如何避免车削时已加工表面的刀花
车加工时铁屑划伤解决方法
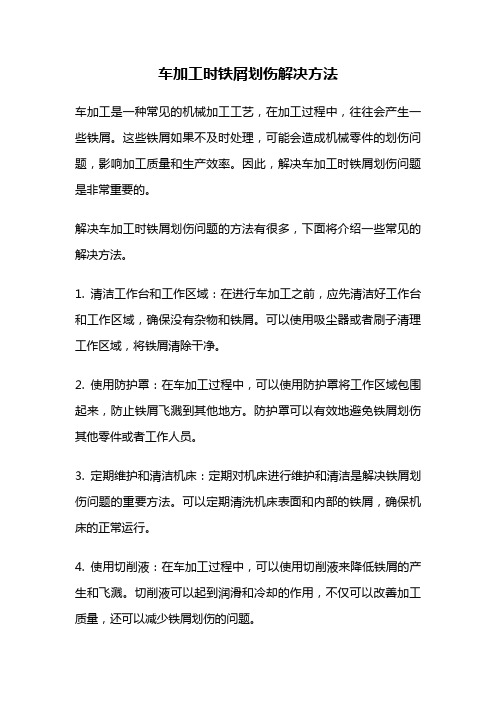
车加工时铁屑划伤解决方法车加工是一种常见的机械加工工艺,在加工过程中,往往会产生一些铁屑。
这些铁屑如果不及时处理,可能会造成机械零件的划伤问题,影响加工质量和生产效率。
因此,解决车加工时铁屑划伤问题是非常重要的。
解决车加工时铁屑划伤问题的方法有很多,下面将介绍一些常见的解决方法。
1. 清洁工作台和工作区域:在进行车加工之前,应先清洁好工作台和工作区域,确保没有杂物和铁屑。
可以使用吸尘器或者刷子清理工作区域,将铁屑清除干净。
2. 使用防护罩:在车加工过程中,可以使用防护罩将工作区域包围起来,防止铁屑飞溅到其他地方。
防护罩可以有效地避免铁屑划伤其他零件或者工作人员。
3. 定期维护和清洁机床:定期对机床进行维护和清洁是解决铁屑划伤问题的重要方法。
可以定期清洗机床表面和内部的铁屑,确保机床的正常运行。
4. 使用切削液:在车加工过程中,可以使用切削液来降低铁屑的产生和飞溅。
切削液可以起到润滑和冷却的作用,不仅可以改善加工质量,还可以减少铁屑划伤的问题。
5. 使用合适的刀具和切削参数:选择合适的刀具和切削参数也是解决铁屑划伤问题的关键。
刀具的选择应根据加工材料和加工要求来确定,切削参数的设置应合理,避免过大的切削力和过高的切削温度,从而减少铁屑的产生。
6. 做好工作人员的防护措施:在车加工过程中,工作人员应做好个人防护措施,如佩戴防护眼镜、手套和防护服等。
这样可以有效地保护工作人员不受铁屑划伤的影响。
7. 建立良好的工艺流程:建立良好的工艺流程对于解决铁屑划伤问题也非常重要。
要根据具体的加工要求和工艺特点,合理安排加工顺序和加工方法,减少铁屑产生的可能性。
车加工时铁屑划伤问题是一个需要重视和解决的技术难题。
通过采取适当的措施,如清洁工作台和工作区域、使用防护罩、定期维护和清洁机床、使用切削液、选择合适的刀具和切削参数、做好工作人员的防护措施和建立良好的工艺流程等,可以有效地解决车加工时铁屑划伤问题,提高加工质量和生产效率。
车槽时“啃刀”现象发生的原因及消除方法

OCCUPATION2011 11158车槽时“啃刀”现象发生的原因及消除方法文/骆海华采用一夹一顶安装,粗车双线梯形螺纹。
刀具安装:将制作好的双刀装在刀架上,刀尖位置应对准工件的旋转中心,且两刀尖角的对称中心线必须与工件轴线垂直,伸出的长度尽可能短,以增强刀具的刚性。
五、切削用量的选择采用双刀粗车梯形双线螺纹,提高生产效率,必须选择合理的切削速度和背吃刀量。
切削速度的选择应考虑两点。
一是安全,避免发生人身事故或车床、刀具损坏等事故。
二是零件加工过程中留有合适精加工余量。
切削速度高、效率高,但刀具耐用度会降低。
根据刀具材料和工艺刚性、机床、工件的安装方式、退刀槽的宽度等,选切削速度10m/min较合适。
从工件直径,通过计算,取主轴转速为105r/min。
车削前,检查车床(包含床鞍、中滑板、小滑板、刻度盘、刀架)间隙量并作调整。
如果间隙大,受到较大切削力的作用,就会产生扎刀、振动、损坏刀具等问题。
车削时,加充足的乳化液,因为乳化液可吸收切削中大量的热量,改善切削条件,提高刀具的寿命。
背吃刀量第一刀取0.8mm,以后进刀逐步减小,并利用小滑板两边借刀,减小切削力,避免“扎刀”,注意牙两侧留有合适的精加工余量,直至车到螺纹小径尺寸(留0.2mm精车余量)。
六、结论采用倒顺车粗加工Tr30×10(P5),用一把刀粗车双线梯形螺纹(包括分线)和用制作的双刀粗车双线梯形螺纹(一次进刀加工两条螺旋槽)的比较结论如下:用一把刀粗车Tr30×10(P5),长度25mm,所用时间约25分钟;而用双刀粗车Tr30×10(P5),长度25mm,所用时间约10分钟。
通过对比,用双刀粗车双线梯形螺纹比用一把刀粗车双线梯形螺纹时间缩短一半多,大大提高了劳动生产率。
由于提高了粗车双线梯形螺纹的效率,因此这批导程为10毫米的双线梯形螺纹轴能按时、按质完成。
采用双刀粗车双线梯形螺纹必须注意:一是退刀槽的宽度大于或等于一个导程;二是适用于加工导程为12毫米及以下的双线螺纹。
数控机床加工出现刀痕的预防与改善
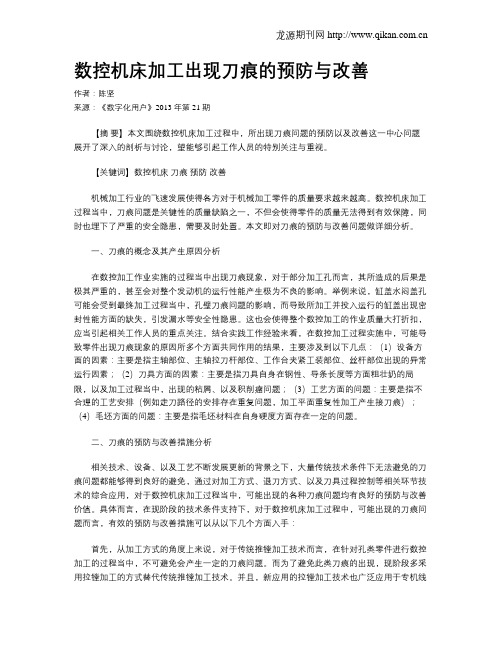
数控机床加工出现刀痕的预防与改善作者:陈坚来源:《数字化用户》2013年第21期【摘要】本文围绕数控机床加工过程中,所出现刀痕问题的预防以及改善这一中心问题展开了深入的剖析与讨论,望能够引起工作人员的特别关注与重视。
【关键词】数控机床刀痕预防改善机械加工行业的飞速发展使得各方对于机械加工零件的质量要求越来越高。
数控机床加工过程当中,刀痕问题是关键性的质量缺陷之一,不但会使得零件的质量无法得到有效保障,同时也埋下了严重的安全隐患,需要及时处置。
本文即对刀痕的预防与改善问题做详细分析。
一、刀痕的概念及其产生原因分析在数控加工作业实施的过程当中出现刀痕现象,对于部分加工孔而言,其所造成的后果是极其严重的,甚至会对整个发动机的运行性能产生极为不良的影响。
