气输送管道体积型缺陷安全评定方法
含缺陷压力管道的安全评定技术

含缺陷压力管道的安全评定技术摘要:压力管道主要是用来输送液体或者气体的设备,管道运输在多个领域都有广泛的应用。
由于管道运输介质的特殊性,对管道的质量安全有极高的要求,但是管道应用过程中,因为受到腐蚀、外部损伤、制管缺陷等因素的影响,就容易引起管道开裂、泄漏,进而发生爆炸、火灾等安全事故。
所以,对于含缺陷的压力管道要通过合理的技术进行安全评定,判断管道是否能够应用,这样才能有效的保证管道运输的安全。
关键词:安全评定;含缺陷压力管道;技术应用含缺陷压力管道能不能继续应用,对管道运行的经济性和安全性都有较大的影响,因此,需要通过使用合理的技术进行安全评定,明确其是否能够继续进行使用。
有关安全评定的方法国际上有很多,我国也发布了有关含缺陷压力容器安全评定的国家标准,对压力管道的安全评定也适用。
1.缺陷种类对管道含缺陷的种类以及其表现形式有了充分的认识,才能更好的选择适合的安全评定方法。
从缺陷的不同角度来讲,可以分为不同的种类。
1.1不同性质的缺陷按照缺陷性质的不同,管道缺陷主要表现有孔穴、熔合不全、裂纹、夹杂、焊接不足等。
具体来讲,孔穴主要是由于在进行管道焊接时,熔化焊缝吸收的气体没有在冷却前排出而在内部形成,表现形式有气孔和缩孔。
裂纹主要是焊接接头因遭到破坏而产生缝隙,有层状裂纹、冷裂纹、热裂纹等。
1.2不同位置的缺陷按照缺陷所在位置的不同,主要分为内外表面缺陷、穿透缺陷、隐藏缺陷。
内外表面缺陷就是在管道壁的内外侧出现的缺陷。
穿透缺陷是指贯穿管道内外壁的缺陷。
而隐藏缺陷就是存在于管道内外壁内部的缺陷。
1.3不同几何特征的缺陷按照缺陷的不同几何特征,主要有体积型缺陷和平面型缺陷。
体积型的缺陷主要有夹杂、孔穴。
平面型缺陷主要有熔合不全、裂纹等。
对管道进行安全评定时,主要是按照几何特征划分,通过对其表征化来进行安全评定。
2.安全评定技术2.1塑性极限载荷评价压力管道的焊缝一般都是对接式的,焊接缺陷类型主要是环向缺陷,与其他的压力容器相比较,具有较小的缺陷尺寸,管壁较薄,材料具有良好的韧性,所以在极限载荷控制下会容易出现塑形失效。
《2024年油气输送管道检测方法及安全评价》范文

《油气输送管道检测方法及安全评价》篇一一、引言随着油气工业的不断发展,油气输送管道的安全问题显得尤为重要。
油气输送管道作为能源运输的重要通道,其安全性和稳定性直接关系到国家经济命脉和人民生命财产安全。
因此,对油气输送管道进行定期检测和安全评价,是保障管道安全运行的重要措施。
本文将介绍油气输送管道的检测方法及安全评价,以期为相关领域的研究和应用提供参考。
二、油气输送管道检测方法(一)常规检测方法1. 视觉检测:通过人工巡检、无人机航测等方式,对管道外观进行检查,包括管道颜色、腐蚀情况、泄漏等。
2. 漏磁检测:利用磁场原理检测管道表面裂纹、凹陷等缺陷。
3. 超声波检测:利用超声波对管道内部进行检测,判断管道内部是否存在腐蚀、结垢等现象。
(二)特殊检测方法1. 智能检测:通过安装传感器等设备,实时监测管道的变形、应力、温度等参数,实现管道的智能监测。
2. 无损检测:采用射线、超声波等无损检测技术,对管道进行全面检测,以发现潜在的安全隐患。
3. 地质雷达检测:利用地质雷达技术对地下管道进行探测,了解管道周围地质环境的变化情况。
三、安全评价(一)定性评价定性评价主要是根据检测结果,对管道的安全状况进行评估。
通过对比管道设计参数、运行参数以及实际检测结果,判断管道是否存在安全隐患。
定性评价的结果通常以文字描述或图表形式呈现。
(二)定量评价定量评价是利用数学模型、软件算法等手段,对管道的安全状况进行量化评估。
通过建立管道的数学模型,分析管道在不同工况下的应力、变形等情况,从而判断管道的安全性能。
定量评价的结果通常以数值形式呈现,为制定针对性的安全措施提供依据。
四、安全措施与建议针对油气输送管道的检测和安全评价结果,提出以下安全措施与建议:1. 定期进行管道检测和安全评价,及时发现并处理潜在的安全隐患。
2. 加强管道巡检力度,提高人工巡检和智能巡检的结合程度,确保及时发现并处理问题。
3. 对老旧、腐蚀严重的管道进行更换或修复,提高管道的整体安全性。
含体积型缺陷管道的剩余强度评价
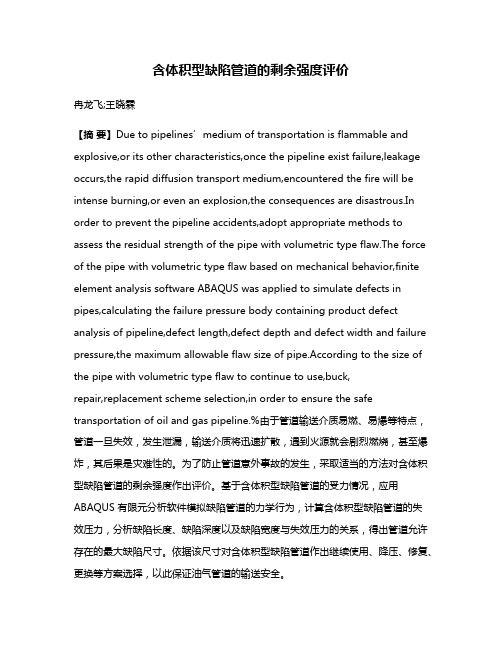
含体积型缺陷管道的剩余强度评价冉龙飞;王晓霖【摘要】Due to pipelines’medium of transportation is flammable and explosive,or its other characteristics,once the pipeline exist failure,leakage occurs,the rapid diffusion transport medium,encountered the fire will be intense burning,or even an explosion,the consequences are disastrous.In order to prevent the pipeline accidents,adopt appropriate methods to assess the residual strength of the pipe with volumetric type flaw.The force of the pipe with volumetric type flaw based on mechanical behavior,finite element analysis software ABAQUS was applied to simulate defects in pipes,calculating the failure pressure body containing product defect analysis of pipeline,defect length,defect depth and defect width and failure pressure,the maximum allowable flaw size of pipe.According to the size of the pipe with volumetric type flaw to continue to use,buck,repair,replacement scheme selection,in order to ensure the safe transportation of oil and gas pipeline.%由于管道输送介质易燃、易爆等特点,管道一旦失效,发生泄漏,输送介质将迅速扩散,遇到火源就会剧烈燃烧,甚至爆炸,其后果是灾难性的。
