基于烟化炉节能途径分析
浅谈工业炉窑节能的途径

浅谈工业炉窑节能的途径摘要:目前,我国在工业现代化进程中取得了举世瞩目的成就,国家的工业生产制造能力位居世界前列,是全球少数几个拥有全部工业门类的国家,基础工业技术的提升与信息化水平的增强,也为工业炉窑的节能增效升级带来了更为有利的条件。
从当前应用实际来看,工业炉窑的节能主要是通过改进燃烧技术,提升热效率,使用先进材料,计算机智能化控制等途径来实现,文章围绕其中重点的路径做了探讨,为节能减排提出了一些意见建议。
关键词:工业炉窑 ; 节能 ; 计算机控制引言党的十八大以来,中央和国家高度重视生态文明建设,加快工业产业结构转型升级,尽快淘汰高耗能、高污染的产业,去产能、去杠杆、调结构,推动工业经济的高质量发展成为了工业现代化的一条主线。
当然在这个过程中,工业炉窑的节能减排与技术升级也在持续的推进。
当前,我国的工业炉窑节能技术路径不断的优化升级,很多关键技术取得了突破。
比如在轧钢加热炉的使用上,节能达到三成左右,均热炉超过了35%,不过与国际老牌工业强国比,一些关键指标上还有一定的差距,比如热效率方面,和国际水平50%比较还要做出更多的努力。
一、炉窑燃烧效率提升技术燃料炉主要是通过提高燃烧效率来提升其节能水平,它的燃烧过程需要符合炉窑的工艺标准,在一些指标上都有明确的要求,如温度、火焰构型、气氛等。
当前已经较为成熟和全面推广的燃烧装置包括了调焰、平焰、高速、亚速、独立预热、油气混合型烧嘴等,如果能够合理准确的利用好这些烧嘴,那么燃烧装置可以为炉窑节能5%左右。
就使用重油,且雾化水平不高的燃烧器来说,使用重油掺水乳化技术,可以大幅的提升乳化的成效,改善乳化的最后质量,在提升燃烧率的同时,还能够解决重油过度损耗与烟气污染问题。
在燃烧装置的制造工艺上,设备制造厂商需要不断的优化和改进性能检验和检测制度,确保装置的工艺规格、型号更加地标准统一,系统集中地批量化作业[1],一些配套的管路阀、风机、油泵、打火以及火焰形态监控等设施也要及时配套,以够符合工业炉窑节能要求。
燃气蒸汽锅炉的节能改造及优化策略

燃气蒸汽锅炉的节能改造及优化策略随着全球能源危机的加剧,节能减排已成为全球各个行业的共同关注点。
在工业领域,特别是在能源消耗较大的锅炉行业,通过节能改造和优化策略实现能源效益的提升是非常重要的。
本文将针对燃气蒸汽锅炉进行节能改造及优化策略的探讨,旨在提供一些解决方案和指导意见。
1. 锅炉的节能改造燃气蒸汽锅炉的节能改造可以从以下几个方面入手:1.1 烟气余热回收利用:通过安装余热回收装置,将烟气中的高温热能回收利用,供应给其他热能需求设备,如暖气、生活用水等。
这不仅可以减少能源浪费,还可以大幅度降低锅炉的燃料消耗。
1.2 烟囱和锅炉的换热效率优化:提高锅炉的换热效率是降低能源消耗的关键。
通过烟囱的改造,增加烟气与空气之间的接触面积,提高烟气的冷却效果。
此外,合理调整锅炉的运行参数,如燃烧温度、风量等,也可以进一步提高锅炉的换热效率,降低燃料的消耗量。
1.3 锅炉能量损失识别与防止:通过监测和分析锅炉运行中的各种能量损失,如烟气中的未燃烧气体、热量的辐射散失等,可以有针对性地采取措施进行防止和修复。
例如,通过优化燃烧系统,提高烟气的洁净度,减少未燃烧气体的损失。
2. 锅炉的优化策略除了节能改造,优化锅炉的运行策略也可以提高能源的利用效率。
2.1 锅炉负荷匹配优化:根据实际需求来调整锅炉的负荷,避免不必要的能源浪费。
通过合理设计和规划,可以实现多台锅炉的联合运行,达到负荷匹配的效果,提高燃料的利用率。
2.2 锅炉的智能控制系统:采用先进的控制系统,将锅炉的运行参数进行实时监测和控制,以达到最佳的运行效果。
这样可以根据锅炉的实际负荷情况和周围环境的变化来自动调整锅炉的运行状态,实现能源消耗的最小化。
2.3 锅炉的预防性维护和定期检修:定期对锅炉进行维护和检修,保持其正常运行并发现潜在问题。
及时清洗锅炉管道、压力阀等设备,清除结垢和污垢,可以保持锅炉的高效运行,避免能源浪费。
3. 锅炉运行管理除了节能改造和优化策略之外,合理的运行管理也是提高蒸汽锅炉能源效益的关键。
燃气锅炉节能降耗方案的新途径

燃气锅炉节能降耗方案的新途径燃气锅炉是现代工业生产、居民供暖和热水供应的重要设备之一。
然而,由于燃煤锅炉的高能耗和高排放,以及传统的节能降耗措施已经逐渐达到瓶颈,寻找新的途径来提高燃气锅炉的能效已经变得迫在眉睫。
本文将探讨一些新的节能降耗方案,以实现燃气锅炉的高效运行。
我们可以采用先进的燃烧技术来提高燃气锅炉的热效率。
传统锅炉的燃烧效率较低,会产生大量的烟气和热损失。
采用先进的燃烧技术,如低氮燃烧技术、风燃比调节技术和燃烧控制系统,可以有效降低燃气锅炉的烟气排放量和热损失,提高能量利用效率。
我们可以结合智能化技术来实施燃气锅炉的节能降耗方案。
智能化技术可以通过传感器和自动化控制系统实时监测锅炉的运行状态和能耗情况,并根据需求进行调节。
通过室外温度和室内温度的实时监测,自动调节燃烧器的运行模式和供热量,以达到最佳的节能效果。
智能化技术还可以进行燃气锅炉的维护管理和故障诊断,及时发现和解决潜在问题,提高设备的可靠性和使用寿命。
第三,我们可以采用余热回收技术来提高燃气锅炉的热能利用效率。
燃气锅炉在运行过程中产生大量的废热,传统锅炉无法充分利用这些热能。
利用余热回收技术,可以将废热回收利用,供给其他热能需求,如加热生活用水、加热工业过程中的水或空调系统的加热等。
通过有效的余热回收,可以减少能源消耗,提高能源利用率。
我们可以加强燃气锅炉的定期检查和维护,以确保设备的正常运行和高效工作。
定期清洗燃烧器和燃烧室,检查和更换燃烧器的零部件、附件和辅助设备,及时清除积灰和杂物,保持锅炉的良好状态。
制定合理的运行方案和能源管理策略,提供员工培训和技术支持,制定并实施有效的节能措施,提高锅炉的整体性能和能源利用效率。
燃气锅炉节能降耗方案的新途径包括采用先进的燃烧技术、结合智能化技术、利用余热回收技术和加强定期检查和维护。
通过这些方案的实施,可以提高燃气锅炉的能效和能源利用效率,减少能源消耗和环境污染,为可持续发展做出贡献。
浅析烟化炉冶炼工艺的节能措施

