pcb流程简介-全制程--By jsea
pcb制作的基本流程
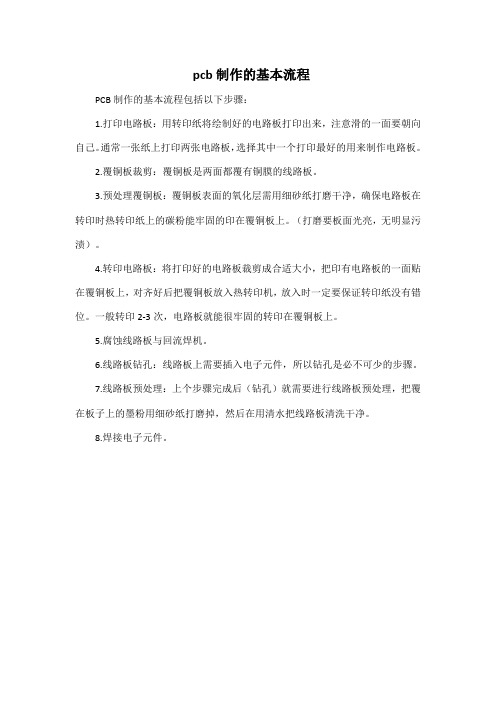
pcb制作的基本流程
PCB制作的基本流程包括以下步骤:
1.打印电路板:用转印纸将绘制好的电路板打印出来,注意滑的一面要朝向自己。
通常一张纸上打印两张电路板,选择其中一个打印最好的用来制作电路板。
2.覆铜板裁剪:覆铜板是两面都覆有铜膜的线路板。
3.预处理覆铜板:覆铜板表面的氧化层需用细砂纸打磨干净,确保电路板在转印时热转印纸上的碳粉能牢固的印在覆铜板上。
(打磨要板面光亮,无明显污渍)。
4.转印电路板:将打印好的电路板裁剪成合适大小,把印有电路板的一面贴在覆铜板上,对齐好后把覆铜板放入热转印机,放入时一定要保证转印纸没有错位。
一般转印2-3次,电路板就能很牢固的转印在覆铜板上。
5.腐蚀线路板与回流焊机。
6.线路板钻孔:线路板上需要插入电子元件,所以钻孔是必不可少的步骤。
7.线路板预处理:上个步骤完成后(钻孔)就需要进行线路板预处理,把覆在板子上的墨粉用细砂纸打磨掉,然后在用清水把线路板清洗干净。
8.焊接电子元件。
pcb流程简介全制程

表面处理
表面处理是PCB制造中的重要环节,主要目的是提高 PCB的可靠性和性能。
输标02入题
表面处理工艺包括镀金、镀银、喷锡等。镀金可以增 强导电性能和耐腐蚀性,镀银可以提高焊接性能,喷 锡则可以提高可焊性和耐热性。
01
03
在表面处理过程中,需要注意防止表面氧化、变色和 脱落等问题。
05
02
制作
将设计好的PCB图转换为实际电路板, 需要进行覆铜、钻孔、电镀等处理。
03
检测
对制作好的电路板进行检测,包括外 观检测、电气性能检测等,确保质量 合格。
04
组装
将电子元器件焊接到电路板上,完成 PCB的组装。
02
PCB设计
原理图设计
总结词
原理图设计是PCB流程的起始阶段,主要任务是创建电路原理图,将电路的功 能需求转化为图形表示。
确保使用的原材料质量合格, 无缺陷且符合设计要求。
生产过程监控
对PCB制造过程中的各个环节 进行严格监控,确保工艺参数
符合标准。
成品检验
对完成的PCB进行全面的质量 检查,包括外观、尺寸、电气
性能等。
环境条件控制
确保生产环境满足温湿度、清 洁度等要求,以降低品质风险
。
可靠性评估方法
寿命测试
模拟实际使用环境,对 PCB进行长时间运行测试 ,评估其寿命和稳定性。
详细描述
PCB布线是电路板设计的最后阶段,它需要考虑布线的长度、宽度、弯曲半径等 因素,以确保电路的电气性能和可靠性。同时,布线还需要考虑制造工艺的要求 ,以确保生产的可行性和效率。
03
PCB材料选择与处
PCB流程简介-全制程
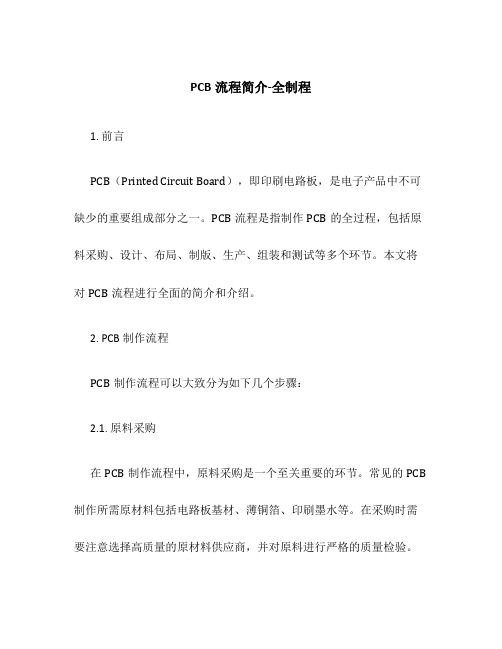
PCB流程简介-全制程1. 前言PCB(Printed Circuit Board),即印刷电路板,是电子产品中不可缺少的重要组成部分之一。
PCB流程是指制作PCB的全过程,包括原料采购、设计、布局、制版、生产、组装和测试等多个环节。
本文将对PCB流程进行全面的简介和介绍。
2. PCB制作流程PCB制作流程可以大致分为如下几个步骤:2.1. 原料采购在PCB制作流程中,原料采购是一个至关重要的环节。
常见的PCB 制作所需原材料包括电路板基材、薄铜箔、印刷墨水等。
在采购时需要注意选择高质量的原材料供应商,并对原料进行严格的质量检验。
2.2. 设计和布局PCB设计是整个流程中重要的阶段之一。
在这个阶段,设计师会使用专业的电路设计软件,根据电子产品的功能要求和电路原理图进行PCB电路板的设计和布局。
设计师需要考虑电路板的大小、层次、电路连接、电源布局等因素,并与其他硬件模块进行兼容性和接口匹配的设计。
2.3. 制版制版是将PCB设计文件转化成实际可用的制板文件的过程。
在这个阶段,设计师会将PCB设计文件输出为Gerber文件,并将Gerber文件发送给制板厂家。
制板厂家会根据Gerber文件进行图形的翻版和制版,最终得到制版后的电路板。
2.4. 生产和组装生产和组装是将制版的电路板进行生产和组装的过程。
在这个阶段,制板厂家会采用先进的生产工艺和设备,将电路板上的电子元器件和连接线进行焊接和组装。
生产和组装的目标是将电路板上的各个元器件正确地安装到预定位置,并确保电路板的良好连接和可靠性。
2.5. 测试和质检测试和质检是确保PCB质量和性能的关键环节。
在这个阶段,制板厂家会进行全面的测试和质检,包括电气测试、可靠性测试和功能测试等。
只有通过了严格的测试和质检,才能确保PCB的质量和可靠性。
3. PCB制作的注意事项在PCB制作流程中,需要注意以下几个重要的事项:3.1. 设计准则在进行PCB设计和布局时,应遵循一些设计准则,如规避电源干扰、保持信号完整性、合理布局元器件和线路等。
简述pcb制作工艺过程

简述pcb制作工艺过程
PCB制作工艺包括以下几个基本步骤:
1. 设计:首先进行电路设计,使用专业PCB设计软件,根据电路要求和功能需求进行布线和布局设计。
2. 制版:将设计好的电路图转变为物理铜板,使用光刻技术将电路图形转移到感光胶片上,再通过化学刻蚀将铜板的电路图形刻蚀出来。
3. 清洗:将刻蚀完成的铜板进行清洗,去除残留的感光胶片和化学蚀刻剂。
4. 高精度加工:对清洗后的铜板进行钻孔、插件和线束位置加工,确保电路板的精度和功能性。
5. 焊接:将需要焊接的元件,如电阻、电容等,通过SMT或THT技术焊接到电路板上。
6. 排线:通过焊接和插件之间的线路连接,将各个功能模块进行电气连接。
