配方设计与硫化胶撕裂强度的关系
橡胶与各指标的关系
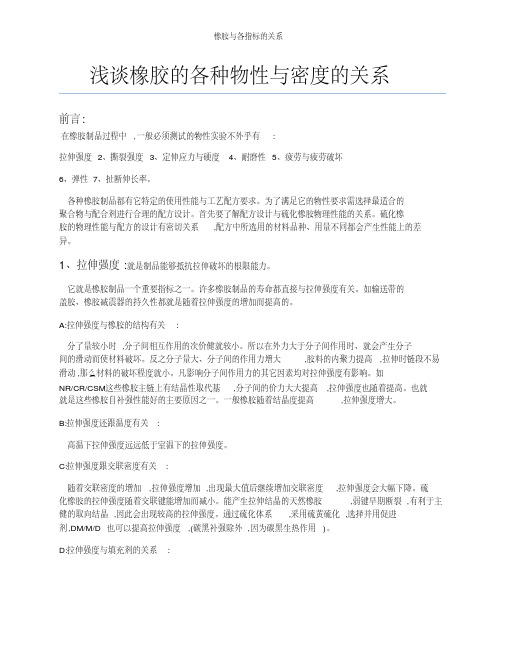
浅谈橡胶的各种物性与密度的关系前言:在橡胶制品过程中,一般必须测试的物性实验不外乎有:拉伸强度 2、撕裂强度 3、定伸应力与硬度 4、耐磨性 5、疲劳与疲劳破坏6、弹性7、扯断伸长率。
各种橡胶制品都有它特定的使用性能与工艺配方要求。
为了满足它的物性要求需选择最适合的聚合物与配合剂进行合理的配方设计。
首先要了解配方设计与硫化橡胶物理性能的关系。
硫化橡胶的物理性能与配方的设计有密切关系,配方中所选用的材料品种、用量不同都会产生性能上的差异。
1、拉伸强度:就是制品能够抵抗拉伸破坏的根限能力。
它就是橡胶制品一个重要指标之一。
许多橡胶制品的寿命都直接与拉伸强度有关。
如输送带的盖胶、橡胶减震器的持久性都就是随着拉伸强度的增加而提高的。
A:拉伸强度与橡胶的结构有关:分了量较小时,分子间相互作用的次价健就较小。
所以在外力大于分子间作用时、就会产生分子间的滑动而使材料破坏。
反之分子量大、分子间的作用力增大,胶料的内聚力提高,拉伸时链段不易滑动,那么材料的破坏程度就小。
凡影响分子间作用力的其它因素均对拉伸强度有影响。
如NR/CR/CSM这些橡胶主链上有结晶性取代基,分子间的价力大大提高,拉伸强度也随着提高。
也就就是这些橡胶自补强性能好的主要原因之一。
一般橡胶随着结晶度提高,拉伸强度增大。
B:拉伸强度还跟温度有关:高温下拉伸强度远远低于室温下的拉伸强度。
C:拉伸强度跟交联密度有关:随着交联密度的增加,拉伸强度增加,出现最大值后继续增加交联密度,拉伸强度会大幅下降。
硫化橡胶的拉伸强度随着交联键能增加而减小。
能产生拉伸结晶的天然橡胶,弱键早期断裂,有利于主健的取向结晶,因此会出现较高的拉伸强度。
通过硫化体系,采用硫黄硫化,选择并用促进剂,DM/M/D也可以提高拉伸强度,(碳黑补强除外,因为碳黑生热作用)。
D:拉伸强度与填充剂的关系:补强剂就是影响拉伸强度的重要因素之一,填料的料径越小,比表面积越大、表面活性越大补强性能越好。
配方因素对CR/PU并用胶性能的影响

硫 黄用 量 / 份
图 1 C / U并 用 比对 并 用 胶 拉 伸 强 度 和 RP
拉 断 伸 长 率 的影 响
试 验配 方 为 : 胶 生 氧化镁 1 0 炭 黑 N3 0 3 , 0, 3 O 硬脂 酸 锌 15 ., l , 4增塑剂 D 5硫黄 , OP ,
一
C P 并用 比对 并用 胶 物 理性 能 的影 响如 R/ U
图 1和 2所 示 。
厂产 品 。
从 图 1和 2可 以看 出 , U 具 有 良好 的物 理 P 性能 , 邵尔 A型 硬度 、 伸强度 和撕裂 强度 明显 高 拉
12 主 要 设 备 与 仪 器 .
X 一6 K 1 O型 开ቤተ መጻሕፍቲ ባይዱ炼 机 , 东 湛 江 机 械 厂 产 品 ; 广
*通 讯 联 系 人
份时 , 用胶 的拉伸强 度和撕 裂强度 明显增 大 。 并 由此 可 见 , 整 C P 调 R/ U并 用 比可 调 节 并 用
第 1 2期
邓
华 等 . 方 因 素 对 C / U 并 用 胶 性 能 的影 响 配 RP
\、
瓣
堡
瓣
廷
豁
塔
CR P / U并用 比
2 结 果 与 讨 论 2 1 C / U 并 用 比 . R P
产品 ; 聚醚型 P 牌 号 Urp n 0 L 6 德 国拜 u, e a 5 E O G,
耳公司产 品 ; 塑剂 D P, 国爱敬 公 司产 品 ; 增 O 韩 炭
黑 N2 0 N3 0 N5 0 N 6 2 , 3 , 5 , 6 0和 N7 4 茂 名 市 化 工 5,
7O 3
橡
胶
配方设计与硫化胶拉伸强度的关系.