燃气管道安全评估方法

燃气管道安全评估方法
燃气管道安全评估是指对燃气管道系统进行系统化、科学化的安全性评估。
评估方法主要包括以下几个方面:
1. 设计评估:对燃气管道系统的设计方案进行评估,包括管道布置、管径选择、材料选择等,并通过计算和模型分析验证设计的合理性和可靠性。
2. 施工评估:对燃气管道系统的施工过程进行评估,包括施工管理、质量控制等,确保施工过程符合相关规范和标准,并进行现场监督检查。
3. 运行评估:对燃气管道系统的运行状态进行评估,包括管道的运行压力、温度、流量等参数的监测和记录,并进行运行风险分析,发现潜在的安全问题。
4. 维护评估:对燃气管道系统的维护和维修工作进行评估,包括维护计划的制定和执行情况,维修工作的质量和效果评估,确保管道系统的正常运行和安全可靠。
5. 管理评估:对燃气管道系统的管理工作进行评估,包括安全管理制度的完善程度、操作人员的素质和培训情况、应急预案的制定和执行情况等,确保安全管理工作的有效性。
综上所述,燃气管道安全评估方法是一种综合性的评估方法,通过对燃气管道系统的设计、施工、运行、维护和管理等方面
进行评估,识别和控制燃气管道系统的潜在风险,从而确保燃气管道的安全运行。
《2024年油气输送管道检测方法及安全评价》范文
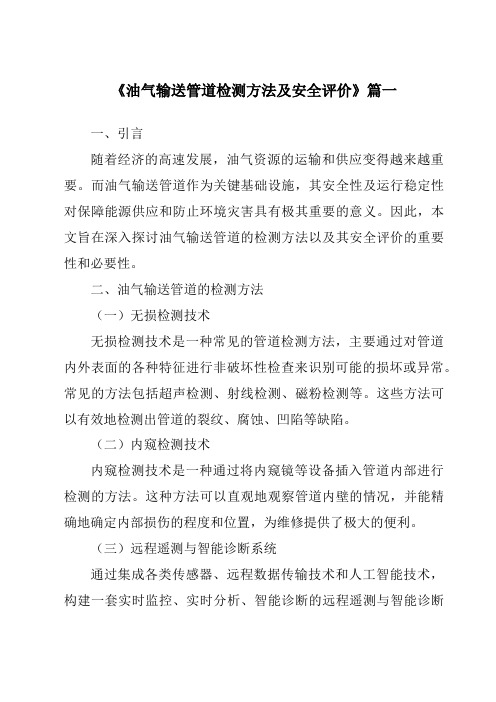
《油气输送管道检测方法及安全评价》篇一一、引言随着经济的高速发展,油气资源的运输和供应变得越来越重要。
而油气输送管道作为关键基础设施,其安全性及运行稳定性对保障能源供应和防止环境灾害具有极其重要的意义。
因此,本文旨在深入探讨油气输送管道的检测方法以及其安全评价的重要性和必要性。
二、油气输送管道的检测方法(一)无损检测技术无损检测技术是一种常见的管道检测方法,主要通过对管道内外表面的各种特征进行非破坏性检查来识别可能的损坏或异常。
常见的方法包括超声检测、射线检测、磁粉检测等。
这些方法可以有效地检测出管道的裂纹、腐蚀、凹陷等缺陷。
(二)内窥检测技术内窥检测技术是一种通过将内窥镜等设备插入管道内部进行检测的方法。
这种方法可以直观地观察管道内壁的情况,并能精确地确定内部损伤的程度和位置,为维修提供了极大的便利。
(三)远程遥测与智能诊断系统通过集成各类传感器、远程数据传输技术和人工智能技术,构建一套实时监控、实时分析、智能诊断的远程遥测与智能诊断系统。
该系统可以实时监测管道的运行状态,及时发现异常情况并给出预警,为管道的安全运行提供了有力保障。
三、油气输送管道的安全评价(一)风险评估风险评估是安全评价的重要环节,主要是通过识别和评估可能存在的危险源、事件及后果,来确定其安全风险等级。
风险评估过程中需综合考虑管道的物理性质、化学性质、运行环境、设备情况等因素。
(二)完整性评价完整性评价主要针对管道的结构和功能进行评价。
其主要是通过对管道进行检测,包括前面所提及的几种检测方法,综合评估管道的结构完整性、防腐保护、内外壁腐蚀等指标。
这种评价能够及时发现问题并进行处理,对提高管道的运行效率和安全性有着至关重要的作用。
(三)综合安全评价综合安全评价是对整个油气输送系统进行全面评价的过程。
其包括了风险评估和完整性评价的所有环节,同时还包括对管理和操作的评估。
该评价的目的是确定整个系统的安全水平,并为改进措施提供依据。
管道输气系统安全性评估与控制
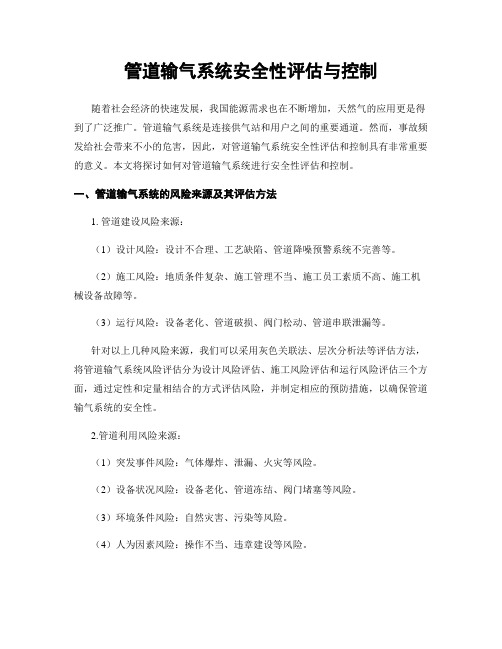
管道输气系统安全性评估与控制随着社会经济的快速发展,我国能源需求也在不断增加,天然气的应用更是得到了广泛推广。
管道输气系统是连接供气站和用户之间的重要通道。
然而,事故频发给社会带来不小的危害,因此,对管道输气系统安全性评估和控制具有非常重要的意义。
本文将探讨如何对管道输气系统进行安全性评估和控制。
一、管道输气系统的风险来源及其评估方法1. 管道建设风险来源:(1)设计风险:设计不合理、工艺缺陷、管道降噪预警系统不完善等。
(2)施工风险:地质条件复杂、施工管理不当、施工员工素质不高、施工机械设备故障等。
(3)运行风险:设备老化、管道破损、阀门松动、管道串联泄漏等。
针对以上几种风险来源,我们可以采用灰色关联法、层次分析法等评估方法,将管道输气系统风险评估分为设计风险评估、施工风险评估和运行风险评估三个方面,通过定性和定量相结合的方式评估风险,并制定相应的预防措施,以确保管道输气系统的安全性。
2.管道利用风险来源:(1)突发事件风险:气体爆炸、泄漏、火灾等风险。
(2)设备状况风险:设备老化、管道冻结、阀门堵塞等风险。
(3)环境条件风险:自然灾害、污染等风险。
(4)人为因素风险:操作不当、违章建设等风险。
针对利用过程中的风险来源,我们可以采用风险辨识、风险评估、风险控制三个步骤来进行风险管控。
这种方法需要依靠各种管道硬件设施和软件系统,如监控系统、预警系统、跟踪系统、事故分析系统等,收集管道利用过程中的数据,及时发现管道问题,做出相应的调整和修复,以防止管道输气事故的发生。
二、管道输气系统的安全性控制措施1. 故障预防控制措施故障预防控制措施是保障管道安全的重要手段,主要包括:(1)正常运维及常规检修:定期检查设备和管道,确认运行状态正常,对不正常的情况及时进行维修。
(2)提升安全意识:加强培训,让每个员工都能了解管道安全危险的因素。
(3)加强装备检测:对各种管道设备进行定期检测,确保设备完好无损。
2. 特殊安全控制措施特殊安全控制措施主要考虑管道的环境和条件,通过不同的控制措施实现管道的保障。
天然气输送管道系统的安全评估
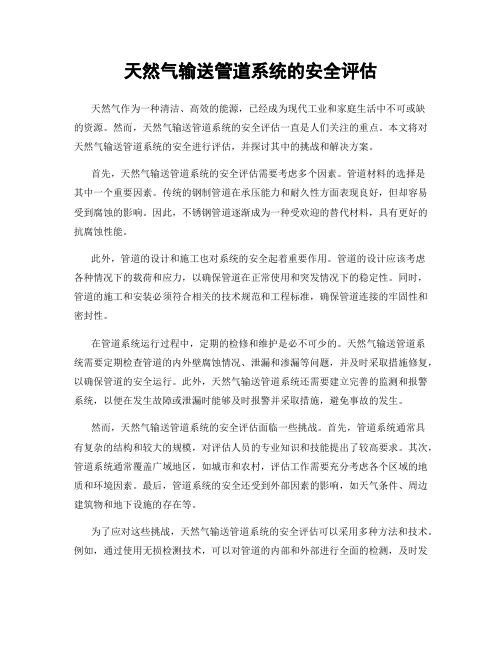
天然气输送管道系统的安全评估天然气作为一种清洁、高效的能源,已经成为现代工业和家庭生活中不可或缺的资源。