7. 防护层:为了保护电路板免受湿气和氧化的损害,在电路板上涂覆一层防护层,通常使用化学镀层或喷涂脂肪酸等材料。
8. 裁剪:将制作好的电路板按照设计要求裁剪成适当的尺寸。
9. 测量和测试:对制作好的电路板进行电气测试,确保电路板的正常工作和可靠性。
10. 组装:将制作好的电路板与相应的外部设备进行组装和连接。
11. 最终检验:对组装好的电路板进行全面检测,确保其功能和性能达到设计要求。
12. 成品包装:对通过检验的电路板进行包装,以保护其不受损坏。
整个过程包括了电路设计、制板、加工、焊接、防护、分切、测试、组装和包装等多个环节,其中每个环节都需要严格操作和控制。
PCB流程简介-全制程
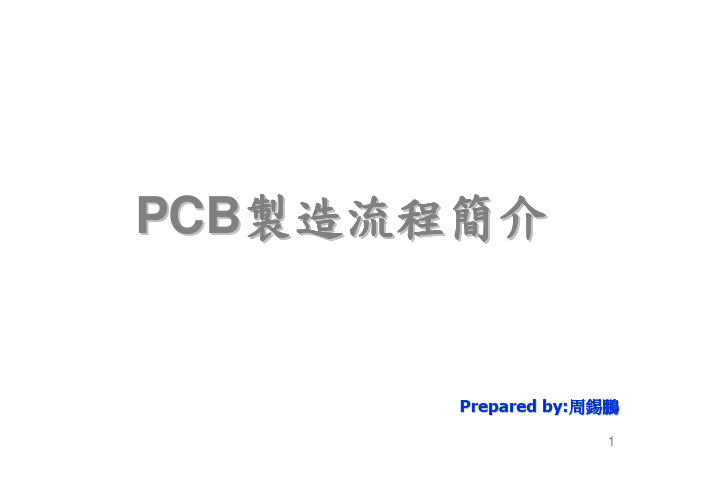
PCB製造流程簡介Prepared by:周錫鵬1PCB制造流程简介(1)内层课内层课介紹介紹介紹::裁板裁板;;内层内层前前处理;压膜;曝光曝光;DES ;DES ;DES连连线CCD CCD冲冲孔;AOI ;AOI检验检验检验;VRS ;VRS ;VRS确确认;黑棕化壓合課介紹壓合課介紹::铆钉铆钉;;叠板;压合;X ;X--Ray Ray鑽靶鑽靶鑽靶;;后处理钻孔课:上PIN;PIN;钻钻孔;下PIN流程介流程介绍绍:目的目的::利用影像利用影像转转移原理制作移原理制作内层线内层线内层线路路DES DES为显为显为显影影;蚀刻;去膜去膜连线简称连线简称前处理涂佈曝光DES 裁板黑棕化裁板裁板(BOARD CUT):(BOARD CUT):目的目的::依制前依制前设计设计设计所所规划要求划要求,,将基板材料裁切成工作所需尺寸 主要原物料主要原物料::基板基板;;鋁片基板由基板由铜铜皮和皮和绝缘层压绝缘层压绝缘层压合而成合而成合而成,,依要求有不同板厚依要求有不同板厚规规格,依铜厚可分厚可分为为H/H;1oz/1oz;2oz/2oz H/H;1oz/1oz;2oz/2oz等种等种等种类类注意事注意事项项:避免板避免板边边巴里影巴里影响响品质,裁切后裁切后进进行磨行磨边边,圆角处理考虑涨缩虑涨缩影影响,薄板需送下制程前薄板需送下制程前进进行烘烤 裁切裁切须须注意机械方向一致的原注意机械方向一致的原则则前处理(PRETREAT): 目的目的::去除銅面上的污染物去除銅面上的污染物,,增加銅面粗糙度加銅面粗糙度,,以利於後續的壓膜制程主要原物料主要原物料::刷輪铜箔绝缘层前处理后铜面状况示意示意图图目的目的::将经处将经处理之基板理之基板理之基板铜铜面COATING 方式涂佈上抗方式涂佈上抗蚀蚀油墨 主要原物料主要原物料::油墨油墨(INK)(INK) 溶劑顯像型半水溶液顯像型鹼水溶液顯像型 水溶型油墨主要是由於其組成中含有機酸根中含有機酸根,,會與強會與強碱碱反應使成為有機酸的鹽類使成為有機酸的鹽類,,可被水溶掉溶掉。
pcb主要生产流程

PCB主要生产流程PCB(Printed Circuit Board,印刷电路板)是电子产品中不可或缺的组成部分,它通过连接电子元件,实现电路的功能。
PCB的生产流程主要包括设计、制版、印刷、成型、组装和测试等步骤。
下面将详细介绍PCB主要生产流程的步骤和流程。
1. 设计PCB的设计是整个生产流程的起点,它决定了电路板的布局、连接方式、尺寸等重要参数。
设计师根据电路原理图和功能需求,使用专业的PCB设计软件进行布线、布局,确定电路板上各个元件的位置和连接方式。
2. 制版制版是将设计好的PCB图纸转化为可供生产使用的制版文件。
制版过程主要包括图纸转换、图纸校对和图纸输出等步骤。
首先,设计师将PCB设计文件转化为制版软件可识别的格式,通常是Gerber格式。
然后,进行图纸校对,检查图纸是否与设计要求一致,是否存在错误或问题。
最后,将校对无误的图纸输出为制版文件,通常是光刻胶层、蚀刻层、钻孔层等。
3. 印刷印刷是将制版文件上的电路图案印制到电路板上的过程。
印刷过程主要包括基材准备、蚀刻、镀铜等步骤。
首先,准备好电路板基材,通常是玻璃纤维增强树脂板(FR-4)。
然后,将制版文件上的图案通过光刻技术转移到电路板上的光刻胶层。
接下来,使用蚀刻液将未被光刻胶保护的铜层蚀刻掉,形成电路图案。
最后,在蚀刻后的电路板上进行镀铜,增加电路板的导电性和耐腐蚀性。
4. 成型成型是将印刷好的电路板进行切割和打孔,使其符合设计要求的尺寸和形状。
成型过程主要包括切割、打孔、去毛刺等步骤。
首先,根据设计要求,将印刷好的电路板进行切割,通常使用切割机进行。
然后,使用钻孔机在电路板上打孔,以便安装元件和连接电路。
最后,去除切割和打孔过程中产生的毛刺,保证电路板表面的平整和光滑。
5. 组装组装是将印刷好的电路板上的元件进行安装和焊接,形成完整的电路功能。
组装过程主要包括元件贴装和焊接等步骤。
首先,将需要安装的元件按照设计要求的位置放置在电路板上。
pcb制作流程
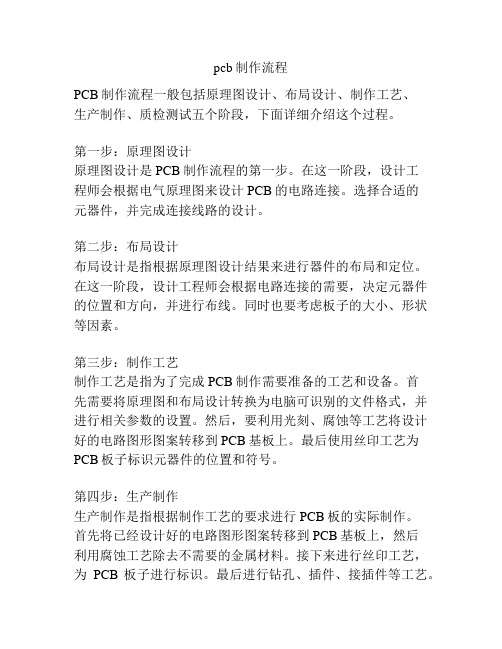
pcb制作流程PCB制作流程一般包括原理图设计、布局设计、制作工艺、生产制作、质检测试五个阶段,下面详细介绍这个过程。
第一步:原理图设计原理图设计是PCB制作流程的第一步。
在这一阶段,设计工程师会根据电气原理图来设计PCB的电路连接。
选择合适的元器件,并完成连接线路的设计。
第二步:布局设计布局设计是指根据原理图设计结果来进行器件的布局和定位。
在这一阶段,设计工程师会根据电路连接的需要,决定元器件的位置和方向,并进行布线。
同时也要考虑板子的大小、形状等因素。
