界最高纪录,为唐钢创造了巨大的经济效益。
进入2008年以来,受世界金融危机及国内冶金行业产能过剩影响,国内钢铁市场形势急转直下。
面对市场普通结构钢中厚规格激烈的同质化竞争及对热轧薄规格产品的迫切需求,2012年唐钢决定调整1810线产品定位,重新将1810线打造成以薄规格为主的新型薄板坯连铸连轧生产线。
唐钢通过对1810线组织一系列技术攻关,使1.1mm薄规格带钢达到了批量生产的水平,同时开发了系列薄规格品种钢,有力的提高了产品的市场竞争力。
1.1810线生产线简介唐钢1810线是国内第一条应用半无头轧制工艺的热轧带钢生产线,生产线的布置如图1所示,其连铸采用意大利DANIELI公司的FTSC连铸机,铸坯厚度65~90mm;加热炉采用美国BRICMONT公司的辊底式均热炉,炉长230.195米;轧机采用2RM+5FM布置,由意大利DANIELI和日本三菱重工共同设计,具有动态PC和FGC功能;卷取区采用了石川岛播磨设计制造的高速飞剪、双地下卷取机。
2.薄规格带钢生产技术的应用与开发2.1 .连铸工序2.1.1 .连铸坯内部质量及坯型控制技术连铸坯内部质量及坯型质量是影响轧机轧制稳定性的重要因素。
为保证铸坯质量,通过调整二次冷却和压下参数、加强设备维护与管理等手段,保证了连铸坯的坯型及厚度精度。
目前,连铸坯的厚度精度控制在0.2mm以内,楔形控制在0.15mm以内,30米长度连铸坯的镰刀弯精度控制在30mm以内。
2.1.2 .铸坯入炉温度控制与提高连铸入炉坯温度关乎出钢节奏及铸坯的加热温度的高低。
唐钢1810mm生产线热轧带钢宽度精度控制
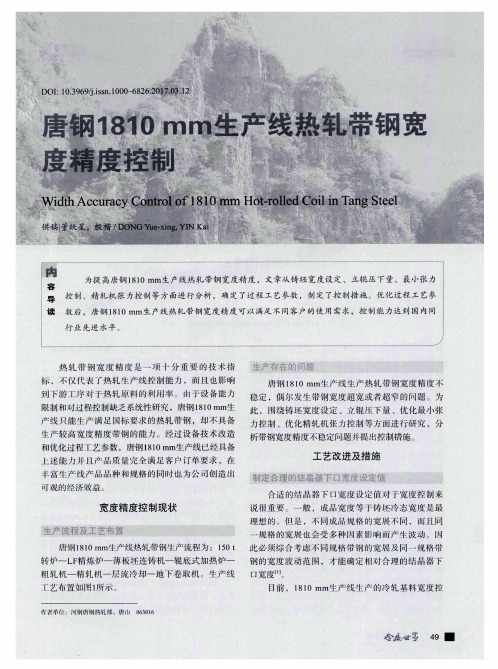
终 点数 据档 案 ,重 点跟 踪不 同压 下终点 对铸 坯宽 度
唐钢l 8 1 0 mm生 产线立辊 轧 机安装 在Rl 粗 轧机
影 响 。数据 分析表 明 ,0 段压 下终 点 比3 段 压下终 点 前 面 ,配 有液 压缸 。受 立辊 设备 结构 和板 坯厚 度 的
铸 坯宽度 / I , 3 mm,这对于生 产过程 中通 过结 晶器在 双重 影 响 ,立 辊 不能无 限 幅的压 下 ,必须 有合适 的
图l 唐钢1 8 1 0 mm生产线工艺布置 图
制 范 同是 公 称宽 度 + ( 0 ~1 8 mm) 这样 的控 制 范
线 凋宽实 现不 同乐下 终 点铸坯 宽 发控制 非常 重要 ,
虽 然符合 生产 制造部 要求 的控 制标 准 ,但 常常 会造 能够在很 大程度上提高板坯 宽度精度 。
格到 1 . 6 mm规格的成品宽 展已经超过 了l 0 mm。而这
一
度控制范 隔是公称宽度+ ( 5 ~ 1 2 mm) ,提高冷轧工序成 材率0 . 3 %,全年为公司创造经济效益近2 0 0 万元 。
扇 形段 压 下终 点对 板坯 费度 的影 响
唐钢 l 8 1 0 mm生 产线连 铸 区域扇形 段压 下采 用 动态软 压下 控制 ,主要 作用 是提 高铸坯 内部 质量 。
粗 轧机一 精 轧机一 层 流冷却一 地 下卷取 机 。牛产线
口宽 度 ” 】 。
工 艺布置如 l 所示 、
作并 位 :河钢f I l f 钢热轧部 .府1 ¨ 0 6 3 0 1 6
目前 ,l 8 l 0 mm生产线 生产 的冷轧 基料宽 度控
含蓬 荨
4 9 ■
念海世誓
热轧产品质量的控制

引言:热轧产品是一种常见的金属材料,广泛应用于建筑、汽车制造、机械制造等领域。
而热轧产品的质量是保证其使用性能的关键。
在上一篇文章中,我们已经介绍了热轧产品质量控制的一些基本知识,本文将继续探讨热轧产品质量控制的相关内容,希望为读者更好地了解和掌握热轧产品质量控制的方法和技术。
