CAT811TTBIGT10中文资料
gt810g光猫说明书
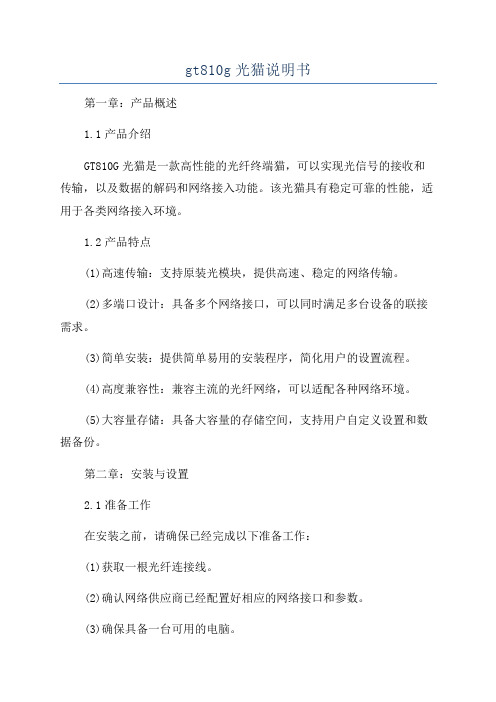
gt810g光猫说明书第一章:产品概述1.1产品介绍GT810G光猫是一款高性能的光纤终端猫,可以实现光信号的接收和传输,以及数据的解码和网络接入功能。
该光猫具有稳定可靠的性能,适用于各类网络接入环境。
1.2产品特点(1)高速传输:支持原装光模块,提供高速、稳定的网络传输。
(2)多端口设计:具备多个网络接口,可以同时满足多台设备的联接需求。
(3)简单安装:提供简单易用的安装程序,简化用户的设置流程。
(4)高度兼容性:兼容主流的光纤网络,可以适配各种网络环境。
(5)大容量存储:具备大容量的存储空间,支持用户自定义设置和数据备份。
第二章:安装与设置2.1准备工作在安装之前,请确保已经完成以下准备工作:(1)获取一根光纤连接线。
(2)确认网络供应商已经配置好相应的网络接口和参数。
(3)确保具备一台可用的电脑。
2.2硬件连接(1)将光纤连接线的一端插入GT810G光猫的光纤口,并固定好连接线。
(2)将光猫的另一端连接到网络供应商提供的接口。
2.3软件设置(1)打开电脑,并连接光猫和电脑。
(2)打开浏览器,输入指定的IP地址,并进入光猫管理界面。
(3)根据网络供应商的要求,进行相应的设置,包括PPPoE账号、IP地址等参数。
(4)保存设置,并重启光猫,等待联网成功。
第三章:用户界面介绍3.1系统概况在系统概况界面中,可以查看光猫的各项参数和状态信息,包括连接状态、WAN口状态等。
3.2安全设置在安全设置界面中,可以设置登陆光猫管理界面的密码,以及查看和修改黑名单等安全相关选项。
3.3网络设置在网络设置界面中,可以进行IP地址设置、DNS服务器设置、MAC地址绑定等操作,以适应不同的网络环境。
3.4WIFI设置在WIFI设置界面中,可以设置无线网络的名称、密码、加密方式等,以及查看连接的设备列表和信号强度。
3.5系统工具在系统工具界面中,可以进行诊断工具的运行、固件升级、备份还原等操作,以保障光猫的正常运行。
Yokogawa P10系列产品参数说明书
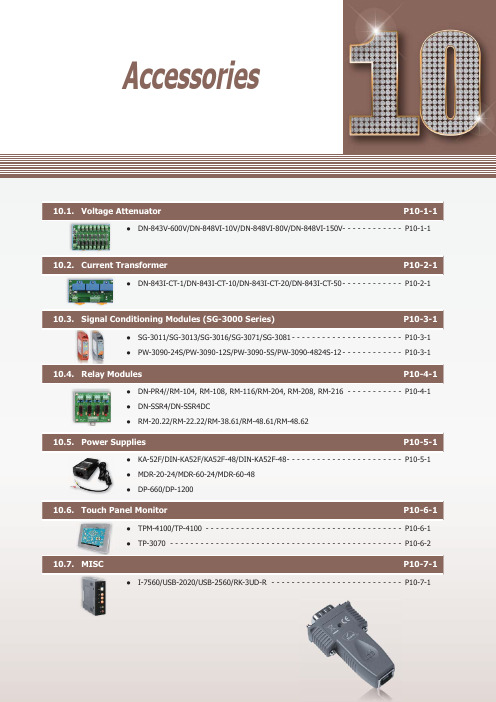
P10-1-1●DN-843V-600V/DN-848VI-10V/DN-848VI-80V/DN-848VI-150V- - - - - - - - - - - - P 10-1-1Current P10-2-1●DN-843I-CT-1/DN-843I-CT-10/DN-843I-CT-20/DN-843I-CT-50 - - - - - - - - - - - - P 10-2-1P10-3-1●SG-3011/SG-3013/SG-3016/SG-3071/SG-3081 - - - - - - - - - - - - - - - - - - - - - - P 10-3-1 ●PW-3090-24S/PW-3090-12S/PW-3090-5S/PW-3090-4824S-12 - - - - - - - - - - - - P 10-3-1Relay Modules P10-4-1●DN-PR4//RM-104, RM-108, RM-116/RM-204, RM-208, RM-216 - - - - - - - - - - - P 10-4-1 ●DN-SSR4/DN-SSR4DC●RM-20.22/RM-22.22/RM-38.61/RM-48.61/RM-48.62Power Supplies P10-5-1●KA-52F/DIN-KA52F/KA52F-48/DIN-KA52F-48 - - - - - - - - - - - - - - - - - - - - - - - P 10-5-1 ●MDR-20-24/MDR-60-24/MDR-60-48 ●DP-660/DP-1200P10-6-1●TPM-4100/TP-4100 - - - - - - - - - - - - - - - - - - - - - - - - - - - - - - - - - - - - - - - P 10-6-1 ●TP-3070 - - - - - - - - - - - - - - - - - - - - - - - - - - - - - - - - - - - - - - - - - - - - - - P 10-6-2MISC P10-7-1●I-7560/USB-2020/USB-2560/RK-3UD-R - - - - - - - - - - - - - - - - - - - - - - - - - - P 10-7-1AccessoriesProfessional Provider of High Quality I ndustrial C omputer P roducts and D ata A cquisition S ystems Vol. PAC 2.0.0A c c e s s o r i e s101Vout1GND Vout2GND Vout3GND+Vs GND F .G.NC Vin 1 -Vin 1+NC Vin 2 -Vin 2+NC Vin 3 -Vin 3+Vin 1 -Vin 1+Vin 2 -Vin 2+Vin 3 -Vin 3+Vin 4 -Vin 4+Vin 5 -Vin 5+Vin 6 -Vin 6+Vin 7 -Vin 7+Vin 8 -Vin 8++Vs GND F .G.Vout1 +OP Amp1OP Amp2OP Amp3OP Amp4OP Amp5OP Amp6OP Amp7OP Amp8Vout1 -Vout2 +Vout2 -Vout3 +Vout3 -Vout4 +Vout4 -Vout5 +Vout5 -Vout6 +Vout6 -Vout7 +Vout7 -Vout8 +Vout8 -DN-843V-600VDN-848VI-10V/DN-848VI-80V/DN-848VI-150V10.1. Voltage AttenuatorThe DN-800V series are voltage input attenuator . The maximum input range is from ±80 V to +/- 600 V and can be attenuated to ±10 V . The "I" version provide 3000 V DC intra-modules isolation and 3000 V DC channel to channel isolation to avoid the noise interference from inputs to outputs or channel to channel. It can be used with the analog input modules such as I-7017 and I-87017 etc. to measure the high voltage.DN-848VI-80VDN-848VI-150VAC/DC Source InputHigh Voltage Input Measurement Linear Attenuation Ratio High Input ImpedanceChannel to Channel Isolation forDN-848VI-10V , DN-848VI-80V and DN-848VI-150V 4 kV ESD Protection 3 kV Surge Protection RoHS ComplianceOperating Temperature: -25 ~ +75°C Easily Wire ConnectionDN-848VI-10VDN-843V-600V IntroductionApplicationsAppearanceProgrammable Automation Controller Products10-1-2Website:E-mail:*******************.PAC2.0.00Accessories101General Channels 8883Input Type AC/DC VoltageInput Range +/- 10 V pp+/- 80 V pp+/- 150 V pp+/- 600 V ppOutput Range +/- 10 V pp Accuracy1% of FSRChanel to Channel Isolation Yes, 3000 V DC-Bandwidth 30 KHz100 KHzInput Impedance> 1 M ΩIntra-module Isolation, Input to Output 3000 V DC -EMS Protection ESD (IEC 61000-4-2)+/- 4 kV contact for power line, input and output channels , +/- 8 kV air for random pointSurge (IEC 61000-4-5)+/- 3 kV for power linerPower Input Input Range +10 ~ +30 V DCPower Consumption 9.2 W9.2 W9.2 W0.56 WMechanicalDimensions (W x L x H)122 mm x 174 mm x 33 mm122 mm x 174 mm x 24.5 mmInstallation DIN-Rail MountingEnvironment Operating Temperature -25 ~ + 75°C Storage Temperature -30 ~ +75°CHumidity10 ~ 90% RH (non-condensing)8-channel 10 V Voltage Attenuator (RoHS)8-channel 80 V Voltage Attenuator (RoHS)8-channel 150 V Voltage Attenuator (RoHS)3-channel 600 V Voltage Attenuator (RoHS)MDR-20-24 CR24 V/1 A, 24 W Power Supply with DIN-Rail Mounting (RoHS)I-7017-G CR 8-channel Analog Input Module (RoHS)I-87017-G CR 8-channel Analog Input Module (RoHS)Selection GuideDN-84-x xx xxx Number of Channels 3: 3 channels 8: 8 channelsV: VoltageI: Channel to channel IsolationInput Voltage RangeDimensions (Units: mm)Bottom View Top View Bottom ViewTop View Left View Front View Rear ViewRight View Left View Front View Rear ViewRight View Speci fi cationsOrdering InformationAccessoriesProfessional Provider of High Quality I ndustrial C omputer P roducts and D ata A cquisition S ystems Vol. PAC 2.0.00102A c c e s s o r i e sDN-843I-CT-20DN-843I-CT-50DN-843I-CT-10DN-843I-CT-1 10.2. Current TransformerThe maximum input range is from ±1 A to +/- 50 A and can be attenuated to from ±1.6 V to ±10 V . The "I" version provide 3000 V DC intra-modules isolation and 3000 V DC channel to channel isolation to avoid the noise interference from inputs to outputs or channel to channel. It can be used with the analog input modules such as I-7017 and I-87017 etc. to measure the high current.AC/DC Source Input Linear Attenuation RatioHigh Current Input MeasurementIsolation InputChannel to Channel Isolation4 kV ESD Protection RoHS ComplianceOperating Temperature: -25 ~ +75°C Easily Wire ConnectionInstallationCh1 Current InputCh2 Current InputCh3 Current Input24 V DCCh1 OutputCh2 OutputCh3 OutputF.G. IntroductionApplicationsProgrammable Automation Controller Products10-2-2Website:E-mail:*******************.PAC2.0.00Accessories102General Channels 3Input Type AC/DC CurrentInput Range +/- 1 A+/- 10 A+/- 20 A+/- 50 AOutput Type AC/DC VoltageOutput Range +/- 1.6 V pp+/- 10 V pp+/- 10 V pp+/- 4 V ppCT Type Solid Core (closed)Accuracy1% of FSR Chanel to Channel IsolationYes, 3000 V rmsIntra-module Isolation, Input to Output 3000 V DC Bandwidth 50 KHz Input Impedance > 1 M ΩEMS Protection ESD (IEC 61000-4-2)+/- 4 kV contact for power line, input and output channels, +/- 8 kV air for random pointPower Input Input Range +10 ~ +24 V DCPower Consumption 1.2 WMechanicalDimensions (W x L x H)148 mm x 83 mm x 39 mmInstallation DIN-Rail Mounting Environment Operating Temperature -25 ~ + 75°C Storage Temperature -30 ~ +75°CHumidity10 ~ 90% RH (non-condensing)3-channel 1 A Current Transformer (RoHS)3-channel 10 A Current Transformer (RoHS)3-channel 20 A Current Transformer (RoHS)3-channel 50 A Current Transformer (RoHS)MDR-20-24 CR24 V/1 A, 24 W Power Supply with DIN-Rail Mounting (RoHS)I-7017-G CR 8-channel Analog Input Module (RoHS)I-87017-G CR8-channel Analog Input Module (RoHS)DN-84--xxxx xC: CurrentCT: Current TransformerInput Current RangeBottom ViewTop ViewLeft ViewFront ViewRight ViewNumber of Channels3: 3 channelsSelection GuideDimensions (Units: mm)Speci fi cationsOrdering InformationAccessoriesI C P roducts and D ata A cquisition S ystems Vol. PAC 2.0.00103A c c e s s o r i e s10.3. Signal Conditioning Modules (SG-3000 Series)DescriptionSG-3016SG-3071SG-3081PicturesAnalog Input Channel 11111Wiring Differential 2/3/4 wiresDifferential Differential Differential Signal ThermocoupleRTDStrain GaugeVoltage Current Type Type J, K, T , E, R, S, B, N, C, L,M, L2Pt100 α=0.00385, Pt100α=0.003916, Ni 120, Pt1000α=0.00385±10 mV , ±20 mV , ±30 mV ,±50 mV , ±100 mV ±5 V ,±10 V 0 ~ 20 mA, 4 ~ 20 mAResolution 12-bit 12-bit ---Accuracy ±0.2% of FSR±0.1% of FSR±0.1% of FSR±0.1% of FSR±0.1% of FSRInput Impedance 1.8 M Ω-- 1.6 M Ω250 ΩExcitation Voltage --0 ~ 10 V--Analog Output Channel 11111Current Output 0 ~ 20 mA 0 ~ 20 mA, 4 ~ 2 0mA 0 ~ 20 mA0 ~ 20 mA, 4 ~ 20 mA0 ~ 20 mA, 4 ~ 20 mA Voltage output 0 ~ 10 V0 ~ 5 V , 0 ~ 10 V±5 V , ±10 V , 0 ~ 5 V , 0 ~ 10 V±5 V , ±10 V0 ~ 5 V , 0 ~ 10 VSystem 3-way Isolation 1000 V DC Power Input 10 ~ 30 V DCPower Consumption 1.44 W1.2 W1.44 W 1.8 W1.61 WOperating Temperature -25 ~ +75°CDimensions (W x H x D)25 mm x 114 mm x 71 mmPW-3090-5SPW-3090-4824S-12PicturesInput 18 ~ 36 V (non-regulated)18 ~ 36 V (non-regulated)18 ~ 36 V (non-regulated)48 V (non-regulated)Output ********(Max.)********(Max.)5 V @ 2 A (Max.)********(Max.)Isolation 1000 V DCEf fi ciency83% Typical Operating Temperature -25 ~ +75°CDimensions (W x H x D)25 mm x 114 mm x 71 mmSG-3000 series signal conditioning modules are used to accept wide range of input signals, such as voltage, current, temperature (thermocouple and RTD) and provide 0 ~ 10 V DC , 0 ~ 20 mA, 4 ~ 20 mA output signals. It gives following good features for industrial applications • 3-way (power/input/output) isolation (1000 V DC )• Wide operating temperature (-25 ~ +75°C)• DIN-Rail mounting• Input and output connectors on the opposite side • Signal range con fi gureable by swtichIntroductionApplicationsProgrammable Automation Controller Products10-4-1Website:E-mail:*******************.PAC2.0.00Accessories104RM-38.61RM-48.61RM-48.62PicturesRelay Finder 20.22.9.024.4000Finder 22.22.9.024.4000Finder 34.51.7.024.0010FINDER - 40.61.7.024.0000FINDER - 44.62.7.024.0000Type Step RelayPower RelayChannel 1ContactForm A (DPST)Form A (DPST)Form C (SPDT)Form C (SPDT)Form C (SPDT)Operating Voltage Range 230 V AC 230 V AC 250 V AC 250 V AC 250 V AC Max. Load Current 16 A 20 A 6 A 16 A 10 A Operate Time 15 ms 15 ms 5 ms 7 ms 7 ms Release Time 8 ms8 ms3 ms 3 ms3 msLED Indicator -MechanicalDimensions (W x L x D)17.5 mm x 84 mm x 62.7 mm 76.5 mm x 6.5 mm x 89 mm75 mm x 15.5 mm x 78.5 mmInstallationDIN-Rail MountingNote1: RM-38.61: 5 pcs in one packageRM-48.61: 4 pcs in one package RM-48.62: 4 pcs in one packageNote2: RM-38-093.20is a 20-way jumper link for RM-38.61DN-SSR4PicturesRelay A5P-204UD3P-054Type Solid-State Relay Channel 4 channels ContactForm A (SPST)Operating Voltage Range 250 V AC /30 V DC50 V DCMax. Load Current 4 AOperate Time 1/2 Cycle + 1ms and below 0.5 ms and below (Resistance load)Release Time 1/2 Cycle + 1ms and below0.5 ms and below (Resistance load)LED Indicator Yes (for Relay status)MechanicalDimensions (W x L x D)101 mm x 77 mm x 66 mmInstallationDIN-Rail MountingPicturesRelay VE-24H5-K FINDER - 40.61.7.024.0000FINDER - 44.52.7.024.0000Type Power Relay Channel 4RM-104: 4 channels RM-108: 8 channels RM-116: 16 channels RM-204: 4 channels RM-208: 8 channels RM-216: 16 channels ContactForm C Form C (SPDT)Form C (DPDT)Operating Voltage Range 250 V AC /30 V DC250 V AC 250 V AC Max. Load Current 5 A 16 A 6 A Operate Time 10 ms (Typical)7 ms (Typical)8 ms (Typical)Release Time 5 ms (Typical)3 ms (Typical) 5 ms (Typical)LED Indicator Yes (for Relay status)MechanicalDimensions (W x L x D)96 mm x 103 mm x 34 mmRM-104: 79 mm x 87 mm x 63 mm RM-108: 135 mm x 87 mm x 63 mm RM-116: 270 mm x 87 mm x 63 mmRM-204: 90 mm x 87 mm x 63 mm RM-208: 169 mm x 87 mm x 63 mm RM-216: 327 mm x 87 mm x 63 mmInstallationDIN-Rail Mounting10.4. Relay ModulesI ndustrial C omputer P roducts and D ata A cquisition S 105A c c e s s o r i e s10.5. Power SuppliesModelsKA-52F DIN-KA52F KA-52F-48DIN-KA52F-48Input Range 100 ~ 250 V AC Frequency 50 ~ 60 HzOutput Power 24 V DC /1.04 A Max., 25 W48 V DC /0.52 A Max., 25 WMechanicalDimensions(W x H x D, Units: mm)54 x 93 x 36 68 x 107 x 50 54 x 93 x 36 68 x 107 x 50 Installation No-mountingDIN-Rail MountingNo-mountingDIN-Rail MountingEnvironmentalOperating Temperature 0 ~ +50°C Storage Temperature-20 ~ +85°CModelsMDR-20-24MDR-60-24MDR-60-48Input Range 100 ~ 250 V AC Frequency 50 ~ 60 HzOutput Power 24 V DC /1 A Max., 24 W24 V DC /2.5 A Max., 60 W48 V DC /1.25 A Max., 60 WMechanicalDimensions (W x H x D)22.5 mm x 90 mm x 100 mm 40 mm x 90 mm x 100 mm 40 mm x 90 mm x 100 mmInstallation DIN-Rail MountingEnvironmental Operating Temperature -20 ~ +70°C Storage Temperature-20 ~ +85°CModelsDP-660DP-1200Input Range 100 ~ 250 V AC Frequency 50 ~ 60 HzOutputPower 24 V DC /2.5 A Max., 60 W and5 V DC /0.5 A Max., 2.5 W24 V DC /5.0 A Max., 120 WMechanicalDimensions (W x H x D)44 mm x 145 mm x 158 mm 65 mm x 111 mm x 125 mmInstallation DIN-Rail MountingEnvironmentalOperating Temperature 0 ~ +50°C -10 ~ +70°C Storage Temperature-20 ~ +85°C-25 ~ +85°CKA-52F CR 24 V DC /1.04 A, 25 W Power Supply (RoHS)DIN-KA52F CR 24 V DC /1.04 A, 25 W Power Supply with DIN-Rail Mounting (RoHS)KA-52F-48 CR 48 V DC /0.52 A, 25 W Power Supply (RoHS)DIN-KA52F-48 CR48 V DC /0.52 A, 25 W Power Supply with DIN-Rail Mounting (RoHS)MDR-20-24 CR 24 V DC /1 A, 24 W Power Supply with DIN-Rail Mounting (RoHS)MDR-60-24 CR 24 V DC /2.5 A, 60 W Power Supply with DIN-Rail Mounting (RoHS)MDR-60-48 CR48 V DC /1.25 A, 60 W Power Supply with DIN-Rail Mounting (RoHS)DP-660 CR 24 V DC /2.5 A, 60 W and 5 V DC /0.5 A, 2.5 W Power Supply with DIN-Rail Mounting (RoHS)DP-1200 CR24 V DC /5.0 A, 120 W Power Supply with DIN-Rail Mounting (RoHS)KA-52F/DIN-KA52F KA52F-48/DIN-KA52F-48MDR-20-24MDR-60-24MDR-60-48DP-660DP-1200KA-52F KA-52F-48MDR-60-24/MDR-60-48DP-1200MDR-20-24DP-660DIN-KA52F DIN-KA52F-48Speci fi cationsSpeci fi cationsSpeci fi cationsOrdering InformationOrdering InformationOrdering InformationProgrammable Automation Controller Products10-6-1Website:E-mail:*******************.PAC2.0.00Accessories106TPM-4100TP-410010.6. Touch Panel MonitorTPM-4100/TP-410010.4" Touch Panel Monitor10.4" LCD supports 800 x 600 resolution Resistive Touch Panel Full-function OSD controlDriver Support: Windows 2k/XP/Vista/7/WESWinCE 5.0/6.0 LED backlight technology Aluminum Casing for TPM-4100 IP65 Comlipant Front PanelWide operating temperature: -25 ~ +75°CTPM-4100TP-4100Display Size 10.4”Resolution 800 x 600Max. Color 16.7 M Brightness (cd/m2)320Contrast Ratio 500 : 1Viewing Angle (H/V)140/130Backlight Life (hrs)50,000Touch Panel 4-wire5-wireanalog resistive, RS-232 or USB1.1 (Type B) interfaceInput SignalVGA (Analog RGB)MMI (Man Machine Interface)OSD Control Functions: Brightness, Contrast, Phase, Horizontal Position,Vertical Position and SharpnessPower Switch YesLED Indicators Power , Display signal is detectedPower Input Range +12 ~ 48 V DCPower Consumption 8.5 WMechanical MaterialAluminumPlasticDimensions (W x L x H)293 mm x 231 mm x 53 mm290 mm x 228 mm x 53 mm Installation Panel MonutingPanel Monuting, VESA (75 × 75) MountingIngress Protection Front panel: IP65Environmental Operating Temperature -25 ~ +75°C Storage Temperature -30 ~ +80°CAmbient Relative Humidity10 ~ 90% RH (non-condensing)10.4" (800 x 600) resistive touch panel monitor with RS-232 or USB interfaceAccessories: Power supply, VGA cable, RS-232 cable, USB cable, Mounting clamps and screws TP-4100 with Aluminum Casing273210.8TPM-4100 Dimensions (Units: mm)Speci fi cationsAppearanceOrdering InformationUSB USBOSD OSDRS-232RS-232VGAVGA Power Switch Power Switch VESA (75 × 75) Mounting12 ~ 48 DC IN12 ~ 48 DC INI ndustrial C omputer P roducts and D ata A cquisition S ystems Vol. PAC 2.0.00106A c c e s s o r i e sTP-30707" Touch Panel Monitor7" LCD supports 800 x 480 resolution Resistive Touch Panel Full-function OSD controlDriver Support: Windows 2k/XP/Vista/7/WESWinCE 5.0/6/0 LED backlight technology IP65 Comlipant Front PanelWide operating temperature: -20 ~ +70°CTP-3070Display Size 7”Resolution 800 x 480Brightness (cd/m2)320Contrast Ratio 500 : 1Viewing Angle (H/V)140/120Backlight Life (hrs)20,000Touch Panel 4-wire, analog resistive, RS-232 or USB1.1 (TypeB) interfaceInput SignalVGA (Analog RGB)MMI (Man Machine Interface)OSD Control Functions: Brightness, Contrast, Clock, Phase, Horizontal Position, Vertical Position and SharpnessPower Switch YesLED Indicators Power , Display signal is detectedPower Input Range +12 ~ 48 V DCPower Consumption 5 WMechanicalDimensions (W x L x H)213 mm x 148 mm x 44 mmCasingPlastic Ingress Protection Front panel: IP65Environmental Operating Temperature -20 ~ +70°C Storage Temperature -30 ~ +80°CAmbient Relative Humidity10 ~ 90% RH (non-condensing)7" (800 x 480) resistive touch panel monitor with RS-232 or USB interfaceAccessories: Power supply, VGA cable, RS-232 cable, USB cable, Mounting clamps and screwsDimensions (Units: mm)Speci fi cationsOrdering InformationProgrammable Automation Controller Products10-7-1Website:E-mail:*******************.PAC2.0.00Accessories 107InterfaceUSBCompatibility: USB 1.1 and 2.0 standards RS-232TxD, RxD, RTS, CTS, DSR, DTR, DCD, RI and GND; non-isolated Baud Rate300 ~ 115200 bps DriverWindows 98/ME/2000/XP/Vista (32/64-bit)/7 (32/64-bit)/LinuxMechanicalDimensions (W x H x D)33 mm x 60 mm x 15 mm Environmental Operating Temperature-25 ~ +75°C Storage Temperature -30 ~ +75°CInterfacePortsUpstream x 1 (Type B); Downstream x 4 (Type A)CompatibilitySpeci fi cation Rev. 2.0/1.1/1.0Transfer Speed480 Mbit/s-high speed mode Input Voltage Range+10 ~ +30 V DCMechanicalDimensions (W x H x D)33 mm x 107 mm x 78 mm InstallationDIN-Rail Mounting Environmental Operating Temperature -0 ~ +70°C Storage Temperature -20 ~ +80°CMechanical Dimensions (W x H x D)481 mm x 132 mm x 125 mm USB-2020 CR USB Audio Device (RoHS)RK-3UD-R 19" Rack Mounting Kit, 3U I-7560 CR USB to RS-232 Converter (RoHS)USB-2560 CR4-port Industrial USB 2.0 Hub (RoHS)USB-2560/S CR 4-port Industrial USB 2.0 Hub (RoHS) with GPSU06U-6 (Power Supply)RK-3UD-R I-7560InterfaceOutput ChannelsMono, Stereo (L + R)Input ChannelsMono, Stereo (L + R)ButtonHID volume up, volume down and Mute Input Voltage Range+10 ~ +30 V DCMechanicalDimensions (W x H x D)33 mm x 107 mm x 78 mm Installation DIN-Rail Mounting Environmental Operating Temperature-25 ~ +75°C Storage Temperature -40 ~ +85°C 10.7. MISC Speci fi cationsSpeci fi cationsSpeci fi cationsSpeci fi cationsOrdering InformationOrdering InformationOrdering Information Ordering Information USB to RS-232 Converter