减少炼钢连铸钢中夹杂物的工艺措施(续)
304不锈钢中夹杂物的控制

304不锈钢中夹杂物的控制304不锈钢是一种广泛应用的奥氏体不锈钢,具有优良的耐腐蚀性和高温强度。
然而,夹杂物的存在可能会对其组织和性能产生不利影响。
因此,控制304不锈钢中的夹杂物对于保证其质量和性能具有重要意义。
本文将介绍夹杂物控制的重要性、夹杂物的来源和分类,以及夹杂物控制的措施和效果。
夹杂物是指存在于金属内部或表面的非金属杂质。
在304不锈钢中,夹杂物可能会破坏材料的连续性,导致应力集中,降低材料的耐腐蚀性和力学性能。
夹杂物对304不锈钢组织和性能的影响主要表现在以下几个方面:降低材料的耐腐蚀性:夹杂物能够破坏不锈钢表面的氧化膜,加速局部腐蚀,降低材料的耐腐蚀性。
降低材料的力学性能:夹杂物会破坏材料的连续性,导致应力集中,降低材料的强度和韧性。
影响材料的加工性能:夹杂物可能引起材料加工过程中的缺陷,如裂纹、折叠等,影响加工质量和精度。
夹杂物主要分为有意夹杂物和无意夹杂物。
有意夹杂物是人为添加的,如为了改善材料的某些性能而特意加入的合金元素。
无意夹杂物是在冶炼、加工过程中引入的,如炉渣、耐火材料、以及与炉气、熔剂、燃料等反应生成的产物。
为了控制304不锈钢中的夹杂物,可以采取以下措施:增加夹杂物球化处理:通过适当的热处理,使夹杂物呈球形颗粒分布,降低其对材料性能的不利影响。
控制原材料及熔炼过程:选用低杂质含量的原材料,严格控制熔炼工艺,避免过度氧化和污染。
精炼和净化处理:采用精炼技术,如电渣重熔、真空熔炼等,去除熔体中的夹杂物;同时,进行净化处理,如加入稀土元素细化晶粒,提高材料的纯净度。
合理安排工艺流程:在加工过程中合理安排工艺流程,避免过度变形和加热,以减少夹杂物的引入。
采取上述控制措施后,可以显著降低304不锈钢中的夹杂物数量和尺寸,改善材料的组织和性能。
具体效果如下:夹杂物形态:通过控制措施,可以使夹杂物呈球形或不规则形态分布,降低其对材料性能的不利影响。
夹杂物分布:采取控制措施后,夹杂物分布更加均匀,避免了局部浓度过高现象,降低材料脆性。
炼钢工—简答题 207

1.什么是溅渣护炉技术?答案:溅渣护炉技术是向炉渣中加入含MgO的造渣剂造粘渣补炉技术的基础上, 采用氧枪喷吹高压N2在2-4mm 内将出钢后留在炉内的残余炉渣喷溅涂敷在转炉内衬表面上,生成炉渣保护层的护炉技术。
2.炉渣来源何处?它在炼钢中起什么作用?答案:来源:(1)钢铁料中夹杂氧化的产物。
(2)造渣材料(石灰、白云石、萤石等)。
(3)冷却剂(氧化铁皮、矿石等)。
(4)被浸蚀和冲刷下来的炉衬耐火材料。
(5)各种原料带来的泥沙。
作用:(1)去夹杂(P、S);(2)传氧媒介;(3)清洁钢液;(4)对熔池保温;(5)影响金属损失;(6)影响炉衬浸蚀。
3.脱碳反应对炼钢过程的重要意义是什么?答案:(1)铁水中C氧化到钢种所要求的范围。
(2)氧化产生CO气泡对熔池起着循环搅拌作用,均匀钢液成份、温度, 改变各种化学反应的动力学条件。
(3)CO气泡有利于去除N2、H2等。
(4)利于非金属夹杂物上浮。
(5)提供炼钢的大部分热源。
(6)CO气泡使炉渣形成泡沫渣。
4.造成钢包回磷的原因是什么?如何防止?答案:原因:(1)出钢下渣;(2)脱氧产物SiO2;(3)氧含量降低。
防止措施:(1)挡渣出钢,尽量减少出钢带渣。
(2)采用碱性钢包或渣线部位用碱性材料。
(3)出钢过程中投入钢包中石灰粉。
(4)减少钢水在钢包中停留时间。
5.为什么兑铁时,有时会发生大喷?答案:因为转炉吹炼到终点,钢中氧含量和炉渣氧化性高, 留渣或未倒净的渣子和钢水,兑铁时炉内碳含量急剧增加且铁水温度低及钢水温度骤然下降, 促使碳氧反应剧烈进行在炉内产生强烈沸腾,如果兑铁水过猛且炉内残留钢渣较多就会大喷。
6.为什么转炉炼钢脱硫比脱磷困难?答案:碱性转炉渣中含有较高的(FeO),炉渣脱硫的分配比较低,降低了炉渣的脱硫能力,高(FeO)对脱磷工艺是一个相当有利的因素, 转炉炼钢条件下钢渣间磷的分配比较高, 一般可达100-400,而硫的分配比一般为6-15,此外,脱磷反应速度快,很快可达到平衡,而脱硫速度较慢,一般达不到平衡。
连铸坯夹杂物产生原因分析及改进

连铸坯夹杂物产生原因分析及改进一、引言连铸是现代钢铁生产中常用的一种工艺。
它可以提高生产效率、降低能耗、改善工作环境、减少劳动强度,因此被广泛应用。
在连铸过程中,一些夹杂物的产生会导致产品质量下降、生产效率降低,并严重影响设备寿命。
如何减少夹杂物的产生,提高产品质量,成为生产中亟需解决的问题。
二、夹杂物产生原因分析1.原料质量不稳定连铸坯的原料主要是钢水,而钢水的质量直接影响夹杂物的产生。
如果原料中含有较多的杂质、氧化物等,就会增加夹杂物的产生几率。
而且,原料的成分不稳定也是引起夹杂物产生的一个因素,一旦成分变化,就容易导致夹杂物出现。
2.连铸设备使用不当连铸设备的使用不当也是夹杂物产生的重要原因。
操作不规范、设备维护不到位、温度控制不稳定等都会导致夹杂物的产生。
