MC10H210FNR2中文资料
MC10H641FNR2G;MC10H641FNG;MC10H641FNR2;MC100H641FN;MC100H641FNG;中文规格书,Datasheet资料

MC10H641, MC100H641 Single Supply PECL to TTL 1:9 Clock Distribution ChipDescriptionThe MC10H/100H641 is a single supply, low skew translating 1:9 clock driver. Devices in the ON Semiconductor H641 translator series utilize the PLCC−28 for optimal power pinning, signal flow through and electrical performance.The device features a 24 mA TTL output stage, with AC performance specified into a 50 pF load capacitance. A latch is provided on−chip. When LEN is LOW (or left open, in which case it is pulled LOW by the internal pulldown) the latch is transparent. A HIGH on the enable pin (EN) forces all outputs LOW. Both the LEN and EN pins are positive ECL inputs.The V BB output is provided in case the user wants to drive the device with a single−ended input. For single−ended use, the V BB should be connected to the D input and bypassed with a 0.01 m F capacitor.The 10H version of the H641 is compatible with positiveMECL 10H™ logic levels. The 100H version is compatible with positive 100K levels.Features•PECL − TTL Version of Popular ECLinPS E111•Low Skew•Guaranteed Skew Spec•Latched Input•Differential ECL Internal Design•V BB Output for Single−Ended Use•Single +5.0 V Supply•Logic Enable•Extra Power and Ground Supplies•Separate ECL and TTL Supply Pins•Pb−Free Packages are Available**For additional information on our Pb−Free strategy and soldering details, please download the ON Semiconductor Soldering and Mounting Techniques Reference Manual, SOLDERRM/D.MARKING DIAGRAM*xxx= 10 or 100A= Assembly LocationWL= Wafer LotYY= YearWW= Work WeekG=Pb−Free PackagePLCC−28FN SUFFIXCASE 776MCxxxH641GAWLYYWW1*For additional marking information, refer toApplication Note AND8002/D.See detailed ordering and shipping information in the package dimensions section on page 8 of this data sheet.ORDERING INFORMATIONV BB D D VE LEN GE EN1GT Q5VT Q4VT Q3GTGT Q6VT Q7VT Q8GT GTQ2VTQ1VTQ0GT5678910112524232221201926272823418171615141312Figure 1. Pinout: PLCC −28 (Top View)TTL OutputsQ0Q1Q2Q3Q4Q5Q6Q7Q8Figure 2. Logic DiagramTable 2. 10H PECL DC CHARACTERISTICSSymbol Characteristic Condition0°C25°C85°CUnit Min Max Min Max Min MaxI INH Input HIGH Current255175175m A I IL Input LOW Current0.50.50.5m A V IH Input HIGH Voltage V E = 5.0 V (Note 1) 3.83 4.16 3.87 4.19 3.94 4.28V V IL Input LOW Voltage V E = 5.0 V (Note 1) 3.05 3.52 3.05 3.52 3.05 3.55V V BB Output Reference Voltage V E = 5.0 V (Note 1) 3.62 3.73 3.65 3.75 3.69 3.81V NOTE:Device will meet the specifications after thermal equilibrium has been established when mounted in a test socket or printed circuit board with maintained transverse airflow greater than 500 lfpm. Electrical parameters are guaranteed only over the declared operating temperature range. Functional operation of the device exceeding these conditions is not implied. Device specification limit values are applied individually under normal operating conditions and not valid simultaneously.1.PECL V IH, V IL, and V BB are referenced to VE and will vary 1:1 with the power supply. The levels shown are for VE = 5.0 V.Table 3. 100H PECL DC CHARACTERISTICSSymbol Characteristic Condition0°C25°C85°CUnit Min Max Min Max Min MaxI INH Input HIGH Current255175175m A I INL Input LOW Current0.50.50.5m A V IH Input HIGH Voltage V E = 5.0 V (Note 2) 3.835 4.120 3.835 4.120 3.835 4.120V V IL Input LOW Voltage V E = 5.0 V (Note 2) 3.190 3.525 3.190 3.525 3.190 3.525V V BB Output Reference Voltage V E = 5.0 V (Note 2) 3.62 3.74 3.62 3.74 3.62 3.74V NOTE:Device will meet the specifications after thermal equilibrium has been established when mounted in a test socket or printed circuit board with maintained transverse airflow greater than 500 lfpm. Electrical parameters are guaranteed only over the declared operating temperature range. Functional operation of the device exceeding these conditions is not implied. Device specification limit values are applied individually under normal operating conditions and not valid simultaneously.2.PECL V IH, V IL, and V BB are referenced to VE and will vary 1:1 with the power supply. The levels shown are for VE = 5.0 V.Table 4. DC CHARACTERISTICS (V T = V E = 5.0 V ± 5%)Symbol CharacteristicT A = 0°C T A = + 25°C T A = + 85°CUnit Min Typ Max Min Typ Max Min Typ MaxI EE Power Supply CurrentPECL243024302430mA I CCH TTL243024302430mA I CCL273527352735mA NOTE:Device will meet the specifications after thermal equilibrium has been established when mounted in a test socket or printed circuit board with maintained transverse airflow greater than 500 lfpm. Electrical parameters are guaranteed only over the declared operating temperature range. Functional operation of the device exceeding these conditions is not implied. Device specification limit values are applied individually under normal operating conditions and not valid simultaneously.Table 5. TTL DC CHARACTERISTICS (V T = V E = 5.0 V ± 5%)Symbol0°C25°C85°C Characteristic Condition Min Max Min Max Min Max UnitV OH Output HIGH Voltage I OH = −15 mA 2.5 2.5 2.5V V OL Output LOW Voltage I OL = 24 mA0.50.50.5V I OS Output Short Circuit Current V OUT = 0 V−100−225−100−225−100−225mA NOTE:Device will meet the specifications after thermal equilibrium has been established when mounted in a test socket or printed circuit board with maintained transverse airflow greater than 500 lfpm. Electrical parameters are guaranteed only over the declared operating temperature range. Functional operation of the device exceeding these conditions is not implied. Device specification limit values are applied individually under normal operating conditions and not valid simultaneously.Table 6. AC CHARACTERISTICS (V T = V E = 5.0 V ± 5%)Characteristic T J = 0°C T J = + 25°C T J = + 85°CSymbol Condition Min Typ Max Min Typ Max Min Typ Max Unitt PLH t PHL Propagation DelayD to QCL = 50 pF (Note 3) 5.005.365.505.866.006.364.865.275.365.775.866.275.085.435.585.936.086.43nst skew Device SkewPart−to−PartSingle V CCOutput−to−Output CL = 50 pF (Note 4)CL = 50 pF (Note 5)CL = 50 pF (Note 6)100075035010007503501000750350pst PLH t PHL Propagation DelayLEN to QCL = 50 pF 4.9 6.9 4.9 6.9 5.07.0nst PLH t PHL Propagation DelayEN to QCL = 50 pF 5.07.0 4.9 6.9 5.07.0nst r t f Output Rise/Fall0.8 V to 2.0 VCL = 50 pF 1.71.61.71.61.71.6nsf MAX Max Input Frequency CL = 50 pF (Note 7)656565MHz t S Setup Time0.750.500.750.500.750.50ns t H Hold Time0.750.500.750.500.750.50ns NOTE:Device will meet the specifications after thermal equilibrium has been established when mounted in a test socket or printed circuit board with maintained transverse airflow greater than 500 lfpm. Electrical parameters are guaranteed only over the declared operating temperature range. Functional operation of the device exceeding these conditions is not implied. Device specification limit values are applied individually under normal operating conditions and not valid simultaneously.3.Propagation delay measurement guaranteed for junction temperatures. Measurements performed at 50 MHz input frequency.4.Skew window guaranteed for a single temperature across a V CC = V T = V E of 4.75 V to5.25 V (See Application Note in this data sheet).5.Skew window guaranteed for a single temperature and single V CC = V T = V E6.Output−to−output skew is specified for identical transitions through the device.7.Frequency at which output levels will meet a 0.8 V to 2.0 V minimum swing.Determining Skew for a Specific ApplicationThe H641 has been designed to meet the needs of very low skew clock distribution applications. In order to optimize the device for this application special considerations are necessary in the determining of the part−to−part skew specification limits. Older standard logic devices are specified with relatively slack limits so that the device can be guaranteed over a wide range of potential environmental conditions. This range of conditions represented all of the potential applications in which the device could be used. The result was a specification limit that in the vast majority of cases was extremely conservative and thus did not allow for an optimum system design. For non−critical skew designs this practice is acceptable, however as the clock speeds of systems increase overly conservative specification limits can kill a design.The following will discuss how users can use the information provided in this data sheet to tailor a part−to−part skew specification limit to their application. The skew determination process may appear somewhat tedious and time consuming, however if the utmost in performance is required this procedure is necessary. For applications which do not require this level of skew performance a generic part−to−part skew limit of 2.5 ns can be used. This limit is good for the entire ambient temperature range, the guaranteed V CC (V T, V E) range and the guaranteed operating frequency range.Temperature DependenceA unique characteristic of the H641 data sheet is that the AC parameters are specified for a junction temperature rather than the usual ambient temperature. Because very few designs will actually utilize the entire commercial temperature range of a device a tighter propagation delay window can be established given the smaller temperature range. Because the junction temperature and not the ambient temperature is what affects the performance of the device the parameter limits are specified for junction temperature. In addition the relationship between the ambient and junction temperature will vary depending on the frequency, load and board environment of the application. Since these factors are all under the control of the user it is impossible to provide specification limits for every possible application. Therefore a baseline specification was established for specific junction temperatures and the information that follows will allow these to be tailored to specific applications.Since the junction temperature of a device is difficult to measure directly, the first requirement is to be able to “translate” from ambient to junction temperatures. The standard method of doing this is to use the power dissipation of the device and the thermal resistance of the package. For a TTL output device the power dissipation will be a function of the load capacitance and the frequency of the output. The total power dissipation of a device can be described by the following equation:P D (watts) = I CC (no load) * V CC +V S* V CC * f * C L * # Outputswhere:V S= Output V oltage Swing = 3.0 Vf = Output FrequencyC L = Load CapacitanceI CC = I EE + I CCHFigure 1 plots the I CC versus Frequency of the H641 with no load capacitance on the output. Using this graph and the information specific to the application a user can determine the power dissipation of the H641.Figure 1. I CC versus f (No Load)01020304050607080FREQUENCY (MHz)NORMALIZEDICC12345Figure 2 illustrates the thermal resistance (in °C/W) for the PLCC−28 under various air flow conditions. By reading the thermal resistance from the graph and multiplying by the power dissipation calculated above the junction temperature increase above ambient of the device can be calculated.02004006008001000AIRFLOW (LFPM)THERMALRESISTANCE(3040506070C/W)°Figure 2. j JA versus Air FlowFinally taking this value for junction temperature and applying it to Figure 3 allows the user to determine thepropagation delay for the device in question. A more common use would be to establish an ambient temperature range for the H641’s in the system and utilize the above methodology to determine the potential increased skew of the distribution network. Note that for this information if the T PD versus Temperature curve were linear the calculations would not be required. If the curve were linear over all temperatures a simple temperature coefficient could be provided.Figure 3. T PD versus Junction Temperature−30JUNCTION TEMPERATURE (P R O P A G A T I O N D E L A Y (n s )5.2−101030507090110130°C)5.45.65.86.06.26.4V CC DependenceTTL and CMOS devices show a significant propagationdelay dependence with V CC . Therefore the V CC variation in a system will have a direct impact on the total skew of the clock distribution network. When calculating the skew between two devices on a single board it is very likely an assumption of identical V CC ’s can be made. In this case the number provided in the data sheet for part −to −part skew would be overly conservative. By using Figure 4 the skew given in the data sheet can be reduced to represent a smaller or zero variation in V CC . The delay variation due to the specified V CC variation is ≈ 270 ps. Therefore, the 1 ns window on the data sheet can be reduced by 270 ps if the devices in question will always experience the same V CC .The distribution of the propagation delay ranges given in the data sheet is actually a composite of three distributions whose means are separated by the fixed difference inpropagation delay at the typical, minimum and maximum V CC .Figure 4. D T PD versus V CC4.75VCC (V)T −1404.85 4.955.05 5.15 5.25−100−60−202060100140ΔP D (p s )Capacitive Load DependenceAs with V CC the propagation delay of a TTL output is intimately tied to variation in the load capacitance. The skew specifications