材料特种制备新技术
特种陶瓷涂层的制备

特种陶瓷及涂层制备与加工中的新原理与新工艺摘要:特种陶瓷及其涂层以其良好的抗腐蚀和抗摩擦性能,受到人们的广泛关注。
尤其是陶瓷涂层的应用,大大提高了材料的抗腐蚀抗磨损能力。
近些年来,陶瓷涂层的制备加工新技术和新工艺层出不穷,本文将就介绍陶瓷涂层的制备方法,制备工艺及其原理予以简要介绍。
关键词:陶瓷涂层;原理;工艺众所周知,陶瓷材料具有良好的耐腐蚀和耐磨损性能,可以较好的弥补金属材料在这一方面的缺点,但是陶瓷材料具有本征的脆性,韧性较差。
金属表面喷涂陶瓷涂层可以很好的解决这一问题,充分利用了陶瓷的抗腐蚀和抗磨损能力和金属的良好韧性。
一、热喷涂技术热喷涂技术是在1908年由瑞士的肖普(schoop)博士发明(首创)并用雾化装置进行喷涂试验的。
在1913年制作出世界首台丝材喷枪,并在其后逐渐完善和得到应用。
1920年,日本人去瑞士考察后,发明了以交流电为热源的电弧热喷涂装置,但因交流电不稳定,效率低,涂层质量差等原因,这种交流电弧热喷涂技术及装置未能得到实际的推广和应用。
后来德国改用直流电源后,电弧喷涂才有了真正的实用价值。
1938年,美国研制成功了电弧丝材喷枪,其后又研制出粉末氧-乙炔火焰喷枪。
1953年,当时的西德研制出自熔性合金粉,这是喷涂材料发展的一次重大突破(是粉末喷涂材料从单一金属向合金材料发展,从低熔点材料向高熔点材料发展,从低耐磨性向高耐磨性发展的里程碑)。
上世纪50年代后期,美国又相继研制出爆炸喷涂和等离子喷涂,满足了当时航空、导弹等尖端技术对涂层性能的需要。
上世纪60~70年代,是喷涂材料发展十分活跃的时期,美国、加拿大、瑞士、西德、比利时等国分别研制生产出系列的复合粉、多种自熔合金粉、陶瓷粉、金属陶瓷粉和自粘结复合粉等,这其中包括以Ni-AL为基础的放热型复合粉,这些材料的出现以及材料生产技术的不断完善,使得喷涂材料更加齐备和商品化,满足了当时,直到今天人们在这方面的需求。
我国的热喷涂技术及工程应用早在上世纪50年代初就开始了丝的电弧热喷涂(据资料报道,就在江浙一带的高压输电钢结构塔上喷涂Zn涂层防腐,至今仍在起着防腐蚀的作用)。
材料加工新技术与新工艺(详细版)
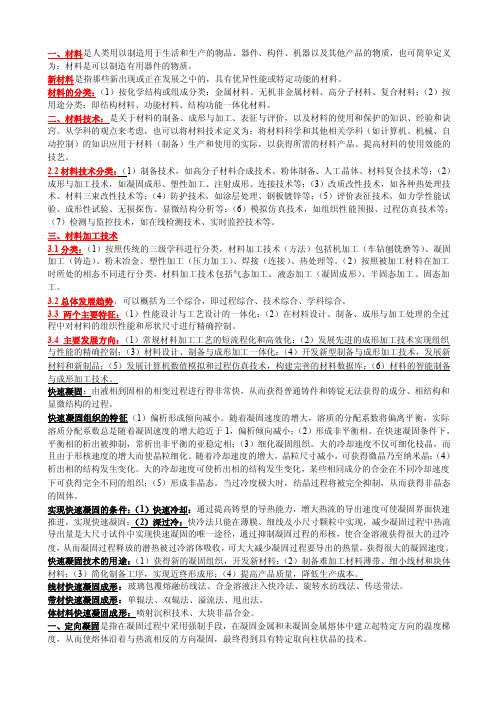
一、材料是人类用以制造用于生活和生产的物品、器件、构件、机器以及其他产品的物质,也可简单定义为:材料是可以制造有用器件的物质。
新材料是指那些新出现或正在发展之中的,具有优异性能或特定功能的材料。
材料的分类:(1)按化学结构或组成分类:金属材料、无机非金属材料、高分子材料、复合材料;(2)按用途分类:即结构材料、功能材料、结构功能一体化材料。
二、材料技术:是关于材料的制备、成形与加工、表征与评价,以及材料的使用和保护的知识、经验和诀窍。
从学科的观点来考虑,也可以将材料技术定义为:将材料科学和其他相关学科(如计算机、机械、自动控制)的知识应用于材料(制备)生产和使用的实际,以获得所需的材料产品、提高材料的使用效能的技艺。
2.2材料技术分类:(1)制备技术,如高分子材料合成技术、粉体制备、人工晶体、材料复合技术等;(2)成形与加工技术,如凝固成形、塑性加工、注射成形、连接技术等;(3)改质改性技术,如各种热处理技术、材料三束改性技术等;(4)防护技术,如涂层处理、钢板镀锌等;(5)评价表征技术,如力学性能试验、成形性试验、无损探伤、显微结构分析等;(6)模拟仿真技术,如组织性能预报、过程仿真技术等;(7)检测与监控技术,如在线检测技术、实时监控技术等。
三、材料加工技术3.1分类:(1)按照传统的三级学科进行分类,材料加工技术(方法)包括机加工(车钻刨铣磨等)、凝固加工(铸造)、粉末冶金、塑性加工(压力加工)、焊接(连接)、热处理等。
(2)按照被加工材料在加工时所处的相态不同进行分类,材料加工技术包括气态加工、液态加工(凝固成形)、半固态加工、固态加工。
3.2总体发展趋势,可以概括为三个综合,即过程综合、技术综合、学科综合。
3.3两个主要特征:(1)性能设计与工艺设计的一体化;(2)在材料设计、制备、成形与加工处理的全过程中对材料的组织性能和形状尺寸进行精确控制。
3.4主要发展方向:(1)常规材料加工工艺的短流程化和高效化;(2)发展先进的成形加工技术实现组织与性能的精确控制;(3)材料设计、制备与成形加工一体化;(4)开发新型制备与成形加工技术,发展新材料和新制品;(5)发展计算机数值模拟和过程仿真技术,构建完善的材料数据库;(6)材料的智能制备与成形加工技术。
特种材料冶炼技术装备优化与创新

管理及其他M anagement and other 特种材料冶炼技术装备优化与创新张永涛摘要:特材公司特种材料冶炼主体工艺设备包括4台1.5T、3T、6T、10T恒熔速保护气氛电渣炉,VIM500、VIM1500两座真空感应炉,一座2T真空电弧自耗炉以及加热炉和热处理设备。
在过去一年的的设备运行过程中,这些设备陆续出现了一些故障或不适应的问题,通过对这些关键设备的关键部位进行系统性的分析、调整、优化,提出了技术创新方案并付诸实施,效果显著,不仅完善设备性能,同时极大提高了生产作业率。
并为进一步提升产线产量、降低设备故障率、提高产品质量打下基础。
关键词:技术创新;设备改进;降低故障率随着科技的不断进步和工业的快速发展,特种材料的需求日益增长。
