涡轮机匣加工技术研究
对机匣零件加工工艺的研究
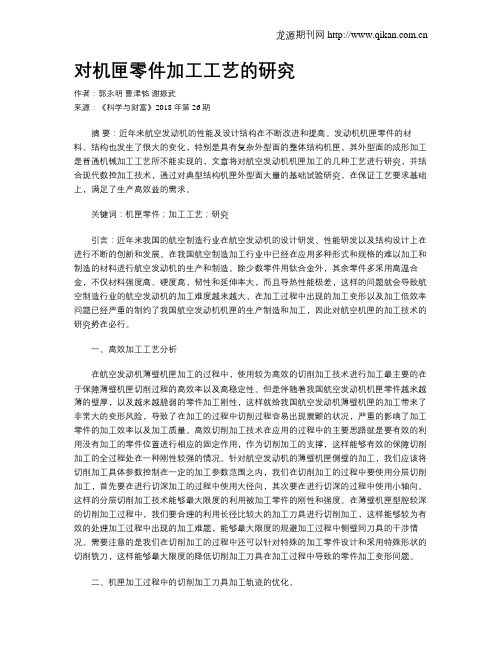
对机匣零件加工工艺的研究作者:郭永明曹津铭谢振武来源:《科学与财富》2018年第26期摘要:近年来航空发动机的性能及设计结构在不断改进和提高。
发动机机匣零件的材料、结构也发生了很大的变化,特别是具有复杂外型面的整体结构机匣,其外型面的成形加工是普通机械加工工艺所不能实现的,文章将对航空发动机机匣加工的几种工艺进行研究,并结合现代数控加工技术,通过对典型结构机匣外型面大量的基础试验研究,在保证工艺要求基础上,满足了生产高效益的需求。
关键词:机匣零件;加工工艺;研究引言:近年来我国的航空制造行业在航空发动机的设计研发、性能研发以及结构设计上在进行不断的创新和发展。
在我国航空制造加工行业中已经在应用多种形式和规格的难以加工和制造的材料进行航空发动机的生产和制造。
除少数零件用钛合金外,其余零件多采用高温合金,不仅材料强度高、硬度高,韧性和延伸率大,而且导热性能极差,这样的问题就会导致航空制造行业的航空发动机的加工难度越来越大,在加工过程中出现的加工变形以及加工低效率问题已经严重的制约了我国航空发动机机匣的生产制造和加工,因此对航空机匣的加工技术的研究势在必行。
一、高效加工工艺分析在航空发动机薄壁机匣加工的过程中,使用较为高效的切削加工技术进行加工最主要的在于保障薄壁机匣切削过程的高效率以及高稳定性。
但是伴随着我国航空发动机机匣零件越来越薄的壁厚,以及越来越脆弱的零件加工刚性,这样就给我国航空发动机薄壁机匣的加工带来了非常大的变形风险,导致了在加工的过程中切削过程容易出现震颤的状况,严重的影响了加工零件的加工效率以及加工质量。
高效切削加工技术在应用的过程中的主要思路就是要有效的利用没有加工的零件位置进行相应的固定作用,作为切削加工的支撑,这样能够有效的保障切削加工的全过程处在一种刚性较强的情况。
针对航空发动机的薄壁机匣侧壁的加工,我们应该将切削加工具体参数控制在一定的加工参数范围之内,我们在切削加工的过程中要使用分层切削加工,首先要在进行切深加工的过程中使用大径向,其次要在进行切深的过程中使用小轴向。
机匣加工工艺

机匣加工工艺机匣一般是一个圆柱形或圆锥形的薄壁筒体,主要起承力和包容作用,而且对不同段机匣的要求不一样。
涡轮机匣通常是带有安装边的圆柱形或截锥形壳体,其前后安装边分别与燃烧室机匣和动力涡轮前的中间机匣连接,涡轮机匣上作用有扭矩、轴向力、惯性力和内环压差力等。
近年来航空发动机的性能及设计结构在不断改进和提高。
随之而来,发动机机匣零件的材料、结构也发生了很大的变化,越来越多的难加工材料,像钛合金、高温合金、不锈钢、硬质合金以及复合材料等被采用。
机匣设计结构也越来越先进,整体结构机匣、单一机匣所具有的功能也越来越多,因此,机匣零件的制造成形难度也越来越大。
特别是具有复杂外型面的整体结构机匣,其外型面的成形加工是普通机械加工工艺所不能实现的,只有应用多轴数控加工技术才能实现复杂外型面的成形加工。
但在加工过程中存在着刀具费用高,加工效率低,设备占用量大。
针对多年来生产中的加工难题,寻求品质的提升、效率的提高、成本降低的途径和方法,运用特种加工技术——电火花加工技术和电解加工技术,同时结合现代数控加工技术,通过对典型结构机匣外型面大量的基础试验研究,取得了良好的加工效果,在保证工艺要求基础上,满足了生产高效益的需求。
多轴数控铣削机匣型面的成形,国内通常是通过在多轴数控铣削设备上加工完成的。
该零件外环形面共分二级,分布有二条环形凸缘,下部有1个纵向小凸缘,两个纵向凸缘对称分布。
由于机匣毛坯是自自锻件,加工余量很大,且零件材料难切削,为了保证尺寸加工精度和表面加工质量,防止加工后零件变形。
其外型面加工分层、分块进行,采取合理的走刀路径,采用对称的切削加工余量。
分几次走刀加工到最后尺寸的方法,以减少加工后的变形。
因此,该机匣加工划分三个主要阶段并附加特征工序热处理,以去除材料内应力,防止零件变形。
火花高效放电铣电火花高效放电铣加工技术原理。
电火花高效放电铣借鉴了数控铣削加工方式,采用简单的超长铜管做工具电极,由导向器导向,在工作中电极作高速旋转,在电极与工件之间施加高效高频脉冲电源,电流高达上百安培,对加工区施以冲、浸工作液进行有效冷却排屑,通过专用数控系统控制工件与电极之间的相对运动轨迹,在电极与工件之间产生高效脉冲放电,加工出所需工件的形状,实现零件复杂型面的高效去余量加工。
涡轮后机匣加工工艺优化
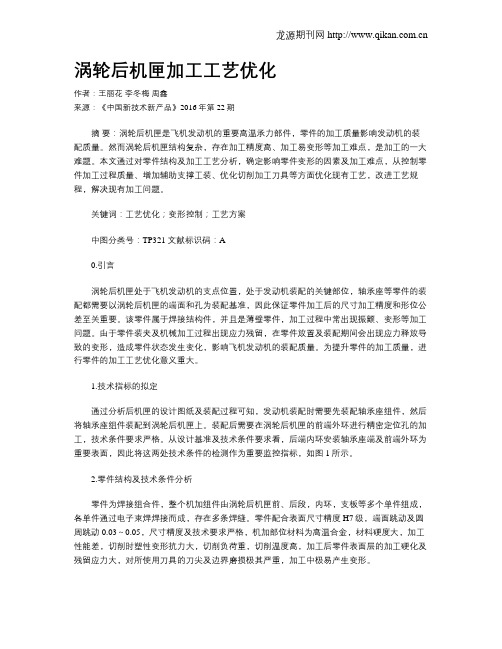
涡轮后机匣加工工艺优化作者:王丽花李冬梅周鑫来源:《中国新技术新产品》2016年第22期摘要:涡轮后机匣是飞机发动机的重要高温承力部件,零件的加工质量影响发动机的装配质量。
然而涡轮后机匣结构复杂,存在加工精度高、加工易变形等加工难点,是加工的一大难题。
本文通过对零件结构及加工工艺分析,确定影响零件变形的因素及加工难点,从控制零件加工过程质量、增加辅助支撑工装、优化切削加工刀具等方面优化现有工艺,改进工艺规程,解决现有加工问题。
关键词:工艺优化;变形控制;工艺方案中图分类号:TP321 文献标识码:A0.引言涡轮后机匣处于飞机发动机的支点位置,处于发动机装配的关键部位,轴承座等零件的装配都需要以涡轮后机匣的端面和孔为装配基准,因此保证零件加工后的尺寸加工精度和形位公差至关重要。
