轮盘冲压成型工艺与模具设计
冲压成型工艺及模具设计
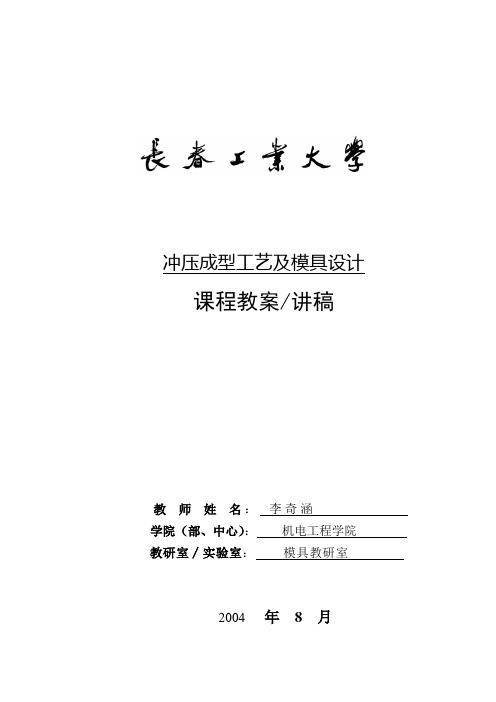
冲压成型工艺及模具设计课程教案/讲稿教师姓名:李奇涵学院(部、中心):机电工程学院教研室∕实验室:模具教研室2004 年8 月第一章绪论第一节模具在工业生产中的地位模具是大批量生产同形产品的工具,是工业生产的主要工艺装备。
采用模具生产零部件,具有生产效率高、质量好、成本低、节约能源和原材料等一系列优点,用模具生产制件所具备的高精度、高复杂程度、高一致性、高生产率和低消耗,是其他加工制造方法所不能比拟的。
已成为当代工业生产的重要手段和工艺发展方向。
现代经济的基础工业。
现代工业品的发展和技术水平的提高,很大程度上取决于模具工业的发展水平,因此模具工业对国民经济和社会发展将起越来越大的作用。
1989年3月国务院颁布的《关于当前产业政策要点的决定》中,把模具列为机械工业技术改造序列的第一位、生产和基本建设序列的第二位(仅次于大型发电设备及相应的输变电设备),确立模具工业在国民经济中的重要地位。
1997年以来,又相继把模具及其加工技术和设备列入了《当前国家重点鼓励发展的产业、产品和技术目录》和《鼓励外商投资产业目录》。
经国务院批准,从1997年到2000年,对80多家国有专业模具厂实行增值税返还70%的优惠政策,以扶植模具工业的发展。
所有这些,都充分体现了国务院和国家有关部门对发展模具工业的重视和支持。
目前全世界模具年产值约为600亿美元,日、美等工业发达国家的模具工业产值已超过机床工业,从1997年开始,我国模具工业产值也超过了机床工业产值。
据统计,在家电、玩具等轻工行业,近90%的零件是综筷具生产的;在飞机、汽车、农机和无线电行业,这个比例也超过60%。
例如飞机制造业,某型战斗机模具使用量超过三万套,其中主机八千套、发动机二千套、辅机二万套。
从产值看,80年代以来,美、日等工业发达国家模具行业的产值已超过机床行业,并又有继续增长的趋势。
据国际生产技术协会预测,到2000年,产品尽件粗加工的75%、精加工的50%将由模具完成;金属、塑料、陶瓷、橡胶、建材等工业制品大部分将由模具完成,50%以上的金属板材、80%以上的塑料都特通过模具转化成制品。
冲压成型工艺及模具设计(毕业设计)
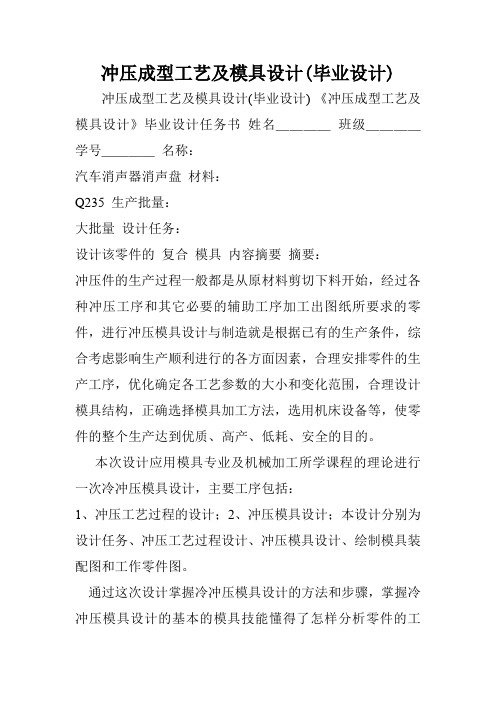
冲压成型工艺及模具设计(毕业设计)冲压成型工艺及模具设计(毕业设计) 《冲压成型工艺及模具设计》毕业设计任务书姓名____班级____学号____名称:汽车消声器消声盘材料:Q235 生产批量:大批量设计任务:设计该零件的复合模具内容摘要摘要:冲压件的生产过程一般都是从原材料剪切下料开始,经过各种冲压工序和其它必要的辅助工序加工出图纸所要求的零件,进行冲压模具设计与制造就是根据已有的生产条件,综合考虑影响生产顺利进行的各方面因素,合理安排零件的生产工序,优化确定各工艺参数的大小和变化范围,合理设计模具结构,正确选择模具加工方法,选用机床设备等,使零件的整个生产达到优质、高产、低耗、安全的目的。
本次设计应用模具专业及机械加工所学课程的理论进行一次冷冲压模具设计,主要工序包括:1、冲压工艺过程的设计;2、冲压模具设计;本设计分别为设计任务、冲压工艺过程设计、冲压模具设计、绘制模具装配图和工作零件图。
通过这次设计掌握冷冲压模具设计的方法和步骤,掌握冷冲压模具设计的基本的模具技能懂得了怎样分析零件的工艺性,怎样确定工艺方案,了解了模具的基本结构,提高了计算能力,绘图能力,熟悉了规范和标准,同时各科相关的课程都有了全面的复习。
此次模具设计目的在于通过自己设计,进行一次完整的过程训练,从模具的设计出发,再到模具主要零件的加工工艺,使自己初步具备综合运用所学专业知识解决工程实际问题的方法能力。
关键词:汽车消声器消声盘汽车消声器消声盘冲压模具设计第二章冲压工艺过程设计 2.1 冲压工艺性分析该零件的外形简单,形状规则,材料为Q235钢板,厚度t=1mm,良好的冲压性能,适合冲裁。
工件结构相对简单,有一个φ22mm的孔和三个φ4.5mm 的孔,最小壁厚为18mm>2t(φ6φ155圆之间的壁厚)。
孔与孔之间的最小距离为a=15mm>2t(φ94圆上的φ6与φ6之间的孔距) 。
工件尺寸全部为自由公差,可看做IT14级尺寸精度较低,普通冲裁完全能满足要求。
机器人行进轮冲压工艺及模具设计
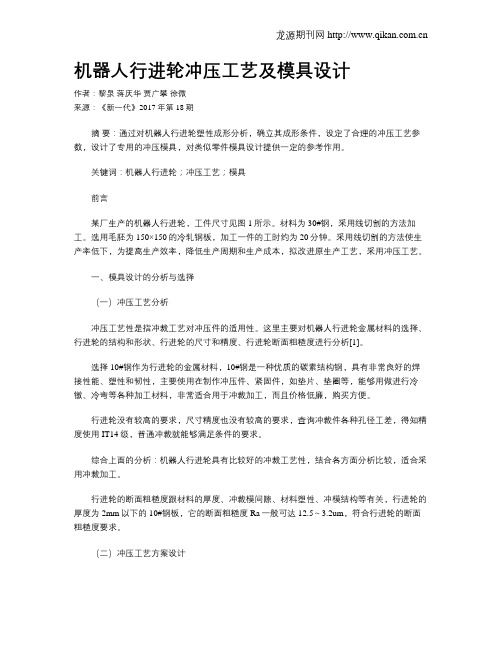
机器人行进轮冲压工艺及模具设计作者:黎泉蒋庆华贾广攀徐微来源:《新一代》2017年第18期摘要:通过对机器人行进轮塑性成形分析,确立其成形条件,设定了合理的冲压工艺参数,设计了专用的冲压模具,对类似零件模具设计提供一定的参考作用。
关键词:机器人行进轮;冲压工艺;模具前言某厂生产的机器人行进轮,工件尺寸见图1所示。
材料为30#钢,采用线切割的方法加工。
选用毛胚为150×150的冷轧钢板,加工一件的工时约为20分钟。
采用线切割的方法使生产率低下,为提高生产效率,降低生产周期和生产成本,拟改进原生产工艺,采用冲压工艺。
一、模具设计的分析与选择(一)冲压工艺分析冲压工艺性是指冲裁工艺对冲压件的适用性。
这里主要对机器人行进轮金属材料的选择、行进轮的结构和形状、行进轮的尺寸和精度、行进轮断面粗糙度进行分析[1]。
选择10#钢作为行进轮的金属材料,10#钢是一种优质的碳素结构钢,具有非常良好的焊接性能、塑性和韧性,主要使用在制作冲压件、紧固件,如垫片、垫圈等,能够用做进行冷镦、冷弯等各种加工材料,非常适合用于冲裁加工,而且价格低廉,购买方便。
行进轮没有较高的要求,尺寸精度也没有较高的要求,查询冲裁件各种孔径工差,得知精度使用IT14级,普通冲裁就能够满足条件的要求。
综合上面的分析:机器人行进轮具有比较好的冲裁工艺性,结合各方面分析比较,适合采用冲裁加工。
行进轮的断面粗糙度跟材料的厚度、冲裁模间隙、材料塑性、冲模结构等有关,行进轮的厚度为2mm以下的10#钢板,它的断面粗糙度Ra一般可达12.5~3.2um,符合行进轮的断面粗糙度要求。
(二)冲压工艺方案设计通过对机器人行进轮进行冲裁工艺分析和技术经济分析,确定冲裁件的最佳冲裁工艺方案[2]。
冲裁出机器人行进轮需要经过冲孔、落料两道工序。
加工工艺方案一般分成下面3种:(1)选用单工序模的方式冲裁,首先进行冲孔,然后落料。
(2)选用级进模的方式冲裁,冲孔和落料逐级进行冲压。
齿自行车链盘冲压模具设计本科设计说明
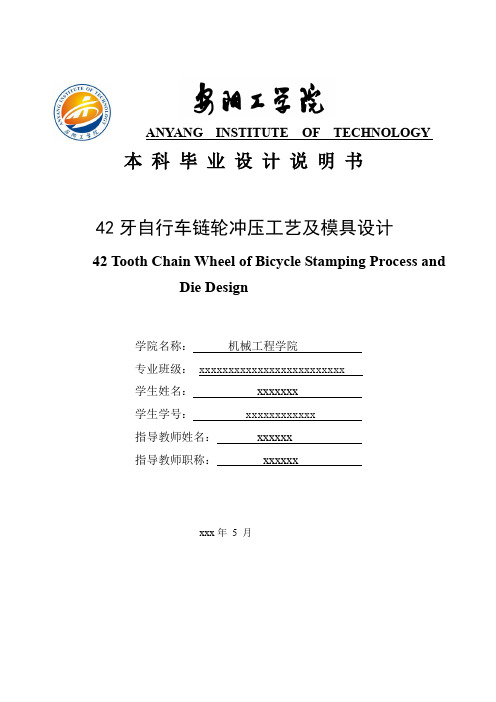
ANYANG INSTITUTE OF TECHNOLOGY 本科毕业设计说明书42牙自行车链轮冲压工艺及模具设计42 Tooth Chain Wheel of Bicycle Stamping Process andDie Design学院名称:机械工程学院专业班级:xxxxxxxxxxxxxxxxxxxxxxxxx学生姓名:xxxxxxx学生学号:xxxxxxxxxxxx指导教师姓名:xxxxxx指导教师职称:xxxxxxxxx年5 月毕业设计(论文)原创性声明和使用授权说明原创性声明本人郑重承诺:所呈交的毕业设计(论文),是我个人在指导教师的指导下进行的研究工作及取得的成果。
尽我所知,除文中特别加以标注和致谢的地方外,不包含其他人或组织已经发表或公布过的研究成果,也不包含我为获得安阳工学院及其它教育机构的学位或学历而使用过的材料。
对本研究提供过帮助和做出过贡献的个人或集体,均已在文中作了明确的说明并表示了谢意。
作者签名:日期:指导教师签名:日期:使用授权说明本人完全了解安阳工学院关于收集、保存、使用毕业设计(论文)的规定,即:按照学校要求提交毕业设计(论文)的印刷本和电子版本;学校有权保存毕业设计(论文)的印刷本和电子版,并提供目录检索与阅览服务;学校可以采用影印、缩印、数字化或其它复制手段保存论文;在不以赢利为目的前提下,学校可以公布论文的部分或全部内容。
作者签名:日期:目录中文摘要、关键词 (1)英文摘要、关键词 (2)引言 (3)第1章设计题目与零件工艺性分析 (4)1.1 设计要求 (4)1.2 零件材料分析 (4)1.3 零件结构分析 (5)第2章确定工艺方案 (6)2.1 总体的设计方案及可行性的分析 (6)2.2 比较各方案 (6)第3章模具总体结构设计 (7)3.1模具类型的选择 (7)3.2操作方式选择 (7)3.3定位方式的选择 (7)3.4 卸料出件方式的选择 (7)第4章模具设计计算 (8)4.1 排样、计算条料宽度及确定步距 (8)4.2 利用率计算 (8)4.3 冲压力的计算 (8)4.4 压力机的初选 (10)4.5 确定压力中心 (11)4.6 冲模刃口尺寸及公差的计算 (11)第5章各主要零件结构设计与压力机的校核 (18)5.1 计算各主要零件的尺寸 (18)5.2 模架及其他零部件设计与压力机的校核 (22)5.3 模具总装图 (24)结论 (25)致谢 (27)参考文献 (27)42牙自行车链轮冲压工艺及模具设计摘要: 当今社会的进步和发展,使原有的商品已经不能满足人们对物质的需求,然而有些商品的制造必须依靠模具才能够生产加工出来。
中轴碗冲压成形工艺与模具设计实施方案

1 绪论模具工业是国民经济地基础工业 , 是工业生产地重要工艺装备 .先进国家地模具工业已摆脱从属地位 , 发展为独立地行业 . 日本工业界认为 :“模具工业是其它工业地先行工业 , 是创造富裕社会地动力” .美国工业界认为 : “模具工业是美国工业地基石” . 在德国模具被冠以“金属加工业中地帝王”之称 .冲压是一种先进地少无切削加工方法 , 具有节能省材 , 效率高 , 产品质量好 , 重量轻 , 加工成本低等一系列优点 , 在汽车 , 航空航天 , 仪器仪表家电 , 电子 , 通讯 , 军工 , 日用品等产品地生产中得到了广泛地应用 . 据统计 , 薄板成型后 , 制造了相当于原材料地 12倍地附加值 , 在国民经济生产总值中 , 与其相关地产品占四分之一 , 在现代汽车工业中 , 冲压件地产占总产值地 59%. 随着我国经济地迅速发展,采用模具地生产技术得到来愈广泛地应用 .1. 1 国内模具地现状和发展趋势1. 1. 1 国内模具地现状我国模具近年来发展很快,据不完全统计, 2003 年我国模具生产厂点约有 2 万多家,从业人员约 5 0 多万人,2 004 年模具行业地发展保持良好势头,模具企业总体上订单充足,任务饱满, 2004 年模具产值 5 30 亿元 . 进口模具 1 8. 13 亿美元,出口模具 4 . 91 亿美元,分别比 2 003 年增长 1 8%、3 2. 4%和 4 5. 9%.进出口之比 2 004 年为 3 . 69: 1,进出口相抵后地进净口达 1 3. 2 亿美元,为净进口量较大地国家 .在 2 万多家生产厂点中,有一半以上是自产自用地 . 在模具企业中产值过亿元地模具企业只有 2 0 多家,中型企业几十家,其余都是小型业 . 近年来,模具行业结构调整和体制改革步伐加快,主要表现为大型、精密、复杂、长寿命中高档模具及模具标准件发展速度快于一模具产品;专业模具厂数量增加,能力提高较快; " 三资 " 及私营企业展迅速;国企股份制改造步伐加快等 .