当温度过高或过低时,容易使得钢水和坯料中的气体凝固,形成夹杂物。
3.连铸工艺参数不合理连铸过程中,工艺参数的设置直接影响了夹杂物的产生。
如果连铸速度过快或者过慢,结晶器冷却不均匀等,都会导致夹杂物产生。
结晶器振动频率、结晶器倾斜角度、结晶器冷却水温度等参数的选择也会影响夹杂物的产生。
4.人为因素在连铸过程中,人为操作失误也是夹杂物产生的一个主要原因。
操作工不熟练、设备检查不到位等都可能导致夹杂物的产生。
而且,人为因素不可控因素多,所以造成夹杂物的产生很容易。
三、改进措施1.原料质量监控首先要保证原料的质量稳定,及时清洁处理原料,确保原料的成分合理、纯净。
加强对原料的把控,对于原料中可能含有的杂质要及时剔除,确保连铸坯的质量。
2.加强设备维护连铸设备是关键的生产装备,要加强对设备的维护。
定期检查、保养设备,确保设备各项功能正常,减少因为设备问题导致的夹杂物的产生。
3.优化连铸工艺对于工艺参数的设置要进行优化,选择合适的连铸速度、结晶器振动频率、结晶器倾斜角度、结晶器冷却水温度等参数,保证连铸坯的质量。
要对工艺参数进行严格的控制,确保温度、速度等参数的稳定。
精炼渣系对钢中夹杂物的影响
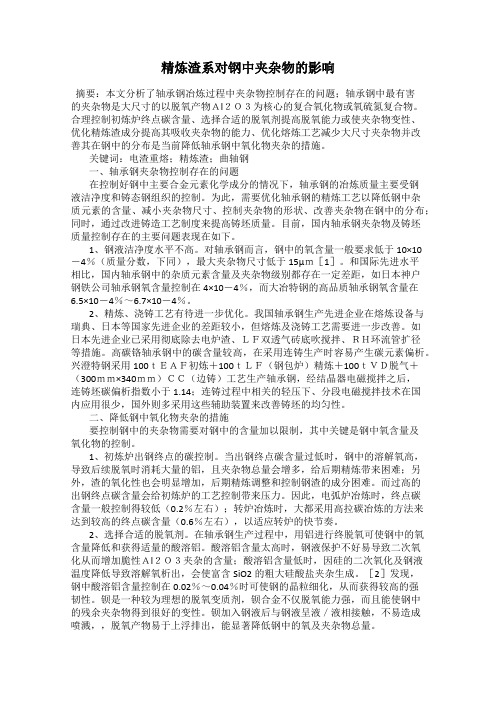
精炼渣系对钢中夹杂物的影响摘要:本文分析了轴承钢冶炼过程中夹杂物控制存在的问题;轴承钢中最有害的夹杂物是大尺寸的以脱氧产物Al2O3为核心的复合氧化物或氧硫氮复合物。
合理控制初炼炉终点碳含量、选择合适的脱氧剂提高脱氧能力或使夹杂物变性、优化精炼渣成分提高其吸收夹杂物的能力、优化熔炼工艺减少大尺寸夹杂物并改善其在钢中的分布是当前降低轴承钢中氧化物夹杂的措施。
关键词:电渣重熔;精炼渣;曲轴钢一、轴承钢夹杂物控制存在的问题在控制好钢中主要合金元素化学成分的情况下,轴承钢的冶炼质量主要受钢液洁净度和铸态钢组织的控制。
为此,需要优化轴承钢的精炼工艺以降低钢中杂质元素的含量、减小夹杂物尺寸、控制夹杂物的形状、改善夹杂物在钢中的分布;同时,通过改进铸造工艺制度来提高铸坯质量。
目前,国内轴承钢夹杂物及铸坯质量控制存在的主要问题表现在如下。
1、钢液洁净度水平不高。
对轴承钢而言,钢中的氧含量一般要求低于10×10-4%(质量分数,下同),最大夹杂物尺寸低于15μm[1]。
和国际先进水平相比,国内轴承钢中的杂质元素含量及夹杂物级别都存在一定差距,如日本神户钢铁公司轴承钢氧含量控制在4×10-4%,而大冶特钢的高品质轴承钢氧含量在6.5×10-4%~6.7×10-4%。
2、精炼、浇铸工艺有待进一步优化。
我国轴承钢生产先进企业在熔炼设备与瑞典、日本等国家先进企业的差距较小,但熔炼及浇铸工艺需要进一步改善。
如日本先进企业已采用彻底除去电炉渣、LF双透气砖底吹搅拌、RH环流管扩径等措施。
高碳铬轴承钢中的碳含量较高,在采用连铸生产时容易产生碳元素偏析。
兴澄特钢采用100tEAF初炼+100tLF(钢包炉)精炼+100tVD脱气+(300mm×340mm)CC(边铸)工艺生产轴承钢,经结晶器电磁搅拌之后,连铸坯碳偏析指数小于1.14;连铸过程中相关的轻压下、分段电磁搅拌技术在国内应用很少,国外则多采用这些辅助装置来改善铸坯的均匀性。
连铸工考试考试试题(题库版)

连铸工考试考试试题(题库版)1、判断题单位时间内单位长度的铸坯被带走的热量称为结晶器的冷却强度。
正确答案:错2、判断题连铸坯的柱状晶越发达,质量就越好。
正确答案:错3、问答题中间包结瘤的原因?正确答案:(江南博哥)⑴钢水温度低;⑵钢中AL2O3含量高;4、判断题压缩铸造应用在高拉速铸机中。
正确答案:对5、单选中包永久层小火烘烤时间为()A、12小时B、18小时C、24小时D、36小时正确答案:D6、问答题高效连铸技术包括的主要内容是什么?正确答案:①保证适宜的钢水温度,最佳的钢水成份,并保证其稳定性的连铸相关配套技术。
②供应清洁的钢水和良好流动性钢水的连铸相关技术。
③连铸的关键技术——高冷却强度的,导热均匀的长寿结晶器总成。
④高精度、长寿的结晶器振动装置是高效连铸关键技术之一。
⑤保护渣技术。
⑥结晶器钢水液面控制技术。
⑦二次冷却的硬件及软件技术。
⑧连续矫直技术。
⑨其它技术。
铸坯支撑及强化冷却技术、保护浇注技术、钢包技术、中间包技术、电磁搅拌技术、自动开浇技术、低温浇注技术等。
7、判断题连铸坯的液芯长度就是冶金长度。
正确答案:错8、问答题什么是洁净钢连铸?正确答案:高质量连铸坯的生产要求钢水夹杂物的含量控制在规定的范围内。
在炼钢—精炼—连铸工艺过程中,炼钢和精炼是保证钢水洁净的基础。
同模铸相比,由于连铸的特殊条件,炼钢和精炼后的洁净钢水获得夹杂物含量极低的洁净铸坯比模铸存在更大的困难。
如何保证钢水的洁净,获得洁净铸坯,这就是洁净钢连铸技术。
9、判断题连铸坯的低倍组织是当铸坯完全凝固后,从铸坯上取下一块横断面试样,经磨光酸浸后用肉眼所观察到的组织。
正确答案:对10、问答题敞开浇注时配水量的要求?正确答案:⑴二冷室足辊I段转为“手动”配水方式;⑵I、II、III流足辊段水量调节为16m3/h;⑶I、II、III流I段水量调节为20m3/h;⑷二冷室II段用“自动”配水方式。
