CAS-OB精炼和连铸过程钢中夹杂物来源示踪研究
轴承钢点状夹杂物成因及消除机理的探讨

第5卷第4期材 料 与 冶 金 学 报V ol 15N o 14 收稿日期:2006-05-08.作者简介:徐世铮(1937-),男,黑龙江哈尔滨人,苏联技术科学博士,东北大学教授.2006年12月Jour nal ofM ateria ls andM eta ll u rgyD ec .2006轴承钢点状夹杂物成因及消除机理的探讨徐世铮,马晓禾,赵卫东(东北大学 材料与冶金学院,沈阳110004)摘 要:轴承钢点状夹杂物严重影响钢的疲劳寿命.半个世纪以来,冶金工作者研究在精炼过程中如何消除轴承钢点状夹杂物.通过研究首次指出,精炼过程由渣中还原进入钢液中的钙是生成点状夹杂物的主要原因;并且从理论上分析用氯去除钢液中钙的工艺原理.关键词:轴承钢;点状夹杂物中图分类号:TF 76214 文献标识码:A 文章编号:1671-6620(2006)04-0250-03For mati on of globul ar incl usions i nbearing steel and their re m oval m echanis mXU Sh-i zheng ,MA X iao -he ,Z HAO W e-i dong(School ofM ateri als and M etall u rgy ,Northeastern Un ivers i ty ,Sh enyang 110004,Ch i n a)Ab stract :The for m ation of g l obu l ar i ncl usions i n bear i ng stee l i nfl uences seriously the fa tigue strength o f t he stee.l In t he pa rt ha lf o f a cen t ury ,m etall urg ists have m ade a l ot of st udies on the re m oval o f the globu l ar i nclusi on i n bear i ng stee l i n the process of refi n i ng .T his paper po i nted out t hat the m ain or i g i nati on o f t he i nclusi on i s fro m the reducti on of ca l c i u m from slag.The re fi ning process f o r the remova l o f [C a]is theo re ti ca lly ill ustra ted .K ey w ords :beari ng stee;l g l obu lar i ncl usion轴承钢是制造金属轴承的原料.检验轴承钢质量的主要项目是接触疲劳强度和冲击韧性,对其影响最大的是钢中[O ]、[H ]以及夹杂物的种类和数量、尺寸、分布,其中氧化物夹杂A l 2O 3和点状夹杂物)))m Ca O #n A l 2O 3对钢的疲劳强度危害最大[1].在轴承钢轧制过程,点状夹杂物沿着轧制轴向,使钢材产生裂纹.在轴承实验过程,这些裂纹导致零件破损.对于钢中点状夹杂物的成因,有许多学说,诸如在出钢过程炉渣混入钢液、炉渣中(Fe O )、[O]、[H ]及炉渣碱度过高等.半个多世纪以来,为消除轴承钢点状夹杂物研究采用合成渣洗,电炉电石渣)))白渣同炉渣洗,出钢前加大插铝量,电炉钢液钢包吹氩,钢包钢液真空吹氩,RH,DH 精炼轴承钢,VAD 精炼轴承钢,ASEA -SKF 精炼轴承钢,LF-VD 精炼轴承钢,钢包喷Ca-S i 粉,钢包喷A l-S i 粉.由于未能对生成点状夹杂物机理有一个理论说法.使得去除点状夹杂物的精炼工艺效果不佳.因此,本文从热力学角度来分析点状夹杂物在精炼过程的成因,并由此制订出相应的合理精炼工艺.1 在精炼轴承钢过程中,[Ca]在生成点状夹杂物的作用多年精炼轴承钢实践得知,在强还原条件下,渣中Ca O 被还原进入钢液[Ca].为从热力学角度计算,给出轴承钢成分及炉渣成分相关数据,列于表1,表2.计算炉渣组元活度是采用全电子系炉渣理论完成计算的[2].计算渣中各元素原子活度系数U i :U i =Ekj=1X j e-E ij/RT-1(1)式中,k )渣中组元数;E ij )置换能,kJ.计算出:U(A l)=21331;U(Ca)=21410.[A l]+3/4O2y(A l O115)l g K p=37790/T-81457K p1873=51025#1011k A l=X(A l)#U(A l)/A[A l]#p M A l/4O2(2) p3/4O2=X(A l)U(A l)/A[A l]#k A l=11044#10-11p O2=2128#10-10Pa,[O]=0100012%[C a]+1/2O2y(C a O)k(Ca)=X(Ca)#U(C a)/A[C a]#p M(Ca)/4O2(3)l g K p=37197/T-712K1873=4157#1012计算得出:a[Ca]=2#10-6,[Ca]=5#10-6%表1GC r15S M i n钢成分及相关数据Tab le1Composition and re lated data o f GCr15S M i n st ee lC S i M n C r P S Ca A l H O