铝合金管道焊接气孔产生原因分析及克服措施
铝合金焊接气孔产生的原因及解决方法

铝合金焊接气孔产生的原因及解决方法以铝合金焊接气孔产生的原因及解决方法为标题,本文将从气孔的形成原因、影响因素、解决方法等方面进行探讨。
一、气孔的形成原因1. 气体溶解度:铝合金焊接过程中,焊缝区域受到高温,气体在熔化池中容易溶解,当焊接材料凝固时,溶解的气体迅速析出形成气孔。
2. 氧化物和气体:铝合金表面常存在氧化物和气体,当焊接时没有进行适当的预处理,氧化物和气体会进入焊缝区域,造成气孔的形成。
3. 杂质和污染物:铝合金焊接前,如果没有进行彻底的清洁处理,焊接材料会受到杂质和污染物的影响,从而导致气孔的产生。
4. 焊接参数不合理:焊接电流、焊接速度、焊接温度等参数设置不当,会导致焊接熔池中的气体无法充分逸出,从而形成气孔。
二、影响因素1. 铝合金成分:铝合金的成分对气孔形成有一定影响,一般来说,铝合金中硅、铁等元素的含量越高,气孔的产生越容易。
2. 焊接方法:不同的焊接方法对气孔的产生也有影响,例如手工电弧焊、氩弧焊、激光焊等,焊接过程中的温度和气体环境都不同,会影响气孔的形成。
3. 焊接设备和工艺:焊接设备的性能和焊接工艺的选择都会对气孔的产生产生影响,例如焊接电流、焊接速度、焊接电极材料等。
4. 焊接环境:焊接环境中的湿度、气氛等因素也会对气孔的产生产生一定影响,潮湿的环境和含有大量氧气的环境都会增加气孔的形成。
三、解决方法1. 优化焊接工艺:合理选择焊接方法、设备和工艺参数,根据具体的铝合金材料和焊接要求进行调整,确保焊接过程中的温度、电流和速度等参数控制在合适范围内。
2. 预处理:在焊接前对铝合金材料进行充分的清洁处理,去除氧化物和污染物,减少杂质的影响。
3. 使用惰性气体保护:在焊接过程中,使用惰性气体进行保护,如氩气,可以有效减少氧气进入焊缝区域,减少气孔的产生。
4. 合理焊接顺序:在多道焊接时,合理安排焊接顺序,避免后续焊缝的气体进入前面焊缝,造成气孔的形成。
5. 加热预热和后热处理:对于一些特殊的铝合金材料,可以通过加热预热和后热处理等方式,改善焊接过程中的温度分布,减少气孔的产生。
铝和铝镁合金熔化极氩弧焊气孔及防止

铝和铝镁合金熔化极氩弧焊气孔及防止摘要:本文研究了铝和铝镁合金焊接过程中气孔的形成原因及防止方法,对熔化极氩弧焊气孔检测技术进行研究,通过优化焊接工艺参数、表面处理、保护气体能有效阻止氧化和气孔的发生。
关键词:铝和铝镁合金;熔化极氩弧焊气孔检测技术;气孔铝和铝镁合金作为广泛应用的轻质高强度材料,其焊接质量对于工业应用的安全性和可靠性至关重要。
然而,由于其特殊的物理和化学性质,焊接过程中容易产生气孔,从而影响焊缝的质量和强度。
1、铝和铝镁合金焊接的气孔形成原因1.1 气体溶解度铝和铝镁合金具有较高的气体溶解度,尤其是氢气。
在焊接过程中,当电弧加热金属时,吸附在金属内部的氢气逐渐释放,形成气体泡沫,导致气孔形成。
氢气的溶解度与焊接材料的温度和压力密切相关,因此,高温和高压条件下,气孔形成的风险更大。
1.2 氧化物含量铝和铝镁合金表面容易形成氧化物层,该氧化物层在焊接过程中会被熔化并混入焊缝中。
氧化物的存在不仅降低了焊接金属的表面张力,还会成为气体泡沫的核心,促进气孔形成。
因此,在焊接前必须对材料表面进行充分的清洁和处理,以减少氧化物含量。
1.3 焊接速度焊接速度过快可能导致熔融池冷却不均匀,使气体无法及时逸出,从而形成气孔。
适当降低焊接速度可以增加焊缝的热输入,有利于气体的释放和减少气孔的形成。
1.4 焊接参数焊接参数的选择对气孔的形成有直接影响。
过高的电流和电压会导致过度的金属熔化,同时增加气体的产生。
此外,不正确的电极角度和间隙也可能导致焊接过程中气孔的产生[1]。
1.5 氩气纯度氩气是常用的保护气体,在焊接过程中用于防止金属与空气中氧气发生反应。
然而,如果氩气纯度不高,含有杂质或水分,将增加气孔形成的风险。
1.6 气体流量控制适当的气体流量可以有效保护焊接区域,并帮助排除产生的气体。
过低的气体流量可能无法有效地将气体从焊缝中排出,从而导致气孔的形成。
图1 气孔图2、熔化极氩弧焊气孔检测技术熔化极氩弧焊气孔检测技术是在焊接过程或焊接后对焊缝中的气孔进行检测和评估的一系列方法和技术。
5356铝镁MIG焊表面有气孔是怎么回事

