激光打孔技术在印制电路板上的应用
FPCPCB高精度激光钻孔

FPCPCB高精度激光钻孔
随着市场上对小型化手持式电子设备需求的持续增长,电子器件封装、电路板的集成度越来越稠密、多层,这就要求电路板上通孔尺寸更小、更
精确,典型的孔径要<65μm。
高精度紫外激光钻孔技术的引入为PCB,
FPC以及倒装芯片封装上面盲孔、通孔加工不但带来了极高的精密度与加
工质量,也带来了最低的制造成本与最高的产能。
Spectra-PhyicPuleo系列激光器是PCB、FPC加工导通孔和其他切割
成型的完美工具。
Puleo激光器既有532nm波长也有355nm波长,对于大
多数被加工的材料这两种波长吸收率都是相当高的,尤其是紫外波长。
Puleo激光器的超短脉冲、高峰值功率以及高重复频率等优势可为加工工
艺带来:清洁、碎屑极少;通孔圆度高;生产效率高以及对工件最小的热
效应损伤等诸多益处。
Spectra-Phyic激光加工FPC通孔的细节特征,入口(左),出口(右)。
柔性电路板(8μmCu/24μmPolyimide/8μmCu)上面激光钻孔,孔径小,圆度高,周围材料人损伤小。
高性能高可靠性的Spectra-PhyicPuleo系列激光器
重复频率(nominal)产品型号波长峰值功率平均功率脉冲宽度
Puleo532-34Puleo355-20Puleo355-
10532nm~13kW>34W<30nat120kHz120kHz355nm~10kW>20W<23nat100kHz100k Hz355nm~5kW>10W<23nat90kHz90kHz。
HDI印制电路板中的激光钻孔工艺研究及应用

HDI印制电路板中的激光钻孔工艺研究及应用杨婷;何为;成丽娟;周国云;徐缓【摘要】This paper has studied the process and theory of fabricating micro-via using the CO2 lasers on the HDI high density interconnect printed circuit board. Experiment described the process of fabricating micro-via in FR4 substrates using the CO2 laser. Bind via was drilled and evaluated for taper, wall-angle and smoothness through metallurgical microscopy. The effects of the process parameters such as pulse energy, pulse width, the number of pulses and mask dimension were also studied and further optimized. The best process parameters for micro-via with different sizes have been fund.%文章研究采用CO2激光器研究了HDI印制电路板制作微孔的技术,通过金相显微镜分析了CO2激光器制作的盲孔的锥形度、孔壁角度和孔壁平整性。
讨论了激光参数对孔的影响,用优化试验优化参数进,一步确定了真圆度和上下孔径比最优的脉冲能量、脉冲宽度、脉冲次数和光罩尺寸。
得到了不同孔径微孔的制作最优工艺参数。
【期刊名称】《印制电路信息》【年(卷),期】2014(000)004【总页数】5页(P210-214)【关键词】CO2激光钻孔;HDI;盲孔;优化试验【作者】杨婷;何为;成丽娟;周国云;徐缓【作者单位】电子科技大学,四川成都 610000;电子科技大学,四川成都610000;电子科技大学,四川成都 610000;电子科技大学,四川成都 610000;博敏电子股份有限公司,广东梅州 513768【正文语种】中文【中图分类】TN411 引言CO2激光钻孔是目前刚性HDI板中盲孔的主要加工方式[1]。
激光打孔机标准

激光打孔机标准激光打孔机是一种利用激光技术和数控技术设计而成的打孔专用设备。
其主要应用于印制线路板的内层与内层、外层与内层之间的连接,以及其他行业的小孔加工。
下面将从激光打孔机的技术参数、应用范围、特点、选购要点等方面进行详细介绍。
一、技术参数激光打孔机的技术参数是其性能的重要体现,主要包括激光功率、光束模式、峰值功率、打孔速度、打孔精度等。
这些参数直接影响着激光打孔机的加工效果和适用范围。
1. 激光功率:激光功率是激光打孔机加工能力的重要指标,通常有50W、100W、200W、300W等不同型号。
激光功率越高,加工速度和效率越高,适用范围也越广。
2. 光束模式:光束模式是指激光束在空间中的分布形态,好的光束模式可以提高激光加工的质量和效率。
常见的光束模式有TEM00、TEM10等。
3. 峰值功率:峰值功率是指激光在短时间内达到的最大功率,峰值功率越高,打孔速度越快,加工效果越好。
4. 打孔速度:打孔速度是指激光打孔机在单位时间内完成的打孔数量,打孔速度快,效率高,可以提高生产效率。
