GMW 16740
TSI Incorporated EVERWATCH Model 8610 Face Velocit
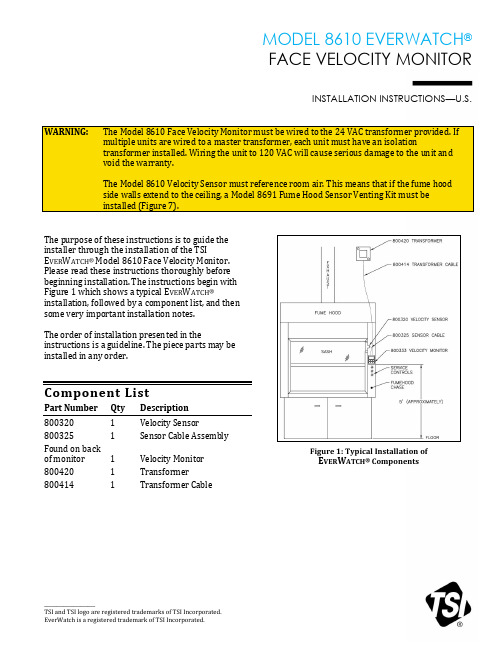
_____________________TSI and TSI logo are registered trademarks of TSI Incorporated. EverWatch is a registered trademark of TSI Incorporated. MODEL 8610 EVERWATCH®FACE VELOCITY MONITOR INSTALLATION INSTRUCTIONS—U.S.The purpose of these instructions is to guide the installer through the installation of the TSIE VER W ATCH® Model 8610 Face Velocity Monitor. Please read these instructions thoroughly before beginning installation. The instructions begin with Figure 1 which shows a typical E VER W ATCH®installation, followed by a component list, and then some very important installation notes.The order of installation presented in the instructions is a guideline. The piece parts may be installed in any order.Part Number Qty Description800320 1 Velocity Sensor800325 1 Sensor Cable AssemblyFound on backof monitor 1 Velocity Monitor 800420 1 Transformer 800414 1 Transformer Cable Figure 1: Typical Installation of E VER W ATCH® Components1. Select the mounting location of the VELOCITYMONITOR. The monitor is typically mounted above the service controls (see Figure 1). 2. Cut a hole at this location, sized to mount astandard single gang electrical box. 3. Mount a single gang electrical box.4. Determine VELOCITY SENSOR location. UseFigure 2 as a guideline. 5. VELOCITY SENSOR is mounted to liner wallinside hood. 6. Drill 2¼-inch holes through the fume hood linerwall at this location.1.Install MOUNTING PLATES to fume hood linerwall using 2 of the 8-32 ⨯ 5/8-inch screws provided. The MOUNTING PLATES must be configured as shown in Figure 3. 2. Plug SENSOR CABLE ASSEMBLY into theVELOCITY SENSOR.3. Thread the SENSOR CABLE ASSEMBLY throughthe mounting plates down to the VELOCITYMONITOR electrical rough-in box (Figure 4). The space between the fume hood liner wall and outer sheet metal panel works well as a chase. Leave 8 inches of slack at the VELOCITYMONITOR end (DO NOT CUT SENSOR CABLE LENGTH). 4. Mount the VELOCITY SENSOR to the MOUNTINGPLATE using the remaining two 8-32 ⨯ 5/8-inch screws provided (Figure 4). 5. The mounted VELOCITY SENSOR should look likeFigure 4.Figure 2: Velocity Sensor LocationFigure 3: Mounting PlatesFigure 4: Mounted Velocity SensorFigure 5: Transformer InstallationNOTE : 120 Volt, single-phase, 60 Hertz powersource is required to power the 800420 TRANSFORMER. If TSI Transformer is not installed, a regulated 24 volt, single-phase, 60 Hertz power source is required to power the monitor. If multiple units are wired to a master transformer, an isolationtransformer must be installed for each monitor. 1. Mount a standard 4" ⨯ 4" ⨯ 1½" electrical box, ata convenient location within 20 feet of VELOCITY MONITOR (typically on the wall behind the fume hood).2. Run 120 Volt, single-phase, 60 hertz line voltage(120 VAC) to electrical box. Follow all applicable electrical codes. 3. Connect 120 VAC line voltage HOT wire to BLACKwire on TRANSFORMER and NEUTRAL wire to WHITE wire on TRANSFORMER. Connect the RED wire on 800414 TRANSFORMER CABLE to either YELLOW wire on the TRANSFORMER and the BLACK wire to the remaining YELLOW wire. Screw the TRANSFORMER to the electrical box. 4. Run TRANSFORMER CABLE from theTRANSFORMER electrical box to the VELOCITY MONITOR electrical box. Have at least 8 inches of cable coming out of the VELOCITY MONITOR rough-in box before trimming cable to length.1. Remove 10-pin connector from the back ofVELOCITY MONITOR. 2. Refer to the wiring diagram (Figure 6) for properwiring installation. If additional options need to bewired, refer to building prints for proper wiring diagram.3. Plug the 10-pin and sensor connectors into themonitor. 4. Carefully push the wires into the electrical Boxand mount the monitor electronics. Insert the twoscrews, with lock washers, into the holes on the VELOCITY MONITOR. Screw unit snug to hood ensuring a good ground between monitor, screws, and fume hood.WARNING:Do not connect more than 24 VAC to any terminal. Do not connect more than one monitoring device per transformer.Do not apply voltage to the RS-485 or analog output. Severe damage may occur to the unit ifvoltage is applied. This voids the warranty.Figure 6: Wiring Velocity MonitorTSI Incorporated– Visit our website for more information.USA Tel: +1 800 874 2811 UK Tel: +44 149 4 459200 France Tel: +33 491 11 87 64 Germany Tel: +49 241 523030India Tel: +91 80 67877200 China Tel: +86 10 8251 6588 Singapore Tel: +65 6595 6388Figure 7: Fume Hood Sensor Venting KitIf you need assistance installing the system, call TSI Customer Service at 651-490-2811 or 800-874-2811.。
汽车电线束技术要求 泛亚汽车设计中心规范 (双语)

汽车电线束技术要求1.范围本标准规定了用于泛亚汽车技术中心有限公司(以下称PATAC)开发的低压线束制造工艺过程技术要求。
按线束的生产流程分,该标准主要分为三部分,分别为开线、预装和总装。
2.术语和定义下列文件对于本标准的应用是必不可少的。
凡是注日期的引用文件,仅注日期的版本适用于本标准。
凡是不注日期的引用文件,其最新版本(包括所有的修改单)适用于本标准。
ISO 8820 保险丝设计规范USCAR 21 美国汽车研究委员会标准21USCAR 38 美国汽车研究委员会标准38QC/T29106-2014 汽车低压电线束技术条件GME 15339 电气功能通用规格标准GMW3172 电子电气部件环境和耐久通用规范GMW3173 ISO导线截面及汽车通讯用导线物理层要求GMW3176 ISO标准的导线规格命名要求GMW3191 接插件测试验证规范GMW3248 扎带规格标准GMW3251 通用紧固件规格标准GMW14124 汽车环境循环测试规范GMW14650 汽车外饰塑料件性能要求GMW14744 橡胶件材料规格标准GMW15267 机电式插头、印刷电路板、线圈式继电器通用规范GMW15608 热缩套管性能要求GMW15626 单芯ISO导线规范GMW15841 连接器及端子设计规范GMW15839 屏蔽及非屏蔽导线规格标准GMW15925 柔性扁平导线测试规范GMW15926 波纹管规格标准GMW16740 胶带规格标准GMW17136 热缩管设计标准3.要求3.1.开线区域3.1.1.开线要求3.1.1.1.尺寸和公差导线开线公差要求,见表1PATAC Confidential表1导线开线长度公差表3.1.1.2.设计标准1)电线原材料符合标准GMW 15626和GMW 15839;2)同轴电缆、水管、USB导线等特殊电线材料,需满足图纸要求;3)断线符合USCAR 21要求。
3.1.1.3.工艺要求,具体如下:1)铜丝不能外露;2)切割须平整;3)绝缘皮不能回缩;4)导线绝缘层完好。
艾тон Moeller 系列快速链接速度调节器 199050说明书

Eaton 199050Eaton Moeller® series Rapid Link - Speed controllers, 8.5 A, 4 kW, Sensor input 4, Actuator output 2, 230/277 V AC, PROFINET, HAN Q4/2, with manual override switch, with braking resistance, with fanGeneral specificationsEaton Moeller® series Rapid Link Speed controller1990504015081971084195 mm 270 mm 220 mm 3.82 kg UL 61800-5-1 UL approval IEC/EN 61800-5-1 RoHS CEProduct NameCatalog NumberEANProduct Length/Depth Product Height Product Width Product Weight Certifications Catalog Notes 3 fixed speeds and 1 potentiometer speedcan be switched over from U/f to (vector) speed control Connection of supply voltage via adapter cable on round or flexible busbar junction Diagnostics and reset on the device and via PROFINETInternal and on heat sink, temperature-controlled Fan Parameterization: KeypadParameterization: drivesConnect mobile (App) Parameterization: drivesConnectParameterization: FieldbusManual override switchBraking resistanceControl unitIGBT inverterTwo sensor inputs through M12 sockets (max. 150 mA) for quick stop and interlocked manual operationFanInternal DC linkPC connectionKey switch position AUTOSelector switch (Positions: REV - OFF - FWD)Breaking resistancePTC thermistor monitoringKey switch position HANDThermo-click with safe isolation2 Actuator outputsKey switch position OFF/RESET4-quadrant operation possible1 potentiometer speedFor actuation of motors with mechanical brake3 fixed speedsBrake chopper with braking resistance for dynamic braking NEMA 12IP651st and 2nd environments (according to EN 61800-3)IIISpeed controllerPROFINET IOC1: for conducted emissions onlyC2, C3: depending on the motor cable length, the connected load, and ambient conditions. External radio interference suppression filters (optional) may be necessary.2000 VPhase-earthed AC supply systems are not permitted.AC voltageCenter-point earthed star network (TN-S network)Vertical15 g, Mechanical, According to IEC/EN 60068-2-27, 11 ms, Half-sinusoidal shock 11 ms, 1000 shocks per shaftResistance: 6 Hz, Amplitude 0.15 mmResistance: 10 - 150 Hz, Oscillation frequencyResistance: 57 Hz, Amplitude transition frequency on accelerationResistance: According to IEC/EN 60068-2-6Features Fitted with:Functions Degree of protectionElectromagnetic compatibility Overvoltage categoryProduct categoryProtocolRadio interference classRated impulse withstand voltage (Uimp) System configuration typeMounting positionShock resistanceVibrationAbove 1000 m with 1 % performance reduction per 100 m Max. 2000 m-10 °C40 °C-40 °C70 °C< 95 %, no condensationIn accordance with IEC/EN 50178Adjustable, motor, main circuit0.8 - 8.5 A, motor, main circuit< 10 ms, Off-delay< 10 ms, On-delay98 % (η)7.8 A3.5 mA120 %Maximum of one time every 60 seconds 380 V480 V380 - 480 V (-10 %/+10 %, at 50/60 Hz)U/f controlBLDC motorsSynchronous reluctance motors Sensorless vector control (SLV)PM and LSPM motors0 Hz500 HzAt 40 °CFor 60 s every 600 s12.7 AAltitudeAmbient operating temperature - min Ambient operating temperature - max Ambient storage temperature - min Ambient storage temperature - max Climatic proofing Current limitationDelay timeEfficiencyInput current ILN at 150% overload Leakage current at ground IPE - max Mains current distortionMains switch-on frequencyMains voltage - minMains voltage - maxMains voltage toleranceOperating modeOutput frequency - minOutput frequency - maxOverload currentOverload current IL at 150% overload45 Hz66 Hz4 kW400 V AC, 3-phase 480 V AC, 3-phase 0.1 Hz (Frequency resolution, setpoint value)200 %, IH, max. starting current (High Overload), For 2 seconds every 20 seconds, Power section 50/60 Hz8 kHz, 4 - 32 kHz adjustable, fPWM, Power section, Main circuit Phase-earthed AC supply systems are not permitted. AC voltageCenter-point earthed star network (TN-S network)5 HP≤ 0.6 A (max. 6 A for 120 ms), Actuator for external motor brake Adjustable to 100 % (I/Ie), DC - Main circuit ≤ 30 % (I/Ie)230/277 V AC -15 % / +10 %, Actuator for external motor brake 765 VDC10 kAType 1 coordination via the power bus' feeder unit, Main circuit24 V DC (-15 %/+20 %, external via AS-Interface® plug) 230/277 V AC (external brake 50/60 Hz)PROFINET, optional Plug type: HAN Q4/2Specification: S-7.4 (AS-Interface®)Max. total power consumption from AS-Interface® power supply unit (30 V): 250 mANumber of slave addresses: 31 (AS-Interface®)Rated frequency - min Rated frequency - max Rated operational power at 380/400 V, 50 Hz, 3-phase Rated operational voltage ResolutionStarting current - maxSupply frequency Switching frequencySystem configuration typeAssigned motor power at 460/480 V, 60 Hz, 3-phase Braking currentBraking torqueBraking voltageSwitch-on threshold for the braking transistor Rated conditional short-circuit current (Iq)Short-circuit protection (external output circuits)Rated control voltage (Uc)Communication interface ConnectionInterfacesC2 ≤ 5 m, maximum motor cable length C1 ≤ 1 m, maximum motor cable length C3 ≤ 25 m, maximum motor cable length Meets the product standard's requirements.Meets the product standard's requirements.Meets the product standard's requirements.Meets the product standard's requirements.Meets the product standard's requirements.Does not apply, since the entire switchgear needs to be evaluated.Does not apply, since the entire switchgear needs to be evaluated.Meets the product standard's requirements.Does not apply, since the entire switchgear needs to be evaluated.Meets the product standard's requirements.Does not apply, since the entire switchgear needs to be evaluated.Does not apply, since the entire switchgear needs to be evaluated.Is the panel builder's responsibility.Is the panel builder's responsibility.Is the panel builder's responsibility.Is the panel builder's responsibility.Cable length10.2.2 Corrosion resistance10.2.3.1 Verification of thermal stability of enclosures10.2.3.2 Verification of resistance of insulating materials tonormal heat10.2.3.3 Resist. of insul. mat. to abnormal heat/fire by internalelect. effects10.2.4 Resistance to ultra-violet (UV) radiation10.2.5 Lifting10.2.6 Mechanical impact10.2.7 Inscriptions10.3 Degree of protection of assemblies10.4 Clearances and creepage distances10.5 Protection against electric shock10.6 Incorporation of switching devices and components10.7 Internal electrical circuits and connections10.8 Connections for external conductors10.9.2 Power-frequency electric strength10.9.3 Impulse withstand voltageIs the panel builder's responsibility.The panel builder is responsible for the temperature rise calculation. Eaton will provide heat dissipation data for the devices.Is the panel builder's responsibility. The specifications for the switchgear must be observed.Is the panel builder's responsibility. The specifications for the switchgear must be observed.The device meets the requirements, provided the information in the instruction leaflet (IL) is observed.Rapid Link 5 - brochureDA-SW-USB Driver PC Cable DX-CBL-PC-1M5DA-SW-drivesConnect - installation helpDA-SW-Driver DX-CBL-PC-3M0DA-SW-drivesConnect - InstallationshilfeDA-SW-drivesConnectDA-SW-USB Driver DX-COM-STICK3-KITMaterial handling applications - airports, warehouses and intra-logisticseaton-bus-adapter-rapidlink-speed-controller-dimensions-005.eps eaton-bus-adapter-rapidlink-speed-controller-dimensions-004.eps eaton-bus-adapter-rapidlink-speed-controller-dimensions-003.eps eaton-bus-adapter-rapidlink-speed-controller-dimensions-002.epsETN.RASP5-8422PNT-412R101S1.edzIL034093ZUramo5_v32.dwgrasp5_v32.stpGeneration Change RA-SP to RASP5Generation change RAMO4 to RAMO5Generation change from RA-MO to RAMO 4.0Configuration to Rockwell PLC for Rapid LinkGeneration Change RASP4 to RASP5Generation change from RA-SP to RASP 4.0DA-DC-00004508.pdfDA-DC-00003964.pdfDA-DC-00004514.pdfDA-DC-00004184.pdf10.9.4 Testing of enclosures made of insulating material10.10 Temperature rise10.11 Short-circuit rating10.12 Electromagnetic compatibility 10.13 Mechanical function BrochureDisegnieCAD modelIstruzioni di installazione mCAD modelNote per l'applicazione Report di certificazioneEaton Corporation plc Eaton House30 Pembroke Road Dublin 4, Ireland © 2023 Eaton. Tutti i diritti riservati. Eaton is a registered trademark.All other trademarks areproperty of their respectiveowners./socialmedia。