然而,天然气输送管道系统的安全评估一直是人们关注的重点。
本文将对天然气输送管道系统的安全进行评估,并探讨其中的挑战和解决方案。
首先,天然气输送管道系统的安全评估需要考虑多个因素。
管道材料的选择是其中一个重要因素。
传统的钢制管道在承压能力和耐久性方面表现良好,但却容易受到腐蚀的影响。
因此,不锈钢管道逐渐成为一种受欢迎的替代材料,具有更好的抗腐蚀性能。
此外,管道的设计和施工也对系统的安全起着重要作用。
管道的设计应该考虑各种情况下的载荷和应力,以确保管道在正常使用和突发情况下的稳定性。
同时,管道的施工和安装必须符合相关的技术规范和工程标准,确保管道连接的牢固性和密封性。
在管道系统运行过程中,定期的检修和维护是必不可少的。
天然气输送管道系统需要定期检查管道的内外壁腐蚀情况、泄漏和渗漏等问题,并及时采取措施修复,以确保管道的安全运行。
此外,天然气输送管道系统还需要建立完善的监测和报警系统,以便在发生故障或泄漏时能够及时报警并采取措施,避免事故的发生。
然而,天然气输送管道系统的安全评估面临一些挑战。
首先,管道系统通常具有复杂的结构和较大的规模,对评估人员的专业知识和技能提出了较高要求。
其次,管道系统通常覆盖广域地区,如城市和农村,评估工作需要充分考虑各个区域的地质和环境因素。
最后,管道系统的安全还受到外部因素的影响,如天气条件、周边建筑物和地下设施的存在等。
为了应对这些挑战,天然气输送管道系统的安全评估可以采用多种方法和技术。
例如,通过使用无损检测技术,可以对管道的内部和外部进行全面的检测,及时发现潜在的问题。
另外,利用物联网和大数据技术,可以实时监测管道的运行状态和性能指标,提前预测潜在风险的发生。
总之,天然气输送管道系统的安全评估是一个复杂而重要的任务。
在管道材料选择、设计和施工、运行和维护等方面都需要高度重视。
石油天然气输送管道的缺陷评定方法及应用
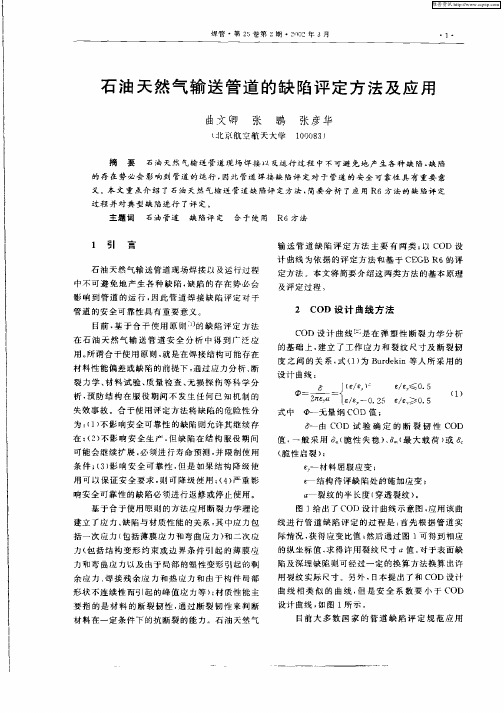
/
//
/
V¥ 线 一 E l
0 2t ≤ 0 5 的缺 陷 . 长度 L 4 ; 于深 度 . 5<a . t 其 ≤ 对
d 05 的缺 陷是不 允许 的。 > .t
¨
/
n2
② B 5 —8 S4 1 5 4标准 附录 H 英 国 B 4 1 —8 S 5 5 4标 准 附 录 H 给 出 了管 道
主 题 词 石 油 管 道
缺 陷评 定 舍 于使 用 R 6方 法
1 引 言
石 油天然 气输 送 管道现 场焊 接 以及运行 过程 中不 可 避免 地 产 生 各种 缺陷 . 陷 的存 在 势必 会 缺 影 响到 管 道 的运 行 , 因此 管 道焊 接 缺 陷评 定 对 于 管道 的安 全可 靠性 具有 重要 意义 目前 , 于 合 于使 用 原 则 - 基 的缺 陷 评 定 方法 在 石 油 天 然 气输 送 管 道 安 全 分 析 中得 到 广 泛 应 用。 所谓合 于使 用 原则 , 就是 在焊接 结 构可 能存在 材料 性能偏 差 或 歃陷 的前提 下 , 过应 力分 析 、 通 断
裂 力 学 、 料 试 验 、 量 检 查 、 损 探 伤 等 科 学 分 材 质 无
输 送 管 道 缺 陷 评定 方 法 主 要 有 两 类 : C 以 OD 设 计 曲线 为依 据 的评 定方 法 和基 于 C GB R6的评 E 定方 法 。本文将 简要 介 绍这两类 方 法 的基本原 理
的存在 势必会 影 响到 管道 的运 行 , 因此 管道 焊接 铁 陷评 定 对 于管道 的 安 全 可靠性 具 有 重要 意
义 本 文 重 点 介 绍 了 石 油 天 然 气 输 送 管 道 缺 陷评 定 方 法 , 要 分 析 了应 用 R6方 法 的 缺 陷 评 定 简
含腐蚀缺陷管道的安全评价

含腐蚀缺陷管道的安全评价石油天然气管道服役时间比较长,普遍存在腐蚀性体积缺陷,以及第三方破坏、地质灾害和误操作等因素造成的损伤[1]。
为保障管道的安全运行,避免管体腐蚀所导致的爆裂、泄漏事故,确定是否需要立即停产检修更换管段,或因生产繁忙暂时不能停产而采取降压运行,需要及时发现缺陷并评估其安全可靠性。
鉴于含缺陷管道的极限应力分析比较复杂,本文试用有限元法分析某一天然气管道的极限强度及安全状况,并与有关评价标准进行了对比。
1管道极限载荷的有限元分析本文研究对象为一含硫天然气输送管道的弯管段,管道材质为20#钢,工作温度为常温,工作压力0.05MPa,最小屈服强度313.95MP,管材的裂纹尖端张开位移(CTOD)值&=0.068mm,焊缝系数为0.8。
该管段在内部介质作用下,出现比较严重的腐蚀和减薄现象,最大蚀坑深度为3.8mm,最大纵向投影长度6mm,环向腐蚀长度120mm,利用有限元法分析其极限承载情况如下:(1)有限元模型。
管段的有限元单元模型如图1所示,共划分1969个单元,4450个节点。
(2)材料的本构模型。
材料的本构模型(应力应变关系)用双线性表示。
经计算分析。
材料的塑性极限许用应力值为294MPa。
(3)弯管的弹塑性分析。
当内压增大到6MPa时,管道内弯处局部材料开始进人屈服状态,但其屈服区域较小。
此时屈服区域外围未屈服的材料可限制屈服区域材料的变形,随载荷的增加,管道不会无限制地变形,因此管段还有进一步承载的能力。
当内压达到9.7MPa时,最大应力处沿厚度方向整体屈服。
由于屈服区域较大,此时随载荷的增加,屈服区域外围未屈服的材料已无法限制屈服区域中心部位的变形。
因此管道此时已完全达到其塑性极限状态,塑性极限内压为9.7MPa。
2标准对管道腐蚀缺陷的评价SY/T6151-1995《钢质管道管体腐蚀损伤评价方法》标准是在消化吸收ASMEB3lG基础上制订的,考虑了环向腐蚀的影响,并将腐蚀区面积折算成当量半裂纹长,采用断裂力学分别计算环向和轴向所能承受的最大压力值[2]。
天然气输送管道安全评估方法研究

天然气输送管道安全评估方法研究天然气输送管道的安全问题一直备受关注。
天然气作为一种高压气体,在输送过程中存在着许多潜在的安全隐患。
因此,对天然气输送管道的安全进行评估显得尤为重要。
本文将介绍天然气输送管道安全评估的方法研究。
一、天然气输送管道的安全问题天然气在输送过程中往往要经过数百公里的距离,这期间遇到的问题非常多,包括设计规范不合理、设备材质疲劳等。
