常化炉燃烧控制系统改造_pdf
常化线燃烧系统

2.3.2 常化炉内热电偶的布置为保证炉内各段温度的可控性,首先须对各段设置独立的炉温控制回路。
根据工艺的供热要求,设置20个供热段自动控制。
沿炉长分10个炉节,每个炉节分上、下温度控制段,装料口1.6 m长为不供热的预热段,即供热段长度为68.4m:炉膛上部供热区,从上1段,上2段,直到上10段;炉膛下部供热区,从下1段,下2段,直到下10段;每个供热段都设有2根热电偶,总计40根热电偶.2.3.3 常化炉供热区工作状态与报警功能设置(1)温度测量功能:对于各燃烧控制段,自动选择2支热电偶中一支所测温度值或该2只热电偶所测温度的温度平均值,作为段温度控制的PV值。
(2)炉段温度超温报警功能:当相应炉段的温度超过允许值,系统发出报警信号;(3)测温热电偶断偶报警功能:当任何一只热电偶被烧毁,系统发出报警信号;(4)温度调节器输出限幅功能:根据最大加热速率,对温度调节器输出限幅,防止钢板过热。
3 常化线燃烧系统该控制器为脉冲控制器,和PLC控制器一起完成对常化炉内152个烧嘴的燃烧控制。
控制器的模块配置图见图3-1。
图3-1 MPT模块结构图注:此图为BGT 1的模块原理图,BGT2-10的模块原理图与此相同。
图3-2 MPT 模块原理图3.1 烧嘴的工艺布置整个常化炉共安装配置152个LBE 公司的烧嘴,在炉子上的工艺布置如图3-3所示。
图3-3 152个烧嘴布置图3.2供热区段温度控制功能注:1.常化炉前9个炉节各有16个烧嘴(上8,下8),第10个炉节有8个烧嘴(上4,下4),共152个烧嘴。
常化炉S7-400 PLC常化炉S7-400 PLC图3-4 燃烧控制系统原理图(第10炉节)3.2.1供热区段炉温温度自动调节功能(1)温度指示和控制功能:炉子沿炉长分10个炉节,对每个炉节的上部和下部分别进行炉温自动控制,即整个炉子上、下共有20个温度控制段。
前9个炉节的上、下温度控制段各有8个脉冲控制的烧嘴,第10个炉节的上、下温度控制段各有4个脉冲控制的烧嘴。
加热炉燃烧控制系统的几项改进措施

Metallur g ical Industr y Automation 2002No 4・48・[收稿日期]2001208206;[修改稿收到日期]2002202227[作者简介]曹世海(1968-),男,甘肃会宁人,工程师,主要从事冶金自动化应用工作。
系统与装置加热炉燃烧控制系统的几项改进措施曹世海(酒泉钢铁集团宏兴股份公司,甘肃嘉峪关735100)[摘要]在理论和实际分析的基础上提出了对加热炉常规燃烧控制系统的几项改进,并就改进措施进行了较为详细的描述。
系统自1999年9月投入运行,效果良好。
实践证明,对常规控制系统的改进不但使控制系统更趋完善合理,同时也大大提高了控制质量。
[关键词]加热炉;燃烧控制;改进措施[中图分类号]T G15512[文献标识码]B[文章编号]100027059(2002)0420048203(Hon g xin g Joint 2Stock Com p an y of Jiu q uan Iron and Steel Grou p Co ,Jia y u g uan 735100,China )1问题的提出为了满足轧制工艺要求,需要为加热炉配备高水平且实用性较强的燃烧控制系统,以达到提高钢坯温度控制精度和节能的双重目标。
如何在传统控制理论和控制手段的基础上进行改进以实现加热炉燃烧控制的最优化,在实际工作中,酒钢三轧钢厂对加热炉燃烧控制系统进行了几项改进。
2燃烧控制的几项改进措施211数据处理中的抗干扰数据源的准确与否直接关系到系统能否正常运行。
目前,加热炉介质流量信号的测量仍以节流装置为主,节流装置测流量噪声大,工业现场的电磁干扰等各种干扰比较强,再加上压力变送器的温漂等,都可能导致测量信号的瞬间非真实波动,甚至可能是尖峰脉动,造成控制系统“无谓”波动和不稳定。
因此对工艺过程流量和压力等滞后较小的测量信号进行抗干扰处理是非常必要的。
抗干扰措施除了利用信号输入模板的硬件抗干扰外,在控制软件的设计中采取相应的处理则更为有效。
常、减压炉新型节能燃烧器的应用研究
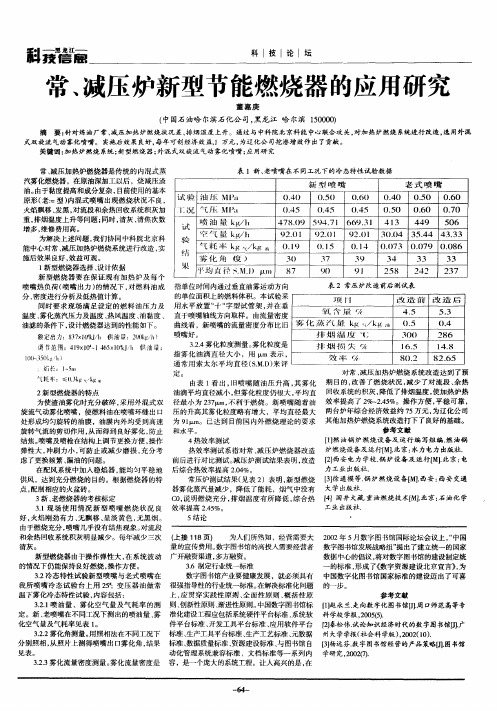
一
6 4—
式 双 旋流 气动 雾化 喷 嘴 。 实施 后 效 果 良好 , 年 可创 经 济 效益 , 万 元 , 每 1 为辽 化 公 司挖 潜 增 效 作 出了贡 献 。 关 键 词 : 热 炉 燃 烧 系统 ; 型燃 烧 器 ; 混式 双 旋 流 气动 雾 化 喷嘴 ; 用研 究 加 新 外 应
常、 减压加热炉燃烧器是传统的内混式蒸 表 1新 、 老喷嘴在不同X ̄ - . LT的冷 态特性试验数据 汽雾化燃烧器,在原油深加工以后 ,烧减压渣 新! 喷 嘴 老 式 喷 嘴 油。 由于黏度提高和成分复杂 , 目前使用的基本 试 验 油 Ml l ’ (. ) ) 4( 0.( 5) (.( ) ) 6 0.0 4 (.O ) 0.0 5 6 原形( =型 ) 老: 内混式喷嘴出现燃烧状况 不良 , l: 气 豫 M Ia l况 (. ) 45 (_5 )4 (.5 ) (.0 4 ) (. 0.0 5 ) 60 7 火焰飘移 、 , 发黑 对流段和余热回收系统积灰加 重, 排烟温度上升等问题 ; 同时, 清灰 、 清焦次数 试 喷 油 最 k /l g 1 47809 . 59 7l 66 3l 4l 449 4. 9. 3 56 O 增多 , 费用高。 维修 验 气 餐 k/ gh 9 . l 9 l 9 . l 3 .4 3 .4 4 . 3 2【 ) 2( ) 2( 00 54 33 ) 为解决上述问题, 我们协 同中科院北京科 气 末 率 k / g 乏 g k ( 1 ( 1 ) 9 . ) 5 . ( 1 0 0 3 0 0 9 (0 6 ) 4 . .7 .7 ) 8 . 能中心对常 、 减压加热炉燃烧系统进行改造 , 实 结 施后效果 良好, 效益可观。 雾化 朗 嫂 ) 3 0 3 7 3 9 3 4 33 3 3 粜 、 均 卣 { ‘ l 新型燃烧器选择 、 设计依据 1 批l ) 1 l 8 7 9 0 9J 258 2 42 2 37 新型燃烧器 要在保证现有 加热炉及每个 表 2常压炉改造前后测试表 喷嘴热负荷 ( 喷嘴 出力 ) 的情况下 , 对燃料油成 指单位时间内通过垂直油雾运动方向 分、 密度进行分析及低热值计算 。 的单位面积上 的燃料体积 。本试验采 项 H 改 造 前 改 造 后 同时要求现场满 足设定的燃料 油压力及 用水平放置 “ “ 型试管架 , 十 字 并在垂 氧 ‘ 4. 5 5. 3 温 度 、 化 蒸 汽压 力 及 温 度 、 风 温 度 、 黏 度 、 直于喷嘴轴线方向取样 。由流量 密度 雾 热 油 雾 化 熊 汽 龌 k /k 油 g g (. )5 (. ) 4 油滤的条件下 , 设计燃烧 器达到的性能如下。 曲线看 ,新喷嘴的流量密度分布 比l 目 喷 嘴好 。 排 烟 潞 俊 。 3 O0 28 6 额定出力:8 7 l'/ 供 油嚣:2 0g h 3 x  ̄k h t. / 0 k/ ) 32 .. 化 粒 度 测 量 。 4雾 雾化 粒 度 是 州 损 火 4 1 5 6. l 8 4. 