Fe质量分数/%1100015011001150010201010100201030100050100395193相对原子质量122855523132402811656摩尔分数4145@10-2917@10-3917@10-3116@10-2315@10-41166@10-4217@10-5519@10-41134@10-41101@10-40191f[i]113661174113501686112991139911251a[i]113360187113511029010026010420100061p*i /Pa116@10-76102@10-1518@10373131186@1052161@10226p i /Pa212@10-752718@10324418@1021126表2精炼轴承钢炉渣成分及相关数据Tab l e2Co m position o f slag and re la t ed da t aCaO S i O2M gO A l2O3F e O M nO CaF2S O质量分数/%4217817144141812012901760124315013摩尔分数Xi011920106901088010940100301001010210100201552 Mi242322由1873K降至1773K,氧分压由21281# 10-10Pa降至612#10-12Pa.则w[Ca]由5# 10-6%降至211#10-6%.得出钢液降温100e 时,钢中钙由于脱氧能力的提高,58%的[Ca]将与[O]反应生成CaO.其将在钢液内残留的刚玉或外来夹杂物这些现成表面上析出,形成m Ca O #n A l2O3.随钢液温度降低还有反应[H]y1/2 {H2}也将在上述现成表面上析出,而强化了液态点状夹杂物聚集长大.上述分析得出,要降低[C a],一是降低渣中(Ca O)的量,也就是降低炉渣碱度,但不能完全去除点状夹杂;另一种办法就是去除[Ca].2氯化法去除钢液中的钙采用氩气做载体,向钢液内吹入氩氯混合气体.当气泡上升至钢液表面,气泡与钢液相处于平衡状态,此时气泡内的总压力为110@105Pa.气泡内各组分的分压间关系为:E p M eCl+E p M e+p C l2+p A r=110@105Pa(4)因为氩不参与反应,初始气泡中p i C l2=110@105 -p A r,Pa.喷入钢液的氩氯气泡上浮达钢液表面时,气泡内将含有C l2、Ca、CaC l2、A l、A l C l3、C r、Cr C l3、M n、M nC l2、S i、Si C l4、C、CC l4、H2、H C l、Fe、Fe C l2.钢液中各元素与氯反应为:[Ca]+C l2y C a C l2(g)K1873=3184#1016[A l]+3/2C l2y A l C l3(g)K1873=6139#109[S i]+2C l4y S i C l4(g)K1873=3133@105[M n]+C l2y M nC l2(g)K1873=1105#106[C]+2C l2y CC l4(g)K1873=1146#106[H]+1/2C l2y H C l(g)K1873=3170#105[Fe]+C l2y FeC l2(g)K1873=6171#103将初始氯分压p i Cl定为310@104Pa情况下,平衡各分压计算值如表3:251第4期徐世铮等:轴承钢点状夹杂物成因及消除机理的探讨表3氯化产物平衡分压值Tab l e3Equ ili b rium pa rtia l p ressures of ch lo ride products Pap C l2pC a C l2pHC lpM nC l2pFeC l2pAlC l3pC r C l2pSiC l4219#10-10219#1041124#10-4119#10-6411#10-9110#10-9217#10-19由上表可见,钢液中各元素氯化次序为:Ca y H y M n y Fe y A l y C r y Si钙是优先氯化的元素,采用氯化去除是可行的.3精炼工艺参数的确定311加氯方式的选择氯化脱除钢液中钙的工艺,可在RH、DH、VAD、LF-VD精炼轴承钢过程中实施.为考虑首次工业性实验简便可行而选用SL钢包喷粉.312氯进入钢液的方式采用卤化物-氧化物合成粉剂[3](其成分见表4),用氩气做载体,经SL喷粉罐-喷枪,喷入钢包.表4合成粉剂成分Tab l e4Co m position o f compound powde r%CaO S i O2A l2O3M gO质量分数38~5812~157~127~11CaF2F eO CC l4质量分数5~7<0155~515粉剂粒度平均直径为01165mm.313卤化物配入量及卤化物合成粉剂用量计算按钢液中w[C a]=01002%计算[Ca]+C l2y C a C l2401m o l20015m o l每吨钢去除20g钙需015m o lC l2.采用CC l4分解生成C l2去除[Ca].炼钢温度下CC l4分解完全.每吨钢需用0125 m o lCC l4,即3815g,考虑到钢中其他元素氯化耗氯,配入50~60g CC l4/t为考虑,初始p i C l2为3#10-4Pa计,氩气用量为350~420L/.t在氧化物粉剂[3]中配入515%CC l4时,卤化物合成粉剂用量为1~111kg/.t若配入量为3%CC l4时,粉剂用量为117~2kg/.t供氩速度v A r=50~70L/m i n.