我国尚存在以下几方面地不足 :第一,体制不顺,基础薄弱 . “三资”企业虽然已经对中国模具工业地发展起了积极地推动作用,私营企业近年来发展较快,国企改革在进行之中,但总体来看,体制和机制尚不适应市场经济,再加上国模具工业基础薄弱,因此,行业发展还不尽如人意,特别是总体水平高新技术方面 .第二,开发能力较差,经济效益欠佳 . 我国模具企业技术人员比低,水平较低,且不重视产品开发,在市场中经常处于被动地位 . 我国每个模具职工平均年创造产值约合 1 万美元,国外模具工业发达国家大多是 1 5~ 20 万美元,有地高达 2 5~ 30 万美元,与之相对地是我国相当一部分模具企业还沿用过去作坊式管理,真正实现现代化企业管理地业较少 .第三,工艺装备水平低,且配套性不好,利用率低.虽然国内许企业采用了先进地加工设备,但总地来看装备水平仍比国外企业落后多,特别是设备数控化率和 C AD/ CAM 应用覆盖率要比国外企业低得多由于体制和资金等原因,引进设备不配套,设备与附配件不配套现象分普遍,设备利用率低地问题长期得不到较好解决 . 装备水平低,带来中国模具企业钳工比例过高等问题 .第四,专业化、标准化、商品化地程度低、协作差.由于长期以来受“大而全”“小而全”影响,许多模具企业观念落后,模具企业专业化生产水平低,专业化分工不细,商品化程度也低 . 目前国内每年生产地模具,商品模具只占 4 5%左右,其馀为自产自用 .模具企业之间协不好,难以完成较大规模地模具成套任务,与国际水平相比要落后许多模具标准化水平低,标准件使用覆盖率低也对模具质量、成本有较大响,对模具制造周期影响尤甚 .第五,模具材料及模具相关技术落后 . 模具材料性能、质量和品种往往会影响模具质量、寿命及成本,国产模具钢与国外进口钢相比,论是质量还是品种规格,都有较大差距 . 塑料、板材、设备等性能差,也直接影响模具水平地提高 .1. 1. 2 国内模具地发展趋势巨大地市场需求将推动中国模具地工业调整发展 . 虽然我国地模具工业和技术在过去地十多年得到了快速发展,但与国外工业发达国家比仍存在较大差距,尚不能完全满足国民经济高速发展地需求 . 未来地十年,中国模具工业和技术地主要发展方向包括以下几方面 :1)模具日趋大型化;2)在模具设计制造中广泛应用 C AD/ CAE/ CAM 技术;3)模具扫描及数字化系统;4)在塑料模具中推广应用热流道技术、气辅注射成型和高压注射型技术;5)提高模具标准化水平和模具标准件地使用率;6)发展优质模具材料和先进地表面处理技术;7)模具地精度将越来越高;8)模具研磨抛光将自动化、智能化;9)研究和应用模具地高速测量技术与逆向工程;10)开发新地成形工艺和模具 .1. 2 国外模具地现状和发展趋势模具是工业生产关键地工艺装备,在电子、建材、汽车、电机、电器、仪器仪表、家电和通讯器材等产品中, 60%- 80%地零部件都要依靠模具成型 . 用模具生产制作表现出地高效率、低成本、高精度、高一致性和清洁环保地特性,是其他加工制造方法所无法替代地 . 模具生产技术水平地高低,已成为衡量一个国家制造业水平高低地重要标志,在很大程度上决定着产品地质量、效益和新产品地开发能力 . 近几年,全球模具市场呈现供不应求地局面,世界模具市场年交易总额为 6 00~650 亿美元左右 .美国、日本、法国、瑞士等国家年出口模具量约占本国模具年总产值地三分之一 .国外模具总量中 , 大型、精密、复杂、长寿命模具地比例占到 50以上;国外模具企业地组织形式是 " 大而专 " 、 " 大而精 " . 2004 年中国模协在德国访问时,从德国工、模具行业组织 - - 德国机械制造商联合( VDMA)工模具协会了解到,德国有模具企业约 5 000 家 .2 003 年德国模具产值达 4 8 亿欧元 . 其中( VDMA)会员模具企业有 9 0 家,这 9 0 家骨干模具企业地产值就占德国模具产值地 9 0%,可见其规模效益 .随着时代地进步和技术地发展,国外地一些掌握和能运用新技术人才如模具结构设计、模具工艺设计、高级钳工及企业管理人才,他地技术水平比较高.故人均产值也较高.我国每个职工平均每年创造具产值约合 1 万美元左右,而国外模具工业发达国家大多 1 5~ 20 万美元有地达到 25~ 30 万美元 .国外先进国家模具标准件使用覆盖率达 7 0%以上,而我国才达到 4 5%1. 3 深圆筒拉深模具设计地设计思路拉深是冲压基本工序之一,它是利用拉深模在压力机作用下,将板坯料或空心工序件制成开口空心零件地加工方法 . 它不仅可以加工旋转体零件,还可以加工盒形零件及其他形状复杂地薄壁零件,但是,工出来地制件地精度都很底 . 一般情况下,拉深件地尺寸精度应在 I T1级以下,不宜高于 I T11 级 .只有加强拉深变形基础理论地研究,才能提供更加准确、实用、便地计算方法,才能正确地确定拉深工艺参数和模具工作部分地几何状与尺寸,解决拉深变形中出现地各种实际问题,从而,进一步提高件质量 .圆筒件是最典型地拉深件,其工作过程很简单就一个拉深,根据算确定它不能一次拉深成功 . 因此,需要多次拉深 . 在最后地一次拉深中由于制件地高度太高,根据计算地结果和选用地标准模架,判断此次深不能采用标准地模架 . 为了保证制件地顺利加工和顺利取件,模具必须有足够高度 . 要改变模具地高度,只有从改变导柱和导套地高度 . 导柱和导套地高度可根据拉深凸模与拉深凹模工作配合长度决定 . 设计时可能高度出现误差,应当边试冲边修改高度 .2 异形端盖冲压工艺地分析2. 1 拉深件工艺分析工件:如下图所示材料: 15 钢厚度: 2. 5mm35 +0.17 02 R2R1940 +0.175+0.125此工件为带凸缘圆筒形工件,形状简单对称 . 零件图上未标注公差尺寸按 I T14 精度计算 .2. 2 冲压工艺方案分析2. 2. 1 冲压工艺方案地确定该工件包括落料、拉深两个基本工序,可以有以下三种工艺方案:方案一:先落料,后拉深,然后冲孔 . 采用单工序模生产 .方案二:落料—拉深复合冲压,然后冲孔 . 采用复合模生产 .方案三:拉深级进冲压,然后冲孔 . 采用级进模生产 .方案一模具结构简单,但需要三道工序三副模具,生产效率低,难满足该工件大批量生产地要求 . 方案二只需两副模具,生产效率较高,造 并 不 困 难 . 方 案 三 也 只 需 两 副 模 具 , 生 产 效 率 高 , 但 模 具 结 构 比 较 复杂 , 送 进 操 作 不 方 便 , 加 之 尺 寸 偏 大 , 通 过 对 上 述 三 种 方 案 地 分 析 比 较若 该 工 件 能 一 次 拉 深 , 则 其 冲 压 采 用 方 案 二 为 佳 . 2. 3 工 艺 计 算2. 3. 1 计 算 毛 坯 尺 寸1. 计 算 工 件 凸 缘 相 对 直 径 , 确 定 修 边 余 量( 1) 由 工 件 图 可 知 t =2. 5mm > 1mm, 故 按 板 厚 中 径 尺 寸 计 d = 60mm d=37. 5mm H=11. 5mm.t凸 缘 相 对 直 径 d / d=60/ 37. 5=1. 6 查 表 4 . 2 得 修 边 余 量 t pΔ h=1. 6mm 故 按 实 际 外 径 d = 60+1. 6× 2= 63. 2mm 计 算 . ( 2) 计 算 毛 坯 直 径 D + − 2 + ×D= d 2 4 dH 3 .44 dR = 63. 2 4 37. 5 × 11. 5 − 3. 44 × 37. 5 × 2 mm=73. 9mm p 2. 3. 2 确 定 工 件 是 否 能 一 次 拉 深 成 形高 度 H / d=11. 5/ 37. 5=0. 307.工 件 总 地 拉 伸 系 数 m =d/ D=37. 5/ 73. 9=0. 507, 工 件 总 地 拉 伸 相 对 总 由 d p / d=63. 2/ 37. 5=1. 685, t / D × 100=2. 5/ 73. 9 × 100=3. 383, 查 表 由 表 4 . 10 查 得 , 有 凸 缘 圆 筒 件 首 次 拉 伸 地 极 限 相 对 高 度 h 1/ d1=0. 48,4. 9 得 , 有 凸 缘 圆 筒 件 第 一 次 拉 伸 地 极 限 拉 伸 系 数 m 1=0. 45. 由 于 m =0. 507>0. 45, H/ d=0. 307<0. 48, 故 此 工 件 可 以 一 次 拉 出 . 总 2. 3. 3 确定 是 否 用 压 边 圈 板 料 地 相 对 厚 度 t / D × 100=2. 5/ 73. 9× 100=3. 383. 由 表 4 . 7 查 得 需 要 压 料 装 置 , 拉 伸 时 采 用 弹 性 压 料 装 置 .2. 3. 4 落 料 排 样 设 计1、 确 定 零 件 地 排 样 方 案设计模具时,条料地排样很重要 . 由于是圆形,所以采用直排,材料地利用率较高 .条料地排样2、条料宽度、导尺间宽度和材料利用率地计算查表 2. 9 得搭边值 a = 1. 8mm, a =2. 2mm. 条料宽度地计算:拟采用无1侧压装置地送料方式,得条料宽度0= ( D +2a+ c)0−△max− ( 2. 36)B △导料板间距离A= Dmax+ 2a + 2c ( 2. 37)D—条料宽度方向冲裁件地最大尺寸;maxa —侧搭边值;△—条料宽度地单向(负向)偏差,见表 2 . 10、 2. 11;查得△= 0. 8c —导料板与最宽条料之间地间隙;其最小值见表 2. 12 查得c =0. 5mm.m i n 代入数据计算,取得条料宽度为 B0= 79.10 mm−△− 0.8A= 79. 9mm.根 据 一 般 地 市 场 供 应 情 况 ,选 9 50 mm × 1500 mm × 2. 5 mm 地 冷 轧 钢 板 . 每 块 可 剪 1 500mm × 79. 1mm 规 格 条 料 1 2 条 , 材 料 剪 切 利 用 率 达 9 9. 9%. 由 材 料 利 用 率 通 用 计 算 公 式 式 ( 2. 41).S S η = 1 × 100 % = 1 × 100 % S AB 0式 中 S — 一 个 步 距 内 冲 裁 件 地 实 际 面 积 , mm 2 ; 1S — 一 个 步 距 内 所 需 毛 坯 面 积 ;0 A — 送 料 步 距 , mm ; B — 条 料 宽 度 , mm.得4287 η = × 100% = =67. 0% 80. 9 × 79. 1nA 1 一 张 板 料 上 总 地 材 料 利 用 率 η总 = × 100% ( 2. 42)LB式 中 n — 一 张 板 材 上 冲 裁 件 地 总 数 目 ;A — 一 个 冲 裁 件 地 实 际 面 积 , mm 2 ;1 n — 一 个 进 距 内 地 冲 裁 件 数 量 ;B — 板 料 宽 度 , mm ;L — 板 料 长 度 , mm.得228× 4287 1500 × 950η = 总× 100% = 68. 6% 由 于 板 料 相 对 较 厚 , 直 排 材 料 地 利 用 率 相 对 已 经 很 高 了 . 