试车记录
单机试车原始记录表【范本模板】
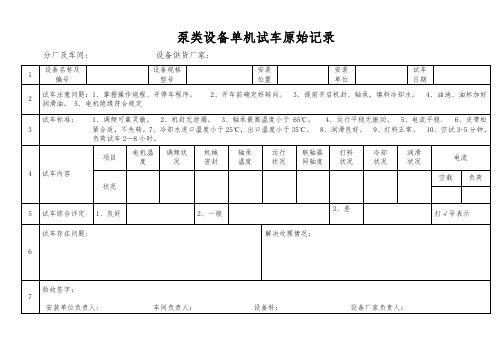
泵类设备单机试车原始记录分厂及车间: 设备供货厂家:
氧化铝三分公司浓密机单机试车原始记录分厂及车间: 设备供货厂家:
分厂及车间:设备供货厂家:
分厂及车间:设备供货厂家:
球磨机单机试车表记录分厂及车间:设备供货厂家:
分厂及车间:供货设备厂家:
分厂及车间: 设备供货厂家:
分厂及车间: 设备供货厂家:
氧化铝三分公司搅拌类设备单机试车原始记录分厂及车间:设备供货厂家:
氧化铝三分公司板式换热器单机试车原始记录分厂及车间:设备供货厂家:
氧化铝三分公司化灰机单机试车原始记录分厂及车间:设备供货厂家:
氧化铝三分公司起重设备单机试车原始记录分厂及车间:设备供货厂家:
氧化铝三分公司重型板式给料机单机试车原始记录分厂及车间:设备供货厂家:
氧化铝三分公司除尘器单机试车原始记录分厂及车间:设备供货厂家:
氧化铝三分公司旋流器组单机试车原始记录分厂及车间: 设备供货厂家:
氧化铝三分公司回转筛单机试车原始记录分厂及车间:设备供货厂家:
氧化铝三分公司回转筛单机试车原始记录分厂及车间: 设备供货厂家:
氧化铝三分公司煤气发生炉单机试车原始记录分厂及车间:设备供货厂家:
氧化铝三分公司矿石定量给料机单机试车原始记录分厂及车间: 设备供货厂家:
氧化铝三分公司石灰定量给料机单机试车原始记录分厂及车间:设备供货厂家:。
鼓风机试车记录
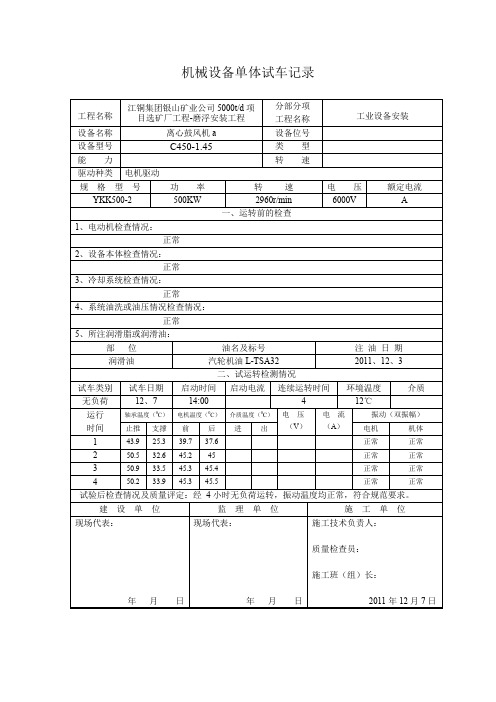
工程名称江铜集团银山矿业公司5000t/d项目选矿厂工程-磨浮安装工程分部分项工程名称工业设备安装设备名称离心鼓风机a 设备位号设备型号C450-1.45类型能力转速驱动种类电机驱动规格型号功率转速电压额定电流YKK500-2 500KW 2960r/min 6000V A一、运转前的检查1、电动机检查情况:正常2、设备本体检查情况:正常3、冷却系统检查情况:正常4、系统油洗或油压情况检查情况:正常5、所注润滑脂或润滑油:部位油名及标号注油日期润滑油汽轮机油L-TSA32 2011、12、3二、试运转检测情况试车类别试车日期启动时间启动电流连续运转时间环境温度介质无负荷12、7 14:00 4 12℃运行时间轴承温度(0C)电机温度(0C)介质温度(0C)电压(V)电流(A)振动(双振幅)止推支撑前后进出电机机体1 43.9 25.3 39.7 37.6 正常正常2 50.5 32.6 45.2 45 正常正常3 50.9 33.5 45.3 45.4 正常正常4 50.2 33.9 45.3 45.5 正常正常试验后检查情况及质量评定:经4小时无负荷运转,振动温度均正常,符合规范要求。