5356铝镁MIG焊表面有气孔是怎么回事在铝及铝合金MIG焊中,气孔是常见的一种缺陷。
要彻底清/除焊缝中的气孔是很难办到的,只能是大限度地减小其含量。
按其种类,铝焊缝中的气孔主要有表面气孔、弥散气孔、局部密集气孔、单个大气孔、根部链状气孔、柱状气孔等。
气孔不但会降低焊缝的致密性,减小接头的承载面积,而且使接头的强度、塑性降低,特别是冷弯角和冲击韧性降低更多,必加以防止。
产生原因有以下几点:
⑴气体保护不良,保护气体不纯;
⑵焊丝、焊件被污染;
⑶大气中的湿度过大;
⑷电弧不稳,电弧过长;
⑸焊丝伸出长度过长、喷嘴与焊件之间的距离过大;
⑹焊丝直径与坡口形式选择不当;
⑺在同一部位重复起弧,接头数太多。
在焊接过程中一定要挑选合适的焊丝,不同的铝板对于焊丝的需求不同,需挑选抗压,拉伸能力所匹配的焊丝,郑州船王铝焊丝17年专注研制生产铝及铝合金焊丝,目前在行业内已经能取代进口焊丝使用。
能为终端客户节约大量生产成本。
所以,要选物美价廉性、价比高的焊丝就选郑州船王铝焊丝。
船王焊材可以选择客户定制,根据您的焊接需求提供和母材匹配的焊丝,并有焊接工程师来为你解决焊接过程中的疑难问题,给您好的焊接体验,欢迎您前来咨询!可扫描上方二维码,更多焊接知识等着你哦!!。
焊接钢管焊缝气孔产生的原因及防治措施
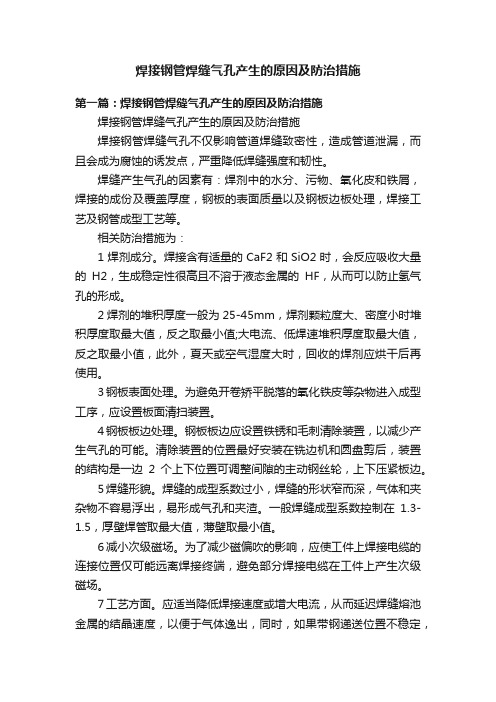
焊接钢管焊缝气孔产生的原因及防治措施第一篇:焊接钢管焊缝气孔产生的原因及防治措施焊接钢管焊缝气孔产生的原因及防治措施焊接钢管焊缝气孔不仅影响管道焊缝致密性,造成管道泄漏,而且会成为腐蚀的诱发点,严重降低焊缝强度和韧性。
焊缝产生气孔的因素有:焊剂中的水分、污物、氧化皮和铁屑,焊接的成份及覆盖厚度,钢板的表面质量以及钢板边板处理,焊接工艺及钢管成型工艺等。
相关防治措施为:1焊剂成分。
焊接含有适量的CaF2和SiO2时,会反应吸收大量的H2,生成稳定性很高且不溶于液态金属的HF,从而可以防止氢气孔的形成。
2焊剂的堆积厚度一般为25-45mm,焊剂颗粒度大、密度小时堆积厚度取最大值,反之取最小值;大电流、低焊速堆积厚度取最大值,反之取最小值,此外,夏天或空气湿度大时,回收的焊剂应烘干后再使用。
3钢板表面处理。
为避免开卷矫平脱落的氧化铁皮等杂物进入成型工序,应设置板面清扫装置。
4钢板板边处理。
钢板板边应设置铁锈和毛刺清除装置,以减少产生气孔的可能。
清除装置的位置最好安装在铣边机和圆盘剪后,装置的结构是一边2个上下位置可调整间隙的主动钢丝轮,上下压紧板边。
5焊缝形貌。
焊缝的成型系数过小,焊缝的形状窄而深,气体和夹杂物不容易浮出,易形成气孔和夹渣。
一般焊缝成型系数控制在1.3-1.5,厚壁焊管取最大值,薄壁取最小值。
6减小次级磁场。
为了减少磁偏吹的影响,应使工件上焊接电缆的连接位置仅可能远离焊接终端,避免部分焊接电缆在工件上产生次级磁场。
7工艺方面。
应适当降低焊接速度或增大电流,从而延迟焊缝熔池金属的结晶速度,以便于气体逸出,同时,如果带钢递送位置不稳定,应及时进行调整,杜绝通过频繁微调前桥或后桥维持成型,造成气体逸出困难。
焊接钢管焊缝夹渣产生的原因及防治措施焊后残留在焊缝中的熔渣称为夹渣,夹渣对接头的性能影响比较大。
因夹渣多数呈不规则状,会降低焊缝的塑性和韧性,其尖角会引起很大的应力集中,尖角顶点常导致裂纹产生,焊缝中的针形氧化物和磷化物夹渣会使焊缝金属变脆,降低力学性能,氧化铁及硫化铁夹渣容易使焊缝产生脆性。
铝合金焊接气孔产生的原因及解决方法
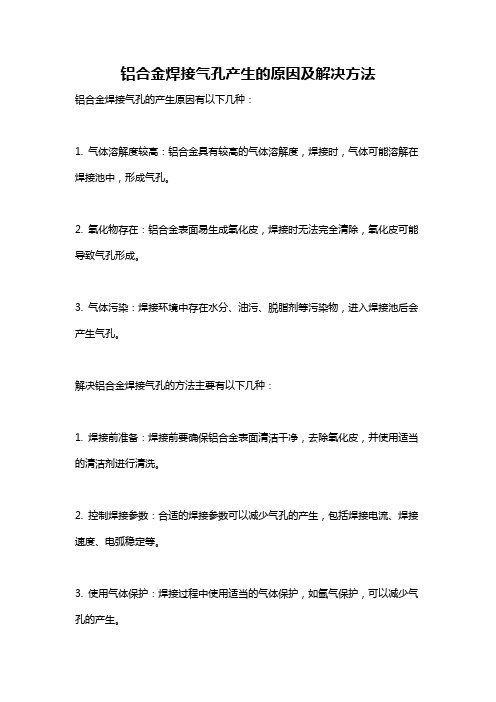
铝合金焊接气孔产生的原因及解决方法
铝合金焊接气孔的产生原因有以下几种:
1. 气体溶解度较高:铝合金具有较高的气体溶解度,焊接时,气体可能溶解在焊接池中,形成气孔。
2. 氧化物存在:铝合金表面易生成氧化皮,焊接时无法完全清除,氧化皮可能导致气孔形成。
3. 气体污染:焊接环境中存在水分、油污、脱脂剂等污染物,进入焊接池后会产生气孔。
解决铝合金焊接气孔的方法主要有以下几种:
1. 焊接前准备:焊接前要确保铝合金表面清洁干净,去除氧化皮,并使用适当的清洁剂进行清洗。
2. 控制焊接参数:合适的焊接参数可以减少气孔的产生,包括焊接电流、焊接速度、电弧稳定等。
3. 使用气体保护:焊接过程中使用适当的气体保护,如氩气保护,可以减少气孔的产生。