given in the data sheet, of course, assume equal loading on all of the outputs. However situations could arise where this is an impossibility and it may be necessary to estimate the skew added by asymmetric loading. In addition the propagation delay numbers are provided only for 50 pF loads, thus necessitating a method of determining the propagation delay for alternative loads.Figure 5 shows the relationship between the two propagation delays with respect to the capacitive load on the output. Utilizing this graph and the 50 pF limits the specification of the H641 can be mapped into a spec for either a different value load or asymmetric loads.Figure 5. T PD versus LoadCAPACITIVE LOAD (pF)M O R M A L I Z E D P R O P A G A T I O N D E L A Y (n s )0.751020304050607080901000.800.850.900.951.001.051.101.15Rise/Fall Skew DeterminationThe rise−to−fall skew is defined as simply the difference between the T PLH and the T PHL propagation delays. This skew for the H641 is dependent on the V CC applied to the device. Notice from Figure 4 the opposite relationship of T PD versus V CC between T PLH and T PHL. Because of this the rise−to−fall skew will vary depending on V CC. Since in all likelihood it will be impossible to establish the exact value for V CC, the expected variation range for V CC should be used. If this variation will be the ± 5% shown in the data sheet the rise−to−fall skew could be established by simply subtracting the fastest T PLH from the slowest T PHL; this exercise yields 1.41 ns. If a tighter V CC range can be realized Figure 4 can be used to establish the rise−to−fall skew. Specification Limit Determination ExampleThe situation pictured in Figure 6 will be analyzed as an example. The central clock is distributed to two different cards; on one card a single H641 is used to distribute the clock while on the second card two H641’s are required to supply the needed clocks. The data sheet as well as the graphical information of this section will be used to calculate the skew between H641a and H641b as well as the skew between all three of the devices. Only the T PLH will be analyzed, the T PHL numbers can be found using the same technique. The following assumptions will be used:−All outputs will be loaded with 50 pF−All outputs will toggle at 30 MHz−The V CC variation between the two boards is ± 3 %−The temperature variation between the threedevices is ± 15°C around an ambient of 45°C.−500 lfpm air flowThe first task is to calculate the junction temperature for the devices under these conditions. Using the power equation yields:P D=I CC (no load) * V CC +V CC * V S * f * C L * # outputs=4.3 * 48m A * 5.0 V + 5.0 V * 3.0 V * 30 MHz *50 pF * 9=432 mW + 203 mW = 635 mWUsing the thermal resistance graph of Figure 2 yields a thermal resistance of 41°C/W which yields a junction temperature of 71°C with a range of 56°C to 86°C. Using the T PD versus Temperature curve of Figure 3 yields a propagation delay of 5.42 ns and a variation of 0.19 ns. Since the design will not experience the full ± 5% V CC variation of the data sheet the 1.0 ns window provided will be unnecessarily conservative. Using the curve of Figure 4 shows a delay variation due to a ± 3% V CC variation of ± 0.075 ns. Therefore the 1.0 ns window can be reduced to 1.0 ns − (0.27 ns − 0.15 ns) = 0.88 ns. Since H641a and H641b are on the same board we will assume that they will always be at the same V CC; therefore the propagation delay window will only be 1 ns − 0.27 ns = 0.73 ns.Putting all of this information together leads to a skew between all devices of0.19 ns + 0.88 ns(temperature + supply, and inherent device),while the skew between devices A and B will be only 0.19 ns + 0.73 ns(temperature + inherent device only).In both cases, the propagation delays will be centered around 5.42 ns, resulting in the following t PLH windows: T PLH = 4.92 ns − 5.99 ns; 1.07 ns window(all devices)T PLH= 5.00 ns − 5.92 ns; 0.92 ns window(devices a & b)Of course the output−to−output skew will be as shown in the data sheet since all outputs are equally loaded.This process may seem cumbersome, however the delay windows, and thus skew, obtained are significantly better than the conservative worst case limits provided at the beginning of this note. For very high performance designs, this extra information and effort can mean the difference between going ahead with prototypes or spending valuableFigure 6. Example ApplicationORDERING INFORMATIONDevice Package Shipping†MC10H641FN PLCC−2837 Units / Rail37 Units / RailMC10H641FNG PLCC−28(Pb−Free)MC10H641FNR2PLCC−28500 / Tape & Reel500 / Tape & ReelMC10H641FNR2G PLCC−28(Pb−Free)MC100H641FN PLCC−2837 Units / Rail37 Units / RailMC100H641FNG PLCC−28(Pb−Free)MC100H641FNR2PLCC−28500 / Tape & Reel500 / Tape & ReelMC100H641FNR2G PLCC−28(Pb−Free)†For information on tape and reel specifications, including part orientation and tape sizes, please refer to our Tape and Reel Packaging Specifications Brochure, BRD8011/D.Resource Reference of Application NotesAN1405/D−ECL Clock Distribution TechniquesAN1406/D−Designing with PECL (ECL at +5.0 V)AN1503/D−ECLinPS t I/O SPiCE Modeling KitAN1504/D−Metastability and the ECLinPS FamilyAN1568/D−Interfacing Between LVDS and ECLAN1672/D−The ECL Translator GuideAND8001/D−Odd Number Counters DesignAND8002/D−Marking and Date CodesAND8020/D−Termination of ECL Logic DevicesAND8066/D−Interfacing with ECLinPSAND8090/D−AC Characteristics of ECL DevicesPACKAGE DIMENSIONSPLCC −28FN SUFFIXPLASTIC PLCC PACKAGECASE 776−02ISSUE ESL−M S 0.010 (0.250) NST VIEW SNOTES:1.DATUMS −L−, −M−, AND −N− DETERMINED WHERE TOP OF LEAD SHOULDER EXITS PLASTIC BODY AT MOLD PARTING LINE.2.DIMENSION G1, TRUE POSITION TO BEMEASURED AT DATUM −T−, SEATING PLANE.3.DIMENSIONS R AND U DO NOT INCLUDE MOLD FLASH. ALLOWABLE MOLD FLASH IS 0.010 (0.250) PER SIDE.4.DIMENSIONING AND TOLERANCING PER ANSI Y14.5M, 1982.5.CONTROLLING DIMENSION: INCH.6.THE PACKAGE TOP MAY BE SMALLER THAN THE PACKAGE BOTTOM BY UP TO 0.012(0.300). DIMENSIONS R AND U ARE DETERMINED AT THE OUTERMOST EXTREMES OF THE PLASTIC BODY EXCLUSIVE OF MOLD FLASH, TIE BAR BURRS, GATE BURRS AND INTERLEAD FLASH, BUT INCLUDING ANY MISMATCH BETWEEN THE TOP AND BOTTOM OF THE PLASTIC BODY.7.DIMENSION H DOES NOT INCLUDE DAMBAR PROTRUSION OR INTRUSION. THE DAMBAR PROTRUSION(S) SHALL NOT CAUSE THE H DIMENSION TO BE GREATER THAN 0.037(0.940). THE DAMBAR INTRUSION(S) SHALL NOT CAUSE THE H DIMENSION TO BE SMALLER THAN 0.025 (0.635).DIM MIN MAX MIN MAX MILLIMETERSINCHES A 0.4850.49512.3212.57B 0.4850.49512.3212.57C 0.1650.180 4.20 4.57E 0.0900.110 2.29 2.79F 0.0130.0190.330.48G 0.050 BSC 1.27 BSC H 0.0260.0320.660.81J 0.020−−−0.51−−−K 0.025−−−0.64−−−R 0.4500.45611.4311.58U 0.4500.45611.4311.58V 0.0420.048 1.07 1.21W 0.0420.048 1.07 1.21X 0.0420.056 1.07 1.42Y −−−0.020−−−0.50Z 2 10 2 10 G10.4100.43010.4210.92K10.040−−− 1.02−−−____ON Semiconductor and are registered trademarks of Semiconductor Components Industries, LLC (SCILLC). SCILLC reserves the right to make changes without further notice to any products herein. SCILLC makes no warranty, representation or guarantee regarding the suitability of its products for any particular purpose, nor does SCILLC assume any liability arising out of the application or use of any product or circuit, and specifically disclaims any and all liability, including without limitation special, consequential or incidental damages.“Typical” parameters which may be provided in SCILLC data sheets and/or specifications can and do vary in different applications and actual performance may vary over time. All operating parameters, including “Typicals” must be validated for each customer application by customer’s technical experts. SCILLC does not convey any license under its patent rights nor the rights of others. SCILLC products are not designed, intended, or authorized for use as components in systems intended for surgical implant into the body, or other applications intended to support or sustain life, or for any other application in which the failure of the SCILLC product could create a situation where personal injury or death may occur. Should Buyer purchase or use SCILLC products for any such unintended or unauthorized application, Buyer shall indemnify and hold SCILLC and its officers, employees, subsidiaries, affiliates,and distributors harmless against all claims, costs, damages, and expenses, and reasonable attorney fees arising out of, directly or indirectly, any claim of personal injury or death associated with such unintended or unauthorized use, even if such claim alleges that SCILLC was negligent regarding the design or manufacture of the part. SCILLC is an Equal Opportunity/Affirmative Action Employer. This literature is subject to all applicable copyright laws and is not for resale in any manner.PUBLICATION ORDERING INFORMATIONECLinPS is a trademark of Semiconductor Components Industries, LLC (SCILLC).MECL 10H is a trademark of Motorola, Inc.分销商库存信息:ONSEMIMC10H641FNR2G MC10H641FNG MC10H641FNR2 MC100H641FN MC100H641FNG MC100H641FNR2 MC100H641FNR2G MC10H641FN。
飞凌OK210硬件手册说明书
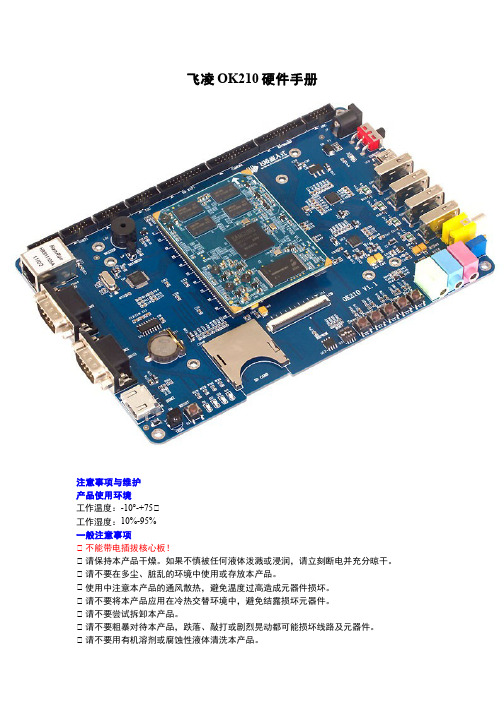
飞凌OK210硬件手册注意事项与维护产品使用环境工作温度:-10°-+75℃工作湿度:10%-95%一般注意事项℃ 不能带电插拔核心板!℃ 请保持本产品干燥。
如果不慎被任何液体泼溅或浸润,请立刻断电并充分晾干。
℃ 请不要在多尘、脏乱的环境中使用或存放本产品。
℃ 使用中注意本产品的通风散热,避免温度过高造成元器件损坏。
℃ 请不要将本产品应用在冷热交替环境中,避免结露损坏元器件。
℃ 请不要尝试拆卸本产品。
℃ 请不要粗暴对待本产品,跌落、敲打或剧烈晃动都可能损坏线路及元器件。
℃ 请不要用有机溶剂或腐蚀性液体清洗本产品。
℃ 请不要用颜料涂抹本产品。
℃ 擅自修改或使用未经授权的配件可能损坏本产品,由此造成的损坏将不给予保修。
如果产品出现故障,请联系飞凌技术服务部。
版权声明本手册所有权由保定市飞凌嵌入式有限公司独家持有。
未经本公司的书面许可,任何单位和个人无权以任何形式复制、传播、转载本手册的任何部分,否则一切后果由违者自负。
技术支持与更新技术支持说明技术支持范围:开发板软、硬件资源;判断开发板是否存在故障;如何烧写和更新系统;如何测试和运行开发板提供的程序。
技术支持时间:周一到周五:9:00—11:30,13:30—17:00。
公司按照国家法定节假日安排休息,在此期间无法提供技术支持,有问题请在论坛发帖。
保修范围及内容说明:1.凡飞凌出售的产品,除特殊说明外,提供一年的保修服务,(液晶屏提供三个月质保)。
2.保修期间凡产品出现质量问题,均可享受飞凌的免费维修服务,运费由双方均摊。
3.保修期满后出现性能故障和硬件问题,可与飞凌取得联系,飞凌提供有偿的维修服务,视具体情况而定。
注:凡是不在免费保修范围之内,邮费由客户来承担。
如客户不能提供购买时间的凭证,将开发板出厂日期视为购买日期。
维修周期:收到需维修的产品后,安排维修工程师测试、维修。
一般七个工作日即可修好(不包括邮寄路途上的时间)。
如有特殊情况,会向客户说明再与客户协商处理。
MC2的详细参数
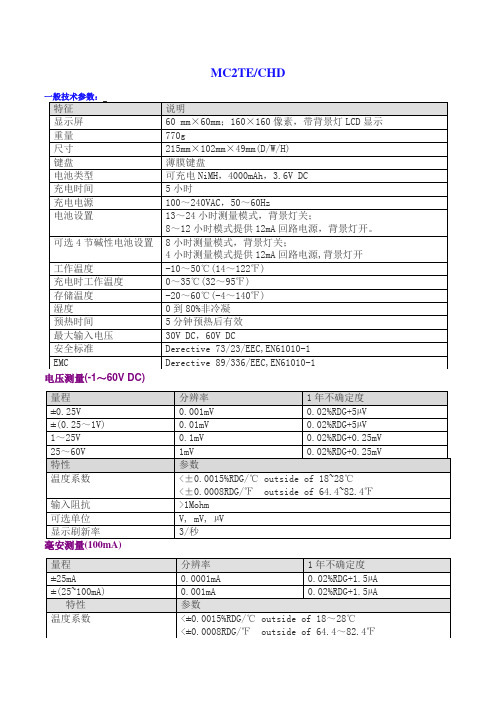
特性
参数
量程
0 ~ 9999999 pulse
输入阻抗
>1Mohm
触发电平
-1~14V in 1V steps and open collector inputs
最小信号幅度
2Vpp(pulse length>50us),3Vpp(pulse length 10..50us)
开关量测试
特点
参数
0.01%FS+0.025%RDG
EXT100
EXT100-IS
0 to 10 MPa
0 to 100 bar
0.0001
0.001
0.005%FS+0.0125%RDG
0.01%FS+0.025%RDG
EXT160
EXT160-IS
0 to 16 MPa
0 to 160 bar
0.0001
0.001
0.01 mV
0.02% RDG + 0.1 mV
-3 ~ -0.25 V
0.1 mV
0.02% RDG + 0.1 mV
0.25 ~ 12 V
0.1 mV
0.02% RDG + 0.1 mV
特征
参数
温度系数
< ±0.0015% RDG /℃outside of 18 ~28℃
< ±0.0008% RDG /℉outside of 64.4 ~82.4℉
输入阻抗
<7.5ohm
可选单位
mA,µA
显示刷新率
3/秒
回路电源
特性
参数
输出电流
最大25mA,短路保护
输出电压
MC10H209FN,MC10H209FNG,MC10H209FNR2,MC10H209FNR2G,MC10H209L,MC10H209MELG, 规格书,Datasheet 资料

MC10H209Dual 4−5−Input OR/NOR GateDescriptionThe MC10H209 is a Dual 4−5−input OR/NOR gate. This MECL part is a functional/pinout duplication of the MECL III part MC1688.Features•Propagation Delay Average, 0.75 ns Typical •Power Dissipation 125 mW Typical•Improved Noise Margin 150 mV (Over Operating V oltage and Temperature Range)•V oltage Compensated •MECL 10K ™ Compatible•Pb −Free Packages are Available*LOGIC DIAGRAMDIPPIN ASSIGNMENTV CC1A OUT A OUT A IN A IN A IN A IN V EEV CC2B OUT B OUT B IN B IN B IN B IN B IN16151413121110912345678V CC1 = PIN 1V CC2 = PIN 16V EE = PIN 81215131110976541423Pin assignment is for Dual −in −Line Package.For PLCC pin assignment, see the Pin Conversion Tables on page 18of the ON Semiconductor MECL Data Book (DL122/D).