FMEA潜在失效模式及分析标准表格模版
潜在失效模式及后果分析FMEA新版表格2020.10.9

第2步 结构分析
第3步 功能分析
1.上一较高级别 2.关注要素
3.低一较低级别或 特性类型
1.上一较高 级别功能及
要求
2.关注要素功 能及要求
3.下一较低级别 功能及要求或特
性
AIAG - VDA DFMEA
项目: DFMEA开始时间: DFMEA修订日期: 多功能组:
FC的频度 (O)
针对FC或FM的 当前探测控制
DC
FC/FM 探测度
(D)
设计 FMEA措 标识(选 预防 施优先级 填) 措施
AP
探测 措施
责任人
计划完成 时间
第6步 改进措施
第6步 改进措施
状态:
采取基于证 据的措施
实际 完成 时间
S
O
D AP
第7步 结果文件化
第4步
失效分析
风
1.对于上一较高级 别要素和/或最终 用户的失效影响 (即:失效影响)
FE
FE的严重度 (S)
2.关注要ቤተ መጻሕፍቲ ባይዱ的失效模式 (即:失效模式) FM
3.下一较低级别要素 或特性的失效起因 (即:失效起因)
FC
对FC的当前 预防控制 PC
VDA DFMEA
第5步 风险分析
DFMEA ID 编号: 设计责任: 保密级别:
FMEA手册第五版工具书上的标准范本(PFMEA)
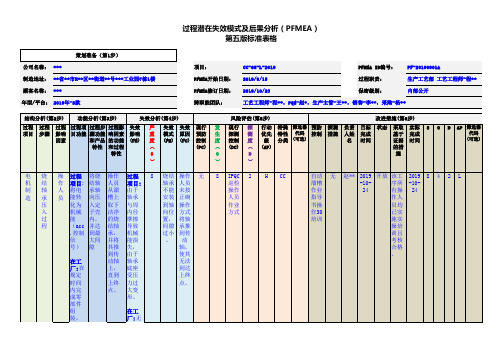
PFMEA ID编号: PF-20190901A
2019/9/15
过程职责:
生产工艺部 工艺工程师-程**
2019/10/23
保密级别:
内部公开
工艺工程师-程**,PQE-赵*,生产主管-王**,销售-李**,采购-杨**
结构分析(第2步) 功能分析(第3步)
失效分析(第4步)
风险评估(第5步)
改进措施(第6步)
过程 过程 过程 过程项 过程步 过程影 失效 严 失效 失效 现行 发 现行 探 行动 特殊 筛选器 预防 探测 负责 目标 状态 采取 实际 S O D AP 筛选器
项目 步骤 影响 目功能 骤功能 响因素 影响 重 模式 原因 预防 生 探测 测 优先 特性 代码 控制 措施 人姓 完成
因素
和产品 的功能 (FE) 度 (FM) (FC) 控制 度 控制 度 级 分类 (可选)
名 时间
基于 完成 证据 时间
代码 (可选)
特性 和过程
(PC)
(DC)
(AP)
的措
特性
S
O
D
过程 将烧 操作 过程 8 烧结 操作 无
机 结 作 项目: 结轴 人员 项目:
轴承 人员
制 轴 人 将电 承轴 从溜 由于
不能 未按
造 承 员 能转 向压 槽上 轴承
安装 正确
压 返工
无
前设
入
备停
设 工厂
最终
止运
备 流转:
用户:
行
) 将电
车窗
(力
机安
玻璃
太
装在
上升
小)
车门
、下
上,
降困
安装
FMEA第三版标准表格
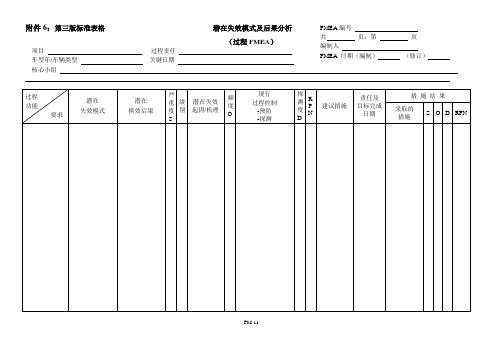
潜在失效起因/机理
频度O
现行过程控制预防
现行过程控制探测
探测度D
R
P
N
建议措施
责任及
目标完成日期
措施结果
采取的措施
S
O
D
RPN
车门内部人工涂蜡
为覆盖车门内侧,车门下层表面涂以最小厚度的蜡,以延缓腐蚀
规定表面涂蜡不足
车门寿命下降导致:
由于漆面经过长时间后生锈,使顾客对外观不满意
车门内附件功能下降
7
附件6:第三版标准表格潜在失效模式及后果分析
(过程FMEA)
项目过程责任
车型年/车辆类型关键日期
核心小组
过程
功能
要求
潜在
失效模式
潜在
换效后果
严重度S
级别
潜在失效起因/机理
频度O
现行
过程控制
-预防
-探测
探测度D
RPN
建议措施
责任及
目标完成日期
措施结果
采取的
措施
S
O
D
RPN
附件6 (续) 潜在失效模式及后果分析
7
车门内板保护蜡上边缘规定得太低
6
整车耐久性试验
T-118
T-109
T-301
7
294
增加实验室强化腐蚀试验
泰特-车身工程师
8X 09 30
根据试验结果(1481号试验),上边缘规范增加125mm
7
2
2
28
7
蜡层厚度规定不足
4
整车耐久性试验
同上
7
196
增加实验室强化腐蚀试验
对蜡层厚度进行实验设计(DOE)
标签及铭板 FMEA潜在失效模式及分析
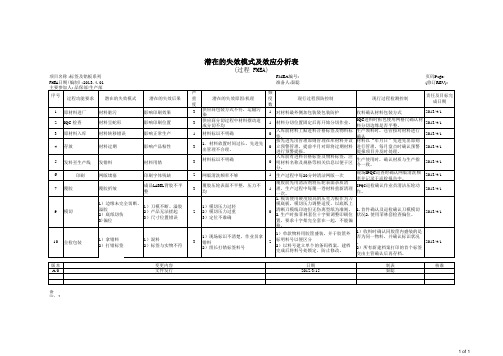
9
模切
1)边缘未完全切断、 1)刀模不断、溢胶 溢胶 2)产品无法搓起 2)底纸切伤 3)尺寸位置错误 3)偏位
2
0
10
全检包装
1)拿错料 2)打错标签
偏小
1)混料 2)标签与实物不符
3
1)现场标识不清楚,作业员拿 错料 2)组长打错标签料号
2