4. 选择合适的焊接材料:合适的焊丝和焊剂可以有效降低气孔的产生。
5. 严格控制焊接环境:避免焊接环境中存在水分、油污、脱脂剂等污染物。
总之,减少铝合金焊接气孔的关键是从焊接前的准备工作开始,包括清洁表面、选择合适的焊接参数和材料,以及控制焊接环境,保证焊接质量。
铝合金压铸件气孔产生原因及解决办法

铝合⾦压铸件⽓孔产⽣原因及解决办法 2008-12-13 13:28:51压铸件缺陷中,出现最多的是⽓孔。
⽓孔特征。
有光滑的表⾯,形状是圆形或椭圆形。
表现形式可以在铸件表⾯、或⽪下针孔、也可能在铸件内部。
(1)⽓体来源1)合⾦液析出⽓体—a与原材料有关b与熔炼⼯艺有关2)压铸过程中卷⼊⽓体—a与压铸⼯艺参数有关b与模具结构有关3)脱模剂分解产⽣⽓体—a与涂料本⾝特性有关b与喷涂⼯艺有关(2)原材料及熔炼过程产⽣⽓体分析铝液中的⽓体主要是氢,约占了⽓体总量的85%。
熔炼温度越⾼,氢在铝液中溶解度越⾼,但在固态铝中溶解度⾮常低,因此在凝固过程中,氢析出形成⽓孔。
氢的来源:1)⼤⽓中⽔蒸⽓,⾦属液从潮湿空⽓中吸氢。
2)原材料本⾝含氢量,合⾦锭表⾯潮湿,回炉料脏,油污。
3)⼯具、熔剂潮湿。
(3)压铸过程产⽣⽓体分析由于压室、浇注系统、型腔均与⼤⽓相通,⽽⾦属液是以⾼压、⾼速充填,如果不能实现有序、平稳的流动状态,⾦属液产⽣涡流,会把⽓体卷进去。
压铸⼯艺制定需考虑以下问题:1)⾦属液在浇注系统内能否⼲净、平稳地流动,不会产⽣分离和涡流。
2)有没有尖⾓区或死亡区存在3)浇注系统是否有截⾯积的变化?4)排⽓槽、溢流槽位置是否正确?是否够⼤?是否会被堵住?⽓体能否有效、顺畅排出?应⽤计算机模拟充填过程,就是为了分析以上现象,以作判断来选择合理的⼯艺参数。
(4)涂料产⽣⽓体分析涂料性能:如发⽓量⼤对铸件⽓孔率有直接影响。
喷涂⼯艺:使⽤量过多,造成⽓体挥发量⼤,冲头润滑剂太多,或被烧焦,都是⽓体的来源。
(5)解决压铸件⽓孔的办法先分析出是什么原因导致的⽓孔,再来取相应的措施。
1)⼲燥、⼲净的合⾦料。
2)控制熔炼温度,避免过热,进⾏除⽓处理。
3)合理选择压铸⼯艺参数,特别是压射速度。
调整⾼速切换起点。
4)顺序填充有利于型腔⽓体排出,直浇道和横浇道有⾜够的长度(>50mm),以利于合⾦液平稳流动和⽓体有机会排出。
铝合金铸造出现气孔的原因分析与解决办法

铝合金铸造出现气孔的原因分析与解决办法核心提示:简单来说,气孔分两类,一类是析出性气孔,即铝液在凝固过程中因气体溶解度的变化而析出,老大在这方面说的很详细;另一类就是卷入性气孔,与铝液无关,主要是铝液填充过程中因紊流包卷在产品中的空气及涂料或型腔内未干的水分。
卷入性气孔主要与浇排系统的合理性密切相关,只有涂料和水,纯属操作不当。
至于说在喷丸后出现,应该主要与高速转换点的位置关联密切。
问题1:材料ACD12铝合金压铸件在机加工或喷砂后出现较多气孔的问题,这一技术上问题困扰着我们回复:1 设备抽真空设备是什么设备啊?压铸件的气孔问题好像还没有办法解决只能通过调节压铸参数,模温和修改相关的模具温度使气孔在一个合理的等级范围2 一.人的因素:1.脱模剂是否噴得太多? 因脱模济发气量大,用量过多时,浇注前未燃尽,使挥发气体被包在铸件表层。
所以在同一条件下,某些工人操作时会产生较多的气孔的原因之一。
选用发气量小的脱模济,用量薄而均匀,燃净后合模。
2未经常清理溢流槽和排气道?3开模是否过早? 是否对模具进行了预热?各部位是否慢慢均匀升温,使型腔、型芯表面温度为150℃~200℃。
4刚开始模温低时生产的产品有无隔离?5如果无预热装置时是否使用铝合金料慢速推入型腔预热或用其它方法加热?6是否取干净的铝液,有无将氧化层注入压室? 7倒料时,是否将勺子靠近压室注入口,避免飞溅、氧化或卷入空气降温等。
8金属液一倒入压室,是否即进行压射,温度有无降低了?。
9冷却与开模,是否根据不同的产品选择开模时间?10有无因怕铝液飞出(飞水),不敢采用正常压铸压力?更不敢偿试适当增加比压。
?11操作员有无严格遵守压铸工艺?12有无采用定量浇注?如何确定浇注量?二.机(设备、模具、工装)的因素: 主要是指模具质量、设备性能。
1压铸模具设计是否合理,会否导致有气孔?压铸模具方面的原因:1.浇口位置的选择和导流形状是否不当,导致金属液进入型腔产生正面撞击和产生旋涡。
MIG焊中气孔缺陷和焊缝裂纹的原因及防范措施

