偏八辊轧机液压伺服系统调试与改进
轧辊加工机床控制系统及其故障处理实例

轧辊加工机床控制系统及其故障处理实例轧辊加工机床是金属加工行业常用的设备,其关键部件之一就是控制系统。
控制系统的作用是实现机床的自动化加工,提高生产效率和加工质量。
轧辊加工机床控制系统通常包括硬件部分和软件部分,硬件主要包括PLC、数控系统、伺服系统等,软件主要包括运动控制程序、人机界面等。
轧辊加工机床控制系统的工作原理是通过控制系统发送控制指令,实现轧辊的运动控制和工艺参数的调整。
整个加工过程通过程序控制,可以实现自动化生产,提高生产效率。
1. 故障现象:轧辊加工机床启动后,轧辊无法转动。
故障原因:可能是轧辊伺服系统故障,或者是轧辊PLC控制系统故障。
故障处理:首先检查轧辊伺服系统,查看伺服电机是否正常,电缆是否松动,伺服控制器是否故障等。
如果伺服系统正常,再检查PLC控制系统,查看PLC程序是否正常,输入输出信号是否正常。
2. 故障现象:轧辊加工机床加工出的产品尺寸不符合要求。
故障原因:可能是轧辊数控系统参数设置错误,或者是轧辊轴承磨损导致轧辊位置偏差。
故障处理:首先检查数控系统参数设置,查看轧辊运动参数是否正确,是否需要调整。
然后检查轧辊轴承,确认轴承是否正常,需要更换或修理。
3. 故障现象:轧辊加工机床显示屏出现故障代码。
故障处理:首先检查人机界面设备,查看是否有损坏或显示异常。
然后检查控制系统与显示屏的通信线路,确认是否有松动或短路等问题。
四、轧辊加工机床控制系统的维护保养轧辊加工机床控制系统的维护保养对于保证设备运行稳定性和延长设备寿命非常重要。
维护保养工作主要包括以下几个方面:1. 定期清洁控制系统的外部器件和线路,防止灰尘和杂物影响设备正常运行。
2. 定期检查控制系统的连接线路和接口,确认是否松动或短路等问题,及时进行调整和维修。
3. 定期检查控制系统的参数设置,确认是否符合加工要求,及时调整参数。
4. 定期更换控制系统的易损件,如电缆、连接器等。
五、结语轧辊加工机床控制系统是机床的核心部件,其性能稳定与否直接影响着加工质量和生产效率。
液压机伺服技术改造的实施方案

液压机伺服技术改造实施方案一、需求分析与评估在进行液压机伺服技术改造前,需要深入了解企业的实际需求,如提高生产效率、改善产品质量、降低能耗等。
对现有液压机的工作状况进行全面评估,包括性能、效率、精度、可靠性等方面,找出存在的问题和改进的空间。
根据评估结果,制定改造目标和实施计划。
二、伺服系统选型根据液压机的实际需求和评估结果,选择适合的伺服系统型号。
需要考虑的因素包括:1. 伺服系统的性能参数,如最大输出功率、动态响应、控制精度等;2. 液压机的负载特性和工艺要求;3. 伺服系统的可靠性和稳定性;4. 系统的成本和性价比。
三、旧设备拆除在安装新伺服系统之前,需要对旧设备进行拆除。
需要拆卸的部件包括:液压泵、液压缸、传动装置等。
在拆除过程中,要保证设备的完整性,以便后续的回收和再利用。
同时,要注意安全问题,采取必要的防护措施,确保操作人员的人身安全。
四、新伺服系统安装按照安装说明书的指引,正确安装新伺服系统。
需要安装的部件包括:伺服电机、控制器、传感器等。
在安装过程中,要确保各部件的连接牢固可靠,避免出现松动或脱落的情况。
同时,要注意电气安全和机械安全,确保设备和操作人员的安全。
五、系统调试与测试完成新伺服系统的安装后,需要进行系统调试与测试。
首先进行电气调试,检查线路连接是否正确,各部件的电源是否正常。
然后进行机械调试,调整各部件的安装位置和间隙,确保设备的运动轨迹和精度符合要求。
最后进行性能测试,检查设备的各项性能指标是否达到预期要求。
六、员工培训为了确保操作人员能够熟练掌握新伺服系统的操作和维护技能,需要进行员工培训。
培训内容包括:新伺服系统的基本原理、操作方法、维护保养等方面。
通过培训,使操作人员能够快速适应新设备,提高工作效率。
同时,也要进行安全培训,加强员工的安全意识,避免发生安全事故。
七、运行监控与优化在新伺服系统投入使用后,需要进行运行监控与优化。
通过实时监测设备的运行状态和性能参数,及时发现和处理异常情况。
轧机液压AGC伺服缸优化分析
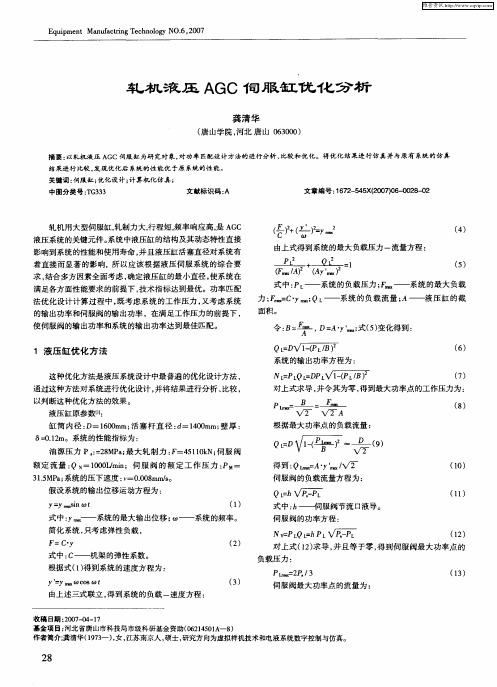
轧机用大型伺服缸, 轧制力大, 程短, 响应 高, A C 行 频率 是 G
液压系统的关键 元件 。 系统 中液压缸 的结构及其动态特性直接 影 响到系统 的性能和使用寿命 , 并且液压缸活塞直径对系统有 着直接 而显著 的影 响,所 以应该根据 液压伺 服系统 的综合要 求, 结合 多方 因素全面考虑 , 确定液压缸 的最小直径 , 使系统在 满 足各方面性能要求 的前提下 , 技术指标 达到最优 。功率 匹配 法优化设计计算 过程中 , 既考虑 系统的工作 压力 , 又考虑系统 的输 出功率和伺 服阀的输 出功率 ,在满足工作压力 的前提 下 , 使伺服 阀的输出功率和系统的输 出功率达到最佳 匹配。