该零件属于焊接结构件,并且是薄壁零件,加工过程中常出现振颤、变形等加工问题。
由于零件装夹及机械加工过程出现应力残留,在零件放置及装配期间会出现应力释放导致的变形,造成零件状态发生变化,影响飞机发动机的装配质量。
为提升零件的加工质量,进行零件的加工工艺优化意义重大。
1.技术指标的拟定通过分析后机匣的设计图纸及装配过程可知,发动机装配时需要先装配轴承座组件,然后将轴承座组件装配到涡轮后机匣上。
装配后需要在涡轮后机匣的前端外环进行精密定位孔的加工,技术条件要求严格。
从设计基准及技术条件要求看,后端内环安装轴承座端及前端外环为重要表面,因此将这两处技术条件的检测作为重要监控指标,如图1所示。
2.零件结构及技术条件分析零件为焊接组合件,整个机加组件由涡轮后机匣前、后段,内环,支板等多个单件组成,各单件通过电子束焊焊接而成,存在多条焊缝。
零件配合表面尺寸精度H7级,端面跳动及圆周跳动0.03~0.05,尺寸精度及技术要求严格,机加部位材料为高温合金,材料硬度大,加工性能差,切削时塑性变形抗力大,切削负荷重,切削温度高,加工后零件表面层的加工硬化及残留应力大,对所使用刀具的刀尖及边界磨损极其严重,加工中极易产生变形。
航空发动机机匣加工工艺研究

航空发动机机匣加工工艺研究摘要:随着我国综合国力的增强,同时也在促进国产发动机的性能逐渐朝着优良的方向不断发展。
近年来航空发动机的性能及设计结构在不断改进和提高,发动机机匣零件的材料、结构也发生了很大的变化。
本文就航空发动机机匣加工工艺展开探讨。
关键词:航空发动机;机匣;加工工艺1加工工艺特点机匣加工表面主要分为内、外两部分。
由于其外部需要连接到许多如电气、冷却、油路及管路等附件系统,导致其表面形状结构复杂,对机加要求比较高,尤其是对位置和尺寸精度要求较高;另外发动机机匣的内部主要是承载其压气机的涡轮叶片,包括动、静力叶片,这些都是其关键的动力输出部分,所以也对制造精度要求较高。
综上所述,机匣制造加工工艺的难点主要体现在材料切除率高、薄壁易变形、材料难切削和对刀具切削性能要求高等多个方面。
2.1轴数控铣削机匣型面的成形,国内通常是通过在多轴数控铣削设备上加工完成的。
数控机床的出现以及带来的巨大利益,引起世界各国科技界和工业界的普遍重视。
在航空机闸机械加工中,发展数控机床是当前我国机械制造业技术改造的必由之路,是未来工厂自动化的基础。
数控机床的大量使用,需要大批熟练掌握现代数控技术的人员。
数控技术的应用不但给传统制造业带来了革命性的变化,使制造业成为工业化的象征,而且随着数控技术的不断发展和应用领域的扩大,它对国计民生的一些重要行业的发展起着越来越重要的作用。
机匣零件外环形面共分二级,分布有二条环形凸缘,下部有1个纵向小凸缘,两个纵向凸缘对称分布。
由于机匣毛坯是自锻件,加工余量很大,且零件材料难切削,为了保证尺寸加工精度和表面加工质量,防止加工后零件变形。
其外型面加工分层、分块进行,采取合理的走刀路径,采用对称的切削加工余量。
分几次走刀加工到最后尺寸的方法,以减少加工后的变形。
因此,该机匣加工划分三个主要阶段并附加特征工序热处理,以去除材料内应力,防止零件变形。
2.2磨粒流加工磨粒流加工就是用流体作为载体,将具有实际切削技术性能的末了悬浮于其中,形成一个流体磨料,依靠末了相对于被加工材料表面的流动提供能量进行加工分析的一种技术。
某型号涡轮机匣的工艺试制与改进方案研究

在本篇文章中,我将围绕着某型号涡轮机匣的工艺试制与改进方案展开讨论。
我将从该型号涡轮机匣的基本结构和工艺流程入手,然后逐步深入分析其制造中遇到的问题和改进方案。
我将以严谨的态度和深度的思考,撰写一篇高质量且富有观点的文章,让您对这一主题有更深入的了解。
一、某型号涡轮机匣的基本结构和工艺流程1.1 涡轮机匣的定义和作用在工程领域中,涡轮机匣是一种重要的零部件,它在涡轮机内起着支撑和密封的作用,对于涡轮机的稳定运行起着至关重要的作用。
某型号涡轮机匣在飞机引擎中起到支持转子、固定定子以及保持叶片形状的作用。
1.2 工艺流程概述某型号涡轮机匣的制造工艺流程包括铸造、热处理、精密加工、表面处理等多个环节。
在每个环节中都存在着技术难点和改进空间,需要不断地进行研究和探索。
二、某型号涡轮机匣的工艺问题分析2.1 铸造工艺中存在的缺陷在某型号涡轮机匣的铸造过程中,可能会出现晶粒过大、孔洞、夹渣等缺陷,这些缺陷会直接影响铸件的力学性能和表面质量。
2.2 热处理工艺的优化空间热处理工艺对于铸件的组织和性能具有重要影响,如何在保证强度的情况下提高材料的韧性,是当前研究的重点和难点。
2.3 精密加工和表面处理技术的挑战涡轮机匣的精密加工和表面处理对于其尺寸精度和表面粗糙度要求极高,这对加工设备和工艺技术都提出了严格要求。
三、某型号涡轮机匣的改进方案探讨3.1 铸造工艺改进针对铸造中的缺陷问题,可以通过调整熔炼工艺、优化浇注系统、改进冷却方式等来提高铸件的质量。
3.2 热处理工艺优化通过淬火温度、保温时间、冷却速度等工艺参数的优化,可以实现涡轮机匣材料的综合性能提升。
3.3 精密加工和表面处理技术改进引入先进的数控加工设备、超声波振动加工技术、表面镀层等新工艺,可以提高涡轮机匣的加工精度和表面质量。
四、个人观点和总结通过对某型号涡轮机匣的工艺试制与改进方案的研究,我们可以看到这一领域中存在着诸多技术难题和改进空间。
