6金属化与多层互连-unprotected
合集下载
金属化和多层互连

TiSi2 和 CoSi2的自对准工艺:
• 溅射剥离从衬底表面去除原生氧化层 • Ti 或 Co 沉积 • 退火形成金属硅化物 • Ti 或 Co 不与SiO2反应,金属硅化物在硅和Ti 或Co接
触处形成 • 去除Ti 或 Co • 选择性再次退火以增强电导率
多晶硅/硅化物复合栅结构
TiSi 2
多晶硅栅极
从中可以看出,采用低电阻率的互连材料和 低介电常数的介质材料可以有效降低互连系统的 延迟时间。
铜及低K介质
铜及低K介质的优势:
铜的电阻率低,可以极大降低互连引线电阻;
Cu
1.7 mWcm
Al
2.65 mWcm
铜的抗电迁移能力强,没有应力迁移,可靠性强; 低K介质,减少了分布电容;
所以,采用铜及低K介质可以进一步减小引线宽度和 厚度,提高集成电路的密度。
铜及低K介质
Cu互连工艺中的关键技术: Cu的沉积技术 低K介质材料的选择和沉积 势垒层材料的选择和沉积技术 Cu的CMP平整化技术 大马士革(镶嵌式)结构的互连工艺 可靠性问题
深亚微米技术的发展:
90nm、45nm线宽 300mm(12寸)晶圆
铜及低K介质
系统集成(SOC)
nn+
SiO2
nn+
退火产生金属硅化物
nn+
SiO2
nn+
湿法腐蚀Ti薄膜
自对准栅技术加离子注入可以大幅减小掺杂横向 效应引起的覆盖电容,提高工作频率。
多晶硅栅取代Al栅,由于栅与衬底Si的功函数差 减少,可以使PMOS的开启电压VT绝对值下降1.21.4V左右。
开启电压VTX降低后,器件充放电幅度降低,时间 缩短,从而也可提高工作频率。
• 溅射剥离从衬底表面去除原生氧化层 • Ti 或 Co 沉积 • 退火形成金属硅化物 • Ti 或 Co 不与SiO2反应,金属硅化物在硅和Ti 或Co接
触处形成 • 去除Ti 或 Co • 选择性再次退火以增强电导率
多晶硅/硅化物复合栅结构
TiSi 2
多晶硅栅极
从中可以看出,采用低电阻率的互连材料和 低介电常数的介质材料可以有效降低互连系统的 延迟时间。
铜及低K介质
铜及低K介质的优势:
铜的电阻率低,可以极大降低互连引线电阻;
Cu
1.7 mWcm
Al
2.65 mWcm
铜的抗电迁移能力强,没有应力迁移,可靠性强; 低K介质,减少了分布电容;
所以,采用铜及低K介质可以进一步减小引线宽度和 厚度,提高集成电路的密度。
铜及低K介质
Cu互连工艺中的关键技术: Cu的沉积技术 低K介质材料的选择和沉积 势垒层材料的选择和沉积技术 Cu的CMP平整化技术 大马士革(镶嵌式)结构的互连工艺 可靠性问题
深亚微米技术的发展:
90nm、45nm线宽 300mm(12寸)晶圆
铜及低K介质
系统集成(SOC)
nn+
SiO2
nn+
退火产生金属硅化物
nn+
SiO2
nn+
湿法腐蚀Ti薄膜
自对准栅技术加离子注入可以大幅减小掺杂横向 效应引起的覆盖电容,提高工作频率。
多晶硅栅取代Al栅,由于栅与衬底Si的功函数差 减少,可以使PMOS的开启电压VT绝对值下降1.21.4V左右。
开启电压VTX降低后,器件充放电幅度降低,时间 缩短,从而也可提高工作频率。
《金属化与多层互连》课件

金属化与多层互连的应用领域
半导体制造:用于制造集成电路和芯片
医疗设备制造:用于制造医疗设备,如CT、 MRI等
电子设备制造:用于制造电子设备,如手 机、电脑等
汽车制造:用于制造汽车电子设备,如车 载导航、车载娱乐系统等
航空航天:用于制造航天器和卫星等
通信设备制造:用于制造通信设备,如基 站、路由器等
金属化与多层互连的材料性能要求
导电性:良好 的导电性能, 保证信号传输 的稳定性和速
度
热稳定性:在 机械强度:足 高温环境下保 够的机械强度, 持良好的性能, 保证电路的稳 防止电路损坏 定性和可靠性
化学稳定性: 良好的化学稳 定性,防止电 路受到腐蚀和
氧化
成本:合理的 成本,保证产 品的市场竞争
金属化与多层互连的解决方案
采用先进的金属化工艺,如电镀、溅射等,提高金属化层的质量 优化多层互连的设计,如减小层间距、增加层数等,提高互连的密度和可靠性 采用先进的封装技术,如晶圆级封装、系统级封装等,提高封装的集成度和可靠性 采用先进的测试技术,如X射线、光学显微镜等,提高测试的准确性和效率
金属化与多层互连的发展历程
1960年代:金属化技术开始应用于集成 电路制造
1990年代:金属化技术进一步发展,多 层互连技术成为集成电路制造的主流技术
1970年代:多层互连技术开始出现,提 高了集成电路的密度和性能
2000年代:金属化技术不断创新,多层 互连技术逐渐向高密度、高性能方向发展
1980年代:金属化技术逐渐成熟,多层 互连技术得到广泛应用
沉积:在硅片上沉积金属或 绝缘材料
电镀:在硅片上沉积金属层
热处理:提高金属层的导电 性和稳定性
金属化与多层互连的工艺流程细节
金属化和多层互连
