材料液态成型工艺学-4(XXXX)
材料成型原理及工艺第一章液态成型工艺基础理论
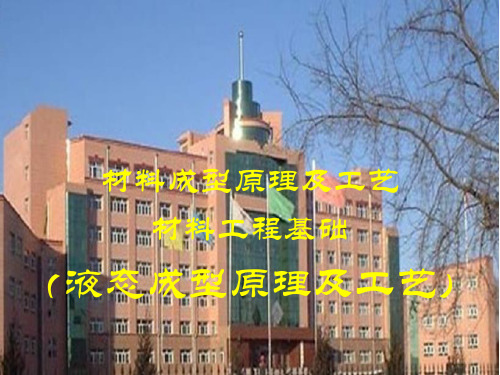
态 陷产生,导致成型件力学性能,
成 特别是冲击性能较低。
型 2. 涉及的工序很多,难以精确控
的 制,成型件质量不稳定。
缺 3.由于目前仍以砂型铸造为主,
点:
自动化程度还不很高,且属于热 加工行业,因而工作环境较差。
4.大多数成型件只是毛坯件,需 经过切削加工才能成为零件。
液态成型原理及工艺
冲天炉出铁
缸体等。
液态成型原理及工艺
液 (3) 成本较低
态
所用原料大都来源广泛,价格
成
低廉,一般不需要昂贵的设备。
型
的 (4)成型件尺寸精度高
优
成型件与最终零件的形状相似、
点:
尺寸相近,因而切削加工余量可 减少到最小,从而减少了金属材
料消耗,节省了切削加工工时。
液态成型原理及工艺
液
1. 组织疏松,晶粒粗大,成型件 内部常有缩孔、缩松、气孔等缺
液态成型原理及工艺
一、液态合金的流动性
1、合金流动性:是指液态合金本身的
流动能力。
合金的流动性用浇注 流动性试样的方法来 衡量。流动性试样的 种类很多,如螺旋形、 球形、α形、真空试 样等等,应用最多的 是螺旋形试样,如图11所示。
图1-1 液态成型原理及工艺
合金流动性主要取决于合金化学成分。对应着纯 金属、共晶点和形成金属间化合物的成分,流动 性出现最大值;而有结晶温度范围的合金,流动 性下降。这是因为纯金属和共晶成分的合金是在 恒温下结晶的,凝固层表面光滑,对尚未凝固的 金属液流动阻力小,因此流动性好;如图1-2a。
液态成型原理及工艺
绪 论 复习题
1、什么是液态成型?优缺点有哪些?
液态成型原理及工艺
第一章液态成型工艺基础理论
液态成形工艺知识点总结

液态成形工艺知识点总结液态成形工艺的主要特点是能够将液态材料通过模具加工成所需的零件、产品,具有成形周期短、生产效率高、成形精度高、批量生产能力强等优点。
其成型材料包括热塑性塑料、热固性塑料、金属合金等,广泛应用于各种制造工艺中。
注塑成形是将热塑性塑料通过加热并加压的方式,使其溶解成为流动状态,然后通过注射机将其注入模具中进行成型。
注塑成形工艺主要包括原料预处理、注塑机操作、模具设计、成型工艺参数控制等多个方面。
在注塑成形工艺中,模具设计是至关重要的,其质量直接影响到成型产品的质量和生产效率。
同时,成型工艺参数的控制也非常重要,包括注塑温度、注射速度、模具温度、冷却时间等参数的控制都会影响到成型产品的质量。
压铸成形是将金属合金通过加热并加压的方式,使其溶解成为流动状态,然后通过压铸机将其注入模具中进行成型。
压铸成形工艺主要包括原料预处理、压铸机操作、模具设计、成型工艺参数控制等多个方面。
在压铸成形工艺中,原料的质量和成分控制是至关重要的,影响到成型产品的力学性能和表面质量。
同时,模具设计和成型工艺参数的控制也非常重要,直接影响到成型产品的形状精度和表面粗糙度。
吹塑成形是将热塑性塑料通过加热并加压的方式,使其溶解成为流动状态,然后通过气流将其吹入模具中进行成型。
吹塑成形工艺主要包括原料预处理、吹塑机操作、模具设计、成型工艺参数控制等多个方面。
在吹塑成形工艺中,原料的质量和成分控制同样非常重要,直接影响到成型产品的力学性能和表面质量。
模具设计和成型工艺参数的控制也是影响成型产品质量的重要因素。
挤塑成形是将热塑性塑料通过加热并压力的方式,使其在挤出机中形成带状截面的坯料,然后通过挤出头模具进行成型。
挤塑成形工艺主要包括原料预处理、挤出机操作、模具设计、成型工艺参数控制等多个方面。
在挤塑成形工艺中,原料的质量和成分控制同样非常重要,直接影响到成型产品的力学性能和表面质量。
同时,模具设计和成型工艺参数的控制也是影响成型产品质量的重要因素。
材料成型工艺及液态成形工艺简介

载
观
看
10、阅读一切好书如同和过去最杰出的人谈话。20:16:2220:16:2220:163/9/2021 8:16:22 PM
11、越是没有本领的就越加自命不凡。21.3.920:16:2220:16Mar-219-Mar-21
MOMODA POWERPOINT
12、越是无能的人,越喜欢挑剔别人的错儿。20:16:2220:16:2220:16Tuesday, March 09, 2021