*For additional information on our Pb −Free strategy and soldering details, please download the ON Semiconductor Soldering and Mounting Techniques Reference Manual, SOLDERRM/D.See detailed ordering and shipping information in the package dimensions section on page 3 of this data sheet.ORDERING INFORMATIONTable 1. MAXIMUM RATINGSSymbol Characteristic Rating Unit V EE Power Supply (V CC = 0)−8.0 to 0Vdc V I Input Voltage (V CC = 0)0 to V EE VdcI out Output Current− Continuous− Surge 50100mAT A Operating Temperature Range0 to +75°CT stg Storage Temperature Range− Plastic− Ceramic −55 to +150−55 to +165°C°CMaximum ratings are those values beyond which device damage can occur. Maximum ratings applied to the device are individual stress limit values (not normal operating conditions) and are not valid simultaneously. If these limits are exceeded, device functional operation is not implied, damage may occur and reliability may be affected.Table 2. ELECTRICAL CHARACTERISTICS (V EE = −5.2 V ±5%) (Note 1)0°25°75°Symbol Characteristic Min Max Min Max Min Max UnitI E Power Supply Current−−−30−−mAI inH Input Current High−640−400−400m AI inL Input Current Low0.5−0.5−0.3−m AV OH High Output Voltage−1.02−0.84−0.98−0.81−0.92−0.735Vdc V OL Low Output Voltage−1.95−1.63−1.95−1.63−1.95−1.60Vdc V IH High Input Voltage−1.17−0.84−1.13−0.81−1.07−0.735Vdc V IL Low Input Voltage−1.95−1.48−1.95−1.48−1.95−1.45Vdc 1.Each MECL 10H™ series circuit has been designed to meet the dc specifications shown in the test table, after thermal equilibrium has beenestablished. The circuit is in a test socket or mounted on a printed circuit board and transverse air flow greater than 500 lfpm is maintained.Outputs are terminated through a 50 W resistor to −2.0 V.Table 3. AC PARAMETERS0°25°75°Symbol Characteristic Min Max Min Max Min Max Unit t pd Propagation Delay0.4 1.150.4 1.150.4 1.15ns t r Rise Time0.4 1.50.4 1.50.4 1.6ns t f Fall Time0.4 1.50.4 1.50.4 1.6ns NOTE:Device will meet the specifications after thermal equilibrium has been established when mounted in a test socket or printed circuit board with maintained transverse airflow greater than 500 lfpm. Electrical parameters are guaranteed only over the declaredoperating temperature range. Functional operation of the device exceeding these conditions is not implied. Device specification limit values are applied individually under normal operating conditions and not valid simultaneously.ORDERING INFORMATIONDevice Package Shipping†MC10H209FN PLLC−2046 Units / Rail46 Units / RailMC10H209FNG PLLC−20(Pb−Free)MC10H209FNR2PLLC−20500 / Tape & Reel500 / Tape & ReelMC10H209FNR2G PLLC−20(Pb−Free)MC10H209L CDIP−1625 Unit / RailMC10H209M SOEIAJ−1650 Unit / RailMC10H209MEL SOEIAJ−162000 / Tape & Reel2000 / Tape & ReelMC10H209MELG SOEIAJ−16(Pb−Free)MC10H209P PDIP−1625 Unit / Rail†For information on tape and reel specifications, including part orientation and tape sizes, please refer to our Tape and Reel Packaging Specifications Brochure, BRD8011/D.SL−MS 0.010 (0.250) NST 20 LEAD PLLC CASE 775−02ISSUE ENOTES:1.DIMENSIONS AND TOLERANCING PER ANSI Y14.5M,1982.2.DIMENSIONS IN INCHES.3.DATUMS −L −, −M −, AND −N − DETERMINED WHERE TOP OF LEAD SHOULDER EXITS PLASTIC BODY AT MOLD PARTING LINE.4.DIMENSION G1, TRUE POSITION TO BE MEASURED AT DATUM −T −, SEATING PLANE.5.DIMENSIONS R AND U DO NOT INCLUDE MOLD FLASH.ALLOWABLE MOLD FLASH IS 0.010 (0.250) PER SIDE.6.DIMENSIONS IN THE PACKAGE TOP MAY BE SMALLER THAN THE PACKAGE BOTTOM BY UP TO 0.012 (0.300).DIMENSIONS R AND U ARE DETERMINED AT THE OUTERMOST EXTREMES OF THE PLASTIC BODY EXCLUSIVE OF MOLD FLASH, TIE BAR BURRS, GATE BURRS AND INTERLEAD FLASH, BUT INCLUDING ANY MISMATCH BETWEEN THE TOP AND BOTTOM OF THE PLASTIC BODY .7.DIMENSION H DOES NOT INCLUDE DAMBAR PROTRUSION OR INTRUSION. THE DAMBARPROTRUSION(S) SHALL NOT CAUSE THE H DIMENSION TO BE GREATER THAN 0.037 (0.940). THE DAMBARINTRUSION(S) SHALL NOT CAUSE THE H DIMENSION TO BE SMALLER THAN 0.025 (0.635).DIM MIN MAX MIN MAX MILLIMETERSINCHES A 0.3850.3959.7810.03B 0.3850.3959.7810.03C 0.1650.180 4.20 4.57E 0.0900.110 2.29 2.79F 0.0130.0190.330.48G 0.050 BSC 1.27 BSC H 0.0260.0320.660.81J 0.020−−−0.51−−−K 0.025−−−0.64−−−R 0.3500.3568.899.04U 0.3500.3568.899.04V 0.0420.048 1.07 1.21W 0.0420.048 1.07 1.21X 0.0420.056 1.07 1.42Y −−−0.020−−−0.50Z 2 10 2 10 G10.3100.3307.888.38K10.040−−− 1.02−−−____SOEIAJ −16CASE 966−01ISSUE ANOTES:1.DIMENSIONING AND TOLERANCING PER ANSI Y14.5M, 1982.CDIP −16L SUFFIXCERAMIC DIP PACKAGECASE 620A −01NOTES:1.DIMENSIONING AND TOLERANCING PER ASME Y14.5M, 1994.2.CONTROLLING DIMENSION: INCH.3.DIMENSION L TO CENTER OF LEAD WHEN FORMED PARALLEL.4.DIMENSION F MAY NARROW TO 0.76 (0.030)WHERE THE LEAD ENTERS THE CERAMIC BODY.5THIS DRAWING REPLACES OBSOLETE CASE OUTLINE 620−10.AM0.25 (0.010)T DIM MIN MAX MIN MAX MILLIMETERSINCHES A 0.7500.78519.0519.93B 0.2400.295 6.107.49C −−−0.200−−− 5.08D 0.0150.0200.390.50E 0.050 BSC 1.27 BSC F 0.0550.065 1.40 1.65G 0.100 BSC 2.54 BSC H 0.0080.0150.210.38K 0.1250.170 3.18 4.31L 0.300 BSC 7.62 BSC M 0 15 0 15 N0.0200.0400.51 1.01____NOTES:1.DIMENSIONING AND TOLERANCING PER ANSI Y14.5M, 1982.2.CONTROLLING DIMENSION: INCH.3.DIMENSION L TO CENTER OF LEADS WHEN FORMED PARALLEL.4.DIMENSION B DOES NOT INCLUDE MOLD FLASH.5.ROUNDED CORNERS OPTIONAL.MDIM MIN MAX MIN MAX MILLIMETERSINCHES A 0.7400.77018.8019.55B 0.2500.270 6.35 6.85C 0.1450.175 3.69 4.44D 0.0150.0210.390.53F 0.0400.70 1.02 1.77G 0.100 BSC 2.54 BSC H 0.050 BSC 1.27 BSC J 0.0080.0150.210.38K 0.1100.130 2.80 3.30L 0.2950.3057.507.74M 0 10 0 10 S0.0200.0400.51 1.01____PDIP −16P SUFFIXPLASTIC DIP PACKAGEON Semiconductor and are registered trademarks of Semiconductor Components Industries, LLC (SCILLC). SCILLC reserves the right to make changes without further notice to any products herein. SCILLC makes no warranty, representation or guarantee regarding the suitability of its products for any particular purpose, nor does SCILLC assume any liability arising out of the application or use of any product or circuit, and specifically disclaims any and all liability, including without limitation special, consequential or incidental damages.“Typical” parameters which may be provided in SCILLC data sheets and/or specifications can and do vary in different applications and actual performance may vary over time. All operating parameters, including “Typicals” must be validated for each customer application by customer’s technical experts. SCILLC does not convey any license under its patent rights nor the rights of others. SCILLC products are not designed, intended, or authorized for use as components in systems intended for surgical implant into the body, or other applications intended to support or sustain life, or for any other application in which the failure of the SCILLC product could create a situation where personal injury or death may occur. Should Buyer purchase or use SCILLC products for any such unintended or unauthorized application, Buyer shall indemnify and hold SCILLC and its officers, employees, subsidiaries, affiliates,and distributors harmless against all claims, costs, damages, and expenses, and reasonable attorney fees arising out of, directly or indirectly, any claim of personal injury or death associated with such unintended or unauthorized use, even if such claim alleges that SCILLC was negligent regarding the design or manufacture of the part. SCILLC is an Equal Opportunity/Affirmative Action Employer. This literature is subject to all applicable copyright laws and is not for resale in any manner.PUBLICATION ORDERING INFORMATIONMECL 10H and MECL 10K are trademarks of Motorola, Inc.。
MCR10EZHJL资料

ResistorsRev.A 1/4Thick film rectangular Low resistance seriesMCR10 (2012 size (0805 size) : 1 / 4W )z Features1) Power rating of 1 / 4W 2) Highly reliable chip resistorRuthenium oxide dielectric offers superior resistance to the elements. 3) Electrodes not corroded by solderingThick film makes the electrodes very strong.4) Design and specifications are subject to change without notice. Carefully check the specification sheet before using or ordering it.z Ratings0.25W (1 / 4W)−55°C to + 155°C at 70°CItemConditionsSpecificationsRated powerRated voltageOperating temperatureNominal resistance See Table 1.Limiting element voltage1.58V(10Ω)20406080100−55070100155AMBIENT TEMPERATURE (°C)P O W E R L O A D (%)Fig.1The voltage rating is calculated by the following equation. If the value obtained exceeds the limiting element voltage, the voltage rating is equal to the maximum operating voltage.E: Rated voltage (V)P: Rated power (W)R: Nominal resistance (Ω)E= P ×RPower must be derated according to the power derating curve in Figure 1 when ambient temperature exceeds 70°C .ResistorsRev.A 2/4F (±1%)J (±5%)0.15≤ R ≤ 9.1(E24)(E24)(E24)(E24)±2500.1≤ R ≤ 0.13(E24)400±2000.047 ≤ R ≤ 0.091(E24)500±3000.1 ≤ R ≤ 0.13400±2000.15 ≤ R ≤ 0.91±250500±3000.047 ≤ R ≤ 0.091Table 1Resistance tolerance Resistance range(Ω)Special specificationL L SL L SResistance temperature coefficient(ppm/°C)z Before using components in circuits where they will be exposed to transients such as pulse loads (short–duration, high– level loads), be certain to evaluate the component in the mounted state. In addition, the reliability and performance of this component cannot be guaranteed if it is used with a steady state voltage that is greater than its rated voltage.z CharacteristicsResistorsRev.A 3/4z Dimensions (Unit : mm)z PackagingResistorsRev.A 4/4z Part No. ExplanationSpecial part numberPart No.M C 1R Nominal resistanceE Z HJ LResistance tolerance ±1%±5%F J10Ω less than (class F)1Ω less than (class J)0.1Ω less thanL Sφ180) : JEITA ET-7200B: Standard productFL,FS,JSJL :: 4 digits 3 digitsResistance code, 3 or 4 digits.Resistancetolerance+Special P/NResistance codeAppendixAbout Export Control Order in JapanProducts described herein are the objects of controlled goods in Annex 1 (Item 16) of Export T rade ControlOrder in Japan.In case of export from Japan, please confirm if it applies to "objective" criteria or an "informed" (by MITI clause)on the basis of "catch all controls for Non-Proliferation of Weapons of Mass Destruction.Appendix1-Rev1.1。
CM04MC10T中文资料

5
FERRITE PRODUCTS
Inductance decrease 04 30L 05 20L 06 10L
Commom mode choke coilD The maximum DC value having temperature increase within specified temperature,as detailed in individual specification. 4.Impedance Within the specified tolerance Commom mode choke coilD Measuring equipmentDHP 4291A or its equivalent Measuring frequencyDSpecified frequency 5. Inductance Within the specified tolerance Refer to individual specification SMD inductorD Measuring equipmentDHP 4284A or its equivalent Measuring frequencyD1kHz Measuring voltageD1V osc. Measurement in series connection 6.DC Resisitance Within the specified tolerance SMD transformer SMD inductor Commom mode choke coilD Measuring equipmentDDC ohmmeter 7.Self resonance frequency Within the specification SMD inductorD Measuring equipmentDImpedance analyzer fHP 4191A, 4192Ag or its equivalent 8.Temperature characteristic 04, 05, 06 TypeDWithin M10L 08TypeDWithinM5L SMD inductorD Change of maximum inductance deviation in step 1 to 5 Temperature at step 1 Temperature at step 2 Temperature at step 3 Temperature at step 4 Temperature st step 5 20C Minimum operating temperature 20C fStandard temperatureg Maximum oparating temperature 20C
MC33970DWR2;中文规格书,Datasheet资料
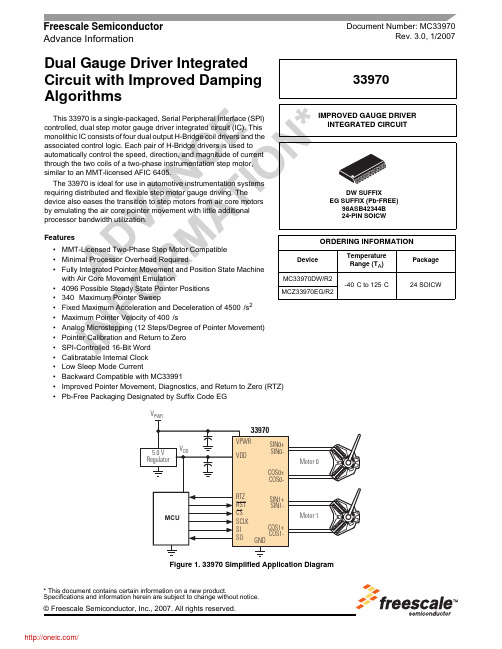
Document Number: MC33970Rev. 3.0, 1/2007Freescale Semiconductor Advance Information* This document contains certain information on a new product.Specifications and information herein are subject to change without notice.© Freescale Semiconductor, Inc., 2007. All rights reserved.Dual Gauge Driver Integrated Circuit with Improved Damping••••••••••••Low Sleep Mode Current•Backward Compatible with MC33991•Improved Pointer Movement, Diagnostics, and Return to Zero (RTZ) •Pb-Free Packaging Designated by Suffix Code EGFigure 1. 33970 Simplified Application Diagram33970Analog Integrated Circuit Device Data33970INTERNAL BLOCK DIAGRAMINTERNAL BLOCK DIAGRAMFigure 2. 33970 Simplified Internal Block DiagramH-BRIDGE COS0+INTERNAL VPWRVDDSIN0COS0COS0-SIN0+SIN0-COS1+COS1-COS1REGULATORLOGICSPIILIMOVERTEMPERATUREAND CONTROLSIN1OSCILLATORDETECTUNDER -ANDOVERVOLTAGE DETECTCS SCLK SO SIRSTRTZSIN1+SIN1-GND (8)MULTIPLEXERSIGMA-DELTAADCAGNDSTATE MACHINEVDDAnalog Integrated Circuit Device Data 33970PIN CONNECTIONSPIN CONNECTIONSFigure 3. 33970 Pin ConnectionsTable 1. 33970 Pin DefinitionsA functional description of each pin can be found in the Functional Pin Description section beginning on page 10.Pin NumberPin Name Pin FunctionFormal Name Definition1234COS0+COS0−SIN0+SIN0−OutputH-Bridge Outputs 0Each pin is the output pin of a half bridge, designed to source or sink current.5 – 8,17– 20GND Ground Ground These pins serve as the ground for the source of the low-side output transistors as well as the logic portion of the device.9CS Input Chip Select This pin is connected to a chip select output of a LSI IC.10SCLK Input Serial Clock This pin is connected to the SCLK pin of the master device and acts as a bit clock for the SPI port.11SO Output Serial Output This pin is connected to the SPI Serial Data Input pin of the master device, or to the SI pin of the next device in a daisy chain.12SI Input Serial Input This pin is connected to the SPI Serial Data Output pin of the master device from which it receives output command data.13RTZ Output Multiplexed OutputThis is a multiplexed output pin, for the non-driven coil, during a Return to Zero (RTZ) event.14VDD Input Voltage This SPI and logic power supply input will work with 5.0 V supplies. 