耐磨损性能和抗崩刃性能的PCD刀具材料
刀具材料PCD

XX大学2014~2015 学年秋季学期研究生课程考试课程名称:课程编号:论文题目:刀具材料PCD概述研究生:学号:论文评语:成绩:任课教师:评阅日期:刀具材料PCD概述摘要:好的刀具材料是制造出好的刀具的前提,更是加工出好的产品的关键。
随着制造业的快速发展,金刚石刀具的生产和应用正在逐年增加。
天然金刚石价格昂贵,金刚石广泛应用于切削加工的还是PCD。
本文针对刀具材料PCD做了比较系统的论述,主要包括PCD材料的介绍,PCD复合片及刀具的制造技术,PCD 复合片的主要优缺点以及PCD刀具材料的应用。
关键词:PCD;材料;刀具The overview about cutting tool materials of PCDAbstract:Good tool material is a prerequisite to create a good tool, it is also a key processing of making a good product .With the sharp development of making industry, production and application of diamond tools is increasing year by year.Natural diamonds are expensive,PCD is widely used in cutting .This paper makes a systematic introduction of tool material PCD,including the introduction of PCD materials ,the manufacturing techniques of PCD composite sheet and tool, the main advantages and disadvantages of PCD composite sheet materials and the application of PCD tools.Key words:PCD;Materials ; Tool1引言随着人类生活、生产水平的提高,高速钢刀具已不能满足高加工效率和高加工质量的新要求。
PCD刀具的应用与发展
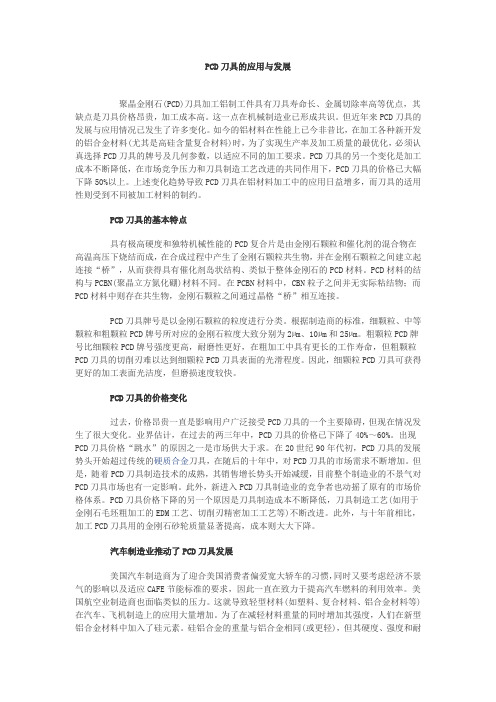
PCD刀具的应用与发展聚晶金刚石(PCD)刀具加工铝制工件具有刀具寿命长、金属切除率高等优点,其缺点是刀具价格昂贵,加工成本高。
这一点在机械制造业已形成共识。
但近年来PCD刀具的发展与应用情况已发生了许多变化。
如今的铝材料在性能上已今非昔比,在加工各种新开发的铝合金材料(尤其是高硅含量复合材料)时,为了实现生产率及加工质量的最优化,必须认真选择PCD刀具的牌号及几何参数,以适应不同的加工要求。
PCD刀具的另一个变化是加工成本不断降低,在市场竞争压力和刀具制造工艺改进的共同作用下,PCD刀具的价格已大幅下降50%以上。
上述变化趋势导致PCD刀具在铝材料加工中的应用日益增多,而刀具的适用性则受到不同被加工材料的制约。
PCD刀具的基本特点具有极高硬度和独特机械性能的PCD复合片是由金刚石颗粒和催化剂的混合物在高温高压下烧结而成,在合成过程中产生了金刚石颗粒共生物,并在金刚石颗粒之间建立起连接“桥”,从而获得具有催化剂岛状结构、类似于整体金刚石的PCD材料。
PCD材料的结构与PCBN(聚晶立方氮化硼)材料不同。
在PCBN材料中,CBN粒子之间并无实际粘结物;而PCD材料中则存在共生物,金刚石颗粒之间通过晶格“桥”相互连接。
PCD刀具牌号是以金刚石颗粒的粒度进行分类。
根据制造商的标准,细颗粒、中等颗粒和粗颗粒PCD牌号所对应的金刚石粒度大致分别为2µm、10µm和25µm。
粗颗粒PCD牌号比细颗粒PCD牌号强度更高,耐磨性更好,在粗加工中具有更长的工作寿命,但粗颗粒PCD刀具的切削刃难以达到细颗粒PCD刀具表面的光滑程度。
因此,细颗粒PCD刀具可获得更好的加工表面光洁度,但磨损速度较快。
PCD刀具的价格变化过去,价格昂贵一直是影响用户广泛接受PCD刀具的一个主要障碍,但现在情况发生了很大变化。
业界估计,在过去的两三年中,PCD刀具的价格已下降了40%~60%。
出现PCD刀具价格“跳水”的原因之一是市场供大于求。
PCD刀具介绍
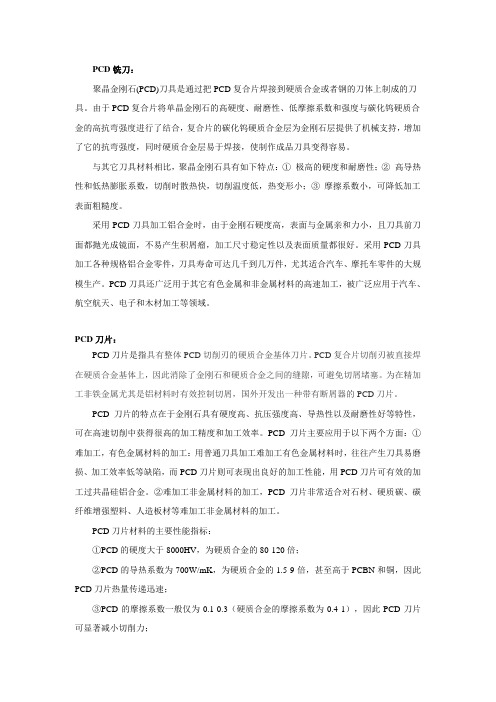
PCD铣刀:聚晶金刚石(PCD)刀具是通过把PCD复合片焊接到硬质合金或者钢的刀体上制成的刀具。
由于PCD复合片将单晶金刚石的高硬度、耐磨性、低摩擦系数和强度与碳化钨硬质合金的高抗弯强度进行了结合,复合片的碳化钨硬质合金层为金刚石层提供了机械支持,增加了它的抗弯强度,同时硬质合金层易于焊接,使制作成品刀具变得容易。
与其它刀具材料相比,聚晶金刚石具有如下特点:① 极高的硬度和耐磨性;② 高导热性和低热膨胀系数,切削时散热快,切削温度低,热变形小;③ 摩擦系数小,可降低加工表面粗糙度。
采用PCD刀具加工铝合金时,由于金刚石硬度高,表面与金属亲和力小,且刀具前刀面都抛光成镜面,不易产生积屑瘤,加工尺寸稳定性以及表面质量都很好。
采用PCD刀具加工各种规格铝合金零件,刀具寿命可达几千到几万件,尤其适合汽车、摩托车零件的大规模生产。
PCD刀具还广泛用于其它有色金属和非金属材料的高速加工,被广泛应用于汽车、航空航天、电子和木材加工等领域。