∙配方设计与硫化胶拉伸强度的关系∙拉伸强度表征制品能够抵抗拉伸破坏的极限能力橡胶的拉伸强度:未填充硫化胶:聚氨酯橡胶PUR>天然橡胶NR/异戊IR>氯丁橡胶CR>丁基橡胶IIR>氯磺化聚乙烯CSM>丁晴橡胶NBR/氟橡胶FKM>顺丁橡胶BR>三元乙丙橡胶EPDM>丁苯橡胶SBR>丙烯酸酯橡胶ACM>氯醇橡胶CO>硅橡胶Q。
填充硫化胶:聚氨酯橡胶PUR>聚酯型热塑性弹性体>天然橡胶NR/异戊IR>SBS热塑性弹性体>丁晴橡胶NBR/氯丁橡胶CR>丁苯橡胶SBR/三元乙丙橡胶EPDM/氟橡胶FKM>氯磺化聚乙烯CSM>丁基橡胶IIR>顺丁橡胶BR/氯醇橡胶CO>丙烯酸酯橡胶ACM>硅橡胶Q。
在快速形变下,橡胶的拉伸强度比慢速形变时高;高温下测试的拉伸强度,远远低与室温下的拉伸强度。
硫化体系的影响对常用的软质硫化胶而言,欲通过硫化体系提高拉伸强度时,应采用硫磺-促进剂的传统硫化体系,并适当提高硫磺用量。
同时促进剂选用噻唑类如M,DM与胍类并用,并适当增加用量。
填充体系的影响填料的粒径越小,比表面积越大,表面活性越大,则补强效果越好。
结晶型(如天然橡胶)为基础的硫化胶,拉伸强度随填充剂用量增大,可出现单调下降。
非结晶型(如丁苯橡胶)为基础的硫化胶,拉伸强度随填充剂用量增大而增大,达到最大值,然后下降。
低不饱和度橡胶(如三元乙丙橡胶,丁基橡胶)为基础的硫化胶,拉伸强度随填充剂用量增大而增大,达到最大值后可以保持不变。
对热塑型弹性体而言,填充剂使其拉伸强度降低。
一般情况下,软质橡胶的碳黑用量在40-60份时,硫化胶的拉伸性能比较好。
软化体系的影响总的来说,加入软化剂会降低硫化橡胶的拉伸强度。
但软化剂数量不超过5份时,硫化橡胶的拉伸强度有可能增大。
因为含有少量软化剂,可以使碳黑的分散效果好。
橡胶配方设计整理
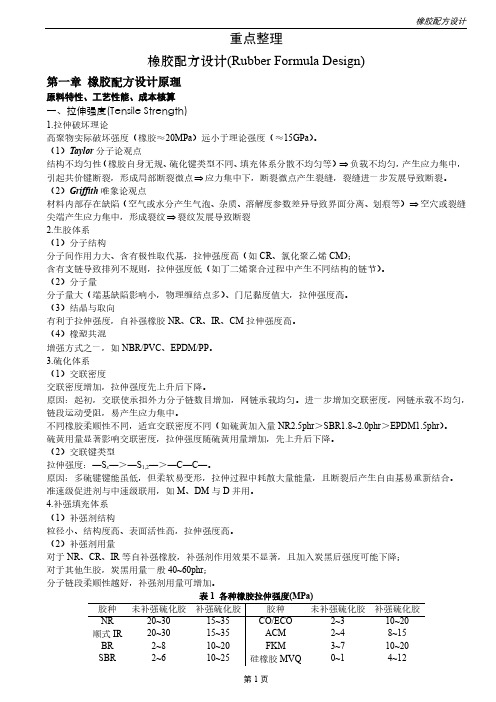
重点整理橡胶配方设计(Rubber Formula Design)第一章橡胶配方设计原理原料特性、工艺性能、成本核算一、拉伸强度(Tensile Strength)1.拉伸破坏理论高聚物实际破坏强度(橡胶≈20MPa)远小于理论强度(≈15GPa)。
(1)Taylor分子论观点结构不均匀性(橡胶自身无规、硫化键类型不同、填充体系分散不均匀等)⇒负载不均匀,产生应力集中,引起共价键断裂,形成局部断裂微点⇒应力集中下,断裂微点产生裂缝,裂缝进一步发展导致断裂。
(2)Griffith唯象论观点材料内部存在缺陷(空气或水分产生气泡、杂质、溶解度参数差异导致界面分离、划痕等)⇒空穴或裂缝尖端产生应力集中,形成裂纹⇒裂纹发展导致断裂2.生胶体系(1)分子结构分子间作用力大、含有极性取代基,拉伸强度高(如CR、氯化聚乙烯CM);含有支链导致排列不规则,拉伸强度低(如丁二烯聚合过程中产生不同结构的链节)。
(2)分子量分子量大(端基缺陷影响小,物理缠结点多)、门尼黏度值大,拉伸强度高。
(3)结晶与取向有利于拉伸强度,自补强橡胶NR、CR、IR、CM拉伸强度高。
(4)橡塑共混增强方式之一,如NBR/PVC、EPDM/PP。
3.硫化体系(1)交联密度交联密度增加,拉伸强度先上升后下降。
原因:起初,交联使承担外力分子链数目增加,网链承载均匀。
进一步增加交联密度,网链承载不均匀,链段运动受阻,易产生应力集中。
不同橡胶柔顺性不同,适宜交联密度不同(如硫黄加入量NR2.5phr>SBR1.8~2.0phr>EPDM1.5phr)。
硫黄用量显著影响交联密度,拉伸强度随硫黄用量增加,先上升后下降。
(2)交联键类型拉伸强度:—S x—>—S1,2—>—C—C—。
原因:多硫键键能虽低,但柔软易变形,拉伸过程中耗散大量能量,且断裂后产生自由基易重新结合。
准速级促进剂与中速级联用,如M、DM与D并用。
4.补强填充体系(1)补强剂结构粒径小、结构度高、表面活性高,拉伸强度高。
配方体系对EPDM 耐热撕裂性能的影响
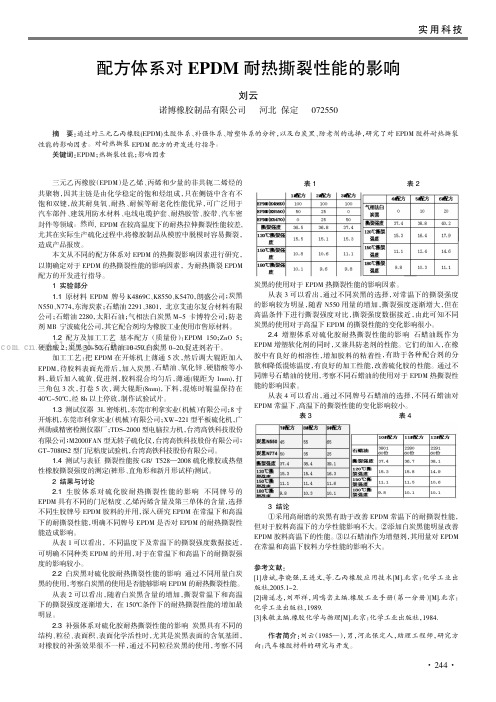
三元乙丙橡胶(EPDM)是乙烯、丙烯和少量的非共轭二烯烃的共聚物,因其主链是由化学稳定的饱和烃组成,只在侧链中含有不饱和双键,故其耐臭氧、耐热、耐候等耐老化性能优异,可广泛用于汽车部件、建筑用防水材料、电线电缆护套、耐热胶管、胶带、汽车密封件等领域。
然而,EPDM在较高温度下的耐热拉伸撕裂性能较差,尤其在实际生产硫化过程中,将橡胶制品从模腔中脱模时容易撕裂,造成产品报废。
本文从不同的配方体系对EPDM的热撕裂影响因素进行研究,以期确定对于EPDM的热撕裂性能的影响因素,为耐热撕裂EPDM 配方的开发进行指导。
1实验部分1.1原材料EPDM牌号K4869C、K8550、K5470,朗盛公司;炭黑N550、N774,东海炭素;石蜡油2291、3801,北京艾迪尔复合材料有限公司;石蜡油2280,太阳石油;气相法白炭黑M-5卡博特公司;防老剂MB宁波硫化公司,其它配合剂均为橡胶工业使用市售原材料。
1.2配方及加工工艺基本配方(质量份):EPDM150;ZnO5;硬脂酸2;炭黑30~50,石蜡油10~50,白炭黑0~20,促进剂若干。
加工工艺:把EPDM在开炼机上薄通5次,然后调大辊距加入EPDM,待胶料表面光滑后,加入炭黑、石蜡油、氧化锌、硬脂酸等小料,最后加入硫黄、促进剂,胶料混合均匀后,薄通(辊距为1mm),打三角包3次,打卷5次,调大辊距(8mm),下料,混炼时辊温保持在40℃~50℃,经8h以上停放,制作试验试片。