IQC进料时拆包使用网格尺确认材 2013-4-1 料分切边缘是否平整。 入库前材料上贴进料合格标签及物料标 生产领料时,仓管按对材料进行 2013-4-1 签。 确认 按先进先出管理原则管理在库材料并设 材料以“年月日”先进先出原则 立预警管理,提前半月对即将过期材料 进行管理,每月盘点时确认预警 2013-4-1 进行预警提报。 提报项目并及时处理。 入库前有进料合格标签及物料标签,注 生产使用时,确认材质与生产指 2013-4-1 明材料名称及规格等相关信息以便于区 令一致。 分。 现场IPQC巡查时确认网版清洗频 2013-4-1 生产过程中每20分钟清洁网版一次 率并记录于巡检报告中。 覆胶前先用清洁剂将压轮表面杂质清 IPQC巡检确认作业员清洁压轮动 2013-4-1 理,生产过程中每覆一卷材料重新清理 作。 一次。 1.模切使用硬度较高的压克力板作为刀 模底板,模切压力调整适度,以底纸上 清晰刀模线印迹但无伤离型纸为准则。 1.首件确认及巡检确认刀模模切 2013-4-1 2.生产时按菲林套位十字架调整印刷位 状况2.使用菲林套检查偏位。 置,要求十字架完全套在一起,不能偏 移。 1)收料时确认同胶筐内盛装的是 1)单款物料用胶筐盛装,并于胶筐外标 否为同一物料,并确认标识状况 明料号以便区分 2013-4-1 。 2)以料号建立单个的条码档案,建档完 2)所有新建档案打印的首个标签 成后将料号处锁定,防止修改。 交由主管确认后再存档。 日期 2012-3-15 制表 秦聪 核准
FMEA过程潜在失效模式及后果分析表

2
28 —— ——
3
每天检查
2
36
钳工修 模
——
2
项目 功能 潜在失效模式 模具失灵
潜在的失效后果
模具失灵,产品尺寸可能不合 格
严重 度 (S )
6
级别
潜在的失效起因/机 理
sc
设置错误
频度数 (O)
3
模具变形
产品变形,部份产品不合格, 顾客无法装配
8
设置错误
3
设备失灵
1
冲压方法不对,使模具使用寿
潜在的失效后果
严重
度 (S
级别
潜在的失效起因/机 理
)
频度数 (O)
设备失灵
1
产品尺寸超差
产品尺寸不标准,影响产品使 用性能
7
sc
设置错误
2
人为提前开模
2
设备失灵
3
模具失灵
模具失灵,产品尺寸可能不合 格
6
sc
设置错误
3
模具变形
产品变形,部份产品不合格, 顾客无法装配
8
设置错误
3
设备失灵
1
头部整 形
冲压方法
不放心
设置错误
2
人为拖延时间
1
现行过程控制
不易探 测度数 (D)
风险 顺序 数 RPN
建议的 措施
责任和 完成目
标
每班参数检查
2
28
——
处罚
5
35
——
设备失灵
1
产品尺寸超差
产品尺寸不标准,影响产品使 用性能
7
sc
设置错误
2
人为提前开模
2
过程潜在失效模式与效果分析表(PFMEA)
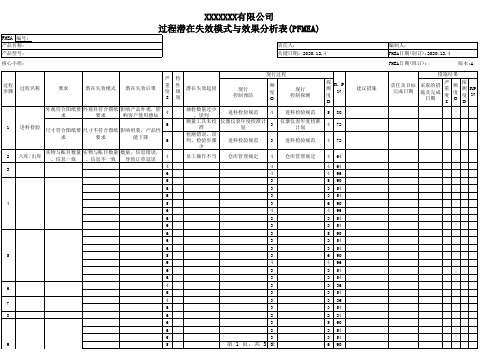
求
要求
响客户使用感知
4
1
进料检验 尺寸符合图纸要 尺寸不符合图纸 影响组装,产品性 6
求
要求
能下降
6
2
入库/出库
实物与账目数量 实物与账目数量 数量、信息错误, 、信息一致 、信息不一致 导致订单延误
4
抽检数量过少 、误判
进料检验规范
4
进料检验规范
5 80
测量工具未校 准
仪器仪表年度校准计 划
3
仪器仪表年度校准 计划
4 96
18
6
第 2 页,共 3 页4
4 96
18
6
4
4 96
5
4
4 80
19
5
4
4 80
6
3
4 72
6
4
4 96
20
6
4
4 96
6
4
4 96
21
4
4
5 80
4
4
4 64
22
4
4
5 80
23
4
4
4 64
备注:S、O、D评分标准详见《过程潜在失效模式后果分析PFMEA管理程序》,仅需对新部件进行评价分析,当RPN值超过200时要制定改善措施。
核准:
会签:
审查:
拟制:
表单 编 号:
第 3 页,共 3 页
6
4
4 96
6
3
3 54
6
3
3 54
6
3
5 90
6
3
3 54
6
3
3 54
13
5
3
FMEA潜在失效模式及分析标准表格模版
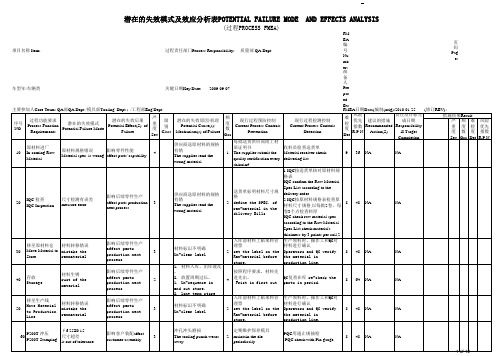