天然气的高压状态下,一旦发生泄漏,其造成的破坏性也非同小可。
虽然天然气管道的建设符合标准和规范,但仍不能排除一定的安全隐患。
因此,对于天然气输送管道的安全评估非常重要。
二、天然气输送管道安全评估方法(一)管道基础信息收集进行天然气输送管道的安全评估首先要收集管道基础信息,包括管道的材质、长度、管径、设计参数等,以及管道附近的土壤类型、地形地貌等信息。
这些信息对于安全评估具有很重要的参考意义。
(二)分析管道情况对管道进行检测和分析,以确定管道的安全性评估。
通常包括以下几个步骤:1. 管道的视觉检查:对管道外部表面进行检查,找出破损部位、腐蚀情况等。
2. 管道的振动分析:运用相应的仪器进行管道的振动分析,分析管道是否存在振动过大等问题。
3. 管道的承载能力分析:采取相应的计算方法分析管道是否承载不住输送的天然气压力。
4. 管道的材质分析:根据管道的材质和历史记录,进行材质疲劳分析,找出管道可能存在的疲劳问题。
(三)管道检测对天然气输送管道进行全面检测,以确保管道的安全性。
常用的检测方法包括无损检测、声波检测、磁粉检测等。
这些检测方法可以找出管道内可能存在的裂纹、腐蚀等问题,从而对管道的安全进行评估。
(四)管道修复与替换对于发现的管道问题,应该及时修复。
例如,管道的破损部位需要进行修补,管道的腐蚀部位需要进行防腐涂层等处理。
如果管道的问题严重,需要进行管道替换。
三、天然气输送管道安全评估的意义天然气输送管道的安全评估是管道运营的必要工作。
对管道进行安全评估,可以及时检测和发现存在的安全隐患,从而进行及时的修复和改善。
燃气输气管道安全评价方案

燃气输气管道安全评价方案燃气输气管道是燃气系统的核心设施,其安全性对于人民生命财产安全以及社会稳定至关重要。
为了确保燃气输气管道的安全性,需要进行全面的安全评价。
下面是一个燃气输气管道安全评价的方案,包括评价目标、评价内容、评价方法以及评价结果处理等。
1. 评价目标燃气输气管道安全评价的目标是全面评估管道系统的安全性,并找出与安全相关的问题,为制定安全管理措施提供依据。
2. 评价内容燃气输气管道安全评价的内容包括以下几个方面:- 管道设计评价:评估管道系统的设计是否符合相关标准和规定,是否存在设计缺陷。
- 材料评价:评估管道材料的质量和可靠性,确保其能够承受运行条件下的压力和温度。
- 施工评价:评估管道系统的施工质量,包括管道的安装、焊接和防腐等。
- 运行评价:评估管道系统的运行状态,检查管道是否存在破损、腐蚀、渗漏等问题。
- 管道设备评价:评估与管道相关的设备,包括阀门、仪表等的性能和可靠性。
- 管道管理评价:评估管道管理的制度和措施,包括巡检、检修、维护等。
3. 评价方法燃气输气管道安全评价可以采用以下几种方法:- 文件审核:通过审核设计文件、施工记录、运行记录等,评估管道是否符合相关标准和规定。
- 现场检查:实地检查管道系统的设计、施工和运行情况,查找可能存在的安全问题。
- 检测技术:使用无损检测技术,对管道进行检测,包括超声波检测、磁粉检测等,发现管道内部的缺陷和破损。
- 数据分析:通过对管道运行数据进行分析,评估管道的安全状况。
4. 评价结果处理评价结果根据问题的严重性划分为不同级别,包括一般问题、较为严重的问题和紧急问题。
对于一般问题,可以给出改进意见和建议,由相关部门负责整改。
对于严重问题和紧急问题,应立即采取措施进行修复或停机修复,确保人员和设施的安全。
此外,针对评价结果中发现的问题,还应制定相应的改进措施,并监督其执行情况。
重点关注问题的整改进展和效果,并定期进行复查和追踪评估,确保问题得到彻底解决。
《油气输送管道检测方法及安全评价》
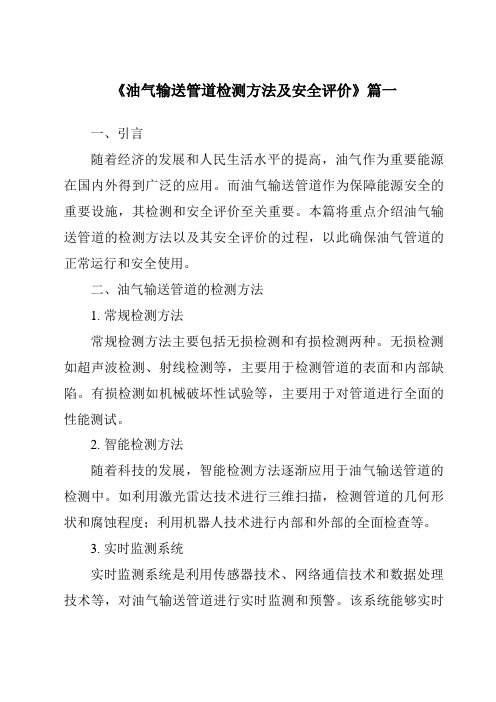
《油气输送管道检测方法及安全评价》篇一一、引言随着经济的发展和人民生活水平的提高,油气作为重要能源在国内外得到广泛的应用。
而油气输送管道作为保障能源安全的重要设施,其检测和安全评价至关重要。
本篇将重点介绍油气输送管道的检测方法以及其安全评价的过程,以此确保油气管道的正常运行和安全使用。
二、油气输送管道的检测方法1. 常规检测方法常规检测方法主要包括无损检测和有损检测两种。
无损检测如超声波检测、射线检测等,主要用于检测管道的表面和内部缺陷。
有损检测如机械破坏性试验等,主要用于对管道进行全面的性能测试。
2. 智能检测方法随着科技的发展,智能检测方法逐渐应用于油气输送管道的检测中。
如利用激光雷达技术进行三维扫描,检测管道的几何形状和腐蚀程度;利用机器人技术进行内部和外部的全面检查等。
3. 实时监测系统实时监测系统是利用传感器技术、网络通信技术和数据处理技术等,对油气输送管道进行实时监测和预警。
该系统能够实时监测管道的压力、温度、流量等参数,及时发现并预警可能的安全隐患。
三、油气输送管道的安全评价安全评价是对油气输送管道的运行状态进行全面的评估,以确定其安全性和可靠性。
主要步骤如下:1. 收集数据:收集管道的基本信息、运行数据、历史事故记录等。
2. 风险评估:根据收集的数据,对管道的运行风险进行评估,包括事故发生的可能性、后果严重程度等。
3. 安全评价:根据风险评估的结果,对管道的安全性和可靠性进行评价。
包括管道的强度、刚度、稳定性等。
4. 制定措施:根据安全评价的结果,制定相应的措施,如维修、更换、加固等,以提高管道的安全性和可靠性。
四、结论油气输送管道的检测和安全评价是保障能源安全和人民生活的重要措施。
常规检测方法、智能检测方法和实时监测系统等方法可以全面检查和监控管道的状态。
同时,安全评价的全面实施能够确保管道的长期稳定运行和安全使用。
在未来的发展中,应进一步研究和应用新的检测技术和方法,提高油气输送管道的检测和安全评价水平,确保能源安全和人民生活的正常进行。
《油气输送管道检测方法及安全评价》
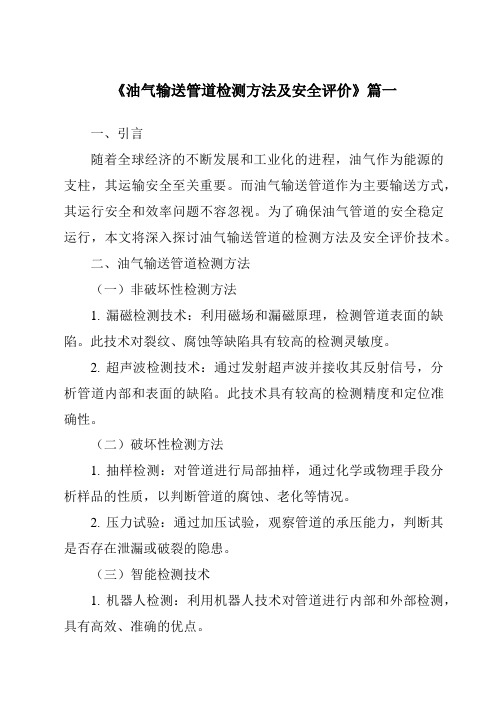
《油气输送管道检测方法及安全评价》篇一一、引言随着全球经济的不断发展和工业化的进程,油气作为能源的支柱,其运输安全至关重要。
而油气输送管道作为主要输送方式,其运行安全和效率问题不容忽视。
为了确保油气管道的安全稳定运行,本文将深入探讨油气输送管道的检测方法及安全评价技术。