1.3测试仪器3L密炼机,东莞市利拿实业(机械)有限公司;8寸开炼机,东莞市利拿实业(机械)有限公司;XW-221型平板硫化机,广州勋威精密检测仪器厂;TDS-2000型电脑拉力机,台湾高铁科技股份有限公司;M2000FAN型无转子硫化仪,台湾高铁科技股份有限公司;GT-7080S2型门尼粘度试验机,台湾高铁科技股份有限公司。
1.4测试与表征撕裂性能按GB/T528—2008硫化橡胶或热塑性橡胶撕裂强度的测定(裤形、直角形和新月形试样)测试。
硅胶管抗撕裂性能配方的优化

硅胶管抗撕裂性能配方的优化硅胶管的基材是以Si—O键为主链的高相对分子质量的聚硅氧烷,具有优异的耐高低温性能(-65~250℃)、电绝缘性能、耐臭氧、耐高电压及耐天候等性能,同时对油类等介质表现出优异的化学惰性,因此在航空航天、电子化学、轻工、化工、交通运输、医疗卫生等方面均得到广泛应用。
但由于硅原子上连有甲基,其分子柔性大,分子链间相互作用力弱,因而硅橡胶硫化后拉伸强度和撕裂强度较差。
市面上大量的硅胶管产品,由于硫化过程不能形成很好的三维交织网络,导致硫化后产品的抗撕裂性能差,在热启模过程中产品容易被撕裂,在使用条件较苛刻的环境下,产品也很容易被挤压撕裂,影响产品的使用性能。
本工作采用过氧化物硫化体系,采用正交试验法考察硫化剂、补强填充剂以及结构控制剂等对硅橡胶抗撕裂性能有明显作用的助剂,以及其对硅橡胶抗撕裂性能的影响,通过对结果的分析和比较,确定出最优化的硅胶管抗撕裂配方。
1实验1.1主要原材料2,4一二氯苯酰过氧化物硅橡胶,牌号110—2,四川晨光化工研究院产品;气相法白炭黑,牌号HL—300,苏州威特化工有限公司产品:过氧化二异丙苯(DCP),上海高桥石化产品;羟基硅油,四川晨光化工研究院产品;其它原材料均为常用市售产品。
1.2基本配方2,4—二氯苯酰过氧化物硅橡胶,100;过氧化硫DCP,变量;白炭黑,变量;羟基硅油,变量;二苯基硅二醇,变量。
1.3主要仪器和设备X(K)--160型开炼机,QLB平板硫化机,上海第一橡胶机械厂产品;AI--8000S电子拉力机,台湾高铁科技股份有限公司产品;QP—16型橡胶,塑料冲片机,上海化工机械四厂产品;MM4130C无转子硫化仪,北京瑞达宇辰仪器有限公司产品。
1.4试样制备用X(K)—160开炼机进行混炼,辊温40-~50℃。
破胶一将辊距调至2mm,生胶包辊后,先加入白炭黑——缓慢加入结构控制剂——加硫化剂DCP——下片(5mm)。
停放8h后,按MM4130C无转子硫化仪所测的时间,采用QLB平板硫化机在170℃进行试样一段硫化,二段硫化分别在50℃、100℃、150℃下硫化0.5h 后,再在200℃下硫化2h。
青岛科技大学橡胶工艺复习题

一、简答题1、何谓喷霜?何谓焦烧?其产生原因何在?答:喷霜即为某些配合剂(如硫磺、促进剂、防老剂、石蜡等)析出胶料或硫化胶表面的现象;造成这种现象的原因主要是某些配合剂用量过大,超过其常温下在橡胶中的溶解度所造成的。
焦烧是一种胶料早期硫化的现象,即胶料在硫化前的操作或停放中发生不应有的提前硫化现象;原因是配合不当,炼胶操作不当,胶料冷却停放不当。
2、何谓老化?影响橡胶老化的因素有哪些?答:橡胶或橡胶制品的在加工、贮存和使用的过程中,由于受到各种外界因素的作用,而逐步失去原有的优良性能,以致最后失去使用价值,这种现象称为橡胶老化;影响因素有热、氧、臭氧、金属离子、电离辐射、光、机械力等。
3、何谓塑炼?其目的意义何在?答:把具有弹性的生胶变成柔软的具有可塑性的胶料的工艺过程称为塑炼;生胶塑炼的目的:一、使生胶获得一定的可塑性,适合混炼、压延、挤出、成型等后续工艺操作;二、使生胶的可塑性均匀化,以便制得质量均匀的胶料。
4、何谓混炼?其目的意义何在?答:在炼胶机上将各种配合剂加入到橡胶中制成混合胶的工艺过程叫混炼;使配合剂均匀分散,制得质量均匀的混炼胶,并使胶料具有适合的可塑性;混炼不好,出现配合剂分散不均匀,可塑度过高或低、焦烧、喷霜现象,影响压延等后续工序的正常进行,还会导致产品的性能下降。
5、何谓压延?它包括哪些作业形式?答:压延工艺是利用压延机辊筒的挤压力作用使胶料发生塑性流动和变形,将胶料制成具有一定断面规格和一定断面几何形状的胶片,或者将胶料覆盖于纺织物表面制成具有一定断面厚度的胶布的工艺加工过程;作业形式:胶料的压片、压型和胶片贴合及纺织物的贴胶、擦胶和压力贴胶。
6、何谓挤出?它有何作用?答:橡胶的挤出是使胶料通过挤出机连续地制成各种不同形状半成品的工艺过程;应用于制造胎面、内胎、胶管以及各种复杂断面形状或空心、实心、包胶等半成品。
7、何谓弹性变形和塑性变形?答:弹性变形:橡胶在变形后能够恢复其原来状态的形变行为。
橡胶配方设计
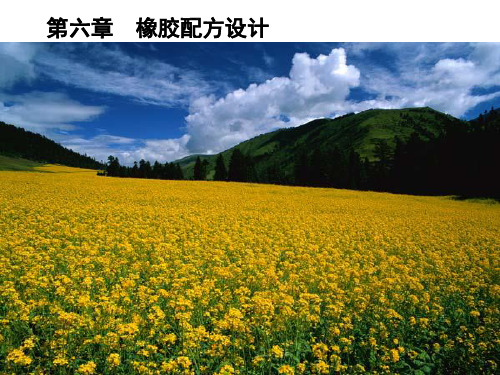
橡胶配方设计
耐70℃的非极 性油,Shore A硬度为70,
适用于注射硫 化成型工艺。
配方设计
橡胶性能要求 工艺要求 配方 配合 加工 制品 成本要求
2020/2/11
橡胶配方设计
2020/2/11
橡胶配方设计
二、橡胶配方设计的原则
a. 达到指定的硫化胶技术性能; b. 加工工艺性能良好; c. 降低生产成本。包括原材料成本和加工成本,如
多组分:橡胶、硫化剂、促进剂、活性剂、 防老剂、填料、软化剂等
b. 橡胶配方设计是个因子水平数不等的试验
设计方法、活用正交表(因子、水平数不等)
c. 橡胶配方设计中各组分间有复杂的交互关系
配方中原材料之间产生的协同效应、加和效应或对抗作用.
