万能轧机轴承座轴向窜动超差原因分析及控制
万能轧机轧辊轴向窜动分析与控制
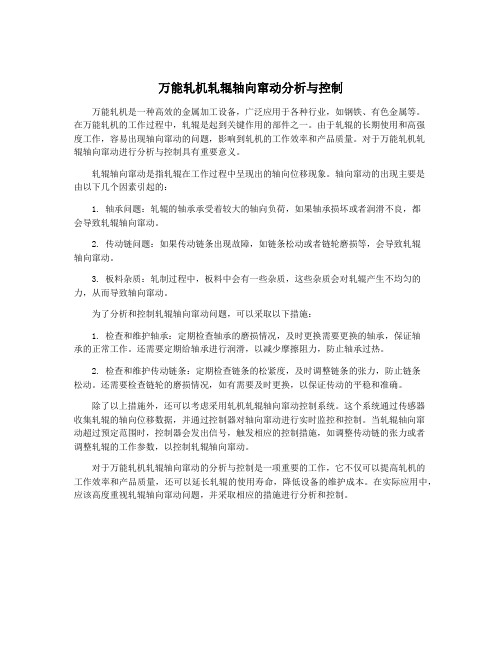
万能轧机轧辊轴向窜动分析与控制万能轧机是一种高效的金属加工设备,广泛应用于各种行业,如钢铁、有色金属等。
在万能轧机的工作过程中,轧辊是起到关键作用的部件之一。
由于轧辊的长期使用和高强度工作,容易出现轴向窜动的问题,影响到轧机的工作效率和产品质量。
对于万能轧机轧辊轴向窜动进行分析与控制具有重要意义。
轧辊轴向窜动是指轧辊在工作过程中呈现出的轴向位移现象。
轴向窜动的出现主要是由以下几个因素引起的:1. 轴承问题:轧辊的轴承承受着较大的轴向负荷,如果轴承损坏或者润滑不良,都会导致轧辊轴向窜动。
2. 传动链问题:如果传动链条出现故障,如链条松动或者链轮磨损等,会导致轧辊轴向窜动。
3. 板料杂质:轧制过程中,板料中会有一些杂质,这些杂质会对轧辊产生不均匀的力,从而导致轴向窜动。
为了分析和控制轧辊轴向窜动问题,可以采取以下措施:1. 检查和维护轴承:定期检查轴承的磨损情况,及时更换需要更换的轴承,保证轴承的正常工作。
还需要定期给轴承进行润滑,以减少摩擦阻力,防止轴承过热。
2. 检查和维护传动链条:定期检查链条的松紧度,及时调整链条的张力,防止链条松动。
还需要检查链轮的磨损情况,如有需要及时更换,以保证传动的平稳和准确。
除了以上措施外,还可以考虑采用轧机轧辊轴向窜动控制系统。
这个系统通过传感器收集轧辊的轴向位移数据,并通过控制器对轴向窜动进行实时监控和控制。
当轧辊轴向窜动超过预定范围时,控制器会发出信号,触发相应的控制措施,如调整传动链的张力或者调整轧辊的工作参数,以控制轧辊轴向窜动。
对于万能轧机轧辊轴向窜动的分析与控制是一项重要的工作,它不仅可以提高轧机的工作效率和产品质量,还可以延长轧辊的使用寿命,降低设备的维护成本。
在实际应用中,应该高度重视轧辊轴向窜动问题,并采取相应的措施进行分析和控制。
万能轧机轧辊轴向窜动分析与控制
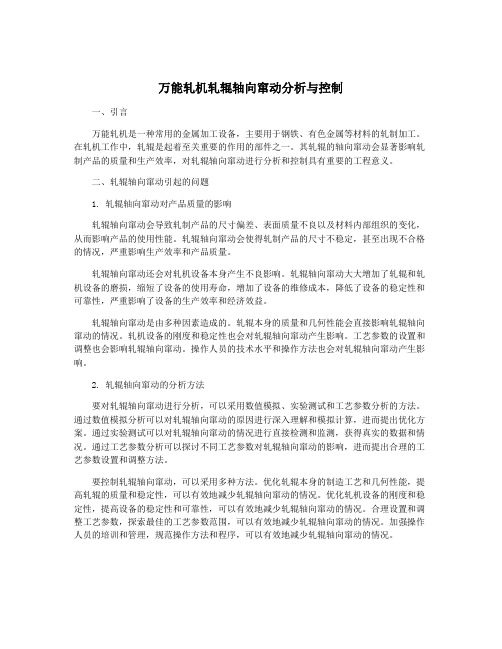
万能轧机轧辊轴向窜动分析与控制一、引言万能轧机是一种常用的金属加工设备,主要用于钢铁、有色金属等材料的轧制加工。
在轧机工作中,轧辊是起着至关重要的作用的部件之一。
其轧辊的轴向窜动会显著影响轧制产品的质量和生产效率,对轧辊轴向窜动进行分析和控制具有重要的工程意义。
二、轧辊轴向窜动引起的问题1. 轧辊轴向窜动对产品质量的影响轧辊轴向窜动会导致轧制产品的尺寸偏差、表面质量不良以及材料内部组织的变化,从而影响产品的使用性能。
轧辊轴向窜动会使得轧制产品的尺寸不稳定,甚至出现不合格的情况,严重影响生产效率和产品质量。
轧辊轴向窜动还会对轧机设备本身产生不良影响。
轧辊轴向窜动大大增加了轧辊和轧机设备的磨损,缩短了设备的使用寿命,增加了设备的维修成本,降低了设备的稳定性和可靠性,严重影响了设备的生产效率和经济效益。
轧辊轴向窜动是由多种因素造成的。
轧辊本身的质量和几何性能会直接影响轧辊轴向窜动的情况。
轧机设备的刚度和稳定性也会对轧辊轴向窜动产生影响。
工艺参数的设置和调整也会影响轧辊轴向窜动。
操作人员的技术水平和操作方法也会对轧辊轴向窜动产生影响。
2. 轧辊轴向窜动的分析方法要对轧辊轴向窜动进行分析,可以采用数值模拟、实验测试和工艺参数分析的方法。
通过数值模拟分析可以对轧辊轴向窜动的原因进行深入理解和模拟计算,进而提出优化方案。
通过实验测试可以对轧辊轴向窜动的情况进行直接检测和监测,获得真实的数据和情况。
通过工艺参数分析可以探讨不同工艺参数对轧辊轴向窜动的影响,进而提出合理的工艺参数设置和调整方法。
要控制轧辊轴向窜动,可以采用多种方法。
优化轧辊本身的制造工艺和几何性能,提高轧辊的质量和稳定性,可以有效地减少轧辊轴向窜动的情况。
优化轧机设备的刚度和稳定性,提高设备的稳定性和可靠性,可以有效地减少轧辊轴向窜动的情况。
合理设置和调整工艺参数,探索最佳的工艺参数范围,可以有效地减少轧辊轴向窜动的情况。
加强操作人员的培训和管理,规范操作方法和程序,可以有效地减少轧辊轴向窜动的情况。
轴承轴向窜动的原因
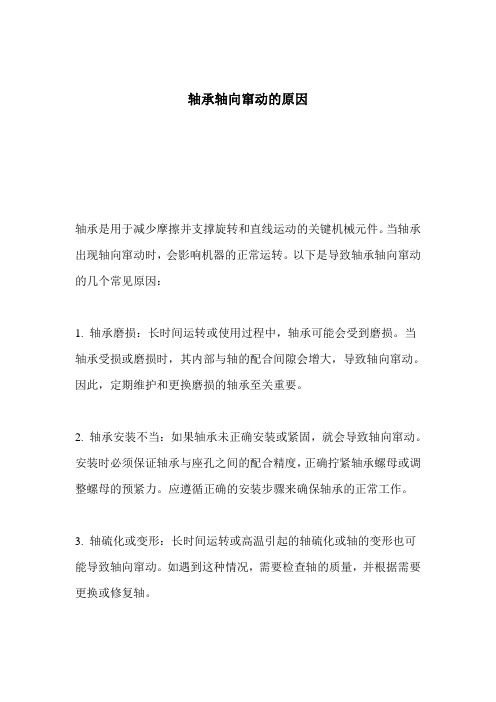
轴承轴向窜动的原因
轴承是用于减少摩擦并支撑旋转和直线运动的关键机械元件。
当轴承出现轴向窜动时,会影响机器的正常运转。
以下是导致轴承轴向窜动的几个常见原因:
1. 轴承磨损:长时间运转或使用过程中,轴承可能会受到磨损。
当轴承受损或磨损时,其内部与轴的配合间隙会增大,导致轴向窜动。
因此,定期维护和更换磨损的轴承至关重要。
2. 轴承安装不当:如果轴承未正确安装或紧固,就会导致轴向窜动。
安装时必须保证轴承与座孔之间的配合精度,正确拧紧轴承螺母或调整螺母的预紧力。
应遵循正确的安装步骤来确保轴承的正常工作。
3. 轴硫化或变形:长时间运转或高温引起的轴硫化或轴的变形也可能导致轴向窜动。
如遇到这种情况,需要检查轴的质量,并根据需要更换或修复轴。
4. 轴承润滑不足:轴承的润滑对其正常运行至关重要。
如果轴承润滑不足或使用了不适当的润滑剂,会增加轴承的摩擦,导致轴向窜动。
应正确选择润滑剂,定期检查和补充润滑剂,保持轴承的良好润滑。
5. 加重载或震动:过大的负载或频繁的震动可能导致轴向窜动。
在设计和使用中,应合理控制负载的大小和分布,避免过度震动,从而减少轴承的轴向窜动。
总结:
轴承轴向窜动可能由轴承磨损、安装不当、轴硫化或变形、轴承润滑不足以及加重载或震动等原因引起。