15RST Input Reset This input has an internal active pull-up. 16VPWR Input Battery Voltage Power supply.21222324SIN1−SIN1+COS1−COS1+OutputH-Bridge Outputs 1Each of these pins are the output pin of a half bridge, designed to source or sink current.COS0+COS0-SIN0+SIN0-GND GND GND CS SCLK SO SI123456789101112242322212019181716151413COS1+COS1-SIN1+SIN1-GND GND GND VPWR RST VDD RTZGND GNDAnalog Integrated Circuit Device Data33970ELECTRICAL CHARACTERISTICS MAXIMUM RATINGSELECTRICAL CHARACTERISTICSMAXIMUM RATINGSTable 2. Maximum RatingsAll voltages are with respect to ground unless otherwise noted. Exceeding these ratings may cause a malfunction or permanent damage to the device.RatingsSymbolValueUnitELECTRICAL RATINGS Power Supply Voltage Steady State V PWR(SUS)-0.3 to 41VInput Pin Voltage (1)V IN -0.3 to 7.0V SIN +/- COS +/- Continuous Per Output Current (2)I OUTMAX 40mA ESD Voltage (3)Human Body Model Machine Model V ESD1V ESD2±2000 ±200V THERMAL RATINGS Storage TemperatureT STG -55 to 150°C Operating Junction Temperature T J-40 to 150°C Thermal Resistance Junction to Ambient Junction to Lead R θJA R θJL6020°C/WTHERMAL RESISTANCEPeak Package Reflow Temperature During Reflow (4), (5)T PPRTNote 5°CNotes1.Exceeding voltage limits on Input pins may cause permanent damage to the device.2.Output continuous output rating so long as maximum junction temperature is not exceeded. Operation at 125°C ambient temperaturewill require maximum output current computation using package thermal resistances.3.ESD1 testing is performed in accordance with the Human Body Model (C ZAP = 100 pF, R ZAP = 1500 Ω), ESD2 testing is performed inaccordance with the Machine Model (C ZAP = 200 pF, R ZAP = 0 Ω).4.Pin soldering temperature limit is for 10 seconds maximum duration. Not designed for immersion soldering. Exceeding these limits may cause malfunction or permanent damage to the device.5.Freescale’s Package Reflow capability meets Pb-free requirements for JEDEC standard J-STD-020C. For Peak Package Reflow Temperature and Moisture Sensitivity Levels (MSL),Go to , search by part number [e.g. remove prefixes/suffixes and enter the core ID to view all orderable parts. (i.e. MC33xxxD enter 33xxx), and review parametrics.Analog Integrated Circuit Device Data 33970ELECTRICAL CHARACTERISTICSSTATIC ELECTRICAL CHARACTERISTICSSTATIC ELECTRICAL CHARACTERISTICSTable 3. Static Electrical CharacteristicsCharacteristics noted under conditions 4.75 V < V DD < 5.25 V, -40°C < T A < 125°C, GND = 0 V unless otherwise noted. Typical values noted reflect the approximate parameter means at T A = 25°C under nominal conditions unless otherwise noted.CharacteristicSymbol Min Typ Max UnitPOWER INPUT Supply Voltage Range Fully Operational Limited Operational (6),(7)V PWR6.54.0––2626VVPWR Supply CurrentGauge 1 and 2 Outputs ON, No Output Loads I PWR(ON)–4.06.0mAVPWR Supply Current (All Outputs Disabled)Reset = Logic [0], V DD = 5.0 V Reset = Logic [0], V DD = 0 V I PWSLP1I PWRSLP2––42156025µAOvervoltage Detection Level (8)V PWROV 263238V Undervoltage Detection Level (9)V PWRUV 5.0 5.6 6.2V Logic Supply Voltage Range (5.0 V Nominal Supply)V DD 4.5 5.0 5.5V Under VDD Logic Reset V DDUV––4.5VVDD Supply Current Sleep: Reset Logic [0]Outputs Enabled I DD(OFF)I DD(ON)––401.0651.8µA mAPOWER OUTPUTSMicrostep Output (Measured Across Coil Outputs) SIN0,1, ± (COS0,1, ±) (refer to Table 1)R OUT = 200 ΩSteps 6, 18 (0, 12)Steps 5, 7, 17, 19 (1, 11, 13, 23)Steps 4, 8, 16, 20 (2, 10, 14, 22)Steps 3, 9, 15, 21 (3, 9, 15, 21)Steps 2, 10, 14, 22 (4, 8,16, 20)Steps 1, 11, 13, 23 (5, 7, 17, 19)Steps 0, 12 (6, 18)V ST6V ST5V ST4V ST3V ST2V ST1V ST0 4.820.94 V ST60.84 V ST60.68 V ST60.47 V ST60.23 V ST6-0.15.30.97 V ST60.87 V ST60.71 V ST60.50 V ST60.26 V ST60.06.01.0 V ST60.96 V ST60.8 V ST60.57 V ST60.31 V ST60.1VFull Step Active Output (Measured Across Coil Outputs) SIN0, 1, ± (COS0, 1, ±) (see Figure 9, page 23)Steps 1, 3 (0, 2)V FS4.95.36.0V Microstep, Full Step Output (Measured from Coil Low Side to Ground)SIN0, 1, ± (COS0, 1, ±), I OUT = 30 mAV LS0.00.10.3VNotes6.Outputs and logic remain active; however, the larger coil voltage levels may be clipped. The reduction in drive voltage may result in aloss of position control.7.The logic will reset at some level below the specified Limited Operational minimum. 8.Outputs will disable and must be re-enabled via the PECCR command.9.Outputs remain active; however, the reduction in drive voltage may result in a loss of position control.Analog Integrated Circuit Device Data33970ELECTRICAL CHARACTERISTICSSTATIC ELECTRICAL CHARACTERISTICSPOWER OUTPUTS (continued)Output Flyback Clamp (10)V FB –V ST6 + 0.5V ST6 + 1.0V Output Current Limit (Output = VST6)I LIM 40100170mA Overtemperature Shutdown (10)OT SD 155–180°C Overtemperature Hysteresis (10)OT HYST8.0–16°CCONTROL I/OInput Logic High Voltage (11)V IH 2.0––V Input Logic Low Voltage (11)V IL ––0.8V Input Logic Voltage Hysteresis (10)V IN(HYST)–100–mV Input Logic Pull Down Current (SI, SCLK)I DWN 3.0–20µA Input Logic Pull-Up Current (CS , RST )I UP 5.0–20µA SO High-State Output Voltage (I OH = 1.0 mA)V SOH 0.8 V DD––V SO Low-State Output Voltage (I OL = -1.6 mA)V SOL –0.20.4V SO Tri-State Leakage Current (CS ≥ 3.5 V)I SOLK -5.00 5.0µA Input Capacitance (12)C IN – 4.012pF SO Tri-State Capacitance (12)C SO––20pFANALOG TO DIGITAL CONVERTER (RTZ ACCUMULATOR COUNT)ADC Gain (10), (13)G ADC100188270Counts/V/msNotes10.This parameter is guaranteed by design; however, it is not production tested.11.V DD = 5.0 V.12.Capacitance not measured. This parameter is guaranteed by design; however, it is not production tested.13.Reference Figure 8, RTZ Accumulator (Typical)Table 3. Static Electrical Characteristics (continued)Characteristics noted under conditions 4.75 V < V DD < 5.25 V, -40°C < T A < 125°C, GND = 0 V unless otherwise noted. Typical values noted reflect the approximate parameter means at T A = 25°C under nominal conditions unless otherwise noted.CharacteristicSymbolMinTypMaxUnitAnalog Integrated Circuit Device Data 33970ELECTRICAL CHARACTERISTICSDYNAMIC ELECTRICAL CHARACTERISTICSDYNAMIC ELECTRICAL CHARACTERISTICSTable 4. Dynamic Electrical CharacteristicsCharacteristics noted under conditions 4.75 V < V DD < 5.25 V, -40°C < T A < 125°C, GND = 0 V unless otherwise noted. Typical values noted reflect the approximate parameter means at T A = 25°C under nominal conditions unless otherwise noted.CharacteristicSymbolMinTypMaxUnitPOWER OUTPUT AND CLOCK TIMINGSSIN, COS Output Turn ON Delay Time (Time from Rising CS Enabling Outputs to Steady State Coil Voltages and Currents) (14)t DLY (ON)––1.0msSIN, COS Output Turn OFF Delay Time (Time from Rising CS Disables Outputs to Steady State Coil Voltages and Currents) (14)t DLY (OFF)–– 1.0msUncalibrated Oscillator Cycle Time t CLU 0.65 1.01.7µs Calibrated Oscillator Cycle TimeCal Pulse = 8.0 µs, PECCR D4 = Logic [0]Cal pulse = 8.0 µs, PECCR D4 = Logic [1]t CLC1.00.9 1.11.0 1.21.1µsMaximum Pointer Speed (15)V MAX ––400°/s Maximum Pointer Acceleration (15) A MAX ––4500°/s 2SPI INTERFACE TIMING (16)Recommended Frequency of SPI Operationf SPI – 1.0 3.0MHz Falling Edge of CS to Rising Edge of SCLK (Required Setup Time) (17)t LEAD –50167ns Falling Edge of SCLK to Rising Edge of CS (Required Setup Time) (17)t LAG –50167ns SI to Falling Edge of SCLK (Required Setup Time) (17)t S ISU –2583ns Required High State Duration of SCLK (Required Setup Time) (17)t WSCLKH ––167ns Required Low State Duration of SCLK (Required Setup Time) (17)t WSCLKL ––167ns Falling Edge of SCLK to SI (Required Hold Time) (17)t SI (HOLD)–2583ns SO Rise Time C L = 200 pF t R SO–2550nsSO Fall Time C L = 200 pFt F SO–2550nsSI, CS , SCLK, Incoming Signal Rise Time (18)t RSI ––50ns SI, CS , SCLK, Incoming Signal Fall Time (18)t F SI ––50ns Falling Edge of RST to Rising Edge of RST (Required Setup Time) (17)t W RST –– 3.0µs Rising Edge of CS to Falling Edge of CS (Required Setup Time) (17), (19) t CS –– 5.0µs Rising Edge of RST to Falling Edge of CS (Required Setup Time) (17)t EN ––5.0µsNotes14.Maximum specified time for the 33970 is the minimum guaranteed time needed from the microcontroller.15.The minimum and maximum value will vary proportionally to the internal clock tolerance. These numbers are based on an ideallycalibrated clock frequency of 1.0 MHz. These are not 100 percent tested.16.The device shall meet all SPI interface timing requirements specified in the SPI Interface Timing section of this table, over the temperaturerange specified. Digital interface timing is based on a symmetrical 50 percent duty cycle SCLK Clock Period of 333 ns. The device shall be fully functional for slower clock speeds. See Figure 4 and 5.17.The maximum setup time specified for the 33970 is the minimum time needed from the microcontroller to guarantee correct operation.18.Rise and Fall time of incoming SI, CS, and SCLK signals suggested for design consideration to prevent the occurrence of double pulsing.19.The value is for a 1.0 MHz calibrated internal clock. The value will change proportionally as the internal clock frequency changesAnalog Integrated Circuit Device Data33970ELECTRICAL CHARACTERISTICSDYNAMIC ELECTRICAL CHARACTERISTICSTime from Falling Edge of CS to SO Low Impedance (20)t SO(EN)––145ns Time from Rising Edge of CS to SO High Impedance (21)t SO(DIS)–1.34.0µs Time from Rising Edge of SCLK to SO Data Valid (22)0.2 V DD ≤ SO ≥ 0.8 V DD , C L = 200 pFt VALID–65105nsNotes20.Time required for output status data to be terminated at SO. 1.0 k Ω load on SO21.Time required for output status data to be available for use at SO. 1.0 k Ω load on SO.22.Time required to obtain valid data out from SO following the rise of SCLK.Table 4. Dynamic Electrical CharacteristicsCharacteristics noted under conditions 4.75 V < V DD < 5.25 V, -40°C < T A < 125°C, GND = 0 V unless otherwise noted. Typical values noted reflect the approximate parameter means at T A = 25°C under nominal conditions unless otherwise noted.CharacteristicSymbol Min Typ Max UnitAnalog Integrated Circuit Device Data 33970ELECTRICAL CHARACTERISTICSTIMING DIAGRAMSTIMING DIAGRAMSFigure 4. Input Timing Switching CharacteristicsFigure 5. Valid Data Delay Time and Valid Time WaveformsRSTCSSISCLKV INV ILV IH V ILV IH V ILV IHV ILDon’t CareValidValidDon’t CareDon’t Care0.2 V DD0.2 V DD 0.2 V DD0.7 V DD0.7 V DD0.7 V DD 0.7 V DDt ENt WRSTt CSt LAGt RSIt LEAD t LEADt WSCLKht WSCLKlt FSIt SI(HOLD)SCLKSOSOLow-to-HighHigh-to-Low3.5 V0.2 V DD0.7 V DD0.2 V DD1.0 VV OHV OLV OH V OLV OH V OLt FSIt RSI0.7 V DD50%t SO(EN)t RSOt FSOt SO(DIS)t VALIDAnalog Integrated Circuit Device Data33970FUNCTIONAL DESCRIPTION INTRODUCTIONFUNCTIONAL DESCRIPTIONINTRODUCTIONThis 33970 is a single-packaged, Serial Peripheral Interface (SPI) controlled, dual step motor gauge driverintegrated circuit (IC). This monolithic IC consists of four dual output H-Bridge coil drivers and the associated control logic. Each pair of H-Bridge drivers is used to automatically control the speed, direction, and magnitude of current through the two coils of a two-phase instrumentation step motor, similar to an MMT-licensed AFIC 6405.The 33970 is ideal for use in automotive instrumentation systems requiring distributed and flexible step motor gauge driving. The device also eases the transition to step motors from air core motors by emulating the air core pointer movement with little additional processor bandwidth utilization.FUNCTIONAL PIN DESCRIPTIONH-Bridge Outputs 0 (COS0+, COS0-, SIN0+, SIN0-)Each pin is the output pin of a half bridge, designed to source or sink current. The H-Bridge pins linearly drive the sine and cosine coils of two separate step motors to provide four-quadrant operation.GROUND (GND)These pins serve as the ground for the source of the low-side output transistors as well as the logic portion of the device. They also help dissipate heat from the device.CHIP SELECT (CS)The CS pin enables communication with the master device. When this pin is in a logic [0] state, the 33970 is capable of transferring information to, and receivinginformation from, the master. The 33970 latches data in from the Input Shift registers to the addressed registers on the rising edge of CS when CS is logic [0]. When CS is logic high, signals at the SCLK and SI pins are ignored and the SO pin is tri-stated (high impedance). CS will only be transitioned from a logic [1] state to a logic [0] state when SCLK is a logic [0]. CS has an internal pull-up (l UP ) connected to the pin, as specified in the section of the Static Electrical Characteristics table entitled CONTROL I/O , which is found on page 6.SERIAL CLOCK (SCLK)SCLK clocks the Internal Shift registers of the 33970 device. The Serial Input (SI) pin accepts data into the Input Shift register on the falling edge of the SCLK signal, while the Serial Output pin (SO) shifts data information out of the SO Line Driver on the rising edge of the SCLK signal. It isimportant that the SCLK pin be in a logic [0] state whenever the CS makes any transition. SCLK has an internal pull down (l DWN ), as specified in the section of the Static Electrical Characteristics table entitled CONTROL I/O , which is found on page 6. When CS is logic [1], signals at the SCLK and SI pins are ignored and SO is tri-stated (high impedance). Refer to the data transfer timing diagrams in Figure 6 and Figure 7 on page 12.SERIAL OUTPUT (SO)The SO data pin is a tri-stateable output from the Shift register. The Status register bits are the first 16 bits shifted out. Those bits are followed by the message bits clocked in FIFO, when the device is in a daisy chain connection or being sent words that are multiples of 16 bits. Data is shifted on the rising edge of the SCLK signal. The SO pin will remain in a high impedance state until the CS pin is put into a logic low state.SERIAL INPUT (SI)The SI pin is the input of the Serial Peripheral Interface (SPI). Serial Input (SI) information is read on the falling edge of SCLK. A 16-bit stream of serial data is required on the SI pin, beginning with the most significant bit (MSB). Messages that are not multiples of 16 bits (e.g., daisy chained device messages) are ignored. After transmitting a 16-bit word, the CS pin must be de-asserted (logic [1]) before transmitting a new word. SI information is ignored when CS state.Multiplexed Output (RTZ)This is a multiplexed output pin, for the non-driven coil, during a Return to Zero (RTZ) event.Voltage (VDD)This SPI and logic power supply input will work with 5.0 V supplies.RESET (RST)If the master decides to reset the device, or place it into a sleep state, the RST pin is driven to a logic [0]. A logic [0] on the RST pin will force all internal logic to the known default state. This input has an internal active pull-up.BATTERY VOLTAGE (VPWR)Power supply.分销商库存信息: FREESCALEMC33970DWR2。