USB-2020USB-2560USB Audio Device 4-Port Industrial USB 2.0 Hub19" Rack Mounting Kit, 3UiP-84112-4-3 iP-88112-4-3 iP-84412-4-3 iP-88412-4-3 iP-8441-FD2-4-3 iP-8841-FD2-4-3 iP-84172-4-5Model Name PageiP-84472-4-5iP-88172-4-5iP-88472-4-5I-87005W5-2-1I-87013W5-2-1I-87015PW5-2-2I-87015W5-2-2I-8014W5-2-3I-8017DW5-2-3I-8017HCW5-2-3I-8017HW5-2-3I-8024DW5-2-3I-8024W5-2-3I-87017DW5-2-4I-87017RCDW5-2-4I-87017RCDW-AI5-2-4I-87017RCW 5-2-4I-87017RW 5-2-4I-87017W5-2-4I-87017W-A55-2-4I-87017ZW5-2-4I-87018PW5-2-5I-87018RW5-2-5I-87018W5-2-5I-87018ZW5-2-5I-87019PW5-2-6I-87019RW5-2-6I-87019ZW5-2-6I-87024W 5-2-7I-87024CW5-2-7I-87024DW 5-2-7I-87024RW 5-2-7I-87024UW 5-2-7I-87028CW5-2-7I-8040PW5-3-1I-8040W5-3-1I-8046W5-3-1I-8048W5-3-1I-8051W5-3-1I-8052W5-3-1I-8053W5-3-1I-8053PW5-3-1Model Name PageI-8058W5-3-1I-87040W5-3-2I-87040PW5-3-2I-87046W5-3-2I-87051W5-3-2I-87052W5-3-2I-87058W5-3-2I-87059W5-3-2I-87053W5-3-3I-87053PW5-3-3I-87053W-A55-3-3I-87053W-AC15-3-3I-87053W-E55-3-3I-8037W5-3-4I-8041W5-3-4I-8041RW5-3-4I-8041AW5-3-4I-8056W5-3-4I-8057W5-3-4I-8057RW5-3-4I-8057PW5-3-4I-8060W5-3-4I-8064W5-3-4I-8068W5-3-4I-8069RW5-3-4I-8069W5-3-4I-87037W5-3-5I-87041W 5-3-5I-87057W5-3-5I-87057PW5-3-5I-87061W5-3-5I-87064W5-3-5I-87065W5-3-5I-87066W5-3-5I-87068W5-3-5I-87069W5-3-5I-87069PW5-3-5I-8042W5-3-6I-8050W5-3-6I-8054W5-3-6I-8054RW5-3-6I-8055W5-3-6Model Name PageI-8063W5-3-6I-87042W5-3-7I-87054W5-3-7I-87055W5-3-7I-87063W5-3-7I-8026PW5-4-1I-87016W5-4-1I-87026PW5-4-1I-87089W/S5-5-1I-8084W5-6-1I-8088W5-6-1I-87082W5-6-1I-87084W5-6-1I-87088W5-6-1I-8092F5-7-1I-8093W5-7-1I-80945-7-1I-8094A5-7-1I-8094F5-7-1I-8094H5-7-1I-75105-8-1I-7510A5-8-1I-7510AR5-8-1I-75135-8-1I-7514U5-8-1I-7520 5-8-1I-7520A5-8-1I-7520AR5-8-1I-7520R5-8-1I-7520U45-8-1I-75515-8-1I-8112iW5-8-1I-8114iW5-8-1I-8114W5-8-1I-8142iW5-8-1I-8144iW5-8-1I-25325-9-2I-25335-9-2I-75305-9-2I-7530A5-9-2I-7530A-MR5-9-2I-7530-FT5-9-2Model IndexI-75315-9-2 I-75325-9-2 I-7540D5-9-2 I-7540D-MTCP5-9-2 I-7540D-WF5-9-2 I-75655-9-2I-7565-H15-9-2 I-7565-H25-9-2 I-8120W5-9-2 I-8123W5-9-2 I-8124W5-9-2 I-871235-9-2 I-871245-9-2 I-87H17W5-10-1 I-87H24W5-10-1 I-75475-10-1 I-75675-10-1 I-75705-10-1 I-8172W5-11-1 I-8212W5-12-1 I-8212W-3GWA5-12-1 I-8213W5-12-1 I-8213W-3GWA5-12-1 I-87211W 5-12-1 iP-8441-MTCP6-3-2 iP-8841-MTCP6-3-2 I-7188XG7-1-6 I-7188XGD7-1-6 I-71887-1-9 I-7188D7-1-9 I-7188XA7-1-9 I-7188XAD7-1-9 I-7188XB7-1-9 I-7188XBD7-1-9 I-7188XC7-1-9 I-7188XCD7-1-9 I-7188EA7-1-11 I-7188EAD7-1-11 I-7188EX7-1-11 I-7188EXD7-1-11 I-756010-7-1 iDCS-88309-1-3USB-87P25-4-2USB-87P45-4-2USB-87P85-4-2USB-202010-7-1USB-256010-7-1WP-8131 2-2-3WP-84312-2-3WP-88312-2-3WP-81412-2-3WP-84412-2-3WP-88412-2-3WP-80512-2-3WP-83512-2-3WP-87512-2-3WP-81372-2-6WP-84372-2-6WP-88372-2-6WP-81472-2-6WP-84472-2-6WP-88472-2-6WP-80572-2-6WP-83572-2-6WP-87572-2-6WP-81392-2-11WP-84392-2-11WP-88392-2-11PROFI-82556-6-2PROFI-84556-6-2PROFI-88556-6-2PW-3090-5S10-3-1PW-3090-12S10-3-1PW-3090-24S10-3-1PW-3090-4824S-1210-3-1USB-87P15-4-2iDCS-8830R9-1-3PROFI-81556-6-2XP-8349-Atom-CE62-1-14 XP-8749-CE62-1-14 XP-8749-Atom-CE62-1-14 X1017-2-3 X1067-2-3 X1077-2-3 X1107-2-3 X1117-2-3 X2007-2-3 X2027-2-3 X2037-2-3 X3027-2-3 X3037-2-3 X3047-2-3 X3057-2-3 X3087-2-3 X3107-2-3 X3247-2-3 X5037-2-3 X5047-2-3 X5057-2-3 X5067-2-3 X5077-2-3 X5087-2-3 X5097-2-3 X5107-2-3 X510-1287-2-3 X5117-2-3 X5187-2-3 X6037-2-3 X6077-2-3 X6087-2-3 X7027-2-3 X7037-2-3 XV1168-4-1 XV107Ai8-4-2 XV107i8-4-2 XV110i8-4-2 XV111Ai8-4-2 XV111i8-4-2 XW1078-4-2 XW107i8-4-2μPAC-51078-1-7μPAC-5107D8-1-7μPAC-52078-1-7μPAC-5207D8-1-7μPAC-53078-1-7μPAC-5307D8-1-7μPAC-55078-1-7μPAC-5507D8-1-7 XW110i8-4-2XV304i8-4-3XV305i8-4-3XV308i8-4-3XV310i8-4-3XW3048-4-4XW3108-4-4XW310C8-4-4XW5068-4-5XW5078-4-5XW5088-4-5XW5098-4-5XW511i8-4-5XW5148-4-5μμPAC-7186EX 7-1-4μPAC-7186EXD 7-1-4μPAC-7186EX-FD 7-1-4μPAC-7186EXD-FD 7-1-4μPAC-7186EX-SM 7-1-4μPAC-7186EXD-SM 7-1-4μPAC-7186EG7-1-6μPAC-7186EG-D7-1-6μPAC-50018-1-6μPAC-5001D8-1-6μPAC-5001-FD8-1-6μPAC-5001D-FD8-1-6μPAC-5101 8-1-6μPAC-5101D 8-1-6μPAC-52018-1-6μPAC-5201D8-1-6μPAC-53018-1-6μPAC-5301D8-1-6μPAC-55018-1-6μPAC-5501D8-1-6μPAC-5801 8-1-6μPAC-5801D8-1-6μPAC-59018-1-6μPAC-5901D8-1-6μPAC-50078-1-7μPAC-5007D8-1-7WP-81492-2-11WP-84492-2-11WP-88492-2-11WP-80592-2-11WP-83592-2-11WP-87592-2-11WP-51418-2-4WP-5141-OD8-2-4WP-52318-2-6WP-5231-2G8-2-6WP-5231-3G8-2-6WP-5231-GPS8-2-6WP-5231-WF8-2-6WP-5231-ZH8-2-6WP-5231-ZS8-2-6WP-51478-2-8WP-5147-OD8-2-8WP-51498-2-11WP-5149-OD8-2-11XXP-8041 2-1-5XP-8141-Atom2-1-5XP-83412-1-5XP-8341-Atom2-1-5XP-87412-1-5XP-8741-Atom2-1-5XP-8041-CE62-1-7XP-8141-Atom-CE62-1-7XP-8341-CE62-1-7XP-8341-Atom-CE62-1-7XP-8741-CE62-1-7XP-8741-Atom-CE62-1-7XP-8047-CE62-1-9XP-8147-Atom-CE62-1-9XP-8347-CE62-1-9XP-8347-Atom-CE62-1-9XP-8747-CE62-1-9XP-8747-Atom-CE62-1-9XP-8049-CE62-1-14XP-8149-Atom-CE62-1-14XP-8349-CE62-1-14 Model Index。
CAT811STBI-T中文资料

CAT811, CAT8124-Pin Microprocessor Power Supply Supervisors FEATURESs Precision monitoring of+5.0 V (+/- 5%, +/- 10%, +/- 20%),+3.3 V (+/- 5%, +/ 10%),+3.0 V (+/- 10%) and+2.5 V (+/- 5%) power suppliess Offered in two output configurations: - CAT811: Active LOW reset- CAT812: Active HIGH resets Manual reset input s Direct replacements for the MAX811 and MAX812 in applications operating over the industrial temperature ranges Reset valid down to VCC= 1.0 Vs 6 µA power supply currents Power supply transient immunitys Compact 4-pin SOT143 packages Industrial temperature range: -40˚C to +85˚C© 2004 by Catalyst Semiconductor, Inc., Patent Pending Characteristics subject to change without notice Doc. No. 3005, Rev. PAPPLICATIONSs Computerss Serverss Laptopss Cable modemss Wireless communications s Embedded control systemss White goodss Power meterss Intelligent instrumentss PDAs and handheld equipmentDESCRIPTIONThe CAT811 and CAT812 are µP supervisory circuits that monitor power supplies in digital systems. The CAT811 and CAT812 are direct replacements for the MAX811 and MAX812 in applications operating over the industrial temperature range; both have a manual reset input.These devices generate a reset signal, which is asserted while the power supply voltage is below a preset threshold level and for at least 140 ms after the power supply level has risen above that level. The underlying floating gate technology, AE2(TM) used by Catalyst Semiconductor, makes it possible to offer any custom reset threshold value. Seven industry standard threshold levels are offered to support +5.0 V, +3.3 V, +3.0 V and +2.5 V systems.The CAT811 features a RESET push-pull output (active LOW) and the CAT812 features a RESET push-pull output (active HIGH).Fast transients on the power supply are ignored and the output is guaranteed to be in the correct state at V cc levels as low as 1.0 V.The CAT811/812 are fully specified over the industrial temperature range (-40˚C to 85˚C) and are available in a compact 4-pin SOT143 package.PIN CONFIGURATIONTHRESHOLD SUFFIX SELECTORNominal Threshold Threshold Suffix Voltage Designation4.63V L4.38V M4.00V J3.08V T2.93V S2.63V R2.32V ZHA L OG E N F REETML EA D F R E EGND V CCRESET12CAT811, CAT812Doc. No. 3005, Rev. PPatent PendingORDERING INFORMATIONInsert threshold suffix (L, M, J, T, S, R or Z) into the blank position. Example: CAT811LTBI-T for 4.63 V, and lead-free SOT143 package.TOP MARKINGWhere YM stands for Year and Month.re b m u N t r a P g n i r e d r O y t i r a l o P T E S E R e g a k c a P le e R r e p s t r a P T -S U E _118T A C l l u P -h s u P T E S E R 341T O S ,n i p -4k 301T -S U E _118T A C l l u P -h s u P T E S E R 341T O S ,n i p -4k 01T -I B T _118T A C l l u P -h s u P T E S E R n e e r G 341T O S ,n i p -4k 301T -I B T _118T A C l l u P -h s u P T E S E R ne e r G 341T O S ,n i p -4k 01T -S U E _218T A C T E S E R l l u P -h s u P 341T O S ,n i p -4k 301T -S U E _218T A C T E S E R l l u P -h s u P 341T O S ,n i p -4k 01T -I B T _218T A C l l u P -h s u P T E S E R ,n i p -4341T O S n e e r G k 301T -I B T _218T A C l l u P -h s u P TE S E R ,n i p -4341T O S ne e r G k01341T O S ne e r G 341T O S L 118T A C M Y M A M Y H D M 118T A C M Y N A M Y J D J 118T A C M Y Z A M Y K C T 118T A C M Y P A M Y L D S 118T A C M Y Q A M Y M D R 118T A C M Y R A M Y N D Z 118T A C M Y Y A M Y P C L 218T A C M Y S A M Y R D M 218T A C M Y T A M Y T D J 218T A C M Y U A M Y U D T 218T A C M Y V A M Y V D S 218T A C M Y W A M Y W D R 218T A C M Y X A M Y X D Z218T A C MY I C MY Y C3CAT811, CAT812Patent PendingDoc. No. 3005, Rev. P4Doc. No. 3005, Rev. PPatent Pending5CAT811, CAT812Patent PendingDoc. No. 3005, Rev. P6Doc. No. 3005, Rev. PPatent Pending7CAT811, CAT812Patent PendingDoc. No. 3005, Rev. P8Doc. No. 3005, Rev. PPatent Pending9CAT811, CAT812Patent PendingDoc. No. 3005, Rev. P10CAT811, CAT812Doc. No. 3005, Rev. PPatent PendingREVISION HISTORYDate Rev.Reason10/22/03L Updated Ordering Information 12/22/2003MUpdated FeaturesReplaced power-up reset timeout vs. temperature graph with updated oneRelaced VCC Transient Response graph with updated one3/22/04NUpdated Features Updated DescriptionUpdated Ordering Information Added Top MarkingsUpdated Absolute Maximum Ratings Updated Electrical Characteristics Updated Detailed Description3/25/2004OChanged Preliminary designation to Final Updated Top MarkingsUpdated Electrical Characteristics (Reset Active Timeout Period Max)Copyrights, Trademarks and PatentsTrademarks and registered trademarks of Catalyst Semiconductor include each of the following:DPP ™AE 2 ™Catalyst Semiconductor has been issued U.S. and foreign patents and has patent applications pending that protect its products. For a complete list of patents issued to Catalyst Semiconductor contact the Company ’s corporate office at 408.542.1000.CATALYST SEMICONDUCTOR MAKES NO WARRANTY, REPRESENTATION OR GUARANTEE, EXPRESS OR IMPLIED, REGARDING THE SUITABILITY OF ITS PRODUCTS FOR ANY PARTICULAR PURPOSE, NOR THAT THE USE OF ITS PRODUCTS WILL NOT INFRINGE ITS INTELLECTUAL PROPERTY RIGHTS OR THE RIGHTS OF THIRD PARTIES WITH RESPECT TO ANY PARTICULAR USE OR APPLICATION AND SPECIFICALLY DISCLAIMS ANY AND ALL LIABILITY ARISING OUT OF ANY SUCH USE OR APPLICATION, INCLUDING BUT NOT LIMITED TO, CONSEQUENTIAL OR INCIDENTAL DAMAGES.Catalyst Semiconductor products are not designed, intended, or authorized for use as components in systems intended for surgical implant into the body, or other applications intended to support or sustain life, or for any other application in which the failure of the Catalyst Semiconductor product could create a situation where personal injury or death may occur.Catalyst Semiconductor reserves the right to make changes to or discontinue any product or service described herein without notice. Products with data sheets labeled "Advance Information" or "Preliminary" and other products described herein may not be in production or offered for sale.Catalyst Semiconductor advises customers to obtain the current version of the relevant product information before placing orders. Circuit diagrams illustrate typical semiconductor applications and may not be complete.Publication #:3005Revison:P Issue date:3/25/04Type:FinalPatent Pending Catalyst Semiconductor, Inc.Corporate Headquarters1250 Borregas AvenueSunnyvale, CA 94089Phone: 408.542.1000Fax: 408.542.1200 元器件交易网。
Agilent 81110A 数字信号源数据手册说明书
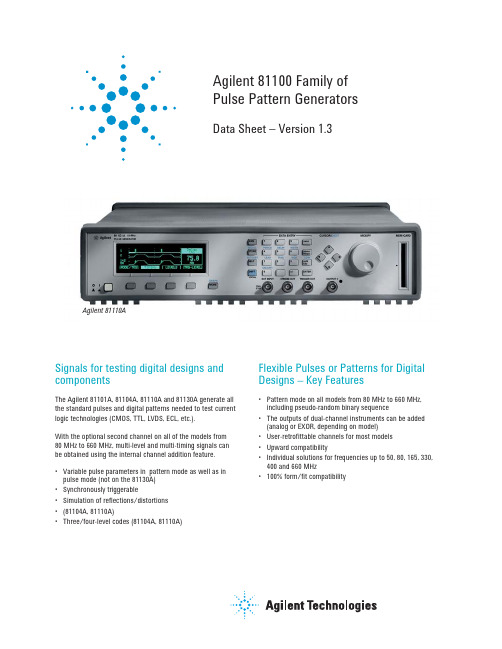
Agilent 81110A Agilent 81100 Family ofPulse Pattern GeneratorsData Sheet – Version 1.3Flexible Pulses or Patterns for DigitalDesigns – Key Features• Pattern mode on all models from 80 MHz to 660 MHz,including pseudo-random binary sequence• The outputs of dual-channel instruments can be added(analog or EXOR, depending on model)• User-retrofittable channels for most models• Upward compatibility• Individual solutions for frequencies up to 50, 80, 165, 330, 400 and 660 MHz• 100% form/fit compatibilitySignals for testing digital designs and componentsThe Agilent 81101A, 81104A, 81110A and 81130A generate all the standard pulses and digital patterns needed to test current logic technologies (CMOS, TTL, LVDS, ECL, etc.).With the optional second channel on all of the models from 80 MHz to 660 MHz, multi-level and multi-timing signals can be obtained using the internal channel addition feature.• Variable pulse parameters in pattern mode as well as in pulse mode (not on the 81130A)• Synchronously triggerable• Simulation of reflections/distortions• (81104A, 81110A)• Three/four-level codes (81104A, 81110A)Glitch-free timing changesTiming values can now be swept without the danger of misleading pulses ordropouts that could cause measurement errors. (Applies to continuous mode, values < 100 ms, consecutive values between 0.5 and twice the previous value on the 81101A, 81104A, 81110A).Reliable measurementsAll models provide clean, accurate pulses with excellent repeatability, thus contribut-ing to measurement integrity.The Agilent 81110A features self-calibration for more accuracy. It also offers a choice of output modules. The Agilent 81111A 165 MHz 10 V module with variable transitions.Along with the Agilent 81112A 330 MHz 3.8 V module, which has differential out-puts and two selectable transition times.The Agilent 81130A offers a choice of output modules: the Agilent 81131A 400 MHz, 3.8 V module and the Agilent 81132A 660 MHz, 2.5 V module which has complementary outputs.Easy-to-useFeatures such as the clear graphicaldisplay, autoset, help, store/recall, preset TTL/ECL levels, selectable units (such as current/voltage, width/duty-cycle), and load compensation ensure a high level of convenience.Stimulate the device’s environmentToday’s devices can require very complex stimuli. To meet this, the Agilent 81130A can sequence and loop its memory for very deep patterns. RZ (return-to-zero), NRZ (non-return-to- zero) and R1 (return-to-one) formats are available. Digital channel addition allows the generation of signals with two different pulse widths and delays or of data rates up to 1.32 Gbit/s in one single channel.Frequency rangeThe Agilent 81130A is designed and recommended for an operation in the frequency range of 170 kHz to 400/660 MHz. However it can be operated in the extended range down to 1 kHz.Data Sheet 81100 Family of Pulse Pattern Generators21. Depends on selected impedance (all other values for 50 Ω source impedance into 50 Ω load).2. 0.001% +15 ps with internal PLL as clock source.3. Also avalable as VXI pulse pattern generators E8311A and E8312A.Agilent 81100 - Family of Pulse Pattern Generators81101A SpecificationsBurst Count : 2 to 65536 (single or double pulses).Delay : Delay, phase or % of period.Double pulse delay : Double pulse and delay are mutually exclusive.Duty cycle : Set between 0.1% and 95% (subject to width limits. 99.9% with overprogramming).Transition times: These can be entered as leading/trailing edge or % of width. Leading and trailing edges are indepen-dent within one of the following over-lapping segments (1:20 ratio):• 5 ns - 20 ns • 10 ns - 200 ns • 100 ns - 2 µs • 1µs - 20 µs • 10 µs - 200 µs • 100 µs - 2 ms • 1 ms - 20 ms •10 ms - 200 msData Sheet 81100 Family of Pulse Pattern Generators3Repeatability : Is typically four times better than accuracyOutput timing fidelity : Period, delay and width are continuously variable without any output glitches or dropouts.Data Sheet 81100 Family of Pulse Pattern GeneratorsTrigger modesContinuous : Continuous pulses, double pulses or bursts (single or double pulses).External triggered : Each active inputtransition (rising, falling or both) generates a single or double pulse or burst.External gated : The active input level (high or low) enables pulses, double pulses or bursts. The last single/double pulse or burst is always completed.External width : The pulse shape can be recovered whilst the period and width of an external input signal are maintained. Levels and transitions can be set.Manual : Simulates an external input signal.Internal triggered : Internal PLL replaces an external trigger source.Inputs and outputsClock input/PLL reference and external input: One input (BNC connector at rear panel) is used for clock input or alterna-tively for the PLL.PLL reference : The internal PLL is locked to an external 5 MHz or 10 MHz reference frequency.Clock input : The output period isdetermined by the signal at CLK input. Ext. input : Used for trigger, gate or external width.Level parameters: Can be entered as volt-age or current, as high and low level, or as offset and amplitude.Load compensation:The actual load value can be entered (for loads ≠ 50 Ω) to display actual output values. On/off: Relays connect/disconnect output (HiZ).Normal/complement: Selectable.Limit : Programmable high and low levels can be limited to protect the device-under-test.Input impedance : 50 Ω/10 kΩ selectable.Threshold : -10 V to +10 V.Max. input voltage : ±15 Vpp.Sensitivity : 300 mVpp typical.Input transitions : < 100 ns.Frequency : Dc to 50 MHz.Minimum pulse width : 10 nsStrobe output and trigger output trigger format : One pulse per period with 50% duty cycle typical.External mode : 9 ns typ.Level : TTL or ECL selectable.Output impedance : 50 Ω typical.Max. external voltage : -2 V/+7 V.Transition times : 1.0 ns typical for TTL, 600 ps typical for ECL.41. In ±19 V level window81104A and 81110A SpecificationsBurst count: 2 to 65536 (single or double pulses).Delay : Delay, phase or % of period.Double pulse and delay : Mutually exclusive.Duty cycle : Set between 0.1% and 95% (subject to width limits. 