在使用轴承时,需要进行定期维护和检查,确保轴承的正常运转。
同时,合理安装、正确润滑和控制负载大小和震动对于防止轴向窜动也十分重要。
通过采取适当的预防措施和保养措施,可以提高轴承的使用寿命和性能,确保机器的正常工作。
万能轧机轧辊轴向窜动分析与控制
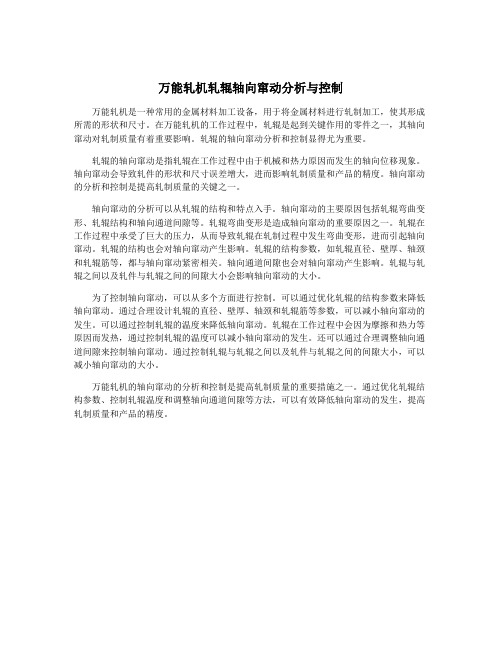
万能轧机轧辊轴向窜动分析与控制万能轧机是一种常用的金属材料加工设备,用于将金属材料进行轧制加工,使其形成所需的形状和尺寸。
在万能轧机的工作过程中,轧辊是起到关键作用的零件之一,其轴向窜动对轧制质量有着重要影响。
轧辊的轴向窜动分析和控制显得尤为重要。
轧辊的轴向窜动是指轧辊在工作过程中由于机械和热力原因而发生的轴向位移现象。
轴向窜动会导致轧件的形状和尺寸误差增大,进而影响轧制质量和产品的精度。
轴向窜动的分析和控制是提高轧制质量的关键之一。
轴向窜动的分析可以从轧辊的结构和特点入手。
轴向窜动的主要原因包括轧辊弯曲变形、轧辊结构和轴向通道间隙等。
轧辊弯曲变形是造成轴向窜动的重要原因之一。
轧辊在工作过程中承受了巨大的压力,从而导致轧辊在轧制过程中发生弯曲变形,进而引起轴向窜动。
轧辊的结构也会对轴向窜动产生影响。
轧辊的结构参数,如轧辊直径、壁厚、轴颈和轧辊筋等,都与轴向窜动紧密相关。
轴向通道间隙也会对轴向窜动产生影响。
轧辊与轧辊之间以及轧件与轧辊之间的间隙大小会影响轴向窜动的大小。
为了控制轴向窜动,可以从多个方面进行控制。
可以通过优化轧辊的结构参数来降低轴向窜动。
通过合理设计轧辊的直径、壁厚、轴颈和轧辊筋等参数,可以减小轴向窜动的发生。
可以通过控制轧辊的温度来降低轴向窜动。
轧辊在工作过程中会因为摩擦和热力等原因而发热,通过控制轧辊的温度可以减小轴向窜动的发生。
还可以通过合理调整轴向通道间隙来控制轴向窜动。
通过控制轧辊与轧辊之间以及轧件与轧辊之间的间隙大小,可以减小轴向窜动的大小。
万能轧机的轴向窜动的分析和控制是提高轧制质量的重要措施之一。
通过优化轧辊结构参数、控制轧辊温度和调整轴向通道间隙等方法,可以有效降低轴向窜动的发生,提高轧制质量和产品的精度。
万能轧机轧辊轴向窜动分析与控制
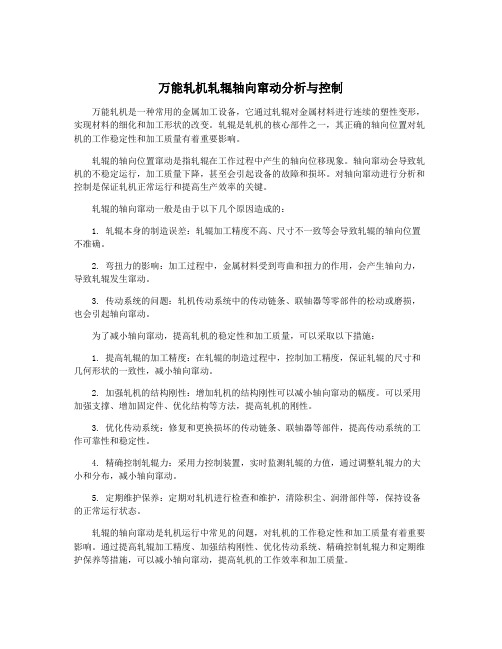
万能轧机轧辊轴向窜动分析与控制万能轧机是一种常用的金属加工设备,它通过轧辊对金属材料进行连续的塑性变形,实现材料的细化和加工形状的改变。
轧辊是轧机的核心部件之一,其正确的轴向位置对轧机的工作稳定性和加工质量有着重要影响。
轧辊的轴向位置窜动是指轧辊在工作过程中产生的轴向位移现象。
轴向窜动会导致轧机的不稳定运行,加工质量下降,甚至会引起设备的故障和损坏。
对轴向窜动进行分析和控制是保证轧机正常运行和提高生产效率的关键。
轧辊的轴向窜动一般是由于以下几个原因造成的:1. 轧辊本身的制造误差:轧辊加工精度不高、尺寸不一致等会导致轧辊的轴向位置不准确。
2. 弯扭力的影响:加工过程中,金属材料受到弯曲和扭力的作用,会产生轴向力,导致轧辊发生窜动。
3. 传动系统的问题:轧机传动系统中的传动链条、联轴器等零部件的松动或磨损,也会引起轴向窜动。
为了减小轴向窜动,提高轧机的稳定性和加工质量,可以采取以下措施:1. 提高轧辊的加工精度:在轧辊的制造过程中,控制加工精度,保证轧辊的尺寸和几何形状的一致性,减小轴向窜动。
2. 加强轧机的结构刚性:增加轧机的结构刚性可以减小轴向窜动的幅度。
可以采用加强支撑、增加固定件、优化结构等方法,提高轧机的刚性。
3. 优化传动系统:修复和更换损坏的传动链条、联轴器等部件,提高传动系统的工作可靠性和稳定性。
4. 精确控制轧辊力:采用力控制装置,实时监测轧辊的力值,通过调整轧辊力的大小和分布,减小轴向窜动。
5. 定期维护保养:定期对轧机进行检查和维护,清除积尘、润滑部件等,保持设备的正常运行状态。
轧辊的轴向窜动是轧机运行中常见的问题,对轧机的工作稳定性和加工质量有着重要影响。
通过提高轧辊加工精度、加强结构刚性、优化传动系统、精确控制轧辊力和定期维护保养等措施,可以减小轴向窜动,提高轧机的工作效率和加工质量。
轧机轴向力产生的原因及减少轴承在线损坏的改进方法
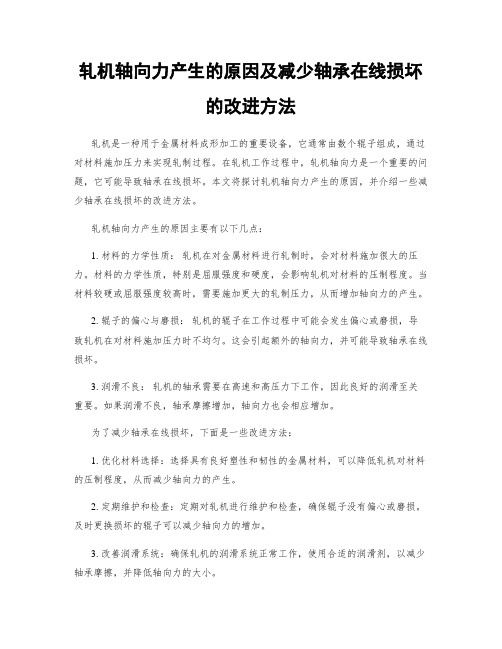
轧机轴向力产生的原因及减少轴承在线损坏的改进方法轧机是一种用于金属材料成形加工的重要设备,它通常由数个辊子组成,通过对材料施加压力来实现轧制过程。
在轧机工作过程中,轧机轴向力是一个重要的问题,它可能导致轴承在线损坏。
本文将探讨轧机轴向力产生的原因,并介绍一些减少轴承在线损坏的改进方法。
轧机轴向力产生的原因主要有以下几点:1. 材料的力学性质:轧机在对金属材料进行轧制时,会对材料施加很大的压力。
材料的力学性质,特别是屈服强度和硬度,会影响轧机对材料的压制程度。
当材料较硬或屈服强度较高时,需要施加更大的轧制压力,从而增加轴向力的产生。
2. 辊子的偏心与磨损:轧机的辊子在工作过程中可能会发生偏心或磨损,导致轧机在对材料施加压力时不均匀。
这会引起额外的轴向力,并可能导致轴承在线损坏。
3. 润滑不良:轧机的轴承需要在高速和高压力下工作,因此良好的润滑至关重要。
如果润滑不良,轴承摩擦增加,轴向力也会相应增加。
为了减少轴承在线损坏,下面是一些改进方法:1. 优化材料选择:选择具有良好塑性和韧性的金属材料,可以降低轧机对材料的压制程度,从而减少轴向力的产生。
2. 定期维护和检查:定期对轧机进行维护和检查,确保辊子没有偏心或磨损。
及时更换损坏的辊子可以减少轴向力的增加。