FMEA 编号Number:页码Page:准备人Prepared By:潜在的失效模式及效应分析表POTENTIAL FAILURE MODE AND EFFECTS ANALYSIS(过程PROCESS FMEA)过程责任部门Process Responsibility: 质量部 QA Dept.项目名称 Item: 关键日期Key Date: 2009.09.07车型年/车辆类工FMEA 编号Number:页码Page:准备人Prepared By:潜在的失效模式及效应分析表POTENTIAL FAILURE MODE AND EFFECTS ANALYSIS(过程PROCESS FMEA)过程责任部门Process Responsibility: 质量部 QA Dept.项目名称 Item: 关键日期Key Date: 2009.09.07车型年/车辆类工FMEA 编号Number:页码Page:准备人Prepared By:潜在的失效模式及效应分析表POTENTIAL FAILURE MODE AND EFFECTS ANALYSIS(过程PROCESS FMEA)过程责任部门Process Responsibility: 质量部 QA Dept.项目名称 Item: 关键日期Key Date: 2009.09.07车型年/车辆类工FMEA 编号Number:页码Page:准备人Prepared By:潜在的失效模式及效应分析表POTENTIAL FAILURE MODE AND EFFECTS ANALYSIS(过程PROCESS FMEA)过程责任部门Process Responsibility: 质量部 QA Dept.项目名称 Item: 关键日期Key Date: 2009.09.07车型年/车辆类工FMEA 编号Number:页码Page:准备人Prepared By:潜在的失效模式及效应分析表POTENTIAL FAILURE MODE AND EFFECTS ANALYSIS(过程PROCESS FMEA)过程责任部门Process Responsibility: 质量部 QA Dept.项目名称 Item: 关键日期Key Date: 2009.09.07车型年/车辆类工machiningFMEA 编号Number:页码Page:准备人Prepared By:潜在的失效模式及效应分析表POTENTIAL FAILURE MODE AND EFFECTS ANALYSIS(过程PROCESS FMEA)过程责任部门Process Responsibility: 质量部 QA Dept.项目名称 Item: 关键日期Key Date: 2009.09.07车型年/车辆类工FMEA 编号Number:页码Page:准备人Prepared By:潜在的失效模式及效应分析表POTENTIAL FAILURE MODE AND EFFECTS ANALYSIS(过程PROCESS FMEA)过程责任部门Process Responsibility: 质量部 QA Dept.项目名称 Item: 关键日期Key Date: 2009.09.07车型年/车辆类工FMEA 编号Number:页码Page:准备人Prepared By:潜在的失效模式及效应分析表POTENTIAL FAILURE MODE AND EFFECTS ANALYSIS(过程PROCESS FMEA)过程责任部门Process Responsibility: 质量部 QA Dept.项目名称 Item: 关键日期Key Date: 2009.09.07车型年/车辆类工FMEA 编号Number:页码Page:准备人Prepared By:潜在的失效模式及效应分析表POTENTIAL FAILURE MODE AND EFFECTS ANALYSIS(过程PROCESS FMEA)过程责任部门Process Responsibility: 质量部 QA Dept.项目名称 Item: 关键日期Key Date: 2009.09.07车型年/车辆类工FMEA 编号Number:页码Page:准备人Prepared By:潜在的失效模式及效应分析表POTENTIAL FAILURE MODE AND EFFECTS ANALYSIS(过程PROCESS FMEA)过程责任部门Process Responsibility: 质量部 QA Dept.项目名称 Item: 关键日期Key Date: 2009.09.07车型年/车辆类工。
潜在失效模式(FMEA)表格
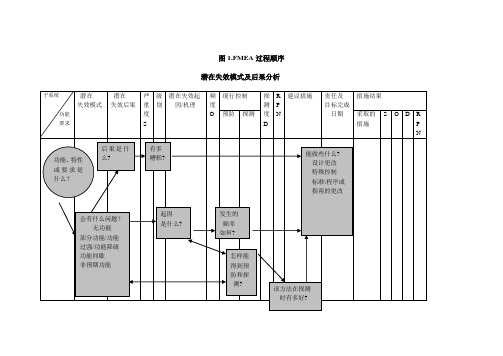
车门寿命降 低,导致: ·因漆面长期 生锈,使顾 客对外观不满 ·使车门内附 件功能降低 7 7 蜡的西文规定得 不当 混入的空气静止 蜡进入边角部分 5 2 理化实验室实验报告 No。1265 用非功能喷头进 行设计辅助调查 8 280 利用正式生产喷 蜡设备和规定的 蜡,增加小组评 价 7 ;车门板之间窨不 够,容不下喷头 喷头可进入情况 的图纸评价 4 112 利用辅助设计模 型和喷头,增加 小组评价 车身工程部和总装 厂 8X 11 15 评价表明入口是充分的 7 1 1 7 车身工程部和总装 厂 8X 11 15 根据试验,在有关区域增设 3 个通气孔 7 1 3 2 1 2 28 7 蜡层厚度规定不 足 4