Agilent 53131A 132A 181A计数器说明书
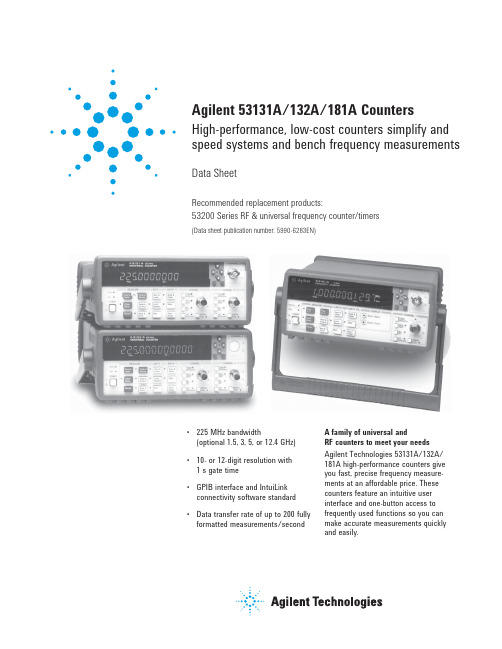
• 225 MHz bandwidth(optional 1.5, 3, 5, or 12.4 GHz)• 10- or 12-digit resolution with 1 s gate time • GPIB interface and IntuiLink connectivity software standard • Data transfer rate of up to 200 fully formatted measurements/secondAgilent 53131A/132A/181A CountersHigh-performance, low-cost counters simplify and speed systems and bench frequency measurementsData SheetRecommended replacement products:53200 Series RF & universal frequency counter/timers(Data sheet publication number: 5990-6283EN)A family of universal andRF counters to meet your needs Agilent Technologies 53131A/132A/181A high-performance counters give you fast, precise frequency measure-ments at an affordable price. These counters feature an intuitive user interface and one-button access to frequently used functions so you can make accurate measurements quickly and easily.Real-time digital signal processing technology is used to analyze data while simultaneously taking new read-ings, speeding measurement through-put. The technology, developed for Agilent’s high-end line of modulation domain analyzers, allows the counters to gather more data for each measure-ment, so you get higher-resolution measurements in a fraction of the time it takes other counters.The 53131A/132A/181A counters offer built-in statistics and math functions so you can scale measurements and simultaneously measure and track average, min/max and standard devia-tion. Automated limit testing lets you set upper and lower limits for any mea-surement. An analog display mode lets you see at a glance whether a mea-surement is within pass/fail limits. The counters flag out-of-limit conditions and can generate an output signal to trigger external devices when a limitis exceeded. For quick access to fre-quently used tests, a single keystroke recalls up to 20 different stored front-panel set-ups. For computer-controlled systemsapplications, each counter includesa standard GPIB interface with fullSCPI-compatible programmability anda data transfer rate of up to 200 fullyformatted measurements per second.The standard RS-232 talk-only interfaceprovides printer support or data trans-fer to a computer through a terminal-emulation program.Agilent 53131A universal counterThe two-channel 53131A counter offers10 digits per second of frequency/period resolution and a bandwidth of225 MHz. Time interval resolution isspecified at 500 ps. An optional thirdchannel provides frequency measure-ments up to 3 GHz, 5 GHz, or 12.4 GHz.Standard measurements include fre-quency, period, ratio, time interval,pulse width, rise/fall time, phaseangle, duty cycle, totalize, and peakvoltage.Agilent 53132A universal counterFor applications requiring higherresolution, the 53132A offers the samefeatures and functions as the 53131A,with up to 12 digits/sec frequency/period resolution and 150 ps timeinterval resolution. In addition, the53132A offers advanced arming modesfor time interval measurements.Agilent 53181A RF counterOptimized for RF applications, thesingle-channel 10 digit/s 53181Ameasures frequency, period and peakvoltage. A digit-blanking function letsyou easily eliminate unnecessary digitswhen you want to read measurementsquickly. For higher-frequency measure-ments, choose an optional secondchannel that provides measurementsup to 1.5 GHz, 3 GHz, 5 GHz, or 12.4 GHz.A self-guided shallow menu makes thiscounter exceptionally easy to use.Agilent IntuiLink provides easy access to the counter’s data from your PC The Agilent 53131A/132A/181A counters, capture precise frequencyand time measurements. IntuiLink software allows that data to be putto work easily. You work in a familiar environment at all times, using PC applications such as Microsoft Excel®or Word® to analyze, interpret, display, print, and document the data you get from the counter.It gives you the flexibility to configure and run tests from your PC making data gathering more convenient.Agilent IntuiLink lets you:• Configure tests, including measure-ment type, number of readings,measurement speed, and more.• Choose display modes from real-time strip chart, histogram, readout,and table mode.• Scale measurements data.• Copy captured data to otherprograms.Optional timebases offerincreased stabilityOptional timebases are availablefor 53131A/132A/181A counters toincrease measurement accuracy. Option010 provides a high stability oventimebase with aging of less than5 x 10-10 per day.1-year warrantyEach counter comes with operating,programming and service manuals,IntuiLink software, a power cord anda full 1-year warranty.Time BaseInternal time base stability (see graph 3 for timebase contribution of measurement error)Standard Medium oven High oven Ultra high oven(0° to 50°C) (Option 001) (Option 010) (Option 012 for 53132A only) Temperature stability (referenced to 25°C)< 5 x 10-6< 2 x 10-7< 2.5 x 10-9< 2.5 x 10-9Aging rate Per Day: < 4 x 10-8< 5 x 10-10< 1 x 10-10(after 30 days) Per Month: < 3 x 10-7 < 2 x 10-7< 1.5 x 10-8< 3 x 10-9Per Year: < 2 x 10-8Turn-on stability vs. time(in 30 minutes) < 2 x 10-7 < 5 x 10-9< 5 x 10-9referenced to 2 h referenced to 24 h referenced to 24 h Calibration Manual adjust Electronic Electronic ElectronicNote that power to the time base is maintained when the counter is placed in standby via the front panel switch. The internal fan will continue to operate when in standby to maintain long-term measurement reliability.Input specificationsChannel 1 & 2 (53131A, 53132A)1Channel 1 (53181A)Frequency rangedc coupled dc to 225 MHzac coupled 1 MHz to 225 MHz (50 Ω)30 Hz to 225 MHz (1 MΩ)FM tolerance 25%Voltage range and sensitivity (Sinusoid)2dc to 100 MHz 20 mVrms to ±5 V ac + dc 100 MHz 30 mVrms to ±5 V ac + dcto 200 MHz200 MHz 40 mVrms to ±5 V ac + dcto 225 MHz (all specified at 75 mVrmswith opt. rear connectors)3 Voltage range and sensitivity(Single-shot pulse)24.5 ns to 10 ns 100 mVpp to 10 Vpppulse width (150 mVpp with optionalrearconnectors)3>10 ns 50 mVpp to 10 Vpppulse width (100 mVpp with optionalrearconnectors)3Trigger level2Range ± 5.125 VAccuracy ± (15 mV + 1% of trigger level) Resolution 5mVDamage level50 Ω 5 Vrms0 to 3.5 kHz, 350 Vdc + ac pk1 MΩ3.5 kHz to 350 Vdc + ac pk linearly100 kHz, 1 MΩderated to 5 Vrms>100 kHz, 5 Vrms1 MΩ Input characteristicsChannel 1 & 2 (53131A, 53132A)1Channel 1 (53181A)Impedance 1 MΩ or 50 Ω1 MΩ 30 pFcapacitanceCoupling ac or dcLow-pass filter 100 kHz, switchable-20 dB at > 1 MHzInput Selectable between Low,sensitivity Medium,orHigh(default).Low is approximately 2xHighSensitivity.Trigger slope Positive or negativeAuto trigger levelRange 0 to 100% in 10% stepsFrequency > 100 HzInput amplitude> 100 mVpp(No amplitude modulation)AttenuatorVoltage range x10Trigger range x10Input Specifications4Channel 3 (53131A, 53132A)Channel 2 (53181A)Frequency rangeOption 015 100 MHz to 1.5 GHz(for 53181A (see Opt. 030 foronly) additionalspecs)Option 030 100 MHz to 3 GHzOption 050 200 MHz to 5 GHzOption 124 200 MHz to 12.4 GHzPower range and sensitivity (Sinusoid)Option 030 100 MHz to 2.7 GHz:-27 dBm to +19 dBm2.7 GHz to 3 GHz:-21 dBm to +13 dBmOption 050 200 MHz to 5 GHz:-23 dBm to +13 dBmOption 124 200 MHz to 12.4 GHz-23 dBm to +13 dBmDamage levelOption 030 5 VrmsOption 050 +25 dBmOption 124 +25 dBmCharacteristicsImpedance 50ΩCoupling ACVSWR <2.5:1External arm input specifications5Signal input rangeTTL compatibleTiming RestrictionsPulse width > 50 nsTransition time < 250 nsStart-to-stop time> 50 nsDamage level 10VrmsExternal arm input characteristics5Impedance 1kΩInput capacitance 17 pFStart/stop slope Positive or negativeExternal time base input specificationsVoltage range 200 mVrms to 10 VrmsDamage level 10 VrmsFrequency 1 MHz, 5 MHz, and 10 MHz(53132A 10 MHz only)Time base output specificationsOutput frequency 10 MHzVoltage > 1 Vpp into 50 Ω(centered around 0 V)1. Specifications and characteristics for Channels1 and2 are identical for both common andseparate configurations.2. Values shown are for X1 attenuator setting.Multiply all values by 10 (nominal) when usingthe X10 attenuator setting.3. When the 53131A or 53132A are ordered withthe optional rear terminals (Opt. 060), the channel1 and2 inputs are active on both front and rearof the counter. When the 53181A is ordered withthe optional rear terminal, the channel 1 input isactive on both front and rear of the counter. Forthis condition, specifications indicated for the rearconnections also apply to the front connections.4. When optional additional channels are orderedwith Opt. 060, refer to configuration table forOpt. 060 under ordering info on page 8. There isno degradation in specifications for this input,as applicable.5. Available for all measurements except peak volts.External arm is referred to as external gate forInstrument InputsFrequency (53131A, 53132A, 53181A) Channel 1 and 2 (53131A, 53132A)Channel 1 (53181A)Range 0.1 Hz to 225 MHzChannel 3 (53131A, 53132A)Channel 2 (53181A)Option 015 100 MHz to 1.5 GHz(53181 A only)Option 030 100 MHz to 3 GHzOption 050 200 MHz to 5 GHzOption 124 200 MHz to 12.4 GHz (Period 2 or 3 selectable via GPIB only)Period (53131A, 53132A, 53181A) Channel 1 and 2 (53131A, 53132A)Channel 1 (53181A)Range 4.44 ns to 10 sChannel 3 (53131A, 53132A)Channel 2 (53181A)Option 015 0.66 ns to 10 ns(53181A only)Option 030 0.33 ns to 10 nsOption 050 0.2 ns to 5 nsOption 124 80 ps to 5 nsFrequency ratio (53131A, 53132A, 53181A) Measurement is specified over the full signal range of each input.Results range 10-10 to 1011“Auto” gate time 100 msTime interval (53131A, 53132A) Measurement is specified over the full signal ranges6 of Channels 1 and 2.Results range -1 ns to 105 sLSD 500 ps (53131A)/150 ps(53132A)Phase (53131A, 53132A)Measurement is specified over thefull signal range of Channels 1 and 2.Results range -180° to +360°Duty cycle (53131A, 53132A)Measurement is specified over the fullsignal range of Channel 1. However, both thepositive and negative pulse widths must begreater than 4 ns.Results range 0 to 1 (e.g. 50% duty cyclewould be displayed as .5)Rise/fall time (53131A, 53132A)Measurement is specified over the full signalranges of Channel 1. The interval between theend of one edge and start of a similar edgemust be greater than 4 ns.Edge selection Positive or negativeTrigger D efault setting is auto triggerat 10% and 90%Results range 5 ns to 105 sLSD 500 ps (53131A)/150 ps(53132A)Pulse width (53131A, 53132A)Measurement is specified over the full signalrange of Channel 1. The width of the opposingpulse must be greater than 4 ns.Pulse selection Positive or negativeTrigger D efault setting is auto triggerat 50%Results range 5 ns to 105 sLSD 500 ps (53131A)/150 ps(53132A)Totalize (53131A, 53132A)Measurement is specified over thefull signal range of Channel 1.Results range 0 to 1015Resolution ± 1 countPeak volts (53131A, 53132A, 53181A)Measurement is specified on Channels 1 and 2for dc signals; or for ac signals of frequenciesbetween 100 Hz and 30 MHz with peak-to-peakamplitude greater than 100 mV.Results range -5.1 V to +5.1 VResolution 10mVPeak volts systematic uncertaintyfor ac signals: 25 mV + 10% of Vfor dc signals: 25 mV + 2% of VUse of the input attenuator multiplies allvoltage specifications (input range, resultsrange, resolution and systematic uncertainty)by a nominal factor of 10.Gate timeAuto mode, or 1 ms to 1000 sMeasurement throughputGPIB ASCII 200 measurements/s (maximum)Measurement armingStart Free run, manual, or externalmeasurementStop Continuous, single, external,measurement or timedTime interval 100 µs to 10 s (53131A)Delayed 100 ns to 10 s (53132A)armingArming modes(Note that not all arming modes are availablefor every measurement function.)5. Available for all measurements except peak volts.External arm is referred to as external gate for somemeasurements.6. See specifications for pulse width and rise/fall timemeasurements for additional restrictions on signaltiming characteristics.Measurement SpecificationsAuto arming: Measurements are initiated immediately and acquired as fast as possible, using a minimum number of signal edges. Timed arming: The duration of the measurement is internally timed to a user-specified value (also known as the “gate time”).Digits arming: Measurements are performedto the requested resolution (number of digits) through automatic selection of the acquisition time.External arming: An edge on the external arm Input enables the start of each measurement. Auto arming, timed arming modes or another edge on the external arm input may be used to complete the measurement.Time interval delayed arming: For time intervalmeasurements, the stop trigger condition isinhibited for a user-specified time following thestart trigger. The 53132A offers advanced timeinterval arming capabilities including use of userspecified time or Channel 2 events to delay bothstart and stop triggers.Measurement limitsLimit checking: The measurement value ischecked against user-specified limits at theend of each measurement.Display modes: The measurement result maybe displayed as either the traditional numericvalue or graphically as an asterisk movingbetween two vertical bars.Out-of-limits Indications:• The limits annunciator will light on the frontpanel display.