调 静范嗣:4 9 “ 一 6 × 0k, 供 油量: × r 14 5 1a h J J 指 雾 化 油 滴 直 径 大 小 ,用 I x m表 示 , 1 0 3 ( l) 0  ̄ 5幔 1 效 璋i 8 2 0. 8 65 2. 通常用索太尔 平均直径 (. D) sM. 来评 焰 长 :l 5 ~m 对 常 、 压 加 热 炉燃 烧 系统 改 造 达 到 了预 减 定。 气耗牢:≤ k ,g 3 k 改 减 余 由表 1看 出, 旧喷嘴随油 压升高 , 雾化 期 目的 , 善 了 燃 烧 状 况 , 少 了 对 流 段 、 热 其 降低了排烟温度 , 使加热炉热 2新型燃烧器的特点 油滴平均直径减小, 但雾化粒度仍很大 , 平均直 回收系统的积灰 , %~ . %。操作方便 , 4 平稳可靠 , 为使渣油雾化 时充分破碎 , 采用外混式双 径最小为 2 7 m, 3 1 不利于燃烧 。新喷嘴随着油 效率提高 了 2 2 5  ̄ 5万元 , 为辽化公司 旋流气动雾化 喷嘴 ,使燃料油在喷嘴环缝出 口 压 的升 高 其 雾化 粒 度 略 有增 大 ,平 均 直径 最 大 两 台炉年综合经济效益约 7 处形成均匀旋转 的油膜,油膜内外均受到高速 为 9 m。 已达 到 目前 国 内外 燃 烧 理 论 的要 求 其他加热炉燃烧系统改造打下了良好的基础 。 1 参考文献 旋转气流的剪切作用 , 从而得到良好雾化 , 防止 和水 平 。
循环流化床锅炉燃烧过程自动控制的优化方法
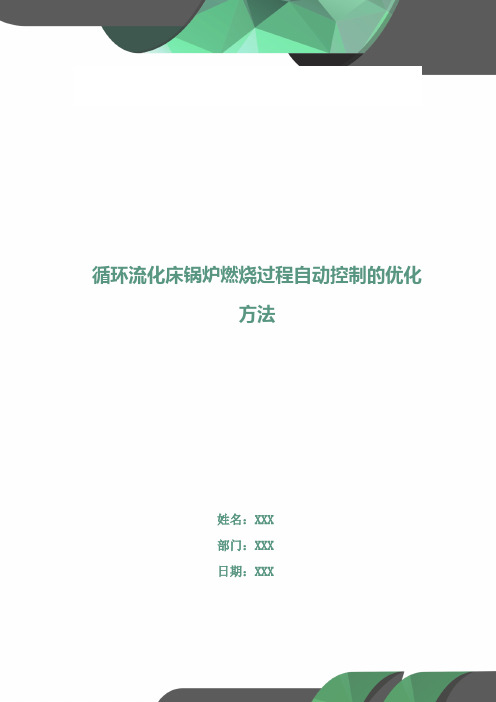
循环流化床锅炉燃烧过程自动控制的优化方法姓名:XXX部门:XXX日期:XXX循环流化床锅炉燃烧过程自动控制的优化方法循环流化床锅炉CFB的控制系统的现状目前,国内中、大型循环流化床锅炉CFB(CirculatingFluidizeBed)投运数量越来越多,这些电厂一般采用DCS(DistributedControlSystem:分散控制系统)进行机组运行控制。
DCS控制系统应用于煤粉锅炉经验已经很成熟,而且自动化水平、安全性都比较高。
对于国内的循环流化床锅炉,目前的DCS控制系统现状基本是套用煤粉炉的DCS控制逻辑,只是稍加改动;另外基于国内电厂基建现状,多数机组都是在抢工期的情况下投运的,所以留给控制系统研究人员的研究时间几乎没有。
然而循环流化床锅炉的燃烧机理十分复杂,循环流化床锅炉的设计尚处于经验设计阶段,系统中变量之间的耦合比较紧密,而且具有严重的非线性。
循环流化床锅炉热工自动控制,特别是燃烧自动控制方面的问题已成为其进一步推广应用的主要障碍,循环流化床锅炉的运行自动化已成为其走向实用的关键之一。
在机组基建调试期间,大家对于控制系统一般都是只要能保证锅炉正常启动和停运就行了,至于控制系统的优化、逻辑的优化、自动的投入与优化、锅炉保护的设定等都是简单地在煤粉炉的控制理念下做一些简单修改。
然而,循环流化床锅炉和煤粉锅炉从燃烧机理上说有很大的区别,这就决定了控制逻辑及理念应该有很大的不同。
所以套用煤粉锅炉的控制理念往往不能适合循环流化床锅炉。
这也就是目前为什么许多循环流化床锅炉很多自动投不上、许多保护不敢投,从而造成循环流化床锅炉的运行人员数量多,劳动强度高,效率低下等,而且锅炉的运行也极为不稳定。
这就给我们的制造厂、电厂及试验研究人员提出了一个第 2 页共 7 页课题:如何使DCS控制系统更加适合循环流化床锅炉。
循环流化床锅炉燃烧过程自动控制的特点循环流化床锅炉不同于煤粉炉,其控制回路多,系统比较复杂,控制系统一般包括以下主要回路:汽包水位控制;过热汽温控制;燃料控制;风量及烟气含氧量控制;炉膛负压控制;床层温度控制;料层高度控制;循环灰控制。
1号常化炉使用手册

1号常化炉维护手册一轧钢电气自动化车间目录1、常化炉简介 (3)2、控制系统 (3)2.1、控制系统构成 (3)2.2、控制柜的构造 (4)3、现场仪表 (6)3.1 现场仪表简介 (6)3.2 常见故障处理 (7)3.2.1变送器常见故障处理 (7)3.2.2电动阀门常见故障处理 (8)3.2.3切断阀常见故障处理 (8)4、风机 (8)4.1 风机控制简介 (8)4.2风机供电 (9)4.3风机接线 (9)5、维护 (10)5.1PLC维护 (10)5.2电柜及不间断电源(UPS)维护 (10)5.3计算机维护 (11)5.4软件维护 (11)6、使用(操作规程) (11)6.1 点炉前风机操作 (11)6.2、风机启动后切断阀操作 (12)6.3、停炉风机操作 (12)6.4、停炉切断阀操作 (12)1、常化炉简介1号常化炉是轧钢厂重要的热处理炉,炉体共分为7段,可完成回火、正火、淬火等热处理工艺。
由于建成较早,自动化程度落后,对常化炉进行了升级改造。
升级改造后,原风机及引风机改为变频风机,余热锅炉拆除,新增加预热器,将原控制系统更换为西门子PLC控制系统。
2、控制系统2.1、控制系统构成1号常化炉使用了西门子的S400系统作为控制系统,控制系统主要有以下几部分构成:处理器,采用400CPU作为控制系统的处理器;子站,该控制系统共分为三个子站,使用300系列模板;通讯,控制系统之间使用DP网线通讯,工程师和控制系统之间使用tc/tip网线进行通讯。
详细组成见图2-1。
图2-12.2、控制柜的构造控制柜的开关均有明显标注,端子接线在柜门上有明显标注,控制柜的构造主要见图2-2、图2-3:图2-2图2-33、现场仪表3.1 现场仪表简介现场仪表在这次改造后全部进行了更换,阀门更换为361系列,变送器更换为EJA系列。
其中变送器的量程(差压范围)见下表:差压(kPa)流量m3/h1段空气流量 1 60001段煤气流量 1 45002段空气流量 1 60002段煤气流量 1 45003段空气流量 1 32003段煤气流量 1 40004段空气流量 1 32004段煤气流量 1 40005段空气流量 1 22005段煤气流量 1 19006段空气流量 1 22006段煤气流量 1 19007段空气流量 1 32007段煤气流量 1 4000冷风压力16热风压力16煤气压力10氮气压力100表3-1电动调节蝶阀是电动单元组合仪表的执行机构,是生产过程自动调节系统中的重要环节之一,他接受控制信号,自动的控制被调节介质的流量等参数,实现对工业生产过程中自动调节。
加热炉智能燃烧控制系统的优化
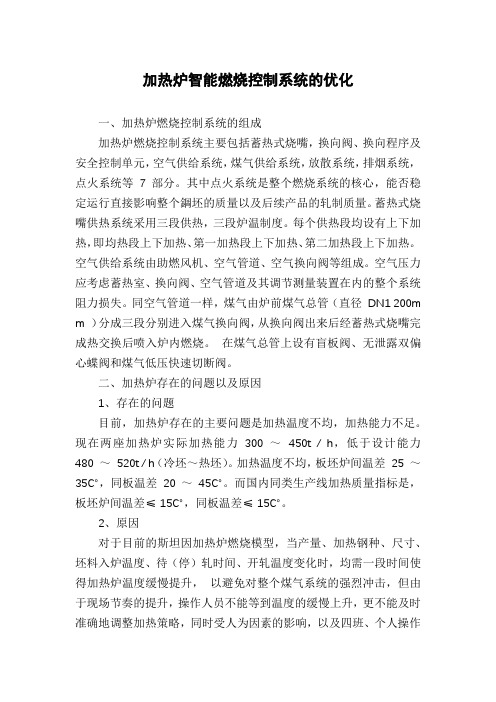
加热炉智能燃烧控制系统的优化一、加热炉燃烧控制系统的组成加热炉燃烧控制系统主要包括蓄热式烧嘴,换向阀、换向程序及安全控制单元,空气供给系统,煤气供给系统,放散系统,排烟系统,点火系统等7 部分。
其中点火系统是整个燃烧系统的核心,能否稳定运行直接影响整个鋼坯的质量以及后续产品的轧制质量。
蓄热式烧嘴供热系统采用三段供热,三段炉温制度。
每个供热段均设有上下加热,即均热段上下加热、第一加热段上下加热、第二加热段上下加热。
空气供给系统由助燃风机、空气管道、空气换向阀等组成。
空气压力应考虑蓄热室、换向阀、空气管道及其调节测量装置在内的整个系统阻力损失。
同空气管道一样,煤气由炉前煤气总管(直径DN1 200m m )分成三段分别进入煤气换向阀,从换向阀出来后经蓄热式烧嘴完成热交换后喷入炉内燃烧。
在煤气总管上设有盲板阀、无泄露双偏心蝶阀和煤气低压快速切断阀。
二、加热炉存在的问题以及原因1、存在的问题目前,加热炉存在的主要问题是加热温度不均,加热能力不足。