99.9% with over-programming).Repeatability : Is typ. four times better than accuracy.Transition times : leading/ trailing edge or % of width. Leading and trailing edges are independent Agilent 81111A/Agilent 81105A) within one of the following overlapping segments (1:20 ratio): • 2 ns (3 ns) - 20 ns • 10 ns - 200 ns • 100 ns - 2 ms • 1µs - 20 µs • 10 µs - 200 µs • 100 µs - 2 ms • 1 ms - 20 ms •10 ms - 200 msOutput timing fidelity : Period, delay and width are continuously variable without any output glitches or dropouts.Overprogramming : All parameters of the Agilent 81110A, except transitions, can be set to whatever the 330 MHz timing system will allow. This applies also when the Agilent 81111A (165 MHz) output module is used.Data Sheet 81100 Family of Pulse Pattern Generators51. Source impedance is selectable from 50 Ω to 1 KΩ for the Agilent 81111A.2. Changing of amplitude may add 0.5 ns.Level/Pulse Performance CharacteristicsLevel parameters: voltage or current, high or low level, offset or amplitude.On/off: relays connect/ disconnect output (HiZ).Load compensation: the actual load value can be entered (forloads ≠ 50 Ω) to display actual output values. (Applies to theAgilent 81105A and Agilent 81111A only).Normal/complement: selectable.Limit: programmable high and low levels can be limited to protect the device-under-test.Channel Addition (with Agilent 81105A or Agilent 81111A output channels)If the instrument is equipped with 2 output modules, channel 2 can be added to channel 1 internally. In this case the second output is disabled. The additional fixed delay on the second channel is typ. 2.5 ns. The following parameters differ from the above specifications if two output modules (Agilent 81105A/Agilent 81111A) are added.Data Sheet 81100 Family of Pulse Pattern Generators61. In ± 19 V level window.Pattern modePattern length: 16 kbit/channel and strobe output.Output format: RZ (return to zero), NRZ (non-return to zero), DNRZ (delayednon-return to zero).Random pattern:PRBS 2 ^ (n - 1) n = 7,8, (14)Trigger modesContinuous: Continuous pulses, double pulses, bursts (single or double pulses)or patterns.External triggered: Each active input transition (rising, falling or both) generates a single or double pulse,burst or pattern.External gated: The active input level (high or low) enables pulses, double pulses, bursts or patterns. The last single/double pulse, burst or patternis always completed.External width: The pulse shape can be recovered. Period and width of an external input signal is maintained. Delay, levels and transitions can be set.Manual: Simulates an external input signal.Internal triggered: Internal PLL replaces an external trigger source. Pulses, double pulses, bursts or patterns can be set.Strobe output and trigger outputStrobe output: User-defined, 16 kbitpattern (NRZ) when in pattern mode.Trigger format: One pulse per period with50% duty cycle typical. External mode:1.5 ns typ. for Agilent 81110A. 5.9 ns typ.for Agilent 81104A.Level: TTL or ECL selectable.Output impedance: 50 Ω typical.Max. external voltage: - 2 V/+7 V.Transition times: 1.0 ns typical for TTL,600 ps typical for ECL.Inputs and OutputsClock input/PLL reference andexternal inputPLL reference: (BNC connector at rearpanel). The internal PLL is locked to anexternal 5 MHz or 10 MHz referencefrequency.Clock input: (BNC connector at rearpanel). The output period is determinedby the signal at CLK input.Ext. input: Used for trigger, gate orexternal width.Input impedance: 50 Ω/10 kΩ selectable.Threshold: - 10 V to + 10 V.Max. input voltage: ± 15 Vpp.Sensitivity: ≤ 300 mVpp typical.Transitions: < 100 ns.Frequency: dc to max. frequencyof output module.Min. pulse width: 1.5 ns (as width ofoutput module in external width mode).711. Subtract 4 ns from the typ. delay value when referring to OUTPUT 1 / 2 for the Agilent 81112A output module and add 1 ns when referring toOUTPUT 1 / 2 for the Agilent 81104A with the Agilent 81105A output module.Data Sheet 81100 Family of Pulse Pattern GeneratorsData Sheet 81100 Family of Pulse Pattern Generators8Burst count : 2 to 65504.Delay : Delay, phase or % of period.Duty cycle : Set between 0.1% and 99,9% (subject to width limits).Repeatability : Is typ. four times better than accuracy.1. The uncertainty of 1 period can be eliminated if an external clock and the following setup and hold times are upheld. setup time: 0.3 ns to 4.3 ns; hold time: -2.8 ns to 4.0 ns.Data Sheet 81100 Family of Pulse Pattern GeneratorsSequencing : A sequence is a succession of segments. One outer loop running once or continuous, and one nested loop can be applied. The nested loop can be set from 1 to 2 ^ 20 repetitions.Segment : The memory can be divided into maximal 4 segments.Segment length resolution : This is the resolution for which the segment can be set dependent on the maximum data rate. See Table 1.Limit : Programmable high and low levels can be limited to protect the device-under-test.Segment types: Pattern, PRBS, high and low segments ( “0” or “1” levels segments selectable).Note : If one channel is set to PRBS the other channel can only be high or low segments, or PRBS type.Random pattern : PRBS 2 ^ n - 1,n = 7,8,...,15 (CCITT 0.151).Level parameters : Voltage or current, high and low level, or offset and amplitude.Pattern and sequencingPattern length: 65504 bit/channel. If PRBS is used: (65503-RBLength).Pattern formats : NRZ (non-return-to-zero), DNRZ (delayed non-return-to-zero), RZ (return-to-zero) and R1 (return-to-one) can be selected (see Figure 1).On/off : Relays connect/disconnect output (HiZ).9Segment length resolution trade-offs1. The minimum length in the first segment of a nestedloop is two times that of the segment length resolution.Width is a multiple of clock periods.Width and delay can be set as required.Width and delay can be set as required.The signal can be delayed as required.Output pattern formats Non-return-to-zeroR1RZ DNRZNRZReturn-to-oneReturn-to-zero Delayed non-return-to-zeroData Sheet 81100 Family of Pulse Pattern GeneratorsTrigger modesContinuous : Continuous pulses, bursts or patterns.External started : Each active input transi-tion (rising, falling edge) generates pulses, bursts or patterns.External gated : The active input level (high or low) enables pulses, bursts or patterns. On an external gate signal the output is immediately stopped, that means the last cycle will not be completed.Manual : Simulates an external input signal with push of a front panel button.Inputs and outputsClock input/PLL reference and external inputConnectors : SMA (f) 3.5 mm Input impedance : 50 ΩTermination voltage : -2.10 V to 3.30 V Input sensitivity : < 400 mV typ.Max. input voltage : -3 V to + 6 V Input transitions : < 20 nsOnly valid for clock input/PLL reference One input is used for clock input or for the PLL reference alternatively.Reference : The internal PLL is locked to the 1,2,5 or 10 MHz. The output frequency of the instrument must be larger than the clock input/PLL reference frequency.External clock : The output period is determined by the signal at clock input. Clock input frequency : 170 kHz to 660 MHz (at 50% ±10% duty cycle).Delay from input trigger output : 21 ns.Delay from input to output : 53 ns.Threshold : ac coupled. Only valid for external input.External input : Used for external started or gated.Input frequency : DC to 330MHz.Delay from external input to trigger output : 22ns + 0 to 1 period.Delay from external input to output : 54 ns + 0 to 1 period.Threshold : -1.4 V to +3.7 V.Trigger outputTrigger format : One pulse per period with 50% duty cycle typical. In pattern mode the trigger pulse can be set to mark the start of any segment.Output impedance : 50 Ω typical.Level : TTL/ETTL (for frequency < 180 MHz), 1 V to GND, ECL 50 Ω to GND/-2 V, PECL 50 Ω to + 3 V.Max. external voltage : -2 V/+3 V.Transition times : 1.0 ns typical for TTL, 600 ps typical for ECL.Delay from external input to trigger output : 32 ns typical.Channel 1 +Figure 2: Channel addition10Programming times: (measured at display off)1. Range depends on segment length resolution, see previous table.Data Sheet 81100 Family of Pulse Pattern Generators11Ordering Information - 81100 FamilyThe minimum configuration for a working instrument consists of a mainframe and one output module. The second output module can be added later. Output modules can be exchanged and retrofitted by the user. The Reference Guide (811xx-91021) is supplied with each mainframe for all configurations. A memory card is not included.Each Agilent 81101A mainframe includes one output channel (in comparison to the other models of the Agilent 81100 family). The output module of the 81101A does not need to be ordered separately.Agilent 81101A50 MHz one channel pulse generator, 10 V Quick start guide language options Opt OBI Engish Guide(811xx-91021)Opt ABF French Guide(81101-91210)Opt ABJ Japanese Guide(81101-91510)Opt AB0Taiwan Chinese Guide(81101-91610)Opt AB1Korean Guide(81101-91710)Opt AB2Chinese Guide(81101-91810)Additional documentation optionsOpt 0BW Service Manual(81101-91021)Agilent 81104A80 MHz pulse/pattern generatormainframeOutput module:Agilent 81105A 80 MHz, 10 VAgilent 81110A330/165 MHz pulse/pattern generatormainframeOutput modules:Agilent 81111A 165 MHz, 10 VAgilent 81112A 330 MHz, 3.8 VNote: Only use output modules of thesame module number. A combination ofthe Agilent 81111A and Agilent 81112A inone Agilent 81110A is not possible.Quick start guide language optionsOpt OBI Engish Guide(811xx-91021)Opt ABF French Guide(81110-91210)Opt ABJ Japanese Guide(81110-91510)Opt AB0 Taiwan Chinese Guide(81110-91610)Opt AB1Korean Guide(81110-91710)Opt AB2 Chinese Guide(81110-91810)Additional documentation optionsOpt 0BW Service Manual(81110-91021)Agilent 81130A400/660 MHz pulse/data generatormainframeOutput modules:Agilent 81131A 400 MHz, 3.8 VAgilent 81132A 660 MHz, 2.4 VNote: Only use output modules of thesame module number. A combination ofthe Agilent 81131A and Agilent 81132A inone Agilent 81130A is not possible.Quick start guide language optionsOpt OBI Engish Guide(811xx-91021)Opt ABF French Guide(81130-91220)Opt ABJ Japanese Guide(81130-91520)Opt AB0Taiwan Chinese Guide(81130-91620)Opt AB1Korean Guide(81130-91720)Opt AB2Chinese Guide(81130-91820)Additional documentation optionsOpt 0BW Service Manual(81130-91021)Opt 0B1English Quick StartGuide (includes EnglishRef eremceGuide)Opt ABJ Japanese Quick StartGuide (includes EnglishRef erecnceGuide)Opt 0B0 Does not include anyQuick Start Guide(includes EnglishReferenceGuide)All options are orderable with themainframes.AccessoriesOpt UN2Rear panel connectors (insteadof front panel)Opt 1CP Rack mount and handle kit(5063-9219)Opt 1CN Handle kit (5063-9226)Opt 1CM Rack mount kit (5063-9212)Opt 1CR Rack slide kit (1494-0059)Opt UFJ 1 MB SRAM memory card(0950-3380)Opt UK6Commercial cal. certificate withtestdataData Sheet 81100 Family of Pulse Pattern Generators 12Product specifications and descriptions in this document subject to change without notice.© Agilent Technologies, Inc. 2009Printed in USA, November 24, 20095980-1215E。
GS88118T中文资料

512K x 18, 256K x 36 ByteSafe™8Mb Sync Burst SRAMs100 MHz–66 MHz3.3 V V DD 3.3 V and 2.5 V I/O100-Pin TQFP Commercial TempIndustrial Temp1.11 9/2000Featuresoperation• Single Cycle Deselect (SCD) Operation• IEEE 1149.1 JTAG-compatible Boundary Scan• On-chip write parity checking; even or odd selectable• 3.3 V +10%/–5% core power supply• 2.5 V or 3.3 V I/O supply• Internal input resistors on mode pins allow floating mode pins • Default to Interleaved Pipeline mode• Common data inputs and data outputs• Clock Control, registered, address, data, and control• Internal self-timed write cycle• Automatic power-down for portable applications• 100-lead TQFP packageFunctional DescriptionApplicationsThe GS88118//36T is a 9,437,184-bit high performance synchronous SRAM with a 2-bit burst address counter. Although of a type originally developed for Level 2 Cache applications supporting high performance CPUs, the device now finds application in synchronous SRAM applications, ranging from DSP main store to networking chip set support. Controlsand power down control (ZZ) are asynchronous inputs. Burst Burst mode, subsequent burst addresses are generated counter may be configured to count in either linear or interleave order with the Linear Burst Order (LBO) input. The Burst function need not be used. New addresses can be loaded on every cycle with no degradation of chip performance. Flow Through/Pipeline ReadsThe function of the Data Output register can be controlled by the user via the FT mode pin (Pin 14). Holding the FT mode pin low places the RAM in Flow Through mode, causing output data to bypass the Data Output Register. Holding FT high places the RAM in Pipeline mode, activating the rising-edge-triggered Data Output Register.SCD Pipelined ReadsThe GS88118//36T is a SCD (Single Cycle Deselect) pipelined synchronous SRAM. DCD (Dual Cycle Deselect) versions are also available. SCD SRAMs pipeline deselect commands one stage less than read commands. SCD RAMs begin turning off their outputs immediately after the deselect command has been captured in the input registers.Byte Write and Global WriteByte write operation is performed by using Byte Write enable (BW) input combined with one or more individual byte write signals (Bx). In addition, Global Write (GW) is available for writing all bytes at one time, regardless of the byte write control inputs.ByteSafe™ Parity FunctionsThe GS88118/36T features ByteSafe data security functions. See detailed discussion following.Sleep ModeLow power (Sleep mode) is attained through the assertion (high) of the ZZ signal, or by stopping the clock (CK). Memory data is retained during Sleep mode.Core and Interface VoltagesThe GS88118//36T operates on a 3.3 V power supply, and all inputs/outputs are 3.3 V- and 2.5 V-compatible. Separate output power (V DDQ) pins are used to decouple output noise from the internal circuit.-11-11.5-100-80-663-1-1-1t KQI DD4.0 ns225 mA4.0 ns225 mA4.0 ns225 mA4.5 ns200 mA5.0 ns185 mAThrough 2-1-1-1KQtCycleI DD15 ns180 mA15 ns180 mA15 ns180 mA15 ns175 mA20 ns165 mAGS88118 100-Pin TQFP Pinout807978777675747372717069686766656463626160595857565554535251123456789101112131415161718192021222324252627282930V DDQ V SS DQ B1DQ B2V SS V DDQ DQ B3DQ B4FT V DD DP V SS DQ B5DQ B6V DDQ V SS DQ B7DQ B8DQ B9V SS V DDQ V DDQ V SS DQ A8DQ A7V SS V DDQ DQ A6DQ A5V SS QE V DD ZZ DQ A4DQ A3V DDQ V SS DQ A2DQ A1V SS V DDQ L B O A 5A 4A 3A 2A 1A 0T M S T D I V S SV D DT D O T C K A 10A 11A 12A 13A 14A 16A 6A 7E 1E 2 N C N C B BB AA 17C K G W B W VD DV S SG A D S C A D S P A D V A 8A 9A 15512K X 18Top ViewDQ A9A 18NC NC NC NC NC NC NC NCNC NC NC NC NC NC NCNC NC 100999897969594939291908988878685848382813132333435363738394041424344454647484950GS88136 100-Pin TQFP Pinout807978777675747372717069686766656463626160595857565554535251123456789101112131415161718192021222324252627282930V DDQ V SS DQ C4DQ C3V SS V DDQ DQ C2DQ C1FT V DD DP V SS DQ D1DQ D2V DDQ V SS DQ D3DQ D4DQ D5V SS V DDQ V DDQ V SS DQ B4DQ B3V SS V DDQ DQ B2DQ B1V SS QE V DD ZZ DQ A1DQ A2V DDQ V SS DQ A3DQ A4V SS V DDQ L B O A 5A 4A 3A 2A 1A 0T M S T D I V S ST D O T C K A 10A 11A 12A 13A 14A 16A 6A 7E 1E 2 B DB CB BB AA 17C K G W B W VD DV S SG A D S C A D S P A D V A 8A 9A 15256K x 36Top ViewDQ B5DQ B9DQ B7DQ B8DQ B6DQ A6DQ A5DQ A8DQ A7DQ A9DQ C7DQ C8DQ C6DQ D6DQ D8DQ D7DQ D9DQ C5DQ C9100999897969594939291908988878685848382813132333435363738394041424344454647484950V D DTQFP Pin DescriptionPin Location Symbol TypeDescription37, 36A0, A1I Address field LSBs and Address Counter preset Inputs 35, 34, 33, 32, 100, 99, 82, 81, 44, 45,46, 47, 48, 49, 50, 92A2–A17I Address Inputs80A18I Address Inputs63, 62, 59, 58, 57, 56, 53, 52 68, 69, 72, 73, 74, 75, 78, 79 13, 12, 9, 8, 7, 6, 3, 2 18, 19, 22, 23, 24, 25, 28, 29DQ A1–DQ A8DQ B1–DQ B8DQ C1–DQ C8DQ D1–DQ D8I/O Data Input and Output pins ( x36 Version)51, 80, 1, 30DQ A9, DQ B9,DQ C9, DQ D9I/O Data Input and Output pins58, 59, 62, 63, 68, 69, 72, 73, 74 8, 9, 12, 13, 18, 19, 22, 23, 24DQ A1–DQ A9DQ B1–DQ B9I/O Data Input and Output pins51, 52, 53, 56, 5775, 78, 79,1, 2, 3, 6, 725, 28, 29, 30NC—No Connect16DP I Parity Input; 1 = Even, 0 = Odd66QE O Parity Error Out; Open Drain Output87BW I Byte Write—Writes all enabled bytes; active low93, 94B A, B B I Byte Write Enable for DQ A, DQ B Data I/Os; active low95, 96B C, B D I Byte Write Enable for DQ C, DQ D Data I/Os; active low ( x36 Version) 95, 96NC—No Connect (x18 Version)89CK I Clock Input Signal; active high88GW I Global Write Enable—Writes all bytes; active low98E1I Chip Enable; active low97E2I Chip Enable; active high86G I Output Enable; active low83ADV I Burst address counter advance enable; active low84, 85ADSP, ADSC I Address Strobe (Processor, Cache Controller); active low64ZZ I Sleep mode control; active high 14FT I Flow Through or Pipeline mode; active low 31LBO I Linear Burst Order mode; active low38TMS I Scan Test Mode Select 39TDI I Scan Test Data In 42TDO O Scan Test Data Out 43TCK I Scan Test Clock 15, 41, 65, 91V DD I Core power supply 5,10,17, 21, 26, 40, 55, 60, 67, 71, 76, 90V SS I I/O and Core Ground 4, 11, 20, 27, 54, 61, 70, 77V DDQIOutput driver power supplyPin LocationSymbolTyp eDescriptionByteSafe ™ Parity FunctionsGS881881E18/36 Block DiagramA1A0A0A1D0D1Q1Q0Counter LoadD QDQRegisterRegisterDQRegisterDQRegisterDQRegisterD QRegisterD QRegisterD QRegisterD QR e g i s t e rDQ RegisterA0–An LBO ADV CK ADSC ADSP GW BW B AB BB CB DFT GZZPower Down ControlMemory Array36364AQD DQx0–DQx9DPParity QEParity EncodeCompare3643636432Note: Only x36 version shown for simplicity.13636DQR e g i s t e r 4E 1E 2This SRAM includes a write data parity check that checks the validity of data coming into the RAM on write cycles. In Flow Through mode, write data errors are reported in the cycle following the data input cycle. In Pipeline mode, write data errors are reported one clock cycle later. (See Write Parity Error Output Timing Diagram .) The Data Parity Mode (DP) pin must be tied high to set the RAM to check for even parity or low to check for odd parity. Read data parity is not checked by the RAM as data. Validity is best established at the data’s destination. The Parity Error Output is an open drain output and drives low to indicate a parity error. Multiple Parity Error Output pins may share a common pull-up resistor.Write Parity Error Output Timing DiagramBPR 1999.05.18Mode Pin