概述:热轧产品质量控制是指通过合理的生产工艺和控制措施,确保热轧产品达到所需的质量指标。
热轧产品的质量控制是一项复杂的工作,需要涉及材料、设备、工艺等多个方面因素的综合考虑,以保证产品的物理性能、化学性能、表面质量等指标都能满足要求。
正文:1.材料控制1.1选择合适的原材料:热轧产品的质量首先要从原材料入手,选择合适的原材料对于确保产品的质量至关重要。
对于不同用途的热轧产品,可以采用不同的原材料标准和级别,以满足不同的技术要求。
1.2原材料的质量把控:在材料进厂前,需要对原材料进行严格的质量检查,包括外观检查、化学成分分析等。
对于不符合要求的原材料应及时退回或进行处理,以确保产品的质量。
1.3优化熔炼工艺:热轧产品的质量受到熔炼工艺的影响,通过优化熔炼工艺可以提高材料的均匀性和纯度,从而提高产品的质量。
1.4控制锭材的质量:锭材是热轧产品的初加工材料,通过对锭材的质量进行控制,可以有效提高产品的均匀性和内部质量。
1.5热处理工艺的控制:热处理工艺对于热轧产品的性能具有重要影响,需要控制好热处理工艺的参数,以保证产品的力学性能、硬度、耐腐蚀性等指标符合要求。
2.设备控制2.1设备的维护与调试:热轧产品的质量与设备的性能密切相关,因此,定期对设备进行检修、维护和调试是确保产品质量的关键步骤。
工厂应制定相应的设备维护和检修计划,及时处理设备故障,确保设备始终处于良好的运行状态。
2.2温度控制:热轧产品在轧制过程中需要控制适宜的温度,以保证产品的微结构和力学性能。
通过调整轧机温度和冷却速度等参数,可以有效控制产品的温度分布和组织形态。
唐钢热轧带钢尾部控制优化
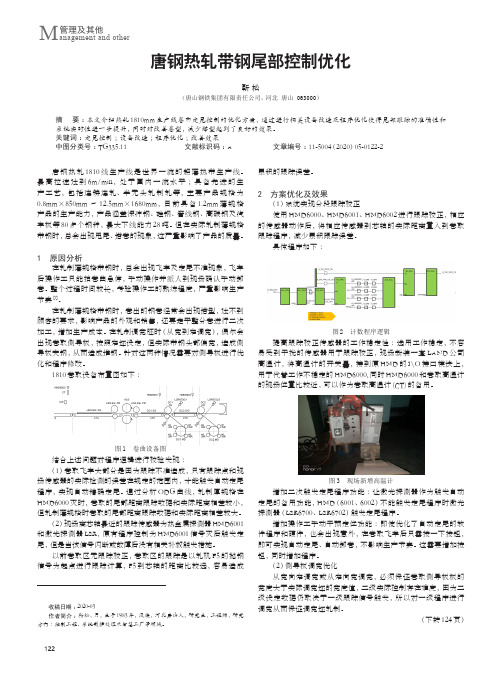
122唐钢热轧带钢尾部控制优化靳 松(唐山钢铁集团有限责任公司,河北 唐山 063000)摘 要:本文介绍热轧1810mm 生产线卷曲定尾控制的优化方案,通过进行相关设备改造及程序优化使得尾部跟踪的准确性和系统实时性进一步提升,同时对改善卷型,减少塔型起到了良好的效果。
关键词:定尾控制;设备改造;程序优化;改善效果中图分类号:TG335.11 文献标识码:A 文章编号:11-5004(2020)05-0122-2收稿日期:2020-03作者简介:靳松,男,生于1983年,汉族,河北唐山人,研究生,工程师,研究方向:控制工程、系统数据处理及智慧工厂等领域。
唐钢热轧1810线生产线是世界一流的超薄热带生产线。
最高拉速达到6m/min,处于国内一流水平;具备先进的生产工艺,包括连铸连轧、半无头轧制轧等,主要产品规格为0.8mm×850mm ~12.5mm×1680mm,目前具备1.2mm 薄规格产品的生产能力,产品涵盖深冲钢、硅钢、管线钢、高碳钢及汽车板等80多个钢种,最大下线能力28吨。
但在实际轧制薄规格带钢时,总会出现甩尾、塔卷的现象,这严重影响了产品的质量。
1 原因分析在轧制薄规格带钢时,总会出现飞车及定尾不准现象,飞车后操作工只能拍卷曲急停,手动操作并派人到现场确认手动卸卷。
整个过程时间较长,考验操作工的熟练程度,严重影响生产节奏[1]。
在轧制薄规格带钢时,卷出的钢卷经常会出现塔型,达不到顾客的要求,影响产品的外观和销售,还要走平整分卷进行二次加工,增加生产成本。
在轧制调宽胚时(从宽到窄调宽),偶尔会出现卷取侧导板,按照窄坯设定,但实际带钢头部偏宽,造成侧导板夹钢,从而造成堆钢。
针对这两种情况需要对侧导板进行优化和程序修改。
1810卷取设备布置图如下:图1 卷曲设备图结合上述问题对程序逻辑进行校验发现:(1)卷取飞车大部分是因为跟踪不准造成,只有跟踪点和现场传感器的实际检测的误差在规定的范围内,才能触发自动定尾程序,实现自动精确定尾。
