30t EAF-LF-VD-13t铸锭流程生产14Cr1Mo钢的工艺实践
14cr1mo锻件最低温度

14cr1mo锻件最低温度【实用版】目录1.14Cr1Mo 钢的概述2.亚温淬火和模拟焊后热处理对 14Cr1Mo 钢的影响3.14Cr1Mo 钢在铸锻件生产中的应用实践4.14Cr1Mo 锻件最低温度正文一、14Cr1Mo 钢的概述14Cr1Mo 钢是一种合金结构钢,其主要成分为:碳(C)0.12%、硅(Si)0.57%、锰(Mn)0.48%、磷(P)0.003%、硫(S)0.001%、铬(Cr)1.20%。
这种钢材具有较高的强度、良好的韧性和耐磨性,因此在机械制造、石油化工、船舶等领域得到了广泛应用。
二、亚温淬火和模拟焊后热处理对 14Cr1Mo 钢的影响亚温淬火是指在低于钢的临界温度下进行的淬火处理。
这种处理方法能够提高钢的韧性,降低脆性,提高钢的抗拉强度和屈服强度。
而模拟焊后热处理则是模拟实际焊接过程后的热处理,目的是改善焊接接头的组织和性能。
研究表明,亚温淬火和模拟焊后热处理对 14Cr1Mo 钢的组织和力学性能有显著影响。
经过处理后,钢的晶粒细化,组织均匀,抗拉强度、屈服强度和冲击韧性等力学性能得到了明显提高。
三、14Cr1Mo 钢在铸锻件生产中的应用实践14Cr1Mo 钢在我国铸锻件生产中具有广泛的应用。
例如,30t 级的eaf-lf-vd-13t 铸锭流程就可以生产 14Cr1Mo 钢。
通过合理的热处理工艺,可以进一步提高铸锻件的性能,满足不同领域的使用要求。
四、14Cr1Mo 锻件最低温度14Cr1Mo 锻件在生产过程中,需要进行热处理以提高其力学性能。
而最低温度则是指在热处理过程中,钢所需要达到的最低温度。
根据相关资料,14Cr1Mo 锻件的最低温度为 -80℃。
在这个温度下,钢的组织结构得到进一步优化,性能得到提高。
综上所述,14Cr1Mo 钢具有良好的力学性能和应用前景,通过亚温淬火和模拟焊后热处理等工艺手段,可以进一步提高其性能,满足不同领域的使用要求。
UHP、LF电炉冶炼工艺技术操作规程

常州中天EAF、LF炉冶炼工艺技术操作规程1.1冶炼前准备及注意事项1.1.1新炉冶炼第一炉,只许冶炼无特殊要求的低碳钢或45#钢。
1.1.2新炉前两炉应注意吹氧操作,氧气工作压力控制在0.7—0.9Mpa,防止大喷。
1.1.3冶炼前,必须清楚冶炼钢种的条件及配套设备的运行情况,否则不得安排生产计划。
1.1.4各种原材料尤其是铁合金和增碳剂,使用前,必须知其主要的成份含量,如不详或混号者,不得使用。
1.1.5出钢前,出钢料仓应按照各钢种规定备料。
1.1.6下一炉需出净钢渣时,一定要准确估测本炉次的留钢量,并合理调整装入量,避免下一炉次的钢水出不净或钢水欠缺太多。
1.1.7冶炼前应仔细检查各部分水冷系统,机电设备,液压设备和控制仪表及钢液测量系统,如有故障,及时联系处理。
1.1.8如操作人员在操作过程中发现下列报警,应及时通知有经验的电气人员及时检修(1)EAF变压器(2)气体吹扫系统的主电机(3)皮带运输机、泵和振动给料器系统的所有电机和辅助电气系统。
1.1.9冶炼前应检查调整电极长度,保证冶炼的正常进行。
1.1.9.1接电极:吹净电极螺纹处积灰,对正,旋紧电极接头和电极。
1.1.9.2放电极:调整电极,使电极夹持器下到最低位置时,电极头部距炉底高度不得小于300mm,且能满足冶炼需要,电极夹持器不得夹在电极接缝处正面200mm 内(白线以内),防止电极螺纹处损坏,折断电极。
1.1.9.3换电极:如果电极的端部已出电炉盖的弧形坑,且伸出夹持器的距离只有几厘米,则更换电极。
更换电极时,将一个合适的吊具挂到行车中,稍微用力吊住电极,打开夹持器,吊出电极至电极接长站,将接好的电极放入电极夹持器内,调整电极长度。
1.2补炉1.2.1每炉出钢后,炉长要对炉壁,渣线,炉盖中间耐材部位,出钢口及水冷元件进行检查。
1.2。
2出钢口的检查,更换,填充。
1.2.2.1出钢后,检查出钢口管砖浸蚀程度。
如端砖内径超过直径200mm,或出钢时间小于80秒,应立即通知有关人员,做好更换出钢口管砖,端砖的准备。
30吨LF炉冶炼记录12

热处理其铸钢生产的重要工序、为保证铸钢热处理质量,指导生产,特制订本规程。
1.热处理工艺及操作要点:1.1组炉原则上应按铸钢钢种、壁厚和热处理方法(如正火、退火、淬火或调质等)分类组合,但在品种多,批量小,分类组合困难时,允许按下列范围组装。
