主轴加工工艺
车床主轴的加工工艺
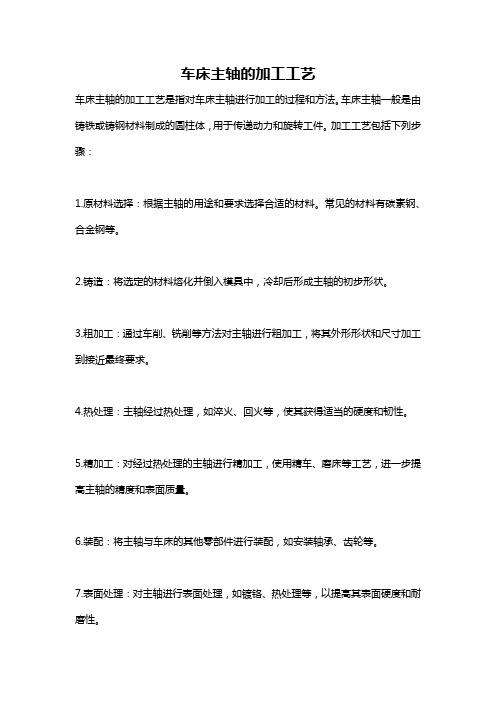
车床主轴的加工工艺
车床主轴的加工工艺是指对车床主轴进行加工的过程和方法。
车床主轴一般是由铸铁或铸钢材料制成的圆柱体,用于传递动力和旋转工件。
加工工艺包括下列步骤:
1.原材料选择:根据主轴的用途和要求选择合适的材料。
常见的材料有碳素钢、合金钢等。
2.铸造:将选定的材料熔化并倒入模具中,冷却后形成主轴的初步形状。
3.粗加工:通过车削、铣削等方法对主轴进行粗加工,将其外形形状和尺寸加工到接近最终要求。
4.热处理:主轴经过热处理,如淬火、回火等,使其获得适当的硬度和韧性。
5.精加工:对经过热处理的主轴进行精加工,使用精车、磨床等工艺,进一步提高主轴的精度和表面质量。
6.装配:将主轴与车床的其他零部件进行装配,如安装轴承、齿轮等。
7.表面处理:对主轴进行表面处理,如镀铬、热处理等,以提高其表面硬度和耐磨性。
8.检测:对加工完成的主轴进行检测,包括尺寸、形状、硬度等的检测,确保其达到设计要求。
以上是车床主轴加工的一般工艺流程,具体的加工工艺还会根据不同的要求和设计进行调整和改进。
C6150车床主轴箱箱体加工工艺及工装夹具设计

C6150车床主轴箱箱体加工工艺及工装夹具设计1.C6150车床主轴箱箱体加工工艺主轴箱箱体一般由铸铁材料制成,其加工工艺主要包括以下几个步骤:(1)铸造准备:对铸铁材料进行熔炼、净化和浇铸前的处理,确保铸件质量。
(2)铸件浇铸:将熔化的铸铁材料倒入模具中,使其冷却、凝固成型。
(3)铸件脱模:待铸件冷却后,从模具中取出,进行清理和修整。
(4)精密加工:对铸件进行加工,包括切割、铣削、钻孔等工序,以使得箱体尺寸和形状精确到达要求。
(5)表面处理:对箱体表面进行打磨、抛光,以提高外观质量。
(6)检测和装配:对加工好的主轴箱箱体进行检测,确保质量达到要求,然后进行组装。
在主轴箱箱体的加工过程中,合理设计工装夹具可以提高加工效率和加工质量,减少劳动强度。
(1)定位夹具设计:主要用于确定箱体的位置和角度,以保证加工精度。
定位夹具可以根据箱体形状和尺寸设计,一般采用刚性夹具,如V型块。
(2)夹紧夹具设计:用于夹紧箱体,以防止其在加工过程中发生松动或位移。
夹紧夹具可以采用螺栓和垫圈进行固定,或者采用气动或液压夹紧装置。
(3)切削夹具设计:用于加工箱体的切削过程,包括刀具和刀架的选择和安装。
切削夹具要根据加工要求和箱体材料的切削特性来设计,以保证加工质量和效率。
(4)保护夹具设计:用于保护箱体的外表面和内孔。
保护夹具可以采用橡胶垫和保护套等材料进行设计,以确保箱体不被切削工具碰伤。
(5)检测夹具设计:用于检测箱体的尺寸和形状,以确保其符合加工要求。
检测夹具可以采用测量工具和传感器等设备进行设计,以确保检测的准确性和可靠性。
总之,C6150车床主轴箱箱体加工工艺和工装夹具设计是车床加工中的重要环节,可以通过合理的工艺和夹具设计来提高加工效率和加工质量。
主轴的加工工艺路线
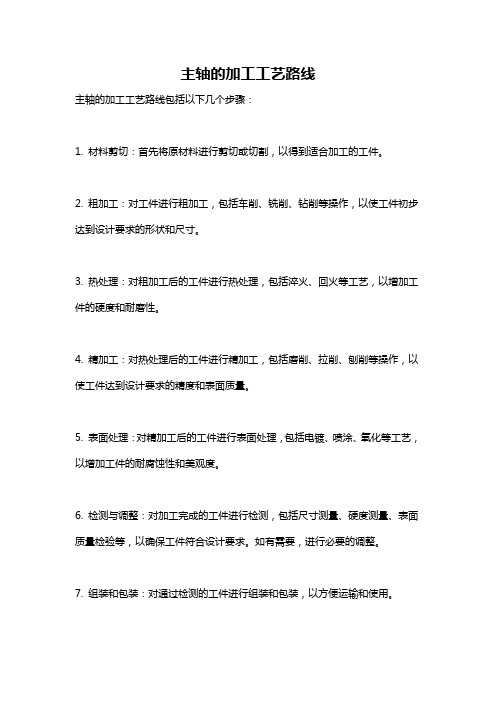
主轴的加工工艺路线
主轴的加工工艺路线包括以下几个步骤:
1. 材料剪切:首先将原材料进行剪切或切割,以得到适合加工的工件。
2. 粗加工:对工件进行粗加工,包括车削、铣削、钻削等操作,以使工件初步达到设计要求的形状和尺寸。
3. 热处理:对粗加工后的工件进行热处理,包括淬火、回火等工艺,以增加工件的硬度和耐磨性。
4. 精加工:对热处理后的工件进行精加工,包括磨削、拉削、刨削等操作,以使工件达到设计要求的精度和表面质量。
5. 表面处理:对精加工后的工件进行表面处理,包括电镀、喷涂、氧化等工艺,以增加工件的耐腐蚀性和美观度。
6. 检测与调整:对加工完成的工件进行检测,包括尺寸测量、硬度测量、表面质量检验等,以确保工件符合设计要求。
如有需要,进行必要的调整。
7. 组装和包装:对通过检测的工件进行组装和包装,以方便运输和使用。
8. 质量控制:对整个加工过程进行质量控制,包括使用符合要求的设备和工具、制定合理的工艺流程、操作规范等,以确保加工出的主轴达到设计和客户要求的质量标准。
