化学抛光缺陷及对策
铝合金化学抛光三酸配方和优劣

铝合金化学抛光三酸配方和优劣在我国传统的铝合金化学抛光溶液中,应用较为广泛的是磷酸-硫酸-硝酸化学抛光液。
根据其磷酸相对含量的不同,可分为甲类(磷酸相对含量较低)和乙类(磷酸相对含量较高)。
其三酸抛光液成分和抛光温度如下。
长期的工业生产发现,三酸基本可以满足产品要求,但是也有些致命缺陷,如产生黄烟(毒性气体,污染环境),达不到环保要求。
因此,我总结罗列了一些缺陷特点。
1、氧化严重失光,质量大打折扣。
三酸抛光,一般都能形成镜面,一经阳极氧化,光泽大打折扣。
2、硝酸分解太快,大量黄烟污染严重,处理成本昂贵。
硝酸为强氧化剂,在高温条件下,遇到铝这种还原性很强的金属,分解速度之快令人难以想象:大量黄烟象着火一样瞬间溢出,抽风都困难,彻底吸收更难!此外,硝酸浓度的上下波动,势必造成抛光铝合金表面亮暗交替,成品率低。
3、不能起砂、去机械纹。
铝合金成型过程中,表面有许多机械纹,经三酸抛光处理后,纹路更加明显,严重影响铝合金外观质量。
除了用效率较低的机械方法(如喷砂,机抛)等进行预处理外,近几十年来,没有开发出用化学方法进行去纹和起砂配套处理、然后再行抛光的成熟技术,制约了抛光技术的推广。
4、滴流时间太短、药剂消耗太大、成品率太低。
因此,尽管抛光工艺如此简捷,但成本却是所有氧化前处理技术之最!高达6000-8000元/吨材。
铝合金离开抛光液后,在空中滴流时间一般不得超过30秒,否则会出现流痕,产生废品。
抛光材的流痕问题,是困扰铝加工行业的世界难题。
如此短的滴流时间,势必造成两大严重后果:其一是药剂消耗太大,竟然高达400-600kg/吨材,还要为如此高的废酸处理增加约800Kg片碱处理废水!其二是成品率太低,一般不到70%,大部分废品是由于流痕或花材造成,进一步增加了生产成本。
目前一般使用的方法是用化学抛光去冲孔剂添加剂用于抛光原液中,以此解决流痕问题。
随着研究的深入,市面上已经有很多厂家在使用无烟两酸化学抛光高光光亮剂,主要是磷酸和硫酸组成,不会产生黄烟,能满足环保要求。
铜及铜合金化学抛光工艺的改进

铜及铜合金化学抛光工艺的改进铜及铜合金化学抛光工艺的改进摘要:由于铜及铜合金的表面比较脆,加工困难,所以应用较多的方法是用化学抛光来改善表面质量。
本文介绍了铜及铜合金化学抛光的原理、工艺及改进方法。
关键词:铜,铜合金,化学抛光,改进1. 绪论近年来,铜及铜合金被广泛应用于汽车、航空、科技、医疗、家电等各个领域,其主要原因在于铜及铜合金具有良好的导电性、抗腐蚀性、易加工以及低成本等特点。
然而,由于铜及铜合金的表面比较脆,加工困难,所以应用较多的方法是用化学抛光来改善表面质量。
本文的主要内容是介绍铜及铜合金化学抛光的原理、工艺及改进方法。
2. 化学抛光工艺化学抛光是一种改善金属表面外观的技术,它的工艺可以分为三个阶段:一是化学溶剂去除金属表面的污渍;二是用一种中和剂对铜及铜合金表面进行处理;三是用腐蚀性溶液和钢丝布进行化学抛光。
在这一工艺过程中,主要关注的重点是表面净化、腐蚀剂的选择和抛光参数的调整。
一般来说,化学抛光因处理温度和抛光深度的不同而有些不同。
如果温度偏低,则铜及铜合金表面处理时会很不稳定,结果会有明显的表面不平或污渍等缺陷;如果温度偏高,则会使表面处理较柔和,出现较少的缺陷,但是会使抛光表面失去光泽。
此外,抛光深度也会影响表面质量,如果抛光深度过大,则会使表面损坏;如果抛光深度不够,则会使表面的光泽度和表面粗糙度增加。
3. 改进技术为了提高铜及铜合金的表面质量,采用不同的改进技术是必要的,其中一些是:(1)改善清洗工艺。
在化学抛光之前,铜及铜合金表面的污渍必须被清洗净。
为了改进清洗工艺,应使用更有效的清洗剂,如碱性清洗剂、有机溶剂清洗剂或磷酸盐清洗剂。
(2)选择腐蚀性溶液。
不同物料的表面处理看到不同结果,所以必须选择合适的腐蚀性溶液来改善抛光表面的质量。
(3)改变参数。
为了提高抛光表面的光泽,必须更改抛光参数,如抛光时间、温度和抛光深度。
4. 结论铜及铜合金的表面质量往往是影响其加工效果的重要因素。
化学抛光和电解抛光

2)磷酸-硝酸 化学抛光
3)磷酸-硫酸-硝酸化学抛光(普遍应用)
Ⅰ类:适用于表面粗糙的纯度大于99.5%的高纯铝 Ⅱ类:适用于经机械抛光的纯铝,<8%Zn的Al-Mg-Zn合金, ≤5%Cu的Al-Cu-Mg合金
朱祖芳. 铝合金阳极氧化与表面处理技术,北京:化学工业出版社,2010.
纯铝抛光
2)白色附着物
原因:槽液中溶铝量太高。
3)表面粗糙
原因:硝酸含量太高; 铜含量过高; 铝材内部组织缺陷(如疏松、夹杂等)。
4)转移性腐蚀
原因:铝材抛光完成到水洗之间的转移迟缓。
5)点腐蚀
原因:铝工件表面气体累积,形成气穴而致; 槽液中硝酸或铜含量偏低; 铝工件表面化学清洗不充分。
电化学抛光缺陷(磷酸-硫酸-铬酸) 1)电灼伤
第三讲 化学抛光和电解抛光
邢亚哲 博士/副教授 长安大学 材料表面强化研究所
主要内容
概论
化学抛光和电化学抛光机理
化学抛光工艺
电化学抛光工艺
抛光缺陷及对策
第一节 概论
物理作用 (切削,研磨等)
机械抛光
化学作用 (化学腐蚀)
化学抛光
电化学抛光(电解抛光)
化学抛光、电化学抛光和机械抛光特点比较
第三节 化学抛光工艺
以磷酸为基的化学抛光工艺 1)磷酸-硫酸化学抛光
朱祖芳. 铝合金阳极氧化与表面处理技术,北京:化学工业出版社,2010.
李珍芳,等. 科技信息,28(2010)4.
李珍芳,等. 科技信息,28(2010)4.
磷酸-硫酸基础上开发的无黄烟化学抛光
朱祖芳. 铝合金阳极氧化与表面处理技术,北京:化学工业出版社,2010.