15、楚塞三湘接,荆门九派通。。。2021年3月下午8时16分21.3.920:16March 9, 2021
感 谢 您 的 下 16、少年十五二十时,步行夺得胡马骑。。2021年3月9日星期二8时16分22秒20:16:229 March 2021
17、空山新雨后,天气晚来秋。。下午8时16分22秒下午8时16分20:16:2221.3.9 9、杨柳散和风,青山澹吾虑。。21.3.921.3.9Tuesday, March 09, 2021
15、比不了得就不比,得不到的就不要。。。2021年3月下午8时16分21.3.920:16March 9, 2021
16、行动出成果,工作出财富。。2021年3月9日星期二8时16分22秒20:16:229 March 2021
17、做前,能够环视四周;做时,你只能或者最好沿着以脚为起点的射线向前。。下午8时16分22秒下午8时16分20:16:2221.3.9
13、知人者智,自知者明。胜人者有力,自胜者强。21.3.921.3.920:16:2220:16:22March 9, 2021
14、意志坚强的人能把世界放在手中像泥块一样任Lor意em揉ip捏su。m 2d0o2lo1r年sit3a月me9t日, c星ons期ec二tet下ur午ad8ip时isc1i6n分g e2li2t.秒Fu2s0c:e1i6d:2u2rn2a1.b3la.9ndit, eleifend nulla ac,
材料液态成型工艺学
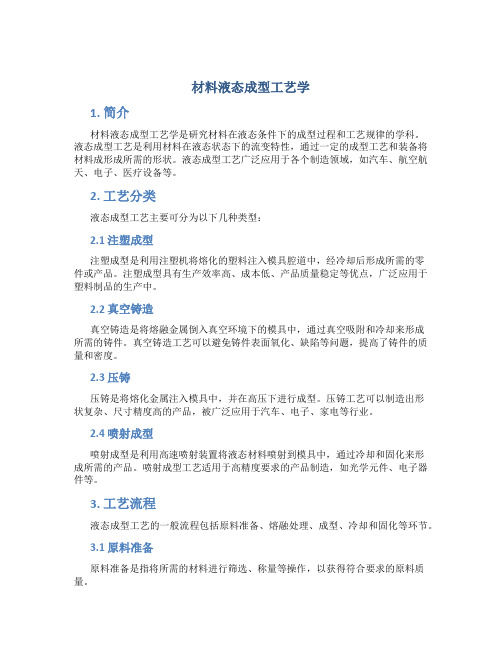
材料液态成型工艺学1. 简介材料液态成型工艺学是研究材料在液态条件下的成型过程和工艺规律的学科。
液态成型工艺是利用材料在液态状态下的流变特性,通过一定的成型工艺和装备将材料成形成所需的形状。
液态成型工艺广泛应用于各个制造领域,如汽车、航空航天、电子、医疗设备等。
2. 工艺分类液态成型工艺主要可分为以下几种类型:2.1 注塑成型注塑成型是利用注塑机将熔化的塑料注入模具腔道中,经冷却后形成所需的零件或产品。
注塑成型具有生产效率高、成本低、产品质量稳定等优点,广泛应用于塑料制品的生产中。
2.2 真空铸造真空铸造是将熔融金属倒入真空环境下的模具中,通过真空吸附和冷却来形成所需的铸件。
真空铸造工艺可以避免铸件表面氧化、缺陷等问题,提高了铸件的质量和密度。
2.3 压铸压铸是将熔化金属注入模具中,并在高压下进行成型。
压铸工艺可以制造出形状复杂、尺寸精度高的产品,被广泛应用于汽车、电子、家电等行业。
2.4 喷射成型喷射成型是利用高速喷射装置将液态材料喷射到模具中,通过冷却和固化来形成所需的产品。
喷射成型工艺适用于高精度要求的产品制造,如光学元件、电子器件等。
3. 工艺流程液态成型工艺的一般流程包括原料准备、熔融处理、成型、冷却和固化等环节。
3.1 原料准备原料准备是指将所需的材料进行筛选、称量等操作,以获得符合要求的原料质量。
3.2 熔融处理熔融处理是指将原料加热并熔化,使其达到液态转变的温度。
熔融处理通常使用加热炉、熔炉等设备来完成。
3.3 成型成型是将熔融的材料注入模具中,并施加适当的压力或加热条件,以获得所需的形状和尺寸。
3.4 冷却和固化成型完成后,材料需要经过冷却和固化过程。
冷却可以通过冷却水、风扇等方式快速降温,固化则是通过材料的结构变化实现。
4. 工艺参数液态成型过程中的工艺参数对成型质量有重要影响,常见的工艺参数包括:•温度:熔融处理温度、模具温度等;•压力:注塑成型中的注射压力、压铸中的压力等;•流速:喷射成型中的喷射速度、流道设计等。
材料液态成形工艺

3.铸造有色金属 常用的有铸造铝合金、铸造铜合金等。它们大都具有
流动性好,收缩性大,容易吸气和氧化等特点,特别容 易产生气孔、夹渣缺陷。
六、新型材料-金属间化合物及其铸造性能 特点
第三节 砂型铸造
第三节 砂型铸造
1.金属液的流动性 液态金属的流动性是指金属液的流动能力。流动性越好
的金属液,充型能力越强。流动性的好坏,通常用在特定 情况下金属液浇注的螺旋形试样的长度来衡量,如图7-2 所示。
图7-3为铁-碳合金的流动性与成分的关系。 2.浇注(Pouring)条件 3.铸型特性
为改善铸型的充填条件,在设计铸件时必须保证其壁厚 (Wall Thickness)不小于规定的“最小壁厚”(如表7-1所 示)。