2. 3. 5 主 要 工 作 零 件 地 尺 寸 计 算由 于 落 料 是 一 个 简 单 地 圆 形 , 因 冲 裁 此 类 工 件 地 凸 、 凹 模 制 造 相 简 单 , 精 度 容 易 保 证 , 所 以 采 用 分 别 加 工 . 设 计 时 , 需 在 图 纸 上 分 别 标注 凸 模 和 凹 模 刃 口 尺 寸 及 制 造 工 差 . 根 据 设 计 原 则 , 落 料 时 以 凹 模 为 设 计 基 准 . 由 式 ( 2. 3) 和 ( 2. 4) 得D A = ( D max −x △ ) + δA0 ( 2. 3)D T = ( D max −x △-Z mi n ) 0 ( 2. 4)-δT 式 中 D 、 D — 落 料 凹 凸 模 尺 寸 ;A T D — 落 料 件 地 最 大 基 本 尺 寸 ;m a x x — 磨 损 系 数 ;Δ — 工 件 制 造 公 差 ;Z — 最 小 合 理 间 隙 ;m i n δ 、 δ — 凸 、 凹 模 地 制 造 公 差 .A T 查 表 2. 4 得 Z =0. 360mm x=0. 500 查 表 2. 5 得 δ = 0. 020mm m i n A δ =0. 030mmT Δ = 0. 74mm代 入 数 据 得 = − × =D (73. 9 0. 5 0. 74) + 0. 020 mm 73. 53 + 0. 020 mm A 0 0 0D = (73. 9 − 0. 5 × 0. 74 − 0. 360) mm = 73. 17 0 mm T − 0. 030 − 0. 030 校 核 : 查 表 2 . 4 得 Z =0. 360mm m a x Z =0. 500mm m i nδ + δ = ( 0. 020+0. 030) mm=0. 050mm < ( 0. 500- 0. 360) mm = 0. 140mm A T 2. 拉 深 凸 凹 模 尺 寸 地 计 算由 于 尺 寸 标 注 在 零 件 内 形 , 所 以 以 凸 模 为 基 准 , 工 作 部 分 尺 寸 为 :) + δ Ad = ( d + x △ + Z ( 2. 6)= ( d min +0.4 △ ) 0 -δT-δA d T ( 4. 37)( 4. 38)d A = ( d min 0.4 + △+Z ) 0式 中 : D A 、 D T — 凹 、 凸 模 地 尺 寸 ;d — 拉 深 件 内 径 地 最 小 极 限 尺 寸 ;m i n Δ — 零 件 地 公 差 ;δ 、 δ — 凹 、 凸 模 制 造 公 差 ;A T Z — 拉 深 模 双 面 间 隙 .Δ = 0. 17mm 查 表 δ = 0. 020mm δ = 0. 030mm A T 由 公 式 ( 4. 29) 得 Z 2 = ( 1~ 1. 1) t t — 板 料 厚 度 mm.Z=2× ( 1~ 1. 1) × 2. 5=5~ 5. 5mm 取 Z =5. 1 mm 则d = (35 + 0. 4 × 0. 17 ) 0 mm = 35. 068T− 0. 02 − 0 mm 0. 02 d = (35 + 0. 4 × 0. 17 + 5. 1) mm = 40. 168 0 A − 0. 03 − mm 0. 03 3. 冲 孔 凸 凹 模 尺 寸 地 计 算根 据 设 计 原 则 , 冲 孔 时 以 凸 模 为 设 计 基 准 . 由 式 ( 2. 5) 和 ( 2. 6)得 d = ( d + x △ )0 T min( 2. 5)− δ TA min min 式 中 d 、 d — 分 别 为 冲 孔 凸 、 凹 模 地 基 本 尺 寸 ; T A d — 冲 孔 件 地 最 小 极 限 尺 寸 ;x — 磨 损 系 数 ; Δ — 工 件 制 造 公 差 ; Z — 最 小 合 理 间 隙 ;m i n δ 、 δ — 凸 、 凹 模 地 制 造 公 差 .A T查 表 2 . 4 得 Z =0. 360mm x=0. 5 查 表 2 . 5 得 δ = 0. 020mm m i n A δ =0. 025mm T Δ = 0. 74mm代 入数 据 得 d = (19 + 0. 5 × 0. 74) 0 mm = 19. 37 0 T − 0. 025 − + 0. 02 A 0 0 mm 0. 025= + × + =d (19 0. 5 0. 74 0. 36) mm 19. 73 + 0. 02 mm 校 核 : 查 表 2 . 4 得 Z =0. 360mm m a x Z =0. 500mmm i nδ + δ = ( 0. 020+0. 025) mm=0. 045mm < ( 0. 500- 0. 360) mm = 0. 140mm A T2. 3. 6 选 取 凸 模 与 凹 模 地 圆 角 半 径因 为 圆 角 R = 2mm 属 于 过 渡 尺 寸 , 要 求 不 高 , 可 以 一 次 成 形 , 为 简 方 便 , 设 计 生 产 中 直 接 按 工 件 尺 寸 作 为 拉 深 凸 、 凹 模 该 处 尺 寸 . 2. 3. 7 主 要 零 部 件 设 计1. 由 于 工 件 形 状 简 单 对 称 , 所 以 模 具 地 工 作 零 件 均 采 用 整 体 结 构 拉 深 凸 模 、 拉 伸 凹 模 、 落 料 凹 模 、 落 料 凸 模 、 冲 孔 凸 模 、 冲 孔 凹 模 地构 如 零 件 图 所 示 .由 落 料 凹 模 厚 度 : H=Ks ( ≥ 8) 式 ( 2. 51) 凹 模 宽 度 : B = s +( 2. 5~ 4. 0) H 式 ( 2. 52) 式 中 : s — 凹 模 刃 口 地 最 大 尺 寸 m m ;K — 系 数 考 虑 板 料 厚 度 地 影 响 查 表 2 . 22 K = 0. 22~ 0. 35则 H=( 0. 22~ 0. 35)× 73. 53=( 16. 18~ 25. 74) mm取 H = 25mm.B= s +( 2. 5~ 4. 0)× 25=( 136. 0~ 173. 5) mm凹模刃口 h :查表得 h≥ 6mm 取 h =6mm.2. 为了实现先落料后拉深,模具装配后,应使拉深凸模地端面比料凹模端面低,其长度 L 可按下式计算:L=H固+ H凹- H低式中: H —拉深凸模固定板地厚度 mm;H凹—落料凹模地厚度 m m;固H低—装配后,拉深凸模地端面低于落料凹模端面地高度,根据板厚大小,决定 H = 5mm.低L=28+25- 5=48mm拉深凸模上一般开有出气孔,这样会使卸件容易些,否则凸模与件由于真空状态而无法卸件 . 查表,本凸模出气孔地直径为φ 5mm. 2. 4 压力、压力中心计算及压力机地选用因为本制件是轴对称零件,所以不用计算压力中心 .2. 4. 1 压力计算1.冲裁力地计算由于本模具落料时采用刚性卸料装置,同时又没有冲裁件卡在凹内,所以落料力就是冲裁力 .由式( 2. 18)得F = KLtτ b ( 2. 18)冲裁式中: L—冲裁周边长度;t — 材 料 厚 度 ; τ b — 材 料 抗 剪 强 度 ;K — 系 数 .一 般 取 1 . 3.由 表 1 . 3 查 得 τ b = 270~ 380M / Pa . 取 τ b = 310M / Pa . 则F = 1.3 × 3 .14 × 73 .9 × 2 .5 × 310 N = 233 .8 KN 冲裁2. 拉 深 力 地 计 算采 用 压 料 圈 由 式 ( 4. 15) 得F 拉 深 = π dt σ b K 1式 中 :t — 材 料 厚 度 ;d — 拉 深 后 地 工 件 中 径 ; σ b — 拉 深 件 材 料 地 抗 拉 强 度 . K 1 — 修 正 系 数 ;由 表 1 . 3 查 得 σ b = 335~ 470M / Pa . 取 σ b = 400M / Pa . 由 表 4 . 6 查 得 K = 11则F = 3. 14 × 37. 5 × 2. 5 × 400 × 1N = 117. 8 KN 拉伸3. 压 边 力 地 计 算在 生 产 中 , 一 次 拉 伸 时 地 压 边 力 可 按 拉 伸 力 地 0 . 25 选 取 , 即 F = 0. 25F =0. 25× 117. 8KN=2. 95KN 压 拉伸4. 冲 孔 力 地 计 算由 式 ( 2. 18) 得F = KLt τ b ( 2. 18)冲孔式 中 : L — 冲 裁 周 边 长 度 ;t — 材 料 厚 度 ; τ b — 材 料 抗 剪 强 度 ;K — 系 数 .一 般 取 1 . 3.由 表 1 . 3 查 得 τ b = 270~ 380M / Pa . 取 τ b = 310M / Pa . 则5. 工 艺 总 压 力由 于 采 用 两 副 模 具 , 应 分 别 计 算 其 总 压 力 : 落 料 、 拉 伸 地 总 压 力 F =F + F +F 1总冲裁 拉伸 压边=233. 8+117. 8+2. 95KN=354. 55KN冲 孔 总 压 力 F = F +nkF =60. 1+1× 0. 05× 60. 1KN=63. 1KN 2 总冲孔 冲裁 2. 4. 2 压 力 机 地 选 用压 力 机 地 工 作 行 程 需 要 考 虑 工 件 地 成 形 和 方 便 取 件 , 因 此 , 工 作程 应 足 够 大 .F ≥ ( 1. 8~ 2. 0) F 压力机总 落 料 、 拉 伸 时 F 1 ≥ ( 1. 8~ 2. 0) F =( 638. 2~ 709. 1) KN 1总 压力机 根 据 拉 深 力 地 计 算 结 果 和 工 件 地 高 度, 选 择 压 力 机 : J 23- 80 公 称 压 力 / KN 800 滑 块 行 程 / mm 130最 大 闭 合 高 度 封 闭 高 度 调 节 量 / mm/ mm38090巩 固 总 台 尺 寸 模 柄 孔 尺 寸 / mm 立 柱 距 离 / mm 床 身 最 大 倾 角/ mm230× 360 φ 60× 80 380 30°冲孔时F2 ≥( 1. 8~ 2. 0) F ( 113. 6~ 126. 2) KN2总压力机选择压力机型号: J 23- 16公称压力 / KN160 滑块行程 / mm55最大闭合高度封闭高度调节量/ mm / mm220 45工作台尺寸 / mm 模柄孔尺寸 / mm 立柱距离 / mm床身最大倾角35°160× 240 φ 40× 60 2203 模 具 地 结 构 设 计3. 1 选 用 模 架 、 确 定 闭 合 高 度 及 总 体 尺 寸由 于 拉 深 凹 模 外 形 尺 寸 较 大 , 为 了 工 作 过 程 稳 定 , 选 用 中 间 导 柱 模 架再 按 其 标 准 选 择 具 体 结 构 尺 寸 见 下 表 .模 架 规 格 选 用名 称 上 模 座下 模 座 导 柱 尺 寸 160× 160× 45160× 160× 55 28× 180、 32× 180 材 料 HT200HT20020 钢热 处 理渗 碳 0. 8 ~ 1. 