化学机械抛光(CMP)技术的发展、应用及存在问题
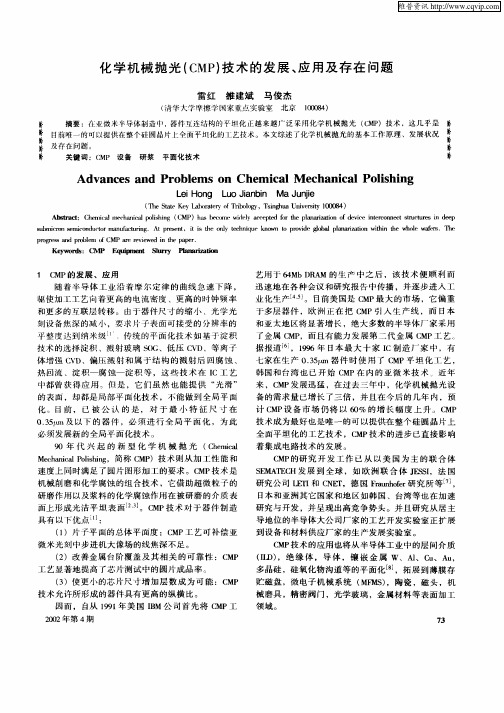
来 ,C P发 展迅猛 ,在 过去三 年中 ,化学 机械抛 光设 M
备 的需 求量 已增长 了三倍 ,并且 在今后 的几年 内 ,预 计 C 设 备 市 场仍 将 以 6 % 的增 长 幅 度 上 升 。C P MP o M 技术 成为最好 也是唯一 的可 以提 供在整个 硅圆 晶片上 全面平坦化 的工艺技术 ,C P技术 的进 步 已直接 影 响 M 着集 成 电路 技术的发展 。 CP M 的研 究 开 发 工 作 已从 以美 国 为 主 的联 合 体 SM TC E A E H发 展 到 全球 ,如 欧 洲 联 合 体 J SI E s,法 国 研究公 司 L f 和 c Ⅱ’ 国 Fano r 究 所等 | , E t N ,德 r hf 研 u e 7 j 日本和亚洲 其它 国家和地 区如韩 国 、台湾等也在 加速 研究 与开发 ,并 呈现 出高竞争势 头 。并且研 究从 居主 导地位 的半 导体大公 司厂家 的工 艺开发 实验室正 扩展 到设 备和材料 供应厂 家的生 产发 展实验 室。 C P技术 的应用也将 从半导 体工业 中的层间介 质 M ( D ,绝 缘 体 ,导 体 ,镶 嵌 金 属 w、A 、C 、A , I ) L J u u 多晶硅 ,硅 氧化 物沟道 等的平面化 [ ,拓展 到薄膜 存 贮磁 盘 ,微 电子机 械系统 ( M ) MF S ,陶 瓷 ,磁 头 ,机 械磨 具 ,精密 阀 门,光学玻 璃 ,金 属材料 等表面 加工
机械抛光、化学抛光和电解抛光的定义及优缺点
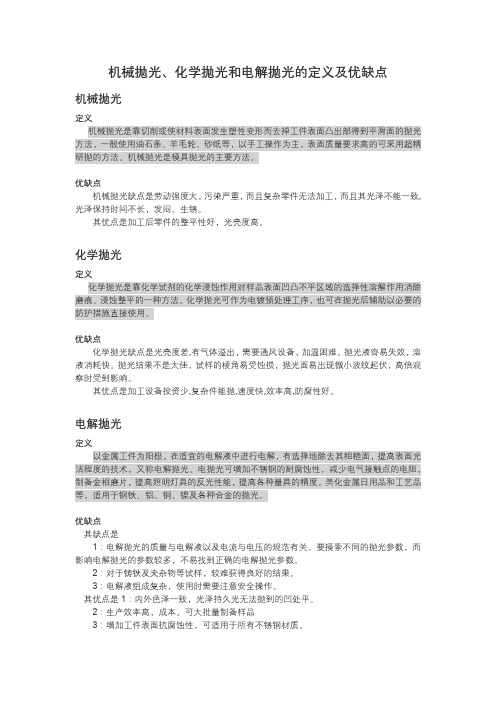
机械抛光、化学抛光和电解抛光的定义及优缺点机械抛光定义机械抛光是靠切削或使材料表面发生塑性变形而去掉工件表面凸出部得到平滑面的抛光方法,一般使用油石条、羊毛轮、砂纸等,以手工操作为主,表面质量要求高的可采用超精研抛的方法。
机械抛光是模具抛光的主要方法。
优缺点机械抛光缺点是劳动强度大,污染严重,而且复杂零件无法加工,而且其光泽不能一致,光泽保持时间不长,发闷、生锈。
其优点是加工后零件的整平性好,光亮度高。
化学抛光定义化学抛光是靠化学试剂的化学浸蚀作用对样品表面凹凸不平区域的选择性溶解作用消除磨痕、浸蚀整平的一种方法。
化学抛光可作为电镀预处理工序,也可在抛光后辅助以必要的防护措施直接使用。
优缺点化学抛光缺点是光亮度差,有气体溢出,需要通风设备,加温困难。
抛光液容易失效,溶液消耗快。
抛光结果不是太佳,试样的棱角易受蚀损,抛光面易出现微小波纹起伏,高倍观察时受到影响。
其优点是加工设备投资少,复杂件能抛,速度快,效率高,防腐性好。
电解抛光定义以金属工件为阳极,在适宜的电解液中进行电解,有选择地除去其粗糙面,提高表面光洁程度的技术,又称电解抛光。
电抛光可增加不锈钢的耐腐蚀性,减少电气接触点的电阻,制备金相磨片,提高照明灯具的反光性能,提高各种量具的精度,美化金属日用品和工艺品等,适用于钢铁、铝、铜、镍及各种合金的抛光。
优缺点其缺点是1:电解抛光的质量与电解液以及电流与电压的规范有关。
要摸索不同的抛光参数,而影响电解抛光的参数较多,不易找到正确的电解抛光参数。
2:对于铸铁及夹杂物等试样,较难获得良好的结果。
3:电解液组成复杂,使用时需要注意安全操作。
其优点是1:内外色泽一致,光泽持久光无法抛到的凹处平。
2:生产效率高,成本。
可大批量制备样品3:增加工件表面抗腐蚀性,可适用于所有不锈钢材质。
电解抛光中的常见问题及解决方法

电解抛光中的常见问题及解决方法1.电解抛光后,表面为什么会发现似未抛光的斑点或小块?抛光前除油不彻底,表面尚附有油迹。
选用“QX0116不锈钢除油剂”,1:(15-20)溶解后使用,10~40℃条件下浸泡10~20分钟,如除油剂已长时间使用应考虑更换新槽液。
2.抛光过后表面局部为什么有灰黑色斑块存在?可能氧化皮未彻底除干净,局部尚存在氧化皮。
加大清除工件表面氧化皮力度。
可以考虑选择专用酸洗液来除氧化皮。
3.抛光后工件棱角处及尖端过腐蚀是什么原因引起的?棱角、尖端的部位电流过大,或电解液温度过高,抛光时间过长,导致过度溶解。
调整电流密度或溶液温度,或缩短时间。
检查电极位置,在棱角处设置屏蔽等。
4.为什么工件抛光后不光亮并呈灰暗色?如果工艺指标都对的情况下,可能是电化学抛光溶液已老化不起作用,或作用不明显。
检查电解抛光液是否使用时间过长,质量下降,或溶液成分比例失调,然后做相应调整。
5.工件抛光后表面有白色的条纹是怎么回事?溶液相对密度太大,液体太稠,相对密度大于1.8。
增大抛光液的搅拌程度,如果电解液相对密度太大,适当的添加些新鲜抛光液或适当量水稀释至比重为1.77左右。
6.为什么抛光后表面有阴阳面,及局部无光泽的现象?工件放置的位置没有与阴极对正,或工件互相有屏蔽。
将工件进行适当的调整,使工件与阴极的位置适当,使电力分布合理。
7.抛光后工件表面平整光洁,但有些点或块不够光亮,或出现垂直状不亮条纹,一般是什么原因引起的?可能是抛光后期工件表面上产生的气泡未能及时脱离并附在表面或表面有气流线路。