3. 改善润滑系统:确保轧机的润滑系统正常工作,使用合适的润滑剂,以减少轴承摩擦,并降低轴向力的大小。
4. 使用轴向力控制装置:安装轴向力控制装置可以实时监测轴向力的大小,并采取相应的措施来减少轴向力的产生。
综上所述,轧机轴向力的产生是由材料的力学性质、辊子的偏心与磨损以及润滑不良等因素引起的。
通过优化材料选择、定期维护和检查、改善润滑系统以及使用轴向力控制装置等改进方法,可以减少轴承在线损坏并提高轧机的工作效率。
万能轧机轧辊轴向窜动分析与控制

万能轧机轧辊轴向窜动分析与控制随着高速铁路的迅速发展,重轨产品的质量要求越来越高,部分尺寸已达到板带材精度的要求。
本文结合万能轧机生产重轨时出现的轧辊轴向窜动进行了影响分析、窜动值测量、原因分析及控制实施。
标签:万能轧机;轧辊轴向窜动;分析控制1、前言轧辊与两端的轴承座连接在一起,上机后上辊在轴承座内无法移动,而下辊可通过轴向调整装置实现轴向窜动。
本文所述方法对轧辊轴向窜动进行了较好的控制,轧辊轴向窜动由4-5mm减少到1mm左右,大幅度降低了轧机轴向窜动值。
2、轧辊轴向窜动现状分析2.1軋辊轴向固定与磨损轧辊与两端的轴承座连接在一起,上机后上辊在轴承座内无法移动,而下辊可通过轴向调整装置实现轴向窜动。
使用中轴承座、轴承及轧辊连接紧密,轧辊相对于轴承的轴向窜动小,在轴承使用后期在0.3mm以内。
2.2轴向窜动的调整万能轧机采用四辊轧制,与普通轧制相比,控制难度较大,辊缝调整要求沿轧制中心线对中调整。
在空载情况下,辊缝调零的目的就是确定机械的参照点,亦即上、下水平辊和左、右立辊辊缝压靠,此时上、下水平辊轴向位置作为液压动态轴向控制的基准,上、下轴承座均与上、下水平辊相连。
上下水平辊、左右立辊均采用电气传动控制。
轴向位置采用液压伺服阀控制。
动态轧制过程中,势必造成上、下辊轴向产生位移,为此系统采用保持板FC缸、增压缸相互配合来保证上下水平辊的轴向位置。
动态轴向位置控制是以上辊轴向位置为基准,通过对下辊的轴向位置控制来完成动态的调整过程。
控制系统由2台PLC控制,其中一台控制液压平衡、伺服阀电源OK、位置传感器、伺服阀的电流信号采集、液压压力采集、液压缸位置行程编码器、动态轴向偏差值计算、保持板(FC)基准值计算及增压缸控制基准值计算等。
另一台PLC则进行液压位置控制。
2.3轴向窜动值测量2.3.1静态测量静态测量是指换完辊并做完标定后用塞尺测量耐磨板3、耐磨板4的间隙。
此时轧机没有轧件通过,不存在轴向力,立辊标定力(500KN)只起定位作用,也会消除轧机各部位连接间隙,用塞尺测出的间隙值小于均0.1毫米。
轴承轴向窜动的原因

轴承轴向窜动的原因引言轴承是机械设备中常见的关键部件之一,用于支撑和转动轴。
然而,在使用过程中,轴承轴向窜动是一个常见的问题,会导致设备的不稳定性和运行故障。
本文将详细介绍轴承轴向窜动的原因,以及可能的解决方法。
1. 轴承轴向窜动的定义轴承轴向窜动指的是轴在轴承内部产生沿轴向方向的移动现象。
通常情况下,轴承应该能够承受轴的旋转和一定的轴向力,但当轴向力过大或其他因素导致轴承失效时,轴就会发生窜动。
2. 轴承轴向窜动的原因轴承轴向窜动的原因有多种,下面列举了一些常见的原因:2.1 轴向载荷过大当设备的工作负荷超过轴承的承载能力时,轴承容易发生轴向窜动。
这可能是由于设计不当、工作条件改变或设备故障等原因导致的。
2.2 轴承间隙过大轴承在安装过程中需要预留一定的间隙,以确保轴承的正常运转。
然而,如果轴承间隙过大,就会导致轴向窜动的发生。
2.3 轴承磨损长时间的使用会导致轴承磨损,进而导致轴向窜动。
磨损可能是由于使用寿命到期、润滑不足或污染物进入轴承等原因引起的。
2.4 轴承安装不当轴承的安装过程需要严格按照规范进行,如果安装不当,如轴承偏斜、不平行或不垂直等,都可能导致轴向窜动的发生。
2.5 温度变化轴承的工作温度变化也可能导致轴向窜动。
当温度升高时,由于热胀冷缩效应,轴承内部的尺寸会发生变化,从而导致轴向窜动。
2.6 润滑不良轴承需要适当的润滑以减少摩擦和磨损。
如果润滑不足或润滑剂质量不合格,就会导致轴承轴向窜动。
3. 轴承轴向窜动的解决方法为了解决轴承轴向窜动问题,可以采取以下一些方法:3.1 调整轴向载荷在设计设备时,应根据实际工作负荷选择合适的轴承和轴向载荷。
如果轴向载荷过大,可以考虑增加轴承数量或采用更高承载能力的轴承。
3.2 控制轴承间隙在轴承安装过程中,要按照规范进行操作,确保轴承间隙在合理范围内。
如果间隙过大,可以采取调整或更换轴承的方法来解决问题。
3.3 定期维护和更换轴承定期维护和更换轴承是保持设备正常运行的重要措施。
万能轧机轧辊轴向窜动分析与控制
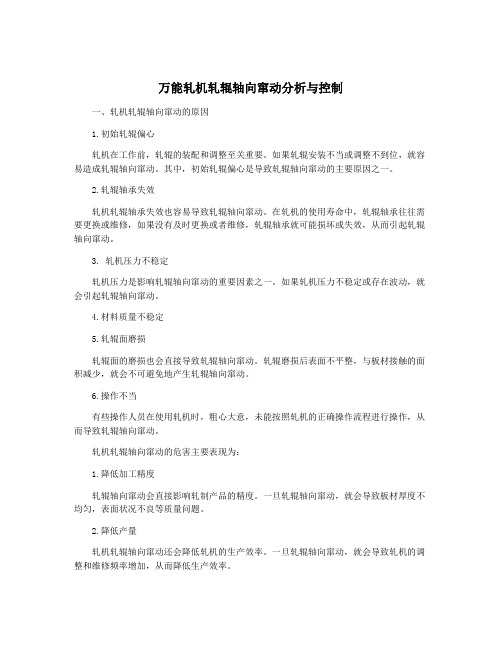
万能轧机轧辊轴向窜动分析与控制一、轧机轧辊轴向窜动的原因1.初始轧辊偏心轧机在工作前,轧辊的装配和调整至关重要。
如果轧辊安装不当或调整不到位,就容易造成轧辊轴向窜动。
其中,初始轧辊偏心是导致轧辊轴向窜动的主要原因之一。
2.轧辊轴承失效轧机轧辊轴承失效也容易导致轧辊轴向窜动。
在轧机的使用寿命中,轧辊轴承往往需要更换或维修,如果没有及时更换或者维修,轧辊轴承就可能损坏或失效,从而引起轧辊轴向窜动。
3. 轧机压力不稳定轧机压力是影响轧辊轴向窜动的重要因素之一。
如果轧机压力不稳定或存在波动,就会引起轧辊轴向窜动。
4.材料质量不稳定5.轧辊面磨损轧辊面的磨损也会直接导致轧辊轴向窜动。
轧辊磨损后表面不平整,与板材接触的面积减少,就会不可避免地产生轧辊轴向窜动。