频 度 O
6
◄⒂ 现行设 计控制 预防 ⒃
⒄► 现行设计控制 探测 ⒃
整车耐久性试验 T-188 T-109 T-301 整车耐久性试验 同上
探 测 度 D
7
措施结果确良 R P N
294
◄⒅ 建议措施 ⒆
增加实验室强化 腐蚀试验
责任及目标完成 日期 ⒇
泰特-车身工程师 8X 09 30
采取的措施 (21)
7
2
2
8
示例
项目
⑨
功能
左前车门 H8HX-000 0-A ·上、下车 · 保护乘员免受天气、 噪声侧碰撞的影响 车门附件视镜、 门锁、 门铰链及门窗升降器 等的固定支撑 ·为外观项目提供适 当的表面 ·喷漆和软内饰
潜在 失效后果 ⑩
车门内板 下部腐蚀
严 重 级 度 别 S
7
◄⒀ 潜在失效起因 /机理 ⒁
车门内板保护蜡 上边缘规定得太 低
有多 糟糕?
能做些什么? 设计更改 特殊控制 标准\程序或 指南的更改
DFMEA潜在失效模式及分析标准表格模版
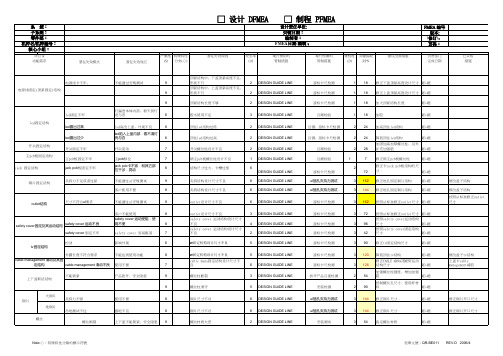
FMEA日期(编制):
潜在失效原因
发生率 (O)
现行预防的 管制措施
现行检测的 管制措施
难检度 关键指数
(D)
RPN
建议改善措施
FMEA 编号 版本:
(修订): 页码:
负责部门 完成日期
switch
主体线路
失去开通﹐关闭电源作用 不能使用﹐安全隐患
9
breaker
修正铜片开口尺寸 修正铜片开口尺寸
Note:◇:特殊特性分類的標示符號
表單文號:QR-BE011 REV.D 2006/4
系 统: 子系统: 零件部: 机种名/机种编号: 核心小组:
项目 & 功能需求
潜在失效模式
潜在失效效应
严重度 特殊特性 (S) 分类(◇)
□ 设计 DFMEA
□ 制程 PFMEA
系 统: 子系统: 零件部: 机种名/机种编号: 核心小组:
项目 & 功能需求
潜在失效模式
潜在失效效应
严重度 特殊特性 (S) 分类(◇)
□ 设计 DFMEA
□ 制程 PFMEA
设计责任单位: 关键日期: 编制者:
FMEA日期(编制):
潜在失效原因
发生率 (O)
现行预防的 管制措施
现行检测的 管制措施
DESIGN GUIDE LINE 6 DESIGN GUIDE LINE 6 DESIGN GUIDE LINE
outlet设计尺寸不良
6 DESIGN GUIDE LINE
outlet设计尺寸不良 safety cover 运动结构设计尺寸 不良 safety cover 运动结构设计尺寸 不良
FMEA失效模式及后果分析的评分标准
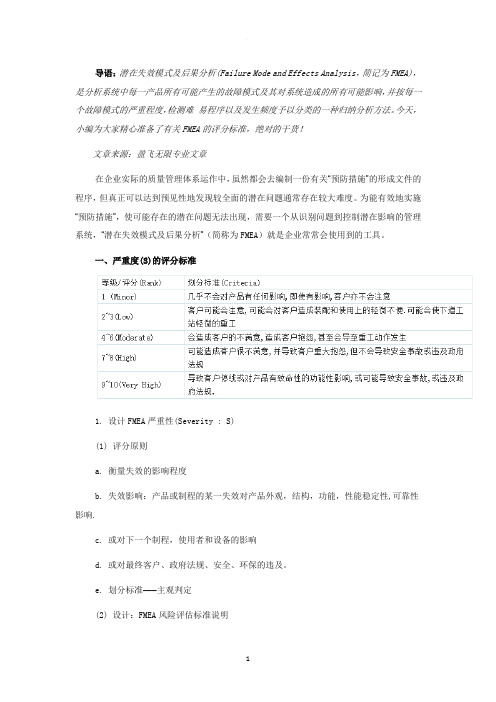
导语:潜在失效模式及后果分析(Failure Mode and Effects Analysis,简记为FMEA),是分析系统中每一产品所有可能产生的故障模式及其对系统造成的所有可能影响,并按每一个故障模式的严重程度,检测难易程序以及发生频度予以分类的一种归纳分析方法。
今天,小编为大家精心准备了有关FMEA的评分标准,绝对的干货!文章来源:盈飞无限专业文章在企业实际的质量管理体系运作中,虽然都会去编制一份有关“预防措施”的形成文件的程序,但真正可以达到预见性地发现较全面的潜在问题通常存在较大难度。
为能有效地实施“预防措施”,使可能存在的潜在问题无法出现,需要一个从识别问题到控制潜在影响的管理系统,“潜在失效模式及后果分析”(简称为FMEA)就是企业常常会使用到的工具。
一、严重度(S)的评分标准1. 设计FMEA严重性(Severity : S)(1) 评分原则a. 衡量失效的影响程度b. 失效影响:产品或制程的某一失效对产品外观,结构,功能,性能稳定性,可靠性影响.c. 或对下一个制程,使用者和设备的影响d. 或对最终客户、政府法规、安全、环保的违及。
e. 划分标准—–主观判定(2) 设计:FMEA风险评估标准说明严重性(Severity) (S):严重性是对下个零组件,次系统,系统或顾客所发生的潜在失效模式效果的严重性进行评估,严重性仅适用于效果,严重性等级指数的减低只能透过设计更改才能够生效,严重性应该在1至10的等级上估计。
2. 制程FMEA严重性(Severity : S)制程FMEA Failure mode engineering analysis失效模式分析风险评估标准说明:严重性(Severity)(S):对用户而言,严重性是对潜在失效模式效果(列在前面字段)的严重性评估,严重性仅适用于效果,如果受失效影响的顾客指的是组装厂或产品用户,那么评估严重性处在制程工程师或团队的经验(知识)领域以外,在这些情况下,设计FMEA,设计工程师,和(或)随后的制造或组装厂制程工程师应该被咨询,严重性应在1-10的等级上估计。