FunctionsMode NamePin NameStateFunctionBurst Order Control LBO L Linear Burst H or NC Interleaved Burst Output Register Control FT L Flow Through H or NC Pipeline Power Down Control ZZ L or NC Active H Standby, I DD = I SB ByteSafe Data Parity ControlDPL Check for Odd Parity H or NCCheck for Even ParityCK D In AD In BD In C D In D D In EtKQ tLZDQQEF l o w T h r o u g h M o d eP i p e l i n e d M o d etKQ tLZDQQED In A D In BD In CD In D D In EErr AErr AErr CErr CtHZ tKQX tHZ tKQXNote:There are pull-up devices on the LBO, DP and FT pins and a pull down device on the ZZ pin, so those input pins can be unconnected and the chip will operate in the default states as specified in the above table.Burst Counter SequencesBPR 1999.05.18Byte Write Truth TableNotes:1.All byte outputs are active in read cycles regardless of the state of Byte Write Enable inputs.2.Byte Write Enable inputs B A , B B , B C, and/or B D may be used in any combination with BW to write single or multiple bytes.3.All byte I/Os remain High-Z during all write operations regardless of the state of Byte Write Enable inputs.4.Bytes “C ” and “D ” are only available on the x36 version.FunctionGWBWB AB BB CB DNotesRead H H X X X X 1Read H L H H H H 1Write byte a H L L H H H 2, 3Write byte b H L H L H H 2, 3Write byte c H L H H L H 2, 3, 4Write byte d H L H H H L 2, 3, 4Write all bytes H L L L L L 2, 3, 4Write all bytesLXXXXXLinear Burst SequenceNote: The burst counter wraps to initial state on the 5th clock.I nterleaved Burst SequenceNote: The burst counter wraps to initial state on the 5th clock.A[1:0]A[1:0]A[1:0]A[1:0]1st address 000110112nd address 011011003rd address 101100014th address11000110A[1:0]A[1:0]A[1:0]A[1:0]1st address 000110112nd address 010011103rd address 101100014th address11100100Synchronous Truth TableOperation AddressUsedStateDiagramKey5E1E22(x36only)ADSP ADSC ADV W3DQ4Deselect Cycle, Power Down None X H X X L X X High-Z Deselect Cycle, Power Down None X L F L X X X High-Z Deselect Cycle, Power Down None X L F H L X X High-Z Read Cycle, Begin Burst External R L T L X X X Q Read Cycle, Begin Burst External R L T H L X F Q Write Cycle, Begin Burst External W L T H L X T D Read Cycle, Continue Burst Next CR X X H H L F Q Read Cycle, Continue Burst Next CR H X X H L F Q Write Cycle, Continue Burst Next CW X X H H L T D Write Cycle, Continue Burst Next CW H X X H L T D Read Cycle, Suspend Burst Current X X H H H F Q Read Cycle, Suspend Burst Current H X X H H F Q Write Cycle, Suspend Burst Current X X H H H T D Write Cycle, Suspend Burst Current H X X H H T D Notes:1.X = Don’t Care, H = High, L = Low.2.For x36 Version, E = T (True) if E2 = 1; E = F (False) if E2 = 0.3.W = T (True) and F (False) is defined in the Byte Write Truth Table preceding.4.G is an asynchronous input. G can be driven high at any time to disable active output drivers. G low can only enable active drivers (shownas “Q” in the Truth Table above).5.All input combinations shown above are tested and supported. Input combinations shown in gray boxes need not be used to accomplishbasic synchronous or synchronous burst operations and may be avoided for simplicity.6.Tying ADSP high and ADSC low allows simple non-burst synchronous operations. See BOLD items above.7.Tying ADSP high and ADV low while using ADSC to load new addresses allows simple burst operations. See ITALIC items above.First WriteFirst ReadBurst WriteBurst ReadDeselectR WCRCWX XWRRWRXXX S i m p l e S y n c h r o n o u s O p e r a t i o nS i m p l e B u r s t S y n c h r o n o u s O p e r a t i o nCR RCWCRCRSimplified State DiagramNotes:1.The diagram shows only supported (tested) synchronous state transitions. The diagram presumes G is tied low.2.The upper portion of the diagram assumes active use of only the Enable (E1and E2) and Write (B A , B B , B C , B D , BW, and GW) controlinputs, and that ADSP is tied high and ADSC is tied low.3.The upper and lower portions of the diagram together assume active use of only the Enable, Write, and ADSC control inputs, andassumes ADSP is tied high and ADV is tied low.First WriteFirst ReadBurst WriteBurst ReadDeselectR WCRCWXXWRRWRXXX CRR CW CRCRW CWW CWSimplified State Diagram with GNotes:1.The diagram shows supported (tested) synchronous state transitions plus supported transitions that depend upon the use of G.e of “Dummy Reads” (Read Cycles with G High) may be used to make the transition from Read cycles to Write cycles without passingthrough a Deselect cycle. Dummy Read cycles increment the address counter just like normal Read cycles.3.Transitions shown in grey tone assume G has been pulsed high long enough to turn the RAM’s drivers off and for incoming data to meetData Input Set Up Time.Absolute Maximum Ratings(All voltages reference to V SS)Symbol Description Value UnitV DD Voltage on V DD Pins–0.5 to 4.6VV DDQ Voltage in V DDQ Pins–0.5 to V DD VV CK Voltage on Clock Input Pin–0.5 to 6VV I/O Voltage on I/O Pins–0.5 to V DDQ +0.5 (≤ 4.6 V max.)VV IN Voltage on Other Input Pins–0.5 to V DD +0.5 (≤ 4.6 V max.)VI IN Input Current on Any Pin+/–20mAI OUT Output Current on Any I/O Pin+/–20mAP D Package Power Dissipation 1.5WT STG Storage Temperature–55 to 125o CT BIAS Temperature Under Bias–55 to 125o CNote:Permanent damage to the device may occur if the Absolute Maximum Ratings are exceeded. Operation should be restricted to Recommended Operating Conditions. Exposure to conditions exceeding the Absolute Maximum Ratings, for an extended period of time, may affect reliability of this component.Recommended Operating ConditionsParameter Symbol Min.Typ.Max.Unit NotesSupply Voltage V DD 3.135 3.3 3.6VI/O Supply Voltage V DDQ 2.375 2.5V DD V1Input High Voltage V IH 1.7—V DD +0.3V2Input Low Voltage V IL–0.3—0.8V2 Ambient Temperature (Commercial Range Versions)T A02570°C3 Ambient Temperature (Industrial Range Versions)T A–402585°C3 Notes:1.Unless otherwise noted, all performance specifications quoted are evaluated for worst case at both2.75 V ≤ V DDQ≤ 2.375 V(i.e., 2.5 V I/O) and 3.6 V ≤ V DDQ≤ 3.135 V (i.e., 3.3 V I/O), and quoted at whichever condition is worst case.2.This device features input buffers compatible with both3.3 V and 2.5 V I/O drivers.3.Most speed grades and configurations of this device are offered in both Commercial and Industrial Temperature ranges. The part number ofIndustrial Temperature Range versions end the character “I”. Unless otherwise noted, all performance specifications quoted are evaluated for worst case in the temperature range marked on the device.4.Input Under/overshoot voltage must be –2 V > Vi < V DD +2 V with a pulse width not to exceed 20% tKC.Note: These parameters are sample tested.Notes:1.Junction temperature is a function of SRAM power dissipation, package thermal resistance, mounting board temperature, ambient. Temper-ature air flow, board density, and PCB thermal resistance.2.SCMI G-38-873.Average thermal resistance between die and top surface, MIL SPEC-883, Method 1012.1Capacitance(T A = 25o C, f = 1 MH Z , V DD = 3.3 V)ParameterSymbolTest conditionsTyp.Max.UnitInput Capacitance C IN V IN = 0 V 45pF Input/Output CapacitanceC I/OV OUT = 0 V67pFPackage Thermal CharacteristicsRatingLayer BoardSymbolMaxUnitNotesJunction to Ambient (at 200 lfm)single R ΘJA 40°C/W 1,2Junction to Ambient (at 200 lfm)four R ΘJA 24°C/W 1,2Junction to Case (TOP)—R ΘJC9°C/W320% tKCV SS – 2.0 V50%V SS V IHUndershoot Measurement and TimingOvershoot Measurement and Timing20% tKCV DD + 2.0 V50%V DDV ILNotes:1.Include scope and jig capacitance.2.Test conditions as specified with output loading as shown in Fig. 1 unless otherwise noted.3.Output Load 2 for t LZ , t HZ , t OLZ and t OHZ4.Device is deselected as defined by the Truth Table.AC Test ConditionsParameterConditionsInput high level 2.3 V Input low level 0.2 V Input slew rate 1 V/ns Input reference level 1.25 V Output reference level1.25 V Output loadFig. 1& 2DC Electrical CharacteristicsParameterSymbolTest ConditionsMinMaxInput Leakage Current (except mode pins)I IL V IN = 0 to V DD –1 uA 1 uA ZZ Input Current I INZZ V DD ≥ V IN ≥ V IH 0 V ≤ V IN ≤ V IH –1 uA –1 uA 1 uA 300 uA Mode Pin Input Current I INM V DD ≥ V IN ≥ V IL 0 V ≤ V IN ≤ V IL –300 uA –1 uA 1 uA 1 uA Output Leakage Current I OL Output Disable,V OUT = 0 to V DD –1 uA 1 uA Output High Voltage V OH I OH = –8 mA, V DDQ = 2.375 V 1.7 V —Output High Voltage V OH I OH = –8 mA, V DDQ = 3.135 V2.4 V —Output Low VoltageV OLI OL = 8 mA—0.4 VDQVT = 1.25 V50Ω30pF *DQ2.5 VOutput Load 1Output Load 2225Ω225Ω5pF ** Distributed Test Jig CapacitanceOperating CurrentsParameter Test Conditions Symbol-11-11.5-100-80-66Unit 0to70°C–40to85°Cto70°C–40to85°Cto70°C–40to85°Cto70°C–40to85°Cto70°C–40to85°COperating Current Device Selected;All other inputs≥V IH o r ≤ V ILOutput openI DDPipeline225235225235225235200210185195mAI DDFlow-Thru180 190 180 190 180190175185165175mAStandbyCurrent ZZ≥ V DD- 0.2VI SBPipeline30 40 30 40 304030403040mAI SBFlow-Thru30 40 30 40304030403040mADeselect Current Device Deselected;All other inputs≥ V IH or≤ V ILI DDPipeline80 90 80 90809070806070mAI DDFlow-Thru65 75 65 75657555655060mAAC Electrical CharacteristicsNotes:1.These parameters are sampled and are not 100% tested.2.ZZ is an asynchronous signal. However, in order to be recognized on any given clock cycle, ZZ must meet the specified setup and holdtimes as specified above.Parameter Symbol -11-11.5-100-80-66Unit Min Max MinMax MinMax Min Max Min Max PipelineClock Cycle TimetKC 10—10—10—12.5—15—ns Clock to Output Valid tKQ — 4.0— 4.0— 4.0— 4.5—5ns Clock to Output Invalid tKQX 1.5— 1.5— 1.5— 1.5— 1.5—ns Clock to Output in Low-Z tLZ 1 1.5— 1.5— 1.5— 1.5— 1.5—ns Flow-ThruClock Cycle TimetKC 15.0—15.0—15.0—15.0—20—ns Clock to Output Valid tKQ —11.0—11.5—12.0—14.0—18ns Clock to Output Invalid tKQX 3.0— 3.0— 3.0— 3.0— 3.0—ns Clock to Output in Low-Z tLZ 1 3.0— 3.0— 3.0— 3.0— 3.0—ns Clock HIGH Time tKH 1.7— 1.7—2—2— 2.3—ns Clock LOW Time tKL 2—2— 2.2— 2.2— 2.5—ns Clock to Output in High-Z tHZ 1 1.5 4.0 1.5 4.2 1.5 4.5 1.5 4.5 1.5 4.8ns G to Output Valid tOE — 4.0— 4.2— 4.5— 4.5— 4.8ns G to output in Low-Z tOLZ 10—0—0—0—0—ns G to output in High-ZtOHZ 1— 4.0— 4.2— 4.5— 4.5— 4.8ns Setup time tS 1.5— 2.0— 2.0— 2.0— 2.0—ns Hold time tH 0.5—0.5—0.5—0.5—0.5—ns ZZ setup time tZZS 25—5—5—5—5—ns ZZ hold time tZZH 21—1—1—1—1—ns ZZ recoverytZZR20—20—20—20—20—nsCKADSPADSCADVGWBWWR2WR3WR1WR1WR2WR3tKCSingle WriteBurst Write t KLt KH tS tHtS tHtS tHtS tHtS tHtStHtS tHWrite specified byte for 2A and all bytes for 2B , 2C & 2DADV must be inactive for ADSP WriteADSC initiated writeADSP is blocked by E inactiveA 0–A nB A –B DDQ A –DQ DWrite DeselectedWR1WR3Write Cycle TimingE 1tS tHE 2 only sampled with ADSP or ADSCE 1 masks ADSPDeselected with E 2GtS tHD2AD2BD2CD2DD3AD1AHi-ZtS tHE 2Q1AQ3AQ2DQ2cQ2BQ2AtKQtLZtOEtOHZtOLZtKQXtHZtKQXCKADSP ADSCBW GGWADVBurst ReadRD2RD3tKLtStHtHtS tHtS tHADSC initiated readSuspend Burst Single ReadADSP is blocked by E inactiveA 0–A nB A –B DtKHtKCtS tHtS tStHDQ A –DQ DRD1Hi-ZSuspend BurstFlow Through Read Cycle TimingtHtHE 1 masks ADSPDeselected with E 2E 1tS tS E 2E 2 only sampled with ADSP or ADSCFlow Through Read-Write Cycle TimingCKADSPADVGWBWGQ1AD1AQ2AQ2BQ2cQ2DSingle ReadBurst ReadtOEtOHZtS tHtStHtHtS tHtS tHtKH DQ A –DQ DB A –B DtKLtKCtS Single WriteADSP is blocked by E inactivetKQtStHHi-ZQ2ABurst wrap around to it’s initial stateWR1E 1tS tS tHE 1 masks ADSPE 2 only sampled with ADSP and ADSCtHADSCtS tHADSC initiated readRD1WR1RD2tS tHA 0–A nE 2CKADSPADVGWBWGQ1AD1AQ2AQ2BQ2cQ2DSingle ReadBurst ReadtOEtOHZtS tHtStHtHtS tHtS tHtKHDQ A –DQ DBW A –BW DtKLtKCtS Single WriteADSP is blocked by E inactivetKQtS tH Hi-ZPipelined SCD Read-Write Cycle TimingWR1E 1tS tS tHE 1 masks ADSPE 2 only sampled with ADSP and ADSCtHADSCtS tHADSC initiated readRD1WR1RD2tS tHA 0–A nE 2Pipelined SCD Read Cycle TimingQ1AQ3AQ2DQ2cQ2BQ2AtKQtLZtOEtOHZtOLZtKQXtHZtKQXCKADSP ADSCBWGGWADVBurst ReadRD2RD3tKLtStHtHtS tHtS tHADSC initiated readSuspend BurstSingle ReadADSP is blocked by E inactiveA 0–A nBW A –BW DtKHtKCtS tHtS tStHDQ A –DQ DRD1Hi-ZtHtHE 1 masks ADSPE 2 only sampled with ADSP or ADSCDeselected with E 2E 1tS tS E 2Application TipsSingle and Dual Cycle DeselectSCD devices force the use of “dummy read cycles” (read cycles that are launched normally but that are ended with the outputdrivers inactive) in a fully synchronous environment. Dummy read cycles waste performance but their use usually assures there will be no bus contention in transitions from reads to writes or between banks of RAMs. DCD SRAMs do not waste bandwidth on dummy cycles and are logically simpler to manage in a multiple bank application (wait states need not be inserted at bank address boundary crossings) but greater care must be exercised to avoid excessive bus contention.JTAG Port OperationOverviewThe JTAG Port on this RAM operates in a manner consistent with IEEE Standard 1149.1-1990, a serial boundary scan interface standard (commonly referred to as JTAG), but does not implement all of the functions required for 1149.1 compliance. Some functions have been modified or eliminated because they can slow the RAM. Nevertheless, the RAM supports 1149.1-1990 TAP (Test Access Port) Controller architecture, and can be expected to function in a manner that does not conflict with the operation of Standard 1149.1 compliant devices. The JTAG Port interfaces with conventional TTL / CMOS logic level signaling.Disabling the JTAG PortIt is possible to use this device without utilizing the JTAG port. The port is reset at power-up and will remain inactive unlessclocked. TCK, TDI, and TMS are designed with internal pull-up circuits. To assure normal operation of the RAM with the JTAG Port unused, TCK, TDI, and TMS may be left floating or tied to either V DD or V SS . TDO should be left unconnected.CKADSP ADSCtHtKH tKLtKCtS ZZtZZRtZZHtZZS~~~~~~~~~SnoozeSleep Mode Timing DiagramJTAG Port RegistersOverviewThe various JTAG registers, refered to as TAP Registers, are selected (one at a time) via the sequences of 1s and 0s applied to TMS as TCK is strobed. Each of the TAP Registers are serial shift registers that capture serial input data on the rising edge of TCK and push serial data out on the next falling edge of TCK. When a register is selected it is placed between the TDI and TDO pins.Instruction RegisterThe Instruction Register holds the instructions that are executed by the TAP controller when it is moved into the Run, Test/Idle or the various data register states. Instructions are 3 bits long. The Instruction Register can be loaded when it is placed between the TDI and TDO pins. The Instruction Register is automatically preloaded with the IDCODE instruction at power-up or whenever the controller is placed in Test-Logic-Reset state.Bypass RegisterThe Bypass Register is a single-bit register that can be placed between TDI and TDO. It allows serial test data to be passed through the RAMs JTAG Port to another device in the scan chain with as little delay as possible.Boundary Scan RegisterBoundary Scan Register is a collection of flip flops that can be preset by the logic level found on the RAM’s input or I/O pins. The flip flops are then daisy chained together so the levels found can be shifted serially out of the JTAG Port’s TDO pin. TheBoundary Scan Register also includes a number of place holder flip flops (always set to a logic 1). The relationship between the device pins and the bits in the Boundary Scan Register is described in the Scan Order Table following. The Boundary Scan Register, under the control of the TAP Controller, is loaded with the contents of the RAMs I/O ring when the controller is in Capture-DR state and then is placed between the TDI and TDO pins when the controller is moved to Shift-DR state. Two TAP instructions can be used to activate the Boundary Scan Register.JTAG Pin Descriptions PinPin NameI/ODescriptionTCK Test Clock In Clocks all TAP events. All inputs are captured on the rising edge of TCK and all outputs propagate from the falling edge of TCK.TMSTest Mode SelectInThe TMS input is sampled on the rising edge of TCK. This is the command input for the TAP controller state machine. An undriven TMS input will produce the same result as a logic one input level.TDI Test Data In InThe TDI input is sampled on the rising edge of TCK. This is the input side of the serial registers placed between TDI and TDO. The register placed between TDI and TDO is determined by the state of the TAP Controller state machine and the instruction that is currently loaded in the TAP Instruction Register (refer to the TAP Controller State Diagram). An undriven TDI pin will produce the same result as a logic one input level.TDO Test Data Out OutOutput that is active depending on the state of the TAP state machine. Output changes in response to the falling edge of TCK. This is the output side of the serial registers placed between TDI and TDO.Note:This device does not have a TRST (TAP Reset) pin. TRST is optional in IEEE 1149.1. The Test-Logic-Reset state is entered while TMS is held high for five rising edges of TCK. The TAP Controller is also reset automaticly at power-up.。
杜比检测器 T-10 零件清单说明书