1.1.1高锰钢铸件,原则上按18小时与21小时两类(在有条件的情况下可分为四类)组装,见工艺指示图,而斗齿应单独组装,当斗齿装炉不够时,可在炉门处适当地装少量同类产品,特大厚件应另外有工艺。
1.1.2碳素钢、低合金结构钢,高合金钢,轧辊等分别按退火,正火,淬火调质等不同热处理类别组装,在铸件较多又能分类的情况下,应按壁厚差100mm者组装。
1.2要求:1.2.1要求所有热处理炉炉体完好(如果炉体损坏、不得强行进炉)附属机械,电路、仪表等运转正常。
1.2.2要求计划进炉产品、外观质量经检查合格、组炉正确,技术要求明确,新产品有其具体工艺。
1.2.3待退火热割冒口的铸件应将型砂、冷铁、芯骨、浇口、披缝等清理干净才能组织进炉,退火后热割冒口,高锰钢铸件一般在清砂热处理淬火后打水(或浸水)切割冒口。
1.2.4一般铸件在铸钢车间最终热处理前,应清除芯砂,冷铁,芯骨、浇口、冒口、披缝等,并经检验员允许,按工艺规程焊补好铸件有关缺陷,经初步检验合格方可按工艺,按计划组炉热处理。
1.3 装炉1.3.1 台车面在装炉前必须清理平整,冷炉进炉前必须整理好进火孔,烟道孔,填满砂封槽的砂子,清理炉内砖头等杂物,堆好台车后部的砂子。
1.3.2正、退火时,铸件底部距离台车平面必须垫高校平150~250mm大型铸件重迭堆码时上、下间隙﹥160mm,ZGMn13铸件,一般件间隙要﹥30mm,厚大件间隙要大于铸件壁厚的1/2,轧臼壁,破碎壁、护套装炉时大头冒口一定朝下,在其内装的铸件一定要与工件有空隙,不能下挤上压,斗前壁装炉时要塞稳、垫好、一律不允许用耐火砖做垫铁。
1.3.3厚大铸件装高温区,细、薄,长铸件垫平不受压,矫正变形件须找好基准面选择好支点加够重压块,条形呈“井”字形,板条状件侧装。
连铸轴承钢生产工艺流程
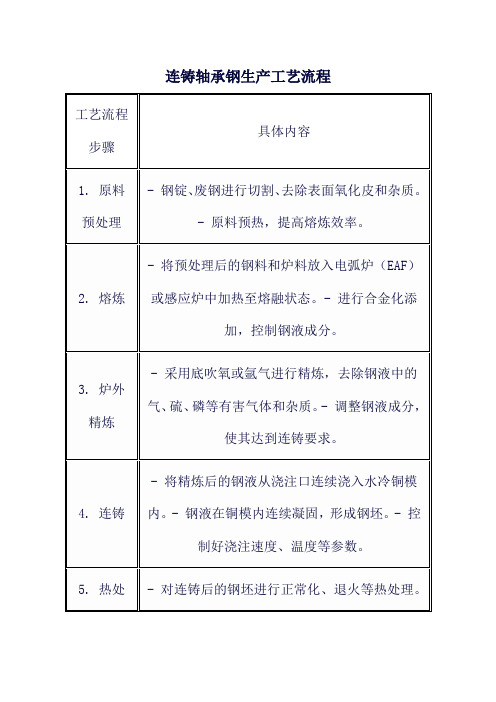
- 将精炼后的钢液从浇注口连续浇入水冷铜模内。- 钢液在铜模内连续凝固,形成钢坯。- 控制好浇注速度、温度等参数。
5. 热处理
- 对连铸后的钢坯进行正常化、退火等热处理。- 调整组织,消除内应力。
6. 切割与标记
- 将连铸的钢坯切割成定长。- 进行标记,作为后续加工的原材料。
连铸轴承钢生产工艺流程
工艺流程步骤Biblioteka 具体内容1. 原料预处理
- 钢锭、废钢进行切割、去除表面氧化皮和杂质。- 原料预热,提高熔炼效率。
2. 熔炼
- 将预处理后的钢料和炉料放入电弧炉(EAF)或感应炉中加热至熔融状态。- 进行合金化添加,控制钢液成分。
3. 炉外精炼
- 采用底吹氧或氩气进行精炼,去除钢液中的气、硫、磷等有害气体和杂质。- 调整钢液成分,使其达到连铸要求。
铸锭技术操作规程
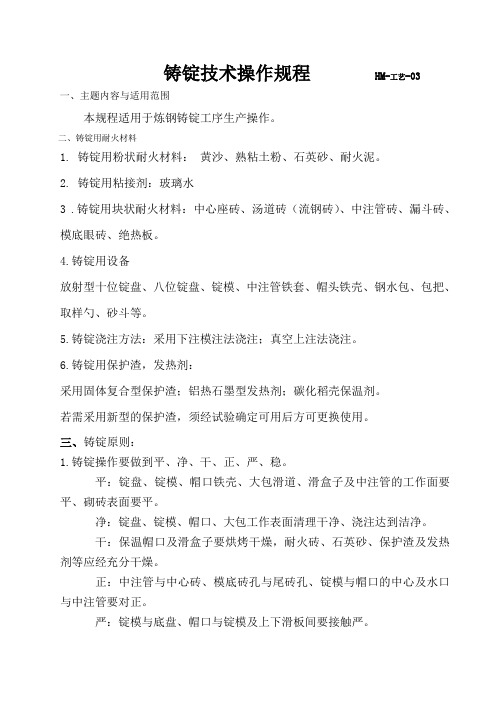
铸锭技术操作规程HM-工艺-03一、主题内容与适用范围本规程适用于炼钢铸锭工序生产操作。
二、铸锭用耐火材料1. 铸锭用粉状耐火材料:黄沙、熟粘土粉、石英砂、耐火泥。
2. 铸锭用粘接剂:玻璃水3 .铸锭用块状耐火材料:中心座砖、汤道砖(流钢砖)、中注管砖、漏斗砖、模底眼砖、绝热板。
4.铸锭用设备放射型十位锭盘、八位锭盘、锭模、中注管铁套、帽头铁壳、钢水包、包把、取样勺、砂斗等。
5.铸锭浇注方法:采用下注模注法浇注;真空上注法浇注。
6.铸锭用保护渣,发热剂:采用固体复合型保护渣;铝热石墨型发热剂;碳化稻壳保温剂。
若需采用新型的保护渣,须经试验确定可用后方可更换使用。
三、铸锭原则:1.铸锭操作要做到平、净、干、正、严、稳。
平:锭盘、锭模、帽口铁壳、大包滑道、滑盒子及中注管的工作面要平、砌砖表面要平。
净:锭盘、锭模、帽口、大包工作表面清理干净、浇注达到洁净。
干:保温帽口及滑盒子要烘烤干燥,耐火砖、石英砂、保护渣及发热剂等应经充分干燥。
正:中注管与中心砖、模底砖孔与尾砖孔、锭模与帽口的中心及水口与中注管要对正。
严:锭模与底盘、帽口与锭模及上下滑板间要接触严。
稳:浇注速度适当,模内钢水上升平稳。
2.使用的钢锭模、保温帽、底盘等冶金辅具应符合有关标准的规定。
3.铸锭用的耐火砖、耐火水泥、保温剂、发热剂必须有合格证方可进入分厂。
保温剂、发热剂必须堆放在干燥的地方。
4.汤道砖、注管砖使用前必须干燥,并刷净内孔的浮砂和毛刺。