5. 打孔精度:打孔精度是指激光打孔机加工出的孔洞尺寸和位置的准确性,高精度加工可以满足高品质产品的生产需求。
二、应用范围激光打孔机的应用范围广泛,主要应用于以下行业和领域:1. 电子行业:激光打孔机可以用于印制线路板的内外层连接,以及手机、电脑等电子产品的零部件加工。
2. 汽车行业:激光打孔机可用于汽车零部件的加工,如燃油喷嘴、涡轮叶片、传感器等。
3. 医疗器械行业:激光打孔机可用于医疗器械的加工,如内燃机燃油喷嘴、探测器、传感器等。
4. 包装行业:激光打孔机可用于包装材料的加工,如激光打孔纸袋、塑料包装等。
5. 其他行业:激光打孔机还可用于制鞋、箱包、皮具等行业的皮革打孔,以及光伏玻璃、建材等行业的打孔加工。
三、特点激光打孔机具有以下特点:1. 加工精度高:激光打孔机采用高精度的数控系统,可以实现精确的孔洞位置和尺寸控制。
激光技术在制造工业中的应用

激光技术在制造工业中的应用在当今的制造工业领域,激光技术正以其独特的优势发挥着日益重要的作用。
从汽车制造到电子设备生产,从航空航天到医疗器械,激光技术的应用几乎无处不在,为提高生产效率、提升产品质量以及实现创新设计提供了强大的支持。
激光切割是激光技术在制造工业中最常见的应用之一。
它利用高能量密度的激光束照射到被切割材料的表面,瞬间使其局部熔化、汽化,并通过高压气体将熔化或汽化的物质吹走,从而实现材料的分离。
与传统的切割方法相比,激光切割具有极高的精度和速度。
无论是金属薄板还是厚板,激光切割都能轻松应对,切口光滑平整,几乎无需后续加工。
在汽车制造中,激光切割常用于车身零部件的加工,能够精确地切割出各种复杂形状的零件,大大提高了汽车的装配精度和整体质量。
在电子设备制造中,激光切割可以对印刷电路板进行精细加工,确保线路的准确性和完整性。
激光焊接是另一个重要的应用领域。
激光焊接通过将激光束聚焦在焊接部位,使材料瞬间达到熔点并融合在一起。
它具有焊缝窄、热影响区小、焊接强度高等优点。
在汽车制造中,激光焊接被广泛应用于车身结构的连接,不仅提高了车身的强度和安全性,还减少了焊接变形。
在航空航天领域,激光焊接用于飞机发动机零部件的制造,能够满足高强度、高精度的焊接要求。
此外,激光焊接在医疗器械、珠宝制造等行业也有着广泛的应用。
激光打标是一种非接触式的标记方法,通过激光束在材料表面留下永久性的标记。
它可以实现高精度、高清晰度的标记效果,无论是文字、图案还是二维码,都能清晰准确地呈现。
在电子元器件制造中,激光打标用于标记产品的型号、规格等信息,便于识别和追溯。
在食品和药品包装上,激光打标可以标记生产日期、保质期等重要信息,具有防伪、环保等优点。
激光打孔也是激光技术的一项重要应用。
它能够在各种材料上加工出微小而精确的孔洞,广泛应用于航空航天、医疗器械、化纤等领域。
例如,在航空发动机的叶片上加工冷却孔,在化纤喷丝板上加工微孔,都需要高精度的激光打孔技术。
印刷制版中的激光技术应用的原理

印刷制版中的激光技术应用的原理激光技术在印刷制版中的应用原理主要包括激光光束的形成、激光光束的调制和激光光束的投射。
激光光束的形成是通过激光器产生的。
激光器通常由激光介质、泵浦源和光学谐振腔组成。
激光介质的种类有很多,如气体、液体或固体等。
当激光介质处于激发态时,外界的泵浦源(如电流、光、化学反应等)可以使其处于受激辐射的状态,进而激发介质分子向较低能级跃迁。
这种辐射过程是自发辐射和受激辐射的综合效果,它产生了具有高能量、高亮度和高方向性的激光光束。
光学谐振腔是一个能够反射激光光线的结构,它可以反射光线,并将它们反复通过激光介质,从而提高激光光束的放大程度。
最终,通过一系列的过程,激光器可以产生高功率的激光光束。
激光光束的调制是为了满足印刷制版的要求。
调制一般包括功率调制和空间调制。
功率调制是通过改变输入光束的功率来实现的,可以通过控制激光的泵浦源或激发介质的参数来调节,以获得所需的功率输出。
空间调制是指通过空间光调制器(如光栅、液晶等)改变激光光束的相位和振幅来实现,以进一步调试光束的特性。
这样可以将光束聚焦到一个确定的位置,以便在制版过程中更好地控制激光的能量分布。
激光光束的投射是通过合适的光学系统来实现的,以便将光束准确地投射到印刷制版的目标上。
投射一般需要满足激光光束的均匀性、稳定性和焦距等要求,以确保最终的印刷质量。
激光光束的均匀性通过调节光束形状(如圆形、方形等)和能量分布来实现。
光束的稳定性通过合理设计和调节光学系统的参数来实现。
焦距的调节是基于制版材料的类型和厚度来实现的,以实现所需的刻印或曝光效果。
除了激光技术在印刷制版中的基本原理外,还有一些与激光技术相关的辅助技术也在印刷制版中得到了应用。
例如,激光束的散斑技术可以通过调整激光光源和光学系统来消除激光光束的散斑效应,从而获得更好的印刷效果。
激光束的光谱分析和调控技术可以用于实时监测激光光束的性能,并根据需求进行调节,以获得更好的印刷质量。
电路板镭射钻孔流程

电路板镭射钻孔流程
激光钻孔技术是一种高精度、高效率的加工方法,广泛应用于电路板制造行业。
电路板镭射钻孔是一种使用激光束将孔洞精确地加工在电路板上的加工技术。