轧钢生产过程产品质量控制方法与应用概述
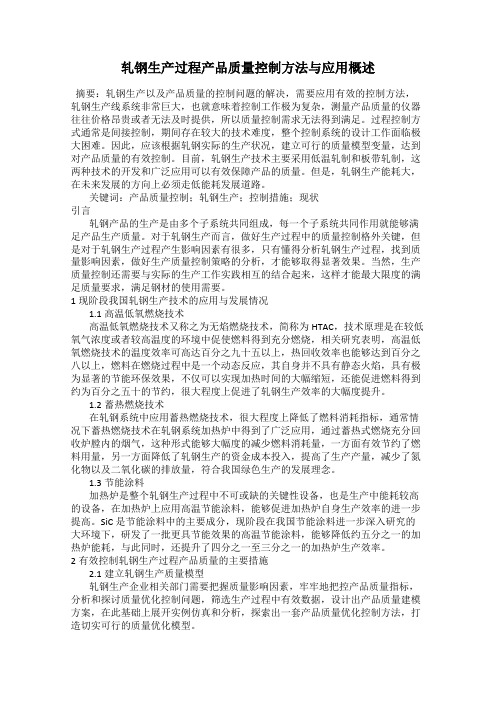
关键词:产品质量控制;轧钢生产;控制措施;现状
引言
轧钢产品的生产是由多个子系统共同组成,每一个子系统共同作用就能够满足产品生产质量。对于轧钢生产而言,做好生产过程中的质量控制格外关键,但是对于轧钢生产过程产生影响因素有很多,只有懂得分析轧钢生产过程,找到质量影响因素,做好生产质量控制策略的分析,才能够取得显著效果。当然,生产质量控制还需要与实际的生产工作实践相互的结合起来,这样才能最大限度的满足质量要求,满足钢材的使用需要。
2.3规范操作轧辊装配工艺
轧钢车间必须在质量管理体系的要求之下展开工作,轧辊装配人员必须严格遵守规章制度,依照流程图规范操作。标准作业可以避免很多产品质量问题的产生。另外,在钢板轧制过程中,需要及时检查成形变化情况,比如,检查是否出现出现麻点、裂纹、折叠等现象,及时进行专业的处理。
2.4降低轧钢的宽度公差
轧钢生产车间要严格落实质量管理制度,依据文件要求,明确各职能部门的岗位职责。与此同时,需要科学地制定各项质量问题管理规定,界定质量问题的含义,一般而言,由于违章操作或者设备故障等因素,造成车间生产出一定数量的废品或者质量不合格的产品,都属于质量问题。生产过程中,一旦发生质量问题,必须根据具体情况及时上报,主管车间质量的相关人员需要追究责任人的责任,启动质量问题处理程序,组织人员调查问题原因,探讨应对策略,以减少或避免后续质量问题的发生。
热轧带钢轧制过程中的厚度波动问题的控制技术

AGC 的各种补偿功能
AGC的一般功能以厚度计AGC为基础, 配备X射线监控AGC功能。 为了解决 厚度计AGC所不能控制的带钢厚度部分,设置了尾部补偿控制、速度补偿、张 力补偿、油膜厚度变化补偿及消除轧辊偏心控制等。 1、尾部补偿控制 当带钢尾部每离开一个机架时,由于张力消失,必然导致尾部增厚。为避免 尾部增厚,在带钢尾部离开第i-1机架时,应增大第i机架的压下量,尾部补偿时 的压下位移调节量为: ∆Yp =
厚度自动控制技术不断完善,并且实现了整个生产过程从基础级到管理级的多级 计算机控制。 20 世纪 80 年代以后出现了以高精度数学模型和智能轧制技术为代表的高新 技术群,并取得了不断完善。此外,高精度的厚度自动控制技术以及液压 AGC 技术 应用到带钢生产中,通过不断提高轧制参数设定精度和开发高性能的在线自动控 制系统使带钢全长上的厚度精度达±30μ m。 我国的热轧带钢的发展历史大约从 1957 年从苏联引进了一套 2800/1700mm 半连续式板带轧机,既生产中厚钢板又生产钢卷。随着 1958 年 7 月中厚板轧机和 1959 年精轧机的相继建成投产,我国开始迎来了自行生产宽带钢卷的历史。从该 套轧机建成到 1972 年十多年间,我国一直没有建设能够生产宽带钢卷的轧机,随 后几年建设的带钢热连轧机也都是参照这套设备设计的。 从上世纪 70 年代末开始我国开始从国外引进热带轧机生产线,武钢 1700mm 热带轧机是 20 世纪 70 年代从日本引进的全部成套设备;宝钢 2050mm 热带轧机 是 20 世纪 80 年代从德国引进的成套设备,国内合作制造了部分机电设备;宝钢 1580mm 热连轧机及鞍钢 1780mm 热连轧机是 20 世纪 90 年代国外(日本)引进和 国内制造的机电设备。这 4 套现代化的带钢热连轧机所采用的工艺技术,技术设 备和计算机控制系统,具有当时国际上一流的技术水平。