钢液开喷温度为1600e时,吹毕温度为1520~1510e,可喷吹6~7m i n;喷吹时间依据出钢温度相应调整.314喷粉喉口临界速度从动力学角度出发,研究在炼钢温度条件下,为保证喷入钢液的气粉流中,粉剂不侵入钢液而导出粉剂在喷嘴喉口的临界速度v c.v c=8g(Q s/Q p-1)+12R/r Q p3(k Q s/Q p-1)1/2#(e R(Q s/Q p-1)-1)1/2(5)式中:Q s,Q p为钢液、粉剂密度,kg/m3;r为粉剂中平均粉粒半径,m;R为粉剂与钢液间界面张力, N/m;k为粉粒在钢液中阻力系数.将下列数据代入(5)式Q s=6800kg/m3,Q p=3410kg/m3,R=1152 N/m,k=113,得出临界速度:v c=(163138+01479r+1112#10-2/r)1/2,m/s(6) 4结语从热力学角度分析,在炼钢温度下当p O2[ 213#10-10Pa的条件下,促使渣中Ca O被还原成钙进入钢液中.精炼后随钢液温度降低,钢液中钙的脱氧能力提高,在w[C a]有01002%时,有58%的[Ca]参加脱氧反应生成初生C a O,又有反应2[H]y{H2},同时在钢液中现存夹杂物表面同时析出并长大,形成了m Ca O#n A l2O3点状夹杂物.热力学分析得出,用氯去除钢液中钙的可能性和合理性.对采用氯去除钢中钙的精炼工艺及相应的工艺参数进行了必要的理论分析和研究,为精炼工艺的制定提供依据.参考文献:[1] . . Å»¼À, . . Å»¼À. ¶ÀºѺĶǿÀ½À´ºÑϽ¶¼ÄÂÀ½½±³¼ºÃı½Î[M]. ºË±Ê¼À½±.1983.179-192. [2] . . º´ÀÂÑ¿. . . ¶½Ñ¿Éº¼À³. .¡. ÄÀ¾±Çº¿ . .À¿À¾±Â¶¿¼À. ¶Àºĺɶüº ÿÀ³Í½¶¼ÄÂÀÃı½¶Á½±³º½Î¿ÍÇ ÂÀȶÃÃÀ³[M]. ¶Ä±½½ÅÂĺÑ,Àü³±.1987.8-89.[3]徐世铮,刘沛环,刑玉录,等.喷射冶金用合成粉剂及其制造工艺:中国,8510031.1[P].1988.252材料与冶金学报第5卷。
CAS—OB简介(连铸工艺附件)
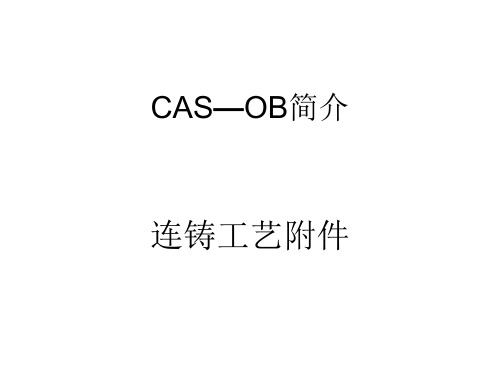
特点:RH-KTB法在真空脱气的同时,吹氧进行脱 碳,以生产碳含量极低( [C]≤0.0020%(20ppm》 的超深冲用薄板钢。吹氧二次燃烧所产生的化学 热还可用于钢水升温。与RH-OB热补偿工艺相比, RH-KTB工艺有如下优点:
●成本低,不需要额外热源;
●生产效率高,不需要额外延长处理时,KC↑; ●在吹氧脱碳期,炉气二次燃OB是在CAS的基础上发展起来 的。 • 它在隔离罩内增设了氧枪吹氧,利用 加入的铝和硅铁与氧反应所放出的热 量直接对钢水加热,其目的为转炉钢 水进行快速升温,补偿CAS法工序的 温降,为中间包内钢水提供准确的目 标温度,使转炉和连铸协调配合。
工艺原理
• 2Al+3/2O2===Al2O3+30932kJ/kg • Si+O2===SiO2+29260kJ/kg • C+1/2O2===CO+9209kJ/kg • CO+1/2O2====CO2+23567kJ/kg
RH+IJ ( RH-IJ法/ RH-injection ) RH-IJ法由日本新日铁于1985年提出 的钢液进行RH处理的同时进行喷粉的工艺 方法。 ①工作原理及工艺过程:在进行RH处理过程 中,从真空室的外部向RH真空室上升管的 底部插一支喷枪,向即将上升到真空室的 钢水喷吹合成渣料,以达到深脱硫的目的。 渣料使用氩气携带。 (从RH上升管下方的喷枪吹入Ar或粉剂加 作为载气的Ar。脱S时,粉剂通常为CaO系 熔剂(CaO+CaF2)。
CAS—OB简介
连铸工艺附件
• CAS(Composition Adjustment by Sealed Argon Bubbing,就是密封 吹氩合金成分调整),是一种钢包 炉外处理手段。 • CAS基本功能:均匀钢液成分和温 度;调整钢水成分和温度(废钢降 温);提高合金收的率(特别是 铝));净化钢液,去除夹杂物。
连铸过程DC04钢中夹杂物的研究_彭其春
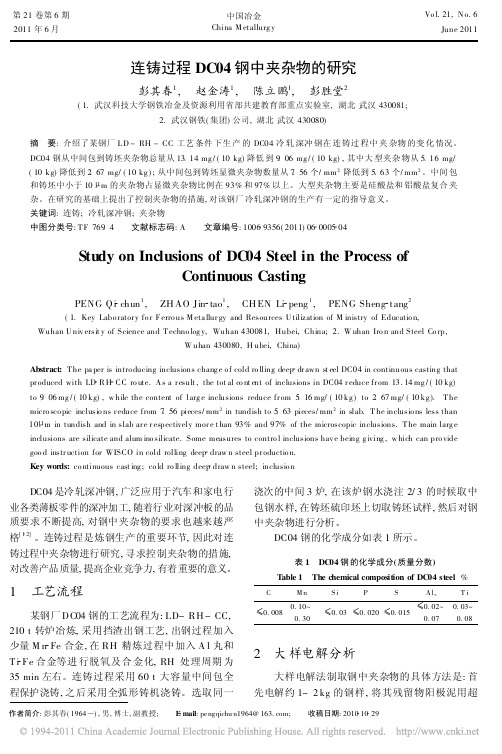
第21卷第6期 2011年6月中国冶金China M etallurg yVo l.21,N o.6June 2011连铸过程DC04钢中夹杂物的研究彭其春1, 赵金涛1, 陈立鹏1, 彭胜堂2(1.武汉科技大学钢铁冶金及资源利用省部共建教育部重点实验室,湖北武汉430081;2.武汉钢铁(集团)公司,湖北武汉430080)摘 要:介绍了某钢厂L D -RH -CC 工艺条件下生产的DC04冷轧深冲钢在连铸过程中夹杂物的变化情况。
DC04钢从中间包到铸坯夹杂物总量从13 14mg /(10kg)降低到9 06mg /(10kg),其中大型夹杂物从5 16mg/(10kg)降低到2 67mg/(10kg );从中间包到铸坯显微夹杂物数量从7 56个/mm 2降低到5 63个/mm 2。
中间包和铸坯中小于10 m 的夹杂物占显微夹杂物比例在93%和97%以上。
大型夹杂物主要是硅酸盐和铝酸盐复合夹杂。
在研究的基础上提出了控制夹杂物的措施,对该钢厂冷轧深冲钢的生产有一定的指导意义。