在未来的研究中,我们需要继续深入探索铸造、热处理、精密加工和表面处理等多个环节,不断推动涡轮机匣工艺技术的创新与发展,以满足不断提升的工程需求。
辐条式高温合金涡轮后机匣焊接工艺研究
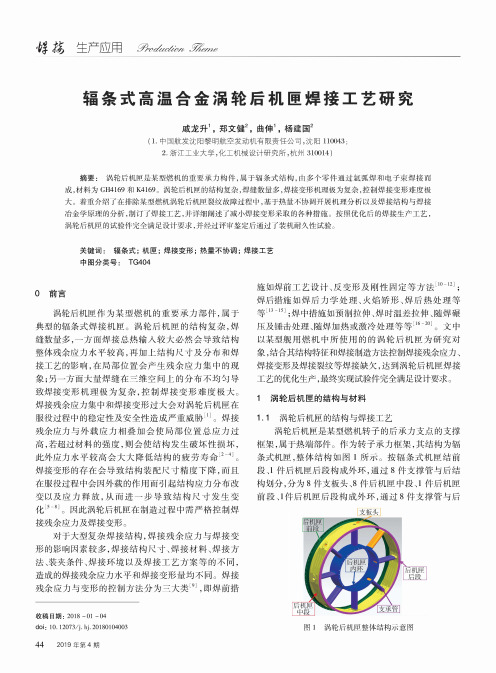
辐条式高温合金涡轮后机匣焊接工艺研究戚龙升1,郑文健2,曲伸1,杨建国2(1.中国航发沈阳黎明航空发动机有限责任公司,沈阳110043;2.浙江工业大学,化工机械设计研究所,杭州310014)摘要:涡轮后机匣是某型燃机的重要承力构件,属于辐条式结构,由多个零件通过氩弧焊和电子束焊接而 成,材料为GH4169和K4169。
涡轮后机匣的结构复杂,焊缝数量多,焊接变形机理极为复杂,控制焊接变形难度极 大。
着重介绍了在排除某型燃机涡轮后机匣裂纹故障过程中,基于热量不协调开展机理分析以及焊接结构与焊接 冶金学原理的分析,制订了焊接工艺,并详细阐述了减小焊接变形采取的各种措施。
按照优化后的焊接生产工艺,涡轮后机匣的试验件完全满足设计要求,并经过评审鉴定后通过了装机耐久性试验。
关键词:辐条式;机匣;焊接变形;热量不协调;焊接工艺中图分类号:TG404〇前言涡轮后机匣作为某型燃机的重要承力部件,属于 典型的辐条式焊接机匣。
涡轮后机匣的结构复杂,焊 缝数量多,一方面焊接总热输入较大必然会导致结构 整体残余应力水平较高,再加上结构尺寸及分布和焊 接工艺的影响,在局部位置会产生残余应力集中的现 象;另一方面大量焊缝在三维空间上的分布不均匀导 致焊接变形机理极为复杂,控制焊接变形难度极大。
焊接残余应力集中和焊接变形过大会对涡轮后机匣在 服役过程中的稳定性及安全性造成严重威胁[1]。
焊接 残余应力与外载应力相叠加会使局部位置总应力过 高,若超过材料的强度,则会使结构发生破坏性损坏,此外应力水平较高会大大降低结构的疲劳寿命[2_4]。
焊接变形的存在会导致结构装配尺寸精度下降,而且 在服役过程中会因外载的作用而引起结构应力分布改 变以及应力释放,从而进一步导致结构尺寸发生变化[5_8]。
因此涡轮后机匣在制造过程中需严格控制焊 接残余应力及焊接变形。
对于大型复杂焊接结构,焊接残余应力与焊接变 形的影响因素较多,焊接结构尺寸、焊接材料、焊接方 法、装夹条件、焊接环境以及焊接工艺方案等的不同,造成的焊接残余应力水平和焊接变形量均不同。
航空发动机机匣高效加工方法研究
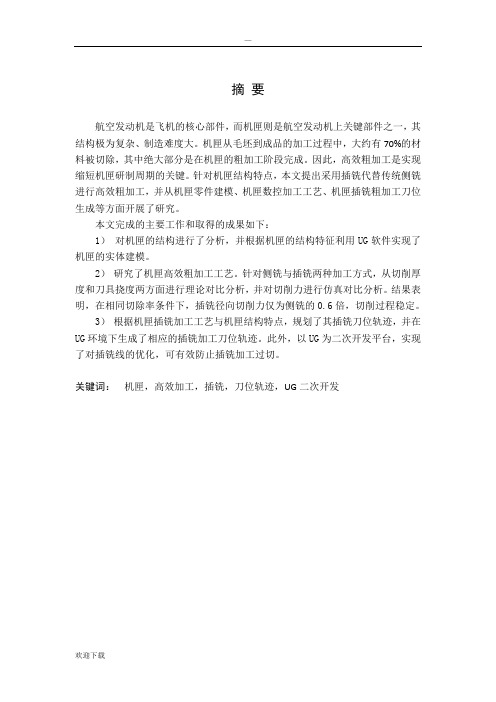
摘要航空发动机是飞机的核心部件,而机匣则是航空发动机上关键部件之一,其结构极为复杂、制造难度大。
机匣从毛坯到成品的加工过程中,大约有70%的材料被切除,其中绝大部分是在机匣的粗加工阶段完成。
因此,高效粗加工是实现缩短机匣研制周期的关键。
针对机匣结构特点,本文提出采用插铣代替传统侧铣进行高效粗加工,并从机匣零件建模、机匣数控加工工艺、机匣插铣粗加工刀位生成等方面开展了研究。
本文完成的主要工作和取得的成果如下:1)对机匣的结构进行了分析,并根据机匣的结构特征利用UG软件实现了机匣的实体建模。
2)研究了机匣高效粗加工工艺。
针对侧铣与插铣两种加工方式,从切削厚度和刀具挠度两方面进行理论对比分析,并对切削力进行仿真对比分析。
结果表明,在相同切除率条件下,插铣径向切削力仅为侧铣的0.6倍,切削过程稳定。
3)根据机匣插铣加工工艺与机匣结构特点,规划了其插铣刀位轨迹,并在UG环境下生成了相应的插铣加工刀位轨迹。
此外,以UG为二次开发平台,实现了对插铣线的优化,可有效防止插铣加工过切。
关键词:机匣,高效加工,插铣,刀位轨迹,UG二次开发ABSTRACTAero-engine is the core component of the aircraft, and the casing which is a key part of the engine is difficult to manufacture because its extremely complicate structure. About 70% of the material is removed from blank to finished product, while the most material is removed in rough milling of casing. Therefore, high efficiency roughing of the casing is a key technology to realizing higher efficiency manufacturing and shorter developing cycle. Based on characteristics of casing, plunge milling was proposed to instead of traditional layered flank milling in this paper. And the part modeling, the CNC machining process modeling, the cut-location generation of the plunge milling in rough machining were studied.The main work and achievements