钙基湿法烟气脱硫的工艺过程
钙基sds脱硫工艺
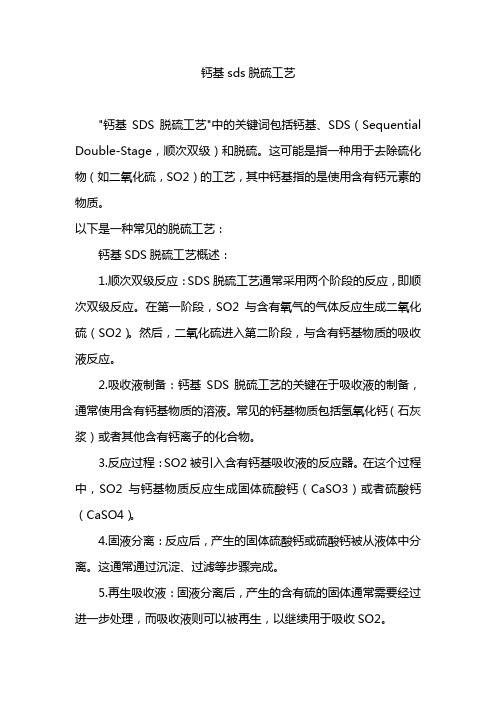
钙基sds脱硫工艺
"钙基SDS脱硫工艺"中的关键词包括钙基、SDS(Sequential Double-Stage,顺次双级)和脱硫。
这可能是指一种用于去除硫化物(如二氧化硫,SO2)的工艺,其中钙基指的是使用含有钙元素的物质。
以下是一种常见的脱硫工艺:
钙基SDS脱硫工艺概述:
1.顺次双级反应:SDS脱硫工艺通常采用两个阶段的反应,即顺次双级反应。
在第一阶段,SO2与含有氧气的气体反应生成二氧化硫(SO2)。
然后,二氧化硫进入第二阶段,与含有钙基物质的吸收液反应。
2.吸收液制备:钙基SDS脱硫工艺的关键在于吸收液的制备,通常使用含有钙基物质的溶液。
常见的钙基物质包括氢氧化钙(石灰浆)或者其他含有钙离子的化合物。
3.反应过程:SO2被引入含有钙基吸收液的反应器。
在这个过程中,SO2与钙基物质反应生成固体硫酸钙(CaSO3)或者硫酸钙(CaSO4)。
4.固液分离:反应后,产生的固体硫酸钙或硫酸钙被从液体中分离。
这通常通过沉淀、过滤等步骤完成。
5.再生吸收液:固液分离后,产生的含有硫的固体通常需要经过进一步处理,而吸收液则可以被再生,以继续用于吸收SO2。
这是一个一般性的描述,实际的工艺可能因具体的应用、工厂设置和硫化物的浓度而有所不同。
这种工艺的优势之一是相对于一些传统的脱硫方法,它可能更具成本效益和环保性。
在实际应用中,还需要考虑工厂规模、操作条件、废物处理等方面的因素。
四种脱硫方法工艺简介

一、石灰石/石灰-石膏法脱硫工艺一)、工作原理石灰石/石灰-石膏法烟气脱硫采用石灰石或石灰作为脱硫吸收剂,石灰石经破碎磨细成粉状与水混合搅拌成吸收浆液,当采用石灰为吸收剂时,石灰粉经消化处理后加水制成吸收剂浆液。
在吸收塔内,吸收浆液与烟气接触混合,烟气中的二氧化硫与浆液中的碳酸钙以及鼓入的氧化空气进行化学反应从而被脱除,最终反应产物为石膏。
二)、反应过程1、吸收SO2+ H2O—>H2SO3SO3+ H2O—>H2SO42、中和CaCO3+ H2SO3—>CaSO3+CO2+ H2OCaCO3+ H2SO4—>CaSO4+CO2+ H2OCaCO3+2HCl—>CaCl2+CO2+ H2OCaCO3+2HF—>CaF2+CO2+ H2O3、氧化2CaSO3+O2—>2 CaSO44、结晶CaSO4+ 2H2O—>CaSO4·2H2O三)、系统组成脱硫系统主要由烟气系统、吸收氧化系统、石灰石/石灰浆液制备系统、副产品处理系统、废水处理系统、公用系统(工艺水、压缩空气、事故浆液罐系统等)、电气控制系统等几部分组成。
四)、工艺流程锅炉/窑炉—>除尘器—>引风机—>吸收塔—>烟囱来自于锅炉或窑炉的烟气经过除尘后在引风机作用下进入吸收塔,吸收塔为逆流喷淋空塔结构,集吸收、氧化功能于一体,上部为吸收区,下部为氧化区,经过除尘后的烟气与吸收塔内的循环浆液逆向接触。
系统一般装3-5台浆液循环泵,每台循环泵对应一层雾化喷淋层。
当只有一台机组运行时或负荷较小时,可以停运1-2层喷淋层,此时系统仍保持较高的液气比,从而可达到所需的脱硫效果。
吸收区上部装二级除雾器,除雾器出口烟气中的游离水份不超过75mg/Nm3。
吸收SO2后的浆液进入循环氧化区,在循环氧化区中,亚硫酸钙被鼓入的空气氧化成石膏晶体。
同时,由吸收剂制备系统向吸收氧化系统供给新鲜的石灰石浆液,用于补充被消耗掉的石灰石,使吸收浆液保持一定的pH值。
脱硫工艺简介

. 1. 湿法烟气脱硫石灰石(石灰)—石膏烟气脱硫是以石灰石或石灰浆液与烟气中的SO2反应,脱硫产物是含水15-20%的石膏。
氧化镁烟气脱硫是以氧化镁浆液与烟气中的SO2反应,脱硫产物是含结晶水的亚硫酸镁和硫酸镁的固体吸收产物。
氨法烟气脱硫用亚硫酸铵(NH4)2SO3吸收SO2生成亚硫酸氢铵NH4HSO3,循环槽中用补充的氨使NH4HSO3亚硫酸氢铵再生为(NH4)2SO3亚硫酸铵循环使用。
双碱法烟气脱硫是利用氢氧化钠溶液作为启动脱硫剂,配制好的氢氧化钠溶液直接打入脱硫塔洗涤脱除烟气中SO2来达到烟气脱硫的目的,然后脱硫产物经脱硫剂再生池还原成氢氧化钠再打回脱硫塔内循环使用海水法烟气脱硫海水通常呈弱碱性具有天然的二氧化硫吸收能力,生成亚硫酸根离子和氢离子,洗涤后的海水呈酸性,经过处理合格后排入大海。
2.干法或半干法烟气脱硫所谓干法烟气脱硫,是指脱硫的最终产物是干态的喷雾法:利用高速旋转雾化器,将石灰浆液雾化成细小液滴与烟气进行传热和反应,吸收烟气中的SO2。
炉内喷钙尾部增湿活化法:将钙基吸收剂如石灰石、白云石等喷入到炉膛燃烧室上部温度低于1200℃的区域,石灰石煅烧成氧化钙,新生成的氧化钙CaO与SO2进行反应生成CaSO4硫酸钙,并随飞灰在除尘器中收集,并且在活化反应器内喷水增湿,促进脱硫反应。
循环流化床法:将干粉吸收剂粉喷入塔内,与烟气中的SO2反应,同时喷入一定量的雾化水,增湿颗粒表面,增进反应,控制塔出口烟气的温度,吸收剂和生成的产物一起经过除尘器的收集,再进行多次循环,延长吸收剂与烟气的接触时间,大大提高吸收剂的利用率和脱硫效率。
荷电干式喷射脱硫法:吸收剂干粉以高速通过高压静电电晕充电区,使干粉荷上相同的负电荷被喷射到烟气中荷电干粉同电荷相斥,在烟气中形成均匀的悬浊状态,离子表面充分暴露,增加了与SO2的反应机会。
同时荷电粒子增强了活性,缩短了反应所需停留时间,提高了脱硫效率。