第三步:制作工艺制作工艺是指为了完成PCB制作需要准备的工艺和设备。
首先需要将原理图和布局设计转换为电脑可识别的文件格式,并进行相关参数的设置。
然后,要利用光刻、腐蚀等工艺将设计好的电路图形图案转移到PCB基板上。
最后使用丝印工艺为PCB板子标识元器件的位置和符号。
第四步:生产制作生产制作是指根据制作工艺的要求进行PCB板的实际制作。
首先将已经设计好的电路图形图案转移到PCB基板上,然后利用腐蚀工艺除去不需要的金属材料。
接下来进行丝印工艺,为PCB板子进行标识。
最后进行钻孔、插件、接插件等工艺。
第五步:质检测试质检测试是指对制作好的PCB板进行质量检查和测试。
主要包括外观检查、性能测试、电路连接测试等。
通过对PCB板的检查和测试,来确保其符合设计的要求和标准。
总结:整个PCB制作流程包括原理图设计、布局设计、制作工艺、生产制作、质检测试五个阶段,每个阶段都会对PCB板的质量和性能进行相关的操作和检查。
通过这个流程,可以生产出满足电路连接需求的高质量PCB板。
注:内容参考自个人对有关知识的了解,并结合相关资料整理而成,仅供参考。
PCB制程流程是什么

PCB制程流程是什么PCB制程流程是什么单面板:开料-钻孔-图形转移(包括丝印溼膜,对位暴光,显影)-蚀刻-印阻焊(绿油)-喷锡(分有铅和无铅两种)-印文字-成型(用数控铣床或者冲床)双面板:开料-钻孔-沉铜-图形转移(包括丝印溼膜,对位暴光,显影)-图形电镀(先镀铜后镀锡)-退膜-蚀刻-印阻焊(绿油)-喷锡(分有铅和无铅两种)-印文字-成型(用数控铣床或者冲床)四层板:开料-内层图形转移-内层蚀刻-层压-钻孔-沉铜-外层图形转移-图形电镀-退膜蚀刻-印阻焊(绿油)-喷锡(分有铅和无铅两种)-印文字-成型(用数控铣床或者冲床)基本上一般的流程就是这样了。
从什么资料上看?客户发过来的档案还是什么?有压合的话就是多层板了,压一次是四层,总之每压一次就多两层。
制程检验IPQC流程是什么样的IPQC:是指对全生产过程的品质控制,IPQC的基本流程首先是生产指令到生产现场的整理及装置的除错到首件的检验到IPQC的正式巡查到巡查过程中出现品质异常的处理到品质异常处理的跟踪。
流程图请关注jibu三皮的百度文库,里面有大量的企业管理档案及资料。
制程检验(IPQC)工作流程及工作内容1、IPQC人员应于在每天下班之前了解次日所负责制造部门的生产计划状况,以提前准备检验相关资料。
2、制造部门生产某一产品前,IPQC人员应事先了解查询相关资料:(A)制造命令单;(B)检验用技术图纸;(C)产品用料明细表;(D)检验范围及检验标准;(E)工艺流程、作业指导书(作业标准);(F)品质异常记录;(G)其他相关档案;3、制造部门开始生产时,IPQC人员应协助制造部门主要协助如下:(A)工艺流程查核;(B)相关物料、工装夹具查核;(C)使用计量仪器点检;(D)作业人员品质标准指导;(E)首检产品检验记录;4、IPQC根据图纸、限度样本所检结果合格时,方可正常生产,并极时填写产品首检检验报告与留首检合格产品(生产判定第一个合格品)作为此批生产限度样板。
PCB全流程范文

PCB全流程范文PCB的全流程包括设计、制造和组装,下面将对每个环节进行详细介绍。
1.设计阶段PCB设计是整个流程的关键步骤,它决定了电路连接、功耗分配、布线风格和信号完整性。
首先,设计师根据电路原理图绘制PCB原理图,将电路的各个元件连接起来。
然后,设计师可以使用CAD软件进行布局设计,将元件合理地安置在PCB板上,并确定连接线的走向。
最后,设计师进行布线操作,即连接元器件的引脚,确保信号能够正确地在电路板上流动。
2.制造阶段制造PCB板需要经历多个步骤,包括材料准备、划线、腐蚀、穿孔、镀铜和掩膜等。
首先,根据设计要求,选择合适的基板材料,如玻璃纤维、陶瓷或聚酰亚胺。
然后,使用光刻胶在基板上进行划线,形成电路图案。
接下来,将划好线的基板放入腐蚀液中,除去未被光刻胶保护的部分铜质,形成电路图案的铜层。
然后,在需要连接的地方进行穿孔,以便将元器件插入PCB板上。
接下来,通过电解过程,在整个电路板表面均匀地镀上一层铜,以保护电路板并改善导电性能。
最后,使用掩膜覆盖铜层,以防止短路和腐蚀。
3.组装阶段在PCB板制造完成后,需要将元器件安装到电路板上。
首先,将元器件插入之前预留的穿孔中,确保引脚正确插入,并使用焊锡将其固定在电路板上。
随后,使用焊接技术将元器件与PCB板的引脚连接起来,如表面贴装技术(SMT)或插针焊接。
在焊接完成后,可以进行电路板的测试和调试,以确保电路能够正常工作。
总结PCB的全流程包括设计、制造和组装。
在设计阶段,设计师绘制原理图、进行布局设计和布线操作。
在制造阶段,根据设计要求选择基板材料,进行划线、腐蚀、穿孔、镀铜和掩膜。
在组装阶段,将元器件插入穿孔中,使用焊接技术将其与PCB板连接,并进行测试和调试。
这些步骤共同构成了PCB的全流程,确保电路板能够正常工作。
PCB流程简介-全制程
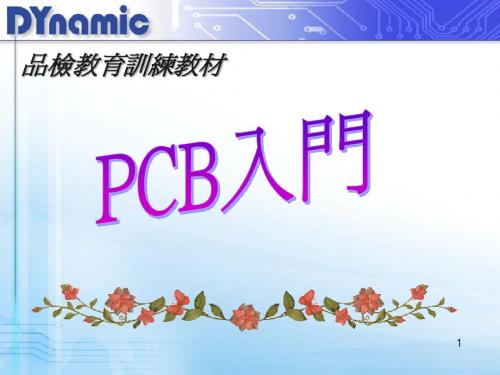
曝光前
曝光后
内层课介绍
显影(DEVELOPING): 显影(DEVELOPING): 目的: 目的: 用碱液作用将未发生化学反 应之油墨 油墨部分冲掉 应之油墨部分冲掉 主要原物料: 主要原物料:Na2CO3 使用将未发生聚合反应之油 使用将未发生聚合反应之油 冲掉, 墨冲掉,而发生聚合反应之 干膜则保留在板面上作为蚀 刻时之抗蚀保护层
内层课介绍