特种材料在航空航天、能源、汽车、电子等领域具有重要的应用价值,因此,特种材料冶炼技术装备的优化与创新成为了迫切的需求。
本文将探讨特种材料冶炼技术装备的优化与创新方向,以期实现冶炼过程的高效、环保和可持续发展。
特材公司特种材料冶炼主体工艺设备包括4台1.5T、3T、6T、10T恒熔速保护气氛电渣炉,VIM500、VIM1500两座真空感应炉,一座2T真空电弧自耗炉以及加热炉和热处理设备。
在过去一年的的设备运行过程中,这些设备陆续出现了一些故障或不适应的问题,主要包括电渣炉4台加渣小车不能互为备用的问题;真空炉上加料室隔离阀开闭刮蹭密封圈的问题;真空炉罗茨泵吸入杂物导致叶片卡阻的问题,真空自耗炉炉头升降卡阻的问题。
这些问题在投产初期对设备稳定运行产生了较大影响,通过对这些关键设备的关键部位进行系统性的分析、调整、优化,提出了技术创新方案并付诸实施,效果显著,不仅完善设备性能,同时极大提高了生产作业率。
并为进一步提升产线产量、降低设备故障率、提高产品质量打下基础。
1 技术现状及原因分析 绿色冶炼技术是特种材料冶炼技术装备优化与创新的重要方向之一。
随着全球环境问题的日益严重,传统的高温冶炼工艺不仅能耗高,还会产生大量的二氧化碳排放。
(完整版)材料先进加工技术

(完整版)材料先进加工技术1. 快速凝固快速凝固技术的发展,把液态成型加工推进到远离平衡的状态,极大地推动了非晶、细晶、微晶等非平衡新材料的发展。
传统的快速凝固追求高的冷却速度而限于低维材料的制备,非晶丝材、箔材的制备。
近年来快速凝固技术主要在两个方面得到发展:①利用喷射成型、超高压、深过冷,结合适当的成分设计,发展体材料直接成型的快速凝固技术;②在近快速凝固条件下,制备具有特殊取向和组织结构的新材料。
目前快速凝固技术被广泛地用于非晶或超细组织的线材、带材和体材料的制备与成型。
2. 半固态成型半固态成型是利用凝固组织控制的技术.20世纪70年代初期,美国麻省理工学院的Flemings 教授等首先提出了半固态加工技术,打破了传统的枝晶凝固式,开辟了强制均匀凝固的先河。
半固态成型包括半固态流变成型和半固态触变成形两类:前者是将制备的半固态浆料直接成型,如压铸成型(称为半固态流变压铸);后者是对制备好的半固态坯料进行重新加热,使其达到半熔融状态,然后进行成型,如挤压成型(称为半固态触变挤压)3. 无模成型为了解决复杂形状或深壳件产品冲压、拉深成型设备规模大、模具成本高、生产工艺复杂、灵活度低等缺点,满足社会发展对产品多样性(多品种、小规模)的需求,20世纪80年代以来,柔性加工技术的开发受到工业发达国家的重视。
典型的无模成型技术有增量成型、无摸拉拔、无模多点成型、激光冲击成型等。
4.超塑性成型技术超塑性成型加工技术具有成型压力低、产品尺寸与形状精度高等特点,近年来发展方向主要包括两个方面:一是大型结构件、复杂结构件、精密薄壁件的超塑性成型,如铝合金汽车覆盖件、大型球罐结构、飞机舱门,与盥洗盆等;二是难加工材料的精确成形加工,如钛合金、镁合金、高温合金结构件的成形加工等。
5. 金属粉末材料成型加工粉末材料的成型加工是一种典型的近终形、短流程制备加工技术,可以实现材料设计、制备预成型一体化;可自由组装材料结构从而精确调控材料性能;既可用于制备陶瓷、金属材料,也可制备各种复合材料。
八大特种加工技术

非常工艺:八大特种加工技术特种加工亦称“非传统加工”或“现代加工方法”,泛指用电能、热能、光能、电化学能、化学能、声能及特殊机械能等能量达到去除或增加材料的加工方法,从而实现材料被去除、变形、改变性能或被镀覆等。
一、特种加工的发展和定义传统的机械加工已有很久的历史,它对人类的生产和物质文明起了极大的作用。
目前我们的大部分产品还是依靠传统的方法加工和装配得到的,如我们的家用电器:电冰箱、洗衣机、空调等;我们的交通工具:如汽车、火车、飞机等,以及各种武器装备:枪、炮、坦克、火箭等。
传统的机械加工方法是用机械能量和切削力切除多余的金属,使零件具有一定的几何形状、尺寸和表面粗糙度。
它要求刀具材料比工件材料硬。
随着科学技术的发展,特别是上个世纪50年代以来,随着生产发展和科学实验的需要,很多工业部门,尤其是国防工业部门的要求尖端科学技术产品向高精度、高速度、高温、高压、大功率、小型化等方向发展,它们使用的材料越来越难加工,零件的形状越来越复杂,尺寸精度、表面粗糙度和某些特殊要求也越来越高,因而对机械制造部门提出一些新的要求:•解决各种难切削材料的加工问题。
如硬质合金、钛合金、耐热钢、不锈钢、淬火钢、金刚石、宝玉石、石英以及锗、硅等各种高硬度、高强度、高韧性、高脆性的金属及非金属材料的加工。
•解决各种特殊复杂表面的加工问题。
如喷汽涡轮机叶片、整体涡轮、发动机机匣、锻压模和注射模的立体成型表面,各种冲模、冷拔模上特殊断面的型孔,炮管内膛线,喷油咀、栅网、喷丝头上的小孔、窄缝等的加工。
•解决各种超精、光整或具有特殊要求的零件的加工问题。
如对表面质量和精度要求很高的航天、航空陀螺仪、伺服阀,以及细长轴、薄壁零件、弹性元件等低刚度零件的加工。
要解决上述一系列工艺问题,仅仅依靠传统的切削加工方法就很难实现,甚至根本无法实现。
人们相继探索研究新的加工方法,特种加工就是在这种前提条件下产生和发展起来的。