5.钢锭一般情况下进行热送,按“钢锭热送制度”执行,必要时也可带模热送。
6.凡冷锭,必须在钢锭上写上炉号、钢号、盘号及规定标识。
7.浇注中发生事故的钢锭,应根据有关部门的意见,决定是否按原件使用或降级处理,事故情况及处理结果在记录上作详细记载。
四、浇注前的准备1. 锭盘的准备及砌砖1.1 新锭盘必须进行退火后才能使用。
1.2锭盘表面要求平整光滑。
放置时,须用水平尺校正水平,并保持稳定。
日常使用的锭盘必须保持平整,并随时校正。
14Cr1Mo钢锭开坯裂纹分析及预防措施

0. 45
0. 57 0. 003
P ≤0. 025 0. 004
Ni ≤0. 30 0. 16
Cr
Mo
As
1. 15 ~ 1. 50 0. 45 ~ 0. 65 ≤0. 012
1. 26
0. 45
0. 014
Sn ≤0. 010 0. 003
Sb ≤0. 003 < 0. 001
2. 2 硬度检测 分别 从 裂 纹 附 近 和 未 开 裂 部 位 取 样 ,依 据
No. 4 July 2019
《大型铸锻件》 HEAVY CASTING AND FORGING
DOI:10.14147/ki.51-1396/tg.2019.04.018
14Cr1Mo 钢锭开坯裂纹分析及预防措施
杨德生1,2 韩文科1,2 祁庆花1,2 曹 琨1,2
( 1. 兰州兰石能源装备工程研究院有限公司,甘肃 730314; 2. 甘肃省高端铸锻件工程技术研究中心,甘肃 730314)
without cracks
( a) 裂纹处
( b) 远离裂纹处
( c) 裂纹形貌
( d) 裂纹形貌
( e) 裂纹尖端暗场形貌
( f) 裂纹尖端明场形貌
( g) 锻件近表面组织
Key words: 14Cr1Mo steel ingot; crack; inclusion
14Cr1Mo 属于 Cr-Mo 抗氢钢,具有良好的综 面存在的缺陷属应力裂纹。
合性能,该钢种适用于石油化工、核电、汽轮机缸 体、火电等高温高压、与氢或氢混合介质接触的大
2 检测结果与分析
型设备。某铸造厂生产材质为 14Cr1Mo 的 19 t 2. 1 化学成分分析
14cr1mo生产技术要求

14Cr1MoR钢板的生产技术要求包括以下方面:
1. 化学成分:C≤0.17%,Si 0.5~0.8%,Mn 0.4~0.65%,
P≤0.02%,S≤0.01%,Ni≤0.3%,Cr 1.15~1.5%,Mo 0.45~0.65%。
2. 生产工艺:采用电炉炼钢、LF炉精炼、VD炉真空脱气、轧板、探伤、正火、回火、钢板精整和性能检验等工序进行生产。
公司需要制定合适的内控成分,严格控制化学成分波动范围,确保钢板性能的稳定。
3. 配料控制及冶炼操作:加强配料控制及冶炼操作,有效控制Sn、Sb、As、Cu等有害元素含量,降低P、S含量以提高钢的纯净度,减少回火脆化倾向,提高钢的高温耐蚀性能。
4. 升温控制:采用控制升温,保证加热时间与温度,采用控制轧制等措施,保证钢板内在质量。
5. 轧制及热处理工艺:严格控制轧制及热处理工艺,使钢板获得合理的组织结构及晶粒大小,保证钢板具有良好的综合性能。
6. 钢板应满足GB/T 713-2014标准要求。
7. 采用电炉冶炼工艺生产的细晶粒钢,并经炉外精炼,封头用板为退火状态,封头冲压成型后,再进行正火+急冷+回火处理的恢复性能热处理。
8. 熔炼分析必须满足:X=(10P+5Sb+4Sn+As)×10-2≤15×10-6。
以上信息仅供参考,如需了解更多信息,建议查阅相关书籍或咨询专业人士。
贵钢30t EAF-LF(VD)-CCM工艺实践

精炼时间均处于可控范围内, 连铸每个浇次的浇铸炉数从 4 炉提高到了 1 0炉, 生产效率大大提高, 生产成本有 了显 著降低 , 吨钢冶炼成本下降超过 8 直接 %。
32质量控制 . 32 1 .. 理论允许浇铸 时间
长水 口保护铸流; 在钢包下水 口与长水口之间采用氩气密
封; 中间包内加入中间包保护渣和保温剂进行钢水液面保
好坏的关键点之一 , 第一炼钢厂连铸机采用 3段式全气雾
Байду номын сангаас
冷却控制方式 , 二次冷却水的水量是根据浇铸钢种 、 断面、
拉坯速度以及 中间包钢水温度 , P C进行计算 , 由 L 并按 PD闭环调节方式进行控制 。 I
表3
不同拉速下的浇铸时间( i) m n
3 生产实践
3 1生产 匹配 .