45钢车床主轴加工工艺路线
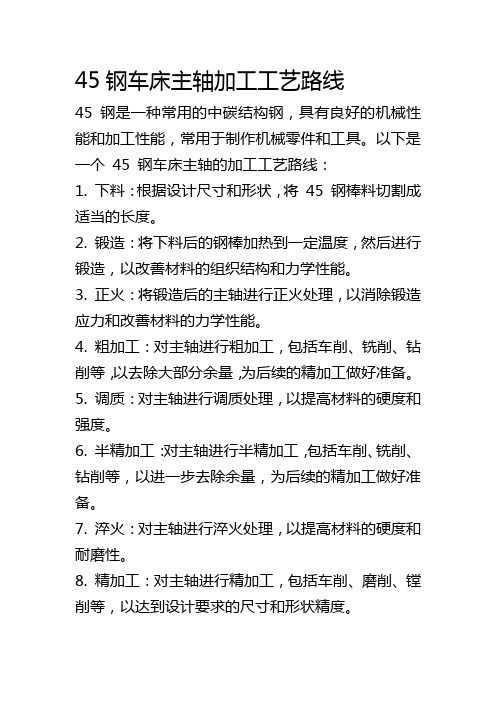
45钢车床主轴加工工艺路线
45 钢是一种常用的中碳结构钢,具有良好的机械性能和加工性能,常用于制作机械零件和工具。
以下是一个45 钢车床主轴的加工工艺路线:
1. 下料:根据设计尺寸和形状,将45 钢棒料切割成适当的长度。
2. 锻造:将下料后的钢棒加热到一定温度,然后进行锻造,以改善材料的组织结构和力学性能。
3. 正火:将锻造后的主轴进行正火处理,以消除锻造应力和改善材料的力学性能。
4. 粗加工:对主轴进行粗加工,包括车削、铣削、钻削等,以去除大部分余量,为后续的精加工做好准备。
5. 调质:对主轴进行调质处理,以提高材料的硬度和强度。
6. 半精加工:对主轴进行半精加工,包括车削、铣削、钻削等,以进一步去除余量,为后续的精加工做好准备。
7. 淬火:对主轴进行淬火处理,以提高材料的硬度和耐磨性。
8. 精加工:对主轴进行精加工,包括车削、磨削、镗削等,以达到设计要求的尺寸和形状精度。
9. 珩磨:对主轴进行珩磨处理,以提高表面质量和精度。
10. 检验:对主轴进行检验,以确保其符合设计要求和质量标准。
11. 包装:对主轴进行包装,以方便运输和储存。
需要注意的是,具体的加工工艺路线可能因不同的加工要求和设备条件而有所不同,以上仅为参考。
同时,在加工过程中还需要注意安全和环保问题。
电机主轴加工工艺

电机主轴加工工艺电机主轴加工工艺是电机制造过程中不可或缺的一环。
主轴作为电机的核心部件之一,其加工工艺直接关系到电机的使用效果和寿命。
本文将从主轴加工的工艺流程、加工方法和注意事项三个方面进行探讨。
一、主轴加工的工艺流程1.原材料选购主轴加工的第一步是原材料的选购。
通常情况下,主轴的材质要求为优质合金钢或不锈钢。
原材料的选购要求材质均匀、无气孔、无裂纹等缺陷。
2.粗加工粗加工是主轴加工的第二步。
主要的粗加工方法有车削、铣削、钻削等。
粗加工时要注意加工精度和表面光洁度。
3.热处理热处理是主轴加工的重要步骤之一。
通过热处理可以改善主轴的机械性能和物理性能,并且可以提高主轴的硬度和耐磨性。
4.精加工经过热处理后的主轴需要进行精加工。
主要的精加工方法有磨削、拉削、镗削等。
精加工时要注意加工精度和表面光洁度。
5.表面处理表面处理是主轴加工的最后一步。
通过表面处理可以提高主轴的耐腐蚀性和美观度。
主要的表面处理方法有喷漆、电镀、阳极氧化等。
二、主轴加工的方法1.车削法车削法是主轴加工中最常用的一种方法。
其优点是加工精度高、效率高、成本低。
但是需要注意的是车削法容易产生划痕和表面粗糙度较高的问题。
2.磨削法磨削法是主轴加工中另一种常用的方法。
其优点是加工精度高、表面光洁度高、不易产生划痕等问题。
但是磨削法的成本较高,加工效率也较低。
3.拉削法拉削法是主轴加工中一种比较新颖的方法。
其优点是加工效率高、表面光洁度高、不易产生划痕等问题。
但是需要注意的是拉削法需要专门的设备和技术,成本较高。
三、主轴加工的注意事项1.加工前要对原材料进行检查在加工前要对原材料进行检查,排除材料的缺陷和不合格问题。
2.加工时要注意加工精度和表面光洁度加工时要注意加工精度和表面光洁度,尽可能减少划痕和表面粗糙度。
3.热处理时要注意温度和时间的控制热处理时要注意温度和时间的控制,以确保主轴的机械性能和物理性能得到有效的改善。
4.表面处理时要注意材料的选择和表面光洁度表面处理时要注意材料的选择和表面光洁度,以确保主轴的耐腐蚀性和美观度得到有效的提高。
电机主轴加工工艺

电机主轴加工工艺1. 引言电机主轴是电机的核心部件,其加工工艺直接影响电机的性能和质量。
本文将详细介绍电机主轴的加工工艺,包括材料选择、加工方法、表面处理等方面内容。
2. 材料选择电机主轴通常采用高强度、高硬度的合金钢作为材料。
常见的材料有45#钢、40Cr、42CrMo等。
材料选择需要综合考虑电机使用环境、承载能力和加工难度等因素。
3. 加工方法3.1 切削加工切削加工是电机主轴最常用的加工方法之一。
其常见的切削方式包括车削、铣削和钻削等。
具体步骤如下: 1. 车削:通过车床将材料转动起来,利用刀具对其进行切削。