提高电流密度,使析气量加大以便气泡脱附,或提高溶液的搅拌速度,增加溶液的流动。
8.零件和挂具接触点无光泽并有褐色斑点,表面其余部分都光亮是什么原因?可能是零件与挂具的接触不良,造成电流分布不均,或零件与挂具接触点少。
擦亮挂具接触点,使导电良好,或增大零件与挂具的接触点面积。
9.同一槽抛光的零件有的光亮,有的不亮,或者局部不亮。
电解抛光不成功的原因

电解抛光不成功的原因
电解抛光不成功的原因可能有以下几点:
1. 材料问题:材料的成分、纯度和组织结构对电解抛光效果有很大影响。
如果材料中含有大量杂质或组织结构不均匀,可能会导致抛光效果不佳。
2. 电解液的问题:电解液的组成、浓度和温度等都会影响抛光效果。
如果电解液不合适或者使用不当,也可能导致抛光失败。
3. 抛光参数的问题:如电流密度、抛光时间、搅拌速度等参数设置不合理,也会影响抛光效果。
4. 设备问题:设备的性能、操作方法等也会对抛光效果产生影响。
改进措施如下:
1. 对于材料问题,可以尝试更换更合适的材料或者对材料进行预处理,以改善其抛光性能。
2. 对于电解液的问题,需要根据具体情况调整电解液的配方和使用条件,比如增加或减少某些成分,改变电解液的浓度和温度等。
3. 对于抛光参数的问题,可以通过实验来优化各参数,找到最佳的抛光条件。
4. 对于设备问题,可以检查和维护设备,确保其正常运行。
同时,也可以考虑升级设备,提高抛光效率和质量。
金属钨化学机械研磨清洗缺陷研究及解决方法

金属钨化学机械研磨清洗缺陷研究及解决方法金属钨化学机械研磨清洗是钨表面处理的一种新技术,可以改善钨表面的质量。
它提供了一种新的、有效的方法来清除表面的污渍、污垢和污秽,恢复表面光洁度。
本文将研究钨表面处理中存在的缺陷,以及采用金属钨化学机械研磨清洗技术对其进行解决的方法。
一、钨表面处理中存在的缺陷钨表面处理中存在的缺陷主要有以下几类:1、表面开裂:钨表面处理过程中,由于钨的特殊性质,可能会造成表面开裂、折断、压痕等一系列问题。
2、粗糙度:由于钨表面处理时采用的磨具、磨料等有限,容易造成表面粗糙度较高。
3、浮层:钨表面处理中,由于处理液长期暴露在空气中,可能会造成浮层形成,影响表面质量。
4、表面污渍:钨表面处理过程中,污渍会从外界进入,造成表面污渍,影响表面质量。
二、采用金属钨化学机械研磨清洗技术的优势1、可以消除表面的污渍、污垢和污秽,恢复表面光洁度。
2、可以提高表面的粗糙度,同时可以使表面的折射率和反射率得到改善。
3、可以有效的清除钨表面的开裂、折断、压痕等缺陷,恢复表面光洁度。
4、可以提高金属钨表面的耐腐蚀性、耐热性和耐磨性,延长表面使用寿命。
三、金属钨化学机械研磨清洗的方法1、清洗:采用碱性溶液进行钨表面清洗,清除表面污渍、污垢和污秽,恢复表面光洁度。
2、研磨:采用机械研磨的方法对钨表面进行抛光,消除表面的折射线、折断、压痕等缺陷,恢复表面光洁度。
3、涂覆:采用涂覆技术,在钨表面涂覆一层保护层,以提高金属钨表面的耐腐蚀性、耐热性和耐磨性,延长表面使用寿命。
四、总结经过上述讨论,金属钨化学机械研磨清洗技术可以有效的清除表面的污渍、污垢和污秽,恢复表面光洁度,同时可以清除钨表面的开裂、折断、压痕等缺陷,提高金属钨表面的耐腐蚀性、耐热性和耐磨性,延长表面使用寿命。
同时,在钨表面处理过程,应避免由于操作不当,表面处理液长期暴露在空气中,从而造成浮层形成,影响表面质量。
金属钨化学机械研磨清洗技术是一种新技术,它为改善钨表面质量提供了有效而可靠的方法,进而可以有效提高钨表面处理的精度和质量,满足客户的需求。
电解抛光不成功的原因
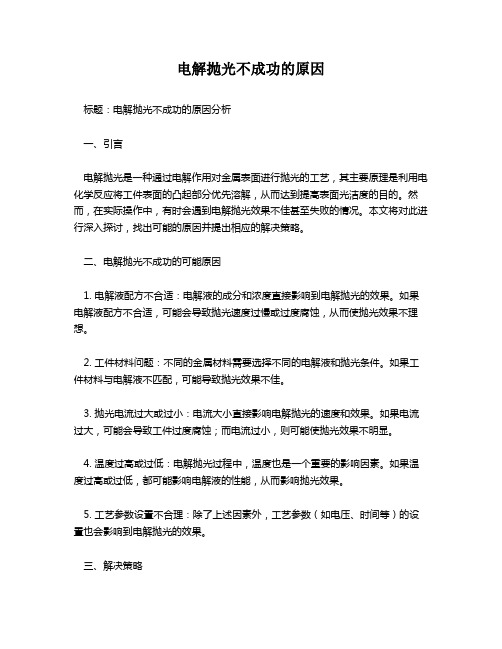
电解抛光不成功的原因标题:电解抛光不成功的原因分析一、引言电解抛光是一种通过电解作用对金属表面进行抛光的工艺,其主要原理是利用电化学反应将工件表面的凸起部分优先溶解,从而达到提高表面光洁度的目的。
然而,在实际操作中,有时会遇到电解抛光效果不佳甚至失败的情况。
本文将对此进行深入探讨,找出可能的原因并提出相应的解决策略。
二、电解抛光不成功的可能原因1. 电解液配方不合适:电解液的成分和浓度直接影响到电解抛光的效果。
如果电解液配方不合适,可能会导致抛光速度过慢或过度腐蚀,从而使抛光效果不理想。
2. 工件材料问题:不同的金属材料需要选择不同的电解液和抛光条件。
如果工件材料与电解液不匹配,可能导致抛光效果不佳。
3. 抛光电流过大或过小:电流大小直接影响电解抛光的速度和效果。
如果电流过大,可能会导致工件过度腐蚀;而电流过小,则可能使抛光效果不明显。
4. 温度过高或过低:电解抛光过程中,温度也是一个重要的影响因素。
如果温度过高或过低,都可能影响电解液的性能,从而影响抛光效果。
5. 工艺参数设置不合理:除了上述因素外,工艺参数(如电压、时间等)的设置也会影响到电解抛光的效果。
三、解决策略1. 根据工件材料选择合适的电解液,并调整其浓度,以保证抛光效果。
2. 对于不适合电解抛光的材料,可以考虑采用其他抛光方法,如机械抛光、化学抛光等。
3. 调整抛光电流,使之在适宜的范围内。
4. 控制好电解抛光过程中的温度,避免过高或过低。
5. 合理设置工艺参数,优化抛光效果。