二、油气输送管道检测方法(一)非破坏性检测方法1. 漏磁检测技术:利用磁场和漏磁原理,检测管道表面的缺陷。
此技术对裂纹、腐蚀等缺陷具有较高的检测灵敏度。
2. 超声波检测技术:通过发射超声波并接收其反射信号,分析管道内部和表面的缺陷。
此技术具有较高的检测精度和定位准确性。
(二)破坏性检测方法1. 抽样检测:对管道进行局部抽样,通过化学或物理手段分析样品的性质,以判断管道的腐蚀、老化等情况。
2. 压力试验:通过加压试验,观察管道的承压能力,判断其是否存在泄漏或破裂的隐患。
(三)智能检测技术1. 机器人检测:利用机器人技术对管道进行内部和外部检测,具有高效、准确的优点。
2. 无线传感器网络:通过在管道上布置无线传感器,实时监测管道的温度、压力、泄漏等参数,实现远程监控和预警。
三、安全评价技术(一)风险评估风险评估是安全评价的核心,通过对管道的运行环境、设备状况、管理情况等因素进行综合分析,评估管道发生事故的概率和后果严重程度。
常用的风险评估方法包括定性和定量评估。
(二)安全检查表与审核安全检查表是针对管道系统的各个部分和环节,列出可能存在的安全隐患和问题,进行逐项检查和评价。
而安全审核则是对管道的安全管理制度、操作规程等进行审查和评价。
(三)事故后果模拟与分析通过建立事故模型,对可能发生的事故进行模拟和分析,预测事故的发生概率和后果严重程度,为制定安全措施提供依据。
四、综合评价及应对措施综合运用各种检测方法和安全评价技术,对油气输送管道进行全面评价。
针对发现的问题和隐患,制定相应的应对措施,如加强巡检、提高检测频率、修复或更换设备等。
同时,还应加强管道的安全管理,提高员工的安全意识和技能水平,确保管道的安全稳定运行。
《2024年油气输送管道检测方法及安全评价》范文
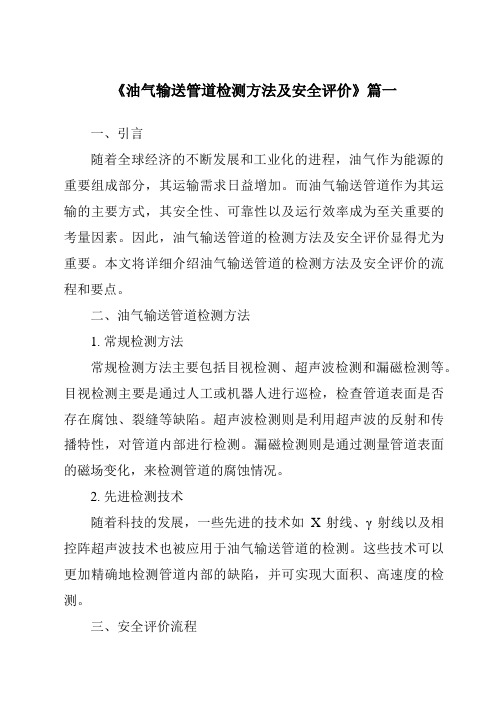
《油气输送管道检测方法及安全评价》篇一一、引言随着全球经济的不断发展和工业化的进程,油气作为能源的重要组成部分,其运输需求日益增加。
而油气输送管道作为其运输的主要方式,其安全性、可靠性以及运行效率成为至关重要的考量因素。
因此,油气输送管道的检测方法及安全评价显得尤为重要。
本文将详细介绍油气输送管道的检测方法及安全评价的流程和要点。
二、油气输送管道检测方法1. 常规检测方法常规检测方法主要包括目视检测、超声波检测和漏磁检测等。
目视检测主要是通过人工或机器人进行巡检,检查管道表面是否存在腐蚀、裂缝等缺陷。
超声波检测则是利用超声波的反射和传播特性,对管道内部进行检测。
漏磁检测则是通过测量管道表面的磁场变化,来检测管道的腐蚀情况。
2. 先进检测技术随着科技的发展,一些先进的技术如X射线、γ射线以及相控阵超声波技术也被应用于油气输送管道的检测。
这些技术可以更加精确地检测管道内部的缺陷,并可实现大面积、高速度的检测。
三、安全评价流程1. 收集数据首先,需要收集管道的基本信息,如管道的材质、规格、运行时间等。
同时,还需要收集管道的检测数据,如腐蚀深度、裂纹长度等。
2. 风险评估根据收集的数据,对管道进行风险评估。
风险评估主要包括对管道的腐蚀、裂纹等缺陷进行定性和定量分析,评估其对管道安全的影响程度。
3. 安全评价根据风险评估的结果,对管道进行安全评价。
安全评价主要包括对管道的整体安全性能进行评价,确定其是否满足运行要求。
四、安全评价要点1. 定期检测与维护定期对油气输送管道进行检测和维护是保证其安全性的重要措施。
通过定期检测,可以及时发现并处理管道的缺陷和问题,防止事故的发生。
2. 科学的风险评估方法科学的风险评估方法是保证安全评价准确性的关键。
应采用先进的风险评估方法和技术,对管道的缺陷和问题进行定性和定量分析,准确评估其对管道安全的影响程度。
3. 综合评价与决策支持综合评价与决策支持是安全评价的重要环节。
管道输送系统安全性评估与优化

管道输送系统安全性评估与优化管道输送系统是工业生产中常用的物料搬运方式,其具有高效、经济、环保等优势。
然而,由于管道输送系统涉及到物料的输送、存储、加工等诸多环节,其在运行过程中也具有一定的风险与隐患。
为了确保管道输送系统的安全性,我们需要进行安全性评估与优化。
一、安全性评估的必要性管道输送系统安全性评估,是指对管道输送系统在运行过程中可能出现的各种安全隐患进行分析和评估,从而找出潜在的安全风险,针对性地采取措施进行改进。
安全性评估对于企业来说非常重要,其具有以下的必要性:1.保障安全生产管道输送系统在企业内扮演着不可或缺的角色,其安全性直接关系到企业的生产安全。
通过安全性评估,企业可以及时发现管道输送系统中的安全隐患,并采取相应的措施进行优化,从而保障安全生产。
2.降低企业成本在管道输送系统中,由于安全隐患的存在,可能会造成物料的浪费、设备的损坏等情况。
通过对管道输送系统进行安全性评估,可以减少运行中的故障发生,降低企业的运营成本。
3.提高工作效率管道输送系统在运行过程中,存在着瓶颈、堵塞等问题。
通过安全性评估,可以找出生产中的次要问题,采用优化措施改进操作流程,大幅提高工作效率。
二、安全性评估的方法管道输送系统安全性评估的方法有很多种,根据具体的情况选择合适的方法进行分析。
下面介绍几种常用的管道输送系统安全性评估方法:1.风险评估法风险评估法是一种全面的管道输送系统安全性评估方法,其目的是确定与管道输送系统有关的风险,并在不同的剖面间建立关联。
该方法可以对隐患的发生概率进行评估,并评估不同风险水平下所需的安全性要求。
2.可靠性评估法可靠性评估法是通过对管道输送系统的可靠性进行分析和计算,确定输送系统各部分的故障、维修需求等信息,进而对系统进行优化改进的方法。
该方法可以考虑各种可能的故障情况,从而为管道输送系统的优化改进提供依据。
3.流程安全分析法流程安全分析法是一种基于操作过程的管道输送系统安全性评估方法,它通过对操作流程中可能出现的隐患进行分析和评估,为优化系统提供方向。
天然气输送管道的安全性评估与优化
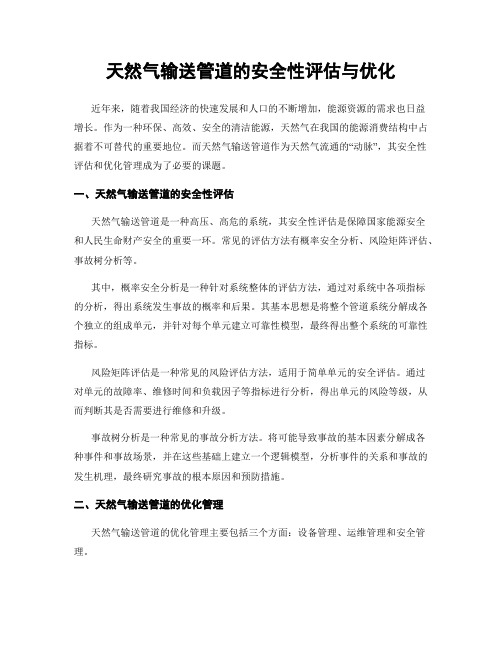
天然气输送管道的安全性评估与优化近年来,随着我国经济的快速发展和人口的不断增加,能源资源的需求也日益增长。
作为一种环保、高效、安全的清洁能源,天然气在我国的能源消费结构中占据着不可替代的重要地位。