2. 铣削:利用铣床或数控铣床进行切削,可实现复杂形状的加工。
3. 钻削:通过钻床或数控钻床进行孔径加工。
3.2 精密磨削精密磨削是电机主轴加工的重要环节,可提高主轴的加工精度和表面质量。
常见的磨削方法包括平面磨削、外圆磨削和内圆磨削等。
3.3 热处理电机主轴在加工完成后需要进行热处理,以提高其硬度和耐磨性。
常见的热处理方法有淬火、回火和表面渗碳等。
具体步骤如下: 1. 淬火:将主轴加热至临界温度,然后迅速冷却,以获得高硬度。
2. 回火:将淬火后的主轴再次加热至一定温度,并保持一段时间,然后冷却至室温。
此过程可减少主轴的脆性。
3. 表面渗碳:通过在主轴表面添加含碳物质,并进行加热处理,使其表层获得高硬度。
4. 表面处理为了提高电机主轴的耐腐蚀性和摩擦特性,常常需要进行表面处理。
常见的表面处理方法有镀铬、喷涂和氮化等。
1. 镀铬:利用电镀技术,在主轴表面形成一层铬镀层,增加其硬度和耐磨性。
2. 喷涂:通过喷涂工艺,在主轴表面形成一层耐磨涂层,提高其摩擦特性。
3. 氮化:将主轴加热至高温,并与氮气反应,使其表面形成氮化层,提高硬度和耐磨性。
5. 质量控制为了确保电机主轴的质量,需要进行严格的质量控制。
常见的质量控制方法包括尺寸检测、硬度检测和金相分析等。
1. 尺寸检测:通过三坐标测量仪、千分尺等工具对主轴的尺寸进行检测,确保其符合设计要求。
主轴的热处理工艺

主轴的热处理工艺主要包括粗加工阶段的正火或退火,半精加工阶段的调质热处理(淬火+高温回火),以及精加工阶段的淬火和回火等步骤。
在粗加工阶段,主轴通常会进行正火或退火处理。
这两种处理方式的目的都是消除锻造应力,细化晶粒,使金属组织均匀化,以利于切削加工。
退火的具体工艺为:加热温度Ac3+(30~50)℃,保温时间120min,冷却方式为随炉冷却。
正火的具体工艺为:加热温度Ac3+(30~50)℃,保温时间120min,冷却方式为空冷。
在半精加工阶段,主轴会进行调质热处理(淬火+高温回火)。
具体的热处理工艺为:870℃淬火,保温70min,油淬,500℃回火,保温100min,油淬。
如果调质热处理不当,可能会导致钢中存在较多的网络状、块状游离铁素体,从而使钢材的强度和冲击韧性下降。
因此,淬火温度偏低,回火温度过高是主要的不当操作。
淬火时冷却速度缓慢时,铁素体会从原奥氏体晶界优先析出,形成网状铁素体;钢在加热过程中,由于加热温度偏低或保温时间不足时,铁素体未完全溶于奥氏体中,淬火后形成块状游离铁素体。
在精加工阶段,主轴通常会进行淬火和回火处理。
淬火的具体工艺为:加热温度偏低,回火温度过高是主要的不当操作。
淬火时冷却速度缓慢时,铁素体会从原奥氏体晶界优先析出,形成网状铁素体;钢在加热过程中,由于加热温度偏低或保温时间不足时,铁素体未完全溶于奥氏体中,淬火后形成块状游离铁素体。
需要注意的是,不同的主轴材料和热处理工艺会产生不同的效果。
例如,对于45钢制造的主轴,其工艺路线为下料→锻造→正火→粗加工→调质→半精加工(花键除外)→局部淬火(内外圆锥面)+低温回火→粗磨→铣花键→花键感应淬火+低温回火→精磨。
整体调质硬度可达到220~250HBS;内外圆锥面采用盐。
以上就是主轴的热处理工艺的基本内容,具体的工艺可能会根据主轴的材质、形状尺寸和使用环境等因素有所不同。
主轴工艺

机床主轴的加工工艺流程
(1)整体淬火主轴:下料→锻造→正火或退火→粗机械加工(粗车,留精车量为3~6mm)
→去应力退火或调质处理→精机械加工(精车,留磨量为0.4~0.8mm)→整体淬火→粗磨(留精磨量为0.15~0.20mm)→低温时效→精磨→成员。
对于开关简单、精度要求不高、不经锻造及不需预先热处理及低温时效时,其加工工艺流程可简化为:下料→切削加工→淬硬→磨削至尺寸。
(2)渗碳淬火主轴:下料→锻造→正火→精机械加工(精车,留磨量子为0.40~0.80mm)
→渗碳→经车削加工去除非需渗碳部位→淬火、低温回火→精磨(留下精磨量为0.15~0.20mm)→低温时效→精磨至尺寸。
(3)表面淬火主轴:下料→锻造→退火或正火→粗机械加工(粗车,留粗量子为3~6mm)