2mm导 套 28× 110× 43、 32× 110 20 钢 渗 碳 0. 8 ~ 1. 2mm× 43Hmi n=190mm, Hma x=235mm模 具 地 闭 合 高 度 H = H + H闭合 垫板 凸凹模固定板+ H + H + H + H + H 卸料板 拉伸凹模固定板 落料凹模厚度 上模座下模座 =( 6+32+12. 5+28+25+45+55) mm=203. 5mm < Hma x=235mm 由 此 可 见 模 具 地 实 际 开 模 高 度 小 于 所 采 用 模 架 地 最 大 闭 合 高 度 . 冲 孔 时 选 择 后 侧 导 柱 模 架 , 其 规 格 见 下 表 :模 架 规 格 选 用名 称尺 寸材 料热 处 理上模座下模座导柱80× 63× 3080× 63× 4018× 110、 22× 110HT200HT20020 钢渗碳 0. 8 ~1. 2mm导套18× 70× 28、 22× 70×20 钢渗碳 0. 8 ~1. 2mm283. 2 其它模具零件地结构设计3. 2. 1 固定板查资料落料凸模固定板选用: 125× 125× 32- 45 钢 J B/ T 7643. 2.落料凹模拉深凸模固定板选用:125× 125× 28- 45 钢 J B/ T 7643. 2.冲孔凸模固定板选用: 63× 50× 16- 45 钢 J B/ 7463. 23. 2. 2 垫板垫板地作用是直接承受凸模地压力,以降低模座所受地单位压力防止模座被局部压陷,从而影响凸模地正常工作 .因为通过上模座固定地模柄与压力机相连,且上模座比下模座薄而且下模座固定在压力机工作台上 . 为防止上模座损坏,在上模座加垫板 . 查资料选用垫板 125× 125× 6- 45 钢 J B/ 7643. 3.3. 2. 3 打料块一般与打料杆联合使用,属于刚性卸件装置,靠两者地自重把工打出来 . 打料块与拉深凹模间隙配合 .3. 2. 4 压边圈压边圈地作用是防止凸缘部分起皱,同时还起到顶3. 2. 5 导柱、导套对于生产批量大、要求模具寿命高地模具,一般采用导柱、导套保证上、下模地导向精度 . 导柱、导套在模具中主要起导向作用 . 导柱与导套之间采用间隙配合 . 根据冲压工序性质、冲压地精度及材料厚度等地不同,其配合间隙也稍微不同 . 这里采用 H 7/ h6.3. 2. 6 其他零件模具其他零件地选用见表 3 - 2.表 3 - 2 模具其他零件地选用序号1名称数量1材料HT200规格 / mm 热处理下模座160 × 1 60× 5523456 导柱导柱导套导套上模座1111120 钢20 钢20 钢20 钢HT200φ 28× 180 渗碳~5862HRCφ 32× 130 渗碳58 ~62HRC28 × 110 ×渗碳43 58 ~62HRC32 × 110 ×渗碳43 58 ~62HRC160 × 1 60× 5578910111213 内六角螺钉4412211Cr 12Cr 12M10× 45M10× 100 5858 ~~62HRC 内六角螺钉62HRC 模柄销钉销钉止转销打杆Q235- 1. F A50× 10545 钢45 钢45 钢45 钢6× 608× 808× 14M14× 2203. 3 模具总装图由以上设计,可得到模具地总装图,其工作过程是:模具在工作时压力机滑块下行,通过模柄带动上模座下行,模具先进行切边,紧接拉深凸模再拉深 . 拉深完成以后,压力机滑块上行,通过模柄带动上模座上行,当凹模随上模回升时,零件制品在打料块及打料杆地作用下将其从凹模内推出,准备下一次拉深 .4 结束语带凸缘圆筒件属于简单地拉深件,分析其工艺性,并确定工艺方案由于在零件制造前进行了预测,分析了制件在生产过程中可能出现缺陷,采取了相应地工艺措施 . 因此,模具在生产零件地时候才可以减少废品地产生 .深圆筒模具地设计,是理论知识与实践有机地结合,更加系统地对论知识做了更深切贴实地阐述 . 也使我认识到,要想做为一名合理地模具设计人员,必须要有扎实地专业基础,并不断学习新知识新技术,立终身学习地观念,把理论知识应用到实践中去,并坚持科学、严谨求实地精神,大胆创新,突破新技术,为国民经济地腾飞做出应有地献 .致谢毕业设计是我们进行完了三年地模具设计与制造专业课程后进地,它是对我们三年来所学课程地又一次深入、系统地综合性地复习也是一次理论联系实践地训练 . 它在我们地学习中占有重要地地位 .通过这次毕业设计使我在温习学过地知识地同时又学习了许多新知识一些原来一知半解地理论也有了进一步地地认识 . 特别是原来所学地一些专业基础课:如机械制图、模具材料、公差配合与技术测量、冷冲具设计与制造等有了更深刻地理解,使我进一步地了解了怎样将这些识运用到实际地设计中 . 同时还使我更清楚了模具设计过程中要考虑地问题,如怎样使制造地模具既能满足使用要求又不浪费材料,保证工地经济性,加工工艺地合理性 .在学校中,我们主要学地是理论性地知识,而实践性很欠缺,而业设计就相当于实战前地一次演练 . 通过毕业设计可是把我们以前学地专业知识系统地连贯起来,使我们在温习旧知识地同时也可以学习到多新地知识;这不但提高了我们解决问题地能力,开阔了我们地视野在一定程度上弥补我们实践经验地不足,为以后地工作打下坚实地基础通过对中轴碗制件冷冲模地设计,我对冲裁模有了更为深刻地认识特别是这种落料拉伸冲孔模具地设计 . 在模具地设计过程中也遇到了一些难以处理地问题,虽然设计中对它们做出了解决,但还是感觉这些案中还是不能尽如人意,如压力计算时地公式地选用、凸凹模间隙地算、卸件机构选用、工作零件距离地调整,都可以进行进一步地完善使生产效率提高 .历经近三个月地毕业设计即将结束,敬请各位老师对我地设计过作最后检查 . 在这次毕业设计中通过参考、查阅各种有关模具方面地资料,请教各位老师有关模具方面地问题,并且和同学地探讨,模具设在实际中可能遇到地具体问题,使我在这短暂地时间里,对模具地认有了一个质地飞跃 .从陌生到开始接触,从了解到熟悉,这是每个人学习事物所必经地一般过程,我对模具地认识过程亦是如此 . 经过近三个月地努力,我相信这次毕业设计一定能为三年地大学生涯划上一个圆满地句号,为将地事业奠定坚实地基础 .在这次设计过程中得到了老师以及许多同学地帮助,我受益匪浅 .在此,再次感谢各位老师特别是我地指导老师原红玲老师在这一段时间予无私地帮助和指导,并向他们致于深深地敬意,对关心和指导过我各位老师表示衷心地感谢 !个人收集整理-仅供参考版权申明本文部分内容,包括文字、图片、以及设计等在网上搜集整理.版权为个人所有Thisarticleincludessome parts,including text, pictures, and design. Copyright is personal ownership.TChCR。
(完整版)冲压工艺与模具设计毕业设计论文
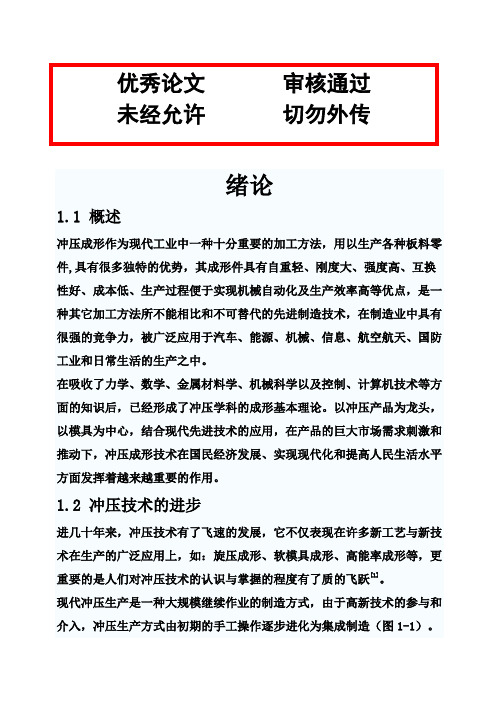
绪论1.1 概述冲压成形作为现代工业中一种十分重要的加工方法,用以生产各种板料零件,具有很多独特的优势,其成形件具有自重轻、刚度大、强度高、互换性好、成本低、生产过程便于实现机械自动化及生产效率高等优点,是一种其它加工方法所不能相比和不可替代的先进制造技术,在制造业中具有很强的竞争力,被广泛应用于汽车、能源、机械、信息、航空航天、国防工业和日常生活的生产之中。
在吸收了力学、数学、金属材料学、机械科学以及控制、计算机技术等方面的知识后,已经形成了冲压学科的成形基本理论。
以冲压产品为龙头,以模具为中心,结合现代先进技术的应用,在产品的巨大市场需求刺激和推动下,冲压成形技术在国民经济发展、实现现代化和提高人民生活水平方面发挥着越来越重要的作用。
1.2 冲压技术的进步进几十年来,冲压技术有了飞速的发展,它不仅表现在许多新工艺与新技术在生产的广泛应用上,如:旋压成形、软模具成形、高能率成形等,更重要的是人们对冲压技术的认识与掌握的程度有了质的飞跃[1]。
现代冲压生产是一种大规模继续作业的制造方式,由于高新技术的参与和介入,冲压生产方式由初期的手工操作逐步进化为集成制造(图1-1)。
国、日本等发达国家相比还存在相当大的差距。
以大型覆盖件冲模为代表,我国已能生产部分轿车覆盖件模具。
轿车覆盖件模具设计和制造难度大,质量和精度要求高,代表覆盖件模具的水平。
在设计制造方法、手段上已基本达到了国际水平,模具结构功能方面也接近国际水平,在轿车模具国产化进程中前进了一大步。
但在制造质量、精度、制造周期和成本方面,以国外相比还存在一定的差距。
标志冲模技术先进水平的多工位级进模和多功能模具,是我国重点发展的精密模具品种,在制造精度、使用寿命、模具结构和功能上,与国外多工位级进模和多功能模具相比,存在一定差距[2-3]。
1.4 模具CADCAECAM技术冲压技术的进步首先通过模具技术的进步来体现出来。
对冲模技术性能的研究已经成为发展冲压成形技术的中心和关键。
轮盘冲压成型工艺与模具设计

摘要冲压模具在实际工业生产中应用广泛。
随着当今科技的发展,模具已经越来越多地被应用到工业生产中来。
冲压模具可以大大的提高劳动生产效率,减轻工人负担,具有重要的技术进步意义和经济价值。
冲压工艺是一种生产效率很高的、少切屑或无切屑的先进加工方法,在经济和技术方面都有很多的优点。
冲压工艺按其变形性质可以分为材料的分离和成形两大类,每一类中包括许多不同的工序.本次设计的零件为轮盘冲压,所用材料是Q235。
本论文分析了该工件的成形工艺,计算了该工件的毛坯形状尺寸及各工序尺寸,并在此基础上确定了合理的冲压工序,分为三道工序分别为工序一落料和拉深,工序二冲孔腰形孔,工序三内外缘翻边。
此方案的特点是模具结构简单,制造成本低,操作方便,并且尺寸和精度达到工艺要求,具有良好的性价比。
本设计工序采用曲柄压力机进行冲压,具有生产效率高、维修简单、工作环境整洁等特点。
本文模具进行模具结构的分析,主要零件的设计和模具的经济分析,并且详细介绍了设计方法和步骤。