MIG焊中气孔缺陷和焊缝裂纹的原因及防范措施MIG焊中气孔缺陷原因及防范措施:在铝及铝合金MIG焊中,气孔是最常见的一种缺陷。
要彻底清除焊缝中的气孔是很难办到的,只能是最大限度地减小其含量。
按其种类,铝焊缝中的气孔主要有表面气孔、弥散气孔、局部密集气孔、单个大气孔、根部链状气孔、柱状气孔等。
气孔不但会降低焊缝的致密性,减小接头的承载面积,而且使接头的强度、塑性降低,特别是冷弯角和冲击韧性降低更多,必须加以防止。
1.、产生原因:⑴气体保护不良,保护气体不纯;⑵焊丝、焊件被污染;⑶大气中的绝对湿度过大;耐磨焊条;⑷电弧不稳,电弧过长;⑸焊丝伸出长度过长、喷嘴与焊件之间的距离过大;⑹焊丝直径与坡口形式选择不当;⑺在同一部位重复起弧,接头数太多。
2、防止措施:⑴保证气体质量,适当增加保护气体流量,以排除焊接区的全部空气,消除气体喷嘴处飞溅物,使保护气流均匀,焊接区要有防止空气流动措施,防止空气侵入焊接区,保护气体流量过大,要适当适当减少流量;阀门进口泵。
⑵焊前仔细清理焊丝、焊件表面的油、污、锈、垢和氧化膜,采用含脱氧剂较高的焊丝;⑶合理选择焊接场所;⑷适当减少电弧长度;⑸保持喷嘴与焊件之间的合理距离范围;⑹尽量选择较粗的焊丝,同时增加工件坡口的钝边厚度,一方面可以允许允许使用大电流,也使焊缝金属中焊丝比例下降,这对降低孔率是行之有效的;⑺尽量不要在同一部位重复起弧,老板娘重复起弧时要对起弧处进行打磨或刮除清理;一道焊缝一旦起弧后要尽量焊长些,不要随意断弧,以减少接头量,在接头处需要有一定的焊缝重叠区域。
铝及铝合金MIG焊焊缝裂纹的原因及防范措施:铝及铝合金焊缝中的裂纹是在焊缝金属结晶过程中产生的,称为热裂纹,又称结晶裂纹。
其形式有纵向裂纹、横向裂纹(往往扩展到基体金属),还有根部裂纹、弧坑裂纹等等。
裂纹将使结构强度降低,甚至引起整个结构的突然破坏,因此是完全不允许的。
1、产生原因:⑴焊缝隙的深宽比过大;⑵焊缝末端的弧坑冷却快;⑶焊丝成分与母材不匹配;⑷操作技术不正确。
铝合金焊接气孔分析及预防措施

铝合金焊接气孔分析及预防措施摘要:本文针对SLM成形的TC4铝合金进行电子束焊接工艺研究,开展电子束焊接工艺参数优化试验,通过工艺优化降低焊缝内部的气孔缺陷产生概率和控制气孔缺陷的数量和尺寸,分析气孔生成的原因及其控制方法,获得力学性能优良的接头,为激光选区熔化成形+电子束焊接的混合制造方法在航空制造领域的应用提供技术基础。
关键词:铝合金;焊接气孔1 试验材料及方法采用SLM成形的TC4铝合金试板化学成分如表1所示,在SLM成形过程中,铺层的TC4合金粉末发生快速的熔化、凝固过程,加热冷却速度极快,最终形成均匀的针状马氏体α′组织。
本研究采用ZD150–15MH CV3M电子束焊机设备。
切割制备SLM成形的XY和XZ两方向的焊接试板,尺寸为200mm×150mm×9mm。
针对焊接试板进行电子束焊接工艺试验,参数如表2所示。
切割制备接头金相试样,采用Leica DM6000M金相显微镜进行焊缝形貌特征分析。
针对满足质量要求的焊接试板,采用线切割设计制备接头拉伸、疲劳试验件(图1),借助Z100电子万能材料试验机进行室温拉伸、疲劳试验。
2 试验结果与讨论在不同的聚焦电流下采用匹配的焊接电流进行初步试验,试板焊缝成形可知,1#~4#工艺焊缝(长度100mm)成形不均匀、稳定,正面均存在咬边(图2);2#、4#工艺焊缝表面宽度约为4mm,宽度较为适中。
图3为焊接接头形貌,观察分析表明,成形TC4铝合金近缝母材区的气孔缺陷较多,而焊缝区气孔缺陷较少,因此,电子束焊接可消除SLM成形所造成的低致密度气孔和空隙。
表1 SLM成形的TC4铝合金化学成分表2 SLM成形TC4铝合金焊接工艺参数图1 室温下拉伸性能、疲劳性能试验件基于上述焊缝成形、接头形貌特征的结果分析,同步进行了SLM成形工艺优化及焊接工艺参数的优化(表2中5#~12#参数),采用了散焦电子束修饰焊接(束流5mA)工艺方法,优化后焊接接头形貌特征及显微组织如图4所示,后续将详细探讨工艺优化过程。
铝合金激光焊接气孔解决方案-概述说明以及解释

铝合金激光焊接气孔解决方案-概述说明以及解释1. 引言1.1 概述在铝合金激光焊接过程中,气孔问题一直是一个令人头痛的难题。
气孔的存在会导致焊接接头的强度下降,从而影响整个铝合金结构的使用性能。
因此,寻找有效解决气孔问题的方法和技术一直是焊接工程师们关注的焦点。