建设单位监理单位施工单位现场代表:年月日现场代表:年月日施工技术负责人:质量检查员:施工班(组)长:2011年12月7日工程名称江铜集团银山矿业公司5000t/d项目选矿厂工程-磨浮安装工程分部分项工程名称工业设备安装设备名称离心鼓风机b 设备位号设备型号C450-1.45类型能力转速驱动种类电机驱动规格型号功率转速电压额定电流YKK500-2 500KW 2960r/min 6000V A一、运转前的检查1、电动机检查情况:正常2、设备本体检查情况:正常3、冷却系统检查情况:正常4、系统油洗或油压情况检查情况:正常5、所注润滑脂或润滑油:部位油名及标号注油日期润滑油汽轮机油L-TSA32 2011、12、3二、试运转检测情况试车类别试车日期启动时间启动电流连续运转时间环境温度介质无负荷12、7 14:00 4 12℃运行时间轴承温度(0C)电机温度(0C)介质温度(0C)电压(V)电流(A)振动(双振幅)止推支撑前后进出电机机体1 43.5 25 39.5 37.4 正常正常2 50 32.2 45.1 45 正常正常3 50.2 33.5 45.3 45.7 正常正常4 51 33.8 45.4 46 正常正常试验后检查情况及质量评定:经4小时无负荷运转,振动温度均正常,符合规范要求。
单机试车记录(风机)
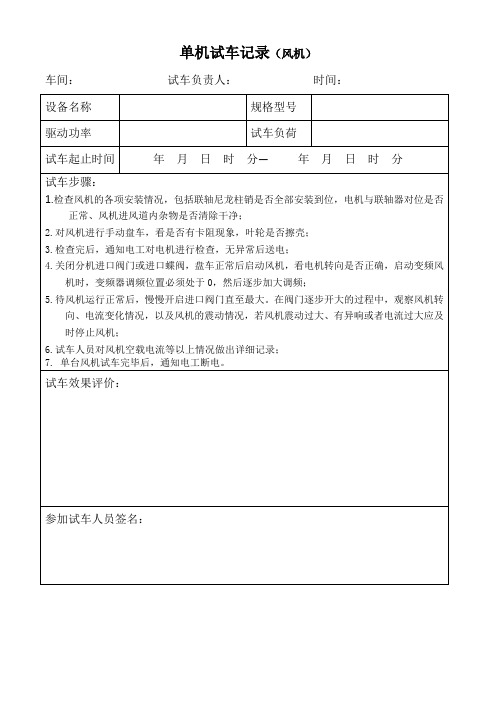
5.待风机运行正常后,慢慢开启进口阀门直至最大。在阀门逐步开大的过程中,观察风机转向、电流变化情况,以及风机的震动情况,若风机震动过大、有异响或者电流过大应及时停止风机;
单机试车记录
车间:试车负责人:时间:
设备名称
规格型号
驱动功率
试车负荷
试车起止时间
年月日时分—年月日时分
试车步骤:
1.检查风机的各项安装情况,包括联轴尼龙柱销是否全部安装到位,电机与联轴器对位是否正常、风机进风道内杂物是否清除干净;
2.对风机进行手动盘车,看是否有卡阻现象,叶轮是否擦壳;
3.检查完后,通知电工对电机进行检查,无异常后送电;
6.试车人员对风机空载电流等以上情况做出详细记录;
7. 单台风机试车完毕后,通知电工断电。
试车效果评价:
参加试车人员签名:
3503-J323电动机试车记录
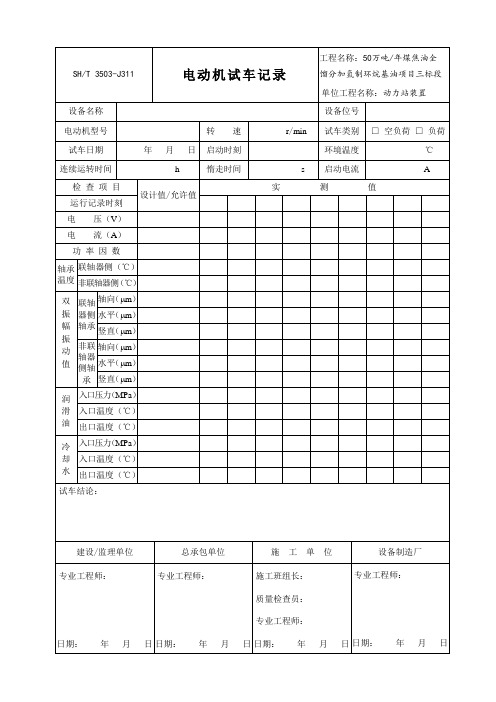
施 工 单 位
设备制造厂
专业工程师:
日期: 年 月 日
专业工程师:
日期: 年 月 日
施工班组长:
质量检查员:
专业工程师:
日期: 年 月 日
专业工程师:
日期: 年 月 日
电 压(V)
电 流(A)
功 率 因 数
轴承
温度
联轴器侧(℃)
非联轴器侧(℃)
双振幅振动值
联轴器侧轴承
轴向(m)
水平(m)
竖直(m)
非联
轴器
侧轴承
轴向(m)
水平(m)
竖直(m)
润
滑
油
入口压力(MPa)
入口温度(℃)
出口温度(℃)
冷
却
水
入口压力(MPa)
入口温度设/监理单位
SH/T3503-J311
电动机试车记录
工程名称:50万吨/年煤焦油全
馏分加氢制环烷基油项目三标段
单位工程名称:动力站装置
设备名称
设备位号
电动机型号
转 速
r/min
试车类别
□空负荷□负荷
试车日期
年 月 日
启动时刻
环境温度
℃
连续运转时间
h
惰走时间
s
启动电流
A
检 查 项 目
设计值/允许值
实 测 值
运行记录时刻
压缩机试车记录

轴向
后
轴
承
水平
竖直
轴向
轴位移值,mm
建设/监理单位
总承包单位
施工单位
设备制造厂
专业工程师:
日期: 年 月 日
专业工程师:
日期: 年 月 日
施工班组长:
质量检查员:
专业工程师:
日期: 年 月 日
现场代表:
日期: 年 月 日
专业工程师:
日期: 年 月 日
施工班组长:
质量检查员:
专业工程师:
日期: 年 月 日
现场代表:
日期: 年 月 日
SH/T 3503—J320-2
往复式压缩机
试车记录(续)
工程名称:
单位工程名称:
检查项目
设计值/
允许值
实测值
运行记录时刻
段
入口
压力,MPa
温度,℃
出口
压力,MPa
温度,℃
填料函温度,℃
段
驱动机种类
转速
r/min
启动电流
A
试车类别
□空负荷□负荷
环境温度
℃
试车日期
年月日
连续运转时间
h
停机惰走时间
s
启动时刻
检查项目
设计值/
允许值
实测值
运行记录时刻
一
段
入
口
流量,Nm3/h
压力,MPa
温度,℃
出口压力ຫໍສະໝຸດ MPa温度,℃轴承
温度
℃
前轴承
后轴承
止推轴承
振动速度(振动幅度)
mm/s
(μm)
前
轴
承
水平
入口
F0606_设备单机试车记录
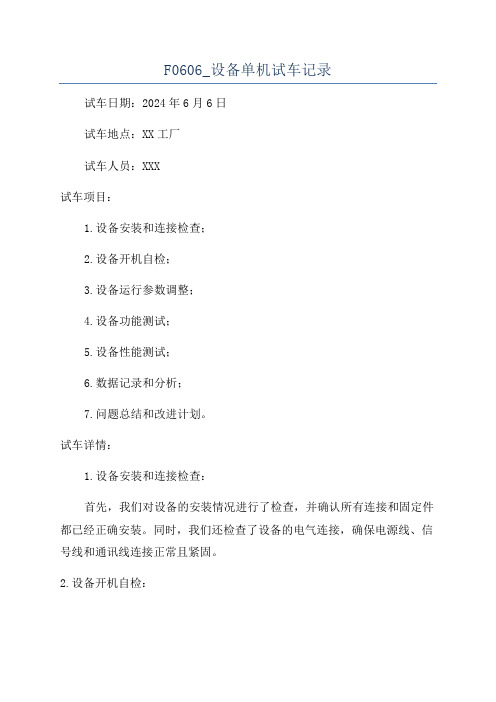
F0606_设备单机试车记录试车日期:2024年6月6日试车地点:XX工厂试车人员:XXX试车项目:1.设备安装和连接检查;2.设备开机自检;3.设备运行参数调整;4.设备功能测试;5.设备性能测试;6.数据记录和分析;7.问题总结和改进计划。
试车详情:1.设备安装和连接检查:首先,我们对设备的安装情况进行了检查,并确认所有连接和固定件都已经正确安装。
同时,我们还检查了设备的电气连接,确保电源线、信号线和通讯线连接正常且紧固。
2.设备开机自检:接着,我们按照说明书的操作流程,打开设备的电源开关,观察设备是否能正常开机。
同时,我们也留意了设备开机时是否有异常声响或异味。
3.设备运行参数调整:设备开机后,我们进入设备的主控系统,根据设计要求和技术参数,对设备的运行参数进行了调整。
我们调整了设备的温度、压力、转速等重要参数,以确保设备能够在设计工况下正常运行。
4.设备功能测试:在设备运行参数调整完成后,我们对设备的各项功能进行了测试。
包括设备的启停、转速调整、温度控制、压力控制等功能的测试。
通过测试,我们确认设备的各项功能正常运行,并且能够满足设计要求。
5.设备性能测试:接下来,我们对设备的性能进行了测试。
我们通过对设备的负载特性、输出功率、效率等进行测试,以验证设备的性能是否符合设计要求。
通过测试,我们确认设备的性能指标达到了设计标准,具有良好的工作性能。
6.数据记录和分析:在试车过程中,我们详细记录了设备的运行数据,包括温度、压力、转速、功率等参数的变化情况。
同时,我们还记录了设备的运行状态和异常情况。
通过对这些数据的分析,我们可以了解设备的运行情况,判断设备是否存在问题,并进行问题定位和解决。
7.问题总结和改进计划:最后,我们对试车过程中出现的问题进行了总结,并提出了改进计划。
我们发现在试车过程中,设备温度上升过快,可能是散热系统设计不够理想所致,建议增加散热面积或改进散热结构。
此外,设备的一些操作界面设计不够友好,操作不够方便,建议对界面进行改进,提高用户体验。
水泵设备单机试车记录
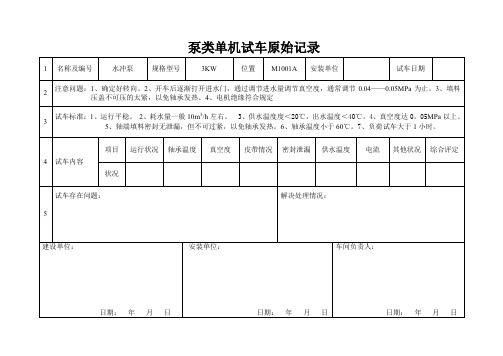
泵类单机试车原始记录
泵类单机试车原始记录
泵类单机试车原始记录
泵类单机试车原始记录