关键词:连铸;冷轧深冲钢;夹杂物中图分类号:T F 769 4 文献标志码:A 文章编号:1006 9356(2011)06 0005 04Study on Inclusions of DC 04Steel in the Process ofContinuous CastingPENG Qi chun 1, ZH AO Jin tao 1, CH EN Li peng 1, PENG Sheng tang 2(1.Key Labo rator y fo r F erro us M eta llur gy and Resources U tilization of M inistry of Educatio n,Wuhan U niv ersit y of Science and T echno log y,Wuhan 430081,Hubei,China; 2.W uhan Iro n and Steel Co rp,W uhan 430080,H ubei,China)Abstract:T he pa per is intro ducing inclusions chang e o f cold ro lling deep dr awn st eel DC04in continuous casting that pr oduced with LD R H CC ro ute.A s a r esult ,the tot al co nt ent of inclusions in DC04r educe fr om 13.14mg /(10kg)to 9 06mg /(10kg),w hile the content of larg e inclusions reduce fr om 5 16mg/(10kg )to 2 67mg/(10kg ) T he micro sco pic inclusio ns r educe from 7 56pieces/mm 2in tundish to 5 63pieces/mm 2in slab.T he inclusio ns less than 10 m in tundish and in slab ar e r espectively mor e t han 93%and 97%of the microscopic inclusions.T he main larg e inclusions are silicate and alum ino silicate.Some measures to contro l inclusions hav e being g iving ,w hich can pro vide goo d instr uction for WISCO in cold rolling deep draw n steel pr oductio n.Key words:co ntinuous cast ing ;co ld ro lling deep draw n steel;inclusio n作者简介:彭其春(1964 ),男,博士,副教授; E mail :pengqichu n1964@; 收稿日期:2010 10 29DC04是冷轧深冲钢,广泛应用于汽车和家电行业各类薄板零件的深冲加工,随着行业对深冲板的品质要求不断提高,对钢中夹杂物的要求也越来越严格[1 2]。
CAS-OB与LF在炉外精炼中应用的比较
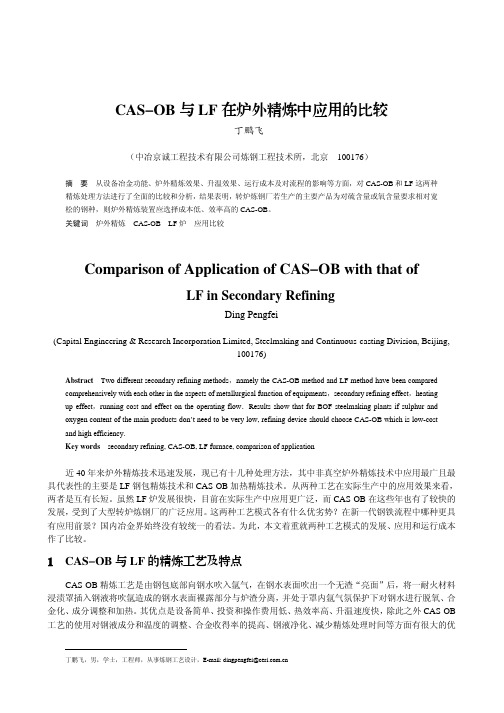
CAS-OB与LF在炉外精炼中应用的比较丁鹏飞(中冶京诚工程技术有限公司炼钢工程技术所,北京 100176)摘 要从设备冶金功能、炉外精炼效果、升温效果、运行成本及对流程的影响等方面,对CAS-OB和LF这两种精炼处理方法进行了全面的比较和分析,结果表明,转炉炼钢厂若生产的主要产品为对硫含量或氧含量要求相对宽松的钢种,则炉外精炼装置应选择成本低、效率高的CAS-OB。
关键词炉外精炼CAS-OB LF炉应用比较Comparison of Application of CAS-OB with that ofLF in Secondary RefiningDing Pengfei(Capital Engineering & Research Incorporation Limited, Steelmaking and Continuous-casting Division, Beijing,100176)Abstract Two different secondary refining methods,namely the CAS-OB method and LF method have been compared comprehensively with each other in the aspects of metallurgical function of equipments,secondary refining effect,heating up effect,running cost and effect on the operating flow.Results show that for BOF steelmaking plants if sulphur and oxygen content of the main products don’t need to be very low, refining device should choose CAS-OB which is low-cost and high efficiency.Key words secondary refining, CAS-OB, LF furnace, comparison of application近40年来炉外精炼技术迅速发展,现已有十几种处理方法,其中非真空炉外精炼技术中应用最广且最具代表性的主要是LF钢包精炼技术和CAS-OB加热精炼技术。