二、烧结机石灰—石膏湿法脱硫工艺概述1、烧结机的烟气特点烧结烟气是烧结混合料点火后,随台车运行,在高温烧结成型过程中产生的含尘废气,烧结烟气的主要特点是:(1)烧结机年作业率较高,达90%以上,烟气排放量大;(2)烟气成分复杂,且根据配料的变化存在多改变性别;(3)烟气温度波动幅度较大,波动规模在90~170 ℃;(4)烟气湿度比较大一般在10%左右;(5)由于烧结原料含硫率关系,引起排放烟气SO2浓度随配料比的变化而发生较大的变化;(6)烧结烟气含氧量高,约占10%~15%左右;(7)含有腐蚀性气体。
目前广泛使用的5种脱硫工艺技术方案简介

目前广泛使用的5种脱硫工艺技术方案简介目录目前广泛使用的5种脱硫工艺技术方案简介 (1)1、湿法烟气脱硫工艺 (1)2、半干法烟气脱硫工艺 (3)3、烟气循环流化床脱硫工艺 (4)4、干法脱硫工艺 (5)5、NID半干法烟气脱硫 (6)目前世界上燃煤电厂烟气脱硫工艺方法很多,这些方法的应用主要取决于锅炉容量和调峰要求、燃烧设备的类型、燃料的种类和含硫量的多少、脱硫率、脱硫剂的供应条件及电厂的地理条件、副产品的利用等因素。
近年来,我国电力工业部门在烟气脱硫技术引进工作方面加大了力度,对目前世界上电厂锅炉较广泛采用的脱硫工艺都有成功运行工程,主要有湿法烟气脱硫、干法烟气脱硫和半干法烟气脱硫。
现将目前应用较为广泛的几种脱硫工艺原理、特点及其应用状况简要说明如下:1、湿法烟气脱硫工艺湿法烟气脱硫包括石灰石/石灰-石膏法烟气脱硫、海水烟气脱硫和用钠基、镁基、氨作吸收剂,一般用于小型电厂和工业锅炉。
氨洗涤法可达很高的脱硫效率,副产物硫酸铵和硝酸铵是可出售的化肥。
以海水为吸收剂的工艺具有结构简单、不用投加化学品、投资小和运行费用低等特点。
而以石灰石/石灰-石膏法湿法烟气脱硫应用最广。
《石灰石/石灰-石膏法烟气脱硫工程设计规范》中关于湿法烟气脱硫工艺的选择原则为:燃用含硫量Sar≥2%煤的机组或大容量机组(200MW及以上)的电厂锅炉建设烟气脱硫装置时,宜优先采用石灰石-石膏湿法脱硫工艺,脱硫率应保证在96%以上。
湿法烟气脱硫工艺采用碱性浆液或溶液作吸收剂,其中石灰石/石灰-石膏湿法脱硫是目前世界上技术最成熟、应用最广,运行最可靠的脱硫工艺方法,石灰石经破碎磨细成粉状与水混合搅拌制成吸收剂浆液;也可以将石灰石直接湿磨成石灰石浆液。
石灰石或石灰浆液在吸收塔内,与烟气接触混合,烟气中的SO2与浆液中的碳酸钙以及鼓入的氧化空气进行化学反应,最终反应产物为石膏,经脱水装置脱水后可抛弃,也可以石膏形式回收。
由于吸收剂浆液的循环利用,脱硫吸收剂的利用率很高。
脱硫吸收塔化学反应原理

脱硫化学反应过程石灰石-石膏湿法烟气脱硫工艺的化学原理如下:①烟气中的二氧化硫溶解于水,生成亚硫酸并离解成、HSO3-和SO32-离子;②产生的H+促进了吸收剂CaCO3的溶解,生成一定浓度的Ca2+,与SO32-或HSO3-结合,生成CaSO3和Ca(HSO3)2;③反应过程中,一部分SO32-和HSO3-被氧化成SO42-和HSO4-;④溶液中存在的大量SO32-及HSO3-被鼓入的空气强制氧化转化为SO42-生成石膏结晶(CaSO4·2H2O)。
化学反应式分别如下:① SO2+H2O→H++HSO3- HSO3-→H++SO32-② Ca2++SO32-→CaSO3 Ca2++HSO3-→Ca(HSO3)2③ SO32-+1/2O2→SO42- HSO3-+1/2O2→HSO4-④Ca2++SO42-+2H2O→CaSO4·2H2O液气比的含义:液气比是指洗涤每立方米烟气所用的洗涤液量,单位是L/m3。
比率为:循环浆液流量/处理烟气流量一般表示为:L/1000 Nm3。
钙硫摩尔比从化学反应的角度,无论何种脱硫工艺,在理论上只要有一个钙基吸收剂分子就可以吸收一个SO2分子,或者说,脱除1mol的硫需要1mol的钙。
但在实际反应设备中,反应的条件并不处于理想状态,因此,一般需要增加脱硫剂的量来保证吸收过程的进行。
钙硫摩尔比就是用来表示达到一定脱硫效率时所需要钙基吸收剂的过量程度,也说明在用钙基吸收剂脱硫时钙的有效利用率。
一般用钙与硫的摩尔比值表示,即Ca/S比,所需的Ca/S越高,钙的利用率则越低。
浆液的pH值浆液的pH值是影响脱硫率、氧化率、吸收剂利用率及系统结垢的主要因素之一。
浆液的pH值高,意味着碱度大,有利于碱性溶液与酸性气体之间的化学反应,对脱除SO2有利,但会对副产物的氧化起抑制作用。
降低pH值可以抑制H2SO3分解为SO32-,使反应生成物大多为易溶性的Ca(HSO3)2,从而减轻系统内的结垢倾向。
钙法脱硫工艺流程

钙法脱硫工艺流程钙法脱硫是一种常用的烟气脱硫工艺,其基本原理是利用钙氢氧化物(Ca(OH)2)与烟气中的硫化物(SO2)反应生成硫酸钙(CaSO4)并沉降,从而达到脱除烟气中SO2的目的。
下面是该工艺的简要流程。
首先,原料准备。
钙法脱硫的主要原料是石灰石和水。
石灰石经过破碎、筛分和干燥等处理后得到适当颗粒大小的石灰石粉末,作为钙源。
水通过处理设备去除杂质,用于与石灰石反应生成钙水浆。
其次,污染气体净化。
通过烟气净化设备对含有SO2的烟气进行预处理,去除大部分气体尘粒和臭气等,保证进入脱硫系统的烟气干净。
然后,钙水浆制备。
将适量的石灰石粉末与水按一定的配比混合,经过搅拌和其他工艺步骤,形成含有一定浓度的钙水浆。
钙水浆的浓度要根据具体的脱硫要求和工艺条件进行调整。
接着,脱硫反应。
将钙水浆通过喷淋系统均匀喷入脱硫塔内的烟气中。
在脱硫塔内,烟气与钙水浆充分接触,硫化物与钙水浆中的Ca(OH)2发生反应,生成硫酸钙。
反应式如下:Ca (OH)2 + SO2 → CaSO4 + H2O。
最后,产物处理和回收。
脱硫后的烟气中的大部分SO2已经被转化为固体硫酸钙,因此烟气中的净SO2含量大大降低。
硫酸钙颗粒沉降至脱硫塔底部,通过输送设备或其他方式将其收集起来。
收集的硫酸钙可以用作水泥生产、建材制造等行业的原料。
同时,在一定条件下,硫酸钙也可以再次回用于脱硫过程。
以上是钙法脱硫的主要流程。