(1)温度和燃料的控制。烟化炉在燃烧时的温度高低会影响到炉内铅锌挥发速度快慢,在其他条件不变的情况下,铅锌的挥发速度会随着炉内温度的增高而加快。温度过高会破坏金属结构,形成不纯合金或积铁,阻碍烟化的作业进程;温度过低会降低炉渣的流动性,甚至有可能导致结炉,带来巨大的安全风险。合理温度应保持在1150~1300℃之间,控制好温度能够有效防止能源的流失。燃料中的H含量较高,所以燃烧效率自然越高越好。焦煤的挥发分约18%~26%,这样的燃料既能尽可能的产生烟化所需的热量,又不至于产生过多容易逸散的烟尘,一定程度上提高烟化炉的烟化效率,提高燃烧效率,节省了能源。
浅析烟化炉冶炼工艺的节能措施
摘要:烟化炉在铅锌厂运行中具有非常大的作用,同时其耗能也非常严重,本文对烟化炉冶炼工艺的节能措施进行了分析,仅供参考。
关键词:烟化炉;冶炼工艺;节能措施
1提高管理水平
(1)注重流程上的系统管理。抛渣也是一项可被再利用的有效资源,建立流程管理信息系统,配合计算机使用,统计好各方数据,了解能源取向与分析能源消耗,将数据用作参考,从而设法减少不必要的能源消耗;(2)重视人员培训,提高员工素质。除了最基本的技能培训,还应积极组织各种活动来提升员工的节能意识,实行奖励机制以提高员工工作积极性。在总结各种经验的基础上,完善并加强生产环节技术性,减少能源损耗,克服生产过程中所遇到的难关;(3)发挥能源管理机构的作用。规划节能方向,保证能源机构措施积极落到实处。
(2)保持合适的氧化还原压。炉渣内的铅锌氧化还原挥发贯穿烟化炉生产过程的始终,铅锌原本的深度只会在挥发中不断变小。有关铅锌氧化还原的实验表明,维持合适的氧化还原压能够控制铅锌的挥发程度。在炉内的全过程,都应保持炉内合适的氧化还原压,加硫量应控制在含铅锌量入炉渣料的20.5-1倍为宜。下面将用两种试验说明氧化还原剂应加入的剂量:第一,在烟化炉吹炼10分钟的时候加入铁矿;第二,在120分钟这一段时间内,分散均匀的加入铁矿。试验表明,前一种方法的挥发速度较快,而且能在短短的60分钟内达成120分钟的挥发效果;后一种方法,每个时段加入还原剂的量与挥发效率有比较紧密的联系,加入剂量为0.5~0.7倍时,铅锌挥发率为90%,计入氧化剂地计量占到0.8~1.0倍时,铅锌挥发效率达到95%。两者一对比后不难发现,前一种在烟化炉开始锤炼后短时间内加入铁矿的方法能够产生较大的还原压力,并且挥发速度能够达到60分钟的挥发效果与后一种方法120分钟的效果同等。在其他条件不变的情况下,明显第一种方法更加有效的节省能源,而且能够获得更强的炉床能力和更高的烟化发热效率,因此吹炼的过程应尽量保持炉内高压,以提高颅内渣料铅锌的挥发率。
烟化炉给煤装置升级改造,实现节能降耗的生产工艺实践研究
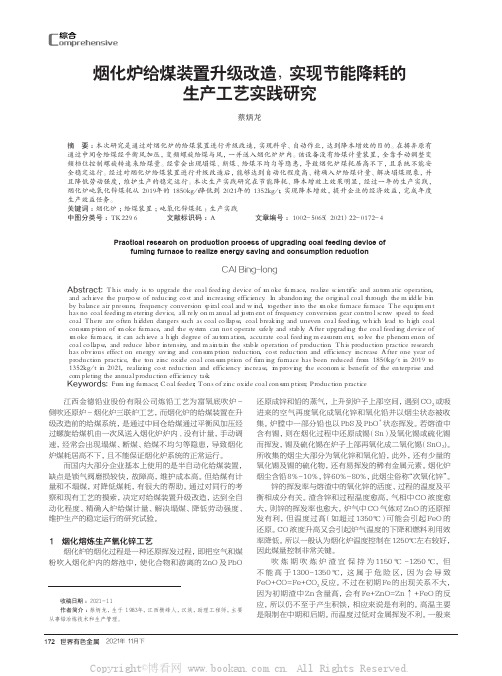
烟化炉给煤装置升级改造,实现节能降耗的生产工艺实践研究蔡炳龙(江西金德铅业股份有限公司,德兴 334200)摘 要:本次研究是通过对烟化炉的给煤装置进行升级改造,实现科学、自动作业,达到降本增效的目的。
在摒弃原有通过中间仓给煤经平衡风加压,变频螺旋给煤与风,一并送入烟化炉炉内。
该设备没有给煤计量装置,全靠手动调整变频档位控制螺旋转速来给煤量。
经常会出现塌煤、断煤、给煤不均匀等隐患,导致烟化炉煤耗居高不下,且系统不能安全稳定运行。
经过对烟化炉给煤装置进行升级改造后,能够达到自动化程度高、精确入炉给煤计量、解决塌煤现象,并且降低劳动强度,维护生产的稳定运行。
本次生产实践研究在节能降耗、降本增效上效果明显,经过一年的生产实践,烟化炉吨氧化锌煤耗从2019年的1850kg/t降低到2021年的1352kg/t,实现降本增效,提升企业的经济效益,完成年度生产效益任务。
关键词:烟化炉;给煤装置;吨氧化锌煤耗:生产实践中图分类号:TK229.6 文献标识码:A 文章编号:1002-5065(2021)22-0172-4Practical research on production process of upgrading coal feeding device offuming furnace to realize energy saving and consumption reductionCAI Bing-long(Jiangxi Jinde lead industry Co., Ltd., Jiangxi Dexing 334200)Abstract: This study is to upgrade the coal feeding device of smoke furnace, realize scientific and automatic operation, and achieve the purpose of reducing cost and increasing efficiency. In abandoning the original coal through the middle bin by balance air pressure, frequency conversion spiral coal and wind, together into the smoke furnace furnace. The equipment has no coal feeding metering device, all rely on manual adjustment of frequency conversion gear control screw speed to feed coal. There are often hidden dangers such as coal collapse, coal breaking and uneven coal feeding, which lead to high coal consumption of smoke furnace, and the system can not operate safely and stably. After upgrading the coal feeding device of smoke furnace, it can achieve a high degree of automation, accurate coal feeding measurement, solve the phenomenon of coal collapse, and reduce labor intensity, and maintain the stable operation of production. This production practice research has obvious effect on energy saving and consumption reduction, cost reduction and efficiency increase. After one year of production practice, the ton zinc oxide coal consumption of fuming furnace has been reduced from 1850kg/t in 2019 to 1352kg/t in 2021, realizing cost reduction and efficiency increase, improving the economic benefit of the enterprise and completing the annual production efficiency task.Keywords: Fuming furnace; Coal feeder; Tons of zinc oxide coal consumption; Production practice江西金德铅业股份有限公司炼铅工艺为富氧底吹炉-侧吹还原炉-烟化炉三联炉工艺,而烟化炉的给煤装置在升级改造前的给煤系统,是通过中间仓给煤通过平衡风加压经过螺旋给煤机由一次风送入烟化炉炉内,没有计量,手动调速,经常会出现塌煤、断煤、给煤不均匀等隐患,导致烟化炉煤耗居高不下,且不能保证烟化炉系统的正常运行。
卷烟厂节能降耗的方法分析
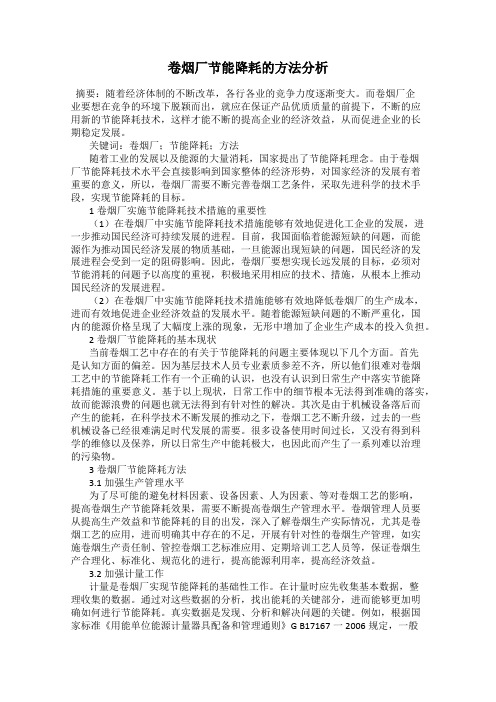
卷烟厂节能降耗的方法分析摘要:随着经济体制的不断改革,各行各业的竞争力度逐渐变大。
而卷烟厂企业要想在竞争的环境下脱颖而出,就应在保证产品优质质量的前提下,不断的应用新的节能降耗技术,这样才能不断的提高企业的经济效益,从而促进企业的长期稳定发展。
关键词:卷烟厂;节能降耗;方法随着工业的发展以及能源的大量消耗,国家提出了节能降耗理念。
由于卷烟厂节能降耗技术水平会直接影响到国家整体的经济形势,对国家经济的发展有着重要的意义,所以,卷烟厂需要不断完善卷烟工艺条件,采取先进科学的技术手段,实现节能降耗的目标。
1卷烟厂实施节能降耗技术措施的重要性(1)在卷烟厂中实施节能降耗技术措施能够有效地促进化工企业的发展,进一步推动国民经济可持续发展的进程。
目前,我国面临着能源短缺的问题,而能源作为推动国民经济发展的物质基础,一旦能源出现短缺的问题,国民经济的发展进程会受到一定的阻碍影响。
因此,卷烟厂要想实现长远发展的目标,必须对节能消耗的问题予以高度的重视,积极地采用相应的技术、措施,从根本上推动国民经济的发展进程。
(2)在卷烟厂中实施节能降耗技术措施能够有效地降低卷烟厂的生产成本,进而有效地促进企业经济效益的发展水平。
随着能源短缺问题的不断严重化,国内的能源价格呈现了大幅度上涨的现象,无形中增加了企业生产成本的投入负担。
2卷烟厂节能降耗的基本现状当前卷烟工艺中存在的有关于节能降耗的问题主要体现以下几个方面。
首先是认知方面的偏差。
因为基层技术人员专业素质参差不齐,所以他们很难对卷烟工艺中的节能降耗工作有一个正确的认识,也没有认识到日常生产中落实节能降耗措施的重要意义。
基于以上现状,日常工作中的细节根本无法得到准确的落实,故而能源浪费的问题也就无法得到有针对性的解决。
其次是由于机械设备落后而产生的能耗,在科学技术不断发展的推动之下,卷烟工艺不断升级,过去的一些机械设备已经很难满足时代发展的需要。
很多设备使用时间过长,又没有得到科学的维修以及保养,所以日常生产中能耗极大,也因此而产生了一系列难以治理的污染物。
工业锅炉运行与烟气治理的节能减排措施