钢中非金属夹杂物来源分析
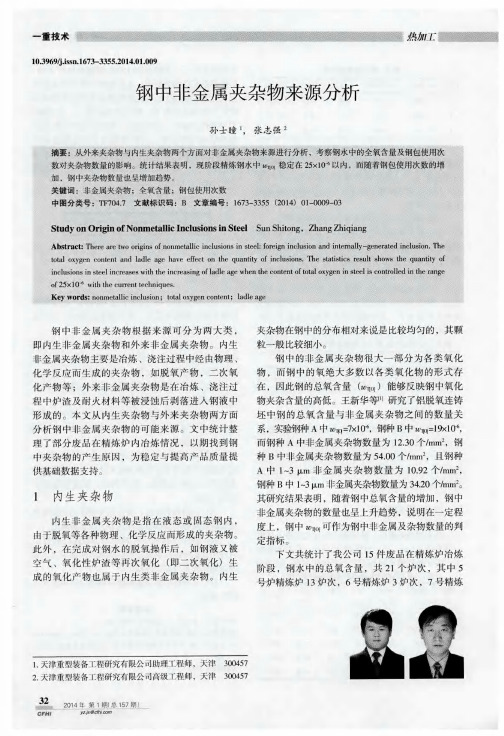
究钢 包使用 次数与钢 水 中夹 杂物之 间 的关 系[ 3 1 。
此次工业实验总共研究 了四类钢中铝脱氧前夹
杂 物数 量 随钢包 使用 次数 的变化 情 况 。从 试 验结果
6 号炉精炼数据统计中 ,钢包使用次数在 5 次以上
的 占了一 半 以上 。 现 阶段部 分 国外研 究结 果认 为钢 包釉 面是 钢包 冶炼 期 间影 响钢水 内非 金属 夹杂 物 的主要 原 因 。研
a g e o n f o r ma t i o n o f n o n — me t a l l i c i n c l u s i o n s i n l a d l e t r e a t me n t【 J 】. I r o n ma k i n g a n d S t e e l ma k i n g ,2 0 0 4 ,3 1( 3 ) :2 3 5  ̄ 2 4 0 . 收 稿 日期 :2 0 1 4 — 0 1 一 O 8
至几百微米 ,其组成较为复杂 ,通常是多种氧化物 的复合 ,而且这些夹杂物在钢 中分布 的偶然性很 大,甚至可能聚集成团 ,因而危害程度更大 。因 此 ,提高钢水洁净度 ,除通过脱氧和精炼操作最大 限度去 除脱 氧夹 杂物外 ,更 重要 的是 要 防止在 浇注
过 程 中 由二 次氧 化产 生大 颗粒 的夹 杂物 。 为 了进 一步 提高 钢水 的冶金 质量 ,应 加强 浇注
C F HI
2 o 1 4 年 第 期( 尊1 7 期)
y z j . s @c f h L c o r n
表2 5号炉 钢 包 使 用 次 数 统 计
夹杂。来源于釉面层的夹杂物数量将取决于釉层的 变化 ,因为随着钢包使用次数的增多 ,浸入耐火砖 内的渣量也将增加。上述研究结果认为 ,如果其它 参数保持不变 ,在冶炼相 同钢种时,操作条件不会
高效多功能CAS-OB精炼炉开发
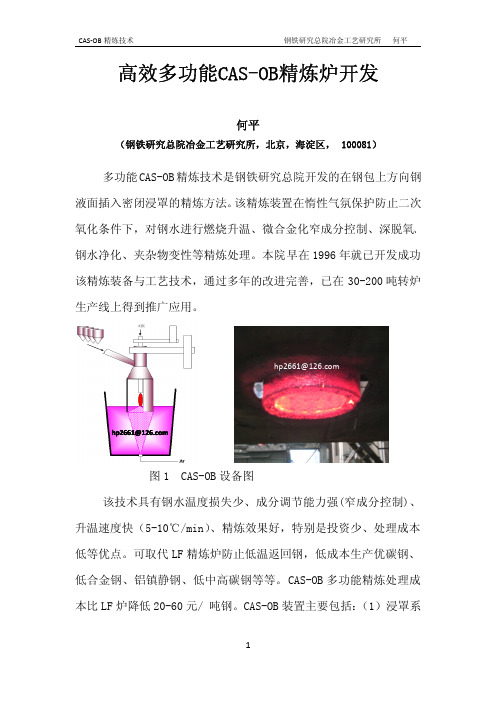
3
hp2661@
hp2661@
图 1 CAS-OB 设备图 该技术具有钢水温度损失少、成分调节能力强(窄成分控制)、 升温速度快(5-10℃/min) 、精炼效果好,特别是投资少、处理成本 低等优点。可取代 LF 精炼炉防止低温返回钢,低成本生产优碳钢、 低合金钢、铝镇静钢、低中高碳钢等等。CAS-OB 多功能精炼处理成 本比 LF 炉降低 20-60 元/ 吨钢。CAS-OB 装置主要包括: (1)浸罩系
1
CAS-OB 精炼技术
钢铁研究总院冶金工艺研究所
何平
统; (2)顶吹氧枪系统; (3)合金下料系统; (4)底吹氩系统; (5) 钢包车系统; (6)电气仪表阀门与计算机控制系统。该装置已获国家 专利。 多功能 CAS-OB 精炼周期短,在浸罩或密闭盖中惰性气氛的保护 下,完成合金成份微调和钢水的净化,可提高金属收得率和避免精炼 钢水氧化,有利于新品种开发和多钢种生产。由于精炼周期短,可在 线对钢水进行精炼处理,设备作业率高,处理能力大,可满足一般多 钢种精炼钢水的要求。多功能 CAS-OB 精炼炉与转炉和连铸流程在生 产节奏上匹配。多功能 CAS-OB 精炼炼炉具备以下精炼功能: � 底吹 Ar 气均匀钢成分、温度; � 满足多钢种精炼,进行合金微调,实现窄成分控制; � 提高钢水成分控制能力和铁合金收得率,降低铁合金消耗; � 大气量搅拌,提高脱氧效果,促进脱氧夹杂物聚合上浮; � 最大程度对钢水进行渣精炼处理; � 防止钢水二次氧化,减少钢水增氮量; � 与喂线机匹配(厂方配备喂线机) ,进行夹杂物变性处理; � 与钢包全程扣盖保温系统相配合,降低钢包散热量。 带 OB 升温功能的多功能 CAS-OB 精炼炉则是在无升温的多功能 CAS 精炼炉基础上增加了加发热剂丸吹氧燃烧升温功能的精炼技术。 OB 作为多功能 CAS-OB 精炼炉工艺的辅助手段,主要用于转炉在生产 中偶然出现低温钢水时采取的升温技术措施。带 OB 升温功能的多功 能 CAS-OB 精炼炉主要特点为:在浸罩内无渣或少渣的条件下或在密
连铸Ca处理钢水过程中夹杂物粘附浸入式水口的机理_井胜浩

为防止氧化铝在浸入式水口内壁的粘附, 以 前采取的办法是对钢水进行 Ca 处理。Ca 处理就 是把钢水中的 Al2O3 夹杂物改性为 CaO#Al2O3 液 态夹杂物, 防止其粘附在浸入式水口内壁上。但 如果 Al2O3 夹杂物的改性不充分, 浸入式水口的 堵塞现象反而会比没有进行 Ca 处理时的更严重, 这一点众所周知。但是, 过去主要是研究防止水 口堵塞的最佳 Ca 处理条件, 对钢水 Ca 处理后, 水 口迅速发生堵塞的机理几乎没有研究过。
钢中非金属夹杂物检测技术

●
沿铸坯厚度方向取试样,在金相显微镜F观察统计夹杂物分布如图2(b)所示。由图2(b)知,金相法得到与硫印 法相似的结果。 那么在铸坯厚度1/4左右夹杂物是由什么组成的呢?用金相法观察夹杂物,探针分析结果与浸入式水口内堵塞 物成分十分相似,见表4。由此可知,铸坯中大颗粒夹杂物是来源于浸入式水口堵塞物。这种以A1203为主的夹杂物 是造成冷轧薄板表面缺陷的主要原因。
●
试样大,电解时间长。为了捕捉更多的大型夹杂物,试样尺寸大(中50’60X 120’150mm),样重3’5kg,电 解时间15’20天。
・
使用物理方法分离碳化物。用淘洗法把碳化物淘洗掉,而夹杂物和铁的氧化物保留下来,用还原磁选把 夹杂物分离出来。
●