举例来说,缸盖水闷盖孔可能会受到最终加工过程当中,孔壁刀痕问题的影响,而导致所加工并投入运行的缸盖出现密封性能方面的缺失,引发漏水等安全性隐患。
这也会使得整个数控加工的作业质量大打折扣,应当引起相关工作人员的重点关注。
结合实践工作经验来看,在数控加工过程实施中,可能导致零件出现刀痕现象的原因所多个方面共同作用的结果,主要涉及到以下几点:(1)设备方面的因素:主要是指主轴部位、主轴拉刀杆部位、工作台夹紧工装部位、丝杆部位出现的异常运行因素;(2)刀具方面的因素:主要是指刀具自身在钢性、导条长度等方面粗壮奶的局限,以及加工过程当中,出现的粘屑、以及积削瘤问题;(3)工艺方面的问题:主要是指不合理的工艺安排(例如走刀路径的安排存在重复问题,加工平面重复性加工产生接刀痕);(4)毛坯方面的问题:主要是指毛坯材料在自身硬度方面存在一定的问题。
二、刀痕的预防与改善措施分析相关技术、设备、以及工艺不断发展更新的背景之下,大量传统技术条件下无法避免的刀痕问题都能够得到良好的避免,通过对加工方式、退刀方式、以及刀具过程控制等相关环节技术的综合应用,对于数控机床加工过程当中,可能出现的各种刀痕问题均有良好的预防与改善价值。
车床加工常见粗糙度缺陷的原因及排除

车床加工常见粗糙度缺陷的原因及排除在机械加工过程中,由于切屑分离时的塑性变形、工艺系统的振动、刀具与已加工表面间的摩擦等因素的影响,使加工后的工件表面总会存在许多高低不平的微小峰谷。
这些零件被加工表面上的微观几何形状误差称为表面粗糙度,它与机械零件的配合性质、耐磨性、疲劳强度、工作精度以及抗腐蚀性等有着密切的关系,直接影响到产品的工作可靠性和使用寿命。
在车床加工中,常见的影响表面粗糙度过大的表现形式为:刀痕粗糙、积屑瘤引起的硬点毛刺、磨损亮斑、划伤和拉毛等。
针对以上因素,我们分别进行了原因分析,并采取了相应的预防措施及排除办法。
一、刀痕粗糙刀痕粗糙通常表现为已加工表面经切削后残留下清楚的加工轮廓,刀痕清晰、均匀,但刀痕较粗,这种粗糙度缺陷经常在加大了切削用量的时候产生。
进给量、主偏角、刀尖圆弧半径都会影响残留面积高度,解决这种粗糙度缺陷可采取下列措施:1.在切削时,尽可能减小进给量,使加工细化。
但需要注意的是,进给量太小,刀具又钝,切削不能顺利进行,反倒会影响粗糙度。
2.刀具方面,在刃磨刀具时,减小主偏角、副偏角,增大刀尖圆弧半径,都可以降低残留面积高度,减小表面粗糙度。
但主偏角太小,刀尖圆弧半径太大,使背向力增加,刀刃会在工件表面打滑或引起振动而影响表面粗糙度。
减小副偏角是减小表面粗糙度的有效措施,减小副偏角等于加大了已加工表面修磨面积,对减小表面粗糙度效果较为明显。
采用修光刃也是减小残留面积高度的有效措施。
适当增大前角,可减小变形,有利于减小表面粗糙度值;适当增大后角,可减小刀具与工件的磨擦和积压,也有利于减小表面粗糙度值,但后角过大,易引起振动。
应注意的是,适当增大刀尖圆弧半径,或在副偏角上适当增加一个修光刃,这两项措施必须在工艺系统刚性允许的条件下增设,若工艺系统刚性不允许,会导致机床及工艺系统产生振动,引起工件产生振纹,从而影响表面粗糙度值。
二、积屑瘤产生硬点毛刺在刀具切削过程中,塑性金属在摩擦和变形的过程中,使切屑与前刀面之间产生了高压、高温。
如何避免车削时已加工表面的刀花
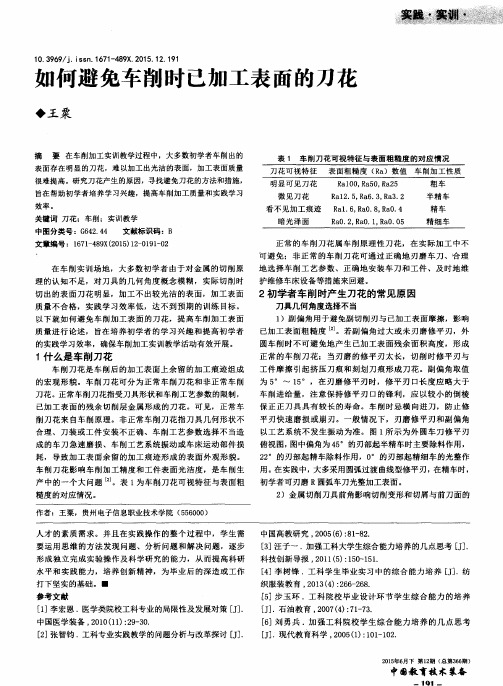
如 何避 免车 削时 已加工表 面的刀花
◆ 王 粟
摘 要 在 车 削加 工 实训 教学 过程 中,大 多数 初 学者 车 削出 的
表面 存在 明 显 的刀 花 ,难 以加 工 出光 洁 的表 面 ,加 工表 面质 量
中国高教研 究 , 2 0 0 5 ( 6 ) : 8 1 — 8 2 .
[ 3 ] 汪子一 . 加强 工科 大学生综合能力培养 的几点思考 [ J ] .
科技创 新导报 , 2 0 1 1 ( 5 ) : 1 5 0 - 1 5 1 . [ 4 ] 李 树锋 .工科学生 毕业实 习中的综 合能力培 养 [ J ] .纺 织服装教育 , 2 0 1 3 ( 4 ) : 2 6 6 — 2 6 8 . [ 5 ]步玉 环 .工科 院校 毕业 设计环 节 学生 综合 能力 的培 养 [ J ] .石油教育 , 2 0 0 7 ( 4 ) : 7 1 — 7 4 8 9 X ( 2 0 1 5 ) 1 2 — 0 1 9 1 — 0 2
正常 的车 削刀花属 车削原理 性刀花 ,在实 际加工 中不 可避 免;非 正常 的车 削刀花可通 过正确 地刃磨 车刀 、合 理 地选 择车 削工 艺参数 、正确地安 装车 刀和工件 、及 时地维
中国医学装备 , 2 0 1 0 ( 1 1 ) : 2 9 - 3 0 .
[ 2 ] 张智钧 . 工科专业实践教学的问题分析 与改革探讨 [ J ] .
[ 6 ]刘 勇兵 .加 强工 科院 校学生 综合 能力 培养 的 几点 思考
[ J ] .现代教育科学 , 2 0 0 5 ( 1 ) : 1 0 1 - 1 0 2 .