11、判断题为保持钢水的清洁度,要求钢水包砖衬具有良好的耐蚀损性,使耐火材料尽可能少溶入钢水内。
钢中非金属夹杂对质量的影响及控制措施
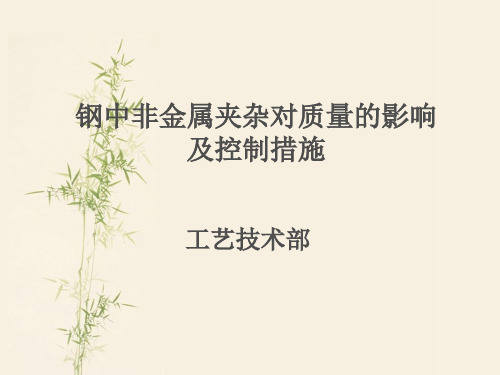
1) 液体钢的脱氧产物; 2) 钢液从浇注温度冷却到凝固温度过程中,由
于温度的降低使溶液中溶质的溶解度降低,
即钢水温度的变化使反应平衡移动,重新析 出脱氧产物;
3) 钢液冷凝时发生溶质树枝形偏析所析出的脱 氧产物;
4) 固相线温度以下钢继续冷却或者由于相变的
缘故,引起的夹杂物重新析出。
1.2
1.5
按化学成分分类
FeS、MnS
A类夹杂:硫化物
B类夹杂: 氧化铝、氧化铁 Al2O3+FeO C类夹杂:硅酸盐、氮化物 2MnO.SiO2 TiN、BN、NbN等 D类夹杂:球状氧化物类 小型氧化物 FeO、MnO、TiO2等
Ds类夹杂:单个大型球状氧化物类
1.6
钢中夹杂物的形貌
25
2.2夹杂物的检测
1.钢材出厂检验:
• • • ASTM标准(A、B、C、D、Ds类夹杂物); 用户标准(SKF、米其林、贝卡尔特等); 分析检验手段:光学显微镜。
2.科学研究:
• • 光学显微镜; 扫描电镜(+EDS);
•
• •
投射电镜(+EPMA、EDS);
图像分析; PDA(Pulse Distribution Analysis)。
炼钢钢坯
氧化铝+硫化钙
氧化铝
15102486N
氧化铁 视场50X
硫化钙
氧化铝
轧钢钢板
氮化物
2、非金属夹杂物对性能影响
使用性能的影响: 1、疲劳性能↓ 2、冲击韧性↓ 塑性↓ 3、耐腐蚀性↓
对工艺性能的影响: 1 、对锻造和冷加工、淬火加热和焊接过程 易开裂。 2 、轧制后表面质量以及磨削后零件表面粗 糙度降低。
连铸坯夹杂物产生原因分析及改进措施
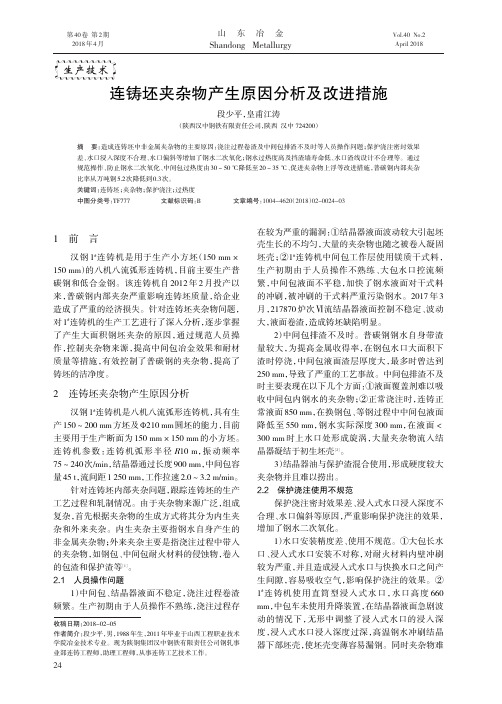
24
在较为严重的漏洞:①结晶器液面波动较大引起坯 壳生长的不均匀,大量的夹杂物也随之被卷入凝固 坯壳;②1#连铸机中间包工作层使用镁质干式料, 生产初期由于人员操作不熟练、大包水口控流频 繁,中间包液面不平稳,加快了钢水液面对干式料 的冲刷,被冲刷的干式料严重污染钢水。2017 年 3 月,217870 炉次Ⅵ流结晶器液面控制不稳定、波动 大,液面卷渣,造成铸坯缺陷明显。
差、水口浸入深度不合理、水口偏斜等增加了钢水二次氧化;钢水过热度高及挡渣墙寿命低、水口渣线设计不合理等。通过
规范操作、防止钢水二次氧化、中间包过热度由 30~50 ℃降低至 20~35 ℃、促进夹杂物上浮等改进措施,普碳钢内部夹杂
比率从万吨钢 5.2 次降低到 0.3 次。
关键词:连铸坯;夹杂物;保护浇注;过热度
1)中间包、结晶器液面不稳定,浇注过程卷渣 频繁。生产初期由于人员操作不熟练,浇注过程存
收稿日期:2018-02-05 作者简介:段少平,男,1988 年生,2011 年毕业于山西工程职业技术 学院冶金技术专业。现为陕钢集团汉中钢铁有限责任公司钢轧事 业部连铸工程师,助理工程师,从事连铸工艺技术工作。
炼钢连铸工艺流程的介绍
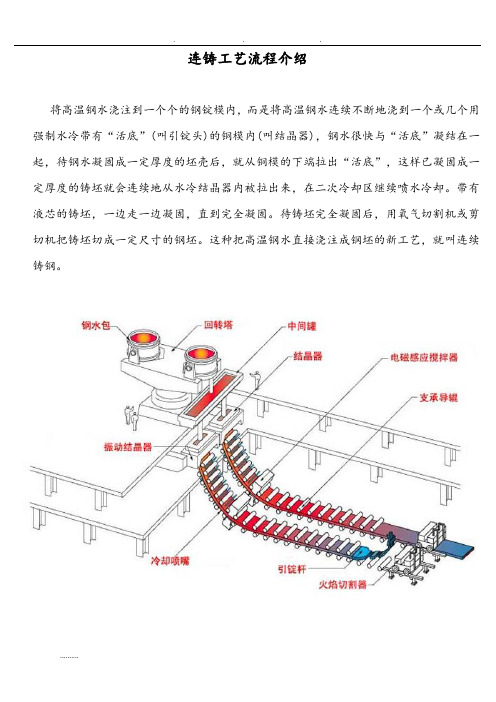
连铸工艺流程介绍将高温钢水浇注到一个个的钢锭模内,而是将高温钢水连续不断地浇到一个或几个用强制水冷带有“活底”(叫引锭头)的铜模内(叫结晶器),钢水很快与“活底”凝结在一起,待钢水凝固成一定厚度的坯壳后,就从铜模的下端拉出“活底”,这样已凝固成一定厚度的铸坯就会连续地从水冷结晶器内被拉出来,在二次冷却区继续喷水冷却。
带有液芯的铸坯,一边走一边凝固,直到完全凝固。
待铸坯完全凝固后,用氧气切割机或剪切机把铸坯切成一定尺寸的钢坯。
这种把高温钢水直接浇注成钢坯的新工艺,就叫连续铸钢。
【导读】:转炉生产出来的钢水经过精炼炉精炼以后,需要将钢水铸造成不同类型、不同规格的钢坯。
连铸工段就是将精炼后的钢水连续铸造成钢坯的生产工序,主要设备包括回转台、中间包,结晶器、拉矫机等。
本专题将详细介绍转炉(以及电炉)炼钢生产的工艺流程,主要工艺设备的工作原理以及控制要求等信息。
由于时间的仓促和编辑水平有限,专题中难免出现遗漏或错误的地方,欢迎大家补充指正。
连铸的目的: 将钢水铸造成钢坯。
将装有精炼好钢水的钢包运至回转台,回转台转动到浇注位置后,将钢水注入中间包,中间包再由水口将钢水分配到各个结晶器中去。
结晶器是连铸机的核心设备之一,它使铸件成形并迅速凝固结晶。
拉矫机与结晶振动装置共同作用,将结晶器内的铸件拉出,经冷却、电磁搅拌后,切割成一定长度的板坯。
连铸钢水的准备一、连铸钢水的温度要求:钢水温度过高的危害:①出结晶器坯壳薄,容易漏钢;②耐火材料侵蚀加快,易导致铸流失控,降低浇铸安全性;③增加非金属夹杂,影响板坯内在质量;④铸坯柱状晶发达;⑤中心偏析加重,易产生中心线裂纹。