泵类单机试车原始记录
泵类单机试车原始记录
泵类单机试车原始记录
泵类单机试车原始记录
泵类单机试车原始记录
泵类单机试车原始记录
泵类单机试车原始记录
泵类单机试车原始记录
泵类单机试车原始记录
泵类单机试车原始记录
泵类单机试车原始记录
泵类单机试车原始记录
泵类单机试车原始记录
泵类单机试车原始记录
泵类单机试车原始记录
泵类单机试车原始记录
泵类单机试车原始记录
泵类单机试车原始记录
泵类单机试车原始记录
泵类单机试车原始记录
泵类单机试车原始记录
泵类单机试车原始记录
泵类单机试车原始记录
泵类单机试车原始记录
泵类单机试车原始记录
泵类单机试车原始记录
泵类单机试车原始记录
泵类单机试车原始记录
泵类单机试车原始记录
泵类单机试车原始记录
泵类单机试车原始记录
泵类单机试车原始记录
泵类单机试车原始记录
泵类单机试车原始记录
泵类单机试车原始记录
泵类单机试车原始记录
泵类单机试车原始记录
泵类单机试车原始记录
泵类单机试车原始记录
泵类单机试车原始记录
泵类单机试车原始记录
泵类单机试车原始记录
泵类单机试车原始记录
泵类单机试车原始记录
泵类单机试车原始记录
泵类单机试车原始记录。
机器单机试车记录3503-J306
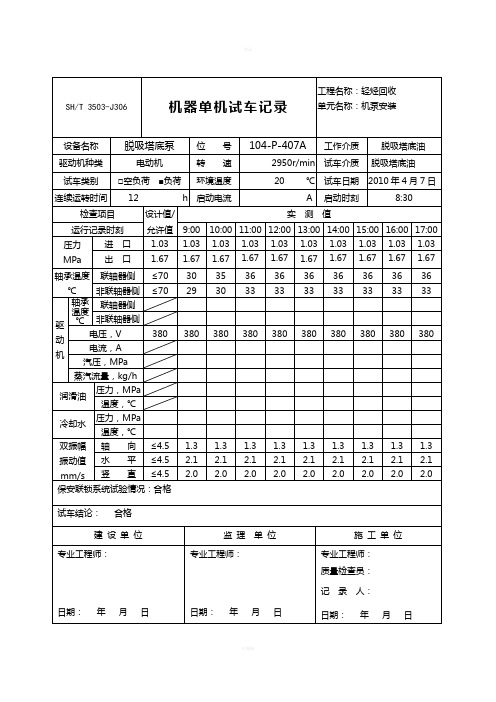
≤4.5
0.6
0.6
0.6
0.6
0.6
0.6
0.6
0.6
0.6
保安联锁系统试验情况:合格
试车结论: 合格
建设单位
监理 单位
施 工 单 位
专业工程师:
日期: 年 月 日
专业工程师:
日期: 年 月 日
专业工程师:
质量检查员:
记 录 人:
日期: 年 月 日
SH/T 3503-J306
机器单机试车记录
冷却水
压力,MPa
温度,℃
≤45
双振幅
振动值
mm/s
轴 向
≤4.5
0.3
0.45
0.45
0.5
0.5
0.5
0.5
0.5
0.5
水 平
≤4.5
0.2
0.3
0.3
0.3
0.3
0.3
0.3
0.3
0.3
竖 直
≤4.5
0.3
0.3
0.3
0.3
0.3
0.3
0.4
0.4
0.4
保安联锁系统试验情况:合格
试车结论: 合格
1.4
1.4
1.4
1.4
轴承温度
℃
联轴器侧
≤70
30
32
33
34
34
34
34
35
35
非联轴器侧
≤70
32
35
40
41
43
43
43
43
43
驱动机
轴承温度
℃
联轴器侧
非联轴器侧
往复式压缩机试车记录

冷 入口压力,MPa 却 入口温度,℃ 水 出口温度,℃
双振幅 轴 向
振动值 水 平
m
竖直
轴承 温度
℃
前轴承 后轴承 止推轴承
入 压力,MPa 口 温度,℃
一 出 压力,MPa 口 温度,℃
段 填料函温度,℃
建设单位 专业工程师:
监理单位 专业工程师:
施工单位
专业工程师: 质量检查员: 记 录 人:
设备制造厂 现场代表:
日期: 年 月 日 日期: 年 月 日 日期: 年 月 日 日期: 年 月 日
Байду номын сангаас
SH/T3503-J308-2
往复式压缩机 试车记录(二)
工程名称: 单元名称:
检查项目
运行记录时刻
入 压力,MPa 口 温度,℃