下面介绍电路板镭射钻孔的流程:
1. 设计:首先,根据电路板的设计图纸确定需要加工的孔洞位置、尺寸和数量等参数。
2. 设备准备:确定采用的激光钻孔设备,并进行设备的调试和检查,确保设备能够正常工作。
3. 材料准备:准备待加工的电路板材料,确保电路板表面平整、清洁,并放置在设备工作台上。
4. 参数设置:根据设计要求和实际情况,设置激光钻孔设备的加工参数,包括激光功率、激光脉冲频率、加工速度等。
5. 对准定位:利用设备上的光学对准系统,将激光束精确对准待加工的位置,并调整好加工头的位置。
6. 开始加工:启动设备,让激光束按照设定的参数和位置进行钻孔加工,通过在电路板材料上聚焦高能量的激光束来熔化和蒸发材料,形成孔洞。
7. 检验质量:完成钻孔后,对加工得到的孔洞进行检查和测试,确保孔洞尺寸和位置精确符合设计要求。
8. 清洗处理:清洁电路板表面和孔洞,去除激光加工时留下的残留物和污垢,保证电路板的表面质量。
9. 检验验证:经过清洗处理后,再次对孔洞进行检验和验证,确保整个加工过程
完成并且符合质量要求。
10. 完成:当电路板上所有需要的孔洞都完成加工后,整个镭射钻孔流程就完成了。
电路板镭射钻孔技术具有高加工精度、加工效率高、操作简便、适应性强等优点,被广泛应用于电子产品的生产制造过程中。
随着激光技术的不断发展和完善,电路板镭射钻孔技术也将会得到进一步提升和发展,为电路板制造业带来更多的发展机遇和挑战。
印制电路板成孔技术
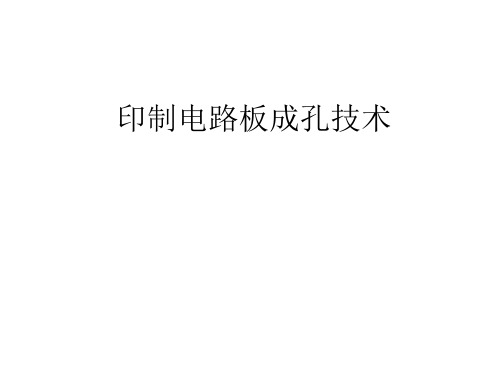
1.1.1钻头
1.1.1.6研磨次数的区分:采用色标法。通常做法是在钻头柄 部着色以区分钻头的研磨次数。
1.1.2套环
1.1.2.1套环的意义:
1.1.2套环
1.1.2.1套环安装示意:
总长:38.1mm 环位:20.32+/-0.1mm 环内径:3.0mm 环外径:7.45mm 环高:4.5mm
1.5质量要求
1.5.1钻孔常规检验工具及设备:
1.5质量要求
1.5.2钻孔缺陷允收标准:
1.5质量要求
1.5.3钻孔主要缺陷评价: 1)孔位置精度评价
1.5质量要求
1.5.3钻孔主要缺陷评价: 2)孔内壁粗糙度评价: a.经孔内电镀铜后再进行显微剖切观察,测量内壁 面基准与凹谷间距离; b.基板重叠加工时,测量全组基板; c.设定钻头的钻孔数,测定最终钻孔加工的孔; d.显微剖切的剖面尽量在孔的中心,剖切位置差异 会影响测量结果。
激光钻孔
2.3.2紫外激光钻孔技术:利用紫外激光的化学能 去破坏有机分子的分子键、金属晶体的金属键和无 机物的离子键,形成悬浮颗粒或原子团、分子团或 原子分子,在局部发生蓬松,配合真空吸力作用, 使小微粒极力从孔中逃逸或被强制吸走形成孔的过 程。成孔必要条件:激光光子能量>分子间键合力
激光钻孔
2.3.3 CO2和UV激光钻孔对比
激光钻孔
2.3.3 CO2和UV激光生产流程:
激光钻孔
2.4 质量要求:激光钻孔主要缺陷有偏孔、漏孔、 多孔、孔壁侧蚀、铜窗分层、孔形不正、玻纤突出、 底垫胶渣、孔底外缘微裂、底垫受损、底垫浮离等。 激光钻孔标准孔形示意图如下:孔形口稍大底略小 成锥状,孔壁光洁。常见的钻孔缺陷有孔形成腰鼓 状,孔壁有玻纤突出和树脂粘附底铜层等问题。
印制电路板激光微孔研究

第5卷 第3期 2007年6月光学与光电技术O PT ICS &OP T O EL ECT RO NI C T ECH N OL OG YVo l.5,No.3 June,2007收稿日期 2006-10-12; 收到修改稿日期 2007-03-06作者简介 颜庙青(1982-),男,硕士,主要从事脉冲激光精细加工方面的研究。
E -mail:zhuhh@文章编号:1672-3392(2007)03-0037-04印制电路板激光微孔研究颜庙青 朱海红 程祖海(华中科技大学武汉光电国家实验室(筹)激光科学与技术研究部,光电子科学与工程学院,武汉430074)摘要 激光微孔技术是当今印制电路板向高密度互连技术发展的关键,采用U VYAG 、RF CO 2和TEA CO 2三种激光器在FR -4基板上作微打孔工艺研究,得到了激光波长、脉冲宽度、脉冲能量和光学系统构成等一系列参数对微孔孔径和质量的影响及规律。
研究结果表明,波长短及脉宽窄的激光脉冲、合适的扩束装置及透镜焦距能有效地减小微孔孔径和提高孔的质量。
此外,通过设计光学系统,还用自行研制的T EA CO 2激光器成功打出了孔径在150L m 以内的微孔。
关键词 印刷电路板;激光微孔;工艺研究;机理中图分类号 TN249 文献标识码 A1 引 言近年来,随着整机电子产品的不断小型化、高速化和多功能化,搭载器件的印刷电路板(Printed Circuit Board,PCB)正向着细线化和高密度互连的方向发展。
微孔技术是实现PCB 板多层高密度互连的关键技术之一。
激光钻孔是目前PCB 微孔市场上的主流钻孔技术,这种方法高速、精确、成本低,适用于任何层数和材料的PCB 。
常用的激光微打孔系统所采用的激光能源主要有三种:横向激励大气(T ransv er se E lec -tric Atm ospheric,T EA )C O 2、射频(Radio -Fre -quency,RF )CO 2和紫外固体(U ltraviolet,UV )YA G 。