钢水温度过低的危害:①容易发生水口堵塞,浇铸中断;②连铸表面容易产生结疱、夹渣、裂纹等缺陷;③非金属夹杂不易上浮,影响铸坯内在质量。
二、钢水在钢包中的温度控制:根据冶炼钢种严格控制出钢温度,使其在较窄的范围内变化;其次,要最大限度地减少从出钢、钢包中、钢包运送途中及进入中间包的整个过程中的温降。
降低钢中夹杂物的途径

降低钢中夹杂物的途径钢是一种重要的金属材料,广泛应用于建筑、机械制造、汽车工业等领域。
然而,钢材中存在着各种夹杂物,如气孔、夹杂、夹锰、夹杂物等,会对钢材的性能产生不利影响,降低其强度、韧性和耐腐蚀性能。
因此,降低钢中夹杂物的含量是提高钢材质量的重要措施之一。
本文将介绍一些降低钢中夹杂物的途径。
1. 优化原料选择:选择优质、纯净的原料是降低钢中夹杂物的首要步骤。
原料中夹杂物的含量直接影响到最终钢材的质量。
因此,需要从供应商选择合格的原料,并在进料前进行严格的质量检验,确保原料的纯度和质量符合要求。
2. 优化熔炼工艺:熔炼是钢材生产中的关键环节,也是夹杂物形成的主要阶段。
通过优化熔炼工艺,可以有效降低钢中夹杂物的含量。
一方面,可以控制炉温和炉压等参数,提高熔炼过程中的熔化效率,减少夹杂物的生成。
另一方面,可以采用真空熔炼、气体保护熔炼等特殊工艺,排除气体和氧化物等夹杂物。
3. 引入精炼工艺:精炼是降低钢中夹杂物的重要手段之一。
通过引入精炼工艺,可以进一步减少钢中的夹杂物含量。
常用的精炼工艺包括钢包精炼、真空精炼、熔化保温精炼等。
这些工艺能够有效地去除钢中的气体、硫化物、氧化物等夹杂物,并提高钢的纯净度和均匀性。
4. 控制浇注温度和速度:钢材的浇铸过程也是夹杂物形成的关键环节。
通过控制浇注温度和速度,可以有效减少夹杂物的生成。
合理的浇注温度和速度可以降低钢液的气化程度,减少气孔和夹杂物的形成。
此外,在浇注过程中还可以采用一些防止夹杂物形成的措施,如振动浇注、渣包覆盖等。
5. 严格控制冷却过程:钢材冷却过程也会影响夹杂物的生成。
过快或过慢的冷却速度都会导致夹杂物的增加。
因此,在冷却过程中需要严格控制冷却速度,确保钢材的均匀冷却,减少夹杂物的生成。
6. 加强质量检验:质量检验是确保钢材质量的重要环节。
通过加强质量检验,可以及时发现和排除钢材中的夹杂物。
常用的质量检验方法包括超声波检测、X射线检测、磁粉检测等。
连铸坯夹杂物产生原因分析及改进

连铸坯夹杂物产生原因分析及改进
连铸坯夹杂物是指钢铁连铸过程中在浇注的过程中,因为一些原因混杂进去的杂质,
这些杂质会影响钢铁的质量和成材率。
夹杂物主要包括氧化物、硫化物、氮化物、矽夹杂等,这些夹杂物可能来自于原料、工艺流程、设备和人为因素等多个方面。
1.原料原因:原料中可能含有硅、锰、硫等杂质,在钢水中形成相应的氧化物、氮化物、硫化物等夹杂物。
2.钢水的气体夹杂:钢水中可能残留气体,当钢水在浇注时,气泡被涡流或不良的结
晶生长引起了空穴,形成气体夹杂物。
3.脱气工艺问题:连铸坯在脱气过程中,如果处理不良,残留大量的气体就会在浇注
过程中形成大量气体夹杂物。
4.连铸工艺问题:浇注工艺不正确,液相氧化被带到坯子内部形成氧化物,结晶器收
缩率不同,产生结合夹杂物。
或者结晶器壁面不平整或有损伤,发生较强的涡流,夹杂物
就会被带进钢水中。
针对夹杂物产生的原因,改进措施如下:
1.原料优化:原料筛选、预处理,降低杂质含量,保证原料的质量。
2.脱气处理:改进脱气工艺,通过增加脱氧剂和还原剂的投加量,在改善气体脱出的
同时,减少气体再进入钢液的可能性。
3.连铸工艺优化:优化连铸工艺,增加浇注速度,减少在坯子内部形成的氧化夹杂物。
4.设备维护:定期对连铸设备进行检查和维护,确保连铸设备的完好性和稳定性,避
免设备问题引起的夹杂物问题。
5.加强管理:加强对人工操作的监管,培训工人正确操作流程,提高工人的专业技能,降低人为因素造成的夹杂物产生率。
总之,针对夹杂物产生原因,可以从原料、工艺、设备和人力资源等多个方面进行改进,进一步提高钢铁的品质和成材率。
炼钢厂钢包渣线结渣原因分析及解决结壳的措施

炼钢厂钢包渣线结渣原因分析及解决结壳的措施炼钢厂生产冷墩系列钢水的工艺路径有3种:①转炉→LF炉→真空RH炉→方坯连铸机。
②转炉→真空RH炉→LF炉→方坯连铸机。
③转炉→LF炉→方坯连铸机。
LF炉出站后造渣在浇注过程中冷却、结壳,在钢水浇完后仍挂留在钢包渣线位置,使钢包清理作业难度及工作量增加,而且钢包遗留钢渣再次使用会带来一系列影响。
如:包壁结渣在连铸机浇注结束后悬空,受重力作用掉落钢包底部,形成包底结渣,再次盛钢时钢渣在钢水中熔化上浮,降低钢水纯净度和钢水可浇性;同时会有部分钢渣散落钢包水口内,堵水口,造成钢水到连铸机平台后无法开浇。
1待浇时间长,钢水顶渣冷却结壳,造成钢包渣线结渣。
(1)韶钢厂冷墩钢工艺要求钙处理结束后需要底吹氩气,弱吹12~20min,弱吹过程钢水表面渣层边缘部位基本呈静止状态,经过长时间温度散失,渣温不断降低,靠包壁位置的渣层就会凝固在钢包渣线位置,造成钢包壁结渣。