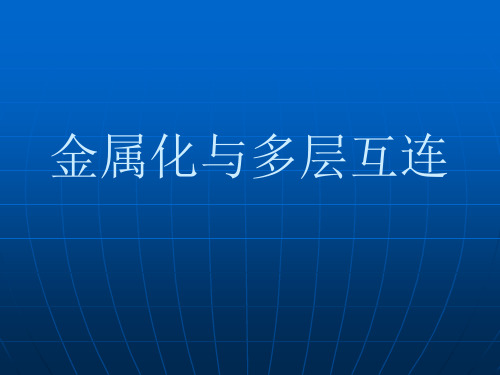
当金属与半导体之间的载流子输运以隧道 穿透为主时,Rc与半导体的掺杂浓度N及 金-半接触的势垒高度qVb 有下面的关系
qVb Rc exp N
qVb在数值上等于金属费米能级上的电子 进入半导体所需的能量。 结论:要获得低接触电阻的金-半接触, 必须减小金-半接触的势垒高度及提高半 导体的掺杂浓度
CoSi2
Ta 或 TaN Cu
W
W
PSG STI n+
+ + n+ p p USG P型井區 N型井區 P型磊晶層 P型晶圓
铜及低K介质
低K介质材料的沉积与刻蚀: 沉积工艺: (1)旋涂工艺:工艺简单,缺陷密度较低,产率高,易于 平整化,不使用危险气体 (2)CVD工艺:与IC工艺兼容性好 刻蚀要求: (1)工艺兼容性好 (2)对刻蚀停止层材料选择性高 (3)能形成垂直图形 (4)对Cu无刻蚀和腐蚀 (5)刻蚀的残留物易于清除
鋁
p+ N型矽
SiO2
鋁
p+
鋁
Al/Si接触的改善
合 金 化 : 采 用 含 少 量 Si 的 Al-Si 合 金 ( 一 般 为 1% ) , 由于合金中已存在足量的 Si ,可以抑制底 层Si的扩散,防止“尖锲”现象。 在 300oC 以上,硅就以一定比例熔于铝中, 在此温度,恒温足够时间,就可在Al-Si界面形成 一层很薄的 Al-Si 合金。 Al 通过 Al-Si 合金和接触 孔下的重掺杂半导体接触,形成欧姆接触
铜及低K介质
势垒层材料: 包括介质势垒层和导电势垒层 介质势垒层材料:SiN、SiC等新材料 主要功能:和介质层形成多层结构,防止介质 在工艺过程或环境中吸潮而影响性能。 导电势垒层:WN、TiN、Ta、TaN等 主要功能:防止Cu扩散、改善Cu的附着性、 作为CMP和刻蚀停止层、作为保护层。
集成电路工艺基础——09_金属化及多层互连
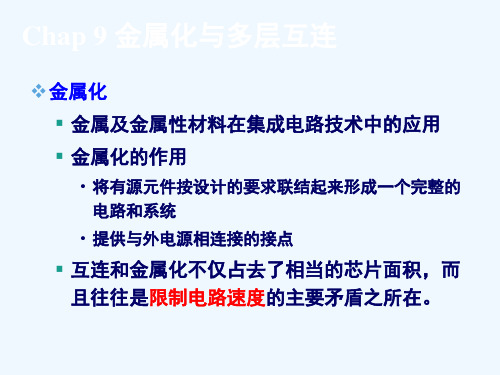
▪ 薄氧(尖楔较浅) ▪ 厚氧(尖楔较深)
❖ 衬底晶向
▪ 〈111〉:横向扩展 、双极集成电路 ▪ 〈100〉:垂直扩展 、pn结短路 、MOS集成电路
(尖楔现象严重)
Al/Si接触的改进
❖Al/Si接触的改进方法: ▪ 铝-硅合金金属化引线 ▪ 铝-掺杂多晶硅双层金属化结构 ▪ 铝-阻挡层结构
铝-硅合金金属化引线-第1种解决方案
铝硅互溶
❖Si在Al中的扩散系数
▪ 在一定的退火温度下,退火时间为ta时,Si原 子的扩散距离为
LSi Dta
其中D为扩散系数
Al与SiO2的反应
❖Al与SiO2的反应 4Al+ 3SiO2 → 3Si+2Al2O3
▪ 吃掉Si表面的SiO2 ,降低接触电阻 ▪ 改善Al引线与下面SiO2 的黏附性
改进电迁移的方法-第2种方法
❖ 铝-铜合金和铝-硅-铜合金 ▪ Al- Si( 1%~2%)-Cu(4%) • 杂质在铝晶粒晶界分凝,可以降低铝原子在 铝晶界的扩散系数,从而使MTF提高一个数 量级。 ▪ 缺点:
• 增大了电阻率 • 不易刻蚀、易受Cl2腐蚀
改进电迁移的方法-第3种方法
❖ 三层夹心结构 ▪ 可以在两次铝之间增加大约500A厚的过渡金属 层。这三层金属通过400℃退火1小时后,在两 层铝之间形成金属间化合物,可以防止空洞穿 越整个金属引线,也可以降低铝在晶粒间界的 扩散系数,使MTF提高2~3个数量级。
❖ 铝硅互溶 ❖ Al与SiO2的反应
铝硅互溶
❖铝硅相图
▪ 相图表示两种组分与温度的关系
• Al-Si系具有低共熔特性 • Al-Si系的共熔温度为577℃,相应的组分配比为Si占
11.3%,Al占88.7% • 淀积Al时Si衬底的温度不得高于577 ℃
❖ 衬底晶向
▪ 〈111〉:横向扩展 、双极集成电路 ▪ 〈100〉:垂直扩展 、pn结短路 、MOS集成电路
(尖楔现象严重)
Al/Si接触的改进
❖Al/Si接触的改进方法: ▪ 铝-硅合金金属化引线 ▪ 铝-掺杂多晶硅双层金属化结构 ▪ 铝-阻挡层结构
铝-硅合金金属化引线-第1种解决方案
铝硅互溶
❖Si在Al中的扩散系数
▪ 在一定的退火温度下,退火时间为ta时,Si原 子的扩散距离为
LSi Dta
其中D为扩散系数
Al与SiO2的反应
❖Al与SiO2的反应 4Al+ 3SiO2 → 3Si+2Al2O3
▪ 吃掉Si表面的SiO2 ,降低接触电阻 ▪ 改善Al引线与下面SiO2 的黏附性
改进电迁移的方法-第2种方法
❖ 铝-铜合金和铝-硅-铜合金 ▪ Al- Si( 1%~2%)-Cu(4%) • 杂质在铝晶粒晶界分凝,可以降低铝原子在 铝晶界的扩散系数,从而使MTF提高一个数 量级。 ▪ 缺点:
• 增大了电阻率 • 不易刻蚀、易受Cl2腐蚀
改进电迁移的方法-第3种方法
❖ 三层夹心结构 ▪ 可以在两次铝之间增加大约500A厚的过渡金属 层。这三层金属通过400℃退火1小时后,在两 层铝之间形成金属间化合物,可以防止空洞穿 越整个金属引线,也可以降低铝在晶粒间界的 扩散系数,使MTF提高2~3个数量级。