维普资讯
E u p n Ma u a t n e h o o y NO. 2 0 q i me t n f cr g T c n l g i 6, 0 7
轧 机 液 压 AGC 伺 服 缸 优 化 分 析
龚清 华
( 山学院 , 唐 河北 唐 山 0 30 ) 6 0 0
液 压 缸 原参 数【 】 1 : 缸 简 内径 : 10 m 活 塞 杆 直 径 : = 10 mm; 厚 : D= 60 m; d 40 壁 6 01m。 系统 的性 能指 标 为 : = .2
系统的输出功率方程为 :
N - L D L 1 P ,) L Q =P 、 一 LB P L /(
() 2
简化系统 , 考虑弹性负载 , 只
NvP Q P VP P = F^ L s L L -
负载压 力: Ph 2 / 3 () 3
(2 1)
对 上式 ( 2 求导 , 1) 并且 等于零 , 得到伺服 阀最 大功率点 的
式中: C——机架 的弹性 系数 。 根据式 ( ) 1 得到系统的速度方 程为 :
轧辊间隙调节注意事项

轧辊间隙调节注意事项轧辊间隙调节是钢铁冶炼过程中的重要环节,它直接影响到轧机的轧制效果和产品质量。
正确的轧辊间隙调节可以保证轧机的正常运行和产品的稳定质量,因此需要特别注意以下几个方面。
1. 轧辊间隙的选择轧辊间隙的选择应根据具体的轧制需求和工艺要求来确定。
一般来说,轧辊间隙较大可以增加轧制的通过率和坯料的塑性变形,但也会降低轧制的控制性能和产品的表面质量。
相反,轧辊间隙较小可以提高产品的表面质量,但过小的间隙可能会导致轧辊卡死和产品的不良变形。
因此,在选择轧辊间隙时需要综合考虑这些因素,并进行合理的调整。
2. 轧辊间隙的调整方法轧辊间隙的调整可以通过机械调节和液压调节两种方法进行。
机械调节是通过调整轧机的轧辊之间的距离来改变轧辊间隙,一般适用于小型轧机。
液压调节则是通过液压系统来控制轧机的轧辊之间的距离,一般适用于大型轧机。
无论是采用哪种调整方法,都需要确保调整的精度和稳定性,以保证轧机的正常运行。
3. 轧辊间隙的实时监测为了确保轧辊间隙的准确调整,需要对轧辊间隙进行实时监测。
常用的监测方法包括压力传感器、位移传感器和温度传感器等。
通过这些传感器可以监测到轧辊之间的压力、位移和温度等参数,并及时反馈给操作人员,以便进行相应的调整。
实时监测轧辊间隙可以及时发现问题并进行处理,避免因间隙调节不当而导致的生产事故和质量问题。
4. 轧辊间隙的定期检查和维护轧辊间隙是轧机的核心部件之一,因此需要定期对轧辊间隙进行检查和维护。
检查的内容包括轧辊间隙的尺寸、平行度和磨损程度等。
如果发现轧辊间隙有异常情况,需要及时采取相应的维护措施,如更换磨损严重的轧辊、调整轧辊的平行度等。
定期检查和维护轧辊间隙可以延长轧辊的使用寿命,提高轧机的工作效率和产品质量。
5. 轧辊间隙的调整记录和分析轧辊间隙的调整记录和分析是轧机管理的重要环节。
通过记录轧辊间隙的调整情况和相关参数,可以及时发现调整不当的问题并进行改进。
同时,对调整记录进行分析可以找出轧辊间隙调整的规律和趋势,为轧机操作提供科学依据。
轧机液压伺服位置系统的自适应输出反馈控制

轧机液压伺服位置系统的自适应输出反馈控制李建雄;方一鸣;石胜利【摘要】针对具有不可测状态、未知参数和非线性的轧机液压伺服位置系统,提出一种基于高增益观测器和参数估计器的自适应输出反馈控制算法.所构造的高增益观测器不依赖于系统输入和参数估计值,它只用于估计系统状态,所设计的动态反馈控制器包括:用于保证系统稳定性的主反馈部分和抵消外部扰动和一些不确定性的补偿部分.理论分析表明,所提出的控制算法能够保证闭环系统的所有信号有界,且系统状态及其估计误差的最终收敛边界依赖于观测器的高增益值.以某650 mm可逆冷带轧机液压伺服位置系统为例进行仿真,仿真结果验证了所提出算法的有效性.%A high-gain observer and parameter estimator based adaptive output feedback control algorithm is proposed for hydraulic servo position system of rolling mill which contains unmeasurable states, unknown parameters and nonlinearies. The constructed high-gain observer is independent on control input and estimates of the unknown parameters, which is only employed to estimate the system state. The designed feedback