2020/2/11
橡胶配方设计
d. 工艺因素对橡胶配方实施有重要的作用
测定100%、200%、300%、500%的定伸应力;
扯断伸长率( %)-试样扯断时,伸长与原长之比;
扯断永久变形 ( %)-试样拉伸至断裂,自由状态下保持3分钟, 不可
恢复的变形长度与原长之比。
(c) 撕裂强度(KN/m) 试样被撕裂时,单位厚度所承受 的负荷。
2020/2/11
橡胶配方设计
(d)磨耗:橡胶表面受到磨擦力作用而使橡胶表面 发生磨损脱落的现象。仪器有阿克隆磨耗仪等
2020/2/11
橡胶配方设计
# 耐疲劳性的配方设计
a. 生胶结构:高应变 NR(拉伸结晶), 低应变 SBR(Tg较高);
b. 硫化体系:~C-SX-C ~、交联密度; c. 软化剂; d.填充体系:高结构炭黑; f. 防老剂:品种及用量
2020/2/11
配方设计与硫化胶撕裂强度的关系.

配方设计与硫化胶撕裂强度的关系撕裂强度是由于材料中的裂纹或裂口受力时迅速扩大开裂而导致破坏的现象。
各种橡胶(硫化胶)的撕裂强度:天然橡胶NR>聚酯型热塑性弹性体>异戊橡胶IR>聚氨酯橡胶PUR>氯醇橡胶CO>丁晴橡胶NBR>丁基橡胶IIR>氯丁橡胶CR>氯磺化聚乙烯CSM>SBS热塑性弹性体>顺丁橡胶BR>丁苯橡胶SBR>三元乙丙橡胶EPDM>氟橡胶FKM>硅橡胶Q>丙烯酸酯橡胶ACM。
撕裂强度和硫化体系的关系:撕裂强度和交联密度的关系有一个极大值,一般随交联密度的增加,撕裂强度增大,并出现一个极大值;然后随交联密度的增加,撕裂强度急剧下降。
和拉伸强度类似,但最佳撕裂强度的交联密度不拉伸强度达到最佳值的交联密度要低。
应采用硫磺-促进剂的传统硫化体系,硫磺用量2。
0-3。
0份。
促进剂选用中等活性,平坦性好的品种,如DM,CZ等;过硫影响大。
在天然橡胶中,如果用有效硫化体系代替普通硫化体系时,撕裂强度明显降低。
但过硫影响不大。
撕裂强度和填充体系的关系:随碳黑粒径的减小,撕裂强度增加。
结构度低的碳黑对撕裂强度的提高有利。
在天然橡胶中增加高耐磨碳黑的用量,可以使撕裂强度增大。
在丁苯橡胶中增加高耐磨碳黑的用量(60-70份),出现最大值,然后逐渐下降。
一般合成橡胶特别是丁基橡胶,使用碳黑补强时,都可以明显的提高撕裂强度。
使用各向同性的补强填充剂,如碳黑,白碳黑,白艳华,立德粉和氧化锌等,可以获得较高的撕裂强度。
而使用各向异性的补强填充剂,如陶土,碳酸镁等则不能获得较高的撕裂强度。
某些偶联剂改性的无机填料,如用羧化聚丁二烯CPB改性的碳酸钙,氢氧化铝,也能提高丁苯橡胶的撕裂强度。
软化体系对撕裂强度的影响通常加入软化剂会使硫化胶的撕裂强度降低,尤其是石蜡油对丁苯橡胶硫化胶的撕裂强度极为不利。
而芳氢油则可以保证丁苯橡胶硫化胶的撕裂强度。
橡胶与各指标的关系
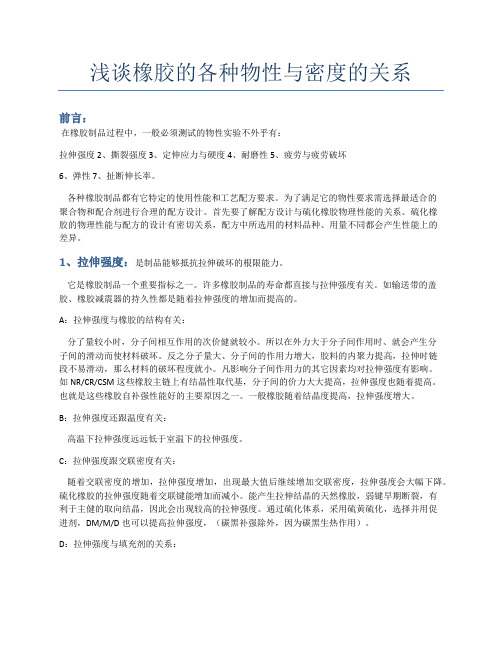
浅谈橡胶的各种物性与密度的关系前言:在橡胶制品过程中,一般必须测试的物性实验不外乎有:拉伸强度 2、撕裂强度 3、定伸应力与硬度 4、耐磨性 5、疲劳与疲劳破坏6、弹性7、扯断伸长率。
各种橡胶制品都有它特定的使用性能和工艺配方要求。
为了满足它的物性要求需选择最适合的聚合物和配合剂进行合理的配方设计。
首先要了解配方设计与硫化橡胶物理性能的关系。
硫化橡胶的物理性能与配方的设计有密切关系,配方中所选用的材料品种、用量不同都会产生性能上的差异。
1、拉伸强度:是制品能够抵抗拉伸破坏的根限能力。
它是橡胶制品一个重要指标之一。
许多橡胶制品的寿命都直接与拉伸强度有关。
如输送带的盖胶、橡胶减震器的持久性都是随着拉伸强度的增加而提高的。
A:拉伸强度与橡胶的结构有关:分了量较小时,分子间相互作用的次价健就较小。
所以在外力大于分子间作用时、就会产生分子间的滑动而使材料破坏。
反之分子量大、分子间的作用力增大,胶料的内聚力提高,拉伸时链段不易滑动,那么材料的破坏程度就小。
凡影响分子间作用力的其它因素均对拉伸强度有影响。
如NR/CR/CSM这些橡胶主链上有结晶性取代基,分子间的价力大大提高,拉伸强度也随着提高。
也就是这些橡胶自补强性能好的主要原因之一。
一般橡胶随着结晶度提高,拉伸强度增大。
B:拉伸强度还跟温度有关:高温下拉伸强度远远低于室温下的拉伸强度。
C:拉伸强度跟交联密度有关:随着交联密度的增加,拉伸强度增加,出现最大值后继续增加交联密度,拉伸强度会大幅下降。
硫化橡胶的拉伸强度随着交联键能增加而减小。
能产生拉伸结晶的天然橡胶,弱键早期断裂,有利于主健的取向结晶,因此会出现较高的拉伸强度。
通过硫化体系,采用硫黄硫化,选择并用促进剂,DM/M/D也可以提高拉伸强度,(碳黑补强除外,因为碳黑生热作用)。
D:拉伸强度与填充剂的关系:补强剂是影响拉伸强度的重要因素之一,填料的料径越小,比表面积越大、表面活性越大补强性能越好。
结晶橡胶的硫化胶,出现单调下降因为是自补强性非结晶橡胶如丁苯随着用量增加补强性能增加、过度使用会有下降趣向。
不同硫化体系对NR、NBR、EPDM硫化胶撕裂强度的影响

・ 8・
《 东橡 胶 》 2 0 广 第 6期 0 6年
不 同硫 化 体 系对 N 、N R P M R B 、E D
硫化胶撕裂强度的影 响
吴 向东 缪桂 韶