四、结语电解抛光是一项技术性很强的工作,需要根据实际情况灵活调整各种参数。
只有充分理解电解抛光的原理,才能更好地应对可能出现的问题,提高抛光效果。
希望本文能对你在电解抛光工作中有所帮助。
化学抛光原理、步骤及优缺点介绍

化学抛光原理、步骤及优缺点介绍化学抛光是一种将金相样品浸入调配的化学抛光液中,借化学药剂的溶解作用而得到的抛光表面的抛光方法。
化学抛光是常见的金相样品抛光方法之一,这种方法操作简便,不需任何仪器设备,只需要选择适当的化学抛光液和掌握最佳的抛光规范,就能快速得到较理想的光洁而无变形层的表面。
基本原理:金属试样表面各组成相的电化学电位不同,形成了许多微电势,在化学溶液中会产生不均匀溶解。
在溶解过程中试样面表层会产生一层氧化膜,试样表面凸出部分由于粘膜薄,金属的溶解扩展速度较慢,抛光后的表面光滑,但形成有小的起伏波形,不能达到十分理想的要求。
在低和中等放大倍数下利用显微镜观察时,这种小的起伏一般在物镜垂直鉴别能力之内,仍能观察到十分清晰的组织。
化学抛光溶液:化学抛光液的成分随抛光材料的不同而不同。
一般为混合酸液。
化学抛光溶液由氧化剂和粘滞剂组成。
氧化剂起抛光作用,它们是酸类和过氧化氢。
常用的酸类有:正磷酸、铬酸、硫酸、醋酸、硝酸、氢氟酸等等。
粘滞剂用于控制溶液中的扩散和对流速度,使化学抛光过程均匀进行。
化学抛光操作步骤1:试样准备:试样经精磨光后清洗。
2:配置化学抛光溶液。
化学抛光溶液应在烧杯中调配,根据试样材料选择化学抛光液配方,配溶液时应用蒸馏水,药品用化学纯试剂。
某些不易溶于水的药品需要加热溶液才能溶解。
过氧化氢和氢氟酸腐蚀性很强,调配时需注意安全。
化学抛光溶液经使用之后,溶液内金属离子增多,抛光作用减弱,如果发现作用缓慢,气泡减少,应更换新药液。
3:试样用竹夹或者木夹夹住浸入抛光液中,一边搅动并适时取出观察至达到抛光要求后取出。
4:化学抛光结束之后,试样应立即清洗、吹干。
化学抛光的优缺点:1:优点:操作简便、快速,无需专用仪器。
抛光后试样表面无变形层,可抛光经镶嵌后的试样,也可同时抛光试样的纵、横断面。
化学抛光时兼有化学侵蚀作用,因此多数情况下能同时显示组织,抛光结束之后可以观察组织,不需再做侵蚀显示。
电解抛光主要缺陷

电解抛光主要缺陷1、铝材及铝件在电解抛光过程中最常见的缺陷是白霜或结霜现象。
白霜究竟是什么物质,成分如何,目前尚无定论,有人认为是磷酸铝析出物,也有人认为是铝表面形成的钝化膜。
白霜可在工件的局部形成,因为那里的氧化膜形成不够快,从而造成电解不足以取代阳极氧化。
若取出工件,清洗后并重新电解抛光时,氧化物会溶解,白霜也会随着消失,然而又可在别处产生。
调整溶液成分与改变处理工艺可控制这类缺陷的产生。
例如,在磷酸一硫酸溶液中电解抛光时,磷酸浓度过高、硫酸浓度过大或过小都可引起白霜,温度太低、电流密度不恰当也会诱发这类缺陷。
1.1溶液成分对白霜的影响磷酸在电鹂抛光过程中主要作用是溶解氧化膜与铝:AL(H2PO4 )3 在铝有面附近浓集,形成糖浆状粘性膜层,对工件表面抛光即整平与光亮起着决定性的作用,但也对白霜的形成有很大影响。
冯宝义等研究证明,在磷酸(3O%~4O%)一硫酸(2o%-30%)一PEG添加剂(20%~3O%)溶液中电解抛光(温度8o℃~90℃、电流密度30-4O 安每平方分米)时,增加磷酸浓度,可提高工件的光亮度、降低电流密度、减少电耗,但磷酸含量过高,会出现白霜”(表24)。
电解抛光液中的硫酸有如下的作用:稳定电解抛光过程,降低抛光温度,提高溶液电导率,降低工作电压,减少能源消耗,可增加铝的允许含量,延长槽液寿命。
然而,硫酸的含量超过一定限度后,会增强溶液的氧化能力,使电解抛光向着有利于阳极氧化过程的方向转变,从而在工件表面诱发白霜;硫酸含量过低,也可使铝表面产生白霜。
因此,应始终使溶液中的硫酸含量保持在工艺规程的允许最佳范围内。
大多数电解抛光液中都含有醇之类的添加剂,因为醇分子间可形成氢键而发生缔合作用,在被抛光工件表面形成粘性膜层,使其凹陷处处于稳定的钝化状态.而凸突处则以更快的速度溶解.最后获得平滑光亮的表面。
醇分子的缔台结构为:这就是小分子醇常常用作电解抛光溶液舔加剂的主要原因,但大分子多元醇聚合物也可作抛光液添加剂。
化学抛光缺陷及对策

化学抛光缺陷及对策有关铝及铝合金材料化学抛光中出现的缺陷及其纠正措施是在生产的发展过程中不断总结完善的。
现以磷酸"硫酸"硝酸的化学抛光生产过程中常见的缺陷和纠正措施归纳如下。
(1)光亮度不足。
这是化学抛光中最关心的事情。
光亮度没有达到预期的目标,其原因可从特殊铝材的生产工艺和化学抛光工艺这两方面分析。
有关特殊铝材的生产工艺已经有详细的论述。
建议采用铝纯度99.70%.及其以上级别的铝锭,来生产特殊铝材;铝材加工工艺中质量控制为化学抛光得到高光亮度表面奠定基础,例如铝—镁合金5056(A199.98Mgl)是用纯度为99.99%的精铝锭生产而成的。
化学抛光后,具有很高的光亮度。
槽液控制中硝酸含量不足,会使表面光亮度不足,其表面可能过多地附着一层铜;硝酸含量太高,铝材表面形成彩虹膜,会使表面模糊或不透明,还引起光亮度不足;化学抛光时间不足,温度不够,搅拌不充分,槽液老化等也会使化学抛光表面光亮度不足。