PCB生产机械加工及激光钻孔工艺基础

PCB生产机械加工及激光钻孔工艺基础概述:PCB是电子产品中不可缺少的一个组成部分,它起着支持和连接电子元器件的重要作用。
PCB生产过程中的机械加工和激光钻孔工艺是制造高质量PCB的关键环节。
本文将介绍PCB生产机械加工及激光钻孔工艺的基础知识。
一、机械加工工艺:1.切割切割是将大尺寸的PCB板材切割成所需尺寸的小块板材的过程。
常见的切割方法有机械切割和电子切割两种。
机械切割使用刀具来切割板材,电子切割则使用切割机械和电磁场等技术。
2.开槽开槽是制造PCB板材成形的工艺,主要是用于制造中低压电器线路板。
开槽通常使用弧形切割器具来切割板材,以方便电路板在成形过程中的弯曲及折叠。
3.钻孔钻孔是为了将电子元器件的引脚连接至电路板上的导线孔。
常见的钻孔方式有机械钻孔和激光钻孔两种。
机械钻孔使用钻头来加工孔位,激光钻孔则利用激光束直接在板材上打孔。
4.铣削铣削是用来对电路板的表面和内部进行加工的工艺。
它主要用于去除多余的铜箔和增加元器件的焊盘等。
铣削使用铣刀进行加工,通过控制铣削工具的位置和旋转方向来实现所需的加工效果。
二、激光钻孔工艺:激光钻孔是一种高精度、高效率的钻孔方式,它广泛应用于PCB生产中。
激光钻孔工艺主要包括以下几个步骤:1.板材预处理激光钻孔前需要对板材进行预处理,包括表面清洁和涂覆保护层等。
这样可以提高激光钻孔的精度和效果。
2.控制系统设置激光钻孔需要通过控制系统进行编程设置,包括设置孔位的坐标、孔径和孔深等参数。
3.激光钻孔通过激光装置向板材上的孔位照射高能激光束,使板材熔化后挥发,形成孔位。
4.孔位清理清理钻孔后的板材,除去多余的残渣和灰尘。
这一步骤非常重要,可以确保孔位的质量和稳定性。
总结:PCB生产中的机械加工和激光钻孔工艺是制造高质量电路板的重要环节。
机械加工包括切割、开槽、钻孔和铣削等工艺,通过使用相应的设备和工具来实现。
激光钻孔作为一种高精度、高效率的钻孔方式,广泛应用于PCB生产中。
紫外线激光器在印制电路板钻孔中的应用

紫外线激光器在印制电路板钻孔中的应用紫外线激光器在印制电路板钻孔中的应用当前用于制作印制电路板微通孔的激光器有四种类型:CO 2 激光器、YAG激光器、准分子激光器和铜蒸气激光器。
CO2激光器典型地用于生产大约75μm的孔,但是由于光束会从铜面上反射回来,所以它仅仅适合于除去电介质。
CO2激光器非常稳定、便宜,且不需维护。
准分子激光器是生产高质量、小直径孔的最佳选择,典型的孔径值为小于10μm。
这些类型最适合用于微型球栅阵列封装(microBGA)设备中聚酷亚胶基板的高密度阵列钻孔。
铜蒸气激光器的发展尚在初期,然而在需要高生产率时仍具有优势。
铜蒸气激光器能除去电介质和铜,然而在生产过程中会带来严重问题,会使得气流只能在受限的环境中生产产品。
在印制电路板工业中应用最普遍的激光器是调QNd: YAG 激光器,其波长为355nm,在紫外线范围内。
这个波长可以在印制电路板钻孔时使大多数金属(Gu , Ni , Au , Ag) 融化,其吸收率超过50% (Meier和Schmidt , 2002) ,有机材料也能被融化。
紫外线激光的光子能量可高达3.5 -7.5eV,在融化过程中能够使化学键断裂,部分通过紫外线激光的光化学作用,部分通过光热作用。
这些性能使紫外线激光成为印制电路板工业应用的首选。
YAG 激光系统有一个激光源,提供的能量密度(流量)超过4J/cm 2 ,这个能量密度是钻开微通孔表面铜循所必需的。
有机材料的融化过程需要的能量密度大约只有100mJ/cm 2 ,例如环氧树脂和聚酷亚肢。
为了在这样宽的频谱范围正确操作,需要非常准确和精密的控制激光能量。
微通孔的钻孔过程需要两步,第一步用高能量密度激光打开铜箔,第二步用低能量密度激光除去电介质。
激光的波长为355nm 时,其典型的光点直径大约为20μm 。
在脉冲时间小于140ns 时,激光的频率在10 - 50kHz之间,这时的材料是不会产生热量的。
激光在印制电路板制造中应用的新进展

单 孔 逐 次 加 工 ,在 加 工 效 率 方 面 大 大 落 后 于 C O 激
光 钻 孔 ,一 般 CO, 光 钻 孔 的速 率 是 uV激 光 的4 5 激  ̄ 倍 [ 】 。同 时uV激 光 钻 孔 由于 可 以实 现 对 铜 和 介 质 基 材 的一 次 性 去 除 而不 需要 对 铜 面进 行 特 殊 处 理 , 因 此 在盲 孑 制 作 时 需要 钻 孔 参 数 的 精 确控 制 ,否 则 L 容 易 出现 盲 孔被 打 穿现 象 。 1 9 年 欧 文 等 人 发 现 94 在uv 激 光烧 蚀铜 时 , 由于铜 材对uV AG激光 的高 Y
余 介质层 并清 除孔 内残渣 ,第 三步利 用频 率非 常低 且 不伤害 底层 铜 的激光执 行L S 程 ,实现 了 非传统 工 A过
序 厚径 比11 :的盲T N作 ( 图2 。采 用L 机 制 进 L 如 ) AS
1. 4.