这些热连轧机的建设使 我国的热轧带钢生产工艺技术很快提高到国际上的先进水平,并为我国国民经济 各部门提供了品种齐全的优质热轧板带钢和冷轧机用原料钢卷,进而为汽车、家 用电器、交通运输业等用户提供紧缺的优质冷轧薄钢板。 20 世纪 90 年代是我国热带钢轧机高速发展的时期,在此期间我国又相继建 成投产了 7 套热轧宽带钢轧机。其中有四套全新热带轧机,即宝钢 1580mm 热轧 机,鞍钢 1780mm 热轧机,珠钢 1500mm 热轧机,邯钢 1900mm 薄板还连铸连轧机。 而 1580mm 热连轧和 1780mm 热连轧机釆用和连铸机直接连接布置的连续生产 线,紧凑式粗轧机布置,精轧机组双交叉 PC 轧机,全液压 AGC 系统和卷取系统,完善 的四级计算机自动化控制和生产管理控制系统,体现了 20 世纪 90 年代最先进的 技术装备水平和一流的产品质量控制水平。 在建造新轧线的同时,我国对技术装备水平低的热轧线进行现代化技术改造。 本钢 1700mm3/4 连续式轧机和攀钢的 1450mm 半连续式热带轧机是我国自行设
轧钢生产过程质量控制的研究

轧钢生产过程质量控制的研究【摘要】钢材的生产过程十分精细,涉及到复杂的生产工艺和生产技术。
本文以轧钢生产为例,从多个方面分析了生产过程中的质量控制策略,从而保证产品的高合格率和可靠性,为企业节约成本、开拓市场奠定坚实的质量基础。
【关键词】轧钢生产过程质量控制随着经济的快速发展以及城镇化进行的逐步推进,我国对钢铁的需求量日趋增大。
在现代化的生产模式下,轧钢的生产过程十分精细,涉及到复杂的生产工艺和生产技术。
怎样才能对产品的质量进行控制,是一个亟待解决的问题,也是钢铁企业增强自身技术实力与核心竞争力的重要因素。
本文以轧钢生产为例,从多个方面分析了生产过程中的质量控制策略,从而保证产品的高合格率和可靠性,为企业节约成本、开拓市场奠定坚实的质量基础,具有比较好的理论价值与实践意义。
一、轧钢生产过程质量控制策略轧钢生产线是非常大的生产系统,因为缺乏有效的控制方法,所以质量问题比较严重,因此,要保证产品质量必须要寻找科学的产品质量控制方法。
笔者认为,要保证轧钢生产过程的质量,应从以下几方面入手。
(1)降低轧钢的厚度公差。
首先,应尽可能使钢坯以均匀的方式受热,并尽力降低黑印现象的发生。
本文结合轧钢生产的实践经验,推荐将现有的解热模式优化为步进式模式,并且在钢材轧制的过程里使用自动补偿来尽可能地减少黑印,在轧钢生产的炉内用绝热滑道的布置来减少黑印现象,并在炉中安装陶瓷纤维耐火材料并辅以信息化的炉内环境控制方法,这些手段均能够提升温控的效果。
其次,可以参照国际上一些发达的钢铁公司通用的做法,引入自动厚度控制来增强产品质量。
不少调查报告均显示,自动厚度控制系统能够明显提升轧钢生产的效率,并且提升产品合格率。
不少生产实践已经能够证明,在轧钢生产过程中,如果为精轧机组配置自动厚度控制系统,则产品的质量会有比较显著的提升。
此外还应该充分结合信息技术,以数字化的传动技术来优化现有的活套。
当前在我国国内,已经有不少大型钢铁企业在宽带钢的生产过程中引入了低惯量电动活套,从而大幅度增强了活套控制的灵敏度,最终使得钢材轧制过程中的微张力参量得到了精准的调节,提升了产品质量。
热轧带钢轧制过程中的表面质量问题与控制技术

热轧带钢轧制过程中的表面质量问题与控制技术摘要:热轧带钢的表面质量对热轧带钢产品的质量有着显著的影响作用,已成为衡量热轧带钢质量的重要指标。
本文总结前人研究成果,分析了影响热轧带钢表面质量的因素,总结了热轧带钢表面质量的形成原因及表面质量的控制方法,并详细介绍了氧化物压入缺陷的控制技术,希望能对提高热轧带钢产品质量能有一定的帮助。