❖ 铝硅互溶 ❖ Al与SiO2的反应
铝硅互溶
❖铝硅相图
▪ 相图表示两种组分与温度的关系
• Al-Si系具有低共熔特性 • Al-Si系的共熔温度为577℃,相应的组分配比为Si占
11.3%,Al占88.7% • 淀积Al时Si衬底的温度不得高于577 ℃
第九章金属化与多层连接1

9.2.4 Al/Si接触的改进
1 Al-Si合金金属化引线
采用铝硅合金代替纯铝作为接触和互连材料, 防止尖楔现象。
问题:出现分凝现象。即,在较高合金退火温 度时熔解在铝中的硅,在冷却过程中又从铝中析出。 该现象产生一个个硅单晶的结瘤。影响器件的 可靠性,有可能导致互连线短路。
2 铝-掺杂多晶硅双层金属化结构
金属势垒层材料(阻挡层金属)选择要求:保形的通 孔和沟槽淀积性能;好的势垒性能;低的通孔电阻;与 铜有好的黏附性;与铜的CMP工艺兼容。如:WN、TiN
9.3.5 金属Cu的淀积技术
采用大马士革(镶嵌)工艺进行Cu布线。 过程与上述相似。
9.3.6 低K介质和Cu互连集成技术中的可靠性问题
可靠性问题涉及:电迁移、应力迁移、热循 环稳定性、介电应力、热导率。
2 中值失效时间
表征电迁移现象的物理量是互连引线的中值失效 时间MTF(media time to failure),即50%互连引线 失效时间,其值正比于引线截面积,反比于质量输 运率
3 改进电迁移的方法
1) 结构的影响和“竹状”结构的选择
MTF随着铝线宽度的减小和长度的增加而降
低。
“竹状”铝引线 结构,组成多晶 体的晶粒从下而 上贯穿引线截面, 晶粒间界垂直于 电流的方向,所 以晶粒间界的扩 散不起作用。
第九章 金属化与多层互连
9.1 引言
金属化:金属及金属材料在集成电路技术中的应用。
根据金属在集成电路中的功能划分,可以分为三类:
互连材料——将同一芯片的各个独立的元器件连接成蚀,好的抗电迁移 特性。
互连连线是金属化工艺的主要组成部分;
大部分使用铜铝合金;
R ( l ) /(wtm )
金属化与多层互连

②Si在Al中扩散:Si在Al薄膜中的扩散比 在晶体Al中大40倍。
③Al与SiO2反应:3SiO2+4Al→3Si+2Al2O3
好处:降低Al/Si欧姆接触电阻;
改善Al与SiO2的粘附性。
9.2.3 Al/Si接触的尖楔现象
图9.3 Al-Si接触引线工艺
T=500℃,t=30min., A=16μm2,W=5μm, d=1μm,消耗Si层厚度
①在低K介质层上刻蚀出Cu互连线用的沟槽; ②CVD淀积一层薄的金属势垒层:防止Cu的扩散; ③溅射淀积Cu的籽晶层:电镀或化学镀Cu需要; ④沟槽和通孔淀积Cu:电镀或化学镀; ⑤400℃下退火; ⑥Cu的CMP。
铜金属化(Copper Metallization)
9.4 多晶硅及硅化物
多晶硅:CMOS多晶硅 栅、局域互连线;
RC常数:表征互连线延迟,即 RC l 。
t m t ox ρ-互连线电阻率,l-互连线长度,ε-介质层介电常数
①低ρ的互连线:Cu,ρ=1.72μΩcm; (Al,ρ=2.82μΩcm)
②低K (ε)的介质材料: ε<3.5
Cu互连工艺的关键
①Cu的淀积:不能采用传统的Al互连布线工艺。 (没有适合Cu的传统刻蚀工艺)
Z=0.35μm。 (相当于VLSI的结深) ∵Si非均匀消耗, ∴实际上,A*<<A,即
Z*>>Z,故 Al形成尖楔
尖楔现象
机理:Si在Al中的溶解度及快速 扩散,使Al像尖钉一样楔进Si衬 底;
深度:超过1μm; 特点: <111>衬底:横向扩展 <100> 衬底:纵向扩展 MOS器件突出。 改善:Al中加1wt%-4wt%的过
微电子工艺之金属化
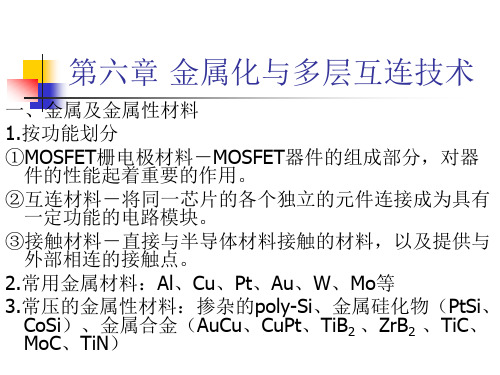
四、 金属化的实现
③类型 直流溅射 磁控溅射 RF溅射 离子束溅射和反应金属
图8-5 平板型磁控溅射源示意图
由于在阴极面上存在极强的磁场,电子受洛伦茲力作用而被限制 在阴影区内,沿着类似摆线的轨迹运动(虚线),于是增加了电子 与气体的碰撞次数,增加了等离子体的密度,提高了溅射速率。
四、 金属化的实现
③改进电迁移的方法
a.“竹状”结构:晶粒间界垂直电流方向。
b.Al-Cu(Al-Si-Cu)合金:Cu等杂质的分凝降低Al在晶粒间界的扩 散系数。
c.三层夹心结构:两层Al之间加一层约500Å的金属过渡层。
六、 多层布线
多层布线是高集成度的必然。 第一层:基本单元布线; 第二层:单元之间电路布线; 介质:SiO2 , P S G ,Al2O3 ,聚铣亚铵
散阻挡层。
第六章 金属化与多层互连技术
三、欧姆接触
1.定义:金属-相对于半导体主体或串联电阻,当半导体 接触处的接触电阻可以忽略不计时,称为欧姆接触。
2.三个重要的参数:
①功函数:费米能级与真空能级的能量差.