D ouble CheckT-10® Meter Parts List5⁄8” T -10 D O U B L E C H E C K R E V E R S E F L O W M E T E RITEM L/C PART NO.DESCRIPTIONQTY 1P 8579-308Retaining Ring, End Plate 22P 11918-002Knob, Shut-Off 23P 8579-037Retaining Ring, Stem 25P 8316-121O-Ring, End Plate 26P 8316-046O-Ring, Stem 27P 8316-120O-Ring, Housing 48P 11937-001Stem29A 11950-000Poppet Valve Assembly 210A 11951-000Shut-Off Valve Assembly 211P 11922-001Housing, Universal 312P 11923-001Hoop, Test Port 213P 8356-534Spring214P 11925-001Housing, Single 115P 11926-001Retainer Guide, Spring 116P 11927-001Strainer, 5⁄8” Meter/Backflow 117P 8368-816Test Cock 418P 7985-032Label Plate119P 11972-001Retainer Plate, Check #2120P 8315-023Pipe Plug, 1/4” NPT, Plastic 421P 8340-028Gasket 122P 9398-001Liner123P 9399-004Strainer, 5⁄8” T-10125A 9400-600Chamber Assembly, 5⁄8” T-10126L 96018-069Loctite 326A/R 27P 11917-00X Maincase (See Spud Size table below)128P 9397-XXX Bottom Cap (See Bottom Cap table below)129P 8353-XXX Bolt (See Bolt table below)430P 17XX-XXX Spud Cup (See Spud Cap table below)231P 11919-001End Plate w/Hole 232L 96018-070Locquic 764 Primer N A/R 33L 96018-015Aqua-Flow Lubricant A/R 34L 96018-056Loctite 567A/R 35P 67946-004Warning Tab (not shown)136A 11959-000Inlet Module 137A 11959-100Check #1 Module 138A 11959-200Check #2 Module 139A 11959-300Outlet Module1N/A P 5500-163Check Valve Removal Tool (not shown)1N/AP11977-001Rubber Repair Kit** (not shown)1* These parts are standard 5⁄8” T-10 water meter parts.** Includes item 5 (qty 2), item 7 (qty 4) and item 9 (qty 2).SPUD SIZE 111917-003211917-004BOTTOM CAP 1Cast Iron 9397-0102Bronze 9397-0233Plastic9397-501BOLT 1302 SST 8353-1062316 SST 8353-105SPUD CAP 11788-00821789-0085⁄8” T -10 D O U B L E C H E C K R E V E R S E F L O W M E T E R R E F E R E N C E S C H E M A T I C ST E S T I N GTo test check valve #1 (#2) for 1.0 psi in the direction of flow under normal no back pressure conditions.The instructions for check valve #2 are provided in parentheses.Before conducting testing, the customer should be contacted and a testing date scheduled. Just prior to testing, the customer should be notified that water service will be temporarily discontinued.1 Verify that the appropriate backflowpreventer is being tested and note the general conditions of the backflow preventer and the surrounding area.To test check valve #1 (#2) will hold back 1.0 psi in the direction of flow under normal no back-pressure conditions.The instructions for check valve #2 are provided in parentheses.Before conducting testing, the customer should be contacted and a testing date scheduled. Just prior to testing, the customer should be notified that water service will be temporarily discontinued.1 Verify that the appropriate reverseflow preventer is being tested and note the general conditions of the reverse flow preventer and the surrounding area.2 Flush the test cocks. This is done toremove any lodged foreign materials that might interfere with the test.3 Install flair fittings on testcock #2 and #3.4 Maintain test kit and low pressurehose at same level as check valve. Close all needle valves.5 Attach high pressure hose from testkit to test cock #2 (#3).6 Close No. 2 shutoff valve (outlet).7 Open test cock #2 (#3). Open thehigh bleed needle valve and bleed all air from hose and test kit. Close high bleed needle valve.8 Close service shutoff valve; thenclose No.1 shutoff valve (inlet).9 Open test cock #3 (#4).10 Observe whether the needle onthe gauge is maintained at 1.0 psi or above.11 Record the results.12 Close test cocks #2 (#3) and #3(#4); disconnect the high pressure hose, and open No. 1 shutoff valve, No. 2 shutoff valve, before opening the service shutoff valve.2 Flush the test cocks. This is done toremove any lodged foreign materials that might interfere with the test.3 Install adapter (tee with ball valve)on test cock #2 (#3).4 Attach a sight tube to testcock #2 (#3).5 Attach a short sight tube or ell totest cock #3 (#4).6 Close No. 2 shutoff valve (outlet).7 Open test cock #2 (#3) and fillthe sight tube so that the water level in the sight tube will be at least 28 inches above the water level at sight tube of ell attached to test cock #3 (#4). Close test cock #2 (#3).8 Close service shutoff valve; thenclose No. 1 shutoff valve (inlet).9 Open test cock #3 (#4) and opentest cock #2 (#3).10 Observe whether the level in thesight tube is maintained at least 28 inches above water level at test cock #3 (#4).11 Record the results.12 Close test cocks #2 (#3) and #3(#4); disconnect the sight tube, and open No. 1 shutoff valve, No. 2 shutoff valve, before opening the service valve.SIGHT TUBE METHODDIFFERENTIAL GAUGE METHOD。
CAT811MTBIGT10中文资料
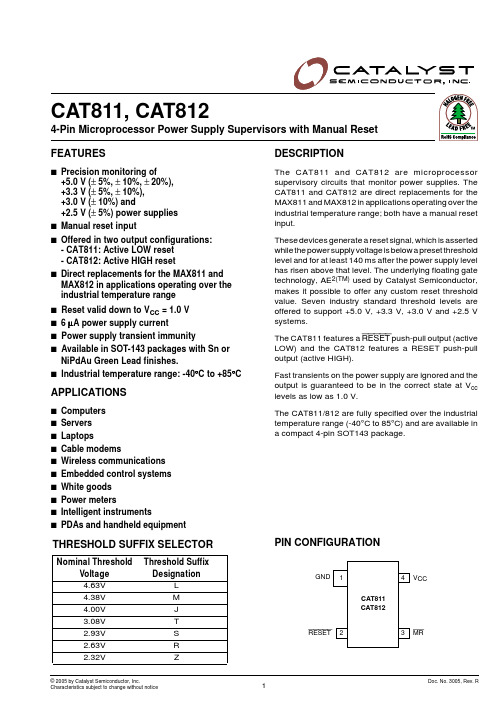
© 2005 by Catalyst Semiconductor, Inc. Characteristics subject to change without notice 1Doc. No. 3005, Rev. RCAT811, CAT8122Doc. No. 3005, Rev. R© 2005 by Catalyst Semiconductor, Inc.Characteristics subject to change without noticeORDERING INFORMATIONPIN DESCRIPTIONSTOP MARKINGNotes1)The “YM” in the SOT-143 package marking indicates the Yearand Month of production.2)All NiPdAu devices will be marked to indicate product type andpackage. Threshold and full part numbers will be provided on box and reel labels as well as all Shipping documents.d n a s t r a P d l o h se r h T 341-T O S )1(341-T O S n S n e e r G d a e L e t t a M h s i n i F )2()1(341-T O S n e e r G d a e L u A d P i N h s i n i F )2()1(8T A C 11L M Y M A M Y H D E MY R 8T A C 11M M Y N A M Y J D J 118T A C A M Y Z M Y K C T 118T A C M Y P A M Y L D S 118T A C M Y Q A M Y M D R 118T A C M Y R A M Y N D Z 118T A C A M Y Y M Y P C L 218T A C M Y S A D M Y R E MY S M 218T A C M Y T A D M Y T J 218T A C M Y U A D M Y U T 218T A C M Y V A D M Y V S 218T A C M Y W A D M Y W R 218T A C M Y X A D M Y X Z218T A C MY I C MY Y C * NiPdAu is a Lead Finish Option on the GreenPackages only. Unless indicated with the “G ” green packages are shipped with a Sn Matte Lead Finish.CAT811, CAT8123Doc No. 3005, Rev. R© 2005 by Catalyst Semiconductor, Inc.Characteristics subject to change without noticeELECTRICAL CHARACTERISTICSV CC = Full range, T A = -40°C to +85°C unless otherwise noted. Typical values at T A = +25°C and V CC = 5 V for the L/M/J versions, V CC = 3.3 V for the T/S versions, V CC = 3 V for the R version and V CC = 2.5 V for the Z version.ABSOLUTE MAXIMUM RATINGS*Any pin with respect to ground ..........-0.3 V to +6.0 V Input Current, V CC .............................................20 mA Output Current, RESET, RESET......................20 mA Rate of Rise, V CC .............................................................100 V/µs Continuous Power DissipationDerate 4mW/°C above 70°C (SOT143)........320 mWOperating Temperature Range...........-40°C to +85°C Storage Temperature Range............-65°C to +105°C Lead Soldering Temperature (10 sec)..............300°C*COMMENTStresses above those listed under “Absolute Maximum Ratings ” may cause permanent damage to the device. These are stress ratings only,and functional operation of the device at these or any other conditions outside of those listed in the operational sections of this specification is not implied. Exposure to any absolute maximum rating for extended periods may affect device performance and reliability.CAT811, CAT8124Doc. No. 3005, Rev. R© 2005 by Catalyst Semiconductor, Inc.Characteristics subject to change without noticeELECTRICAL CHARACTERISTICS V CC = Full range, T A = -40˚C to +85˚C unless otherwise noted. Typical values at T A = +25˚C and V CC = 5 V for L/M/J versions, V CC = 3.3 V for T/S versions, V CC = 3 V for R version and V CC = 2.5 V for Z version.(continued)Note 1: Production testing done at T A = +25˚C; limits over temperature guaranteed by design only.Note 2: RESET output for the CAT811; RESET output for the CAT812Note 3: Glitches of 100 ns or less typically will not generate a reset pulse.CAT811, CAT8125Doc No. 3005, Rev. R© 2005 by Catalyst Semiconductor, Inc.Characteristics subject to change without noticeTYPICAL OPERATING CHARACTERISTICSV CC = Full range, T A = -40˚C to +85˚C unless otherwise noted. Typical values at T A = +25˚C and V CC = 5 V for L/M/J versions, V CC =3.3 V for T/S versions, V CC = 3 V for R version and V CC = 2.5 V for Z version.SUPPLY CURRENT VS. TEMPERATURE(NO LOAD, CAT8xxR/S/T/Z)121086420-50 0 50 100 150S U P P L Y C U R R E N T (µA )TEMPERATURE (˚C)POWER-DOWN RESET DELAY VS. TEMPERATURE(CAT8xxR/S/T/Z)1412108642P O W E R -D O W N R E S E T D E L A Y (µS )TEMPERATURE (˚C)POWER-UP RESET TIMEOUTVS. TEMPERATURE260240220200180160P O W E R -U P R E S E T T I M E O U T (m S )TEMPERATURE (˚C)NORMALIZED RESET THRESHOLDVS. TEMPERATURE1.000210.99980.99960.99940.99920.9990.99880 20 40 60 80 100 120N O R M A L I Z E D T H R E S H O L DTEMPERATURE (˚C)-50 0 50 100 150-50 0 50 100 150CAT811, CAT8126Doc. No. 3005, Rev. R© 2005 by Catalyst Semiconductor, Inc.Characteristics subject to change without noticeDETAILED DESCRIPTIONSRESET TIMINGThe reset signal is asserted LOW for the CAT811 and HIGH for the CAT812 when the power supply voltage falls below the threshold trip voltage and remains asserted for at least 140ms after the power supply voltage has risen above the threshold.Figure 1. Reset Timing DiagramFigure 2. Maximum Transient Duration Without Causing a Reset Pulse vs. Reset Comparator Overdrive3025201510 50T R A N S I E N T D U R A T I O N [µs )RESET OVERDRIVE V TH - V CC [mV]1 10 100 10005V 0V5V 0V 5V0VPower Supply Voltage RESETRESETV CC TRANSIENT RESPONSEThe CAT811/812 protect µPs against brownout failure.Short duration transients of 4µsec or less and 100 mV amplitude typically do not cause a false RESET.Figure 2 shows the maximum pulse duration of negative-going V CC transients that do not cause a reset condition.As the amplitude of the transient goes further below the threshold (increasing V TH - V CC ), the maximum pulse duration decreases. In this test, the V CC starts from an initial voltage of 0.5V above the threshold and drops below it by the amplitude of the overdrive voltage (V TH - V CC ).CAT811, CAT8127Doc No. 3005, Rev. R© 2005 by Catalyst Semiconductor, Inc.Characteristics subject to change without noticeVALID RESET WITH V CC UNDER 1.0 VTo ensure that the CAT811 RESET pin is in a known state when V CC is under 1.0 V, a 100 k Ω pull-down resistor between RESET pin and GND is recommended;the value is not critical. For the CAT812, a pull-up resistor from RESET pin to V CC is needed.Figure 3. RESET Valid with V CC Under 1.0 V Figure 4. RESET Valid with V CC Under 1.1 VFigure 5. Bi-directional Reset Pin Interfacing(For example: 68HC11)BI-DIRECTIONAL RESET PIN INTERFACING The CAT811/812 can interface with µP/µC bi-directional reset pins by connecting a 4.7 k Ω resistor in series with the CAT811/812 reset output and the µP/µC bi-directional reset pin.CAT811, CAT8128Doc. No. 3005, Rev. R© 2005 by Catalyst Semiconductor, Inc.Characteristics subject to change without noticeOTHER SUPERVISORY PRODUCTS0.20GAUGE PLANEPACKAGE INFORMATION Plastic SOT143 (4-Pin)Catalyst Semiconductor, Inc.Corporate Headquarters 1250 Borregas Avenue Sunnyvale, CA 94089Phone: 408.542.1000Fax: 408.542.1200Copyrights, Trademarks and PatentsTrademarks and registered trademarks of Catalyst Semiconductor include each of the following:DPP ™AE 2 ™MiniPot ™Catalyst Semiconductor has been issued U.S. and foreign patents and has patent applications pending that protect its products. For a complete list of patents issued to Catalyst Semiconductor contact the Company ’s corporate office at 408.542.1000.CATALYST SEMICONDUCTOR MAKES NO WARRANTY, REPRESENTATION OR GUARANTEE, EXPRESS OR IMPLIED, REGARDING THE SUITABILITY OF ITS PRODUCTS FOR ANY PARTICULAR PURPOSE, NOR THAT THE USE OF ITS PRODUCTS WILL NOT INFRINGE ITS INTELLECTUAL PROPERTY RIGHTS OR THE RIGHTS OF THIRD PARTIES WITH RESPECT TO ANY PARTICULAR USE OR APPLICATION AND SPECIFICALLY DISCLAIMS ANY AND ALL LIABILITY ARISING OUT OF ANY SUCH USE OR APPLICATION, INCLUDING BUT NOT LIMITED TO, CONSEQUENTIAL OR INCIDENTAL DAMAGES.Catalyst Semiconductor products are not designed, intended, or authorized for use as components in systems intended for surgical implant into the body, or other applications intended to support or sustain life, or for any other application in which the failure of the Catalyst Semiconductor product could create a situation where personal injury or death may occur.Catalyst Semiconductor reserves the right to make changes to or discontinue any product or service described herein without notice. Products with data sheets labeled "Advance Information" or "Preliminary" and other products described herein may not be in production or offered for sale.Catalyst Semiconductor advises customers to obtain the current version of the relevant product information before placing orders. Circuit diagrams illustrate typical semiconductor applications and may not be complete.REVISION HISTORYDate Rev.Reason10/22/03L Updated Ordering Information 12/22/2003MUpdated FeaturesReplaced power-up reset timeout vs. temperature graph with updated oneReplaced VCC Transient Response graph with updated one3/22/04N General data sheet updates3/25/2004O Updated Electrical Characteristics (Reset Active Timeout Period Max)3/25/2004P Corrected Pin Configure diagram 9/28/2004Q Minor changes 12/28/2005RUpdated FeaturesUpdated Ordering Information Updated Yop MarkingPublication #:3005Revison:RIssue date:12/28/05。
静态GPS T10 操作说明

三鼎T10操作流程目录1、仪器外观2、主机按键说明3、装卸电池4、量取天线高5、基本设置6、测量7、备注说明1、三鼎T10外观2、主机按键说明P/D 开/关机键RX遥控数据接收灯:当用遥控对主机有操作时,该灯亮。
BAT 电源灯:当主机采用节能模式测量,彩色屏幕将黑屏以省电,电源灯长亮表示点亮充足;电池严重欠压时,蜂鸣器鸣叫,提示更换电池。
REC 测量记录灯:当主机开始记录数据,记录灯闪烁表示正在记录数据.SAT卫星灯:当测量时,间隔5秒左右,卫星灯连续闪烁,闪烁次数即为接收到的卫星数目。
3、装卸电池4、量取天线高注意:安置好仪器后,用户应在各观测时段的前后,各量测天线高一次,量至毫米。
量测时,由标石(或其它标志)或者地面点中心顶端量至天线中部,即天线上部与下部的中缝。
5、基本设置(1)装好电池,按P/D键开机,然后用遥控器选择:智能(F1)、手动(F2)、节能(F3),通常选择智能。
(2)进入工作界面后,进行设置(按遥控器F2键):采样间隔(一般是5秒)、高度截止角(一般是10°—15°)、采样次数(5次),设定好,按F4确定,就完成了。
( F1 F2 F3 F4 )上图为:主机工作界面注意:F1采集间隔,出厂时默认为10,连续按F1键,设置采集间隔值由1—60秒可改;F2高度截止角,出厂时默认为10°,连续按F1键,设置高度截止角由0—45°可改(变化间隔为5°);F3 采样次数,次数为3次,则表示采三个点取一个平均值。
即若采样间隔设置成5秒,采点次数3次,则每一个点上需测15秒。
联网布测时,同时工作的几台T10,主机的高度截止角、采集间隔最好保证一致,即同样的设置值。
6、测量按F3键进入“测量”功能的操作,界面如下:( F1 F2 F3 F4 )F1 “状态”:显示单点定位的经纬度坐标、高程和精度因子(即PDOP值)、定位模式、锁定卫星数目、可视卫星数;F2 “卫星”:显示卫星号和卫星信躁比;信噪比,英文名称叫做SNR或S/N(SIGNAL-NOICE RATE),是指一个电子设备或者电子系统中信号与噪声的比例,一般来说,信噪比越大,说明混在信号里的噪声越小。
CAT-1 系列 AT 指令集说明书

CAT-1系列AT指令集文件版本:V1.0.7功能特点●网络优,搭载Cat-1网络,10Mbps下载,5Mbps上传,满足80%的数据传输应用场景;●延迟低,4G网络承载,毫秒级延时体验;●支持多制式,LTE Cat-1和GRPS双模双保险;●覆盖广,基于现有运营商4G网络,稳定性高;●无需特殊卡、无需特殊套餐,常规卡即可使用;●支持网络透传功能,串口数据直接传到网络端,简单可靠;●支持KEEP-ALIVE机制,可以保活连接,增强连接稳定性;●每路连接支持20条数据缓存,每条数据最大4K;●每路连接分别支持一路socket备份;●支持注册包,心跳包数据;●支持HTTPD功能;●支持短信透传,发送中英文短信;●支持FTP他升级协议;●支持基站定位和NTP时间更新;●多种参数设置方式:网络、短信、串口AT指令和电脑端设置软件配置;●具有安全机制,可设置指令模式登录密码。
目录CAT-1AT指令集 (1)1.文档简介 (6)2.指令介绍 (6)2.1.指令中“问”的格式 (6)2.2.指令中“答”的格式 (7)3.AT指令集 (8)3.1.响应指令类型说明 (10)3.2.常用指令错误码 (11)4.AT指令详解 (11)4.1.AT (11)4.2.AT+Z (11)4.3.AT+S (12)4.4.AT+CLEAR (12)4.5.AT+E (12)4.6.AT+ENTM (13)4.7.AT+WKMOD (13)4.8.AT+CMDPW (14)4.9.AT+STMSG (15)4.10.AT+RSTIM (15)4.11.AT+SDPEN (16)4.12.AT+NATEN (16)4.13.AT+UATEN (17)4.14.AT+CACHEN (18)4.15.AT+CSQ (18)4.16.AT+SYSINFO (19)4.17.AT+VER (19)4.18.AT+BUILD (20)4.19.AT+SN (20)4.20.AT+IMEI (21)4.21.AT+ICCID (21)4.22.AT+CIP (21)4.23.AT+CNUM (22)4.24.AT+LBS (22)4.25.AT+LBSN (23)4.26.AT+CCLK (24)4.27.AT+SAFEATEN (25)4.29.AT+UART (26)4.30.AT+UARTFL (27)4.31.AT+UARTFT (27)4.32.AT+APN (28)4.33.AT+SOCKA (29)4.34.AT+SOCKB (29)4.35.AT+SOCKC (30)4.36.AT+SOCKD (31)4.37.AT+SOCKAEN (32)4.38.AT+SOCKBEN (32)4.39.AT+SOCKCEN (33)4.40.AT+SOCKDEN (33)4.41.AT+SOCKALK (34)4.42.AT+SOCKBLK (34)4.43.AT+SOCKCLK (35)4.44.AT+SOCKDLK (35)4.45.AT+SOCKASL (36)4.46.AT+KEEPALIVEA (36)4.47.AT+KEEPALIVEB (37)4.48.AT+KEEPALIVEC (38)4.49.AT+KEEPALIVED (38)4.50.AT+SHORTATM (39)4.51.AT+SOCKRSNUM (40)4.52.AT+SOCKRSTIM (40)4.53.AT+SOCKABK (41)4.54.AT+SOCKBBK (41)4.55.AT+SOCKCBK (42)4.56.AT+SOCKDBK (43)4.57.AT+SOCKABKEN (43)4.58.AT+SOCKBBKEN (44)4.59.AT+SOCKCBKEN (44)4.60.AT+SOCKDBKEN (45)4.61.AT+REGEN (46)4.62.AT+REGTP (46)4.63.AT+REGDT (47)4.64.AT+REGSND (48)4.66.AT+HEARTEN (49)4.67.AT+HEARTTP (49)4.68.AT+HEARTDT (50)4.69.AT+HEARTTM (51)4.70.AT+HEARTSORT (51)4.71.AT+HEART (52)4.72.AT+HTPTP (53)4.73.AT+HTPURL (53)4.74.AT+HTPHD (54)4.75.AT+HTPSV (55)4.76.AT+HTPPK (55)4.77.AT+HTPTIM (56)4.78.AT+DSTNUM (56)4.79.AT+SMSFLT (57)4.80.AT+NTPSVR (57)4.81.AT+NTPEN (58)4.82.AT+NTPTM (59)4.83.AT+GPS (59)4.84.AT+GPSDT (60)4.85.AT+GPSOUT (60)4.86.AT+GNSSMOD (61)4.87.AT+GMDBS (62)4.88.AT+GPOSUPTM (63)4.89.AT+SIMSWITCH (63)4.90.AT+BLEEN (64)4.91.AT+BLEMOD (65)4.92.AT+BLEADVEN (65)4.93.AT+BLESG (66)4.94.AT+BLELINK (67)5.异常打印信息 (68)6.联系方式 (69)7.免责声明 (70)8.更新历史 (71)1.文档简介该文档提供了以WH-GM5为例,Cat-1系列产品支持的AT指令的详细说明。
TE 系列产品
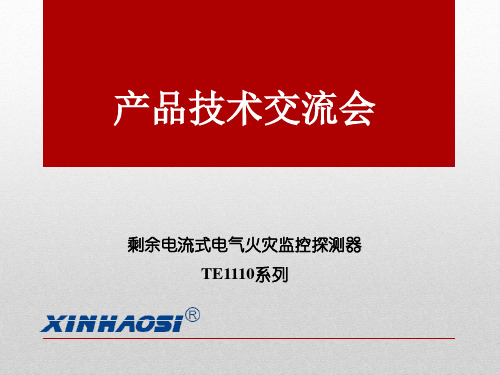
1 重新设置总线地址 2 正确设置总线地址 3 排查线路连接
1 零线没有穿过探测器 监控设备 2 零线穿过互感器后接地
超量程报警 3 PE线穿过互感器 4 多个用电回路的零线共用
显示---
1 表示检测到的漏电流大于 1000mA
正确安装探测器 (正确穿线)
正确安装探测器 (正确穿线)
b 故障分析与处理
探测器检测电流大、;2. 或线路安装不规范,应尽快纠正;3.要么探测器安装的选点不正确,这需 要结合电气火灾消防要求和国家标准GB 13955-2005《剩余电流动作保 护装置的安装和运行》,重新合理选点。
可能有以下几种情况:
LA LB LC N
代号
单位
PCS PCS PCS PCS PCS PCS PCS PCS PCS PCS PCS PCS PCS PCS PCS
数量
1 1 1 1 1 1 1 2 1 1 1 1 1 1 1
每箱数量 540
480
112 84 69 48 38 34
A 发货方式——电路板包装图
主板电路板
防静电气泡袋
五层瓦楞纸
产品技术交流会
剩余电流式电气火灾监控探测器 TE1110系列
➢ 产品简介
TE111X系列剩余电流式 电气火灾监控探测器,是一款 集现场示值显示、光报警, 漏电流采集和信号转换处理 于一体的探测器,适用于对 单个用电回路的漏电流进行 检测,需适配监控设备实现 监控和报警。
该系列产品包括:TE1110、TE1111、TE1112、TE1113、 TE114、TE1115。
379×140×32 305×48
➢ 产品特点
l 国内唯一仅需两根信号线,支持现场示值显示的2
CAT811-MAX811(复位)

4脚微控制器电源监控电路-CAT811/812特性z对以下电源进行精密监控:+5.0V (+/- 5﹪, +/- 10﹪, +/- 20﹪),+3.3V (+/- 5﹪, +/- 10﹪),+3.0V (+/- 10﹪) 和+2.5V (+/- 5﹪)z提供2种输出配置:-CAT811:低有效复位-CAT812:高有效复位z手动复位输入z在工业级温度范围的应用中可直接代替MAX811和MAX812z Vcc低至1.0V时复位有效z6uA的电源电流z抗电源的瞬态干扰z紧凑的4脚SOT143封装z工业级温度范围:-40℃~+85℃应用z计算机z服务器z手提电脑z线调制解调器(Cable modem)z无线通信z嵌入式控制系统z白色家电z功率计z智能仪器z PDA和手持式设备描述CAT811和CAT812是微控制器监控电路,用来监控数字系统的电源。
在工业级温度范围的应用中可直接代替MAX811和MAX812。
CAT811和CAT812都含有手动复位输入管脚。
CAT811和CAT812产生一个复位信号,这个信号在电源电压低于预置的阈值时和电源电压上升到该阈值后的140ms内有效。
由于Catalyst半导体运用了底层浮动闸(floating gate)技术AE2TM,因此器件可以提供任何特定的复位阈值。
7个工业标准的阈值可支持+5.0V、+3.3V、+3.0V和+2.5V的系统。
CAT811的RESET是推挽输出(低有效),CAT812的RESET也是推挽输出(高有效)。
电源的快速瞬态变化可忽略,当Vcc低至1.0V时输出可保证仍处于正确状态。
CAT811/812可工作在整个工业级温度范围内(-40℃~+85℃),包含4脚SOT143的封装形式。
阈值后缀选择器指定阈值电压阈值后缀名称4.63V L4.38V M4.00V J3.08V T2.93V S2.63V R2.32V Z管脚配置订购信息在器件型号的空白处插入后缀(L, M, J, T, S, R或Z)。
特拉T810中文名字:特拉(Tatra)T810中重型小型卡车说明书