而天然气输送管道作为天然气流通的“动脉”,其安全性评估和优化管理成为了必要的课题。
一、天然气输送管道的安全性评估天然气输送管道是一种高压、高危的系统,其安全性评估是保障国家能源安全和人民生命财产安全的重要一环。
常见的评估方法有概率安全分析、风险矩阵评估、事故树分析等。
其中,概率安全分析是一种针对系统整体的评估方法,通过对系统中各项指标的分析,得出系统发生事故的概率和后果。
其基本思想是将整个管道系统分解成各个独立的组成单元,并针对每个单元建立可靠性模型,最终得出整个系统的可靠性指标。
风险矩阵评估是一种常见的风险评估方法,适用于简单单元的安全评估。
通过对单元的故障率、维修时间和负载因子等指标进行分析,得出单元的风险等级,从而判断其是否需要进行维修和升级。
事故树分析是一种常见的事故分析方法。
将可能导致事故的基本因素分解成各种事件和事故场景,并在这些基础上建立一个逻辑模型,分析事件的关系和事故的发生机理,最终研究事故的根本原因和预防措施。
二、天然气输送管道的优化管理天然气输送管道的优化管理主要包括三个方面:设备管理、运维管理和安全管理。
设备管理是天然气输送管道的基础工作,其包括设备的采购、安装和运营维护等。
为了确保天然气输送管道的正常运行,需要对设备进行合理配置和按期保养,在设备发生故障时及时进行检修和更换,保证管道设备的性能和寿命。
运维管理是在设备管理和安全管理基础上进行的重要工作,主要包括管道的日常监测和运行管理等。
通过对管道的监测、检修和保养等工作,发现和解决管道问题,确保天然气处理设施的高效、安全运行。
安全管理是天然气输送管道管理的重要环节。
其包括事故预防、事故应急和事故处理等方面。
在事故预防方面,需要从多个方面考虑,如设备控制、安全控制和检修控制等。
在用氧气管道缺陷安全评定
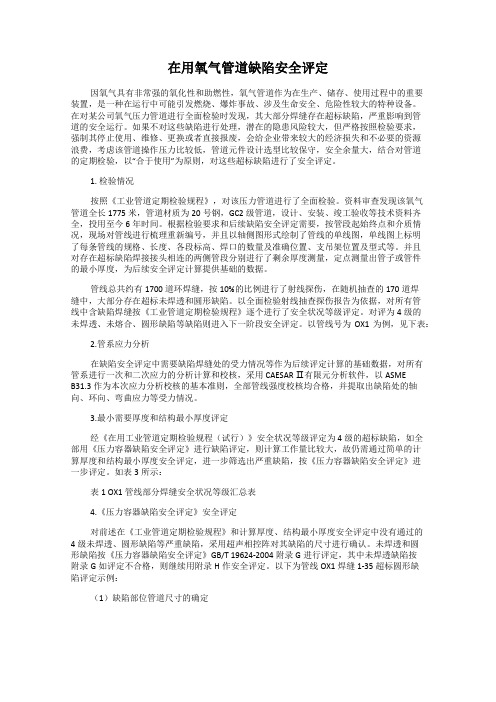
在用氧气管道缺陷安全评定因氧气具有非常强的氧化性和助燃性,氧气管道作为在生产、储存、使用过程中的重要装置,是一种在运行中可能引发燃烧、爆炸事故、涉及生命安全、危险性较大的特种设备。
在对某公司氧气压力管道进行全面检验时发现,其大部分焊缝存在超标缺陷,严重影响到管道的安全运行。
如果不对这些缺陷进行处理,潜在的隐患风险较大,但严格按照检验要求,强制其停止使用、维修、更换或者直接报废,会给企业带来较大的经济损失和不必要的资源浪费,考虑该管道操作压力比较低,管道元件设计选型比较保守,安全余量大,结合对管道的定期检验,以“合于使用”为原则,对这些超标缺陷进行了安全评定。
1. 检验情况按照《工业管道定期检验规程》,对该压力管道进行了全面检验。
资料审查发现该氧气管道全长1775米,管道材质为20号钢,GC2级管道,设计、安装、竣工验收等技术资料齐全,投用至今6年时间。
根据检验要求和后续缺陷安全评定需要,按管段起始终点和介质情况,现场对管线进行梳理重新编号,并且以轴侧图形式绘制了管线的单线图,单线图上标明了每条管线的规格、长度、各段标高、焊口的数量及准确位置、支吊架位置及型式等。
并且对存在超标缺陷焊接接头相连的两侧管段分别进行了剩余厚度测量,定点测量出管子或管件的最小厚度,为后续安全评定计算提供基础的数据。
管线总共约有1700道环焊缝,按10%的比例进行了射线探伤,在随机抽查的170道焊缝中,大部分存在超标未焊透和圆形缺陷。
以全面检验射线抽查探伤报告为依据,对所有管线中含缺陷焊缝按《工业管道定期检验规程》逐个进行了安全状况等级评定。
对评为4级的未焊透、未熔合、圆形缺陷等缺陷则进入下一阶段安全评定。
以管线号为OX1为例,见下表:2.管系应力分析在缺陷安全评定中需要缺陷焊缝处的受力情况等作为后续评定计算的基础数据,对所有管系进行一次和二次应力的分析计算和校核,采用CAESAR Ⅱ有限元分析软件,以ASMEB31.3作为本次应力分析校核的基本准则,全部管线强度校核均合格,并提取出缺陷处的轴向、环向、弯曲应力等受力情况。
在役输气管道分层缺陷无损检测及安全评价
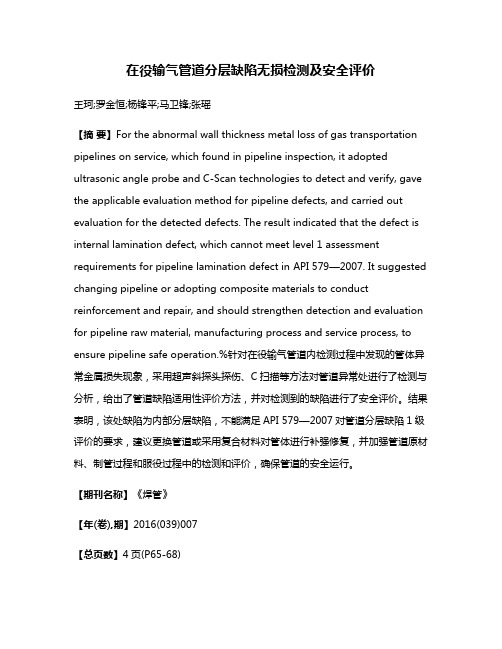
在役输气管道分层缺陷无损检测及安全评价王珂;罗金恒;杨锋平;马卫锋;张瑶【摘要】For the abnormal wall thickness metal loss of gas transportation pipelines on service, which found in pipeline inspection, it adopted ultrasonic angle probe and C-Scan technologies to detect and verify, gave the applicable evaluation method for pipeline defects, and carried out evaluation for the detected defects. The result indicated that the defect is internal lamination defect, which cannot meet level 1 assessment requirements for pipeline lamination defect in API 579—2007. It suggested changing pipeline or adopting composite materials to conduct reinforcement and repair, and should strengthen detection and evaluation for pipeline raw material, manufacturing process and service process, to ensure pipeline safe operation.%针对在役输气管道内检测过程中发现的管体异常金属损失现象,采用超声斜探头探伤、C扫描等方法对管道异常处进行了检测与分析,给出了管道缺陷适用性评价方法,并对检测到的缺陷进行了安全评价。
管道缺陷评估方法
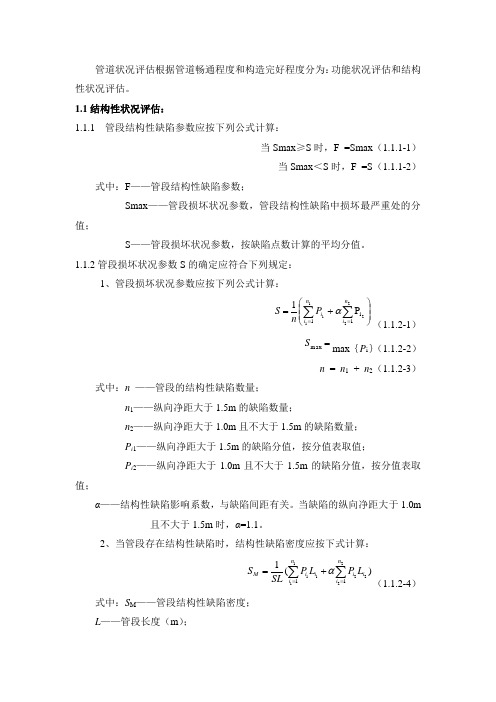