本文将重点探讨铝合金激光焊接气孔的解决方案。
首先,将介绍铝合金激光焊接的应用背景,说明其在工业生产中的重要性和广泛应用。
随后,详细分析气孔在铝合金激光焊接中的问题,探讨气孔形成的原因和对焊接接头性能的影响。
为了解决气孔问题,本文将介绍一些常用的方法和技术。
这些方法包括焊接参数的优化调整、焊接材料的选择和预处理、气体保护技术的改善等。
通过对比实验和案例分析,将分析这些方法的优缺点,并给出建议和指导。
在解决气孔问题的过程中,我们需要加强焊接工艺的控制和质量管理,提高焊接技术人员的素质和水平。
最后,在结论部分,将总结气孔问题的解决方案,并对未来的研究展望进行探讨。
希望通过本文的研究和分析,能够为铝合金激光焊接气孔问题的解决提供一些有价值的参考和建议。
只有通过不断的探索和创新,才能不断改进铝合金激光焊接技术,提高焊接接头的质量和性能。
文章结构:本文将按照以下结构进行介绍铝合金激光焊接气孔解决方案:1. 引言1.1 概述1.2 文章结构1.3 目的2. 正文2.1 铝合金激光焊接的应用背景2.2 气孔在铝合金激光焊接中的问题2.3 解决气孔问题的方法和技术3. 结论3.1 总结气孔问题的解决方案3.2 对未来研究的展望3.3 结束语在引言部分,我们将对铝合金激光焊接及其在工业领域的应用进行概述,并明确本文的目的。
接着,在正文部分的第一部分,将详细介绍铝合金激光焊接的应用背景,包括它在汽车制造、航空航天等行业的重要性和广泛应用。
然后,在第二部分,将重点探讨气孔在铝合金激光焊接中的问题,分析气孔对焊接质量的影响,并介绍其形成的原因。
针对气孔问题,第三部分将介绍解决气孔问题的方法和技术,包括工艺参数的优化、材料选用、预处理措施等。
铝合金MIG焊气孔成因及消除措施

铝合金MIG焊气孔成因及消除措施原创 2015-06-08 彭勇军1. 概述铝合金MIG焊时,焊缝容易产生气孔,这由于焊丝是以细小熔滴形式通过弧柱进入熔池,由于弧柱温度高,且熔滴比表面积大,有利于熔敷金属吸收氢;同时,MIG焊时的熔池熔化母材的深度较大,由于铝合金金属的密度小,冷却速度快,不利于熔池中的气泡逸出,导致焊缝产生气孔。
从焊接生产来分析,导致焊缝产生气孔主要有焊接现场湿度的控制;焊接区的水分、脏物和氧化膜;焊接保护气体的纯度;焊丝表面是否受潮和氧化;焊接设备的影响;焊工的操作技能等。
为查找现场焊缝产生气孔的原因,我们通过焊接性试验及采取相应的检验方法来验证解决措施的有效性。
2. 现场情况及原因分析(1)现场的湿度控制现场采用大型空调进行整体除湿和控温。
现场湿度在45%~60%内,符合铝合金焊接生产湿度控制要求。
由于下午工作结束后,大型空调会自动关闭,到了次日上班时间再启动。
这样,造成在非工作时间段,现场的盘状焊丝的外表层受潮。
(2)焊丝?首先,焊丝储存库房面积45~50m2,高3.2~3.5m,库房空间偏大,且靠窗户部位与其他房间能够形成少量的空气对流。
库房内有一台含水箱除湿机,除湿机降湿形成的水仍然存在于库房中。
这样,造成库房内的焊丝除湿效果有限。
其次,现场使用的盘状焊丝有三家品牌。
三家焊丝焊接出来的焊缝都存在气孔超标的情况。
由于铝合金焊丝易受大气条件的影响,焊丝在海运和陆地的物流过程中,存在包装破损的可能。
包装破损将导致盘状焊丝被受潮和氧化。
从盘状铝合金焊丝生产之日算起,铝合金焊丝在外包装不破损的情况下,存储时限有一年和两年的之分。
焊丝超过期限后,焊丝在使用前应全面检查:即焊丝是否吸潮或氧化应通过焊接性试验来检测焊缝气孔是否超标,确认超过期限能否用于焊接生产。
存储时限为一年的焊丝,其内包装材料为透明的塑料薄膜;存储时限为两年的焊丝,其内包装材料为铝制压膜。
由于三家品牌焊丝为透明的塑料薄膜包装,存储时限不足一个月时间就将到期,不能完全排除焊丝导致气孔产生这一因素。
铝合金焊接焊缝气孔产生的原因分析及预防措施
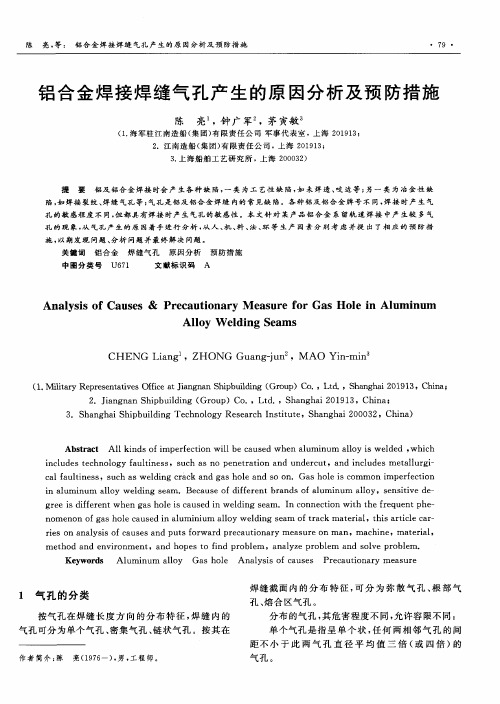
Ab s t r a c t A1 l k i n d s o f i mp e r f e c t i o n wi l l b e c a u s e d wh e n a l u mi n u m a l l o y i S we l d e d。 wh i c h i n c l u d e s t e c h n o l o g y f a u l t i n e s s ,s u c h a s n o p e n e t r a t i o n a n d u n d e r c u t ,a n d i n c l u d e s me t a l l u r g i —