GO-ANYWHERE ABILITY• three drive axles in the category of medium heavy vehicles• ladder frame with exceptional torsion strength• TATRA RIGID portal axles• 480 mm ground clearance under the axle housing• 580 mm ground clearance under the auxiliary transmission• 840 mm of cross-axle twisting between 1st and 3rd axle• 100% climbing ability at total weightNo other vehicle in the medium heavy weight categorycan offer three drive axles at a total weight of 15.5 tons.This gives the T 810 exceptional handling and ridingcharacteristics both on and off road. The portal axle designwith hub reduction gear and a custom-designed solutionfor the axle differentials provides unmatched groundclearance of 480 mm under the axle housing. Thanks toits extraordinary capability in cross-axle twisting of up to840 mm and excellent traction in all driving conditions, theT 810 truck is able to achieve 100% hill climbing capacityat total weight.• WABCO air disc brakes on all axles• front axle coil spring suspension• excellent front and rear axle guiding• powerful liquid-cooled engine• high maximum speed• trailer weight of up to 12 t• total weight of vehicle combination of up to 27.5 tSafe and stable driving in all conditions is one of the fundamental characteristics of the T 810 truck. The high-performance engine (198 kW/270 hp) is entirely consistent with the chassis’ ability to offer a high degree of tractionat all times. Credit for this goes to the TATRA RIGID portal axles, especially their mounting and suspension.The front rigid portal axle with gear ratio 2.294 and the hub reduction gear 2.437 is equipped with an electro-pneumatically controlled axle differential lock and WABCO disc brakes. The axle is guided by the upper pair of longitudinal guide rods and the lower triangular suspension anchored to the vehicle frame. It is suspended by coil springs with telescopic shock absorbers, hydraulic stop, and a torsion stabilizer. Thanks to this solution, the entire steering system does not produce uncomfortable steering wheel drag when overcoming longitudinal and transverse ground unevenness – a problem which is normal for other design solutions. The central and rear TATRA RIGID portal axles forma tandem pair. Both axles are equipped with electro-pneumatically controlled axle differential locks and WABCO disc brakes. In addition, the inter-axle differential with electro-pneumatic lock and rear axle drive outlet are situated in the central axle housing. The tandem pair is guided by six longitudinal guide rods anchored to the vehicle frame and suspended by a pair of sixteen-leaf springs.The T 810 has a high maximum speed of 106 km/h withouta limiter and 85 km/h with a limiter, ensuring that the truck can operate very efficiently on roads of all categories.A high degree of stability is also maintained in a vehicle combination with a 12 t trailer and a total weight ofup to 27.5 t.STABILITY• total weight 15.5 tons• high chassis payload 8.5 tons • single wheels on all axles• low ground pressure• R20’’ or R22.5’’ tires• compact dimensions• EURO 5 emission specificationsA consistent focus on the customer has stimulated highly elegant solutions to problems which designers used to just have to accept and work around. The total weight of 15.5 tons combined with the 8.5 t chassis payload means that the vehicle can be deployed in situations where other vehicles cannot cope and so often have to face high damage repair costs (due to damage often caused to private property). The T 810 offers ingenious solutions for working with electrical power lines, various types of pipelines, other types of technical infrastructure and utility operations. A medium heavy vehicle which handles excellently on both pavedand unpaved roads, the low specific pressure of the T 810 significantly reduces ground compaction. There is a clear difference in total weight and number of axles compared to existing design solutions. The high utility value of the T 810 eliminates many of the costs of remediating land after work is completed.Depending on the type of operation, the vehicle can befitted with 365/80 R20” or 385/65 R22.5” tires, allowingfor optimized operating efficiency levels. This represents another positive response to customer requirements.Thanks to the small vehicle dimensions and the chassis equipped with a specialized superstructure, operators are able to work under severe space limitations, whether in the field or in densely populated urban areas. The optimum size of the T 810 enables it to fit into restricted spaces without occupying more than the necessary area.Another significant aspect of the T 810 is that it has environmentally friendly parameters. The vehicle complies fully with current EURO 5 emission standards applicable to diesel engines, and pollutant emissions are minimized during vehicle production itself.FRIENDLINESSAll chassis and drive train design assemblies are designed for a long service life and provide a high safety coefficient. An extensive service network is available due to the useof widespread and advanced vehicle design assemblies such as the engine, transmission, disc brakes, electronic systems and others. Genuine spare parts are available at all authorized service centers.High-quality production values and sophisticated solutions are reflected in the vehicle’s long service life, which hasa direct impact on operating costs. Exceptional driving characteristics and high utility values are consistent with optimized purchase costs. Thanks to its high operating efficiency, excellent durability in the toughest conditions and higher residual values, the T 810 leads to high quality opportunities of vehicle purchase financing.The T 810 embodies TATRA’s emphasis on customer focus, as users can easily configure the truck according to their specific needs and type of operation.To ensure highest levels of customer satisfaction, all T 810 trucks are automatically included in the Tatra Service Plus TM program that guarantes highest servicing standards.6chassis cab, 6×6cargo with crane, 6×6container carrier, 6×6sheltter, 6×6three-way tipper, 6×6cargo truck, 6×6。
ART T8 八通道变压器隔离器说明书

ART T8Universal Eight Channel Transformer IsolatorIMPORTANT SAFETY INSTRUCTION – READ FIRSTThis symbol, wherever it appears, alerts you to important operating and maintenanceinstructions in the accompanying literature. Please Read the manual.Read instructions:Retain these safety and operating instructions for future reference. Heed all warnings printed here and on the equipment. Follow the operating instructions printed in this user guide.Do not open:There are no user serviceable parts inside. Refer any service work to qualified technical personnel only.Moisture:To reduce the risk of fire or electrical shock do not expose the unit to rain, moisture or use in damp or wet conditions. Do not place container of liquid on it, which may spill into any openings.Environment:Protect from excessive dirt, dust, heat, and vibration when operating and storing. Avoid tobacco ash, drink spillage and smoke, especially that associated with smoke machines.Handling:To prevent damage to the controls and cosmetics avoid rough handling and excessive vibration. Protect the controls from damage during transit. Use adequate padding if you need to ship the unit. To avoid injury to yourself or damage to the equipment take care when lifting, moving or carrying the unit. Servicing:Refer servicing to qualified technical personnel only.INTRODUCTIONThank you for purchasing the ART T8 Universal Eight Channel Transformer Isolator. This is a rock solid, road-worthly 8 channel transformer isolator. “Hum” in an audio system is often caused by loop effects which act like antennas. These loops can easily pick up a 60Hz ( or higher harmonic) hum created by electrical wiring. Typically, these loops are connected via grounds, more commonly called “ ground loops”. The safest way to eliminate unwanted noise is with the T8.The T8 is a quality totally passive audio interface that uses eight high performance low distortion transformers to totally separate input and output signal grounds, thereby isolating two systems and reducing hum and ground-loop noise. The T8’s audio transformers have an extremely flat and wide frequency response and can handle high signal levels while maintaining an isolated balanced output. This gives the T8 a very clean and neutral sound with a wide variety of signal sources. The transformers are wound for 1:1 unity gain and are designed for use with impedances from 600 Ohms to 100k Ohms.What further sets the T8 apart from other lesser isolation boxes is its connection versatility. We have provided XLR, ¼” phone, and RCA type phono connections on all inputs and outputs. This allows it to easily fit into virtually any audio system and be the clean patch point between all types of systems. All ¼” and RCA phono jacks are on the front and all XLR jacks are on the rear. You can use any combination and since the jacks are directly paralleled you can also use them as signal taps or as a signal splitter.The T8’s mounting ears are reversible so you can have either the ¼” and RCA phono jacks on the front or the XLRs on the front. This maximizes flexibility in cabling your system. Whether you need an interface between a computer based audio workstation and your monitor system, isolation on long cable runs in a fixed installation, isolation of multiple signal sources from your recording equipment, or in many cases, just a safer connection between two audio systems, the T8 can accommodate. The 19” 1U black all steel case and its all passive design allow the T8 to provide years of trouble free service in Live Sound, Permanent/Fixed Install, D.J., and virtually any PA application. It is equally valuable in a variety of studio and AV applications. Its full feature set, rugged construction, and high-end specifications make the T8 the obvious choice.APPLICATIONS:LIVE SOUND, D.J.Long unbalanced cables are more susceptible to picking up hum , Using the T8 to help balance these and eliminate any hum.When DJs set up for different jobs there is a potential to pick up hum due to the differences in house wiring, using a T8 Eliminates the potential for hum.MIXERS/FIXED INSTALLS/RECORDING/BROADCAST/VIDEOUse the T8 to eliminate ground loops when using multiple mixers.Taking mixer unbalanced sends and achieving true balanced monitor outputs.Using the T8 between video/broadcast rigs eliminates the potential for hum and loop noise.POWER AMPLIFIERSHum, ground loop noise can be created between multiple amplifiers. This can be eliminated using the T8 on each of the amplifiers input lines.COMPUTERSUsing a T8 can eliminate unwanted ground loops created between the computers and your audio input equipment.You can also use the T8 to balance the unbalanced inputs and outputs from your computers sound card.WARRANTY INFORMATIONLimited WarrantyApplied Research and Technology will provide warranty and service for this unit in accordance with the following warrants:Applied Research and Technology, (A R T) warrants to the original purchaser that this product and the components thereof will be free from defects in workmanship and materials for a period of three years from the date of purchase. Applied Research and Technology will, without charge, repair or replace, at its option, defective product or component parts upon prepaid delivery to the factory service department or authorized service center, accompanied by proof of purchase date in the form of a valid sales receipt.Exclusions:This warranty does not apply in the event of misuse or abuse of the product or as a result of unauthorized alterations or repairs. This warranty is void if the serial number is altered, defaced, or removed.A R T reserves the right to make changes in design or make additions to or improvements upon this product without any obligation to install the same on products previously manufactured.A R T shall not be liable for any consequential damages, including without limitation damages resulting from loss of use. Some states do not allow limitations of incidental or consequential damages, so the above limitation or exclusion may not apply to you. This warranty gives you specific rights and you may have other rights, which vary, from state to state.For units purchased outside the United States, an authorized distributor of Applied Research and Technology will provide service.SERVICEThe following information is provided in the unlikely event that your unit requires service.1) Be sure that the unit is the cause of the problem. Check to make sure that all cables are connected correctly, and the cables themselves are in working condition.2) If you find the unit to be at fault, write down a complete description of the problem, including how and when the problem occurs.3) Contact our Customer Service Department at (716) 297-2920 for your Return Authorization number or questions regarding technical assistance or repairs. Customer Service hours are 9:00 AM to 5:00 PM Eastern Time, Monday through Friday.4) Pack the unit in its original carton or a reasonable substitute. The packing box is not recommended as a shipping carton. Put the packaged unit in another box for shipping. Print the RA number clearly on the outside of the shipping box. Print your return shipping address on the outside of the box.5) Include with your unit: a return shipping address (we cannot ship to a P.O. Box), a copy of your purchase receipt, a daytime phone number, and a description of the problem.6) Ship your unit (keep your manual!) to: Yorkville Sound 4625 Witmer Industrial Estate, Niagara Falls New York 14305Specifications:Frequency Response: 10Hz –50kHz, +/-0.5dB @ +4dBu1kHz,@+18dBu,<0.1% @ 100Hz, +24dBu Ref: 0dBu = 0.775VRMSTHD:0.01%TypicalChannel Separation 90dB typicaltypical60dBCMRR:Phase Error less than 5%, 20Hz – 20kHzInsertion Loss: 0.4dB @ 100k Ohm Load, 5.5dB @ 600 Ohm LoadInput Connections: XLR female balanced, ¼” TRS balanced, and RCA type phono jacksOutput Connection: XLR male balanced, ¼” TRS balanced, and RCA type phono jacksPassivePower Requirements: TotallyDimensions: 1.75”H x 19”W x 3.75”D (44.5mm x 482.6mm x 95mm)(1.7kg)lbs.3.75Weight:。
泰特电子Tait TM8100双频无线通信设备操作指南说明书
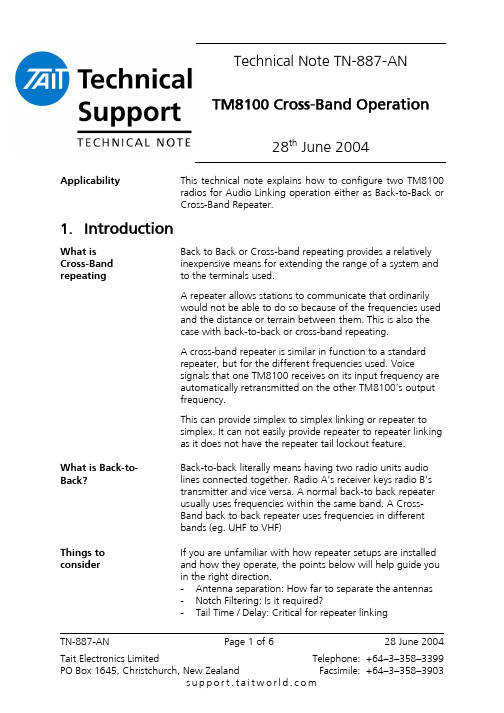
Applicability This technical note explains how to configure two TM8100radios for Audio Linking operation either as Back-to-Back orCross-Band Repeater.1.IntroductionWhat is Cross-Band repeating Back to Back or Cross-band repeating provides a relatively inexpensive means for extending the range of a system and to the terminals used.A repeater allows stations to communicate that ordinarily would not be able to do so because of the frequencies used and the distance or terrain between them. This is also the case with back-to-back or cross-band repeating.A cross-band repeater is similar in function to a standard repeater, but for the different frequencies used. Voice signals that one TM8100 receives on its input frequency are automatically retransmitted on the other TM8100’s output frequency.This can provide simplex to simplex linking or repeater to simplex. It can not easily provide repeater to repeater linking as it does not have the repeater tail lockout feature.What is Back-to-Back?Back-to-back literally means having two radio units audio lines connected together. Radio A’s receiver keys radio B’s transmitter and vice versa. A normal back-to back repeater usually uses frequencies within the same band. A Cross-Band back to back repeater uses frequencies in different bands (eg. UHF to VHF)Things to consider If you are unfamiliar with how repeater setups are installed and how they operate, the points below will help guide you in the right direction.-Antenna separation: How far to separate the antennas -Notch Filtering: Is it required?-Tail Time / Delay: Critical for repeater linkingTechnical Note TN-887-AN TM8100 Cross-Band Operation28thJune 2004TN-887-AN Page 1 of 628 June 2004TN-887-AN Page 2 of 628 June 20042.InstructionsConfigure the Cross-Band interconnect cable as indicated inthe diagram below.Configuring the Cross-Band Interconnect CableFor voice applications the value of Cc should be at least100ηF.For high-speed (base band) data applications then therecommended value for Cc is 4.7µF. The capacitor needs tobe non-polarised.The simplest way to create a 600-Ohm resister is by usingtwo 1k2Ω resistors in parallel.The resistor and capacitor can be mounted inside each DB-15 plug.3.Radio Programming RequirementsInstructions After defining the Tx / Rx parameters, the settings below need to be programmed into both radios to enable cross-band operation.PTT: External PTT 1PTT Transmission Type = Voice.PTT Priority = Highest (PTT or EPTT(2) priority may need changing)Audio Source = Audio Tap In.TN-887-AN Page 3 of 628 June 2004TN-887-AN Page 4 of 628 June 2004Programmable I/O = Digital I/O Settings AUX_GPI04AUX_GPI05DirectionOutput Input LabelBusy / Rx Gate PTT ActionSignalling Audio Mute Status External PTT 1ActiveActive High Active High DebounceNONE 10Signal StateMomentary None Mirrored ToNone NoneProgramminginstructions(cont)TN-887-AN Page 5 of 628 June 2004Audio I/O Settings Rx/PTT TypeRX EPTT1Tap inNoneT5Tap in TypeA - Bypass In A - Bypass In Tap in UnmuteOn PTT On PTT Tap OutR7None Tap Out TypeD – Split C - Bypass Out Tap OutUnmuteBusy Detect +Subaudible On PTTProgrammingInstructions(cont)Cross-BandOperationTesting 1. Inject into the receiving radio an on-channel RF signal of –70dBm with a 1 kHz tone and the deviation set to either 3 kHz Wide Band or 1.5 kHz Narrow Band.2. The transmit deviation on the other radio should be3 kHz (+/- 200Hz) Wide Band or 1.5 kHz (+/- 200 Hz) NarrowBand.Compliance Issues If the link is a fixed site, RF compliance may need to beobtained and / or monies to be paid to regulatory bodies. CSO Instruction Please pass this information onto the field supporttechnicians, technical support engineers and appropriatedealers.3.Issuing AuthorityName and Position of Issuing Officer Barry CratesTechnical Support Team Leader - TerminalsConfidentiality Confidential – This message or document containsproprietary information intended only for the person(s) ororganisation(s) to whom it is addressed. All Recipients arelegally obliged to not disclose Tait technological or businessinformation to any persons or organisations without thewritten permission of Tait.Distribution Level Tait Only, Accredited Service Centre System Integrator,Accredited Service Centre and System Integrator Document History Original Release - TN-NSC078 January 2004BPModified to TEL TN format forpublishing to global audience.28 June 2004BLCTN-887-AN Page 6 of 628 June 2004。