出 压力,MPa 口 温度,℃ 段 填料函温度,℃
设计值/ 允许值
实测值
SH/T3503-J308-1
往复式压缩机 试车记录(一)
工程名称: 单元名称:
设备名称
设备型号
设备位号
试车类别 □空负荷 □负荷 工作介质
试车介质
驱动机种类
转速
r/min 环境温度
℃
连续运转时间
h 试车日期
年 月 日 启动时刻
检查项目 运行记录时刻
设计值/ 允许值
实测值
润 入口压力,MPa 滑 入口温度,℃ 油 出口温度,℃
入 压力,MPa 口 温度,℃
出 压力,MPa 口 温度,℃ 段 填料函温度,℃
入 压力,MPa 口 温度,℃ 出 压力,MPa 口 温度,℃ 段 填料函温度,℃
保安联锁系统试验情况:
试车后检查情况:
试车结论:
3503-J311电动机试车记录
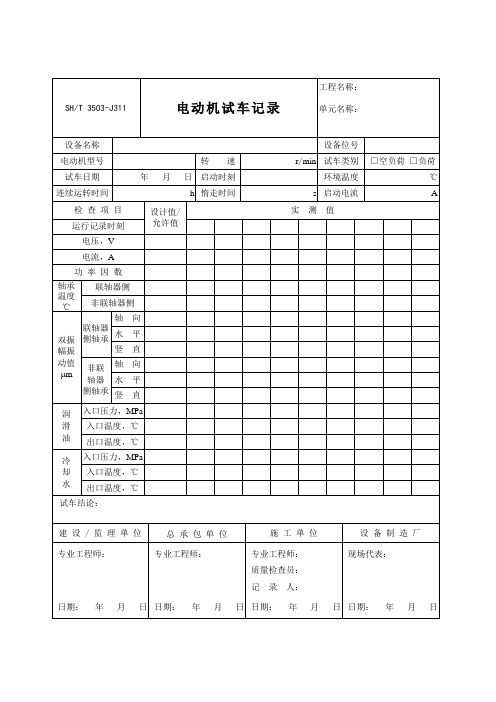
日期:年 月 日
现场代表:
日期:年 月 日
SH/T3503-J311
电动机试车记录
工程名称:
单元名称:
设备名称
设备位号
电动机型号
转速
r/min
试车类别
□空负荷□负荷
试车日期
年 月 日
启动时刻
环境温度
℃
连续运转时间
h
惰走时间
s
启动电流
A
检 查 项 目
设计值/
允许值
实 测 值
运行记录时刻
电压,V
电流,A
功率因数
轴承
温度
℃
联轴器侧
非联轴器侧
双振
幅振
动值
m
联轴器侧轴承
轴向
水平
竖直
非联
轴器
侧轴承
轴向
水平
竖直
润
滑
油
入口压力,MPa
入口温度,℃
出口温度,℃
冷
却
水
入口压力,MPa
入口温度,℃
出口温度,℃
试车结论:
建设/监理单位
总 承 业工程师:
日期:年 月 日
专业工程师:
日期:年 月 日
专业工程师:
质量检查员:
设备名称设备位号电动机型号转速rmin试车类别空负荷负荷试车日期年月日启动时刻环境温度连续运转时间h惰走时间s启动电流a检查项目设计值允许值实测值运行记录时刻电压v电流a功率因数轴承温度联轴器侧非联轴器侧双振幅振动值?m联轴器侧轴承轴向水平竖直非联轴器侧轴承轴向水平竖直润滑油入口压力mpa入口温度出口温度冷却水入口压力mpa入口温度出口温度试车结论
3503-J309-离心式压缩机试车记录1
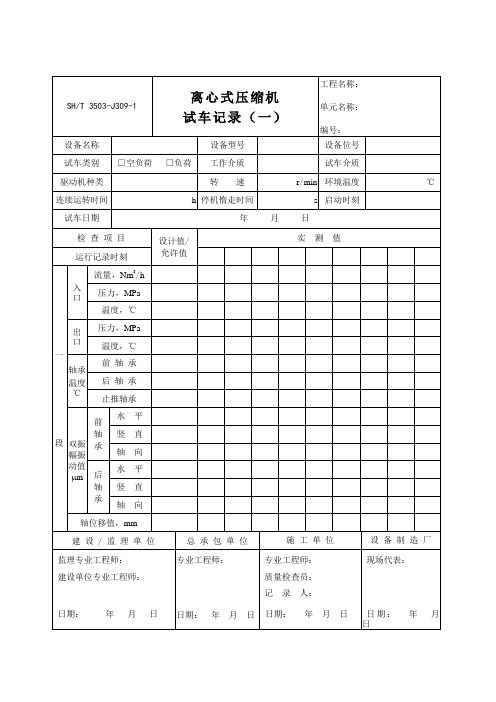
离心式压缩机
试车记录(一)
工程名称:
单元名称:
编号:
设备名称
设备型号
设备位号
试车类别
□空负荷□负荷
工作介质
试车介质
驱动机种类
转速
r/min
环境温度
℃
连续运转时间
h
停机惰走时间
s
启动时刻
试车日期
年月日
检查项目
设计值/
允许值
实测值
运行记录时刻
一
段
入
口
流量,Nm3/h
压力,MPa
温度,℃
出
口
压力,MPa
温度,℃
轴承
温度
℃
前轴承
后轴承
止推轴承
双振
幅振
动值
m
前
轴
承
水平
竖直
轴向
后
轴
承
水平
竖直
轴向
轴位移值,mm
建设/监理单位
总承包单位
施工单位Biblioteka 设备制造厂监理专业工程师:
建设单位专业工程师:
日期:年月日
专业工程师:
日期:年月日
专业工程师:
质量检查员:
记录人:
日期:年月日
现场代表:
日期:年月日
往复式压缩机试车记录