c a l f a u l t i n e s s ,s u c h a s we l d i n g c r a c k a n d g a s h o l e a n d S O o n .Ga s h o l e i s c o mm o n i mp e r f e c t i o n
此类气孔多与氧化膜夹杂物伴生气孔壁与氧化膜夹杂物具有相同的形态有时两者联生在一起如图焊接试验证明此类气孔与铝材对接间隙处表面残存的潮湿含水氧化膜碳氢化合物污染有防此类气孔必须在焊前彻底清理坡口对接表面或将对接接头制成反面大气压下氢在铝一镁合金中的溶解度口使此类链状氧化膜气孔移至垫板槽内或焊缝有效厚度以外以便不影响焊接强度
CHE NG Li a n g ,Z HONG Gu a n g - j u n ,M AO Yi n — mi n 。
焊接气孔产生的原因

焊接气孔是在焊接过程中出现的小孔或气泡。
它们会对焊接接头的质量产生负面影响,因此了解气孔产生的原因是很重要的。
以下是一些常见的焊接气孔产生的原因:
1. 水分和油脂:焊接区域存在水分或油脂会导致气孔的形成。
这些杂质在焊接时会蒸发并形成气体,造成气孔。
2. 气体释放:焊接电弧产生高温,在焊接过程中,焊丝和焊件中的材料可能会释放气体,例如水分、氧化物和揮发性成分等。
这些气体在焊接过程中无法完全逸出,形成气孔。
3. 材料表面污染:焊接材料表面的污染物,如氧化物、锈蚀、油脂等,会阻碍焊接区域的气体排出,导致气孔的形成。
4. 不合适的焊接参数:焊接参数的选择不当也会导致气孔的产生。
例如,焊接电流过低或焊接速度过快会导致焊缝区域没有足够的熔池形成,造成气孔。
5. 不良焊接材料:使用质量不佳的焊丝、焊剂或焊接材料也可能导致气孔的产生。
这些材料可能含有过多的杂质或不良的化学成分,影响焊接质量。
6. 不合适的焊接技术:焊工的焊接技术和技能也会对气孔的形成产生影响。
焊接操作不稳定、焊接枪角度不正确或焊接速度不均匀等因素都可能导致气孔的产生。
为了减少气孔的产生,需要注意以下几点:
-确保焊接区域干燥和清洁,避免水分和油脂的存在。
-使用适当的焊接参数,保证焊接区域有足够的熔池形成。
-使用高质量的焊接材料,避免含有过多杂质的材料。
-掌握良好的焊接技术,包括稳定的焊接操作和正确的焊接枪角度。
-定期检查和清理焊接设备,确保其正常运行和调整。
通过遵循这些原则和注意事项,可以减少焊接气孔的产生,提高焊接质量。
铝合金TIG焊气孔缺陷的类型和产生原因的分析

铝合金TIG焊气孔缺陷的类型和产生原因的分析摘要:气孔是铝合金TIG焊焊接工艺中常见的缺陷,本文结合焊接实践,对气孔缺陷类型和气孔形成原因进行了深入分析,并总结出了其产生的规律,为采取何种工艺措施,避免气孔的产生,积累了一定的技术资料。
关键词:铝合金,TIG焊接,气孔,焊缝铝合金由于比重轻,强度高,可焊性好以及良好的加工成型性能、耐腐蚀性能,被广泛用于各种结构的焊接,但焊接过程中,气孔是最常见的焊接缺陷,气孔的出现不仅影响焊缝质量,而且还会降低焊接接头的承载能力,使焊缝的塑性,冲击强度降低很多,以致于焊缝致密性遭破坏,因此了解气孔类型,产生的条件,掌握防止气孔产生措施,是获得高质量焊接接头的重要条件。
1.气孔的特征和类型气孔是焊接时熔池中的气泡在凝固时未能逸出而残留在焊缝金属中所形成的空穴,是TIG焊中常见的也是主要的一种焊接缺陷。
其形状有球形、椭圆形、旋风形、条虫形等。
在焊缝内部的称内部气孔,露在焊缝表面的称外部气孔。
气孔的大小不等有时是单个的,有时是密集在一起或是沿焊缝连续分布。
根据其分布特点和形貌特征,可分为集中焊缝中部和根部的密集气孔、接近焊缝表层的皮下气孔、以及存在于熔合区边界的氧化膜气孔;有球形、椭圆形、条虫形等。
(1)局部密集气孔:熔池结晶时,氢的脱溶析出可能聚集在晶枝间大量存在的微小孔穴,形成密集的微小气孔,熔池完全结晶时,气泡未能上浮逸出,形成局部密集气孔。