关键字:热轧带钢;表面质量;控制1.概述近些年来,我国国民经济稳步上升,社会基础设施建设逐渐完善,各行各业快速发展的同时对钢材的需求量逐年增加,并且随现代社会人们生活质量的提高,科学技术的发展,对钢材的质量要求也是越来越高。
作为钢材产品中特别重要的组成部分,热轧带钢对整个钢铁产业的技术发展和社会经济效益有着不可估量的影响作用。
统计数据显示:发达国家的热轧钢材产业中,热轧带钢产量差不多能占据50%以上的份额,在国际市场竞争中一直处于领先地位。
近些年来,我国的钢铁产业发展较快,钢材产品的市场份额也逐年增加,但生产出来的钢材质量远与国外的水平相比仍有较大的差距,同时高附加值的钢制品较少。
我国热轧带钢产品的厚度下限一般是1.8mm,但实际生产中只有极少量热轧带钢的厚度能达到小于2.0mm的水平。
因此,当要求带钢厚度小于2.0mm时,通常只能采用冷轧技术,冷轧带钢成本远高于热轧带钢[1]。
热轧带钢产品的质量指标主要有:热轧带钢的尺寸与形状精度、表面质量和力学性能。
其中,热轧带钢产品的表面质量是提高产品总体质量水平最重要,也是最难控制的质量指标之一。
现代科学技术的发展,使得热轧带钢产品的质量控制问题逐渐得以解决。
例如自动宽度控制系统(AWC)、厚度自动控制系统(HAGC)、板形闭环控制系统(PFC)在带钢生产中的应用,使热轧带钢的尺寸与形状精度逐渐提高,现在已经能基本满足各个行业的应用需求[2]。
同时,随着控制炼钢成分的研究和热轧制工艺的研究逐渐取得成功,热轧带钢的各项力学性能指标已经得到了很大提高。
钢铁行业的质量控制方法与技术

钢铁行业的质量控制方法与技术钢铁行业一直是国民经济的重要支柱产业,对于确保钢铁产品的质量具有重要意义。
在如今竞争激烈的市场环境下,钢铁企业需要不断提升质量控制方法与技术,以确保生产出符合标准和客户需求的优质产品。
本文将探讨钢铁行业中常用的质量控制方法和关键技术,以帮助企业更好地提高产品质量和市场竞争力。
一、质量控制方法1. 样品检测法样品检测是钢铁行业常用的质量控制方法之一。
通过从生产线上随机抽取样品进行物理性能、化学成分等方面的测试,以确保产品质量符合要求。
样品检测需要遵循标准操作程序,并配备先进的测试设备,确保准确可靠的测试结果。
2. 工艺控制法工艺控制是钢铁生产中的重要环节,对于产品质量具有决定性影响。
通过合理的工艺流程和优化的工艺参数,可有效控制产品成分、机械性能等指标。
工艺控制需要依靠先进的自动化控制系统和可视化监控技术,以实现对生产过程的实时监控和调整。
3. 过程控制法过程控制是在钢铁生产中实时监测和调整各个环节的关键方法。
利用先进的传感器技术和数据采集系统,对原料、炉温、冷却速度等参数进行实时监控,及时发现并纠正生产过程中的异常情况,以确保产品质量的稳定性和一致性。
二、关键技术1. 精细化制造技术精细化制造技术是钢铁行业提高产品质量的核心技术之一。
通过运用先进的设备、工艺和管理方法,实现生产过程中的细节控制,最大程度地减少产品的变异性和缺陷率。
精细化制造技术需要依靠数字化、智能化的生产设备和管理系统,以提高生产效率和产品质量。
2. 无损检测技术无损检测技术在钢铁行业中被广泛应用,用于检测材料内部缺陷和表面缺陷。
通过利用超声波、X射线、涡流等检测方法,可以高效地发现和评估材料内部的裂纹、夹杂等缺陷。
无损检测技术可以提供及时准确的检测结果,帮助钢铁企业及时采取措施,降低产品的质量风险。
3. 数据分析技术数据分析技术在钢铁行业的质量控制中起着重要作用。
通过对生产过程和产品测试数据的分析,可以找出潜在的问题和改进的空间,并优化生产过程和工艺参数。
- 1、下载文档前请自行甄别文档内容的完整性,平台不提供额外的编辑、内容补充、找答案等附加服务。