( 华南理工大学高分予系,50 4 ) 16 1 N 是人们最早使用的橡胶,同时又是理 R 论上研究得最多的橡胶,在很多教科书以及 专著中, 往往是以N 为代表, R 对橡胶的性能、 配方、 加工工艺等方面进行叙述。 随着科技的 进步, 很多性能、 用途各异的橡胶种类已被合 成 。由于它 们 的化学组 成 、 构不 同,表现 出 结 在物理性能、配方、加工工艺等方面与 N 有 R 很多的不 同之处。这些差异在很多文献资料 中亦有所叙述。但对不同硫化体对不同种类 橡胶 的 撕裂 强度 的影 响未 见详 细 的报道 。本
由表 1 以看到 , 硫磺 一Fra bibliotek进剂 硫化 的 可 用 N , 化胶无 论 是直 角型 撕裂强 度 , 是裤型 R硫 还
化物 的基 础上 加入 少 量硫 磺 ,其 撕裂 强度 并
撕裂强度 , 比过氧化物交联高得多。 都 在过氧
没有得到改善。 硫磺 一促进剂 交联 的天然 胶硫 化胶 具有
双键上地碳原子无推 电子地 甲基存在, B 中 NR 丁二烯链节上的二个 G 一次甲基上的氢原子 c
具 有相 同 的反 应活 性 ,双 键上 亦 可 以进行 加
5,萜烯树脂 3 0 ,环烷油 4 5 E I 硫磺 15 P: .,促进剂 C ,促进剂 Z1 D ,促进剂 T .,促进剂 B MI T 15 Z1
N R2: C 1. D P 5
硫 磺三种硫 化 体系交 联 N 、N R PM R B 、ED ,并
对试验结果作出初步的解释,以期引起更深 入的研究探讨 。
橡胶并用知识
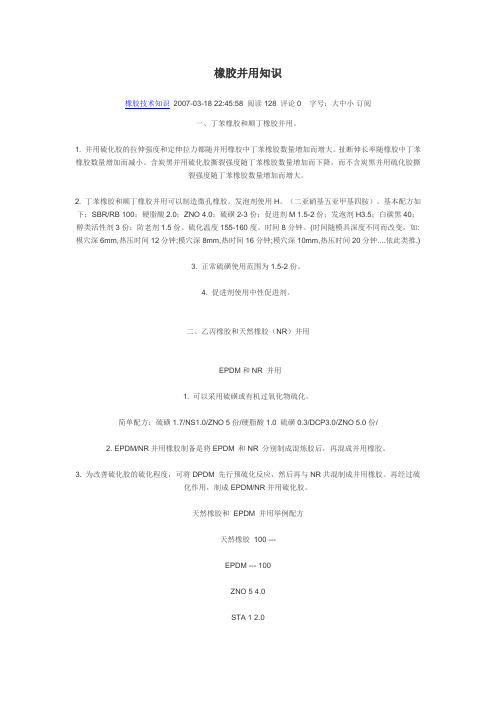
橡胶并用知识橡胶技术知识2007-03-18 22:45:58 阅读128 评论0 字号:大中小订阅一、丁苯橡胶和顺丁橡胶并用。
1. 并用硫化胶的拉伸强度和定伸拉力都随并用橡胶中丁苯橡胶数量增加而增大。
扯断伸长率随橡胶中丁苯橡胶数量增加而减小。
含炭黑并用硫化胶撕裂强度随丁苯橡胶数量增加而下降,而不含炭黑并用硫化胶撕裂强度随丁苯橡胶数量增加而增大。
2. 丁苯橡胶和顺丁橡胶并用可以制造微孔橡胶。
发泡剂使用H。
(二亚硝基五亚甲基四胺)。
基本配方如下:SBR/RB 100;硬脂酸2.0;ZNO 4.0;硫磺2-3份;促进剂M 1.5-2份;发泡剂H3.5;白碳黑40;醇类活性剂3份;防老剂1.5份。
硫化温度155-160度。
时间8分钟。
(时间随模具深度不同而改变,如:模穴深6mm,热压时间12分钟;模穴深8mm,热时间16分钟;模穴深10mm,热压时间20分钟....依此类推.)3. 正常硫磺使用范围为1.5-2份。
4. 促进剂使用中性促进剂。
二、乙丙橡胶和天然橡胶(NR)并用· EPDM和NR 并用1. 可以采用硫磺或有机过氧化物硫化。
简单配方:硫磺1.7/NS1.0/ZNO 5份/硬脂酸1.0 硫磺0.3/DCP3.0/ZNO 5.0份/2. EPDM/NR并用橡胶制备是将EPDM 和NR 分别制成混炼胶后,再混成并用橡胶。
3. 为改善硫化胶的硫化程度,可将DPDM 先行预硫化反应,然后再与NR共混制成并用橡胶。
再经过硫化作用,制成EPDM/NR并用硫化胶。
天然橡胶和EPDM 并用举例配方天然橡胶100 ---EPDM --- 100ZNO 5 4.0STA 1 2.0加工油1-5 1-5碳黑50 50硫磺 2.5 1.5MBTS 0.6 0.6TMTD 0.2 1.0例如:EPDM 与NR 配方中,EPDM 经过160度15分钟预硫化后与NR 制成50:50并用橡胶,拉伸强度可以达到17.4MPA。
硫化橡胶的定伸强度和拉伸扯断强度设计
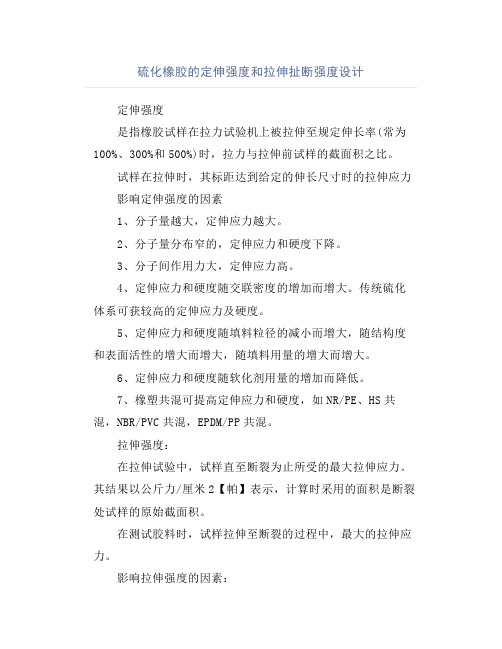
硫化橡胶的定伸强度和拉伸扯断强度设计定伸强度是指橡胶试样在拉力试验机上被拉伸至规定伸长率(常为100%、300%和500%)时,拉力与拉伸前试样的截面积之比。
试样在拉伸时,其标距达到给定的伸长尺寸时的拉伸应力影响定伸强度的因素1、分子量越大,定伸应力越大。
2、分子量分布窄的,定伸应力和硬度下降。
3、分子间作用力大,定伸应力高。
4、定伸应力和硬度随交联密度的增加而增大。
传统硫化体系可获较高的定伸应力及硬度。
5、定伸应力和硬度随填料粒径的减小而增大,随结构度和表面活性的增大而增大,随填料用量的增大而增大。
6、定伸应力和硬度随软化剂用量的增加而降低。
7、橡塑共混可提高定伸应力和硬度,如NR/PE、HS共混,NBR/PVC共混,EPDM/PP共混。
拉伸强度:在拉伸试验中,试样直至断裂为止所受的最大拉伸应力。
其结果以公斤力/厘米2【帕】表示,计算时采用的面积是断裂处试样的原始截面积。
在测试胶料时,试样拉伸至断裂的过程中,最大的拉伸应力。
影响拉伸强度的因素:1、分子量小的橡胶拉伸强度随分子量的增大而增大。
一般分子量在30-35万之间的橡胶拉伸强度最佳。
2、分子量分布窄的拉伸强度较高。
3、主链上有极性取代基时,拉伸强度随分子间的作用力增加而增加。
如丁腈橡胶中,丙烯腈含量增加拉伸强增加。
4、随橡胶结晶度的提高拉伸强度增加。
如NR、CR、CSM、IIR有较高的拉伸强度。
5、橡胶分子链取向后,平行方向的拉伸强度增加,垂直方向的拉伸强度下降。
6、拉伸强度随交联键能的增加而减小,随交联密度的增加而出现峰值。