of this thesis are as follows:1) The casing structure is analyzed, and on this basis, the entity model of casing is established using UG.2) The efficient rough machining of casing is studied for process planning. Between the side milling and plunge milling methods, cutting thickness and tools deflection were contrasted in theory and the cutting force were contrasted in simulation. The results show that, under the same resection rate, the radial cutting force of the plunge is only 0.6 times than the side milling, and the process is stable.3) According to the Plunge milling process and the structure characteristics of casing, the plunge milling cutter path was planned, which is then generated in UG. Additionally, aiming at overcut in plunge milling process, the optimization of the plunge milling line has been implemented using UG secondary development.Key words: Casing, Efficient processing, Plunge milling, tool path, UG Secondary development目录摘要 (I)ABSTRACT........................................................ I I第一章绪论 (1)1.1研究背景 (1)1.2国内外研究现状 (2)1.2.1 复杂结构类零件粗加工技术 (2)1.2.2 插铣工艺技术 (3)1.3 论文主要内容及章节安排 (5)第二章机匣造型 (7)2.1基于特征的建模方法 (7)2.2建模平台选择 (8)2.3机匣造型 (9)2.3.1 机匣模型分析 (9)2.3.2 机匣实体建模 (10)第三章机匣数控加工工艺 (15)3.1工艺规程编制原则 (15)3.2机匣零件的工艺特征 (15)3.3机匣加工工艺阶段的划分 (16)3.4机匣加工工艺路线制定 (16)3.5机匣粗加工工艺方案分析 (18)第四章机匣插铣粗加工刀具轨迹 (25)4.1 UG数控加工 (25)4.2刀具轨迹规划原则 (25)4.3刀具轨迹生成 (27)4.3.1 加工环境设定 (27)4.3.2 刀具轨迹生成 (27)4.3.3 程序后置处理 (33)4.4基于UG的插铣线优化 (35)总结 (38)致谢 (39)参考文献 (40)第一章绪论1.1研究背景航空发动机是飞机的“心脏”,其内部温度高,转速高,压力大,使用寿命长,构件的机械负荷和热负荷大,工作条件十分苛刻和复杂,其研究和发展工作的技术难度大,耗资多,周期长,是一个世界公认的、复杂的多学科综合性系统工程[1]。
航空发动机机匣加工工艺研究

航空发动机机匣加工工艺研究作者:李国明来源:《中国新技术新产品》2012年第13期摘要:本文紧紧围绕建立基于数字化思想、具有数字化特点的机匣的优化工艺,并最终将该工艺应用于机匣的制造过程。
新的优化过程应该能够适应航空发动机机匣生产车间的制造设备状况,能够满足发动机制造厂“小批量生产和规模生产能力”的优化目标。
关键词:航空发动机;机匣;加工工艺中图分类号:TK416+.1 文献标识码:A1 问题的提出和依据航空工艺设计成本高、周期长,这两个特点不仅增加了传统工艺设计的难度,而且是传统工艺无法根本解决的。
因此,对发动机关键零部件传统工艺采用数字化手段进行优化改造势在必行。
数字化的工艺系统可以保证在技术层面上制定产品制造工艺时随时地、充分地考虑企业的制造环境,作业调度,车间底层控制,工装夹具的配套以及毛坯的设计制造等所有工艺信息,将有关信息及时反馈到设计单位并及时得到响应,生成适应性加工工艺,使制造过程达到全局优化,这是未来航空发动机工艺的重要发展方向之一。
2 延伸机匣加工工艺优化的目标工艺方案技术经济性分析的一个重要应用方面是在工艺流程设计过程中,对不同的工艺方案进行评价。
对绝大多数产品来说,工艺过程有许多可变因素,在工艺设计中,如何确定这些可变因素,使制造过程最合理,这就是工艺过程优化研究的问题。
机械制造工艺过程除要保证制造质量之外,还必须实现高的生产效率和低的生产成本,这就是工艺过程优化的主要目标。
3 参数化特征建模方法3.1 基于特征的建模方法概述特征 (Feature)是指描述产品信息的集合,也是设计或制造零部件的基本几何体。