→调质处理→精机械加工(精车,留磨量0.5~0.6mm)→表面淬火、低温回火→粗磨(留下精磨量为0.15~0.25mm)→低温时效→精磨至尺寸。
对于形状简单、精度要求不高、不需锻造、预先热处理及低温时效时,其加工工艺流程可简化为:下料→粗机械加工(粗车)→调质处理→精机械加工(精车)→表面淬火→磨至尺寸。
(4)渗氮主轴:下料→锻造→退火或正火→粗机械加工(粗车,留粗量子为4~6mm)→
调质处理(切割样品检查金相组织)→精机械加工(精车,留磨量0.9~1.0mm)→去应力退火→精磨(留下精磨量为0.06~0.10mm;非渗氮处每面留磨量0.40mm以上或镀镍等防渗层)→渗氮→精磨至尺寸。
应当说明,以上主轴,当精度要求很高时,还可适当增加去应力退火及低温时效次数。
X62W铣床主轴机械加工工艺规程与钻床夹具设计
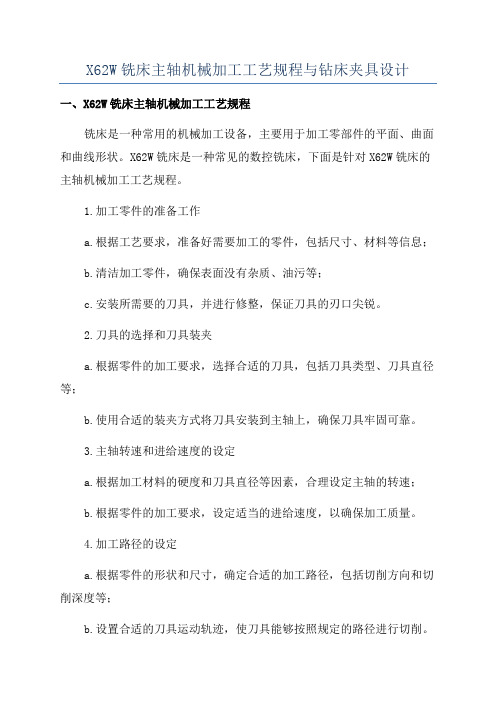
X62W铣床主轴机械加工工艺规程与钻床夹具设计一、X62W铣床主轴机械加工工艺规程铣床是一种常用的机械加工设备,主要用于加工零部件的平面、曲面和曲线形状。
X62W铣床是一种常见的数控铣床,下面是针对X62W铣床的主轴机械加工工艺规程。
1.加工零件的准备工作a.根据工艺要求,准备好需要加工的零件,包括尺寸、材料等信息;b.清洁加工零件,确保表面没有杂质、油污等;c.安装所需要的刀具,并进行修整,保证刀具的刃口尖锐。
2.刀具的选择和刀具装夹a.根据零件的加工要求,选择合适的刀具,包括刀具类型、刀具直径等;b.使用合适的装夹方式将刀具安装到主轴上,确保刀具牢固可靠。
3.主轴转速和进给速度的设定a.根据加工材料的硬度和刀具直径等因素,合理设定主轴的转速;b.根据零件的加工要求,设定适当的进给速度,以确保加工质量。
4.加工路径的设定a.根据零件的形状和尺寸,确定合适的加工路径,包括切削方向和切削深度等;b.设置合适的刀具运动轨迹,使刀具能够按照规定的路径进行切削。
5.加工过程中的操作注意事项a.加工过程中要注意切削液的使用,以减少切削温度,保护工件表面;b.加工过程中要及时清理切削屑,防止其对工件和刀具造成损伤;c.加工过程中要始终保持专注,确保操作的安全和准确性。
6.完成加工后的处理a.加工完成后,进行清洁和检查,确保零件表面没有切削渣等残留物;b.完成零件的加工记录,包括加工时间、精度等信息。
钻床夹具是用于夹持工件,使其保持稳定位置并完成钻削加工的工具。
以下是针对钻床设计的夹具的设计要点。
1.夹具型式的选择a.根据工件形状和加工要求选择合适的夹具型式,如钳夹、原理滑块夹、气动滑块夹等;b.根据工件的特性,选择合适的夹持方式,如上夹、侧夹、角夹等。
2.夹具的结构设计a.夹具的结构应该简单、刚性强,以确保工件在夹持过程中的稳定性;b.夹具应根据工件的形状设计合适的夹持方式和夹具构造,使其能够夹持工件的有关部位,同时不影响钻削加工。
数控车床主轴加工工艺

表1 主轴加工工艺过程
序号 工序名称 1 2 3 4 5 6 7 8 9 10 11 12 13 14 15 16 17 18 备料 钻 车 钻 车 热处理 车 钻 钳 热处理 车 磨 磨 铣 车 磨 热处理 磨 工序内容 锻造-热处理(正火) 以小外圆找正划钻小端顶尖孔 粗车各外圆(见图2) 钻通孔钻成φ85 小端孔角2×30°,圆度φ0.05,各外圆,台 阶面留量1-1.5 调质 各外园,Ra0.4,Ra0.8,Ra1.6各外圆端面及螺 纹外圆,Ra0.4,Ra0.8,Ra1.6端面留量 钻锪铰各孔(钻模) 去毛剌 淬火 总长左端面及M105×2-6H一次成品,上紧 丝堵 上锥堵研好中心孔,Ra0.4,Ra0.8,Ra1.6各外 圆,端面,1:12锥面,留精磨量 7°7′30″锥面,公制120锥孔,留磨量 各键槽成品 拧主轴螺母配车各螺纹成品并成对做标记 半精磨各外圆,端面,两锥面,公制100锥 孔留磨量,倒各角 时效 设备 摇臂钻Z35 C630 深孔钻 C630 热处理 C620 摇臂钻 钳 热处理 C620 MQ1350 M131W X52K C620 M131W 热处理
0.8 0.8 1.6 B 0.8
φ150h6