二、熔模铸造
1.基本工艺过程 熔模铸造的工艺过程如图7-15所示。主要包括蜡
模(Wax pattern)制造、结壳、脱蜡(Dewax) 、焙烧和浇注等过程。 2.熔模铸造的特点和应用
第四节 特种铸造
三、压力铸造
压力铸造(Die Casting)是压铸机上将熔融的金属在高 压下快速压入金属型,并在压力下凝固,以获得铸件的方 法。 压铸机分为立式和卧式两种,图7-16为立式压铸机 工作过程示意图。
图7-4铸铁的凝固方式
图7-5温度梯度对凝固区域的影响
图7-6 缩孔形成示意图
图7-7缩松形成示意图
图7-8顺序凝固示意图
图7-9同时凝固示意图
图7-10热应力引起的变形
图7-11震压造型过程表
图7-12抛砂紧实原理
图7-13射砂机工作原理图
图7-14金属型铸造示意图
液态成形 教学大纲
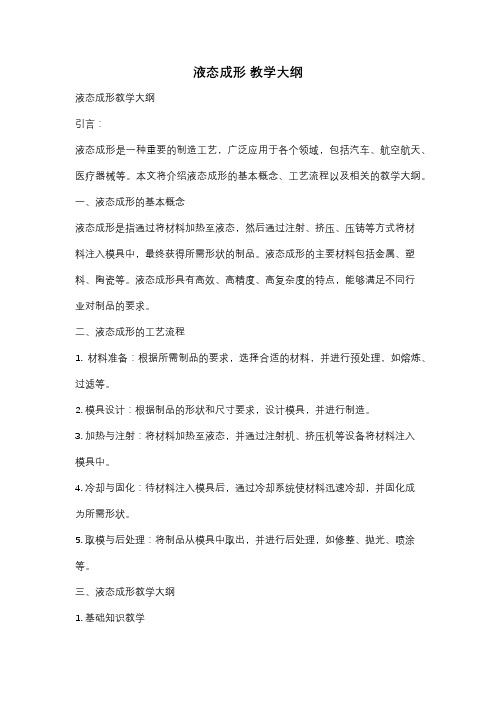
液态成形教学大纲液态成形教学大纲引言:液态成形是一种重要的制造工艺,广泛应用于各个领域,包括汽车、航空航天、医疗器械等。
本文将介绍液态成形的基本概念、工艺流程以及相关的教学大纲。
一、液态成形的基本概念液态成形是指通过将材料加热至液态,然后通过注射、挤压、压铸等方式将材料注入模具中,最终获得所需形状的制品。
液态成形的主要材料包括金属、塑料、陶瓷等。
液态成形具有高效、高精度、高复杂度的特点,能够满足不同行业对制品的要求。
二、液态成形的工艺流程1. 材料准备:根据所需制品的要求,选择合适的材料,并进行预处理,如熔炼、过滤等。
2. 模具设计:根据制品的形状和尺寸要求,设计模具,并进行制造。
3. 加热与注射:将材料加热至液态,并通过注射机、挤压机等设备将材料注入模具中。
4. 冷却与固化:待材料注入模具后,通过冷却系统使材料迅速冷却,并固化成为所需形状。
5. 取模与后处理:将制品从模具中取出,并进行后处理,如修整、抛光、喷涂等。
三、液态成形教学大纲1. 基础知识教学a. 液态成形的定义和分类:介绍液态成形的基本概念,包括不同类型的液态成形工艺。
b. 材料选择与处理:讲解不同材料的特点及其处理方法,包括熔炼、过滤等。
c. 模具设计与制造:介绍模具设计的基本原理和制造过程,包括CAD/CAM技术的应用。
d. 工艺参数控制:讲解液态成形过程中的关键参数控制方法,如温度、压力等。
2. 实践操作教学a. 设备操作与维护:教授液态成形设备的操作方法和维护技巧,确保设备正常运行。
b. 模具安装与调试:指导学生进行模具的安装和调试工作,确保模具能够正常运行。
c. 材料加热与注射:实践操作材料的加热和注射过程,培养学生的操作技能。
d. 制品取模与后处理:指导学生进行制品的取模和后处理工作,确保制品质量达到要求。
结论:液态成形作为一种重要的制造工艺,对于培养学生的实践能力和创新能力具有重要意义。
通过液态成形教学大纲的制定和实施,可以提高学生的专业素养,为相关行业的发展做出贡献。
液态成型工艺(
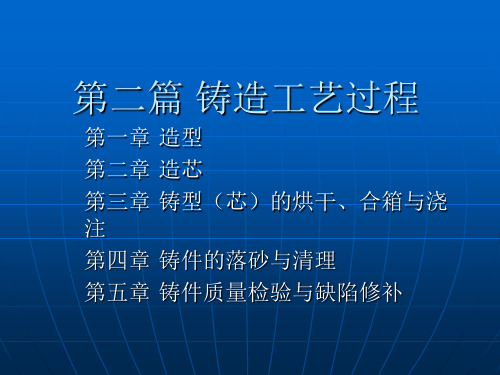
震击噪音小,劳动条件好。
生产率高(120箱/h),铸件质量好。 机器使用可靠,维修方便,价格低。
微震压实原理图
第四节
一、高压造型概述
水平分型高压造型
高压造型优缺点 优点:铸件质量高。 由于铸件质量高,可减少机加工余量,成本低。 降低劳动强度,改善劳动条件,提高生产率。 适应性强,能制造复杂、较大的铸件。 二、水平分型高压造型工艺过程 1、水平分型有箱高压造型 2、水平分型脱箱高压造型
四、冷冻造型
又称低温硬化造型法。其过程是采用普通石英砂作为骨架材料,加入少 量水,必要时加少量粘土,按普通造型方法制好铸型后送入冷冻室中, 用液态氮或二氧化碳作为制冷剂,使铸型冷冻,借助于包覆在砂粒表面 的冷冻水分而实现砂粒的结合,使铸型具有很高的强度及硬度。浇注时, 铸型温度升高,水分蒸发,铸型逐步解冻,稍加振动立即溃散,可方便 地取出铸件。 与其他造型方法相比,冷冻造型法具有以下特点: (1) 型砂中除少量的水及粘土外,无其他辅助材料,铸件的清理落砂方 便,设备简单; (2) 粉尘及有害气体少,环境污染小; (3) 铸型强度高、硬度大、透气性好,铸件表面粗糙度低、缺陷少。采 用这种造型方法生产球墨铸铁件可实现无冒口铸造,不会产生白口组织。