特种加工,国外称作非传统加工(Non - Traditional Machining, NTM)或非常规加工(Non –ConventionalMachining,NCM),是一种采用不同于传统切削磨削加工工艺及装备的加工技术,是将电、磁、声、光、热等物理能量及化学能量或其组合乃至与机械能组合直接施加在被加工的部位上,从而使材料被去除、变形及改变性能等。
特种设备采用新材料新技术新工艺处罚

特种设备采用新材料新技术新工艺处罚特种设备在各行各业中扮演着至关重要的角色,它们的安全性和性能直接关系到生产工作的顺利进行和人员的生命安全。
为了提高特种设备的质量和效率,采用新材料、新技术和新工艺已成为一种必然趋势。
新材料的应用对特种设备的性能提升起着至关重要的作用。
随着科技的不断发展,各种新型材料不断涌现,如碳纤维、陶瓷材料、高强度合金等。
这些新材料具有重量轻、耐磨损、耐腐蚀等优点,能够大幅提高特种设备的使用寿命和安全性。
例如,采用碳纤维制造的压力容器,不仅具有更好的强度和刚度,还可以减轻设备的重量,降低能耗,提升生产效率。
新技术的运用也对特种设备的性能提升具有重要意义。
随着信息技术、智能化技术的不断发展,特种设备的控制系统、监测系统也得到了极大的改善。
智能化的控制系统可以实现设备的自动化操作,提高生产效率的同时减少人为操作失误的可能性。
监测系统可以实时监测设备的工作状态,及时发现问题并进行维护,有效预防设备故障的发生,保障生产安全。
新工艺的应用也是提升特种设备性能的重要手段。
传统的生产工艺可能存在着效率低、能耗高、质量不稳定等问题,而采用新工艺可以改善这些情况。
例如,采用先进的加工工艺可以提高设备零部件的加工精度和表面质量,提升设备的整体性能。
同时,优化生产工艺还可以减少废料产生,提高资源利用率,实现绿色生产。
以特种设备采用新材料、新技术、新工艺处罚可以有效提升特种设备的性能和安全性,推动特种设备行业的发展。
特种设备制造企业应不断引进新技术、新材料,优化工艺流程,提高生产效率和产品质量,为各个行业提供更加安全、可靠的特种设备产品。
同时,政府部门应加大对特种设备行业的监管力度,推动企业创新发展,促进特种设备行业朝着更加智能化、高效化、环保化的方向发展。
只有不断追求创新,才能在激烈的市场竞争中立于不败之地,实现可持续发展的目标。
特种加工方法及各自的应用
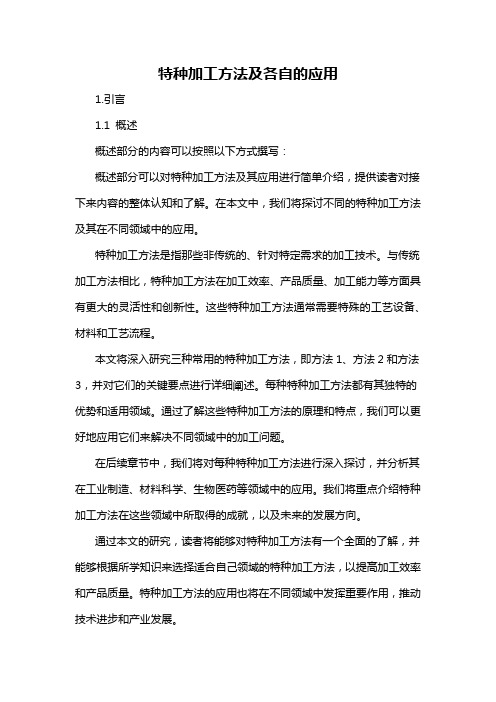
特种加工方法及各自的应用1.引言1.1 概述概述部分的内容可以按照以下方式撰写:概述部分可以对特种加工方法及其应用进行简单介绍,提供读者对接下来内容的整体认知和了解。
在本文中,我们将探讨不同的特种加工方法及其在不同领域中的应用。
特种加工方法是指那些非传统的、针对特定需求的加工技术。
与传统加工方法相比,特种加工方法在加工效率、产品质量、加工能力等方面具有更大的灵活性和创新性。
这些特种加工方法通常需要特殊的工艺设备、材料和工艺流程。
本文将深入研究三种常用的特种加工方法,即方法1、方法2和方法3,并对它们的关键要点进行详细阐述。
每种特种加工方法都有其独特的优势和适用领域。
通过了解这些特种加工方法的原理和特点,我们可以更好地应用它们来解决不同领域中的加工问题。
在后续章节中,我们将对每种特种加工方法进行深入探讨,并分析其在工业制造、材料科学、生物医药等领域中的应用。
我们将重点介绍特种加工方法在这些领域中所取得的成就,以及未来的发展方向。
通过本文的研究,读者将能够对特种加工方法有一个全面的了解,并能够根据所学知识来选择适合自己领域的特种加工方法,以提高加工效率和产品质量。
特种加工方法的应用也将在不同领域中发挥重要作用,推动技术进步和产业发展。
参考以上内容,你可以根据自己的理解和需要进行适当调整和修改。
1.2文章结构1.2 文章结构本文主要探讨了特种加工方法及其各自的应用。
文章结构如下:2. 正文2.1 特种加工方法12.1.1 要点12.1.2 要点22.2 特种加工方法22.2.1 要点12.2.2 要点22.3 特种加工方法32.3.1 要点12.3.2 要点23. 结论3.1 总结3.2 应用展望在正文部分,我们将详细介绍三种特种加工方法及其各自的要点。
每种特种加工方法都将包含详细的解释和应用示例,以便读者更好地理解和应用这些方法。
在结论部分,将总结本文的主要观点和论点,并展望特种加工方法在未来的应用前景。
高性能特种粉体材料近终形制造技术与应用

高性能特种粉体材料近终形制造技术及应用提名单位:中国有色金属工业协会提名奖种:国家技术发明奖提名单位意见:高性能特种材料在高技术领域中具有不可取代的关键作用。
但是,由于硬度高、脆性大等问题,难以采用传统加工技术制备成复杂形状制品,极大限制了其性能的发挥和有效利用,因此亟需研发特种材料复杂零件的近终形制造技术。
项目突破了近球形微细粉末原料制备、精密成形、组织性能精确调控、关键工艺装备和自动化生产质量监测等关键技术。
首创了近球形微细特种粉体制备和改性新技术,实现特种粉末原料的自主化;发明了多种粘结剂体系及成形和高效脱脂工艺,解决了坯体两相分离、变形、增氧、缺陷等控制难题;发明了强化烧结致密化和组织性能精确调控技术,实现高性能近终形制造;发明和开发了微注射成形模具、侧抽芯模具新结构、专用注射成形机、高效脱脂炉和节能烧结炉等关键工艺装备,建立了基于机器视觉的产品尺寸、外观质量在线自动检测,工业机器人动态抓取和分拣软硬件系统,实现自动化生产。