前处理(PRETREAT): 前处理(PRETREAT): 目的: 目的: 去除铜面上的污染物, 去除铜面上的污染物,增 加铜面粗糙度, 加铜面粗糙度,以利於后续 的压膜制程 主要原物料: 主要原物料:刷轮
铜箔 绝缘层
前处理后 铜面状况 示意图
内层课介绍
涂布(COATING): 涂布(COATING): 目的: 目的: 将经处理之基板铜面COATING 将经处理之基板铜面COATING 方式涂布上抗蚀油墨 涂布上抗蚀 方式涂布上抗蚀油墨 主要原物料:油墨(INK) 主要原物料:油墨(INK) 溶剂显像型 半水溶液显像型 油墨 碱水溶液显像型 水溶型油墨主要是由於其组成 中含有机酸根,会与强碱 中含有机酸根,会与强碱反应 使成为有机酸的盐类, 使成为有机酸的盐类,可被水 溶掉. 溶掉.
内层课介绍
黑棕化: 棕化: 目的: 目的: (1)粗化铜面 粗化铜面, (1)粗化铜面,增加与树脂接触表面积 (2)增加铜面对流动树脂之湿润性 (2)增加铜面对流动树脂之湿润性 (3)使铜面钝化 使铜面钝化, (3)使铜面钝化,避免发生不良反应 主要原物料:黑化/ 主要原物料:黑化/棕化药液 注意事项: 注意事项: 黑化/棕化膜很薄,极易发生擦花问题, 黑化/棕化膜很薄,极易发生擦花问题,操作时需注意操 作手势
PCB板生产工艺和制作流程详解

PCB板生产工艺和制作流程详解1. 设计:PCB板的设计是整个制作流程的第一步。
设计师根据电路原理图进行PCB板的布线设计,确定电子元件的安装位置和连接方式。
2. 确定材料:根据设计要求,确定PCB板的基板材料。
常用的基板材料有FR-4玻璃纤维胶片、铝基板、陶瓷基板等。
3. 印制电路:在基板上通过化学腐蚀或机械加工的方法,将设计好的电路图案印制到基板表面。
这一步通常使用光刻技术,将电路图案转移到光刻胶上,然后在化学溶液中去除未曝光的部分。
4. 镀金属化:PCB板上的电路图案通常需要镀上一层金属,以增加导电性。
通常使用的金属化方法包括电镀、喷镀等。
5. 安装元件:在PCB板上进行元件的安装,通常采用表面贴装技术(SMT)或插件式焊接技术。
6. 焊接:通过波峰焊接、回流焊接或手工焊接等方法,将元件与PCB板焊接在一起。
7. 清洗和检验:清洗焊接后的PCB板,去除残留的焊膏和污垢。
然后进行电测试和可视检查,确保PCB板的质量。
8. 包装:对已经检验合格的PCB板进行包装,便于运输和存储。
PCB板的生产工艺和制作流程是复杂而精细的,每一个步骤都需要高度的专业知识和技术。
随着电子技术的发展,PCB板的制作工艺也在不断地更新和完善,以适应更多样化的电子产品需求。
PCB板(Printed Circuit Board)是一种用于支撑和连接电子元件的导电板。
PCB板是现代电子设备中必不可少的部分,它们被广泛应用于手机、计算机、汽车电子、医疗设备等各个领域。
生产PCB板的工艺和制作流程包括以下几个步骤:1. 设计:PCB板的设计是整个制作流程的第一步。
设计师根据电路原理图进行PCB板的布线设计,确定电子元件的安装位置和连接方式。
设计师需要考虑电路的复杂度、电路板的尺寸以及元件的布局等因素,以确保电路的性能和可靠性。
2. 确定材料:根据设计要求,确定PCB板的基板材料。
常用的基板材料有FR-4玻璃纤维胶片、铝基板、陶瓷基板等。
PCB详细工艺流程介绍

PCB详细工艺流程介绍1.开料(CUT)开料是把原始的覆铜板切割成能在生产线上制作的板子的过程首先我们来了解几个概念:(1)UNIT:UNIT是指PCB设计工程师设计的单元图形。
(2)SET:SET是指工程师为了提高生产效率、方便生产等原因,将多个UNIT拼在一起成为的一个整体的图形。
也就是我们常说的拼板,它包括单元图形、工艺边等等。
(3)PANEL:PANEL是指PCB厂家生产时,为了提高效率、方便生产等原因,将多个SET拼在一起并加上工具板边,组成的一块板子。
2.内层干膜(INNER DRY FILM)内层干膜是将内层线路图形转移到PCB板上的过程。
在PCB制作中我们会提到图形转移这个概念,因为导电图形的制作是PCB制作的根本。
所以图形转移过程对PCB制作来说,有非常重要的意义。
内层干膜包括内层贴膜、曝光显影、内层蚀刻等多道工序。
内层贴膜就是在铜板表面贴上一层特殊的感光膜,就是我们所说的干膜。
这种膜遇光会固化,在板子上形成一道保护膜。
曝光显影是将贴好膜的板进行曝光,透光的部分被固化,没透光的部分还是干膜。
然后经过显影,褪掉没固化的干膜,将贴有固化保护膜的板进行蚀刻。
再经过退膜处理,这时内层的线路图形就被转移到板子上了。
其整个工艺流程如下图。
对于设计人员来说,我们最主要考虑的是布线的最小线宽、间距的控制及布线的均匀性。
因为间距过小会造成夹膜,膜无法褪尽造成短路。
线宽太小,膜的附着力不足,造成线路开路。
所以电路设计时的安全间距(包括线与线、线与焊盘、焊盘与焊盘、线与铜面等),都必须考虑生产时的安全间距。
(1)前处理:磨板磨板的主要作用:基本前处理主要是解决表面清洁度和表面粗糙度的问题。
去除氧化,增。
PCB的生产流程简介

PCB的生产流程简介PCB板(Printed Circuit Board,印刷电路板)是一种用于支持和连接电子元件的基础材料。
它起着支撑和传导作用,是电子设备中不可或缺的组成部分。
本文将简要介绍PCB的生产流程。
一、PCB设计在PCB制造的过程中,首先需要进行电路板的设计。
设计人员根据电子设备的需求和功能要求,使用专业的电路设计软件,进行电路板的布局和布线设计。
通过设计软件,我们可以确定电路板的尺寸、层数和线路连接方式。
二、电路板原材料准备在PCB制造过程中,需要准备各种原材料,包括基材、铜箔、耐火材料和覆盖层。