它是以结构的实体几何(CSG:Constructive Solid Geometry)和边界表示(B-Rep:Boundary Representation)为基础的,源于产品的模块化设计思想。
特征是参数化的几何体,通过改变特征的尺寸,可以用有限的特征构造出无限的零、部件模型,具有一定的工程意义。
航空发动机机匣数控加工技术研究
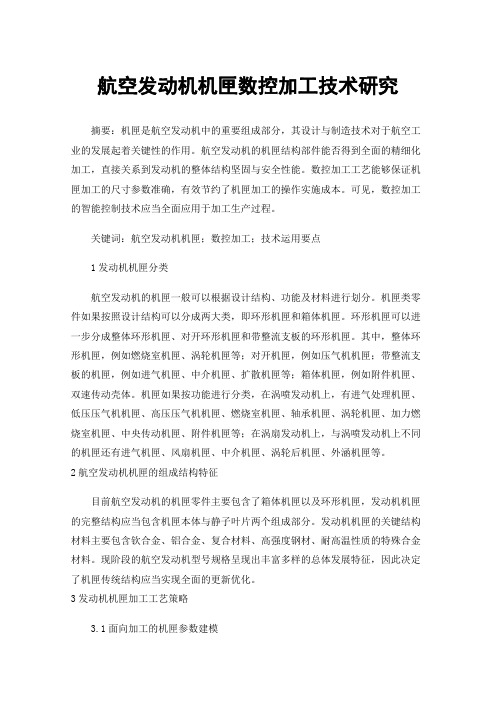
航空发动机机匣数控加工技术研究摘要:机匣是航空发动机中的重要组成部分,其设计与制造技术对于航空工业的发展起着关键性的作用。
航空发动机的机匣结构部件能否得到全面的精细化加工,直接关系到发动机的整体结构坚固与安全性能。
数控加工工艺能够保证机匣加工的尺寸参数准确,有效节约了机匣加工的操作实施成本。
可见,数控加工的智能控制技术应当全面应用于加工生产过程。
关键词:航空发动机机匣;数控加工;技术运用要点1发动机机匣分类航空发动机的机匣一般可以根据设计结构、功能及材料进行划分。
机匣类零件如果按照设计结构可以分成两大类,即环形机匣和箱体机匣。
环形机匣可以进一步分成整体环形机匣、对开环形机匣和带整流支板的环形机匣。
其中,整体环形机匣,例如燃烧室机匣、涡轮机匣等;对开机匣,例如压气机机匣;带整流支板的机匣,例如进气机匣、中介机匣、扩散机匣等;箱体机匣,例如附件机匣、双速传动壳体。
机匣如果按功能进行分类,在涡喷发动机上,有进气处理机匣、低压压气机机匣、高压压气机机匣、燃烧室机匣、轴承机匣、涡轮机匣、加力燃烧室机匣、中央传动机匣、附件机匣等;在涡扇发动机上,与涡喷发动机上不同的机匣还有进气机匣、风扇机匣、中介机匣、涡轮后机匣、外涵机匣等。
2航空发动机机匣的组成结构特征目前航空发动机的机匣零件主要包含了箱体机匣以及环形机匣,发动机机匣的完整结构应当包含机匣本体与静子叶片两个组成部分。
发动机机匣的关键结构材料主要包含钦合金、铝合金、复合材料、高强度钢材、耐高温性质的特殊合金材料。
现阶段的航空发动机型号规格呈现出丰富多样的总体发展特征,因此决定了机匣传统结构应当实现全面的更新优化。
3发动机机匣加工工艺策略3.1面向加工的机匣参数建模机匣的参数建模需要根据具体机匣结构特征进行。
首先需要进行机匣零件的结构特征分析,根据结构形状,结合加工特点及形体特征划分特征单元,并分解成基本的特征系。
其次,根据建立的基本特征系之间的关联关系或者约束条件,建立关联表达式和特征分叉树。
航空发动机机匣的数控加工
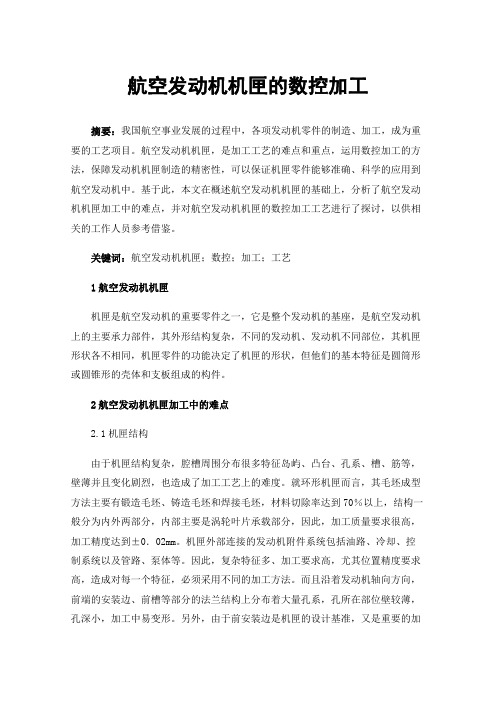
航空发动机机匣的数控加工摘要:我国航空事业发展的过程中,各项发动机零件的制造、加工,成为重要的工艺项目。
航空发动机机匣,是加工工艺的难点和重点,运用数控加工的方法,保障发动机机匣制造的精密性,可以保证机匣零件能够准确、科学的应用到航空发动机中。
基于此,本文在概述航空发动机机匣的基础上,分析了航空发动机机匣加工中的难点,并对航空发动机机匣的数控加工工艺进行了探讨,以供相关的工作人员参考借鉴。
关键词:航空发动机机匣;数控;加工;工艺1航空发动机机匣机匣是航空发动机的重要零件之一,它是整个发动机的基座,是航空发动机上的主要承力部件,其外形结构复杂,不同的发动机、发动机不同部位,其机匣形状各不相同,机匣零件的功能决定了机匣的形状,但他们的基本特征是圆筒形或圆锥形的壳体和支板组成的构件。
2航空发动机机匣加工中的难点2.1机匣结构由于机匣结构复杂,腔槽周围分布很多特征岛屿、凸台、孔系、槽、筋等,壁薄并且变化剧烈,也造成了加工工艺上的难度。
就环形机匣而言,其毛坯成型方法主要有锻造毛坯、铸造毛坯和焊接毛坯,材料切除率达到70%以上,结构一般分为内外两部分,内部主要是涡轮叶片承载部分,因此,加工质量要求很高,加工精度达到±0.02mm。
机匣外部连接的发动机附件系统包括油路、冷却、控制系统以及管路、泵体等。
因此,复杂特征多、加工要求高,尤其位置精度要求高,造成对每一个特征,必须采用不同的加工方法。
而且沿着发动机轴向方向,前端的安装边、前槽等部分的法兰结构上分布着大量孔系,孔所在部位壁较薄,孔深小,加工中易变形。
另外,由于前安装边是机匣的设计基准,又是重要的加工工艺基准。
因此,对孔系的加工具有很高的尺寸精度和位置精度要求。
并且沿着轴向与燃烧室连接的机匣后端部位,除了法兰结构上具有复杂孔系外,沿着机匣加强筋部位周边还分布着放气孔,该类孔一般与发动机轴线成一定角度,这些特殊结构的异型孔加工难度很大。
在加工工艺上,除了结构复杂工艺难度大外,部分机匣采用的对开结构,若在加工过程中采用分散与组合加工相结合,会由此造成二次定位,影响加工一致性。
转包高压涡轮机匣典型加工技术

转包高压涡轮机匣典型加工技术作者:王树锋包大陆孙长友来源:《中国新技术新产品》2011年第17期摘要:本文介绍了罗罗公司BR710涡扇发动机主要机匣组件加工技术,着重论述了铣加工刀具、参数选择、陶瓷刀具、数控程序编制与仿真、滚花加工技术。
关键词:陶瓷刀具;加工参数;滚花加工;数控程序;vericut仿真;硬质合金涂层中图分类号:TQ174 文献标识码:A引言罗罗公司BR710涡扇发动机主要为高速的Bombardier Global 5000飞机和超远程Global Express XRS公务机提供动力,推力范围为1.4万磅-1.7万磅,具有低噪音和低排放的特点。