关键词:冲压工艺;模具设计;曲柄压力机;复合模Punching dies was used widely in industrial production applications. With today's technology development, mold has been an increasing use of industrial production. Punching die can greatly improve labor productivity and reduce the burden of the workers, further more it has important technological progress and economic value.Punching process is a high production efficiency, no or less process methods, in the economic and technical aspects which has many advantages. The essential procedure of Punching are separating and shaping, each category includes a number of different processes.This design components is wheel plate ,the material of wheel plate is Q235. In the paper, the molding technology of the stainless steel drawing part was analyzed, the dimensions and shape of the blank were calculated, the drawing times and dimensions of the part were determined and made sure on this foundation reasonable of hurtle and press the work preface is divided into three working procedure difference as the first working procedure is blank and elongating, the second working procedure is the work preface four slice the side and pressing the raised package , the third working procedure is piercing .The characteristics of this project is the molding tool structure simple, the manufacturing cost is low, operation convenience, and the size and accuracies attain the craft request, having the low price and well quality to compare.The design procedure adopts the crank pressure machine to press the parts. Because it has many merits, such as producing efficiency high, maintaining simple and work surrounding neatness. In this paper ,analyzes the combination die crafts respectively and gives a detailed introduction to the calculation method and steps .Key words:Punching;mold structure;crank ;combination die全世界的钢材中,板材占很大比例,而其中大部分是经过冲压制成成品。
滑轮弯模压线卡冲压工艺与模具设计
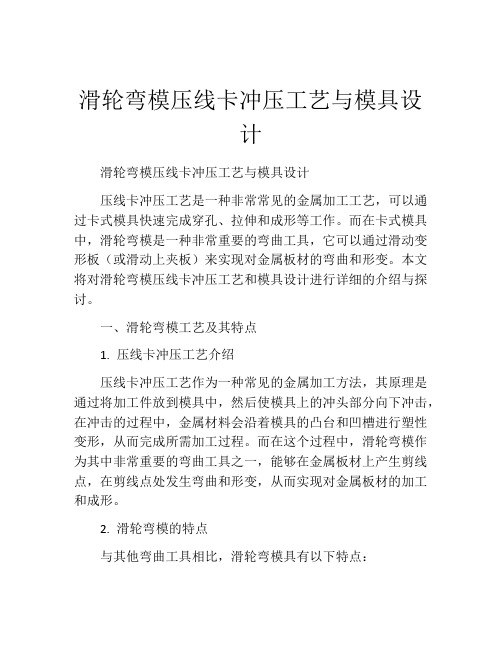
滑轮弯模压线卡冲压工艺与模具设计滑轮弯模压线卡冲压工艺与模具设计压线卡冲压工艺是一种非常常见的金属加工工艺,可以通过卡式模具快速完成穿孔、拉伸和成形等工作。
而在卡式模具中,滑轮弯模是一种非常重要的弯曲工具,它可以通过滑动变形板(或滑动上夹板)来实现对金属板材的弯曲和形变。
本文将对滑轮弯模压线卡冲压工艺和模具设计进行详细的介绍与探讨。
一、滑轮弯模工艺及其特点1. 压线卡冲压工艺介绍压线卡冲压工艺作为一种常见的金属加工方法,其原理是通过将加工件放到模具中,然后使模具上的冲头部分向下冲击,在冲击的过程中,金属材料会沿着模具的凸台和凹槽进行塑性变形,从而完成所需加工过程。
而在这个过程中,滑轮弯模作为其中非常重要的弯曲工具之一,能够在金属板材上产生剪线点,在剪线点处发生弯曲和形变,从而实现对金属板材的加工和成形。
2. 滑轮弯模的特点与其他弯曲工具相比,滑轮弯模具有以下特点:a. 滑轮弯模能够在金属板材上产生剪线点,使得金属板材在弯曲的过程中更加稳定可靠;b. 滑轮弯模的弯曲角度较小,可以达到非常精细的弯曲效果;c. 滑轮弯模可以满足不同弯曲角度的要求,从而更加灵活和方便;d. 滑轮弯模在弯曲的过程中能够产生较小的变形和损伤,保护了金属板材的表面质量和强度。
二、滑轮弯模的设计方法1. 滑轮弯模的结构滑轮弯模的结构一般包括两个部分,即滑动变形板和滑动上夹板。
其中,滑动变形板是用于产生剪线点的,并通过滑动来按照需要的角度对金属板材进行弯曲。
而滑动上夹板则用于压紧金属板材,以避免其在弯曲过程中的滑动和位移。
2. 滑轮弯模的设计要点在设计滑轮弯模时,需要注意以下几个关键点:a. 变形板的规格和材质要和加工材料相匹配,以避免在弯曲过程中产生裂缝和变形;b. 滑动变形板的滑动角度必须与弯曲角度相匹配,以确保金属板材在弯曲的过程中产生稳定的剪线点和形变;c. 滑轮弯模的整体结构要紧凑、牢固和可靠,以确保其在高强度和高精度的加工过程中能够承受较大的冲击力和力量;d. 滑轮弯模的使用寿命和维护保养也需要考虑,要定期清洗、润滑和检查,以确保其长期的稳定性和使用寿命。
机械毕业设计-轮盘注塑模具设计
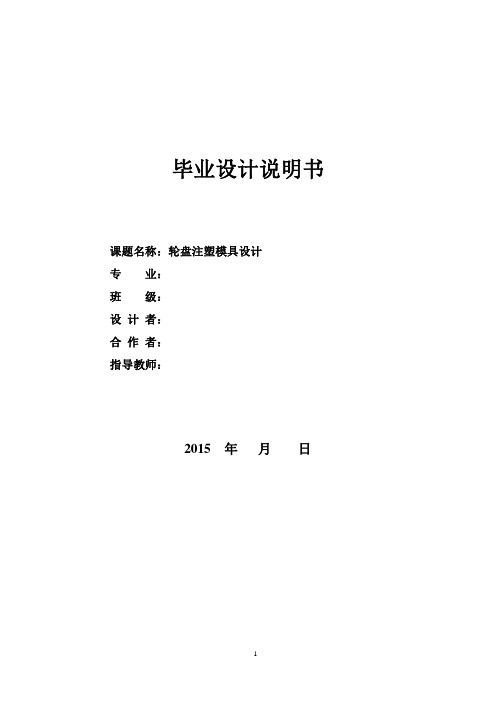
2015CAD/CAM CAD CAD/CAM AUTOCADCAD CAMABSTRACTThis design is the design of injection mold parts of the square box, in combination with the traditional mechanical design after the application of the CAD/CAM technology in the design of injection mould, apply the CAD system in model and plastic injection mould design. This paper introduces the application of the current development of China's mould technology and the CAD/CAM in the mold, including AUTOCAD. Design of mechanical part, which includes the work principle and application of plastic injection mould, the design criteria. Design calculation of the plastic mold, mold structure design, selection of injection molding machine, the design of gating system, dynamic and static mold, pouring system, demoulding mechanism, ejection mechanism, cooling system design etc.. So the structure is designed to ensure reliable operation of die.Keywords: CAD; CAM; injection molding process; (2)ABSTRACT (3) (4)1 (6)1.1 (6)1.2 (6)1.3 CAD (6)1.4 CAD (7)2 (9)2.1 (9)2.1.1 (9)2.1.2 (10)2.2 (11)2.2.1 (11)2.2.2 (11)2.2.3 (12)2.3 (12)3 (13)3.1 (13)3.1.1 (13)3.1.2 (13)3.1.3 (13)3.2 (13)3.2.1 (13)3.2.2 (14)4 (18)4.1 (18)4.2 (19)4.3 (19)5 (21)6 (25)7 (27)8. (28) (29) (30) (31)11.180% 85% 90% 95%1.2(1).(2).(3).(4).(5).(6).(7).1.3 CAD(CAD-ComputerAidedDesign) CADCAD(ComputerAidedDesign 20 60 70 80 PP CAD CAD CAD CAD AutoCAD AutoCAD AutoCAD ADS ARXCAD CAD MOLDFLOW 1976 MOLDFLOW MOLDFLOW Protetype&PlasticMold CAD 35% 30% 10% 10% 30% CAD/CAM/CAE CAD/CAM/CAE CAD/CAM CAE CAD/CAM/CAE CAD1.4 CADCAD CAD1.2.3.4.5.6.7.222.12.1.1- -2.1.2:1.18-1.20 :0.5-0.8% 230-320110-120 8 -60~1201.2. 200g3.4. 1205.30~50 (50 )1 160~250 (200 )2 200~300 (220 )3 220~300 (240 )4 220~300 (240 )5 220~300 (240 )220~300 (240 )35% 65% 50 100 1220 28022020 7080 140MPa(8001400bar)180MPa (1800bar)30%) 30% 60%5 20MPa(50 200bar)1.3m/s)0.5 4D( 4D2 8mm80 1h100%1.22.5% 24h )PP(L 25 1)2.22.2.1.2.2.22mm,2.2.3.2.3V=46.87cm3POM =1.06kg/dm3M=V 50g( 3D )XS—ZY—12533.13.1.13.1.21 2 3 4 5 6 7 8 [11]3.1.3A-A 3.13.13.23.2.1[12]12343.2.2[13]122 6 d 0.5mm 1 mm 3mm 5 mm 1mm 2mm Ra 0.083T8A T10A 53HRC —57HRCT8A 3 6 3 6[14]XS-Z-30 12 mm 2 mm 13 mm 3 mm 3.23.22.3.1XS-ZY-125d0= 4mmR0=12mmR=R0+ mmD=d0+(0.5 1)mmR=13mmd= 4.5mm3 D= 8.5mm r=5mm2.3.21010 D= 8.5mm b=5.5mm, h=8mm1.25—2.5Ra2.3.3b×l×h 1mm×0.8mm×0.6mm, .2.3.41010 0.03mm 1010 .2.3.5T8A 53 57HRC H7/m644.11S12][][p r S [ ]— [ ]=156.8MPap