根据表 3 显示 , 在钢水量为 3 情况下 , 20Ⅱn 5t 生产 6 Ⅱ ×0 30删 时, 拉速必须达到 1 / i, . m m n才能有效进行浇 0
在实际生产中, 连铸每炉钢 的浇铸 时间约为 9 i, 0mn
与电弧炉 、 精炼炉冶炼周期不匹配 。为了保证连浇 , 采用
了以下措施 :
22 . 连铸
221 护 浇铸 .. 保
料, 以进一步降低电弧炉冶炼及 L F炉精炼的时间, 确保连
浇顺行。
经过对电弧炉 、 精炼炉生产调度进行合理调整 , 加强 对电弧炉、 精炼炉操作进行标准化管理, 使每炉钢的冶炼、
连铸过程 中, 在钢包—— 中间包—— 结晶器 之间采 用全程保护浇铸技术 : 中在钢包—— 中间包之间采用 其
1采用连铸等待电弧炉的生产调度方法 : ) 即电弧炉 出两炉钢 , 在第 1 炉钢真空处理完成 , 2 第 炉钢 即将精炼
钢铁生产工艺流程规范

钢铁生产工艺流程规范钢铁生产工艺流程规范对于确保钢铁生产的质量和效率至关重要。
本文将详细介绍钢铁生产的主要工艺流程,并阐述各流程中的规范要求。
1. 原料准备钢铁生产的第一步是原料的准备。
这包括将铁矿石进行破碎、筛分和混合。
规范要求在原料准备过程中遵循以下要点:- 确保铁矿石的质量符合生产要求,包括化学成分和粒度分布。
- 使用适当的设备和工具进行破碎和混合,确保操作安全和效率。
- 对原料进行标识和记录,以便追踪和质量控制。
2. 炼铁炼铁是将铁矿石还原为金属铁的过程。
这个阶段的规范要求如下:- 确保高炉操作参数的稳定,包括温度、风量、原料比例等。
- 控制还原剂的投入量,使还原反应得到充分进行。
- 定期监测和调整炉内的温度和气氛,以保证炼铁反应的顺利进行。
3. 炼钢炼钢是将生铁转化为钢的过程。
规范要求如下:- 严格控制炼钢炉的温度、压力和气氛,以确保化学反应的准确性。
- 操作工人必须熟悉炼钢过程中的各种操作和控制参数,并严格遵循操作规范。
- 对于特殊需求的钢种,需要严格控制添加合金元素的配比和时间。
4. 连铸连铸是将炼钢好的熔融钢水浇铸成坯料的过程。
连铸的规范要求包括:- 使用高质量的结晶器和浇注设备,确保坯料形状和表面质量良好。
- 控制浇注速度和冷却条件,以确保坯料的内部和外部质量均匀。
- 定期检查和维护连铸设备,确保运行的安全和正常。
5. 热轧热轧是将坯料加热并通过轧机轧制成钢材的过程。
热轧的规范要求如下:- 确保轧制温度和轧制力的准确控制,以获得所需的钢材性能和尺寸。
- 操作工人必须熟悉不同的轧制工艺和轧制机器的使用方法,以确保操作安全和质量。
- 加强热轧过程中的质量检查和控制,确保钢材的表面质量和内部质量满足要求。
总结钢铁生产工艺流程规范是确保钢铁生产质量的重要保证。
在每个工艺流程中,严格遵守规范要求,并定期进行检查和维护,以确保工艺的顺利进行和钢铁产品的优质制造。
只有这样,我们才能生产出安全可靠、质量卓越的钢铁产品,满足社会的需求。
炼钢厂连铸工艺操作流程
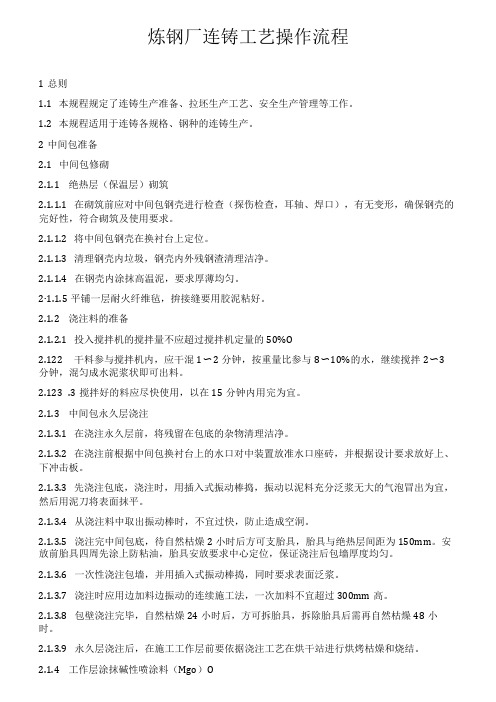
炼钢厂连铸工艺操作流程1总则1.1本规程规定了连铸生产准备、拉坯生产工艺、安全生产管理等工作。
1.2本规程适用于连铸各规格、钢种的连铸生产。
2中间包准备2.1中间包修砌2.1.1绝热层(保温层)砌筑2.1.1.1在砌筑前应对中间包钢壳进行检查(探伤检查,耳轴、焊口),有无变形,确保钢壳的完好性,符合砌筑及使用要求。
2.1.1.2将中间包钢壳在换衬台上定位。
2.1.1.3清理钢壳内垃圾,钢壳内外残钢渣清理洁净。
2.1.1.4在钢壳内涂抹高温泥,要求厚薄均匀。
2∙1.1.5平铺一层耐火纤维毡,拚接缝要用胶泥粘好。
2.1.2浇注料的准备2.1.2.1投入搅拌机的搅拌量不应超过搅拌机定量的50%O2.122干料参与搅拌机内,应干混1〜2分钟,按重量比参与8〜10%的水,继续搅拌2〜3分钟,混匀成水泥浆状即可出料。
2.123.3搅拌好的料应尽快使用,以在15分钟内用完为宜。
2.1.3中间包永久层浇注2.1.3.1在浇注永久层前,将残留在包底的杂物清理洁净。
2.1.3.2在浇注前根据中间包换衬台上的水口对中装置放准水口座砖,并根据设计要求放好上、下冲击板。
2.1.3.3先浇注包底,浇注时,用插入式振动棒捣,振动以泥料充分泛浆无大的气泡冒出为宜,然后用泥刀将表面抹平。