车削切屑伤害的预防(三篇)
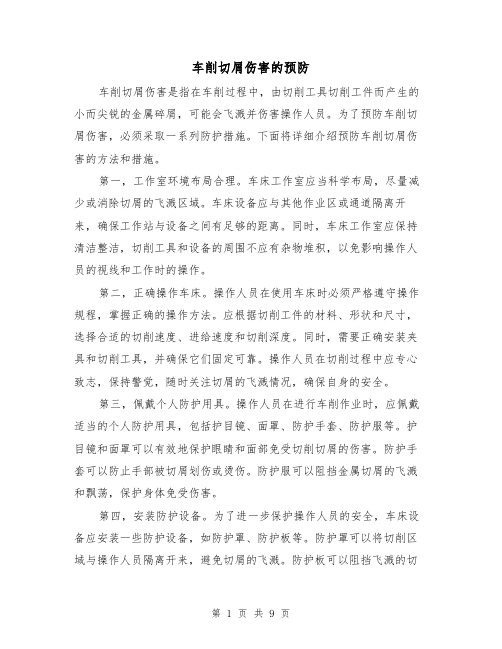
车削切屑伤害的预防车削切屑伤害是指在车削过程中,由切削工具切削工件而产生的小而尖锐的金属碎屑,可能会飞溅并伤害操作人员。
为了预防车削切屑伤害,必须采取一系列防护措施。
下面将详细介绍预防车削切屑伤害的方法和措施。
第一,工作室环境布局合理。
车床工作室应当科学布局,尽量减少或消除切屑的飞溅区域。
车床设备应与其他作业区或通道隔离开来,确保工作站与设备之间有足够的距离。
同时,车床工作室应保持清洁整洁,切削工具和设备的周围不应有杂物堆积,以免影响操作人员的视线和工作时的操作。
第二,正确操作车床。
操作人员在使用车床时必须严格遵守操作规程,掌握正确的操作方法。
应根据切削工件的材料、形状和尺寸,选择合适的切削速度、进给速度和切削深度。
同时,需要正确安装夹具和切削工具,并确保它们固定可靠。
操作人员在切削过程中应专心致志,保持警觉,随时关注切屑的飞溅情况,确保自身的安全。
第三,佩戴个人防护用具。
操作人员在进行车削作业时,应佩戴适当的个人防护用具,包括护目镜、面罩、防护手套、防护服等。
护目镜和面罩可以有效地保护眼睛和面部免受切削切屑的伤害。
防护手套可以防止手部被切屑划伤或烫伤。
防护服可以阻挡金属切屑的飞溅和飘荡,保护身体免受伤害。
第四,安装防护设备。
为了进一步保护操作人员的安全,车床设备应安装一些防护设备,如防护罩、防护板等。
防护罩可以将切削区域与操作人员隔离开来,避免切屑的飞溅。
防护板可以阻挡飞溅的切屑,确保切屑不会伤害到操作人员。
此外,车床设备的操作面板应安装在操作人员无法触及或误触的位置,避免误操作引发事故。
第五,定期维护和检查车床设备。
车床设备应定期进行维护和检查,保证设备的正常运转和安全性能。
切削工具和夹具应经常检查和更换,避免因磨损过度而产生切削切屑。
切削液应定期更换,保持清洁,以免切屑粘附在工件上形成危险。
以上就是预防车削切屑伤害的一些方法和措施。
在日常的车削作业中,操作人员和管理人员应共同加强安全意识,严格执行操作规程,正确佩戴个人防护用具,并定期检查维护车床设备,确保操作人员的安全。
车削加工作业伤害的预防

车削加工作业伤害的预防车削加工是制造业中常用的一种工艺,但由于加工过程中存在一定的风险,容易导致工人受伤。
为了预防车削加工作业伤害,需要从防护措施、操作规范和员工培训等方面综合考虑。
本文将从以下几个方面进行讨论。
一、防护措施1. 车削机床的防护:车削机床应该有有效的防护措施,如安全护罩、阻尼装置等,确保加工过程中尽量减少机械碰撞和切削物飞溅。
2. 加工物料的防护:对于易碎、易飞溅的材料,应采取适当的防护措施,如使用专用夹具、加工保持器等,避免材料碎片伤人。
3. 个体防护用品:工人应该配备个体防护用品,如安全帽、防护眼镜、防护手套等,以保护头部、眼睛和手部等易受伤的部位。
二、操作规范1. 制定明确的作业规程:制定车削加工作业的操作规程,明确操作流程、注意事项和安全警示,保证工人在加工过程中能够按规定进行操作。
2. 加工物料的正确夹持:正确夹持材料是防止工人受伤的关键。
工人应该学习正确的夹持方法,避免将手指或手部靠近切削区域。
3. 安全操作工具:使用锐利的车床刀具时,应注意安全操作工具的选择,确保切削刀具牢固、可靠,避免产生意外。
三、员工培训1. 人员技能培训:对车削加工作业的工人进行技能培训,使其熟练掌握车削加工的操作技巧和安全知识,能够正确使用车削机床和操作工具。
2. 安全教育培训:加强安全教育培训,宣传车削加工作业的危险性和伤害预防方法,提高工人的安全意识,使其时刻保持警觉。
3. 定期复训和考核:定期组织复训和考核,检验工人的安全知识和操作技能,及时纠正不规范操作和错误行为。
四、事故案例分析和经验总结1. 定期分析事故案例:定期组织车削加工作业事故案例的分析,探讨事故原因和规避方法,及时进行改进,提高安全性和效率。
2. 经验总结与分享:将经验总结和防护知识分享给整个企业,促使大家共同关注车削加工作业的安全问题,相互学习和改进。
3. 安全知识宣传教育:在工作区域张贴安全知识宣传海报,定期组织安全宣传教育活动,提高员工对车削加工作业伤害的预防意识。
车削加工作业伤害的预防(三篇)

车削加工作业伤害的预防车削加工是一种常见的金属加工方法,但由于操作复杂、危险性较高,容易造成工伤事故。
为了预防车削加工作业伤害,需要采取一系列的预防措施。
首先,进行车削作业前,必须进行必要的安全培训。
培训内容包括车削机的基本原理、操作规程、安全注意事项等。
培训旨在提高操作工人的安全意识和技能,使其能够正确使用车削机,避免发生事故。
其次,车削作业现场应保持整洁、明亮。
保持现场整洁可以减少操作工人的摔倒和滑倒的风险,避免工具和杂物的乱堆乱放。
同时,现场需要保持明亮的照明条件,以便操作工人能够清楚地看到操作区域,减少操作失误。
第三,操作工人在进行车削作业时,必须正确佩戴个人防护装备。
包括头盔、防护眼镜、防护面罩、防护手套等。
头盔可以保护头部免受坠落物和撞击的伤害,防护眼镜和面罩可以防止金属碎屑溅入眼睛和面部,防护手套可以保护双手免于切割和磨损。
第四,针对车削机的安全装置必须完好有效。
这些安全装置包括急停按钮、防护门、限位开关等。
急停按钮可以在紧急情况下立即停止车削机的运转,防护门能够防止工人误触车削刀具,限位开关则可限制车削机的运行范围,避免意外伤害。