槽液的相对密度较大,防止铝材浮出抛光槽液的液面,致使上部铝材光亮度不足。
水的影响造成光亮度不足,往往容易被忽视。
最好用干燥的铝材进入化学抛光槽液,杜绝水分的带入。
(2)白色附着物。
该缺点的形貌为化学抛光后的铝材表面上附着有一层白色的沉积物,且漫衍不均匀,附着物底部的铝材表面有可能被侵蚀。
通常,该缺点是因为化学抛光槽液中溶铝量太高所致,假如化学抛光槽液的相对密度在"#$%以上,可以得到进一步证实。
则需采取措施调解槽液中的溶铝量到一般的范围内。
(3)表面粗糙。
化学抛光后的铝材表面出现粗糙现象。
该缺陷可能是在槽液中硝酸含量过高,酸性浸蚀造成的;若槽液中铜含量也高,则表面粗糙现象将会更严重。
通常,若槽液中硝酸含量过高,化学抛光反应剧烈,有“沸腾”的现象产生。
若硝酸含量正常,铜含量偏高,则水洗后的铝材表面上附着有一层很明显的金属铜的特征颜色。
如果铜的特征颜色很深,则表明槽液中的铜含量偏高,应采取措施调整硝酸与铜的含量达到正常的范围内。
抛光常见疵病产生原因及克服方法
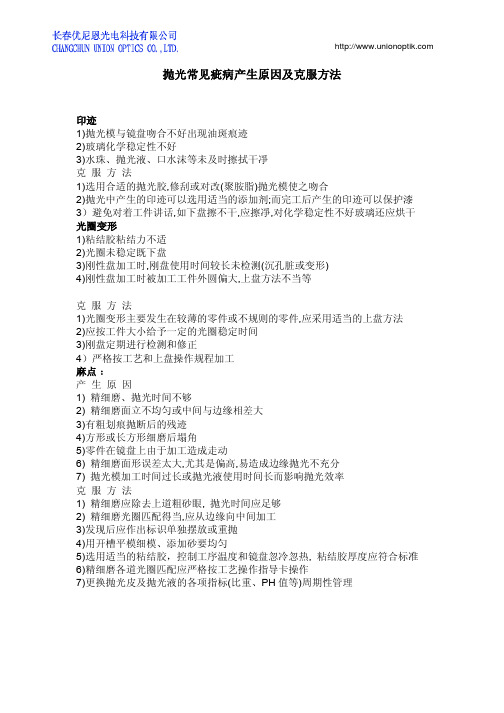
抛光常见疵病产生原因及克服方法
印迹
1)抛光模与镜盘吻合不好出现油斑痕迹
2)玻璃化学稳定性不好
3)水珠、抛光液、口水沫等未及时擦拭干凈
克 服 方 法
1)选用合适的抛光胶,修刮或对改(聚胺脂)抛光模使之吻合
2)抛光中产生的印迹可以选用适当的添加剂;而完工后产生的印迹可以保护漆
3)避免对着工件讲话,如下盘擦不干,应擦凈,对化学稳定性不好玻璃还应烘干 光圈变形
1)粘结胶粘结力不适
2)光圈未稳定既下盘
3)刚性盘加工时,刚盘使用时间较长未检测(沉孔脏或变形)
4)刚性盘加工时被加工工件外圆偏大,上盘方法不当等
克 服 方 法
1)光圈变形主要发生在较薄的零件或不规则的零件,应采用适当的上盘方法
2)应按工件大小给予一定的光圈稳定时间
3)刚盘定期进行检测和修正
4)严格按工艺和上盘操作规程加工
麻点﹕
产 生 原 因
1) 精细磨、抛光时间不够
2) 精细磨面立不均匀或中间与边缘相差大
3)有粗划痕抛断后的残迹
4)方形或长方形细磨后塌角
5)零件在镜盘上由于加工造成走动
6) 精细磨面形误差太大,尤其是偏高,易造成边缘抛光不充分
7) 抛光模加工时间过长或抛光液使用时间长而影响抛光效率
克 服 方 法
1) 精细磨应除去上道粗砂眼, 抛光时间应足够
2) 精细磨光圈匹配得当,应从边缘向中间加工
3)发现后应作出标识单独摆放或重抛
4)用开槽平模细模、添加砂要均匀
5)选用适当的粘结胶,控制工序温度和镜盘忽冷忽热, 粘结胶厚度应符合标准
6)精细磨各道光圈匹配应严格按工艺操作指导卡操作
7)更换抛光皮及抛光液的各项指标(比重、PH 值等)周期性管理。
抛光产品缺陷分析报告模板
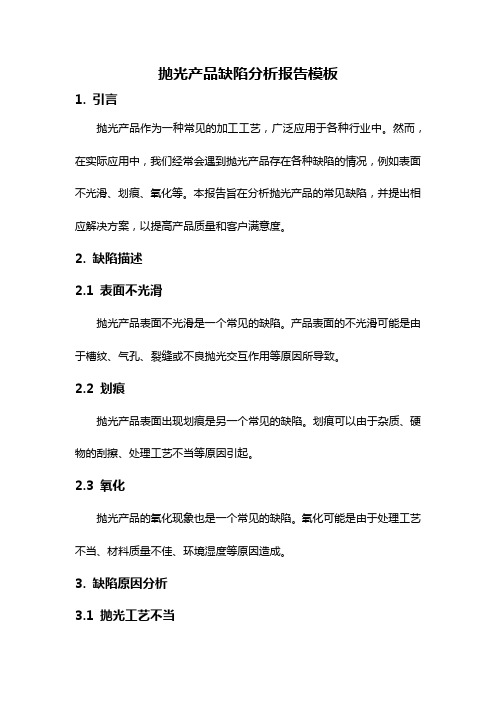
抛光产品缺陷分析报告模板1. 引言抛光产品作为一种常见的加工工艺,广泛应用于各种行业中。
然而,在实际应用中,我们经常会遇到抛光产品存在各种缺陷的情况,例如表面不光滑、划痕、氧化等。
本报告旨在分析抛光产品的常见缺陷,并提出相应解决方案,以提高产品质量和客户满意度。
2. 缺陷描述2.1 表面不光滑抛光产品表面不光滑是一个常见的缺陷。
产品表面的不光滑可能是由于槽纹、气孔、裂缝或不良抛光交互作用等原因所导致。
2.2 划痕抛光产品表面出现划痕是另一个常见的缺陷。
划痕可以由于杂质、硬物的刮擦、处理工艺不当等原因引起。
2.3 氧化抛光产品的氧化现象也是一个常见的缺陷。
氧化可能是由于处理工艺不当、材料质量不佳、环境湿度等原因造成。
3. 缺陷原因分析3.1 抛光工艺不当抛光工艺对于产品表面的质量有着重要的影响。
若抛光工艺不当,例如抛光机器参数设置不准确、抛光剂选择不当等,会导致产品表面不光滑、划痕等缺陷的出现。
3.2 材料质量问题抛光产品使用的材料质量直接影响产品的表面质量。
低质量的材料容易出现氧化等问题,从而导致产品的缺陷。
3.3 人为操作失误在抛光产品的过程中,人为操作失误也是一个导致缺陷的重要原因。
操作人员可能因为疏忽或缺乏经验而引发不良操作,例如抛光时间不够、用力过大等。
3.4 环境因素环境因素也会对抛光产品的质量产生影响。
湿度过高或氧化性环境都可能导致产品氧化、生锈等缺陷的出现。
4. 解决方案4.1 优化抛光工艺针对抛光工艺不当导致的缺陷问题,需要对抛光机器的参数进行调整,确保机器运行稳定。
同时,根据具体产品的特点合理选择抛光剂,以及控制抛光的时间和力度。
4.2 优化材料选择通过加强对供应商的材料质量质检,确保所使用的材料达到质量标准,从而减少材料质量问题导致的缺陷。
4.3 培训与管理加强对于操作人员,进行相关培训,提高其操作技能和意识。
同时,加强对操作环节的管理,确保操作规范执行,减少人为操作失误导致的缺陷。
化学抛光

化学抛光资料1化学抛光操作工艺因素:(1)装料。
铝材化学抛光前先进行装料,装料的基本原则与普通阳极氧化生产的要求相同。
对需要化学抛光的铝材在装料前需要核对铝材的纯度、化学成分、基材的外观质量。
应无严重的擦伤、划伤、腐蚀等缺陷,以确保产品获得满意的光亮度。
装料量相应减少,铝材间距要加大,倾斜度要加大,使气体尽快逸出。