2.1.3.4从浇注料中取出振动棒时,不宜过快,防止造成空洞。
2.1.3.5浇注完中间包底,待自然枯燥2小时后方可支胎具,胎具与绝热层间距为150mm。
安放前胎具四周先涂上防粘油,胎具安放要求中心定位,保证浇注后包墙厚度均匀。
2.1.3.6一次性浇注包墙,并用插入式振动棒捣,同时要求表面泛浆。
2.1.3.7浇注时应用边加料边振动的连续施工法,一次加料不宜超过300mm高。
2.1.3.8包壁浇注完毕,自然枯燥24小时后,方可拆胎具,拆除胎具后需再自然枯燥48小时。
2.1.3.9永久层浇注后,在施工工作层前要依据浇注工艺在烘干站进行烘烤枯燥和烧结。
2.1.4工作层涂抹碱性喷涂料(Mgo)O1.1.1.1中间包内倒入干式料,用木板或其他工具刮平,厚度大于30mm,小于冲击板厚度20mm;在中间包烘烤器外表均匀涂一层石墨,将其放入中间包内,调整其位置,使其与冲击板下口吻合,并且与中间包四周的间距保持一致,大约30mm。
2024版钢铁生产流程
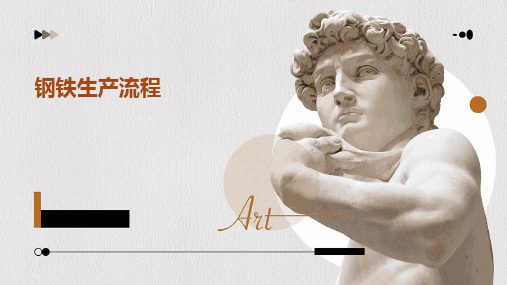
表面处理技术
包括回火炉、时效处理装置、表面处理设备等。
设备
回火、时效和表面处理技术
1
2
3
采用PLC、DCS等控制系统,实现热处理过程的自动化控制,提高生产效率和产品质量稳定性。
自动化控制系统
应用人工智能、大数据等技术,对热处理过程进行智能优化和控制,提高能源利用效率和产品性能。
智能化技术
包括自动化控制装置、智能传感器、数据分析系统等。
大气污染
钢铁生产过程中产生的大量废气,包括一氧化碳、二氧化硫、氮氧化物等有害气体,严重污染空气。
钢铁生产过程中的环境污染问题
余热余压回收利用技术
回收利用钢铁生产过程中产生的余热余压,用于发电、供暖等,降低能源消耗。
环保型烧结技术
采用环保型烧结技术,减少废气排放,提高烧结矿质量。
高效节能冶炼技术
采用高炉喷煤、富氧燃烧等高效节能冶炼技术,提高能源利用效率。
废水处理与回用
钢铁生产废弃物资源化利用途径
低碳冶金技术
应用大数据、人工智能等先进技术,实现钢铁生产过程的智能化和自动化,提高生产效率和资源利用效率。
智能化制造技术
循环经济模式
构建钢铁生产循环经济产业链,实现废弃物资源化利用和能源高效利用,推动钢铁行业可持续发展。
发展低碳冶金技术,减少钢铁生产过程中的碳排放,推动钢铁行业绿色低碳转型。
国家标准
各国均制定了相应的钢材质量标准,如中国的GB标准、美国的ASTM标准等,这些标准规定了钢材的化学成分、力学性能、外观质量等指标。
企业标准
一些大型钢铁企业为了保证自身产品质量和品牌形象,会制定更为严格的企业内部质量标准。
质量评定方法
通常采用抽样检验的方式对钢材进行质量评定,即按照一定的抽样方案从生产批次中抽取一定数量的样品进行检测,然后根据检测结果对整批钢材进行质量评定。
14cr11mov 锻件 标准

14cr11mov 锻件标准一、引言14cr11mov是一种常用的不锈钢材料,广泛应用于石油、化工、航空航天、船舶、核工业等领域。
为了规范14cr11mov锻件的生产和使用,各国相继出台了一系列标准。
本文将重点介绍中国国家标准《GB/T3280-2015不锈钢热轧钢板和钢带》中对14cr11mov锻件的要求和试验方法。
二、材料要求在生产14cr11mov锻件时,需要严格控制材料的质量和性能。
根据国家标准,材料的化学成分应符合表1的要求。
此外,材料的力学性能、工艺性能和外观等也应符合相关规定。
为了保证材料的性能,生产厂家应确保材料的质量稳定可靠。
三、生产工艺要求生产14cr11mov锻件时,应遵循一定的生产工艺流程。
首先,锻件应采用合理的锻造温度范围,并进行充分的锻造和热处理,以获得良好的组织和性能。
其次,锻件的生产应遵循国家相关标准和规范,如《GB/T6479-2000热轧无缝钢管》等。
在生产过程中,应控制好温度、压力、速度等工艺参数,以确保锻件的质量和性能。
四、试验方法为了检验14cr11mov锻件的质量和性能,国家标准规定了相应的试验方法。
主要包括拉伸试验、弯曲试验、冲击试验、化学成分分析等。
试验时应按照国家标准的规范和要求进行,以确保试验结果的准确性和可靠性。
同时,厂家应建立完善的试验检测体系,确保锻件的质量符合相关规定。
五、结论综上所述,国家标准对14cr11mov锻件的材料要求、生产工艺和试验方法等方面进行了明确的规定。