第五,操作工人在车削作业过程中,要保持专注集中,严禁酒后操作或疲劳作业。
酒后操作和疲劳作业会降低工人的反应能力和注意力,容易造成操作失误,增加事故的发生概率。
第六,定期对车削机进行维护和检修,确保设备的正常运行。
车削机在长期使用过程中,设备会出现磨损和故障,如果不及时维修和更换部件,会增加事故的风险。
因此,建议定期对车削机进行维护和检修,并在必要时更换损坏的部件。
另外,对于重要的车削加工作业,可以采取工序划分、作业标准化等措施,降低操作工人的风险。
工序划分可以将复杂的车削作业分解成多个简单的工序,减少操作难度。
作业标准化可以确保每个操作工人都按照相同的操作流程进行工作,并进行互查互控,降低人为失误的发生。
总之,要预防车削加工作业伤害,需要从多个方面入手,包括提高操作工人的安全意识和技能、保持作业现场整洁明亮、正确佩戴个人防护装备、保持车削机的安全装置完好有效、认真检修维护设备、划分工序和作业标准化等。
车削加工如何消除接刀痕

车削加工如何消除接刀痕接刀痕是所有机械加工领域都要面对的问题。
在常规的车削加工中,为了避免出现接刀痕,都会尽可能安排同一个曲面在同一道工序用同一把刀加工完。
在加工回转类零件时,由于装夹方式相对单一,又因某些零件的特殊性,使得同一个曲面在一道工序下无法完成加工,这样,一个回转曲面就不得不分成两道工序加工,曲面接刀痕也就不可避免地产生了。
车床上消除不同工序间的接刀痕的方法一般而言,要消除接刀痕首先要有刚性足够的机床,两道工序的工装定位精度要高,端面跳动在0.01mm内,圆跳动在0.02mm内,好的车床夹具都能够很容易地保证这一点;其次,两道工序加工参数一致,刀具选择一致,这样有利于保证零件接刀痕两侧曲面的粗糙度、加工纹理等的一致性;最后,在加工过程中,两道工序的尺寸精度要求较高。
在车削过程中,暂将形成接刀痕的两道工序称之为上道工序和下道工序。
以下是具体的操作过程:(1)在上道工序中,粗车按照正常路径走刀,留给精车0.1mm 左右的余量;(2)精车时按正常路径切削,但在距离接刀边缘5mm的地方开始走锥度,锥度为1:250,此时会在接刀位置形成一个不明显的小锥度,锥度最高处比底部高约0.02mm;(3)下道工序中粗车按正常路径走刀,注意留给精车余量0.1mm;(4)精刀走刀时要走过接刀处约2mm,即让下道工序精车完上道工序中加工出来的小锥度。
这样,在回转曲面两道接刀处就不会产生明显的接刀痕迹。
需要注意的是,后道工序定位面尽量不要选择有锥度的地方,若该零件此两道工序均为毛坯定位时,应当在此之前安排合理的去余量工艺,以保证该零件装夹的一致性。
在实际生产过程中,一般会让上道工序比下道工序大0.01~0.02mm,这样会使得接刀痕迹的处理达到最佳效果。
数控机床操作中如何避免工件表面破坏的问题

数控机床操作中如何避免工件表面破坏的问题在数控机床操作中,保护工件表面,避免破坏是非常重要的。
工件表面的破坏不仅会影响产品质量,还会增加制造成本。
因此,在进行数控机床操作时,我们需要采取一系列措施来有效地避免工件表面的破坏问题。
首先,要严格控制数控机床的加工参数。
在进行加工操作前,我们需要了解工件的材料特性、结构和工艺要求等重要信息。
根据这些信息,合理设置数控机床的加工参数,包括切削速度、进给速度、切削深度等。
过高或过低的加工参数都可能导致工件表面的破坏。
因此,我们需要根据实际情况和经验进行合理设定,以保证工件能够得到精确而不损坏的加工。
其次,要选择合适的刀具材料和刀具几何形状。
刀具是数控机床加工中非常重要的设备,其选择对工件表面的破坏有着直接的影响。
对于硬度较高的工件材料,我们需要选择更耐磨损的刀具材料,并且保持刀具的锋利度。
此外,根据加工的需求,选择合适的刀具几何形状,以减少切削力集中,降低工件表面的破坏风险。
第三,要合理安装夹具和定位工具。
夹具和定位工具是数控机床操作中保护工件表面的重要手段。
在夹具选择和安装过程中,我们需要考虑工件的形状、尺寸和材料特性等因素,确保夹具能够牢固地固定工件,但不会对其表面造成过大的压力和摩擦。
定位工具的使用也要精确,以避免工件在加工过程中移动或发生偏差,导致表面破坏。
第四,要定期检查和维护数控机床设备。
不定期的设备检查和维护对于延长其使用寿命和保持其正常运行是至关重要的。
我们需要定期检查数控机床的各项设备,包括刀具夹具、润滑系统、传动系统等,并及时发现和解决存在的问题。
通过定期维护,我们能够保持设备的高效稳定工作,减少因设备故障引起的工件表面破坏问题。
最后,培养操作人员的专业技能和经验。
数控机床操作需要经验丰富的专业人员来进行控制和操作。
操作人员要熟悉机床设备的使用方法和特点,掌握操作技能,并具备解决问题的能力。
通过不断学习和实践,不仅能提高操作人员的操作水平和判断能力,还能有效避免因操作不当而导致的工件表面破坏。
磨刀怎么避免大花脸的方法
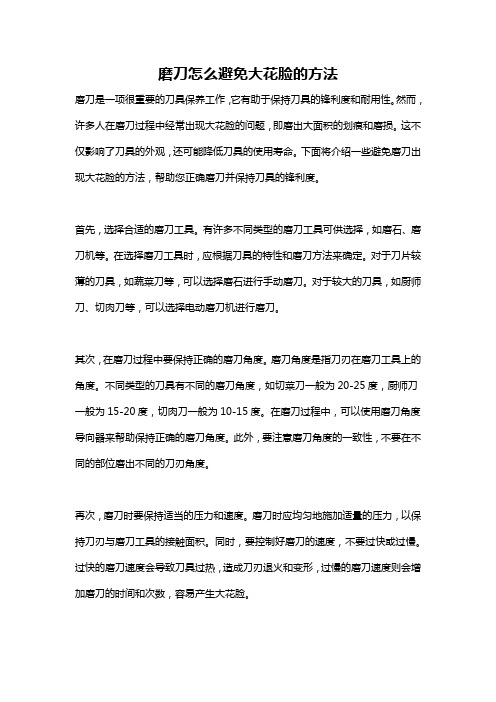
磨刀怎么避免大花脸的方法磨刀是一项很重要的刀具保养工作,它有助于保持刀具的锋利度和耐用性。
然而,许多人在磨刀过程中经常出现大花脸的问题,即磨出大面积的划痕和磨损。
这不仅影响了刀具的外观,还可能降低刀具的使用寿命。
下面将介绍一些避免磨刀出现大花脸的方法,帮助您正确磨刀并保持刀具的锋利度。
首先,选择合适的磨刀工具。
有许多不同类型的磨刀工具可供选择,如磨石、磨刀机等。
在选择磨刀工具时,应根据刀具的特性和磨刀方法来确定。