- 2、"仅部分预览"的文档,不可在线预览部分如存在完整性等问题,可反馈申请退款(可完整预览的文档不适用该条件!)。
- 3、如文档侵犯您的权益,请联系客服反馈,我们会尽快为您处理(人工客服工作时间:9:00-18:30)。
第26卷第2期2005年6月 钢 铁 钒 钛IRON STEE L VANADI UM TIT ANI UM V ol.26,N o.2June2005唐钢超薄热轧带钢生产线的质量控制技术冯运莉1,2,陈华辉1,陈礼斌3(1.中国矿业大学(北京校区)材料科学与工程系,北京100083;2.河北理工大学,河北唐山063009;3.唐山钢铁有限公司,河北唐山063016)摘 要:介绍了唐钢FTSR超薄热轧带钢生产线的工艺流程,以及代表其技术特色的H2结晶器、动态液芯压下、动态PC控制、半无头轧制、铁素体轧制等新技术。
认为:H2结晶器与普通漏斗型结晶器相比,坯壳所受的应力大大降低,不易产生裂纹;优化的辊列设计及动态液芯压下技术确保了铸坯的内部质量;半无头轧制解决了超薄带钢直接穿带和甩尾困难的难题;动态PC和工作辊弯辊技术相互配合,保证了产品质量的稳定;而三点除鳞,尤其是粗轧和精轧之间设中间冷却装置,不仅可以改善板带表面质量,也为实现精轧在铁素体状态下轧制提供了条件。
关键词:超薄热带;H2结晶器;动态液芯压下;半无头轧制;动态PC控制;铁素体轧制中图分类号:TF777.7 文献标识码:A 文章编号:1004-7638(2005)02-0016-04Q uality Controlling Techniques in U ltra-thin H ot Strip ProductionLine of T angshan Iron and Steel Co.LtdFeng Y unli1,2,Chen Huahui1,Chen Libin3(1.Material Science and Engineering Department,China University of M ining&T echnology,Beijing100083,China;2.Hebei P olytechnic University,T angshan063009,Hebei,China;3.T angshan Iron and S teel C o.Ltd.,T angshan063016,Hebei, China)Abstract:The advanced techniques of ultra-thin hot strip production line at T anggang were introduced,which include H2m ould,dynamic s oft reduction,dynamic PC control,semi-endless rolling,ferrite rolling etc.The production survey shows that the stresses in the shell in H2m ould are less than in general funnel m ould,s o there are less cracks in the shell.Optimized roller line device and dynamic s oft reduction ensure the internal quality of billet.Semi-endless rolling s olves the problem of the strips polling and swing.Dynamic