以波 大 于7 0n 6 m的 红外 光 将 有机 板 材 予 以 强热 熔 化
随着 新 型 高 敏 感干 膜材 料 等 研 发 的 不 断 成 熟 ,必 将 成 为 以后 微 影 制 程 技 术 的主 流 。 当前 和 今 后 的 一段 时 间里 ,要解 决P B中 “ 高密 度 ”导线 的精细 度 、 C 甚 位 置度和 层 间对位 问题 ,必 离不 开L I 术[。 D 技 4 】
一
[] 2 林金 堵 . 光 直接成 像 技术 ( I J. 激 V )[ 印制 电路信 1
息 , 0 23 2 0 ,.
[] 困龙 , 迪. 内激光 直接 成像 ( D )技术 发展 3张 马 国 LI
线路板激光阶数

线路板激光阶数线路板激光钻孔技术是一种高效、精确的制造技术,被广泛应用于电子产品制造行业。
该技术经过多年的发展和改进,已经达到了非常成熟的阶段。
本文将从激光钻孔的原理、应用领域、优点和发展趋势等方面进行全面介绍,旨在为相关从业人员提供指导意义的知识。
首先,我们来介绍一下线路板激光钻孔的原理。
激光钻孔就是利用激光束对线路板上的材料进行高能量的照射,使其迅速升温并蒸发,从而形成钻孔。
由于激光束具有高能量密度、小焦点和高方向性等特点,因此可以实现精确而高效的钻孔过程。
线路板激光钻孔技术在电子产品制造领域有着广泛的应用。
首先,它可以用于制造多层线路板中的通孔。
多层线路板中的通孔需要穿透多层不同材料,传统的机械钻孔方式往往效率低且易损坏线路板。
而激光钻孔技术可以轻松穿透多层材料,丝毫不影响线路板的完整性。
其次,激光钻孔技术还可以用于制造盲孔和埋孔。
盲孔是指在线路板上只有一侧有孔通至内层的孔,而另一侧则不通。
而埋孔是在线路板上制造完整的孔,但不通至另一侧,这些特殊的设计可以提高线路板的布线自由度,使得电子产品的设计更加紧凑和高效。
线路板激光钻孔技术相较于传统的机械钻孔方式具有很多优点。
首先,激光钻孔可以实现无接触、非机械化的加工过程,因此不会对线路板表面造成任何损伤和污染,大大提高了线路板的质量和可靠性。
其次,激光钻孔技术可以实现非常小尺寸的孔径,最小可达到几十微米,满足了现代电子产品对线路板尺寸的要求。
此外,激光钻孔技术还具有高加工速度、高精度和高重复性的特点,可以大大提高生产效率和产品一致性。
随着电子产品的不断发展和智能化需求的增长,线路板激光钻孔技术也在不断发展。
首先,随着激光技术的进步,激光钻孔设备的功率越来越高,可以更好地满足复杂线路板的需求。
其次,激光钻孔技术应用的材料范围也在不断扩大,不仅可以用于常见的FR-4基板,还可以用于高频、高速、高密度的特殊材料。
此外,激光钻孔技术还在不断提高加工效率和自动化水平,进一步降低制造成本和提高生产效率。
多阶pcb板的打孔方法

多阶pcb板的打孔方法
多层PCB板的打孔方法通常包括以下几种:
1. 机械打孔,这是最常见的方法。
通过CNC钻床或者冲床,将孔逐个打在PCB板上。
这种方法适用于一般的多层PCB板,但是对于孔径小于0.3mm的孔会比较困难。
2. 激光钻孔,激光钻孔是一种高精度的打孔方法,适用于孔径小而密集的PCB板。
激光钻孔的优点是可以实现非常小的孔径和高密度的布局,但是成本相对较高。
3. 钨钢模具冲孔,这种方法适用于大批量生产,通过模具冲压的方式一次性完成多层PCB板的打孔。
这种方法效率高,成本低,适合于一般要求不是特别高的PCB板。
4. 激光孔加工,激光孔加工是通过激光烧蚀的方式完成PCB板的打孔,适用于特殊材料或者特殊要求的PCB板。
这种方法的优点是可以实现非常小的孔径和复杂的孔型,但是成本较高。
总的来说,选择合适的打孔方法需要根据PCB板的具体要求来
决定,包括孔径大小、孔的密度、成本考量等因素。
同时,还需要考虑到生产效率、设备投资、工艺技术等方面的因素,综合考虑后选择最适合的打孔方法。
激光技术在印制电路板行业的应用

激光技术在印制电路板行业的应用宋金月摘要:激光直接成型(LDS)技术,指利用激光将数字化的图形照射到高分子材料表面,通过对照射过的区域进行直接金属化,最终在高分子材料表面形成图案的技术。
它可以在高分子壳体上直接形成金属化的图案。
本文详细探讨了LDS技术的原理、加工方法、应用方向、在印制电路板中的应用前景以及目前存在的应用缺陷。
关键词:激光技术;印制电路;应用引言:激光(Laser)是20世纪科技领域中与原子能、半导体及计算机齐名的4项重大发明之一。
50年来,激光技术发展异常迅猛。
以激光器为基础的激光技术在我国得到了迅速的发展,现已广泛用于工业生产、通信、信息处理、医疗卫生、军事、文化教育以及科学研究等各个领域。
随着电子产品朝着多功能、便携式、小型化的方向发展,对印制电路板高密度化和小型化提出了越来越高的需求。