FMEA-失效模式与效应分析表

FMEA编号/FMEA NO.:12575490 项 目 名 称:排气管(左)
文件编号/FILE NO. :M10-001-1.0源自(PROCESS FMEA)
过程责任部门:M00 FMEA编制日期:2002.11/01 作成 核 准 Process Responsibility:M00 FMEA Date(orig.):2002.11.01 Prepared By Approval By Item:Manifold-lh 车型年/车辆类型:CAMI 关键日期:2003.06/04 FMEA修订日期:2003.8/30 WENWEI ZHU Model Year(s)/Vehicle(s):CAMI Key Date:2003.6.4 FMEA Date(rev.):2003.8/30 主要参加者:谢玮,洪容伟,尤洪,黄松,余肖汉,张闯,柴升军,汪东成,章勇军,苏显辉 Core Team: XIE WEI/HONG RONGWEI/YOU HONG/HUANG SONG/YU XIAOHAN/ZHANG CHUANG/CHAI SHENGJUN/WANG DONGCHENG/ZHANG YONGJUN/SU XIANHUI 措 施 结 果 过程功能 潜在的 潜在的 严重 级 潜在的失效 现行的 频 建议的 责任及目标 风险 不易 顺序 度 措施 完成日期 Action results Process 失效模式 失效后果 度数 别 起因/机理 工艺控制 探测 数 C r O Function Responsibility 采取的措施 度数 l Potential Cause(s) S R Potential c Potential Current Process Recommended & target R S O D a Dete Effect(s) of e Mechanism(s) of P Action 要求 c failure mode Controls Action(s) Completion P s c Failure Failure v N Taken u Requirements date N s OP05 滚珠试验 流道不畅 发动机烧毁 8 F00粗材不良 1 对粗材进行全检 5 40 Steel ball test Flow no Engine F00 Casting NG casting full check smooth burred OP10 铣面 Face milling 平面度0.04 超差 planeness 0.04 oversize 装配后漏气 leak after assembly 5 A 1.刀具磨耗超限 tool wear away too over 2.加工余量太大 Allowance too much 2 经M10试加工后设定刀具 寿命 set-up toolife by M10 after trying 2 余量及加工程式由M10设 定并经试加工确认 set-up allowance and make NC program by M10, checking on trying 粗材尺寸进料检查 check-in-come about the size of casting 3.夹持力太小 clamp power not enough 2 夹持力由生技试加工时确 定,作成作业标准 clamp pressure set up after trying by M10 and write in the instructor 4 24 4 40 4 40
FMEA失效模式及后果分析的评分标准
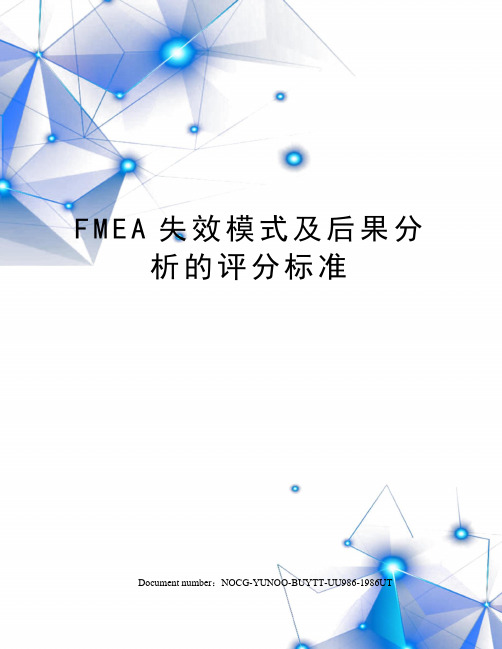
在企业实际的质量管理体系运作中,虽然都会去编制一份有关“预防措施”的形成文件的程序,但真正可以达到预见性地发现较全面的潜在问题通常存在较大难度。为能有效地实施“预防措施”,使可能存在的潜在问题无法出现,需要一个从识别问题到控制潜在影响的管理系统,“潜在失效模式及后果分析”(简称为FMEA)就是企业常常会使用到的工具。
FMEA失效模式及后果分析的评分标准
导语:潜在失效模式及后果分析(FailureModeandEffectsAnalysis,简记为FMEA),是分析系统中每一产品所有可能产生的故障模式及其对系统造成的所有可能影响,并按每一个故障模式的严重程度,检测难易程序以及发生频度予以分类的一种归纳分析方法。今天,小编为大家精心准备了有关FMEA的评分标准,绝对的干货!