controller contained two parts; the main feedback part which was used to ensure the system stability and the compensative part which was used to attenuate the external disturbance and some uncertainties. It can be proved that the proposed algorithm can guarantee all the signals of the resulting closed-loop system are bounded, and the boundaries of the system state and its estimation error are defined by the given high-gain. Finally, simulation was carried out on the hydraulic servo position system of 650mm reversingcold-strip rolling mill. And the simulation results show the validity of the proposed method.【期刊名称】《电机与控制学报》【年(卷),期】2012(016)001【总页数】7页(P104-110)【关键词】液压伺服位置系统;输出反馈控制;高增益观测器;参数估计;最终有界稳定【作者】李建雄;方一鸣;石胜利【作者单位】燕山大学工业计算机控制工程河北省重点实验室,河北秦皇岛066004;燕山大学工业计算机控制工程河北省重点实验室,河北秦皇岛066004;国家冷轧板带装备及工艺工程技术研究中心,河北秦皇岛066004;燕山大学工业计算机控制工程河北省重点实验室,河北秦皇岛066004【正文语种】中文【中图分类】TP2730 引言电液伺服系统因其具有功率体积比大、响应速度快、控制精度高等优点,在工业过程中得到了广泛应用。
辊式矫直机的调试方法

辊式矫直机的调试方法
辊式矫直机的调试方法通常包括以下几个步骤:
1.检查设备:首先,检查辊式矫直机的所有零部件是否齐全,并确保其安装正确。
检查电源、油路等是否连接正常,以及控制系统是否正常工作。
2.调整辊位:调整辊位是辊式矫直机调试的关键步骤之一。
根据工件的尺寸和形状,合理安排辊位的间距和角度。
辊位的调整应保证工件能够均匀受力,从而达到矫直的效果。
3.调整辊压力:根据工件的材料和形状,调整辊压力。
辊压力的大小与工件的尺寸、材料以及矫直要求有关。
太小的压力可能无法达到矫直效果,而过大的压力则可能导致工件损坏。
4.调整输送速度:辊式矫直机的输送速度也是需要调试的参数之一。
根据工件的尺寸和材料,调整输送速度,以确保工件在辊子之间的停留时间足够长,从而达到矫直的效果。
5.观察矫直效果:在调试过程中,观察工件的矫直效果,如果不符合要求,可以适当调整辊位、辊压力或输送速度,直到达到预期目标。
6.调试控制系统:辊式矫直机通常配备了一个控制系统,用于调节辊位、辊压力、
输送速度等参数。
在调试过程中,需要确保控制系统正常工作,能够准确控制各项参数。
总之,辊式矫直机的调试方法主要包括检查设备、调整辊位和辊压力、调整输送速度、观察矫直效果以及调试控制系统等步骤。
通过逐步调试,确保设备正常工作,达到预期的矫直效果。
辊压机偏辊现象如何消除?

辊压机偏辊现象如何消除?辊压机是如何偏辊的呢?偏辊有什么危害呢?为了消除这一现象,我们就必须了解辊压机相关组成部分的作用。
在介绍辊压机相关部件之前,我们先温习一下辊压机的工作原理以及工作过程。
辊压机是根据料床粉碎的原理设计的,即在较高压力的作用下,物料颗粒之间相互挤压而产生破碎。
要实现这种作用,必须保证辊压机的过饱和喂料,即在两辊上方存续有一定高度的料柱,保持一定的料压,这也是辊压机系统必须设置称重仓的原因之一。
辊压机是由轴心线相互平行的一对辊子组成,辊子通过辊轴两端的轴承座安放在框架内,一个辊子相对框架是固定的,称为定辊;另一辊子的轴承座可以在框架内沿滑道作水平往复运动,称为动辊。
工作时两辊相向转动,液压系统施加的压力通过动辊的轴承座将动辊推向定辊,机械限位保持两辊间存在一定间隙,此时压力通过机械限位传递给框架,当有物料喂入两辊之间时,物料被咬入,两辊被撑开,此时液压系统施加的压力通过动辊传给物料,再经定辊、定辊轴承座、定位销、传给框架。
在此过程中,两辊子通过物料产生作用力及反作用力,使物料粉碎,物料的易磨性能得到改善。
由于两辊的转动,物料被不断地咬入,并被强制卸出,从而实现连续的粉碎作业。
通过以上的了解,我们应该对辊压机有了一定的认识。
下面,我再详谈辊压机各部配件的作用。