其中,基材是支持电路板结构的主要材料,可以选择有机基材(如FR-4)或无机基材(如陶瓷);铜箔是用于导电的材料,可根据设计需求进行选择;耐火材料用于板材层之间的隔热和阻燃,通常是一种玻璃纤维材料;覆盖层用于保护电路板上的电子元件。
三、电路板层压电路板层压是将多层电路板结合在一起的过程。
首先,将准备好的基材和覆铜箔放在一起,形成厚度适当的层,在层与层之间放置耐火材料。
然后,将堆叠好的板材放入预热机中进行预热,使板材中的树脂熔化。
最后,将板材放入层压机中进行高温高压处理,使树脂熔化并与铜箔粘合在一起。
四、电路板图形化在电路板层压之后,需要通过图形化的过程来形成电路板的形状和尺寸。
这个过程通常被称为电路板的切割和切割。
首先,将层压好的电路板放入机器中,通过数控机床或激光切割机来切割和切割板材。
完成后,通过机器来修整和打磨电路板的边缘。
五、电路板开孔电路板开孔是为了在板上安装电子元件和连接器。
通过机器或激光,将电路板上需要开孔的位置进行加工。
开孔过程可以分为铣削孔和钻孔两种方式。
铣削孔适用于较大直径的孔,而钻孔则适用于较小孔径。
六、电路板表面处理电路板的表面处理是为了提高电路板的焊接能力和抗氧化能力。
目前常用的表面处理方法有热浸金和喷锡。
热浸金是将电路板浸入一种金属液体中,使金属与电路板表面发生化学反应,形成一层金属保护层。
pcb生产流程简介

PCB的生产流程主要包括以下步骤:
1. 设计:使用CAD软件进行电路原理图和PCB布局的设计,确定PCB板的尺寸、布线方式、焊盘大小等信息。
2. 图形转换:将电路原理图和PCB布局图转换成Gerber文件,以便进行制版和刻蚀等工艺。
3. 制版:通过将Gerber文件转换成光阻膜,然后通过曝光、显影等工艺将光阻膜图形转移到铜箔上,制作出PCB板的线路和图形。
4. 刻蚀:将不需要的铜箔部分去除,形成PCB板的线路和图形。
5. 钻孔:在PCB板上钻出各种孔位,包括焊盘孔、定位孔、安装孔等。
6. 涂覆:将覆铜板上的光阻膜去除,然后覆盖一层焊膜,以便进行焊接操作。
7. 焊接:将元器件安装到PCB板上,并进行焊接。
8. 检测:对焊接后的PCB板进行质量检测,包括AOI检测、X射线检测、ICT检测等。
9. 清洗:将焊接后的PCB板清洗干净,以便进行后续的封装和组装操作。
此外,还包括一些特定类型的PCB板的生产工艺:
1. 内层线路制作:包括前处理、内层涂布、曝光、显影、蚀刻、去
膜等步骤。
2. 外层线路制作:包括前处理、压干膜、曝光、显影、蚀刻、去膜等步骤。
3. 防焊漆流程:包括前处理、刷漆、曝光、显影等步骤。
4. 表面处理:包括化金(化学镍金)、镀金等步骤。
5. 成型:把板子裁切成客户需要的尺寸。
6. 电测&出货检验:包括飞针测试、专用测试机等检测方法。
以上是PCB生产的主要流程,供您参考,建议咨询专业人士获取更准确的信息。
PCB板生产工艺和制作流程详解

PCB板生产工艺和制作流程详解PCB板(Printed Circuit Board)的生产工艺和制作流程是指将原始的电子元器件和电路图设计转化为实际可使用的电路板的过程。
下面将详细介绍PCB板的生产工艺和制作流程。
一、PCB板的生产工艺:1.原料准备:首先需要准备PCB板的基材,一般使用的是玻璃纤维层压板,也可以使用其他材料如陶瓷、聚合物等。
2.制版:制板是将电路图设计转化为PCB板的关键步骤。
根据设计图纸,通过绘图软件将电路图设计成可打印的制板文件,然后通过光绘或激光打印的方式将电路图转印到铜片上,形成导电图形。
3.起膜:将铜片表面涂上一层光敏脂,并通过紫外线曝光,使脂层在光线照射下固化。
4.蚀刻:使用酸性或碱性溶液将未固化的光敏脂搭配的铜层进行蚀刻,使得只剩下需要的导电线路。
5.清洗:将蚀刻后的PCB板进行清洗,去除残留的光敏脂和蚀刻溶液,确保板面干净。
6.穿孔:在PCB板上钻孔,用于安装元器件和导线的连接。
7.导电:通过电镀的方式在孔内和铜层之间形成一层有电导性的金属,以便进行电路的连接。
8.焊接:将元器件按照设计图纸进行贴片焊接或插件焊接,以实现电路的连接。
9.焊盘喷锡:在焊接区域加工焊盘,并通过喷锡等方式对焊盘进行保护和增强导电性能。
10.硬化:将PCB板进行硬化处理,增加板的机械强度和耐腐蚀性。
11.控制:通过各种检测手段对PCB板进行质量控制,确保制造出的板的质量符合要求。
二、PCB板的制作流程:1.设计和绘制电路图:根据电路的要求和功能,使用电路设计软件绘制电路图。
2.制作基板:选择适合的基板材料,根据电路图设计制作PCB板。
3.制作板模和蚀刻:根据制作的PCB板设计制作模板,然后使用蚀刻液将多余的铜层去除,形成电路图案。
4.钻孔:使用电钻钻孔,以便安装元器件和导线的连接。
5.冲孔和抛锡:使用冲孔机进行孔内镀铜,然后将PCB板进行抛锡处理。
6.贴片和焊接:将元器件贴在焊盘上,并通过焊接的方式进行固定和连接。
PCB工艺流程全面介绍

PCB工艺流程全面介绍Printed Circuit Board(PCB)是一种用于支持电子组件的载体,被广泛应用于各种电子设备中。
PCB的质量和性能直接影响设备的可靠性和性能。
了解PCB的制造过程对于设计工程师和制造工程师来说都是非常重要的。
本文将全面介绍PCB 的制造工艺流程,包括设计、原料准备、成型、去电镀、印刷、表面处理、检测以及最后的组装测试等环节。
1. PCB设计PCB设计是PCB制造的第一步,设计工程师通过软件将电路图绘制到PCB板上,并做好规划布局以保证电路的良好连接和信号传输。