工业锅炉运行与烟气治理的节能减排措施
随着工业锅炉的普遍使用,其能量消耗和烟气排放量逐年增加,对环境造成的影响也日益严重。
为了提高工业锅炉的能源利用效率和降低烟气的污染物排放量,需要采取一系列的节能减排措施。
可以通过对工业锅炉的热力系统进行优化来提高能源利用率。
增加汽包烟道氧量、合理调整进胀水温度和排污温度,进行余热回收等。
配备尾气余热回收装置,将烟气中的热能转化为工艺用热或发电,进一步提高能源利用效率。
可以采用先进的燃烧技术来降低烟气的污染物排放量。
采用低氮燃烧技术,通过优化燃烧过程,降低燃烧产生的氮氧化物排放量。
可以应用燃烧过程中的脱硫、脱氮和除尘等技术,减少烟气中的颗粒物、硫氧化物和氮氧化物等污染物排放。
还可以加强对工业锅炉的管理和维护,保障其正常运行和高效工作。
通过定期进行锅炉清洗、检修和调试,保证燃烧设备的正常工作,减少能源的浪费和烟气的污染。
合理安排工业锅炉的负荷,避免过量供热或生产,降低能源的消耗和烟气的排放。
加强对烟气进行治理,采用适当的污染物净化装置来降低烟气中的污染物排放。
可以应用废气净化装置进行脱硫、脱硝和除尘处理,将烟气中的污染物浓度降低到国家标准规定的范围内。
可以增加余热回收装置和烟气再利用装置,将烟气中的热能和可利用的物质进行回收再利用,减少能源的浪费和环境的污染。
工业锅炉运行与烟气治理的节能减排措施包括优化热力系统、采用先进燃烧技术、加强管理和维护、加强烟气治理等。
通过这些措施的综合应用,可以提高工业锅炉的能源利用效率,减少烟气的污染物排放,实现可持续发展的目标。
烟气炉节能技术的研究与应用