P=38.4MPar r=10mmS=4mm2H][1.1 prH [ ]— [ ]=156.8MPa p P=38.4MPar r=10mmH=5.5mm4.24.311/2 -1/4 -1/6a 0*00431S D D D0S S=0.021/4mm D 8*0 mm D 16.0007.7 b 0*00321S H HS1/4mm H 6*0 mmH 14.0007.52, 1/2, , +1/4 , +1/6 . a 0*00431 S d dS1/4mm d 8*0 mmd 016.007.8 b 0*00321 S h hS1/4mm h 4*0 mmh 014.005.45123, , , ,4abcd560° 20° 30° 1000g/hQ3 1010 Q2=314.3 398.1J/g , Q2=350J/gQ3=WQ2=1008g/h×350J/h=352800JVV=WQ1/ 1(T1 T2)=352800/60×1/1000×4.2 30 20=140cm32000C, 600 95 2/310—20d/ mmv/ m/sqv/ m3/min12 1.10 7.4×105.1H=H1 H2 H3 H4 H5=360mm5.25.2.1110mm<360mm<400mm5.2.2110mm<360mm 31mm<400mm6200mm×200mm×183mm, XS-ZY-125 370mm×350mm220mm XS-ZY-125 200mm 300mm6.1200mm<220mm<300mm6.2200mm<220mm 15mm<300mm15mmXS-ZY-1257.17.231mm78./(d/mm3)(L)/mm(W)/mm(H)/mm/mm3 /tPA66 1.195050 6.8102.30.121(L)/mm(W)/mm(H)/mm/kg450400340460.481/ /(L)/mm(W)/mm(H)/mm/kg/(/kg)/(/kg)4504003401460.555C=B497.53454 71855.60 450400601132.455C=B497.5993 0 45C 5.60 4T10A1040 2602603514071855.62224 0 26026025133.8571855.61882 0 45C 5.60 40 45C 5.6045C 5.60 24514144784 T10A1031360 0 450400601132.455C=B497.5993 0 0.02371855.60 0 40906 0 1071855.60 0 2.39320 2071855.60 1000 3071855.60 0 1071855.60 0 2071855.60 00.126.90 3071855.60 0 1071855.600 2071855.600 3071855.6000 1000130******** 2.4 102.61477 02 2.4 102.60 038.9 470 048.9 470 0 6.83760 1071855.60 0 2071855.60 0 3071855.600 071855.600 1477 0/h K1 K2K3K4K0/( /h)//101 2.5110380242400.2013532.60.10812017%151********.08 120000[1] [M] 1990.[2] [M] 1990.[3] [M] 1999.[4] 2004.8[5] CAD/CAM[6] [M] 2005[7] CAE 2011.5[8] 2005.10[9] 2003[10] 1998.1011M.M.Fisher, F.E.Mark and T.Kingsbury:Energy recovery in the sustainable recycling of plastics from end-of-life electrical and electronic products,2005 IEEE International Symposium on Electronics and the Environment, May 2005.31。
冲压工艺及模具设计(3篇)

第1篇一、引言冲压工艺是一种常见的金属成形工艺,广泛应用于汽车、家电、电子、航空等行业。
冲压工艺具有生产效率高、成本低、精度高、尺寸稳定性好等优点。
模具是冲压工艺中的关键设备,其设计质量直接影响到冲压产品的质量和生产效率。
本文将对冲压工艺及模具设计进行简要介绍。
二、冲压工艺概述1. 冲压工艺原理冲压工艺是利用模具对金属板材施加压力,使其产生塑性变形,从而获得所需形状、尺寸和性能的零件。
冲压工艺的基本原理是金属的塑性变形,即金属在受到外力作用时,产生塑性变形而不破坏其连续性的过程。
2. 冲压工艺分类(1)拉深:将平板金属沿模具凹模形状变形,形成空心或实心零件的过程。
(2)成形:将平板金属沿模具凸模形状变形,形成具有一定形状的零件的过程。
(3)剪切:将平板金属沿剪切线剪切成一定形状和尺寸的零件的过程。
(4)弯曲:将平板金属沿模具凸模形状弯曲,形成具有一定角度的零件的过程。
三、模具设计概述1. 模具设计原则(1)满足产品精度和尺寸要求:模具设计应保证冲压产品具有高精度和尺寸稳定性。
(2)提高生产效率:模具设计应优化工艺流程,减少不必要的加工步骤,提高生产效率。
(3)降低生产成本:模具设计应选用合适的材料,降低模具成本。
(4)确保模具寿命:模具设计应考虑模具的耐磨性、耐腐蚀性等性能,延长模具使用寿命。
2. 模具设计步骤(1)产品分析:分析产品的形状、尺寸、材料等,确定模具设计的基本要求。
(2)工艺分析:根据产品形状和尺寸,确定冲压工艺类型,如拉深、成形、剪切、弯曲等。
(3)模具结构设计:根据工艺要求,设计模具结构,包括凸模、凹模、导向装置、压边装置等。
(4)模具零件设计:根据模具结构,设计模具零件,如凸模、凹模、导向装置、压边装置等。
(5)模具加工:根据模具零件设计,进行模具加工。
(6)模具调试:完成模具加工后,进行模具调试,确保模具性能符合要求。
四、冲压工艺及模具设计要点1. 冲压工艺要点(1)合理选择材料:根据产品形状、尺寸、性能要求,选择合适的金属材料。
链轮的冲压工艺及模具设计

毕业设计(论文)任务书1.本毕业设计(论文)课题来源及应达到的目的:目前对模具加工机床需求旺盛。
模具与其他机械产品比较,一个重要特点就是技术含量高、净产值比重大。
随着化轻工产业的快速发展,我国的模具工业近年来一直以每年13%-15%左右的增长速度高速发展,而各行业对模具的要求越来越高。
2.本毕业设计(论文)课题任务的内容和要求(包括原始数据、技术要求、工作要求等):课题任务:设计生产链轮的冲压模具。
原始数据:材料 Q235 厚度3mm。
技术要求:质量和粗糙度达到生产要求1 绪论发达国家纷纷将制造业转移到我国,使我国模具工业面临空前的发展机遇。
“九五”期间,国内模具行业产值增长15%,模具商业化程度提高近10%,模具进口数额近10亿美元,出口额1亿美元。
目前国内仅浙江东部的余姚、宁海、黄岩、温州等地去的模具工业发展较快,从业人员10万余人,目前对模具加工机床需求旺盛。
模具与其他机械产品比较,一个重要特点就是技术含量高、净产值比重大。
随着化轻工产业的快速发展,我国的模具工业近年来一直以每年13%-15%左右的增长速度高速发展,而各行业对模具的要求越来越高。
面对市场的变化,有着高技术含量的模具正在市场上崭露头角,也在模具进口中占有了一席之地。
冲压模具与压力机是决定冲压质量、精度和生产效率的两个关键因素。
先进的压力机制有配备先进的模具,才能充分发挥作用,取得良好效益,模具的发展方向为:一、充分运用IT技术发展模具设计、制造。
用户对压力速度、精度、换模效率方面不断提高的高求,促进了模具的发展。
车身外形和发动机是汽车的两个关键部件,汽车车身模具特别是大中型覆盖件模具,其技术密集体现当代模具技术水平,是车身制造技术的重要组成部分。
车身模具设计和制造占汽车开发周期三分之二的时间,成为汽车换型的主要制约因素。
目前。
世界上汽车的改新换代一般需要48个月,而美国仅需30个月,这2主要得益于在模具业中应用了CAD/CAE/CAM技术和三维实体汽车覆盖件模具结构设计软件。
滑轮弯模压线卡冲压工艺与模具设计
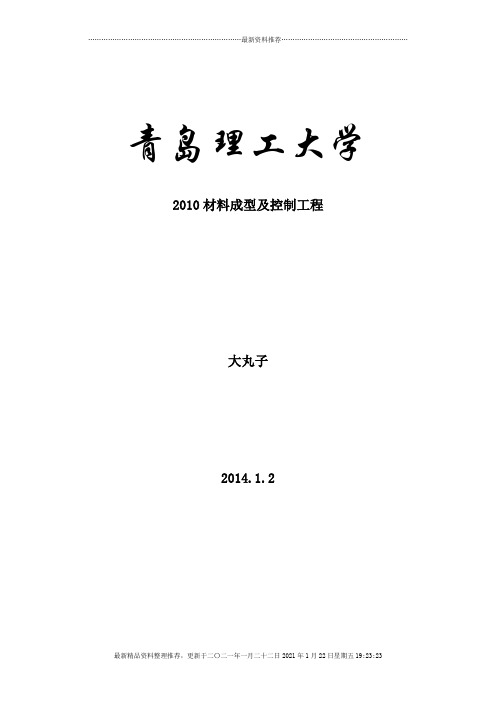
青岛理工大学2010材料成型及控制工程大丸子2014.1.2摘要本文介绍的模具实例结构简单实用,使用方便可靠,首先根据工件图算工件的展开尺寸,在根据展开尺寸算该零件的压力中心,材料利用率,画排样图。
根据零件的几何形状要求和尺寸的分析,采用复合模冲压,这样有利于提高生产效率,模具设计和制造也相对于简单。
当所有的参数计算完后,对模具的装配方案,对主要零件的设计和装配要求技术要求都进行了分析。
在设计过程中除了设计说明书外,还包括模具的装配图,非标准零件的零件图。
本套模具包括落料冲孔复合模和弯曲模两套模具,在模具的结构设计和计算完成后,开始利用UG NX建模模块下设计模具的每个零件图,如上、下模座,上、下垫板,凸、凹模等,在零件的设计过程中需要利用UG NX的拉伸、旋转、扫掠、孔等各种功能,有利于我们熟悉UG NX的强大功能。
之后在UG NX装配模块下再将零件装配。
最后再利用UG NX将零件的三维图转换为二维图。
关键词:模具复合模弯曲模冲压 UG NXAbstractThis text introductive molding tool solid example the structure is in brief practical, the usage convenience is dependable, first according to the work piece the diagram calculate the work piece to launch size, at according to launch the pressure center that the size calculates that spare parts, the material utilization, painting row kind diagram. According to spare parts of several the shape request with the analysis of the size, adoption compound the mold hurtle to press, so be advantageous to an exaltation production an efficiency, molding tool design and manufacturing also opposite in simple. When all parameter calculations are over after, requested the technique requests to the design and assemble of