夹杂粒径分级和组成分析。 不足之处是不能完全保留云雾状的A1203夹杂。
・
●
●
下面把常用的几种方法简介如下:
3.1钢中非金属夹杂物评级法
有国家标准评级图,用于轧材或铸坯中夹杂物评级。评级图片是在100倍纵向抛光面上面积为0.5咖2视场。根 据夹杂物形态和分布,标准图谱分为A、B、C、D和Ds五大类。 A类(硫化物夹杂):延性好,长/宽比较大,夹杂物呈灰色; B类(氧化铝):不变形,带棱角,呈黑色粒状,沿轧制方向排列; C类(硅酸盐):延性好,长/宽比较大,夹杂物呈黑色或灰色; D类(球状氧化物):不变形,带棱角,长/宽比较小(<3),无规则分布,呈黑色或兰色。 Ds类(单颗粒球状):夹杂物呈圆形或近似圆形,直径大于13 ll 取样、制样和评级按规定标准(GB/T1056卜2005)执行。
・
(2)分析流程 大样电解主要用于分析钢9>50u nl大型氧化物夹杂。其分析流程主要包括电解、淘洗、还原和分离。分离出夹 杂物进行粒度分级、形貌照相和电子探针定量成分分析。大样电解分析流程如图5所示。 (3)大样电解设备 电解设备包括整流器(25V,20/I)、电解槽体、淘洗槽、还原磁选装置、体视显微镜、分级筛、称重天平和相机 等。 (4)大型夹杂物实例 下面介绍一下我们在某厂RH、中间包和连铸坯中大型夹杂物照片。图6为RH处理前后大颗粒夹杂物形貌相片。
连铸坯夹杂物产生原因分析及改进
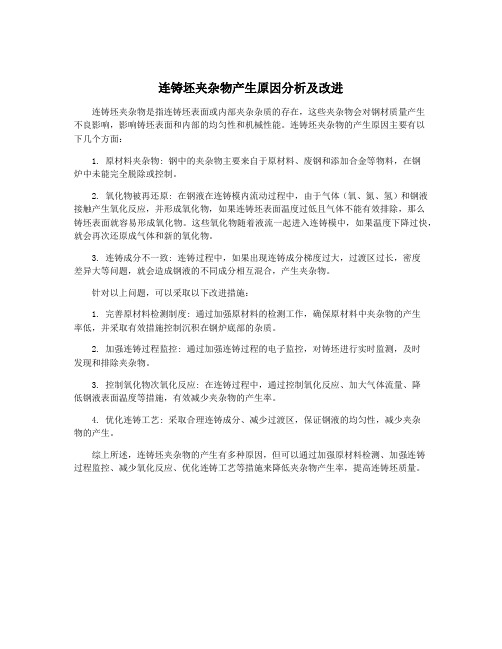
连铸坯夹杂物产生原因分析及改进
连铸坯夹杂物是指连铸坯表面或内部夹杂杂质的存在,这些夹杂物会对钢材质量产生
不良影响,影响铸坯表面和内部的均匀性和机械性能。
连铸坯夹杂物的产生原因主要有以
下几个方面:
1. 原材料夹杂物: 钢中的夹杂物主要来自于原材料、废钢和添加合金等物料,在钢
炉中未能完全脱除或控制。
2. 氧化物被再还原: 在钢液在连铸模内流动过程中,由于气体(氧、氮、氢)和钢液接触产生氧化反应,并形成氧化物,如果连铸坯表面温度过低且气体不能有效排除,那么
铸坯表面就容易形成氧化物。
这些氧化物随着液流一起进入连铸模中,如果温度下降过快,就会再次还原成气体和新的氧化物。
3. 连铸成分不一致: 连铸过程中,如果出现连铸成分梯度过大,过渡区过长,密度
差异大等问题,就会造成钢液的不同成分相互混合,产生夹杂物。
针对以上问题,可以采取以下改进措施:
1. 完善原材料检测制度: 通过加强原材料的检测工作,确保原材料中夹杂物的产生
率低,并采取有效措施控制沉积在钢炉底部的杂质。
2. 加强连铸过程监控: 通过加强连铸过程的电子监控,对铸坯进行实时监测,及时
发现和排除夹杂物。
3. 控制氧化物次氧化反应: 在连铸过程中,通过控制氧化反应、加大气体流量、降
低钢液表面温度等措施,有效减少夹杂物的产生率。
4. 优化连铸工艺: 采取合理连铸成分、减少过渡区,保证钢液的均匀性,减少夹杂
物的产生。
综上所述,连铸坯夹杂物的产生有多种原因,但可以通过加强原材料检测、加强连铸
过程监控、减少氧化反应、优化连铸工艺等措施来降低夹杂物产生率,提高连铸坯质量。
钢中硫化铁夹杂物析出原理_概述说明以及解释

钢中硫化铁夹杂物析出原理概述说明以及解释1. 引言1.1 概述在现代钢铁冶炼过程中,硫化铁夹杂物的析出对于钢材的质量和性能具有重要影响。
硫化铁夹杂物是由于钢中含有过多的硫元素而形成的一种微观结构,在钢材中分布不均匀,并且会导致钢材在使用过程中出现脆化、断裂等问题。
因此,深入研究硫化铁夹杂物析出原理及其相应的控制技术具有重要的理论和实际意义。
1.2 文章结构本文将围绕硫化铁夹杂物析出原理展开全面系统的阐述。
首先,我们将介绍硫化铁夹杂物的含义和特点,探讨其在钢铁材料中的重要作用。
然后,我们将概述硫化铁夹杂物析出原理,并解释其形成与演变机制。
进一步地,我们将介绍并分析影响硫化铁夹杂物析出过程的关键因素,从实验方法与表征手段上进行详细说明。
最后,我们将总结当前已取得的研究成果,并提出未来研究的方向与展望。
1.3 目的本文旨在深入探讨钢中硫化铁夹杂物析出原理,全面了解其形成机理和影响因素。
通过研究不同的控制技术和措施,实现对硫化铁夹杂物的有效控制,以提高钢材的质量和性能。
为此,我们将介绍当前已有的相关研究工作,并总结实践中所取得的成果。
同时,本文还将对未来的研究方向进行展望,为进一步深入研究该领域提供参考。
以上是“1. 引言”部分内容,请根据此内容撰写文章。
2. 钢中硫化铁夹杂物析出原理2.1 硫化铁夹杂物的含义和特点在钢中,硫化铁是一种常见的夹杂物。
硫化铁夹杂物指的是由铁与硫元素结合形成的硫化铁晶体,通常呈现出片状、条状或球状的形态。
这些夹杂物在钢中存在的主要原因是来自于原材料中的硫元素和工艺过程中的硫污染。
2.2 析出原理的概述硫化铁夹杂物析出是指在钢水冷却过程中,由于温度下降和相应成分变化,导致溶解在钢中的硫与其他元素结合生成硫化物并析出。
当钢水冷却至一定温度时,其中所含的溶解性硫会与流动态产生相互作用,并进而促使以二聚、多聚体形态析出出来。
这些形成的固相颗粒就是我们所说的硫化铁夹杂物。
2.3 解释硫化铁夹杂物析出影响因素造成钢中硫化铁夹杂物析出量和分布情况的因素有很多。
示踪剂试验观察钢中夹杂物

中 图分 类 号 : T F ' / 4 I 文献标志码 : B
Te s t Ob s e r v a t i o n o n I n c l u s i o n i n S t e e l wi t h Tr a c e r Ag e n t