(2)转炉的冶炼周期要比LF精炼炉的冶炼周期短,浇次组织不力,出现前工序冶炼速度过快,钢水在精炼区域积压严重,精炼冶炼结束后到连铸浇铸期间等待时间过长,这是造成钢包渣线结渣的主要原因。
2冷镦钢渣系中Al2O3含量高,钢水渣黏稠,精炼结束后钢水镇静过程中随渣面温度降低而凝固结于钢包渣线位置。
据现场观察,冶炼铝镇静钢时,钢包渣线容易结渣,而冶炼硅锰镇静钢时,钢包渣线粘渣程度轻微。
铝镇静钢渣中的Al₂O₃含量高[2],为保证钢水的纯净度,配加的石灰量也较大,形成较厚且密度大的渣壳;硅锰镇静钢中不含Als,相应产生的Al₂O₃也极少,因此加入的石灰量较少,形成的渣层薄。
由此可以推断出,钢包结渣受渣中的Al₂O₃含量影响较大。
3钢包渣线砖浸蚀严重,产生凹陷,易挂渣。
钢包渣线砖是指钢包口向下数第三层砖到第八层砖的区域砌筑的耐火砖。
钢包盛钢后的钢水液面随钢水量而上下浮动,转炉冶炼结束出钢时,炉内部分氧化渣随钢水一起倒入钢包内,俗称“下渣”,钢水经过LF炉工艺时会通过二次精炼造渣,将钢水中的多余氧除去,即“脱氧”,脱氧后的渣为还原渣。
连铸钢水流动性差的原因及改进措施探讨

2010特钢年会论文集2010年10月连铸钢水流动性差的原因及改进措施探讨费三林潘明旭王品刘高利刘月云(湖北新冶钢有限公司,黄石435001)摘要:连铸钢水流动性差,主要表现为大包内钢水流不出或中包水口内的钢水流量小,究其原因,一是钢水温度不适宜,二是水口结瘤。
本文主要着手分析影响中包钢水流动性的结瘤物成分,弄清其来源,再结合实际生产,对造成适铸钢水流动性差的原因进行分析,并对如何采取相应的措施进行探讨。
关键词:钢水流动性重接夹杂物中间包水口The cause for poor fluidity of GCrl5liquid steel and corrective measure probeFE I S an.1in,PA N Ming·XU,WANG Pin,LI U Gao.1i,LIU Y ue-y un(H u be i Xinyegang St eel C o Ltd,Huan gshi435001)Abst rac t:t he poo r flui dity of ca st in g li quid steel mainly s ho w s that t he re is n o liqu id steel outflowing f r om l ad le furnace O r the flow rat e is small in tundish,which is caused by e ith er impr ope r liqu id steel t e m p e r a t u r e o r noz z l e c l o g g i ng.T h i s pape r i s f o c u s o n an al y s i n g the co mp o ne nt of n o d u la t i o n whic h a ffect t he li qu id steel f l ui di t y,a nd cle ar ifi ng its SOUrCe,thereafter analysing the c a u s e fo r p o o r fluidity of liqui d steel c o mb i ng a ct ua l p r o d u c t i on,a n d at las t study o n ho w to tak e measures is p ro ce ed ed.Key Words:FI_uidity of liquid,Rejoining,Inclusion,Tundish no z z l e1前言现实生产中经常发生因连铸钢水流动性差致使连铸机生产波动频繁,严重时导致连铸停浇,既影响铸坯质量的稳定又影响钢厂生产的成本,严重降低炼钢工序收益。
板坯夹杂成因及控制措施

板坯夹杂成因及控制措施为了优化产品的质量,就要对钢材的纯净度予以关注,借助板坯铸坯处理工作,结合影响因素了解对应的管理要点,在过程化控制中优化改进方式。
本文分析了板坯夹杂成因,并集中讨论了控制措施,仅供参考。
标签:板坯夹杂;成因;控制措施在钢材应用使用条件全面提升的背景下,用户对于钢材的质量有了更加明确的认知,夹杂物对于钢材力学性能以及工艺性能的影响,针对塑性、韧性以及疲劳性能等落实对应的管理方针。
一、板坯夹杂成因(一)转炉操作对于板坯的应用管理,要对转炉终点控制予以约束,因为终点控制是夹杂物的根本,在钢水达到终点较差时,钢水中的氧元素含量就会增大,因此,为了避免钢水中氧含量超标,往往会加入较多的含铝的脱氧剂,此时就会产生三氧化二铝,若是进入钢水中就会在化学作用下形成硅酸盐亦或是铝酸盐,这些夹杂就是常见的板坯夹杂物。
基于此,钢水终点氧含量本身就是下形成脱氧产物的根本,所以吹氩操作能有效减少夹杂物的上浮,避免夹杂物在钢种中分布,提升质量水平。