2、机器造型的特点
要使用模板 使用标准或专用砂箱
尽量采用单一砂
砂型只能有一个分型面 一般为流水线生产,浇注速度快,对浇注系统要求高
3、机器造型方法分类
砂型表面单位面积所受的压力称为压实比压。 根据比压大小可分为: 高压造型-----比压≥0.689MPa 中压造型-----比压在0.4~0.7MPa 低压造型-----比压在0.13~0.4MPa
5、出气孔与排气槽
四、垂直分型无箱高造型
材料液态成型工艺学-4
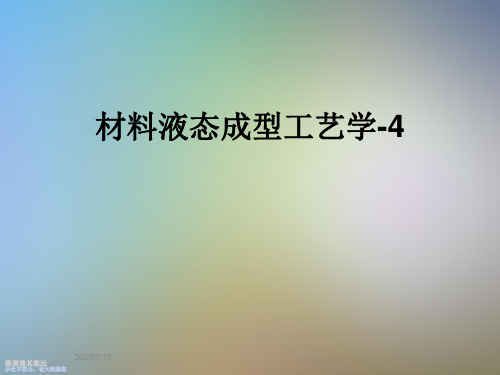
合金 种类
灰铸铁
球铁 碳钢 铝合金
路漫漫其悠远
表6-1 不同合金的临界壁厚
牌号
重 量(kg)
0.1-2.5 2.5-10
>10
HT100,HT150 HT200,HT250
HT300 HT350
QT400-15,QT450-10
QT500-7,QT600-3
ZG200-400,ZG230450
2. 铸件壁的连接应逐渐过渡
路漫漫其悠远
2. 铸件壁的连接应逐渐过渡
路漫漫其悠远
一、从避免缺陷方面审查零件结构的合理性
3.结构圆角的设计 铸件壁的转角处一般要设计出结构圆角。 1) 铸件壁的直角连接易造成连接处的金属堆积,形
成大的热节。而内侧的散热条件差,往往会造成 缩孔、缩松; 2) 在载荷的作用下,直角内侧往往产生应力集中, 内侧实际承受的应力比平均应力大得多; 3) 若采用直角连接,在一些合金凝固的过程中将形 成垂直于铸件表面的柱状晶。因结晶的方向性, 在转角的对角线上形成整齐的分界面。由于分界 面上杂质、缺陷较多,使转角处成为铸件的薄弱 环节,在集中应力作用下很容易产生裂纹。
8-10 12-15 12-18 15-20
10 14-18
15 6-10
10-15 12-15 15-18 15-20 15-20 18-20
20 6-12
20-25 12-18
25 25 50 60 ---10-14
表6-2 灰铸铁相对强度的变化(壁厚单位:mm)
壁厚δ 15-20 相对强度 1.0
前两者产生翘曲变形的主要原因是:铸件结构刚度 差,铸件各面冷却条件的差别所引起的不大的内应力 使其变形。
后者主要是壁厚差别大,厚壁处冷却慢,薄壁处冷 却快,引起较大的内应力促使铸件产生变形。
材料成型原理及工艺第一章液态成型工艺基础理论
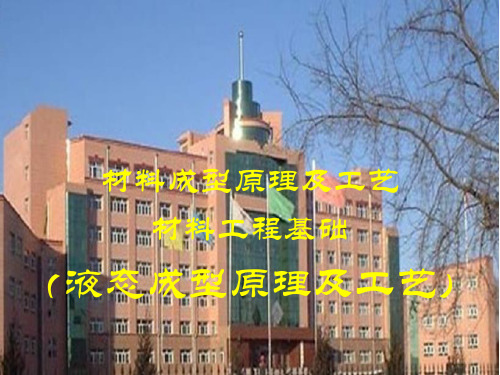
态 陷产生,导致成型件力学性能,
成 特别是冲击性能较低。
型 2. 涉及的工序很多,难以精确控
的 制,成型件质量不稳定。
缺 3.由于目前仍以砂型铸造为主,
点:
自动化程度还不很高,且属于热 加工行业,因而工作环境较差。
4.大多数成型件只是毛坯件,需 经过切削加工才能成为零件。
液态成型原理及工艺
冲天炉出铁
液态成型原理及工艺
绪论:
金属液态成型又称为铸造,
金 它是将固态金属熔炼成符合
属 液 态 成 型:
一定要求的液态金属,然后 将液态金属在重力或外力作 用下充填到具有一定形状型 腔中,待其凝固冷却后获得 所需形状和尺寸的毛坯或零 件,即铸件的方法。
制造毛坯或机器零件的重要方法。
液态成型原理及工艺
绪论:
的 游离原子
级,在此范围 内仍具有一定
近
液
的规律性。原
程
态
子集团间的空
结
空穴或裂纹 穴或裂纹内分
布着排列无规
有 序
构
则的游离的原
子。
液态成型原理及工艺
这样的结构不是静止的,而是 处于瞬息万变的状态,即原子 集团、空穴或裂纹的大小、形 态及分布及热运动的状态都处 于无时无刻不在变化的状态。 液态中存在着很大的能量起伏。
液 液态成型件在机械产品中占有重 态 要比例:
成 在机床、内燃机、重型机器中铸 型 件约占70%-90%;在风机、压
的 缩机中占60%-80%;在拖拉机
重 中占50%-70%;在农业机械中
要 占40%-70%;汽车中占20%-30
性 %。
液态成型原理及工艺
液 态 成 型 的 优 点:
(1) 适应性广,工艺灵活性大
第4章材料的液态成形工艺

第五节 铸件结构工艺性
第五节 铸件结构工艺性
一、铸件结构应利于避免或减少铸件缺陷