p h o t o g r a p h i n g i n s p e c t i o n a n d S E M ,S O a s t o p r o v i d e t h e b a s i s f o r c o n t r o l l i n g t h e a p p e a i r n g o f i n c l u s i o n d u i r n g t h e s me l -
成 分进 行分 析 。 2 取样
取 样 时 机
钢 样 数 量 渣 样 数量
2 . 1 钢 水要 求
生 产两 炉钢 进行示 踪剂 试验 。钢水 炉号 分别
精炼取样 1 前 精 炼 白渣 后 L F 精炼结束 VD放散后 V D吊包前 汤 道样
2 2 2 ห้องสมุดไป่ตู้ 2 2
( 2 ) 中心 试验 室对 试样 采 用 镶嵌 法 进 行高 倍 分析 , 对 高倍 进行 拍 片后 报 出高倍 夹杂物 的数 量 、
大小 和形状 。
( 1 ) V D前 加入 B a C O , 每炉加 人量 2 0 k g 。 ( 2 ) 在保 护渣 中加人 C e C O , , 加入 量按保 护
律, 为 冶炼 实际操 作提供 依据 有着 重要 的意义 。
炉外精炼原理CAS-OB与IR-UT法

钢液送到中间包内,[N]为0.0022%。 ❖ ②中间包水口结瘤改善。两台铸机连浇炉数的统计表明,
CAS处理分别达56和100炉。 ❖ ③钢材质量提高。
5.7.2 CAS-OB法
CAS-OB法是CAS法的改进,增设顶氧枪。 为了快速补偿CAS法处理过程中的温降,在隔离罩内增设
5.7.2 CAS-OB法
1) 隔离罩(浸渍罩)
隔离罩的作用:隔离浮渣,形成无渣液面,并提供加
入微调合金空间,提高合金元素的收得率;容纳上浮的搅
拌氩气,提供氩气保护空间;为铝氧反应加热钢液提供反
应空间;收集和排出烟气(烟罩作用)。CAS-OB隔离罩
为锥形体。由钢板焊成,分上下两部分,上罩体内衬耐火
5.7.2 CAS-OB法
2)氧枪 一般在CAS-OB法中多采用惰性气体包围氧气流股的双
套管顶吹氧枪。常见吹氧枪为消耗型,用双层不锈钢管组 成。套管外涂高铝质耐火材料(A12O3≥90%),套管间隙一 般为2~3mm。中心管吹氧,套管环缝吹氩气冷却,氩气量 大约占氧气量的10%左右。这种喷枪使氧气流股包围在隋性 气氛当中,形成了集中的吹氧点,在大的钢液面则形成低 氧分压区,从而抑制了钢液的氧化。操作中控制外管压力 和内管压力的比值在1.2~3.0之间能收到良好的效果。氧枪 的烧损速度大约为50mm/次,寿命为20-30次。
一般热吸收率可达80%以上。为获得较好的铁、锰、碳 元素烧损,需要保持比较多的与供氧相平衡的理论燃烧物数 量。
5.7.2 CAS-OB法
(2)CAS-OB的设备
● 底吹氩系统 ● 合金称量与加入系统 ● 氧枪升降与吹氧系统 ● 浸渍罩及其升降系统 ● 保温材料加入系统 ● 自动测温取样装置 ● 风动送样及光谱分析系统 ● 除尘系统
钢试样中Na、K类杂质元素来源的新发现
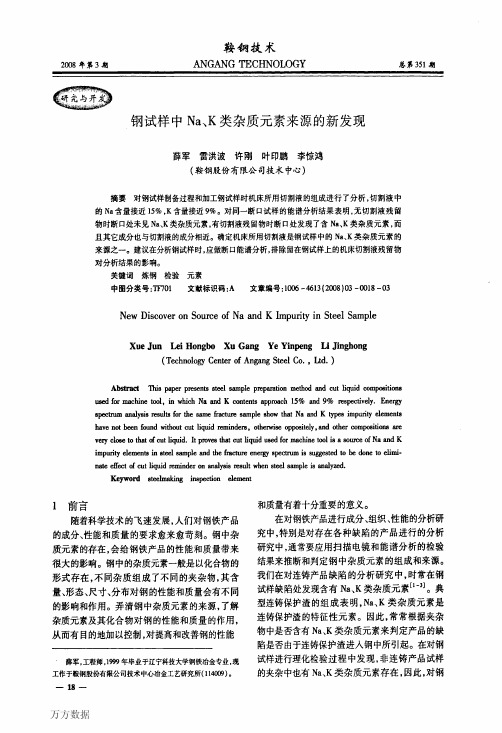
薛军等:铜试样中Na、K类杂质元素来源的新发现
<鞍钢技术)2008年第3期 总第351期
3钢中Na、K元素来源分析
通过对钢样制备过程的分析,发现车床切割 试样时所用的切割液中有可能含有Na、K类杂质 元素。将切割液滴在试样板上,干燥后对试样板 上的残留物进行能谱分析,分析结果如图3和表 3所示。从图中可以看出,切割液的Na含量为 14.76%、K含量为8.93%。在观察和分析的基 础上,初步认为,由于钢样的缺陷常常带有凹坑或 裂缝等征状,在试样加工过程中,机床切割液很有 可能进入并残留在暴露的凹坑内或裂缝等缺陷的 间隙中。因此,在对试样缺陷处的夹杂做能谱分 析时,会发现其组成中含有Na、K类杂质元素。
钢试样中Na、K类杂质元素来源的新发现
薛军雷洪波许刚叶印鹏李惊鸿 (鞍钢股份有限公司技术中心)
摘要对钢试样制备过程和加工钢试样时机床所用切割液的组成进行了分析,切割液中 的Na含量接近15%,K含量接近9%。对同一断口试样的能谱分析结果表明,无切割液残留 物时断口处未见Na、K类杂质元素,有切割液残留物时断13处发现了含Na、K类杂质元素,而 且其它成分也与切割液的成分相近。确定机床所用切割液是钢试样中的Na、K类杂质元素的 来源之一。建议在分析钢试样时,应做断口能谱分析,排除留在钢试样上的机床切割液残留物 对分析结果的影响。
spectrum analysis results for the 8a脚franture sample show that Na and K types impurity elements compositions眦 have not been found without out hqu_ia reminders,otherwise oppositely,and other very close to that of cut liqIlid.It proves that cut aqujd used for machine tool is a 80lllfce of Na and K impurity dements in steel sample and the fracture energy spectrum is suggested to be done tO幽mi· nale effect of cut ljqIlid reminder on analysis result when steel sample is analyzed.