1、蓄能器的作用是吸收和补偿辊压机工作能量,使辊压机保持一定的较稳定的压力对物料做功。
2、液压系统的控制液压油泵的启动条件:①辊压机运行;②预设定压力值。
当系统压力达到预设定压力后,液压油泵停止运行。
当辊压机辊缝偏差大于5mm时,纠偏程序开始执行纠偏,辊缝大的一侧加压,小的一侧泄压,直至辊缝恢复正常。
3、位移传感器的主要作用是检测动辊的实际位移量,再由位移变送器传输到电气控制室中转至中央控制室,纠偏程序以此反馈的数据执行纠偏。
因此,位移传感器所反映辊距必须是真实可靠的,否则,会出现反的作用,给设备带来严重的安全隐患。
4、喂料装置由侧板、手动插板和喂料闸板组成。
轧机液压弯辊系统液压故障分析与对策

轧机液压弯辊系统液压故障分析与对策作者:胡启明来源:《中国科技博览》2017年第23期[摘要]文中叙述了轧机弯辊液压系统,对其产生的故障进行了系统的总结分析,简单介绍了对其产生故障后如何判断和处理方法,供读者参考[关键词]轧机;弯辊;伺服系统中图分类号:R317 文献标识码:A 文章编号:1009-914X(2017)23-0043-011、引言轧机液压弯辊是以液压为动力,用机械力弯曲轧辊辊身,用来控制带钢凸度和平直度的技术。
通常由动力源、换向阀、减压阀、伺服阀、液压锁、传感器、液压缸以及液压附件等组成。
在轧制模式时通过伺服阀输出控制弯辊力,由于该系统反应速度快,可以通过对带钢厚度和板凸度进行不间断的测量所得到的信息,及时的对每一瞬间弯辊力数值进行修正调节。
在换辊模式时通过换向阀实现对弯辊缸活塞杆上下移动,达到换辊的目的。
其原理如(图1)所示;2、轧机弯辊系统在运行中可能出现的故障1)压力控制故障轧机液压弯辊系统压力控制故障主要有:轧制模式时压力传感器故障在轧制模式时,上工作辊弯辊压力传感器参与控制,下工作辊压力继电器不参与控制,当两侧压力偏差较大时可能是压力传感器损坏、伺服阀故障、液压泄露等故障。
轧机液压弯辊控制系统由两套独立且完全相同的伺服系统组成,每一侧的上下工作辊弯辊完全按照相同控制指令控制液压缸上下移动,上下弯辊塞侧压力理论上应完全一样,当上下辊压力监测出现不同时,则必有一个出现故障,根据现场实际情况进行分析测量,确定故障位置,对故障进行排除。
2)电磁阀故障当给出电控逻辑信号后,电磁阀5、电磁阀8、电磁阀9不能正常动作,可能故障是电气断线、电磁阀犯卡或电磁铁烧等。
当电磁阀开关状态与测压接点压力关系不符合时,若捅阀正常,可能故障为电气断线、电磁铁烧等;若捅阀压力不正常,可判断为卡阀故障。
3)减压阀故障减压阀故障,主要有在换辊时减压阀6、减压阀7主阀芯卡死或阻尼孔堵塞,达不到设定压力,弯辊不能正常伸出,影响换辊。
伺服系统的调试方法

伺服系统的调试方法伺服系统是现代自动化控制中常用的一种控制系统,广泛应用于机械、电子、航空航天等领域。
为了保证伺服系统的正常运行和优化性能,对其进行调试是非常重要的一环。
本文将介绍一些常用的伺服系统调试方法,帮助读者更好地掌握伺服系统的调试技巧。
一、伺服系统调试前的准备工作在开始伺服系统的调试之前,我们需要对一些基本参数进行设置和确认,以确保调试的顺利进行。
以下是一些常见的准备工作:1. 系统参数设置:包括电机类型、控制器类型、反馈装置类型等。
根据具体的伺服系统配置,选择相应的参数进行设置。
2. 控制器初始化:将控制器恢复至出厂默认设置,清除之前的调试参数,确保控制器处于初始状态。
3. 反馈装置检查:确认反馈装置(如编码器、传感器等)的连接是否正常,检查其工作状态是否正常。
4. 信号线连接确认:检查伺服驱动器与控制器之间的信号线连接是否正确,确保信号的传输畅通。
二、伺服系统调试步骤在进行伺服系统调试时,可以按照以下步骤进行,逐步验证和调整系统的各个参数。
1. 速度环调试:根据伺服系统的要求,设定一个目标速度,观察伺服驱动器是否能够根据设定值输出相应的转速,并调整速度环参数,使得实际输出速度与设定值相匹配。
2. 位置环调试:在速度环调试的基础上,设定一个目标位置,观察伺服系统是否能够准确地运动到目标位置,并调整位置环参数,使得实际位置与设定值误差最小。
3. 稳定性调试:在调试速度和位置环之后,观察伺服系统在不同负载和工作条件下的稳定性。
调整伺服系统的控制参数,提高系统的稳定性和响应速度。
4. 故障诊断:在进行伺服系统调试时,经常会遇到一些问题和故障。
通过系统日志、故障代码等方式,对伺服系统的工作状态进行诊断和排除故障。
5. 性能优化:如果需要进一步提高伺服系统的性能,可以调整一些高级参数,如加速度、减速度、滤波等,使得系统在高速、高精度等要求下能够更好地运行。
三、常见问题及解决方案在伺服系统调试过程中,可能会遇到一些常见的问题和挑战。
助卷辊液压伺服系统分析改进
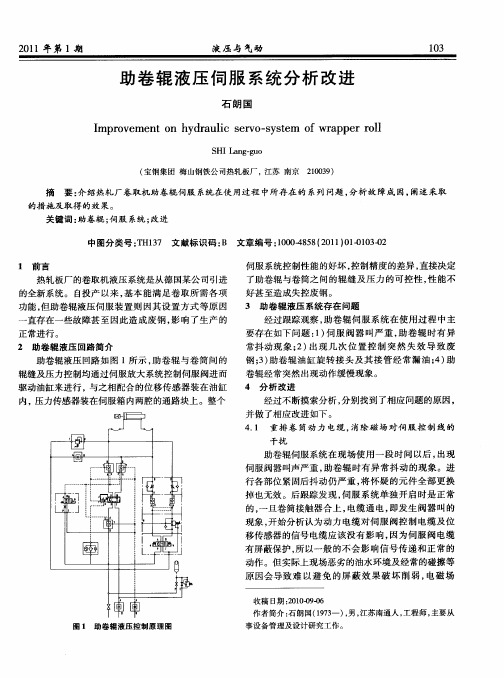
经过 跟踪 观察 , 卷辊 伺 服 系 统 在使 用 过 程 中主 助 要存 在如 下 问题 : ) 服 阀嚣 叫严 重 , 1伺 助卷 辊 时有 异