传动零件传递动力和承受各种负荷,以进行切削加工, 另一方面又要保证安装在主轴上的工件或刀具有较高的 回转精度。主轴加工精度及其装配精度将直接影响到机 床精度和使用寿命,数控车床主轴由于精度要求高于一 般主轴,加工更加困难,一直是国内外各数控机床制造厂 加工的关键。 我公司是卧式数控车床的制造企业,经过多年的探 索、研究、实践,我们对数控车床主轴的加工积累了一 定的经验,主轴加工精度达到了一定水平,取得了可喜 的成绩,现以我公司生产的一种卧式数控车床零件主轴 为例,介绍主轴加工工艺的制订要点。 2 2.1 零件图及精度要求 数控车床主轴零件(见图1) 主轴材料45#钢;毛坯形式:锻件。
主轴轴类零件加工工艺流程

主轴轴类零件加工工艺流程下载温馨提示:该文档是我店铺精心编制而成,希望大家下载以后,能够帮助大家解决实际的问题。
文档下载后可定制随意修改,请根据实际需要进行相应的调整和使用,谢谢!并且,本店铺为大家提供各种各样类型的实用资料,如教育随笔、日记赏析、句子摘抄、古诗大全、经典美文、话题作文、工作总结、词语解析、文案摘录、其他资料等等,如想了解不同资料格式和写法,敬请关注!Download tips: This document is carefully compiled by theeditor.I hope that after you download them,they can help yousolve practical problems. The document can be customized andmodified after downloading,please adjust and use it according toactual needs, thank you!In addition, our shop provides you with various types ofpractical materials,such as educational essays, diaryappreciation,sentence excerpts,ancient poems,classic articles,topic composition,work summary,word parsing,copy excerpts,other materials and so on,want to know different data formats andwriting methods,please pay attention!主轴轴类零件的精密加工工艺流程详解在机械制造领域,主轴轴类零件是设备运行的核心部分,其精度和质量直接影响到设备的性能和寿命。
车床主轴加工工艺流程

车床主轴加工工艺流程
一、原料准备
1.1 根据设计要求,选择合适的材料,如优质钢、合金钢等,确保其具有良好的机械性能和稳定性。
1.2 对原料进行质量检查,确保无缺陷、无锈蚀、无油污。
二、粗加工
2.1 对原料进行初步加工,去除多余部分,形成主轴的大致形状。
2.2 对粗加工后的主轴进行去毛刺、倒角处理,以确保后续加工的顺利进行。
三、半精加工
3.1 对主轴进行半精加工,进一步细化主轴的外形,为后续的热处理和精加工做准备。
3.2 在半精加工过程中,应确保主轴的几何尺寸、形位公差等符合设计要求。
四、热处理
4.1 对主轴进行热处理,如淬火、回火等,以提高其机械性能和稳定性。
4.2 热处理后,对主轴进行冷却、矫直等处理,以确保其直线度和几何精度。
五、精加工
5.1 对主轴进行精加工,如切削、磨削等,以进一步细化主轴的表面质量和几何精度。
5.2 在精加工过程中,应采用合适的切削参数和磨削参数,以确保主轴的加工质量和效率。
六、装配
6.1 根据设计要求,将主轴与其他零部件进行装配,如轴承、密封件等。
6.2 在装配过程中,应确保各零部件的配合精度和安装牢固性。
七、检测
7.1 对装配后的主轴进行检测,如几何尺寸、形位公差、表面粗糙度等。
7.2 检测合格后,应进行必要的标记和记录。
八、包装
8.1 根据产品特点和客户要求,选择合适的包装材料和方式。
电机主轴加工工艺
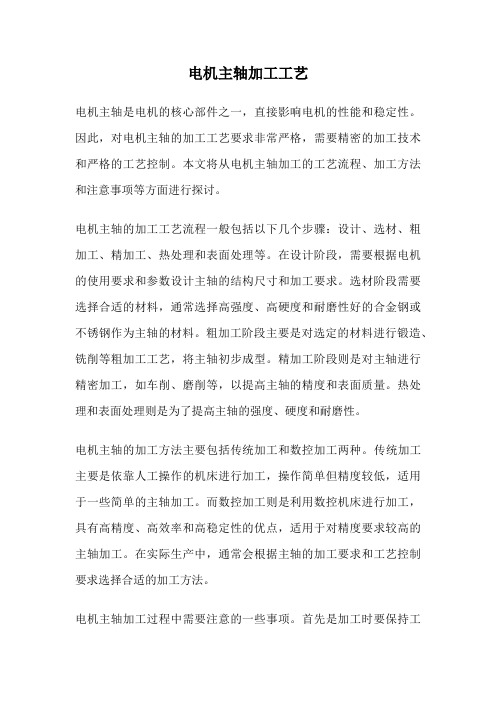
电机主轴加工工艺电机主轴是电机的核心部件之一,直接影响电机的性能和稳定性。