表 1 20 00年 度 吨 煤 粉 能 源成 本 明 细 表
名 称 i 爿
" 1
2月
…
3月
R
4月
’ ^ n
5月
1 4
6爿
1 7 ^
7月 ቤተ መጻሕፍቲ ባይዱ
’ 1
8月
1 8 1
.
9月
】 4
1 q 0 1 月 ;1 1 2月
l 】 7 1 0 5 i 8 3
作 为系统的动 力 , 完成抽 取烟 气 、 煤粉 的 任务 为保 证 产量 、 质量 , 机抽 力 随 时 调节 这样 , 风 机抽 风 在 力与 煤气消耗之 间 就存 在着高 次 曲线关 系。实 际生 产中, 烟气炉炉膛 温 度 变 化 范 围较 小 , 90 0 在 0 ±3 ℃ 之 间。为便于获 取 数 学模 型 , 我们 使 用 了一 元 一次 方程 对曲线送行 回归 F= Q +C k f () 1
Q
Q
,J 、
式 中 : Q —— 实 际空气 流量 , ; Q—— 理论 空气 流量 , 3 . m: Q - 实 际煤 气流 量 , 广 C— —单 位煤 气埔 量 燃 烧 所需 的理 论 空
气 量 , 3m n m / i 对 ( ) 行 变 形 :进
煤 粉 制造过 程 中 , 耗 的能 源 包 括煤 气 、 、 消 水 电 等 , 中煤 气 占较 大 比例 . 其 县体 情 况 见表 1 由表 1 可 见, 能源 消 耗 中 , 气约 占 2 . 并 , 在 煤 6 3 致使 吨媒 粉
制 造 成 本 居 高 不 下
惰 化 剂 , 起 到 携 带 煤 粉 的 作 用 匿 此 , 气 炉 的 燃 并 烟 烧 控 制 在 生 产 中 起 着 非 常 重 要 的 作 用 烟 气 炉 的 燃 烧 控 制 包 括 两 个 方 面 : 是 炉 膛 温 度 的控 制 ; 是 煤 一 二
浅谈烟化炉冶炼工艺的节能措施

48研究与探索Research and Exploration ·改造与更新中国设备工程 2018.02 (下)在采用氧化还原挥发法对铅锌炉渣、铅锌富中矿进行处理时,主要生产设备就是烟化炉。
在大中型铅锌冶炼厂中的年总耗能量中,烟化炉炼渣工序的年消耗能量比重约为40%。
所以,一直以来,铅锌冶炼厂非常重视的一大问题,就是烟化炉冶炼工艺的节能问题。
本文以某炼铅锌厂18平方米烟化炉为例,通过分析该烟化炉的热平衡数据后发现,在全厂总耗热量中,因冷却水、烟气所引发的热损失的比重约为52%,其在燃料化学热中的比重约为68%。
目前,为对上述热量进行有效回收,我国主要采用两种途径,其一,为生产出中压蒸汽,为人们所运用,将烟化炉的水套改成汽化冷却水套;其二,为利用余热进行发电,采用烟化炉和余热锅炉为一体设备。
例如,在2015年,山东铅锌业企业第二冶炼厂对4平方米的烟化炉水套进行改造,将其改造为汽化冷却水套,采用烟化炉和余热锅炉为一体设备,以对蒸汽进行生产,进而进行发电,同时有效降低排烟的温度。
最终,经改造后的烟化炉配套系统,其热效率得到有效提高,即由过去的32%上升至的86%,使本炉能够有效节约约1600吨标准煤。
目前,我国已广泛使用回收热损失方法,基于此,本文深入研究烟化炉冶炼工艺的节能措施,具有重要意义。
1 烟化炉节能的可能性分析一直以来,铅锌冶炼厂非常重视的一大问题,就是烟化炉冶炼工艺的节能问题。
本文以某炼铅锌厂18平方米烟化炉的热平衡为例,对热能流向进行深入研究和分析。
通过分析后不难发现,在本厂总耗热量中,因冷却水、抛渣、烟气等而引发的热损失比重约为75%。
由此可见,对这些热量进行回收,具有非常大的节能可能性。
目前,在我国大多数炼铅锌厂中,烟化炉设备主要对汽化水套、汽化冷却炉壁进行应用,为进行余热发电、供热,采用烟化炉和余热锅炉为一体设备,热利用率得到有效提高,不过蒸汽压力并不高,尚未对其进行充分应用。
提升燃气锅炉的节能效果有哪些办法