钙法脱硫工艺具有设备简单、适应性广、操作方便等优点,被广泛应用于燃煤电厂、石油化工、冶金等行业中的烟气治理领域。
同时,随着环保要求的提高,钙法脱硫技术也在不断优化和改进,以提高脱硫效率和降低能耗,实现更好的环境保护效果。
烟气脱硫工艺流程
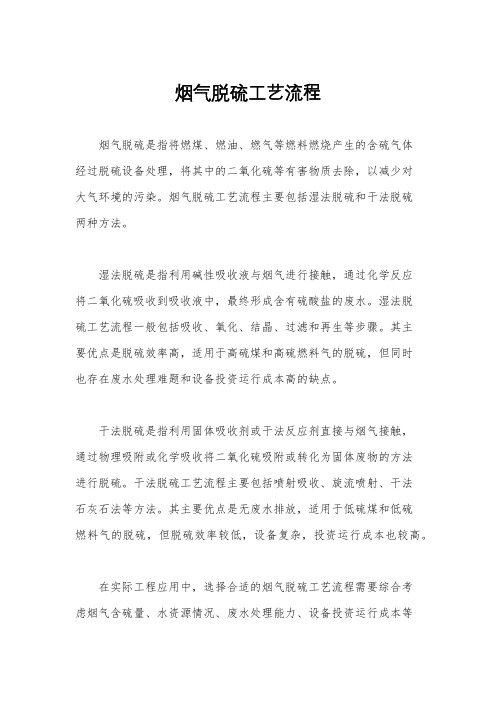
烟气脱硫工艺流程
烟气脱硫是指将燃煤、燃油、燃气等燃料燃烧产生的含硫气体
经过脱硫设备处理,将其中的二氧化硫等有害物质去除,以减少对
大气环境的污染。
烟气脱硫工艺流程主要包括湿法脱硫和干法脱硫
两种方法。
湿法脱硫是指利用碱性吸收液与烟气进行接触,通过化学反应
将二氧化硫吸收到吸收液中,最终形成含有硫酸盐的废水。
湿法脱
硫工艺流程一般包括吸收、氧化、结晶、过滤和再生等步骤。
其主
要优点是脱硫效率高,适用于高硫煤和高硫燃料气的脱硫,但同时
也存在废水处理难题和设备投资运行成本高的缺点。
干法脱硫是指利用固体吸收剂或干法反应剂直接与烟气接触,
通过物理吸附或化学吸收将二氧化硫吸附或转化为固体废物的方法
进行脱硫。
干法脱硫工艺流程主要包括喷射吸收、旋流喷射、干法
石灰石法等方法。
其主要优点是无废水排放,适用于低硫煤和低硫
燃料气的脱硫,但脱硫效率较低,设备复杂,投资运行成本也较高。
在实际工程应用中,选择合适的烟气脱硫工艺流程需要综合考
虑烟气含硫量、水资源情况、废水处理能力、设备投资运行成本等
因素。
此外,还需要考虑脱硫设备的稳定性、可靠性和安全性,以及对烟气中其他污染物的处理效果等因素。
总的来说,烟气脱硫工艺流程的选择应根据实际情况综合考虑各种因素,以达到经济、环保和可持续发展的目标。
希望本文所述内容对烟气脱硫工艺流程的了解有所帮助。
石灰石石膏湿法烟气脱硫工艺
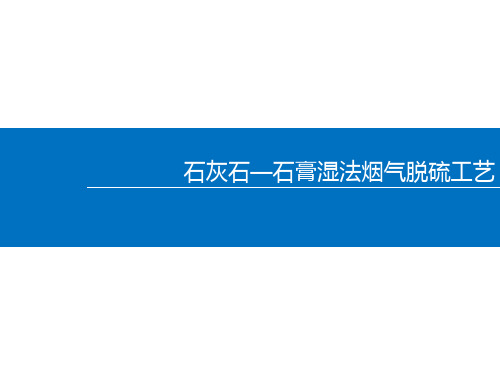
液柱与烟气进行两次接触 (上升 / 落下)
没有背压的直筒式喷嘴
自我冲洗(向上的喷嘴)
单层喷浆管/喷嘴 (结构简单1容8 易维修)
主要系统及设备介绍—浆液循环系统
循环浆泵用来将吸收塔浆池的浆液和加入的石灰石浆液循环不断的送到吸收塔喷淋
层,在一定压力下通过喷嘴充分雾化,与烟气反应。
根据防腐工艺不同,循环浆泵分为衬胶泵和防腐金属泵两种。
后橡Ba胶ck R衬ub套ber Liner B后ac盖k Split Casing
金属合金 叶MIemtaple轮Allellroy
Front Rubber
前Li橡ner胶衬套
F前ro盖nt Split
Casing
金M属et合al A金llo护y 套
Throatbush
((前fro磨nt w损ea盘r )
主要系统及设备介绍—吸收系统及设备
(一)吸收塔
吸收塔一般为钢制塔体,内衬玻璃鳞片,并具备烟气进出口烟道、人孔门、检查门、 钢制平台扶梯、法兰、液位控制、溢流管及所有需要的连接件等。 吸收塔除塔体外,还有搅拌器、喷淋层和两级除雾器(聚丙烯百叶窗式)。 此外,吸收塔还包括循环浆液泵和氧化空气风机。 脱硫塔从结构上来分主要有:填料塔、板式塔、液柱塔、喷淋塔(空塔)和鼓泡塔。
继续与回落的液滴进行同向传质。 烟气从逆流塔流出经过反应罐上部折转180°,自下而上通过顺流塔,与向上喷射的液
柱及向下回落的液滴再次进行气液接触。经除雾器除雾后排出。
净烟气 原(脏)烟气
主要系统及设备介绍—吸收系统及设备
液柱式喷淋塔的优势
净烟气
高密度的液滴层 (高密度的液滴层增大气液 接触面积)
原(脏)烟气
实际球)。
石灰石-石膏湿法烟气脱硫工艺原理及特点

石灰石-石膏湿法烟气脱硫工艺原理及特点一、工艺原理该工艺采用石灰石或石灰做脱硫吸收剂,石灰石破碎与水混合,磨细成粉壮,制成吸收浆液(当采用石灰为吸收剂时,石灰粉经消化处理后加水搅拌制成吸收浆)。
在吸收塔内,烟气中的SO2与浆液中的CaCO3(碳酸钙)以及鼓入的氧化空气进行化学反应生成二水石膏,二氧化硫被脱除。
吸收塔排出的石膏浆液经脱水装置脱水后回收。
脱硫后的烟气经除雾器去水、换热器加热升温后进入烟囱排向大气。
烟气从吸收塔下侧进入,与吸收浆液逆流接触,在塔内CaCO3与SO2、H2O进行反应,生成CaSO3·1/2H2O和CO2↑;对落入吸收塔浆浆池的CaSO3·1/2H2O和O2、H2O 再进行氧气反应,得到脱流副产品二水石膏。
化学反应方程式:2CaCO3+H2O+2SO2====2CaSO3·1/2H2O+2CO22CaSO3·1/2H2O+O2+3H2O====2CaSO4·2H2O二、FGD烟气系统的原理从锅炉引风机后烟道引出的烟气,通过增压风机升压,烟气换热器(GGH)降温后,进入吸收塔,在吸收塔内与雾状石灰石浆液逆流接触,将烟气脱硫净化,经除雾期除去水雾后,又经GGH升温至大于75摄氏度,再进入净烟道经烟囱排放。
脱硫系统在引风机出口与烟囱之间的烟道上设置旁路挡板门,当FGD装置运行时,烟道旁路挡板门关闭,FGD装置进出口挡板门打开,烟气通过增压风机的吸力作用引入FGD系统。
在FGD装置故障和停运时,旁路挡板门打开,FGD装置进出口挡板门关闭,烟气由旁路挡板经烟道直接进入烟囱,排向大气,从而保证锅炉机组的安全稳定运行。
FGD装置的原烟气挡板、净烟气挡板及旁路挡板一般采用双百叶挡板并设置密封空气系统。
旁路挡板具有快开功能,快开时间要小于10s,挡板的调整时间在正常情况下为75s,在事故情况下约为3~10s。
一、旁路挡板门的控制原理概述一、烟气脱硫挡板风门的结构简述1.烟气脱硫挡板风门——风门框架和截面的主体部分和叶片均按设计用不同材质、规格的钢板制造。
石灰石-石膏湿法脱硫工艺的基本原理
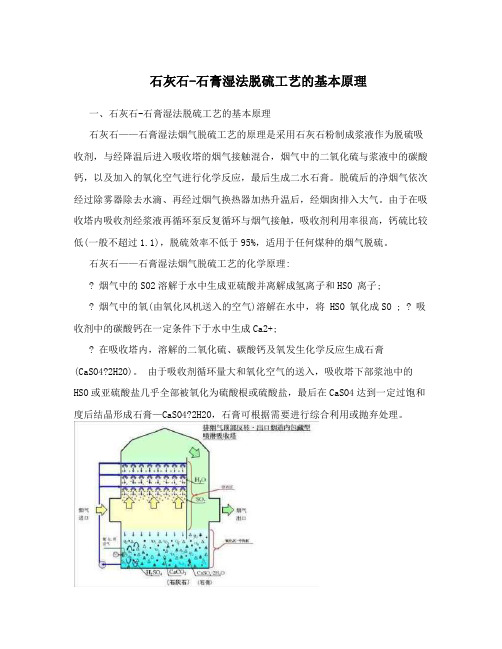