6.操作不当有些操作人员在使用轧机时,粗心大意,未能按照轧机的正确操作流程进行操作,从而导致轧辊轴向窜动。
轧机轧辊轴向窜动的危害主要表现为:1.降低加工精度轧辊轴向窜动会直接影响轧制产品的精度。
一旦轧辊轴向窜动,就会导致板材厚度不均匀,表面状况不良等质量问题。
2.降低产量轧机轧辊轴向窜动还会降低轧机的生产效率。
一旦轧辊轴向窜动,就会导致轧机的调整和维修频率增加,从而降低生产效率。
3.增加能耗4.安全隐患轧机轧辊轴向窜动也会增加安全隐患。
一旦轧机轧辊轴向窜动,轧辊就可能离轨或碰撞,从而导致设备故障或人员伤亡。
针对轧机轧辊轴向窜动的问题,我们提出以下控制方案:1.优化轧辊安装和调整工艺轧辊在安装和调整时需要注意以下几个方面:(1)保证轧辊加工精度和轮廓尺寸的一致性;(2)调整轧辊与轧辊架的间隙,保证轧辊处于正确的位置;(3)保证轧辊与轧机传动系统的配合精度。
通过以上措施,可以有效减少初始轧辊偏心,从而降低轧辊轴向窜动的风险。
2.及时检修和更换轧辊轴承检查轧辊轴承状态,发现损坏及时更换,保证轧辊的正常转动,从而减少轧辊轴向窜动的风险。
通过优化轧机压力稳定控制系统,提升其稳定性和控制精度,降低轧辊轴向窜动的风险。
万能轧机轧辊轴向窜动分析与控制
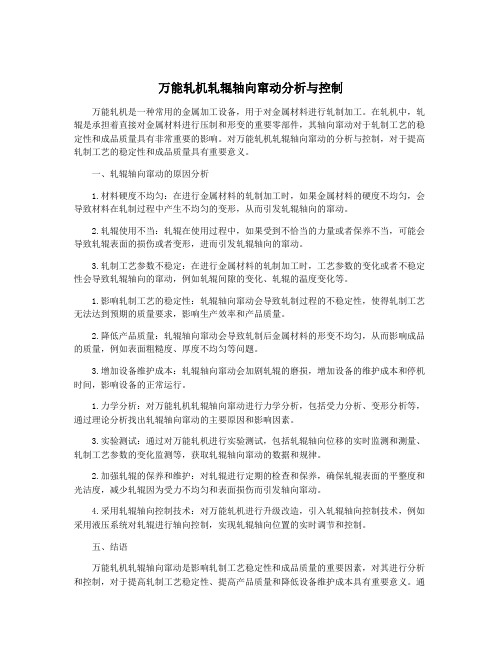
万能轧机轧辊轴向窜动分析与控制万能轧机是一种常用的金属加工设备,用于对金属材料进行轧制加工。
在轧机中,轧辊是承担着直接对金属材料进行压制和形变的重要零部件,其轴向窜动对于轧制工艺的稳定性和成品质量具有非常重要的影响。
对万能轧机轧辊轴向窜动的分析与控制,对于提高轧制工艺的稳定性和成品质量具有重要意义。
一、轧辊轴向窜动的原因分析1.材料硬度不均匀:在进行金属材料的轧制加工时,如果金属材料的硬度不均匀,会导致材料在轧制过程中产生不均匀的变形,从而引发轧辊轴向的窜动。
2.轧辊使用不当:轧辊在使用过程中,如果受到不恰当的力量或者保养不当,可能会导致轧辊表面的损伤或者变形,进而引发轧辊轴向的窜动。
3.轧制工艺参数不稳定:在进行金属材料的轧制加工时,工艺参数的变化或者不稳定性会导致轧辊轴向的窜动,例如轧辊间隙的变化、轧辊的温度变化等。
1.影响轧制工艺的稳定性:轧辊轴向窜动会导致轧制过程的不稳定性,使得轧制工艺无法达到预期的质量要求,影响生产效率和产品质量。
2.降低产品质量:轧辊轴向窜动会导致轧制后金属材料的形变不均匀,从而影响成品的质量,例如表面粗糙度、厚度不均匀等问题。
3.增加设备维护成本:轧辊轴向窜动会加剧轧辊的磨损,增加设备的维护成本和停机时间,影响设备的正常运行。
1.力学分析:对万能轧机轧辊轴向窜动进行力学分析,包括受力分析、变形分析等,通过理论分析找出轧辊轴向窜动的主要原因和影响因素。
3.实验测试:通过对万能轧机进行实验测试,包括轧辊轴向位移的实时监测和测量、轧制工艺参数的变化监测等,获取轧辊轴向窜动的数据和规律。
2.加强轧辊的保养和维护:对轧辊进行定期的检查和保养,确保轧辊表面的平整度和光洁度,减少轧辊因为受力不均匀和表面损伤而引发轴向窜动。
4.采用轧辊轴向控制技术:对万能轧机进行升级改造,引入轧辊轴向控制技术,例如采用液压系统对轧辊进行轴向控制,实现轧辊轴向位置的实时调节和控制。
五、结语万能轧机轧辊轴向窜动是影响轧制工艺稳定性和成品质量的重要因素,对其进行分析和控制,对于提高轧制工艺稳定性、提高产品质量和降低设备维护成本具有重要意义。
万能轧机轴承座轴向窜动超差原因分析及控制
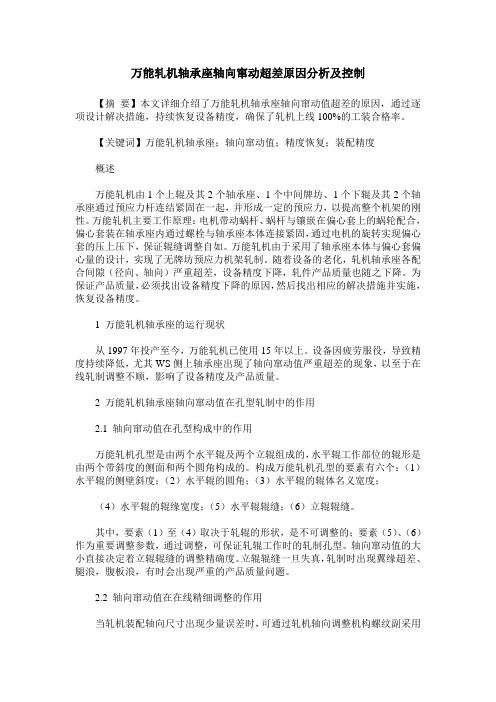
万能轧机轴承座轴向窜动超差原因分析及控制【摘要】本文详细介绍了万能轧机轴承座轴向窜动值超差的原因,通过逐项设计解决措施,持续恢复设备精度,确保了轧机上线100%的工装合格率。
【关键词】万能轧机轴承座;轴向窜动值;精度恢复;装配精度概述万能轧机由1个上辊及其2个轴承座、1个中间牌坊、1个下辊及其2个轴承座通过预应力杆连结紧固在一起,并形成一定的预应力,以提高整个机架的刚性。
万能轧机主要工作原理:电机带动蜗杆、蜗杆与镶嵌在偏心套上的蜗轮配合,偏心套装在轴承座内通过螺栓与轴承座本体连接紧固,通过电机的旋转实现偏心套的压上压下,保证辊缝调整自如。
万能轧机由于采用了轴承座本体与偏心套偏心量的设计,实现了无牌坊预应力机架轧制。
随着设备的老化,轧机轴承座各配合间隙(径向、轴向)严重超差,设备精度下降,轧件产品质量也随之下降。
为保证产品质量,必须找出设备精度下降的原因,然后找出相应的解决措施并实施,恢复设备精度。
1 万能轧机轴承座的运行现状从1997年投产至今,万能轧机已使用15年以上。
设备因疲劳服役,导致精度持续降低,尤其WS侧上轴承座出现了轴向窜动值严重超差的现象,以至于在线轧制调整不顺,影响了设备精度及产品质量。
2 万能轧机轴承座轴向窜动值在孔型轧制中的作用2.1 轴向窜动值在孔型构成中的作用万能轧机孔型是由两个水平辊及两个立辊组成的,水平辊工作部位的辊形是由两个带斜度的侧面和两个圆角构成的。
构成万能轧机孔型的要素有六个:(1)水平辊的侧壁斜度;(2)水平辊的圆角;(3)水平辊的辊体名义宽度;(4)水平辊的辊缘宽度;(5)水平辊辊缝;(6)立辊辊缝。
其中,要素(1)至(4)取决于轧辊的形状,是不可调整的;要素(5)、(6)作为重要调整参数,通过调整,可保证轧辊工作时的轧制孔型。
轴向窜动值的大小直接决定着立辊辊缝的调整精确度。
立辊辊缝一旦失真,轧制时出现翼缘超差、腿浪,腹板浪,有时会出现严重的产品质量问题。