AG-HMR10MC
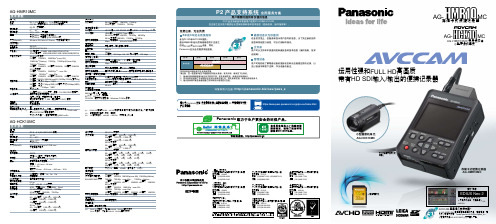
另外购买用于摄像机的连接线※产品限时供应。
成套型号为A G -HMR10U 。
※存储卡需另购。
AVCCAM 三年维修质保方案※※ AG-HMR10MC 用户享受三年维修质保。
有关详情,请浏览公司官方网站:</sav/pass_e>随机※捆绑EDIUS Neo 2非线性编辑软件小型摄像机单元AG-HCK10MC存储卡式便携记录器 AG-HMR10MCAG- MC存储卡式便携记录器AG- MCAG-HMR10MC 专用选购件小型摄像机单元〔营业、技术服务〕北京市朝阳区光华路甲8号和乔大厦C 座6层邮政编码:100026电话:(010)6562-6688传真:(010)6562-6186〔技术服务、维修〕北京技术服务中心北京市朝阳区光华路甲8号和乔大厦C 座6层邮政编码:100026电话:(010)6562-6688传真:(010)6562-6185成都技术服务中心成都市顺城大街206号四川大厦7层D 座邮政编码:610016电话:(028)8652-1585传真:(028)8652-1585广州市流花路中国大酒店商业大楼13楼邮政编码:510015电话:(020)8667-2130 (020)8667-2131传真:(020)8669-5225广州技术服务中心广州市流花路中国大酒店商业大楼13楼邮政编码:510015电话:(020)8667-0381传真:(020)8669-5225济南技术服务中心济南市二环东路3218号发展大厦B 座6层D 室邮政编码:250012电话:(0531)8190-8189传真:(0531)8190-8189上海市陆家嘴环路1000号汇丰大厦5楼邮政编码:200120电话:(021)3866-7799传真:(021)3866-7033上海技术服务中心上海市陆家嘴环路1000号汇丰大厦5楼邮政编码:200120电话:(021)3866-7799传真:(021)3866-7033广告主:松下电器(中国)有限公司 北京市朝阳区光华路甲8号和乔大厦C 座6层 广告经营者:天津富士印商贸有限公司 天津市河西区恒华大厦1号楼905室 印刷日: 2009年8月运用性强和FULL HD 高画质带有HD SDI 输入/输出的便携记录器[常 规]电源: DC 7.2 V(使用电池),7.3 V(使用交流适配器)功耗: 11.7 W (专用选件AG-HCK10MC 连接时) 6.5 W (标准情形)操作温度: 0℃~40℃操作湿度: 10%~80% (无结露)重量: 大约 580g ,不包含附件和电池大约 691g ,安装电池VW-VBG260时尺寸(WxHxD): 96 mm x 52.6 mm x 133 mm ,不包括突出部分[视频录制] 录制格式: AVCHD压缩方法: MPEG-4AVC/H.264录制媒介※1: SD 存储卡:512MB,1GB,2GB(FAT32,FAT16)SDHC 存储卡:4GB,6GB,8GB,12GB,16GB,32GB(FAT32)录制视频格式: 59.94 Hz 设定时PH 模式:1080/60i 、1080/30p ※2(over 60i)、1080/24p ※2(Native)、720/60p 、720/30p ※2(over 60p)、720/24p ※2(Native)HA 模式:1080/60i 、HG 模式:1080/60i 、HE 模式:1080/60i 50 Hz 设定时PH 模式:1080/50i 、1080/25p ※2(over 50i )、720/50p 、720/25p ※2(over 50p )HA 模式:1080/50i 、HG 模式:1080/50i 、HE 模式:1080/50i PH 模式:1080/50i,1080/25p(over50i),720/50p,720/25p(超过50p)传输速率: PH 模式:大约21 Mbps (VBR )HA 模式:大约17 Mbps(VBR),HG 模式:大约13 Mbps(VBR) HE 模式:大约6 Mbps (VBR )录制时间: 大约180分(PH 模式1920×1080像素、使用1个32 GB SDHC 存储卡)SD 存储卡: 每张卡最多可录制剪辑:900(格式化之后,无需拔下/插入存储卡)最多可播放剪辑:1,000(最多显示1,000个剪辑)缩略图: 每页8画面编辑功能: 删除/写保护格式化功能:有连续拍摄时间(大约): 单个使用时,大约150分钟※3(使用标配的电池2640 mAh ) 与AG-HCK10MC 连接使用时,大约70分分钟※3(使用标配的电池2640 mAh )[图像格式]视频信号: 59.94Hz 设定时:1080/60i 、720/60p 50Hz 设定时:1080/50i 、720/50p[图像输出/输出]SDI 接口: HD SDI 输入、HD SDI/SD SDI 输入BNC ×1、0.8 Vp-p 、75 Ω HDMI 接口: HDMI 输入×1(HDMI Type A 接口)、59.94 Hz 设定时:1080/60i 、720/60p 、480/60p50 Hz 设定时:1080/50i 、720/50p 、576/50p 摄像机连接接口: 20pin 专用接口(AG-HCK10MC 使用)[音频格式] 压缩方法: 录制/回放:杜比数字/2声道采样频率: 48 kHz 量化: 16 bit压缩比特率: PH 模式:384 kbps, HA, HG 和HE 模式:256 kbps [音频输入/输出] HDMI 输出:2声道(线性PCM ),5.1声道(杜比数字)摄像机连接接口: 20pin 专用接口(AG-HCK10MC 使用)[其他连接器] USB :迷你B 型连接器(与USB 2.0相兼容)摄像机遥控接口:高级迷你插孔(直径2.5 mm)x 1,用于变焦和录制启动/停止操作[显示屏、话筒和扬声器] LCD 显示屏: 3.5英寸彩色显示屏,大约210,000像素外部麦克风输入: -70 dBV(麦克风灵敏度:等同于-50 dB,0 dB=1V/Pa 1 kHz)耳机: 立体声迷你插孔(3.5 mm 直径)内置扬声器: 20 mm (圆形)[标准配件]AC 适配器/充电器,2640mAh 电池组(安全型),AC 线缆,DC 线缆(捕获型),CD-ROM (带素材修复软件,Windows PC/Mac 版本)※1:SDHC/SD 存储卡(8 MB ~32 GB)可用于存储/读取场景文件和用户文件以及读取元数据。
HMJH-210X型家用小型电话交换机使用说明书

HMJH-210X型家用小型电话交换机使用说明书目录前言一.设备安装二.设置、三.使用四.系统限制五.技术参数六.功能设置表七.售后服务前言HMJH-210X型程控交换模块是专为家庭或小型公司设计的电话交换产品。
其主要特点是:最多可接2条外线,内部可挂接10条分机线,连接10个分机电话。
并具有来电显示功能(注:外线需来电显示业务支持)。
各分机既可使用外线又可与各分机进行直接通话。
内部通话不占用外线资源,因此,不需支付通话费用。
一.设备安装1.将模块条固定在家庭信息箱内,将专用电源四芯插头插入插孔,并保证接触良好。
2.将10个电话分机线头(RJ11水晶头)插入801~810插孔内。
外线插头插入相应插座。
二.设置功能设置用801分机。
2.1恢复出厂设置:一般出厂产品均已为出厂设置。
在设置不明的情况下,请恢复出厂设置。
格式:提801机,拔*#60100#听到确认音后挂机。
2.2设置免打扰格式:提801机,拔*#1NN10#,NN为分机号(01~10)。
805为免打扰状态,摘801分机,在801分机上拔“*#10510#”即可。
出厂值:所有分机无免打扰。
2.3解除免打扰格式:提801机,拔*#1NN00#,NN为分机号(01~10)。
例:设解除805的免打扰,摘801机,在801分机上拔“*#10500#”即可。
2.4设置传真方式功能为:电话进入时,该端口持续保持振铃。
格式:提801机,拔*#1NN80#,取消为*#1NN40#。
例:设805为传真方式(振铃时全响),摘801分机,在801分机上按“*#10580#”即可。
出厂值:所有分机无传真方式。
2.2限制分机只能使用内线格式:提801机,拔*#4NN10#,取消为*#4NN00#。
出厂值:所有分机能使用外线。
2.6设置来电显示功能为:电话进入时,话机上能显示来电号码(注:外线需开通来电显示业务)。
格式:提801机,拔*#5NN10#,NN为分机号(01~10)。
HQ-210 智能计数器 说明书
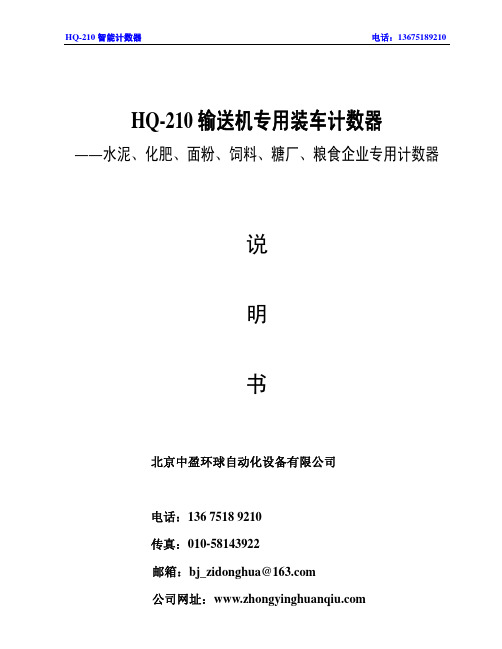
HQ-210输送机专用装车计数器――水泥、化肥、面粉、饲料、糖厂、粮食企业专用计数器说明书北京中盈环球自动化设备有限公司电话:136****9210传真:************邮箱:********************公司网址:警告z在计数器接入电源之前,请检查使用的电压,是否在220V±15%范围之内及频率是否在50HZ±2%范围内。
如果您使用的电源不能满足这一要求,需加交流稳压电源。
z控制器外壳一定要良好接地。
z在启动计数器进行计数工作之前,请确认如下几点:1、计数器侧面的所有接口的接线均已经正确连接。
2、传感器已经安装完好,在一条直线上,并固定牢固。
3、计数器的参数已经正确设定,包括清零模式、连包识别模式、袋时设定、延时停机时间,等等。
F04袋时设定,必须根据不同的包袋长度和传送带的速度做相应的设定!单包模式时,袋时应设定为一个标准包袋在传送带上通过传感器的最快时间。
这种情况下,最快袋时不用精确测定,只用估算即可,尽量设定的小一些!连包模式时,袋时设定请参照第5-4章节注意4(标定F04连包袋时的方法)。
目录1 产品概述 .................................................................................................................................. -2 - 1-1 计数器简介 ....................................................................................................................... -3 - 1-2 应用领域 ........................................................................................................................... - 3 - 1-3 功能特点 ........................................................................................................................... -4 -2 技术参数 .................................................................................................................................. - 5 -3 计数器接线说明 ...................................................................................................................... - 6 - 3-1 定量装车时,计数器连锁控制皮带机接线说明 ........................................................... - 6 - 3-2 传感器插头接线说明 ....................................................................................................... - 7 - 3-3 大屏幕插头接线说明 ....................................................................................................... - 8 -4 传感器安装说明 ...................................................................................................................... - 8 -5 计数器操作说明 ...................................................................................................................... - 9 - 5-1 “启/停”键 ...................................................................................................................... - 9 - 5-2 “清零”键 ....................................................................................................................... - 9 - 5-3 “设包”键 ..................................................................................................................... - 10 - 5-4 “功能”键 ..................................................................................................................... - 10 - 5-5 遥控器 ............................................................................................................................. - 12 -6 日常快捷操作说明1――计数器连锁控制装车机的用户................................................. - 12 -7 日常快捷操作说明2――不需要计数器连锁控制输送机的用户..................................... - 12 -8 日常快捷操作说明3――设定值不变需要计数器循环计数的用户................................. - 13 -9 注意事项 ................................................................................................................................ - 13 -10 常见问题与解决方法 .......................................................................................................... - 13 -1-1 计数器简介信号运行功能停止//图2 计数器主机的正面图(尺寸360×220×60mm)¾单累计/设定值由5位1.2寸LED高亮度数码管显示,用于显示单次计数的数值,以及设定值。
最简,往往给你最多NZXT H210H510i机箱体验

最简,往往给你最多NZXT H210/H510i机箱体验作者:来源:《电脑报》2019年第28期NZXT(恩杰)的机箱产品一向以简洁、高冷且充满科技美学的外观著称。
而正是因为采用了这样的设计风格,让NZXT的机箱非常适合个性化DIY,从而成为了热门的MOD机型,因此,市面上也涌现了很多针对NZXT机箱的第三方改造配件方便玩家选择。
最近NZXT宣布正式推出全新的H系列2019版机箱,在保持家族特有的高冷风格外观之外,也加入了不少新的设计。
我们也在第一时间收到了NZXT提供的H210和H510i两款新产品中的主打型号,一起来看看吧。
H210,精准升级更灵动作为经典mini-ITX机箱H200的升级款,新上市的H210在外观方面保持了一向的家族式简洁风格,体积和容量方面也与H200完全一致,同样提供了红黑、黑白、全黑等配色可选,本次我们拿到的是红黑的版本,从色调风格来看特别适合刚上市的第三代锐龙和NAVI显卡。
红黑版H210机箱主体钢板部分采用了SGCC钢材,并使用亚光漆喷涂,显得相当有质感,而前面板两侧的进气栅格与机箱内部的电缆管理托杆则采用了红色点缀,保持了美观大方的家族风格,完全平整的前面板和钢化玻璃全景侧板也方便玩家DIY各种机箱贴进行MOD。
那么H210相对H200有哪些升级呢?首先就是顶部增加了USB 3.1 Gen2 Type-C接口(支持10Gbps高速传输),方便玩家连接各种Type-C接口的数码设备,包括手机、耳机等等。
特别是耳机,由于现在不少针对手机的Type-C耳机(例如小米活塞耳机Type-C版)都可以直接插在电脑主板的Type-C接口上使用(因为这类耳机都内置了音频解码芯片),而H210在前面板上提供Type-C接口明显接耳机就更加方便了,不用弯腰去插主板后面的接口。
其次,H210的钢化玻璃全景侧面板采用了新的单翼形螺钉固定方式,拧一个螺钉即可侧向翻转打开侧面板,相比上代H200需要拧4个螺钉才能打开侧面板更加方便。
热电阻表TH 210 说明书

59.2 mm115 m m59.2 mm125 mm125 mm100 m m190 mmHumidity and temperature transmitterTH 210KEY POINTSMaterial : ABS V0 as per UL94Protection : IP65Display : 75 x 40 mm, LCD 20 digits 2 lines.Height of digits : Values : 10 mm ; Units : 5 mm Cable gland : For cables Ø 8 mm maximum Weight : 320 g- Configurable measuring ranges from 5 to 95%HR and from -40 to +180 °C (according the type of probe)- Functions : relative and absolute humidity, dew point, wet and dry temperature and enthalpy - Stainless steel or polycarbonate probe- 4 wires analogue output 0-5/10 V or 0/4-20 mA - Power supply 24 Vdc/Vac or 115/230 Vac - Trend indicator- ABS V0 IP65 housing, with or without display - “¼ turn” system mounting with wall-mount plateFEA TURES OF THE HOUSINGTECHNICAL FEA TURES IN HUMIDITYMeasuring range From 5 to 95%RH Unit of measurement%RHAccuracy* (Repeatability, linearity, hysteresis) ±1.5%RH (if 15°C ≤ T ≤ 25 °C)Drift linked to temperature ±0.04 x (T-20)%RH (if T < 15°C or T > 25°C)Resolution0.1%RH Factory calibration uncertainty ±0.88%RHResponse time < 10 seconds (from 10 to 80%RH, V air = 2 m/s)Type of sensor capacitiveType of fluidAir and neutral gases*All accuracies indicated in this technical datasheet were stated in laboratory conditions, and can be guaranteed for measurements carried out in the same conditions, or carried out with calibration compensation.As per NFX 15-113 and the Charter 2000/2001 HYGROMETERS , GAL (Guaranteed Accuracy Limit) which has been calculated with a coverage factor value of 2 is ±2.58%RH between 18 and 28°C on the measuring range from 3 to 98%RH. Sensor drift is less than 1%RH/year.Class 210 transmitters have two analogue outputs which correspond to both displayed parameters. It is possible to activate one or two outputs and to select for each between humidity, temperature and the functions described above** :Absolute humidity : from 2 to 30 000 g/kg ; unit : 1 g/kg Dew point : from -60 to +100 °Ctd ; unit : 0.1°Ctd / 0.1 °FtdDry temperature : from -20 to +102 °C ; unit : 0.1°C / 0.1 °FEnthalpy : from 0 to 15 000 Kj/kg ; unit : 0.1 Kj/kg**The default configuration for the output 1 is 0-100%RH in hygrometry and 0-50°C in temperature for the output 2.FUNCTIONSPower supply / OutputB : 24 Vac/Vdc H : 115 or 230 VacPART NUMBERTH 210To order, just add the codes to complete the part number :Display O : with displayN : without displayMounting of theprobe D : remoteS : ambientExample : TH210 - BNDP150Temperature and humidity transmitter, power supply 24 Vac/Vdc, without display, with remote probe in polycarbonate of 150 mm length.Type of probeI : stainless steel P : polycarbonateProbe length (mm)150 : remote 300 : remoteRemote modelAmbient modelTECHNICAL FEA TURES IN TEMPERA TUREMeasuring rangeAmbient model : from 0 to +50 °CRemote model with polycarbonate probe : from -20 to +80 °C Remote model with stainless steel probe : from -40 to +180 °C Unit of measurement °C / °FAccuracy*±0.3 % of reading ±0.25 °C Response time T 90 = 0.9 second for V air = 1 m/s Resolution 0.1 °CType of sensor Pt100 1/3 as per DIN IEC751Type of fluidAir and neutral gasesTECHNICAL FEA TURES OF THE PROBETECHNICAL SPECIFICA TIONS➢White polycarbonate probe➢316 L stainless steel pronePower supply 24 Vac / Vdc ±10 %115 Vac or 230 Vac ±10 %, 50-60 HzOutput2 x 4-20 mA or 2 x 0-20 mA ou 2 x 0-5 V ou 2 x 0-10 V (4 wires)Maximum load : 500 Ohms (0/4-20 mA)Minimum load : 1 K Ohms (0-5/10 V)Galvanic isolationInputs and outputs (models 115 Vac/230 Vac)Outputs (models 24 Vac/Vdc)Consumption 5 VAElectromagnetical compatibility EN61326Electrical connectionScrew terminal block for cable 2.5 mm²PC communication Kimo USB-Mini Din cable EnvironmentAir and neutral gases Type of fluidAir and neutral gasesOperating temperature From 0 to +50 °C Storage temperature From -10 to +70 °CMeasuring range From -20 to +80 °C Length of standard probe 100 mmLength of remote probe 150 or 300 mm (other on request)CableSilicone Ø4.8 mm, length 2 m (other on request)Polycarbonate probes are supplied with a flow-through polycarbonate protection tip with a stainless steel filter 25 µ (ref. : EPP2).Measuring range From -40 to +180 °CLength of remote probe 150 or 300 mm (other on request)CableSilicone Ø4.8 mm, length 2 m (other on request)Stainless steel probes are supplied with a flow through stainless steel protection tip with a stainless steel filter 25 µ (ref. : EPI25).