常抖 动现 象 ; ) 2 出现 几 次 位 置 控 制 突 然 失 效 导 致 废
正 常进行 。 2 助 卷辊 液压 回路简 介
助卷辊 液压 回路 如 图 1所 示 , 卷 辊 与卷 筒 间 的 助 辊缝 及压力 控制均 通过 伺服放 大 系统控 制伺服 阀进 而
4 2 改进助 卷辊 油缸修 复 方式 , . 确保 检 测准确 性
渡到伺 服控 制箱 , 这对 于管路 安装精 度要求 非 常高 , 管
路 安装 有一点 别劲 即容 易造成 密封偏 磨进 而引发 漏油 现象 , 而且 即使 开始 安 装 时旋 转 接 头 中心 与 管路 中心
线 完全 一致 , 因为油 缸 转轴 铜 套 间隙 的存 在 等 因素 也
1 无 效漏油 。后来 结合 实际 安装 空 间 , 油 缸 两腔 出 1 从 来 的管路 通过旋 转 接头 后 先 以软 管 连 接 , 再通 过 硬管 连 接到伺 服箱本 体 上 , 用 软 管 本 身柔 性 允许 的桡性 利 和旋 转接 头组合 , 免 了过 高 的 安装 精 度 要求 及 设备 避
有屏蔽保护 , 所以一般 的不会影 响信号传递和正常的 动作 。但实 际上 现场恶 劣 的油水环 境及 经常 的碰擦 等
原 因会 导致 难 以避 免 的 屏 蔽 效 果 破 坏 削 弱 , 电磁 场
收稿 日期 :0O 6 2 1 9 作者简介 : 石朗国( 9 3 ) 男 , 17 一 , 江苏南通人 , 工程师 , 主要从
钢 ;) 3 助卷辊油缸旋转接头及其接管经常漏油 ;) 4 助
轧机液压伺服位置系统的自适应反步滑模控制
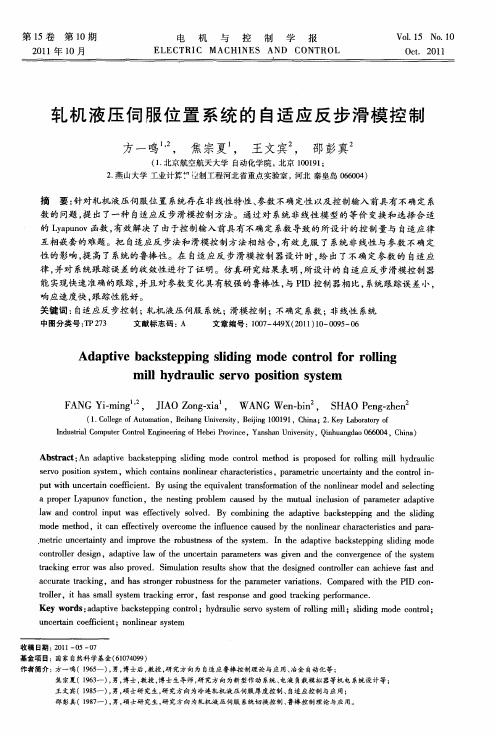
( . 京航 空航 天大学 自动化学 院 , 1北 北京 10 9 ; 0 1 1
2 燕山大学 工业 计算 + 制工程河北省 重点 实验 室 , . n 河北 秦皇岛 0 60 ) 60 4
摘
要: 针对 轧机 液压伺 服位 置 系统存在 非 线性特 性 、 参数 不 确定性 以及控 制 输入前 具有 不确定 系
F ANG Yi n , JAO Z n .i W ANG We .i S - g’ mi I o gxaபைடு நூலகம், n b n , HAO P n .h n e gz e
( . o ee f uo t n B iagU i rt,Bin 0 11 hn ; . e aoa r o 1 C lg t i , e n nv sy eig10 9 ,C ia 2 K yLb rt y f l o A mao h ei j o
数 的 问题 , 出 了一种 自适应反 步 滑模 控 制方 法。通 过 对 系统 非 线性 模 型 的等 价 变换 和选 择 合适 提
的 Lauo yp nv函数 , 效解 决 了由于控 制输入 前具 有不 确定 系数 导致 的所设 计 的控 制 量与 自适 应律 有 互相 嵌套 的难题 。把 自适 应反 步法和 滑模控 制 方法 相 结合 , 效克 服 了 系统 非 线性 与 参数 不 确 定 有
Ab t a t An a a t e b c s p i g si i g mo e c n r l meh d i p o o e o ol g mi y r u i sr c : d p i a k t p n l n d o to t o s r p s d fr r l n l h d a l v e d i l c
液压伺服系统在粗轧机上的应用

液压伺服系统在粗轧机上的应用李鹏来① 贾占涛 张章 贾垭楠 武文飞(首钢京唐钢铁联合有限责任公司 河北唐山063200)摘 要 重点介绍了在轧制过程中液压压下装置、上支承辊液压平衡装置、上工作辊液压平衡装置的功能和液压控制原理,阐述了液压压下装置的闭环控制过程,并提供了上支承辊与上工作辊平衡力的计算方法。
关键词 液压压下装置 平衡装置 平衡力中图法分类号 TG333.1 TH117.2 文献标识码 BDoi:10 3969/j issn 1001-1269 2023 05 029TheApplicationofHydraulicServoSysteminRoughingMillLiPenglai JiaZhantao ZhangZhang JiaYanan WuWenfei(ShougangJingtangIronandSteelCo.,Ltd.,Tangshan063200)ABSTRACT Thefunctionandhydrauliccontrolprincipleofthehydraulicscrewdowndevice,thehydraulicbalancedeviceoftopbackuprollandthehydraulicbalancedeviceoftopworkingrollintherollingprocessareintroducedemphatically.Theclosed loopcontrolprocessofhydraulicscrewdowndeviceisdescribed,andthecalculationmethodofbalanceforceoftopbackuprollandtopworkingrollisprovided.KEYWORDS Hydraulicscrewdowndevice Balancedevice Balanceforce1 前言目前,液压伺服系统在冶金工业领域占有重要地位,特别是需要大功率、响应快速、精确控制的系统大多采用液压伺服控制。