管道状况评估根据管道畅通程度和构造完好程度分为:功能状况评估和结构性状况评估。
1.1结构性状况评估:1.1.1 管段结构性缺陷参数应按下列公式计算:当Smax ≥S 时,F =Smax (1.1.1-1)当Smax <S 时,F =S (1.1.1-2)式中:F ——管段结构性缺陷参数;Smax ——管段损坏状况参数,管段结构性缺陷中损坏最严重处的分值;S ——管段损坏状况参数,按缺陷点数计算的平均分值。
1.1.2管段损坏状况参数S 的确定应符合下列规定:1、管段损坏状况参数应按下列公式计算:⎪⎪⎭⎫⎝⎛+=∑∑==2221111i 1P 1n i n i i P n S α(1.1.2-1)=max S max {P i }(1.1.2-2)n = n 1 + n 2(1.1.2-3)式中:n ——管段的结构性缺陷数量;n 1——纵向净距大于1.5m 的缺陷数量;n 2——纵向净距大于1.0m 且不大于1.5m 的缺陷数量; P i 1——纵向净距大于1.5m 的缺陷分值,按分值表取值;P i 2——纵向净距大于1.0m 且不大于1.5m 的缺陷分值,按分值表取值;α——结构性缺陷影响系数,与缺陷间距有关。
当缺陷的纵向净距大于1.0m且不大于1.5m 时,α=1.1。
2、当管段存在结构性缺陷时,结构性缺陷密度应按下式计算:)(12222111111∑∑==+=n i i i n i i i M L P L P SL S α(1.1.2-4)式中:S M ——管段结构性缺陷密度; L ——管段长度(m );L i1——纵向净距大于1.5m的结构性缺陷长度(m);L i2——纵向净距大于1.0m且不大于1.5m的结构性缺陷长度(m)。
1.1.3管段结构性缺陷等级的确定应符合表1.1.3-1的规定。
管段结构性缺陷类型评估可按表1.1.3-2确定。
表1.1.3-1 管段结构性缺陷等级评定对照表表1.1.3-2 管段结构性缺陷类型评估参考表1.1.4管段修复指数RI按下式计算:RI=0.7×F+ 0.1×K + 0.05×E+ 0.15×T(1.1.4)式中:RI——管段修复指数;K——地区重要性参数,可按表1.1.4-1的规定确定;E——管道重要性参数,可按表1.1.4-2的规定确定;T——土质影响参数,可按表1.1.4-3的规定确定。
- 1、下载文档前请自行甄别文档内容的完整性,平台不提供额外的编辑、内容补充、找答案等附加服务。
- 2、"仅部分预览"的文档,不可在线预览部分如存在完整性等问题,可反馈申请退款(可完整预览的文档不适用该条件!)。
- 3、如文档侵犯您的权益,请联系客服反馈,我们会尽快为您处理(人工客服工作时间:9:00-18:30)。
—1.47A。(a/b>25.0),其中,A。=c’s/瓦,bc=
0.000
789,口。=rain(3.0,口)=rain(3.0,0.609)=
,p、2
0.609,因此,PLs=0.95,则PLs=PLS×PLo=
13.196。根据GB/T19624标准,若式f}I+ 、‘Ls,
,M~2
(栽}≤o.44成立,认为缺陷是安全或可以接受
1 1.1
a.GB/T19624标准规定,进行评定的单位 和人员资格应符合国家有关法律、法规和规章的 规定;而SY/T6477标准对进行评价的单位和人 员资格未作出规定。 b.GB/T19624标准仅适用对直管段的评 定,而SY/T6477标准对均匀腐蚀适用于直管段 和弯头,对局部金属损失评价,一级评价适用于仅 承受内压的直管段,二级评价适用于承受内压和 附加载荷的直管段和弯头;GB/T19624标准还适 用于焊缝的气孔、夹渣和限定条件下的未焊透等 体积型缺陷的评定,而SY/T6477标准无此规定; GB/T19624标准对体积型缺陷的深度和管道内 外径之比提出了限制,而SY/T6477标准未提出; GB/T19624标准对于不符合条件或在服役期间 表面有可能产生裂纹的含体积缺陷压力管道,提 出应按面积型缺陷进行评定,而SY/T6477标准 未提出。 c.按GB/T19624标准进行评定,需要提供 的数据量少,缺陷规则化处理简单,评价程序和运 算过程简便;按¥Y/T6477标准进行评定,相对于 GB/T19624标准,需要的数据量多,缺陷定量化 处理、评价程序和运算过程均复杂。 d.GB/T19624标准中所指的安全评定是为 判别在用含缺陷压力容器、压力管道在规定的使 用工况条件下,能否继续安全使用所进行的综合 分析和评价,其结论有可接受和不可接受两种。 并未规定可降级使用及降级使用后最大允许工作 压力的确定方法。而SY/T6477标准中所指的安 全评定是采用剩余强度评价方法对管道剩余承压 能力的定量评价。其结论也有两种,若剩余强度 评价结果表明损伤管道适应于目前的工作条件, 则只要建立合适的检测(监测)程序,管道便可以 在目前工作条件下继续安全运行;若评价结果表 明损伤管道不适应目前操作条件,则需降压使用 或更换管段。 2缺陷评定案例
2.1
GB/T19624和SY/T6477标准对比分析 标准简介 与含凹坑缺陷的压力容器安全评定相比,含
局部减薄压力管道的安全评定更为复杂。首先, 压力管道除承受内外压外,同时还承受拉弯等组 合载荷;其次,安全评定所需要的管系内力和管道 应力数值一般只能通过数值计算分析方法求得, 这对普通评定人员来说具有很大的难度。为此, GB/T19624采用了国家“九五”科技攻关专题提 出的以塑性极限载荷理论和含局部减薄压力管道 塑性极限载荷拟合计算公式为基础的工程评定方 法,并采用了无需进行复杂的管系内力和管道应 力计算的、应用极为简便的免于评定条件。因此, GB/T19624提出的安全评定方法,适用于在内压 和弯矩的组合载荷下含气孔、夹渣和局部减薄等 体积缺陷及失效模式为塑性失稳的钢制在役压力 管道直管段的安全评定。该评定方法理论严谨、 方法简单,能使大部分缺陷免于焊补,避免了因焊 补促使新裂纹产生的危险,有重大的现实意义。 SY/T6477标准规定了含均匀腐蚀和局部金 属损失两种体积型缺陷管道的剩余强度评价方 法,适用于原设计标准与GB50251或GB50253相 一致的在用油气输送管道。管道的剩余强度评价 方法是在缺陷检测的基础上,以剩余强度因子 (RSF)作为含体积型腐蚀缺陷管道剩余强度评价 的判据,对管道剩余承压能力的定量评价。若 RSF计算值大于推荐的下限值,则管道可以在目 前压力下继续使用,否则应降级使用。SY/T6477 标准在技术内容上与API