金属功函数- WM;半导体功函数- WS。
②肖特基势垒高度Φb: Φb=WM- ,
③接触电阻RC:RC=(dV/dJ)v=0
CMooSCi、)T、iN金)属合金(AuCu、CuPt、TiB2 、ZrB2 、TiC、
第六章 金属化与多层互连技术
二、集成电路对金属化的基本要求 1.对P+、N+或poly-Si形成低阻欧姆接触,即硅/金属接触
电阻越小越好; 2.提供低阻互连线,从而提高集成电路的速度; 3.抗电迁移; 4.良好的附着性; 5.耐腐蚀; 6.易于淀积和刻蚀; 7.易键合; 8.层与层之间绝缘要好,即相互不扩散,即要求有一个扩
(s)第九章 金属化与多层互连

9.2.3 Al/Si接触中的尖楔现象
图9.3 Al-Si接触引线工艺 T=500℃,t=30min., A=4.4μm2,W=5μm, d=1μm,则 消耗Si层厚度Z=0.3μm。 ∵Si非均匀消耗, ∴实际上,A*<<A,即 Z*>>Z,故 Al形成尖楔
尖楔现象
机理: Si在Al中的溶解度及 快速扩散。 特点: <111>衬底:横向扩展 <100> 衬底:纵向扩展 MOS器件突出。
9.3 Cu及低K介质
问题的引出: 互连线延迟随器件尺寸的缩小 而增加;亚微米尺寸,互连延迟 大于栅(门)延迟。 l 2 RC 如何降低RC常数——表征互连线延迟,即 tmtox ρ-互连线电阻率,l-互连线长度,ε-介质层介电常数 tm-引线厚度,tox-互连线下介质层厚度。 ①低ρ的互连线:Cu,ρ=1.72μΩcm; (Al,ρ=2.82μΩcm) ②低K (ε)的介质材料: ε<3.5
9.4.3 多晶硅互连及其局限性
l 2 ox 互连延迟时间常数RC:RC Rs tox
Rs、 l- -互连线方块电阻和长度, εox、tox-多晶硅互连线下面介质层的介电常数和厚度; 局限性:电阻率过高;
9.5 VLSI与多层互连
多层互连的提出: 互连线面积占主要; 时延常数RC占主要。 9.5.1 多层互连对VLSI的意义 1.使集成密度大大增加,集成度提高; 2.使单位芯片面积上可用的互连线面积大大增加; 3.降低互连延迟: ①有效降低了互连线长度; ②使所有互连线接近于平均长度; ③降低连线总电容随连线间隔缩小而增加的效应; ④减少了连线间的干扰,提高了频率; ⑤加快了整个系统工作速度。 4. 降低成本 (目前Cu互连可高达10层)
第九章 金属化与多层互连
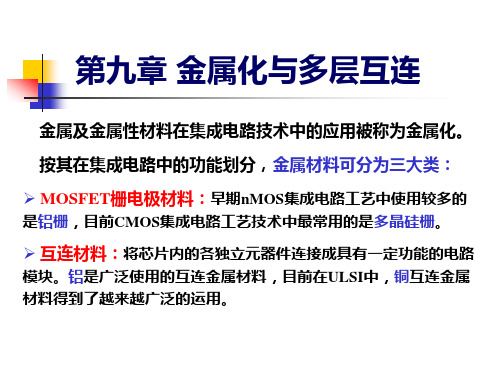
原子受到电子风力的驱动,产生了从阴极向阳极的定向扩散,即发生了金 属原子的电迁移。在相反方向将有质量耗尽,产生空位的聚合。
电迁移现象的结果:在一个方向形成空洞,使互连引线 断裂开路,而在另一个方向则由于铝原子的堆积而形成 小丘,造成光刻的困难和多层布线之间短路,从而使整 个集成电路失效。 金属原子在薄膜中的输运过程是扩散过程,主要是沿晶界进行的。
th
Ef 1Vf
F S T2 T1
Ef杨氏模量,Vf泊松系数,αF 与αS为薄膜和衬底的热膨胀系数, T1为工作 时温度,T2为生长(或退火)温度。 可见减小热应力,最重要的是选择热膨胀系数相近的材料。
应力的存在对互连体系可靠性产生严重影响,应力可导致互连线出现空
及化学反应特性在互连材料的选取以及结构设计时都是必须考虑的问题。
9.2、铝在集成电路技术中的应用
铝是一种经常被采用的金属互连材料,主要优点是:
在室温下的电阻率仅为2.7μΩ·cm; 与n+、p+硅或多晶硅的欧姆接触电阻可低至10-6Ω/cm2;
与硅和磷硅玻璃的附着性很好;
经过短时间热处理后,与SiO2、Si3N4等绝缘层的黏附性很好; 易于淀积和刻蚀。
铝-掺杂多晶硅双层金属化结构
对于Al和重磷或重砷掺杂的多晶硅接触,这种重组现象不存在。
可能是因为杂质磷(砷)在多晶硅晶粒间界分凝,使晶粒间界硅原子 的自由能减小,降低了这些硅原子在铝中的溶解度。 因此可以在淀积铝薄膜之前,先淀积一层重磷或重砷掺杂的多晶 硅薄膜,构成Al-重磷(砷)掺杂多晶硅双层金属化结构。
9.2.1、金属铝膜的制备方法
铝应用于集成电路中的互连引线,主要是采用溅射方法制备,淀积速 率快、厚度均匀、台阶覆盖能力强。
电迁移现象的结果:在一个方向形成空洞,使互连引线 断裂开路,而在另一个方向则由于铝原子的堆积而形成 小丘,造成光刻的困难和多层布线之间短路,从而使整 个集成电路失效。 金属原子在薄膜中的输运过程是扩散过程,主要是沿晶界进行的。
th
Ef 1Vf
F S T2 T1
Ef杨氏模量,Vf泊松系数,αF 与αS为薄膜和衬底的热膨胀系数, T1为工作 时温度,T2为生长(或退火)温度。 可见减小热应力,最重要的是选择热膨胀系数相近的材料。
应力的存在对互连体系可靠性产生严重影响,应力可导致互连线出现空
及化学反应特性在互连材料的选取以及结构设计时都是必须考虑的问题。
9.2、铝在集成电路技术中的应用
铝是一种经常被采用的金属互连材料,主要优点是:
在室温下的电阻率仅为2.7μΩ·cm; 与n+、p+硅或多晶硅的欧姆接触电阻可低至10-6Ω/cm2;
与硅和磷硅玻璃的附着性很好;
经过短时间热处理后,与SiO2、Si3N4等绝缘层的黏附性很好; 易于淀积和刻蚀。
铝-掺杂多晶硅双层金属化结构
对于Al和重磷或重砷掺杂的多晶硅接触,这种重组现象不存在。
可能是因为杂质磷(砷)在多晶硅晶粒间界分凝,使晶粒间界硅原子 的自由能减小,降低了这些硅原子在铝中的溶解度。 因此可以在淀积铝薄膜之前,先淀积一层重磷或重砷掺杂的多晶 硅薄膜,构成Al-重磷(砷)掺杂多晶硅双层金属化结构。
9.2.1、金属铝膜的制备方法
铝应用于集成电路中的互连引线,主要是采用溅射方法制备,淀积速 率快、厚度均匀、台阶覆盖能力强。
金属化与多层互连解析

集成电路对金属化材料特性的要求
1.能与硅基形成低阻的欧姆接触. 2.长时期在较高电流密度负荷下,金属材料的抗电迁移
性能要好. 3.与绝缘体有良好的附着性. 4.耐腐蚀 5.易于淀积和刻蚀 6.易于键合,而且键合点能长期工作 7.多层互连要求层与层间绝缘性好,层间不发生互相渗
透和扩散.