为了保证锻件的质量和性能,厂家应严格遵守相关规定,确保材料的质量稳定可靠,遵循合理的生产工艺流程,并做好相应的试验检测工作。
同时,厂家应加强与相关部门的沟通和合作,确保锻件的生产和使用符合相关标准和规范。
在实际应用中,用户应关注锻件的使用环境和条件,合理选择和使用锻件,以确保设备的稳定运行和安全可靠。
同时,相关部门应加强对锻件生产和使用的监管和管理,确保市场的规范和公平竞争。
最全钢铁企业制造流程教材

这样一个连续和离散混合的生产过程,包括许多的物理、化学变化,每个环 节都要受到生产与管理的控制。
2020/1/30
3
钢铁制造的工艺流程
工位连接线 - 连接线ID : int - 前向工位ID : int - 后继工位ID : int
26
炼钢物流仿真系统——模块划分
炼钢物流仿真系统
仿真建模子系统
通过组态建模方法,使用拖拉连线的交互式建模方式实现“所见即所得” 的生产布局;
仿真任务管理子系统
对仿真生产计划的管理:MES炉次计划仿真 、时间倒退、遗传算法、人 机交互的方式;
2020/1/30
11
转炉炼钢
2020/1/30
12
转炉设备
转炉炉体及转炉倾动系统 铁水、废钢、散状材料设备 氧枪提升机构 转炉烟气净化与回收设备
2020/1/30
13
转炉炼钢过程
上一炉出钢--倒完炉渣(或加添加剂)-- 补炉或溅渣--堵出 钢口--兑铁水--装废钢--下枪--加渣料(石灰、铁皮)-点火-- 熔池升温--脱P、Si 、Mn----降枪脱碳。
看炉口的火,听声音。看火亮度--加第二批(渣料)--提 枪化渣,控制“返干”。
降枪控制终点(FeO),倒炉取样测温,出钢。 技术水平高的炉长,一次命中率高。50%。(宝钢是付枪)
根据分析取样结果--决定出钢(或补吹)--脱氧、合金化 。
不要补吹的就是通常说的一次命中。
2020/1/3014Leabharlann 2020/1/3024
铝合金板锭铸造工艺技术操作规程讲解

铝合金板锭铸造工艺技术操作规程1 铸造工艺参数(详见附表)2 铸造前的准备(1)上岗前要穿戴好劳保用品。
(2)查看上班记录及当班工艺卡片,明确当班工作任务。
(3)检查铸造井、在线精炼装置、过滤盆、Al-Ti-B丝喂料机等是否正常,水盘翻板开启是否正常,底座升降是否正常,石墨转子及加热套管是否正常,发现问题及时处理。
(4)检查液压站油泵、冷却水泵、控制操作台是否正常,水阀门是否灵活、可靠,结晶器各进水管是否连接可靠、无漏水,检查结晶器油润滑系统是否正常,发现问题及时处理。
(5)检查制氮机组的氮气(或氩气瓶)纯度及压力是否符合要求。
(6)准备好生产所需导流管、浮漂、石棉绳、润滑油、硅酸铝岩棉等材料。
(7)将渣箱吊放至在线除气及过滤箱紧急排放口下。
(8)做好各种工器具的除锈、预热工作,确保加入的原材料干燥。
(9)结晶器检查①检查结晶器的形状尺寸,若尺寸误差超出要求范围,应及时调正。
②检查结晶器水孔是否堵塞,若堵塞,用细钢丝将水孔内的杂物捅掉,使其保持畅通。
③检查冷却水温、水压和流量是否正常,看泄流阀工作是否正常。
④检查铸造水盘翻板上的螺丝是否紧固,清理干净翻板上的杂物。
⑤检查活动溜槽导流管安装尺寸是否符合要求。
(10)将结晶器安装平稳牢固,确保结合部位密封严实,不漏水。
(11)检查结晶器内壁是否光滑,若不光滑,用湿布蘸柴油擦洗并用细纱布打磨光滑,然后用毛刷在结晶器内壁均匀涂上一层润滑油。
引锭头上表面涂刷润滑油。
(12)启动液压系统电源,关上井盖,使底座上升到结晶器内20mm 左右。
(13)用石棉绳将结晶器与引锭头之间的缝隙塞紧压平。
(14)将氮气+CC4管路和在线精炼装置连接牢靠,检查在线精炼装置是否漏气。
(15)陶瓷过滤板必须加热至600℃以上方可使用,安装时一定要将其四周塞实,加上压铁,以防在浇铸过程中浮起。
(16)在过滤盆和在线除气装置之间的流槽中安放好过滤网。
(17)调整活动溜槽位置,使导流管口正对结晶器底座中央,然后用硅酸铝岩棉和过滤布将活动流槽和过滤盆连接密封好。
1#板坯工艺技术操作规程
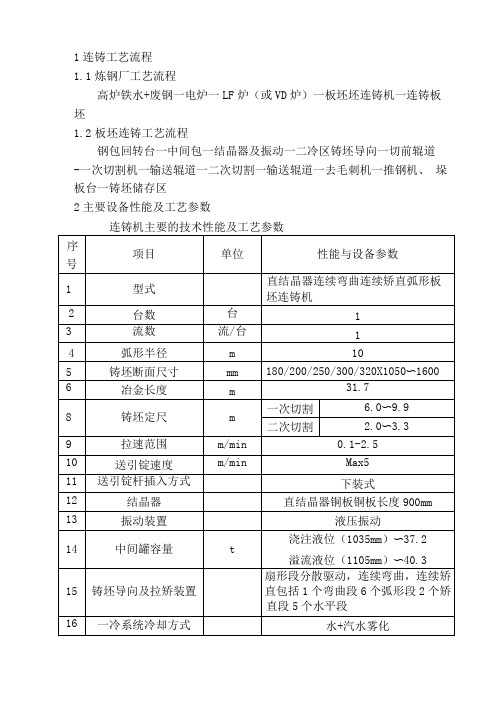