• The instrument will generate an SRQ ifenabled via GPIB.• The limits hardware signal provided via theRS-232 connector will go low for the durationof the out-of-limit condition.• If the analog display mode is enabled, theasterisk appears outside the vertical bars,which define the upper and lower limits.Input signal frequency or timeGraph 6:Trigger level timing error(Level setting error andinput hysteresis)7. Graphs 1, 2, 4 and 5 do not reflect the effects oftrigger error. To place an upper bound on the added effect of this error term, determine the frequencyerror from the appropriate graph and add a trigger error term as follows:T r i g g e r e r r o r p e r t r i g g e r p o i n tAvailable statisticsM ean, Minimum, Maximum, Standard DeviationNumber of measurements 2 to 1,000,000. Statistics may be collected on all measurements or on only those which are between the limit bands. When the limits function is used in conjunction with statistics, N (number of measurements) refers to the number of in-limit measurements. In general, measurement resolution will improve in proportion to N,up to the numerical processing limits ofthe instrument.MeasurementsStatistics may be collected for all measurementsexcept peak volts and totalize.Measurement Statistics General Information1112Ordering Information/find/countersAgilent Email Updates/find/emailupdates Get the latest information on the products and applications you select.AdvancedTCA ® Extensions for Instrumentation and Test (AXIe) is an open standard that extends the AdvancedTCA for general purpose and semiconductor test. Agilent is a founding member of the AXIe consortium.LAN eXtensions for Instruments puts the power of Ethernet and the Web inside your test systems. Agilent is a founding member of the LXI consortium.PCI eXtensions for Instrumentation (PXI) modular instrumentation delivers a rugged, PC-based high-performance measurement and automation system.Agilent Channel Partners/find/channelpartners Get the best of both worlds: Agilent’s measurement expertise and product breadth, combined with channel partner convenience.For more information on AgilentTechnologies’ products, applications or services, please contact your local Agilent office. The complete list is available at:/find/contactus Americas Canada (877) 894 4414Brazil (11) 4197 3500Mexico01800 5064 800United States(800) 829 4444Asia Pacific Australia 1 800 629 485China 800 810 0189Hong Kong 800 938 693India 1 800 112 929Japan 0120 (421) 345Korea 080 769 0800Malaysia 1 800 888 848Singapore 180****8100Taiwan 0800 047 866Other AP Countries (65) 375 8100Europe & Middle East Belgium 32 (0) 2 404 93 40Denmark 45 70 13 15 15Finland 358 (0) 10 855 2100France 0825 010 700**0.125 €/minuteGermany 49 (0) 7031 464 6333Ireland 1890 924 204Israel 972-3-9288-504/544Italy 39 02 92 60 8484Netherlands 31 (0) 20 547 2111Spain 34 (91) 631 3300Sweden 0200-88 22 55United Kingdom 44 (0) 131 452 0200For other unlisted countries:/find/contactusRevised: June 8, 2011Product specifications and descriptions in this document subject to change without notice.© Agilent Technologies, Inc. 2006, 2011Published in USA, November 8, 20115967-6039ENAgilent Advantage Services is committed to your success throughout your equip-ment’s lifetime. To keep you competitive, we continually invest in tools andprocesses that speed up calibration and repair and reduce your cost of ownership. You can also use Infoline Web Services to manage equipment and services more effectively. By sharing our measurement and service expertise, we help you create the products that change our world./quality/find/advantageservices。
GMW16774翻译版

植绒附着力实验1适用范围注:本标准的任何取代适用的法律和法规。
注:如果英语和国内语言发生冲突,英语应优先处理。
1.1目的。
该程序通过测定植绒涂层与基材之间的结合强度来测定纤维涂层(植绒)的粘合性能。
方法A测定植绒胶带的粘附特性。
方法B用于静电植绒的特性测定。
方法C是用来确定静电植绒在较小的植绒后的地区,如成型角落的特点。
1.2引言。
不适用。
1.3适用范围。
本程序适用于所有植绒密封条。
2参考文献注:除非另有规定,只有最新批准的标准是适用的。
2.1外部标准/规范。
没有2.2通用标准/规范。
9981062 B 440 00293资源3.1设施。
不适用。
3.2设备。
3.2.1刮胡刀。
3.2.2弹簧秤可测量0 10 N3.2.3干净的白棉布。
3.2.4溶剂汽油、9981062或B 440 0029。
3.2.5湿度室。
3.2.6热熔胶枪。
3.2.7热熔胶,adchem no.7301-13或等效。
3.2.8热熔夹具/模具,创造一个流动通道75 mm x 5 mm x 5 mm的方法B.见附录,图A1。
3.2.9热熔夹具/模具夹紧装置,创建方法见附录一流道,人物A3和A4。
3.2.10力计、拉力试验机。
3.2.11夹/爪锯齿面。
3.2.12夹紧适合牢牢握住热熔胶使用方法C夹具(见附录,图A6)。
3.3试验车/试件。
测试样本应切割成品零件。
方法A,切割3个样品,大约150毫米×40毫米。
方法B,切6个样品,大约150毫米×40毫米。
方法C,切6个足够大小的样品(最小宽度为15毫米)。
3.4测试时间。
不适用。
3.5测试所需信息。
不适用。
3.6人事/技能。
不适用。
4 步骤4.1 准备。
见第4.3节中列出的方法。
4.2条件环境,除非另有规定,试验应是在23°C±5°C。
4.2.1环境条件,硫化橡胶的硫化和试验之间的最小时间间隔为72小时。
在测试之前,试件应在23 °C ± 5 °C的温度条件下保持至少8小时,在此期间应不受压力。
ADF4360-8资料

Integrated Synthesizer and VCOADF4360-8Rev. 0Information furnished by Analog Devices is believed to be accurate and reliable. However, no responsibility is assumed by Analog Devices for its use, nor for any infringements of patents or other rights of third parties that may result from its use. Specifications subject to change without notice. No license is granted by implication or otherwise under any patent or patent rights of Analog Devices. Trademarks and registered trademarks are the property of their respective owners.One Technology Way, P.O. Box 9106, Norwood, MA 02062-9106, U.S.A. Tel: 781.329.4700 Fax: 781.326.8703© 2004 Analog Devices, Inc. All rights reserved.FEATURESOutput frequency range: 65 MHz to 400 MHz 3.0 V to 3.6 V power supply 1.8 V logic compatibility Integer-N synthesizerProgrammable output power level 3-wire serial interface Digital lock detectHardware and software power-down modeAPPLICATIONSSystem clock generation Test equipment Wireless LANs CATV equipmentGENERAL DESCRIPTIONThe ADF4360-8 is an integrated integer-N synthesizer and voltage controlled oscillator (VCO). The ADF4360-8 center frequency is set by external inductors. This allows a frequency range of between 65 MHz to 400 MHz.Control of all the on-chip registers is through a simple 3-wire interface. The device operates with a power supply ranging from 3.0 V to 3.6 V and can be powered down when not in use.FUNCTIONAL BLOCK DIAGRAMCPV VCOREF INCLK DATALEAV DV CER V TUNE C C C NL2L1RF OUT ARF OUT BFigure 1.ADF4360-8Rev. 0 | Page 2 of 24TABLE OF CONTENTSSpecifications.....................................................................................3 Timing Characteristics.....................................................................5 Absolute Maximum Ratings............................................................6 Transistor Count...........................................................................6 ESD Caution..................................................................................6 Pin Configuration and Function Descriptions.............................7 Typical Performance Characteristics.............................................8 Circuit Description.........................................................................10 Reference Input Section.............................................................10 N Counter....................................................................................10 R Counter....................................................................................10 PFD and Charge Pump..............................................................10 MUXOUT and Lock Detect......................................................10 Input Shift Register.....................................................................11 VCO.............................................................................................11 Output Stage................................................................................12 Latch Structure...........................................................................13 Control Latch..............................................................................17 N Counter Latch.........................................................................18 R Counter Latch.........................................................................18 Choosing the Correct Inductance Value.................................19 Fixed Frequency LO...................................................................19 Power-Up.....................................................................................20 Interfacing...................................................................................20 PCB Design Guidelines for Chip Scale Package...........................20 Output Matching........................................................................21 Outline Dimensions.......................................................................22 Ordering Guide.. (22)REVISION HISTORY10/04—Revision 0: Initial VersionADF4360-8Rev. 0 | Page 3 of 24SPECIFICATIONS 1AV DD = DV DD = V VCO = 3.3 V ± 10%; AGND = DGND = 0 V; T A = T MIN to T MAX , unless otherwise noted. Table 1.Parameter B Version Unit Conditions/Comments REF IN CHARACTERISTICS REF IN Input Frequency 10/250 MHz min/max For f < 10 MHz, use a dc-coupled CMOS-compatiblesquare wave, slew rate > 21 V/µs.REF IN Input Sensitivity 0.7/AV DD V p-p min/max AC-coupled. 0 to AV DD V max CMOS-compatible. REF IN Input Capacitance 5.0 pF max REF IN Input Current ±60 µA max PHASE DETECTORPhase Detector Frequency 28 MHz max CHARGE PUMPI CP Sink/Source 3With R SET = 4.7 kΩ. High Value 2.5 mA typ Low Value 0.312 mA typ R SET Range 2.7/10 kΩ I CP Three-State Leakage Current 0.2 nA typ Sink and Source Current Matching 2 % typ 1.25 V ≤ V CP ≤ 2.5 V. I CP vs. V CP 1.5 % typ 1.25 V ≤ V CP ≤ 2.5 V. I CP vs. Temperature 2 % typ V CP = 2.0 V. LOGIC INPUTS V INH , Input High Voltage 1.5 V min V INL , Input Low Voltage 0.6 V max I INH /I INL , Input Current ±1 µA max C IN , Input Capacitance 3.0 pF max LOGIC OUTPUTS V OH , Output High Voltage DV DD – 0.4 V min CMOS output chosen. I OH , Output High Current 500 µA max V OL , Output Low Voltage 0.4 V max I OL = 500 µA. POWER SUPPLIES AV DD 3.0/3.6 V min/V max DV DD AV DD V VCO AV DD AI DD 4 5 mA typDI DD 4 2.5 mA typ I VCO 4, 5 12.0 mA typ I CORE = 5 mA.I RFOUT 43.5 to 11.0 mA typ RF output stage is programmable.Low Power Sleep Mode 47 µA typ Specifications continued on next page. Footnotes on next page.ADF4360-8Rev. 0 | Page 4 of 24Parameter B Version Unit Conditions/CommentsRF OUTPUT CHARACTERISTICS 5Maximum VCO Output Frequency 400 MHz I CORE = 5 mA. Depending on L. See theChoosing the Correct Inductance Value section.Minimum VCO Output Frequency 65 MHz VCO Output Frequency 88/108 MHz min/max L1, L2 = 270 nH. See the Choosing the Correct Inductance Valuesection for other frequency values.VCO Frequency Range 1.2 Ratio F MAX / F MIN VCO Sensitivity 2 MHz/V typ L1, L2 = 270 nH. See the Choosing the Correct Inductance Valuesection for other sensitivity values.Lock Time 6400 µs typ To within 10 Hz of final frequency. Frequency Pushing (Open Loop) 0.24 MHz/V typ Frequency Pulling (Open Loop) 10 Hz typ Into 2.00 VSWR load. Harmonic Content (Second) −16 dBc typHarmonic Content (Third) −21 dBc typOutput Power 5, 7−9/0 dBm typ Using tuned load, programmable in 3 dB steps. See Table 7. Output Power 5, 8 −14/−9 dBm typ Using 50 Ω resistors to V VCO , programmable in 3 dB steps. See Table 7. Output Power Variation ±3 dB typ VCO Tuning Range 1.25/2.5 V min/maxNOISE CHARACTERISTICS 5VCO Phase Noise Performance 9−120 dBc/Hz typ @ 100 kHz offset from carrier. −139 dBc/Hz typ @ 800 kHz offset from carrier. −140 dBc/Hz typ @ 3 MHz offset from carrier. −142 dBc/Hz typ @ 10 MHz offset from carrier.Synthesizer Phase Noise Floor 10−160 dBc/Hz typ @ 200 kHz PFD frequency. −150 dBc/Hz typ @ 1 MHz PFD frequency. −142 dBc/Hz typ @ 8 MHz PFD frequency.Phase Noise Figure of Merit 10−209 dBc/H z typ In-Band Phase Noise 11, 12 −102 dBc/Hz typ @ 1 kHz offset from carrier.RMS Integrated Phase Error 130.09 Degrees typ 100 Hz to 100 kHz.Spurious Signals due to PFDFrequency 12, 14−75 dBc typ Level of Unlocked Signal withMTLD Enabled−70 dBm typ1 Operating temperature range is –40°C to +85°C.2Guaranteed by design. Sample tested to ensure compliance. 3I CP is internally modified to maintain constant loop gain over the frequency range. 4T A = 25°C; AV DD = DV DD = V VCO = 3.3 V. 5Unless otherwise stated, these characteristics are guaranteed for VCO core power = 5 mA. L1, L2 = 270 nH, 470 Ω resistors to GND in parallel with L1, L2. 6Jumping from 88 MHz to 108 MHz. PFD frequency = 200 kHz; loop bandwidth = 10 kHz. 7For more detail on using tuned loads, see Output Matching section. 