1.壁厚合理 通常情况下,设计铸件壁厚时应首先保证金属液 的充型能力,在此前提下尽量减小铸件壁厚。若铸件 壁的承载能力或刚度不能满足要求时,可采用加强筋 等结构。图 4-19 为台钻底板设计中采用加强筋的例子 。 2.铸件壁厚力求均匀 铸件壁厚均匀,可防止形成热节而产生缩孔、缩 松、晶粒粗大等缺陷,并能减少铸造热应力及因此而 产生的变形和裂纹等缺陷。如图 4-20 所示铸件的结构 设计,铸件上的筋条分布应尽量减少交叉,以防形成 较大的热节,如图4-21。
第一节 金属铸造工艺简介
第二节 铸造工艺基础知识
一、液态金属的充型能力
液态金属的充型能力 (Mold Filling Capacity) 是指 液态金属充满铸型型腔,获得形状完整、轮廓清晰铸件的 能力。 1.金属液的流动性 液态金属的流动性是指金属液的流动能力。流动性越 好的金属液,充型能力越强。流动性的好坏,通常用在特 定情况下金属液浇注的螺旋形试样的长度来衡量,如图42所示。 图4-3为铁-碳合金的流动性与成分的关系。 2.浇注(Pouring)条件 3.铸型特性 为改善铸型的充填条件,在设计铸件时必须保证其壁 厚(Wall Thickness)不小于规定的“最小壁厚”(如表4-1 所示)。
第一节 金属铸造工艺简介
五、常用铸造合金的铸造性能特点
1.铸铁 (1)灰口铸铁 (2)球墨铸铁 (3)可锻铸铁 2.铸钢 铸钢的铸造性能差。铸钢的流动性比铸铁差,熔点 高,易产生浇不足、冷隔和粘砂等缺陷。铸钢的收缩性 大,产生缩孔、缩松、裂纹等缺陷的倾向大 。 3.铸造有色金属 常用的有铸造铝合金、铸造铜合金等。它们大都具 有流动性好,收缩性大,容易吸气和氧化等特点,特别 容易产生气孔、夹渣缺陷。
材料成型与工艺课后答案 1-3,1-4
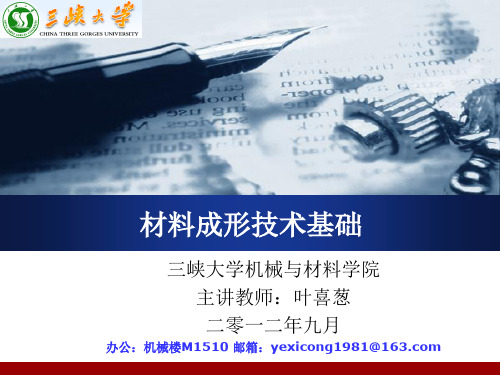
铸造工艺图:铸造工艺图是利用各种工 艺符号,把制造模样和铸型所需的资料, 直接绘在零件图上的图样。
它是制造模样和铸型,进行生产准备和铸件检验的依 据——基本工艺文件 收缩余量
工 浇注位置 艺 方 分型面的选择 案
工 加工余量 艺 参 起模斜度 数 铸造圆角 型芯及芯头
浇 组成及作用 注 常见类型 系 统 冒口
2)铸件的大平面应朝下,减少辐射,防开裂夹渣。
3)面积较大的薄壁部分应置于铸型下部或垂直、 倾斜位置。防止产生浇不足、冷隔。
4)易形成缩孔的铸件,较厚部分置于上部或 侧面。考虑安放冒口利于补缩。
5) 应尽量减少型芯的数量。
6)要便于安放型芯、固定和排气。
Back to page-4
浇注位置
较大的铸件,宜将内浇道
从铸件薄壁处引入,以利 铸件同时凝固,减少铸件 的内应力、变形,防止裂 纹产生。
二、浇注位置的选择-六点注意
浇注位置:浇注时铸件在铸型中所处的空间位置;浇 注位置对铸件质量及铸造工艺都有很大影响。选择时应考 虑如下原则:
选择原则:
1)铸件的重要加工面和受力面应朝下或位于侧面, 避免砂眼气孔和夹渣。
1)冒口就近设在铸件热节的上方或侧旁; 2) 冒口尽量设在铸件最高、最厚的部位,对低处的热节增设补 贴或使用冷铁。 3)冒口不应设在铸件重要的、受力大的部位,以防晶粒粗大降 低力学性能。 4)冒口位置不要选在铸造应力集中处,应注意减轻对铸件的收 缩阻碍,以免引起裂纹。 5)尽量用一个冒口同时补缩几个热节或铸件 6)冒口布置在加工面上,可借加工精整铸件表面,零件外观质 量好。 7)对不同高度上的多个冒口,应用冷铁使各个冒口的补缩范围 相隔开
起模斜度的大小根据立壁的高度、造型方法和模样材料来 确定:立壁愈高,斜度愈小;外壁斜度比内壁小;机器造型 的一般比手工造型的小;金属模斜度比木模小。具体数据可 查有关手册。一般外壁为3º ~ 15°,内壁为3°~10°。
液态成型4
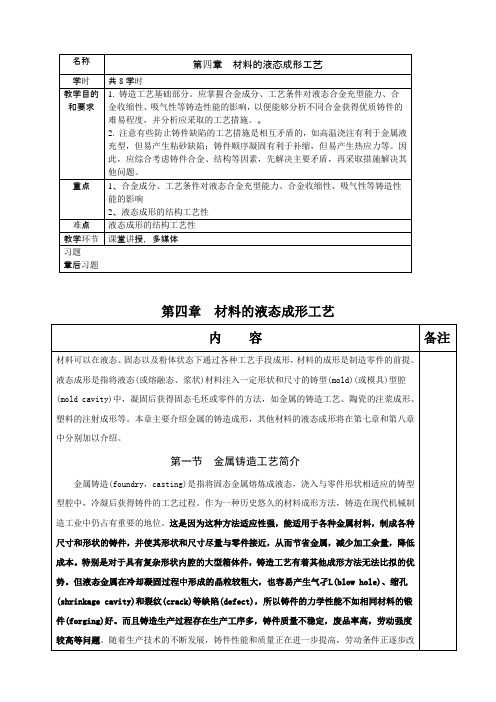
3.铸型特性
铸型结构和铸型材料均影响金属液的充型。铸型中凡能增加金属液流动阻力,降低流动速度和加快冷却速度的因素,如:型腔复杂,直浇道过低,浇口(gating system,running system)截面积小或不合理,型砂水分过多,铸型排气不畅和铸型材料导热性过高等,均能降低金属液的充型能力。为改善铸型的充填条件,在设计铸件时必须保证其壁厚(wall thickness)不小于规定的“最小壁厚”(如表4—1所示)。对于薄壁铸件,要在铸造工艺上采取措施,如加外浇口、适当增加浇注系统的截面积、采用特种铸造方法等。