在设计过程中需要考虑到板子的尺寸、层数、阻抗控制、焊盘、连接孔、线宽等参数。
2. 原料准备PCB制造的原料主要包括基材、铜箔、耐热胶、光敏胶等。
基材主要有FR-4、CEM-1、CEM-3等。
铜箔用于形成线路,耐热胶用于覆盖铜箔,光敏胶用于制作外层图形。
3. 成型成型是将基材、铜箔等原料通过一系列工艺加工成为预定形状的过程。
与预设的设计文件一致。
4. 去电镀去电镀是将已经镀铜的线路上的残留铜除去,保证线路干净平整。
这个环节是PCB工艺中的关键步骤之一。
5. 印刷印刷是在PCB板上印上文字、标志或者特殊图形等内容。
通常使用丝印墨或喷印技术进行印刷。
6. 表面处理表面处理是在PCB的焊盘上涂覆一层保护层以防止氧化。
常见的表面处理方式包括HASL、金手指、沉金等。
7. 检测检测是在PCB制造的各个环节都会进行的步骤,其目的是确保PCB的质量和性能符合设计要求。
常见的检测手段包括目视检查、X射线检测、自动光学检测等方法。
8. 组装测试完成以上工艺后,PCB将进行组装测试,包括插件、焊接、功能测试等环节。
只有通过这些环节的测试,PCB才能被认为是合格的产物。
综上所述,PCB工艺流程包括设计、原料准备、成型、去电镀、印刷、表面处理、检测以及组装测试等多个环节。
每个环节都有其独特的工艺要求和关键步骤。
只有严格按照工艺流程操作,才能保证PCB的质量和性能。
PCB工艺流程全面介绍

PCB工艺流程全面介绍1. 设计阶段PCB设计是整个PCB制造过程的第一步。
在这一阶段,工程师首先根据电路原理图进行布线设计,确定电路的连接和布局。
然后利用CAD软件完成电路板的布局设计,包括元器件的位置和连接方式等。
2. 制作阶段PCB制作包括制版、印刷、腐蚀和钻孔等工序。
首先在铜箔基板上涂覆一层光敏胶,然后将设计好的图案用UV曝光到光敏胶上,形成一个图案。
接着用化学溶剂将未曝光的部分去除,再进行铜板腐蚀,去掉多余的铜箔。
最后进行钻孔、镀锡等步骤,完成电路板的制作。
3. 检查阶段在制作完成后,需要进行丝印、检查和打磨等工序,确保电路板的质量符合要求。
同时还需要进行电气性能测试,以及外观和尺寸的检查。
4. 组装阶段组装阶段包括贴片和焊接等工序。
首先需要将元器件(如电阻、电容等)贴上PCB板上的焊盘,然后通过波峰焊或热风烙铁等方式进行焊接,固定元器件并形成电气连接。
5. 测试阶段最后需要进行电路板的功能测试,确保电路的正常工作。
如果有缺陷或问题,需要修复或更换不合格的元器件。
综上所述,PCB工艺流程包括设计、制作、检查、组装和测试等多个环节,需要严格按照流程进行,以确保电路板的质量和性能。
PCB(Printed Circuit Board)即印刷电路板,在电子产品中发挥着至关重要的作用。
PCB工艺流程的全面介绍涉及到PCB的制造和组装过程。
下文将继续介绍PCB制造和组装的详细内容。
6. 表面处理在PCB制造的过程中,常见的表面处理包括有机保护膜、喷镀油、喷镀锡等。
有机保护膜的作用是保护电路板不受环境条件的影响,防止电路板受到潮气、化学气体的侵蚀。
喷镀油的作用是在PCB表面形成一层保护膜,以提高PCB的防潮性。
而喷镀锡则是为了提高焊接操作的精度和可靠度。
7. 组装PCB组装是将已经制作好的PCB板和电子元器件组合成为功能完整的整体。
这个组装的过程有时候包括两个阶段:表面组装(SMT)和插件组装(THT)。
PCB流程简介-全制程资料
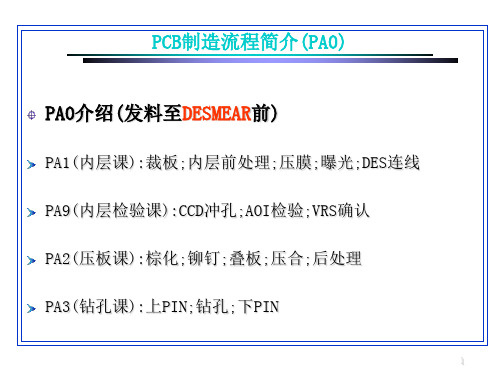
PB1(電鍍一課)介紹
☺ 流程介紹
鑽孔
去毛頭 (Deburr)
去膠渣 (Desmear)
化學銅 (PTH)
一次銅 Panel plating
☺ 目的:
使孔璧上的非導體部導電及焊接之金屬孔璧
26
PB1(電鍍一課)介紹
☺ 去毛頭(Deburr):
PCB制造流程简介(PA0)
PA0介绍(发料至DESMEAR前)
PA1(内层课):裁板;内层前处理;压膜;曝光;DES连线 PA9(内层检验课):CCD冲孔;AOI检验;VRS确认 PA2(压板课):棕化;铆钉;叠板;压合;后处理 PA3(钻孔课):上PIN;钻孔;下PIN
1
流程介绍:
PA1(内层课)介绍
4L
阶(完全固化)三类,生产中使用的
5L
全为B阶状态的P/P
16
PA2(压板课)介绍
叠板: 目的: 将预叠合好之板叠成待压 多层板形式 主要原物料:铜皮 电镀铜皮;按厚度可分为 1/3OZ(代号T) 1/2OZ(代号H) 1OZ(代号1) RCC(覆树脂铜皮)等
Layer 1 Layer 2 Layer 3 Layer 4 Layer 5 Layer 6
19
流程介绍:
PA3(钻孔课)介绍
上PIN
钻孔
下PIN
目的:在板面上钻出层与层之间线路连接的导通孔
20
上PIN:
PA3(钻孔课)介绍
目的:
对于非单片钻之板,预先按STACK之要求钉在一起,便于钻 孔,依板厚和工艺要求每个STACK可两片钻,三片钻或多片 钻
主要原物料:PIN针
注意事项: 上PIN时需开防呆检查,避免因前制程混料造成钻孔报废
PCB生产制造全流程介绍

全板镀铜(主要是为加厚保护那层薄薄的化学铜以防其在空气
中氧化,形成孔内无铜或破洞)
pcb的生产流程
磨板(采用去毛刺、清洁、刷光和研磨等手段来调整金属表面
状态)
pcb的生产流程
贴膜(加热加压的条件下将干膜抗蚀剂粘贴在覆铜箔板上
)
pcb的生产流程
图形转移(将照相底版上的电路图像转移到覆铜箔层压板上,
HPGL 及 Post Script. HPGL 及 Post Script.