➢Type of tipsSpecificationsEPP2EPI25EPI100EPFIEPFTEPH2O2Tip material PC (1)St. steel (2)St. steel (2)St. steel (2)PTFE (3)MnO 2(4)Filter material St. steelSt. steel St. steelSt. steel PTFEPTFEFilter type Meshed Meshed Meshed Sintered Sintered Sintered Maximum particle 25 µ25 µ100 µ10 µ50 µ50 µMaximum air velocity 25 m/s 25 m/s 20 m/s 30 m/s 25 m/s 25 m/s Maximum temperature 120 °C 180 °C 120 °C 180 °C 180 °C 180 °C Relative humidity maximum95%RH 95%RH 100%RH 90%RH 90%RH 95%RH Length30 mm30 mm30 mm30 mm30 mm33 mmApplicationHVAC air-conditioning systemx x x xx x x Cold storage roomx x x x x x Industryx x x x x x Pharma plants / Microelectronicsx x x x x x Dryer x x x x x x Curing x x x x x x Swimming-poolxxxxxxPart numberExternal aggression :Tips protect against the following external aggressions : ●Water droplets : EPFT ●Shaving : EPI25 et EPFI ●Dust : EPFI ●Chemical product and grease : EPFT ●H 2O 2 (hydrogen peroxide) : EPH2O2(1) PC : white polycarbonate (2)Stainless steel : 316 L (3)PTFE : white Teflon ® (4)MnO 2 : manganese dioxide*All the accuracies indicated in this technical datasheet were stated in laboratory conditions, and can be guaranteed for measurements carried out in the same conditions, or carried out with calibration compensation.CONNECTIONSPower supply terminal block (c)LCC-S software connectionsType of power supply of the transmitter (b)Analogue outputs (a)DIP switch (d)Cable glands(a)ELECTRICAL CONNECTIONS – as per NFC15-100 standardThe selection of the output signal in voltage (0-10 V or 0-5 V) or in current (4-20 mA or 0-20 mA) is made via the DIP switch (d) of the electronic board of the transmitter : put the on-of switches as shown in the table below :0/4-20 mA+-0-5/10 VARegulator display or PLC/BMS passivetype4-20 mA output0/4-20 mA-0-5/10 V+VRegulator display or PLC/BMS passivetype0-10 V outputConfigurations 4-20 mA 0-10 V 0-5 V 0-20 mACombinations2341234123412341+-Power supply 24 Vdc+-Vac L~Vac N~~~~PhaseNeutral GroundPower supply 115 / 230 Vac~L NPe 230 Vac orPower supply 24 Vacclass IILN Power supplyN LLN Pe230 Vac0-5/10 V – V o l t a g e0/4-20 m A – C u r r e n tG N D – G r o u n d Analogue output 1(out 1)0-5/10 V – V o l t a g e0/4-20 m A – C u r r e n tG N D – G r o u n d Analogue output 2(out 2)For power supply 24 Vdc modelsFor power supply 24 Vac modelsFor power supply 230 Vac, 115 Vac modelsoror(c)(c)(c)+-Neutral (N)~Phase (L)~Neutral (N)~Phase (L)~Ground This connection must be made by a qualified technician. To make the connection, the transmitter must not be energized.Before making the connection, you must first check the power supply indicated on the transmitter board (see (b) on “Connections” part).➢For transmitters with 24 Vdc power supply :➢For transmitters with 24 Vac power supply :➢For transmitters with 115 or 230 Vac power supply :➢Connection of the output in current 4-20 mA :➢Connection of output in voltage 0-10 V :F T a n g – t r a n s m i t t e r _T H 210 – 02/04/13 – R C S (24) P ér i g u e u x 349 282 095 N o n -c o n t r a c t u a l d o c u m e n t – W e r e s e r v e t h e r i g h t t o m o d i f y t h e c h a r a c t e r i s t i c s o f o u r p r o d u c t s w i t h o u t p r i o r n o t i c e .●Sliding fittings ●Connection fittings ●Cable glands●Protections tips●Wall-mounting support bracket for remote humidity probeCONFIGURA TION OF THE TRANSMITTERSConfigurable analogue output :Range with center zero (-40/0/+40 °C), with offset zero (-30/0/+70 °C) or standard range (0/+100 °C), It is possible to configure your own intermediary rangesCaution : the minimum difference between the high range and the low range is 20.Configure the range according to your needs : outputs are automatically adjusted to the new measuring range-40 °C+180 °C-40 °C+180°C0 V 4 mA10 V 20 mA50New range0 V 4 mA10 V 20 mAMOUNTINGTo mount the transmitter, mount the ABS plate on the wall (drilling : Ø6 mm, screws and pins are supplied).Insert the transmitter on the fixing plate (see A on the drawing beside). Rotate thehousing in clockwise direction until you hear a “click” which confirms that the transmitter is correctly installed.MAINTENANCEPlease avoid any aggressive solvent. Please protect the transmitter and its probes from any cleaning product containing formalin, that may be used for cleaning rooms or ducts.OPTIONS AND ACCESSORIES●LCC-S : configuration software with USB cable ●Calibration certificate7.5 mm8 mm4.5 mm40 mm50 m m68 m m75 mm37.5 mm23.75 m m14 mmCALIBRA TIONOutputs diagnostic : With this function, you can check with a multimeter (or on a regulator / display, or a PLC / BMS) if the transmitter outputs work properly. The transmitter generates a voltage of 0 V, 5 V and 10 V or a current of 4 mA, 12 mA and 20 mACertificate : Class 210 transmitters are supplied with adjusting certificates. Calibration certificates are available as an option.It is possible on the class 210 to configure all the parameters of the transmitter : units, measuring ranges, outputs, channels, calculation functions, etc, via different methods :●Keypad for models with display : a code-locking system allows to secure the installation (See class 210 user manual).●Software (optional) on all models. Simple user-friendly configuration. See LCC-SD user manual.。
TH 210-R 湿度和温度传感器数据手册说明书

(1)Available only with the remote probe / (2)Calculated value / (3)All the accuracies indicated in this technical datasheet were stated in laboratory conditions, and can be guaranteed for measurements carried out in the same conditions, or carried out with calibration compensation.Features•Power supply 24 Vdc/Vac or 100-240 Vac with galavnic insulation •“¼ turn” system mounting with wall-mount plate•Calculated parameters absolutehumidity, dew point, combination ratio, wet temperature and enthalpy •Trend indicatorTwo 4-wire analogue output 0-5/10 V or 0/4-20 mA Sondes en inox ou en polycarbonate ABS V0 IP65 housing, with or without display2 relay outputsTH 210----Power supply / Output B: 24 Vac/Vdc H: 100-240 VacType of probe I: stainless steel (1)P: polycarbonatePart numberDisplayO: with display N: without display Mounting of the probe D: remote S: ambientExample: TH210 – BNDP150 – R: Temperature and humidity transmitter, 24 Vac/Vdc power supply, without display, with remote probe in polycarbonate of 150 mm length and relay outputs.Important note: the TH210 – H model (100-240 Vac) is available only with display.-Probe length (mm)150: remote 300: remote-Relay outputsRClass 210 transmitters have two analogue outputs which correspond to both displayed parameters. It is possible to activate one or two outputs and to select for each between humidi-ty, temperature and the calculated parameters (The default configuration for the output 1 is 0-100% RH in hygrometry and 0-50°C in temperature for the output 2).Warning: risk of electric shock 2 x 4-20 mA or 2 x 0-20 mA or 2 x 0-5 VCommon mode voltage <30 VAC DOUBLE ISOLATION or REINFORCED ISOLATIONTechnical features of probes•White polycarbonate probe•316 L stainless steel probePolycarbonate probes are supplied with a flow-through ABS protection tip with a stainless steel filter 25 µ(ref: EPP2).Stainless steel probes are supplied with a flow through stainless steel protection tip with a stainless steel filter25 µ (ref: EPI25).External aggressionTips protect against the following external aggres-sions:•Water droplets: EPFT •Shaving: EPI25 et EPFI •Duct: EPFI•Chemical product and grease: EPFT •H 2O 2 (hydrogen peroxide): EPH2O2(1) ABS: white acrylonitrile butadiene styrene (2)Stainless steel: 316 L (3)PTFE: white Polytetrafluoroethylene (4)MnO2: manganese dioxideFeatures of the housingAll dimensions are in millimeters.Remote model Ambient modelDimensions056 222 38 18*********************SEN TRONIC AGConnectionsTout changement de fusible doit être réalisé appareil hors tension en utilisant un fusible TR5 630 mA 250 V.50-60 Hz 8 VA 0/4...20 mA / 0...5/10 Von the side of the transmitter123456(c)For 100-240 Vac powersupply models1. DIP switch (d)2. LCC-S software connections3. Relays4. Analogue outputs (a)5. F3.20* fuse6. Power supply terminal block (c)7. Cable glands230 Vac-+0-5/10 V0/4-20 mAAf cheur régulateur ou automate type passifAf cheur régulateur ou automate type passif Sortie 4-20 mASortie 0-10 V 056 222 38 18*********************SEN TRONIC AGConfiguration des capteursIt is possible on the class 210 to configure all the parameters of the transmitter: units, measuring ranges, outputs, channels, calculation func-tions, etc. via different methods:•Keypad for models with display: a code-locking system allows to secure the installation (See class 210 transmitters user manual).•Software (optional) on all models. Simple user-friendly configuration. See LCC-S user manual.Configurable analogue output:Range with center zero (-40/0/+40°C), with offset zero (-30/0/+70°C) or standard range (0/+100°C). It is possible to configure your own intermediary rangesCaution: the minimum difference between the high range and the low range is 20.Configure the range according to your needs: outputs are automatically adjusted to the new measuring range50-40 °C0 V 4 mA 0+180 °C10 V 20 mANew range-40 °C0 V 4 mA 0+180 °C10 V 20 mA50MountingTo mount the transmitter, mount the ABS plate on the wall (drilling: Ø6 mm, screws and pins are supplied).Insert the transmitter on the fixing plate (see A on the drawing beside). Rotate the housing in clockwise direction until you hear a “click” which confirms that the transmitter is correctly installed.MaintenancePlease avoid any aggressive solvent. Please protect the transmitter and its probes from any cleaning product containing formalin, that may be used for cleaning rooms or ducts.CalibrationOutputs diagnostic: With this function, you can check with a multimeter (or on a regulator / display, or a PLC / BMS) if the transmitter out-puts work properly. The transmitter generates a voltage of 0 V , 5 V and 10 V or a current of 4 mA, 12 mA and 20 mA Certificate: Class 210 transmitters are supplied with adjusting certificates. Calibration certificates are available as an option.Options and accessoriesPrecautions for usePlease always use the device in accordance with its intended use and within parameters described in the technical features in order not to compromise the protection ensured by the device.Only the accessories supplied with the device must be used.Les dimensions sont exprimées en millimètres.F T a n g – T H 210-R – 17/04/19 – R C S (24) P ér i g u e u x 349 282 095 N o n -c o n t r a c t u a l d o c u m e n t – W e r e s e r v e t h e r i g h t t o m o d i f y t h e c h a r a c t e r i s t i c s o f o u r p r o d u c t s w i t h o u t p r i o r n o t i c e .056 222 38 18*********************SEN TRONIC AG。
MACH210-12JC资料
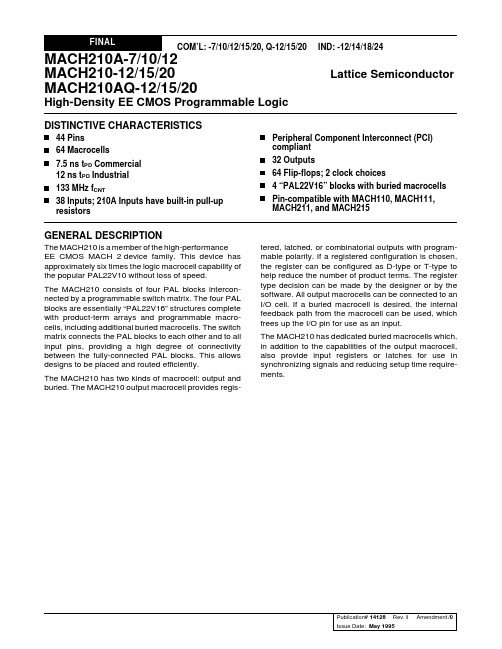
14128I-3
4
MACH210-7/10/12/15/20, Q-12/15/20
ORDERING INFORMATION Commercial Products
Programmable logic products for commercial applications are available with several ordering options. The order number (Valid Combination) is formed by a combination of:
MACH210-12
MACH210-15
MACH210-20
JC
MACH210AQ-12
MACH210AQ-15
MACH210AQ-20
OPTIONAL PROCESSING Blank = Standard Processing
OPERATING CONDITIONS C = Commercial (0°C to +70°C)
I/O16
GND
VCC
I/O15
I/O14
I/O13
I/O12
Note: Pin-compatible with MACH111 and MACH211.
PIN DESIGNATIONS
CLK/I =
GND =
I
=
I/O =
VCC =
Clock or Input Ground Input Input/Output Supply Voltage
The MACH210 consists of four PAL blocks interconnected by a programmable switch matrix. The four PAL blocks are essentially “PAL22V16” structures complete with product-term arrays and programmable macrocells, including additional buried macrocells. The switch matrix connects the PAL blocks to each other and to all input pins, providing a high degree of connectivity between the fully-connected PAL blocks. This allows designs to be placed and routed efficiently.
Futaba10C-10CH中文说明书(1)

滑翔机的功能菜单........................80 子目录...............................80 从基本的 4 通道滑翔机开始.............81 滑翔机的基础功能菜单.................83 模型类型(PARAMETER 子菜单).........83 电动机关闭 MOTOR CUT................84 滑翔机的高级功能菜单.................85 副翼/方向舵混控 AILE/RUDD............86 副翼,襟翼混控 AILE-FLAP(仅限于滑翔机 [2A+2F]).............................87 阻流板混控 SPOILER MIX................88 微调杆偏置 OFFSETs 附加飞行条件)......89 起飞延迟(仅限于滑翔机[1A+’F[)......90 翼型混控 CAMBER MIX.................90 翼型襟翼 CAMBER FLAP.................91 蝶式混控 BUTTERFLY...................92 通道 3 的功能选择(飞行条件/功能) ( CONDITION/FUNCTION) ...............93
MC10E211FN资料
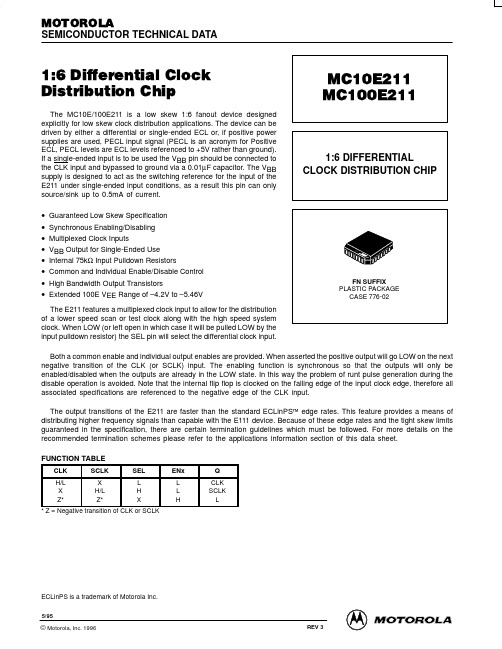
MOTOROLA
2–2
ECLinPS and ECLinPS Lite DL140 — Rev 4
元器件交易网
MC10E211 MC100E211
DC CHARACTERISTICS (VEE = VEE(min) to VEE(max); VCC = VCCO = GND)
0°C Characteristic Output Reference Voltage 10E 100E Input High Current Power Supply Current 10E 100E Symbol VBB –1.38 –1.38 IIH IEE 119 119 160 160 119 119 160 160 119 137 160 164 –1.27 –1.26 150 –1.35 –1.38 –1.25 –1.26 150 –1.31 –1.38 –1.19 –1.26 150 µA mA Min Typ Max Min 25°C Typ Max Min 85°C Typ Max Unit V Condition
ECLinPS and ECLinPS Lite DL140 — Rev 4
2–3
MOTOROLA
元器件交易网
MC10E211 MC100E211
APPLICATIONS INFORMATION
General Description The MC10E/100E211 is a 1:6 fanout tree designed explicitly for low skew high speed clock distribution. The device was targeted to work in conjunction with the E111 device to provide another level of flexibility in the design and implementation of clock distribution trees. The individual synchronous enable controls and multiplexed clock inputs make the device ideal as the first level distribution unit in a distribution tree. The device provides the ability to distribute a lower speed scan or test clock along with the high speed system clock to ease the design of system diagnostics and self test procedures. The individual enables could be used to allow for the disabling of individual cards on a backplane in fault tolerant designs. Because of lower fanout and larger skews the E211 will not likely be used as an alternative to the E111 for the bulk of the clock fanout generation. Figure 1 shows a typical application combining the two devices to take advantage of the strengths of each.