现在两座加热炉实际加热能力300 ~450t / h,低于设计能力480 ~520t / h(冷坯~热坯)。
加热温度不均,板坯炉间温差25 ~35℃,同板温差20 ~45℃。
而国内同类生产线加热质量指标是,板坯炉间温差≤ 15℃,同板温差≤ 15℃。
2、原因对于目前的斯坦因加热炉燃烧模型,当产量、加热钢种、尺寸、坯料入炉温度、待(停)轧时间、开轧温度变化时,均需一段时间使得加热炉温度缓慢提升,以避免对整个煤气系统的强烈冲击,但由于现场节奏的提升,操作人员不能等到温度的缓慢上升,更不能及时准确地调整加热策略,同时受人为因素的影响,以及四班、个人操作不统一,空烧时间长,最终造成加热炉温、钢温波动,加热质量差,单位燃耗高,钢坯氧化烧损多,产品质量稳定性差。
三、加热炉加热系统改造方案1、模型跟踪计算需要对钢坯称重、长度、温度规格型号进行信息确认方可入炉,一般钢坯温度大于100℃ 时按照热坯处理,反之为冷坯,加热模型需要对钢坯温度进行修正处理。
锅炉控制系统改造方案
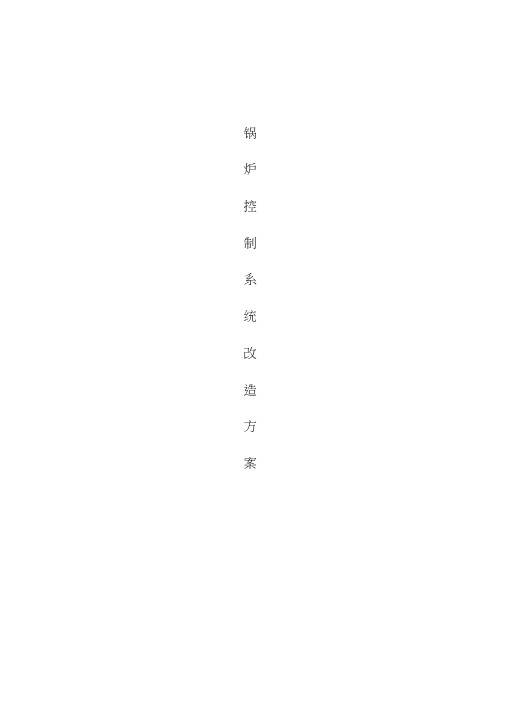
锅炉控制系统改造方案燃气热水锅炉自控系统简介1、产品主器件1)可编程控制器(西门子或合信)2)触摸屏(北京昆仑通态)3)中间继电器(日本OMRON 、施耐德Schneider )、水位控制器(台湾松陵)4)空气开关、交流接触器、热继电器、(德力西、正泰)热水锅炉二合一2、适配燃烧器全配置原装进口意大利利雅路及将军、芬兰奥林、德国欧克等品牌燃烧器。
3、控制功能该自动控制系统采用工业全自动热水锅炉控制技术方案。
硬件按功能模块化设计,信号输入、输出控制器件,全部采用知名品牌器件;软件面向对象,内嵌入精心设计,软硬结合,对热水锅炉全自动安全运行进行自动控制和工况检测。
健全的故障检测、故障报警、故障处理功能,保证了系统的安全可靠运行。
系统采用文本触摸屏,高亮度、全中文显示。
以人机对话方式与用户交换信息,司炉操作通过触摸屏实现一指控制,现场工况参数由触摸屏显示,一目了然,给操作者带来极大方便。
控制系统具有对热水锅炉进行全自动控制及多级安全保护的功能,同时充分考虑锅炉现场和操作检修工的实际,使得锅炉运行更可靠、更安全、更容易检修、降低停炉造成的损失。
控制系统功能概括:1、自动功能:即控制器能根据系统当前采集到的现场信号按用户设置的模式自动对系统进行控制。
2、软手动/ 手动:即用户通过触摸屏/操作面板上的功能键来实现对相应设备的启停等操作以及相应参数的设置。
3、故障识别:系统具备丰富的多级故障检测、故障报警等功能,最大限度地保证了锅炉的安全运行该型号热水锅炉控制柜由PLC 及触摸屏实现全自动控制。
1)燃烧自控当出水温度<设定出水温度下限时,启动锅炉,大火燃烧;讲台式锅炉控制柜当出水温度>出水温度限时,关闭大火,小火燃烧;当出水温度>出水温度上限时,关闭大、小火,停炉待机;当锅炉内热水温度<设定温度中限时,重新启动锅炉,小火燃烧。
2)循环水泵自控出水温度≥设定出水温度下限时,启动循环水泵;停炉时关闭循环水泵。
3)补水泵自控当回水压力低时,启动补水泵;当回水压力高时,关闭补水泵。
锅炉点火控制系统维护总结及改进
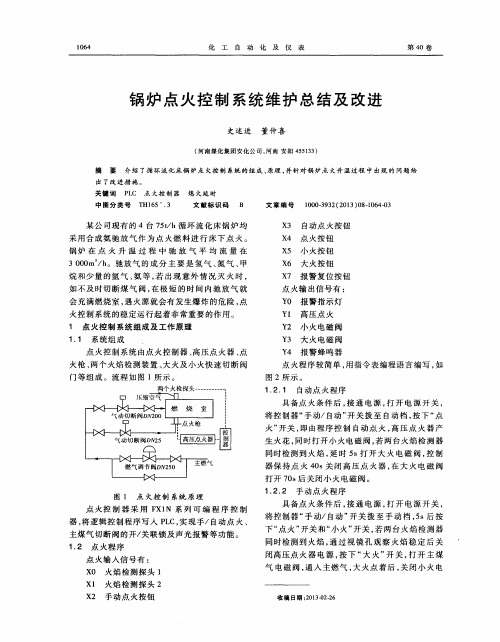
图1 点 火控 制 系 统 原 理
1 . 2 . 2 手动 点火程 序
点火 控 制 器 采 用 F X1 N 系列 可 编 程 序 控 制
具 备点火 条件 后 , 接 通 电源 , 打 开 电源 开关 , 将控制 器 “ 手 动/自动 ” 开关拨至手动档 , 5 s后按 下“ 点火 ” 开关 和 “ 小火 ” 开关 , 若 两 台火焰 检 测 器
^ N P X 5 L r 】 P X 4 ^ N n X 5 0 舳 O R M l O ^ N I 鹕 ^ N I Y 2 O U T —l O L E X 4 ^ N D X 5 O R M I 3 ^ N I 豳 ^ N I Y 2 O U T —l 3 U】 P x 6 O【 , r M1 l L I x 2 0 l X 3 ^ N P x 6 L 工 Y 4 ^ N D X 6 0 舳 0 R 1 1 1 2 ^N I Ml l ^ N I Y 3 0【 , r I 1 1 2 L D F X 4 l D X 6 O R M I 4 ^ N I ■ l l ^ NI Y 3 O U T 一1 4 L D ■ 1 ^ NI 姒 ^ N I T 0 ^ N I ● I 6 L D l ^ N I - l 5 ^ N I T 2 嘲 ^ 岫 x 4 ^ 输 出信 号有 :
Y 0 报警指 示灯 Y l 高压点 火 Y 2 小 火 电磁 阀
Y 3 大 火 电 磁 阀 Y 4 报 警 蜂 鸣 器
点 火控 制系统 由点火 控制器 、 高 压点火 器 、 点 火枪、 两 个火焰 检测 装置 、 大火及 小火快 速切 断 阀 门等组 成 。流程如 图 1 所示 。
同时检测 到火 焰 , 通 过 视镜 孔 观 察火 焰 稳 定后 关
电厂锅炉燃烧过程控制改进方案及实现

控制工程C ontrol Engineering of China Mar .2008Vol.15,No.22008年3月第15卷第2期文章编号:167127848(2008)022******* 收稿日期:2007203222; 收修定稿日期:2007205209基金项目:安徽省发改高技基金资助项目(2005661)作者简介:薛福珍(19492),女,上海人,副教授,研究生,主要从事现代控制理论及应用、电力系统自动化、DCS 等方面的教学与科研工作。
电厂锅炉燃烧过程控制改进方案及实现薛福珍1,刘 涛1,尹 君1,梁 远2,刘洪卫2,梁国杰2(1.中国科学技术大学自动化系,安徽合肥 230027; 2.北京京能热电股份有限公司,北京 100041)摘 要:针对锅炉燃烧系统多变量、强耦合、大时滞的复杂特性,提出一种多变量时滞对象的控制方法,以动态风煤比的形式对燃烧过程实施先进控制。
所实现的改进的多变量Smith 预估算法有效地克服了模型失配对控制的不利影响;多模型智能控制解决了在负荷变化时对象模型的参数不确定性。
对某热电厂锅炉燃烧过程的控制结果表明,该方法易于工程实现,适应性强,控制效果优于原DCS 系统的PI D 控制。
关 键 词:锅炉燃烧系统;多变量时滞控制;多模型;动态风煤比;多变量Smith 预估器中图分类号:TP 273 文献标识码:AIm proved Scheme and Im plement for Boiler C ombustion Processof Thermal P ower PlantXUE Fu 2zhen 1,LIU Tao 1,YIN Jun 1,LIANG Yuan 2,LIU Hong 2wei 2,LIANG Guo 2jie2(1.Department of Automation ,University of Science and T echnology of China ,Hefei 230027,China ;2.Bejing Jingneng Thermal P ower Limited C om pany ,Bejing 100041,China )Abstract :According to the complex features of the boiler combustion system with multivariables ,strong