对于刀片较薄的刀具,如蔬菜刀等,可以选择磨石进行手动磨刀。
对于较大的刀具,如厨师刀、切肉刀等,可以选择电动磨刀机进行磨刀。
其次,在磨刀过程中要保持正确的磨刀角度。
磨刀角度是指刀刃在磨刀工具上的角度。
不同类型的刀具有不同的磨刀角度,如切菜刀一般为20-25度,厨师刀一般为15-20度,切肉刀一般为10-15度。
在磨刀过程中,可以使用磨刀角度导向器来帮助保持正确的磨刀角度。
此外,要注意磨刀角度的一致性,不要在不同的部位磨出不同的刀刃角度。
再次,磨刀时要保持适当的压力和速度。
磨刀时应均匀地施加适量的压力,以保持刀刃与磨刀工具的接触面积。
同时,要控制好磨刀的速度,不要过快或过慢。
过快的磨刀速度会导致刀具过热,造成刀刃退火和变形,过慢的磨刀速度则会增加磨刀的时间和次数,容易产生大花脸。
此外,磨刀前要确保刀具的干净和干燥。
刀具表面的油污和水份会影响磨刀效果,因此在磨刀前要先清洁刀具,并确保刀具完全干燥。
可以使用清洁剂和刷子清洁刀具,然后用干净的毛巾擦干。
磨刀时要保持磨刀工具的清洁,及时清理磨石或磨刀机上的刀屑和金属粉末。
最后,要定期进行磨刀,并且不要等到刀具过于钝才进行磨刀。
刀具在使用中会逐渐变钝,如果等到刀具完全变钝才进行磨刀,往往需要更多的时间和力气来磨刀,并且易产生大花脸。
因此,建议定期检查刀具的锋利度,并及时进行磨刀。
一般来说,家庭使用的刀具每隔2-3个月进行磨刀即可。
总之,避免磨刀出现大花脸的关键在于选择合适的磨刀工具,保持正确的磨刀角度,施加适当的压力和速度,确保刀具的干净和干燥,以及定期进行磨刀。
车削切屑伤害的预防范文(二篇)
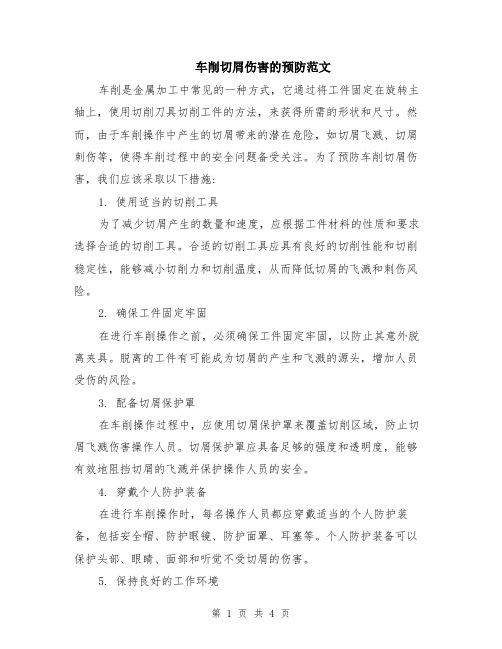
车削切屑伤害的预防范文车削是金属加工中常见的一种方式,它通过将工件固定在旋转主轴上,使用切削刀具切削工件的方法,来获得所需的形状和尺寸。
然而,由于车削操作中产生的切屑带来的潜在危险,如切屑飞溅、切屑刺伤等,使得车削过程中的安全问题备受关注。
为了预防车削切屑伤害,我们应该采取以下措施:1. 使用适当的切削工具为了减少切屑产生的数量和速度,应根据工件材料的性质和要求选择合适的切削工具。
合适的切削工具应具有良好的切削性能和切削稳定性,能够减小切削力和切削温度,从而降低切屑的飞溅和刺伤风险。
2. 确保工件固定牢固在进行车削操作之前,必须确保工件固定牢固,以防止其意外脱离夹具。
脱离的工件有可能成为切屑的产生和飞溅的源头,增加人员受伤的风险。
3. 配备切屑保护罩在车削操作过程中,应使用切屑保护罩来覆盖切削区域,防止切屑飞溅伤害操作人员。
切屑保护罩应具备足够的强度和透明度,能够有效地阻挡切屑的飞溅并保护操作人员的安全。
4. 穿戴个人防护装备在进行车削操作时,每名操作人员都应穿戴适当的个人防护装备,包括安全帽、防护眼镜、防护面罩、耳塞等。
个人防护装备可以保护头部、眼睛、面部和听觉不受切屑的伤害。
5. 保持良好的工作环境为了预防车削切屑伤害,必须保持良好的工作环境。
工作区域应清洁整齐,避免杂物和油污积聚。
此外,应定期对车削设备进行维护和保养,确保其正常运转,减少意外事故的发生。
6. 提供相关培训和教育为了提高操作人员的安全意识和技能,必须提供相关培训和教育。
操作人员应了解车削切屑的危害和预防措施,并熟悉正确的操作方法和紧急处理措施。
他们还应定期接受安全培训,更新相关知识和技能。
7. 建立安全管理制度为了确保车削操作安全可靠,应建立健全的安全管理制度。
通过制定和执行安全规章制度,对车削操作进行管理和监督,包括安全检查、安全记录、事故调查和应急预案等。
同时,还应加强安全意识和责任意识的培养,使每个人都能够以安全为先,形成良好的安全风气。
车削切屑伤害的预防
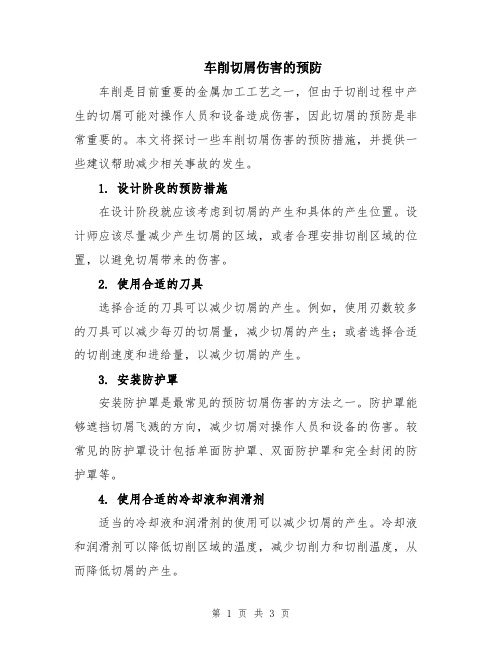
车削切屑伤害的预防车削是目前重要的金属加工工艺之一,但由于切削过程中产生的切屑可能对操作人员和设备造成伤害,因此切屑的预防是非常重要的。
本文将探讨一些车削切屑伤害的预防措施,并提供一些建议帮助减少相关事故的发生。
1. 设计阶段的预防措施在设计阶段就应该考虑到切屑的产生和具体的产生位置。
设计师应该尽量减少产生切屑的区域,或者合理安排切削区域的位置,以避免切屑带来的伤害。
2. 使用合适的刀具选择合适的刀具可以减少切屑的产生。
例如,使用刃数较多的刀具可以减少每刃的切屑量,减少切屑的产生;或者选择合适的切削速度和进给量,以减少切屑的产生。
3. 安装防护罩安装防护罩是最常见的预防切屑伤害的方法之一。
防护罩能够遮挡切屑飞溅的方向,减少切屑对操作人员和设备的伤害。
较常见的防护罩设计包括单面防护罩、双面防护罩和完全封闭的防护罩等。
4. 使用合适的冷却液和润滑剂适当的冷却液和润滑剂的使用可以减少切屑的产生。
冷却液和润滑剂可以降低切削区域的温度,减少切削力和切削温度,从而降低切屑的产生。
5. 使用切屑清理装置切屑清理装置可以有效地清理产生的切屑,避免切屑堆积。
切屑堆积会增加切削区域的热量,增加切屑的飞溅风险。
6. 定期维护设备定期维护设备可以确保设备的正常运转。
检查各个部件的磨损情况,及时更换磨损严重的部件,以减少切屑的产生和相关伤害的发生。
7. 培训操作人员培训操作人员熟悉设备的正确操作和使用防护装置是预防切屑伤害的重要环节。
操作人员应该了解切削过程中的潜在危险和应对措施,熟悉防护装置的使用方法,并掌握正确的切削工艺。