111171 x
18
innl×1.6ram(长×宽× 式中
(5)
深)。测厚检查时发现划伤周围管道平均壁厚为 6.7mm;渗透探伤后在损伤部位未发现缺陷显示 痕迹,符合JB4730-94标准I级要求。按照 GB50251-94{输气管道工程设计规范》,初步进行 强度校核,损伤部位修磨处理后最大允许工作压 力为5.17MPa,强度校核不合格(计算步骤略), 按照设计规范要求需进行焊补修理,考虑到焊补 修理必须停止输气,这样会影响到下游的工业生 产和人民群众的生活,造成更大的损失,可按有关 标准对该缺陷进行安全评定计算,依据评定结果 再作。 2.2安全评定 经审查,该天然气管道及其损伤缺陷符合 GB/T19624标准规定的限定条件,故按照此标准 进行评定。管道材料为X52,规格痧426mm× 7mm,设计压力为6.4MPa,最高工作压力为5.8 MPa,地区级别二级。管道外半径R。为213mm, 管道内半径R;为206mm,缺陷附近管道实测壁厚 为6.7mm,因该部位实施热缩套防腐,故可不计 管道至下一个检验周期末的腐蚀量,因此缺陷附 近计算壁厚r取6.7mm。 对检测查明的壁厚局部减薄缺陷,根据其实 际位置、形状和尺寸,将其规则化为轴向半长A= 23ram、环向半长B=15mm、深度C=1.6mm(因该 缺陷属机械损伤缺陷,在下一个检验期内该缺陷 不会扩展,因此取实测最大损伤深度)的表面缺 陷。 对规则化处理得到的缺陷尺寸,按如下规定 进行无量纲化处理,得:
RP
579{适用性评价推荐做法》、挪威船级社DNV
RP一101《腐蚀管道评价的推荐方法》等,加拿大、 澳大利亚等国也都有相应的技术标准。我国对含 体积型缺陷的油气输送管道进行合乎使用评价方 法有两种技术规范:一种是GB/T19624-2004《在 用含缺陷压力容器安全评定》”1(以下简称GB/ T19624)中的压力管道直管段体积缺陷安全评定 方法;另一种是SY/T6477-2000(含缺陷油气输送 管道剩余强度评价方法》[61(以下简称SY/ 1"6477)中的管道剩余强度评价方法。笔者在介 绍GB/T19624和SY/T6477两个标准的基础上,
(1) (2) (3)
在缺陷定量评价基础上,对在役油气输送
管道直管段存在的体积型缺陷,按照合乎使用原 则进行安全评定,结果科学可靠,使缺陷免于焊补 而继续存在成为可能,不但避免了因焊补而产生 新裂纹等缺陷的危险,而且大大节约了因焊补导 致的油气停输费用,具有重大的现实意义。
3.3
相对深度
根据GB9711—881石油天然气输送管道用螺 旋缝埋弧焊钢管》标准知,在评定工况下,管道材 料的屈服极限矿。=360MPa。由于缺陷处于母材 区(非焊缝区),则评定中所需的材料流动应力孑
简便,适用缺陷类型广,易于掌握和操作,应为缺陷译定首选执行标准。采用该规范对一案例进行评定,
评定结果显示,缺陷的存在是安全可接受的。 关键词 管道 油气输送体积型缺陷 安全评定 文章编号0254-6094(2011)03-0269-04
中图分类号TQ055.8+l
文献标识码A
由于制造、安装、使用及管理等因素,在役油 气输送管道上常常存在着超过制造及安装验收标 准的缺陷,这些缺陷的存在必然会使管道承载能 力降低,甚至导致管道泄漏,尤其是腐蚀坑和机械 损伤这类体积型缺陷。对于制造、运输和安装过 程中在管道表面造成的凿痕、槽痕、刻痕和凹痕等 有害缺陷,可按照质量验收标准GB9711《石油天 然气输送管道用螺旋埋弧焊钢管》、GB50251《输 油管道工程设计规范》、GB50253《输油管道工程 设计规范》及设计技术文件的规定进行修磨、修 补或更换。但对在役油气输送管道,无论是腐蚀 坑、机械损伤还是其它表面缺陷打磨后形成的凹 坑,虽然比裂纹安全得多,但由于壳体几何上的不 连续,使管道原来的应力分布状态发生改变,因 此,对这些体积型缺陷不能简单地采用剩余壁厚 进行强度校核的方法来确定是否允许其存在。由 于油气输送管道具有埋地敷设、长距离输送及管 理难度大的特点,如果这些超标的体积型缺陷一 律不允许存在,进行返修或更换管段不但需要付 出大量的人力、物力,还会因施工前排放介质、中 断油气输送而造成巨大的经济损失。 随着科学技术的进步,以断裂力学、塑性力学 为基础,以合乎使用为原则的一种全新的评价方 法逐步得到认可和应用¨订o。它是在对管道缺陷
第38卷第3期
化工机械
269
在役油气输送管道体积型缺陷安全评定方法
夏锋社¨淡勇2 陈聪2
(1.陕西省锅炉压力容器检验所;2.西北大学化工学院)
摘要针对在役油气输送管道体积型缺陷评定问题.重点分析了我国现有的两个缺陷评定规范的特
色和创新点,并进行了对比。对比分析结果显示,《在用含缺陷压力容器安全评定》规范方法简单,运算
RP
579中的含体积型
缺陷管道剩余强度的一、二级评价等效。一级评 价提供了计算过程简单而评价结果偏于保守的筛 选判据;二级评价提供了详尽的评价程序,评价结 果更为准确。 1.2对比分析 笔者从评价单位和人员资格、适用范围和限 定条件、评价方法以及评价结论4个方面进行了
管道缺陷和检验情况 在某天然气管道防腐层检漏中,发现管道多
处损伤,且伤及母材,其中在1369‘~1370。桩间一 处直管段母材受损最为严重,经查该损伤为推土 机平地、取土所致;外观检查后在该部位未发现凹
万方数据
第38卷第3期
化工机械 管道局部减薄相对深度:
c。=[c+(r0一T)]/n=O.238
271
陷,但存在划伤,划伤形状呈不规则四边形,划伤 最大尺寸为46
相对轴向长度
相对环向长度
死——管道公称壁厚,ro=7mm。
由于损伤缺陷相对环向长度6=0.023,查
GB/T19624标准中的表H.1知,bG0.25时,容许 的最大缺陷相对深度为0.45,可见,管道局部减 薄相对深度符合免于评定条件。管道最大工作压 力P。。与无缺陷管道在纯内压下的塑性极限内压 P。。之比p。。/P。o=0.417,大于免于评定的判别 标准0.3,因此,应继续进行评定。 计算管道(含缺陷)塑性极限内压P嵋=0.95
=盯.=360MPa。
对于案例中的缺陷,GB/T19624标准评定