出口温度,℃
冷
却
水
入口压力,MPa
入口温度,℃
出口温度,℃
双振幅
振动值
m
轴 向
水 平
竖 直
轴承
温度
℃
前轴承
后 轴 承
止推轴承
一
段
入
口
压力,MPa
温度,℃
出
口
压力,MPa
温度,℃
填料函温度,℃
建设/监理单位
总 承 包 单位
施 工 单 位
设 备 制 造 厂
专业工程师:
日期: 年 月 日
专业工程师:
SH/T3503-J308-1
往复式压缩机
试车记录(一)
工程名称:xxxLNG项目
单元名称:
设备名称
设备型号
设备位号
试车类别
□空负荷 □负荷工作介质来自试车介质驱动机种类
转 速
r/min
环境温度
℃
连续运转时间
h
试车日期
年月日
启动时刻
检 查 项 目
设计值/
允许值
实 测 值
运行记录时刻
润
滑
油
入口压力,MPa
段
入口
压力,MPa
温度,℃
出口
压力,MPa
温度,℃
填料函温度,℃
段
入口
压力,MPa
温度,℃
出口
压力,MPa
温度,℃
填料函温度,℃
保安联锁系统试验情况:
试车后检查情况:
试车结论:
日期: 年 月 日
专业工程师:
质量检查员:
记 录 人:
日期: 年 月 日
搅拌类设备单机试车原始记录
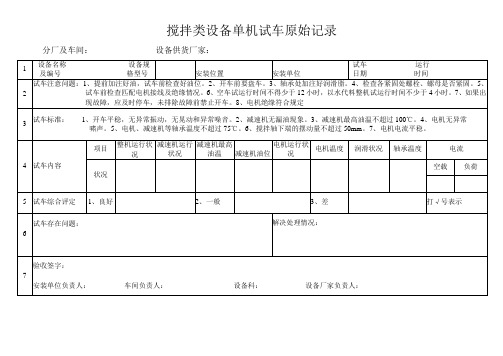
分厂及车间:设备供货厂家:
1
设备名称设备规
及编号格型号
安装位置
安装单位
试车运行
日期时间
2
试车注意问题:1、提前加注好油,试车前检查好油位。2、开车前要盘车。3、轴承处加注好润滑脂。4、检查各紧固处螺栓、螺母是否紧固。5、试车前检查匹配电机接线及绝缘情况。6、空车试运行时间不得少于12小时,以水代料整机试运行时间不少于4小时。7、如果出现故障,应及时停车,未排除故障前禁止开车。8、电机绝缘符合规定
电机温度
润滑
空载
负荷
5
试车综合评定
1、良好
2、一般
3、差
打√号表示
6
试车存在问题:
解决处理情况:
7
验收签字:
安装单位负责人:车间负责人:设备科:设备厂家负责人:
3
试车标准:1、开车平稳,无异常振动,无晃动和异常噪音。2、减速机无漏油现象。3、减速机最高油温不超过100℃。4、电机无异常
啸声。5、电机、减速机等轴承温度不超过75℃。6、搅拌轴下端的摆动量不超过50mm。7、电机电流平稳。
4
试车内容
项目
整机运行状况
减速机运行状况
减速机最高油温
减速机油位
电机运行状况
单体机械试车记录

油名及标号
注油日期
电机轴承座
二、试运转检测情况
试车类别
试车日期
启动时间
启动电流
连续运转时间
环境温度
介质
无负荷
运行
时间
轴承温度(0C)
电机温度(0C)
介质温度(0C)
电压
(V)
电流
(A)
振动(双振幅)
前
后
前
后
进
出
电机
机体
0-1
1-2
2-3
3-4
试验后检查情况及质量评定:经小时无负荷运转,振动温度均正常,符合规范要求。
机械设备单体试车记录
工程名称
江西铜业集团公司100kt/a铅冶炼工程
分部分项
工程名称
鼓风机安装工业设备安装
设备名称
设备位号
设备型号
类型
能力
转速
驱动种类
规格型号
功率
转速
电压
额定电流
一、运转前的检查
1、电动机检查情况:
2、设备本体检查情况:
3、冷却系统检查情况:
4、系统油洗或油压情况检查情况:
5、所注润滑脂或润滑油:
建设单位
监理单位
施工单位
现场代表:
年月日
现场代表:
年月日
施工技术负责人:
质量检查员:
施工班(组)长:
Байду номын сангаас年月日
W0628_水泵试车记录

W0628_水泵试车记录试车日期:2024年6月28日试车地点:XX水泵站一、试车目的:1.验证新安装的水泵设备是否正常运行;2.测试水泵的性能参数,如流量、扬程等;3.检查水泵运行过程中是否存在故障。
二、试车准备:1.水泵设备清洁干净,无异物;2.检查水泵管道连接是否紧固,并确保阀门处于正常启闭状态;3.检查水泵电源线,确认良好接地以及正确连接;4.检查水泵的润滑油水位是否正常。
三、试车步骤:1.启动水泵设备,检查电动机运行是否正常,是否有异常声音和振动;2.检测水泵吸水,确保吸水管道和滤网无阻塞;3.检查水泵吸水出水口,确保出水无堵塞;4.开启水泵出口阀门,逐步调整水泵的启动频率,观察水泵的运行情况;5.根据试验要求,逐渐调整水泵的流量和扬程,记录下不同工况下的水泵性能参数;6.观察水泵运行时的各项指标,如电流、电压、温度等,确保在正常范围内;7.检查水泵设备是否存在漏水、异味等现象;8.观察水泵设备的振动情况,确保在正常范围内;9.完成试验后,及时关闭水泵设备,确保所有阀门关闭。
四、试车结果记录:1.试车时间:XX时XX分;2.试车过程中的各项参数记录,包括电流、电压、流量、扬程、温度等;3.试车过程中的异常情况记录,包括漏水、异味、振动异常等;4.试车过程中的操作记录,包括启动时间、启动频率调整等。
五、试车结论:根据试车结果记录,可以得出以下结论:1.水泵设备运行正常,各项参数在正常范围内;2.所有阀门连接紧固,无漏水现象;3.试车过程中未发现异常振动和异味。
六、试车存在问题及改进措施:1.其中一工况下,流量参数略低于预期值,需要进一步调整;2.试车过程中润滑油需加注,以确保设备正常运行;3.加强试车前的准备工作,确保设备的清洁和正常连接;4.检修水泵设备过程中,发现的相关问题及时整改。
化灰机单机试车原始记录

试车内容
项目减速机温度Biblioteka 轴承温度筒体中心线
减速机密封
齿圈与齿轮啮合情况
四托轮中心线等高
运行状况
电流
状况
空载
负荷
5
试车综合评定
1、良好
2,—般
3、差
打J号表示
6
试车存在问题:
解决处理情况:
7
验收签字:
安装单位负责人:车间负责人:设备科:设备厂家负责人:
化灰机单机试车原始记录
分厂及车间:设备供货厂家:
1
设备名称及设备规格安装安装试车
编号型号位置单位日期
2
试车注意问题:1、掌握操作规程、开停车程序。2、减速机放出防锈油,根据要求加好润滑油。4,提前确定好转向。5、检查减速机透气孔。6、电机绝缘符合规定
3
试车标准:1、减速机无泄漏。2、减速机和轴承温度小于75C。3、设备运行平稳。4、电流平稳。5、筒体中心线标高允许误差正负8mm6、设备安装角度为O度,以地基水平线为设备安装基准。7、四托轮的中心线应等高,其允差为正负1.5mm8、齿圈与齿轮啮合时,应保证其接触点数沿齿高不小于40%,沿齿长度不小于50%
平盘过滤机单机试车原始记录

轴承温度
仪表