万能轧机轧辊轴向窜动分析与控制

万能轧机轧辊轴向窜动分析与控制【摘要】本文主要围绕万能轧机轧辊轴向窜动进行分析与控制展开讨论。
在将介绍研究的背景和意义。
在将深入探讨轧机轴向窜动的原理、影响因素、检测方法以及控制方法,并对不同的控制策略进行比较。
最后在将对文章进行总结并展望未来的研究方向。
通过本文的研究,可以更好地了解轧机轴向窜动的机理与影响因素,为轧机的稳定运行和优化控制提供理论依据和实用指导。
本文的研究对于提高轧机生产效率、产品质量和设备寿命具有重要意义。
【关键词】轧机轧辊、轧辊轴向窜动、检测、控制、控制策略、研究背景、研究意义、原理、影响因素、展望1. 引言1.1 研究背景轧机轧辊在工业生产中扮演着重要的角色,其轧辊轴向窜动问题一直是制约轧机性能的一个重要因素。
轧辊轴向窜动会导致产品质量不稳定、产能降低、设备磨损加剧等问题,给生产带来诸多不利影响。
对轧辊轴向窜动进行深入研究具有重要的意义。
轧机轧辊轴向窜动问题的研究起源于对轧机性能提升的需求。
随着工业生产的发展,对产品质量和生产效率要求越来越高,轧机轧辊轴向窜动成为制约轧机性能提升的瓶颈之一。
探究轧辊轴向窜动的原理和影响因素,以及寻找有效的检测和控制方法,对于提高轧机生产效率、产品质量和设备稳定性具有重要意义。
为了解决轧辊轴向窜动问题,需深入研究轧机的工作原理和轧辊轴向窜动的影响因素,从而提出有效的控制方法。
通过比较不同的控制策略,找到最适合的控制方案,为解决轧辊轴向窜动问题提供科学依据。
对轧机轧辊轴向窜动进行分析和控制研究具有重要意义,将对轧机行业的发展和生产效率的提升产生积极影响。
1.2 研究意义轧机轧辊轴向窜动是轧机生产过程中一个重要且常见的问题,它直接影响着轧辊与工件之间的接触质量和轧制成形的稳定性。
轧机轧辊轴向窜动的存在会导致轧件尺寸精度下降、表面质量变差甚至轧机设备损坏,严重影响着轧机生产的效率和质量。
研究轧机轧辊轴向窜动分析与控制具有重要的理论和实践意义。
通过深入分析轧机轴向窜动的原理和影响因素,可以帮助我们更好地理解其产生机理,为进一步制定有效的检测和控制策略奠定基础。
万能轧机轧辊轴向窜动分析与控制
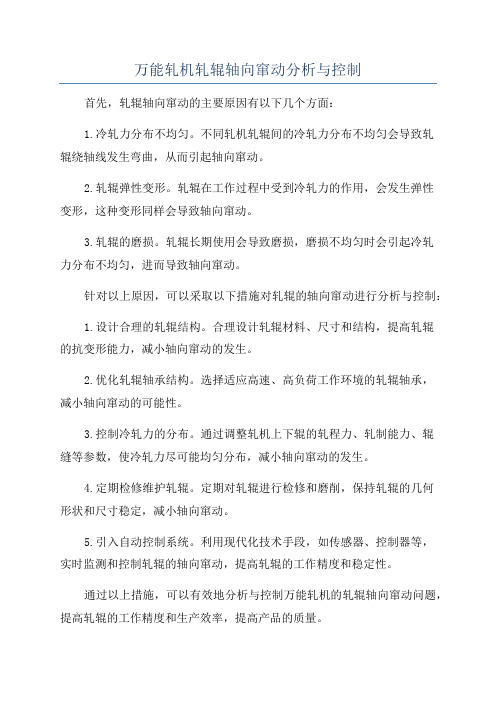
万能轧机轧辊轴向窜动分析与控制
首先,轧辊轴向窜动的主要原因有以下几个方面:
1.冷轧力分布不均匀。
不同轧机轧辊间的冷轧力分布不均匀会导致轧
辊绕轴线发生弯曲,从而引起轴向窜动。
2.轧辊弹性变形。
轧辊在工作过程中受到冷轧力的作用,会发生弹性
变形,这种变形同样会导致轴向窜动。
3.轧辊的磨损。
轧辊长期使用会导致磨损,磨损不均匀时会引起冷轧
力分布不均匀,进而导致轴向窜动。
针对以上原因,可以采取以下措施对轧辊的轴向窜动进行分析与控制:
1.设计合理的轧辊结构。
合理设计轧辊材料、尺寸和结构,提高轧辊
的抗变形能力,减小轴向窜动的发生。
2.优化轧辊轴承结构。
选择适应高速、高负荷工作环境的轧辊轴承,
减小轴向窜动的可能性。
3.控制冷轧力的分布。
通过调整轧机上下辊的轧程力、轧制能力、辊
缝等参数,使冷轧力尽可能均匀分布,减小轴向窜动的发生。
4.定期检修维护轧辊。
定期对轧辊进行检修和磨削,保持轧辊的几何
形状和尺寸稳定,减小轴向窜动。
5.引入自动控制系统。
利用现代化技术手段,如传感器、控制器等,
实时监测和控制轧辊的轴向窜动,提高轧辊的工作精度和稳定性。
通过以上措施,可以有效地分析与控制万能轧机的轧辊轴向窜动问题,提高轧辊的工作精度和生产效率,提高产品的质量。
万能轧机轧辊轴向窜动分析与控制
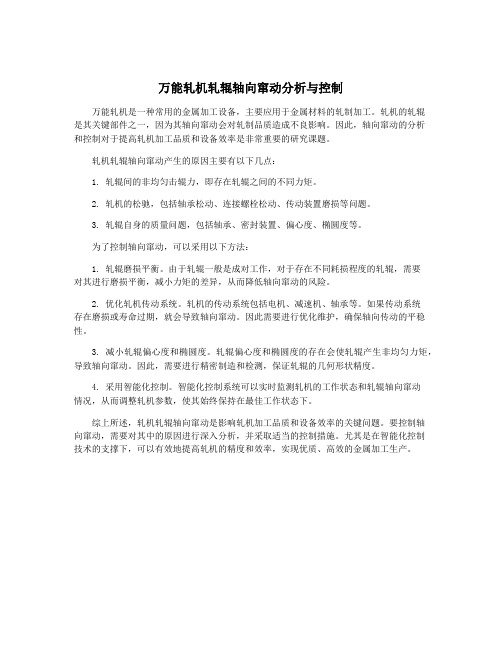
万能轧机轧辊轴向窜动分析与控制万能轧机是一种常用的金属加工设备,主要应用于金属材料的轧制加工。
轧机的轧辊是其关键部件之一,因为其轴向窜动会对轧制品质造成不良影响。
因此,轴向窜动的分析和控制对于提高轧机加工品质和设备效率是非常重要的研究课题。
轧机轧辊轴向窜动产生的原因主要有以下几点:1. 轧辊间的非均匀击辊力,即存在轧辊之间的不同力矩。
2. 轧机的松驰,包括轴承松动、连接螺栓松动、传动装置磨损等问题。
3. 轧辊自身的质量问题,包括轴承、密封装置、偏心度、椭圆度等。
为了控制轴向窜动,可以采用以下方法:1. 轧辊磨损平衡。
由于轧辊一般是成对工作,对于存在不同耗损程度的轧辊,需要对其进行磨损平衡,减小力矩的差异,从而降低轴向窜动的风险。
2. 优化轧机传动系统。
轧机的传动系统包括电机、减速机、轴承等。
如果传动系统存在磨损或寿命过期,就会导致轴向窜动。
因此需要进行优化维护,确保轴向传动的平稳性。
3. 减小轧辊偏心度和椭圆度。
轧辊偏心度和椭圆度的存在会使轧辊产生非均匀力矩,导致轴向窜动。
因此,需要进行精密制造和检测,保证轧辊的几何形状精度。
4. 采用智能化控制。
智能化控制系统可以实时监测轧机的工作状态和轧辊轴向窜动情况,从而调整轧机参数,使其始终保持在最佳工作状态下。
综上所述,轧机轧辊轴向窜动是影响轧机加工品质和设备效率的关键问题。
要控制轴向窜动,需要对其中的原因进行深入分析,并采取适当的控制措施。
尤其是在智能化控制技术的支撑下,可以有效地提高轧机的精度和效率,实现优质、高效的金属加工生产。
万能轧机轧辊轴向窜动分析与控制

万能轧机轧辊轴向窜动分析与控制陶功明吴远洪赵云文本超(攀钢钒轨梁厂,攀枝花 617062)摘 要轧辊轴向窜动在钢材轧制中普遍存在,轧机空间小、周围环境恶劣导致测量困难,轧制前无法预调。