液压伺服系统产品测试生产流程优化

Features中国运载火箭技术研究院科研生产管理最佳实践专辑陶文凯、耿树鳗、滕怀海、黄汕、孙延/北京精密机电控制设备研究所航天液压伺服系统是用来控制火箭发动机推力矢量的液压伺服系统,其根据控制系统指令调整飞行器的姿态,实现俯仰、偏航和滚动控制,并使飞行器按照预定轨道飞行。
液压伺服系统产品生产调试过程中,由于检测项目多、周期长,影响了产品批生产的效率。
为此,北京精密机电控制设备研究所针对需求任务开展了设计要求、工艺流程、生产布局、设备设施等方面的优化挖潜,在保证产品质量的前提下,从工艺和设计2个方面对测试项目和工艺流程进行优化调整,并制定相应措施,以减少产品实做工时,提高生产效率。
|一、工作与实践1.工艺流程调整一是简化伺服机构在装配一调试一装配工序周转间的电气检查要求。
在单机完成装配工序后,产品按规定完成各项电气检査。
装配组转至测试组也是在总装车间进行班组间周转,时间一般在l~2h 之间。
装配组完成电气检查后,测试组在2h内再次进行电气检查操作,在大批量生产过程中属于重复操作,可以优化调整。
W中国运载火箭技术研究院科研生产管理最佳实践专辑Features二是优化合并单机测试工序中对配套电气产品特别是所内配套产品的电气检査要求。
在产品配套后、单机测试前,由于产品入库前已完成了各自的导通绝缘检查,所以后续的测试将通过电缆连同配套产品,并使用测试设备一同进行导通绝缘检查。
三是依托技术进步和工艺布局,调整优化测试工序流程顺序。
对于液压类伺服作动器,根据各级产品的个异性,分别采用少数产品负载试验、多数产品空载稳试的方法来降低产品拆装的辅助时间,从而降低操作人员的劳动强度。
四是通过对现有测试设备的技术升级改造,将测试操作的多人协作转化为自动控制辅助单人操控。
通过改造设备和自动设备的应用,对实现单人操作测试环节中的导通绝缘电气检査。
对产品在稳试时的设备进行优化布局和工装完善,实现在稳试测试时1人对多台产品的同时操作和监控。
液压伺服系统优化控制技术研究

液压伺服系统优化控制技术研究液压伺服系统是一种基于液压传动的自动控制系统,广泛应用于工业生产、军事装备、航空航天等领域。
其控制精确、响应迅速、输出功率大等优点,使得液压伺服系统成为现代工业领域不可或缺的控制设备。
然而,液压伺服系统也存在一些问题,如系统稳定性差、能耗高等,这些问题在现代工业控制中显得尤为紧迫。
因此,为了提高液压伺服系统的性能,优化控制技术的研究变得尤为重要。
一、现有问题1、系统稳定性差液压伺服系统的传动单元是油液,其粘性、压力、流量等参数会随着系统工作状态而变化,从而导致系统性能出现抖动、偏差等问题,影响系统的稳定性。
2、系统响应速度慢由于液压传动的特殊性质,液压伺服系统的响应速度相比于机电伺服系统较慢,从而导致系统难以满足一些要求响应速度较高的场合。
3、能耗较高液压传动所需要的压力和流量较大,而且液压系统中的阀门等部件存在能量损失,从而导致液压伺服系统的能耗较高,给使用和环境带来压力。
二、优化控制技术的研究为了解决液压伺服系统存在的问题,优化控制技术的研究可以从以下几个方面入手。
1、系统建模和控制策略设计通过建立合适的数学模型,对液压伺服系统进行分析和仿真,从而寻找系统优化的方向。
同时,针对不同应用场合的需求,设计不同的控制策略,以实现系统的稳定、响应速度提高、能耗降低等目标。
2、传感器和执行器等部件的优化改善传感器、执行器等部件是液压伺服系统的核心部分,其性能的提高能够大大提高系统的控制精度和响应速度。
因此,通过改进传感器的灵敏度和执行器的精度可以进一步优化液压伺服系统的控制能力。
3、液压元器件的优化改进液压元器件是液压伺服系统的重要组成部分,其结构设计的好坏对系统性能影响很大。
因此,通过优化元器件的结构设计,降低元器件的摩擦和漏油等损失,可以进一步提高系统的能效和响应速度。
4、最优化控制算法随着研究的深入,越来越多的最优化控制算法被应用到液压伺服系统中,例如模型预测控制、广义预测控制和神经网络控制等。
伺服压力机偏载调试方法

伺服压力机偏载调试方法伺服压力机是一种利用伺服电机控制液压系统的压力机。
在使用过程中,为了保证设备的工作效率和质量,需要进行偏载调试。