interaction and large time delay ,a con 2trol alg orithm of multi 2variable object with time delay is presented ,s o as to implement advanced control on combustion process using dynamic air 2to 2coal ratios.The m odified multi 2variable Smith predictor effectively overcomes the disadvantage of unmatched m odel.The multiple 2m odel intelligent control s olves the parameter uncertainty of the object m odel when load changing.The control results of the boiler combustion process of certain thermal power plant show that the method possesses performances of easy implementing and wide adaptability compared with PI D con 2trol in DCS.K ey w ords :boiler combustion system ;multi 2variable control with time delay ;multiple m odel ;dynamic air 2to 2coal ratio ;multi 2variable Smith predicator1 引 言锅炉系统是一个多输入多输出的复杂控制对象[1],根据功能可分为燃烧系统、蒸汽发生系统和蒸汽过热系统[2,3]三个相对独立的部分。
(完整版)锅炉燃烧系统的控制系统设计

(完整版)锅炉燃烧系统的控制系统设计⽬录1锅炉⼯艺简介 (1)1.1锅炉的基本结构 (1)1.2⼯艺流程 (2)1.2煤粉制备常⽤系统 (3)2 锅炉燃烧控制 (4)2.1燃烧控制系统简介 (4)2.2燃料控制 (4)2.2.1燃料燃烧的调整 (4)2.2.2燃烧调节的⽬的 (5)2.2.3直吹式制粉系统锅炉的燃料量的调节 (5)2.2.4影响炉内燃烧的因素 (6)2.3锅炉燃烧的控制要求 (11)2.3.1 锅炉汽压的调整 (11)3锅炉燃烧控制系统设计 (14)3.1锅炉燃烧系统蒸汽压⼒控制 (14)3.1.1该⽅案采⽤串级控制来完成对锅炉蒸汽压⼒的控制 (14)3.2燃烧过程中烟⽓氧含量闭环控制 (17)3.2.1 锅炉的热效率 (18)3.2.2反作⽤及控制阀的开闭形式选择 (20)3.2.3 控制系统参数整定 (20)3.3炉膛的负压控制与有关安全保护保护系统 (21)3.3.1炉膛负压控制系统 (22)3.3.2防⽌回⽕的连锁控制系统 (23)3.3.3防⽌脱⽕的选择控制系统 (24)3.4控制系统单元元件的选择(选型) (24)3.4.1蒸汽压⼒变送器选择 (24)3.4.2 燃料流量变送器的选⽤ (24)4 DCS控制系统控制锅炉燃烧 (26)4.1DCS集散控制系统 (26)4.2基本构成 (27)锅炉燃烧系统的控制4.3锅炉⾃动燃烧控制系统 (31)总结 (33)致谢 (34)参考⽂献 (35)1锅炉⼯艺简介1.1锅炉的基本结构锅炉整体的结构包括锅炉本体和辅助设备两⼤部分。
1、锅炉本体锅炉中的炉膛、锅筒、燃烧器、⽔冷壁、过热器、省煤器、空⽓预热器、构架和炉墙等主要部件构成⽣产蒸汽的核⼼部分,称为锅炉本体。
锅炉本体中两个最主要的部件是炉膛和锅筒。
炉膛⼜称燃烧室,是供燃料燃烧的空间。
将固体燃料放在炉排上进⾏⽕床燃烧的炉膛称为层燃炉,⼜称⽕床炉;将液体、⽓体或磨成粉状的固体燃料喷⼊⽕室燃烧的炉膛称为室燃炉,⼜称⽕室炉;空⽓将煤粒托起使其呈沸腾状态燃烧、适于燃烧劣质燃料的炉膛称为沸腾炉,⼜称流化床炉;利⽤空⽓流使煤粒⾼速旋转并强烈⽕烧的圆筒形炉膛称为旋风炉。
循环流化床锅炉燃烧过程自动控制的优化方法通用版

操作规程编号:YTO-FS-PD348循环流化床锅炉燃烧过程自动控制的优化方法通用版In Order T o Standardize The Management Of Daily Behavior, The Activities And T asks Are Controlled By The Determined Terms, So As T o Achieve The Effect Of Safe Production And Reduce Hidden Dangers.标准/ 权威/ 规范/ 实用Authoritative And Practical Standards循环流化床锅炉燃烧过程自动控制的优化方法通用版使用提示:本操作规程文件可用于工作中为规范日常行为与作业运行过程的管理,通过对确定的条款对活动和任务实施控制,使活动和任务在受控状态,从而达到安全生产和减少隐患的效果。
文件下载后可定制修改,请根据实际需要进行调整和使用。
循环流化床锅炉CFB的控制系统的现状目前,国内中、大型循环流化床锅炉CFB (Circulating Fluidize Bed)投运数量越来越多,这些电厂一般采用DCS (Distributed Control System:分散控制系统)进行机组运行控制。
DCS控制系统应用于煤粉锅炉经验已经很成熟,而且自动化水平、安全性都比较高。
对于国内的循环流化床锅炉,目前的DCS控制系统现状基本是套用煤粉炉的DCS控制逻辑,只是稍加改动;另外基于国内电厂基建现状,多数机组都是在抢工期的情况下投运的,所以留给控制系统研究人员的研究时间几乎没有。
然而循环流化床锅炉的燃烧机理十分复杂,循环流化床锅炉的设计尚处于经验设计阶段,系统中变量之间的耦合比较紧密,而且具有严重的非线性。
循环流化床锅炉热工自动控制,特别是燃烧自动控制方面的问题已成为其进一步推广应用的主要障碍,循环流化床锅炉的运行自动化已成为其走向实用的关键之一。
加热炉燃烧控制系统的改造
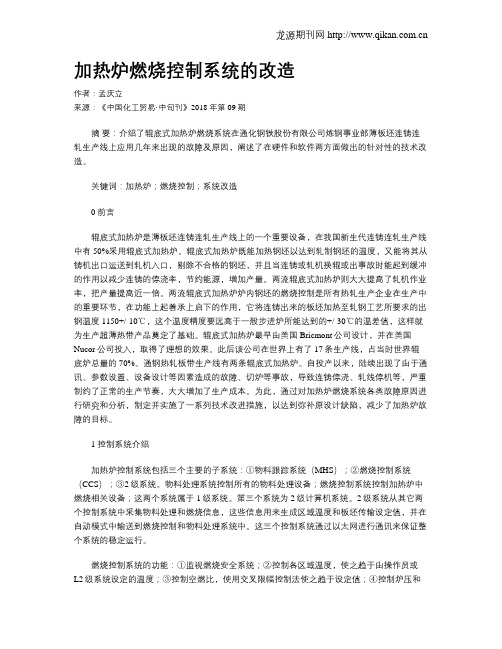
加热炉燃烧控制系统的改造作者:孟庆立来源:《中国化工贸易·中旬刊》2018年第09期摘要:介绍了辊底式加热炉燃烧系统在通化钢铁股份有限公司炼钢事业部薄板坯连铸连轧生产线上应用几年来出现的故障及原因,阐述了在硬件和软件两方面做出的针对性的技术改造。
关键词:加热炉;燃烧控制;系统改造0 前言辊底式加热炉是薄板坯连铸连轧生产线上的一个重要设备,在我国新生代连铸连轧生产线中有50%采用辊底式加热炉。
辊底式加热炉既能加热钢坯以达到轧制钢坯的温度,又能将其从铸机出口运送到轧机入口,剔除不合格的钢坯,并且当连铸或轧机换辊或出事故时能起到缓冲的作用以减少连铸的停浇率,节约能源,增加产量。
两流辊底式加热炉则大大提高了轧机作业率,把产量提高近一倍。
两流辊底式加热炉炉内钢坯的燃烧控制是所有热轧生产企业在生产中的重要环节,在功能上起着承上启下的作用,它将连铸出来的板坯加热至轧钢工艺所要求的出钢温度1150+/-10℃,这个温度精度要远高于一般步进炉所能达到的+/-30℃的温差值,这样就为生产超薄热带产品奠定了基础。