提高印制板高密度化水平的关键在于越来越窄的线宽、线距和越来越小的层间互连孔直径、连接盘,以及严格的尺寸精度,于是激光技术被引入印制板加工中。
一、概述关于激光的起源,最早还要追溯到科学家爱因斯坦,爱因斯坦在上世纪初就提出了受激辐射的理念。
随后,上世纪中期,美国微波领域的著名科学家肖洛和汤斯发表了关于“红外与光学激射器”的论文,全文明确阐述了受激辐射发光的可能性,同时也阐述了受激辐射发光的条件――“粒子数反转”。
1960年,美国科学家梅曼成功发明了一台世界上最早的红宝石激光器。
至此,激光和激光技术开始了迅猛的发展。
而我国的第一台激光器是在王志江院士的主持之下于1961年成功制造出来的。
而关于我国的激光和激光技术起源,主要还是受到国外的影响。
但是激光技术自从在我国起源就得到了良好的发展,无论是发展成果的质量还是数量都与世界水平差异不大。
二、激光技术组成和特性(一)激光器的主要组成结构经过多年的发展和完善,激光器的主要结构已基本定型,主要由三个部分共同组成。
首先是激光工作介质,激光工作介质是激光器最为基础也是最为重要的组成部分,激光器要产生激光必须要选择恰当的工作介质,例如固体、液体、气体或者是半导体。
在PCB中充分利用基板的UV激光

PCB与基板的UV激光加工新工艺目前,UV 激光钻孔设备只占全球市场的15%,但该类设备市场需求的增长要比新型的CO2 激光钻孔设备的需求高3倍。
孔的直径甚至小于50阿,1〜2 的多层导通孔和较小的通孔也是当前竞争的焦点,UV 激光为当前的竞争提出了解决方案;除此之外,它还是一种用于精确地剥离阻焊膜以及生成精密的电路图形的工具。
本文概述了目前UV 激光钻孔和绘图系统的特性和柔性。
还给出了各种材料的不同类型导通孔的质量和产量结果以及在各种蚀刻阻膜上的绘图结果。
本文通过展望今后的发展,讨论了UV 激光的局限性。
本文还对UV 激光工具和CO2 激光工具进行了比较,阐明了二者在哪些方面是可以竞争的,在哪些方面是不可竞争的,以及在哪些方面二者可以综合应用作为互补的工具。
UV 与CO2 的对比UV 激光工具不仅与CO2 的波长不同,而且各自在加工材料,如象PCB 和基板,也是两种不同的工具。
光点尺寸小于10 倍,较短的脉冲宽度和极高频使得在一般的钻孔应用中不得不使用不同的操作方法,并且为不同的应用开辟了其它的窗口。
UV 在极小的脉冲宽度内具有高频和极大的峰值功率。
工作面上光点尺寸决定了能量密度。
CO2 能量密度达到50〜70J/cm2,而UV激光由于光点尺寸小得多,所以能量密度可达50~200J/cm2。
由于UV 光点尺寸比目标孔直径还要小,激光光束以一种所谓的套孔方式聚焦于孔的目标直径内。
对于UV 激光,钻一个完整的孔所需的脉冲数在30 到120 之间,而CO2 激光则只需2 到10 个脉冲。
UV 激光的频率要比CO2 的高 5 到15 倍。
在去除了顶部铜层后,可使用第二步,通过扩大的光点清理孔中的灰色区域。
当然还可使用UV 激光进行冲压,不过光点的大小决定了能量密度,且不同材料的烧蚀极限值决定了所需的最小能量密度。
这样根据不同材料的烧蚀极限就可导出UV 冲压方式使用和最大光点尺寸。
由于UV 激光所具有的能量,目前仅将冲压方式用于孔直径小于75im 、烧蚀极限极低的软材料如TCD,或用于小焊盘开口的阻焊膜烧蚀。
- 1、下载文档前请自行甄别文档内容的完整性,平台不提供额外的编辑、内容补充、找答案等附加服务。
- 2、"仅部分预览"的文档,不可在线预览部分如存在完整性等问题,可反馈申请退款(可完整预览的文档不适用该条件!)。
- 3、如文档侵犯您的权益,请联系客服反馈,我们会尽快为您处理(人工客服工作时间:9:00-18:30)。
一激光成孔的原理激光是当“射线”受到外来的刺激而增加能量下所激发的一种强力光束,其中红外光和可见光具有热能,紫外光另具有光学能。
此种类型的光射到工件的表面时会发生三种现象即反射、吸收和穿透。
图示:透过光学另件击打在基材上激光光点,其组成有多种模式,与被照点会产生三种反应。
激光钻孔的主要作用就是能够很快地除去所要加工的基板材料,它主要靠光热烧蚀和光化学烧蚀或称之谓切除。
(1)光热烧蚀:指被加工的材料吸收高能量的激光,在极短的时间加热到熔化并被蒸发掉的成孔原理。
此种工艺方法在基板材料受到高能量的作用下,在所形成的孔壁上有烧黑的炭化残渣,孔化前必须进行清理。
(2)光化学烧蚀:是指紫外线区所具有的高光子能量(超过2eV电子伏特)、激光波长超过400纳米的高能量光子起作用的结果。
而这种高能量的光子能破坏有机材料的长分子链,成为更小的微粒,而其能量大于原分子,极力从中逸出,在外力的掐吸情况之下,使基板材料被快速除去而形成微孔。
因此种类型的工艺方法,不含有热烧,也就不会产生炭化现象。