因此,对电机主轴的加工工艺要求非常严格,需要精密的加工技术和严格的工艺控制。
本文将从电机主轴加工的工艺流程、加工方法和注意事项等方面进行探讨。
电机主轴的加工工艺流程一般包括以下几个步骤:设计、选材、粗加工、精加工、热处理和表面处理等。
在设计阶段,需要根据电机的使用要求和参数设计主轴的结构尺寸和加工要求。
选材阶段需要选择合适的材料,通常选择高强度、高硬度和耐磨性好的合金钢或不锈钢作为主轴的材料。
粗加工阶段主要是对选定的材料进行锻造、铣削等粗加工工艺,将主轴初步成型。
精加工阶段则是对主轴进行精密加工,如车削、磨削等,以提高主轴的精度和表面质量。
热处理和表面处理则是为了提高主轴的强度、硬度和耐磨性。
电机主轴的加工方法主要包括传统加工和数控加工两种。
传统加工主要是依靠人工操作的机床进行加工,操作简单但精度较低,适用于一些简单的主轴加工。
而数控加工则是利用数控机床进行加工,具有高精度、高效率和高稳定性的优点,适用于对精度要求较高的主轴加工。
在实际生产中,通常会根据主轴的加工要求和工艺控制要求选择合适的加工方法。
电机主轴加工过程中需要注意的一些事项。
首先是加工时要保持工艺参数的稳定,包括刀具的选择、切削速度、进给速度等,以确保加工质量和效率。
其次是要注意加工时的冷却和润滑,以防止主轴因高温而变形或损坏。
另外,还要注意加工过程中的刀具磨损情况,定期更换和修磨刀具,以保证加工质量和加工效率。
此外,还要对加工后的主轴进行质量检测和表面质量检查,以确保主轴的质量和性能达到要求。
总的来说,电机主轴的加工工艺对电机的性能和稳定性有着重要影响,需要严格控制工艺流程、选择合适的加工方法和注意加工过程中的细节。
只有这样,才能保证电机主轴的质量和性能达到要求,确保电机的正常运行和稳定性。
希望本文对电机主轴加工工艺有所帮助,谢谢阅读!。
车床主轴加工工艺过程说明书

题目:车床主轴加工工艺过程姓名:班级学号:指导教师:摘要在机械领域中,车床是应用最广泛为、最为频繁的一种机床,它的应用非常的普遍。
所以它的加工精度就极其的重要,工件能否到达加工要求就取决于车车床本身的精度,而决定车床加工质量的就是它的主轴。
CA6140车床主轴是把旋转运动及扭矩通过主轴端部的夹具传递给工件和刀具,要求有很高的强度及回转精度,其结构为空心阶梯轴,外圆外表有花键、电键等功能槽及螺纹。
故,生产CA6140主轴的工艺以及加工方法,对整个机械加工来说都有着非常重要的作用,本文详细阐述了CA6140主轴的工艺过程、加工余量、切削用量以及生产中所涉及的重要夹具关键词车床;主轴;旋转运动;公差AbstractIn the machine realm, the lather is an application most extensively is,the most multifarious tool machine, especially the CA6140 lathers, its application is very widespread.So it processes accuracy for the very importance, the work piece the accuracy that can attain to process to request and then be decided by the car lather, but decide the CA6140 lathers processing quality is its principal axis.The CA6140 lather principal axis is revolve sport and twist to carry a department through a principal axis of the tongs deliver to have for the work piece and the knife, requesting very high strength and turning round accuracy, its structure is a hollow stairs