装料时要防止铝材表面气体累积,避免形成气体缺陷。
化学抛光槽液的相对密度很大,抛光中刚形成的气体附着在铝材表面上,有可能使导电梁上浮,浮出液面部分的铝材化学抛光就不充分,造成在同一挂料中出现光亮度不均匀的现象。
必要时,减少装料量或采用大型加重的导电梁防止铝材上浮。
对高光亮度要求的装饰面应该向外垂直装料,确保该面上的气体尽快逸出。
装料要稳固,应采用夹具,夹具应安放在非装饰面上,避免在装饰面上留下夹具痕迹。
(2)化学清洗脱脂。
铝材化学抛光前,特别是经过机械抛光的铝材表面可能含有油脂,一般采用高温水或高温蒸汽清洗,但对除去共价键结合的润滑油脂来说,清洗得不很干净。
以前采用三氯乙烯等有机溶剂脱脂清洗,但因含有氯氟烃类有机化合物破坏大气臭氧层的原因而被禁止使用,且成本较高。
现在大多数生产线采用含有表面活性剂的水溶性化学清洗剂清洗,除去铝材表面的油脂比较有效。
(3)搅拌。
在铝材化学抛光中气体逸出很多,如果槽液没有搅拌,很难使气体迅速脱离铝材表面,形成气体累积的缺陷;气体累积到一定量时因气泡向上逸出,又使表面造成气体条纹缺陷,因此用搅拌来克服这类缺陷。
主要采用机械搅拌或无油压缩空气搅拌。
适当的、均匀的搅拌才能保证表面化学抛光的均匀性。
不推荐采用手工操作搅拌,槽液为热的浓酸组成且具有很强的腐蚀性;气体有很强的刺激性;手工搅拌具有危险性;且均匀性很难保证。
(4)时间。
铝材化学抛光所需的时间通常取决于两个部分:一是铝材制造工艺和半成品的表面质量;二是化学抛光所要达到的光亮度要求。
通常化学抛光时间在1—3min,还要根据槽液中的溶铝量与温度而决定,限定抛光时间是为了防止气体缺陷的产生。
抛光常见疪病及克服方法
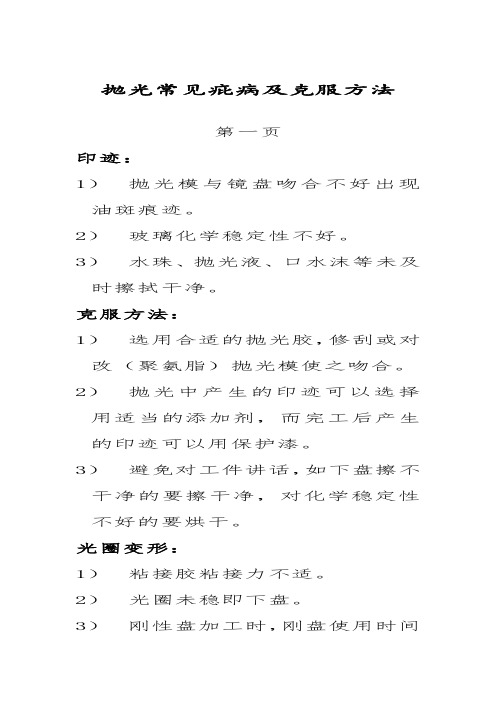
抛光常见疪病及克服方法第一页印迹:1)抛光模与镜盘吻合不好出现油斑痕迹。
2)玻璃化学稳定性不好。
3)水珠、抛光液、口水沫等未及时擦拭干净。
克服方法:1)选用合适的抛光胶,修刮或对改(聚氨脂)抛光模使之吻合。
2)抛光中产生的印迹可以选择用适当的添加剂,而完工后产生的印迹可以用保护漆。
3)避免对工件讲话,如下盘擦不干净的要擦干净,对化学稳定性不好的要烘干。
光圈变形:1)粘接胶粘接力不适。
2)光圈未稳即下盘。
3)刚性盘加工时,刚盘使用时间较长未检测(沉孔变形或脏)4)刚性盘加工时被加工工件外圆偏大,上盘方法不当等克服方法:1)光圈变形主要发生在较薄的零件或不规则的零件,应采用适当的上盘方法。
2)应按工件的大小给予一定的光圈稳定时间。
3)刚盘定期进行检测和修正。
4)严格按工艺和上盘操作规程加工。
麻点:1)精细磨时间、抛光时间不够。
2)精细磨面不均匀或中间与边缘相差大。
3)有粗划痕抛断后的残迹。
4)方形或长方形细磨后塌角。
5)零件在镜盘上由于加工造成走动。
6)精细磨面形误差太大,尤其是偏高,易造成边缘抛光不充分。
7)抛光模加工时间过长或抛光液使用时间过长而影响抛光效率。
克服方法:1)精细磨应除去上道砂眼,抛光时间要足够长。
2)精细磨光圈匹配得当,应从边缘向中间加工3)发现后应当作出标识单独摆放或重抛。
4)用开槽平模细磨、添加砂要均匀。
5)选用适当的粘接胶,控制工序温度和镜盘温度,粘接胶厚度应符合标准。
6)精细磨各道光圈匹配应严格按操作指导卡操作。
7)更换抛光皮及抛光液的各项指标(比重、PH值等)周期性的管理。
化学抛光与金属腐蚀解析化学抛光对金属材料腐蚀行为的影响与防护策略
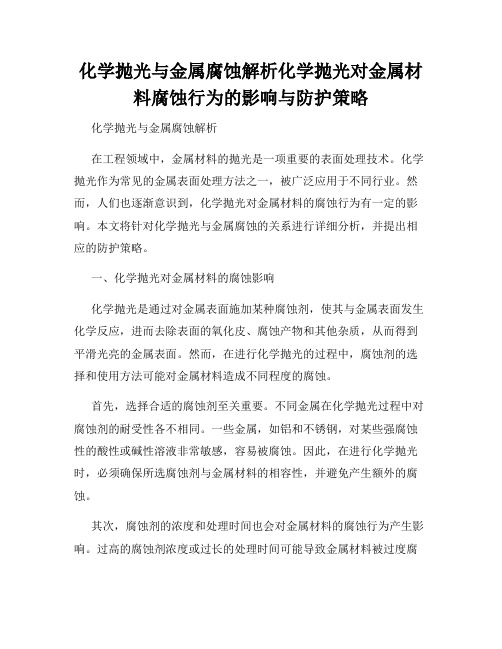
化学抛光与金属腐蚀解析化学抛光对金属材料腐蚀行为的影响与防护策略化学抛光与金属腐蚀解析在工程领域中,金属材料的抛光是一项重要的表面处理技术。
化学抛光作为常见的金属表面处理方法之一,被广泛应用于不同行业。
然而,人们也逐渐意识到,化学抛光对金属材料的腐蚀行为有一定的影响。
本文将针对化学抛光与金属腐蚀的关系进行详细分析,并提出相应的防护策略。
一、化学抛光对金属材料的腐蚀影响化学抛光是通过对金属表面施加某种腐蚀剂,使其与金属表面发生化学反应,进而去除表面的氧化皮、腐蚀产物和其他杂质,从而得到平滑光亮的金属表面。
然而,在进行化学抛光的过程中,腐蚀剂的选择和使用方法可能对金属材料造成不同程度的腐蚀。
首先,选择合适的腐蚀剂至关重要。
不同金属在化学抛光过程中对腐蚀剂的耐受性各不相同。
一些金属,如铝和不锈钢,对某些强腐蚀性的酸性或碱性溶液非常敏感,容易被腐蚀。
因此,在进行化学抛光时,必须确保所选腐蚀剂与金属材料的相容性,并避免产生额外的腐蚀。
其次,腐蚀剂的浓度和处理时间也会对金属材料的腐蚀行为产生影响。
过高的腐蚀剂浓度或过长的处理时间可能导致金属材料被过度腐蚀,从而使其表面产生凹坑、裂纹等缺陷。
因此,在使用化学抛光方法时,必须掌握适当的工艺参数,确保金属表面得到适度的处理。
不可忽视的是,在化学抛光过程中,金属表面还会形成一层抛光产物。
这层产物主要包括金属离子、有机物和水等。
这些产物能够覆盖金属表面,形成一种保护膜,从而减缓后续腐蚀过程的发生。
然而,如果抛光产物残留在表面或处理不当,可能会破坏这种保护膜,加速金属的腐蚀速度。
因此,正确处理和清除抛光产物至关重要。