表44几种常用铸造方法的比较比较项目铸造方法砂型铸造熔模铸造金属型铸造压力铸造低压铸造离心铸造适用金属任意不限制以铸钢为主不限制以有色合金为主铝锌等低熔点合金以有色合金为主以铸铁铜合金为主适用铸件大小任意一般25kg以中小铸件为主也可用于数吨大件一般10kg下小件也可用于中等铸件中小铸件为主不限制生产批量不限制成批大量也可单件生产大批大量大批大量成批大量成批大量铸件尺寸精度itl4itl5itllitl4itl2itl4itllitl3itl2itl4itl2itl4孔径精度低表面粗糙度值ram粗糙125161256332081253212563内孔粗糙铸件内部质量结晶粗结晶粗结晶粗结晶细内部多有气孔不加工结晶细缺陷很少铸件加工余量大小或不加工小小内孔加工量大生产率一般机械化程度低中低中中高最高中中高应用举例机床床身轧钢机机架变速器箱体带轮等一般铸件刀具叶片自行车零件机床零件刀杆风动工具等铝活塞水暖器材水轮机叶片一般有色合金铸件汽车化油器喇叭电器仪表照相机零件发动机缸体缸盖壳体箱体船用螺旋桨纺织机零件各种铁管套筒环辊叶轮滑动轴承等第五节铸件结构工艺性铸件结构工艺性通常是指铸件的本身结构应符合铸造生产的要求既便于整个工艺过程的进行又利于保证产品质量
机械制造基础3.4液态成型

切 削 运手动工 造 型 方 法
手工造型方法
根据模样特征分为: 整模造型; 分模造型; 挖砂造型; 活块造型; 刮板造型; 假箱造型;
切 削 运手动工 造 型 方 法
手工造型方法
根据模样特征分为: 整模造型; 分模造型; 挖砂造型; 活块造型; 刮板造型; 假箱造型;
特点:为克服挖砂造型的缺点,在造型前预先做底胎(假箱),操作简单, 效率高,质量好。 适用范围:需要挖砂铸件的批量生产。
零件图
铸造工艺图
模样图、芯盒图、装配图
配制的型砂
模样 芯盒
砂型 砂芯
熔化的合金
合箱
浇注冷却ຫໍສະໝຸດ 配制的芯砂砂型铸造基本工艺过程
落砂清理 检验
合格的铸件
切 削 运手动工 造 型 方 法
手工造型
手工造型是利用人工的方法将造型材 料及模样等工具制造铸型的过程。
优点:灵活、适用范围广。 缺点:技术水平要求高、劳动强度大、 易产生缺陷、生产率低。
切 削 运手动工 造 型 方 法
手工造型方法
根据模样特征分为: 整模造型; 分模造型; 挖砂造型; 活块造型; 刮板造型; 假箱造型;
特点:模样上侧壁有妨碍起模的凸台,做成活块,依次起出,造型费时, 技术要求高。 适用范围:铸件有突出部分的单件小批生产。
切 削 运手动工 造 型 方 法
有缘学习更多+谓ygd3076考证资料或关注桃报:奉献教育(店铺)
切 削 运手动工 造 型 方 法
手工造型方法
根据模样特征分为: 整模造型; 分模造型; 挖砂造型; 活块造型; 刮板造型; 假箱造型;
切 削 运手动工 造 型 方 法
手工造型方法
根据模样特征分为: 整模造型; 分模造型; 挖砂造型; 活块造型; 刮板造型; 假箱造型;
- 1、下载文档前请自行甄别文档内容的完整性,平台不提供额外的编辑、内容补充、找答案等附加服务。
- 2、"仅部分预览"的文档,不可在线预览部分如存在完整性等问题,可反馈申请退款(可完整预览的文档不适用该条件!)。
- 3、如文档侵犯您的权益,请联系客服反馈,我们会尽快为您处理(人工客服工作时间:9:00-18:30)。
二、从简化铸造工艺过程方面 进行零件结构的工艺性分析
1.铸件结构应便于起模、简化工艺、节省造型和制模 工时
铸件侧壁上的凸台、突缘、筋条等,常常妨碍起模。 而为了这些小的凸台、突缘、筋条等,在大量生产中 不得不增加砂芯。在单件、小批生产中,必须将它们 制成活动模块(活块)。这些活动模块都大大增加造 型、制芯和模具制造的工时,提高了生产成本。
8. 铸件结构应能防止热裂和变形
铸造方 法与铸 件结构 铸件 形状
铸件 大小
铸件 壁厚
铸件最 小壁厚 (mm)
砂型 铸造
可以很 复杂
不限制
不限制
铝合金>3 铸铁>3 铸钢>6
金属型 铸造
不宜太 复杂
中小件 <100kg
不宜壁厚 差太大
铝合金23,灰铸 铁4,铸
钢>5
拔模 斜度 最小铸 出孔槽
镶嵌件
5. 保证砂芯定位稳固, 排气通畅和下芯、检验方便