PCD刀片:PCD刀片是指具有整体PCD切削刃的硬质合金基体刀片。
PCD复合片切削刃被直接焊在硬质合金基体上,因此消除了金刚石和硬质合金之间的缝隙,可避免切屑堵塞。
为在精加工非铁金属尤其是铝材料时有效控制切屑,国外开发出一种带有断屑器的PCD刀片。
PCD刀片的特点在于金刚石具有硬度高、抗压强度高、导热性以及耐磨性好等特性,可在高速切削中获得很高的加工精度和加工效率。
PCD刀片主要应用于以下两个方面:①难加工,有色金属材料的加工:用普通刀具加工难加工有色金属材料时,往往产生刀具易磨损、加工效率低等缺陷,而PCD刀片则可表现出良好的加工性能,用PCD刀片可有效的加工过共晶硅铝合金。
②难加工非金属材料的加工,PCD刀片非常适合对石材、硬质碳、碳纤维增强塑料、人造板材等难加工非金属材料的加工。
PCD刀片材料的主要性能指标:①PCD的硬度大于8000HV,为硬质合金的80-120倍;②PCD的导热系数为700W/mK,为硬质合金的1.5-9倍,甚至高于PCBN和铜,因此PCD刀片热量传递迅速;③PCD的摩擦系数一般仅为0.1-0.3(硬质合金的摩擦系数为0.4-1),因此PCD刀片可显著减小切削力;④PCD的热膨胀系数仅为0.9*10-6-1.18*10-6,仅相当于硬质合金的1/5,因此PCD刀片热变形小,加工精度高;⑤PCD刀片与有色金属和非金属材料的亲和力很小,在加工过程中切屑不易粘结在刀尖上形成积屑瘤。
pcd刀具的设计原则

PCD刀具的设计原则一、合理选择PCD粒度PC D粒度的选择与刀具加工条件有关,如设计用于精加工或超精加工的刀具时,应选用强度高、韧性好、抗冲击性能好、细晶粒的P C D。
粗晶粒PC D刀具则可用于一般的粗加工。
PC D材料的粒度对于刀具的磨损和破损性能影响显著。
研究表明:P C D粒度号越大,刀具的抗磨损性能越强。
采用DeBeers 公司S YN DITE 002和S YN DITE025两种PC D材料的刀具加工S iC基复合材料时的刀具磨损试验结果表明,粒度为2μm的S YN DITE002PC D材料较易磨损。
二、合理选择PCD刀片厚度通常情况下,PC D复合片的层厚约为0.3~1.0mm,加上硬质合金层后的总厚度约为2~8mm。
较薄的PC D层厚有利于刀片的电火花加工。
DeBeers公司推出的0.3mm厚P CD复合片可降低磨削力,提高电火花的切割速度。
PC D复合片与刀体材料焊接时,硬质合金层的厚度不能太小,以避免因两种材料结合面间的应力差而引起分层。
三、几何参数与结构设计PC D刀具的几何参数取决于工件状况、刀具材料与结构等具体加工条件。
由于P CD刀具常用于工件的精加工,切削厚度较小(有时甚至等于刀具的刃口半径),属于微量切削,因此其后角及后刀面对加工质量有明显影响,较小的后角、较高的后刀面质量对于提高P C D 刀具的加工质量可起到重要作用。
P C D复合片与刀杆的连接方式包括机械夹固、焊接、可转位等多种方式。
四、PCD复合片与刀杆连接方式的特点与应用连接方式-特点-应用范围机械夹固-由标准刀体及可做成各种集合角度的可换刀片组成,具有快换和便于重磨的优点-中小型机床整体焊接-结构紧凑、制作方便,可制成小尺寸刀具-专用刀具或难于机夹的刀具,用于小型机床机夹焊接-刀片焊接于刀头上,可使用标准刀杆,便于刃磨及调整刀头位置-自动机床、数控机床可转位-结构紧凑,夹紧可靠,不需重磨和焊接,可节省辅助时间,提高刀具寿命-普通通用机床五、PCD刀具的切削参数与失效机理PC D刀具切削参数对切削性能的影响①切削速度PC D刀具可在极高的主轴转速下进行切削加工,但切削速度的变化对加工质量的影响不容忽视。
加工石墨的刀具选择—PCD刀具

加工石墨的刀具选择—PCD刀具石墨是碳的一种同素异形体,尤其石墨的高磨蚀性、耐高温等性能,广泛应用于模具、坩埚、点击、电池、电刷等领域。
但由于石墨质坚而脆,所以采用车、铣等常规机械加工方法时,旺旺在加工表面会产生崩损现象。
因此车、铣加工石墨模/石墨电极等制品时,切削刀具需具备高的耐磨损性和抗冲击性。
本文就重点介绍一下车、铣加工石墨模具/石墨电极等制品的刀具材质选择,及其加工刀具的规格型号选择。
1、石墨制品的介绍(1)石墨制品之石墨模具的介绍模具作为工业生产中使用极为广泛的基础工艺装备,大到机身外壳,小到一个螺丝,都是根据成型模具,通过冲压、锻压、压铸、挤压、注塑等方式使坯料成为符合产品要求的零件。
模具的形状和加工质量、精度决定着产品的外形和质量。
近年来随着模具行业飞速发展,石墨以其良好的物理和化学性能逐渐成为模具制作的理想选择材料。
现如今许多产业部门,如机电、汽车、家电轻工、电器仪表、通讯、军械等行业的发展均依赖于模具工业的技术提高和发展。
(2)石墨制品之石墨电极的介绍石墨电极是指以石油焦、沥青焦为骨料,煤沥青为黏结剂,经过原料煅烧、破碎磨粉、配料、混捏、成型、焙烧、浸渍、石墨化和机械加工而制成的一种耐高温石墨质导电材料,称为人造石墨电极(简称石墨电极)。
石墨电极的优点是加工较容易,放电加工去除率高,石墨损耗小,因此,部分群基火花机客户放弃了铜电极而改用石墨电极。
目前石墨电极主要用于电弧炼钢炉,矿热电炉,电阻炉等行业,同时石墨电极的毛坯还用于加工成各种坩埚、模具、舟皿和发热体等异型石墨产品。
(3)石墨制品之石墨坩埚的介绍石墨坩埚,又称熔铜包、熔铜等,是指以石墨、粘土、硅石和腊石为原料烧制而成的一类坩埚。
石墨坩埚具有耐高温、导热性能强、热膨胀系数小、抗腐蚀性能好,化学稳定性强,使用寿命长等特点。