PC control and w orking bending roll guarantees the stability of the strip’s quality.The three-point descaling,especially about the intermediate cooling system between roughing mill and finishing mill,can not only im prove the strip surface quality but als o support the rolling in ferrite area.K ey w ords:ultra-thin hot strip;H2m ould;dynamic s oft reduction;semi-endless rolling;dynamic PC con2 trol;rolling in ferrite area0 引言 薄板坯连铸连轧是20世纪80年代末、90年代初开发成功的生产热轧板卷的一项短流程工艺,是继氧气转炉炼钢、连续铸钢之后钢铁工业最主要的革命性技术之一,国外各钢铁大国先后投入了大量人力、物力进行了专项研究。
目前,全球已开发的薄板坯连铸连轧工艺有CSP、ISP、FT SR、C ONRO LL、T SP、CPR等工 收稿日期:2005-01-17作者简介:冯运莉(1966—),女,河北唐山人,副教授,中国矿业大学在读博士,主要从事钢的强韧化机理及控轧控冷等研究。
艺。
据统计,累计到2004年3月,全世界已建成38条各种类型工艺的薄板坯连铸连轧生产线,其中CSP 线24条,FTSR 线3条(美国、加拿大、中国唐钢)。
已开发出的各种薄板坯连铸连轧技术各具特色,同时又相互影响,互相渗透,并在不断地发展和完善[1]。
CSP 技术设备相对简单,流程通畅,生产比较稳定,技术工艺相对成熟[2]。
而FTSR 薄板坯连铸连轧生产线采用了薄板坯连铸连轧第三代技术,是继CSP 连铸连轧后又一种新的生产工艺。
该工艺特点是连铸采用H 2结晶器(凸透镜型结晶器)、动态液芯压下、轧制部分能进行半无头轧制和铁素体轧制、铸坯厚度增加到70~90mm 、三点除鳞等[3]。
该生产工艺不仅为生产高质量的超薄带钢提供了技术保证,同时也达到了环保、节能降耗、降低生产成本、提高市场竞争力的目的。
唐钢超薄热轧带钢生产线于2003年1月29日一次试车成功并投入生产,年生产规划一期为150万t ,二期为250万t 。
该生产线的连铸部分采用意大利达涅利公司的FTSC 技术,轧制采用FTSR 灵活的薄板坯轧制技术,均热炉为美国布里克蒙辊底炉技术。
经过两年多的生产实践,已开发出汽车大梁用钢、集装箱用钢板、冷轧料用钢等新产品及铁素体轧制新技术。
笔者对该生产线的工艺及主要技术特点进行了分析评价。
1 唐钢超薄带钢生产线的基本概况1.1 产品大纲钢种:超低碳钢、低碳钢、包晶钢、中碳钢、高碳钢、低合金钢。
铸坯尺寸:70/65mm ×(850~1680)mm 的高品质薄板坯。
最终产品目标规格:厚0.8~12.7mm ,宽850~1680mm ,其中厚度≤1.5mm 的产品占总产量的60%。
卷重:30t 。
1.2 工艺流程与机组布置唐钢超薄热轧带钢生产线的工艺流程为:转炉钢水包→LF 精炼→大包回转台→中间包→结晶器→0~9扇形段→旋转除鳞机→剪切机→引锭杆回收→剪后输出辊道→引锭杆存放→辊底式加热炉→立辊轧机→高压水除鳞→两架粗轧机轧制→保温罩/中间冷却→飞剪切头→高压水除鳞→五架精轧机轧制→层流冷却→高速飞剪/填充辊道→两台地下卷取机→取样、检查→打捆→称重→打印→入库。