由于断面的特殊性,重轨万能轧制过程中轴向窜动造成上下断面对称度不合、出钢扭转及弯曲损坏辅助设备等问题。
本文分析了轧辊轴向窜动的原因,介绍了轧辊轴向窜动的处理方法和效果。
通过本文介绍的方法解决了轧辊轴向窜动问题,处理后的轧辊轴向窜动值由原来的4~5mm变为了1~1.5mm,大大提高了轧机的轧制精度。
关键词 万能轧机轴向窜动测量装置分析与控制Analysis and Control of Axial Float of Universal MillTao Gongming Wu Yuanhong Zhao Yun Wen Benchao( Rail and Beam Plant of PZH Steel and Vanadium company, Panzhihua, 617062)Abstract Roll axial float generally exists in the production of steel products, and it is difficult to measure and can not be pre-adjusted because of small mill-space and abominable circumstance. Because of the asymmetry of rail, the force of axial float is very great and this will result in non-acceptance of rail size, rail twist and bend, and damaging equipment and other issues. The influence of axial float on size and exit-universal-mill of work piece has been analyzed using numerical simulation method, the solving method to the axial float has been implemented, and the amount of axial float becomes 1~1.5mm from 4~5mm, and the rolling precision improved greatly.Key words universal mill, axial float, measurement equipment, analysis and control1 引言轧辊轴向窜动在板带轧机中普遍存在,并引起了广泛的关注。
万能轧机轧辊轴向窜动分析与控制

万能轧机轧辊轴向窜动分析与控制
万能轧机是金属加工行业中常用的设备之一,用于对金属材料进行塑性变形。
轧机轧
辊是轧机的核心部件,具有很高的精度要求。
轧辊的轴向窜动会对轧机的加工精度和质量
产生重要影响。
对轧辊轴向窜动进行分析和控制是提高轧机加工质量的关键问题之一。
轧辊轴向窜动一般是指轧辊在运行过程中在轴向方向上发生的位移。
导致轧辊轴向窜
动的原因主要有以下几点:
1. 轧辊轴承的不平衡:轧辊轴承的不平衡会导致轧辊在运行过程中产生不均匀的力,进而引起轴向位移。
2. 轧辊支撑结构的刚度不足:轧辊支撑结构的刚度不足会导致轧辊在受力时发生弯曲,引起轴向位移。
针对轧辊轴向窜动问题,可以采取以下的分析与控制措施:
1. 设计合理的轧辊支撑结构:通过合理设计轧辊支撑结构的刚度和精度,可以有效
减小轧辊轴向窜动。
3. 加强轧辊磨削精度控制:通过提高磨削技术和设备的精度,减小轧辊表面的不均
匀性,减少轧辊轴向窜动。
4. 定期对轧辊进行维护与检修:定期检查轧辊的磨损情况,进行必要的维护与检修,保证轧辊的表面光滑度和几何形状的精度。
万能轧机轧辊轴向窜动的分析与控制是保证轧机加工质量的重要环节。
通过优化设计、改善工艺和加强维护等措施,可以有效减小轧辊轴向窜动,提高轧机的加工精度和质量。
万能轧机轧辊轴向窜动分析与控制

万能轧机轧辊轴向窜动分析与控制
万能轧机是一种用于加工金属材料的设备,其关键组成部分为轧辊。
在轧制过程中,
轧辊轴向窜动是一种常见的问题,可能会导致产品尺寸偏差、表面质量不均匀等质量问题。
因此,轧辊轴向窜动的分析与控制对于保证产品质量和提高生产效率具有重要意义。
轧辊轴向窜动的原因主要包括以下几点:
1.轧辊直径的不一致性:在制造轧辊时,由于工艺和设备的限制,轧辊直径会存在一
定的偏差,导致轧辊之间在实际使用过程中的滚动阻力差异较大,从而引起轴向窜动。
2.轧辊轴承的不良:轧辊轴承的损坏、松动或间隙过大都可能导致轴向窜动。
3.钢材入口处的不良:材料入口处的引导辊或导板因磨损或设计不当,也可能导致材
料在加工过程中出现轴向移动。
为了解决轧辊轴向窜动带来的质量问题,需要采取一系列的控制措施。
具体控制手段
包括:
1.优化轧辊和轴承的设计、制造和安装,缩小轧辊直径的偏差,使得轧辊之间的滚动
阻力更加均匀。
2.对于轧辊轴承严格的维护保养,定时检测并更换损坏或松动的轴承。
4.采用自适应控制算法,在生产过程中对轧辊轴向窜动进行实时监测和修正。
以上控制措施是针对轧辊轴向窜动的一般性解决方法,具体的控制方案还需要根据不
同的生产工艺和设备参数进行设计。
在实际应用中,可以采用传感器和控制系统对轧辊轴
向窜动进行控制,以保证产品质量和生产效率的稳定提升。
万能轧机轧辊轴向窜动分析与控制
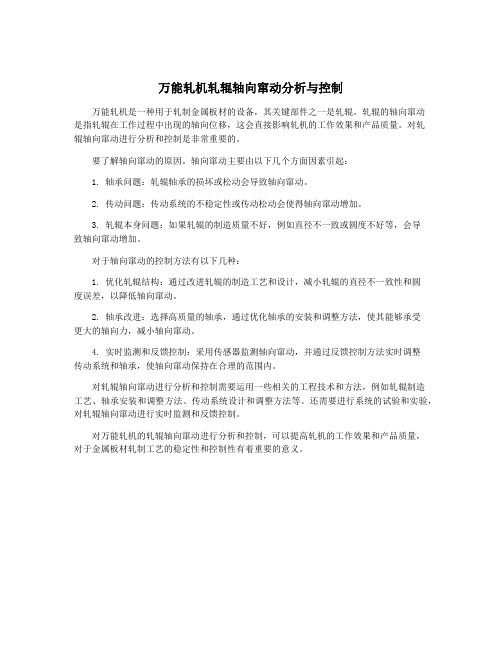
万能轧机轧辊轴向窜动分析与控制