Endress+Hauser CP 210-R 温度与压差传感器数据手册说明书

Features• Input Pt100 on terminal blockfor temperature measurement, range from -100to +400°C (probes as option)• Configurable intermediate ranges• Power supply 24 Vdc/Vacor 100-240 Vac• Trend indicator• “¼ turn” system mounting withwall-mount plate• Solenoid valve for auto-calibration(only on CP211 and CP212 models)Two 4-wire analogue output0-5/10 V or 0/4-20 mARange from ±100 to ±10 000 Pa(according to model, see “Part number”)ABS V0 housing, IP65,with or without display2 relay outputsCP 21----Measuring range1: -100/+100 Pa2: -1000/+1000 Pa3: -10 000/+10 000 PaRRelay outputsPart numberPower Supply / OutputB: 24 Vac/VdcH: 100-240 VacDisplayO: with displayN: without displayExample: CP 211 – HO – RPressure transmitter -100/+100 Pa measuring range, with100-240 Vac power supply, with display and relay outputs.Warning: risk of electric shock2 x 4-20 mA or 2 x 0-20 mA or 2 x 0-5 V or 2 x 0-10 V (4 wires)Common mode voltage <30 VAC DOUBLE ISOLATION or REINFORCED ISOLATIONAll dimensions are in millimeters.*These air velocity ranges are given for information, based on a L type Pitot tube and donot take into account temperature compensation.Airflow and Air Velocity functions*Differential pressure device (Pitot tube, Debimo...) as optionClass 210 transmitters have 2 analogue outputs that correspond to both displayed parameters. It is possible to activate one or two outputs and select for each output between pressure, air velocity and air flow (functions as option).Linked to a differential pressure device (Debimo blade, Pitot tube, orifice plate, …), they can be equipped as option with the SQR 3 function (square root function) allowing to calculate the air velocity and/or air flow in a duct from a differential pressure.•Air Velocity calculation :•Air flow calculation: air flow (m3/h) = air velocity (m/s) x surface(m²) x 3600Surface: setting of duct type (rectangular or circular) and duct size (mm or inch).With:C M : differential pressure device coefficient- Pitot tube type L: C M = 1.0015- Pitot tube type S: C M = 0.84- Debimo blade: C M = 0.8165: given temperature (°C)P O : given atmospheric pressure (Pa)Integration of pressure measurementThe pressure measurement element is very sensitive and reacts to pressure changes. When making measurements in unstable air movement conditions, the pressure measurement may fluctuate. The integration coefficient (from 0 to 9) makes an average of the measurements and then helps avoid any excessive variations; it guarantees a stable measurement.Connections50-60 Hz 8 VA 0/4...20 mA / 0...5/10 Von the side of the transmitter12345810711oupower (c)For 100-240 Vac power supply models9Alimentation 24 Vac classe II norme EN61558-2-6NL Alimentation 100-240 Vacautomate 1. DIP switch (d)2. Pt100 terminal block3. Solenoid valve (only on CP211/212)4. LCC-S software connection5. Autozero6. Pressure connections7. Relays8. Analogue outputs (a)9. F3.20* fuse10. Power supply terminal block (c)11.Cable glandsLPe N L ou230 Vac230 Vacclasse II norme EN61558-2-6LAlimentation100-240 Vac-+0-5/10 V 0/4-20 mA Af cheur régulateur ou automate type passifAf cheur régulateur ou automate type passif Sortie 4-20 mASortie 0-10 VAutozeroAuto-calibrationCP210 transmitters have a temperature compensation of the gain from 0 to 50°C and an auto-calibration process that guarantees over the time an excellent stability and a perfect reliability of the measurement on low and high ranges.Auto-calibration principle: the microprocessor of the transmitter drives a solenoid valve that compensates the possible drifts on the sensitive ele-ment over the time. The compensation is performed by the permanent adjustment of the zero. So the measurement of the differential pressure is then independent from the environmental conditions of the transmitter. Advantage: no driftFrequency of auto-calibration: resetable or from 1 to 60 minutesAutozeroTo perform an autozero, unplug the 2 pressure connections tubes and press the “Autozero” key. On CP211 and CP 212 transmitters, it is not necessary to unplug the 2 pressure connection tubes. When an autozero has been performed, “On” green light turns off then turns on, and on transmitters equipped with a display, “autoZ” is displayed.Configuration of the transmittersIt is possible on the class 210 to configure all the parameters managed by the transmitter : units, measuring ranges, outputs, channels, calcula-tion functions, etc, via different methods:•Keypad for models with display : a code-locking system allows to secure the installation (See class 210 user manual).•Software (optional) on all models. Simple user-friendly configuration. See LCC-SD user manual.Configurable analogue output:Range with central zero (-50/0/+50 Pa), with offset zero (-300/0/+70 Pa) or standard range (0/+100 Pa), it is possible to configure your own intermediate ranges.Caution: the minimum difference between the high range and the low range is 20.Configure the range according to your needs: outputs are automatically adjusted to the new measuring range50-1000 V 4 mA 0+10010 V 20 mANew range-1000 V 4 mA 0+10010 V 20 mA50MountingTo mount the transmitter, mount the ABS plate on the wall (drilling: Ø6 mm, screws and pins areclockwise direction until you hear a “click” which confirms that the transmitter is correctly installed.Once the transmitter is installed and powered up, please make an autozero toguarantee the correct working of the transmitter in any position.MaintenancePlease avoid any aggressive solvent. Please protect the transmitter and its probes from any cleaningproduct containing formalin, that may be used for cleaning rooms or ducts.F T a n g – C P 210 R – 02/04/19 – R C S (24) P ér i g u e u x 349 282 095 N o n -c o n t r a c t u a l d o c u m e n t – W e r e s e r v e t h e r i g h t t o m o d i f y t h e c h a r a c t e r i s t i c s o f o u r p r o d u c t s w i t h o u t p r i o r n o t i c e .CalibrationOutputs diagnostic: With this function, you can check with a multimeter (or on a regulator / display, or a PLC / BMS) if the transmitter outputs work properly. The transmitter generates a vol-tage of 0 V , 5 V and 10 V or a current of 4 mA, 12 mA and 20 mA Certificate: Class 210 transmitters are supplied with adjusting certificates. Calibration certificates are available as an option.Precautions for usePlease always use the device in accordance with its intended use and within parameters described in the technical features in order not to compromise the protection ensured by the device.Only the accessories supplied with the device must be used.Les dimensions sont exprimées en millimètres.。
PCE-HT 210说明书
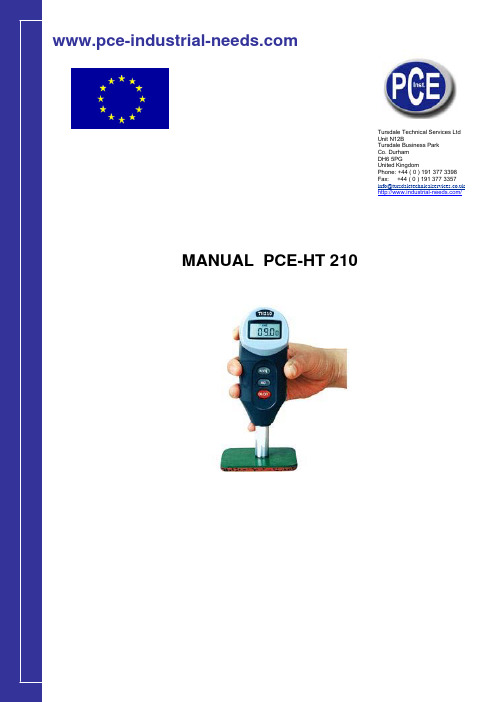
ContentsChapter 1. Introduction (3)1.1 Main features and application (3)1.2 Fundamental (3)Chapter 2. Technical Specification: (3)Chapter 3. Main functions and configuration (3)3.1 Main functions (3)3.2 Basic configurations (4)3.3 Optional configurations: (4)Chapter 4. Composition (4)4.1 Composition of main unit See figure 2 (4)4.2 Usage of protective sleeve (4)4.3 Usage of battery house (4)4.4 Usage of joint cover (5)4.5 Usage of display screen (6)4.6 Usage of press button (6)4.7 Usage of communication interface and power adapter (6)Chapter 5. Functions setting (7)5.1 Start (7)5.2 Max value function (7)5.3 Test times function and average value function setting (7)5.3.1 Setting methods of test times (8)5.3.2 Average value setting: (8)5.4 Auto turn off function (9)Chapter 6. Measuring (9)6.1 Preparation before measuring (9)6.2 Calibration (9)6.3 Operation method (9)6.3.2 Measuring by the operating stand: (10)6.4 Communication with computer (10)Chapter 7. Attention items: (11)Chapter 8. Maintenance (11)Chapter 1. Introduction1.1 Main features and applicationTIME TH210 Shore D hardness tester (hereafter called hardness tester) is a kind of advanced integral digital hardness tester. It includes measuring device and data processing system. It is of the merit of advanced technology, pocketsize, accurate measuring data, appearance beautiful, light weight, and easy to operate. It can be connected with computer by RS-232 communication cable. It is mainly used to measure hardness of hard plastic and rubber such as heat plasticity, hard resin, floor materials, bowling etc. Especially suitable for finished products in working situation.1.2 FundamentalWhen the steel indenter of certain shape is pushed into the sample surface vertically with testing force, and when surfaces of pressure foot and the sample touched completely (see figure 1), the indenter extends out for a certain length “L” from the pressure foot plane. Greater length “L” means lower Shore hardness value and smaller length “L” means bigger Shore hardness value. The formula is HD=100-L/0.025, HD is Shore Dand processing of the CPU.Measuring range:0HD 100HDMeasuring error:Resolution: 0.2HDEnvironmental temperature: 0 ºC 40 °CPower supply: 1.55V×3 button batteries and 5V AC- DC adapterDimensions: 173mm×56mm×42mmWeight: 230gChapter 3. Main functions and configuration3.1 Main functionsPeak value locked storage, average value calculating and low-voltage alarming.Data commu Shut off auto 3.2 Basic TH210 main 3.3 Option RS-232 com Chapter 4.1 Comp 1. Communi 3. Protective 5. Press butt 7. Battery ho 4.2 Usage The prote service, f sleeve sh with mainFigure 34.3 Usage Pull out and into three b reversely un unication with omatically.configura n unit Three S nal config mmunication c 4. Comp osition of cation interfa e sleeve ton ousee of protec ective sleeve first take off hould be pul n unit, see fig e of batter turn the bat button batter ntil clamped ch computer b ationsSR44 button urations:cable 5V A positionf main unit ace 2. Po 4. Dis 6. M 8. Jo ctive sleev e is used to p protective s lled on in tim gure 3.ry housetery house s ries. Take c closely with m by use of RS batteriesAC- DC powet See figuower plug bo splay screen easuring dev oint coverveprevent inde leeve. Grasp me. Put prote slightly to ma are of posit main unit, seS-232 commu er adapter re 2oard n vice nter from da p and pull ou ective sleeveake it rotate a tive pole sym ee figure 5.unication cab Shore hardn Figure 2amage under ut it by hand e on cylinde about 90° aro mbol “+” co ble of compa ness stands o r non working d . When finis r and push u ound axis wi nsistently. A any of TH210FJg condition. shed measur up untill it cl th thumb, se At last, turn Before put in ring, protecti amped close ee figure 4. P battery hou nto ive ely Put useF Figure 64.5 Usage Screen areas w1---MAX 2---AVE 3---BATT 4---Hardn 5---Test t 4.6 Usage Buttons is N/AVE-- MAX----- ON/OFF4.7 UsageIt can com instead of baFigure 9e of displa is used to d which is state Max value Average va T Low-voltage ness value times,e of press s used to turn -- Test times --Max value f F---Switch bu e of comm municate wi atteries, seeay screenisplay results ed as follow, Figure 7function (tes alue function,e indication, buttonn on or turn o s function and function butt tton red.munication ith computer figure 9.3. AC-DC s as well as w see figure 7ster locked au off power as d Average fu ton, n interface r by RS-232 1. Computer C power adap working state utomatically well as set f unction buttoe and powe communicar 2. Commu pter 4. Hard es of tester. and stored p unctions, see n, er adapter ation cable. I unication cab dness tester The screen i peak value), e figure 8: F r t can use 4ble5. Sampleis divided int Figure 8.5V AC-DC to 5 displayin power adap ng ter*********************************.ukF 5.3.1 Sett Under f 9, in which th Method requirement Method circulated am After comple 5.3.2 Aver After te hardness teautomatically figure 15. W are set as 1,clears zero a User ca as max aver average fun method is th value, only n same as abo Figure 12 ing metho figure 12 stat he times can d 1: Press b , then releas d 2: Press bu mong 0 9 ra eted test time rage value st times bein ester display y cancels ro hen test time , tester displa automatically an record me rage value a ction should he same as need to set a ove mentioneods of test te, the test ti n be circled w button N/AV se button at o utton N/AVE ange until rea es setting, m e setting:ng set, hardn s current m ough error a es is set as 2ays the meas y and restore easured data and random a d be set and above ment average func edt timesimes can be within 0 9 ra VE for a wh once and com repeatedly. aches require machine is in ness tester c easured val and displays 2, arithmetica sure value on es ready stat a by manual average valu displays MA ioned and se ction and dis Figure 13 set by press ange. There a hile, the time mpleted.The value a ement, then ready state f can judge ba ue and test average va al mean of th nly. After ave te. The times and calcula ue. When ca AX and AVE etting order splays AVE o s button N/A are two kinds es circulated adds one for release butto for testing, se ased on test times of th lue. If rough e two tested erage value d s to be set ar ates arithmet alculating ma E symbol at s is not requir on screen, se AVE continua s of setting m d among 0 r every times on at once a ee figure 14.times. When his test. Whe h error is too data will be displays for 8re still valid.tic mean. Th ax average v same time s red. When ca ee figure 14. Figure 14 ally. The max method:9 range u s press in w and completen test times en reached o larger, dis displayed. W 8 seconds, h e average v alue, the ma see figure 16alculating ra . The settingx test times a ntil it reach which the tim ed. is among 3the set time plays “E.”, s When test tim hardness tes value is divid ax function a 6. Their setti andom avera g method is t are hes mes 9, es, see mes ter ed nd5.4 Auto t If teste automatically Chapter6.1 Prepa The prepara damaged, no Tester prepa 6.2 Calibr 6.2.1 Zero p indenter nee 6.2.2 Non ze Make bottom hardness va order to prot to damage th6.3 Opera 6.3.1 Manua Place the sa avoid any sh within 1 seco turn off fu r is in ready y.6. Meas ration bef ation of sam o impurities a aration: disas rationpoint calibrat edle is max; t ero point cali m surface o alue displaye tect indenter he point of in ation meth al measure:ample on the hake. When t ond. The dis nctiony state for t uringfore meas mple: The sa and so on. ssemble prot tion: After sw the hardness brationof pressure f ed should be r, it should av ndenter need hodslab. Hold th the bottom o played value three minute uringample thicknetective sleev witch on pow s value displa foot of hard 100 on the void indenter dle of hardne he tester and of pressure fo e then is the es, and flas ess should ve and put int wer, hardnes ayed on the ness tester screen, see r point to tou ess tester and F d press inden oot touches t hardness va hes