Fluke Ti10 热成像仪产品说明书

Thermal ImagingFluke Ti10 Thermal ImagerThe ultimate tool for troubleshooting and maintenanceThis thermal imager is the perfect tool to add to your problem solving arsenal. Built for tough work environments, this high-performance, fully radiometric infrared camera is ideal fortroubleshooting electrical installations, electro-mechanical equipment, process equipment, HVAC/R equipment and others.IR-Fusion® TechnologySee things both ways—infrared and visual (visible light) images fused togethercommunicating critical information faster and easier—traditional infrared images are no longer enough. IR-Fusion, a patent-pending technology that simultaneously captures a digital photo in addition to the infrared image and fuses it together taking the mystery out of IR image analysis. IR-Fusion is standard on Ti10 models.Technical DataFluke Ti25 and Ti10 Thermal ImagersThe perfect tools to add to your problem solving arsenal. Built for tough work environments, these high-performance, fully radiometric imagers are ideal for troubleshooting electrical installations, electro-mechanical equipment, process equipment, HVAC/R equipment and others.•All Fluke imagers come with enhanced prob-lem detection and analysis capabilities with IR-Fusion ® Technology. Simply scroll through the different viewing modes quickly to better identify trouble areas in Full IR thermal, picture-in-picture, or automatic blend visual and thermal images.• Optimized for field use in harsh work environments.• Engineered and tested to withstand a 2 m (6.5 ft) drop—When was the last time you dropped a tool?• Withstands dust and water—tested to an IP54 rating. • Delivers the clear, crisp images needed to find problems fast.• Identify even small temperature differences that could indicate problems with excellent thermal sensitivity (NETD).• Intuitive, three-button menu is easy to use—simply navigate with the push of a thumb.•No need to carry pen and paper—record findings by speaking into the camera. Voice annotations can be recorded with every image you take. Voicecomments are saved along with individual images for future reference (Ti25 only).• Everything needed to get started is included.• Adjustable hand strap for left-or right-handed use. •Manufactured in the U.S.A.Temperature Operating: -10 °C to 50 °C (14 °F to 122 °F)Storage: -20 °C to +50 °C (-4 °F to 122 °F) without batteries Relative humidity 10 % to 90 % non-condensingDisplay9.1 cm (3.6 in) diagonal landscape color VGA (640 x 480) LCD with backlight (selectable bright or auto)Controls and adjustmentsUser selectable temperature scale (°C/°F)Language selection Time/Date setEmissivity selection and Reflected Background Temperature Compensation (Ti25 only)User selectable Hot Spot and Cold Spot on the image (Ti25 only)Ti25 allows user to adjust palette, alpha blend, level, span, PIP, and emissivity on a captured image before it is stored.Software SmartView ® full analysis and reporting software includedPowerBattery: Internal rechargeable battery pack (included)Battery life: Three to four hours continuous use (assumes 50 % brightness of LCD)Battery charge time using ac adapter/charger and dc car charger: Two hours for full charge AC operation/charging AC adapter/charger (110 Vac to 220 Vac, 50 Hz to 60 Hz). Charges battery while imager is operating. Universal ac mains adapters included.Power saving Sleep mode activated after 5 minutes of inactivity, automatic power off after 20 minutes of inactivity Safety standards CE Directive: IEC/EN 61010-1 2nd Edition Pollution Degree 2Electromagnetic compatibility EMC directive: EN61326-1C-Tick: IEC/EN 61326US FCC: CFR 47, Part 15 Class A Vibration 2 G, IEC 68-2-29Shock25 G, IEC 68-2-29 (2 m or 6.5 ft drop, 8 sides)Dimensions (HxWxL)0.27 m x 0.13 m x 0.15 m (10.5 in x 5 in x 6 in)Weight 1.2 kg (2.65 lb)IP rating IP54Warranty Two-yearsCalibration cycle Two-years (assumes normal operation and normal aging)Supported languagesEnglish, Italian, German, Spanish, French, Russian, Portuguese, Swedish, Turkish, Czech, Polish, Finnish, Simplified Chinese, Traditional Chinese, Korean, and JapaneseFLUKE-Ti25 Thermal Imager FLUKE-Ti10Thermal ImagerIncluded with productThermal imaging camera w/20 mm lens, ac powersupply/battery charger (including mains adapters), SD memory card, SD card reader(USB) for downloading images into your computer, SmartView ® software with free software upgrades for life, rugged hard, carrying case, soft transport bag, hand strap, users manual, warranty registration card, interactive training DVD.Optional accessoriesFluke-TI Charger Thermal Imager Car ChargerFluke-T-VisorThermal Imager VisorFluke. Keeping your world up and running.®。
泰特电子TB8100基站连接指南说明书
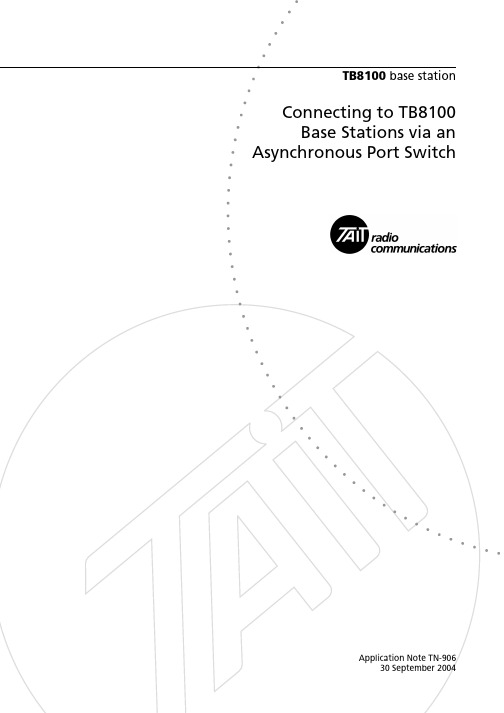
TB8100 base station Connecting to TB8100 Base Stations via an Asynchronous Port SwitchApplication Note TN-90630 September 2004Contents1The Purpose of an APS . . . . . . . . . . . . . . . . . . . . . . . . . . . . . . . . . . . . . . . 32Supported APS Units and their Main Features. . . . . . . . . . . . . . . . . . . . . . . . 42.1Units Supported. . . . . . . . . . . . . . . . . . . . . . . . . . . . . . . . . . . . . . . . . . . . . . . . . 42.2Main Features . . . . . . . . . . . . . . . . . . . . . . . . . . . . . . . . . . . . . . . . . . . . . . . . . . 4 3Physical Connections. . . . . . . . . . . . . . . . . . . . . . . . . . . . . . . . . . . . . . . . . 54Configuring the Service Kit and Base Station . . . . . . . . . . . . . . . . . . . . . . . . 94.1Configuring the Service Kit for Dial-in via an APS . . . . . . . . . . . . . . . . . . . . . . . 94.2Configuring the Service Kit for a Direct Connection via an APS . . . . . . . . . . . . 114.3Configuring the Base Station to Dial Out to an Alarm Center . . . . . . . . . . . . . . 115Configuring the APS . . . . . . . . . . . . . . . . . . . . . . . . . . . . . . . . . . . . . . . . 135.1Ensuring the Security of Configuration Data . . . . . . . . . . . . . . . . . . . . . . . . . . . 135.2Configuring the Set-up Switches. . . . . . . . . . . . . . . . . . . . . . . . . . . . . . . . . . . . 135.3Configuring the Ports. . . . . . . . . . . . . . . . . . . . . . . . . . . . . . . . . . . . . . . . . . . . 14 6Testing the Connection . . . . . . . . . . . . . . . . . . . . . . . . . . . . . . . . . . . . . . 17 7Essential Modem Features. . . . . . . . . . . . . . . . . . . . . . . . . . . . . . . . . . . . . 18 8Known Issues or Limitations. . . . . . . . . . . . . . . . . . . . . . . . . . . . . . . . . . . 18 Document Conventions‘Configure > Communications > Alarm Center’ means ‘click theConfigure icon on the toolbar, then in the navigation pane find theCommunications group, and select Alarm Center from it’.Associated DocumentationTN-742: Remotely Monitoring and Configuring the TB8100 Base StationTB8100 Installation and Operation ManualTB8100 Service Kit and Alarm Center User’s Manuals and online HelpY our APS User’s GuidePage 2 of 20TN-906© Tait Electronics Limited 30 September 2004This Application Note provides information on how to connect multipleTB8100 base stations to a Service Kit or Alarm Center using anAsynchronous Port Switch (APS). It covers connection via direct serial link,and via PSTN lines using modems. T ypical physical connections, APSconfigurations, base station configurations, Service Kit configurations, andmodem settings are also described.1The Purpose of an APSOne of the most powerful features of the TB8100 base station is its abilityto be remotely configured and monitored. This feature includes Service Kitaccess, for remote configuration, monitoring, and diagnostics, andautomatic dial-out to an Alarm Center, as a result of an error condition orTask Manager stimulus. TN-742 describes the use of this feature in detail.Without using an APS, however, a dedicated PSTN line is required for eachbase station installed on a site. The cost of these lines is very high, especiallywhen the base stations are installed in remote locations. Using an APSallows a single phone line to service up to 31 base stations.A typical connection scenario is shown in Figure1 below. The diagramshows:I four base stations connected to various ports on an APSI the dial-up modem at the remote siteI the PSTN connectionI the modem at the local siteI a PC running either Service Kit or Alarm Center software.Figure 1Typical APS ConnectionTN-906Page 3 of 20© Tait Electronics Limited 30 September 2004Page 4 of 20TN-906© Tait Electronics Limited 30 September 20042Supported APS Units and their Main Features2.1Units SupportedThe APS support feature in the TB8100 base station is intended to work with third party products. Tait Electronics Limited does not manufacture its own unit. The following third party units are supported:IW estern T elematic Inc. (WTI) APS-4, APS-8, APS-16, CMS-16, and CMS-32IBlack Box SW543A.Any other APS that uses simple ASCII connect and disconnect commands and responses may work satisfactorily.2.2Main FeaturesThese features are standard on the supported APS units listed above.IY ou can connect up to 3, 7, 15, or 31 base stations per site to a single PSTN line or PC, depending on the APS chosen.I The units are configured as DTE (Data T erminal Equipment).IThe units will support all baud rates recognised by the base station, i.e. 1200, 2400, 9600, 19200, 38400, 57600, and 115200.IAlthough the APS ports can be individually configured, and may be password protected, the TB8100 base station does not support this. (Note that in “Common Configuration for all Ports” on page 14 the password is left undefined)I The APS configurations are stored in non-volatile memory.IData clashes are prevented using a Busy response, i.e. if one base station tries to dial out while another is connected, it will receive a Busy response, and can try again later if configured to do so.IThe Service Kit or base station alarm dial-out software handle allcommon errors such as busy, lack of response, or communications failure.IThe APS can be powered from 115/230VAC or –48VDC. The power consumption is approximately 5W .3Physical ConnectionsIn all the following connection types, only two or three base stations areshown connected to the APS for graphical convenience.The modem is shown connected to the highest numbered port of the APS.This is for user convenience only, and allows an easy mapping between thebase station number and port number when configuring the Service Kit.Any port could be used if desired.A single null modem cable is supplied with the APS. The user must supplyall other cables.Figure 2PSTN connection to base stations without a TaitNet RS-232 system interface boardTN-906Page 5 of 20© Tait Electronics Limited 30 September 2004Figure 3PSTN connection to base stations with a TaitNet RS-232 system interface boardPage 6 of 20TN-906© Tait Electronics Limited 30 September 2004Figure 4Direct connection to base stations with or without a TaitNet RS-232 system interface boardTN-906Page 7 of 20© Tait Electronics Limited 30 September 2004Figure 5Combined PSTN and direct connectionsPage 8 of 20TN-906© Tait Electronics Limited 30 September 2004TN-906Page 9 of 20© Tait Electronics Limited 30 September 20044Configuring the Service Kit and Base Station4.1Configuring the Service Kit for Dial-in via an APS1.Run the Service Kit and select Connect > New Connection. The Edit Connection screen appears.2.In the Connection type list, select Modem Dialup. The Edit Connection screen changes to the one shown below.Page 10 of 20TN-906© Tait Electronics Limited 30 September 20043.Set up the parameters in the Connection tab as usual (use the online Help if required).4.In the Port Switch tab, select the Port switch check box.5.In the Connect command field, enter ^M/Cx^M.This means:Note Use the ^ (carat) symbol to instruct the Service Kit that this is a control character. Do not use the control key.6.In the Connect response field, enter 1.7.In the Disconnect command field, enter ^Mxxx^M/X^M.This means:8.In the Disconnect response field, enter 3.^M instructs the APS to enter command mode a a.This is equivalent to the carriage return character./C requests a connectionx the port number of the base station you wish to connect to ^Mterminates the sequence^M instructs the APS to enter command mode xxx three instances of the logoff character a a.This must match the logoff character chosen when setting up the modem (L was chosen in this case). Refer to “Common Configuration for all Ports” on page 14.^M terminates the sequence /X^Mexits command mode4.2Configuring the Service Kit for a Direct Connection via an APSThis configuration is similar to the one described in the previous section, except that you set the Connection type to Direct Connection. Y ou can then connect the computer running the Service Kit software to any spare port on the APS, and connect to any base station that is not currently busy with either a dial-in or dial-out session.4.3Configuring the Base Station to Dial Out to an Alarm CenterThis section provides details on configuring the Alarm Center connection, the port switch, and the connection timing. For full details on configuring the modem, refer to TN-742.1.Run the Service Kit and select Configure > Communications > Alarm Center.2.In the Alarm Center form, enable the Alarm Center connection and the Port switch (use the on-line Help if required).3.In the Baud rate list, select 57600. If you select a different baud rate, ensure that the APS is set to the same rate (refer to “Configuring the Set-up Switches” on page 13).4.In the Connect command field, enter ^M/Cx^M.This means:The site modem is usually (but does not have to be) connected to the highest port number available. The above screen shows the settings for port 8 of an 8-port APS.^M instructs the APS to enter command mode a a.This is equivalent to the carriage return character./C requests a connectionx the port number to which the site modem is connected ^Mterminates the sequencePage 12 of 20TN-9065.In the Connect response field, enter 1.6.In the Disconnect command field, enter ^Mxxx^M/X^M.This means:7.In the Disconnect response field, enter 3.8.In the Connection timing area, we recommend the following settings:I Set the number of retries to 20, the maximum allowed.ISet the time between retries to 60s for the first base station, and increment in steps of 5s for other base stations (e.g. set base station 2 to 65s, base station 3 to 70s, etc.). This prevents all base stations from retrying at the same time if a fault occurs that affects them all.ISet the minimum interval to at least 30 minutes. The interval should be long enough to allow all base stations to dial out if necessary; we suggest 30 minutes plus an extra 3 minutes for each base station on the site.NoteIf there is a particular condition that can be guaranteed to affect all base stations (e.g. mains failure), we recommend that you enable this alarm on only two base stations. This precaution will prevent a mass dial-out attempt, but will still allow you to check for false alarms.^M instructs the APS to enter command mode xxx three instances of the logoff character a a.This must match the logoff character chosen when setting up the modem (L was chosen in this case). Refer to “Common Configuration for all Ports” on page 14.^M terminates the sequence /X^Mexits command mode5Configuring the APS5.1Ensuring the Security of Configuration DataThe configuration data of many APS units is stored in RAM which has abattery back-up. This battery should have a life of approximately 3 yearswhen the APS is not powered up, and may need to be changed periodically.Y ou may also wish to replace the battery before installing your APS to ensuremaximum battery life and security of configuration data. A typical symptomof battery failure is the loss of configuration data when the APS is powereddown for some time.The battery is typically a BR1225 and is located under a clip on the mainboard of the APS. T o replace the battery, proceed as follows:1.Disconnect the AC mains power.2.Remove the top cover.3.Carefully replace the battery, observing normal antistatic precautions.4.Replace the cover.5.2Configuring the Set-up Switches1.Power up the APS.2.Configure the set-up switches as shown below. These switches arelocated on the rear panel of APS units with up to 8 ports, and on thebottom cover of units with 16 or more ports.Switch Setting FunctionSW1ON (down)sets the baud rate to 57k6SW2OFFSW3OFFSW4OFF no handshakingSW5OFFSW6OFF terse messagesSW7OFF echo disabledSW8–––currently not usedThe settings for SW1, SW2, and SW3 are optional, however the set-tings for all other switches are mandatory. W e recommend a baud rateof 57k6, as it will give the highest possible data transfer rate throughthe modem on a “good” PSTN connection. If you select a differentrate, you must select the same rate for the Alarm Center connection(Configure > Alarm Center > Port Settings > Baud rate; refer to“Configuring the Base Station to Dial Out to an Alarm Center” onpage11).3.After you have set the switches, you must validate the set-up asfollows:a.Simultaneously press the SET and CLEAR buttons on the front ofthe APS.b.Release the CLEAR button, wait for the port ACTIVITY LEDsto flash, then release the SET button.5.3Configuring the PortsConnect a PC running a terminal program (HyperT erminal, ProComm,T erraT erm or similar) to any unused port on the APS, using a null modemcable.Note Refer to the APS User’s Guide for a detailed explanation of all thecommand codes. The commands shown in the following sectionare in upper case for clarity, however you can use lower case if youprefer.Common Configuration for all Ports 1.Enter Command Mode using the [Enter] key.2.Type the following commands:/CP [Enter]copies port parameters7 [Enter] 1 [Enter]sets all ports to Any-to-Any mode9 [Enter] x [Enter]where x sets the logoff characterNote that this must be the same character youchose in the Service Kit procedures describedin Section4.1 and Section4.3 (L in theexamples shown). It must also be differentfrom the character used to take the modemout of data mode, which is usually “+”, butcan be changed by the user. You can alsochoose control characters, which are shown bya preceding ^ (carat).10 [Enter] 1 [Enter]sets the disconnect sequence to 3 consecutivelogoff characters, instead of just 1Note that this is essential to avoid thepossibility of random logoffs.11 [Enter] 6 [Enter]enables the timeout to 1 minute12 [Enter] 3 [Enter]sets the response type to Terse13 [Enter] 1 [Enter]disables the command echo[Esc]copies to all portsY [Enter]answers the question “Are you sure (y/n)?”