所以,孔化前清理就非常简单。
以上就是激光成孔的基本原理。
目前最常用的有两种激光钻孔方式:印制电路板钻孔用的激光器主要有RF激发的CO2气体激光器和UV固态Nd:YAG激光器。
(3)关于基板吸光度:激光成功率的高低与基板材料的吸光率有着直接的关系。
印制电路板是由铜箔与玻璃布和树脂组合而成,此三种材料的吸光度也因波长不同有所不同但其中铜箔与玻璃布在紫外光0.3mμ以下区域的吸收率较高,但进入可见光与IR后却大幅度滑落。
有机树脂材料则在三段光谱中,都能维持相当高的吸收率。
这就是树脂材料所具有的特性,是激光钻孔工艺流行的基础。
二CO2激光成孔的不同的工艺方法CO2激光成孔的钻孔方法主要有直接成孔法和敷形掩膜成孔法两种。
所谓直接成孔工艺方法就是把激光光束经设备主控系统将光束的直径调制到与被加工印制电路板上的孔直径相同,在没有铜箔的绝缘介质表面上直接进行成孔加工。
敷形掩膜工艺方法就是在印制板的表面涂覆一层专用的掩膜,采用常规的工艺方法经曝光/显影/蚀刻工艺去掉孔表面的铜箔面形成的敷形窗口。
然后采用大于孔径的激光束照射这些孔,切除暴露的介质层树脂。
现分别介绍如下:(1)开铜窗法:首先在内层板上复压一层RCC(涂树脂铜箔)通过光化学方法制成窗口,然后进行蚀刻露出树脂,再采用激光烧除窗口内基板材料即形成微盲孔:当光束经增强后通过光圈到达两组电流计式的微动反射扫描镜,并经一次垂直对正(Fθ透镜)而达到可进行激动的台面的管区,然后再逐一烧成微盲孔。
在一英寸见方的小管区内经电子快束这定位后,对0.15mm的盲孔可连打三枪成孔。
其中第一枪的脉冲宽度约为15μs,此时提供能量达到成孔的目的。
后再枪则利用来清理孔壁孔底的残渣和修正孔。
图示:激光能量控制良好的0.15mm微盲孔的SEM横断面及45度的全图,此种开窗口的成孔工艺方法,当底垫(靶标盘)不大时又需大排版或二阶盲孔时,其对准度就比较困难。
(2)开大窗口工艺方法:前一种工艺方法成孔的直径与所开的铜窗口相同,如果操作稍有不慎就会使所开窗口的位置产生偏差,导致成孔的盲孔位置走位致使与底垫中心失准的问题产生。
该铜窗口的偏差产生的原因有可能是基板材料涨缩和图像转移所采用的底片变形有关。
所以采取开大铜窗口的工艺方法,就是将铜窗口直径扩大到比底垫还大经0.05mm左右(通常按照孔径的大小来确定,当孔径为0.15mm时,底垫直径应在0.25mm左右,其大窗口直径为0.30mm)然后再进行激光钻孔,即可烧出位置精确对准底垫的微盲孔。
其主要特点是选择自由度大,进行激光钻孔时可选择另按内层底垫的程式去成孔。
这就有效的避免由于铜窗口直径与成孔直径相同时造成的偏位而使激光点无法对正窗口,使批量大的大拚板面上会出现许多不完整的半孔或残孔的现象。
(3)树脂表面直接成孔工艺方法采用激光成孔有几种类型的工艺方法进行激光钻孔:A.基板是采用在内层板上层压涂树脂铜箔,然后将铜箔全部蚀刻去掉,就可采用CO2激光在裸露的树脂表面直接成孔,再继续按照镀覆孔工艺方法进行孔化处理。
B.基板是采用FR-4半固化片和铜箔以代替涂树脂铜箔的相类似制作工艺方法。
C.涂布感光树脂后续层压铜箔的工艺方法制作。
D.采用干膜作介质层与铜箔的压贴工艺方法制作。
E.涂布其它类型的温膜与铜箔覆压的工艺方法来制作。
4)采用超薄铜箔的直接烧蚀的工艺方法内层芯板两面压贴涂树脂铜箔后,可采用“半蚀方法”将铜箔厚度17m经蚀刻后减薄到5微米,然后进行黑氧化处理,就可采用CO2激光成孔。
其基本原理就是经氧化处理成黑的表面会强烈吸光,就会在提高CO2激光的光束能量的前提下,就可以直接在超薄铜箔与树脂表面成孔。
但最困难的就是如何确保“半蚀方法”能否获得厚度均匀一致的铜层,所以制作起来要特别注视。
当然可采用背铜式可撕性材料(UTC),铜箔相当簿约5微米。
根据这种类型的板加工,目前在工艺上主要采取以下几个方面:这主要对材料供应商提出严格的质量和技术指标,要确保介质层的厚度的差异在5—10μm之间。
因为只有确保涂树脂铜箔基材的介质厚度的均匀性,在同样的激光能量的作用下,才能确保孔型的准确性和孔底部的干净。
同时还需要在后续工序中,采用最佳的除钻污工艺条件,确保激光成孔后盲孔底部的干净无残留物。
对盲孔化学镀和电镀层的质量会产生良好的作用。
三Nd:YAG激光钻孔工艺方法Nd:YAG是钕和钇铝柘榴石。
两种固态晶体共同激发出的UV激光。
最近多采用的二极管脉冲激励的激光束,它可以制成有效的激光密封系统,不需要水冷。
这种激光三次谐波波长为355纳米(nm)、四次谐波波长为266纳米(nm),波长是由光学晶体调制的。
这种类型的激光钻孔的最大特点是属于紫外光(UV)谱区,而覆铜箔层压板所组成的铜箔与玻璃纤维在紫外光区域内吸光度很强,加上此类激光的光点小能量大,故能强力的穿透铜箔与玻璃布而直接成孔。