1连铸工艺流程1.1炼钢厂工艺流程高炉铁水+废钢一电炉一LF炉(或VD炉)一板坯坯连铸机一连铸板坯1.2板坯连铸工艺流程钢包回转台一中间包一结晶器及振动一二冷区铸坯导向一切前辊道-一次切割机一输送辊道一二次切割一输送辊道一去毛刺机一推钢机、垛板台一铸坯储存区2主要设备性能及工艺参数连铸机主要的技术性能及工艺参数3连铸钢水要求3.1对钢水化学成分要求到站钢水化学成分符合钢种要求。
品种钢连铸钢水必须经过炉外精炼,保证充分脱氧。
连铸钢水要求成份均匀,温度均匀,连浇炉次炉与炉之间成份波动范围小。
3.2钢水温度控制3.2.1液相线温度计算:液相线温度 T =1536.6-(90*C%+8*Si%+5*Mn%+30*P% +25*S%L+3*AL%+1.55*Cr%+4*Ni%+2.0*Mo%+18*Ti%+80*N%+5.0*Cu%)3.2.2中间罐中钢水过热度:中间罐钢水过热度,不同钢水分组如下:钢种分组中间罐钢水过热度A、低碳钢25±5℃B、包晶钢25±5℃C、中碳钢、中碳合金钢25±5℃D、高碳钢20±5℃E、超高碳钢15±5℃如中间包温度超过最大温度一一每超过5℃——拉速降低10%;如果中间包温度超过最大温度15℃——停止浇注!!3.2.3钢水罐中钢水温度:T罐二丁液+T中过+(30〜35) T罐:钢水罐中钢水温度 T::钢水液相线温度T±4中间罐中钢水过热度中1寸到达连铸平台的钢水温度应符合连铸浇铸的规定。
连铸中间罐钢水温度应符合各组钢种规定要求。
连铸第一炉相应提高5〜10℃,新包、挖补包不能作为第一炉。
对于新砌钢水罐的情况,到达连铸的钢水温度可提高5〜10℃。
钢水最终化学成分要符合钢种操作要点的要求。
钢水准备要严格按照《电弧炉工艺技术操作规程》和《精炼工艺技术操作规程》执行。
4浇注前的准备与参数调整4.1中间包准备与烘烤中间包的砌筑和工作层的涂抹要严格按照耐火材料工艺技术规程执行。
连铸用钢水炉外精炼工艺路线
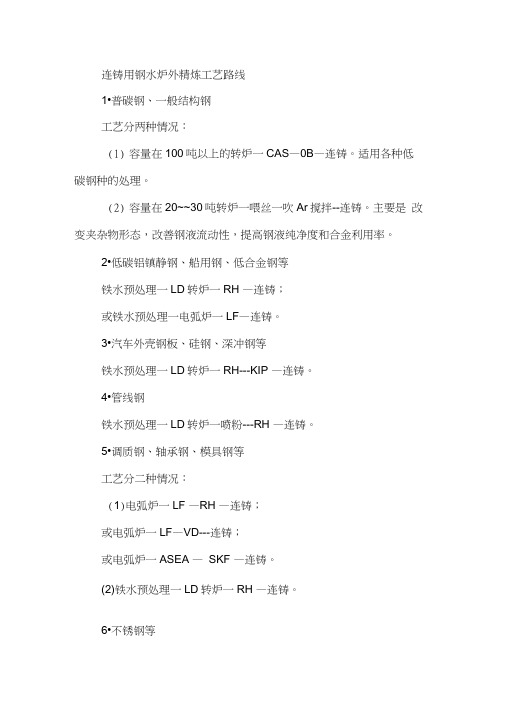
连铸用钢水炉外精炼工艺路线
1•普碳钢、一般结构钢
工艺分两种情况:
(1)容量在100吨以上的转炉一CAS—0B—连铸。
适用各种低碳钢种的处理。
(2)容量在20~~30吨转炉一喂丝一吹Ar搅拌--连铸。
主要是改变夹杂物形态,改善钢液流动性,提高钢液纯净度和合金利用率。
2•低碳铝镇静钢、船用钢、低合金钢等
铁水预处理一LD转炉一RH —连铸;
或铁水预处理一电弧炉一LF—连铸。
3•汽车外壳钢板、硅钢、深冲钢等
铁水预处理一LD转炉一RH---KIP —连铸。
4•管线钢
铁水预处理一LD转炉一喷粉---RH —连铸。
5•调质钢、轴承钢、模具钢等
工艺分二种情况:
(1)电弧炉一LF —RH —连铸;
或电弧炉一LF—VD---连铸;
或电弧炉一ASEA —SKF —连铸。
(2)铁水预处理一LD转炉一RH —连铸。
6•不锈钢等
工艺分二种情况:
(1)电弧炉一VOD —连铸;
(2)铁水预处理一LD转炉一AOD —连铸。
7•超低硫,磷,超纯净钢等
工艺分二种情况:
(1)铁水预处理一LD转炉一LF—喷粉一RH(OB)--喂丝一连
铸;
(2)电弧炉一LF —喷粉一RH(OB)--喂丝一连铸。
- 1、下载文档前请自行甄别文档内容的完整性,平台不提供额外的编辑、内容补充、找答案等附加服务。
- 2、"仅部分预览"的文档,不可在线预览部分如存在完整性等问题,可反馈申请退款(可完整预览的文档不适用该条件!)。
- 3、如文档侵犯您的权益,请联系客服反馈,我们会尽快为您处理(人工客服工作时间:9:00-18:30)。
2 0 1 7年 4月
特殊 钢
S PECI AL STEEL
Vo l | 38 .No. 2
A p i r l 2 0 1 7 ・1 9・
・
工艺技术 ・
3 O t E AF - L F - VD- 1 3 t 铸锭 流 程 生产 1 4 C r l M o钢 的 工 艺 实 践
Q i Q i n g h u a 一, Z h a o Z i w e n 一,H a n g We n k e , a n d Y a n g D e s h e n g ,