吊砂在合箱、浇注时易塌箱,特别是向上半型吊芯 操作不方便;悬臂式砂芯不稳固,在金属液浮力作 用下易发生偏移,应尽量避免使用。
5. 保证砂芯定位稳固, 排气通畅和下芯、检验方便
砂芯不宜过高,以免造成合箱困难。砂芯在上箱时检 验也很困难,对罩形件的排气问题也需注意,可采用 分两阶段进行浇注,或采用盖芯或卧浇。
3. 结构圆角的设计
当铸件壁采用圆角结构时,可以消除应力集中,破坏了柱状 晶的分界面,明显提高转角处的力学性能,也防止了缩孔、缩 松和裂纹的产生。
圆角结构还有利于造型,浇注时可避免熔融金属对铸型的冲 刷,减少砂眼和粘砂缺陷的发生。
3. 结构圆角的设计
不合理
合理
不合理
合理
3. 结构圆角的设计
4. 内壁厚度应小于外壁
6-2 浇注位置的确定原则-总结
1.铸件的重要加工面应朝下或呈侧立面; 2.铸件的大平面朝下,或采用倾斜浇注; 3.应保证铸件能充满; 4.有利于实现顺序凝固; 5.保证砂芯定位稳固、排气通畅和下芯、检验方便; 6.应使合箱位置、浇注位置和冷却位置相一致。
铸件内部的筋和壁,散热条件较差。因此,铸件的结构设计 应使内壁比外壁薄一些,以便使整个铸件能均匀地冷却,防 止产生内应力和裂纹。
一般地,当铸件外壁、铸件内壁和筋的厚度按1:0.8:0.6设 计时,可以保证各部位冷却速度均匀一致。
ቤተ መጻሕፍቲ ባይዱ
4. 内壁厚度应小于外壁
内、外壁厚相差值约为10%-30%是合理的。
5. 壁厚应力求均匀
6. 避免水平大平面
7. 有利于顺序凝固
有的铸件因工作需要,结构设计上造成壁厚不均匀和局部厚 度较大,而且合金的体收缩又比较大,这时很容易形成缩孔和 缩松缺陷。因此,应仔细审查零件结构实现顺序凝固的可能性, 使之便于安放冒口、冷铁,以避免出现缩孔、缩松缺陷。
8. 铸件结构应能防止热裂和变形
经验表明,某些壁厚均匀的细长铸件、较大面积的 平板铸件,及某些壁厚不均匀的长形箱体类铸件,如 床身类铸件,都会产生翘曲变形。
对于砂芯芯头不足、难以固定砂芯的铸件,为使砂芯稳固, 可适当采取开设工艺孔的方法解决。如图所示的铸件,因底面 没有芯头,只好加芯撑。当改成右图所示的结构后,不仅省去 芯撑,也便于排气和清理。
这些工艺孔可用螺钉或柱塞堵住。
6. 复杂铸件分体铸造,简单小件联合铸造
有些大而复杂的铸件,可考虑分成两个以上的简单铸件, 铸造后再用螺栓或焊接的方法连接起来,以简化铸造过程, 也可使本来没有条件生产的大型铸件的生产成为可能。
前两者产生翘曲变形的主要原因是:铸件结构刚度 差,铸件各面冷却条件的差别所引起的不大的内应力 使其变形。
后者主要是壁厚差别大,厚壁处冷却慢,薄壁处冷 却快,引起较大的内应力促使铸件产生变形。
铸件变形可以采用改进铸件结构、设置加强筋提高 刚性、人工时效、采用反变形等方法予以解决。
8. 铸件结构应能防止热裂和变形
2. 减少、简化分型面,尽量采用平直分型面
3. 减少砂芯数量,尽量不用或少用砂芯
有砂芯的铸件不仅增加成本,而且使造型、造芯 和合箱工艺复杂化,影响生产率和铸件质量。
3. 减少砂芯数量,尽量不用和少用砂芯
4. 取消不必要的圆角
虽然铸件的转角处几乎都希望用圆角相连接,这 是由铸件的结晶和凝固的合理性所决定的。但是有些 外圆角对铸件的质量影响并不大,但却对造型、制芯 等工艺过程有不良效果,此时,应将圆角取消。
2.应减少、简化分型面,尽量采用平直分型面; 3.减少砂芯数量,尽量不用和少用砂芯; 4.取消不必要的圆角; 5.有利于砂芯的固定和排气; 6.复杂铸件采用分体铸造,简单小件采用联合铸造。
6-2 浇注位置的确定
浇注位置:浇注时铸件在型内所处的位置(即哪个面朝上的 问题)。
浇注位置应依据铸件的质量要求、大小、结构特点、合 金性能、生产批量、现场条件及综合效益等方面评估,很大 程度上着眼于顺序凝固。
材料成型工艺学
材料科学与工程学院 张兴国
大连理工大学
Dalian University of Technology
第六章 铸型工艺方案的确定
6-1 零件结构的铸造工艺性分析 铸造工艺性:
零件的本身结构应符合铸造生产的要求,既便于整个铸造工 艺过程的顺利进行,又利于保证产品的质量。 作用:
1.审查零件结构是否符合铸造生产的工艺要求; 2.在既定的零件结构条件下,考虑在铸造过程中可能出现的 主要缺陷,在工艺设计中应采取的工艺措施。 一、从避免缺陷方面审查零件结构的合理性 1.铸件应有合理的壁厚 最小壁厚:一定条件下铸造合金能充满铸型的最小壁厚。 铸件的设计壁厚应不小于最小壁厚 。