提升燃气锅炉的节能效果有哪些办法
燃气锅炉在推入市场后便受到广大用户朋友们的广泛喜爱和信赖,因此使用频率也越来越高。
节能是工业生产中一个重要的问题,尤其是为工业生产提高热能动力支持的工业锅炉,节能的功能就体现出了锅炉行业的技术水平。
除了将传统的工业燃煤锅炉改造成天然气蒸汽锅炉外,在锅炉的运行中还可以采取措施进行节能。
四川方快锅炉厂的技术工程师整理了以下关于燃气锅炉节能的措施:
1、根据工业生产的需求了解蒸汽的量,合理选择锅炉的额定功率以及锅炉数量,锅炉实际使用情况的匹配度越高,排烟损失越小,节能效果越好。
2、燃料与空气充分接触:让适量的燃料和适量的空气组成佳比例进行燃烧,这样既能提高燃料的燃烧效率,又能减少污染性气体的排放,实现双重节能的目标。
3、降低天然气蒸汽锅炉的排烟温度:降低锅炉排烟温度,有效利用排烟中产生的余热,常用锅炉的效率为85-88%,排烟温度是
220-230℃。
若设置省能器等利用排烟热量后,排烟温度下降到140-150℃,锅炉效率可提高到90-93%。
4、回收利用锅炉排污水的热量:通过热交换,利用连续排污水中的热量,提高除氧水的给水温度,达到天然气蒸汽锅炉节能的目的。
方快冷凝蒸汽锅炉系列采取了的设计理念和先进的科技技术——冷凝技术,一种新型的节能环保技术,可以结合各阶段的热能变化情况,对锅炉排放的高温烟气进行冷凝处理,将烟气热量进行梯级利用,充分吸收烟气中的显热和水蒸气凝结释放的潜热。
经过冷凝回收装置后的烟气温度只有90℃左右,锅炉热效率可以提高10%以上,既节约了燃料成本,又能够降低有害气体的排放,减少环境污染,一举多得。
工业炉的节能降耗技术
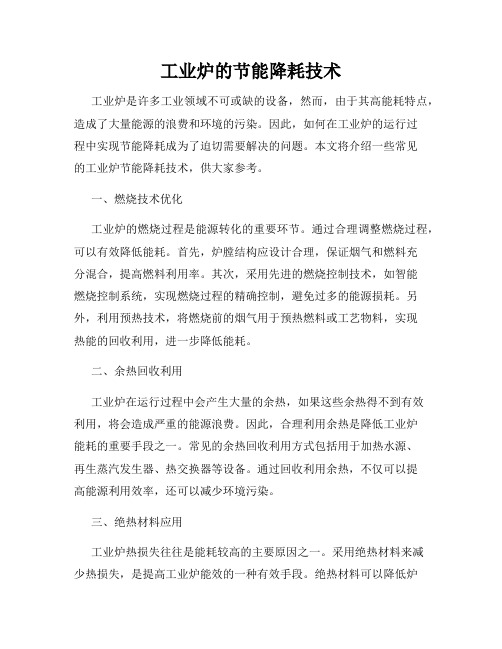
工业炉的节能降耗技术工业炉是许多工业领域不可或缺的设备,然而,由于其高能耗特点,造成了大量能源的浪费和环境的污染。
因此,如何在工业炉的运行过程中实现节能降耗成为了迫切需要解决的问题。
本文将介绍一些常见的工业炉节能降耗技术,供大家参考。
一、燃烧技术优化工业炉的燃烧过程是能源转化的重要环节。
通过合理调整燃烧过程,可以有效降低能耗。
首先,炉膛结构应设计合理,保证烟气和燃料充分混合,提高燃料利用率。
其次,采用先进的燃烧控制技术,如智能燃烧控制系统,实现燃烧过程的精确控制,避免过多的能源损耗。
另外,利用预热技术,将燃烧前的烟气用于预热燃料或工艺物料,实现热能的回收利用,进一步降低能耗。
二、余热回收利用工业炉在运行过程中会产生大量的余热,如果这些余热得不到有效利用,将会造成严重的能源浪费。
因此,合理利用余热是降低工业炉能耗的重要手段之一。
常见的余热回收利用方式包括用于加热水源、再生蒸汽发生器、热交换器等设备。
通过回收利用余热,不仅可以提高能源利用效率,还可以减少环境污染。
三、绝热材料应用工业炉热损失往往是能耗较高的主要原因之一。
采用绝热材料来减少热损失,是提高工业炉能效的一种有效手段。
绝热材料可以降低炉体表面温度,减少热辐射和对流散热,提高工业炉的热效率。
同时,绝热材料还可以减少炉体受热膨胀引起的能量损耗,延长炉体使用寿命。
因此,在设计和改造工业炉时,应考虑使用绝热材料,以降低能耗。
四、智能控制系统应用智能控制技术的发展为工业炉节能降耗提供了新的可能。
智能控制系统可以通过精确的数据采集和分析,实时调整工业炉的运行参数,优化能源利用,减少能耗。
例如,温度、压力等传感器的应用可以实时监测炉内状况,根据实际情况进行智能调节,提高工业炉的能效。
同时,智能控制系统还可以实现对燃料的精确控制,确保燃烧过程的高效进行。
五、定期维护和保养工业炉的定期维护和保养对于提高其能效至关重要。
例如,清理炉体内外的堆积物可以减少热阻和传热阻力,提高传热效率。
浅析化学工艺中常见的节能降耗技术方法

浅析化学工艺中常见的节能降耗技术方法
在化学工艺中,节能降耗技术方法是指通过合理的措施和技术手段,减少能源消耗和物质损耗,达到节约资源、降低生产成本、保护环境的目的。
常见的节能降耗技术方法包括以下几个方面:
1. 回收利用废热:在化学工艺过程中产生的废热可以通过烟气余热回收、蒸汽余热回收等方式进行利用,进行热能回收,以提高燃烧效率和能源利用率。
2. 采用低温技术:在化学反应中,通过降低反应温度可以减少能量损失。
一些高温反应可以通过降低反应温度和采用催化剂等方式,实现反应温度的降低和能量消耗的节约。
3. 改进蒸馏过程:蒸馏是化学工艺中常用的分离技术,但能耗较高。
通过改进蒸馏塔结构、优化操作条件、采用新型分离技术等方式,降低蒸馏能耗,提高分离效率。
4. 优化反应条件:通过优化反应条件,如改变反应物比例、控制反应速率等,可以降低化学工艺中的能耗和原料消耗。
5. 采用节能设备:化学工艺中的诸多设备,如泵、压缩机、换热器等,存在能耗较高的问题。
选择节能设备,如高效泵、节能压缩机等,可以减少能源消耗。
6. 废物资源化利用:化学工艺过程中产生的废物可以通过催化转化、生物降解等技术进行资源化利用,减少物质损耗。
7. 采用先进的控制技术:通过采用先进的自动化控制系统、优化生产计划等手段,实现化工生产过程的优化调控,减少能源消耗和物料损耗。
工业炉的能源节约技术与实践

工业炉的能源节约技术与实践工业炉在现代生产中扮演着重要的角色,但其高耗能特点使得能源消耗成为一个不容忽视的问题。
因此,探索工业炉的能源节约技术与实践对于提高生产效率、降低生产成本、减少能源排放以及实现可持续发展具有重要意义。
本文将介绍几种常见的工业炉能源节约技术以及相关实践案例。
一、燃烧优化技术燃烧优化技术是提高工业炉能源利用效率的关键手段之一。
通过调整燃烧系统的参数,达到最佳的燃烧状态,可以有效减少燃料的消耗,提高热效率。
其中,以下几个方面是需要关注的:1. 氧量控制:合理控制燃烧过程中的氧量,可以有效降低排烟温度和排烟中的氧含量,从而提高热回收效率。
2. 预热燃料与空气:通过在燃烧前对燃料和空气进行预热,可以减少燃料的消耗量,并提高燃料的燃烧效率。
3. 降低过量空气系数:过量空气是造成能源浪费的一个重要因素,合理控制过量空气系数,可以减少过多的氧量对燃料的稀释,提高燃料的利用率。
通过燃烧优化技术的实践案例,我们可以看到其在工业炉节能方面的显著效果。
例如,在某某钢铁厂,引入燃烧优化技术后,工业炉燃料消耗量减少了20%,热效率提高了15%,显著降低了生产成本。
二、热回收技术工业炉释放的废热,如果不能进行有效回收利用,将造成巨大的能源浪费。
因此,热回收技术在工业炉能源节约中具有重要地位。
以下是几种常见的热回收技术:1. 烟气余热回收:通过烟气中的余热进行回收利用,可以用于加热水或产生蒸汽,提高整体能源利用效率。
2. 炉排废气余热回收:利用炉排废气中蕴含的高温高压蒸汽,可以用于发电或加热工艺蒸汽等,提高能源利用效率。
3. 冷却水余热回收:通过冷却水中的余热进行回收利用,可以提供给其他加热或制冷系统,实现能源的综合利用。
热回收技术的实践案例充分展示了其对工业炉能源节约的巨大潜力。
例如,在某某石化企业,通过引入烟气余热回收技术,年节约能源达到xx吨标准煤,同时减少二氧化碳排放量。
三、节能材料与节能设计采用节能材料和合理设计工业炉的结构,也是提高能源利用率的重要途径。
基于烟化炉节能途径分析