交联键类型与拉伸强度关系按下列顺序递减:离子键——多硫键——双硫键——单硫键——碳碳键7、炭黑粒子小的而结构性低(如低结构的高耐磨)、表面含氧基团多的(如槽黑)其拉伸强度、撕裂强度、伸长率高。
8、填料的粒子小,表面积大,表面活性大,则补强效果好。
至于结构性与拉伸强度的关系说法不一,结晶橡胶的结构性高的对拉伸强度反而不利,但对非结晶橡胶则相反。
青岛科技大学橡胶配方设计期末考试复习题及参考答案(见后)

橡胶配方设计(C卷)(考生注意:答案写在答题纸上,写在试题纸上无效)一、选择题:(共5小题,含多项每题3分,共15分)1.符合生产使用要求的质量配方称为oA.基础配方B.性能配方C.实用配方D.生产配方2.为了取得足够长的加工安全性,尽量选用和临界温度较的促进剂。
A.高B.低C.超速级D.迟效性3.试为下列产品选择最佳的橡胶种类:浇铸轮胎、轿车子午胎胎侧胶、耐油胶管、防水卷材oΛ.丁脂橡胶NBR B.三元乙丙橡胶EPDM C.聚氨酯PlJD.NR/EPDM/CIIR4.未硫化橡胶加工性能的测试项目主要有混炼胶的流动性、均匀程度、、和应力松弛等。
A.门尼焦烧B.硬度C.回弹性D.硫化特性5.下列配方设计方法中属于多因素变量设计的是βΛ.黄金分割法 B.平分法C.正交试验法D.分批试验法二、判断题:(共10小题,每题2分,共20分)1.加入适量的固马隆或酚醛树脂,能够提高硫化胶的拉伸强度。
( )2.在正常范围内,硫化胶的定伸应力和硬度随着交联密度的增加先增大后降低。
( )3.下列几种生胶的弹性高低关系为:NR>SBR>BR>EPDM o( )4.不光滑路面的磨耗以卷曲、疲劳磨耗为主,而光滑路面上的磨耗以磨损磨耗为主。
( )5.水封、油封等制品,通常采用适当的表面处理方法来进一步提高制品的耐磨性。
( )6.混炼、压延时胶料的包辐性主要取决于混炼胶的强度、辐温和切变速率。
( )7.不同硫黄硫化体系的抗硫化返原性由高到低的顺序为:EV>SEV>CV o( )8.填料的酸碱性会影响到胶料焦烧特性,通常碱性填料会延迟硫化。
( )9.为提高硫化胶的弹性,应选用粒径小、结构度高的炭黑。
( )10.含胶率高的胶料,弹性复原大,压延后胶片收缩大。
( )三、简答题:(共3小题,每题15分,共45分)1.橡胶配方设计的特点有哪些?2.影响硫化胶撕裂强度大小的因素有哪些?3.试分析如何从配方设计上对挤出胀大现象进行改善?四、综合题(共1小题,共20分)1.某油封制品的配方如下表所示,该胶料的密度为L15g∕c∏Λ试计算出胶料的含胶率、混炼胶的质量成本和体积成本?一、选择题:(共5小题,每题3分,共15分)1.D2.D,A3.C,D,Λ,B4.A,D5.C二、判断题:(共10小题,每题2分,共20分)1-5.√√××√6-10.√√××√三、简答题:(共3小题,每题15分,共45分)1.橡胶配方设计的特点有哪些?答案要点:1)橡胶配方设计是多因素的试验问题;3分2)橡胶配方设计是水平数不等的试验问题;3分3)橡胶配方中各种原材料之间的交互作用较多且强烈;3分4)工艺因素有时对橡胶配方设计其决定性作用;2分5)橡胶配方设计中尽力排除实验误差;2分6)配方经验规律与统计数学相结合。
硫化用量对SIBR性能的影响

98在1984年Nordsiek [1]提出集成橡胶概念,即通过分子设计把几种橡胶的特点集于一身后,1985年德国Hüls公司首先开发成功苯乙烯-异戊二烯-丁二烯共聚橡胶(SIBR)并实现工业化,商品名为Vestogral;1990年美国Goodyear公司亦开始研究SIBR,翌年投入生产,商品名为Cyber [2]。
二者都主要用于全天候、长寿命高速轮胎。
集成橡胶SIBR作为一种新型的主要用于轮胎胎面的合成橡胶,是迄今为止性能最为全面的聚二烯烃类橡胶[3]。
其显著特点是分子链由多种结构的链段构成,不同结构的链段提供给橡胶不同的性能。
这样,集成橡胶SIBR 集成了各种橡胶的优点而弥补了各种橡胶的不足,同时满足了轮胎胎面对全天候、长寿命和经济性的要求,集成橡胶的这些优点使它至今仍是科研人员研究的热点[4-6]。
中国石化北京化工研究院燕山分院结合自己的技术优势和特点,采用一步加料法合成SIBR。
在模试和中试装置上进行了大量的基础研究,合成出了物理机械性能和动态力学性能均较突出的集成橡胶并申请了多项专利,还成功开发出了工业化牌号SIBR2505和SIBR2535。
集成橡胶具有优异的动态力学性能和较好的物理机械性能是其他胶种无法比拟的,完全满足胎面用胶要求具有优异的抗湿滑性能和低滚动阻力性能的需求,从而将促进高速公路网的蓬勃发展。
SIBR的成功开发也将进一步解决我国碳五资源的综合利用问题。
本工作主要研究了在硫磺硫化体系下,不同硫磺用量对SIBR的加工性能、硫化特性及硫化胶的物理机械性能、动态力学性能,以及老化性能的影响规律。
1 实验部分1.1 配方生胶SIBR 100份[S/I/B=20/40/40(质量百分比)];炭黑N330 65份;氧化锌 4份;硬脂酸 2份;防老剂 4.5份;芳烃油 10份;其他 1.7份;促进剂NS 1.4份;硫磺1.4~2.0份。
1.2 混炼工艺一段工艺:1.57L Farril密炼机,温度80℃ 、转速 80r/min。
EPDM硫化体系

三元乙丙混炼胶(EPDM)硫磺硫化体系EPDM的硫黄硫化优化,需要解决的问题是喷霜和硫化速度以及物理机械性能优劣的综合平衡。