5. 有利于砂芯的固定和排气
如轴承架铸件,其内腔采用两个砂芯,其中较大的砂芯采用 悬臂芯,不稳定,必须用芯撑加固。
若改成使用整体芯的工艺,既将两个砂芯做成一个砂芯,既 不影响零件的使用,而且砂芯的稳定性大为提高,下芯也很方 便,排气也通畅。注意:尽量少用或避免使用芯撑。
5. 有利于砂芯的固定和排气
铜合金1015’-2015
0.7
可以,降 低生产率 可以,成
本高
离心 铸造
限中空 回转体 不限制 由浇注 量控制
比同类 重力铸
造薄
7 可以 不可以
挤压 铸造
不宜太 复杂 中小件
较适合于 厚壁铸件
2-5
比压铸 和金属 型大
较难
可以, 较困难
一、从避免缺陷方面审查零件结构的合理性
应考虑的原则: 1.铸件应有合理的壁厚; 2.铸件壁的连接应逐渐过渡; 3.结构圆角的设计; 4.内壁厚度应小于外壁; 5. 壁厚应力求均匀; 6. 避免水平大平面; 7. 有利于顺序凝固; 8. 铸件结构应能防止热裂和变形。
6.复杂铸件分体铸造,简单小件联合铸造
与分体铸造相反,一些很小的零件,如轴套,压环、密封环 等,可把许多小件连在一起,铸成一个较长的铸件再机械加工, 或将多个小件采用叠箱造型的方法生产。
二、从简化铸造工艺过程方面进行零件结 构的工艺性分析-总结
1.铸件结构应便于起模、简化工艺、节省造型和制模 工时;
铸件各部位壁厚如果相差太大,厚壁处会产生金属局部积聚 形成热节,凝固收缩时在热节处形成缩孔、缩松缺陷。此外, 各部位冷却不均匀,易形成热应力,致使铸件在薄壁和厚壁连 接处产生裂纹。因此,在进行铸件结构设计时应做到壁厚力求 均匀。
5. 壁厚应力求均匀
6. 避免水平大平面
如果铸件有大的水平空腔存在,当液体金属上升到该位置 时,由于断面突然扩大,上升速度缓慢,高温金属液较长 时间烘烤顶部型面,极易造成夹砂、浇不足等缺陷,同时 也不利于金属夹杂物和气体的排除。因此,应尽量设计成 倾斜壁。
6. 应使合箱位置、浇注位置和冷却位置相一致
这样可避免合箱后或浇注后再次翻转铸型。翻转铸型不仅 劳动量大,而且容易引起砂芯移动、掉砂等缺陷。
只是在个别情况下,为了造型方便和增加冒口的补缩效果 等原因,要求合箱或浇注后改变冷却位置。例如:曲轴横浇 竖冷,大平板水平合箱,倾斜浇注。
但是对大批量生产,曲轴件仍然要卧浇卧冷。
凸台、 侧凹
最小15’
灰铸铁 ≥30 铸钢≥60
可以, 费用少 可以, 费用少
一般10
6-8 可以 可以
熔模 铸造
可较 复杂 中小件 <25kg 不限制
0.5
0.5 不可以 可以, 较困难
压力 铸造
不宜太 复杂
中小件
不宜壁厚 差太大
铝合金0.5 锌合金0.4 铜合金0.8
铝合金15’
锌合金< 15’
如果从简化铸造工艺过程的角度对其结构稍加改进, 即可避免这些缺点。
1. 铸件结构应便于起模、简化工艺、 节省造型和制模工时
尽量取消铸件外壁的侧凹
2. 应减少、简化分型面,尽量采用平直分型面
分型面最好只有一个,并且最好是简单的平面。这样只需 要两箱造型,减少了造型和模具制造工时,提高铸件精度, 并易于实现机械化生产。平直的分型面可以减少铸件的毛边、 便于清理。
1. 铸件的重要加工面应朝下或呈侧立面
有几个加工面时,应该将主要的或较大的加工面朝下或侧 立,受力的部位放在下部,个别加工面朝上时要适当加大加工 余量。理由是: 浇注位置的下部:冷却快,有静压力作用和上部金属的补缩而 致密,几乎无夹杂和气孔; 浇注位置的上部:因渣、气上浮,故易产生气孔、夹砂、砂眼、 气隔等缺陷。
一、从避免缺陷方面审查零件结构的合理性
临界壁厚:当铸件的壁厚超过临界壁厚时,铸件的力学性能 并不按比例随铸件厚度的增加而增加,反而是显著地下降。
因此,设计铸件壁需要注意的问题是: 1)为防止出现冷隔和浇不足缺陷,铸件应有一定的壁厚; 2)外形尺寸大、结构复杂、合金流动性差的铸件,铸件壁厚 应适当加大; 3)厚壁会增加铸件的重量和金属的消耗,而且易产生缩孔、 缩松等缺陷。另外,厚壁铸件凝固慢,会造成晶粒粗大、力 学性能降低。最好的方法是采用加强筋; 4)对灰铸铁件,最小壁厚的选择应防止出现白口(考虑浇注 条件和孕育条件)。