高压涡轮机匣组件是RR公司BR710涡扇发动机主要核心零件,材料为MSRR7115(相当于Inconel718)属于镍基高温合金,零件尺寸外廓Ф800×Ф650×279.81,最薄壁厚2.1mm,零件形状十分复杂,包含众多岛屿,尺寸多、精度高,加工中易变形,加工难度很大,在加工过程中,优选陶瓷刀具、玉米铣刀进行粗铣,面铣刀精铣等刀具方案,实现了高效率、高质量、低成本的加工。
1 高压涡轮机匣加工的材料Inconel718,是一种沉淀硬化的镍铬合金,含有相当数量的铁、铌和钼,以及少量的铝和钛。
它把耐蚀性、高强度与杰出的焊接性能(包括抗焊后破裂的性能)结合在一起。
在高达700℃的温度下,该合金具有极佳的蠕变断裂强度。
加工难点在铣加工刀具选择、参数选择、程序编制、以及特殊形状滚花加工上,以下从铣加工、滚花加工、硬质合金涂层车加工、典型加工注意事项四方面分别阐述机匣加工技术。
1.1 铣加工:粗铣环带时,余量共10mm,传统的加工方式是选用Ф20R3立铣刀分层加工,每层3mm。
此机匣使用了适用于重切削,效率较高德Ф100玉米铣刀粗铣,具有刀齿交错排列,分屑性能好,减小每齿切削力,排屑顺利的特点,并采用内部带有压盖的专用夹具,通过限力扳手控制压板压紧力80NM,压盖压紧力30NM,根据刀具切削及磨损状态,一刀完成了粗加工,每齿切削厚度增加,使刀齿避开表面的硬化层,刀齿交错有利于切削液的渗透,实现了低耗高效加工。
航空发动机机匣加工关键工艺及其冷却技术方法研究

航空发动机机匣加工关键工艺及其冷却技术方法研究摘要:机匣是航空发动机的关键部件,其材料主要为高温合金这类耐高温的难加工的材料,这类结构和材料特性使在切削加工的过程中遇到很多困难,如果没有采用科学合理的技术工艺将影响机匣的制造质量,对发动机整体性能产生影响。
为此需要重点考虑加工刀具参数、工件材料、切削参数和工艺方法等。
本文将从航空发动机机匣加工技术和冷却方法的角度进行分析研究,并提出相应的设计优化方案。
关键词:航空发动机机匣;加工制造;冷却技术1 航空发动机机匣概述航空发动机机匣是发动机的关键部件,其结构和形状均很复杂,且材料加工难度大、难以保证加工制造的质量,在加工中需要克服许多技术工艺上的难点,且需利用好数控加工的方法。
从发动机机匣种类和结构特点分析来看,可根据设计结构将机匣分成环形机匣与箱体机匣,前者又可以分成整体环形机匣与开环形匣机匣、带整流支板的环形机匣。
如果按照功能来划分,可以将机匣分成进气处理机匣、低压压气机机匣、高压压气机机匣、轴承机匣、涡轮机匣等。
根据材料划分目前常见的有钛合金机匣、耐高温合金机匣和复合材料机匣,大多数机匣低压部分采用的是高强度钢材料,而高压部分大多数采用的是钛合金材料。
分析发动机机匣特征发现,因为材料本身难以加工的性质以及发动机机匣结构的特点使机匣整体加工难度较大。
在材料方面的难度具体表现在,对于采用不锈钢材料的机匣在加工中因为切削力较大且切削温度较高,所以在加工时易于出现黏附问题,使刀具前刀面产生积屑瘤,加上材料具有塑性和韧性较强的特点,使加表面产生撕扯。
而以钛合金为主材料的机匣,在切削加工中切削变形系数无限接近于1,在刀具前刀面滑动摩擦较大使刀具磨损加剧,影响刀具的使用寿命。
此外因为材料化学活性较大、亲和力较强,所以容易出现硬化和黏刀的问题。
对于以高温合金为主材料的机匣,切削力是一般钢材的多倍,刀具磨损异常严重,而且容易出现严重的硬化问题。
加上材料导热系数较低、切削力集中于刀尖,切屑因为韧性较大容易形成卷屑不易清除。
关于航空发动机机匣构件机械加工工艺优化研究

关于航空发动机机匣构件机械加工工艺优化研究发布时间:2022-09-13T09:58:56.777Z 来源:《中国科技信息》2022年第5月9期作者:刘楚煜[导读] 在我国科技不断发展的过程中刘楚煜中国航发长江动力有限公司(湖南岳阳 414000)摘要:在我国科技不断发展的过程中,促进了多个行业的进一步发展,也为航空领域提供了技术支持。
航空发动机的质量对航空领域有着至关重要的影响,而发动机机匣直接关系着航空发动机的质量,因此,必须要采取有效措施,不断优化改进航空发动机机匣的机械加工技术,保障航空领域的安全稳定发展。
因此,本文主要针对航空发动机机匣构件机械加工工艺的优化措施进行探讨分析,旨在提升其加工质量。
关键词:航空发动机;机匣构件;机械加工;工艺优化引言:在制造飞机发动机的过程中,机匣构件是其中非常关键的一个构件,不仅需要承载较大的负荷,还需要承受较高的温度,所以其主要材料为高强度的合金。
在当前的机械加工过程中,经常会出现零件受损或表面不平整等质量问题,严重影响了航空发动机机匣的使用年限。
因此,应严格控制机械加工质量,优化加工工艺,进而保障机匣构件质量,确保航空事业的稳定发展。
一、机匣构件机械加工的重要意义机匣构件机械加工时航空发动机制作中的重要内容,主要由于其需要承担较大的负载和高温的影响。
因此,在实际进行加工的过程中,需要选择具有较高强度的金属材料,并且能够具有抗高温。
现阶段,我国的机匣构件加工质量得到了优化完善,但还存在一些质量问题,如表面受损问题,会导致机匣使用寿命减少。
因此,需要进一步优化机匣机械加工工艺,保障其构件的整体性,提升其机械性能和抗疲劳性能。
同时,需要制定相应的分析流程,如图1所示。
对机匣进行工艺分析是进一步优化其工艺的前提。
即对其构件的加工的工艺性进行分析。