偏载调试是指在没有工作载荷的情况下,对伺服压力机进行调试和优化。
下面将详细介绍伺服压力机偏载调试的方法。
首先,进行系统的初步调整,包括液压系统、伺服电机以及控制系统的参数设定。
液压系统的调整包括调整油泵的压力、速度和流量,确保液压系统的运行平稳。
伺服电机的调整包括调整电机的转速、功率和响应时间等,确保电机的工作效果良好。
控制系统的调整包括调整控制器的增益、反馈和控制信号等,确保控制系统的运行精确。
接下来,进行负载下的程序调整。
在偏载情况下,通过调整控制系统的程序,模拟出工作载荷的情况,检查机械传动、液压控制和电气系统的协调性。
在调整过程中,可以通过改变控制参数来调整伺服系统的运动曲线、速度曲线和力曲线,以实现更加精确的负载调整。
同时,对压力机的运行特性进行测试和分析。
通过测量和分析压力机在不同负载下的压力、速度和力的变化,可以进一步调整和优化控制系统的参数,提高压力机的工作效率和精度。
此外,还可以通过模拟实际工作环境,测试机器在各种工况下的性能和稳定性,以验证机器的负载能力。
最后,进行系统性能测试和调整。
在偏载状态下,进行系统的稳定性、响应速度和界面效果等测试,以评估系统的性能。
根据测试结果,能够进一步调整控制器的参数和算法,提高系统的稳定性和控制精度。
总结来说,伺服压力机的偏载调试是通过系统参数的调整和控制算法的优化,对设备在没有工作载荷下的机械传动、液压控制和电气系统进行调整和优化的过程。
通过偏载调试,可以提高设备的工作效率和质量,提高设备的生产效益。
- 1、下载文档前请自行甄别文档内容的完整性,平台不提供额外的编辑、内容补充、找答案等附加服务。
- 2、"仅部分预览"的文档,不可在线预览部分如存在完整性等问题,可反馈申请退款(可完整预览的文档不适用该条件!)。
- 3、如文档侵犯您的权益,请联系客服反馈,我们会尽快为您处理(人工客服工作时间:9:00-18:30)。
统压力和杆腔的 背压调整适 当,作液压 自身负载控
制 。压 下 液压 缸 上 下 运 动数 次 ,确 认 是 否满 足 位 置
的主要原因。找 出原 因后笔者首先提 出将底座与卷
取机的滚动摩擦副改为滑动摩擦导轨 ,在底座侧受
滤要求特 别严格 。在调试前必须对各路管道及系统
回路 进行 清洁 度 循 环 清 洗处 理 ,油 液 清 洁 度必 须 达
f l j NA S 1 6 3 8 5 ~6 级 ,相 当于q S O 4 4 0 6 标准2 0 / 1 8 级要
求。
状态 ,利 用动态调试 仪器和微机在线调试 ,测试 出 系统的特性 ,进一步校正参数 ,确定满足设计要求
盘车 ,转动灵活、无卡 阻现象后点动电动机确认 方
向 无 误 再 进 入 循 环 泵 及 主 泵 的 调 试 。 ④ 启 动 液 压 泵 ,将 液 压 系统 压 力 调 整 N o . 5 MP a ,拧 松 相 关 排
3 . 现场改进措 施
生 产过 程 中出现 开卷 机 纠 偏 系 统液 压 缸 外 泄 漏 和 工作 辊 夹 紧 不稳 定 问题 ,具体 改进 措 施如 下 : ( I )EP C  ̄ q 偏 系 统 的 伺 服 液 压 缸 使 用一 段 时
处理板、电源板 、编程器板等组成 ,输入板共有 1 4 块 ,用于接收继 电器和光 电管来的信号。输 出板有 2块 ,1 1 2 个直流输 出点,7 2 个交流输出点 ,整机
约4 0 8 个 点 ,控 制 四个 动 力头 上 、 下左 右移 动 及 工 作 台前 后 移 动 ,该 系统 应 用极 不 广 泛 。为 此 ,我 厂 与 北 京机 床 研 究 所 下 属 机 电公 司 合作 对 K2 4 数 控 装
却器、液位液温控制器以及阀站等组成,给A G C 系
统 和 电液 伺 服 阀 提 供一 个稳 定 的 工 作压 力 ,满 足 电
整 颤振信号 的频率 和振幅 ,使分辨 率处于 最高状 态 ;待系统的稳定性 和控制精度指标满足性能要求
后 ,将 系统 压 力 提高 到 工 作 压 力值 ,然 后进 入 闭环 状 态 ,进 行 电气控 制 动 态 调试 ,直 到 满 足控 制 性 能 指 标 为 止 。最 后 与 电 气配 合 将 同路 _ 卜 安 令溢 流 阀进 行标 定后 锁 定保 护 值 。
争 磊 ~ 一 £
7 1
设 备 s 维 修
J L q H i p me n t a n d Ma i n t e na n e e
P L C 与单片机在改造进I 1 设备中的 应用
苏州 苏福马机 械有 限公 司 ( 江苏 2 1 5 1 2 9 ) 陆伟红
以及连 接管路 等装置组 成 ,与计算机 系统 、测厚 仪、位移传感器、压 力传感器等构成位置闭环控制
系统 。
本 台轧 机 选 用 了高精 度 、高 分 辨 率 的位 移 传 感
器和 压 力传 感器 ,实现 连续 线性 反馈控制 ,从而 使 轧制 力波 动 、工作机座 的弹跳 以及其 他 因素对
.