stalk, outside circle the surface contain the function slots, such as HUA JIAN4 and the electricity key...etc. and thread.Past, produce the craft of the CA6140 principal axises and process a method, process to the whole machine to say that all have a count for much function, this text elaborates the craft processes of the CA6140 principal axises,process amount of remaining and slices to pare dosage and produces in detail medium the important tongs involve。
主轴硬度为hrc55的加工工艺

主题:主轴硬度为hrc55的加工工艺一、概述随着机械加工行业的发展,对于工件的加工精度和加工效率要求越来越高。
而主轴作为机床加工中的核心部件,其硬度对加工工艺和加工质量有着至关重要的影响。
本文将围绕主轴硬度为hrc55的加工工艺展开讨论。
二、主轴硬度对加工工艺的影响1. 主轴硬度为hrc55的特点主轴硬度为hrc55意味着其具有一定的硬度和耐磨性,能够满足大多数金属加工的需求。
硬度为hrc55的主轴在加工过程中也有一定的韧性,能够避免加工时的易碎性问题。
2. 主轴硬度对刀具选择的影响在选择刀具的时候,需要考虑主轴的硬度。
对于主轴硬度为hrc55的加工工艺,需要选择耐磨性好的刀具,并且要求刀具具有良好的切削性能,以确保加工过程中的切削效果和加工精度。
3. 主轴硬度对加工参数的影响针对主轴硬度为hrc55的加工工艺,需要根据不同的加工材料和加工形式选择合适的加工参数。
对于铝合金材料的加工,需要采用较高的切削速度和较小的切削深度,以确保刀具的寿命和加工的表面质量;而对于不锈钢材料的高速铣削,需要采用较高的进给速度和切削速度,以提高加工效率和降低加工成本。
4. 主轴硬度对冷却润滑的要求在主轴硬度为hrc55的加工工艺中,冷却润滑系统也显得尤为重要。
良好的冷却润滑系统能够有效的降低加工温度、延长刀具寿命,同时也能够减少加工时产生的热变形和残余应力,从而提高加工精度和表面质量。
5. 主轴硬度对加工工艺的稳定性要求硬度为hrc55的主轴在加工过程中,需要具有较高的加工稳定性,能够满足长时间高速加工的需求。
对于主轴硬度为hrc55的加工工艺,需要提高主轴的动平衡和静平衡性能,保证加工时的稳定性。
三、适合主轴硬度为hrc55的加工工艺1. 铣削加工铣削加工是目前主要的金属加工方式之一,适合主轴硬度为hrc55的加工工艺。
通过合理选择刀具和加工参数,可以获得较高的加工效率和加工精度。
2. 钻孔加工钻孔加工是将圆柱形刀具在工件上进行旋转运动,以切削出孔洞的加工方式,适合主轴硬度为hrc55的加工工艺。
主轴的机械加工工艺

主轴的机械加工工艺嘿,朋友们!今天咱来聊聊主轴的机械加工工艺,这可真是个有趣又重要的事儿啊!你想想看,那主轴就好比是机器的心脏,它得足够强壮、精准,才能让整个机器顺畅地运转起来呀!那怎么才能把主轴加工得完美呢?首先得选好材料,这就跟盖房子打地基一样重要。
要是材料不行,后面再怎么努力也是白搭呀!得找那种结实耐用、性能优良的材料,这样加工出来的主轴才可靠。
然后就是各种加工手段啦!车削、铣削、磨削等等,就像是给主轴做造型的魔法。
车削能让它初步成型,铣削能给它加上各种精细的特征,磨削呢,则让它变得光滑无比,就像打磨一块美玉一样。
在加工的过程中,可得注意精度啊!这可不是闹着玩的,差之毫厘谬以千里呀!就好像你走路,稍微偏一点可能就走到沟里去啦!加工主轴也是一样,尺寸、形状都得把握得死死的,不能有一点马虎。
还有啊,刀具的选择也很关键呢!不同的刀具就像是不同的画笔,能画出不同的效果。
选对了刀具,加工起来那叫一个事半功倍。