( 1 R e s e a r c h o f I n s t i t u t e , L a n z h o u L S E n e r g y E q u i p me n t I n s t i t u t e C o L t d , L a n z h o u 7 3 0 3 1 4 ; 2 G a n s u P r o v i n c e E n g i n e e r i n g R e s e a r c h C e n t e r f o r H i g h — E n d C a s t i n g a n d F o r g i n g s , L a n z h o u 7 3 0 3 1 4 )
州 兰石能源 装备 工程研究院有限公司 , 兰州 7 3 0 3 1 4 ; 2甘肃省高端铸锻件工程技术研究 中心 , 兰州 7 3 0 3 1 4 )
摘 要 试 验 1 4 C r l Mo钢 ( / %: 0 . 1 2 C , 0 . 5 7 S i , 0 . 4 8 M n , 0 . 0 0 3 P, 0 . 0 0 1 S , 1 . 2 0 C r , 0 . 4 2 M o , 0 . 0 1 V, 0 . 0 0 1 N b ,
Ab s t r a c t Th e me t a l l u r g i c a l p r o c e s s f l o ws h e e t o f 6 4 mm ×1 6 0 mm f o r g e d s l a b o f t e s t e d s t e e l 1 4 C r l Mo ( / %: 0 . 1 2 C. 0 . 5 7 S i ,0 . 4 8 Mn, 0 . 0 0 3 P。 0 . 0 o1 S,1 . 2 0 C r ,0 . 4 2 Mo.0 . o l V,0 . 0 0 1 N b,0 . 0 1 7 A l ,0 . 0 0 3 As 。0 . 0 01 S b.0 . 0 0 2 S n )i s
e n d l P l ≤0 . 0 0 2 %a n d e n d f C 1 0 . 0 7 % ~ 0 . 1 0 %. a d d i n g A l i n E A F t a p p i n g o f r p r e — d e o x i d i z a t i o n o f l i q u i d . L F m a i n t a i —
Pr a c t i c e o f Pr o c e s s f o r Pr o d u c t i o n o f S t e e l 1 4 Cr l Mo b y 3 0 t EAF- LF- VD- 1 3 t Ca s t i n g I n g o t Fl o ws h e e t
0 . 0 1 7 A 1 , 0 . 0 0 3 A s , 0 . 0 0 1 S b , 0 . 0 0 2 S n ) 6 4 m m x 1 6 0 m m锻坯的冶金工艺流程为 3 0 t E B T E A F — L F . V D . 1 3 t 铸锭. 锻造 。
通过采用优质废钢 , 控制 E A F终点 [ P ] ≤0 . 0 0 2 %, 终点 [ c] 0 . 0 7 %一 0 . 1 0 %, 出钢加 A l 预脱 氧 , L F白渣 时 间 ≥3 0
m i n , V D 6 7 P a >2 i 5 mi n , V D后 喂 0 . 3 5 k g / t C a — S i 线等 工艺措 施 , 钢中[ H] 为 1 . 5×1 0~, [ O] 1 7×1 0 ~, [ N] 7 0× 1 0~, 各类非金属夹杂物 为 0 . 5级 。经 9 3 0 o C空冷预备热处理 , 9 1 0 o C 水冷 + 7 0 0 o C空冷 回火 , 6 9 0 o C 4— 2 0 h炉 冷 模 拟焊后消除应力处理后 的该钢力学性能满足参考标准 N B / T 4 7 0 0 8 - 2 0 1 0的要求 。 关键词 1 4 C r l Mo 钢 3 0 t E A F - L F — V D 工艺实践 夹杂物 力学性 能
3 0 t EBT EAF- LF— VD一 1 3 t c a s t i n g i ng o t —f o r g i ng .W i t h t h e p r o c e s s me a s u r e s i nc l ud i n g us i ng qu a l i t y s c r a p.c o nt r o l l i n g EAF