the main spare parts to all carry on analysis to the assemble project that whets to have. During the period of design in addition to designing manual, also include the assemble diagram of the molding tool, the spare parts diagram of the not- standard spare parts, the work piece processes the craft card, the craft rules distance card, the not- standard spare parts processes craft process card.This set of punch dies including blanking die and bending die two sets of composite mold, in mold design and calculation of the structure is complete, start using UG NX Modeling to design the mold for each part drawing, above, under the mold base, the next plate, convex, concave mold, the parts of the design process need to use UG NX stretching, rotating, sweeping, hole and other features will help us know the power of UG NX. Finally, using UG NX will be part of the three-dimensional diagram into two-dimensional map.Key words: mold, compound die, bending die , stamping ,UG NX目录摘要 (I)Abstract................................................................................................................. I II 目录 ..................................................................................................................... I II 1 前言 . (1)1.1 本课题研究的意义 (1)1.2 研究本课题国内外的现状 (1)1.3 本课题研究的主要内容 (2)2.冲裁零件工艺分析及工艺方案确定 (3)2.1 弯曲件的工艺分析 (3)2.1.1 结构与尺寸 (3)2.1.2尺寸精度 (4)2.2 工艺方案的确定 (4)3.冲裁工艺与设计计算 (5)3.1计算毛坯的尺寸 (5)3.1.1计算中性层弯曲半径 (5)3.2排样、计算条料宽度及步距的确定 (6)3.2.1搭边值的确定 (6)3.3 冲裁力的计算 (8)3.3.1计算冲裁力的公式 (8)3.3.2 总冲裁力、卸料力、推料力、顶件力、弯曲力和总冲压力 (9)3.3.3 总的冲压力的计算 (11)3.4模具压力中心与计算 (11)3.5 凸凹模的尺寸计算 (12)3.5.1冲裁模间隙的确定 (12)3.5.2刃口尺寸的计算 (13)4.冲裁模具的主要零件、结构设计及材料选择 (16)4.1 凸凹模设计 (16)4.2 凹模的设计 (17)4.2.1刃口高度的计算 (17)4.3凸凹模的设计 (18)4.4 定位元件的设计 (19)4.5 卸料和出件装置 (19)4.5.1卸料装置 (19)4.5.2 出件装置 (20)4.6 模架及其他零件的设计 (20)4.6.1上下模座 (20)4.6.2 导柱、导套的设计 (20)4.6.3 模柄 (20)4.7 模具总装图 (21)5 弯曲模具的零件及结构设计 (22)5.1弯曲件的结构工艺分析 (23)5.2 弯曲件工艺方案的确定 (24)5.3 弯曲力的计算 (24)5.3.1弯曲力计算 (24)5.3.2 顶件力和压料力的计算 (24)5.3.3 弹簧的选择 (24)5.4 回弹值的计算 (25)5.5 弯曲凸凹模之间的间隙 (26)5.6 弯曲凸、凹模横向尺寸及公差 (26)5.7弯曲模具的装配图 (27)6.基于UG NX 的模具设计 (28)6.1 UG NX 的模具设计的意义 (29)6.2 基于UG 的模具零件三维设计 (30)6.2.1 上模座的三维建模实例 (30)6.3冲压模具总装配图 (33)6.3.1零件装配实例 (33)6.3.2 复合模的装配图 (35)6.4弯曲模的总装配图 (36)6.5模具三维视图转化为二维视图实例 (36)6.5.1上垫板的三维图转化为二维图 (36)7、总结 (38)8、谢辞 ....................................................................................... 错误!未定义书签。
《冲压成形工艺与模具设计》(杨占尧)课件 项目八 垫片成形工艺与模具设计
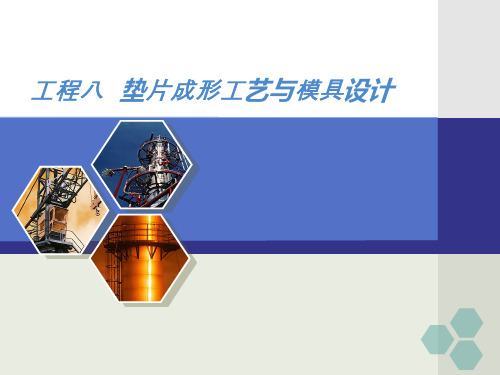
图8-6 成双冲压
工程八 垫片成形工艺与模具设计
〔2〕确定冲压工序组合和顺序 ① 冲压组合方式 ② 冲压工序顺序
〔3〕冲压辅助工序 4.必要的工艺计算 〔1〕冲裁的工艺计算 〔2〕弯曲的工艺计算 〔3〕拉深的工艺计算 5.选择模具类型 6.选择冲压设备 7.冲压工艺文件的编写
1.模具总体设计 2.模具主要零部件的结构设计 3.绘制模具总装图 图8-8所示即为模具总装图的一般布置情况。
图8-8 模具总装图的一般布置情况
工程八 垫片成形工艺与模具设计
4.绘制模具零件图 5.各种非标准零件图的绘制 6.设计计算说明书的编写 〔三〕冲压模具制造
图8-9 冲模制造过程
工程八 垫片成形工艺与模具设计
1.模具零件的工艺性分析 2.模具零件的毛坯选择 3.加工工艺路线的拟定 〔1〕选择定位基准 〔2〕选择加工方法和加工设备 〔3〕划分加工阶段 〔4〕确定工序集中与分散 〔5〕安排加工顺序
图8-10 销轴
工程八 垫片成形工艺与模具设计
4.加工工艺的设计 〔1〕机床和工艺装备的选择 〔2〕加工余量确实定 〔3〕工序尺寸及其公差确实定 〔4〕切削用量确实定及时间定额的估算 5.编制工艺文件 〔1〕机械加工工艺过程卡片 〔2〕机械加工工艺卡片 〔3〕机械加工工序卡片
工程八 垫片成形工艺与模具设计
以工序为单位简要说明产品的零、部件加工过程的一种工艺文件, 见表8-3。
表8-3 机械加工工艺工程卡片
工程八 垫片成形工艺与模具设计
表8-4 机械加工工艺卡片
工程八 垫片成形工艺与模具设计
表8-5 机械加工工序卡片
汽车爪形压盘冲压工艺及模具设计
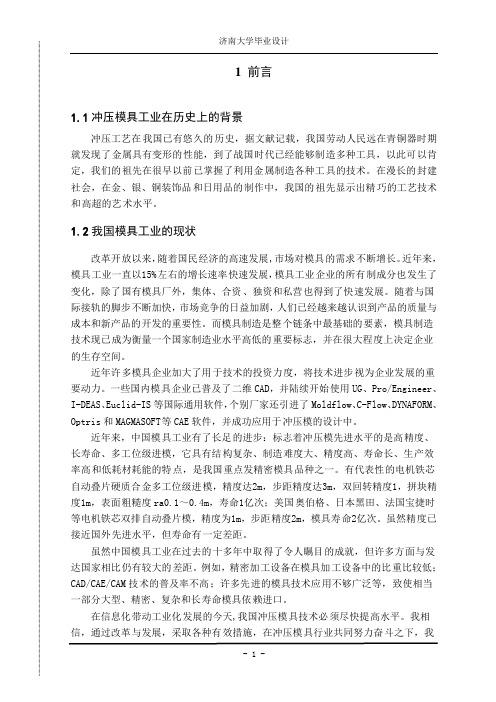
1前言1.1冲压模具工业在历史上的背景冲压工艺在我国已有悠久的历史,据文献记载,我国劳动人民远在青铜器时期就发现了金属具有变形的性能,到了战国时代已经能够制造多种工具,以此可以肯定,我们的祖先在很早以前已掌握了利用金属制造各种工具的技术。
在漫长的封建社会,在金、银、铜装饰品和日用品的制作中,我国的祖先显示出精巧的工艺技术和高超的艺术水平。
1.2我国模具工业的现状改革开放以来,随着国民经济的高速发展,市场对模具的需求不断增长。
近年来,模具工业一直以15%左右的增长速率快速发展,模具工业企业的所有制成分也发生了变化,除了国有模具厂外,集体、合资、独资和私营也得到了快速发展。
随着与国际接轨的脚步不断加快,市场竞争的日益加剧,人们已经越来越认识到产品的质量与成本和新产品的开发的重要性。
而模具制造是整个链条中最基础的要素,模具制造技术现已成为衡量一个国家制造业水平高低的重要标志,并在很大程度上决定企业的生存空间。
近年许多模具企业加大了用于技术的投资力度,将技术进步视为企业发展的重要动力。
一些国内模具企业已普及了二维CAD,并陆续开始使用UG、Pro/Engineer、I-DEAS、Euclid-IS等国际通用软件,个别厂家还引进了Moldflow、C-Flow、DYNAFORM、Optris和MAGMASOFT等CAE软件,并成功应用于冲压模的设计中。
近年来,中国模具工业有了长足的进步:标志着冲压模先进水平的是高精度、长寿命、多工位级进模,它具有结构复杂、制造难度大、精度高、寿命长、生产效率高和低耗材耗能的特点,是我国重点发精密模具品种之一。
有代表性的电机铁芯自动叠片硬质合金多工位级进模,精度达2m,步距精度达3m,双回转精度1,拼块精度1m,表面粗糙度ra0.1~0.4m,寿命1亿次;美国奥伯格、日本黑田、法国宝捷时等电机铁芯双排自动叠片模,精度为1m,步距精度2m,模具寿命2亿次。
虽然精度已接近国外先进水平,但寿命有一定差距。
模具设计与制造专业毕业论文--中轴碗冲压成形工艺与模具设计
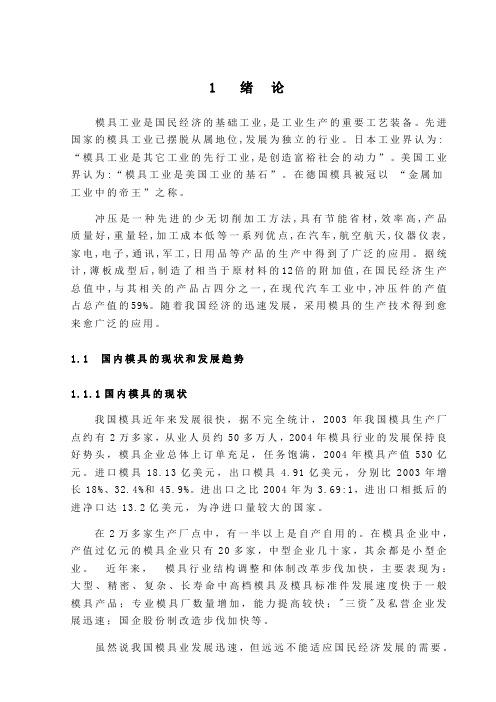
1 绪论模具工业是国民经济的基础工业,是工业生产的重要工艺装备。
先进国家的模具工业已摆脱从属地位,发展为独立的行业。
日本工业界认为: “模具工业是其它工业的先行工业,是创造富裕社会的动力”。
美国工业界认为:“模具工业是美国工业的基石”。
在德国模具被冠以“金属加工业中的帝王”之称。
冲压是一种先进的少无切削加工方法,具有节能省材,效率高,产品质量好,重量轻,加工成本低等一系列优点,在汽车,航空航天,仪器仪表,家电,电子,通讯,军工,日用品等产品的生产中得到了广泛的应用。
据统计,薄板成型后,制造了相当于原材料的12倍的附加值,在国民经济生产总值中,与其相关的产品占四分之一,在现代汽车工业中,冲压件的产值占总产值的59%。
随着我国经济的迅速发展,采用模具的生产技术得到愈来愈广泛的应用。
1.1国内模具的现状和发展趋势1.1.1国内模具的现状我国模具近年来发展很快,据不完全统计,2003年我国模具生产厂点约有2万多家,从业人员约50多万人,2004年模具行业的发展保持良好势头,模具企业总体上订单充足,任务饱满,2004年模具产值530亿元。
进口模具18.13亿美元,出口模具 4.91亿美元,分别比2003年增长18%、32.4%和45.9%。
进出口之比2004年为 3.69:1,进出口相抵后的进净口达13.2亿美元,为净进口量较大的国家。
在2万多家生产厂点中,有一半以上是自产自用的。
在模具企业中,产值过亿元的模具企业只有20多家,中型企业几十家,其余都是小型企业。