授权中国发明专利59项、实用新型专利65项,申请PCT 专利2项,软件著作权6项,出版著作2部,发表SCI论文108篇,多种产品打破国外技术封锁,解决了多项国防装备建设和研发的“卡脖子”问题,满足了国家重大需求。
建成世界排名靠前的注射成形企业,引领和推动了我国粉末注射成形产业的形成和发展,建成47条生产线,近三年新增销售52.96亿元,新增利润6.32亿元。
获教育部技术发明一等奖2项,中国有色金属工业科学技术发明一等奖1项。
项目简介该项目属于材料合成与加工工艺学科。
高性能特种材料具有其他材料不具备的特殊性能,在高技术领域中具有不可取代的关键作用。
然而,这类材料往往硬度高、脆性大,难以采用传统加工技术制备成复杂形状制品,极大限制了其性能的发挥和有效利用,因此亟需研发特种材料复杂零件的近终形制造技术。
项目针对国防装备、汽车、智能电子产品等领域的需要,研究高性能金属钨、氮化铝等特种材料粉末注射成形系统理论和方法,突破近球形微细粉末原料制备、精密成形、组织性能精确调控、关键工艺装备和质量监测软硬件系统等关键技术,实现小型复杂形状制品的近终形制造,并推广应用于其他材料体系。
简述特种加工技术的特点及应用领域。
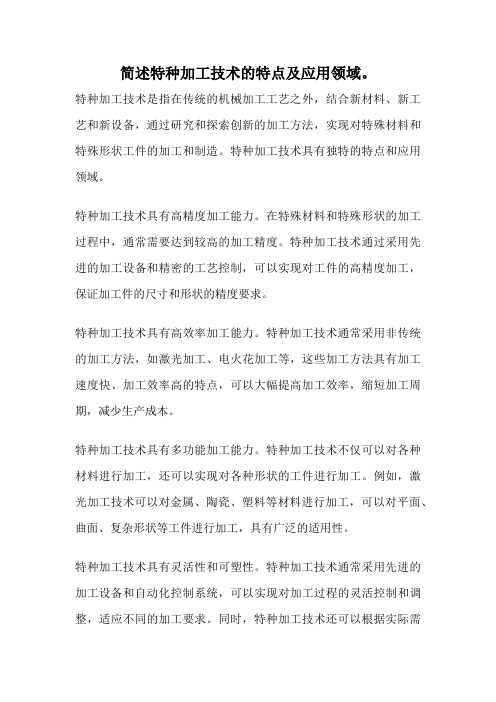
简述特种加工技术的特点及应用领域。
特种加工技术是指在传统的机械加工工艺之外,结合新材料、新工艺和新设备,通过研究和探索创新的加工方法,实现对特殊材料和特殊形状工件的加工和制造。
特种加工技术具有独特的特点和应用领域。
特种加工技术具有高精度加工能力。
在特殊材料和特殊形状的加工过程中,通常需要达到较高的加工精度。
特种加工技术通过采用先进的加工设备和精密的工艺控制,可以实现对工件的高精度加工,保证加工件的尺寸和形状的精度要求。
特种加工技术具有高效率加工能力。
特种加工技术通常采用非传统的加工方法,如激光加工、电火花加工等,这些加工方法具有加工速度快、加工效率高的特点,可以大幅提高加工效率,缩短加工周期,减少生产成本。
特种加工技术具有多功能加工能力。
特种加工技术不仅可以对各种材料进行加工,还可以实现对各种形状的工件进行加工。
例如,激光加工技术可以对金属、陶瓷、塑料等材料进行加工,可以对平面、曲面、复杂形状等工件进行加工,具有广泛的适用性。
特种加工技术具有灵活性和可塑性。
特种加工技术通常采用先进的加工设备和自动化控制系统,可以实现对加工过程的灵活控制和调整,适应不同的加工要求。
同时,特种加工技术还可以根据实际需要进行改进和创新,不断推出新的加工方法和工艺,满足不同行业和领域的加工需求。
特种加工技术的应用领域非常广泛。
首先,特种加工技术在航空航天领域有广泛的应用。
航空航天领域对材料的性能和加工精度要求非常高,特种加工技术可以对航空航天材料进行高精度、高效率的加工,满足航空航天工业的需求。
特种加工技术在电子信息领域也有重要的应用。
随着电子产品的不断发展和更新换代,对电子元器件的加工要求也越来越高。
特种加工技术可以实现对微小、复杂的电子元器件的加工,提高元器件的精度和可靠性。
特种加工技术在生物医学领域也具有重要的应用价值。
生物医学领域对材料的生物相容性和加工精度要求较高,特种加工技术可以实现对生物材料和生物器件的加工,满足医学领域的需求,推动医学科学的发展。
特种铸造及铸造新技术
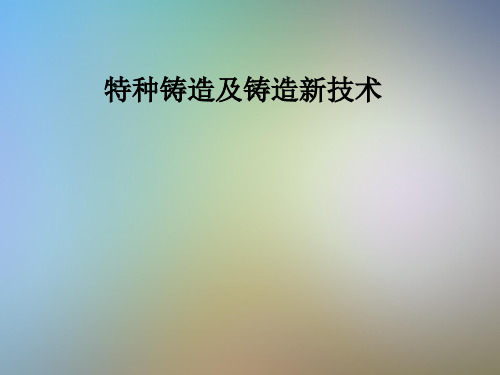
46
离心铸造机
• 立式离心铸造
铸型绕垂直轴旋转。铸件内表面呈抛物线形。用来 铸造高度小于直径的盘、环类或成形铸件。
▪卧式离心铸造
我国的熔模铸造是在50年代开始应用于工业生 产,首先在航天、航空部门逐步发展到所有的工业 部门中,得到广泛的应用。
凸轮圆环铜铸件
汽车传动轴万向节、凸缘叉、套管叉系列
机箱体和曲轴
2、熔模铸造的工艺过程
(1)制作压型
压型是用来压制模样(即熔模)的模具,一般用钢 、青铜或铝合金经切削加工制成。
(2)制作熔模
❖ 生产率高(一般冷压式压铸机平均每小时压铸 600-700次)
❖缺点
❖ 投资大,生产周期长 ❖ 压铸合金的种类受限制,压铸高熔点合金(
铸铁、铸钢)时,压型寿命低 ❖ 铸件内部常有气孔和缩松,不能进行较多余
量的切削加工 ❖压铸件不能用热处理的方法提高性能
❖适用范围
❖主要用于有色合金(如铝合金、锌合金)的中 、小铸件的大量生产。
寿命 低
全自动卧式冷室压铸机
冷压室卧式压铸机的工作过程(目前应用最多)
2、压力铸造的工艺过程
• (1)预热金属铸型,喷涂料 • (2)合型、注入金属液 • (3)压射冲头在高压下推动金属液充满型腔并凝固 • (4)打开铸型,用顶杆顶出铸件
合型并注入液态金属
压射 压力铸造过程
开型并顶出铸件
3、压力铸造的特点和适用范围
特种铸造及铸造新技术
特种铸造
特种铸造
概述
同砂铸相比:铸件精度高,表面质量好;合 金性能改善,劳动生产率高;劳动条件大大改善 ;成本高。
1-3特种铸造及铸造新技术
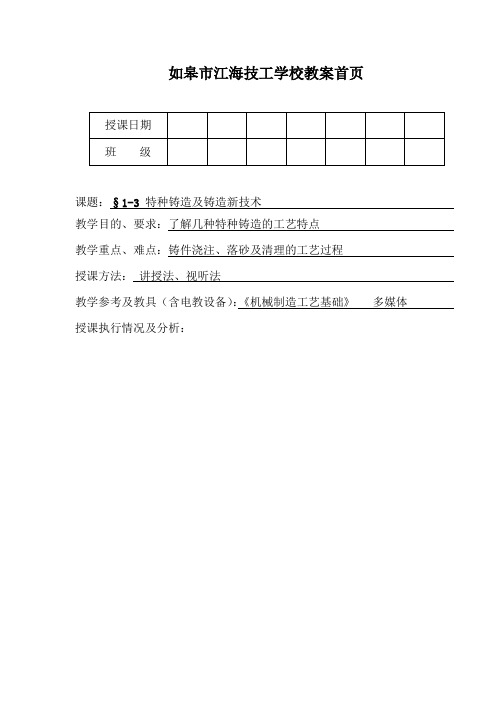
2分
8分
5分
20分
10分
10分
10分
10分
5分
组织教学
点名考勤、稳定学生情绪、宣布上课。
复习旧课
1.型芯怎么制造?
2.怎样设置浇注系统和冒口?