(二)中间包液面控制较差目前,中包的深度为800mm,在正常浇筑液面的情况下,能维持在600mm 到700mm,此时就能减少夹杂的产生,若是页面的深度在400mm以下,则会出现夹杂量明显增多的问题。
究其原因,主要是因为底页面时中包塞棒的位置会形成不规则的涡流,液面上的渣滓就会被钢水卷入钢液的内部,必然会对整体应用效果产生影响。
另外,在大包衔接过程中,正是因为液面控制效果不足,使得钢包不能及时达到台面,液面必然会降低,这就使得下一次开包过程中会因为撞击较为猛烈出现液面内部结晶效果不足的问题,形成表面夹杂的现象[1]。
(三)浇注不当在板坯制作的过程中,浇注过程非常关键,低倍检验过程能对40%的非金属夹杂物进行分析和处理判定,为了减少钢液在浇筑过程中接触大气产生二次氯化,会借助保护套管对大包注流下形成保护作用,若是不能按照标准化处理工序完成对应操作,就会造成氯化严重,形成夹杂物。
板材探伤不合格原因的分析
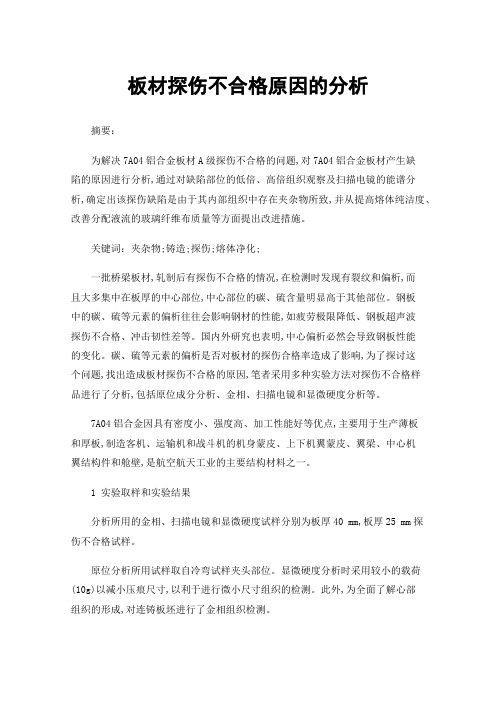
板材探伤不合格原因的分析摘要:为解决7A04铝合金板材A级探伤不合格的问题,对7A04铝合金板材产生缺陷的原因进行分析,通过对缺陷部位的低倍、高倍组织观察及扫描电镜的能谱分析,确定出该探伤缺陷是由于其内部组织中存在夹杂物所致,并从提高熔体纯洁度、改善分配液流的玻璃纤维布质量等方面提出改进措施。
关键词:夹杂物;铸造;探伤;熔体净化;一批桥梁板材,轧制后有探伤不合格的情况,在检测时发现有裂纹和偏析,而且大多集中在板厚的中心部位,中心部位的碳、硫含量明显高于其他部位。
钢板中的碳、硫等元素的偏析往往会影响钢材的性能,如疲劳极限降低、钢板超声波探伤不合格、冲击韧性差等。
国内外研究也表明,中心偏析必然会导致钢板性能的变化。
碳、硫等元素的偏析是否对板材的探伤合格率造成了影响,为了探讨这个问题,找出造成板材探伤不合格的原因,笔者采用多种实验方法对探伤不合格样品进行了分析,包括原位成分分析、金相、扫描电镜和显微硬度分析等。
7A04铝合金因具有密度小、强度高、加工性能好等优点,主要用于生产薄板和厚板,制造客机、运输机和战斗机的机身蒙皮、上下机翼蒙皮、翼梁、中心机翼结构件和舱壁,是航空航天工业的主要结构材料之一。
1 实验取样和实验结果分析所用的金相、扫描电镜和显微硬度试样分别为板厚40 mm,板厚25 mm探伤不合格试样。
原位分析所用试样取自冷弯试样夹头部位。
显微硬度分析时采用较小的载荷(10g)以减小压痕尺寸,以利于进行微小尺寸组织的检测。
此外,为全面了解心部组织的形成,对连铸板坯进行了金相组织检测。
1.1 原位成分分析结果原位分析成分统计结果见表1。
表明碳的偏析较严重,碳的平均含量为0.057%,其最大偏析度为3.44,则偏析处碳含量最大为0.196%,远远大于钢板中的碳含量0.06%,如沿板厚方向的碳元素的分布图1(a)(Y=22.11,Y方向=轧制方向)显示了碳在最大偏析处的分布情况。
此外,有害元素硫的偏析也较严重,检查出的硫最大偏析度为1.53,其最大偏析处的元素分布如图1(b)所示。
钢夹杂物危害及应对措施

钢夹杂物危害及应对措施钢夹杂物危害及应对措施⼀、前⾔钢铁业是⼏乎所有重⼯业的基础与⽀柱,在国民经济中的重要性不⾔⽽喻。
钢铁材料是⼈类社会最主要使⽤的结构材料,也是产量最⼤应⽤最⼴泛的功能材料,在经济发展中发挥着举⾜轻重的作⽤。
钢铁材料是⼈类社会的基础材料,是社会⽂明的标志。
从纪元年代前后,世界主要⽂明地区陆续进⼊铁器时代以后,钢铁材料在⼈类⽣产、⽣活、战争中起到了举⾜轻重的作⽤。
⼀直到今天,钢铁材料的这种作⽤不但没有减弱,⽽是在不断增强。
房屋建筑、交通运输、能源⽣产、机器制造等都是⽴⾜于钢铁材料的应⽤基础之上;钢铁材料是诸多⼯业领域中的必选材料,既是许多领域不可替代的结构材料,也是产量最⼤覆盖⽽极⼴的功能材料。
钢铁⼯业长期以来是世界各国国民经济的基础产业,在国民经济中具有重要的地位,钢铁⼯业发展⽔平如何历来是⼀个国家综合国⼒的重要指标。
洁净钢是⼀个相对概念,⼀般认为:洁净钢指钢中五⼤杂质元素(S 、P 、H 、N 、O) 含量较低,且对夹杂物(主要指氧化物和硫化物) 进⾏严格控制的钢种, 主要包括:钢中总氧含量低,夹杂物数量少、尺⼨⼩、分布均匀,脆性夹杂物少及其合适的夹杂物形态。
钢的纯净化技术是⽣产⾼性能、⾼质量产品的基础,代表钢铁冶⾦企业的技术装备⽔平。
20 世纪80 年代以来,钢的洁净度不断提⾼。
⽇本2000年批量⽣产的洁净钢中,有害元素(P、S、N、O、H) 总量可达0.005 %,中国宝钢可达0.008 %,国内外钢⼚⽣产洁净钢⽔平见表1 表1 国内外⼀些钢⼚⽣产的洁净钢⽔平单位: ×10 - 6随着现代科技的进步和现代⼯业的发展对钢的质量要求越来越⾼,钢中夹杂物(主要是氧化物夹杂)严重影响钢材质量,随着洁净钢和纯净钢概念的提出,更是对钢中夹杂物的控制提出苛刻的要求。
钢中夹杂物能降低钢的塑性,韧性和疲劳寿命,使钢的加⼯性能变坏,对钢材表⾯光洁度和焊接性能有直接影响。
钢中的夹杂物对于钢材性能影响很⼤例如钢中夹杂物可导致汽车和电⽓产品⽤薄钢板的表⾯缺陷、DI罐⽤薄钢板裂纹、管线钢氢致裂纹、轮胎⼦午线加⼯过程断线、轴承钢疲劳性能恶化,同时钢中⾮⾦属夹杂物对于钢板抗撕裂性能和低温冲击韧性也有不利影响。