一、严重度(S)的评分标准
1.设计FMEA严重性(Severity:S)
(1)评分原则
a.衡量失效的影响程度
b.失效影响:产品或制程的某一失效对产品外观,结构,功能,性能稳定性,可靠性影响.
c.或对下一个制程,使用者和设备的影响
d.或对最终客户、政府法规、安全、环保的违及。
e.划分标准—–主观判定
(2)设计:FMEA风险评估标准说明
风险评估标准说明:
严重性(Severity)(S):对用户而言,严重性是对潜在失效模式效果(列在前面字段)的严重性评估,严重性仅适用于效果,如果受失效影响的顾客指的是组装厂或产品用户,那么评估严重性处在制程工程师或团队的经验(知识)领域以外,在这些情况下,设计FMEA,设计工程师,和(或)随后的制造或组装厂制程工程师应该被咨询,严重性应在1-10的等级上估计。
三.难检度(D)的评分标准
1.设计FMEA侦测性:detection(D)
FMEA失效模式分析表

包装 包装
1.产品质量 1.客户抱怨 2、产品混入杂2、客户抱怨 物利器
3
1、 未按包装流程进 2 1. QC 抽检
行组装和包装
1 2、质检不到位
2 2.加强检验
3 18 7 14
1.严格按客人 14/10/30 和包装流程进 行组装和包装 2.员工自检和 14/10/30 品检全检相结 合的检验方式 彻底执行,保 证质量
14/10/30 14/10/30 14/10/30
1.IQC 加强检验 2.IQC 加强检验 3.IQC 加强检验
类别 项目 物料名称 制程 功能要求 潜在风险模式
潜在风险效应
印刷 织造
1. 操作不良 1. 客户抱怨 2. 外观不良 2. 客户抱怨 3. 危害健康 3. 危害员工身体
失效模式(潜在风险评估)效应分析表
2 机器危害危 2 机器设备影响身体 3 2 、操作不当,伤害员工 2 加强检验;
3 18 业,加强检验
害健康
健康,佩戴劳保用 3 身体;
2 2 岗位培训、警示3 27 2 采购加强对 14/10/30
品,
和劳保用品的佩
生产过程的控
戴;
制
1 按照流程作业,加 强检验; 2 采购加强控制 3、加强培训、警示和 劳保用品佩戴;
14/10/30
1 2 2. IQC 对照色样加强14/10/30
检验
1.IQC 根据作业流 程加强检验 2.IQC 根据作业流 程加强检验 3.IQC 和业务量产 排版前核对 4. 用栈板存放于室 内 1.保持此方法 2. IQC 对照色样加 强检验
1 1.IQC 检验
FMEA潜在失效模式及后果分析-含表单及评价标准(2015最新制定)

ZD-700-05版本:10QB文件代码/版本:QI-02-09-A/0潜在失效模式及后果分析2015年新制定编制:审核:批准:颁布日期:实施日期:潜在失效模式及后果分析文件会签/批准记录区分部门姓名签名日期拟制产品与技术中心审核产品与技术中心会签质量管理部批准副总经理1. 目的:1.1 认可并评价产品/过程中的潜在失效以及该失效的后果。
1.2 确定能否消除或减少潜在失效发生的机会并全部文件化。
2. 范围:在进行FMEA时有三种基本的情形,每一种都有不同的范围或关注焦点:2.1 对新设计、新技术或新过程,FMEA的范围是全部设计、技术或过程。
2.2 对现有设计或过程的修改(假设对现有设计或过程已有FMEA),FMEA的范围是对设计或过程的修改、由于修改可能产生手工艺相互影响以及现场的历史情况。
2.3 对现有的设计或过程用于新的环境、场所或应用(假设对现有设计或过程已有FMEA),FMEA的范围是新环境或场所对现有设计或过程的影响。
3. 职责:3.1 产品与技术中心:3.1.1 负责本程序的制定与维护。
3.1.2 负责承担组织FMEA制定的发起者、对FMEA潜在模式及后果分析进行管理。
3.1.3 负责对FMEA措施对策跟踪,以及组织小组人员对措施实施后风险顺序数评估。
3.2 FMEA小组组长:负责调动和协调所有有关方面代表的积极参与,组织小组成员制作FMEA。
3.3 FMEA小组:FMEA组长由产品开发项目负责人担任。
人员由产品开发、质量管理、承接制造的分厂、营运、销售、必要时客户代表、供应商代表等人员组成。
FMEA小组负责编制FMEA,并根据实际制造情况进行补充修订。
3.4 设计/过程FMEA的审核:由产品开发项目责任者负责;3.5 设计/过程FMEA的批准:由产品开发项目主管及产品与技术中心领导负责。
4. 定义:4.1 FMEA:潜在失效模式与后果分析。
4.2 设计FMEA:由负责设计的工程师/小组主要采用的一种分析技术,用以最大限度地保证各种潜在的失效模式及相关的起因/机理已得到充分的考虑和说明。
潜在失效模式及后果分析(过程FMEA)

潜在失效模式及后果分析(过程FMEA)FMEA过程FMEA标准表编制说明1FMEA编号填入FMEA文件编号,以便查询。
2项目注明正在进行过程分析的系统、子系统或部件的名称及编号。
3过程责任填入整车、部门和小组。
如已知,还应包括供方的名称。