导入新课
金属液浇入铸型时所测量到的温度称为浇注温度,是铸造过程必须控制的质量指标之一。温度↑→充型能力↑,温度不足,易产生浇不族和冷隔的缺陷,温度过高,易产生缩松、缩孔、粗晶、气孔等缺陷。灰铸铁(指具有片状石墨的铸铁)的浇注温度一般在1340°。
(5)脱蜡(6)浇注、落砂和清理
(二)熔模铸造的特点及应用
优点:熔模铸造可以生产形状复杂、轮廓清晰、薄壁且无分型面、质量较高的铸件,一般的小孔凸台均可直接铸出。熔模铸造能铸造各种合金铸件,特别适于高熔点、难切削和用别的加工方法难以成形的合金,如耐热合金、磁钢、不锈钢等。它的生产批量也不受限制,可实现机械化流水生产。
离心铸件尺寸公差等级可达IT14~IT12,表面粗糙度Ra12.5~6.3μm。离心铸造导致铸件内表面粗糙不平,质量较差,尺寸也不准确。
应用:离心铸造主要用于制造铸钢、铸铁、非铁金属等材料的种类管状零件的毛坯。
二、铸造新技术和新工艺
1、消失模铸造
⑴ 定义:
⑵ 特点及其应用:
2、陶瓷型铸造
⑴ 定义:
⑵ 特点及其应用:
如皋市江海技工学校教案首页
授课日期
班级
课题:§1-3特种铸造及铸造新技术
教学目的、要求:了解几种特种铸造的工艺特点
教学重点、难点:铸件浇注、落砂及清理的工艺过程
授课方法:讲授法、视听法
教学参考及教具(含电教设备):《机械制造工艺基础》多媒体
授课执行情况及分析:
北京科技大学科技成果——特种合金特种铸件精确制备技术

北京科技大学科技成果——特种合金特种铸件精确
制备技术
项目简介
特种合金特种铸件精确制备技术是把传统的熔模铸造与现代的离心铸造相结合的一种新型的零部件制备技术,它是应用浇注系统的合理设计,以充分利用离心铸造的特点,使得合金液在大流速下充型,在离心力的压力作用下凝固;再辅以合金真空下熔炼、真空下充型,最大限度减少合金中气体含量和氧化夹杂。
该课题在国家863高技术计划的资助下,在该技术的研究与应用开发方面进行了深入系统的研究工作,创造了一系列的从熔模铸件结构设计、浇注系统设计、合金真空熔炼、真空离心铸造等方面独有的技术,目前申请国家发明专利3项。
该技术特点是可以直接制造出具有最终形状的零部件,最大限度地减少机加工量和节省原材料,制得的铸件合金晶粒细小,强化相呈弥散均匀分布,铸件力学性能、致密度高。
如利用该技术,我们制出了强度达400MPa、导电率80%IACS高强高导且无缺陷高致密度的精密铜合金薄壁铸件。
应用该技术研制的一些产品已成功地应用于我国国防军工和民用领域,获到了业界专家的好评。
该项目可用于制造各种精密合金、高温合金、高速钢、铜基合金、钛合金等复杂形状零部件。
典型产品及应用领域包括:叶轮、泵体、铸铁管、汽缸环、齿轮、铸钢管、滚筒、铜合金的管、轴承、艺术品、高速钢轧辊以及轧辊用辊套、汽车发动机用气缸套、轴套等。
经济效益及市场分析
该技术的应用范围广,可应用于一些高性能高质量要求铸件的生产,预计每年可产生100万以上的经济效益。
合作方式
技术转让、技术入股或者其它合作方式。
特种设备采用新材料新技术新工艺处罚
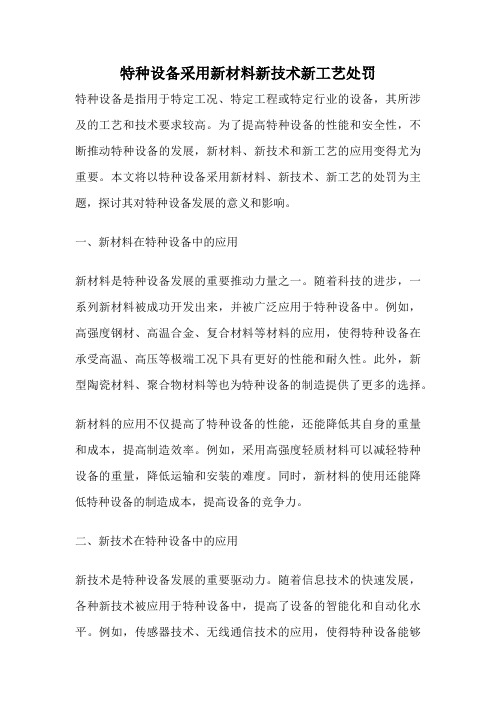
特种设备采用新材料新技术新工艺处罚特种设备是指用于特定工况、特定工程或特定行业的设备,其所涉及的工艺和技术要求较高。
为了提高特种设备的性能和安全性,不断推动特种设备的发展,新材料、新技术和新工艺的应用变得尤为重要。
本文将以特种设备采用新材料、新技术、新工艺的处罚为主题,探讨其对特种设备发展的意义和影响。
一、新材料在特种设备中的应用新材料是特种设备发展的重要推动力量之一。
随着科技的进步,一系列新材料被成功开发出来,并被广泛应用于特种设备中。
例如,高强度钢材、高温合金、复合材料等材料的应用,使得特种设备在承受高温、高压等极端工况下具有更好的性能和耐久性。
此外,新型陶瓷材料、聚合物材料等也为特种设备的制造提供了更多的选择。
新材料的应用不仅提高了特种设备的性能,还能降低其自身的重量和成本,提高制造效率。
例如,采用高强度轻质材料可以减轻特种设备的重量,降低运输和安装的难度。
同时,新材料的使用还能降低特种设备的制造成本,提高设备的竞争力。
二、新技术在特种设备中的应用新技术是特种设备发展的重要驱动力。
随着信息技术的快速发展,各种新技术被应用于特种设备中,提高了设备的智能化和自动化水平。
例如,传感器技术、无线通信技术的应用,使得特种设备能够实时监测工艺参数、状态信息,并通过网络进行远程控制和故障诊断,提高了设备的安全性和可靠性。
新技术还能提高特种设备的制造和维修效率。
例如,采用先进的制造技术,如数控加工、激光焊接等,可以提高设备的制造精度和生产效率。
同时,采用先进的维修技术,如无损检测、远程维修等,可以降低设备的维修成本和停机时间。
三、新工艺在特种设备中的应用新工艺是特种设备发展的重要保障。
随着工艺技术的不断进步,一系列新工艺被应用于特种设备的制造和维修中,提高了设备的可靠性和安全性。
例如,采用先进的焊接工艺,如激光焊接、电弧焊接等,可以提高焊接接头的质量和强度,减少焊接缺陷和故障的发生。
同时,采用先进的表面处理工艺,如喷涂、热处理等,可以提高设备的耐腐蚀性和耐磨性。
特种设备哪些环节需要遵守技术规范及相关标准?当特种设备采用新材料、新技术、新工艺与安全技术规范不一致
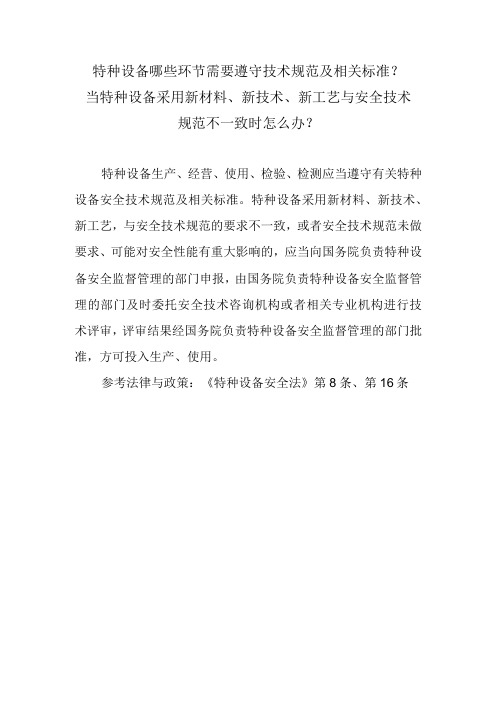
特种设备哪些环节需要遵守技术规范及相关标准?