8Using 50 Ω resistors to V VCO , into a 50 Ω load. 9The noise of the VCO is measured in open-loop conditions. 10The synthesizer phase noise floor is estimated by measuring the in-band phase noise at the output of the VCO and subtracting 20 log N (where N is the N divider value). The phase noise figure of merit subtracts 10 log (PFD frequency). 11The phase noise is measured with the EVAL-ADF4360-xEB1 Evaluation Board and the HP 8562E Spectrum Analyzer. The Spectrum Analyzer provides the REFIN for the synthesizer; offset frequency = 1 kHz. 12f REFIN = 10 MHz; f PFD = 200 kHz; N = 1000; Loop B/W = 10 kHz. 13f REFIN = 10 MHz; f PFD = 1 MHz; N = 120; Loop B/W = 100 kHz. 14The spurious signals are measured with the EVAL-ADF4360-xEB1 Evaluation Board and the HP 8562E Spectrum Analyzer. The Spectrum Analyzer provides the REFIN for the synthesizer; f REFOUT = 10 MHz @ 0 dBm.ADF4360-8Rev. 0 | Page 5 of 24TIMING CHARACTERISTICSAV DD = DV DD = V VCO = 3.3 V ± 10%; AGND = DGND = 0 V; 1.8 V and 3 V logic levels used; T A = T MIN to T MAX , unless otherwise noted. Table 2.Parameter Limit at T MIN to T MAX (B Version) Unit Test Conditions/Comments t 1 20 ns min LE Setup Timet 2 10 ns min DATA to CLOCK Setup Time t 3 10 ns min DATA to CLOCK Hold Time t 4 25 ns min CLOCK High Duration t 5 25 ns min CLOCK Low Duration t 6 10 ns min CLOCK to LE Setup Time t 720ns minLE Pulse WidthCLOCKDATALELEFigure 2. Timing DiagramADF4360-8Rev. 0 | Page 6 of 24ABSOLUTE MAXIMUM RATINGST A = 25°C, unless otherwise noted. Table 3.Parameter RatingAV DD to GND 1 −0.3 V to +3.9 VAV DD to DV DD −0.3 V to +0.3 VV VCO to GND −0.3 V to +3.9 VV VCO to AV DD −0.3 V to +0.3 VDigital I/O Voltage to GND −0.3 V to V DD + 0.3 VAnalog I/O Voltage to GND −0.3 V to V DD + 0.3 VREF IN to GND −0.3 V to V DD + 0.3 V Operating Temperature Range −40°C to + 85°C Storage Temperature Range −65°C to +150°C Maximum Junction Temperature 150°C CSP θJA Thermal ImpedancePaddle Soldered 50°C/W Paddle Not Soldered 88°C/W Lead Temperature, SolderingVapor Phase (60 sec) 215°CInfrared (15 sec) 220°C1GND = AGND = DGND = 0 V.Stresses above those listed under Absolute Maximum Ratings may cause permanent damage to the device. This is a stress rating only; functional operation of the device at these or any other conditions above those listed in the operational sectionsof this specification is not implied. Exposure to absolute maxi-mum rating conditions for extended periods may affect device reliability.This device is a high performance RF integrated circuit with an ESD rating of <1 kV , and it is ESD sensitive. Proper precautions should be taken for handling and assembly.TRANSISTOR COUNT 12543 (CMOS) and 700 (Bipolar)ESD CAUTIONESD (electrostatic discharge) sensitive device. Electrostatic charges as high as 4000 V readily accumulate on thehuman body and test equipment and can discharge without detection. Although this product features proprie-tary ESD protection circuitry, permanent damage may occur on devices subjected to high energy electrostatic discharges. Therefore, proper ESD precautions are recommended to avoid performance degradation or loss of functionality.ADF4360-8Rev. 0 | Page 7 of 24PIN CONFIGURATION AND FUNCTION DESCRIPTIONSCPGND AV DD AGND RF OUT A RF OUT B V VCO DATA CLK REF IN DGND C N R SETV T U N E A G N D L 1L 2A G N D C C C PC EA G N DD V D DM U X O U TL E04763-003Figure 3. Pin ConfigurationADF4360-8Rev. 0 | Page 8 of 24TYPICAL PERFORMANCE CHARACTERISTICS–150–120–130–140–70–60–90–100–110–80–40–501001k10k 100k1M10MFREQUENCY OFFSET (Hz)O U T P U T P O W E R (d B )04763-004Figure 4. Open-Loop VCO Phase Noise, L1, L2 = 560 nH–150–125–130–120–135–140–145–85–80–95–100–105–110–115–90–70–751001k10k 100k1M 10MFREQUENCY OFFSET (Hz)O U T P U T P O W E R (d B )04763-005Figure 5. VCO Phase Noise, 65 MHz, 1 MHz PFD, 100 kHz Loop BandwidthO U T P U T P O W E R (d B )–90–80–70–60–50–40–30–20–100–2kHz–1kHz65MHz 1kHz 2kHzFigure 6. Close-In Phase Noise at 65 MHz (1 MHz Channel Spacing)O U T P U T P O W E R (d B )–90–80–70–60–50–40–30–20–100–1.1MHz–0.55MHz65MHz 0.55MHz 1.1MHzFigure 7. Reference Spurs at 65 MHz(1 MHz Channel Spacing, 100 kHz Loop Bandwidth)–150–120–130–140–70–60–90–100–110–80–40–501001k10k 100k1M10MFREQUENCY OFFSET (Hz)O U T P U T P O W E R (d B )04763-008Figure 8. Open-Loop VCO Phase Noise, L1, L2 = 110 nH–150–125–130–120–135–140–145–85–80–95–100–105–110–115–90–70–751001k10k 100k1M 10MFREQUENCY OFFSET (Hz)O U T P U T P O W E R (d B )04763-009Figure 9. VCO Phase Noise, 160 MHz, 1 MHz PFD, 100 kHz Loop BandwidthADF4360-8Rev. 0 | Page 9 of 24O U T P U T P O W E R (d B )–90–80–70–60–50–40–30–20–100Figure 10. Close-In Phase Noise at 160 MHz (1 MHz Channel Spacing)O U T P U T P O W E R (d B )–90–80–70–60–50–40–30–20–10–1.1MHz–0.55MHz160MHz0.55MHz1.1MHzFigure 11. Reference Spurs at 160 MHz(1 MHz Channel Spacing, 100 kHz Loop Bandwidth)–150–120–130–140–70–60–90–100–110–80–40–501001k10k 100k1M10MFREQUENCY OFFSET (Hz)O U T P U T P O W E R (d B )04763-012Figure 12. Open-Loop VCO Phase Noise, L1, L2 = 18 nH–150–125–130–120–135–140–145–85–80–95–100–105–110–115–90–70–751001k10k 100k1M 10MFREQUENCY OFFSET (Hz)O U T P U T P O W E R (dB )04763-013Figure 13. VCO Phase Noise, 400 MHz, 1 MHz PFD, 100 kHz Loop BandwidthO U T P U T P O W E R (d B )Figure 14. Close-In Phase Noise at 400 MHz (1 MHz Channel Spacing)O U T P U T P O W E R (d B )–90–80–70–60–50–40–30–20–100–1.1MHz–0.55MHz400MHz 0.55MHz 1.1MHzFigure 15. Reference Spurs at 400 MHz(1 MHz Channel Spacing, 100 kHz Loop Bandwidth)ADF4360-8Rev. 0 | Page 10 of 24CIRCUIT DESCRIPTIONREFERENCE INPUT SECTIONThe reference input stage is shown in Figure 16. SW1 and SW2 are normally closed switches. SW3 is normally open. When power-down is initiated, SW3 is closed, and SW1 and SW2 are opened. This ensures that there is no loading of the REF IN pin on power-down.04763-016POWER-DOWNFigure 16. Reference Input StageN COUNTERThe CMOS N counter allows a wide division ratio in the PLL feedback counter. The counters are specified to work when the VCO output is 400 MHz or less. To avoid confusion, this is referred to as the B counter. It makes it possible to generate output frequencies that are spaced only by the reference frequency divided by R . The VCO frequency equation isR f B f REFIN VCO /×=where:f VCO is the output frequency of the VCO. B is the preset divide ratio of the binary 13-bit counter (3 to 8191).f REFIN is the external reference frequency oscillator.R COUNTERThe 14-bit R counter allows the input reference frequency to be divided down to produce the reference clock to the phase frequency detector (PFD). Division ratios from 1 to 16,383 are allowed.PFD AND CHARGE PUMPThe PFD takes inputs from the R counter and N counter (N = BP + A ) and produces an output proportional to the phase and frequency difference between them. Figure 17 is a simplified schematic. The PFD includes a programmable delay element that controls the width of the antibacklash pulse. This pulse ensures that there is no dead zone in the PFD transfer function and minimizes phase noise and reference spurs. Two bits in the R counter latch, ABP2 and ABP1, control the width of the pulse (see Table 9).VFigure 17. PFD Simplified Schematic and Timing (In Lock)MUXOUT AND LOCK DETECTThe output multiplexer on the ADF4360 family allows the user to access various internal points on the chip. The state of MUXOUT is controlled by M3, M2, and M1 in the function latch. The full truth table is shown in Table 7. Figure 18 shows the MUXOUT section in block diagram form.R COUNTER OUTPUT N COUNTER OUTPUTDIGITAL LOCK DETECT DGNDMUXOUTDV 04763-018Figure 18. MUXOUT CircuitLock DetectThe correct band is chosen automatically by the band select logic at power-up or whenever the N counter latch is updated. It is important that the correct write sequence be followed at power-up. This sequence is MUXOUT can be programmed for one type of lock detect. Digital lock detect is active high. When LDP in the R counter latch is set to 0, digital lock detect is set high when the phase error on three consecutive phase detector cycles is less than 15 ns. 1. R counter latch With LDP set to 1, five consecutive cycles of less than 15 ns phase error are required to set the lock detect. It stays set high until a phase error of greater than 25 ns is detected on any subsequent PD cycle.2. Control latch3. N counter latchDuring band select, which takes five PFD cycles, the VCO V TUNE is disconnected from the output of the loop filter and connected to an internal reference voltage.INPUT SHIFT REGISTERThe ADF4360 family’s digital section includes a 24-bit input shift register, a 14-bit R counter, and an 18-bit N counter comprised of a 5-bit A counter and a 13-bit B counter. Data is clocked into the 24-bit shift register on each rising edge of CLK. The data is clocked in MSB first. Data is transferred from the shift register to one of four latches on the rising edge of LE. The destination latch is determined by the state of the two control bits (C2, C1) in the shift register. These are the two LSBs, DB1 and DB0, shown in Figure 2.01.00.52.52.01.53.53.080859010095105115110FREQUENCY (MHz)V T U N E (V )04763-019The truth table for these bits is shown in Table 5. Table 6 shows a summary of how the latches are programmed. Note that the test modes latch is used for factory testing and should not be programmed by the user. Table 5. C2 and C1 Truth TableFigure 19. Frequency vs. V TUNE , ADF4360-8, L1 and L2 = 270 nHControl BitsC2 C1 Data Latch 0 0 Control Latch 0 1 R Counter 1 0 N Counter (B) 11Test Modes LatchThe R counter output is used as the clock for the band select logic and should not exceed 1 MHz. A programmable divider is provided at the R counter input to allow division by 1, 2, 4, or 8 and is controlled by Bits BSC1 and BSC2 in the R counter latch. Where the required PFD frequency exceeds 1 MHz, the divide ratio should be set to allow enough time for correct band selection.VCOThe VCO core in the ADF4360 family uses eight overlapping bands, as shown in Figure 19, to allow a wide frequency range to be covered without a large VCO sensitivity (K V ) and resultant poor phase noise and spurious performance.After band selection, normal PLL action resumes. The value of K V is determined by the value of inductors used (see theChoosing the Correct Inductance Value section). The ADF4360 family contains linearization circuitry to minimize any variation of the product of I CP and K V .The operating current in the VCO core is programmable in four steps: 2.5 mA, 5 mA, 7.5 mA, and 10 mA. This is controlled by Bits PC1 and PC2 in the control latch.OUTPUT STAGEThe RF OUT A and RF OUT B pins of the ADF4360 family are connected to the collectors of an NPN differential pair driven by buffered outputs of the VCO, as shown in Figure 20. To allow the user to optimize the power dissipation versus the output power requirements, the tail current of the differential pair is programmable via Bits PL1 and PL2 in the control latch. Four current levels may be set: 3.5 mA, 5 mA, 7.5 mA, and 11 mA. These levels give output power levels of −9 dBm, −6 dBm,−3 dBm, and 0 dBm, respectively, using the correct shunt inductor to V DD and ac coupling into a 50 Ω load. Alternatively, both outputs can be combined in a 1 + 1:1 transformer or a 180° microstrip coupler (see the Output Matching section). If the outputs are used individually, the optimum output stage consists of a shunt inductor to V DD.Another feature of the ADF4360 family is that the supply current to the RF output stage is shut down until the part achieves lock as measured by the digital lock detect circuitry. This is enabled by the Mute-Till-Lock Detect (MTLD) bit in the control latch.RF OUT A RF OUT BFigure 20. Output Stage ADF4360-8LATCH STRUCTURETable 6 shows the three on-chip latches for the ADF4360 family. The two LSBs decide which latch is programmed. Table 6. Latch StructureCONTROL LATCHN COUNTER LATCHR COUNTER LATCHTable 7. Control LatchTable 8. N Counter LatchTable 9. R Counter LatchCONTROL LATCHWith (C2, C1) = (0,0), the control latch is programmed. Table 7 shows the input data format for programming the control latch. Power-DownDB21 (PD2) and DB20 (PD1) provide programmable power-down modes.In the programmed asynchronous power-down, the device powers down immediately after latching a 1 into Bit PD1,with the condition that PD2 has been loaded with a 0. In the programmed synchronous power-down, the device power-down is gated by the charge pump to prevent unwanted frequency jumps. Once the power-down is enabled by writing a 1 into Bit PD1 (on the condition that a 1 has also been loaded to PD2), the device goes into power-down on the second rising edge of the R counter output, after LE goes high. When the CE pin is low, the device is immediately disabled regardless of the state of PD1 or PD2.When a power-down is activated (either synchronous or asynchronous mode), the following events occur:•All active dc current paths are removed.•The R, N, and timeout counters are forced to their load state conditions.•The charge pump is forced into three-state mode.