唐钢超薄热轧带钢生产线的机组布置如图1所示。
超薄热轧带钢生产线的主要设备有:一台带有H 2结晶器和动态软压下的薄板坯连铸机,一座隧道炉,一套粗轧除鳞机,一架立辊轧机,两架粗轧机,一套中间冷却设备,一台切头机,一套精轧除鳞机,五机架精轧机,一套带钢冷却装置,高速飞剪和两台地下卷取机。
2 主要技术特点2.1 薄板坯连铸工艺新技术2.1.1 直弧型连铸机唐钢薄板坯连铸机采用的是达涅利的直弧型机型,在吸取各种薄板坯连铸工艺的技术和生产实践经验的基础上,从工艺操作、设备结构和自动化控制功能等方面融进了自身创新的技术精华,是新一代薄板坯连铸机的代表。
主要的技术及设备特点表现为薄板坯连铸包晶钢提供有利的保证,并可根据生产带钢的质量和厚度自动地选择需要达到的断面而实现高度的灵活性。
2.1.2 H 2结晶器图1 唐钢超薄热轧带钢生产线的工艺布置Fig.1 T echnology lay out of T anggang ultra -thin hot strip production・71・ 第2期 冯运莉等:唐钢超薄热轧带钢生产线的质量控制技术 针对普通漏斗型结晶器暴露出来的生产品种相对单一、铸坯表面质量不理想的问题,唐钢超薄热带生产线采用了H 2结晶器,见图2。
该结晶器主要特点是鼓肚形状贯穿整个铜板,并一直延续到扇形0段中部。
为了使铸坯鼓肚矫平,在结晶器出口处特设计安装了一套带辊形的辊子。
铸坯鼓肚矫平的设备比仅用结晶器长了一倍,也就是说,这与只使用结晶器来矫平坯壳的鼓肚相比,坯壳所受的应力大大降低了,而且这种结晶器的内部容积比较大,有较好地钢水自然减速的效应。
坯壳在结晶器内变形小,不易产生裂纹,结晶器弯月面处钢液面积大,有利于保护渣的熔化,可使坯壳传热的热流密度相对小一些,有利于浇铸包晶钢等裂纹敏感性强的钢种。
图2 H 2结晶器Fig.2 H 2m ould 另外,浸入式水口在结晶器上口距铜板距离可达50~60mm ,在出口处约为40mm ,这样既有利于保护渣熔化,又可以使用壁厚的水口,以延长其使用寿命。
同时结晶器上部尺寸加大对浸入式水口设计更为有利。
结晶器下部的立辊段,可保证铸坯平滑收缩,承受较小的坯壳应力。
2.1.3 优化的辊列设计及动态液芯压下技术达涅利的灵活薄板坯连铸机FTSC 为直弧铸机,通过辊列计算确定最佳的辊间距和辊径,同时采用多点弯曲、多点矫直技术和分节辊技术有效地防止鼓肚的产生和应力集中,使铸坯在整个弯曲、矫直过程中(即使在液芯压下状态下),其产生的最大应变都低于产生裂纹的临界应变,有效地防止了内部裂纹的产生。
通过计算机二级控制,实现对铸坯温度的计算和对铸坯凝固终点的跟踪,根据不同的钢种、拉速、钢水过热度确定合适的压下终点、各扇形段的压下量和压下速率,避免内部裂纹的产生,同时压下作用促进树枝晶间钢液的流动,使成分均匀,消除中心偏析。
液芯压下技术解决了结晶器的厚度的问题,FTSC 薄板坯连铸机采用厚度为90mm 的结晶器,铸坯由90mm 压下到70或65mm 。
大的结晶器液面能缓冲高速钢流的冲击作用,促进结晶器液面的稳定,减少卷渣的发生。
同时结晶器的热容增加,保护渣熔化条件变好,保证了高质量铸坯的生产。
此外,采用动态液芯压下技术可打碎发达的柱状晶,使铸坯中心形成理想的等轴晶,提高了铸坯的内部质量。
2.2 轧制新技术2.2.1 半无头轧制技术为确保超薄热带的生产,带钢生产线采用了半无头轧制技术,这项技术不仅解决了超薄带钢的直接穿带及甩尾困难的问题,而且在提高超薄带钢质量方面有以下优点:①机架间带钢张力可以保持稳定,使带钢厚度及平直度偏差减至最小;②减少了单块轧制时因带钢头尾形状不良所带来的废品量,提高了产品质量及成材率。