HPGL 及 Post Script. Gerber (RS-274) Text file文字檔 Excellon Format Text file文字檔 IPC-356 or 其它從CAD輸出之各種 格式 Text file文字檔
钻孔刀径=成品孔径+6mil(在满
足最小刀径和板厚孔径比情况下,又 无特殊需求,via孔不必遵循此条件)
阻焊焊盘直径=焊盘直径+4mil
9 最小成品孔径板厚比 10 最小内层隔离环宽(mil) 11 最小焊环宽(mil) 12 最小芯材板厚 13 最大成品板厚范围(mm) 14 最小焊盘直径(mil) 15 最大成品板尺寸(inch) 16 压板厚度公差(mil) 17 成品层间对位精度(mil) 18 成品孔径精度(mil) 19 最小网格间距(mil) 20 最小绿油桥间距(mil) 21 机械加工精度(mil) 22 最小外型铣刀(mm) 23 最大V-CUT板尺寸(inch) 24 最小金属化槽钻咀(mm) 25 层数
PCB厂典型组织结构图
PCB全流程介绍
1.销售(接单---工程审核单-报价规则 ---报价) 2.工程(出菲林,层压叠板) 3.计划 (Bom) 4.生产(品
PCB流程简介
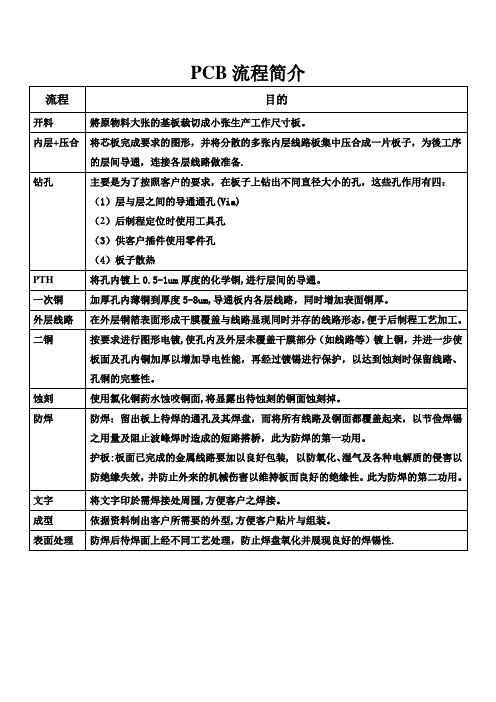
PCB流程简介
流程目的
开料將原物料大张的基板裁切成小张生产工作尺寸板。
内层+压合将芯板完成要求的图形,并将分散的多张内层线路板集中压合成一片板子,为後工序的层间导通,连接各层线路做准备.
钻孔主要是为了按照客户的要求,在板子上钻出不同直径大小的孔,这些孔作用有四:(1)层与层之间的导通通孔(Via)
(2)后制程定位时使用工具孔
(3)供客户插件使用零件孔
(4)板子散热
PTH 将孔内镀上0.5-1um厚度的化学铜,进行层间的导通。
一次铜加厚孔内薄铜到厚度5-8um,导通板内各层线路,同时增加表面铜厚。
外层线路在外层铜箔表面形成干膜覆盖与线路显现同时并存的线路形态,便于后制程工艺加工。
二铜按要求进行图形电镀,使孔内及外层未覆盖干膜部分(如线路等)镀上铜,并进一步使板面及孔内铜加厚以增加导电性能,再经过镀锡进行保护,以达到蚀刻时保留线路、
孔铜的完整性。
蚀刻使用氯化铜药水蚀咬铜面,将显露出待蚀刻的铜面蚀刻掉。
防焊防焊:留出板上待焊的通孔及其焊盘,而将所有线路及铜面都覆盖起来,以节俭焊锡之用量及阻止波峰焊时造成的短路搭桥,此为防焊的第一功用。
护板:板面已完成的金属线路要加以良好包装, 以防氧化、湿气及各种电解质的侵害以
防绝缘失效,并防止外来的机械伤害以维持板面良好的绝缘性。
此为防焊的第二功用。
文字将文字印於需焊接处周围,方便客户之焊接。
成型依据资料制出客户所需要的外型,方便客户贴片与组装。
表面处理防焊后待焊面上经不同工艺处理,防止焊盘氧化并展现良好的焊锡性.。
- 1、下载文档前请自行甄别文档内容的完整性,平台不提供额外的编辑、内容补充、找答案等附加服务。
- 2、"仅部分预览"的文档,不可在线预览部分如存在完整性等问题,可反馈申请退款(可完整预览的文档不适用该条件!)。
- 3、如文档侵犯您的权益,请联系客服反馈,我们会尽快为您处理(人工客服工作时间:9:00-18:30)。
4
蘇州金像電子有限公司
PA1(内层课) PA1(内层课)介绍 内层课
前处理(PRETREAT): 前处理(PRETREAT): 目的: 目的: 去除銅面上的污染物,增 去除銅面上的污染物,增 加銅面粗糙度,以利於後續 面粗糙度,以利於後續 的壓膜制程 主要原物料: 主要原物料:刷輪
MFG Rocky.shi Camel.chen Micro.yao
压膜前
干膜
压膜后
6
蘇州金像電子有限公司
PA1(内层课) PA1(内层课)介绍 内层课
曝光(EXPOSURE): 曝光(EXPOSURE): 目的: 目的: 经光源作用将原始底片上的图像转 经光源作用将原始底片上的图像转 移到感光底板上 主要原物料: 主要原物料:底片 内层所用底片为负片, 内层所用底片为负片,即白色透光部 分发生光聚合反应, 分发生光聚合反应, 黑色部分则因 不透光,不发生反应, 不透光,不发生反应,外层所用底片 刚好与内层相反, 刚好与内层相反,底片为正片
Layer 1 Layer 2 Layer 3 Layer 4 Layer 5 Layer 6
MFG Rocky.shi Camel.chen Micro.yao
18
蘇州金像電子有限公司
PA2(压板课) PA2(压板课)介绍 压板课
压合: 压合: 目的: 目的:通过热压方式将叠合板压成多层板 主要原物料:牛皮纸; 主要原物料:牛皮纸;钢板
MFG Rocky.shi Camel.chen Micro.yao
显影前
显影后
8
蘇州金像電子有限公司
PA1(内层课) PA1(内层课)介绍 内层课
蚀刻(ETCHING): 蚀刻(ETCHING): 目的: 目的: 利用药液将显影后露出的 铜蚀掉, 铜蚀掉,形成内层线路图 形 主要原物料: 主要原物料:蚀刻药液 (CuCl2)
MFG Rocky.shi Camel.chen Micro.yao
12
蘇州金像電子有限公司
PA9(内层检验课) PA9(内层检验课)介绍 内层检验课
AOI检验 AOI检验: 检验: 全称为Automatic Optical Inspection,自动光学检测 目的: 目的: 通过光学反射原理将图像回馈至设备处理,与设定的逻辑 判断原则或资料图形相比较,找出缺点位置 注意事項 注意事項: 由于AOI所用的测试方式为逻辑比较,一定会存在一些误 判的缺点,故需通过人工加以确认
MFG Rocky.shi Camel.chen Micro.yao
16
蘇州金像電子有限公司
PA2(压板课) PA2(压板课)介绍 压板课
铆合:(铆合;预叠) 铆合:(铆合;预叠) :(铆合 目的:(四层板不需铆钉) 目的:(四层板不需铆钉) 利用铆钉将多张内层板钉在一起, 利用铆钉将多张内层板钉在一起, 以避免后续加工时产生层间滑移 主要原物料:铆钉;P/P 主要原物料:铆钉;P/P P/P(PREPREG):由树脂和玻璃纤维 P/P(PREPREG):由树脂和玻璃纤维 布组成, 布组成,据玻璃布种类可分为 1060;1080;2116;7628等几种 1060;1080;2116;7628等几种 树脂据交联状况可分为: 树脂据交联状况可分为: A阶(完全未固化);B阶(半固化);C 完全未固化);B阶 半固化);C 阶(完全固化)三类,生产中使用的 完全固化)三类, 全为B阶状态的P/P 全为B阶状态的P/P