/W [Enter]displays port parametersPage 14 of 20TN-9063.V erify that the following is displayed.PORT PARAMETERS #01:1. Port Name: (undefined)2. Password: (undefined)3. Baud Rate: 57.6K4. Bits/Parity: 8-None5. Stop Bits: 16. Handshake Mode: None7. Port Mode: Any-to-Any74. DTR Output: Pulse8. Supervisor Mode: Permit9. Logoff Character: L10. Sequence Disconnect: Three Characters11. Timeout Disconnect: 1 Min12. Response Type: Terse13. Command Echo: Off14. Accept Break: YesIf everything is correct, proceed to step 4, or re-enter the incorrect parameter as required.4.WTI APS-4, APS-8 and APS-16 Units OnlyThis step is required because of a bug in the firmware of the APS-4, APS-8 and APS-16 units. The Copy Port Parameters command does not work for the timeout setting.T ype the following commands:/Pn [Enter]sets RS-232 parameterswhere n is the port number11 [Enter] 6 [Enter]enables the timeout to 1 minute[Esc]Repeat this procedure for all ports.5.If you do not want to configure a port as a modem port (refer to“Configuration for a Modem Port (if a modem is used)” below), exit Command mode by typing:/X [Enter]exits command modeOtherwise, continue with “Configuration for a Modem Port (if amodem is used)” on page16.Configuration for a Modem Port(if a modem is used)W e recommend that you configure the port to which the modem is connected as a modem port. This will ensure that the modem is re-configured after a power outage, and prevent it from using the wrong serial baud rate.T ype the following commands:/Pn [Enter]sets RS-232 parameterswhere n is the number of the port to whichthe modem is connected, usually the highestnumbered portVerify that the timeout has been set correctlyto 1 minute. If not, type 11 [Enter] 6 [Enter].7 [Enter] 4 [Enter]configures the port as a modem port71 [Enter] AT [Enter]sets the reset string to AT72 [Enter] AT [Enter]sets the initialisation string to ATThis is just to ensure that no unwantedcommands are issued to the modem.73 [Enter] +++~~ATH0[Enter]ensures that modem hangs up after a timeoutNote that the double ~ (tilde) puts a 2s delaybetween +++ and ATH0, allowing the modemto enter command mode.[Esc]/X [Enter]exits Command modePage 16 of 20TN-9066Testing the ConnectionConnecting to the Base Station via the APS Once everything has been configured, dial in to the base station via the APS.1.Run the Service Kit software and click Connect.2.Select the APS connection previously set up. The following screenappears, as for a normal (non-APS) connection.Once the modems have connected and established their protocol, the following screen appears. This screen is unique to APS connections.Shortly afterwards, the correct port is connected, and the base station responds to its connection protocol. The normal base station logon screen now appears.3.Continue with the connection session as normal.4.When you have completed your session, disconnect in the normalway.Page 18 of 20TN-906If the Connection is Unsuccessful1.If an error occurs which is related to the APS, the following screen will appear.2.If this screen appears, check the settings of both the APS and the Service Kit very carefully. If the you cannot resolve the problem, it may be useful to insert a serial communications monitor between the Service Kit PC and the modem. Compare the strings actually transmitted with those expected, and consult the APS User’s Guide.7Essential Modem FeaturesThe ATX0 command must be available in any modem which is used with the APS. This command limits the result codes to 0-4, i.e:I 0 – OK I 1 – connect I 2 – ring I 3 – no carrier I4 – errorNoteSome modems will include result code 8 (no answer) in the list for ATX0. This is also acceptable. Refer to TN-742 for modem set-tings and configurations.8Known Issues or LimitationsKnown Issue or LimitationSolutionSome APS units store their configuration data in RAM with battery back-up. This data will be lost if the unit is powered down and the battery fails.If you are unsure about the condition of the back-up battery, replace it before installing the APS (refer to “Ensuring the Security of Configuration Data” on page 13).Applies to WTI APS-4, APS-8 and APS-16 units:You cannot use the Copy Port Parameterscommand to set the timeout.You must set the port timeout on each port individually. If you try to set this parameter globally, it will appear to be successful, but the timeout will not work. Refer to“Common Configuration for all Ports” on page 14.Issuing AuthorityThis TN was issued by:John CrosslandT echnical Publications ManagerPublication HistoryAmendment RecordTait Contact InformationCorporate Head OfficeNew ZealandTait Electronics Limited, P .O. Box 1645, Christchurch, New Zealand E-mail (Marketing): *********************E-mail (Sales): *******************Technical SupportT echnical Support ManagerTait Electronics Ltd, P .O. Box 1645, Christchurch, New Zealand E-mail: *********************InternetPublication Date Author 30 September 2004D ReynoldsPublication Date PageAmendment 30 September 2004First releasePage 20 of 20TN-906。
ConST811用户手册(中文)
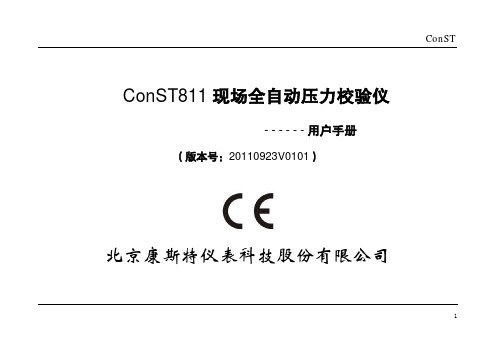
2.1 检查设备及配件 .................................................................................................................................................................................................. 11 2.2 仪器图示 ............................................................................................................................................................................................................ 12
亿佰特-E810-TTL-01产品使用手册

模块介绍E810-TTL-01是一款体积小,功能强大的串口转以太网模块。
实现了RJ45网口与TTL串口之间的数据透明传输。
模块搭载M0+系列32位处理器,运行速率快,效率高。
具备自适应网络速率(最高支持100M全双工)、TCP Server、TCP Client、UDP Server、UDP Client 四种通信机制。
E810-TTL-01操作简单,用户可直接通过上位机对模块进行参数配置。
轻松实现数据传输。
目录1.产品规格及特性 (4)2.硬件参数及设计介绍 (4)2.1.尺寸图4 2.2.引脚定义 (5)2.3.连接方法 (5)2.3.1.典型应用硬件连接 (5)2.3.2.UART串口电平转换 (6)1.1.1.以太网接口外置变压器的应用 (6)1.1.2.以太网接口内置变压器的应用 (7)2.网络基础功能介绍 (7)2.1.IP地址/子网掩码/网关 (7)2.2.DNS服务器地址 (8)3.SOCKET功能特性 (8)4.1.TCP S ERVER模式特性 (9)4.2.TCP C LIENT模式特性 (10)4.3.UDP S ERVER模式特性 (10)4.4.UDP C LIENT模式特性 (11)4.特殊功能 (11)4.1.短连接11 4.2.注册包机制 (11)4.3.心跳包机制 (12)4.4.超时重启 (12)4.5.TCP多连接功能 (13)4.6.清除缓存数据 (13)4.7.L INK和数据传输指示 (13)5.快速使用说明 (13)5.1.参数设置说明 (13)5.2.S OCKET使用说明 (14)5.2.1.TCP Server使用说明 (14)5.2.2.TCP Client使用说明 (15)5.2.3.UDP Server使用说明 (16)5.2.4.UDP Client使用说明 (18)5.3.特殊功能使用说明 (19)5.3.1.短连接使用说明 (19)5.3.2.注册包使用说明 (20)5.3.3.心跳包使用说明 (21)5.3.4.超时重启使用说明 (22)5.3.5.清除缓存使用说明 (22)6.AT指令配置 (23)6.1.AT指令概述 (23)6.2.AT指令错误码 (23)6.3.AT指令集 (23)6.4.AT指令详解 (24)6.4.1.AT+REBT246.4.2.AT+VER246.4.3.AT+EXAT246.4.4.AT+RESTORE (24)6.4.5.AT+UART246.4.6.AT+UARTCLR (25)6.4.7.AT+MAC256.4.8.AT+USERMAC (25)6.4.9.AT+LINKSTA (25)6.4.10.AT+WAN266.4.11.AT+LPORT (26)6.4.12.AT+SOCK266.4.13.AT+REGMOD (27)6.4.14.AT+REGINFO (27)6.4.15.AT+HEARTMOD (27)6.4.16.AT+HEARTINFO (28)6.4.17.AT+HEARTM (28)6.4.18.AT+SHORTM (28)6.4.19.AT+TMORST (28)6.4.20.AT+H (29)8.重要声明 (29)9.关于我们 (29)1.产品规格及特性2.硬件参数及设计介绍2.1.尺寸图2.2.引脚定义2.3.连接方法2.3.1.典型应用硬件连接图2-1典型硬件连接原理图2.3.2.UART串口电平转换图2-2UART串口电平转换原理图1.1.1.以太网接口外置变压器的应用图2-3以太网接口外置变压器原理图1.1.2.以太网接口内置变压器的应用图2-4以太网接口内置变压器原理图2.网络基础功能介绍2.1.IP地址/子网掩码/网关1.IP地址是模块在局域网中的身份表示,在局域网中具有唯一性,因此不能与同局域网的其他设备重复。
你知道LTE Cat.1到Cat.10 那你知道Cat.0吗?

你知道LTE Cat.1到Cat.10 那你知道Cat.0吗?据说,到2020年,有500亿设备要连接网络,这是未来物联网的广阔前景。
好消息,以后运营商也不用跪着发展客户了,坐等设备连接就好了!不过,没那么乐观!支持物联网的无线技术太多,蜂窝网络也只是其中一小部分而已。
做个计算题,假设500亿连接设备中,减去100亿连接手机和PC,剩下400亿去连接物联网,按照目前的蜂窝网技术,估计只有2%(约8亿)的物联网设备可接入蜂窝网络。
才8亿?我泱泱中华的手机用户数都超过啦,何况物联网那点流量,呵呵!为了解决这些问题,Cat.0就来了!什么是Cat.0?Cat.即UE-Category,根据3GPP的定义,UE-Category分为1~10共10个等级,其中Cat.1-5为R8定义,Ca t.6-8为R10定义,Cat.9-10为R11定义。
如上图,UE-Category主要定义了UE终端能支持的上下行速率。
Cat.0是被写入3GPP Rel.12标准,支持更低速率、更低功耗版本的LTE终端等级。
Cat.0 和Cat.1都是指向广阔的物联网市场,实现更低功耗、更低成本物联网设备连接到LTE网络。
支持更低Category,对可穿戴设备、智慧家庭和智慧电表等物联网应用非常关键。
不过,一直以来,无论是网络还是终端芯片,LTE与物联网之间总是存在一条难以跨越的鸿沟,不过,随着这些年一些通信设备公司和芯片公司的积极投入,可望改变市场局势,为LTE网络连接物联网提供更广阔的前景。
比如,前不久,Sequans与Altair相继宣布近期将推出Cat.0和Cat.1芯片组。
为什么要定义Cat.0呢?为了应对物联网,LTE-M(M2M)必须对LTE网络进行几个方面的优化:1)设备成本尽管大量设备接入带来巨大价值,但是,连接设备的成本却是一个大问题。
连接蜂窝网络的设备需要芯片支持,为了支持高清视频、在线游戏,目前LTE芯片主要支持几十到几百Mpbs的高速高性能LTE网络。
- 1、下载文档前请自行甄别文档内容的完整性,平台不提供额外的编辑、内容补充、找答案等附加服务。
- 2、"仅部分预览"的文档,不可在线预览部分如存在完整性等问题,可反馈申请退款(可完整预览的文档不适用该条件!)。
- 3、如文档侵犯您的权益,请联系客服反馈,我们会尽快为您处理(人工客服工作时间:9:00-18:30)。
© 2005 by Catalyst Semiconductor, Inc. Characteristics subject to change without notice 1Doc. No. 3005, Rev. RCAT811, CAT8122Doc. No. 3005, Rev. R© 2005 by Catalyst Semiconductor, Inc.Characteristics subject to change without noticeORDERING INFORMATIONPIN DESCRIPTIONSTOP MARKINGNotes1)The “YM” in the SOT-143 package marking indicates the Yearand Month of production.2)All NiPdAu devices will be marked to indicate product type andpackage. Threshold and full part numbers will be provided on box and reel labels as well as all Shipping documents.d n a s t r a P d l o h se r h T 341-T O S )1(341-T O S n S n e e r G d a e L e t t a M h s i n i F )2()1(341-T O S n e e r G d a e L u A d P i N h s i n i F )2()1(8T A C 11L M Y M A M Y H D E MY R 8T A C 11M M Y N A M Y J D J 118T A C A M Y Z M Y K C T 118T A C M Y P A M Y L D S 118T A C M Y Q A M Y M D R 118T A C M Y R A M Y N D Z 118T A C A M Y Y M Y P C L 218T A C M Y S A D M Y R E MY S M 218T A C M Y T A D M Y T J 218T A C M Y U A D M Y U T 218T A C M Y V A D M Y V S 218T A C M Y W A D M Y W R 218T A C M Y X A D M Y X Z218T A C MY I C MY Y C * NiPdAu is a Lead Finish Option on the GreenPackages only. Unless indicated with the “G ” green packages are shipped with a Sn Matte Lead Finish.CAT811, CAT8123Doc No. 3005, Rev. R© 2005 by Catalyst Semiconductor, Inc.Characteristics subject to change without noticeELECTRICAL CHARACTERISTICSV CC = Full range, T A = -40°C to +85°C unless otherwise noted. Typical values at T A = +25°C and V CC = 5 V for the L/M/J versions, V CC = 3.3 V for the T/S versions, V CC = 3 V for the R version and V CC = 2.5 V for the Z version.ABSOLUTE MAXIMUM RATINGS*Any pin with respect to ground ..........-0.3 V to +6.0 V Input Current, V CC .............................................20 mA Output Current, RESET, RESET......................20 mA Rate of Rise, V CC .............................................................100 V/µs Continuous Power DissipationDerate 4mW/°C above 70°C (SOT143)........320 mWOperating Temperature Range...........-40°C to +85°C Storage Temperature Range............-65°C to +105°C Lead Soldering Temperature (10 sec)..............300°C*COMMENTStresses above those listed under “Absolute Maximum Ratings ” may cause permanent damage to the device. These are stress ratings only,and functional operation of the device at these or any other conditions outside of those listed in the operational sections of this specification is not implied. Exposure to any absolute maximum rating for extended periods may affect device performance and reliability.CAT811, CAT8124Doc. No. 3005, Rev. R© 2005 by Catalyst Semiconductor, Inc.Characteristics subject to change without noticeELECTRICAL CHARACTERISTICS V CC = Full range, T A = -40˚C to +85˚C unless otherwise noted. Typical values at T A = +25˚C and V CC = 5 V for L/M/J versions, V CC = 3.3 V for T/S versions, V CC = 3 V for R version and V CC = 2.5 V for Z version.(continued)Note 1: Production testing done at T A = +25˚C; limits over temperature guaranteed by design only.Note 2: RESET output for the CAT811; RESET output for the CAT812Note 3: Glitches of 100 ns or less typically will not generate a reset pulse.CAT811, CAT8125Doc No. 3005, Rev. R© 2005 by Catalyst Semiconductor, Inc.Characteristics subject to change without noticeTYPICAL OPERATING CHARACTERISTICSV CC = Full range, T A = -40˚C to +85˚C unless otherwise noted. Typical values at T A = +25˚C and V CC = 5 V for L/M/J versions, V CC =3.3 V for T/S versions, V CC = 3 V for R version and V CC = 2.5 V for Z version.SUPPLY CURRENT VS. TEMPERATURE(NO LOAD, CAT8xxR/S/T/Z)121086420-50 0 50 100 150S U P P L Y C U R R E N T (µA )TEMPERATURE (˚C)POWER-DOWN RESET DELAY VS. TEMPERATURE(CAT8xxR/S/T/Z)1412108642P O W E R -D O W N R E S E T D E L A Y (µS )TEMPERATURE (˚C)POWER-UP RESET TIMEOUTVS. TEMPERATURE260240220200180160P O W E R -U P R E S E T T I M E O U T (m S )TEMPERATURE (˚C)NORMALIZED RESET THRESHOLDVS. TEMPERATURE1.000210.99980.99960.99940.99920.9990.99880 20 40 60 80 100 120N O R M A L I Z E D T H R E S H O L DTEMPERATURE (˚C)-50 0 50 100 150-50 0 50 100 150CAT811, CAT8126Doc. No. 3005, Rev. R© 2005 by Catalyst Semiconductor, Inc.Characteristics subject to change without noticeDETAILED DESCRIPTIONSRESET TIMINGThe reset signal is asserted LOW for the CAT811 and HIGH for the CAT812 when the power supply voltage falls below the threshold trip voltage and remains asserted for at least 140ms after the power supply voltage has risen above the threshold.Figure 1. Reset Timing DiagramFigure 2. Maximum Transient Duration Without Causing a Reset Pulse vs. Reset Comparator Overdrive3025201510 50T R A N S I E N T D U R A T I O N [µs )RESET OVERDRIVE V TH - V CC [mV]1 10 100 10005V 0V5V 0V 5V0VPower Supply Voltage RESETRESETV CC TRANSIENT RESPONSEThe CAT811/812 protect µPs against brownout failure.Short duration transients of 4µsec or less and 100 mV amplitude typically do not cause a false RESET.Figure 2 shows the maximum pulse duration of negative-going V CC transients that do not cause a reset condition.As the amplitude of the transient goes further below the threshold (increasing V TH - V CC ), the maximum pulse duration decreases. In this test, the V CC starts from an initial voltage of 0.5V above the threshold and drops below it by the amplitude of the overdrive voltage (V TH - V CC ).CAT811, CAT8127Doc No. 3005, Rev. R© 2005 by Catalyst Semiconductor, Inc.Characteristics subject to change without noticeVALID RESET WITH V CC UNDER 1.0 VTo ensure that the CAT811 RESET pin is in a known state when V CC is under 1.0 V, a 100 k Ω pull-down resistor between RESET pin and GND is recommended;the value is not critical. For the CAT812, a pull-up resistor from RESET pin to V CC is needed.Figure 3. RESET Valid with V CC Under 1.0 V Figure 4. RESET Valid with V CC Under 1.1 VFigure 5. Bi-directional Reset Pin Interfacing(For example: 68HC11)BI-DIRECTIONAL RESET PIN INTERFACING The CAT811/812 can interface with µP/µC bi-directional reset pins by connecting a 4.7 k Ω resistor in series with the CAT811/812 reset output and the µP/µC bi-directional reset pin.CAT811, CAT8128Doc. No. 3005, Rev. R© 2005 by Catalyst Semiconductor, Inc.Characteristics subject to change without noticeOTHER SUPERVISORY PRODUCTS0.20GAUGE PLANEPACKAGE INFORMATION Plastic SOT143 (4-Pin)Catalyst Semiconductor, Inc.Corporate Headquarters 1250 Borregas Avenue Sunnyvale, CA 94089Phone: 408.542.1000Fax: 408.542.1200Copyrights, Trademarks and PatentsTrademarks and registered trademarks of Catalyst Semiconductor include each of the following:DPP ™AE 2 ™MiniPot ™Catalyst Semiconductor has been issued U.S. and foreign patents and has patent applications pending that protect its products. For a complete list of patents issued to Catalyst Semiconductor contact the Company ’s corporate office at 408.542.1000.CATALYST SEMICONDUCTOR MAKES NO WARRANTY, REPRESENTATION OR GUARANTEE, EXPRESS OR IMPLIED, REGARDING THE SUITABILITY OF ITS PRODUCTS FOR ANY PARTICULAR PURPOSE, NOR THAT THE USE OF ITS PRODUCTS WILL NOT INFRINGE ITS INTELLECTUAL PROPERTY RIGHTS OR THE RIGHTS OF THIRD PARTIES WITH RESPECT TO ANY PARTICULAR USE OR APPLICATION AND SPECIFICALLY DISCLAIMS ANY AND ALL LIABILITY ARISING OUT OF ANY SUCH USE OR APPLICATION, INCLUDING BUT NOT LIMITED TO, CONSEQUENTIAL OR INCIDENTAL DAMAGES.Catalyst Semiconductor products are not designed, intended, or authorized for use as components in systems intended for surgical implant into the body, or other applications intended to support or sustain life, or for any other application in which the failure of the Catalyst Semiconductor product could create a situation where personal injury or death may occur.Catalyst Semiconductor reserves the right to make changes to or discontinue any product or service described herein without notice. Products with data sheets labeled "Advance Information" or "Preliminary" and other products described herein may not be in production or offered for sale.Catalyst Semiconductor advises customers to obtain the current version of the relevant product information before placing orders. Circuit diagrams illustrate typical semiconductor applications and may not be complete.REVISION HISTORYDate Rev.Reason10/22/03L Updated Ordering Information 12/22/2003MUpdated FeaturesReplaced power-up reset timeout vs. temperature graph with updated oneReplaced VCC Transient Response graph with updated one3/22/04N General data sheet updates3/25/2004O Updated Electrical Characteristics (Reset Active Timeout Period Max)3/25/2004P Corrected Pin Configure diagram 9/28/2004Q Minor changes 12/28/2005RUpdated FeaturesUpdated Ordering Information Updated Yop MarkingPublication #:3005Revison:RIssue date:12/28/05。