石灰石-石膏湿法脱硫工艺的基本原理一、石灰石-石膏湿法脱硫工艺的基本原理石灰石——石膏湿法烟气脱硫工艺的原理是采用石灰石粉制成浆液作为脱硫吸收剂,与经降温后进入吸收塔的烟气接触混合,烟气中的二氧化硫与浆液中的碳酸钙,以及加入的氧化空气进行化学反应,最后生成二水石膏。
脱硫后的净烟气依次经过除雾器除去水滴、再经过烟气换热器加热升温后,经烟囱排入大气。
由于在吸收塔内吸收剂经浆液再循环泵反复循环与烟气接触,吸收剂利用率很高,钙硫比较低(一般不超过1.1),脱硫效率不低于95%,适用于任何煤种的烟气脱硫。
石灰石——石膏湿法烟气脱硫工艺的化学原理:烟气中的SO2溶解于水中生成亚硫酸并离解成氢离子和HSO 离子;烟气中的氧(由氧化风机送入的空气)溶解在水中,将 HSO 氧化成SO ; ? 吸收剂中的碳酸钙在一定条件下于水中生成Ca2+;在吸收塔内,溶解的二氧化硫、碳酸钙及氧发生化学反应生成石膏(CaSO4?2H2O)。
由于吸收剂循环量大和氧化空气的送入,吸收塔下部浆池中的HSO或亚硫酸盐几乎全部被氧化为硫酸根或硫酸盐,最后在CaSO4达到一定过饱和度后结晶形成石膏—CaSO4?2H2O,石膏可根据需要进行综合利用或抛弃处理。
二、工艺流程及系统湿法脱硫工艺系统整套装置一般布置在锅炉引风机之后,主要的设备是吸收塔、烟气换热器、升压风机和浆液循环泵我公司采用高效脱除SO2的川崎湿法石灰石,石膏工艺。
该套烟气脱硫系统(FGD)处理烟气量为定洲发电厂,1和,2机组(2×600MW)100,的烟气量,定洲电厂的FGD系统由以下子系统组成:(1)吸收塔系统(2)烟气系统(包括烟气再热系统和增压风机)(3)石膏脱水系统(包括真空皮带脱水系统和石膏储仓系统)(4)石灰石制备系统(包括石灰石接收和储存系统、石灰石磨制系统、石灰石供浆系统) (5)公用系统(6)排放系统(7)废水处理系统1、吸收塔系统吸收塔采用川崎公司先进的逆流喷雾塔,烟气由侧面进气口进入吸收塔,并在上升区与雾状浆液逆流接触,处理后的烟气在吸收塔顶部翻转向下,从与吸收塔烟气入口同一水平位置的烟气出口排至烟气再热系统。
烟气脱硫技术简述

烟气脱硫技术简述1.1烟气脱硫技术的分类烟气脱硫(Flue Gas Desulfurization,FGD)是世界上唯一大规模商业化应用的脱硫方法,是控制酸雨和二氧化硫污染的最为有效的和主要的技术手段。
目前,世界上各国对烟气脱硫都非常重视,已开发了数十种行之有效的脱硫技术,但是,其基本原理都是以一种碱性物质作为SO2的吸收剂,即脱硫剂。
按脱硫剂的种类划分,烟气脱硫技术可分为如下几种方法。
(1)以CaCO3(石灰石)为基础的钙法;(2)以MgO为基础的镁法;(3)以Na2SO3为基础的钙法;(4)以NH3为基础的氨法;(5)以有机碱为基础的有机碱法。
世界上普遍使用的商业化技术是钙法,所占比例在90%以上。
烟气脱硫装置相对占有率最大的国家是日本。
日本的燃煤和燃油锅炉基本上都装有烟气脱硫装置。
众所周知,日本的煤资源和石油资源都很缺乏,也没有石膏资源,而其石灰石资源却极为丰富。
因此FGD的石膏产品在日本得到广泛的应用。
这便是钙法在日本得到广泛应用的原因。
因此,其他发达国家的火电厂锅炉烟气脱硫装置多数是由日本技术商提供的。
在美国,镁法和钠法得到了较深入的研究,但实践证明,它们都不如钙法。
在我国,氨法具有很好的发展土壤。
我国是一个粮食大国,也是化肥大国。
氮肥以合成氨计,我国的需求量目前达到33Mt/a,其中近45%是由小型氮肥厂生产的,而且这些小氮肥厂的分布很广,每个县基本上都有氮肥厂。
因此,每个电厂周围100km内,都能找到可以提供合成氨的氮肥厂,SO2吸收剂的供应很丰富。
更有意义的是,氨法的产品本身就是化肥,就有很好的应用价值。
在电力界,尤其是脱硫界,还有两种分类方法,一种方法将脱硫技术根据脱硫过程是否有水参与及脱硫产物的干湿状态分为湿法、干法和半干(半湿)法。
另一种分类方法是以脱硫产物的用途为根据,分为抛弃法和回收法。
在我国,抛弃法多指钙法,回收法多指氨法。
下面我们将依据脱硫界的分类,先介绍湿式和干式两种脱硫方法。
脱硫工艺流程说明

脱硫工艺流程说明湿法脱硫工艺流程主要包括石灰石-石膏法和碱性洗涤液法两种方式。
1. 石灰石-石膏法:将石灰石(CaCO3)加入到反应塔中与燃烧产生的SO2发生反应,生成石膏(CaSO4)和二氧化碳(CO2)。
石膏随后被分离出来用于再利用或处理。
2. 碱性洗涤液法:用碱性洗涤液(如氢氧化钠、氨水等)与燃烧产生的SO2进行反应,生成相应的盐类,然后通过沉淀或其他方式分离出来。
干法脱硫工艺流程主要包括石灰石喷雾干法脱硫和双碱法两种方式。
1. 石灰石喷雾干法脱硫:将粉状石灰石喷射到燃烧产生的SO2气流中,通过干法吸收,然后分离出SO2和粉尘。
2. 双碱法:使用两种碱性吸收剂,通常是碳酸氢钠和氢氧化钙,通过干法反应吸收SO2,然后分离出生成的产物。
脱硫工艺流程中需要考虑的参数包括燃料类型、SO2排放浓度、处理效率、再生利用和处理废料等。
不同的工艺流程适用于不同的工业设备和排放标准,因此在选择和设计脱硫工艺时需要综合考虑各种因素。
对于脱硫工艺流程,还有一些其他重要的细节和注意事项需要考虑。
首先,脱硫工艺需要根据具体的工业设备和生产流程进行选择和设计。
比如在煤电厂中,石灰石-石膏法常被用于处理燃煤产生的二氧化硫。
而在工业炉窑中,干法脱硫工艺更为常见。
各种工艺都需要根据具体情况进行优化设计,以提高脱硫效率、减少能耗和减少对环境的影响。
其次,脱硫工艺需要考虑处理后的副产品处理问题。
例如,石膏、除尘灰等副产品需要经过处理后才能达到国家排放标准,或者进行再利用。
对副产品的有效利用不仅可以减少环境污染,还可以降低生产成本。
此外,脱硫工艺的运行参数也需要严格控制。
这包括脱硫剂的投加量、反应温度、气体流速以及脱硫设备的清洁维护等。