有文献指出,TRA0.75/BZ1.5/M0.5/S 1.5[1];M1.0/BZ1.4/TMTD0.6/Px0.3/S1.5;M0.5/TMTD0.3/Px0.8/OTOS0.5/S1.5;M0.5/TMTD0.3/Px0.8/DTDM0.5/S1.5[2](均为质量份)等体系不喷霜。
本文在前人研究的基础上,针对EPDM的硫黄硫化体系中常用的促进剂种类的挑选、促进剂并用对EPDM硫化胶物理机械性能和喷霜的影响作了一些初步探索,并与上述文献所列硫化体系进行对比实验,试图研制出综合性能较好的配方,并模索出EPDM硫黄硫化体系优化设计的思路。
N T A-u:s b }1 实验1B l5Q9e(g H1 .1 原材料EPDM,荷兰DSM公司K512×50(充油50%);ZBPD,广州联腾橡塑商贸有限公司提供(产地:美国);其他均为橡胶工业常用的原材料和助剂。
:u5H6Z U.E 1 .2 主要设备及仪器6z b4X P YXSK 160型开放式炼胶机(上海第一橡胶机械厂),QLBD400×400电热平板硫化机(上海第一橡胶机械厂),P3555B2盘式硫化仪(北京环峰化工机械实验厂),XL 100型拉力实验机(广州广材实验仪器有限公司),LXA型邵氏橡胶硬度计(上海六中量仪厂),百分测厚仪(上海六菱仪器厂),101-2型烘箱(上海沪南科学仪器联营厂),401A型老化试验箱(上海市试验仪器总厂)。
&L z*O d"s c R1 .3 配方 Y _ F(D"v _ P'{/o-l1 .3 .1 母炼胶(份)EPDM150(含石蜡油50%);氧化锌5 0;硬脂酸1 0;防老剂1 7;高耐磨炉黑55;石蜡油30。
1 .3 .2 硫化体系硫化体系的设计见表1。
硫化橡胶的力学性能
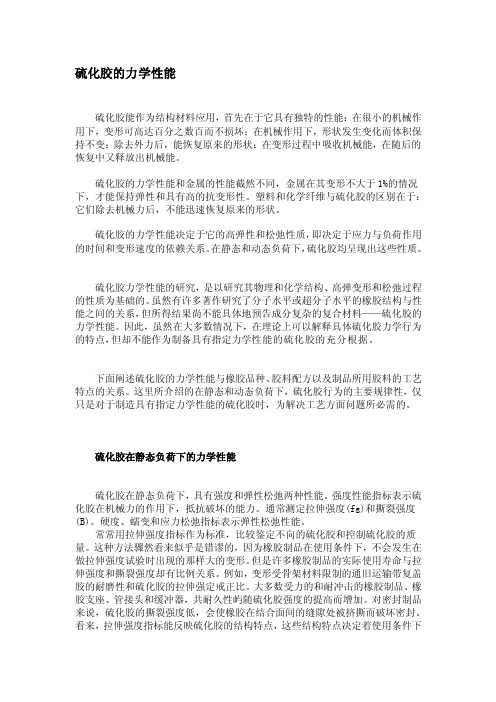
硫化胶的力学性能硫化胶能作为结构材料应用,首先在于它具有独特的性能:在很小的机械作用下,变形可高达百分之数百而不损坏;在机械作用下,形状发生变化而体积保持不变:除去外力后,能恢复原来的形状:在变形过程中吸收机械能,在随后的恢复中又释放出机械能。
硫化胶的力学性能和金属的性能截然不同,金属在其变形不大于1%的情况下,才能保持弹性和具有高的抗变形性。
塑料和化学纤维与硫化胶的区别在于:它们除去机械力后,不能迅速恢复原来的形状。
硫化胶的力学性能决定于它的高弹性和松弛性质,即决定于应力与负荷作用的时间和变形速度的依赖关系。
在静态和动态负荷下,硫化胶均呈现出这些性质。
硫化胶力学性能的研究,是以研究其物理和化学结构、高弹变形和松弛过程的性质为基础的。
虽然有许多著作研究了分子水平或超分子水平的橡胶结构与性能之间的关系,但所得结果尚不能具体地预告成分复杂的复合材料——硫化胶的力学性能。
因此,虽然在大多数情况下,在理论上可以解释具体硫化胶力学行为的特点,但却不能作为制备具有指定力学性能的硫化胶的充分根据。
下面阐述硫化胶的力学性能与橡胶品种、胶料配方以及制品所用胶料的工艺特点的关系。
这里所介绍的在静态和动态负荷下,硫化胶行为的主要规律性,仅只是对于制造具有指定力学性能的硫化胶时,为解决工艺方面问题所必需的。
硫化胶在静态负荷下的力学性能硫化胶在静态负荷下,具有强度和弹性松弛两种性能。
强度性能指标表示硫化胶在机械力的作用下,抵抗破坏的能力。
通常测定拉伸强度(fg)和撕裂强度(B)。
硬度、蠕变和应力松弛指标表示弹性松弛性能。
常常用拉伸强度指标作为标准,比较鉴定不向的硫化胶和控制硫化胶的质量。
这种方法骤然看来似乎是错谬的,因为橡胶制品在使用条件下,不会发生在做拉伸强度试验时出现的那样大的变形。
但是许多橡胶制品的实际使用寿命与拉伸强度和撕裂强度却有比例关系。
例如,变形受骨架材料限制的通旧运输带复盖胶的耐磨性和硫化胶的拉伸强定戒正比。
热硫化硅橡胶撕裂强度的影响因素探讨

术叙琏看料,2021,35(1):35〜41SILICONE MATERIAL 研究・开发热硫化硅橡胶撕裂强度的影响因素探讨詹学贵-2,张红岩1,刘洋洋S陈京1,胡盛S沃雪亮1(1.浙江新安化工集团股份有限公司,杭州310000;2.浙江新安进出口有限公司,杭州310000)摘要:以甲基乙烯基硅橡胶(生胶)为主要原料,添加气相法白炭黑、—基硅油、含氢硅油、硬脂酸等制得热硫化硅橡胶。
探讨了生胶、气相法白炭黑、多乙烯基硅油、四甲基二乙烯基二硅氮烷对热硫化硅橡胶性能的影响。
结果表明,当采用单一乙烯基摩尔分数的生胶时,随着生胶中乙烯基摩尔分数从0.05%提高到0.23%,二次硫化后的硅橡胶邵尔A硬度从55.5度升至76.5度,拉伸强度先由10.7MPa升至11.2MPa后再降至8.9MPa,拉断伸长率由540%逐渐降至260%;采用较高乙烯基含量的生胶与较低乙烯基含量的生胶并用时,能大幅提升硅橡胶的撕裂强度;随着气相法白炭黑N20用量从30份增加到55份,二次硫化后硅橡胶的邵尔A硬度由50度升至70度,拉伸强度由7.7MPa升至11MPa拉断伸长率先降后升再下降,撕裂强度在气相法白炭黑N20用量为40份时达到最大值26.3kN/m;在2种生胶并用的体系中,对于同一系列的气相法白炭黑来讲,随着气相法白炭黑比表面积的增加,硅橡胶的撕裂强度逐渐提高;随着多乙烯基硅油中乙烯基摩尔分数和用量的增加,硅橡胶的邵尔A硬度变化不明显,拉伸强度和撕裂强度均先升后降;随着四甲基二乙烯基二硅氮烷用量的增加,硅橡胶的邵尔A硬度变化不明显,拉伸强度和撕裂强度均先升后降。