被广泛用于合金工具钢冶炼和有色金属(紫铜、黄铜、金、银、锌和铅)及其合金的冶炼。
(4)其他石墨制品介绍除了以上是那种零部件,石墨广泛用于耐火材料、导电材料、耐磨材料、润滑剂、耐高温密封材料、耐腐蚀材料、隔热材料、吸附材料、摩擦材料和防辐射等材料中,这些材料广泛应用于冶金、石油化工、机械工业、电子产业、核工业和国防等。
PCD﹑PCBN刀具材料及刀具涂层
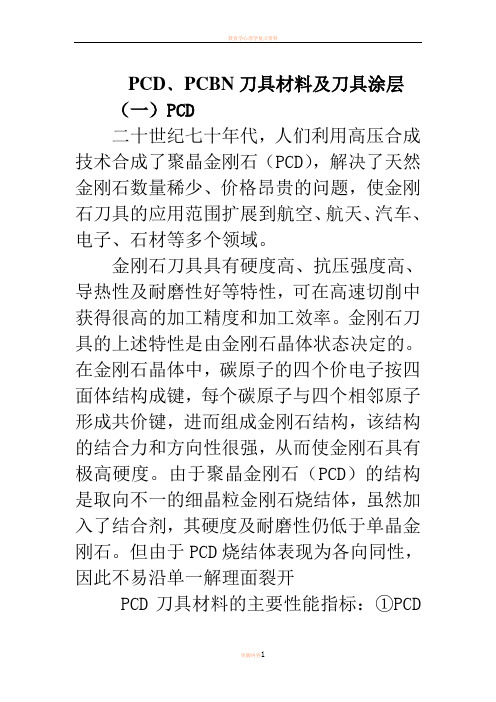
PCD﹑PCBN刀具材料及刀具涂层(一)PCD二十世纪七十年代,人们利用高压合成技术合成了聚晶金刚石(PCD),解决了天然金刚石数量稀少、价格昂贵的问题,使金刚石刀具的应用范围扩展到航空、航天、汽车、电子、石材等多个领域。
金刚石刀具具有硬度高、抗压强度高、导热性及耐磨性好等特性,可在高速切削中获得很高的加工精度和加工效率。
金刚石刀具的上述特性是由金刚石晶体状态决定的。
在金刚石晶体中,碳原子的四个价电子按四面体结构成键,每个碳原子与四个相邻原子形成共价键,进而组成金刚石结构,该结构的结合力和方向性很强,从而使金刚石具有极高硬度。
由于聚晶金刚石(PCD)的结构是取向不一的细晶粒金刚石烧结体,虽然加入了结合剂,其硬度及耐磨性仍低于单晶金刚石。
但由于PCD烧结体表现为各向同性,因此不易沿单一解理面裂开PCD刀具材料的主要性能指标:①PCD的硬度可达8000HV,为硬质合金的80~120倍;②PCD的导热系数为700W/mK,为硬质合金的1.5~9倍,甚至高于PCBN和铜,因此PCD刀具热量传递迅速;③PCD的摩擦系数一般仅为0.1~0.3(硬质合金的摩擦系数为0.4~1),因此PCD刀具可显著减小切削力;④PCD的热膨胀系数仅为0.9×10 -6~1.18×10 -6,仅相当于硬质合金的1/5,因此PCD刀具热变形小,加工精度高;⑤PCD刀具与有色金属和非金属材料间的亲和力很小,在加工过程中切屑不易粘结在刀尖上形成积屑瘤。
PCD刀具的应用: 工业发达国家对PCD刀具的研究开展较早,其应用已比较成熟。
自1953年在瑞典首次合成人造金刚石以来,对PCD刀具切削性能的研究获得了大量成果,PCD刀具的应用范围及使用量迅速扩大。
目前,国际上著名的人造金刚石复合片生产商主要有英国De Beers公司、美国GE公司、日本住友电工株式会社等。
据报道,1995年一季度仅日本的PCD刀具产量即达10.7万把。
pcd木工刀片简介

1 引言随着现代科学技术的高速发展,由聚晶金刚石(PCD)、聚晶立方氮化硼(PCBN)等超硬材料制成的刀具品种越来越丰富,其性能也得到不断发展和提高。
刀片磨料粒径从数十微米、几微米到纳米级;金刚石、立方氮化硼的含量分为低含量、中等含量和高含量;结合剂既有金属、非金属也有混合材料;PCD层厚度从毫米级到微米级;PCD层与硬质合金衬底的结合方式有平面、波纹面;PCD层有高耐磨、高韧性、高耐热等不同特性。
目前PCD、PCBN刀具的应用范围扩大到汽车、航天航空、精密机械、家电、木材、电子电气等行业,用于制作车刀、镗刀、铣刀和钻头、铰刀、锪刀、锯刀、镂刀、剃刀等。
尽管PCD、PCBN刀具发展如此之快,但因其高硬度导致的刀具刃磨困难一直困扰着大多数用户,刀片的重磨也主要由原刀具生产厂家来完成。
不仅刀具价格高,交货期长,而且占用企业流动资金。
因此,很有必要认真研究PCD的磨削特点及PCD刀具的刃磨技术。
2 PCD刀具的制造工艺PCD切削刀具的生产工艺流程一般包括抛光、切割、固接、刃磨、质检等。
PCD超硬材料毛坯直径通常有1/2、1、2、3、4英寸,其表面一般较粗糙(Ra2~10μm),不能直接用于制作刀具,需经研磨抛光使其表面达到镜面(Ra≤0.01μm),然后通过激光切割或电火花线切割加工成一定几何形状和尺寸要求的刀片,再进一步对刀片和基体待固接面进行机械和化学处理,然后采用银基硬钎焊将刀片固接于基体上,最后经金刚石砂轮刃磨。
PCD切削刀具制造技术的关键之一是切削刃的刃磨质量。
优质刀头材料缺乏理想的刃磨工艺和技术将会造成资源浪费,采用好的刃磨工艺则会提升刀具的产品质量,降低刀具使用成本。
3 PCD材料的磨削加工特点PCD是由特殊处理的金刚石与少量粘结剂在高温超高压下烧结而成。
无序排列的金刚石晶粒使PCD具有均匀的、极高的硬度和耐磨性。
PCD可用于切削刀具、砂轮修整、地质钻探、量具测头、拉丝摸具、喷砂摸具等。
PCD刀具在木材加工中的应用
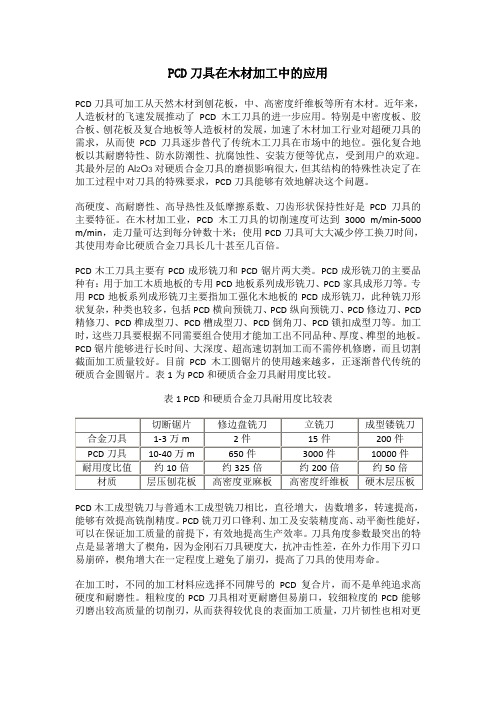
PCD刀具在木材加工中的应用PCD刀具可加工从天然木材到刨花板,中、高密度纤维板等所有木材。
近年来,人造板材的飞速发展推动了PCD木工刀具的进一步应用。
特别是中密度板、胶合板、刨花板及复合地板等人造板材的发展,加速了木材加工行业对超硬刀具的需求,从而使PCD刀具逐步替代了传统木工刀具在市场中的地位。
强化复合地板以其耐磨特性、防水防潮性、抗腐蚀性、安装方便等优点,受到用户的欢迎。
其最外层的Al2O3对硬质合金刀具的磨损影响很大,但其结构的特殊性决定了在加工过程中对刀具的特殊要求,PCD刀具能够有效地解决这个问题。
高硬度、高耐磨性、高导热性及低摩擦系数、刀齿形状保持性好是PCD刀具的主要特征。
在木材加工业,PCD木工刀具的切削速度可达到3000 m/min-5000 m/min,走刀量可达到每分钟数十米;使用PCD刀具可大大减少停工换刀时间,其使用寿命比硬质合金刀具长几十甚至几百倍。