钢液内非金属夹杂物的形成及去除条件

钢液内非金属夹杂物的形成及去除条件一…}=7氧化碱度-――一一1前言随着科学的发展,现代工业对钢铁材料的强度、韧性及加工性能等要求 E t趋提高 .实际上也是对钢铁材料的化学成份及组织均匀性的要求越来越高.因此我们在冶炼一般钢种时应尽力提高钢液的纯净度,尽量降低钢液内非金属夹杂物 .虽然钢液内少量的徽觖杂物在结晶时对钢质有利的一面,如控铷本质细晶粒 .促进晶粒的取向.弥散的沉淀相将改善钢材的切削性能等,但这些非金属夹杂物在钢中都以独立相存在,这些夹杂物的大量存在将破坏钢基体的连续性,造成钢组织的不均匀性,在压力加工过程中可能造成应力在此集中,形成裂纹源,对钢材的成材率及冷热加工性能造成严重影响。
因此 .我们在冶炼及浇注过程中应尽盈降低钢液内的非金属夹杂物。
2钢液内非金属夹杂物来源钢液内非金属夹杂糖主要来源于两部份:一部份由合金材料、耐火材料及氇瓷材料等外部因素进人钢液,另一部份是由于钢液内部所发生脱氧、脱硫,调硅锰等反应及锵渡凝固时造成相平衡移动在钢内形成。
由此 .我们可以把饲内的非金属夷杂物分为外来夹杂物及内生夹杂物两类。
21外来央杂糖:这类夹杂物主要是在冶炼莳期进人钢 .及锭模,耐火砖的诂净面癌人钢中,这类夹杂钧在锕液中一般不易溶解,它豹产生和存在具有偶然性。
它的寸较大 .对钢材的后期成材又极具破坏性。
操作人员只有雏致前局到的操作.通过减少夹杂协的来源来降低钢中此类夹杂物的含量。
2内生夹杂物:这囊壶杂物是由于钢渣界面的反应及钢液凝同时各种复杂癌麴理化学 . 2反应而形成。
内生央寐糖强 .中形成有几个阶段:第一阶段墨售渣界面反应生硪舞恶物 .懑I硫化物,氮化物及爱食辅台犍辞。
它在锕液内有一定的溶解度,这是钢液内的原生夹蓉。
在出钢后钢水静置过程日 .镪液 .下降,平衡移动部份夹杂物析出,钢液内产生了二敬央杂。
镀钢液在凝固时,蹇祭罄蜘寝;身奎啤 .因而夹杂物聚集、再生,钢中第三次有夹杂物析出,钢中温暖进一步下降时÷日足态搬,夹杂麴会进一步析出,产生四次夹杂。
精炼和连铸反应器内夹杂物物理行为的研究的开题报告

精炼和连铸反应器内夹杂物物理行为的研究的开题报告题目:精炼和连铸反应器内夹杂物物理行为的研究一、选题背景在钢铁冶炼过程中,夹杂物是对钢材质量影响最大的较严重缺陷之一,其对钢材的机械性能、成形性能等均有很大的影响。
因此,对夹杂物的形成机理、规律以及行为进行深入的研究,对提高钢材的质量和性能具有十分重要的意义。
二、研究内容和目标本项目旨在采用现代计算机模拟方法,探究精炼和连铸反应器内夹杂物的物理行为,包括夹杂物在熔体中的形态演变、漂浮和沉淀等,并研究相关的影响因素,如处理工艺、反应器结构等。
通过研究,我们将深入了解夹杂物的形成、演变和影响因素,为加强对夹杂物的控制和改善钢材质量提供理论参考和实践指导。
三、研究内容和方法1.研究物理行为:通过分子动力学模拟和数值计算方法,研究夹杂物在熔体中的演变、漂浮和沉淀过程。
同时考虑处理工艺和反应器结构等因素的影响,从而深入了解夹杂物的行为规律和物理机制。
2.研究形态演变:通过分析夹杂物的化学组成和形态特点,探究夹杂物在熔体中的形态演变规律,如气泡、颗粒等的形态变化,了解夹杂物在熔体中的行为规律和特征。
3.研究夹杂物对钢材性能的影响:通过对夹杂物形成、演变和行为规律进行深入研究,探究夹杂物对钢材质量和性能的影响,为控制夹杂物和改善钢材质量提供科学依据和实践指导。
四、预期成果通过对精炼和连铸反应器内夹杂物物理行为的研究,可以:1.深入了解夹杂物的形成机理和演变规律;2.了解夹杂物在熔体中的行为特征和影响因素;3.探究夹杂物对钢材质量和性能的影响;4.提出加强对夹杂物控制与改善钢材质量的技术措施和理论指导。
五、研究难点1.反应器内夹杂物形成过程的复杂性;2.夹杂物和熔体相互作用的复杂性;3.实验与理论的互动和验证。
六、研究意义本研究可为加强钢材质量控制和改进加工工艺提供准确的理论依据和实践指导,为钢材制造业的发展提供技术支持。
同时,也可为相关领域学者和从业人员提供学术资料和参考。
连铸坯夹杂物产生原因分析及改进

连铸坯夹杂物产生原因分析及改进连铸是指通过连续铸造设备将熔液连续浇铸成坯料的一种方法。
在连铸过程中,夹杂物是最常见的缺陷之一,它们对铸坯的质量和性能有着重要的影响。
分析连铸坯夹杂物产生原因,并采取相应的改进措施,可以有效地提高铸坯质量和生产效率。
连铸坯夹杂物产生的主要原因有以下几个方面:1.原料质量:连铸坯的夹杂物往往与原料的质量有关。
原料中存在的金属夹杂物、非金属夹杂物和气泡等会成为连铸夹杂物的来源。
提高原料的质量和纯净度,减少夹杂物的含量是解决连铸坯夹杂物问题的一项重要措施。
2.炉次操作:炉次操作对连铸坯夹杂物的产生也有较大的影响。
炉渣的不合理处理、熔炼温度和时间的控制不当等都可能导致夹杂物产生。
合理的炉次操作和炉渣处理是减少夹杂物产生的关键。
3.结晶器和冷却系统:结晶器和冷却系统的设计和使用状态对连铸坯夹杂物的产生起着重要的作用。
结晶器的凝固状态、结晶器涂层的质量和结晶器冷却水流量的控制都会影响到连铸坯的质量和夹杂物含量。
合理设计结晶器和冷却系统,并保持其良好的使用状态,对减少夹杂物具有重要意义。
4.连铸工艺参数:连铸工艺参数的选择和控制也是减少夹杂物产生的关键。
保证浇注速度、拉伸速度、结晶器超熔度、超温和过度冷却等参数的合理选择和控制,对提高铸坯质量和减少夹杂物具有重要的影响。
改进方法:1.加强原料质量控制:加强对原料的质量控制,选择优质的原料供应商,进行严格的质检,确保原料的纯净度和无夹杂物。
2.优化炉次操作:加强炉次操作的管理和控制,合理控制熔炼温度和时间,严格进行炉渣处理,确保炉渣中夹杂物的除去。
3.改善结晶器和冷却系统:优化结晶器和冷却系统的设计,确保结晶器的良好工作状态,减少结晶器涂层的破损和脱落,调整冷却水流量,避免过度冷却和不足冷却的情况。
连铸坯夹杂物的产生是多方面因素共同作用的结果。
通过加强原料质量控制、优化炉次操作、改善结晶器和冷却系统以及优化连铸工艺参数等措施,可以有效地减少夹杂物产生,提高铸坯质量和生产效率。