•The digital lock detect circuitry is reset.•The RF outputs are debiased to a high impedance state. •The reference input buffer circuitry is disabled.•The input register remains active and capable of loading and latching data. Charge Pump CurrentsCPI3, CPI2, and CPI1 in the ADF4360 family determine Current Setting 1.CPI6, CPI5, and CPI4 determine Current Setting 2. See the truth table in Table 7.Output Power LevelBits PL1 and PL2 set the output power level of the VCO. See the truth table in Table 7.Mute-Till-Lock DetectDB11 of the control latch in the ADF4360 family is the Mute-Till-Lock Detect bit. This function, when enabled, ensures that the RF outputs are not switched on until the PLL is locked.CP GainDB10 of the control latch in the ADF4360 family is the Charge Pump Gain bit. When it is programmed to 1, Current Setting 2 is used. When it is programmed to 0, Current Setting 1 is used. Charge Pump Three-StateThis bit puts the charge pump into three-state mode when programmed to a 1. It should be set to 0 for normal operation. Phase Detector PolarityThe PDP bit in the ADF4360 family sets the phase detector polarity. The positive setting enabled by programming a 1 is used when using the on-chip VCO with a passive loop filter or with an active noninverting filter. It can also be set to 0, which is required if an active inverting loop filter is used.MUXOUT ControlThe on-chip multiplexer is controlled by M3, M2, and M1. See the truth table in Table 7.Counter ResetDB4 is the counter reset bit for the ADF4360 family. When this is 1, the R counter and the A, B counters are reset. For normal operation, this bit should be 0.Core Power LevelPC1 and PC2 set the power level in the VCO core. The recom-mended setting is 5 mA. See the truth table in Table 7.N COUNTER LATCHTable 8shows the input data format for programming theN counter latch.Reserved BitsDB2 to DB7 are spare bits and have been designated as Reserved. They should be programmed to 0.B Counter LatchB13 to B1 program the B counter. The divide range is 3 (00.....0011) to 8191 (11....111).Overall Divide RangeThe overall VCO feedback divide range is defined by B.CP GainDB21 of the N counter latch in the ADF4360 family is the charge pump gain bit. When this is programmed to 1, Current Setting 2 is used. When programmed to 0, Current Setting 1 is used. This bit can also be programmed through DB10 of the control latch. The bit always reflects the latest value written to it, whether this is through the control latch or the N counter latch. R COUNTER LATCHWith (C2, C1) = (0, 1), the R counter latch is programmed. Table 9shows the input data format for programming theR counter latch.R CounterR1 to R14 set the counter divide ratio. The divide range is1 (00......001) to 16383 (111......111).Antibacklash Pulse WidthDB16 and DB17 set the antibacklash pulse width.Lock Detect PrecisionDB18 is the lock detect precision bit. This bit sets the number of reference cycles with less than 15 ns phase error for entering the locked state. With LDP at 1, five cycles are taken; with LDP at 0, three cycles are taken.Test Mode BitDB19 is the test mode bit (TMB) and should be set to 0. With TMB = 0, the contents of the test mode latch are ignored and normal operation occurs as determined by the contents of the control latch, R counter latch, and N counter latch. Note that test modes are for factory testing only and should not be programmed by the user.Band Select ClockThese bits set a divider for the band select logic clock input. The output of the R counter is by default the value used to clock the band select logic, but if this value is too high (>1 MHz), a divider can be switched on to divide the R counter output to a smaller value (see Table 9).Reserved BitsDB23 to DB22 are spare bits that have been designated as Reserved. They should be programmed to 0.CHOOSING THE CORRECT INDUCTANCE VALUEThe ADF4360-8 can be used at many different frequencies simply by choosing the external inductors to give the correct output frequency. Figure 21 shows a graph of both minimum and maximum frequency versus the external inductor value. The correct inductor should cover the maximum and minimum frequencies desired. The inductors used are 0603 CS or 0805 CS type from Coilcraft. To reduce mutual coupling, the inductors should be placed at right angles to one another.The lowest center frequency of oscillation possible is approxi-mately 65 MHz, which is achieved using 560 nH inductors. This relationship can be expressed by()EXT O L F +=nH 0.9pF 9.32π10150501003502503002004504000100200300400600500INDUCTANCE (nH)F R E Q U E N C Y (M H z )04763-025Figure 21. Output Center Frequency vs. External Inductor ValueWhere F O is the center frequency and L EXT is the external induc-tance. The approximate value of capacitance at the midpoint of the center band of the VCO is 9.3 pF, and the approximate value of internal inductance due to the bond wires is 0.9 nH. The VCO sensitivity is a measure of the frequency change versus the tuning voltage. It is a very important parameter for the low-pass filter. Figure 22 shows a graph of the tuning sensitivity (in MHz/V) versus the inductance (nH). It can be seen that as the inductance increases, the sensitivity decreases. This relationship can be derived from the equation above, i.e., since the induc-tance has increased, the change in capacitance from the varactor has less of an effect on the frequency.421086120100200300400600500INDUCTANCE (nH)S E N S I T I V I T Y (M H z /V)04763-026Figure 22. Tuning Sensitivity (in MHz/V) vs. Inductance (nH)FIXED FREQUENCY LOFigure 23 shows the ADF4360-8 used as a fixed frequency LO at 200 MHz. The low-pass filter was designed using ADIsimPLL for a channel spacing of 2 MHz and an open-loop bandwidth of 100 kHz. The maximum PFD frequency of the ADF4360-8 is 8 MHz. Since using a larger PFD frequency allows the use of a smaller N, the in-band phase noise is reduced to as low as possible, −109 dBc/Hz. The typical rms phase noise (100 Hz to 100 kHz) of the LO in this configuration is 0.09°. The reference frequency is from a 16MHz TCXO from Fox; thus, an R value of 2 is programmed. Taking into account the high PFD frequency and its effect on the band select logic, the band select clock divider is enabled. In this case, a value of 8 is chosen. A verysimple shunt inductor and dc blocking capacitor complete the RF output stage.LOCKFigure 23. Fixed Frequency LO。
IXYS CORPORATION H82N120C3 高速 IGBT 数据手册说明书
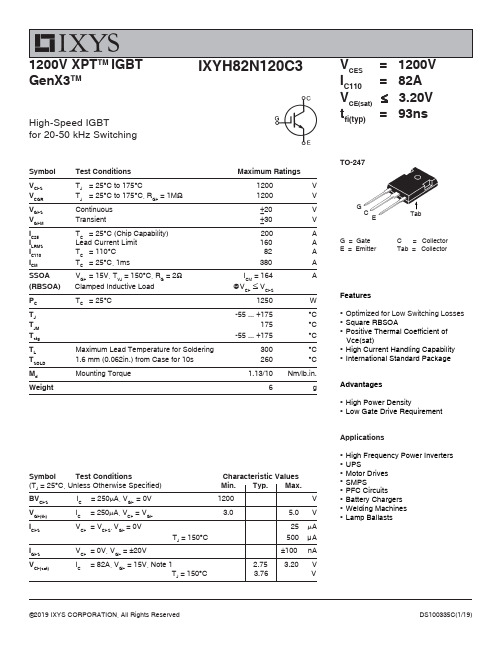
CES I C110= 82A V CE(sat) ≤ 3.20V t fi(typ)= 93nsG = Gate C = Collector E = Emitter Tab = CollectorTO-247High-Speed IGBTfor 20-50 kHz SwitchingFeatures●Optimized for Low Switching Losses ●Square RBSOA ●Positive Thermal Coefficient of Vce(sat)●High Current Handling Capability ●International Standard PackageAdvantages●High Power Density●Low Gate Drive RequirementApplications●High Frequency Power Inverters ●UPS●Motor Drives ●SMPS●PFC Circuits ●Battery Chargers ●Welding Machines ●Lamp BallastsSymbol Test Conditions Characteristic Values (T J = 25︒C, Unless Otherwise Specified) Min. Typ. Max.BV CES I C = 250μA, V GE = 0V 1200 V V GE(th)I C= 250μA, V CE = V GE3.05.0VI CES V CE = V CES , V GE = 0V25μA T J = 150︒C 500 μA I GES V CE = 0V, V GE = ±20V±100 nAV CE(sat)I C = 82A, V GE = 15V, Note 12.753.20 V T J = 150︒C3.76 VSymbol Test ConditionsMaximum Ratings V CES T J = 25°C to 175°C1200V V CGR T J = 25°C to 175°C, R GE = 1M Ω 1200V V GES Continuous ±20V V GEM Transient±30VI C25T C = 25°C (Chip Capability) 200A I LRMS Lead Current Limit 160 A I C110T C = 110°C 82A I CMT C = 25°C, 1ms 380ASSOA V GE = 15V, T VJ = 150°C, R G = 2Ω I CM = 164A (RBSOA) Clamped Inductive Load @V CE ≤ V CES P C T C = 25°C1250W T J -55 ... +175°CT JM 175°C T stg -55 ... +175°CT LMaximum Lead Temperature for Soldering 300°CT SOLD 1.6 mm (0.062in.) from Case for 10s 260 °C M d Mounting Torque 1.13/10Nm/lb.in.Weight6g1200V XPT TM IGBT GenX3TMIXYS Reserves the Right to Change Limits, Test Conditions, and Dimensions.Notes:1. Pulse test, t ≤ 300μs, duty cycle, d ≤ 2%.2. Switching times & energy losses may increase for higher V CE (clamp), T J or R G .Symbol Test Conditions (T J = 25°C Unless Otherwise Specified)fs I C = 60A, V CE = 10V, Note 1 30 50C ie sC oes V CE = 25V, V GE C resQ g(on)Q ge I C = 82A, V GE = 15V, V Q gc d(on)Fig. 1. Output Characteristics @ T 6080100120140160I C - A m p e r e sIXYS Reserves the Right to Change Limits, Test Conditions, and Dimensions.Fig. 7. Transconductance304050607080g f s - S i e m e n sFig. 12. Inductive Switching Energy Loss vs.Gate Resistance345678E o f f - M i l l i J o u l e sE off E on T J = 125oC , V GE = 15V V CE = 600VIXYS Reserves the Right to Change Limits, Test Conditions, and Dimensions.Fig. 18. Inductive Turn-on Switching Times vs.Gate Resistance6080100120140160 r i - N a n o s e c o n d st r i t d(on)T J = 125oC, V GE = 15V V CE = 600VI C = 80ATO-247 (IXYH) Outline1 - Gate2,4 - Collector3 -EmitterDisclaimer Notice - Information furnished is believed to be accurate and reliable. However, users should independently evaluate the suitability of and test each product selected for their own applications. Littelfuse products are not designed for, and may not be used in, all applications. Read complete Disclaimer Notice at /disclaimer-electronics. IXYS Reserves the Right to Change Limits, Test Conditions, and Dimensions.。
汽车线束加工-通用技术要求

PA TAC General SpecificationPES10012PATAC ConfidentialSeptember 2014 Page 1 of 29 汽车电线束技术汽车电线束技术要求要求1. 范围本标准规定了用于泛亚汽车技术中心有限公司(以下称PATAC )开发的低压线束制造工艺过程技术要求。
按线束的生产流程分,该标准主要分为三部分,分别为开线、预装和总装。
2. 术语和定义下列文件对于本标准的应用是必不可少的。
凡是注日期的引用文件,仅注日期的版本适用于本标准。
凡是不注日期的引用文件,其最新版本(包括所有的修改单)适用于本标准。
ISO 8820 保险丝设计规范USCAR 21 美国汽车研究委员会 标准21 USCAR 38 美国汽车研究委员会 标准38 QC/T29106-2014 汽车低压电线束技术条件 GME 15339 电气功能通用规格标准GMW3172 电子电气部件环境和耐久通用规范GMW3173 ISO 导线截面及汽车通讯用导线物理层要求 GMW3176 ISO 标准的导线规格命名要求 GMW3191 接插件测试验证规范 GMW3248 扎带规格标准GMW3251 通用紧固件规格标准 GMW14124 汽车环境循环测试规范 GMW14650 汽车外饰塑料件性能要求 GMW14744 橡胶件材料规格标准GMW15267 机电式插头、印刷电路板、线圈式继电器通用规范 GMW15608 热缩套管性能要求 GMW15626 单芯ISO 导线规范GMW15841 连接器及端子设计规范 GMW15839 屏蔽及非屏蔽导线规格标准 GMW15925 柔性扁平导线测试规范 GMW15926 波纹管规格标准 GMW16740 胶带规格标准 GMW17136 热缩管设计标准3. 要求3.1. 开线区域 3.1.1. 开线要求3.1.1.1.尺寸和公差导线开线公差要求,见表1表1导线开线长度公差表电线长度mm 公差mm0 – 500 ±3501-1 000 ±51 001-2 500 ±8>2 500 ±103.1.1.2.设计标准1)电线原材料符合标准GMW 15626和GMW 15839;2)同轴电缆、水管、USB导线等特殊电线材料,需满足图纸要求;3)断线符合USCAR 21要求。
NorthStar Rim Tach 6200 Digital Tachometer 使用说明书

NorthStar T M brandInstruction ManualRim Tach® 6200Digital TachometerDesigned for use in4.5” 56C-Face, Coupled, Foot Mounted,or Pulley Driven ApplicationsCustomer Service: Tel.: +1.800.873.8731 Fax: +1.847.662.4150 custserv@ Technical SupportTel.: +1.800.234.8731Fax: +1.847.782.5277northstar.techsupport@d Website: *791-1003-00*Table of ContentsChapter/Paragraph/Illustration Page 1 Introduction (4)Safety Summary (4)1.0General (5)1.11.2 Description (5)Figure 1: 6200 Dimensional Drawing (5)Safety Summary (6)1.32 Installation (7)2.0 Inspection and Unpacking (7)Figure 2: 6200 Spare Parts (7)2.1 Painting Considerations (8)2.2 56 C-Face Bracket Mounting (8)Figure 3: Model 6200 56 C Bracket Mounting (8)2.3 Foot Mounting (9)Figure 4: Model 6200 Foot Mounting (9)2.4 Pulley Mounting (10)Figure 5: Model 5200 Pulley Mounting (10)2.5 Sensor Module Installation (11)Figure 6: Sensor Module Installation (11)Figure 7: Sensor Module Installation (Continued (12)Electrical Installation (13)2.62.6.1 Quick Release Connector Hood Wiring (13)Figure 8: Quick Release Connector Installation (14)Methods and apparatus disclosed and described herein have been developed solely on company funds of Dynapar No government or other contractualsupport or relationship whatsoever has existed which in any way affects or mitigates proprietary rights of Dynapar in these developments. Methods andapparatus disclosed herein may be subject to U.S. Patents existing or applied for. Dynapar reserves the right to add, improve, modify, or withdraw functions,design modifications, or products at any time without notice. Dynapar shall not be liable for errors contained herein or for incidental or consequentialdamages in connection with furnishing, performance, or use of this material.CHAPTER 1INTRODUCTION1.0 Safety SummaryHigh current, voltage, and rotating parts can cause serious or fatal injury. The use of electric machinery, like all other uses of concentrated power and rotating equipment, may be hazardous. Only qualified personnel should install, operate, and maintain electric machinery in accordance with applicable provisions of the National Electrical Code and sound local practices. Failure to comply with these precautions or with specific warnings elsewhere in this manual violates safety standards of design, manufacture, and intended use of the instrument. Dynapar assumes no liability for the customer's failure to comply with these requirements.Rotating MachineryAvoid contact with rotating parts. Avoid by-passing or rendering inoperative any safety guards or protection devices. Avoid extended exposure in close proximity to machinery with high noise levels. Use proper care and procedures in handling, lifting, installing, operating