设 备 与 维 修
■ q u i p me n t a n d Mn i n t e n a n c e
拦旦 圭 持 拄盎垒
偏八辊轧机液压伺服系统调试与改进
陕西重 型机械制 造有限公 司 ( 西安 7 1 0 0 3 2 ) 胡 红军
随着国民经济的迅速发展 ,近年来市场 不但对
压 力继 电器 、行程开关等各发讯元件达到系统控制 要求 。⑦确认管道压力试验合格 、油液清洁度化验 合格 、各运动部件状态 良好、电气设备安装完毕满
足 试 车 条 件 后 ,方可 进 入 系 统调 试 。 ⑧压 力调 定 符
护成本 。发现问题后 ,笔者根据 自己多年来的装配 经验结合现场实际情况判断 :这是 由于E P C 液压缸 密封件 因受 力不均匀产 生单侧磨 损 。用量仪进 行 位移检测后 ,发现卷取机作用力中心线与E P C 液压
行最大轧制力压 力 ( 最大极限压力)标定后锁定保
护值。
( 3 )辊 型调 整 系 统 调 试 。 与压 下 系 统 调 试 大
致相 同,油液清洁度及管道试压合格后 ,确认极性 换 装 电液伺 服 阀。电气切换 到开环 状态 ,将 系统
压 力逐 次逐 级 调 整 ,同时 进 行 各液 压 缸 排 气并 试 动 作 。正 常后 电气 进 入 压 力环 、位 置环 手 动 调试 ,调
辊 缝 的 影 响 通 过 液 压 缸 位 置 闭 环 控 制 系统 自动 完
辊稳定性好 ,轧制力小 ,它可以轧制出部分2 0 辊轧 机轧制的产品 ,多用于轧制冷轧难变形钢材 、硅钢
以 及有 色金 属 钢带 ,但 它 的结 构 和 调 整要 比2 0 辊 轧
成补 偿 ,调 整和控 制轧机辊 缝并 实现厚 度 自动控
薄 板 和 宽板 幅 带 材 的需 求 快 速 增长 , 同时 对 带钢 的 质量 要 求 也越 来 越 高 ,因此 对 于 带钢 轧 制 设 备 也提 出 了新 的 要求 。偏 八辊 轧 机 具 有 刚性 较 大 的 辊 系结 构和 独 特 的辊 系调 整 装 置 ,轧 机 总弹 跳 值 小 辊轧机液压伺 服系统 的组 成和功 能
( 1 )辊 型调整 系统 的组 成和功能 。辊型调 整 系统由伺服液压站 、背衬 ( 弯辊 )控制阀组 、背衬
液 压缸 、工 作辊 夹 紧 机构 等 组 成 。
背衬液压缸安装位移传感器应用线 陛反馈控制 ; 液压缸通过铰座带动四块活动斜楔在固定斜楔中上下 移动,这样斜楔移动就可通过侧支承辊和中间辊使工
压缸承受的侧向力使活塞杆伸出困难加速 了密封件
磨 损 。产 生 两 作用 线 交 叉 的根 源 是 因为 卷取 机 与 底 座 在水 平 方 向 做相 对 移 动 ,移 动 副 采 用 的是 滚 动 摩 擦 承受 卷 取 时 的恒 张 力 ,互 为支 点 的 两组 滚 轮 在短 距 离 内往 复运 动 ,滚 轮 表面 与卷 取 机滑 座 受 力 面 以
缝”控制 ,可以获得厚度均匀、高精度带材 。利用 安装在液压缸上的压 力传感器检测液压缸 内的压力 来检测轧制力 ,并将其反馈到压 力闭环 回路 中去 , 以调节轧机厚度控制 系统的刚性并作为动态压力反 馈信号 ,改善系统的动态特性 ,由计算机进行实时 控制和 自动调节 ,从而获得最小的带材纵 向厚度波 动。 “ 恒辊缝 ”控制是提 高带材厚度精 度的主要方
工作辊抱颈装置上并使工作辊与支承辊紧贴 ,保证 工作辊在可逆及高速轧制中都具有可靠的稳定性 ,
能实现在轧制过程中的板形调节 ,用以控制带材横 向厚度的均匀性 ,从而达到控制板形的 目的。因此
统的性 能及其系统工作的可靠性 ,对成品精度起着
非常重要的作用 。在调试前熟悉所需技术文件 ,了 解 系统的控制思想 ,对整个 系统的控制元件和执行 机构要有一定的认识 。 电液伺服 阀是 电液转换元件 ,也是功率放大元 件 ,是电液伺服 系统的核心 。它的工作可靠性直接 影 响到液压伺服系统的性能。电液伺服阀对液压油
的清洁度要求很高 ,油液污染是 引起伺服 阀故障和 液压元件过早磨损甚至损坏的重要原因 ,所以对过
精 度 需 要 。 ⑥进 行 压 下液 压 缸 的位 置 闭环 和压 力 闭
环 的调试 。⑦待系统的稳定性 、控制精度 、动态响 应等指标达到系统控制性能要求后再将系统压 力提
高 到 工 作设 定 压 力值 。⑧ 电 气A G C 系统 切 入 到 闭环
后 并 记 录 。 ⑨ 电气 将 压 下液 压 缸上 的安 全 溢流 阀进
调 试 前 制 定 周 详 的 调试 计 划 ,清理 所 有 设 备 周
围的杂物 ,设置安全设施和标志 ,并对操作者进行 必要培训 ,参与人 员明确分工 ,统一指挥 。做好安
全 文 明生 产 工 作 ,确保 人身 和 设 备 安全 ,使 调 试 工 作 顺利 进 行 。 ( 1 )伺 服 液 压 站 调 试 。伺 服 液 压 站 主 要 由 恒 压 变量 泵 、循 环 泵 、背压 泵 、蓄 能 器 、过 滤 器 、冷
偏八辊液压轧机具有良好的板型控制能力。
( 2 )液压 下伺服系统的组 成和功能 。本 系统
主要 由高 压 泵站 、控 制 阀组 、蓄 能 器 、伺 服 液 压 缸
7 0
,
争磊
棚工
设 备 s 维 修
| l - q u i p me n t a n d Ma r i n t e n a n c e
制 。 另外 伺 服 液 压 缸 行 程 仅 6 0 am ,油柱 高 度低 , r
机简单得 多。也正是在这样的背景下在国内得到普
遍 认 可 ,并 被 广泛 使 用 。 笔者 在7 5 0 am偏 八辊 精 密 r 液 压 轧 机 的安 装 调试 过 程 中 ,总结 了一 些 现场 调 试
俄 罗 斯 乌 里 扬 诺 夫 重 型 及 特 种 机 床 厂 生 产 读 写 存储 器板 、只读 存 储 器 板 、框 格 间联接 板 、微
的UF 5 2 2 5 型龙 门铣床 ,其工作 台长度 8 m,宽度
2 . 5 m ,工作 台最 大 载 重 6 0 t ,是 机 械 制 造 行 业 的 重 要 设 备 ,主 要 用 于 加 工 大 型 机 架 、机 械 框 架 ,其4
可以提高 位置精 度和液 压缸的 固有频率 ,有利于
获 得 最 大 刚 度 ;速 度 响 应 快 ,辊 缝 改 变 0 . 1 mm仅需 0 . 0 5 ~0 . 1 S ;位 置分 辨 率 0 . 0 0 2 mm,能 实现 “ 恒 辊