on scre be equable, to batteries o ss tester is in screen is ze touch glass figure 17. N uch glass pro d operate ab Figure 17nter needle i the sample s alue of the sa een for fiftee surface sm or connect po n ready state ro. s surface co ote: when ca omptly and ru bnormally.nto sample v surface comp ample.en seconds mooth, no bu ower adapte e. The protru ompletely. At alibrating in t udely. Otherw vertically and pletely, read then turns ubble inner, r.usion length t this mome this method,wise, it is ea d slowly to the value off no of ent, in asy*********************************.uk6.3.2 Measuring by the operating stand:Before using Shore hardness operating stand for measurement, the hardness tester should be assembled with the operating stand firstly, the assembled state see figure 18. Assemble 5 kg balancing weight on top of fixing rod through its middle hole. Place sample 3 on working table 2, then loosen locked wheel. Adjust height between hardness tester 4 and sample 3 by using of lifting and descending sliding arm 9. Make proper distance between indenter point and sample surface (forbid to touch). Fasten locked wheel 10. Fix sliding arm 9, then press down handle 7. At this moment, test sample 3 moves up with working table 2 until the pressure foot 4 touches sample 3 surface with balancing weight 5 lifted up slightly. The value displayed on the screen is hardness value, read it within 1 second.6.4 Communication with computerThis tester can communicate with computer which the band rate is 9600. The data is transferred by text file which can receive by common communication software (such as super technical device of WINDOWS). The RS-232 communication cable is needed to connect the tester with a computer, see figure 9. It can send signal to computer when gets the reading value. The operation procedure is as follow when using super terminal device of WINDOWS:6.4.1 Connect the nine cores bottom of RS-232 communication cable to series interface of computer. Insert the other bottom into communication interface of hardness tester (series interface), see figure9. Switch on the tester.6.4.2 Click “start” “program” “ Accessories” “communication” on WINDOWS to HyperTerminal.6.4.3 Run HyperTerminal, type in a file name at new established connection, then press “Enter”.6.4.4 Select the series interface of communication cable, then select band rate 9600, press “Enter”. At this moment, the measured value should be displayed on computer.6.4.5 If you want to store the measured result, select “Disconnect” under “dial” menu of HyperTerminal, select1. base3. sample7. handleChapter 7. Attention items:7.1. The indenter of hardness tester is sharp cone, forbid to touch it with glass plate forcely in order to protect it. Otherwise, it is easy to be damaged and to operate abnormally.7.2. Forbid hardness tester collision and fall break. After service, pull on protective sleeve so as to protectthe indenter needle.7.3. When displays symbol BATT in low-voltage, see figure 8, replace batteries in time and pay attention to the pole of batteries, see figure 5.7.4 After completed measurement by using operating stand, see figure 7, close the joint cover of hardness tester so as to avoid dust entering into.Chapter 8. Maintenance8.1. Routine maintenanceThis hardness tester should avoid impact and heavy loading, and keep away from strong magnetic field, damp or oil environment.If store for long time and do not use it, take out batteries and take care of them.When do not using the tester, please put it into packing box.8.2. Maintenance:If any abnormal phenomenon occurs, please contact the service maintenance center of company.8.3. The list of non maintenance parts:Items Name Quantity Remarksneedle 11 Indenterbattery 32 ButtonPoints for consumers attention1. From purchased date, the products occur any fault except for non guarantee maintenance parts, will freemaintain by warranty card and inovice copy within one year. If you could not show above mentioned requirement, company calculates guarantee period in accordance with the date of leaving factory, valid period is one year.2. If the fault product exceeds maintenance period, in accordance with stipulation of Company, it will be takencharge of maintenance and service.3. The “special configuration” out of Company’s approved products would take fees in accordance with relatedstandards.4. The product should not receive free maintenance service if belongs to conditions as follow: storageunsuitable, operated incorrectly which is not in accordance with manual book, disassembled, altered by oneself as well as no purchasing proof.In this direction will find a vision of the measurement technique:/measuring-instruments.htmNOTE: "This instrument doesn’t have ATEX protection, so it should not be used in potentially explosive atmospheres (powder, flammable gases)."。
Futaba10C-10CH中文说明书(1)

项设置或者功能的时候,都包含了大量的解释、描述文字,突出进行该项设置的“目的”、 该功能的“用途”,不像 14 通道或 12 通道设备配备的说明书,大量的篇幅用来说明菜单系 统、屏幕格局。此外,10C 说明书还注重功能设置、数据与和实际动作、设备的紧密联系, 对设置产生的实际效果描述十分清晰。 2. 英文说明书中对屏幕按键的使用方法写得“极为”详细,例如滚轮、导航键的组台使用方法 在几乎存在于每一页的设置举例中,这些表格看起来很复杂,但其实很简单,对于已经使用 过 Futaba9 通道遥控设备的用户,不必每 1 页的操作动作指引都看,按键使用方法与其它的 设备近似。之所以写得如此详细,是为了便于未接触过遥控器的初学者使用。 3. 对于各种类犁飞机、各重要功能项的基本设置原则介绍,是 10C 英文说明书中最“精华”的 内容,引导使用者进行正确的、快速的设置,请初次接触航空模型的用户多多注意,通过阅 读、揣摩,可以学到很多有用知识,本来译者有翻译 14z 说明书的成功先例,以为 10c 的说 明书会相对容易翻译一些,但仔细看过 10c 英文说明书后,即觉得它几乎是一本遥控模型设 置的基本手册,其间不乏模犁技术、原理、应用举倒,有些内容译者自己能理解,但用文字 正确表述出来,让爱好者在实际使用时能明白含义并且设定正确,确实让我们颇费番脑筋。 其中广泛涉及到各种倾斜盘操纵方式的直升机;各种空气动力布局的固定翼(3A 和滑翔机) 各种尾翼的操纵形式,让我们在翻译说明书的同时,对相对应的空气动力知识进行补充学习, 这个过程对我们自身的专业知识也是一个促进和提高。 4. 不同功能之间的关联性描述得十分清楚。例如在解释一项舵面混控功能之后,会列出与之相 关的多个混控项,并给出页码。 5. 不仅说明书正文通俗易懂,而且说明书的最后附有名词解释(专业词汇表),这也是其“贴 心”设计的重要表现。对文字理解有困难的用户可以用作参考。
- 1、下载文档前请自行甄别文档内容的完整性,平台不提供额外的编辑、内容补充、找答案等附加服务。
- 2、"仅部分预览"的文档,不可在线预览部分如存在完整性等问题,可反馈申请退款(可完整预览的文档不适用该条件!)。
- 3、如文档侵犯您的权益,请联系客服反馈,我们会尽快为您处理(人工客服工作时间:9:00-18:30)。
MC10H210Dual 3−Input 3−Output OR GateDescriptionThe MC10H210 is designed to drive up to six transmission lines simultaneously. The multiple outputs of this device also allow the wire ORing of several levels of gating for minimization of gate and package count.The ability to control three parallel lines with minimum propagation delay from a single point makes the MC10H210 particularly useful in clock distribution applications where minimum clock skew is desired. Features•Propagation Delay Average, 1.0 ns Typical•Power Dissipation, 160 mW Typical•Improved Noise Margin 150 mV (Over Operating V oltage and Temperature Range)•V oltage Compensated•MECL 10K™ Compatible•Pb−Free Packages are Available*LOGIC DIAGRAMDIPPIN ASSIGNMENTV CC1 A OUT A OUT A OUT A IN A IN A IN V EEV CC2V CC1B OUTB OUTB OUTB INB INB IN1615141312111091234567811109765V CC1 = PINS 1, 15V CC2 = PIN 16V EE = PIN 8Pin assignment is for Dual−in−Line Package.For PLCC pin assignment, see the Pin Conversion Tables on page 18of the ON Semiconductor MECL Data Book (DL122/D).*For additional information on our Pb−Free strategy and soldering details, please download the ON Semiconductor Soldering and Mounting Techniques Reference Manual, SOLDERRM/D.See detailed ordering and shipping information in the package dimensions section on page 3 of this data sheet.ORDERING INFORMATIONTable 1. MAXIMUM RATINGSSymbol Characteristic Rating Unit V EE Power Supply (V CC = 0)−8.0 to 0Vdc V I Input Voltage (V CC = 0)0 to V EE VdcI out Output Current− Continuous− Surge 50100mAT A Operating Temperature Range0 to +75°CT stg Storage Temperature Range− Plastic− Ceramic −55 to +150−55 to +165°C°CMaximum ratings are those values beyond which device damage can occur. Maximum ratings applied to the device are individual stress limit values (not normal operating conditions) and are not valid simultaneously. If these limits are exceeded, device functional operation is not implied, damage may occur and reliability may be affected.Table 2. ELECTRICAL CHARACTERISTICS (V EE = −5.2 V ±5%) (Note 1)0°25°75°Symbol Characteristic Min Max Min Max Min Max UnitI E Power Supply Current−42−38−42mAI inH Input Current High−720−450−450m AI inL Input Current Low0.5−0.5−0.3−m AV OH High Output Voltage−1.02−0.84−0.98−0.81−0.92−0.735Vdc V OL Low Output Voltage−1.95−1.63−1.95−1.63−1.95−1.60Vdc V IH High Input Voltage−1.17−0.84−1.13−0.81−1.07−0.735Vdc V IL Low Input Voltage−1.95−1.48−1.95−1.48−1.95−1.45Vdc 1.Each MECL 10H™ series circuit has been designed to meet the dc specifications shown in the test table, after thermal equilibrium has beenestablished. The circuit is in a test socket or mounted on a printed circuit board and transverse air flow greater than 500 linear fpm is maintained. Outputs are terminated through a 50 W resistor to −2.0 V. Note: If crosstalk is present, double bypass capacitor to 0.2 m F.Table 3. AC PARAMETERS0°25°75°Symbol Characteristic Min Max Min Max Min Max Unit t pd Propagation Delay0.5 1.550.55 1.550.6 1.7ns t r Rise Time0.75 1.80.75 1.90.8 2.0ns t f Fall Time0.75 1.80.75 1.90.8 2.0ns NOTE:Device will meet the specifications after thermal equilibrium has been established when mounted in a test socket or printed circuit board with maintained transverse airflow greater than 500 lfpm. Electrical parameters are guaranteed only over the declaredoperating temperature range. Functional operation of the device exceeding these conditions is not implied. Device specification limit values are applied individually under normal operating conditions and not valid simultaneously.ORDERING INFORMATIONDevice Package Shipping†MC10H210FN PLLC−2046 Units / RailMC10H210FNG PLLC−2046 Units / Rail(Pb−Free)MC10H210FNR2PLLC−20500 / Tape & ReelMC10H210FNR2G PLLC−20500 / Tape & Reel(Pb−Free)MC10H210L CDIP−1625 Unit / RailMC10H210M SOEIAJ−1650 Unit / Rail50 Unit / RailMC10H210MG SOEIAJ−16(Pb−Free)MC10H210MEL SOEIAJ−162000 / Tape & Reel2000 / Tape & ReelMC10H210MELG SOEIAJ−16(Pb−Free)MC10H210P PDIP−1625 Unit / RailMC10H210PG PDIP−1625 Unit / Rail(Pb−Free)†For information on tape and reel specifications, including part orientation and tape sizes, please refer to our Tape and Reel Packaging Specifications Brochure, BRD8011/D.PACKAGE DIMENSIONSSL−MS 0.010 (0.250) NST 20 LEAD PLLC CASE 775−02ISSUE ENOTES:1.DIMENSIONS AND TOLERANCING PER ANSI Y14.5M,1982.2.DIMENSIONS IN INCHES.3.DATUMS −L −, −M −, AND −N − DETERMINED WHERE TOP OF LEAD SHOULDER EXITS PLASTIC BODY AT MOLD PARTING LINE.4.DIMENSION G1, TRUE POSITION TO BE MEASURED AT DATUM −T −, SEATING PLANE.5.DIMENSIONS R AND U DO NOT INCLUDE MOLD FLASH.ALLOWABLE MOLD FLASH IS 0.010 (0.250) PER SIDE.6.DIMENSIONS IN THE PACKAGE TOP MAY BE SMALLER THAN THE PACKAGE BOTTOM BY UP TO 0.012 (0.300).DIMENSIONS R AND U ARE DETERMINED AT THE OUTERMOST EXTREMES OF THE PLASTIC BODY EXCLUSIVE OF MOLD FLASH, TIE BAR BURRS, GATE BURRS AND INTERLEAD FLASH, BUT INCLUDING ANY MISMATCH BETWEEN THE TOP AND BOTTOM OF THE PLASTIC BODY .7.DIMENSION H DOES NOT INCLUDE DAMBAR PROTRUSION OR INTRUSION. THE DAMBARPROTRUSION(S) SHALL NOT CAUSE THE H DIMENSION TO BE GREATER THAN 0.037 (0.940). THE DAMBARINTRUSION(S) SHALL NOT CAUSE THE H DIMENSION TO BE SMALLER THAN 0.025 (0.635).DIM MIN MAX MIN MAX MILLIMETERSINCHES A 0.3850.3959.7810.03B 0.3850.3959.7810.03C 0.1650.180 4.20 4.57E 0.0900.110 2.29 2.79F 0.0130.0190.330.48G 0.050 BSC 1.27 BSC H 0.0260.0320.660.81J 0.020−−−0.51−−−K 0.025−−−0.64−−−R 0.3500.3568.899.04U 0.3500.3568.899.04V 0.0420.048 1.07 1.21W 0.0420.048 1.07 1.21X 0.0420.056 1.07 1.42Y −−−0.020−−−0.50Z 2 10 2 10 G10.3100.3307.888.38K10.040−−− 1.02−−−____PACKAGE DIMENSIONSSOEIAJ −16CASE 966−01ISSUE ANOTES:1.DIMENSIONING AND TOLERANCING PER ANSI Y14.5M, 1982.CDIP −16L SUFFIXCERAMIC DIP PACKAGECASE 620A −01NOTES:1.DIMENSIONING AND TOLERANCING PER ASME Y14.5M, 1994.2.CONTROLLING DIMENSION: INCH.3.DIMENSION L TO CENTER OF LEAD WHEN FORMED PARALLEL.4.DIMENSION F MAY NARROW TO 0.76 (0.030)WHERE THE LEAD ENTERS THE CERAMIC BODY.5THIS DRAWING REPLACES OBSOLETE CASE OUTLINE 620−10.AM0.25 (0.010)T DIM MIN MAX MIN MAX MILLIMETERSINCHES A 0.7500.78519.0519.93B 0.2400.295 6.107.49C −−−0.200−−− 5.08D 0.0150.0200.390.50E 0.050 BSC 1.27 BSC F 0.0550.065 1.40 1.65G 0.100 BSC 2.54 BSC H 0.0080.0150.210.38K 0.1250.170 3.18 4.31L 0.300 BSC 7.62 BSC M 0 15 0 15 N0.0200.0400.51 1.01____PACKAGE DIMENSIONSNOTES:1.DIMENSIONING AND TOLERANCING PER ANSI Y14.5M, 1982.2.CONTROLLING DIMENSION: INCH.3.DIMENSION L TO CENTER OF LEADS WHEN FORMED PARALLEL.4.DIMENSION B DOES NOT INCLUDE MOLD FLASH.5.ROUNDED CORNERS OPTIONAL.MDIM MIN MAX MIN MAX MILLIMETERSINCHES A 0.7400.77018.8019.55B 0.2500.270 6.35 6.85C 0.1450.175 3.69 4.44D 0.0150.0210.390.53F 0.0400.70 1.02 1.77G 0.100 BSC 2.54 BSC H 0.050 BSC 1.27 BSC J 0.0080.0150.210.38K 0.1100.130 2.80 3.30L 0.2950.3057.507.74M 0 10 0 10 S0.0200.0400.51 1.01____PDIP −16P SUFFIXPLASTIC DIP PACKAGEON Semiconductor and are registered trademarks of Semiconductor Components Industries, LLC (SCILLC). SCILLC reserves the right to make changes without further notice to any products herein. SCILLC makes no warranty, representation or guarantee regarding the suitability of its products for any particular purpose, nor does SCILLC assume any liability arising out of the application or use of any product or circuit, and specifically disclaims any and all liability, including without limitation special, consequential or incidental damages.“Typical” parameters which may be provided in SCILLC data sheets and/or specifications can and do vary in different applications and actual performance may vary over time. All operating parameters, including “Typicals” must be validated for each customer application by customer’s technical experts. SCILLC does not convey any license under its patent rights nor the rights of others. SCILLC products are not designed, intended, or authorized for use as components in systems intended for surgical implant into the body, or other applications intended to support or sustain life, or for any other application in which the failure of the SCILLC product could create a situation where personal injury or death may occur. Should Buyer purchase or use SCILLC products for any such unintended or unauthorized application, Buyer shall indemnify and hold SCILLC and its officers, employees, subsidiaries, affiliates,and distributors harmless against all claims, costs, damages, and expenses, and reasonable attorney fees arising out of, directly or indirectly, any claim of personal injury or death associated with such unintended or unauthorized use, even if such claim alleges that SCILLC was negligent regarding the design or manufacture of the part. SCILLC is an Equal Opportunity/Affirmative Action Employer. This literature is subject to all applicable copyright laws and is not for resale in any manner.PUBLICATION ORDERING INFORMATIONMECL 10H and MECL 10K are trademarks of Motorola, Inc.。