你说,要是主轴加工不好,那机器还能好好工作吗?就好比一个人心脏有毛病,那还能活蹦乱跳吗?肯定不行呀!所以说,这主轴的机械加工工艺可真是太重要啦!在实际操作中,师傅们得像对待宝贝一样对待主轴,每一个步骤都要小心翼翼。
这可不是随随便便就能搞定的事情,需要经验、技术,还需要那份认真负责的态度。
你看那些厉害的机器,不都是因为有了完美的主轴才能发挥出强大的威力吗?就像一辆跑车,要是发动机不行,再好看又有啥用呢?总之呢,主轴的机械加工工艺是一门大学问,需要我们不断地去学习、去探索。
只有这样,我们才能制造出更好、更强的机器,为我们的生活和工作带来更多的便利和进步。
这可不是我在吹牛哦,这是实实在在的道理呀!大家可得重视起来呀!。
电机主轴加工工艺
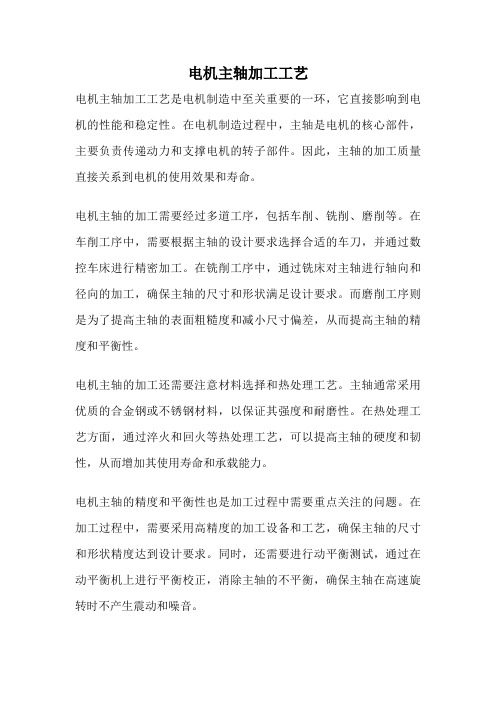
电机主轴加工工艺电机主轴加工工艺是电机制造中至关重要的一环,它直接影响到电机的性能和稳定性。
在电机制造过程中,主轴是电机的核心部件,主要负责传递动力和支撑电机的转子部件。
因此,主轴的加工质量直接关系到电机的使用效果和寿命。
电机主轴的加工需要经过多道工序,包括车削、铣削、磨削等。
在车削工序中,需要根据主轴的设计要求选择合适的车刀,并通过数控车床进行精密加工。
在铣削工序中,通过铣床对主轴进行轴向和径向的加工,确保主轴的尺寸和形状满足设计要求。
而磨削工序则是为了提高主轴的表面粗糙度和减小尺寸偏差,从而提高主轴的精度和平衡性。
电机主轴的加工还需要注意材料选择和热处理工艺。
主轴通常采用优质的合金钢或不锈钢材料,以保证其强度和耐磨性。
在热处理工艺方面,通过淬火和回火等热处理工艺,可以提高主轴的硬度和韧性,从而增加其使用寿命和承载能力。
电机主轴的精度和平衡性也是加工过程中需要重点关注的问题。
在加工过程中,需要采用高精度的加工设备和工艺,确保主轴的尺寸和形状精度达到设计要求。
同时,还需要进行动平衡测试,通过在动平衡机上进行平衡校正,消除主轴的不平衡,确保主轴在高速旋转时不产生震动和噪音。
电机主轴加工工艺还需要注重质量控制和检测。
在加工过程中,需要严格执行工艺流程和操作规程,确保每道工序的质量和精度。
同时,还需要进行尺寸检测、表面质量检查和功能测试,确保主轴的质量达到标准要求。
电机主轴加工工艺是电机制造中的关键环节,它直接影响到电机的性能和稳定性。
通过合理的工艺流程和严格的质量控制,可以确保电机主轴具有优良的加工质量和稳定性,从而提高电机的使用效果和寿命。
在未来的电机制造中,我们需要不断优化主轴加工工艺,推动电机制造技术的进步和发展。
- 1、下载文档前请自行甄别文档内容的完整性,平台不提供额外的编辑、内容补充、找答案等附加服务。
- 2、"仅部分预览"的文档,不可在线预览部分如存在完整性等问题,可反馈申请退款(可完整预览的文档不适用该条件!)。
- 3、如文档侵犯您的权益,请联系客服反馈,我们会尽快为您处理(人工客服工作时间:9:00-18:30)。
主轴加工工艺的研究与探讨
主轴的功用、精度:
1.功用:
在一般的金属切削机床中,主轴把旋转运动及扭矩通过主轴端部的夹具或刀具。
在工作中,主轴不但承受扭转力矩,而且承弯曲力矩。
所以要求机床主轴的扭转刚度和弯曲刚度都很高。
2.机床主轴精度:(机床精度的重要组成部分)
即输出旋转精度,也为主轴的工作表面精度。
下面仅真对主轴自身的关键精度而言:
1)主轴支承轴径、轴肩端面的精度:
●主轴支承轴径的制造精度(椭圆度、锥度、不同轴
度、不垂直度等)
●主轴轴肩端面对主轴回转轴心线的不垂直度
2)主轴工作表面的精度:
●内外锥面的尺寸精度、几何形状精度、光洁度和接触
精度;
●定心表面相对与支承轴径表面的同轴度;
●定位端面相对与支承轴径轴心线的垂直度。
注:机床主轴的工作表面指主轴的莫氏锥孔、轴端外锥或法蓝外圆等。
3.主轴材料、热处理及作用
材料:45#,65Mn,40Cr,38CrMoAl(氮化钢),20Cr或20Cr MnTi(渗碳钢)等
热处理:退火,正火,调质,高频淬火,渗碳,氮化,
热处理作用:提高主轴强度,刚性,表面硬度,及耐疲劳强
度、尺寸稳定性等综合机械性能。
退火及正火:降低材料硬度,改善切削加工性能,消除锻造
内应力,细化晶粒,并使金属组织均匀。