PCD木工刀具主要有PCD成形铣刀和PCD锯片两大类。
PCD成形铣刀的主要品种有:用于加工木质地板的专用PCD地板系列成形铣刀、PCD家具成形刀等。
专用PCD地板系列成形铣刀主要指加工强化木地板的PCD成形铣刀,此种铣刀形状复杂,种类也较多,包括PCD横向预铣刀、PCD纵向预铣刀、PCD修边刀、PCD 精修刀、PCD榫成型刀、PCD槽成型刀、PCD倒角刀、PCD锁扣成型刀等。
加工时,这些刀具要根据不同需要组合使用才能加工出不同品种、厚度、榫型的地板。
PCD锯片能够进行长时间、大深度、超高速切割加工而不需停机修磨,而且切割截面加工质量较好。
目前PCD木工圆锯片的使用越来越多,正逐渐替代传统的硬质合金圆锯片。
表1为PCD和硬质合金刀具耐用度比较。
表1 PCD和硬质合金刀具耐用度比较表PCD木工成型铣刀与普通木工成型铣刀相比,直径增大,齿数增多,转速提高,能够有效提高铣削精度。
PCD铣刀刃口锋利、加工及安装精度高、动平衡性能好,可以在保证加工质量的前提下,有效地提高生产效率。
PCD(金刚石)刀片

ø85 19
ø70 ø85
■ 切削数据
• 活塞 • Vc = 1000m/min • ap = 2.0mm (Only spree d=5mm) • f = 0.25mm/rev • 湿式 • CNMM120408M
AC8A
Spree 凹面部
60
(加工长度)
75
超微颗粒
KPD001
10,000 个/刃
■ 应用
被加工材料
切削范围 JIS(日本工业规格)分类
精加工 N01
KPD001
PCD
KPD025 KPD010
KPD002
非铁材料 (铝/非铁金属)
N10
N20
粗加工 N30
精加工 S01
KPD001 KPD025
KPD010 KPD002
难于加工材料 (钛合金/镍合金)
S10
S20
粗加工 S30
• 湿式
• 铜焊圆形刀柄
(刀尖半径 = 0.5mm)
超微颗粒
KPD001
1,350 个/刃
传统PCD H
500 ~ 1,060 个/刃
•由于切屑控制情况差而发生崩损。KPD001加工时无崩损
与毛边,工具寿命得到改善。
烧结金属(Cu)
• 连杆 • Vc = 350m/min • ap = 0.08 ~ 0.1mm • f = 0.07mm/rev • 湿式 • TPGN160304SE
90 切削部件
烧结金属(Cu)
超微颗粒
KPD001
300 个/刃
其他公司的PCD G (超微颗粒聚晶PCD)
•间断加工。
(烧结金属存在微小的间隙)
•耐磨损性较其他公司的G更佳。
PCD聚晶金刚石刀具特性及其适合加工的材料简介

PCD 聚晶金刚石刀具特性及其适合加工的材料简介图1努氏硬度图2断裂韧性图3导热性制备工艺PCD是由大量随机定向的金刚石颗粒在极困难的条件下进行人工合成得到的。
它通过在高压高温下烧结精选的金刚石颗粒进行制备。
烧结过程在金刚石稳定区内被严格地控制,于是生产出一种极硬且耐磨的结构。
特性PCD是由大量随机定向的金刚石颗粒在极困难的条件下进行人工合成得到的。
它通过在高压高温下烧结精选的金刚石颗粒进行制备。
烧结过程在金刚石稳定区内被严格地控制,于是生产出一种极硬且耐磨的结构。
特性以聚晶形态组成的金刚石提供了一种强大的切削刀具,它提供极好的硬度及由此得到的耐磨性,并与聚晶结构所带来的极佳韧性相结合。
此外,金刚石拥有所有刀具材料中最高的导热性,使得热量迅速从切削刃传递出来。
除PCD与铁的高亲合力以外,PCD不会与工件材料粘结,在正确的切削参数下,积屑瘤是最小化的。
所有的SecomaxPCD刀具都拥有镜面抛光的前刀面,提供最低的摩擦系数和光滑的切削刃。
适合加工的工件材料铝合金铝合金已成为交通工业需求的致力于减轻重量的理想材料。
尽管铝合金的生产在能量消耗上具有更大的初始需求,但在长期运作中证明有更多的益处,这些合金的性能将超过其它与其竞争的材料。
纯铝的硬度低、耐腐蚀。
举例讲,添加铜或镁等合金元素将使该材料具有更高的强度。
巿场上有很多种铝合金,最著名的莫过于分别用于汽车与航空航天行业的2000及6000系列。
锻造和铸造铝合金之间有明显的分界线,各有几种不同的材质等级,而且有各式各样的硬化处理性能。
对于硅(Si)含量低到中等的硅合金来说,PCD在铣削应用与粗加工中提供了最好的耐磨性,见下表。
所遭遇到的最常见的问题应该是积屑瘤。
即使是很高的切削速度,加工低硅铝合金时也会发生这种情况。
切削刃的几何角度和质量必须要被小心地应用。
采用这样的参数,当与工件的接触时间越久,产生的热量上升,其直接的影响就是刀具寿命的缩短。
对于加工高硅铝合金,PCD的耐磨性被完全地利用。
pcd数控刀具切削参数
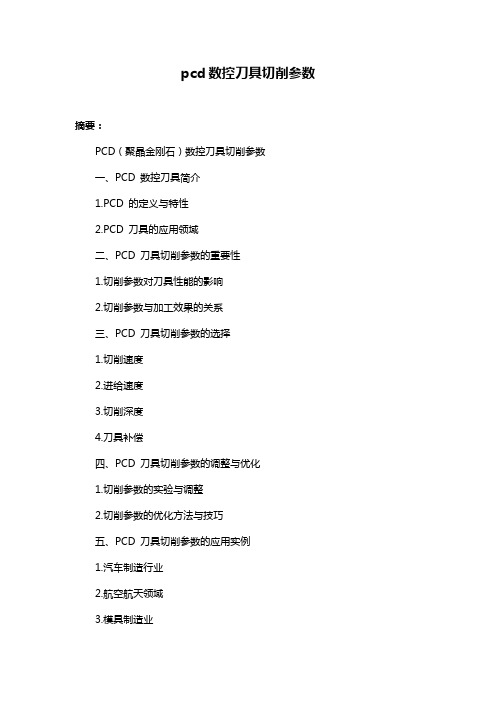
pcd数控刀具切削参数摘要:PCD(聚晶金刚石)数控刀具切削参数一、PCD 数控刀具简介1.PCD 的定义与特性2.PCD 刀具的应用领域二、PCD 刀具切削参数的重要性1.切削参数对刀具性能的影响2.切削参数与加工效果的关系三、PCD 刀具切削参数的选择1.切削速度2.进给速度3.切削深度4.刀具补偿四、PCD 刀具切削参数的调整与优化1.切削参数的实验与调整2.切削参数的优化方法与技巧五、PCD 刀具切削参数的应用实例1.汽车制造行业2.航空航天领域3.模具制造业六、总结1.PCD 刀具切削参数的发展趋势2.对我国制造业的意义与启示正文:PCD(聚晶金刚石)数控刀具切削参数PCD(聚晶金刚石)是一种具有高硬度、高热导率和高抗磨损性能的材料。