and maintaining the equipment.Before InstallationSafe maintenance practice with qualified personnel is imperative. Before starting maintenance procedures, be positive that, (1) equipment connected to the shaft will not cause mechanical rotation, (2) main machine windings have been disconnected and secured from all electrical power sources, and (3) all accessory devices associates with the work area have been de-energized. If high potential insulation test is required, follow procedures and precautions outlined in NEMA standards MG-1. GroundingImproperly grounding the frame of the machine can cause serious or fatal injury to personnel. Grounding of the machine frame and structure should comply with the National Electrical Code and with sound local practices. Check wiring diagram before connecting power.Do Not Operate In An Explosive AtmosphereDo not operate the instrument in the presence of flammable gases or fumes. Operating any electrical instrument in such an environment constitutes a definite safety hazard.Keep Away From Live CircuitsOperating personnel must not remove instrument covers. Qualified maintenance personnel must make component replacement and internal adjustments. Do not replace components with power cable connected. To avoid injuries, always disconnect power and discharge circuits before touching them.Do Not Substitute Parts Or Modify InstrumentDo not install substitute parts or perform any unauthorized modification to the instrument. Introducing additional hazards is dangerous. Return the instrument to an authorized Dynapar representative for service and repair to ensure that safety features are maintained.Dangerous Procedure CautionsA CAUTION heading precedes potentially dangerous procedures throughout this manual. Instructions in the warnings must be followed.1.1 GeneralThese instructions do not claim to cover all details of variation in equipment or to provide for every possible contingency or hazard met in connection with installation, operation, and service. If further information is desired or should particular problems arise which are not covered sufficiently for the purchaser’s purposes, please contact Dynapar, or one of its designated representatives.1.2 DescriptionThe RIM Tach® 6200 is a high performance and reliable Digital Tachometer, designed to provide position and velocity feedback from both AC and DC electric motors with pulse counts ranging from 60 through 2048 pulses per revolution. The RIM Tach6200 utilizes rugged ductile iron casting construction and provides interchangeable sensor modules and a magneto-resistive technology capable of withstanding the harshest industrial environments. This ensures precise and consistent digital motor speed feedback.The NorthStar RIM Tach® 6200 is mounted in a variety of ways and utilizes a patented, heavy-duty, one piece, magneto-resistance sensor module with encapsulated surface mount electronics. The encapsulation provides resistance to water, oil mist, dirt, high temperatures, and other harsh environments. The sensor module includes a 10-pin quick connector requiring only a screwdriver for final electrical installation. The non-contact magneto-resistive sensor and rugged magnetized pulse wheel are designed and machined to function properly without any adjustments. The RIM Tach 6200 provides precise, reliable speed signals for many monitoring and control applications, and is a standard feedback device for AC and DC variable speed drives. The unit is bi-directional providing square wave outputs.Figure 1: 6200 Dimensional Drawing1.3 SpecificationsElectrical SpecificationsFrequency Response 0 - 120 kHzPulse Code A, B, Z (Index), and complements (A, B, Z)Output Phases A phase, B phase @ quadrature 90°, Z phase: Once per rev. (gated) Pulse Duty Cycle 50 ± 15% (within defined mechanical specifications) Quadrature Accuracy 90 ± 22° (within defined mechanical specifications)Output Type High speed, differential line driverRise and Fall Time Less than 1µs @ 10,000 pf typical loadCurrent Consumption 45 mA typical plus line driver loadOutput Current 150 mA maximum continuousESD Protection 2kVMechanical SpecificationsEnclosure Configurations 4.5-inch diameter, 56 C motor face or accessory flange to meetNEMA MG1-4 standards; foot mount with 4 slotted bolt holes Material Ductile iron cast enclosure, stainless steel probe moduleShaft Interfacing 0.625 inch diameter x 1.87 inch long, 3/16” square-parallel key,optional double ended shaft, optional 14 mm shaft with metric key Maximum Operational Speed 7,000 RPM (120khz)Axial, Radial Load 15 lbf axial, 50 lbf radialSlew Rate 3600 RPM/secondApproximate Box Weight 28lbs.Box Dimensions 21” x 10” x 10”Environmental SpecificationsOperational Temperature -40° to +80° COperational Humidity Range Maximum of 90%Chemical Resistance Salt spray, most solvents, mild acids and basesVibration Minimum 18 g’s RMS, 5-2000 Hz shock spectrumShock (Sensor Module) 1 meter drop tested, min. 30g’sInterface SpecificationsPower +5.0 to +15.0 VDCOutput Differential output swinging between Vcc - 0.6V and ground Connector 10 pin industrial latching connector with ½ inch NPT fitting,IP-65 NEMA 4, 12 ratedSuggested Cable 22 - 16 AWG, 10 conductor, shielded, twisted pairSpecifications subject to change without notice.CHAPTER 2INSTALLATION2.0 Inspection and UnpackingInspect shipping container for external damage. All claims for damage (apparent or concealed) or partial loss of shipment must be made in writing to Dynapar within (5) days from receipt of goods. If damage or loss is apparent, please notify the shipping agent immediately.Open shipping container and locate the packing list. The packing list is included to verify that all components, accessories, and manual were received. Please use the packing list to check off each item as the unit is unpacked. Inspect for damage. We recommend that the shipping container be retained for future shipping, storage, or return to factory purposes.If any equipment was damaged in transit, be sure to file proper claims promptly with the carrier and insurance company. Please advise us of such filing. In case of part shortages, advise us immediately. Dynapar cannot be responsible for any missing parts unless notified within 60 days of shipment.The RIM Tach® 6200 utilizes a modular construction that permits the user to configure the unit as a one or two signal output tachometer. Sensor modules are universal and interchangeable. If one output requires replacement, simply remove four screws, and replace with a new sensor module. No electrical adjustment or alignment is required. After unpacking the unit and verifying receipt of the items listed in the packing list, you may proceed with mechanical installation.The Model 6200 has no user maintainable components. The bearings are permanently lubricated and sealed for the operational life of the unit. The Pulse Wheel also needs no service. Disassembly of the unit will void the Warranty. The magnetoresistive sensor end electronics modules need no adjustment, but can be replaced by the user in case of failure.Figure 2: 6200 Spare Parts2.1 Painting ConsiderationsThe enclosure may be painted. Please pay attention to the following considerations.NOTECorrosion preventative coating has been applied to the enclosure. Standard degreasingpractices must be followed before applying paint.•Do not hinder the latches on the connector if the connector is painted.•If the enclosure is painted before the sensor module(s) is added, be sure to mask off the area where the sensor module(s) will be placed. The module must mate directly to the enclosure with nothing between. Failure to do this will degrade the alignment of the system and may cause it to fail.•Ensure excess paint runoff does not clog enclosure drain holes.2.2 56 C-Face / Bracket MountingFlexible couplings are generally used to couple the Model 6200 to its driver (NorthStar part number RIMFLEX-5858). There are a wide variety of speeds, loads, environment, and alignment conditions found in various applications. If there is doubt to suitability, we recommend you consult the flexible coupling manufacturer on your particular application requirement. One simple design of coupling can not fulfill all potential applications or conditions.1.Mount the C-Face adapter bracket (not supplied) onto the motor per manufacture’s instructions. See Figure 3. Be surethe 4.5 inch C-Face is concentric to the motor shaft.2.Insert flexible coupling onto the motor shaft. Do not tighten at this time.3.Place the Model 6200 onto the4.5 inch C-Face. Insert and tighten four 3/8-16 UNC bolts. Be sure it is seated flat againstthe mounting bracket.4.Connect flexible coupling onto the Model 6200 shaft and tighten per manufacturer’s specifications.5.Rotate the shaft by hand to ensure free rotation.6.Place or replace appropriate safety shields.Figure 3: Model 6200 56 C Face/ Bracket Mounting2.3 Foot MountingFoot mounting brackets are included on the bottom of the Model 6200. The bolt hole pattern in slotted to permit a measure of adjustment. Flexible couplings are generally used to couple the Model 6200 to its driver (NorthStar part number RIMFLEX-5858). There are a wide variety of speeds, loads, environment, and alignment conditions found in various applications. If there is doubt to suitability, we recommend you consult the flexible coupling manufacturer on your particular application requirement. A simple coupling design can not fulfill all potential applications or conditions.1.Place the Model 6200 mounting bracket in the approximate final position.NOTEThe mounting should be strong enough to sufficiently support the weight of the Model6200 ( approximately 25 pounds) without excessive deflection due to load orvibration. Deflection can cause erroneous outputs and shorten the operational life ofthe unit.2. Insert, but do not tighten, four 3/8-16 UNC bolts into the mounting bracket holes.3. Insert and connect flexible coupling onto the motor and Model 6200 shaft per manufacture’s specifications.NOTEThe life expectancy of the flexible coupling and Model 6200 are influenced by theaccuracy to which the shafts are aligned in this step.4. Tighten mounting bolts to nominal 30 foot-pounds.5. Rotate shaft by hand to ensure free rotation.6. Place or replace appropriate shields.Figure 4: Model 6200 Foot Mounting2.4 Pulley Mounting1. Mounting the Model 6200 onto mounting bracket with four 3/8-16 UNC bolts through foot mounting bracket holes.NOTEThe mounting bracket should be strong enough to sufficiently support the weight of the Model 6200 (approximately 25 pounds) without excessive deflection of play due to load or excessive vibration. Deflection can cause erroneous outputs and shorten operational life of the unit.2. Mount and connect 5/8 inch I.D. pulley on to the Model 6200 input shaft.3. Install a tension belt according to the manufacturer’s specifications. If the belt tension is too light it can cause pulleyslippage or backlash, thereby creating an erroneous signal output. However, for maximum operational life of the Model 6200, a belt tension loading of less than 40 pounds should be used.Model6200Figure 5: Model 6200 Pulley Mounting2.5 Sensor Module InstallationTo install the sensor Module, perform the following steps. See Figure 6.1. Remove sensor module and mating connector from packaging.CAUTION!Although the device is protected from Electrostatic Discharges up to 2000 Volts, standard ESDprecautions should be followed.2. Separate mating connector from sensor module by releasing the two latches.CAUTION!Use caution when handling the sensor module. The sensor at the end of the module can be easilydamaged by sharp objects. The sensor module can be damaged by sudden shocks (dropping,hammer blows, etc.).3. Insert sensor module into opening in enclosure. The sensor assembly is keyed to ensure proper.4. Locate four shoulder screws. Insert shoulder screws through clearance holes in sensor module and into tapped holes inenclosure. Tighten to a nominal 5 inch-pounds.CAUTION!There should not be a gap between the lip on the housing and the enclosure. The stainless steelsensor module is designed to seat in metal to metal contact with the enclosure. Ensure that nogaskets, paint, dirt, etc., interferes with the complete seating of the module in the enclosure.Figure 6: SensorModule InstallationSensor Must Mate Directlyto Enclosure Surface Figure 7: Sensor Module Installation (Continued)2.6 Electrical InstallationElectrical connections are made to the sensor module through a standard 1/2 inch NPT liquid tight flexible conduit. The nipple length may be changed to extend the outlet box if desired. Interconnection cable recommendations are as follows: stranded copper, 22 through 16 gage, braided or foil with drain wire shielding 0.05 µF maximum total mutual or direct capacitance, outer sheath insulated. Shrink tubing may be placed over any wires without insulation. For lengths over 100 feet, use 18 gage or larger, to a maximum of 1000 feet. If shielded twisted pair wire is used, do not cross channels. Keep each pair of complementary channel outputs together in a single twisted pair (e.g., A and A complement).CAUTION!Reversing power and common will not damage the unit. However, applying power toany of the sensor outputs may cause damage.Table 1. Signal Coding TableSignal Connector Pin Pigtail Cable MS 3102E18-IT#CommonBAZ *No Connection Vcc (5-15 VDC) /B/A/Z *Shield12345678910BlackGreenBlueViolet-----RedYellowGrayOrangeBraidAEDC-----BHGIJ* Applies only to units with index pulse capability.