辊底式加热炉最早由美国Bricmont公司设计,并在美国Nucor公司投入,取得了理想的效果。
此后该公司在世界上有了17条生产线,占当时世界辊底炉总量的70%。
通钢热轧板带生产线有两条辊底式加热炉。
自投产以来,陆续出现了由于通讯、参数设置、设备设计等因素造成的故障、切炉等事故,导致连铸停浇、轧线停机等,严重制约了正常的生产节奏,大大增加了生产成本。
为此,通过对加热炉燃烧系统各类故障原因进行研究和分析,制定并实施了一系列技术改进措施,以达到弥补原设计缺陷,减少了加热炉故障的目标。
1 控制系统介绍加热炉控制系统包括三个主要的子系统:①物料跟踪系统(MHS);②燃烧控制系统(CCS);③2级系统。
物料处理系统控制所有的物料处理设备;燃烧控制系统控制加热炉中燃烧相关设备;这两个系统属于1级系统。
第三个系统为2级计算机系统。
常减压加热炉燃烧优化控制仪表改造

第27卷 第4期2020年4月仪器仪表用户INSTRUMENTATIONVol.272020 No.4常减压加热炉燃烧优化控制仪表改造刘惠文(中化泉州石化有限公司 设备管理部,福建 泉州 362000)摘 要:本公司1200万吨/年炼油项目于2014年正式投入生产运营,并产出合格油品。
在生产过程中,加热炉会消耗燃料并排放污染物,而目前常减压装置加热炉的热效率仍有较大的提升空间。
常减压装置2017年综合能耗10.2 kg OE/t,其中加热炉燃料消耗占总能耗的78.6%,占装置能耗比例大,为提高加热炉热效率,并减少装置污染物排放,对常减压装置加热炉进行低氧燃烧控制优化改造。
结合常减压加热炉燃烧优化控制系统改造,重点介绍常减压加热炉控制、CO 在线监测技术、低氧燃烧控制策略组态。
关键词:常减压加热炉控制;CO 在线监测技术;低氧燃烧控制策略组态中图分类号:TH;TP273.2 文献标志码:AReform of Combustion Optimization Control Instrument ofAtmospheric and Vacuum Heating FurnaceLiu Huiwen(Equipment Department Sinochem Quanzhou Petrochemical Co., Ltd., Fujian,Quanzhou, 362000,China)Abstract:The 12 million T / a refining project was put into operation in 2014, and qualified oil products were produced. In the production process, the heating furnace will consume fuel and discharge pollutants. At present, the thermal efficiency of the heating furnace in atmospheric and vacuum distillation unit still has a large space to improve. In 2017, the comprehensive energy consumption of atmospheric and vacuum distillation unit was 10.2 kgoe / T, in which the fuel consumption of heating furnace accounted for 78.6% of the total energy consumption, accounting for a large proportion of the energy consumption of the unit. In order to improve the thermal efficiency of the heating furnace and reduce the pollutant emission of the unit, the heating furnace of atmospheric and vacuum distillation unit was optimized for low oxygen combustion control. Combined with the reform of com-bustion optimization control system of atmospheric and vacuum heater, the control of atmospheric and vacuum heater, CO online monitoring technology and low oxygen combustion control strategy configuration are mainly introduced.Key words:normal decompression furnace control;CO online monitoring technology;configuration of low oxygen combus-tion control strategy加热炉是石化企业重要的耗能设备,同时也是二氧化碳、氮氧化物等污染物排放的主要来源之一。
常化炉安全操作规程(四篇)
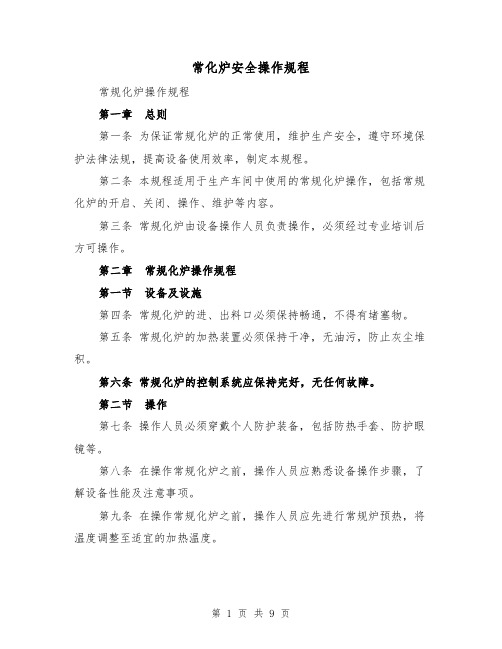
常化炉安全操作规程常规化炉操作规程第一章总则第一条为保证常规化炉的正常使用,维护生产安全,遵守环境保护法律法规,提高设备使用效率,制定本规程。
第二条本规程适用于生产车间中使用的常规化炉操作,包括常规化炉的开启、关闭、操作、维护等内容。
第三条常规化炉由设备操作人员负责操作,必须经过专业培训后方可操作。
第二章常规化炉操作规程第一节设备及设施第四条常规化炉的进、出料口必须保持畅通,不得有堵塞物。
第五条常规化炉的加热装置必须保持干净,无油污,防止灰尘堆积。
第六条常规化炉的控制系统应保持完好,无任何故障。
第二节操作第七条操作人员必须穿戴个人防护装备,包括防热手套、防护眼镜等。
第八条在操作常规化炉之前,操作人员应熟悉设备操作步骤,了解设备性能及注意事项。
第九条在操作常规化炉之前,操作人员应先进行常规炉预热,将温度调整至适宜的加热温度。
第十条加热过程中,操作人员应密切关注设备运行状态,及时调整温度和运行参数。
第十一条加热过程中,操作人员不得离开设备操作位置,且应保持设备周围的整洁。
第十二条加热过程中,操作人员应注意观察常规化炉的运行情况,特别是温度变化和防爆装置是否正常。
第十三条加热过程中,若出现设备异常情况,如温度过高、压力异常等,操作人员应立即停止加热,并将异常情况报告主管人员。
第十四条加热结束后,操作人员应将设备停止运行,并进行常规的设备检查和维护。
第三节维护保养第十五条常规化炉的清洁工作应定期进行,以确保设备的正常运行。
第十六条常规化炉的加热元件应保持清洁干燥,不得有油污等。
第十七条常规化炉的控制系统应经常检查,确保其正常运行。
第十八条常规化炉的防爆装置应定期检查,确保其可靠性。
第十九条常规化炉的操作记录应及时填写,包括开机时间、运行情况、操作人员等信息。
第四节安全措施第二十条操作人员在操作常规化炉时应严格遵守操作规程,不得擅自变更或调整设备运行参数。
第二十一条操作人员应保持工作场所的整洁,不得将废弃物堆放在设备周围。