4编制人填入负责编制FMEA的工程师的姓名、电话和所在公司的名称。
5车型年/车辆类型填入所分析的设计/过程将要应用和/或影响的车型年/车辆类型(如已知的话)。
6关键日期填入初次FMEA应完成的时间,该日期不应超过计划的投入生产日期。
7FMEA日期(编制)填入编制FMEA原始稿的日期及最新修订的日期。
8核心小组列出有权确定和/或执行任务的部门的名称和个人的姓名。
9过程功能/要求填入被分析过程或工序的简要说明(如车削、钻孔、功丝、焊接、装配等)。
——过程功能:列出与所分析的每一个过程步骤相或操作相对应的过程功能。
——要求:列出所分析的过程步骤/操作的每一个过程功能的要求。
10潜在失效模式所谓潜在失效模式是指过程有可能不能满足过程功能/要求栏中所描述的过程要求和/或设计意图。
11潜在失效后果失效的潜在后果是指失效模式对顾客产生的影响。
12严重度(S)严重度是一给定失效模式最严重的影响后果的级别。
严重度数值的降低只有通过设计更改才能够实现。
13级别本栏目可用于对那些可能需要附加的过程控制的部件、子系统或系统的特殊产品或过程特性的分级(如关键、主要、重要、重点)。
14潜在失效起因/机理所谓失效的潜在要因是指失效是怎样发生的,并应依据可以纠正或可以控制的原则予以描述。
15频度(O)频度是指某一特定的要因发生的可能性。
16现行过程控制现有的过程控制是对已经采用的防止失效模式或其要因发生的控制措施的现状说明。
有两类过程控制可以考虑:——预防:防止失效的要因或失效模式出现,或者降低其出现的几率;——探测:探测出失效的要因或者失效模式,导致采取纠正措施。
17探测度(D)探测度是与过程控制栏中所列的最佳探测控制相关联的定级数。
FMEA分析量化评定参照表(失效模式分析)
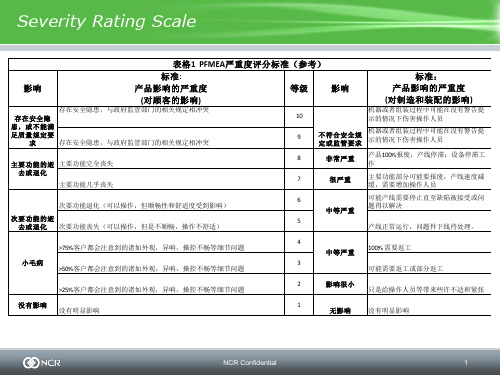
存在安全隐患,与政府监管部门的相关规定相冲突 存在安全隐 患,或不能满 足质量规定要 求 存在安全隐患,与政府监管部门的相关规定相冲突 主要功能的逝 主要功能完全丧失 去或退化 主要功能几乎丧失 次要功能退化(可以操作,但顺畅性和舒适度受到影响) 次要功能的逝 去或退化 次要功能丧失(可以操作,但是不顺畅,操作不舒适) >75%客户都会注意到的诸如外观,异响,操控不畅等细节问题 小毛病 >50%客户都会注意到的诸如外观,异响,操控不畅等细节问题 >25%客户都会注意到的诸如外观,异响,操控不畅等细节问题 没有影响 没有明显影响
5
中等水平
过程中监测
4
中等偏上
源头处监测
3
高
有部分防错手段
自动控制装置能自动检测到即将发生的失效并避免错误的发生
2
很高
有防错,不需要监测
夹具,机器或者产品设计本身具有放错功能,能够完全规避制作过程中可 能发生的失效
1
必然的(能被发 现)
NCR Confidential
3
Severity Rating Scale
表格 1 PFMEA 严重度评分标准(参考) 标准 : 产品影响的严重度 等级 影响 (对顾客的影响 )
10 9 8 7 6 中等严重 5 4 中等严重 3 2 1 影响很小
影响
标准: 产品影响的严重度 (对制造和装配的影响 )
机器或者组装过程中可能在没有警告提 示的情况下伤害操作人员
等级 10 9 8 7 6 5 4 3 2
1
NCR Confidential
2
Detection Rating Scale
可探测性表格
探测机会
没有机会探测到 任何阶段都好像不容 易探测到 问题探测总是滞后
FMEA潜在失效模式及分析表格模版
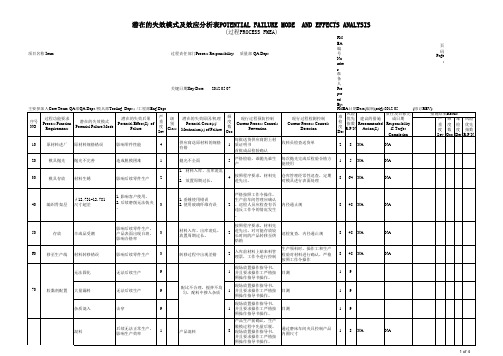
(过程PROCESS FMEA)
项目名称 Item: 主要参加人Core Team: QA部QA Dept./模具部Tooling. Dept.; /工程部Eng.Dept. 序号 NO. 过程功能要求 Process Function Requirements 潜在的失效模式 Potential Failure Mode 潜在的失效后果 Potential Effect(S) of Failure 严 级 重 别 度 Class Sev 4 潜在的失效原因/机理 Potential Cause(s)/ Mechanism(s) of Failure 供应商送原材料的规格 有错 抛光不全面 1. 材料入库、出库凌乱 。 2. 放置周期过长。 频 现行过程预防控制 度 Current Process Controls 数 Prevention Occ 1 每批送货供应商附上材 质证明书 首批成品检验确认 严格检验,谁抛光谁生 产 按照程序要求,材料先 进先出。 严格按照工作令操作。 生产前车间管理应确认 。巡检人员应检查有否 违反工作令的情况发生 。 按照程序要求,材料先 进先出。对可能存放较 长时间的产品转移至烘 焙箱 入库前材料上贴来料管 理票,工作令进行控制 现场放置操作指导书, 并且要求操作工严格按 照操作指导书操作。 现场放置操作指导书, 并且要求操作工严格按 照操作指导书操作。 现场放置操作指导书, 并且要求操作工严格按 照操作指导书操作。 产品生产前确认,生产 脱模过程中先量后脱。 现场放置操作指导书, 并且要求操作工严格按 照操作指导书操作。 控制真空度。现场放置 操作指导书,并且要求 操作工严格按照操作指 导书操作。 每日记录烘箱温度,升 温时间,固化时间,严 格按照工作令进行生产 活动。现场放置操作指 导书,并且要求操作工 严格按照操作指导书操 作。芯棒先行加热 严格按照工作令要求加 温 过程责任部门Process Responsibility: 关键日期Key Date: 2012.05.07 质量部 QA Dept.