万能轧机是一种用于轧制金属板材的设备,其关键部件之一是轧辊。
轧辊的轴向窜动
是指轧辊在工作过程中出现的轴向位移,这会直接影响轧机的工作效果和产品质量。
对轧
辊轴向窜动进行分析和控制是非常重要的。
要了解轴向窜动的原因。
轴向窜动主要由以下几个方面因素引起:
1. 轴承问题:轧辊轴承的损坏或松动会导致轴向窜动。
2. 传动问题:传动系统的不稳定性或传动松动会使得轴向窜动增加。
3. 轧辊本身问题:如果轧辊的制造质量不好,例如直径不一致或圆度不好等,会导
致轴向窜动增加。
对于轴向窜动的控制方法有以下几种:
1. 优化轧辊结构:通过改进轧辊的制造工艺和设计,减小轧辊的直径不一致性和圆
度误差,以降低轴向窜动。
2. 轴承改进:选择高质量的轴承,通过优化轴承的安装和调整方法,使其能够承受
更大的轴向力,减小轴向窜动。
4. 实时监测和反馈控制:采用传感器监测轴向窜动,并通过反馈控制方法实时调整
传动系统和轴承,使轴向窜动保持在合理的范围内。
对轧辊轴向窜动进行分析和控制需要运用一些相关的工程技术和方法,例如轧辊制造
工艺、轴承安装和调整方法、传动系统设计和调整方法等。
还需要进行系统的试验和实验,对轧辊轴向窜动进行实时监测和反馈控制。
对万能轧机的轧辊轴向窜动进行分析和控制,可以提高轧机的工作效果和产品质量,
对于金属板材轧制工艺的稳定性和控制性有着重要的意义。
精轧机轴承座轴向窜动超差原因分析与控制措施
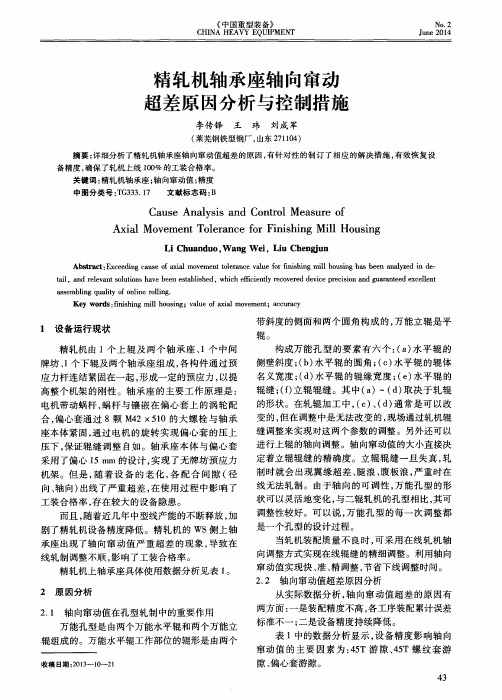
线轧制调整不顺 , 影响了工装合格率。 精 轧机 上轴 承 座具体 使 用数 据分 析见 表 1 。
2 原 因分 析
2 . 2 轴向窜动值超差原 因分析
从 实 际数据 分 析 , 轴 向窜 动值 超 差 的原 因 有 两方 面 : 一是 装 配精度 不高 , 各工 序装 配 累计 误差
L i C h u a n d u o , Wa n g We i , L i u C h e n g j u n
Ab s t r a c t : E x c e e d i n g c a u s e o f a x i a l mo v e me n t t o l e r a n c e v lu a e f o r i f n i s h i n g mi l l h o u s i n g h a s b e e n a n ly a z e d i n d e ・
《 中国重型装备》 C HI N A H E A V Y E Q U I P ME N T
No . 2
J u n e 2 0 1 4
精轧机轴 承座ቤተ መጻሕፍቲ ባይዱ 向窜动 超 差原 因分析 与控制措施
李传铎 王 玮 刘成军
( 莱芜 钢铁 型钢厂 , 山东 2 7 1 1 0 4 )
t a i l ,a n d r e l e v a n t s o l u t i o n s h a v e b e e n e s t a b l i s h e d, wh i c h e ic f i e n t l y r e c o v e r e d d e v i c e p r e c i s i o n a n d g u a r a n t e e d e x c e l l e n t
轴承故障及原因分析与防止措施

轴承故障及原因分析与防止措施运转时有异响1•滚动体或滚道剥落重皮,表面不平2. 轴承零件安装不当,轴承附件有松动和摩擦3. 缺乏润滑剂4. 轴承内有铁屑或污物1. 拆卸检查或更换2. 注意安装质量3. 按规定定时加润滑剂4. 拆卸、清洗或更换滚动体严重磨损1. 轴承承受了不当的轴向载荷2. 滚动体安装歪斜3. 润滑剂太稠4. 滚动体不滚动,产生滑动摩擦,以致磨伤5. 轴承温升过高导致滚动体损伤6. 机械振动或轴承安装不当,使滚动体挤碎7. 轴承制造精度不高,热处理不当,硬度低,滚动体被磨成多棱形1、2按要求保证安装质量3. 按规定使用润滑剂,或定期更换润滑剂4、5、6、7.注意使用中的维护滚道出现坑疤1. 金属剥落,锈蚀2. 缺少润滑剂3. 使用材料不当4. 轴承受冲击载荷5. 电流通过轴承,产生局部高温,金属熔化按轴承的工作性能正确选用轴承按规定定时加润滑剂严禁电气设备漏电,机器要有接地装置1.轴颈或轴承座孔配合面接触不良, 1.按要求保证安装滚道受力部位出现空隙,轴承受力大质量轴承内而不均匀,产生疲劳裂纹 2.按规程正确拆装外圈裂2.拆装不当,安装时受到敲打 3.及时更换磨损的纹 3.轴承间隙磨大造成冲击振动轴承4.轴承制造质量不良,内部有裂纹4.严格检查轴承的制造质量1.轴承受冲击力和交变载荷及滚动体按要求保证安装质表面接触应力反复变化hl2.内外圈安装歪斜,轴向配合台阶面正确使用轴承不垂直,轴弯曲,轴孔不同心注意不要将铁屑和3.轴承间隙调整过紧其他污物落入轴承轴承金4.轴承配合面之间落入铁屑或硬质脏内属剥落物正确选用轴承注意使用维护5. 轴颈或轴承座孔呈椭圆形,导致滚道局部负担过重6. 所选代用或换用轴承型号不符合规定滚动体1.安装间隙过小,挤压力过大合理调整间隙被压2.使用时受到剧烈冲击注意润滑剂的洁净碎,多 3.润滑剂中混入坚硬的铁屑等污物按规定时间更换或出现于 4.滚动体原来有裂纹或轴承使用时检修轴承推力球间过长轴承1•轴承清洗不干净,滚动体与滚道 1.注意清洗质量有砂粒或铁屑2.注意安装质量2.保持架变形,滚动体与轴承圈碰3.刮研轴径(或壳安装后触孔径),使其配合手转不3.轴承和轴(或壳孔)的配合过紧过盈适当减小;轴动(过盈量过大,轴承游隙减少)或轴承原始游隙太小,承原始游隙太小无法修理,必须更换1•轴承上下圈不平行按要求保证安装质轴承滚 2.回转速度过大道产生 3.滚动体在滚道上滑转按使用要求正确选刮痕 4.润滑剂不干净用轴承加强润滑管理。