当特种设备采用新材料、新技术、新工艺与安全技术
规范不一致时怎么办?
特种设备生产、经营、使用、检验、检测应当遵守有关特种设备安全技术规范及相关标准。
特种设备采用新材料、新技术、新工艺,与安全技术规范的要求不一致,或者安全技术规范未做要求、可能对安全性能有重大影响的,应当向国务院负责特种设备安全监督管理的部门申报,由国务院负责特种设备安全监督管理的部门及时委托安全技术咨询机构或者相关专业机构进行技术评审,评审结果经国务院负责特种设备安全监督管理的部门批准,方可投入生产、使用。
参考法律与政策:《特种设备安全法》第8条、第16条。
特种钢的制备与性能研究
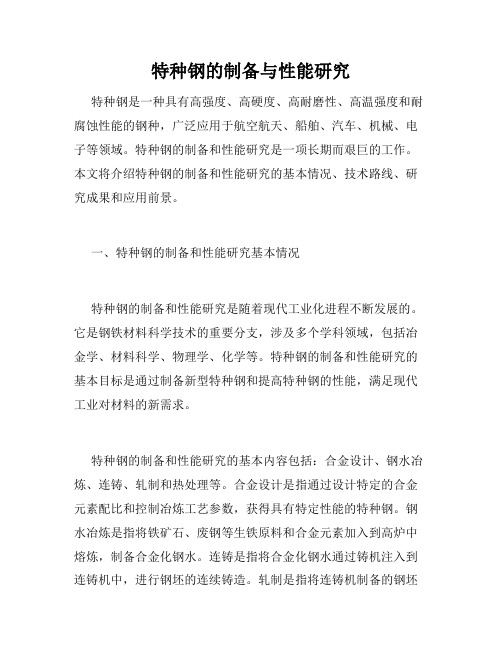
特种钢的制备与性能研究特种钢是一种具有高强度、高硬度、高耐磨性、高温强度和耐腐蚀性能的钢种,广泛应用于航空航天、船舶、汽车、机械、电子等领域。
特种钢的制备和性能研究是一项长期而艰巨的工作。
本文将介绍特种钢的制备和性能研究的基本情况、技术路线、研究成果和应用前景。
一、特种钢的制备和性能研究基本情况特种钢的制备和性能研究是随着现代工业化进程不断发展的。
它是钢铁材料科学技术的重要分支,涉及多个学科领域,包括冶金学、材料科学、物理学、化学等。
特种钢的制备和性能研究的基本目标是通过制备新型特种钢和提高特种钢的性能,满足现代工业对材料的新需求。
特种钢的制备和性能研究的基本内容包括:合金设计、钢水冶炼、连铸、轧制和热处理等。
合金设计是指通过设计特定的合金元素配比和控制冶炼工艺参数,获得具有特定性能的特种钢。
钢水冶炼是指将铁矿石、废钢等生铁原料和合金元素加入到高炉中熔炼,制备合金化钢水。
连铸是指将合金化钢水通过铸机注入到连铸机中,进行钢坯的连续铸造。
轧制是指将连铸机制备的钢坯通过热轧机进行加工成具有特定厚度和宽度的特种钢板。
热处理是指通过将特种钢板加热和冷却处理的方法,改善特种钢的性能和组织结构。
二、特种钢的制备和性能研究技术路线特种钢的制备和性能研究技术路线包括:合金设计、钢水冶炼、连铸、轧制和热处理等。
其中合金设计是特种钢制备和性能研究的关键。
钢铁行业通过对新型合金配比的研究和冶炼工艺的改进,可以大大提高特种钢的力学性能和耐腐蚀性能。
合金设计要考虑特种钢所需的性能指标,并根据这些指标筛选合适的元素进行配比,最终制备出适用于特定应用场合的特种钢。
例如,航空航天领域需要的特种钢要求强度高、韧性好、耐腐蚀性好,因此需要加入具有高强度、高韧性和耐腐蚀性能的特殊合金元素。
钢水冶炼是实现特种钢制备和性能研究的关键环节。
冶炼工艺要根据特种钢所需的合金元素调整配比和控制炉温、氧化还原等参数,以确保合金元素在钢铁中充分溶解和均匀分布。
特种材料的改性技术研究及应用
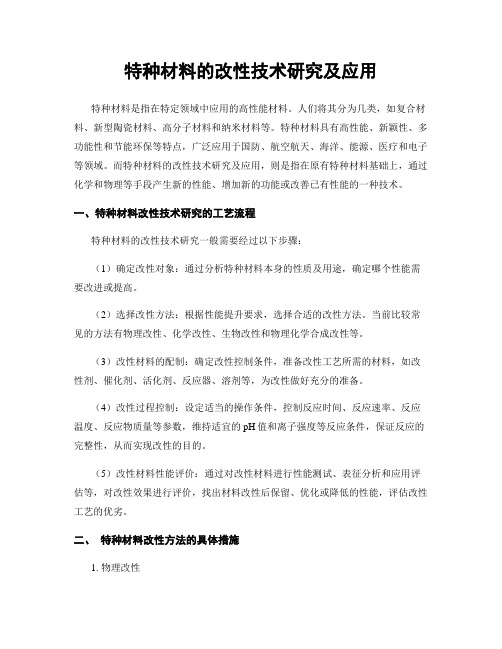
特种材料的改性技术研究及应用特种材料是指在特定领域中应用的高性能材料。
人们将其分为几类,如复合材料、新型陶瓷材料、高分子材料和纳米材料等。
特种材料具有高性能、新颖性、多功能性和节能环保等特点,广泛应用于国防、航空航天、海洋、能源、医疗和电子等领域。
而特种材料的改性技术研究及应用,则是指在原有特种材料基础上,通过化学和物理等手段产生新的性能、增加新的功能或改善已有性能的一种技术。
一、特种材料改性技术研究的工艺流程特种材料的改性技术研究一般需要经过以下步骤:(1)确定改性对象:通过分析特种材料本身的性质及用途,确定哪个性能需要改进或提高。
(2)选择改性方法:根据性能提升要求,选择合适的改性方法。
当前比较常见的方法有物理改性、化学改性、生物改性和物理化学合成改性等。
(3)改性材料的配制:确定改性控制条件,准备改性工艺所需的材料,如改性剂、催化剂、活化剂、反应器、溶剂等,为改性做好充分的准备。
(4)改性过程控制:设定适当的操作条件,控制反应时间、反应速率、反应温度、反应物质量等参数,维持适宜的pH值和离子强度等反应条件,保证反应的完整性,从而实现改性的目的。
(5)改性材料性能评价:通过对改性材料进行性能测试、表征分析和应用评估等,对改性效果进行评价,找出材料改性后保留、优化或降低的性能,评估改性工艺的优劣。
二、特种材料改性方法的具体措施1. 物理改性物理改性的主要手段是通过材料本身的物理性质改变其性能。
物理改性的方法有:表面改性、热处理改性、辐射改性、超临界流体改性、等离子处理改性等。
其中,表面改性是比较常用的改性方法之一,可通过表面涂层、表面氟化、表面氧化等方式,提高特种材料的耐磨、耐摩擦等性能,为其应用提供可靠保障。
2. 化学改性化学改性是在材料化学结构上对其进行修饰或转化的过程,通常是在材料化学反应的条件下进行的。
化学改性包括基质化学修饰、核心-壳结构改性、化学交联等多种手段。
常见的方法有聚合改性、交联改性、酯化反应改性等。
材料制备新技术

结构材料:耐磨部件(水轮机叶片、数控刀片) 结构材料:耐磨部件(水轮机叶片、数控刀片) 功能材料:光电子器件 功能材料: 信息存储介质 金属铋、锑等薄膜, 光全息存储 金属铋、锑等薄膜,
As-Se-Ge系、Te-As-Ge系薄膜 系 系薄膜
光盘存储材料
基质上涂覆铁系或钴系 磁光薄膜: 磁光薄膜:TbFe DyFe DyCo等。 等
制备技术: 制备技术:
机械粉碎法 蒸发凝聚法 溶胶—凝胶法 Sol-Gel法 凝胶法( 溶胶 凝胶法(Sol-Gel法) 气相反应法
材料成型与烧结
材料要获得最终的使用性能必须进行成型。 材料要获得最终的使用性能必须进行成型。 绝大多数材料要经过的主要加工工艺环节包括: 绝大多数材料要经过的主要加工工艺环节包括:
材 料 先 进 制 备 技 术
王 为 民
(wangwm@)
武汉理工大学材料复合新技术国家重点实验室
课程的主要内容