- 1、下载文档前请自行甄别文档内容的完整性,平台不提供额外的编辑、内容补充、找答案等附加服务。
- 2、"仅部分预览"的文档,不可在线预览部分如存在完整性等问题,可反馈申请退款(可完整预览的文档不适用该条件!)。
- 3、如文档侵犯您的权益,请联系客服反馈,我们会尽快为您处理(人工客服工作时间:9:00-18:30)。
FMEA 编号Number:页码Page:准备人Prepared By:
潜在的失效模式及效应分析表POTENTIAL FAILURE MODE AND EFFECTS ANALYSIS
(过程PROCESS FMEA)
项目名称 Item: 过程责任部门Process Responsibility: 质量部 QA Dept.车型年/车辆类 关键日期Key Date: 2009.09.07工
FMEA 编号Number:页码Page:准备人Prepared By:
潜在的失效模式及效应分析表POTENTIAL FAILURE MODE AND EFFECTS ANALYSIS
(过程PROCESS FMEA)
项目名称 Item: 过程责任部门Process Responsibility: 质量部 QA Dept.车型年/车辆类 关键日期Key Date: 2009.09.07工
FMEA 编号Number:页码Page:准备人Prepared By:
潜在的失效模式及效应分析表POTENTIAL FAILURE MODE AND EFFECTS ANALYSIS
(过程PROCESS FMEA)项目名称 Item: 过程责任部门Process Responsibility: 质量部 QA Dept.车型年/车辆类 关键日期Key Date: 2009.09.07工
冲压
P200T Stamping
FMEA 编号Number:页码Page:准备人Prepared By:
潜在的失效模式及效应分析表POTENTIAL FAILURE MODE AND EFFECTS ANALYSIS
(过程PROCESS FMEA)
项目名称 Item: 过程责任部门Process Responsibility: 质量部 QA Dept.车型年/车辆类 关键日期Key Date: 2009.09.07工
FMEA 编号Number:页码Page:准备人Prepared By:
潜在的失效模式及效应分析表POTENTIAL FAILURE MODE AND EFFECTS ANALYSIS
(过程PROCESS FMEA)
项目名称 Item: 过程责任部门Process Responsibility: 质量部 QA Dept.车型年/车辆类 关键日期Key Date: 2009.09.07工
FMEA 编号Number:页码Page:准备人Prepared By:
(过程PROCESS FMEA)
项目名称 Item: 过程责任部门Process Responsibility: 质量部 QA Dept.车型年/车辆类 关键日期Key Date: 2009.09.07
FMEA 编号Number:页码Page:
准备人Prepared By:
(过程PROCESS FMEA)
项目名称 Item: 过程责任部门Process Responsibility: 质量部 QA Dept.车型年/车辆类 关键日期Key Date: 2009.09.07
FMEA 编号Number:页码Page:准备人Prepared By:
潜在的失效模式及效应分析表POTENTIAL FAILURE MODE AND EFFECTS ANALYSIS
(过程PROCESS FMEA)
项目名称 Item: 过程责任部门Process Responsibility: 质量部 QA Dept.车型年/车辆类 关键日期Key Date: 2009.09.07工
FMEA 编号Number:页码Page:
准备人Prepared By:
潜在的失效模式及效应分析表POTENTIAL FAILURE MODE AND EFFECTS ANALYSIS
(过程PROCESS FMEA)
项目名称 Item: 过程责任部门Process Responsibility: 质量部 QA Dept.车型年/车辆类 关键日期Key Date: 2009.09.07工。