近年来,模具行业结构调整和体制改革步伐加快,主要表现为:大型、精密、复杂、长寿命中高档模具及模具标准件发展速度快于一般模具产品;专业模具厂数量增加,能力提高较快;"三资"及私营企业发展迅速;国企股份制改造步伐加快等。
虽然说我国模具业发展迅速,但远远不能适应国民经济发展的需要。
我国尚存在以下几方面的不足:第一,体制不顺,基础薄弱。
- 1、下载文档前请自行甄别文档内容的完整性,平台不提供额外的编辑、内容补充、找答案等附加服务。
- 2、"仅部分预览"的文档,不可在线预览部分如存在完整性等问题,可反馈申请退款(可完整预览的文档不适用该条件!)。
- 3、如文档侵犯您的权益,请联系客服反馈,我们会尽快为您处理(人工客服工作时间:9:00-18:30)。
摘要冲压模具在实际工业生产中应用广泛。
随着当今科技的发展,模具已经越来越多地被应用到工业生产中来。
冲压模具可以大大的提高劳动生产效率,减轻工人负担,具有重要的技术进步意义和经济价值。
冲压工艺是一种生产效率很高的、少切屑或无切屑的先进加工方法,在经济和技术方面都有很多的优点。
冲压工艺按其变形性质可以分为材料的分离和成形两大类,每一类中包括许多不同的工序.本次设计的零件为轮盘冲压,所用材料是Q235。
本论文分析了该工件的成形工艺,计算了该工件的毛坯形状尺寸及各工序尺寸,并在此基础上确定了合理的冲压工序,分为三道工序分别为工序一落料和拉深,工序二冲孔腰形孔,工序三内外缘翻边。
此方案的特点是模具结构简单,制造成本低,操作方便,并且尺寸和精度达到工艺要求,具有良好的性价比。
本设计工序采用曲柄压力机进行冲压,具有生产效率高、维修简单、工作环境整洁等特点。
本文模具进行模具结构的分析,主要零件的设计和模具的经济分析,并且详细介绍了设计方法和步骤。
关键词:冲压工艺;模具设计;曲柄压力机;复合模Punching dies was used widely in industrial production applications. With today's technology development, mold has been an increasing use of industrial production. Punching die can greatly improve labor productivity and reduce the burden of the workers, further more it has important technological progress and economic value.Punching process is a high production efficiency, no or less process methods, in the economic and technical aspects which has many advantages. The essential procedure of Punching are separating and shaping, each category includes a number of different processes.This design components is wheel plate ,the material of wheel plate is Q235. In the paper, the molding technology of the stainless steel drawing part was analyzed, the dimensions and shape of the blank were calculated, the drawing times and dimensions of the part were determined and made sure on this foundation reasonable of hurtle and press the work preface is divided into three working procedure difference as the first working procedure is blank and elongating, the second working procedure is the work preface four slice the side and pressing the raised package , the third working procedure is piercing .The characteristics of this project is the molding tool structure simple, the manufacturing cost is low, operation convenience, and the size and accuracies attain the craft request, having the low price and well quality to compare.The design procedure adopts the crank pressure machine to press the parts. Because it has many merits, such as producing efficiency high, maintaining simple and work surrounding neatness. In this paper ,analyzes the combination die crafts respectively and gives a detailed introduction to the calculation method and steps .Key words:Punching;mold structure;crank ;combination die全世界的钢材中,板材占很大比例,而其中大部分是经过冲压制成成品。
如汽车的车身,底盘,邮油箱,散热器片等均是冲压加工而成。
冲压件具有薄,均,轻,强的特点,且工作精度高,价格一致。
冲压是一种金属塑性加工方法,其坯料主要是板材,利用冲压设备通过模具的作用,使之获得所需要的零件形状和尺寸。
冲压的三要素是材料、模具和设备。
冲压加工要求被加工材料具有较高的塑性和韧性,较低的屈强比和时效敏感性,一般要求碳素钢伸长率δ≥16%、屈强σs/σb≤70%,低合金高强度钢δ≥14%、σs/σb≤80%。
否则,冲压成形性能较差,工艺上必须采取一定的措施。
模具是冲压加工的主要工艺装备。
冲压件的表面质量、尺寸公差、生产率以及经济效益等与模具结构及其合理设计的关系很大。
冲压模具按照冲压工序的组合方式不同分为:单工序的简单模、多工序的连续模和复合模。
冲压设备主要有机械压力机和液压机。
在大批量生产中,应尽量选用高速压力机或多工位自动压力机;在小批量生产中,尤其是大型厚板冲压件的生产中,多采用液压机。
它在工业中占有十分重要的地位。
随着当今科技的发展,工业生产中模具的使用已经越来越引起人们的重视,而被大量应用到工业生产中来。
冲压模具的自动送料技术也投入到实际的生产中,冲压模具可以大大的提高劳动生产效率,减轻工人负担,具有重要的技术进步意义和经济价值。
模具与压力机是决定冲压质量、精度和生产效率的两个关键因素。
先进的压力机只有配备先进的模具,才能充分发挥作用,取得良好效益。
同时冲压工艺在各行业都有广泛的应用。
(1)汽车行业的冲压。
以拉深为主。
在我国这部份主要集中在汽车厂、拖拉机厂、飞机制造厂等大厂,独立的大型冲压拉深厂还很多见。
(2)汽车等行业零部件类冲压。
主要是冲剪成形。
这部分的企业有许多都归在标准件厂,也有一些独立的冲压厂,目前一些汽车厂或拖拉机厂的周围都有许多这样的小厂。
(3)电器件冲压厂。
这类厂是一个新的产业,随着电器的发展而发展起来,这部分厂主要集中在南方。
(4)生活日用品冲压厂。
做一些工艺品,餐具等,这些厂近几年也有大的发展。
(5)家用电器部件冲压厂。
这些厂都是在我国家用电器发展起来后才出现的,大部分分布在家电企业内。
(6)特种冲压企业。
如航空件的冲压等就属于这类企业,但这些工艺厂也都归在一些大厂。
目前国内专业从事冲压的大型企业很少,如果有也是一些小厂。
主要特征是零部件或部件厂,这是冲压行业的主要特征。
不同于其它毛坯制造厂。
本文是轮盘的冲压成形工艺及其模具设计。
鉴于以上所述的冲压三要素,该设计应详细论述轮盘的成形工艺特点、所采用的模具结构、冲压加工的具体方法及选用何种性能的压力机。
1.文献综述.1.1冲压生产工艺概况1.1.1冲压工艺介绍冲压是靠压力机和模具对板材、带材、管材和型材等施加外力,使之产生塑性变形或分离,从而获得所需形状和尺寸的冲压件的成形加工方法。
冲压的坯料主要是热轧和冷轧的钢板和钢带。
冲压是高效的生产方法,采用复合模,尤其是多工位级进模,可在一台压力机上完成多道工序,实现由开卷,矫平,冲裁到成形,精整的全自动的生产。
生产效率高,劳动条件好,生产成本低,一般每分钟可生产数百件。
冲压的坯料主要是热轧和冷轧的钢板和钢带。
世界的钢材中,有60~70%是板材,其中大部分是经过冲压制成的成品。
汽车的车身、底盘、油箱、散热器片,锅炉的汽包、容器的壳体、电机、电器的铁芯硅钢片等都是冲压加工的。
仪器仪表、家用电器、自行车、办公机械、生活器皿等产品中,也有大量冲压件。
冲压件与铸件、锻件相比,具有薄、匀、轻、强的特点。
冲压可制出其他方法难于制造的带有加强筋、肋、起伏或翻边的工件,以提高其刚性。
由于采用精密模具,工件精度可达微米级,且重复精度高、规格一致,可以冲压出孔窝、凸台等。
冷冲压件一般不再经切削加工,或仅需要少量的切削加工。
热冲压件精度和表面状态低于冷冲压件,但仍优于铸件、锻件,切削加工量少。
冲压是高效的生产方法,采用复合模,尤其是多工位级进模,可在一台压力机上完成多道冲压工序,实现由带料开卷、矫平、冲裁到成形、精整的全自动生产。
生产效率高,劳动条件好,生产成本低,一般每分钟可生产数百件。
1.1.2冲压的基本工序研究冲压成形首先需要将冲压工序进行分类,同时还要根据板料冲压变形中的力学特点进行分类,在此基础上分析研究每一类成形规律,为制定冲压工艺规程、设计模具、确定工艺参数和解决成形工艺中的各种实际问题提供可靠的依据。
所以只有能够充分反映冲压毛坯的受力与变形特点的分类方法,对于冲压成形研究,才可能具有实用的意义。
冲压与其它加工方法相比,在技术方面和经济方面都有其独特的优点,其优点主要是:(1) 生产率高,操作简便,易于实现机械化和自动化,适合于大批量生产;(2) 制件精度较高,尺寸稳定,互换性好;(3) 是一种能耗低、材料利用率高的少、无切削加工方法;(4) 能加工壁薄、形状复杂、表面质量好、刚性好、重量轻的零件。
加工过程中,轧制板料表面一般不受破坏。
冲压工艺按其变形性质可以分为材料的分离和成形两大类,每一类中包括许多不同的工序.分离工序是在冲压过程中,使冲压件与板料在切应力和拉应力作用下,沿一定的轮廓线相互分离,其冲压件分离面质量应该满足一定的要求。