(2)溅射:溅射需要在真空系统中充入一定的惰性气体Ar, 这样在高压电场的作用下,由于气体放电形成离子,这些离 子在强电场作用下被加速,然后轰击靶材料,使其原子逸出 并被溅射到晶片上,形成金属膜。 采用这种方法可以淀积各种合金和难熔技术薄层,利用磁控 溅射所需要的电压比电子束蒸发要小一个数量级,产生的辐 射较小,磁控溅射是目前集成电路工艺中广泛采用的形成技
电阻) 机械特性 总的应力体现为两种情形:张应力和压应力 总应力造成的因素: 固有应力(由淀积生长条件决定,如晶格失配,结构,缺
陷,表面效应...) 热应力(衬底和薄膜热膨胀系数不同,生长温度与使用温
度不同)
金属材料的常规特性
危害:对互连体系可靠性产生严重影响,导致互连线出现 空洞,互连材料的电迁移
晶格结构和外延生长特性的影响
外延生长的单晶膜具有理想的特性. 影响单晶膜生长的因素: ✓ 薄膜和衬底材料晶格结构匹配程度 ✓ 界面附着稳定程度 ✓ 薄膜晶化生长稳定性 ✓ 淀积条件 ✓ 材料纯净度 ✓ 后续工艺处理的影响
晶格常数失配因子
薄膜和衬底材料晶格结构匹配程度
量化表征:晶格常数失配因子( )
Al与SiO2的反应
4Al+ 3SiO2
3Si+2Al2O3
吃掉Si表面的SiO2 ,降低接触电阻
改善与SiO2 的黏附性
尖楔现象
原因: 当铝硅形成接触孔时,由于硅在铝中有可观溶解度,在接触
硅集成电路工艺——金属化与多层互连
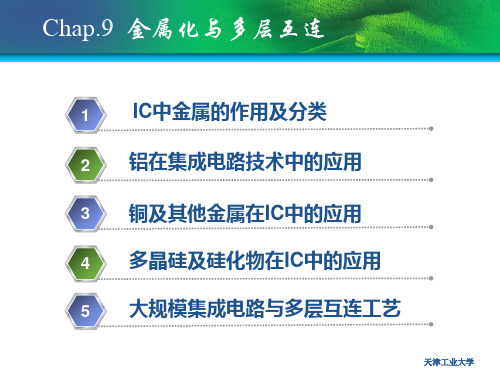
天津工业大学
金属硅化物的特点和制备方法
难熔金属硅化物的特点: 难熔金属硅化物的特点: 特点 低的、类金属的电阻率 低的、 高温稳定性好 抗电迁移能力强 与硅衬底接触电阻小, 与硅衬底接触电阻小,附 着性好( 着性好(TiSi2, WSi2, CoSi2) 主要作为接触材料, 主要作为接触材料,也可 作为栅极和互连材料 硅化物的淀积方法: 硅化物的淀积方法: 淀积方法 共溅射方法 共蒸发方法 溅射或蒸发单层难熔金属 于多晶硅衬底上再退火, 于多晶硅衬底上再退火, 发生反应生成硅化物 合金靶溅射 CVD淀积硅化物 淀积硅化物
Si
Al SiO2 Z Si
天津工业大学
Al/Si接触的改进
Al-Si合金金属化引线(铝中加入1%~4%的硅,同时 合金金属化引线(铝中加入 的硅, 合金金属化引线 的硅 存在硅的分凝问题) 存在硅的分凝问题) 铝-掺杂多晶硅双层金属化结构(多晶硅提供溶解 掺杂多晶硅双层金属化结构( 于铝中而消耗的硅) 于铝中而消耗的硅) 作为欧姆接触层, 铝-阻挡层结构(PtSi, CoSi作为欧姆接触层, 阻挡层结构( 作为欧姆接触层 TiN,TaN作为阻挡层) 作为阻挡层) 作为阻挡层 减小铝的体积( 阻挡层 阻挡层/Al-Si-Cu三层夹心结构) 三层夹心结构) 减小铝的体积(Al/阻挡层 三层夹心结构 降低硅在铝中的扩散系数(铝中掺氧或Al2O3) 降低硅在铝中的扩散系数(铝中掺氧或
天津工业大学
互连引线的延迟时间: 互连引线的延迟时间: RC常数: 常数: 常数 R=(ρl)/(ωtm) C=(εωl)/tox RC=(ρεl2)/(tm tox)
Cu作为互连材料的工艺流 作为互连材料的工艺流 程: ——Dual Damascene 双大马士革工艺
金属化与多层互连
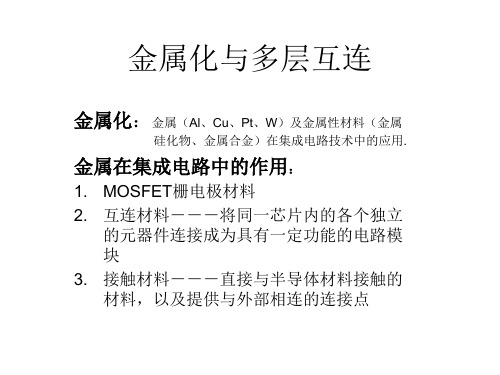
改进电迁移的方法
• 结构的影响和“竹状”结构的选择 晶粒大小对MTF有影响,多晶铝的优选晶向也会影响MTF值。 电子束蒸发的铝薄膜(晶粒的优选晶向为〈111〉晶向),其 MTF值比溅射的铝薄膜大2~3倍(溅射的铝薄膜更加无序)。 MTF随铝线宽度的减小和长度的增加而降低。具有“竹状”结 构的铝引线(P277图9.7),组成多晶体的晶粒从下而上贯穿 引线截面,晶粒间界垂直于电流方向,晶粒间界的扩散不起作 用,可以使MTF提高二个数量级。 MTF • Al-Cu合金和Al-Si-Cu合金 在Al中加入Cu、Ni、Cr、Mg等,这些杂质在铝晶界分凝降低 了Al原子在Al晶界的扩散系数,提高MTF一个数量级,但电阻 率增加。 • 三层夹心结构 在二层Al薄膜之间增加一个约500A的过渡金属层(Ti、Hf、 Cr、Ta等),400℃退火1小时后在二层铝引线间形成金属化 合物,是很好的铝扩散阻挡层,减小旅原子的迁移率,防止空 洞和小丘的形成。可以提高MTF2~3个数量级。
互连引线的延迟时间
• 随着器件尺寸的减小,降低互连线延迟时间十分 重要。表征互连引线延迟时间的物理量是RC常数, R为引线的电阻、C为互连系统的电容 • R与互连材料电阻率ρ、连线长度L和截面积wtm有 关(w为引线宽度,tm为引线的厚度)。R= (ρL) / ( wtm) • 互连系统的电容与互连引线几何尺寸及互连引线 下面介质层的介电常数ε和厚度tax有关。C=(εwL)/ tax • RC= (ρεL2)/(tm tax) • 从上式可以看出,采用低电阻率的互连材料及低 介电常数的介质材料可以有效地降低互连系统的 延迟时间。
电学特性
电学特性:电阻率、电阻率的温度系数 (TCR)、功函数、与半导体接触的肖特 基势垒高度(不同材料的电学特性参见P342附录6) 对接触金属材料和栅电极材料,其功函数、 与半导体接触的肖特基势垒高度、接触电 阻是非常重要的参数。
金属化与多层互连(1)

Al-Si合金退火:相当可观的Si
溶解到Al中。 编辑ppt
15
9.3 Al的性质及现象
9.2.2 Al/Si接触的物理现象
①Al/Si互溶:Al在Si中的溶解度非常低; Si在Al中的溶解度相对较高:
②Si在Al中扩散:Si在Al薄膜中的扩散比在晶体Al中 大40倍。
③Al与SiO2反应:3SiO2+4Al→3Si+2Al2O3 好处:降低Al/Si欧姆接触电阻;
改善Al与SiO2的粘附性。