基于烟化炉节能途径分析烟化炉是熔炼的设备,主要用来处理铅渣,回收容易挥发的金属铅、锌。
烟化过程实际上是将空气和粉煤的混合物通入熔融的铅、锌进行还原吹炼。
但是我国烟化炉存在能耗大、成本高等多方面的问题,所以中国的烟化炉特别是节能途径亟待解决。
标签:烟化炉;改善燃烧;烟化炉控制节能0 引言我国基本上都以粉煤作为烟化的燃料,在熔炼过程中还会存在燃烧等各种问题。
本文将着重介绍烟化炉内粉煤燃烧的机理、过程,结合生产的实际提出改善燃烧的方法,针对燃烧过程存在的问题进行了系统的分析,对今后的工作作出参考。
1 烟化炉内粉煤燃烧机理与过程烟化炉熔炼是一个周期性的工作,可以进行加料、升温、还原吹炼、放渣四步。
粉煤在熔炼过程中具有还原和供热双重作用。
粉煤气流燃尽的过程比较漫长。
让烟气过快离开炉膛会造成机械燃烧不完全而造成燃料损失。
在升温阶段,应该根据粉煤气流的燃尽时间来确定气流操作速度。
选取合适的气流速度,保证粉煤燃烧发挥完全。
2 烟化炉节能分析烟化炉的节能一直以来都是大中型铅冶炼厂的追求,烟化炉炼渣系统能耗量一般占总能耗量的40%左右。
我厂烟化炉采用余热锅炉回收余热,能够提高热利用率。
3 烟化炉节能途径3.1 工艺冶炼节能烟化炉中铅的挥发速率因为含氧率的增大而提高,因为吹炼时间会缩短,所以节能效果更加明显。
但是很多炼铅厂欠缺很多制氧工艺设备,氧吹的成本很高,没有进行广泛应用。
3.2 烟化炉余热利用对高温烟气进行余热回收。
(1)汽化冷却法。
如果在炼铅厂安装汽化冷却装置,既能节约用水又能够回收热量,保证烟化炉能够正常运行。
然而使用汽化冷却水会降低烟化炉使用寿命,需要对烟化炉进行改进才可以使用。
(2)安装余热锅炉回收余热。
在烟化炉中安装余热锅炉装置,通过生产证明得出这种强制循环和自然循环的方法是切实可行的。
通过在烟化炉内安装余热锅炉,能够有效利用高温烟气余热,回收烟气中的二氧化硫,对环境起到保护作用。
4 烟化炉节能管理4.1 提高管理水平(1)建立炼渣流程管理系统。
工业锅炉运行与烟气治理的节能减排措施

工业锅炉运行与烟气治理的节能减排措施工业锅炉作为工业生产中的重要设备之一,在生产中扮演着重要的角色。
然而,其运行过程中产生的废气和废水等问题已经成为环境污染的主要来源之一。
其中,烟气排放是工业锅炉生产中的主要污染物之一。
因此,为了减少烟气排放,促进环保和节能减排,采取相应的措施非常必要。
一、节能减排措施1. 烟气余热回收在工业锅炉燃烧时,会产生大量的烟气,其中的余热利用率通常非常低。
烟气余热回收是一种有效的节能减排措施。
通过在锅炉烟气系统中增加余热回收设备,可以有效地提高热能利用率,减少烟气的排放。
2. 锅炉节水技术给水作为锅炉的一个重要组成部分,在运行过程中不仅仅是为锅炉提供水分,同时还会用来冷却和清洗设备等。
因此,节约水资源非常重要。
采用节水技术,如回收锅炉排放的废水和回收各种工艺用水,可以有效地降低生产过程中的水耗,减少水资源的浪费。
3. 锅炉燃烧增效技术锅炉燃烧增效技术是指通过增加锅炉的燃烧效率来降低烟气排放。
具体实现方法有优化燃烧设备设计、改进燃烧控制系统、优化燃烧过程等。
同时,还可以采用一些技术手段,如增加空气预热、降低氧含量等来实现燃烧增效。
二、烟气治理措施在燃烧过程中,硫化物会被转化为二氧化硫等含硫物质。
如果直接排放到大气中,会对环境产生严重的影响。
因此,采取烟气脱硫措施是非常必要的。
常见的脱硫方式有石灰石/石膏湿法脱硫、活性炭吸附法脱硫和催化氧化/洗涤法脱硫等。
2. 烟气脱硝氮氧化物是烟气中的一种重要污染物。
如果没有有效的治理方法,会对空气质量和环境产生严重影响。
烟气脱硝可以采用SCR(Selective Catalytic Reduction,选择性催化还原技术)、SNCR(Selective Non-Catalytic Reduction,选择性非催化还原技术)、催化氧化等技术来实现。
3. 烟气净化器烟气净化器是一种可以有效治理烟气污染的设备。
常见的烟气净化器有静电除尘器、布袋除尘器、湿式电除尘器等。
工业锅炉运行与烟气治理的节能减排措施

工业锅炉运行与烟气治理的节能减排措施工业锅炉是工厂生产中常用的设备,它使用燃煤、燃气、生物质等燃料进行燃烧,产生热量,从而供应工厂的生产需求。
工业锅炉的运行不仅消耗大量能源,同时也会产生大量的排放物,给环境带来很大的压力。
加强工业锅炉的运行与烟气治理的节能减排措施,对于实现可持续发展具有重要意义。
工业锅炉的节能减排需要从源头入手,选择清洁高效的燃料是关键。
相比于传统的燃煤,燃气和生物质燃料是更清洁高效的选择。
燃气燃烧产生的废气排放较少,热值高,燃烧效率高,对环境的影响也相对较小。
而生物质燃料往往是废弃物的再利用,可以减少对于原生态的破坏。
选择清洁高效的燃料是工业锅炉节能减排的第一步。
优化锅炉的燃烧技术也是提高能源利用效率、减少排放的关键。
采用先进的燃烧技术,如流化床燃烧、低氮燃烧技术等,可以有效提高燃烧效率,减少燃料的消耗,降低排放物的产生。
采用高效的余热利用技术,对烟气中的热能进行回收利用,不仅可以减少能源的浪费,还可以降低对环境的影响。
工业锅炉的运行与烟气治理需要配备有效的除尘设备和脱硫脱硝装置。
在锅炉燃烧过程中会产生大量的灰尘和二氧化硫、氮氧化物等有害物质,直接排放到大气中会造成严重的空气污染。
安装高效的除尘装置和脱硫脱硝设备,能够有效地去除烟气中的颗粒物和有害气体,保护环境、改善空气质量。
定期进行锅炉设备的检修和维护也是保证其运行效率和减少排放的重要措施。
及时清理锅炉中的积灰、检修燃烧系统,保证锅炉的正常运行,不仅可以提高其燃烧效率,同时也可以降低烟气的排放。
定期对烟气治理设备进行检查和维护,保证其正常运行,也能够有效降低排放物对环境的影响。
加强工业锅炉运行与烟气治理的监管和管理,对所有的工业锅炉进行严格的排放标准和监测要求。
建立完善的监测体系,动态监控燃烧过程中的排放物的情况,及时发现问题并加以处理。
加大对违反排放标准的企业的处罚力度,推动企业自觉加强对工业锅炉的管理和维护,积极应对环保要求。
【记XX冶炼厂烟化炉车间开展节能降耗活动】玉溪冶炼厂 烟化炉