(2)皮下气孔:焊缝结晶过程中,当液态铝从高温冷却接近凝固点时,液态铝中的氢由于溶解度下降而脱溶形成气泡,在氢气泡上浮过程中,上浮速度低于熔池冷却速度,已上浮至熔池表面附近的氢气泡来不及逸出而残留在焊缝表层,从而形成皮下气孔。
(3)氧化膜气孔:在熔合区的边界处,由于母材坡口附近的氧化膜未能熔化,氧化膜有很强的吸水性,氧化膜在电弧高温作用下分解析出氢,并在氧化膜上形成气泡,熔池结晶后形成气孔,多数呈圆形或椭圆形,分布不均。
2.铝合金焊缝气孔产生原因的分析焊件在焊前要进行表面清洗,除锈、去油污、去灰尘等杂质;钨极承载电流的能力有限,过大的电流会引起钨棒的熔化和蒸发,其微粒有可能进入熔池而出现夹钨,所以TIG焊的焊接电流会受到钨棒限制,故焊接速度较小,生成效率较低;TIG焊采用的氩气纯度较高,通常要求达到99.9%以上,且氩弧焊机又较复杂,因此TIG焊的成本较高;氩弧受周围气流影响较大,不适宜在室外和有风处进行操作。
铝镁合金管道现场焊接气孔产生原因及防止措施
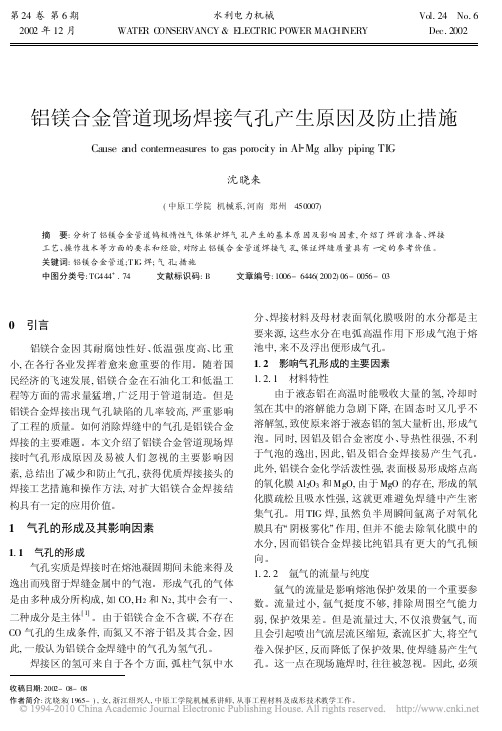
中图分类号: TG444+ . 74
文献标识码: B
文章编号: 1006- 6446( 2002) 06- 0056- 03
0 引言
铝镁合金因 其耐腐蚀性好、低温强 度高、比 重 小, 在各行各业发挥着愈来愈重要的作用。随着国 民经济的飞速发展, 铝镁合金在石油化工和低温工 程等方面的需求量猛增, 广泛用于管道制造。但是 铝镁合金焊接出现气孔缺陷的几率较高, 严重影响 了工程的质量。如何消除焊缝中的气孔是铝镁合金 焊接的主要难题。本文介绍了铝镁合金管道现场焊 接时气孔形成原因及易被人们 忽视的主要影 响因 素, 总结出了减少和防止气孔, 获得优质焊接接头的 焊接工艺措施和操作方法, 对扩大铝镁合金焊接结 构具有一定的应用价值。
2. 1 焊前准备
氩气的纯度对焊接质量也有较大的影响。氩气 2. 1. 1 坡口加工及焊件清理
纯度低、杂质多, 可增加弧柱气氛中氢的含量, 同时
坡口用铣刀或锉刀 加工, 均采用 V 形 坡口, 如
也降低 阴极雾化 效果。
图 1 所示。衬环、焊件坡口附近内外表面 50mm 范
1. 2. 3 焊接工艺 焊件坡口准备、组对方式和焊接工艺参数的选
第 24 卷 第 6 期 2002 年 12 月
水利电力机械 WATER CONSERVANCY & ELECTRIC POWER MACHINERY
Vol. 24 No. 6 Dec. 2002
铝镁合金管道现场焊接气孔产生原因及防止措施
Cause and contermeasures to gas porocity in Al Mg alloy piping TIG
收稿日期: 2002- 08- 08 作者简介: 沈晓来( 1965- ) , 女, 浙江绍兴人, 中原工学院机械系讲师, 从事工程材料及成形技术教学工作。
焊接气孔产生的主要原因

焊接气孔产生的主要原因:1、电弧焊接中所产生的气体里含有过量的氢气及一氧化碳所造成的;2、母材钢材中含硫量过多;3、焊剂的性质和烘赔温度不够高;4、焊接部位冷却速度过快;5、焊接区域有油污、油漆、铁锈、水或镀锌层等造成;6、空气中潮气太大、有风;7、电弧发生偏吹。
CO2电弧焊时,由于熔池表面没有熔渣盖覆,CO2气流又有较强的冷却作用,因而熔池金属凝固比较快,但其中气体来不及逸出时,就容易在焊缝中产生气孔。
可能产生的气孔主要有3种:一氧化碳气孔、氢气孔和氮气孔。
1、一氧化碳气孔产生CO气孔的原因,主要是熔池中的FeO和C发生如下的还原反应:FeO+C==Fe+CO该反应在熔池处于结晶温度时,进行得比较剧烈,由于这时熔池已开始凝固,CO气体不易逸出,于是在焊缝中形成CO气孔。
如果焊丝中含有足够的脱氧元素Si和Mn,以及限制焊丝中的含碳量,就可以抑制上述的还原反应,有效地防止CO气孔的产生。
所以CO2电弧焊中,只要焊丝选择适当,产生CO气孔的可能性是很小的。
2、氢气孔如果熔池在高温时溶入了大量氢气,在结晶过程中又不能充分排出,则留在焊缝金属中形成气孔。
电弧区的氢主要来自焊丝、工件表面的油污及铁锈,以及CO2气体中所含的水分。
油污为碳氢化合物,铁锈中含有结晶水,它们在电弧高温下都能分解出氢气。
减少熔池中氢的溶解量,不仅可防止氢气孔,而且可提高焊缝金属的塑性。
所以,一方面焊前要适当清除工件和焊丝表面的油污及铁锈,另一方面应尽可能使用含水分低的CO2气体。