通过对这些参数的严格控制,能够确保脱硫工艺的高效运行,减少设备的停机维护,提高设备的使用寿命。
在脱硫工艺的选择中,也需要考虑对能源的消耗。
比如干法脱硫通常需要更多的能源用于干燥和加热过程,而湿法脱硫则需要更多的水资源。
湿法烟气脱硫技术

湿法烟气脱硫技术湿法烟气脱硫技术定义:脱硫剂(钙、钠、铝、镁的氢氧化物或氨)与烟气中二氧化硫在液态下发生反应,生成的副产品为湿态。
化学反应机理(以Ca2+为例):在水中气相SO2被吸收并生成H2SO3SO2+H2O → H++SO32-Ca2+与SO32-或HSO3- 结合,生成CaSO3Ca2++SO32-→ CaSO3吸收液中大量的SO32-,被鼓入的空气强制氧化为SO42-,生成石膏结晶Ca2++SO42-+2H2O →CaSO4· 2H2O1 石灰石-石膏湿法脱硫技术石灰石-石膏湿法脱硫技术是目前世界上技术最为成熟、应用最多的脱硫工艺,特别在美国、德国和日本,应用该工艺的机组容量约占电站脱硫总容量的90%,应用的单机最大容量已达1000MW。
反应方程式:SO2 + 1/2O2 + 2H20 + CaCO3 → CaSO4• 2H20 + CO22HCl + CaCO3 → CaCl2 + H20 + CO22HF + CaCO3 → CaF2 + H20 + CO2技术特点1) 技术成熟可靠2) 脱硫吸收剂有效利用率高3) 高脱硫效率4) 系统运行稳定、煤种和机组负荷变化适应性广5) 脱硫副产品石膏可综合利用6) 大机组使用利用率高技术参数钙硫比(Ca/S): <1.03脱硫效率: >90%系统可利用率:≥98%石灰石-石膏湿法脱硫技术2 湿式烟气脱硫除尘一体化技术工艺原理一级除尘利用除尘脱硫塔中8层喷嘴形成由上而下的16层水膜,与向上运动的含尘烟气通过相互碰撞、拦截和凝集等作用来对烟气进行洗涤;二级除尘采用文丘里管中的小喷嘴形成的水膜与含尘细小液滴碰撞通过绝热膨胀作用形成大液滴,从而去除微小尘粒;经过文丘里管的烟气进入原有的捕滴器形成第三次除尘;石灰(CaO)或熟石灰(Ca(OH)2)配制成石灰浆液加入循环水系统的溶液中,在除尘的同时脱除烟气中的二氧化硫,取得较高脱硫效率;脱硫副产品与除尘的灰浆经浓缩后排入灰场。
电厂脱硫工艺流程介绍

电厂脱硫工艺流程介绍
电厂脱硫工艺是指通过化学反应的方式将烟气中的二氧化硫转化为硫酸盐,从而减少二氧化硫的排放,并达到环保要求。
下面是电厂脱硫工艺的流程介绍:
一、湿法脱硫工艺:
1. 烟气处理:将烟气送入烟囱后,首先进行烟气的处理,包括烟气冷却、水雾除尘、烟气加湿等过程。
2. 石灰石磨制:将石灰石破碎后送到振动筛进行筛分,然后送至磨煤机中进一步磨碎,以提高石灰石的活性。
3. 石灰石搅拌:将磨好的石灰石与水混合并搅拌,使其形成一定浓度的石灰石浆液。
4. 石灰石浆液泵送:将浆液通过泵送至吸收塔,等待烟气和石灰石浆液进行反应。
5. 烟气吸收:吸收塔内将石灰石浆液喷入烟气中,二氧化硫与石灰石浆液中的氢氧根离子发生反应,生成硫酸钙(CaSO4)沉淀。
6. 沉淀堆积:沉淀下来的硫酸钙(CaSO4)经过沉淀池排放。
二、干法脱硫工艺:
1. 烟气处理:将烟气送入烟囱后,同湿法脱硫一样,也需要进行各种
预处理,比如烟气冷却、水雾除尘等。
2. 活性炭制备:通过将煤质活性炭进行破碎磨制和筛分,然后再进行
活化处理和干燥等过程,最终制成活性炭。
3. 活性炭喷射:将制成的活性炭通过喷枪喷入烟道中,与二氧化硫进
行吸附反应,形成活性炭上的硫酸盐。
4. 活性炭回收:将反应完成的活性炭与吸附的硫酸盐分离,分别回收
并再次利用。
以上就是电厂脱硫的基本工艺流程介绍。
不同的电厂所采用的脱硫工
艺可能会有所差异,但在基本流程上都是一致的。
随着环保法规的不
断加强,电厂的脱硫工艺也将不断完善,以更好地减少对环境的影响。
石灰石湿法烟气脱硫技术

石灰石湿法烟气脱硫技术一.工艺流程1脱硫系统由下列子系统组成:1.1石灰石制粉系统1.2吸收剂制备与供应系统1.3烟气系统1.4 SO2吸收系统1.5石膏处理系统1.6废水处理系统1.7公用系统1.8电气系统2 .烟气脱硫工艺流程简介(石灰石——石膏湿法脱硫工艺流程图)作为脱硫吸收剂的石灰石选用石灰石矿生产的3-10mm、水份<1%的石灰石颗粒,运输至石灰石料仓。
石灰石经磨粉机磨制成325目90%通过、颗粒度≤43μm的石灰石粉。
合格的石灰石粉经制浆系统与水配置成30%浓度的悬浮浆液,根据烟气脱硫的需要,在自动控制系统的操纵下通过石灰石浆液泵和管道送入吸收塔系统。
石灰石由于其良好的活性和低廉的价格因素是目前世界上广泛采用的脱硫剂制备原料。
烟气脱硫系统采用将升压风机布置在吸收塔上游烟气侧运行的设计方案,以保证整个FGD 系统均为正压运行操作,同时还可以避免升压风机可能受到的低温烟气腐蚀。
升压风机为烟气提供压头,使烟气能克服整个FGD系统从进口分界到烟囱之间的烟气阻力。
为了将FGD系统与锅炉分离开来在整个脱硫烟气系统中设置有带气动执行机构保证零泄漏的烟气档板门.在要求紧急关闭FGD系统的状态下,旁路档板门在5s自动快速开启,原烟气档板门在55s、净烟气档板门50s内自动关闭。
为防止烟气在档板门中泄漏,原烟气和旁路档板门设有密封空气系统。
脱硫系统运行时,锅炉至烟囱的旁路档板门关闭,锅炉引风机来的全部烟气经过各自的原烟气档板门汇合后进入升压风机.升压后的烟气至气气热交换器(GGH)原烟气侧,GGH 选用回转再生式烟气换热器,涂搪瓷换热元件选用先进波形和高传热系数产品, 以减小GGH总重和节约业主方未来更换换热元件的费用。
GGH利用锅炉出来的原烟气来加热经脱硫之后的净烟气,使净烟气在烟囱进口的最低温度达到80℃以上, 大于酸露点温度后排放至烟囱。
GGH转子采用中心驱动方式。