1、概述 2、粉末材料的加工和制备新技术 3、先进的成型 4、先进的烧结 5、燃烧合成技术 6、薄膜材料及制备技术
粉末材料及其加工和制备
粉末材料:绝大多数材料都以粉末状材料为原料。 粉末材料:绝大多数材料都以粉末状材料为原料。 粉末材料的特性很大地影响最终材料的性能。 粉末材料的特性很大地影响最终材料的性能。 纯度、粒度、形状 纯度、粒度、 陶瓷材料: 陶瓷材料: ZrO2, Al2O3, TiC, Si3N4, SiC, BN 金属基复合材料: Al—SiC, CuFe金属基复合材料: Al SiC, Cu-Al2O3, Fe-TiC 功能复合材料:磁性复合材料, 导电复合材料,摩擦材料。 功能复合材料:磁性复合材料, 导电复合材料,摩擦材料。 高分子复合材料: 高分子复合材料:工程塑料
- 1、下载文档前请自行甄别文档内容的完整性,平台不提供额外的编辑、内容补充、找答案等附加服务。
- 2、"仅部分预览"的文档,不可在线预览部分如存在完整性等问题,可反馈申请退款(可完整预览的文档不适用该条件!)。
- 3、如文档侵犯您的权益,请联系客服反馈,我们会尽快为您处理(人工客服工作时间:9:00-18:30)。
大塑性变形技术(SPD)制备超细晶材料的研究现状1 前言随着现代工业和科学技术的发展,不断提高钢铁和有色金属材料的综合性能,减少结构件自重,已成为制造业亟待解决的问题。
根据经典的HallPetch关系,金属材料的强度与其晶粒大小成反比。
因此,晶粒细化作为提高金属材料强度的有效方法之一,获得了广泛关注。
近年,超细晶(包括亚微米级和纳米级)金属材料更是由于其表现出的一系列有别于传统材料的优异的物理、力学和成形性能而引起了科学家们的广泛关注[1]。
大塑性变形是一种有效的制备超细晶乃至纳米晶结构材料的方法,已广泛应用于各种金属材料的制备中,不仅改善了其他超细晶材料制备方法存在的问题,同时拓宽了传统塑性加工技术的应用领域,使传统材料的性能获得大幅度的提高与改善;SPD材料表现出优良的力学性能、独特的物理和化学性能、优异的超塑性,这在实际应用中是极具吸弓f力的,并使其越来越受到人们的重视。
目前,通过SPD法取得了纯金属、合金、钢、金属问化合物和复合材料等的超细晶或纳米结构,并在实际应用中不断得到认可,如采用ECAP制备获得的钛合金螺钉已应用于汽车及航天工业,这些零件可以满足高强度、高韧性、高疲劳性能的要求,从而不仅延长零件的使用寿命,并可节约资源,降低成本,实现可持续发展。
2 超细晶体金属材料的制备方法大体积超细晶金属材料的制备方法主要可以分为两类。
第一类, 是把用不同技术制得的原子、分子、离子或纳米颗粒等超微粉体进行致密化。
超微粉体的制备方法主要有惰性气氛中的气相冷凝法、电沉积以及高能球磨法等。
这类方法虽然是多数超细晶材料组织和性能研究的基础, 但这些方法在发展中还存在一些难以解决的问题, 如致密化后的残留孔洞、制粉或粉体团聚过程中的污染、所获试样的几何尺寸增大和这些方法的工业应用等。
第二类, 是对现有粗晶材料进行剧烈塑性变形,使其获得稳定的超细晶组织,即剧烈塑性变形法( Severe Plastic Deformation,SPD)。
SPD法具有许多独特的优点,如不存在超微粉体的制备过程,不易引入杂质; 适用范围宽,可以制备大体积无残留孔洞试样,并且具有工业应用的可能性。
基于第二类方法的这些独特优点, 第一类方法存在的问题,可以由第二类方法予以解决。
大塑性变形技术简称(SPD)具有强烈的晶粒细化能力,可以直接将材料的内部组织细化到亚微米乃至纳米级,已被国际材料学界公认为是制备块体纳米晶粒(大小于100nm)和超细晶材料(晶粒大小为100nm-1μm)的最有前途的方法,其主要的变形方式是剪切变形。
组织细化的主要目的在于①充分挖掘材料的潜能,获得满足军事和日益发展的航空航天等领域对高强高韧材料的需求②在较高温度下,提高材料的超塑性能力,以提高零件的生产效率和开拓难变形材料如镁合金等的加工制备新途径。
众所周知, 在低温情况下采用大的形变,如冷轧或冷拔,可极大地细化金属组织, 但用这种方法难以使晶粒细化到超细晶,并且所获得的组织一般为网状位错结构式亚结构,其晶界是小角度混乱取向。
但纳米组织应是主要含有大角度晶界颗粒型的超微晶组织,因此,采用SPD 法制备大体积超细晶材料必须满足以下要求。
(1) 能够在材料内部获得具有大角度晶界的超细晶结构。
只有这样,材料的性能才能出现质的变化。
(2) 整个试样中的超细晶结构应该是均匀的, 这是获得稳定性能的必要条件。
(3) 试样虽然经历了剧烈的塑性变形, 但是试样不应有机械损伤或裂纹。
在这一原则的指导下, 大塑性变形工艺得到了迅猛发展;等通道转角挤压(ECAE ),扭转(HPT),循环挤压(CE)或往复挤压(CEC),大挤压比挤压(HRE ),累积轧制(ARB),快速凝固加粉末冶金等。
应用大塑性变形技术, 已经成功地制备了纯金属、合金、钢、金属间化合物、陶瓷基复合材料、金属基复合材料、半导体等的细晶材料。
3 现有的SPD 法及其制备原理3.1 等通道转角挤压(ECAE )等通道转角挤压是一种通过对块体材料施加剧烈的塑性形变直接细化其内部组织,制备具有大角度晶界的块体纳米材料的方法。
这一方法可使材料在塑性变形时不改变试样断面,因而它建立了重复形变的可能性。
目前,等通道转角挤压技术已经成为剧塑性成形技术中发展最为快速的技术之一,已被用于制备超细晶甚至纳米晶块体材料中。
其原理是将试样在一定挤压力下通过两个轴线相交且截面尺寸相等并成一定角度的通道,将试样在一定挤压力下发生纯剪切变形,进而达到细化晶粒的目的,等通道转角示意图如图l 所示。
试样经Ⅳ道次挤压变形后其累积等效理论应变量为2cot(22)cos (22)=n 3n ec ψωωψωε+++⎧⎫⎨⎬⎩⎭式中:ψ为模具内角;ω为模具外角;n 为挤压道次。