MFG Rocky.shi Camel.chen Micro.yao
11
蘇州金像電子有限公司
PA9(内层检验课) PA9(内层检验课)介绍 内层检验课
CCD冲孔 CCD冲孔: 冲孔: 目的: 目的: 利用CCD对位冲出检验作业之定位孔及铆钉孔 利用CCD对位冲出检验作业之定位孔及铆钉孔 主要原物料: 主要原物料:冲头 注意事项: 注意事项: CCD冲孔精度直接影响铆合对准度, CCD冲孔精度直接影响铆合对准度,故机台精度定期确认非 常重要
21
蘇州金像電子有限公司
PA3(钻孔课) PA3(钻孔课)介绍 钻孔课
上PIN: 目的: 目的: 对于非单片钻之板,预先按STACK之要求钉在一起, 对于非单片钻之板,预先按STACK之要求钉在一起,便于钻 孔,依板厚和工艺要求每个STACK可两片钻,三片钻或多片 依板厚和工艺要求每个STACK可两片钻, 钻 主要原物料:PIN针 主要原物料:PIN针 注意事项: 注意事项: 上PIN时需开防呆检查,避免因前制程混料造成钻孔报废 PIN时需开防呆检查,
MFG Rocky.shi Camel.chen Micro.yao
20
蘇州金像電子有限公司
PA3(钻孔课) PA3(钻孔课)介绍 钻孔课
流程介绍: 流程介绍:
上PIN
钻孔
下PIN
目的: 目的:在板面上钻出层与层之间线路连接的导通孔
MFG Rocky.shi Camel.chen Micro.yao
MFG Rocky.shi Camel.chen Micro.yao
13
蘇州金像電子有限公司
PA9(内层检验课) PA9(内层检验课)介绍 内层检验课
VRS确认: VRS确认: 确认 全称为Verify Repair Station,确认系统 目的: 目的: 通过与AOI连线,将每片板子的测试资料传给V.R.S,并由 人工对AOI的测试缺点进行确认 注意事項 注意事項: VRS的确认人员不光要对测试缺点进行确认,另外就是对 一些可以直接修补的确认缺点进行修补
苏州金像电子有限公司
课 程 名 称: 製造流程簡介 造流程簡
制 作 单 位: 製造處 制 作 者: 石俊杰/陳祥/姚箭 石俊杰/ 核 准: 石智中 核 准 日 期: 2001/9/26 序: A 版
2001-09-26 1
蘇州金像電子有限公司
PCB制造流程简介(PA0) PCB制造流程简介(PA0) 制造流程简介
MFG Rocky.shi Camel.chen Micro.yao
14
蘇州金像電子有限公司
PA2(压板课) PA2(压板课)介绍 压板课
流程介绍: 流程介绍:
棕化
铆合
叠板
压合
后处理
目的: 目的: 将铜箔(Copper)、胶片(Prepreg)与氧化处理后的内层 将铜箔(Copper)、胶片(Prepreg)与氧化处理后的内层 线路板压合成多层板
UV光 光
曝光前
曝光后
MFG Rocky.shi Camel.chen Micro.yao
7
蘇州金像電子有限公司
PA1(内层课) PA1(内层课)介绍 内层课
显影(DEVELOPING): 显影(DEVELOPING): 目的: 目的: 用碱液作用将未发生化学反 应之干膜部分冲掉 主要原物料: 主要原物料:Na2CO3 使用将未发生聚合反应之干 膜冲掉, 膜冲掉,而发生聚合反应之 干膜则保留在板面上作为蚀 刻时之抗蚀保护层
MFG Rocky.shi Camel.chen Micro.yao
铆钉
2L 3L 4L 5L
2L 3L 4L 5L
17
蘇州金像電子有限公司
PA2(压板课) PA2(压板课)介绍 压板课
叠板: 叠板: 目的: 目的: 将预叠合好之板叠成待压 多层板形式 主要原物料: 主要原物料:铜皮 电镀铜皮; 电镀铜皮;按厚度可分为 1/3OZ(代号T) 1/3OZ(代号T) 1/2OZ(代号H) 1/2OZ(代号H) 1OZ(代号1) 1OZ(代号1) RCC(覆树脂铜皮) RCC(覆树mel.chen Micro.yao
3
蘇州金像電子有限公司
PA1(内层课) PA1(内层课)介绍 内层课
裁板(BOARD 裁板(BOARD CUT): 目的: 目的: 依制前设计所规划要求, 依制前设计所规划要求,将基板材料裁切成工作所需尺寸 主要原物料:基板; 主要原物料:基板;锯片 基板由铜皮和绝缘层压合而成,依要求有不同板厚规格, 基板由铜皮和绝缘层压合而成,依要求有不同板厚规格,依 铜厚可分为H/H;1oz/1oz;2oz/2oz等种类 铜厚可分为H/H;1oz/1oz;2oz/2oz等种类 注意事项: 注意事项: 避免板边巴里影响品质,裁切后进行磨边, 避免板边巴里影响品质,裁切后进行磨边,圆角处理 考虑涨缩影响, 考虑涨缩影响,裁切板送下制程前进行烘烤 裁切须注意机械方向一致的原则
蚀刻前
蚀刻后
MFG Rocky.shi Camel.chen Micro.yao
9
蘇州金像電子有限公司
PA1(内层课) PA1(内层课)介绍 内层课
去膜(STRIP): 去膜(STRIP): 目的: 目的: 利用强碱将保护铜面之抗 蚀层剥掉, 蚀层剥掉,露出线路图形
去膜前
主要原物料: 主要原物料:NaOH
MFG Rocky.shi Camel.chen Micro.yao
2
蘇州金像電子有限公司
PA1(内层课) PA1(内层课)介绍 内层课
流程介绍: 流程介绍:
裁板
前处理
压膜
曝光
DES
目的: 目的: 利用影像转移原理制作内层线路 利用影像转移原理制作内层线路 DES为显影;蚀刻; DES为显影;蚀刻;去膜连线简称
去膜后
MFG Rocky.shi Camel.chen Micro.yao
10
蘇州金像電子有限公司
PA9(内层检验课) PA9(内层检验课)介绍 内层检验课
流程介绍: 流程介绍:
CCD冲孔
AOI检验
VRS确认
目的: 目的: 对内层生产板进行检查, 对内层生产板进行检查,挑出异常板并进行处理 收集品质资讯,及时反馈处理, 收集品质资讯,及时反馈处理,避免重大异常发生