每台GGH设两台电动驱动装置,一台主驱动,一台备用, 电机均采用空气冷却形式。
烟气脱硫工艺介绍

下面是静调和动调风机曲线:
由上图我们可以看出,静调风机有一个非运行区,静调风机在启动时必须窜过该区域,才能到达需要的运行工况。另外,静调风机的理论失速线非常陡,这是静调风机的最大弱点。
吸收塔搅拌器
吸收塔搅拌器主要作用有两个,一个是使吸收塔浆液池的固体物质离底悬浮,第二个作用使氧化空气均匀分布在吸收塔浆液池内,提高氧化效果。搅拌器是一个技术性很强的设备,一般由专业的搅拌器厂家制造。它的关键部件有:搅拌器叶片、机械密封和轴承;主要技术参数有叶片和轴的直径、搅拌器转速。
EKATO公司在FGD侧进式搅拌器使用的材料
(2)石灰石浆液系统:石灰石浆液系统主要设备包括石灰石浆液箱搅拌器、石灰石浆液泵等。
(3)吸收系统:吸收系统主要设备包括吸收塔(包括吸收塔搅拌器、托盘、喷淋层、喷嘴、除雾器及除雾器清洗系统)、浆液循环泵、氧化风机等。
(4)石膏处理系统:石膏处理系统主要设备有石膏排出泵、石膏旋流器、真空皮带过滤机及辅助设备、真空泵、石膏布料皮带、废水旋流器及废水泵等
对于动调增压风机主要由以下部分组成:进气箱、机壳、转轴、轴承、轮毂、叶片、导流筒、冷却风机系统、润滑油系统、液压调节系统、风机振动监测系统等。对于静调增压风机还有进口导叶及导叶调节系统等。
风机的进气箱主要起到整流作用,使烟气流畅地进入风机而不产生涡流。
机壳配合转子工作的外壳,对转子起支撑作用。
转子包括风机转轴、轮毂、叶片等,是风机工作的主要动部件,它将机械能转化为烟气的动能和势能(静压能),转化效率一般在85%以上。
42CrMo
烟气脱硫技术方案

烟气脱硫技术方案烟气脱硫技术方案一、背景随着能源需求的不断增加,传统煤炭等化石能源的使用也不断增多。
而燃烧这些化石能源会产生大量的二氧化硫等有害气体,对环境及人类健康造成很大的危害。
因此,对烟气进行脱硫处理已成为现代工业生产的必要手段。
本文旨在探讨一种适用于大气污染治理的烟气脱硫技术方案。
二、技术原理目前烟气脱硫的主要方式有湿法脱硫和干法脱硫两种。
本方案采用湿法脱硫技术,其基本原理是将烟气中的二氧化硫与喷洒进入吸收塔内的脱硫剂反应生成硫酸钙或硫酸铁等水溶性盐,从而使烟气中的二氧化硫得到有效的去除。
三、技术流程及设备本方案的技术流程主要分为四个步骤:喷射、吸收、分离、再生。
下面将详细介绍每个步骤所需的设备。
1. 喷射喷射是将脱硫剂裂解成雾状液体后喷洒到吸收塔内与烟气进行接触反应的过程。
该步骤所需设备为脱硫剂处理装置,主要包括水箱、加料器、裂解器以及喷射管等部分。
2. 吸收吸收即是将喷洒进入吸收塔内的脱硫液体与进入吸收塔内的烟气进行接触反应的过程。
为保证吸收效果,该步骤所需设备包括吸收塔、除雾器、进出口管道以及循环泵等部分。
3. 分离分离即是将已吸收的废气通过除雾器进行除雾,然后通过气体处理系统进行处理、净化,最终排放。
为了保证分离效果,该步骤所需设备包括除雾器和气体处理系统。
4. 再生再生即是将脱硫液体与吸收的二氧化硫形成的硫酸钙或硫酸铁等水溶性盐进行再生的过程。
为了保证再生效率,该步骤所需设备为再生设备,主要包括加热器、再生器以及输送管等部分。
加入步骤之间的配套设备,如泵站、调节阀等,即可形成完整的烟气脱硫处理系统。
四、技术优势本方案采用的烟气脱硫技术具有以下优势:1. 脱除效果好:湿法脱硫技术能够去除90%以上的二氧化硫,对国家的环境保护和污染防治具有重要意义。
2. 技术成熟:湿法脱硫技术已被广泛应用于各类工程中,其操作简便、技术成熟、稳定可靠,能够达到较好的脱硫效果。
3. 设备可靠:本方案所需设备大多数是国内知名厂家生产的成熟设备,且设备性能稳定,可以确保设备的可靠运行。
湿法脱硫流程
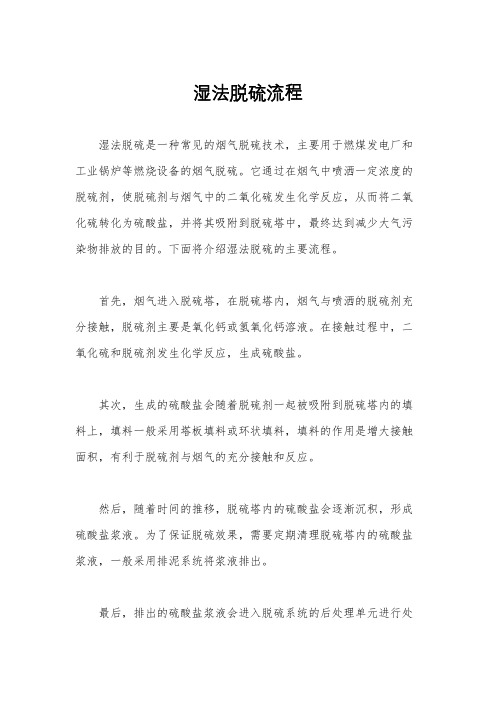
湿法脱硫流程湿法脱硫是一种常见的烟气脱硫技术,主要用于燃煤发电厂和工业锅炉等燃烧设备的烟气脱硫。
它通过在烟气中喷洒一定浓度的脱硫剂,使脱硫剂与烟气中的二氧化硫发生化学反应,从而将二氧化硫转化为硫酸盐,并将其吸附到脱硫塔中,最终达到减少大气污染物排放的目的。
下面将介绍湿法脱硫的主要流程。
首先,烟气进入脱硫塔,在脱硫塔内,烟气与喷洒的脱硫剂充分接触,脱硫剂主要是氧化钙或氢氧化钙溶液。
在接触过程中,二氧化硫和脱硫剂发生化学反应,生成硫酸盐。
其次,生成的硫酸盐会随着脱硫剂一起被吸附到脱硫塔内的填料上,填料一般采用塔板填料或环状填料,填料的作用是增大接触面积,有利于脱硫剂与烟气的充分接触和反应。
然后,随着时间的推移,脱硫塔内的硫酸盐会逐渐沉积,形成硫酸盐浆液。
为了保证脱硫效果,需要定期清理脱硫塔内的硫酸盐浆液,一般采用排泥系统将浆液排出。
最后,排出的硫酸盐浆液会进入脱硫系统的后处理单元进行处理,通常采用浓缩、结晶和干燥等工艺,将硫酸盐浆液转化为干粉状的硫酸盐产品,以便于运输和处置。
总的来说,湿法脱硫流程主要包括烟气脱硫塔、脱硫剂喷洒系统、填料层、排泥系统和后处理单元等部分。
通过这些部分的协同作用,能够有效地将烟气中的二氧化硫转化为无害的硫酸盐,达到减少大气污染物排放的目的。
在实际应用中,湿法脱硫技术具有脱硫效率高、适用范围广、操作维护方便等优点,因此得到了广泛的应用。
然而,也需要注意的是,湿法脱硫过程中会产生大量废水和废渣,需要合理处理,以免对环境造成二次污染。
综上所述,湿法脱硫是一种成熟、高效的烟气脱硫技术,通过合理的工艺设计和操作管理,能够有效地减少燃煤发电厂和工业锅炉等设备的大气污染物排放,对环境保护具有重要意义。
- 1、下载文档前请自行甄别文档内容的完整性,平台不提供额外的编辑、内容补充、找答案等附加服务。
- 2、"仅部分预览"的文档,不可在线预览部分如存在完整性等问题,可反馈申请退款(可完整预览的文档不适用该条件!)。