【记XX冶炼厂烟化炉车间开展节能降耗活动】玉溪冶炼厂烟化炉节能降耗,提高经济技术指标——记XX冶炼厂烟化炉车间开展节能降耗活动节能降耗,简言之就是节约能源、降低消耗,用最少的投入去获取最大的经济效益。
从企业的角度来说,就是在生产过程中有效节水,节电,节约资源,提高单位资源的综合利用率,进而用最少的资源产生更高的利润。
近期,XX冶炼厂烟化炉车间积极落实控股公司及厂部提出的“十一五”期间关于节能减排的号召,开展了节能降耗活动。
减少资源消耗,提高资源综合利用率,是从源头上节能降耗的重要措施。
该车间以技术改造为突破口,努力提高自身的节能降耗水平。
技术改造和技术创新是提高节能降耗最有效的途径。
技术改造主要是指依靠科技进步,采用新技术、新工艺、新材料和新方法对原有生产工艺设备进行系统技术改造,逐步淘汰低效设备和高耗能产品群在企业生产中的使用等技术,技术改造会带来更好的效果。
烟化炉车间主要是以粉煤为燃料,以吹炼技术生产次氧化锌产品。
为了进一步提高经济指标,提高产量,降低空气消耗和节约燃料,车间积极组织了富氧吹炼实验。
实验成功后,将大大增加单位时间内燃烧反应的放热量,能迅速提高熔渣温度,加快冷料的溶化速度,温度较高的熔渣还能有效的促进金属氧化物的还原和金属的挥发过程,鼓入了富氧空气将进一步加速燃料的燃烧,节约生产时间和降低生产成本。
目前,车间最主要的燃料是粉煤,粉煤资源消耗约占生产成本的40℅左右。
采用新技术后,预计将节约用煤200公斤∕吨锌,加快了吹炼速度,使吹炼炉数每天增加一炉,从而有效提高了产量。
在企业内部,节能降耗无处不在,因此,车间在实施节能降耗时不仅仅盯着大的项目,在抓好重大设备节能降耗技术攻关的同时,还通过开展了小改小革,挖潜增效,节能降耗活动。
比如对输煤运行方式进行优化调整,减少了输煤系统空负荷运行时间;采取错峰避电措施,改为夜班开启磨煤机,节约电费约1万∕月。
又如在吹炼待料阶段,根据停歇时间长短来降低高压风机的转数,提高节电率;再如回收上炉生产时行车渣包里的渣壳及鼓风炉的水淬,投入炉中再次进行吹炼。
实施节能措施,减少散热损失和排烟损失,降低加热炉能耗