由于这些特性,PCD 刀具在数控加工领域得到了广泛应用。
本文将介绍PCD 数控刀具的切削参数及其在制造业中的应用。
一、PCD 数控刀具简介PCD 是由金刚石微粉和金属结合剂经过高温高压制成的一种复合材料。
它具有极高的硬度和热导率,以及良好的抗磨损性能。
因此,PCD 刀具在难加工材料、高硬材料和高温材料加工方面具有显著优势。
PCD 刀具广泛应用于汽车制造、航空航天、模具制造等行业。
二、PCD 刀具切削参数的重要性切削参数是影响PCD 刀具性能和加工效果的重要因素。
合适的切削参数可以提高刀具的耐用度、加工效率和加工质量。
切削参数与刀具性能和加工效果之间的关系主要表现在以下几个方面:1.切削速度:影响刀具的磨损、加工热量和加工表面的质量。
2.进给速度:影响刀具的磨损、加工热量和加工表面的质量。
3.切削深度:影响刀具的磨损和加工效率。
4.刀具补偿:影响刀具的加工精度和加工质量。
三、PCD 刀具切削参数的选择选择合适的切削参数是提高PCD 刀具加工效果的关键。
以下是一些建议:1.切削速度:根据加工材料和刀具材质选择合适的切削速度,以降低刀具磨损和加工热量。
2.进给速度:根据加工材料和刀具材质选择合适的进给速度,以降低刀具磨损和加工热量。
关于PCD刀具,最全的都在这了

关于PCD刀具,最全的都在这了PCD刀具介绍:PCD刀具是采用超硬材料PCD(聚晶金刚石)与刀具基体通过特殊工艺制成的刀具。
PCD刀具的特点:硬度高、抗压强度高、导热性好、耐磨性好。
PCD刀具主要指标:1、PCD的硬度可达8000HV,为硬质合金的8~12倍;2、PCD的导热系数为700W/mK,为硬质合金的1.5~9倍,甚至高于PCBN和铜,因此PCD刀具热量传递迅速;3、PCD的摩擦系数一般仅为0.1~0.3(硬质合金的摩擦系数为0.4~1),因此PCD刀具可显著减小切削力;4、PCD的热膨胀系数仅为0.9×10^-6~1.18×10^-6,仅相当于硬质合金的1/5,因此PCD刀具热变形小,加工精度高;5、PCD刀具与有色金属和非金属材料间的亲和力很小,在加工过程中切屑不易粘结在刀尖上形成积屑瘤。
PCD刀具制造技术:制造过程PCD刀具的制造过程主要包括两个阶段:1、PCD复合片的制造:PCD复合片是由天然或人工合成的金刚石粉末与结合剂(其中含钴、镍等金属)按一定比例在高温(1000~2000℃)、高压(5~10万个大气压)下烧结而成。
在烧结过程中,由于结合剂的加入,使金刚石晶体间形成以TiC、SiC、Fe、Co、Ni等为主要成分的结合桥,金刚石晶体以共价键形式镶嵌于结合桥的骨架中。
通常将复合片制成固定直径和厚度的圆盘,还需对烧结成的复合片进行研磨抛光及其它相应的物理、化学处理。
2、PCD刀片的加工:PCD刀片的加工主要包括复合片的切割、刀片的焊接、刀片刃磨等步骤。
切割工艺由于PCD刀具具有很高的硬度及耐磨性,因此必须采用特殊的加工工艺。
目前,加工PCD复合片主要采用电火花线切割、激光加工、超声波加工、高压水射流等几种工艺方法,其工艺特点的比较见表1。
在上述加工方法中,电火花加工效果较佳。
PCD中结合桥的存在使电火花加工复合片成为可能。
在有工作液的条件下,利用脉冲电压使靠近电极金属处的工作液形成放电通道,并在局部产生放电火花,瞬间高温可使聚晶金刚石熔化、脱落,从而形成所要求的三角形、长方形或正方形的刀头毛坯。
PCD刀具应用综述
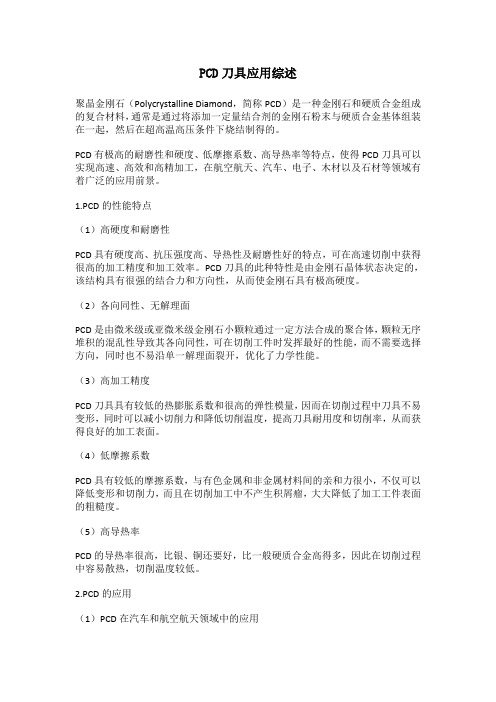
PCD刀具应用综述聚晶金刚石(Polycrystalline Diamond,简称PCD)是一种金刚石和硬质合金组成的复合材料,通常是通过将添加一定量结合剂的金刚石粉末与硬质合金基体组装在一起,然后在超高温高压条件下烧结制得的。
PCD有极高的耐磨性和硬度、低摩擦系数、高导热率等特点,使得PCD刀具可以实现高速、高效和高精加工,在航空航天、汽车、电子、木材以及石材等领域有着广泛的应用前景。
1.PCD的性能特点(1)高硬度和耐磨性PCD具有硬度高、抗压强度高、导热性及耐磨性好的特点,可在高速切削中获得很高的加工精度和加工效率。
PCD刀具的此种特性是由金刚石晶体状态决定的,该结构具有很强的结合力和方向性,从而使金刚石具有极高硬度。
(2)各向同性、无解理面PCD是由微米级或亚微米级金刚石小颗粒通过一定方法合成的聚合体,颗粒无序堆积的混乱性导致其各向同性,可在切削工件时发挥最好的性能,而不需要选择方向,同时也不易沿单一解理面裂开,优化了力学性能。
(3)高加工精度PCD刀具具有较低的热膨胀系数和很高的弹性模量,因而在切削过程中刀具不易变形,同时可以减小切削力和降低切削温度,提高刀具耐用度和切削率,从而获得良好的加工表面。
(4)低摩擦系数PCD具有较低的摩擦系数,与有色金属和非金属材料间的亲和力很小,不仅可以降低变形和切削力,而且在切削加工中不产生积屑瘤,大大降低了加工工件表面的粗糙度。
(5)高导热率PCD的导热率很高,比银、铜还要好,比一般硬质合金高得多,因此在切削过程中容易散热,切削温度较低。
2.PCD的应用(1)PCD在汽车和航空航天领域中的应用PCD刀具在汽车领域主要用于加工发动机活塞的裙部、销孔、汽缸体、变速箱等。
由于这些部件材料含硅量较高(10%以上),对刀具的使用寿命要求高,而PCD 刀具耐用度是硬质合金刀具的1-50倍,可保证零部件尺寸的稳定性,并可大大提高切削速度、加工效率和工件的表面质量。
金刚石刀具材料的品种分类