- 3、如文档侵犯您的权益,请联系客服反馈,我们会尽快为您处理(人工客服工作时间:9:00-18:30)。
2008 年第 6 卷
36.7%, 因此本文拟对其工作 原 理 、化 学 反 应 机 理 、 工 程 流 程 、主 要 设 备 及 其 在 实 际 应 用 中 易 出 现 的 问 题进行探讨。
2 湿法烟气脱硫的工作原理
湿法石灰石 / 石膏烟气脱硫工艺是以价廉易得 的石灰石粉作为吸收剂, 烟气中的二氧化硫与浆液 中的碳酸钙以及通入的空气进行化学反应, 最终产 品为石膏。由于吸收浆液是循环利用, 脱硫吸收剂 的利用率很高[3 ̄5]。湿法烟气脱硫装置的核心是吸收 塔, 它是一个单 级 的 开 放 式 喷 淋 、一 体 化 吸 收 二 氧 化 硫 的 装 置 。 吸 收 塔 分 为 洗 涤 区 、再 循 环 区 和 气 流 区三部分。在洗涤区中二氧化硫和三氧化硫溶解生 成亚硫酸和硫酸, 此区由四层喷淋层组成, 浆液从 再循环区通过四个循环泵打至各喷淋层, 在喷嘴的
2008 年第 6 卷第 4 期
干燥技术与设备 Drying Technology & Equipment
!"
!"
!设!备!与!!工!艺!"
!!!!!!!"
钙基湿法烟气脱硫的工艺过程
周 玲 1, 张 军 1, 廖传华 2
( 1.南京凯盛水泥工业设计研究院, 南京 210014; 2.南京工业大学机械与动力工程学院, 南京 210009)
脱硫风机安置在冷的净化烟气侧, 处于洗涤塔 到热交换器烟道 中 , 此 段 烟 道 由 收 缩 段 、直 管 段 和 扩压段组成。在吸入侧和压力侧均装有消音设备。 脱硫风机是一台轴流式风机, 电机为直联式; 要求 风机拆卸方便, 有防腐措施。 4.2 洗涤塔及工艺流程
洗涤塔为脱硫系统的核心部分, 脱硫的吸收过 程、氧化过程、结晶过程、沉淀过程( 分离沉淀) 和洗 涤分离过程均在洗涤塔中完成。
·203·
摘 要: 以典型的原则性湿式脱硫工艺系统为基础, 介绍了石灰石 / 石膏湿法烟气脱硫的工艺流程
及工作原理, 从理论上分析了湿法脱硫的化学反应机理, 叙述了该系统的结构、工艺流程及系统的特点,
探 讨 了 湿 法 烟 气 脱 硫 的 影 响 因 素 、存 在 问 题 及 解 决 方 法 。
关键词: 烟气脱硫; 湿法; 钙法; 洗涤塔; 分离器; 工艺流程
作用下浆液被雾化, 与逆流而上的原烟气充分接触 并吸收烟气中的二氧化硫和三氧化硫, 同时溶解并 洗涤烟气中的大部分烟尘。吸收塔底部为石灰石浆 液的储存底槽, 储存浓度为 20%的石灰石浆液。底 槽四周安装有贴边搅拌器, 以保持对底槽浆液的不 停搅拌, 使新鲜石灰石浆与因吸收了 SO2 而酸化的 洗涤液能良好地混合和反应。同时底槽还布置有很 多大口径空气管, 空气管出口加在搅拌器叶片加压 面上, 以产生非常小的气泡, 有利于物质交换。因空 气泡还能带出液体中的 CO2, 改善了石灰石粉的溶 解条件。在加了空气管的底槽中, 进行石灰石溶解、 中 和 、氧 化 和 石 膏 结 晶 等 过 程 。 该 工 艺 的 脱 硫 效 率 可达 90%, 其脱硫系统见图 1。
( 1) 工艺流程 洗涤塔采用对流方式运行, 用石灰石作脱硫 剂, 经喷嘴喷出的石灰石液体呈雾状, 与烟气充分 接触, 将 SO2 等有害物质进行分离。洗涤塔脱硫的工 艺流程为: SO2 洗涤( 吸附) 、氧化、结晶、沉淀和液滴 分离, 将其组合成一体, 并产生脱硫的副产物石膏。 当原烟气经烟 / 烟热交换器冷却到 80℃左右时, 以 18m/s 的速度通过洗涤塔的短接管, 从上至下流经 吸收区。 ( 2) 吸收区 吸收区有 6 层交错布置的喷嘴, 喷嘴上有直径 8mm 的锥孔。这些喷嘴使循环使用的洗 涤 悬 浮 液 ( 即石灰石浆液) 通过雾化分散成很细的液滴, 在吸 收区形成 1 个反应面, 烟气在该区域有短暂的滞留 时间, 且有一定的速度, 强烈的喷射导致烟气达到 饱和水蒸气温度, SO2 等有害气体通过 6 层 交 错 布 置的喷嘴与喷射出的石灰悬浮液进行物质交换, SO2、HCl 和 HF 被分离融合到溶液中, 液体中的水
考虑到热膨胀的平衡, 在烟气系统装入了补偿 器, 热烟气侧的补偿器是氟弹性体, 冷烟气侧的补 偿器是由氯丁基橡胶制成的。
( 2) 烟 / 烟热交换器 烟 / 烟热交换器是由涂珐琅质的薄钢板制成
的, 由垂直布置的转子带动, 烟气以垂直对流方式 工作。烟 / 烟热交换器的功能分为两部分: 右侧的功 能是将温度约 130℃的原烟气降到 80℃左右, 并送 入洗涤塔; 左侧的功能是将净化后的冷烟气由 47℃ 加热到 95℃, 使其达到烟囱排放所需的温度。运行 时, 烟 / 烟热交换器的内表面会有沉积物附着, 沉积 物一方面是由原烟气的飞灰和灰尘颗粒引起的, 另 一方面是由净化烟道气所含液态盐类和固态物质 的残余液滴形成的结壳, 因此需定期采用高压空气 和高压水进行清污。加热器和烟道在停运时, 需用 加热的干燥空气进行保护。
4 工艺过程及主要设备
4.1 烟气侧工艺流程 ( 1) 工艺流程 原烟气通过双关断阀到烟 / 烟热交换器的入
口, 经交换器冷却后进入洗涤塔。烟气在洗涤塔中 与石灰石悬浮液充分对流交换后 , SO2 等 有 害 气 体 被捕捉( 在洗涤过程中烟气被降温) , 而后携带水蒸 气的烟气经过双层特殊结构的液滴分离器, 将烟气 中的液滴分离, 分离后的水分排入集水箱, 烟气经 脱硫风机的扩压段出口到热交换器的入口, 在热交 换器被加热后, 经关断阀排入烟囱, 其平均流速约 为 15m/s。烟气通道截面呈矩形, 烟气通道和加热器 的导向罩需作防腐处理。为冲洗方便, 烟道应有落 差坡度, 中部方向为 3%, 纵轴方向为 1%。