加热炉燃烧系统自动化控制方案探讨
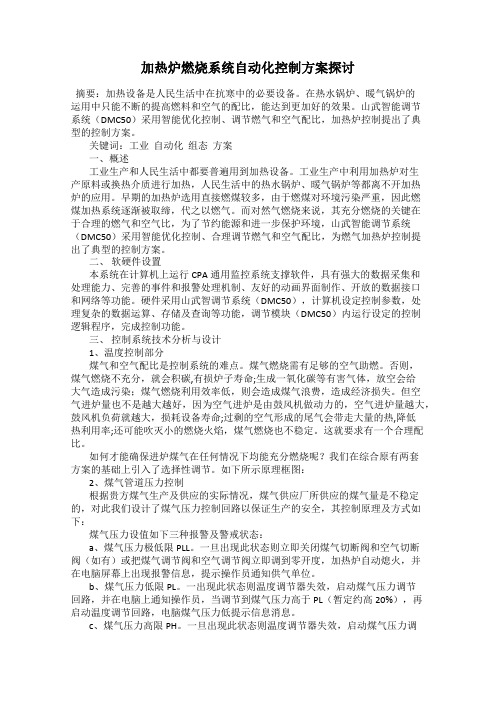
加热炉燃烧系统自动化控制方案探讨摘要:加热设备是人民生活中在抗寒中的必要设备。
在热水锅炉、暖气锅炉的运用中只能不断的提高燃料和空气的配比,能达到更加好的效果。
山武智能调节系统(DMC50)采用智能优化控制、调节燃气和空气配比,加热炉控制提出了典型的控制方案。
关键词:工业自动化组态方案一、概述工业生产和人民生活中都要普遍用到加热设备。
工业生产中利用加热炉对生产原料或换热介质进行加热,人民生活中的热水锅炉、暖气锅炉等都离不开加热炉的应用。
早期的加热炉选用直接燃煤较多,由于燃煤对环境污染严重,因此燃煤加热系统逐渐被取缔,代之以燃气。
而对然气燃烧来说,其充分燃烧的关键在于合理的燃气和空气比,为了节约能源和进一步保护环境,山武智能调节系统(DMC50)采用智能优化控制、合理调节燃气和空气配比,为燃气加热炉控制提出了典型的控制方案。
二、软硬件设置本系统在计算机上运行CPA通用监控系统支撑软件,具有强大的数据采集和处理能力、完善的事件和报警处理机制、友好的动画界面制作、开放的数据接口和网络等功能。
硬件采用山武智调节系统(DMC50),计算机设定控制参数,处理复杂的数据运算、存储及查询等功能,调节模块(DMC50)内运行设定的控制逻辑程序,完成控制功能。
三、控制系统技术分析与设计1、温度控制部分煤气和空气配比是控制系统的难点。
煤气燃烧需有足够的空气助燃。
否则,煤气燃烧不充分,就会积碳,有损炉子寿命;生成一氧化碳等有害气体,放空会给大气造成污染;煤气燃烧利用效率低,则会造成煤气浪费,造成经济损失。
但空气进炉量也不是越大越好,因为空气进炉是由鼓风机做动力的,空气进炉量越大,鼓风机负荷就越大,损耗设备寿命;过剩的空气形成的尾气会带走大量的热,降低热利用率;还可能吹灭小的燃烧火焰,煤气燃烧也不稳定。
这就要求有一个合理配比。
如何才能确保进炉煤气在任何情况下均能充分燃烧呢?我们在综合原有两套方案的基础上引入了选择性调节。
如下所示原理框图:2、煤气管道压力控制根据贵方煤气生产及供应的实际情况,煤气供应厂所供应的煤气量是不稳定的,对此我们设计了煤气压力控制回路以保证生产的安全,其控制原理及方式如下:煤气压力设值如下三种报警及警戒状态:a、煤气压力极低限PLL。
锅炉燃烧器控制系统数字化改造

锅炉燃烧器控制系统数字化改造摘要:长庆油田第三采油厂***作业区真空加热炉现有控制系统在实际工作过程中,所采集的信号是通过现场二次仪表所采集的数据对燃烧器进行控制,不够准确,现场一次仪表试用年限较长,不够精确。
且运行数据无法远传,不能实现集中监控。
报警信息不能存储,故障排除较为繁琐。
通过技术改造以实现数据远传集中监控的功能、现场数据动态清晰显示、实现报警记录可查功能及两地同时报警功能及实现RTU精确控制燃烧器等功能,最终使燃烧器控制系统安全平稳运行。
关键词:燃烧器RTU 采集信息远程控制引言就目前使用的百得燃烧器使用情况看,现有控制系统在实际工作过程中,所采集的信号是通过现场二次仪表所采集的数据对燃烧器进行控制,不够准确,现场一次仪表试用年限较长,不够精确。
所以可能导致控制不够精确。
虽然可以实现自动控制,但是数据无法远传,不能实现集中监控,工作人员无法第一时间了解设备运转情况。
报警信息不能存储,故障排除较为繁琐。
一、控制系统改造概况1.现有控制系统存在的问题:百德燃烧器控制系统在实际使用过程中存在如下的问题和不足:1.1现有温度控制单元、水位控制单元及压力控制单元等控制精度不够精确。
1.2现有控制系统只能实现现场数据显示,无法实现数据远传。
1.3现有元器件配置老化,安全性及准确性能较低。
1.4现有控制箱过于复杂,线路过多,维护工作不方便。
1.5现有显示设备显示不够清晰明了,无动态效果。
1.6现有控制系统无法查看报警信息及故障。
2.控制系统改造内容2.1将原有温度控制器去掉2.2将原有压力控制器去掉2.3将原有液位转换二次仪表去掉2.4添加温度变送单元2.5添加液位信号检测转换仪2.6添加触摸屏3.燃烧器控制系统设计原则3.1确保系统设计效果可控可逆,所有改造措施和策略都是在不改变设备使用和工作原理上进行优化和调整完善;3.2确保系统设计后燃烧器能正常使用并且保证使用中的安全要求;3.3确保系统设计后燃烧器天然气系统的安全性、可用性、稳定性;3.4确保系统设计后锅炉控制系统的安全性、稳定性、先进性;3.5由于原有参与锅炉的各类控制元件较为老化,控制精度不够、控制要求无法满足、无法实现数据集中监控。
常化炉燃烧控制系统改造

常化炉燃烧控制系统改造秦静【期刊名称】《《天津冶金》》【年(卷),期】2019(000)0z1【总页数】3页(P45-47)【关键词】常化炉; 温度; 控制; 烧嘴; 系统; 改造【作者】秦静【作者单位】天津钢铁集团有限公司天津300301【正文语种】中文0 引言当前我厂使用的常化炉为辐射管烧嘴式烧嘴常化炉,温度设计控制在300~900℃,温度设计精度为10℃。
随着工业的不断发展,各种新型钢板材料也层出不穷。
为了能够在钢板生产中除去其内应力,保证其韧性,就必须要经过160℃的低温回火处理,进一步提高韧性,由此来满足钢板在实际使用当中的力学性能需求。
但是160℃低温回火处理已经远远超出了当前常化炉燃烧控制系统当中的生产低温极限值,因此通过对该系统进行改造,实现了超低温度指标钢板的正常生产。
一般而言,对于常化炉燃烧控制系统的改造都是通过减少单个常化炉烧嘴的燃烧输出功率的方式,实现低温回火过程当中的温度下降。
改造的主要方法有两种:一是在原有的常化炉烧嘴的煤气管道上新接入一根管径较细的煤气管路,在钢板进行低温回火处理时可以通过关闭之前的煤气管道直接使用较细的新煤气管路,进而减少煤气量的燃烧;二是在常化炉烧嘴低温回火的燃烧时改进其燃烧策略,通过对每一个区域的烧嘴燃烧周期、燃烧时间加以计算,最后对其加以控制。
这两种方式各有优点,前者能够从整体上对常化炉的温度进行下降控制,而后者则确保了常化炉当中的温度的稳定性和准确性。
1 常化炉燃烧控制器线路的改造常化炉当中的烧嘴点火方式采用的是脉冲点火,常化炉当中燃烧控制器直接控制空气管道上的电磁阀门,可以保证在不同条件下煤气管路的自由切换以及烧嘴的正常点火不会受到影响,因此有必要针对当前的燃烧控制器的线路进行改造。
下面从初始改造方案和最终改造方案对于常化炉燃烧控制器线路的改造展开分析,以下为详细内容。
1.1 初次改造方案为了能够保证煤气管路能够切换到重新接入的较细管道,就需要重点对该系统进行管路改造。
启动锅炉控制系统改造

启动锅炉控制系统改造摘要本文介绍我厂2×50t/h燃气蒸汽锅炉(燃用天然气)控制系统由PLC改为DCS的具体方案。
详细论述了原PLC系统的拆除与新的程控逻辑,并且针对施工方案在现场实施过程中存在的问题,提出了改造方案。
以此方案为基础,完成了启动锅炉控制系统的全面改造。
关键词 PLC;DCS;程控逻辑;施工方案前言采用现有OVATION 的DCS系统的远程I/O控制功能,实现启动锅炉的远程操作和监视,能够达到如下效果:控制系统的统一,提高了电厂控制的自动化水平,提高了现场设备的维护效率、控制平台的统一,消除了数据的孤岛,增强系统数据的互动,保障了电厂完整的控制功能和数据监视模式、控制平台的统一、软件的一致、组态的便捷,为机组大顺序控制的实现创造了有利条件、控制系统软件的统一,利于检修人员的集中掌握,方便了系统的维护、控制系统硬件的统一,减少备件的储备,同时也为热控检修的统一管理提供便利。