# Pinouts are for the sensors with the MS 3102E18IT connectorNOTEThe shield in the sensor module is isolated from the frame of the encoder for maximumnoise immunity. The shield wire or pin should be connected to the shield of the cable andthat of the drive or other receiving device.2.7 Quick Release Connector Hood WiringTo install the Quick Release Connector, perform the following steps.1.Remove the four screws from the mating connector housing that hold the terminal block in place. Remove terminalblock from housing.2.Insert wiring through liquid tight flexible seal and mating connector housing. Leave enough wire exposed tocomfortably reach the terminal block. Wire to terminal block according to wire code in Table 1. A similar wiring list is attached to enclosure.NOTEThere are two orientations of the connector hood. The terminal block can be insertedeither way so the connector hood points up or down. Choose the direction best for yourapplication.4. Tighten Liquid Tight fitting on housing. OPTIONAL: In some hostile environments, seal between connector body andSensor Module can be improved by smearing a sealant (silicone grease, etc.) on the neoprene seal of the connector. 5. Mate connector into place on sensor mount and snap the two latches into place. If only one sensor is being installed, ensure cover plate is installed over other sensor hole.Terminal BlockFigure 8: Quick Release Connector InstallationCustomer Service: Tel.: +1.800.873.8731 Fax: +1.847.662.4150 custserv@d Technical SupportTel.: +1.800.234.8731Fax: +1.847.782.5277northstar.techsupport@d Website: 。
3M Interam Mat Mount 1670HT技术数据表说明书

January 20213M™ Interam™ Mat Mount 1670HTTechnical Data SheetProduct Description3M™ Interam™ Mat Mount 1670HT is a non-intumescent,high temperature, needled polycrystalline fiber mat withlow organic binder. Interam Mat Mount 1670HT is a high-performance solution that can be used in a wide range ofgap designs, temperature conditions and applications. It isdesigned for easy canning performance.Features•Surface coating for lower push-in forces•Wide range of operating temperatures (ambient to 1100°C)•Single layer mat solution for small to large gap designs•Excellent fiber resiliency for substrate retention•Excellent erosion resistance•Moderate peak compression force•Low thermal conductivity•Low organic content (approx. 2%)•Color coating on mat monolith interface surface enables easy visual control during assemblyApplications:•Ultra-thin wall monoliths•Close coupled or manifold mounted converters•System with bigger gap (e.g. 6mm as frequently desired today)•Light-duty and commercial vehicle applications, including gasoline and diesel particulate filtersPreliminary Technical Data Sheet 3M™ Interam™ Mat Mount 1670HTRegulatory InformationPlease refer to the product label and Safety Data Sheet (SDS) for health and safety information before using.Contact InformationThe information provided in this technical document is intended as a guide for these products. For more information or help in selecting a 3M product for an application, please contact your 3M technical service representative or call 1-800-328-1684.Technical Information: The technical information, guidance, and other statements contained in this document or otherwise provided by 3M are based upon records, tests, or experience that 3M believes to be reliable, but the accuracy, completeness, and representative nature of suchinformation is not guaranteed. Such information is intended for people with knowledge and technical skills sufficient to assess and apply their own informed judgment to the information. No license under any 3M or third party intellectual property rights is granted or implied with this information. Product Selection and Use: Many factors beyond 3M’s control and uniquely within user’s knowledge and control can affect the use and performance of a 3M product in a particular application. As a result, customer is solely responsible for evaluating the product and determining whether it isappropriate and suitable for customer’s application, including conducting a workplace hazard assessment and reviewing all app licable regulations and standards (e.g., OSHA, ANSI, etc.). Failure to properly evaluate, select, and use a 3M product and appropriate safety products, or to meet allapplicable safety regulations, may result in injury, sickness, death, and/or harm to property. Warranty, Limited Remedy, and Disclaimer: Unless a different warranty is specifically stated on the applicable 3M product packaging or product literature (in which case such warranty governs), 3M warrants that each 3M product meets the applicable 3M product specification at the time 3M ships the product. 3M MAKES NO OTHERWARRANTIES OR CONDITIONS, EXPRESS OR IMPLIED, INCLUDING, BUT NOT LIMITED TO, ANY IMPLIED WARRANTY OR CONDITION OFMERCHANTABILITY, FITNESS FOR A PARTICULAR PURPOSE, OR ARISING OUT OF A COURSE OF DEALING, CUSTOM, OR USAGE OF TRADE. If a 3M product does not conform to this warranty, then the sole and exclusive remedy is, at 3M’s option, replacement of the 3M product or refund of the purchase price. Limitation of Liability: Except for the limited remedy stated above, and except to the extent prohibited by law, 3M will not be liable for any loss or damage arising from or related to the 3M product, whether direct, indirect, special, incidental, or consequential (including, but not limited to, lost profits or business opportunity), regardless of the legal or equitable theory asserted, including, but not limited to, warranty, contract, negligence, or strict liability.Automotive Aerospace Solutions Division 3M Center, Building 224-6NE-45 St. Paul, MN 55144-1000 Phone: 1-800-328-1684Web: /autosolutions3M and Interam are trademarks of 3M Company Please recycle. Printed in USA © 3M 2021 All rights reserved.。
触摸屏用户手册说明书

感谢您购买 COOLMAY MT 系列触摸屏。
本手册主要说明MT 系列触摸屏的产品特性、一般规格、硬件接口和软件设置方法等。
详细编程请参见《COOLMAY 触摸屏使用手册》。
触摸屏的主要特点:1、提供大量的矢量图库及支持自建图库2、高精度/高可靠性的电阻式触摸面板3、支持各种格式静态图片及GIF 动画4、支持windows 所提供的所有字体5、6万TFT 真彩显示器6、支持配方功能和数据存储、U 盘导出数据7、自带一个RS232和一个RS485通讯口8、基本版可竖屏显示9、可选装网口或音频10、基本版(基于WINCE 5.0系统)和升级版(基于WINCE 7.0系统)可选11、MT6037H /MT6050H (A )灰色/金色/银色面板可选,黑色/白色底壳可选 12、MT6037H /MT6050H (A )可墙体安装,可应用于智能家居/工业等领域产品信息1、 公司产品系列 MT 系列触摸屏2、 HMI 尺寸 6037:3.5寸 6043: 4.3寸 6050: 5寸 6070: 7寸 6100: 10寸3、 版本 H : 基本版 HV : 基本版竖屏;HA /HAS : 升级版 HAV /HAVS : 升级版竖屏4、 网口 W : 网口(选装)5、 音频 Y : 音频(选装)命名规则MT 123456070图1 安装尺寸图MT6100HAMT6043HMT6070H(A/AS)电气设计参考产品构造COM :PLC 与触摸屏 通讯上时快闪安装尺寸机械设计参考规格参数触摸屏用户手册表三:安装尺寸型 号安装尺寸外形尺寸W*H*D(mm)A(mm)B(mm)MT6050H(A)MT6070H(A/AS)MT6100HA13719426172138180146*88*25212*148*40275*194*36电源用端子台 USB 口PWR :通电指示灯触摸屏编程口液晶屏RS232/RS485网口(选装) ◆◆◆◆YW H--6143257图2 产品构造※ 更多规格批量客户可定制MT6043H(A)MT6070H(A/AS)MT6100HAMT6037H背面图MT6050H背面图型号MT6037H 3.5"TFT 液晶屏 4.3"TFT 液晶屏7.0"TFT 液晶屏10.2"TFT 液晶屏MT6043H(A)MT6070H(A/AS)MT6100HA 320*240480*272800*480/1024*6001024*60088*88*25mm 134*102*30mm 212*148*40mm 275*194*36mm 72*72mm 119*93mm 194*138mm 261*180mm 73*56mm 97*56mm 154*87mm 222*133mm 300cd/m²300cd/m²300cd/m²300cd/m²LED LED LED LED 128MB Flash ROM 65536真彩4线电阻屏100mA/24V150mA/24V200mA/24V280mA/24VCOM1: RS232 COM2: RS485400:1H 系列: ARM9内核 640MHz HA(S)系列: Cortex A8 720MHz-1GHz20ms 以内有电源失效检测12-24VDC ±10%<150mA @24VDC 符合EN50081-2和EN50082-2标准符合FCC Class A电压1500Vp -p ,脉冲周期1μs ,持续1s 10-25Hz (X 、Y 、Z 方向2G 30分钟)超过10M Ω@500VDC工程塑料ABS +PC 500VAC 1分钟IP65(前面板)0~50℃20~90%RH -20~70℃显示屏分辨率外形尺寸安装开孔尺寸显示尺寸亮度背光类型存储器颜色触摸面板功耗通讯端口对比度CPU 容许掉电USB??系统诊断供电电源认证FCC 兼容性抗干扰测试防震测试绝缘电阻外壳材料耐压测试防护等级工作环境温度工作环境湿度存储温度65536真彩4线电阻屏65536真彩4线电阻屏65536真彩4线电阻屏0.3kg0.33kg0.54kg0.7kg重量MT6050H(A)5.0"TFT 液晶屏800*480146*88*25mm 137*72mm 108*65mm 300cd/m²LED 150mA/24V65536真彩4线电阻屏0.33kg128MB Flash ROM 128MB Flash ROM 128MB Flash ROM 128MB Flash ROMH 系列: 64MB HA(S)系列: 128M运行内存121264357643572264357673541234657侧面四个安装扣位孔888888MT6037H 727288*88*25MT6043H(A)11993134*102*30MT6037H硬件接口◆FG 0V 24V触摸屏232/485口触摸屏下载口USB口网口COM1/COM2MT6043H(A)/MT6043KH(A)/MT6050KH(A) COM口引脚定义管脚号信号描述23TXDRXD 发送接收5地线GNDRS232通讯口定义RS485通讯口定义16BA485-485+MT6043H(A)背光寿命60000小时60000小时60000小时60000小时60000小时以太网口可选装万年历输入电压有常规为DC24±10%VDC ,也可以特别做成DC12V /DC5V 电源输入墙体安装镶嵌安装墙体安装镶嵌安装MT6050H(A)型号MT6037H MT6043H(A)MT6070H(A/AS)MT6100HAMT6050H(A)自然风冷冷却方式接上表FG 0V 24V 触摸屏485口USB口触摸屏下载口触摸屏232/485口网口(选装)(同COM1中的485口)COM1/COM2MT6070H(A/AS ) COM口引脚定义管脚号信号描述23TXDRXD 发送接收5地线GNDCOM1 RS232通讯口定义COM1/COM2 RS485通讯口定义16BA 485-485+MT6070H(A/AS)FG 0V 24V USB口触摸屏下载口网口(选装)触摸屏232/485口COM1MT6100HACOM口引脚定义管脚号信号描述23TXDRXD 发送接收5地线GNDRS232通讯口定义RS485通讯口定义16BA 485-485+MT6100HA* 编程软件触摸屏:CoolMayHMI 触摸屏编程软件* 详细资料参考《CoolMayHMI 触摸屏使用手册》温馨提示.......................................................01产品特点.......................................................02产品信息.......................................................03 电气参数......................................................04 机械设计参考................................................05 产品构造.......................................................06 硬件接口.......................................................07软件参数设置................................................08 与个厂牌联机说明.........................................09 抗干扰处理...........................................10 编程参考.......................................................11资料参考. (12)深圳市顾美科技有限公司 86960332 26051858 26400661营销QQ:800053919邮箱:**************.com 网址:2018/02 版目 录1、请在确认了本产品的电源电压范围(常规产品电源仅限24V?DC!建议电源的 输出功率为18W及以上)和正确接线之后再通电,以避免损坏。
网康ICG产品性能参数表
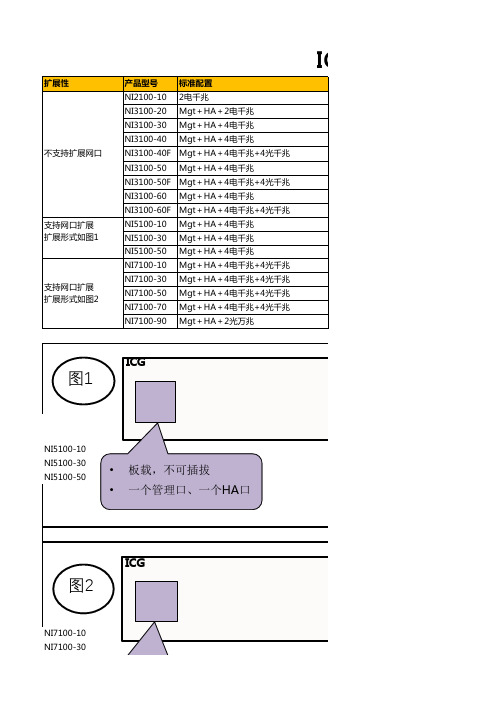
•可 插 拔 的 插
槽 •支
持
4 电 千
兆 •支
持
4 光 千
兆 •支
持
2 光 万
兆
备注
1,橙色是板载配置,蓝色 是可配置插槽。
可插拔 支持四 千兆电 口或光
可 插 拔 的 插
槽 支 持
4 电 千
兆 支
持
4 光 千
兆 支 持
2 光 万
兆
扩展性
不支持扩展网口
支持网口扩展 扩展形式如图1 支持网口扩展 扩展形式如图2
产品型号
标准配置
NI2100-10 2电千兆
NI3100-20 Mgt+HA+2电千兆
NI3100-30 Mgt+HA+4电千兆
NI3100-40 Mgt+HA+4电千兆
NI3100-40F Mgt+HA+4电千兆+4光千兆
• 板载,不可插拔 • 一个管理口、一个HA口
ICG
图2
NI7100-10 NI7100-30
NI7100-50 NI7100-70 NI7100-90
• 板载,不可插拔 • 一个管理口、一个HA口
ICG各型号可扩展网卡说明
扩展方式 不支持 不支持 不支持 不支持 不支持 不支持 不支持 不支持 不支持 2个扩展槽,每个扩展槽支持4个千兆电口或光口 2个扩展槽,每个扩展槽支持4个千兆电口或光口 2个扩展槽,每个扩展槽支持4个千兆电口或光口 共4个插槽均可插拔,默认板载占用2个。每个插槽均可支持4个千兆电口、光口,或者2个万兆光口 共4个插槽均可插拔,默认板载占用2个。每个插槽均可支持4个千兆电口、光口,或者2个万兆光口 共4个插槽均可插拔,默认板载占用2个。每个插槽均可支持4个千兆电口、光口,或者2个万兆光口 共4个插槽均可插拔,默认板载占用2个。每个插槽均可支持4个千兆电口、光口,或者2个万兆光口 共4个插槽均可插拔,默认板载占用1个。每个插槽均可支持4个千兆电口、光口,或者2个万兆光口
产品号序列号

名称 SUP SUP SUP SUP(机框内) 机柜 6601机框(MU) 6201机柜 IP GE光模块(MU TNB侧) 地震防护组件(交换) 电缆夹(交换) 6601机框(MU) 接地组件 2.5m接地线 底座 扎带包 SPD电源接线柜 SPD电源接线柜 PSU-AC PSU-AC(RRU侧) AC PSU 三相电源线 及 MU电源线 通宇 D频段天线(八通道) 10m接地线 15m室内接地线 GPS放大器 F频段双通道天线安佛士 AC配电箱 室内型交流电源线 3X4MM2 电源线(交换) 3频段合路器,1.8G/1.9G/2.6G 走线槽 3X1.5MM2 电源线(交换) PSU-AC(MU侧) 两头1/2的6M馈线 海天 D频段天线(八通道) 防水胶带 1/2馈线(300M) 3x1mm2 电源线 冷缩管 10m MU-FC室内光纤 15m MU-FC室内光纤 20m MU-FC室内光纤 八通道馈线标贴 AUB安装组件GPS天线抱杆件 6601 19英寸MU安装支架 京信 D频段天线(八通道) 10m RRU-FC室外光纤 20m RRU-FC室外光纤 30m RRU-FC室外光纤 50m RRU-FC室外光纤 70m RRU-FC室外光纤 1/2馈线 6201机柜(总箱) 6601机柜(总箱)
爱立信 爱立信 爱立信 爱立信
FAD频段0.7λ8阵元天 TYD 线(内置合路器) FAD频段0.7λ8阵元天 TYD 线(内置合路器) FAD频段0.5λ2阵元天 S-W 线 FAD频段0.5λ2阵元天 TD 线 F频段0.7λ2阵元天线 (独立电调)
R6_DU_PRODUCTS VCO DU 产品 R6_RU_DU_CABLES DU,TCU电缆 VCO_6601_CAB RBS 6601 KRC118039/1R2C RRUS 61B39 ENC-ODS-090R15CV 八通道合路天线 ENC-20152616D4T6BC普通FA/D内置合路器智能天线通宇 RBS6601主单元AC/DC转换模块电源线 ENC-04110502 ENC-NETSURE212C23RBS6601主单元AC/DC转换模块 BML901250/1 电源模块 ENC-TSR951342/3M 同轴电缆(带接头) KRC161309/1R1G RRU 62B40 RPM2531610/150M 150M室外光纤 KRE1012182/1 GPS天线 KRC161308/1R1G RRUL 62B38
MAX1674EUA-T中文资料

ELECTRICAL CHARACTERISTICS
(VBATT = 2V, FB = OUT (VOUT = 3.3V), RL = ˙∞, TA = 0°C to +85°C, unless otherwise noted. Typical values are at TA = +25°C.) PARAMETER Minimum Input Voltage Operating Voltage Start-Up Voltage Start-Up Voltage Tempco Output Voltage Output Voltage Range FB = OUT (VOUT = 3.3V) Steady-State Output Current (Note 2) IOUT FB = GND (VOUT = 5V) Reference Voltage Reference Voltage Tempco Reference Voltage Load Regulation Reference Voltage Line Regulation FB, LBI Input Threshold Internal NFET, PFET On-Resistance LX Switch Current Limit (NFET) LX Leakage Current RDS(ON) ILIM ILEAK ILX = 100mA MAX1674, MAX1676 (CLSEL = OUT) MAX1675, MAX1676 (CLSEL = GND) VLX = 0, 5.5V; VOUT = 5.5V 0.80 0.4 VREF TEMPCO VREF_LOAD VREF_LINE IREF = 0 to 100µA VOUT = 2V to 5.5V 1.274 IREF = 0 MAX1674, MAX1676 (CLSEL = OUT) MAX1675, MAX1676 (CLSEL = GND) MAX1674, MAX1676 (CLSEL = OUT) MAX1675, MAX1676 (CLSEL = GND) VOUT FB = OUT FB = GND 3.17 4.80 2 300 150 180 90 1.274 420 220 mA 285 130 1.30 0.024 3 0.08 1.30 0.3 1 0.5 0.05 15 2.5 1.326 0.6 1.20 0.65 1 1.326 V mV/°C mV mV/V V Ω A µA VIN TA = +25°C TA = +25°C, RL = 3kΩ (Note 1) 1.1 0.9 -2 3.30 5 3.43 5.20 5.5 SYMBOL CONDITIONS MIN TYP 0.7 5.5 1.1 MAX UNITS V V V mV/°C V V
GMW3172_AUG2008中文版

如果不一致,GM元件验证工程师或GM ENV/DUR专家,除了GM供应商质量工程师(SQE)和DRE,应 重审测试结果并决定是否需要再次反复DV。GM元件验证工程师或GM ENV/DUR专家应执行硬件设计重 审。基于纠正性活动,根据需要修正元件环境测试方案。
z 执行产品验证(PV)任务。PV任务应不迟于验证测试结束(VTC)成功完成。评审元件环境测试方案, 使其适用于相应的生产流程变动/变化和DV测试结果。
3.2 参数公差.