CO2气体中的水分常常是引起氢气孔的主要原因。
另外,氢是以离子形态溶解于熔池的。
直流反极性时,熔池为负极,它发射大量电子,使熔池表面的氢离子又复合为原子,因而减少了进入熔池的氢离子的数量。
所以直流反极性时,焊缝中含氢量为正极性时的1/3~1/5,产生氢气孔的倾向也比正极性时小。
3、氮气孔氮气的来源:一是空气侵入焊接区;二是CO2气体不纯。
试验表明:在短路过渡时CO2气体中加入φ(N2)=3%的氮气,射流过渡时CO2气体中加入φ(N2)=4%的氮气,仍不会产生氮气孔。
用TIG焊接铝管产生气孔的原因探讨

为清除管内壁的氧化膜, 必须采用铝专用焊剂。
图 2 坡口
焊剂功能如下: (1) 容易熔化, 且熔点比母材和填充材料
我们总共焊接了 500 道水平固定位置的焊 口, 通过外观检查, 管内壁焊缝中心处有一条 融合线, 这条线时深、时浅, 不影响外观成形。 将外观检查合格的部分焊口通过 X 射线检查, 按 JB T 6895- 93 附录 的要求, 拍片 20 道坡 口, 无一道坡口合格。 焊缝缺陷均是底部接头 气孔。我们把有气孔的焊口在焊缝两侧锯开, 并 在底部接头处用锉刀锉掉簿簿的一层, 便可见 气孔, 继续往下锉, 可以看见焊缝内部气孔 (见图 3)。
为消除焊缝气孔, 我们采取如下措施: 首 先, 考虑将氧化膜的清除由化学清洗改为机械 清理, 这样氧化膜可以彻底清除掉, 电弧停留 时间可以缩短, 减少氢气的溶入量。 其结果确 实比化学清洗效果好, 用这种清理方法焊接
焊缝冷却时, 气体的逸出不受阻碍, 焊缝就不 会有气孔了。 实际焊接中, 采用焊剂连续焊接 水平固定位置管 4 道坡口, 通过 X 射线检查, 底部接头均无气孔。
使用焊剂后, 气孔问题大有改善, 焊前将
焊剂与水调成糊状, 涂在管内壁坡口上, 也可
将焊丝烧热后沾取焊剂进行施焊, 因焊剂具有
溶解AL 2O 3 功能, 焊接时管内壁AL 2O 3 氧化膜
图 3 焊缝内部气孔分布
已清除掉, 也失去了氢的来源之一, 即使起弧 停留时间长, 水分解出的氢溶解到焊缝中, 在
表5
参 数
部 位
结晶器
段
段
P
70%
70%
100%
I
10s
6s
10s
5 效果
本系统投产后, 效果非常明显, 主要表现 在:
气孔产生的原因
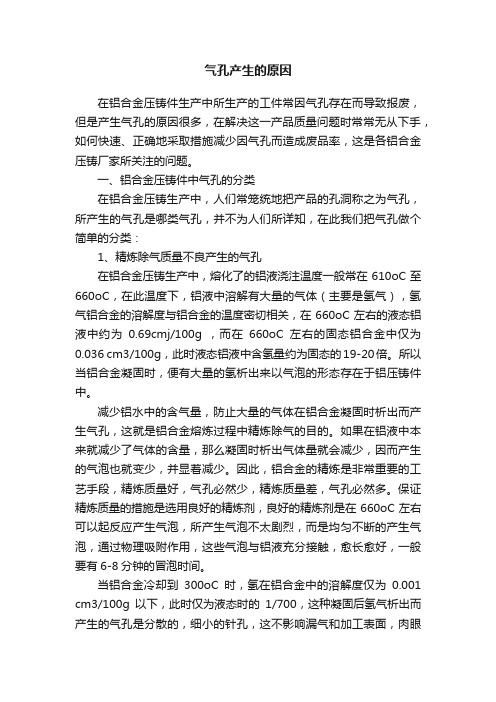
气孔产生的原因在铝合金压铸件生产中所生产的工件常因气孔存在而导致报废,但是产生气孔的原因很多,在解决这一产品质量问题时常常无从下手,如何快速、正确地采取措施减少因气孔而造成废品率,这是各铝合金压铸厂家所关注的问题。
一、铝合金压铸件中气孔的分类在铝合金压铸生产中,人们常笼统地把产品的孔洞称之为气孔,所产生的气孔是哪类气孔,并不为人们所详知,在此我们把气孔做个简单的分类:1、精炼除气质量不良产生的气孔在铝合金压铸生产中,熔化了的铝液浇注温度一般常在610oC至660oC,在此温度下,铝液中溶解有大量的气体(主要是氢气),氢气铝合金的溶解度与铝合金的温度密切相关,在660oC左右的液态铝液中约为0.69cmj/100g ,而在660oC左右的固态铝合金中仅为0.036 cm3/100g,此时液态铝液中含氢量约为固态的19-20倍。
所以当铝合金凝固时,便有大量的氢析出来以气泡的形态存在于铝压铸件中。
减少铝水中的含气量,防止大量的气体在铝合金凝固时析出而产生气孔,这就是铝合金熔炼过程中精炼除气的目的。
如果在铝液中本来就减少了气体的含量,那么凝固时析出气体量就会减少,因而产生的气泡也就变少,并显着减少。
因此,铝合金的精炼是非常重要的工艺手段,精炼质量好,气孔必然少,精炼质量差,气孔必然多。
保证精炼质量的措施是选用良好的精炼剂,良好的精炼剂是在660oC左右可以起反应产生气泡,所产生气泡不太剧烈,而是均匀不断的产生气泡,通过物理吸附作用,这些气泡与铝液充分接触,愈长愈好,一般要有6-8分钟的冒泡时间。
当铝合金冷却到300oC时,氢在铝合金中的溶解度仅为0.001 cm3/100g以下,此时仅为液态时的1/700,这种凝固后氢气析出而产生的气孔是分散的,细小的针孔,这不影响漏气和加工表面,肉眼基本看不见。
而在铝液凝固时因氢气析出所产生的气泡比较大,多在铝液最后凝固的部位,虽然也分散,但这些气泡常常导致渗漏。
严重时常导致工件报废。