8. 强化安全意识所有工作人员都应该时刻保持高度的安全意识。
清晰的标识和警示提醒可以帮助人员迅速识别和规避潜在危险。
9. 建立维护规范建立一套科学且明确的维护规范是预防切屑伤害的关键。
维护规范应包括设备的定期检查和维护流程、切削参数的调整和标定方法、切屑清理装置的使用和维护方法等。
10. 按规程操作按照规程操作是保证操作人员的安全的基本要求。
数控车床加工时,切屑总是缠刀怎么办?分享十条小方法
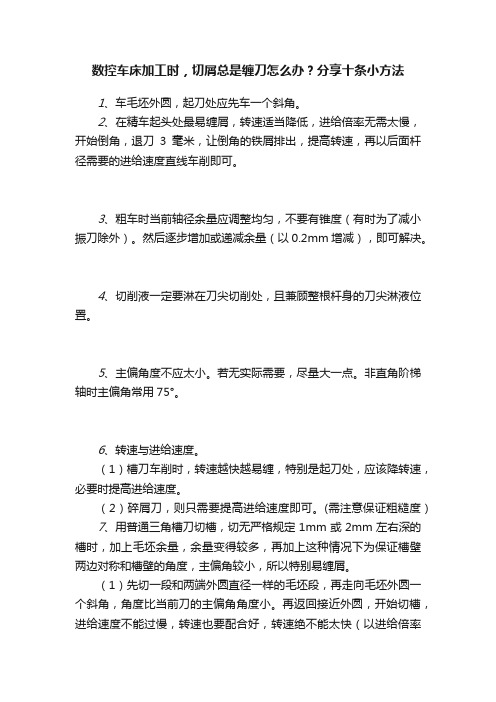
数控车床加工时,切屑总是缠刀怎么办?分享十条小方法1、车毛坯外圆,起刀处应先车一个斜角。
2、在精车起头处最易缠屑,转速适当降低,进给倍率无需太慢,开始倒角,退刀3毫米,让倒角的铁屑排出,提高转速,再以后面杆径需要的进给速度直线车削即可。
3、粗车时当前轴径余量应调整均匀,不要有锥度(有时为了减小振刀除外)。
然后逐步增加或递减余量(以0.2mm增减),即可解决。
4、切削液一定要淋在刀尖切削处,且兼顾整根杆身的刀尖淋液位置。
5、主偏角度不应太小。
若无实际需要,尽量大一点。
非直角阶梯轴时主偏角常用75°。
6、转速与进给速度。
(1)槽刀车削时,转速越快越易缠,特别是起刀处,应该降转速,必要时提高进给速度。
(2)碎屑刀,则只需要提高进给速度即可。
(需注意保证粗糙度)7、用普通三角槽刀切槽,切无严格规定1mm或2mm左右深的槽时,加上毛坯余量,余量变得较多,再加上这种情况下为保证槽壁两边对称和槽壁的角度,主偏角较小,所以特别易缠屑。
(1)先切一段和两端外圆直径一样的毛坯段,再走向毛坯外圆一个斜角,角度比当前刀的主偏角角度小。
再返回接近外圆,开始切槽,进给速度不能过慢,转速也要配合好,转速绝不能太快(以进给倍率在150%时,编程“F”值在160至260左右,主轴转速在1500~1700r/min左右,但也并非一定要在这样的范围,根据实际情况及产品需要、机床性能和车工经验自行定)。
(2)为保险起见,降低缠屑的概率,保证减少因余量过多副偏角擦工件引起的边角毛刺。
最好分两刀车,粗车时适当降低转速,进给倍率适当提高车削,且为精车预留较少的余量,精车时提高转速和进给倍率,可保证粗糙度和时效。
8、产品的材质需要选用合适硬度的刀具,材质较软的产品需要刀刃锋利和排屑非常顺畅的槽刀,材质较硬的产品需要刀刃稍钝一些,可以选择碎屑刀,则不会存在缠屑。
9、用槽刀时,不要让铁屑从刀尖处垂直而下,应该安装一个铁钩,让铁屑离工件一段距离垂下。
车削切屑伤害的预防
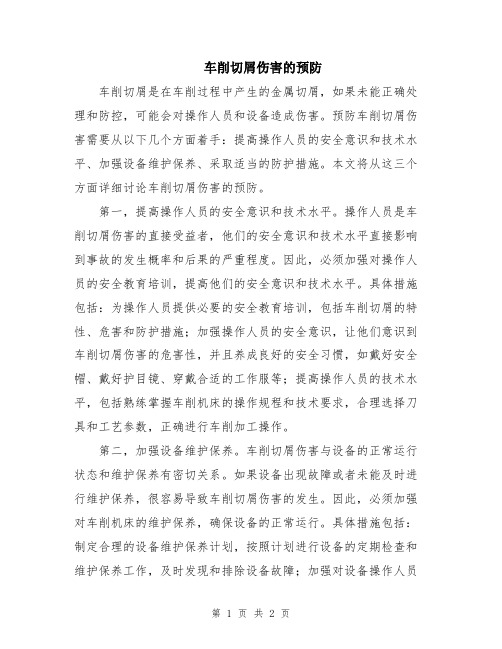
车削切屑伤害的预防车削切屑是在车削过程中产生的金属切屑,如果未能正确处理和防控,可能会对操作人员和设备造成伤害。
预防车削切屑伤害需要从以下几个方面着手:提高操作人员的安全意识和技术水平、加强设备维护保养、采取适当的防护措施。
本文将从这三个方面详细讨论车削切屑伤害的预防。
第一,提高操作人员的安全意识和技术水平。
操作人员是车削切屑伤害的直接受益者,他们的安全意识和技术水平直接影响到事故的发生概率和后果的严重程度。
因此,必须加强对操作人员的安全教育培训,提高他们的安全意识和技术水平。
具体措施包括:为操作人员提供必要的安全教育培训,包括车削切屑的特性、危害和防护措施;加强操作人员的安全意识,让他们意识到车削切屑伤害的危害性,并且养成良好的安全习惯,如戴好安全帽、戴好护目镜、穿戴合适的工作服等;提高操作人员的技术水平,包括熟练掌握车削机床的操作规程和技术要求,合理选择刀具和工艺参数,正确进行车削加工操作。
第二,加强设备维护保养。
车削切屑伤害与设备的正常运行状态和维护保养有密切关系。
如果设备出现故障或者未能及时进行维护保养,很容易导致车削切屑伤害的发生。
因此,必须加强对车削机床的维护保养,确保设备的正常运行。
具体措施包括:制定合理的设备维护保养计划,按照计划进行设备的定期检查和维护保养工作,及时发现和排除设备故障;加强对设备操作人员的技术培训,提高其对设备的操作和维护能力;定期检查和维护设备的防护装置,确保其正常运行和有效防护。
第三,采取适当的防护措施。
车削切屑伤害的发生主要是因为切屑溅射和切削刀具的脱落等原因,因此,必须采取适当的防护措施,以减少事故的发生概率和后果的严重程度。
具体措施包括:加装防护罩或安全屏障,以阻挡切屑溅射和刀具脱落,注意防止切屑飞溅着火的情况发生;加装护目镜和耳塞等个体防护装备,以保护操作人员的视听器官;对容易产生大量切屑的工件进行合理的固定和夹紧,以减少切屑的产生;定期清理工作区域,防止切屑堆积和引发其他事故。
如何防止工件划碰伤
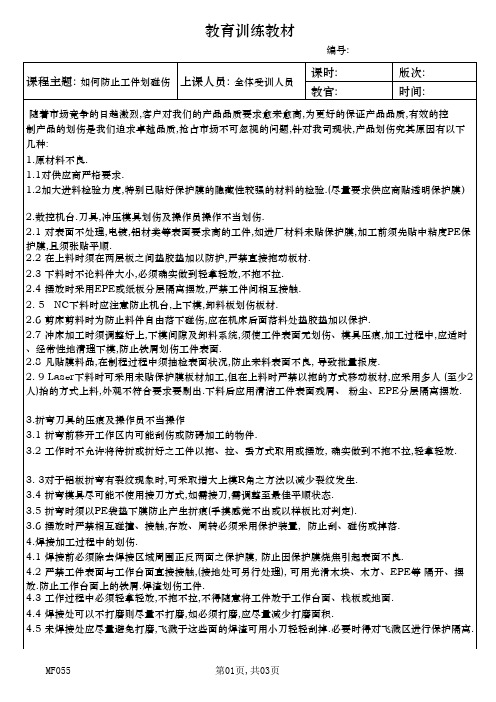
教育训练教材
编号:
课程主题: 如何防止工件划碰伤 上课人员: 全体受训人员
课时: 教官:
版次: 时间:
随着市场竞争的日趋激烈,客户对我们的产品品质要求愈来愈高,为更好的保证产品品质,有效的控 制产品的划伤是我们追求卓越品质,抢占市场不可忽视的问题,针对我司现状,产品划伤究其原因有以下 几种: 1.原材料不良. 1.1对供应商严格要求. 1.2加大进料检验力度,特别已贴好保护膜的隐藏性较强的材料的检验.(尽量要求供应商贴透明保 护膜) 2.数控机台.刀具,冲压模具划伤及操作员操作不当划伤. 2.1 对表面不处理,电镀,铝材类等表面要求高的工件,如进厂材料未贴保护膜,加工前须先贴中粘 度PE保护膜,且须张贴平顺. 2.2 在上料时须在两层板之间垫胶垫加以防护,严禁直接拖动板材. 2.3 下料时不论料件大小,必须确实做到轻拿轻放,不拖不拉. 2.4 摆放时采用EPE或纸板分层隔离摆放,严禁工件间相互接触. 2. 5 NC下料时应注意防止机台,上下模,卸料板划伤板材. 2.6 剪床剪料时为防止料件自由落下碰伤,应在机床后面落料处垫胶垫加以保护. 2.7 冲床加工时须调整好上,下模间隙及卸料系统,须使工件表面无划伤、模具压痕,加工过程中, 应适时、经常性地清理下模,防止铁屑划伤工件表面. 2.8 凡贴膜料品,在制程过程中须抽检表面状况,防止来料表面不良, 导致批量报废. 2. 9 Laser下料时可采用未贴保护膜板材加工,但在上料时严禁以拖的方式移动板材,应采用多人 (至少2人)抬的方式上料,外观不符合要求要剔出.下料后应用清洁工件表面残屑、 粉尘、EPE分 层隔离摆放. 3.折弯刀具的压痕及操作员不当操作 3.1 折弯前移开工作区内可能刮伤或防碍加工的物件. 3.2 工作时不允许将待折或折好之工件以拖、拉、丢方式取用或摆放, 确实做到不拖不拉,轻拿 轻放. 3. 3对于铝板折弯有裂纹现象时,可采取增大上模R角之方法以减少裂纹发生. 3.4 折弯模具尽可能不使用接刀方式,如需接刀,需调整至最佳平顺状态. 3.5 折弯时须以PE袋垫下膜防止产生折痕(手摸感觉不出或以样板比对判定). 3.6 摆放时严禁相互碰撞、接触,存放、周转必须采用保护装臵, 防止刮、碰伤或掉落. 4.焊接加工过程中的划伤. 4.1 焊接前必须除去焊接区域周围正反两面之保护膜, 防止因保护膜烧焦引起表面不良. 4.2 严禁工件表面与工作台面直接接触,(接地处可另行处理), 可用光滑木块、木方、EPE等 隔 开、摆放.防止工作台面上的铁屑.焊渣划伤工件. 4.3 工作过程中必须轻拿轻放,不拖不拉,不得随意将工件放于工作台面、栈板或地面. 4.4 焊接处可以不打磨则尽量不打磨,如必须打磨,应尽量减少打磨面积. 4.5 未焊接处应尽量避免打磨,飞溅于这些面的焊渣可用小刀轻轻刮掉.必要时得对飞溅区进行保 护隔离. MF055 第01页,共03页
如何预防毛刺
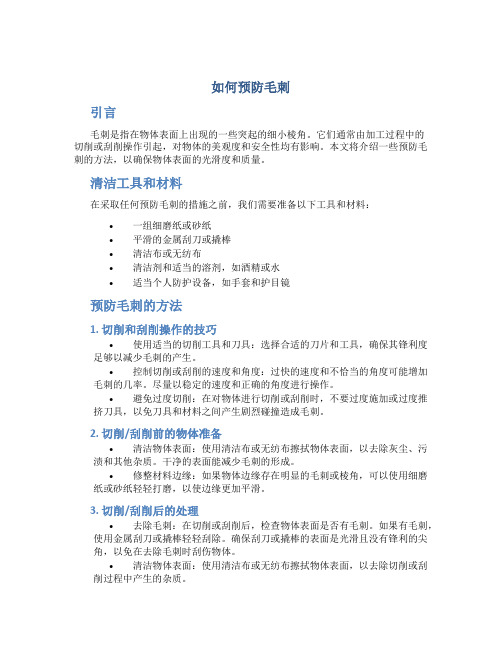
如何预防毛刺引言毛刺是指在物体表面上出现的一些突起的细小棱角。
它们通常由加工过程中的切削或刮削操作引起,对物体的美观度和安全性均有影响。
本文将介绍一些预防毛刺的方法,以确保物体表面的光滑度和质量。
清洁工具和材料在采取任何预防毛刺的措施之前,我们需要准备以下工具和材料:•一组细磨纸或砂纸•平滑的金属刮刀或撬棒•清洁布或无纺布•清洁剂和适当的溶剂,如酒精或水•适当个人防护设备,如手套和护目镜预防毛刺的方法1. 切削和刮削操作的技巧•使用适当的切削工具和刀具:选择合适的刀片和工具,确保其锋利度足够以减少毛刺的产生。
•控制切削或刮削的速度和角度:过快的速度和不恰当的角度可能增加毛刺的几率。
尽量以稳定的速度和正确的角度进行操作。
•避免过度切削:在对物体进行切削或刮削时,不要过度施加或过度推挤刀具,以免刀具和材料之间产生剧烈碰撞造成毛刺。
2. 切削/刮削前的物体准备•清洁物体表面:使用清洁布或无纺布擦拭物体表面,以去除灰尘、污渍和其他杂质。
干净的表面能减少毛刺的形成。
•修整材料边缘:如果物体边缘存在明显的毛刺或棱角,可以使用细磨纸或砂纸轻轻打磨,以使边缘更加平滑。
3. 切削/刮削后的处理•去除毛刺:在切削或刮削后,检查物体表面是否有毛刺。
如果有毛刺,使用金属刮刀或撬棒轻轻刮除。
确保刮刀或撬棒的表面是光滑且没有锋利的尖角,以免在去除毛刺时刮伤物体。
•清洁物体表面:使用清洁布或无纺布擦拭物体表面,以去除切削或刮削过程中产生的杂质。
•检查和修整:仔细检查物体表面,确保没有剩余的毛刺。
如果有,使用细磨纸或砂纸进行矫正。
4. 维护工具和设备的良好状态•定期保养工具:保持切削工具和刀具的锋利度和良好状态。
定期修整或更换刀片和刀具,以确保它们的效果和功能。
•保持清洁:定期清洁工具表面,确保其没有附着着附着物和积聚的杂质,以免在使用时引入毛刺。
结论通过正确的切削和刮削操作技巧、物体的准备和处理、以及对工具和设备的维护,我们可以有效地预防和减少毛刺的产生。
- 1、下载文档前请自行甄别文档内容的完整性,平台不提供额外的编辑、内容补充、找答案等附加服务。
- 2、"仅部分预览"的文档,不可在线预览部分如存在完整性等问题,可反馈申请退款(可完整预览的文档不适用该条件!)。
- 3、如文档侵犯您的权益,请联系客服反馈,我们会尽快为您处理(人工客服工作时间:9:00-18:30)。
如何避免车削时已加工表面的刀花
作者:王粟
来源:《中国教育技术装备》2015年第12期
摘要在车削加工实训教学过程中,大多数初学者车削出的表面存在明显的刀花,难以加工出光洁的表面,加工表面质量很难提高。
研究刀花产生的原因,寻找避免刀花的方法和措施,旨在帮助初学者培养学习兴趣,提高车削加工质量和实践学习效率。
关键词刀花;车削;实训教学
中图分类号:G642.44 文献标识码:B
文章编号:1671-489X(2015)12-0191-02
在车削实训场地,大多数初学者由于对金属的切削原理的认知不足,对刀具的几何角度概念模糊,实际切削时切出的表面刀花明显,加工不出较光洁的表面,加工表面质量不合格,实践学习效率低,达不到预期的训练目标。