减速机密封
运行状况
真空度
调频状况
电流
状况(空
载)
空载
负荷
状况
(带料)
5ቤተ መጻሕፍቲ ባይዱ
试车综合评定
1、良好
2、一般
3、差
打J号表Z5
6
试车存在问题:
解决处理情况:
7
验收签字:
安装单位负责人:车间负责人:设备科:设备厂家负责人:
平盘过滤机单机试车原始记录
分厂及车间:设备供货厂家:
1
设备名称及编号
设备规
格型号
安装位置
安装单位
试车日期
2
试车注意问题:1、掌握操作规程、开停车程序。2、转盘电机、卸料螺旋电机、进料泵电机要调试好联锁。3、转盘变步避免电机发热。4、保证系统真空度-20KP〜-60KP。5、滤盘平面最高点与卸料螺旋保证间隙4-6mm。(油,加好润滑油。7、盘面水平误差正负Imm8、电机绝缘符合规定
页要大于15Hz,以入减速机放出防锈
3
试车标准:1、平盘、卸料螺旋减速机无泄漏。2、各减速机温度小于65C,轴承温度小于65C。3、过滤机圆盘不磨不抗。4、电流平
稳。5、设备运行平稳。6、托轮、挡轮与转盘转轨调节合理,受力均匀。7、空载试车大于8小时,负荷连续试车72小时以上。
4
试车内容
项目
减速机温度
分馏塔联动试车记录
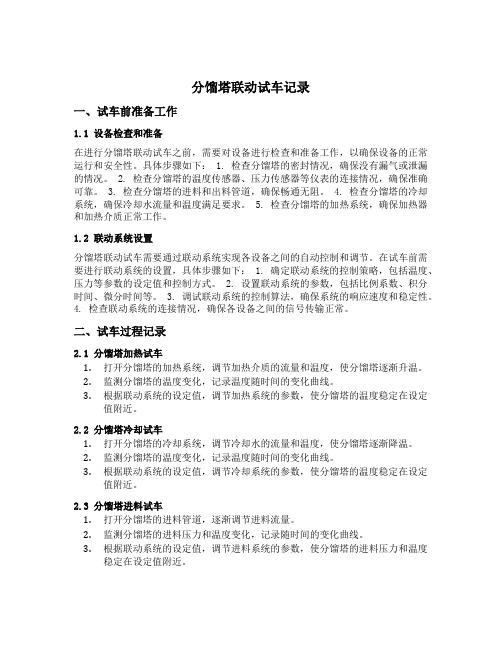
分馏塔联动试车记录一、试车前准备工作1.1 设备检查和准备在进行分馏塔联动试车之前,需要对设备进行检查和准备工作,以确保设备的正常运行和安全性。
具体步骤如下: 1. 检查分馏塔的密封情况,确保没有漏气或泄漏的情况。
2. 检查分馏塔的温度传感器、压力传感器等仪表的连接情况,确保准确可靠。
3. 检查分馏塔的进料和出料管道,确保畅通无阻。
4. 检查分馏塔的冷却系统,确保冷却水流量和温度满足要求。
5. 检查分馏塔的加热系统,确保加热器和加热介质正常工作。
1.2 联动系统设置分馏塔联动试车需要通过联动系统实现各设备之间的自动控制和调节。
在试车前需要进行联动系统的设置,具体步骤如下: 1. 确定联动系统的控制策略,包括温度、压力等参数的设定值和控制方式。
2. 设置联动系统的参数,包括比例系数、积分时间、微分时间等。
3. 调试联动系统的控制算法,确保系统的响应速度和稳定性。
4. 检查联动系统的连接情况,确保各设备之间的信号传输正常。
二、试车过程记录2.1 分馏塔加热试车1.打开分馏塔的加热系统,调节加热介质的流量和温度,使分馏塔逐渐升温。
2.监测分馏塔的温度变化,记录温度随时间的变化曲线。
3.根据联动系统的设定值,调节加热系统的参数,使分馏塔的温度稳定在设定值附近。
2.2 分馏塔冷却试车1.打开分馏塔的冷却系统,调节冷却水的流量和温度,使分馏塔逐渐降温。
2.监测分馏塔的温度变化,记录温度随时间的变化曲线。
3.根据联动系统的设定值,调节冷却系统的参数,使分馏塔的温度稳定在设定值附近。
2.3 分馏塔进料试车1.打开分馏塔的进料管道,逐渐调节进料流量。
2.监测分馏塔的进料压力和温度变化,记录随时间的变化曲线。
3.根据联动系统的设定值,调节进料系统的参数,使分馏塔的进料压力和温度稳定在设定值附近。
2.4 分馏塔出料试车1.打开分馏塔的出料管道,逐渐调节出料流量。
2.监测分馏塔的出料压力和温度变化,记录随时间的变化曲线。