二、金属腐蚀的防护策略针对化学抛光对金属材料腐蚀的影响,我们可以采取一些防护措施,以减少金属腐蚀的发生。
首先,选择适当的化学抛光剂。
在进行化学抛光前,必须对要处理的金属材料进行分析和评估,选择与之相容的腐蚀剂。
同时,应注意腐蚀剂的浓度和处理时间,避免过度腐蚀。
化学抛光与材料界面揭示化学抛光对材料界面的影响与调控策略
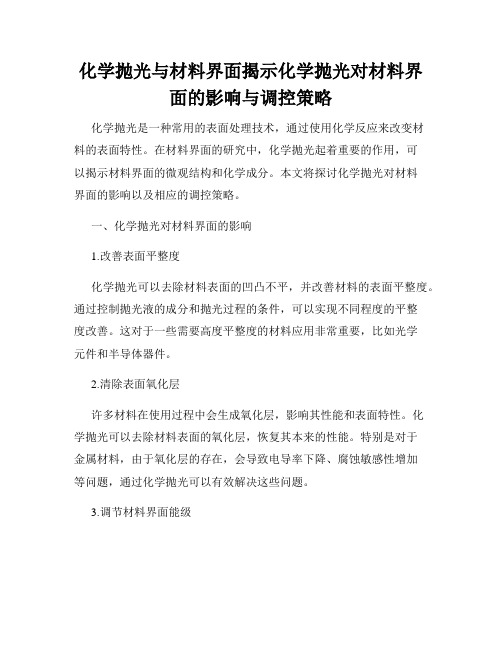
化学抛光与材料界面揭示化学抛光对材料界面的影响与调控策略化学抛光是一种常用的表面处理技术,通过使用化学反应来改变材料的表面特性。
在材料界面的研究中,化学抛光起着重要的作用,可以揭示材料界面的微观结构和化学成分。
本文将探讨化学抛光对材料界面的影响以及相应的调控策略。
一、化学抛光对材料界面的影响1.改善表面平整度化学抛光可以去除材料表面的凹凸不平,并改善材料的表面平整度。
通过控制抛光液的成分和抛光过程的条件,可以实现不同程度的平整度改善。
这对于一些需要高度平整度的材料应用非常重要,比如光学元件和半导体器件。
2.清除表面氧化层许多材料在使用过程中会生成氧化层,影响其性能和表面特性。
化学抛光可以去除材料表面的氧化层,恢复其本来的性能。
特别是对于金属材料,由于氧化层的存在,会导致电导率下降、腐蚀敏感性增加等问题,通过化学抛光可以有效解决这些问题。
3.调节材料界面能级化学抛光可以改变材料表面的化学成分,从而调节材料界面的能级。
这对于某些材料的电子器件应用十分关键。
例如,通过改变半导体材料表面的成分,可以调节电子行为和载流子的输运性质。
二、化学抛光的调控策略1.选择适当的抛光液选择适合的抛光液是实现化学抛光的关键。
抛光液的成分要与被抛光材料相适应,并具有良好的表面活性剂和腐蚀剂,以保证抛光效果。
不同材料需要不同的抛光液配方,因此需要对材料的特性进行了解,并进行实验验证。
2.控制抛光时间和温度抛光时间和温度是影响化学抛光效果的重要参数。
过长的抛光时间或过高的温度可能导致过度抛光和材料表面损伤。
因此,在进行化学抛光时,要根据具体材料和要求来控制抛光时间和温度,以达到最佳的抛光效果。
3.采用辅助手段为了进一步提高化学抛光的效果,可以采用辅助手段,如超声波辅助抛光、电动力学抛光等。
这些辅助手段可以增强抛光液的流动性和抛光剂的腐蚀性,从而提高整体抛光效果。
4.表面处理后的后续处理在完成化学抛光后,需要进行适当的后续处理,以防止再次生成氧化层或其他不良现象。
化学机械抛光设备在制造过程中的质量控制方法与技术

化学机械抛光设备在制造过程中的质量控制方法与技术化学机械抛光(Chemical Mechanical Polishing,CMP)是一种广泛应用于集成电路制造、光学元件加工等领域的表面处理技术。
制造过程中的质量控制方法和技术对于确保产品质量的稳定和一致性起着重要作用。
本文将介绍化学机械抛光设备制造过程中的质量控制方法和技术。
一、原材料质量控制原材料是化学机械抛光过程中的关键因素之一,它直接影响到成品的质量。
因此,在制造过程中,必须对原材料进行严格的质量控制。
首先,选用优质的研磨材料和化学材料,保证其纯度和稳定性。
其次,对原材料进行全面的检测和测试,确保其符合产品规格要求。
例如,可以对研磨材料进行粒度分析,对化学材料进行成分分析,以确保其质量和性能均达到要求。
二、设备运行参数的控制化学机械抛光设备的运行参数对于产品的质量具有重要影响。
为了达到理想的抛光效果,必须对设备的运行参数进行准确的控制。
首先,对于抛光液的流量、压力和浓度等参数,需要根据不同的工艺要求进行调整。
这些参数的调整可以通过改变泵的速度、泵的位置以及抛光头的位置来实现。
其次,对于研磨盘的旋转速度、研磨盘和衬底之间的压力等参数,也需要进行精确的控制。
这些参数的合理调整可以提高抛光效率,减少表面缺陷和残余应力,提高产品的质量。
三、工艺参数的控制化学机械抛光工艺是制造过程中的关键环节,合理的工艺参数设置可以提高产品的表面质量和加工精度。
在制造过程中,需要根据具体的产品要求和工艺流程,确定合适的工艺参数。
例如,对于抛光时间、抛光速度、抛光液配比等参数,需要进行精确的控制。
此外,还需要根据产品的要求,选择合适的抛光液和研磨材料,以及合适的抛光头和研磨盘。
通过合理设置工艺参数,可以提高抛光效率,降低表面粗糙度和突出度,提高产品的光学性能和电学性能等方面的质量。
四、检测与监控技术的应用为了确保产品质量的稳定和一致性,化学机械抛光过程中的检测与监控技术至关重要。
抛光后常见表面缺陷分类及产生原因
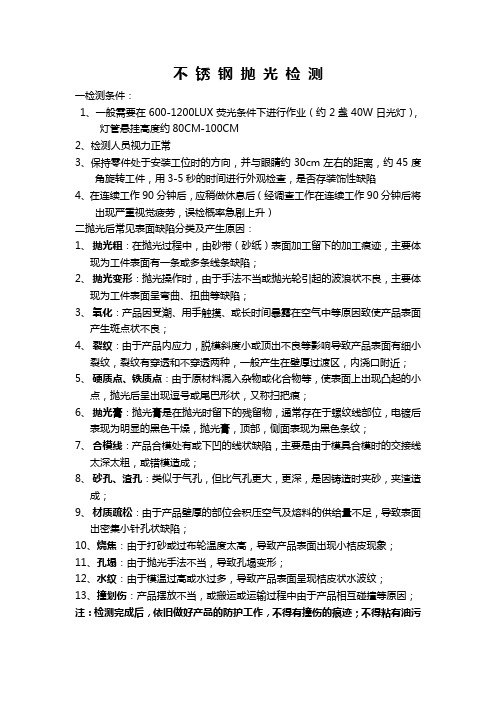