1、改造的背景及必要性某电厂建设规模为两套400MW等级、“F”系列高效单轴联合循环热电联产机组。
配备了两台2×50t/h燃气蒸汽锅炉(燃用天然气)。
现场锅炉本体和燃烧器分属不同厂家,分别使用了施耐德和西门子的PLC控制系统,各自独立实现功能,且互相之间联络及兼容性较差。
由于PLC版本较低,所供I/O点数量有限,无法实现对燃气锅炉的顺控控制,运行需长期留有人员在现场控制室。
前期施工过程中,内部接线混乱,厂家无法提供完整准确的终版图示。
因此,实际运行中,在发生跳炉后,维护人员无法准确查出造成跳炉的根本原因。
设备、机柜电源混乱:现场中除了PLC、燃烧器机柜分别从电气MCC间抽屉取电源,其他内部电源无明确标示,甚至出现现场气动门电磁阀电源从PLC机柜内部接取、不同现场设备在燃烧器柜内公用一路电源的现象,给设备维护及使用造成了极大的不便,急需改造。
2、改造方案的描述启动锅炉燃烧器包括燃烧调整,启动锅炉的所有设备都由目前主机使用的DCS控制系统控制,改造后的启动锅炉类似目前我厂化学水系统就地设置操作员站,运行人员可选择集控室监视和操作或就地电子间监视和操作启动锅炉任何设备。
燃气锅炉的燃烧优化控制

燃气锅炉的燃烧优化控制发布时间:2023-02-03T06:00:19.470Z 来源:《中国电业与能源》2022年第18期作者:张进峰辛海涛米春雷刘小飞宋昕东[导读] 燃气蒸汽锅炉以煤气或天然气为燃料,广泛应用于化工、冶金张进峰辛海涛米春雷刘小飞宋昕东陕西煤业化工集团神木能源发展有限公司陕西榆林719300摘要:燃气蒸汽锅炉以煤气或天然气为燃料,广泛应用于化工、冶金、建材等行业。
在燃气锅炉的实际生产运行中,常存在自动化投入率低,受燃料压力、热值不稳定等因素的影响,自动控制效果不佳的问题。
基于以上采用和隆优化的燃烧优化技术(简称BCS),实现锅炉的自动运行,并在自动运行的基础上优化燃烧效果。
关键词:燃气锅炉;优化控制;燃烧优化1 引言陕西煤业化工集团神木能源发展有限公司有4台240t/h高温高压燃气锅炉。
受荒煤气压力、热值波动影响,导致锅炉效率不能长期稳定在最佳状态。
因多数回路均处于人工手动操作模式,空燃比调整不及时,造成燃烧效果不稳定,锅炉效率低。
通过利用和隆优化的BCS通用燃烧优化技术进行改造,对燃烧效果进行自寻优优化控制,从而降低了发电煤气单耗。
实现了锅炉长周期安全、稳定、经济运行。
2 燃烧优化控制方案2.1 燃烧优化技术原理燃气锅炉要实现燃烧的经济性,必需确保燃烧系统处于最佳的燃烧状态,同时尽可能降低热损失。
根据锅炉的燃烧热平衡原理,在很大程度上,锅炉运行中的空燃比k或过量空气系数影响着锅炉的各项热量损失。
如果k的值过于小,就易出现燃气燃烧不充分的状况,从而不充分燃烧热损会增加。
如果k的值过于大,就易引起排烟量增加,从而导致排烟损失增加。
过量空气系数与排烟损失、燃烧效率以及不完全燃烧热损的关系如图1所示。
图1过量空气系数k与燃烧效率的关系在BCS通用燃烧优化控制技术中,为自动寻找最佳空燃比k,采用软测量技术构造了一个可以代表燃烧效果的中间变量Ф,以产生等量的热量用最少的煤气量为优化目标,采用动态滚动寻优算法,在不断的调整过程中找到最佳燃烧状态、自动检测各种因素引起的最佳燃烧点的偏移,并重新将控制点拉回到燃烧效率曲线的“山顶”。
- 1、下载文档前请自行甄别文档内容的完整性,平台不提供额外的编辑、内容补充、找答案等附加服务。
- 2、"仅部分预览"的文档,不可在线预览部分如存在完整性等问题,可反馈申请退款(可完整预览的文档不适用该条件!)。
- 3、如文档侵犯您的权益,请联系客服反馈,我们会尽快为您处理(人工客服工作时间:9:00-18:30)。
常化炉燃烧控制系统改造刘 辉,杨 超(1.武钢热轧总厂中厚板分厂,湖北武汉430083;2.武钢研究院,湖北武汉430080)摘 要:为了实现中厚板160℃低温回火,对中厚板厂1号常化炉的燃烧控制系统进行改造。
通过对燃烧控制器的硬件线路改造,实现了常化炉在不同加热模式下,不同直径的煤气管路自动切换,同时确保燃烧系统的稳定以及安全性。
烧嘴燃烧时间优化后较原来固定开关周期的控制方式,在系统响应速度以及精度上都有很大提升。
改造后,常化炉可以应用于低温回火的生产。
关键词:常化炉;温度控制;烧嘴控制;开关控制中图分类号:TP271+.4 文献标识码:B 文章编号:1008-4371(2015)03-0043-04Revamping of the normalizing furnace’s burner control systemLIU Hui,YANG Chao(1.Platemaking Branch of Hot Strip Rolling Mill of WISCO,Wuhan 430083,China;2.Research and Development Center of WISCO,Wuhan 430080,China)Abstract:To realize the heavy plate tempering at low temperature,i.e.at 160℃,No.1normalizing furnace’s burner control system had been revamped in the heavy plateplant.Through the revamping of the electric circuit of the burner control unit,the gaspipes with different diameters can be switched automatically according to the differentheating mode,and the stability and security of the burner control has been ensured.Comparing to the control mode with the fixed switching cycle,the responding speed andprecision of the control system has been improved dramatically after optimizing theburner switching time.The furnace can be applied for the low temperature tempering.Key words:normalizing furnace;temperature control;burner control;switching control 武钢中厚板1号常化炉是1座开关式明火烧嘴常化炉,于2009年建成投产,其设计温控范围为300~900℃,温度控制精度±10℃。
随着钢板新品种的开发,有些高强度耐磨钢,例如NM400等,需要经过160℃左右的低温回火处理,才能消除钢板内应力,提高钢材韧性,达到产品要求的力学性能。
但此温度要求超出了此常化炉的正常生产低温的极限值。
必须要通过改造,才能满足这种超低温度指标钢板的正常生产。
1 改造方法为了降低低温回火时的温度下限,即减小单个烧嘴的燃烧输出功率。
在改造中采用了2种措施。