当ψ=90℃时,ω=0,n=l 时,从式(1)可知,其累积应变=1.15ε,经n 道次变形后,其累积应变为n ε。
等通道转角挤压变形细化组织时,挤压路径和挤压道次是试样变形过程中的重要参数。
图2所示为等通道转角挤压的4种不同路径。
这4种路径的差别在于试样在重复挤压过程中,在通过交叉的通道时不断改变切变方向,使经等通道转角形变时晶粒细化效果发生变化。
对于路径A ,每道次挤压后试样不旋转直接进入下一道次挤压;对于路径BA ,每道次挤压后试样按90。
交替旋转进入下一道次挤压;对于路径Bc ,每道次挤压后试样按同一方向旋转90。
进入下一道次挤压;对于路径C ,每道次挤压后试样旋转180℃进入下一道次。
相关研究发现,采用路径Bc 进行挤压变形时,晶粒在3个方向均可获得均匀剧烈变形,易形成大角度晶界,晶粒细化效果最明显。
NEMOTO 等对纯铝进行等通道挤压变形后发现,采用路径A 进行10道次变形与采用路径Bc 进行4道次变形具有相同的超细晶微观组织。
然而,采用传统ECAP 对材料进行挤压变形时具有一定的局限性,即在每道次挤压变形后,须把材料取出后再放进去,而不是通过中间转换部分来实现材料的快速进出转换以获得较多挤压道次及高压应变,这使得工作过程繁琐,同时浪费时间。
因此,在传统ECAP 的基础上越来越多的新型ECAP 得到发展,并改进了传统ECAP 所存在的局限性。
如旋转模具ECAP(rotary-die ECAP)、反复侧边挤压(repetitiveside extrusion process ,RSEP)、连续剪切工艺(con-shearing process)及等径角轧制(equal channelangular rolling ,ECAR)191等方法。
图1 等通道角挤压原理图3.2 高压扭转高压扭转是由BRIDGMAN 第一次提出并逐步发展起来的对材料进行剧塑性变形的方法。
大量研究证明,高压扭转可应用于各种金属材料的制备过程,并使材料晶粒尺寸均匀细化至亚微米级甚至纳米级,从而获得超细晶结构材料。
采用此装置变形时,将薄片盘状试样施以GPa 级的高压使其发生扭转。
由于变试样的尺寸不发生改变,试样的外侧可引入较大的剪切应变,使金属材料发生剧塑性变形,从而使晶粒尺寸不断减小,直至形成超细晶甚至纳米晶粒。
同时由于材料在许可的压力和试样外压力的作用下,受模具的影响,使得材料在类似于静压力的条件下发生剪切变形,因此,尽管其应变量较大,试样仍不易发生破裂。
材料变形量由冲头转动圈数控制,其等效应变eq r 如下:23eq rN r l π= 式中:N 为冲头转动圈数;r 为距试样中心距离;为试样厚度。
对试样进行高压扭转时,由于试样局限于薄片盘状限制了其对块状材料的应用,同时材料组织变化完全依赖于所施加压力大小以及试样受力部位,造成所制备材料存在从中心至外侧组织不均匀的现象。
为解决这一问题,SAKAI 等开发了一种适用于块状材料的高压扭转装置(与薄片状试样高压扭转装置相比)。
在HPT 工艺过程中,影响其工艺性能的参数有加载力、转动道次及其产生的强力应变和变形过程中的加工硬化及动态回复。
高压扭转原理图如图2所示,HPT作为一种有效的制备超细晶晶粒(晶粒尺寸在100~300 nm范围,甚至更小)的工艺,制备的合金可获得包括超高强度和高温条件下优良超塑性在内的独特性能。
图2 高压扭转原理图3.3 累积叠轧焊累积叠轧焊(Accumulative roll bonding,触淝)是由日本大阪大学SAITO等首次提出并逐步发展起来的一种变形方法。
目前,由于ARB工艺易于在传统轧机上实现,制备的板材具有层压复合钢板的特性,因此可用于各种材料的制备中。
其原理是一个材料的不断堆叠和轧焊的过程。
累积叠轧焊原理图如图3所示,在该过程中,首先将一块原始板材有序地放置于另一块板材上面,通过传统轧焊加工使板材轧焊在一起,在必要的时候对堆层之间进行表面处理以提高其结合强度,然后从中间板材剪开分成两部分,再将这两部分进行表面处理、堆叠,然后进行循环轧焊。
整个过程需在低于再结晶温度的高温条件下进行,若温度过高易使材料出现再结晶,将抵消叠轧过程中所产生的累积应变;若在较低温条件下则将导致延展性及结合强度的下降。
轧制是制备板材最具优势的塑性变形工艺,但随着压下量的增加,材料尺寸相应减小,材料的总应变量将受到限制。
在A.R.B加工过程中,当每次轧制压下量维持在50%的时候,板材轧制过程中产生的宽度变化可以忽略,因而可获得高塑性应变并保持材料的几何形状不发生变化。
试样经ARB加工m次循环过程后原始板材所包含的次数变为岁。
如试样经lO次循环ARB加工后,所包含的层数变为1 024,这意味着原始材料的厚度将小于1μm。
然而,ARB工艺存在一个较大的问题即材料裂纹现象。
由于在轧焊过程中产生极大的累积塑性应变,导致板材尤其是多次循环轧焊后产生边缘裂纹。
在一些材料的应用中,如A1-Mg合金,边缘裂纹将迅速扩展到板材中央,从而限制了板材叠轧循环次数,同时也限制了ARB工艺对材料的应用。
目前,采用ARB工艺加工的材料大多为具有较好延展性及塑性变形能力的金属材料,比如纯铝、铜及铁,通过ARB工艺对这些材料可制备出超细晶材料,同时不出现任何裂纹:对于塑性较差的金属材料,则需通过加热到较高温度以改善其塑性然后再进行叠轧,如Mg合金。
图3 累积叠轧焊原理图3.4 多向锻造多向锻造(Multiple foxing,ME)是20世纪90年代由SALISHCHEV等提出的对块状试样加工成形获得超细晶组织的一种新型方法。
该技术的原理等同于多次自由锻造过程,即依次沿不同的轴向锻压材料,在变形过程中晶粒因发生动态再结晶而得到细化。
材料在锻造过程中由于不同锻造区域材料变形的不均匀性导致MF工艺制备的材料存在组织不均匀现象,其均匀性均低于等通道转角挤压变形和高压扭转变形的,然而该工艺的变形温度通常在0.1Tm-0.5 Tm(Tm为金属熔点)之间。