实施节能措施,减少散热损失和排烟损失降低加热炉能耗摘要:本文以大连石化公司加热炉运行情况为实例,提出通过改良辐射室衬里材料、管网瓦斯脱硫、采用空燃比串级调节控制技术可以降低加热炉的散热损失和排烟损失,降低加热炉能耗。
关键字:加热炉、热效率、散热损失、排烟损失1.引言加热炉在生产中的任务是:利用燃料燃烧释放出热量把工艺介质加热到生产工艺规定的温度。
当处理能力一定时,热效率越高,加热炉消耗的燃料量越少。
提高热效率,减少燃料消耗量是降低大连石化公司加热炉能耗的主要任务。
2007年大连石化公司在运行加热炉21台,2007年1-10月加热炉累计平均热效率86.99%,2007年1-10月加热炉累计平均排烟温度184.25℃,其中运行情况较差的有柴油加氢加热炉排烟温度328℃,热效率仅达81%;三苯F101、F104炉排烟温度均大于250℃,热效率仅达83%;三酮苯加热炉氧含量高达12% ,热效率仅达83。
由此可见,公司加热炉实现“挖潜降耗”是有很大空间的。
加热炉热效率反平衡法计算公式为:η=100%-(Qa+ Qb+ Qc)。
其中η—加热炉热效率%;Qa—排烟损失热量占供给能量的百分数%;Qb—表面散热损失热量占供给能量的百分数%;Qc—不完全燃烧损失热量占供给能量的百分数%。
散热损失和排烟损失占总热损的70%左右,本文试以实施三项技术措施为例,分析大连石化公司加热炉降低能耗的潜能。
2.减少散热损失加热炉外壁温度随环境温度的降低而下降,外壁温度在夏季和冬季相差虽多,但散热损失差值不是太大。
国外某些设计公司规定,在环境温度为25℃,风速为2m/s条件下的外壁温度为80-90℃。
12月份大连环境温度为4℃左右,风速平均为3-6m/s,大连石化公司加热炉炉壁测温显示柴油加氢加热炉炉表面平均温度达到300℃,三苯F301加热炉炉表面平均温度达到200℃,连续重整四合一炉炉表面平均温度达到100℃。
可见,上述几台加热炉炉表温度已严重超设计值。
- 1、下载文档前请自行甄别文档内容的完整性,平台不提供额外的编辑、内容补充、找答案等附加服务。
- 2、"仅部分预览"的文档,不可在线预览部分如存在完整性等问题,可反馈申请退款(可完整预览的文档不适用该条件!)。
- 3、如文档侵犯您的权益,请联系客服反馈,我们会尽快为您处理(人工客服工作时间:9:00-18:30)。
基于烟化炉节能途径分析
作者:刘吉良
来源:《山东工业技术》2016年第10期
摘要:烟化炉是熔炼的设备,主要用来处理铅渣,回收容易挥发的金属铅、锌。
烟化过程实际上是将空气和粉煤的混合物通入熔融的铅、锌进行还原吹炼。
但是我国烟化炉存在能耗大、成本高等多方面的问题,所以中国的烟化炉特别是节能途径亟待解决。
关键词:烟化炉;改善燃烧;烟化炉控制节能
DOI:10.16640/ki.37-1222/t.2016.10.061
0 引言
我国基本上都以粉煤作为烟化的燃料,在熔炼过程中还会存在燃烧等各种问题。
本文将着重介绍烟化炉内粉煤燃烧的机理、过程,结合生产的实际提出改善燃烧的方法,针对燃烧过程存在的问题进行了系统的分析,对今后的工作作出参考。
1 烟化炉内粉煤燃烧机理与过程
烟化炉熔炼是一个周期性的工作,可以进行加料、升温、还原吹炼、放渣四步。
粉煤在熔炼过程中具有还原和供热双重作用。
粉煤气流燃尽的过程比较漫长。
让烟气过快离开炉膛会造成机械燃烧不完全而造成燃料损失。
在升温阶段,应该根据粉煤气流的燃尽时间来确定气流操作速度。
选取合适的气流速度,保证粉煤燃烧发挥完全。
2 烟化炉节能分析
烟化炉的节能一直以来都是大中型铅冶炼厂的追求,烟化炉炼渣系统能耗量一般占总能耗量的40%左右。
我厂烟化炉采用余热锅炉回收余热,能够提高热利用率。
3 烟化炉节能途径
3.1 工艺冶炼节能
烟化炉中铅的挥发速率因为含氧率的增大而提高,因为吹炼时间会缩短,所以节能效果更加明显。
但是很多炼铅厂欠缺很多制氧工艺设备,氧吹的成本很高,没有进行广泛应用。
3.2 烟化炉余热利用
对高温烟气进行余热回收。
(1)汽化冷却法。
如果在炼铅厂安装汽化冷却装置,既能节约用水又能够回收热量,保证烟化炉能够正常运行。
然而使用汽化冷却水会降低烟化炉使用寿命,需要对烟化炉进行改进才可以使用。
(2)安装余热锅炉回收余热。
在烟化炉中安装余热锅炉装置,通过生产证明得出这种强制循环和自然循环的方法是切实可行的。
通过在烟化炉内安装余热锅炉,能够有效利用高温烟气余热,回收烟气中的二氧化硫,对环境起到保护作用。
4 烟化炉节能管理
4.1 提高管理水平
(1)建立炼渣流程管理系统。
建立炼渣流程管理信息系统,用计算机代替人为操作统计,及时分析烟化炉能源损耗,能够提高管理水平。
(2)强化人工和工序管理。
不仅建立人员技能培训,还要树立节能意识。
发挥人员积极性,尽量避免烟化炉能源损耗。
在生产经验总结基础上,能够制定完善的烟化炉生产工序,克服生产过程的盲目。
(3)发挥能源管理机构作用。
制定节能规划,保障能源机构措施积极落到实处。
4.2 实现烟化炉控制节能
为了达到节能的目的应该完善节能控制方法措施,必须控制好下列条件,即温度、燃料、送风量、和炉渣成分。
(1)烟化炉燃烧温度控制。
烟化温度和时间对铅锌挥发速度的影响,在其它条件一定时,铅锌的挥发速度随着温度的升高而增大。
但温度过高(如超过1350℃),可能会形成积铁或Zn—Fe、Sn—Fe合金,有害于烟化作业的进行。
温度过低,金属氧化物的还原速度变慢,挥发速度降低,炉渣流动性变坏,甚至有结炉的危险,所以烟化实践中的温度保持在1150~1300℃的范围。
合理的温度能够减小能源浪费,达到节能效果。
(2)燃料控制。
燃料中含H愈多,则烟化过程的效率愈好。
所以煤以挥发分高者为宜,一般为21~25%,其消耗因质量而异。
粉煤质量的要求:发热量≥6500、挥发份≥25、固定碳≥60、灰分≤6%、水份
≤1% 。
(3)送风量。
影响烟化过程挥发速度最活跃的因素是送风量。
因为炉内的温度、
CO/CO2的比例、气体量以及金属的蒸汽压力等都与送风的数量有关。
送风量的大小决定于粉煤消耗和空气利用系数(α),空气利用系数愈大,则燃料的热效应愈高,CO2的分压也愈大,炉内温度亦愈高;空气利用系数小时,热效应降低,CO分压变大,还原能力增强。
粉煤在烟化过程中既是还原剂,又是发热剂,因此燃烧时的CO、CO2应有适当的比例。
工厂实际上采用的空气利用系数是变动的。
通常在烟化开始时,接近于1.0的空气利用系数使碳几乎全部燃烧成CO2,以提高熔渣温度。
转动还原期后,调整空气利用系数使碳尽可能地变成CO,以提高还原能力。
(4)炉渣成分。
炉渣含锌率越高,则回收率越大,现实含锌量以>6%为宜,低于4%的炉渣,烟化处理量是不经济的。
废渣含锌也不应降至2%以下。
入炉熔渣成分:Zn 9~12、 Pb 1~2、 SiO2 18~22 、Fe 30~35 、 CaO 16~20。
关于炉渣组成对锌挥发速度的影响,可以归纳为:
①CaO含量的增大可增高锌的挥发速度;
②渣中FeO含量的增加,对ZnO活度的影响不大;
③SiO2的含量增加,锌的挥发速度减小。
所以,炉渣的硅酸度最好是在1.1~1.2的范围内。
5 热风助燃
我国的烟化炉空气助燃一般为冷风。
冷风既不利于烟气余热回收,又不利于燃烧和冶炼工艺的发展,而国外已经选择热风助燃。
采用热风,能够增加气态金属氧化过程,小颗粒粉煤也能燃烧透彻。
产品纯度将会大大提高,烟道高温区也相对集中,更加有利于余热回收。
6 结语
烟化炉操作工艺已经得到很大的进步,烟气余热方法也成功地运用到了生产中。
虽然目前国内烟化炉工艺具有一定的节能效果,但是技术依旧不成熟,依然存在环境污染等问题。
在工业发达的经济时代,应该不断推广技术,强调节能管理方法。
技术人员应当努力将烟化炉节能技术提升到一定的水平,实现烟化炉操作自动化,从而节约能源,实现经济绿色发展。
参考文献:
[1]王少龙,张殿彬,赵红梅,朱海成.粉煤固定碳含量对烟化炉冶炼指标的影响[J].有色金属(冶炼部分),2014(09):12-15+33.
[2]曾锦波,卜文平.余热利用在有色行业的应用[J].科技与企业,2013(19):158.
[3]聂文斌,彭红寒,王洪礼,邓威威.一种烟化炉新型水套研发及生产实践[J].云南冶金,2015(01):78-82.
[4]范高峰,王建峰.一种烟化炉余热锅炉的开发设计[J].工业锅炉,2015(02):20-22+31.
[5]夏明军,廖舟,苏佳兴,熊勇,夏玮,马骥,成慰.冶金安全节能专家控制系统在烟化炉中的应用[J].工业炉,2015(06):52-55.。