炼钢培训问答题

-炼钢培训问答复习题1、简述连铸用保护渣的基本作用?答:(1)绝热保温、防止散热;(2)隔绝空气、防止二次氧化,提高钢水质量;(3)吸收钢水中上浮的夹杂物;(4)充填坯壳与结晶器壁气隙,改善传热;(5)形成的渣膜起到润滑作用,减少拉坯阻力,防止粘接。
2、连铸工艺对钢水水成分有什么要求?答:(1)成分的稳定性要高;(2)良好的钢水可浇性;(3)抗热裂纹敏感性强。
3、如何减少夹杂物的带入量?答:防止措施:(1)控制脱氧产物(真空脱气,吹气搅拌,Ca处理);(2)防止钢水二次氧化(液面和钢流保护,实现无氧化浇注);(3)避免渣子卷入(挡渣出钢,底吹氩,结构合理的中间包,设置挡墙,控制结晶器液面);(4)减小耐火材料的熔损;(5)采用Ca处理(钢水中加Ca,使串簇状的Al2O3变为低熔点的球状CaO-Al2O3系夹杂物,易于从钢水中分离);(6)促进夹杂物在结晶器内的上浮分离(采用合适的浸入式水口出口形状和倾角;合理控制水口浸入深度;选用合适的保护渣;保持结晶器液面稳定)。
4、简述铸坯表面纵裂纹的产生原因及防止措施。
答:(1)钢水温度过高或拉速过快;(2)中间包水口与结晶器水口不对中或浇注中水口变形,钢流偏移,靠近钢流一边的坯生长减慢,坯壳减薄,造成裂纹;(3)结晶器冷却水量不足,水缝流速低;(4)结晶器使用时间过长,铜管损伤、磨损、变形严重;(5)结晶器足辊调节不当;(6)二冷区弧变误差大;(7)二冷水喷嘴位置不当,水嘴堵塞或水管漏不均可造成二次冷却不均;(8)结晶器润滑不良;(9)钢液面波动过大;(10)钢中碳含量处于裂纹敏感区。
防止措施:(1)严格控制好钢水浇注温度;(2)严格控制好结晶器水压、水流量、水温差和进水温度,确保有足够的冷却强度;(3)认真进行结晶器的检查维护工作,建立铜管管理档案;(4)定期检查结晶器、导向架的弧度;(5)二冷系统要勤检查、勤维护,保证水嘴位置均匀,水流畅通;(6)拉坯速度稳定;(7)中间包水口严格对中。
钢中夹杂物的产生与去除途径
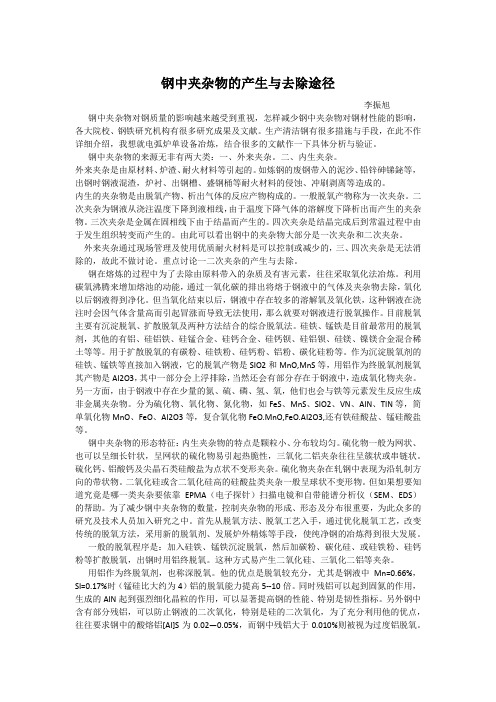
钢中夹杂物的产生与去除途径李振旭钢中夹杂物对钢质量的影响越来越受到重视,怎样减少钢中夹杂物对钢材性能的影响,各大院校、钢铁研究机构有很多研究成果及文献。
生产清洁钢有很多措施与手段,在此不作详细介绍,我想就电弧炉单设备冶炼,结合很多的文献作一下具体分析与验证。
钢中夹杂物的来源无非有两大类:一、外来夹杂。
二、内生夹杂。
外来夹杂是由原材料、炉渣、耐火材料等引起的。
如炼钢的废钢带入的泥沙、铅锌砷锑鉍等,出钢时钢液混渣,炉衬、出钢槽、盛钢桶等耐火材料的侵蚀、冲刷剥离等造成的。
内生的夹杂物是由脱氧产物、析出气体的反应产物构成的。
一般脱氧产物称为一次夹杂。
二次夹杂为钢液从浇注温度下降到液相线,由于温度下降气体的溶解度下降析出而产生的夹杂物。
三次夹杂是金属在固相线下由于结晶而产生的。
四次夹杂是结晶完成后到常温过程中由于发生组织转变而产生的。
由此可以看出钢中的夹杂物大部分是一次夹杂和二次夹杂。
外来夹杂通过现场管理及使用优质耐火材料是可以控制或减少的,三、四次夹杂是无法消除的,故此不做讨论。
重点讨论一二次夹杂的产生与去除。
钢在熔炼的过程中为了去除由原料带入的杂质及有害元素,往往采取氧化法冶炼。
利用碳氧沸腾来增加熔池的动能,通过一氧化碳的排出将熔于钢液中的气体及夹杂物去除,氧化以后钢液得到净化。
但当氧化结束以后,钢液中存在较多的溶解氧及氧化铁,这种钢液在浇注时会因气体含量高而引起冒涨而导致无法使用,那么就要对钢液进行脱氧操作。
目前脱氧主要有沉淀脱氧、扩散脱氧及两种方法结合的综合脱氧法。
硅铁、锰铁是目前最常用的脱氧剂,其他的有铝、硅铝铁、硅锰合金、硅钙合金、硅钙钡、硅铝钡、硅镁、镍镁合金混合稀土等等。
用于扩散脱氧的有碳粉、硅铁粉、硅钙粉、铝粉、碳化硅粉等。
作为沉淀脱氧剂的硅铁、锰铁等直接加入钢液,它的脱氧产物是SIO2和MnO,MnS等,用铝作为终脱氧剂脱氧其产物是AI2O3,其中一部分会上浮排除,当然还会有部分存在于钢液中,造成氧化物夹杂。
铸钢铸锭中产生夹杂物的原因

炼钢、铸锭过程中产生非金属夹杂物的原因摘要:论述钢中非金属夹杂物对钢锭质圣的影响,分析了非金属夹杂物在冶炼和铸锭过程中产生的原因,提出了控制夹杂物产生的几点行之有效的措施。
关键词:非金属夹杂物冶炼浇注电弧炉精炼炉质控制2010-02-02 08:34非金属夹杂物,一般是指钢锭在冶炼和浇注过程中产生或混人的非金属相,都是一些金属元素(Fe、Mn、Al等)及51与非金属元素(0、S、N、P、C等)结合而生成的氧化物和硫化物(如Feo、Si02、Mno、A12O3、MnS、MnC)等。
非金属夹杂物按来源分为内生夹杂物和外来夹杂物。
内生夹杂物是钢内部发生的反应产物或者因为温度降低而形成夹杂析出。
外来夹杂物是由炉料带人,耐火材料及炉渣混人的颗粒。