1种是在原有的烧嘴煤气管道上并接1个管径较细的煤气管道,在低温生产时,关闭原有煤气管路,使用新管路,以减少燃烧时通向烧嘴的煤气量;另1措施是改进烧嘴在低温回火时的燃烧策略,为每个区域的烧嘴计算出合适的控制周期,以及在周期内的燃烧时间。
这2种方式,前者从整体上控制了炉温下降,而后者保证了温度的稳定和精度。
1.1 燃烧控制器线路的改造烧嘴的点火脉冲,以及煤气、空气的管路上的电磁阀门的通断,都由燃烧控制器IES258来控制。
在改造中,为了实现煤气管路在不同生产模式下的自动切换,以及正常的点火功能,需要对原燃烧控制器的线路进行改造。
下面简单介绍烧嘴控制器的原理,原理图见图1。
烧嘴控制器在接受到PLC的点火信号后,将检测此时烧嘴是否已经点燃,如果已经点燃,则不进行点火程序。
否则进入点火程序。
烧嘴控制器使用的是电离式火焰检测方式。
进入点火程序,烧嘴控制器打开接在11号、12号端子上的空气、煤气电磁阀,同时通过10号端子向点火变压器发出点火脉冲信号,点火变压器将向烧嘴提供6kV的点火电压。
经过3s的检测时间,烧嘴控制器通过检测流经5号,7号端子上的微弱电流,一般为μA(2~20μA)级的电流,来判断烧嘴是否点燃。
如果烧嘴未正常点燃(未检测到足够大的点火电流),则8号、9号端子闭合,向PLC报警。
如果检测到烧嘴正常燃烧,则13号,14号端子闭合,向PLC报告此烧嘴处于燃烧状态。
1.1.1 初始改造方案为了实现低温回火时,煤气管路能切换到较细的管路上,改造中对烧嘴控制线路进行了改造,图2是改造初期的线路图。
由图2可见,线路中,增加了继电器K,它起着切换大小煤气阀的作用。
继电器由PLC控制。
但现场采用了这种设计后,烧嘴点燃的成功率很低,大量的烧嘴在工作中报错。
现在分析其原因。
首先,为控制继电器K的开启时间,PLC必须与IES258打开空气阀门的时间同步。
这种时间同步,得依靠人工调试。
常化炉有128个烧嘴,每个烧嘴都需要人工调式,维护量非常大。
如果以后更换新阀门,阀门开关时间特性不一致,则需要手动修改时间更改程序,维护十分不便利。
其次,为了保持同步,PLC会滞后于点火控制器动作。
所以在低温回火时,点火控制器会先驱动原有管路上的煤气阀打开,然后被PLC切换关闭,细管路上的煤气阀打开,导致IES258的负载变化冲击,极易造成IES258损坏。
其次,这种设计还存在安全隐患。
如果IES258故障,把空气阀切断,但是,小火煤气阀由PLC控制,如果继电器K没有切换过来,则小火煤气阀常开,煤气持续通入炉膛,造成危险。
图1 烧嘴控制器原理图图2 初始改造方案1.1.2 最终改造方案初始设计产生的问题,是由于其违背了“高内聚,低耦合”的系统设计理念。
它设计的低内聚表现在,PLC剥夺了烧嘴控制器对较细管路上的煤气阀的控制。
将1个完整功能,分成了由PLC与烧嘴控制器2个完成。
它的高耦合,表现在PLC需要与烧嘴控制器通讯来确保烧嘴无法点燃时,关闭煤气阀以保证安全,而这些功能都应依赖于烧嘴控制器来完成。
这也导致PLC程序冗杂,且安全性不宜保障。
PLC需要通过手工的方式设定时间来保证空气阀与煤气阀的同步,造成大量的调试和维护成本。
对此,我们把线路做了如图3的改进。
将较细的煤气管路上的电磁阀的电源也接到了烧嘴控制器上。
此时PLC只根据炉温的设定值来对烧嘴控制器控制的煤气管路做切换。
解决了PLC程序冗杂、安全性能不宜保证、系统功能不稳定和维护成本高的问题。
图3 最终改造方案1.2 低温燃烧控制改进除了减小煤气管道的管径,对于1座开关式烧嘴常化炉,其烧嘴的燃烧控制策略更是保证炉温稳定的关键。
因而,在改造中要对PLC控制系统中的燃烧控制程序进行优化,使系统的响应更快,温度更加稳定。
1.2.1 低温回火温度控制系统图4为低温回火温度控制系统的框架图。
设定值SP从热处理炉设置的1条升温曲线上得到。
PV为常化炉内热电偶测得的炉区温度。
这2个温度,通过统一的归一化处理,(计算与1 100℃的百分比)带入到PID控制块中。
PID控制块,根据实际值与目标值得到差值,计算出此时烧嘴应该输出的功率。
烧嘴的功率值通过脉冲宽度调制,得到烧嘴的点火信号。
这个信号,要通过炉温的限幅,才能最终达到烧嘴控制器来驱动烧嘴点火。
图4 低温回火温度控制框架图1.2.2 设置升温/降温曲线当工艺人员设定目标温度时,控制系统并不是立刻把此目标温度作为控制系统此刻要达到的目标温度,否则必然造成炉温控制系统的超调,炉内烧嘴全开、或全关。
炉内温度的迅速变化,将大大缩短炉体以及烧嘴的使用寿命。
控制系统通过设定的升温速率,来计算此刻要达到的目标温度。
在升温时,当此刻系统目标温度与设定温度差大于升温步长时,其计算公式如下。
Setpoint_new[n]=Setpoint_new[n-1]+Gradient_Poistive/Step_Num(1)式中,Setpoint_new[n]为此刻系统控制的目标温度,Setpoint_new[n-1]为上1个周期时系统控制的目标温度,Gradient_Poistive为升温系数,它的单位是℃/h。
Step_Num与程序设定的执行周期有关。
如果程序以3s为1个控制周期,则Step_Num=3 600/3=1 200,如果以1s为1个周期,则其值为3 600。
为了提高温度响应的快速性,将改造前3s的控制周期提高到1s。
这导致系统以后由PID的结果调制到烧嘴的开关脉冲的方式改变。
1.2.3 烧嘴的开关时间控制改进改造前的烧嘴开关时间采用的是简单的脉冲宽度调制方式,即先设定1个固定的开关周期,在此固定的周期内,烧嘴的开启时间与上级PID控制器计算得到的功率成正比。
以1个拥有10个烧嘴的加热区域为例,设定60s为1个周期,烧嘴开启间隔时间为6s,当PID控制器计算出此刻功率需求为80%时,此时该区每个烧嘴的开启时间为60s×80%=48s。
关闭时间则为12s。
下个控制周期到来时,烧嘴的开启时间才会根据上级PID控制的结果来发生变化。
当钢板进入炉内加热段时,由于钢板吸热,会瞬时拉低此区域的温度。
为了保持炉温恒定,希望更多的烧嘴能迅速地开启以提供更多的功率。
当钢板离开时,烧嘴又需要立刻降低输出功率。
常化炉燃烧控制系统改造这对系统的响应性提出了更高的要求。
由于PID控制器每秒计算1次,对于温度控制来说是足够快了。
因而在改造中,减少烧嘴的开关时间周期,是提高系统响应性的关键。
但是烧嘴的控制周期,也不能太短,否则,烧嘴的开关太频繁,容易造成烧嘴的故障。
在保证烧嘴的最低开启时间和最低关闭时间的基础上,改进的算法使烧嘴的控制周期尽可能的短。
在输出功率大于50%时,由于烧嘴的开启时间比烧嘴的关闭时间长,所以应该保证烧嘴的最短关闭时间。
在输出功率小于50%时,由于烧嘴的关闭时间比开启时间长,所以应该保证烧嘴的最低开启时间。
烧嘴的开启时间Time_on以及关闭时间Time_off由公式(2)(3)计算。
Time_on=Time_off_min×Y_contr1-Y_contr(Y_contr>50%)Time_on_min(Y_contr≤50%烅烄烆)(2)Time_off=Time_on_min(Y_contrr>50%)Time_on_minxY_contr-Time_on_min(Y_contr≤50%烅烄烆)(3)式中,Time_on为烧嘴的开启时间;Time_off为关闭时间;Y_contr为控制烧嘴的输出功率;Time_on_min为设定的烧嘴最短开启时间;Time_off_min为设定的烧嘴最短关断时间。