编辑ppt
16
9.3 Al的性质及现象
9.2.3 Al/Si接触的尖楔现象
图9.3 Al-Si接触引线工艺
T=500℃,t=30min.,
A=16μm2,W=5μm,
d=1μm,消耗Si层厚度
Z=0.35μm。
(相当于VLSI的结深)
∵Si非均匀消耗,
∴实际上,A*<<A,即Z*>>Z,故
集成电路制造技术
第九章 金属化与多层互连
西安电子科技大学
微电子学院
戴显英 2012年8月
编辑ppt
1
第九章 金属化与多层互连
金属化:金属及金属性材料在IC中的应用。 金属化材料分类:(按功能划分) ①MOSFET栅电极材料-MOSFET器件的组成部分; ②互连材料-将各个独立的元件连接成为具有一
定功能的电路模块。 ③接触材料-直接与半导体材料接触的材料,
高光刻分辨率
编辑ppt
10
9.2 金属化材料及应用
5、钨W
• 接触孔和通孔中的金属塞
• 接触孔变得越来越小和越窄 • PVD Al合金: 台阶覆盖性差,产生空洞 • CVD W: 出色的台阶覆盖性和空隙填充能力 • CVD W:更高电阻率: 8.0-12 mW-cm
《金属化与多层互连》课件

刻蚀
去除多余的金属,形成所需的电路和元件结 构。
沉积
通过物理或化学方法在基材表面形成金属薄 膜。
检测与修复
检查金属化质量,对缺陷进行修复。
金属薄膜制备技术
物理气相沉积(PVD)
利用物理方法将金属原子或分子沉积 在基材表面。
化学气相沉积(CVD)
利用化学反应将金属化合物沉积在基 材面,再通过热分解得到金属薄膜 。
THANKS
节能减排
优化生产工艺,降低能耗和减少废弃 物排放,实现绿色制造和可持续发展 。
智能制造与数字化转型
智能监控与检测
利用传感器、机器视觉等技术实现生产过程的实时监控和检测,提高产品质量和生产效率。
数字化转型
推动金属化与多层互连产业的数字化转型,实现生产数据的实时采集、分析和优化,提升企业核心竞争力。
感谢观看
《金属化与多层互连 》PPT课件
• 金属化与多层互连概述 • 金属化材料与技术 • 多层互连结构与设计 • 金属化与多层互连的挑战与解决
方案 • 金属化与多层互连的未来发展
目录
01
金属化与多层互连概述
定义与特点
定义
金属化与多层互连是指在电子设备中,通过金属材料和多层互联结构实现电子 元器件之间的连接。
电性能问题
总结词
金属化与多层互连的电性能问题主要表现在信号传输延迟、噪声干扰和电磁干扰等方面。
详细描述
随着电子设备工作频率的不断提高,信号传输延迟、噪声干扰和电磁干扰等问题愈发突出。需要优化 金属化与多层互连的结构和材料,以减小信号传输延迟、降低噪声和电磁干扰,提高电子设备的性能 。
制程技术挑战
总结词
金属化与多层互连的制程技术挑战主要表现在高精度加工、高密度集成以及异种材料连 接等方面。
去除多余的金属,形成所需的电路和元件结 构。
沉积
通过物理或化学方法在基材表面形成金属薄 膜。
检测与修复
检查金属化质量,对缺陷进行修复。
金属薄膜制备技术
物理气相沉积(PVD)
利用物理方法将金属原子或分子沉积 在基材表面。
化学气相沉积(CVD)
利用化学反应将金属化合物沉积在基 材面,再通过热分解得到金属薄膜 。
THANKS
节能减排
优化生产工艺,降低能耗和减少废弃 物排放,实现绿色制造和可持续发展 。
智能制造与数字化转型
智能监控与检测
利用传感器、机器视觉等技术实现生产过程的实时监控和检测,提高产品质量和生产效率。
数字化转型
推动金属化与多层互连产业的数字化转型,实现生产数据的实时采集、分析和优化,提升企业核心竞争力。
感谢观看
《金属化与多层互连 》PPT课件
• 金属化与多层互连概述 • 金属化材料与技术 • 多层互连结构与设计 • 金属化与多层互连的挑战与解决
方案 • 金属化与多层互连的未来发展
目录
01
金属化与多层互连概述
定义与特点
定义
金属化与多层互连是指在电子设备中,通过金属材料和多层互联结构实现电子 元器件之间的连接。
电性能问题
总结词
金属化与多层互连的电性能问题主要表现在信号传输延迟、噪声干扰和电磁干扰等方面。
详细描述
随着电子设备工作频率的不断提高,信号传输延迟、噪声干扰和电磁干扰等问题愈发突出。需要优化 金属化与多层互连的结构和材料,以减小信号传输延迟、降低噪声和电磁干扰,提高电子设备的性能 。
制程技术挑战
总结词
金属化与多层互连的制程技术挑战主要表现在高精度加工、高密度集成以及异种材料连 接等方面。
金属化与多层互连

微电子工艺 电信学院微电子教研室
用于铜互连结构的阻挡层:提高欧姆接触可靠性更有效 的方法是用阻挡层金属化,这种方法可消除诸如浅结材 料刻蚀或结尖刺的问题。阻挡层金属是淀积金属或金属 塞,作用是阻止层上下的材料互相混合(见下图)。其 厚度对0.25µm工艺来说为100nm;对0.35µm工艺来说 为400~600nm。
金属铝
在半导体制造业中,最早的互连金属是铝, 目前在VLSI以下的工艺中仍然是最普通的互连金 属。在21世纪制造高性能IC工艺中,铜互连金属 有望取代铝。然而,由于基本工艺中铝互连金属 的普遍性, 所以选择铝金属化的背景是有益的。 铝在20℃时具有2.65µΩ-cm的低电阻率,比 铜、金及银的电阻率稍高。然而铜和银都比较容 易腐蚀,在硅和二氧化硅中有高的扩散率,这些 都阻止它们被用于半导体制造。另一方面,铝能 够很容易和二氧化硅反应,加热形成氧化铝( AL2O3 ),这促进了氧化硅和铝之间的附着。还 有铝容易淀积在硅片上。基于这些原因。铝仍然 作为首先的金属应用于金属化。
电信学院微电子教研室
微电子工艺
引 言