金刚石刀具材料的品种分类金刚石刀具材料分为单晶金刚石(有天然和人造两种,天然单晶金刚石价格昂贵,被人造单晶金刚石替代)、人造聚晶金刚石(PCD)和人造聚晶金刚石与硬质合金复合刀片(PCD/CC)以及CVD金刚石。
单晶金刚石单晶金刚石用作切削刀具必需是大颗粒的(质量大於0.1g,最小径长不得小於3mm),重要用于表面粗糙度、几何形状精度和尺寸精度有较高要求的精密和超精密加工应用领域。
天然单晶金刚石是金刚石中最耐磨的材料。
它本身质地细密,经过精细研磨,切削刃的刃口钝圆半径可小到0.008~0.005m。
但天然单晶金刚石较脆,其结晶各向异性,不同晶面或同一晶面不同方向的晶体硬度均有差异,在进行刃磨和使用时必需选择合适的方向。
由於使用条件苛刻,加上天然单晶金刚石资源有限,价格非常昂贵,所以生产上大多采纳PCD、PCD/CC和CVD金刚石刀具。
天然单晶金刚石重要用於某些有色金属的超精紧密削加工或黄金首饰的生产中。
人工合成单晶金刚石的尺寸、形状和性能都具有良好的一致性,目前由于高温高压技术日趋成熟,能够制备肯定尺寸的人工合成单晶金刚石,尤其在加工高耐磨的层状木板时,其性能要优于PCD金刚石,不会引起刃口过早钝化。
人造聚晶金刚石(PCD)和人造聚晶金刚石与硬质合金复合刀片(PCD/CC)PCD是在高温(约1800℃)、高压(5~6MPa)下,利用钴等金属结合剂将很多金刚石单晶粉聚晶成多晶体材料,其硬度虽稍低于单晶金刚石,但它是随机取向的金刚石晶粒的聚合,属各向同性,用作切削刀具时可以任意取向刃磨,无需像天然金刚石那样必需选用最佳的解理面作为前刀面。
在切削时,切削刃对意外损坏很不敏感,抗磨损本领也较强,可长时间保持锋利的切削刃,加工时可采纳很高的切削速度和较大的背吃刀量(吃深),使用寿命一般高于WC基硬质合金刀具10~500倍,而且由於PCD中金属结合剂具有导电性,使得PCD便于切割成形,且原材料来源丰富,其价格只有天然金刚石的几非常之一至十几分之一,已成为传统WC基硬质合金刀具的高性能替代品。
PCD双刃刀加工参数表

PCD双刃刀加工参数表
1、PCD刀具介绍
金刚石作为一种超硬刀具材料已广泛应用于切削加工,天然金刚石价格昂贵限制了金刚石刀具的发展,20世纪70年代,人们利用高压合成技术合成了聚晶金刚石(PCD),解决了天然金刚石数量稀少、价格昂贵的问题,使金刚石刀具的应用范围扩展到航空、航天、汽车、电子、石材等多个领域。
聚晶金刚石(PCD)刀具主要用于加工有色金属等非黑色金属,
能够刃磨出很锋利的刃口,得到较好的加工表面,而且还是加工非金属新型材料的首选材料,可以切削硬质合金及工业陶瓷等高硬度产品。
2、PCD刀具的性能优势
(1)PCD的硬度可达8000HV,为硬质合金的80~120倍,而且PCD的耐磨性更好。
(2)PCD的导热系数为700W/MK,为硬质合金的1.5~9倍,甚
至高于PCBN和铜。
因此PCD刀具热量传递迅速,良好的传热性在很
大程度上能够延长刀具寿命。
(3)PCD的摩擦系数一般仅为0.1至0.3,而硬质合金的摩擦系数为0.4~1。
因此PCD刀具可显著减小切削力,从而延长了刀具寿命。
(4)PCD的热膨胀系数小,因此PCD刀具热变形小,加工精度高。
刀具热变形越大,加工出的工件表面质量就越差,要想加工出良好加工表面质量的工件就必须严格控制刀具的热变形。
(5)PCD刀具与有色金属和非金属材料的亲和力小,在加工过程中刀尖不易形成积屑瘤。
刀具与被加工材料的亲和力小,那么在加工过程中被加工材料就不容易粘接在刀具表面,也就不容易形成积屑瘤。
(6)PCD刀具的弹性模量大,断裂强度高(比氧化铝高三倍),切削刃钝圆半径值可以磨得很小,不易断裂,能长期保持切削刃的锋利程度。
刀具材料PCD

XX大学2014~2015 学年秋季学期研究生课程考试课程名称:课程编号:论文题目:刀具材料PCD概述研究生姓名:学号:论文评语:成绩:任课教师:评阅日期:刀具材料PCD概述摘要:好的刀具材料是制造出好的刀具的前提,更是加工出好的产品的关键。
随着制造业的快速发展,金刚石刀具的生产和应用正在逐年增加。
天然金刚石价格昂贵,金刚石广泛应用于切削加工的还是PCD。
本文针对刀具材料PCD做了比较系统的论述,主要包括PCD材料的介绍,PCD复合片及刀具的制造技术,PCD 复合片的主要优缺点以及PCD刀具材料的应用。
关键词:PCD;材料;刀具The overview about cutting tool materials of PCDAbstract:Good tool material is a prerequisite to create a good tool, it is also a key processing of making a good product .With the sharp development of making industry, production and application of diamond tools is increasing year by year.Natural diamonds are expensive,PCD is widely used in cutting .This paper makes a systematic introduction of tool material PCD,including the introduction of PCD materials ,the manufacturing techniques of PCD composite sheet and tool, the main advantages and disadvantages of PCD composite sheet materials and the application of PCD tools.Key words:PCD;Materials ; Tool1引言随着人类生活、生产水平的提高,高速钢刀具已不能满足高加工效率和高加工质量的新要求。