第4期
周玲等 . 钙基湿法烟气脱硫的工艺过程
·205·
SO2 向浆滴的传质主要受气膜控制, 而在高浓度区, 传质受浆滴内部液相控制。有学者认为, SO2 向浆滴 表面的扩散过程受气膜控制, 而液相一侧并非由液 膜来控制, 而是由参与反应的离子扩散速度来决 定。从反应动力学来看, SO2 是溶解度大小为中等的 气体, 在烟道内温度较高, SO2 溶解度很低, 气相 推 动力最大, SO2 在气相的扩散不再是整 个 反 应 过 程 的控制速率, 液相参与反应的离子扩散成为主导因 素。随着反应温度与 SO2 浓度的逐渐降低, 气相推动 力减弱, SO2 向浆滴表面的扩散速率与 液 相 参 与 反 应离子的扩散速率等共同成为控制反应的因素。当 反应温度接近于湿球温度时, SO2 浓度达到最小, 此 时气相推动力也最小。SO2 向液相的扩散所受阻力 相对于参与反应的离子扩散过程来说处于主导地 位, 传质阻力为气相传质所控制。在 Ca(OH)2 石灰浆 滴 与 SO2 吸 附 反 应 的 过 程 中 , O2 也 参 与 了 反 应 , 其 反应过程可描述为:
当前已开发的湿法烟气脱硫技术, 主要是石灰 石 / 石膏洗涤法, 它占整个湿法烟气脱硫技术的
收稿日期: 2008- 7- 2。 作者简介: 周玲( 1974—) , 女, 湖北仙桃人, 工程师, 主要从事水泥 过程与设备的设计工作。
·204·
干燥技术与设备 Drying Technology & Equipment
中图分类号: TQ113.264.1
文献标( 2008) 04- 0203- 06
1 概述
能源和环境是当今社会发展的两大主题。中国 的资源特点和经济发展水平决定了以煤为主的能 源结构将长期存在, 国内每年都会消费数亿吨煤。 煤所含的杂质硫在燃烧时会排放酸 性 气 体 SO2, 这 种气体在高空为雨雪所溶解而形成酸雨, 可导致动 植物大量死亡, 给生态系统造成很大的破坏, 还会 严重侵蚀桥梁楼屋、船舶车辆、机电设备等, 给经济 的发展带来严重影响, 并对人类的健康造成危害。 自上世纪 80 年代以来, 由于我国经济的飞速发展, SO2 排放量也日益增多, 据统计, 2005 年全国 SO2 排 放量为 2549 万吨。大量 SO2 的排放, 使中国酸雨区 迅速扩大, 目前 已 覆 盖 四 川 盆 地 和 长 江 以 南 、青 藏 高原以东的广大地区, 占国土总面积的 1/3, 而且每 年还以 10 万 km2 的速度在递增。因此, 控制和减少 SO2 排放量已是刻不容缓、迫在眉睫了, 国家环保总 局和国家发改委将采用多项措施加强 SO2 污染的防 治。专家认为消减 SO2 排放总量是今后中国环保工 作的重点, 对烟气脱硫是控制 SO2 污染的主要措施 之一。但到目前为止, 我国还仅限于燃煤电厂的脱 硫 ( 仅有 12%装 机 容 量 的 火 电 厂 建 有 烟 气 脱 硫 装 置) 。因此开发新型高效、脱硫产物可循环再利用的
以 CaO 为例, 主要的反应为: ① SO2(g)+H2O H2SO3
② Ca(OH)2(aq)+H2SO3(aq) CaSO3(aq)+2H2O ③ CaSO3(aq) CaSO3(s) ④ CaSO3(aq)+1/2O2(aq) CaSO4(aq) ⑤ CaSO4(aq) CaSO4(s) ⑥ Ca(OH)2(s) Ca(OH)2(aq) Ca(OH)2 石灰浆滴与 SO2 的反应过程较为复杂, 许多科研工作者先后进行了这方面的研究工作, Brogren 和 Kanlesson 认为, 石灰浆滴与 SO2 的反应 存在 2 个受控区域: 在烟道内 SO2 浓度低的区域,
·206·
干燥技术与设备 Drying Technology & Equipment
2008 年第 6 卷
转移至气相中( 水蒸发) , 并将气体中的热能传导给 溶液, 脱硫剂从固态溶解至溶液中。
( 3) 点滴分离器 洗涤塔头部装有 8 个垂直安装的弓形点滴分 离器( 由 8 个扇形部分组成) 。每个扇形部分由 2 个 单元分离器组成, 每个单元分离器由 3 个彼此重叠 在一起的直立的一束分离器组成。烟气流水平地由 内向外通过这些分离元件, 流至外部分离元件后, 进入 1 个环形通道, 再经 1 个连续的扩张室至烟气 的出口。由于分离器的特殊构造, 前排分离器将烟 气携带的大部分液滴分离, 从第 2 排起起着细分离 的作用。由于烟气运动的惯性, 在烟气转向时, 液滴 不可能跟随, 因分离元件平面上设置了分隔室, 烟 气在其后形成回流漩涡, 将被分离的液滴集中至集 水箱。由于分离器表面粘有石膏和灰尘颗粒, 因此 需定期用水冲洗。 ( 4) 氧化区 洗涤塔中氧化区的空气是由 2 个旋转鼓风机 提供的, 输送空气的管线呈向上指引式敷设, 通过 吹射使空气中的氧气溶解到溶液中, 并使液体中 溶 解 的 物 质( 主 要 指 Ca(HSO3)2) 进 一 步 氧 化 形 成 CaSO4, 并以固态形式沉淀。 ( 5) 沉淀区 氧化区的下面是沉淀区, 在氧化区形成的细小 石膏颗粒进一步变大, 通过悬浮液中固态浓液的调 整, 使结晶过程达到最佳。在沉淀区将含有石膏的 悬浮液用泵送至液压旋流分离器。 ( 6) 循环系统 在沉淀区下部的圆锥体部位连接洗涤循环泵, 洗涤悬浮液由 3 台循环泵输送到喷嘴平台上, 洗涤 悬浮液基本上是 由 水 、脱 硫 剂 、石 膏 以 及 被 溶 解 的 盐类物质组成。脱硫剂配料站配好的洗涤悬浮液由 添加剂泵送至圆锥体部位。脱硫剂量与被分离的二 氧化硫量成比例, 且确定服从 SO2 负荷的信号。为了 防止带盐洗涤液的过载, 将液体旋流分离器上部澄 清层的悬浮液与真空履带式过滤器的排水引至排 水箱, 并将一部分循环至洗涤塔。