以下就如何避免车削加工表面的刀花,提高车削加工表面质量进行论述,旨在培养初学者的学习兴趣和提高初学者的实践学习效率,确保车削加工实训教学活动有效开展。
1 什么是车削刀花
车削刀花是车削后的加工表面上余留的加工痕迹组成的宏观形貌。
车削刀花可分为正常车削刀花和非正常车削刀花。
正常车削刀花指受刀具形状和车削工艺参数的限制,已加工表面的残余切削层金属形成的刀花。
可见,正常车削刀花来自车削原理。
非正常车削刀花指刀具几何形状不合理、刀装或工件安装不正确、车削工艺参数选择不当造成的车刀急速磨损、车削工艺系统振动或车床运动部件损耗,导致加工表面余留的加工痕迹形成的表面外观形貌。
车削刀花影响车削加工精度和工件表面光洁度,是车削生产中的一个大问题[2]。
表1为车削刀花可视特征与表面粗糙度的对应情况。
正常的车削刀花属车削原理性刀花,在实际加工中不可避免;非正常的车削刀花可通过正确地刃磨车刀、合理地选择车削工艺参数、正确地安装车刀和工件、及时地维护维修车床设备等措施来回避。
2 初学者车削时产生刀花的常见原因
刀具几何角度选择不当
1)副偏角用于避免副切削刃与已加工表面摩擦,影响已加工表面粗糙度[2]。
若副偏角过大或未刃磨修平刃,外圆车削时不可避免地产生已加工表面残余面积高度,形成正常的车削刀
花;当刃磨的修平刃太长,切削时修平刃与工件摩擦引起挤压刀痕和刻划刀痕形成刀花。
副偏角取值为5°~15°,在刃磨修平刃时,修平刃口长度应略大于车削进给量,注意保持修平刃口的锋利,应以较小的倒棱保正正刀具具有较长的寿命。
车削时忌横向进刀,防止修平刃快速磨损或崩刃。
一般情况下,刃磨修平刃和副偏角以工艺系统不发生振动为准。
图1所示为外圆车刀修平刃俯视图,图中偏角为45°的刃部起半精车时主要除料作用,22°的刃部起精车除料作用,0°的刃部起精细车的光整作用。
在实践中,大多采用圆弧过渡曲线型修平刃,在精车时,初学者可刃磨R圆弧车刀光整加工表面。
2)金属切削刀具前角影响切削变形和切屑与前刀面的摩擦及刀具强度,后角用于减少主后刀面与工件的摩擦[2]。
刃磨车刀时,前角与后角过大,刃口过于锋利,车削时刀具急速磨损,车削力增大,磨损的刀刃会在加工表面上留下熨压刀痕和工艺系统振痕,严重时会出现较深的啃纹。
熨压刀痕和工艺系统振痕较浅,轻微时操作者肉眼难于觉察,可视为正常刀花;车削啃纹较深较宽,属非正常刀花,产生时车削噪音较大,操作者应终止切削加工。
表2为硬质合金刀具前角参考。
3)当背吃刀量和进给量一定时,改变主偏角可以使切屑变薄或变厚,影响散热情况和切削削力的变化[2]。
主偏角过小,外圆车削时参与切削的刃口长,切削力较大,当刀具或工件的刚性不足时,容易引发工艺系统振动,导致已加工表面表面上出现工艺系统振痕,若刀具或工件的刚性严重不足时,会出现较窄的啃纹。
车削工艺参数选择不正确
1)背吃刀量选择不当容易形成刀花。
当背吃刀量太小时,车刀在加工面上留下刻划和熨压的刀痕;当背吃刀量太大时,切削力较大,刀具或工件的刚性不足,容易引发工艺系统振动,导致已加工表面出现工艺系统振痕;若刀具或工件的刚性严重不足时,会出现啃纹,严重的会导致扎刀或崩刃现象。
2)进给量选择不当容易形成刀花。
当进给量小于修平刃长度时,可以回避正常切削刀花,但车削进给量太小,主切刃难于切入工件,刃口与工件加工面挤压和刻划,刃口容易磨损,切削将难于进行,已加工表面将留下轻微的熨压刀痕和刻划刀痕。
3)切削速度选择不当容易形成刀花。
如果切削速度选择在容易形成积屑瘤的速度区间内,切削时形成的积屑瘤将改变车刀的几何角度,一方面刻划刀痕会加深,另一方面残留在加工表面的部分积屑瘤将影响表面光洁度。
车刀与工件安装不正确
1)在安装刀具时,刀杆伸出太长,车刀刚性不足,切削时容易出现工艺系统振痕;车刀装偏,增大了副偏角,已加工表面残余面积高度增大,使刀花明显。
2)工件装夹时伸出太长,工件难于找正,车削时刀具容易磨损,加工表面上容易形成明显的工艺系统振纹、刻划刀痕和慰压刀痕。
3)操作时小溜板伸出太长,刀架刚度下降,车削时容易产生振动,加工表面容易形成工艺振痕。
车床的维护维修不及时就机床本身而言,传动系统零件的制造精度、各部件配合间隙和机床各部运转的平稳性等,对工件表面都会产生不同的刀痕[3],形成刀花。
3 避免车削加工表面刀花的措施
1)认真练习刀具刃磨,掌握刀具刃磨技巧,培养刀具刃磨技能。
在刃磨训练时应注重记忆刀具几何角度的定义,注意练习修平刃、正倒棱、负倒棱和圆倒棱的刃磨方法,在实践中深刻体会刀具几何角度的作用。
2)加强对切削三要素的理论学习,做到在实际操作中灵活选择切削速度、进给量与背吃刀量。
3)在实操练习时注意耳听与眼观,当切削区域出现异常的噪音和刀杆振动时,应停止车削,及时检查和修磨刀具刃口,及时调整切削工艺参数。
4)加强对工艺系统刚度的认识,在实际操作时应考虑刀具的刚度、工件的刚度,认真维护保养和使用机床,严格回避因工艺系统刚度不足造成的刀花。
总之,形成车削刀花的原因复杂,初学者应以如何回避车削刀花为学习切入点,深入学习金属切削原理,在实际操作训练中不断探究提高车削表面质量的方法和措施,加强质量意识的培养,提高实践学习的效率。
参考文献
[1]陈理敖.关于车削刀花问题的产生及其排除方法[J].机床,1988(12).
[2]王平,叶晓苇.车削工艺技术[M].沈阳:辽宁科学技术出版社,2009.
[3]张春年.车削刀花的产生及其排除方法[J].机床,
1991(8).。