pcd是什么材料
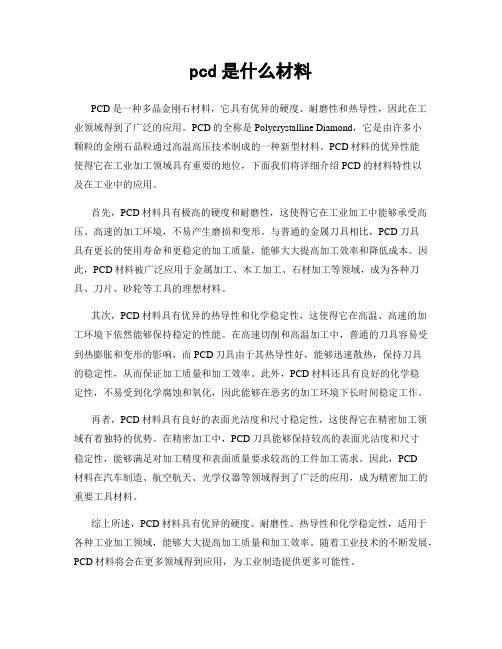
pcd是什么材料PCD是一种多晶金刚石材料,它具有优异的硬度、耐磨性和热导性,因此在工业领域得到了广泛的应用。
PCD的全称是Polycrystalline Diamond,它是由许多小颗粒的金刚石晶粒通过高温高压技术制成的一种新型材料。
PCD材料的优异性能使得它在工业加工领域具有重要的地位,下面我们将详细介绍PCD的材料特性以及在工业中的应用。
首先,PCD材料具有极高的硬度和耐磨性,这使得它在工业加工中能够承受高压、高速的加工环境,不易产生磨损和变形。
与普通的金属刀具相比,PCD刀具具有更长的使用寿命和更稳定的加工质量,能够大大提高加工效率和降低成本。
因此,PCD材料被广泛应用于金属加工、木工加工、石材加工等领域,成为各种刀具、刀片、砂轮等工具的理想材料。
其次,PCD材料具有优异的热导性和化学稳定性,这使得它在高温、高速的加工环境下依然能够保持稳定的性能。
在高速切削和高温加工中,普通的刀具容易受到热膨胀和变形的影响,而PCD刀具由于其热导性好,能够迅速散热,保持刀具的稳定性,从而保证加工质量和加工效率。
此外,PCD材料还具有良好的化学稳定性,不易受到化学腐蚀和氧化,因此能够在恶劣的加工环境下长时间稳定工作。
再者,PCD材料具有良好的表面光洁度和尺寸稳定性,这使得它在精密加工领域有着独特的优势。
在精密加工中,PCD刀具能够保持较高的表面光洁度和尺寸稳定性,能够满足对加工精度和表面质量要求较高的工件加工需求。
因此,PCD材料在汽车制造、航空航天、光学仪器等领域得到了广泛的应用,成为精密加工的重要工具材料。
综上所述,PCD材料具有优异的硬度、耐磨性、热导性和化学稳定性,适用于各种工业加工领域,能够大大提高加工质量和加工效率。
随着工业技术的不断发展,PCD材料将会在更多领域得到应用,为工业制造提供更多可能性。
pcd材料

pcd材料PCD (Polycrystalline Diamond) 是一种具有高硬度和优异耐磨性的材料,由多个小晶体颗粒组成。
PCD材料在工业领域具有广泛的应用,尤其是在切削和磨削工具领域,其独特的性能使其成为一种非常受欢迎的选择。
PCD材料的主要成分是人工合成的金刚石微粉和硬质合金基体。
通过高温高压的工艺,在合适的温度和压力条件下,将金刚石微粉和金属粉末进行烧结,最终形成了坚硬且具有优异耐磨性的PCD材料。
PCD材料具有几个显著的特点。
首先,PCD材料具有极高的硬度,比普通刚玉和硬质合金要高。
其硬度可达到5800-10000HV,使得PCD材料具有出色的切削性能,可以用于切割各种高硬度材料,如铸铁、铝合金、镍合金等。
其次,PCD材料具有出色的耐磨性。
其耐磨性能比一般刚玉和硬质合金高5-10倍,可以大大延长刀具的使用寿命。
这使得PCD材料成为高效率切削工具的理想选择,在高速加工和大批量生产中发挥了重要的作用。
此外,PCD材料还具有良好的导热性能和化学稳定性。
它的导热系数很高,能够迅速将切削过程中产生的热量分散,从而减少切削温度,保护切削刀具不易被热疲劳破坏。
同时,PCD 材料对酸、碱和大部分有机溶剂具有较高的耐腐蚀性,适用于多种工作环境。
在实际应用中,PCD材料可用于制造各种切削工具,如刀具、钻头、车刀和铣刀等。
这些工具广泛用于机械加工、汽车制造、航空航天、电子、模具制造等领域。
虽然PCD材料具有众多优点,但也存在一些限制。
首先,由于其高硬度和脆性,PCD材料容易受到冲击和碰撞而破裂。
因此,在使用过程中需要注意避免过大的冲击力。
其次,PCD 材料的制造成本较高,导致其价格相对较高。
这也限制了其在某些领域的应用。
总之,PCD材料以其高硬度、优异耐磨性和良好的导热性能而受到广泛关注。
在工业领域,PCD材料被广泛应用于切削和磨削工具制造中,并发挥了重要的作用。
随着科学技术的不断进步,相信PCD材料将在更多领域发挥其优势,为人们的生产和生活带来更多便利和效益。
- 1、下载文档前请自行甄别文档内容的完整性,平台不提供额外的编辑、内容补充、找答案等附加服务。
- 2、"仅部分预览"的文档,不可在线预览部分如存在完整性等问题,可反馈申请退款(可完整预览的文档不适用该条件!)。
- 3、如文档侵犯您的权益,请联系客服反馈,我们会尽快为您处理(人工客服工作时间:9:00-18:30)。
耐磨损性能和抗崩刃性能的PCD刀具材料
近年来,为了减少汽车的总重量和燃油费用,铝合金材料在汽车零部件中的使用越来
越多。
为此,加工铝合金汽车零部件用聚晶金刚石(PCD)刀具的使用量也在快速增长。
PCD刀具寿命长,能实现高效、高速、高精度切削加工。
但由于其刀尖强度较低,通
常只适用于精加工,而在切削抗力变化较大的粗加工中容易发生崩刃,且刀具寿命的分散
性较大。
为了克服原有金刚石刀具的缺点,日本住友电工硬质材料公司开发了耐磨损性能
和抗崩刃性能兼优的sumidia DA2200牌号PCD刀具材料。
1.Sumidia DA2200的特点
(1)原有PCD牌号的性能