内生夹杂物可以以外来夹杂物为核心聚集到后者的颗粒上。
外来夹杂物也可能与钢液反应被还原。
钢中如果有非金属夹杂物的存在,即使在钢中含量极少(通常是小于万分之一)也会给钢的质量带来极为有害的影响。
从2002年1~7月份重点产品的投料统计情况看,锻钢支承辊共生产68支,经探伤发现其中2支因有密集夹杂物缺陷而报废,有4支因有夹杂物等缺陷造成锻造裂纹。
电站锻件钢共生产41支,经探伤发现其中4支有严重的条状缺陷,缺陷性质为夹杂物。
半钢辊钢共生产27支,其中14支因夹杂物造成不同程度的裂纹。
可见夹杂物对钢锭质量造成的经济损失是非常巨大的。
1 冶炼过程中产生非金属夹杂物的原因造渣材料碱性电弧炉常用的造渣材料采用石灰、萤石。
石灰,主要成份为C aO,其含量不应小于85%,SiO2含量不大于2%,硫含量应小于0.15%。
石灰易吸收水分而变成粉末,所以,造渣时要使用刚烧好的、烧透的石灰,或对石灰进行预热后再使用,这样能防止石灰给钢液带人过多的水分,否则就会使钢液氢含量增加,影响钢的质量,严重时会使钢报废。
连铸坯夹杂物产生原因分析及改进

连铸坯夹杂物产生原因分析及改进一、引言连铸是一种重要的钢铁生产工艺,通过将液态金属直接连续浇注成坯,在一定程度上能够提高铸坯质量,提高生产效率。
在连铸生产过程中,常常会出现夹杂物问题,严重影响了铸坯的质量和使用性能。
对连铸坯夹杂物产生原因进行深入分析,找出问题根源,采取相应的改进措施,是非常有必要的。
二、连铸坯夹杂物的产生原因分析1.原料水分过高在连铸生产过程中,原料的水分含量过高是造成坯内夹杂物的一个重要原因。
当原料表面的水分在铸造过程中蒸发时,会产生气泡,导致坯内夹杂物的生成。
原料的水分控制非常重要。
2.连铸坯结晶器冷却不足结晶器的冷却不足也是连铸坯夹杂物的常见原因之一。
当结晶器温度过高时,坯内的气体无法充分排出,导致夹杂物的产生。
保证结晶器的有效冷却是减少坯内夹杂物的关键。
3.连铸过程中的气体包被排除不彻底在连铸过程中,气体包会随着液态金属一起进入坯内,如果气体包排除不彻底,就会在坯内停留,并在坯内形成夹杂物。
连铸过程中对气体排除的控制非常重要。
4.结晶器内流动状态不佳结晶器内的流动状态不佳也会导致坯内夹杂物的产生。
如果结晶器内的金属流动不畅,坯内的气体排出不畅,就会产生夹杂物。
结晶器内流动状态的改善对减少坯内夹杂物至关重要。
6.连铸坯冷却过程不足连铸坯冷却过程不足也是坯内夹杂物产生的一个重要原因。
在坯冷却过程中,如果冷却不足,坯内的气体和夹杂物无法充分排出,就会在坯内停留,影响坯的质量。
三、连铸坯夹杂物产生原因改进方案1.加强对原料水分的控制首先要加强对原料水分的控制,确保原料表面的水分含量符合要求。
通过调整原料的储存和运输环节,减少原料表面的水分含量,从源头上减少坯内夹杂物的产生。
2.优化结晶器冷却系统优化结晶器冷却系统,确保结晶器的冷却效果达到要求。
通过调整冷却水的流量和温度,确保结晶器内的金属流动状态良好,坯内的气体排出畅通。
3.加强气体排除措施在连铸过程中,加强气体排除措施,确保气体包在坯内充分排除。
对减少C级钢夹杂物的几点意见

减少C级钢夹杂物的工艺分析要减少钢的夹杂物就必须了解钢中夹杂物的种类及性质、来源等,综合分析,钢中夹杂物的来源有以下几个方面:1.原材料中的杂质等。
2.耐火材料带入的夹杂,其中包括熔池砖的腐蚀,包子砖、注口砖的冲刷等。
3.夹渣、夹砂等4.冶炼及浇注过程中未能及时上浮的的反应产物。
以上就是钢中夹杂物的几个来源,其中2、4两种在钢中所占的比例是比较大的,要想减少夹杂物就必须从这几个来源上入手。
特有以下几点意见:1.通过电弧炉的三期炼钢,特别是加强静沸腾的操作能大大的减少氧化期之前带入的各种杂质及钢中的各种气体,同时这也是保证钢水质量的最重要措施。
2.冶炼及浇注过程中未能及时上浮的脱氧产物是相对难去除的一类夹杂,就我分厂现在的工艺来说,采用单加锰铁和硅铁的沉淀脱氧方式虽然能较快的达到还原脱氧的效果,但大的增加了钢水中的氧化系夹杂,要解决这个问题就必须使脱氧产物能尽快的上浮。
形成低熔点的、颗粒大的氧化物甚至氧化络合物,界面张力大的氧化物是最利于上浮的。
针对这两点有如下几种措施:①,单纯锰的脱氧产物MnO和硅的脱氧产物SiO2熔点都在1700℃以上,且聚合上浮速度非常慢,而MnO ·SiO2的熔点仅为1200℃多,且颗粒相对较大,特别容易上浮,现有工艺中采取先加锰后加硅也是基于次点考虑。
若能在同一时间、同一区域内形成合适比例的MnO和SiO2就能很大程度的减少该类夹杂,因此,建议采用合适比例的硅锰合金能有效的解决这个问题。
②,适当加大终脱氧用铝量,铝的脱氧产物是界面张力相对较大的一类氧化物,非常易于上浮,在上浮过程中还与其他脱氧产物络合增大将其他脱氧产物带出钢水。
3.耐火材料带入的夹杂是现在C级钢中的另一类相对较多的夹杂,经过对现在用包子砖的调查,在一次使用过程中(特别是C级钢镇静时间要求相对较长)能冲刷、腐蚀掉5~8mm左右,若能将现在包子砖改为高铝砖甚至采用抗冲刷更好的镁碳砖,也能使此类夹杂大为减少。