芯片金属化是应用化学或物理处理方法在芯片 上淀积导电金属膜的过程。这一过程与介质的淀积 紧密相关,金属线在IC电路中传输信号,介质层则 保证信号不受邻近金属线的影响。 金属化对不同金属连接有专门的术语名称。互 连(interconnect)意指由导电材料(铝、多晶硅或 铜)制成的连线将信号传输到芯片的不同部分。互 连也被用做芯片上器件和整个封装之间普通的金属 连接。接触(contact)意指硅芯片内的器件与第一 层金属之间在硅表面的连接。通孔(via)是穿过 各种介质层从某一金属层到毗邻的另一金属层之间 形成电通路的开口。“填充薄膜”是指用金属薄膜填 充通孔,以便在两金属层之间形成电连接。
用于铜互连结构的阻挡层:提高欧姆接触可靠性更有效 的方法是用阻挡层金属化,这种方法可消除诸如浅结材 料刻蚀或结尖刺的问题。阻挡层金属是淀积金属或金属 塞,作用是阻止层上下的材料互相混合(见下图)。其 厚度对0.25µm工艺来说为100nm;对0.35µm工艺来说 为400~600nm。
金属铝
在半导体制造业中,最早的互连金属是铝, 目前在VLSI以下的工艺中仍然是最普通的互连金 属。在21世纪制造高性能IC工艺中,铜互连金属 有望取代铝。然而,由于基本工艺中铝互连金属 的普遍性, 所以选择铝金属化的背景是有益的。 铝在20℃时具有2.65µΩ-cm的低电阻率,比 铜、金及银的电阻率稍高。然而铜和银都比较容 易腐蚀,在硅和二氧化硅中有高的扩散率,这些 都阻止它们被用于半导体制造。另一方面,铝能 够很容易和二氧化硅反应,加热形成氧化铝( AL2O3 ),这促进了氧化硅和铝之间的附着。还 有铝容易淀积在硅片上。基于这些原因。铝仍然 作为首先的金属应用于金属化。
电信学院微电子教研室
微电子工艺
引 言
芯片金属化是应用化学或物理处理方法在芯片 上淀积导电金属膜的过程。这一过程与介质的淀积 紧密相关,金属线在IC电路中传输信号,介质层则 保证信号不受邻近金属线的影响。 金属化对不同金属连接有专门的术语名称。互 连(interconnect)意指由导电材料(铝、多晶硅或 铜)制成的连线将信号传输到芯片的不同部分。互 连也被用做芯片上器件和整个封装之间普通的金属 连接。接触(contact)意指硅芯片内的器件与第一 层金属之间在硅表面的连接。通孔(via)是穿过 各种介质层从某一金属层到毗邻的另一金属层之间 形成电通路的开口。“填充薄膜”是指用金属薄膜填 充通孔,以便在两金属层之间形成电连接。
- 1、下载文档前请自行甄别文档内容的完整性,平台不提供额外的编辑、内容补充、找答案等附加服务。
- 2、"仅部分预览"的文档,不可在线预览部分如存在完整性等问题,可反馈申请退款(可完整预览的文档不适用该条件!)。
- 3、如文档侵犯您的权益,请联系客服反馈,我们会尽快为您处理(人工客服工作时间:9:00-18:30)。
Jincheng Zhang
23
导电薄膜
4、钛Ti:硅化钛、氮化钛
TiN:阻挡层,防止W扩散 TiN:粘合层,帮助W与SiO2 表面粘合在一起 TiN:防反射涂层ARC(Antireflection coating),防止反射 提高光刻分辨率
Jincheng Zhang
24
导电薄膜
5、钨W
• 接触孔和通孔中的金属塞 • 接触孔变得越来越小和越窄 • PVD Al合金: 台阶覆盖性差,产生空洞 • CVD W: 出色的台阶覆盖性和空隙填充能力 • CVD W:更高电阻率: 8.0~12 μΩ−cm PVD Al合金 (2.9 ~3.3 μΩ−cm) • W只用作局部互连和金属塞
9
互连材料-Interconnection
互连在金属化工艺中占有主要地位 Al-Cu合金最为常用 W塞(80s和90s) Ti:焊接层 TiN:阻挡、黏附层 未来互连金属--Cu
Jincheng Zhang
10
铜金属化(Copper Metallization)
Jincheng Zhang
11
栅电极和金半接触电极
Jincheng Zhang
41
CMP (Chemical Mechanical Polishing/ planarization )--化学机械抛光
多层金属互连 介质层的平坦化 焦深要求平坦表面获得高分辨率 粗糙的介质表面会引起金属化问题
Jincheng Zhang
42
钨CMP
W:形成金属塞 W CVD填充接触孔和通孔,覆盖整个圆片表面 需要从表面去除钨薄膜 以前:F基等离子体刻蚀 钨CMP替代刻蚀
Jincheng Zhang
4
圆片工艺流程(Wafer Process Flow)
Jincheng Zhang
5
金属化
定义:金属及金属性材料在集成电路技术中的应用 应用: -栅电极材料:MOSFET和MISFET器件的栅极 -金半接触电极材料:直接与半导体材料接触,提供与 外部相连的连接点 -互连材料:连接芯片内各独立元器件
Jincheng Zhang
13
硅化物
2、硅化物
-电阻率比多晶硅更低, -常用TiSi2, WSi2和 CoSi2
Байду номын сангаас
TiSi2 and CoSi2
– Ar离子溅射去除本征氧化层(Ti或Co不与SiO2反应) – 淀积Ti或Co – 退火形成硅化物 – 湿法剥离去除未反应的Ti或Co – 二次退火(可选)提高电导率
Jincheng Zhang
36
Cobalt Silicide: Process
Pre-deposition argon sputtering clean Cobalt sputtering deposition First anneal, 600 °C Co + Si → CoSi Strip Unreacted cobalt Second anneal, 700 °C Co + Si → CoSi2
Jincheng Zhang
14
自对准形成硅化钛
Jincheng Zhang
15
导电薄膜
3、铝(Al)
最常用的金属 导电性第四好的金属 – 铝 2.65 μΩ−cm – 金 2.2 μΩ−cm – 银 1.6 μΩ−cm – 铜 1.7 μΩ−cm 1970s中期以前用作栅电极金属
Jincheng Zhang
Jincheng Zhang
6