原有PCD牌号中有网状烧结组织,其最大特征是由金刚石和助烧剂Co组成的单一组织,其中金刚石所占比例最高。
金刚石的抗弯强度在很大程度上取决于其粒度大小。
在该公司
原有的3种不同粒度的PCD牌号Sumidia DA90、DA150、DA200中,Sumidia DA90粒度最大,耐磨性能最好;Sumidia DA200粒度最小,强度和耐破损性最好;Sumidia DA150为中等粒度,耐磨性能与抗崩刃性能匹配平衡,性能优良。
加工铝件时通常采用Sumidia DA150。
(2)Sumidia DA2200的性能
由于实现了超细微金刚石颗粒均匀而牢固的结合,Sumidia DA2200的抗弯强度可与
K10类硬质合金相匹敌,因此大幅度提高了刀尖强度,从而能稳定实现铝合金的粗加工,
并保证了刀具有较长使用寿命。
2.RF型铣刀的性能特点
采用PCD制造的铝合金加工用铣刀可以不受铣削速度的制约,目前高速铣削的速度可
达2000~3000m/min。
但是,在开发高速铣刀时,需要考虑铣刀的轻量化和因离心力可能
导致切削刃及铣刀零件飞出的问题。
(1)刀体采用高强度铝合金
在设计高速铣刀时,如果仍采用质量较大的钢制刀体,就无法减小刀具的旋转力矩,
这就意味着不能缩短铣刀达到设定转速、自动换刀等非切削时间。
虽然可通过去除刀体多
余部分来减轻重量,但去除量过多容易引发高频切削振动。
为解决上述问题,可采用比重
仅为钢的1/2的铝合金作为刀体材料。
但是,普通铝合金的抗拉强度和硬度都只有钢的
1/2,为弥补强度和硬度的不足,采用了抗拉强度为573N/mm2、硬度为HB150的特殊铝合
金材料,其强度和硬度约为普通铝合金的2倍。
(2)刀体结构设计特点
设计刀体结构时,如果采用楔块式紧固机构将刀片固紧在刀体上,容易导致刀体产生
裂纹并使精度恶化;如果采用利用刀片中心孔和螺钉将刀片直接固紧在刀体上的紧固机构,则存在切削刃跳动精度调整范围小、重磨后刀尖高度和直径与新刀不一致等缺点。
为解决
上述问题,采用了先将刀片用螺钉固紧在钢制刀夹上,然后将装好刀片的刀夹紧固在刀体
上的结构设计,这种结构对于消除高频切削振动十分有效。
(3)高速铣刀离心力和加工安全的研究
在高速铣削中,铣刀的转速越高,产生的离心力越大。
离心力的大小与速度的平方成
正比,如φ100mm铣刀以5000m/min的切削速度旋转时,刀片质量为7.3克,作用于其上
的离心力达到1014N(130kgf),刀片夹紧机构必须能承受这样大的离心力而不会发生松动。
现在ISO和DIN标准对高速铣刀的最高转数均有规定。
DIN标准将破坏转数的1/2作为该
铣刀的最高允许转数。
本铣刀在设计时采用了DIN标准。
住友电工通过铣刀破坏性实验和CAE解析两种方式验证了铣刀的安全性。
通过用有限元法进行CAE解析,获得了紧固刀夹
主夹紧螺钉颈部的应力分布状况。
此外还进行了铣刀破坏性试验,主夹紧螺钉的螺纹部分
发生了破损,结果与CAE解析相同。
除了主夹紧机构外,对辅助夹紧部分的安全性也下了
很大功夫,最终设计出了新型RF型铣刀结构。
(4)高效铣削加工
分别用硬质合金刀片和Sumidia DA2200刀片铣削ADC12箱体的加工实例表明,在相同的铣削条件下,Sumidia DA2200刀片的精加工表面粗糙度为Ra0.2μm,刀具寿命是硬质合金刀片的30倍;用Sumidia DA2200刀片精铣变速箱体接合面的加工实例表明,可在切深
1.5mm的条件下一次完成精铣。
在使用卧式加工中心加工、刀柄悬伸量较长时,也能有效
防止高频切削振动。
自润滑轴承
3.SRF型PCD铣刀的特点
为了减少设备投资和厂房面积,降低生产成本,小型加工中心的使用日益增多。
与此
同时,对用于小型加工中心的铣刀需求也日益增加。
为此,住友电工硬质材料公司针对铝
及铝合金加工开发了采用钢制刀体的小直径SRF型PCD铣刀。
该铣刀具有以下特点。
(1)采用将刀片直接紧固在刀体上的夹紧机构
虽然采用钢制刀体,但因直径小,因此在重量方面不会有问题;考虑到采用RF型的机
夹结构会降低刀体刚性,因此采用了将刀片直接紧固在刀体上的夹紧机构。
(2)刀体设计
小型加工中心的主轴较小,所用铣刀可设计为高转速铣刀。
市售小型加工中心的最高
转速为10000~20000r/min,因此将铣刀允许最高转速设计为20000r/min。
为了实现高效
铣削,虽然刀具直径较小,设计时仍应尽可能增加刀齿数。
通常使用内切圆为12.7mm的刀片,本铣刀设计时采用了9.525mm的小规格刀片,以增加刀齿数。
(3)离心力和安全性设计
采用小规格刀片能减小刀片质量,抑制高速旋转时产生的离心力。
当铣刀直径为φ
63mm、刀片质量3.2g、转速为20000r/min时,作用于刀片上的离心力为445N(45kgf)。
刀片紧固螺钉选用M4,其破损力为4900N,相对于离心力而言是安全的。
(4)高效铣削加工实例
使用SRF型Sumidia DA2200牌号PCD小直径铣刀加工凸轮箱(ADC12)的实例表明,加
工12000件后刀尖未崩刃,没有出现任何问题。
用焊接式PCD立铣刀加工电脑箱的实例表明,重磨后刀尖精度控制困难,寿命分散度大,无法继续使用;而使用SRF型可转位PCD铣刀加工时,在确保重磨精度的同时,加工效率也提高了2.5倍。
在高效铣削中,SRF型PCD
铣刀的切削刃比普通PCD铣刀的切削刃增加了5mm的切深量,从而提高了小型零件的大批
量生产能力,用一把铣刀即可完成粗铣和精铣加工。
本文档来自刀网:
转载请注明出处于刀网。