- 1、下载文档前请自行甄别文档内容的完整性,平台不提供额外的编辑、内容补充、找答案等附加服务。
- 2、"仅部分预览"的文档,不可在线预览部分如存在完整性等问题,可反馈申请退款(可完整预览的文档不适用该条件!)。
- 3、如文档侵犯您的权益,请联系客服反馈,我们会尽快为您处理(人工客服工作时间:9:00-18:30)。
【摘要】本文详细介绍了万能轧机轴承座轴向窜动值超差的原因,通过逐项设计解决措施,持续恢复设备精度,确保了轧机上线100%的工装合格率。
【关键词】万能轧机轴承座;轴向窜动值;精度恢复;装配精度
概述
万能轧机由1个上辊及其2个轴承座、1个中间牌坊、1个下辊及其2个轴承座通过预应力杆连结紧固在一起,并形成一定的预应力,以提高整个机架的刚性。
万能轧机主要工作原理:电机带动蜗杆、蜗杆与镶嵌在偏心套上的蜗轮配合,偏心套装在轴承座内通过螺栓与轴承座本体连接紧固,通过电机的旋转实现偏心套的压上压下,保证辊缝调整自如。
万能轧机由于采用了轴承座本体与偏心套偏心量的设计,实现了无牌坊预应力机架轧制。
随着设备的老化,轧机轴承座各配合间隙(径向、轴向)严重超差,设备精度下降,轧件产品质量也随之下降。
为保证产品质量,必须找出设备精度下降的原因,然后找出相应的解决措施并实施,恢复设备精度。
1 万能轧机轴承座的运行现状
2 万能轧机轴承座轴向窜动值在孔型轧制中的作用
2.1 轴向窜动值在孔型构成中的作用
万能轧机孔型是由两个水平辊及两个立辊组成的,水平辊工作部位的辊形是由两个带斜度的侧面和两个圆角构成的。
构成万能轧机孔型的要素有六个:(1)水平辊的侧壁斜度;(2)水平辊的圆角;(3)水平辊的辊体名义宽度;
(4)水平辊的辊缘宽度;(5)水平辊辊缝;(6)立辊辊缝。
其中,要素(1)至(4)取决于轧辊的形状,是不可调整的;要素(5)、(6)作为重要调整参数,通过调整,可保证轧辊工作时的轧制孔型。
轴向窜动值的大小直接决定着立辊辊缝的调整精确度。
立辊辊缝一旦失真,轧制时出现翼缘超差、腿浪,腹板浪,有时会出现严重的产品质量问题。
2.2 轴向窜动值在在线精细调整的作用
当轧机装配轴向尺寸出现少量误差时,可通过轧机轴向调整机构螺纹副采用轧机轴向调整方式,实现在线辊缝的精细调整,避免或节省下线调整时间。
3 轧机轴承座轴向窜动值测量情况
根据生产现场反馈信息,万能轧机轴承座轴向窜动量较大,对产品质量造成较大影响。
我厂技术人员、现场操作人员及设备维护人员对轴承座轴向窜动情况进行了讨论分析,并对轴承座的窜动量进行了测量。
万能轧机轴承座的轴向窜动量由以下三部分组成:
(1)轧机轴承的轴向游隙(0.085~0.14mm)。
(2)轧机压下机构蜗轮蜗杆的齿侧间隙(0.5~0.85 mm)。
(3)轧机轴向调整机构螺纹副的齿侧间隙(0.125 mm)。
万能轧机轴承座的最大轴向窜动量为1.115毫米(δ=0.14 +0.85+0.125),由于实际使用过程中上述部件之间的磨损不断加大,我厂结合现场实际制定的轴向窜动最大值为1.2毫米。
经过测量,万能轧机轴承座轴向窜动的具体情况汇总如下:
(1)轴向窜动量小于1.2毫米的共2个。
(2)轴向窜动量大于1.2毫米小于1.5毫米的共3个。
(3)轴向窜动量大于1.5毫米小于1.9毫米的共9个。
从测量结果看,80%以上的轴承座轴向窜动量过大,已满足不了轧制工艺要求。
4 精轧机轴承座轴向窜动值超差的原因与分析
轴承座轴向窜动值超差的原因有两方面:一是轴承座各部件的磨损,设备精度持续降低;二是装配精度不高,各装配工序的累计误差。
4.1 设备精度持续降低的原因分析
(1)产量逐年提升,目前已远超设计产量,轧机超负荷运行。
(2)轧机轴承座已连续使用15年以上,新轴承座及蜗轮蜗杆等关键部件的投入较少而且轴承座的修复不足。
上述因素导致设备超期服役、带病作业。
(3)部分超设计规格产品以及特殊钢种的轧制,超过了轧机的轧制能力,导致轧机的设备精度不断恶化。
(4)万能轧机止推轴承轴向游隙因磨损超差。
(5)轧机轴向调整机构螺纹副在轧机调整时轴向持续摩擦转动、轧机在轧件咬入时的瞬时冲击,造成轧机螺纹副齿侧间隙超差。
(6)轧机压下机构蜗轮蜗杆的齿侧间隙因磨损超差。
(7)因堆钢或特殊规格轧制导致轧机过载、轴承座与偏心套的磨损,造成轧机轴承座与偏心套的配合间隙超差。
4.2 装配精度影响轴向窜动值的要素及分析
(1)设备在维护清理更换过程中各接触面清理不彻底;
(2)备件本身接触面的表面粗糙度未达到使用要求;
(3)装配方法(装配过程中存在倾斜现象)不合适;
(4)各连接紧固件未紧固到位,紧固后机械防松未及时加设;
(5)各工序质量确认不到位等。
5 万能轧机轴承座轴向窜动值超差的解决措施
(1)严格按工艺操作规程进行轧机装配和调整,保证轧机装配质量;严格按工艺操作规程进行生产,严禁过负荷、超设计能力轧制。
(2)加大新轴承座及蜗轮蜗杆等关键部件的投入数量,确保实现设备的周期更替,避免设备连续疲劳作业。
(3)采用再制造技术修复轴承座内孔,恢复轴承座的设备精度。
测量轴承座内孔尺寸,当轴承座内孔的磨损量大于0.5mm时,采用特种焊接工艺焊接轴承座内孔并镗削至图纸规定尺寸;测量偏心套外径尺寸,当偏心套外径的磨损量大于0.5mm时,更换偏心套。
(4)设计轧机止推轴承游隙的测量方法,及时测量并更换游隙超差的止推轴承。