由于上种类型的激光热量较小,不会象CO2激光钻孔后生成炭渣,对孔壁后续工序提供了很好的处理表面。
Nd:YAG激光技术在很多种材料上进行徽盲孔与通孔的加工。
其中在聚酰亚胺覆铜箔层压板上钻导通孔,最小孔径是25微米。
从制作成本分析,最经济的所采用的直径是25—125微米。
钻孔速度为10000孔/分。
可采用直接激光冲孔工艺方法,孔径最大50微米。
其成型的孔内表干净无碳化,很容易进行电镀。
同样也可在聚四氟乙烯覆铜箔层压板钻导通孔,最小孔径为25微米,最经济的所采用的直径为25—125微米。
钻孔速度为4500孔/分。
不需预蚀刻出窗口。
所成孔很干净,不需要附加特别的处理工艺要求。
还有其它材料成型孔加工等。
具体加工中可采用以下几种工艺方法:(1)根据两类激光钻孔的速度采取两种并用的工艺方法基本作业方法就是先用YAG把孔位上表面的铜箔烧蚀,然后再采用速度比YAG钻孔快的CO2激光直接烧蚀树脂后成孔。
四实际生产中产生的质量问题激光钻孔过程中,产生的质量问题比较多,不准备全面讲述,只将最易出现的质量问题提出供同行参考。
(1)开铜窗法的CO2激光钻孔位置与底靶标位置之间失准在激光钻孔中,光束定位系统对于孔径成型的准确性极关重要。
尽管采用光束定位系统的精确定位,但由于其它因素的影响往往会产生孔形变形的缺焰。
生产过程中产生的质量问题,其原因分析如下:1.制作内层芯板焊盘与导线图形的底片,与涂树脂铜箔(RCC)增层后开窗口用的底片,由于两者都会因为湿度与温度的影响尺寸增大与缩小的潜在因素。
2.芯板制作导线焊盘图形时基材本身的尺寸的涨缩,以及高温压贴涂树脂铜箔(RCC)增层后,内外层基板材料又出现尺寸的涨缩因素存在所至。
3.蚀刻所开铜窗口尺寸大小与位置也都会产生误差。
4.激光机本身的光点与台面位移之间的所造成的误差。
5.二阶盲孔对准度难度就更大,更易引起位置误差。
根据上述原因分析,根据生产所掌握的有关技术资料与实际运作过程的经验,主要采取的工艺对策有以下几个方面:1.采取缩小排版尺寸,多数厂家制作多层板排版采取450×600或525×600(mm)。
但对于加工导线宽度为0.10mm与盲孔孔径为0.15mm的手机板,最好采用排版尺寸为350×450(mm)上限。
2.加大激光直径:目的就是增加对铜窗口被罩住的范围。
其具体的做法采取“光束直径=孔直径+90~100μm”。
能量密度不足时可多打一两枪加以解决。
3.采取开大铜窗口工艺方法:这时只是铜窗口尺寸变大而孔径却未改动,因此激光成孔的直径已不再完全由窗口位置来决定,使得孔位可直接根据芯板的上的底垫靶标位置去烧孔。
4.由光化学成像与蚀刻开窗口改成YAG激光开窗法:就是采用YAG激光光点按芯板的基准孔首先开窗口,然后再用CO2激光就其窗位去烧出孔来,解决成像所造成的误差。
5.积层两次再制作二阶微盲孔法:当芯板两面各积层一层涂树脂铜箔(RCC)后,若还需再积层一次RCC与制作出二阶盲孔(即积二)者,其“积二”的盲孔的对位,就必须按照瞄准“积一”去成孔。
而无法再利用芯板的原始靶标。
也就是当“积一”成孔与成垫时,其板边也会制作出靶标。
所以,“积二”的RCC压贴上后,即可通过X—射线机对“积一”上的靶标而另钻出“积二”的四个机械基准孔,然后再成孔成线,采取此法可使“积二”尽量对准“积一”。
2.孔型不正确根据多次生产经验积累,主要因为所采用的基材成型所存在的质量问题,其主要质量问题是涂树脂铜箔经压贴后介质层的厚度难免有差异,在相同钻孔的能量下,对介质层较薄的部分的底垫不但要承受较多的能量,也会反射较多的能量,因而将孔壁打成向外扩张的壶形。
这将对积层多层板层间的电气互连品质产生较大的影响。
由于孔型不正确,对积层多层印制电路板的高密度互连结构的可靠性会带来一系列的技术问题。
所以,必须采用工艺措施加以控制和解决。
主要采用以下几种工艺方法:(1)严格控制涂树脂铜箔压贴时介质层厚度差异在5—10μm之间。
(2)改变激光的能量密度与脉冲数(枪数),可通过试验方法找出批量生产的工艺条件。
(3)孔底胶渣与孔壁的破渣的清除不良这类质量问题最容易发生,这是由于稍为控制不当就会产生此种关型的问题。
特别是对于处理大拚版上多孔类型的积层板,不可能百分之百保证无质量问题。
这是因为所加工的大排板上的微盲孔数量太多(平均约6~9万个孔),介质层厚度不同,采取同一能量的激光钻孔时,底垫上所残留下的胶渣的厚薄也就不相同。
经除钻污处理就不可能确保全部残留物彻底干净,再加上检查手段比较差,一旦有缺陷时,常会造成后续镀铜层与底垫与孔壁的结合力。
本文出自: 深圳市通发激光设备有限公司,专业从事模具激光焊机的开发、销售与维护和模具激光焊技术的推广。
转载请注明出处,谢谢!。