除非有其它规定外,全部的验证实验遵照下表规定的环境参数和公差。
表2: 参数公差
参数 环境温度 室温 测试时间 室内相对环境湿度 房间湿度 电压 电流 电阻 自由加速度 (GRMS) 加速度 (机械振动, G) 频度 力 距离 (不包括尺寸检验) 3.3 操作类型
表3:操作类型
公差 Spec. ±3℃ (+23 ± 5) ℃ Spec. ± 0.5 % (30...70) % Spec. ± 5% Spec. ± 0.1 V Spec. ± 1% Spec. ± 10 % Spec. ± 20 %(没有GM批准,PSD偏差来自适用性表格中)是不被允许的 Spec. ± 20 % Spec. ± 1% Spec. ± 10 % Spec. ± 5%
2008年11月开始, 全部A/D/V测试方案、测试结果、程序说明书以及供应商与GM之间交换的关于环境/持久性 A/D/V程序的数据,应通过GM提交系统,提交给GM’s Global EMC/环境/持久性数据库。
4.2 A/D/V程序流程.
A/D/V程序流程应遵照图1.
A/D/V流程由以下主要的任务组成:
2.2 GM标准/技术规范
GMN5345 GMW3091 GMW3097 GMW3103 GMW3191 GMW3431 GMW8287 GMW8288 GMW14082
Motorola MOTOTRBO XPR 7550 6550 无线通信设备说明书

Accelerated Life T estMotorola’s Accelerated Life Test (ALT) is a developmental process of rigorous laboratory testing that simulates years of field use. Motorola has a firm commitment to quality and reliability. These radios have been designed, manufactured and tested to achieve high levels of component and workmanship quality. Motorola radios are designed to minimize costly repairs and downtime.POWER AND BATTERY DRAINModel Type 380-470 MHz 136-174 MHzMinimum RF Power Output 25-110 Watt 25-110 WattOperation 12V DC Negative Ground 12V DC Negative Ground Standby at 13.8V 0.65A-0.85A 0.5A-0.7A Receive at Rate Audio at 13.8V1.5A-3.2A1.3A-3.0ASPECIFICATION SHEETPM1500 PROFESSIONAL SERIES Two-Way Mobile RadioMOTOROLA and the Stylized M Logo are registered in the U.S. Patent and Trademark Office. All other product or service names are the prop-erty of their registered owners. © Motorola, Inc. 2007.MD-PM1500SPECS 5/07,PM1500Professional Series Two-Way Mobile RadioT o keep things running efficiently, safely, and productively, you need to stay connected. That’s why so much quality and performance isbuilt into the Professional Series PM1500 two-way mobile radio from Motorola. Long-range com-munications are robust with the mobile radio that packs 110 watts of power. The rugged housing and standard external speaker of the PM1500 make it the dependable choice in tough, loud environments. Y ou’ll appreciate the user-friendly design of the controls, backlit alphanumeric display and program-mable buttons for easy access to favorite features. The PM1500 puts quality Motorola technology to work helping public safety, utility, transportation and construction users with strong, reliable communica-tions – even over long distances.Linking Communities with Project 25 (P25)With a single software upgrade, the PM1500 becomes P25 interoperable. This vital feature gives you the ability to interact with other networks in times of crisis.255 ChannelsMulticolored LED Indicators4 Programmable ButtonsEasy access to favorite features.Optional keypad microphone allows youto scroll through the menu and access up to 16 programmable features Programmable Emergency ButtonAlerts dispatcher in an emergency situation Backlit 8-CharacterAlphanumeric DisplayUser friendly icons and soft menu soyou easily view status and access features. Display for viewing of channel namesand Caller IDLarge Channel and Push ButtonOn/Off Volume Knobs7.5 Watt External SpeakerAllows for clear, crisp communicationin loud environmentsP25 Conventional UpgradableDual Control Head OptionEnables multiple radio control heads tobe located within the same vehicle. Available with independent volumeand backlight display PM1500Standard Package• Palm Microphone• 7.5 Watt External Speaker• Mounting Hardware• 20 Ft. Power Cable• 17 Ft. Remote Mount Cable• Ignition Sense Cable• User Guide CD• 2-Y ear Standard WarrantyDual Control HeadStandard Packagealso includes:• Two Palm Microphones• One 7.5 Watt External Speaker• One 13 Watt External Speaker• Two 17 Ft. Remote Mount Cables• Additional Mounting BracketAdditional FeaturesSend and receive informationin a variety of ways:Quik-Call II™, MDC1200and DTMF Signaling• Selective Call (Decode)Receive a call from a specificgroup or individual• Call Alert (Decode)Receive alerts of incoming callswhen a short distance from radioMDC1200 Signaling Only• Push-to-T alk ID (Encode)Identify outgoing calls• R adio Check (Decode)Lets others check users radio status• Emergency (Encode)Alerts dispatcher in urgent situations• Selective Radio Inhibit (Decode)Allows system owner to disablestolen or missing radiosSPECIFICATION SHEET。
GMW14700-CHINESE

GMW14700覆盖层碎石冲击性能1 范围注:本标准不能取代适用的法律和规章,除非已经取得了特定的许可。
注:如果出现英文版与国内语言冲突时,优先考虑英文版。
本标准描述的测试步骤用于评价覆盖层的碎石冲击性能。
方法A是将碎石冲击仪置于恒温的冰库中,方法B是将测试样板从冰箱中取出放入到处于室温下的碎石冲击仪中,而方法C是将碎石冲击仪置于一个恒温的房间内。
2 参考注:仅仅最新的认可标准是适用的,除非特别指定。
2.1 外部标准/规范SAE J4002.2 GM标准/规范无2.3 其他参考零件号,GME:92740433 测试仪器3.1 碎石冲击仪一种碎石发射仪器,在SAE J400中通过设计说明书描述了它的构造。
(满足本标准的相似类型商业仪器能够在下面列出的厂家得到:the Q-Panel Col. 800 Canterbury Rd., Cleveland, OH 44145; German representation: Pausch Meßtechnik GmbH, Nordstraße 32, 42781 Haan); Q-Panel Europe, Express Trading Estate, Farnsworth, Bolton, BL49TP England; Q-Panel China, RM1809/1810, Liangyou Building, 618 SHabgcheng Road, Pudong District, Shanghai, 200120 China.3.2 碎石-水-浸蚀冲击碎石大小至8到16mm。
重新使用碎石之前,移除小的碎块是很重要的。
(满足本标准的碎石能从下面列出的厂家获得:the Q-Panel Col. 800 Canterbury Rd., Cleveland, OH 44145.); German representation: Pausch Meßtechnik GmbH, Nordstraße 32, 42781 Haan)。
GMW14400 2012 中文翻译版
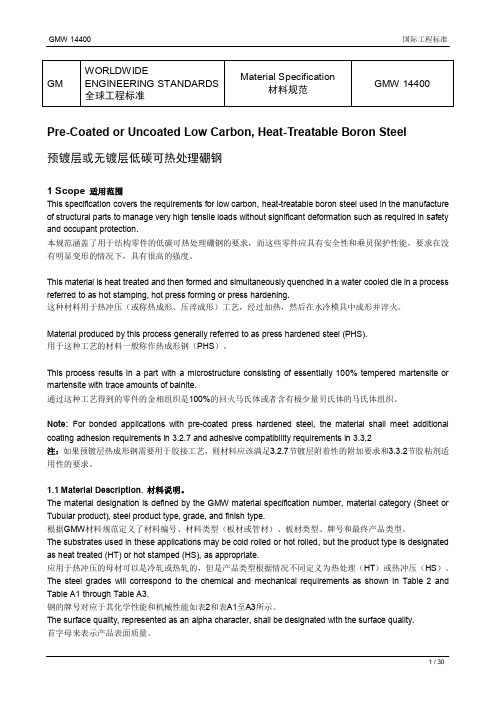
Pre-Coated or Uncoated Low Carbon, Heat-Treatable Boron Steel预镀层或无镀层低碳可热处理硼钢1 Scope适用范围This specification covers the requirements for low carbon, heat-treatable boron steel used in the manufacture of structural parts to manage very high tensile loads without significant deformation such as required in safety and occupant protection.本规范涵盖了用于结构零件的低碳可热处理硼钢的要求,而这些零件应具有安全性和乘员保护性能,要求在没有明显变形的情况下,具有很高的强度。
This material is heat treated and then formed and simultaneously quenched in a water cooled die in a process referred to as hot stamping, hot press forming or press hardening.这种材料用于热冲压(或称热成形、压淬成形)工艺,经过加热,然后在水冷模具中成形并淬火。
Material produced by this process generally referred to as press hardened steel(PHS).用于这种工艺的材料一般称作热成形钢(PHS)。
This process results in a part with a microstructure consisting of essentially 100% tempered martensite or martensite with trace amounts of bainite.通过这种工艺得到的零件的金相组织是100%的回火马氏体或者含有极少量贝氏体的马氏体组织。
- 1、下载文档前请自行甄别文档内容的完整性,平台不提供额外的编辑、内容补充、找答案等附加服务。
- 2、"仅部分预览"的文档,不可在线预览部分如存在完整性等问题,可反馈申请退款(可完整预览的文档不适用该条件!)。
- 3、如文档侵犯您的权益,请联系客服反馈,我们会尽快为您处理(人工客服工作时间:9:00-18:30)。
General Specification
GMW16740
Harness Tape
1 Introduction
Note: Nothing in this standard supercedes applicable laws and regulations. Note: In the event of conflict between the English and domestic language, the English language shall take precedence. 1.1 Scope. There is no international or national equivalent to this standard. 1.2 Mission/Theme. This standard specifies dimensions, test methods and requirements for harness tapes. 1.3 Classification. 1.3.1 Temperatures. Class designations have been defined in Table 1 to classify the various temperature ranges encountered in/on vehicles. Table 1: Temperature Classes Class A B C D E F G H Operating Temperature (-40 to +85) °C (-40 to +100) °C (-40 to +125) °C (-40 to +150) °C (-40 to +175) °C (-40 to +200) °C (-40 to +225) °C (-40 to +250) °C Long-term Aging Temperature 3000 h (+85 ± 2) °C (+100 ± 2) °C (+125 ± 3) °C (+150 ± 3) °C (+175 ± 3) °C (+200 ± 3) °C (+225 ± 4) °C (+250 ± 4) °C Short-term Aging Temperature 240 h (+110 ± 2) °C (+125 ± 3) °C (+150 ± 3) °C (+175 ± 3) °C (+200 ± 3) °C (+225 ± 4) °C (+250 ± 4) °C (+275 ± 4) °C Overload Aging Temperature 6h (+135 ± 3) °C (+150 ± 3) °C (+175 ± 3) °C (+200 ± 3) °C (+225 ± 4) °C (+250 ± 4) °C (+275 ± 4) °C (+300 ± 4) °C
Sold to:RELATS, W1530296 Not for Resale,2013/8/23 7:40:12 GMT
GM WORLDWIDE ENGINEERING STANDARDS
GMW16740
3.1.1 Calibration. The test facilities and equipment shall be in good working order and shall have a valid calibration label. 3.1.2 Alternatives. Alternative test facilities and equipment may also be used. However, all measuring variables as specified in this standard shall be determined correctly with respect to their physical definition. 3.1.3 Facilities. 3.1.3.1 Ovens. When an oven is required, a naturally ventilated oven shall be used. 3.1.4 Equipment. As specified in each test. 3.1.5 Test Vehicle/Test Piece. Number of test pieces as specified in each paragraph. No parts out of prototype tools shall be used. Discard the first three layers of tape from the roll to be tested before removing the test material. For each test, only specimens shall be used which, at the start of the test, are not older than 6 months, and have not been used in previous test. 3.1.6 Test Time. As specified in each test. 3.1.7 Test Required Information. Not applicable. 3.1.8 Personnel/Skills. Not applicable. 3.2 Preparation. See each individual test. 3.3 Conditions. 3.3.1 Environmental Conditions. If not otherwise specified, all test samples shall be maintained at (+23 ± 5) °C and a relative humidity of (50 ± 20)% for ≥ 24 h before the start of any test sequence 3.3.2 Test Conditions. Deviations from the requirements of this standard shall have been agreed upon. Such requirements shall be specified on component drawings, test certificates, reports, etc. Test pieces for all tests shall be preconditioned for at least 16 h at a temperature of (+23 ± 5) °C and a relative humidity of (45 to 75)%. Unless otherwise specified, all tests other than “in process” tests shall be performed at this temperature. Where no tolerance is specified, all values shall be considered to be approximate. 3.4 Instructions. Not applicable. 3.5 Data. Not applicable. 3.6 Safety. This standard may involve hazardous materials, operations, and equipment. This standard does not propose to address all the safety problems associated with its use. It is the responsibility of the user of this standard to establish appropriate safety and health practices and determine the applicability of regulatory limitations prior to use. 3.7 Documentation. Samples of components or material released to this standard shall be tested for conformity with the requirements of this standard and approved by the responsible GM Department prior to the start of delivery of production level components or materials. Any change to the component or material, e.g., design, function, properties, manufacturing process and/or location of manufacture requires a new release of the product. It is the sole responsibility of the supplier to provide the customer, unsolicited, with documentation of any change or modification to the product/process, and to apply for a new release. If not otherwise agreed to, the entire verification test shall be repeated and documented by the supplier prior to start of delivery of the modified or changed product. In some cases, a shorter test can be agreed to between the responsible GM department and the supplier. 3.7.1 Test Results. Test results shall be reported in a test report (see example in GMW15626). The test report shall include as minimum: Name of the supplier. Date. Designation of product. International Material Data System Identification (IMDS ID) and information, if the IMDS datasheet has been approved by the customer.