因为航空发动机的结构具有较强的复杂性,所以在机匣制造的过程中,很容易出现结构性问题,增强了其工艺问题的复杂性。
在制作机匣构件的过程中,要想保障其质量合格,需要采用机械加工的方式对其表面质量和形状等进行调整,是技巧和方法的结合[1]。
某型号涡轮机匣的工艺试制与改进方案研究
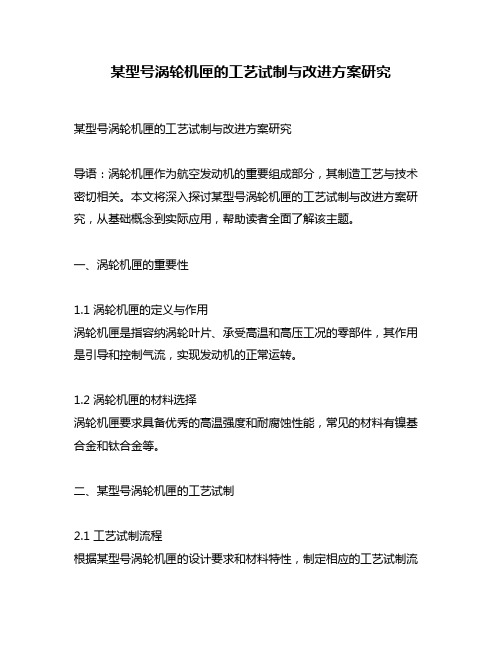
某型号涡轮机匣的工艺试制与改进方案研究某型号涡轮机匣的工艺试制与改进方案研究导语:涡轮机匣作为航空发动机的重要组成部分,其制造工艺与技术密切相关。
本文将深入探讨某型号涡轮机匣的工艺试制与改进方案研究,从基础概念到实际应用,帮助读者全面了解该主题。
一、涡轮机匣的重要性1.1 涡轮机匣的定义与作用涡轮机匣是指容纳涡轮叶片、承受高温和高压工况的零部件,其作用是引导和控制气流,实现发动机的正常运转。
1.2 涡轮机匣的材料选择涡轮机匣要求具备优秀的高温强度和耐腐蚀性能,常见的材料有镍基合金和钛合金等。
二、某型号涡轮机匣的工艺试制2.1 工艺试制流程根据某型号涡轮机匣的设计要求和材料特性,制定相应的工艺试制流程。
包括材料准备、铸造或锻造、热处理、毛坯修整等环节。
2.2 工艺试制难点及解决方案涡轮机匣的工艺试制中存在一些难点,如如何降低残余应力、提高制造精度等。
针对这些问题,可以采用压力补偿技术、真空热处理等改进方案。
三、某型号涡轮机匣的改进方案研究3.1 现有涡轮机匣的问题分析分析当前某型号涡轮机匣在制造和使用过程中存在的问题,如制造精度不高、腐蚀疲劳寿命不长等。
3.2 改进方案一:优化制造工艺针对现有涡轮机匣制造过程中的问题,可以通过优化工艺参数、改进工艺流程等措施来提高制造精度和质量。
3.3 改进方案二:新材料应用通过引入新材料,如先进的镍基合金、高温陶瓷复合材料等,来提升涡轮机匣的耐热性和耐腐蚀性,从而延长其使用寿命。
四、个人观点与理解本文主要探讨了某型号涡轮机匣的工艺试制与改进方案研究。
通过对涡轮机匣的重要性、工艺试制流程以及改进方案的探讨,我深刻理解了涡轮机匣制造的复杂性与关键性。
在工艺试制方面,要解决涡轮机匣中的难题,需要依靠先进的技术手段和精细的工艺流程。
通过应用压力补偿技术和真空热处理等方法,能够有效降低残余应力,提高制造精度。
在改进方案研究中,优化制造工艺和引入新材料是可行的途径。
通过优化工艺参数,改进工艺流程,可以提高涡轮机匣的制造精度和质量,进而提升性能。
某型机高温合金材料机匣加工工艺研究
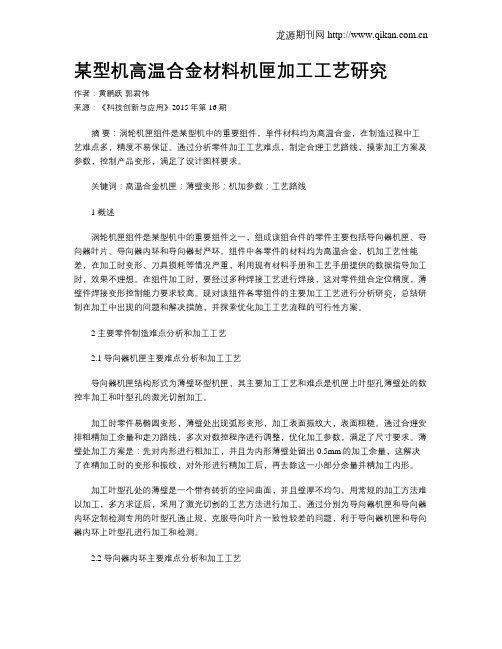
某型机高温合金材料机匣加工工艺研究作者:黄鹏跃郭君伟来源:《科技创新与应用》2015年第16期摘要:涡轮机匣组件是某型机中的重要组件,单件材料均为高温合金,在制造过程中工艺难点多,精度不易保证。
通过分析零件加工工艺难点,制定合理工艺路线,摸索加工方案及参数,控制产品变形,满足了设计图样要求。
关键词:高温合金机匣;薄壁变形;机加参数;工艺路线1 概述涡轮机匣组件是某型机中的重要组件之一,组成该组合件的零件主要包括导向器机匣、导向器叶片、导向器内环和导向器封严环。
组件中各零件的材料均为高温合金,机加工艺性能差,在加工时变形、刀具损耗等情况严重,利用现有材料手册和工艺手册提供的数据指导加工时,效果不理想。
在组件加工时,要经过多种焊接工艺进行焊接,这对零件组合定位精度,薄壁件焊接变形控制能力要求较高。
现对该组件各零组件的主要加工工艺进行分析研究,总结研制在加工中出现的问题和解决措施,并探索优化加工工艺流程的可行性方案。
2 主要零件制造难点分析和加工工艺2.1 导向器机匣主要难点分析和加工工艺导向器机匣结构形式为薄壁环型机匣,其主要加工工艺和难点是机匣上叶型孔薄壁处的数控车加工和叶型孔的激光切割加工。
加工时零件易椭圆变形,薄壁处出现弧形变形,加工表面振纹大,表面粗糙。
通过合理安排粗精加工余量和走刀路线,多次对数控程序进行调整,优化加工参数,满足了尺寸要求。
薄壁处加工方案是:先对内形进行粗加工,并且为内形薄壁处留出0.5mm的加工余量,这解决了在精加工时的变形和振纹,对外形进行精加工后,再去除这一小部分余量并精加工内形。
加工叶型孔处的薄壁是一个带有转折的空间曲面,并且壁厚不均匀,用常规的加工方法难以加工,多方求证后,采用了激光切割的工艺方法进行加工。
通过分别为导向器机匣和导向器内环定制检测专用的叶型孔通止规,克服导向叶片一致性较差的问题,利于导向器机匣和导向器内环上叶型孔进行加工和检测。
2.2 导向器内环主要难点分析和加工工艺导向器内环属于薄壁环类零件,其主要加工难点是薄壁处的数控车成形加工。
- 1、下载文档前请自行甄别文档内容的完整性,平台不提供额外的编辑、内容补充、找答案等附加服务。
- 2、"仅部分预览"的文档,不可在线预览部分如存在完整性等问题,可反馈申请退款(可完整预览的文档不适用该条件!)。
- 3、如文档侵犯您的权益,请联系客服反馈,我们会尽快为您处理(人工客服工作时间:9:00-18:30)。
艺仿真 以及新件研制过程应注意的问题等方面进行论述,对类似零件的加 工有借鉴意义。
关 键词 :涡轮 ;机 匣;加 工 ;技 术
中 图分 类号 :T Q1 7
文献标 识码 :A