常用的金属及金属性材料
常用的金属材料: Al、Cu、Pt、Au、W、Mo、Ti、Co、Ta等 常用的金属性材料: 掺杂的poly-Si; 金属硅化物--PtSi、TiSi、CoSi2、WSi2; 金属合金--AlSi、AlCu、AuCu、CuPt、 TiB2 、 SiGe 、 ZrB2 、 TiC、 MoC、TiN。
Jincheng Zhang
40
金属化总结
金属化主要应用: 互连 CVD (W, TiN, Ti)和PVD (Al-Cu, Ti, TiN) Al-Cu合金在互连材料中占有主要地位 Al-Cu PVD需要超高真空 W 作为接触孔和互连通孔的金属塞 Ti 作为不同金属间的焊接层 TiN: 阻挡层、黏附层和防反射涂层 未来: Cu代替Al-Cu,Ta/TaN代替Ti/TiN
16
Al-Si合金
在源/漏区Al与Si直接接触 Al/Si互溶:Al在Si中的溶解度非常低; Si在Al中的溶解度相对较高(~1% ) Si在Al中扩散:Si在Al薄膜中的扩散比在晶体Al中大40倍 Al/Si接触的尖楔现象: Si在Al中的溶解度及快速扩散 PN结穿刺 – Al刺穿过掺杂PN结,使源/漏与衬底短路 400 ℃ 热退火在Si-Al界面形成Si-Al合金
29
Jincheng Zhang
Cu互连及低K介质
问题的引出: 互连线延迟随器件 尺寸的缩小而增加; 亚微米尺寸,互连延 迟大于栅(门)延迟
Jincheng Zhang
30
Cu互连及低K介质
如何降低互连延迟: ρεl RC常数:表征互连线延迟,即 RC = 。 t m t ox ρ-互连线电阻率,l-互连线长度,ε-介质层介电常数 ①低ρ的互连线:Cu,ρ=1.72μΩcm; (Al,ρ=2.82μΩcm) ②低ε(K)的介质材料: ε<3.5
Jincheng Zhang
7
集成电路对金属化的基本要求
1. 形成低阻欧姆接触; 2. 提供低阻互连线; 3. 抗电迁移; 4. 良好的附着性; 5. 耐腐蚀; 6. 易于淀积和刻蚀; 7. 易键合; 8. 层与层之间绝缘要好。
Jincheng Zhang
8
CMOS标准金属化
Jincheng Zhang
少量铜与铝形成的合金将大大提供Al对电迁移的抵 抗, 铜作为Al晶粒间的粘合剂,防止Al晶粒因电子轰 击而迁移 Al-Cu (0.5%) 最常用 使用Al-Si-Cu 合金
Jincheng Zhang
22
铝合金的淀积
PVD(物理气相淀积) –溅射Sputtering –蒸发Evaporation:热蒸发和电子束蒸发 CVD(化学气相淀积) – 二甲基氢化物 [DMAH, Al(CH3)2H] – 热处理
集成电路工艺基础
6、金属化与多层互连(薄膜淀 积、介质)
微电子学院 戴显英 2010 年9月
课程内容
1、引言 2、硅片制备与高温工艺(拉单晶、氧化、扩散) 3、薄膜生长(PVD和CVD) 4、掺杂技术(扩散、注入) 5、光刻与刻蚀工艺(曝光、刻蚀)
6、金属化与多层互连(薄膜淀积、介 质)
7、CMOS集成电路工艺流程 8、双极集成电路和BiCMOS的工艺集成
31
Jincheng Zhang
Copper Deposition
PVD of seed layer ECP or CVD bulk layer Thermal anneal after bulk copper deposition – increase the grain size – improving conductivity
Jincheng Zhang
17
尖楔现象
Jincheng Zhang
18
PN结穿刺
(Junction spike)
Jincheng Zhang
19
电迁移
Electromigration
电迁移:大电流密度下发生质量(离子/晶粒)输运。 现象:在阳极端堆积形成小丘或须晶,造成电极间短路; 在阴极端形成空洞,导致电极开路。 机理:在大电流密度作用下,导电电子与铝离子/晶粒发生 动量交换,使金属离子/晶粒沿电子流方向迁移。
33
Cu互连工艺流程
Jincheng Zhang
34
多层Cu互连
Jincheng Zhang
35
导电薄膜
7、Tantalum钽 • Barrier layer • Prevent copper diffusion • Sputtering deposition 8、Cobalt钴 • Mainly used for silicide (CoSi2). • Normally deposited with a sputtering process • Cobalt silicide grain size: ~ 0.2 μm • Can’t be used for 0.18 um gate
25
Jincheng Zhang
接触工艺的演变
Jincheng Zhang
26
W钨 CVD
W原料:WF6 与SiH4反应形成成核层 W淀积:与H2反应 需要TiN层与氧化物黏附
Jincheng Zhang
27
W Plug and TiN/Ti Barrier/Adhesion Layer
Jincheng Zhang
本章主要内容
金属化(Metallization)
化学机械抛光(Chemical Mechanical Polishing/
Chemical Mechanical planarization )
Jincheng Zhang
3
要求
金属化的作用 三种最常用的金属及三种不同的金属化方法 Al栅及互连与多晶硅栅及互连 Cu互连及互连延迟 W塞及TiN CMP:必要性及应用
Jincheng Zhang
20
电迁移
Electromigration
电迁移使金属线变窄变薄 残留引线中电流密度更高
– 使电子轰击加剧,引起进一步Al晶粒的迁移, 甚至使金属线断裂
电迁移影响IC的可靠性
Jincheng Zhang