不锈钢抛光检测一检测条件:1、一般需要在600-1200LUX荧光条件下进行作业(约2盏40W日光灯),灯管悬挂高度约80CM-100CM2、检测人员视力正常3、保持零件处于安装工位时的方向,并与眼睛约30cm左右的距离,约45度角旋转工件,用3-5秒的时间进行外观检查,是否存装饰性缺陷4、在连续工作90分钟后,应稍做休息后(经调查工作在连续工作90分钟后将出现严重视觉疲劳,误检概率急剧上升)二抛光后常见表面缺陷分类及产生原因:1、抛光粗:在抛光过程中,由砂带(砂纸)表面加工留下的加工痕迹,主要体现为工件表面有一条或多条线条缺陷;2、抛光变形:抛光操作时,由于手法不当或抛光轮引起的波浪状不良,主要体现为工件表面呈弯曲、扭曲等缺陷;3、氧化:产品因受潮、用手触摸、或长时间暴露在空气中等原因致使产品表面产生斑点状不良;4、裂纹:由于产品内应力,脱模斜度小或顶出不良等影响导致产品表面有细小裂纹,裂纹有穿透和不穿透两种,一般产生在壁厚过渡区,内浇口附近;5、硬质点、铁质点:由于原材料混入杂物或化合物等,使表面上出现凸起的小点,抛光后呈出现逗号或尾巴形状,又称扫把痕;6、抛光膏:抛光膏是在抛光时留下的残留物,通常存在于螺纹线部位,电镀后表现为明显的黑色干燥,抛光膏,顶部,侧面表现为黑色条纹;7、合模线:产品合模处有或下凹的线状缺陷,主要是由于模具合模时的交接线太深太粗,或错模造成;8、砂孔、渣孔:类似于气孔,但比气孔更大,更深,是因铸造时夹砂,夹渣造成;9、材质疏松:由于产品壁厚的部位会积压空气及熔料的供给量不足,导致表面出密集小针孔状缺陷;10、烧焦:由于打砂或过布轮温度太高,导致产品表面出现小桔皮现象;11、孔塌:由于抛光手法不当,导致孔塌变形;12、水纹:由于模温过高或水过多,导致产品表面呈现桔皮状水波纹;13、撞划伤:产品摆放不当,或搬运或运输过程中由于产品相互碰撞等原因;注:检测完成后,依旧做好产品的防护工作,不得有撞伤的痕迹;不得粘有油污。
- 1、下载文档前请自行甄别文档内容的完整性,平台不提供额外的编辑、内容补充、找答案等附加服务。
- 2、"仅部分预览"的文档,不可在线预览部分如存在完整性等问题,可反馈申请退款(可完整预览的文档不适用该条件!)。
- 3、如文档侵犯您的权益,请联系客服反馈,我们会尽快为您处理(人工客服工作时间:9:00-18:30)。
有关铝及铝合金材料化学抛光中出现的缺陷及其纠正措施是在生产的发展过程中不断总结完善的。
现以磷酸" 硫酸" 硝酸的化学抛光生产过程中常见的缺陷和纠正措施归纳如下。
(1)光亮度不足。
这是化学抛光中最关心的事情。
光亮度没有达到预期的目标,其原因可从特殊铝材的生产工艺和化学抛光工艺这两方面分析。
有关特殊铝材的生产工艺已经有详细的论述。
建议采用铝纯度99.70%.及其以上级别的铝锭,来生产特殊铝材;铝材加工工艺中质量控制为化学抛光得到高光亮度表面奠定基础,例如铝—镁合金
5056(A199.98Mgl)是用纯度为99.99%的精铝锭生产而成的。
化学抛光后,具有很高的光亮度。
槽液控制中硝酸含量不足,会使表面光亮度不足,其表面可能过多地附着一层铜;硝酸含量太高,铝材表面形成彩虹膜,会使表面模糊或不透明,还引起光亮度不足;化学抛光时间不足,温度不够,搅拌不充分,槽液老化等也会使化学抛光表面光亮度不足。
槽液的相对密度较大,防止铝材浮出抛光槽液的液面,致使上部铝材光亮度不足。
水的影响造成光亮度不足,往往容易被忽视。
最好用干燥的铝材进入化学抛光槽液,杜绝水分的带入。
(2)白色附着物。
该缺陷的形貌为化学抛光后的铝材表面上附着有一层白色的沉积物,且分布不均匀,附着物底部的铝材表面有可能被腐蚀。
通常,该缺陷是因为化学抛光槽液中溶铝量太高所致,如果化学抛光槽液的相对密度在"#$% 以上,可以得到进一步证实。
则需采取措施调整槽液中的溶铝量到正常的范围内。
(3)表面粗糙。
化学抛光后的铝材表面出现粗糙现象。
该缺陷可能是在槽液中硝酸含量过高,酸性浸蚀造成的;若槽液中铜含量也高,则表面粗糙现象将会更严重。
通常,若槽液中硝酸含量过高,化学抛光反应剧烈,有“沸腾”的现象产生。
若硝酸含量正常,铜含量偏高,则水洗后的铝材表面上附着有一层很明显的金属铜的特征颜色。
如果铜的特征颜色很深,则表明槽液中的铜含量偏高,应采取措施调整硝酸与铜的含量达到正常的范围内。
如果添加剂中含铜量高,则应适当少加;如果槽液中的铜来自于含铜铝材的化学抛光,则采取措施添加不含铜的添加剂或调整槽液。
如果铝材内部组织缺陷引起表面粗糙:铸造状态组织,如铸造或压铸的铝工件;铝材晶粒细化不充分及疏松、夹渣等缺陷;加工过程中变形量不充分、松枝状花纹等缺陷造成表面粗糙,则由提高铝材内部质量来完成。
因此,铝材的生产工艺对提高化学抛光的表面质量显得尤为重要。
(4)转移性浸蚀。
该缺陷发生在铝材化学抛光完成后转移到水洗的过程中,主要是由铝材转移迟缓造成的。
对该缺陷进一步的确认,化学抛光后的铝
材表面出现光亮度偏低,并带有一些浅蓝色。
也有可能槽液中硫酸含量偏高协同所致。
铝材从化学抛光槽液中提升出来,那么热的抛光槽液仍在表面起剧烈的反应,硝酸消耗最快;若转移迟缓,甚至水洗过程中搅拌不充分都会出现该缺陷。
因此,铝材化学抛光完成后,应迅速转移到水洗槽中水洗,并充分搅拌水洗干净。
(5)点腐蚀。
该类缺陷通常是在铝材表面上由气体累积,形成气穴,产生点腐蚀;或因硝酸含量偏低或与铜含量偏低一起造成的。
根据具体情况,确因气体累积所致,则应合理装料,增加工件倾斜度,加强搅拌尽快让气体逸出。
夹具应选择正确位置夹紧,不能夹在装饰面上,不宜阻碍气体逸出。
如果铝材表面化学清洗不充分,也会引起点腐蚀。
如果铝材表面已经有浅表腐蚀缺陷或烤干的乳液斑痕,则会加剧该类缺陷的产生。
应事前采取措施消除这样的缺陷并加强铝材的表面质量控制。
如果确认硝酸等含量偏低,则应及时补加到规定的范围内。