黎 明 公 司有 多年 机 匣加 工 经 验 ,包 括 三 代 机 、 四代 机 以及 重 型燃 机 等 ,培 养 了一 批从 事 机 匣加 工 的工 程技 术 人 员。 2 0 0 8 年 以来 ,结 合 黎 明公 司技 术 发 展 方 向 ,转 包 系统 积 极 与 国际 知 名 航 空 企 业 开展技术交流 ,积极 投身国际市场 ,引 进 国外 先 进 技 术 及 加 工 理 念 。转 包 大 机 匣项 目正 是 在 这 种 背 景 下 展 开 的 。机 匣 项 目的开 展 ,一 方 面 提 高 了公 司 的制 造 技 术 水平 ,另 一 方 面 也 给 黎 明公 司传 统 加工 理念 带来 冲击 。
口匿翟盈圈
工 业 技 术
涡轮机 匣加工技术研 究
王 柱 康 建 铭
( 沈阳黎明航发 集 团 ( 有限 )责任公 司国际业务 事业部 ,辽宁 沈 阳 1 1 0 0 4 3 )
摘 要 :本 文结 合 I T RE NT发 动机 涡轮 机 匣加 工 ,对 涡轮 机 匣加 工工 艺路线 、尺 寸控 制 、支撑减 震 、技 术条件 保证 、 工
1 零件 特 点
a
将 轴 向 尺 寸 基
准 转 换 到销 子 孔 上 , 减 少 了 轴 向 尺 寸 误 差 累积 ,实 现 了次 要 表 面粗 加 工 阶段 即加
涡 轮 机 匣 ,铣 加 工 内圆 槽 角 向 位 置 公差 O . 1 0 , 可 含包 容 。外 圆 岛屿不 均布 , 引起 零 件变 形不 均匀 。 2 工 艺路 线及 尺寸 关系 结合生产现场情况 ,制定工艺路线
一
工 至 最 终 ,较 好 的保 证 了 内 外壁 轮廓 都要 求。 b增加 辅 助支 撑 , 减 少 铣 加 工 震 动 、变 形 ,实 现 大 刀 粗 铣 , 提 高 了加工效 率 。 C端 面 槽 位 置 度 0 . 1 0 ,先 采 用 ( b 8 铣 刀 粗 铣 ,再 采 用 1 0 R 2 . 5 铣 刀精 铣 ,较 好 的保 证 位 置 都 要求。 d 端 面 孔 位 置 度 0 . 1 0 , 而 一 般 五 座 标 机 床 C盘 分 度 精 度 0 . 0 0 5 度, D MU 2 0 0 P设 备 为 2 2度 ,不 能 满 足 位 置 度要求,而采用机床走 x、 Y坐标方式加 工 ,可实 现位 置度 要求 0 . 0 6 。 e 精 车过 程 中 , 自顶 向下走 刀 ,零件 剧 烈 震 动 ,而 自底 向上 走 刀 ,零 件 状 态 较好 。 f 精 车工 序 ,最后 车大 端基 准 面 ,以 保 证 大 端 平 面 度 。所 有 与 大 端 基 准 有关 系 的尺 寸加 工至 中差 。 g 防错 。加 工过 程 中 ,角 向孑 L 不易 辨 别 、 区分 ,在 角 向孔 加工 完成 后 涂 漆 , 避 免 了后续 角 向混 乱 。 h孔 的加工 ,在粗 铣工 序 岛屿表 面及 孑 L 径留 1 . 0 m m余量 , 在 精加 工工 序去 除 , 同一 工序 加工 , 保 证孔 与 岛屿表 面垂 直 。 5 工 艺仿 真技术 的应 用 南 于零 件 复 杂 ,尺 寸 众 多 且价 值 昂 贵 ,大 尺 寸 成 型 刀 具 应 用 较 多 ,程 序 数 量 大 ,如 何 防范 研 制 风 险 ,提 高加 工质 量 ,提 高研 制 效 率 ,是 一 个 比较棘 手 的 问题 。在研 制 过程 中 ,结 合夹 具 、刀具 、 数 控 程序 开 展工 艺仿 真 及数 控 程序 优 化 、 加 工 方 案 评 估 ,为零 件 顺 利 加 工 扫 除 了 障碍 。 6机匣 新件研 制应 注 意 的问题 作 为 复 杂 机 匣 零 件 的加 工 ,研 制 过 程比较艰 苦,从降低成本 ,降低风险, 提 高研 制 效 率 的角 度 ,有 以 下 问题 需 要
ห้องสมุดไป่ตู้如下:
大体上是粗车一粗铣一精车一精铣 的工 艺 思 路 。 而 机 匣 内外 表 面尺 寸 关 系 复杂 ,牵 一 发 而 动 全 身 ,需 要 有 明确 的 尺 寸关 系 。在 大 端 基 准 面 未 形 成 之 前 , 将所有工序轴向尺寸基准与基准孔关联 , 实现机匣内外 次要 表面车、铣加工,在 精铣 外形 结束后 ,完成 内外 圆的精车。 实践证明,用机床打表 的方式 ,容易 实 现轴 向尺 寸正 负 0 . 0 2的要求 。 3 支撑 减震 多年 以来 ,在新件研制阶段 由于条 件 限制 ,工 艺 人 员 习惯 使 用 简 易 工装 。
黎 明公司传统 的铣床夹具也多为底座 、 拉杆 、压盖组成的简单 结构。由于缺乏 必 要 的支 撑 ,零 件 刚 性 差 ,容 易震 动 , 切 削 参 数 难 以提 高 。作 为转 包 生 产 的第 个 大 机 匣 ,从 加 工 伊 始 ,对 这 个 问题 就 充 分 重 视 ,采 取 了必 要 的 措 施 ,提 高 零件 刚性 。精铣 内圆工序 ,由于刀具尺 寸较 大 ,切削 力较 大 。为 防止零 件震 动 , 采 取 过 定 位 的方 式 ,支 撑 S 面 。 实 际 加 工 中采 用 直 径 由1 0 4成 型 铣 刀 ,为增 加 零 件 刚 性 ,支 撑 了 四个 部 位 。正 是 由于 采 取 了 必 要 的 措 施 ,使 得 工 艺 人 员 能 够 排除震动 、变形等因素的影 响,零件始 终 处 于较好 的状 态 。 4 技 术 条件保 证 在 加 工 过 程 中 ,主要 在 以下 方 面 采 取 措施 ,保 证技 术条 件 : 注意 :