当四甲基二乙烯基二硅氮烷用量为0.4份时,二次硫化后硅橡胶的撕裂强度达到最大值44.3kN/m&关键词:撕裂强度,多乙烯基硅油,四甲基二乙烯基二硅氮烷,硅橡胶,气相法白炭黑中图分类号:TQ333.93文献标识码:A doi:10.11941/j.issn.1009-4369.2021.01.006随着各行各业对有机硅材料的需求越来越大,有机硅产品的品种也越来越丰富。
您真的了解配方设计与硫化橡胶物理性能的关系

您真的了解配方设计与硫化橡胶物理性能的关系配方与各种物性之间的关系:各种橡胶制品都有它特定的使有用性能和工艺要求.为了满足它的物性要求需选择最适合的聚合物和配合剂进行合理的配方设计.首先要了解配方设计与硫化橡胶物理性能的关系.硫化橡胶的物理性能与配方的设计有密切关系,配方中所选用的材料品种、用量不同都会产生性能上的差异.一、拉伸强度拉伸强度是制品能够抵抗拉伸破坏的根限能力.它是橡胶制品一个重要指标之一.许多橡胶制品的寿命都直接与拉伸强度有关.如输送带的盖胶、橡胶减震器的持久性都是随着拉伸强度的增加而提高的.拉伸强度与橡胶的结构有关,分了量较小时,分子间相互作用的次价健就较小.所以在外力大于分子间作用时、就会产生分子间的滑动而使材料破坏.反之分子量大、分子间的作用力增大,胶料的内聚力提高,拉伸时链段不易滑动,那么材料的破坏程度就小.凡影响分子间作用力的其它因素均对拉伸强度有影响.如NR/CR/CSM这些橡胶主链上有结晶性取代基,分子间的价力大大提高,拉伸强度也随着提高.也就是这些橡胶自补强性能好的主要原因之一.一般橡胶随着结晶度提高,拉伸强度增大.拉伸强度还根温度有关,高温下拉伸强度远远低于室温下的拉伸强度.拉伸强度根交联密度有关,随着交联密度的增加,拉伸强度增加,出现最大值后继续增加交联密度,拉伸强度会大幅下降.硫化橡胶的拉伸强度随着交联键能增加而减小.能产生拉伸结晶的天然橡胶,弱键早期断裂,有利于主健的取向结晶,因此会出现较高的拉伸强度.通过硫化体系,采用硫黄硫化,选择并用促进剂,DM/M/D也可以提高拉伸强度,(碳黑补强除外,因为碳黑生热作用),拉伸强度与填充剂的关系,补强剂是影响拉伸强度的重要因素之一,填料的料径越小,比表面积越大、表面活性越大补强性能越好.结晶橡胶的硫化胶,出现单调下降因为是自补强性非结晶橡胶如丁苯随着用量增加补强性能增加、过度使用会有下降趣向.低不和橡胶随着用量的增加达到最在值可保持不变.拉伸强度与软化剂的关系加入软化剂会降低拉伸强度,但少量加入,一般在开练机7份以下,密练机在5份以下会改善分散,有利于提高拉伸强度.软化剂的不同对拉伸强度降低的程度也不同.一般天然橡胶适用于植物油类.非极性橡胶用芳烃油如SBR/IR/BR..如IIR/EPDM用石腊油、环烷油.NBR/CR用DBP/DOP.之类.提高拉伸强度的其它放法有,用橡胶与树脂共混、橡胶化学改性、填料表面改性(如加桂烷等)。
- 1、下载文档前请自行甄别文档内容的完整性,平台不提供额外的编辑、内容补充、找答案等附加服务。
- 2、"仅部分预览"的文档,不可在线预览部分如存在完整性等问题,可反馈申请退款(可完整预览的文档不适用该条件!)。
- 3、如文档侵犯您的权益,请联系客服反馈,我们会尽快为您处理(人工客服工作时间:9:00-18:30)。
配方设计与硫化胶撕裂强度的关系
撕裂强度是由于材料中的裂纹或裂口受力时迅速扩大开裂而导致破坏的现象。
各种橡胶(硫化胶)的撕裂强度:
天然橡胶NR>聚酯型热塑性弹性体>异戊橡胶IR>聚氨酯橡胶PUR>氯醇橡胶CO>丁晴橡胶NBR>丁基橡胶IIR>氯丁橡胶CR>氯磺化聚乙烯CSM>SBS热塑性弹性体>顺丁橡胶BR>丁苯橡胶SBR>三元乙丙橡胶EPDM>氟橡胶FKM>硅橡胶Q>丙烯酸酯橡胶ACM。
撕裂强度和硫化体系的关系:
撕裂强度和交联密度的关系有一个极大值,一般随交联密度的增加,撕裂强度增大,并出现一个极大值;然后随交联密度的增加,撕裂强度急剧下降。
和拉伸强度类似,但最佳撕裂强度的交联密度不拉伸强度达到最佳值的交联密度要低。
应采用硫磺-促进剂的传统硫化体系,硫磺用
量2。
0-3。
0份。
促进剂选用中等活性,平坦性好的品种,如DM,CZ等;过硫影响大。
在天然橡胶中,如果用有效硫化体系代替普通硫化体系时,撕裂强度明显降低。
但过硫影响
不大。
撕裂强度和填充体系的关系:
随碳黑粒径的减小,撕裂强度增加。
结构度低的碳黑对撕裂强度的提高有利。
在天然橡胶中增加高耐磨碳黑的用量,可以使撕裂强度增大。
在丁苯橡胶中增加高耐磨碳黑的用量(60-70份),出现最大值,然后逐渐下降。
一般合成橡胶特别是丁基橡胶,使用碳黑补强时,都可以明显的提高撕裂强度。
使用各向同性的补强填充剂,如碳黑,白碳黑,白艳华,立德粉和氧化锌等,可以获得较高
的撕裂强度。
而使用各向异性的补强填充剂,如陶土,碳酸镁等则不能获得较高的撕裂强度。
某些偶联剂改性的无机填料,如用羧化聚丁二烯CPB改性的碳酸钙,氢氧化铝,也能提高丁苯
橡胶的撕裂强度。
软化体系对撕裂强度的影响通常加入软化剂会使硫化胶的撕裂强度降低,尤其是石蜡油对丁苯橡胶硫化胶的撕裂强度极为不利。
而芳氢油则可以保证丁苯橡胶硫化胶的撕裂强度。
采用石油系软化剂作为丁晴橡胶和氯丁橡胶的软化剂时,应使用芳氢含量高于50-60%的高
芳氢油,而不能使用石蜡。