六角螺母注塑模设计
塑料件镶入螺母的设计,你会吗?

塑料件镶入螺母的设计,你会吗?一、螺母的埋入方式热熔螺母热熔埋置是最常见、最通常的埋入方式,一般以热熔机及手工电烙铁埋钉。
注塑螺母注塑成型埋置一般对螺母的孔径要求很严格,孔径管控在0.05mm以内,因为产品以Molding Pin固定后放置于射出成型模具中,螺母孔径要以注塑成型机的PIN针的大小来管控。
超声螺母超声埋置是一种通过超声振动,使螺母与工件表面及内在分子间的磨擦而使传处到接口的温度升高,当温度达到此工件自身的软化温度时,将螺母埋植于胶件中,当震动停止,工件同时在一定的压力下冷却定形。
二、塑胶孔设计与螺母选择图1 螺母基本尺寸图2 塑胶基本尺寸注:D:螺母外径 L:螺母长度 d:螺母底座 C:塑胶孔径 W:塑胶孔壁厚Y:塑胶孔深三、塑胶孔与螺母的选择参数1、d尺寸为螺母底座,也称导向定位部分,在埋入前与塑胶C部分配合,因此螺母底端d部分要比塑胶BOSS内孔径C尺寸小,以方便定位;2、D尺寸为螺母外径,它与塑胶BOSS内孔径C尺寸相配,一般手机螺母塑胶内孔径比螺母外径小约0.25-0.3mm;3、L尺寸为螺母长度,它与塑胶BOSS孔深度Y尺寸配合,一般塑胶孔深比螺母高(长)度大0.5-1.0mm的深度用于储胶;4、W为塑胶孔壁厚,一般塑胶BOSS孔肉厚为0.8-1.0mm以上,螺母尺寸规格越大,肉厚越大。
(见下表参数)四、塑胶BOSS孔尺寸开立大小的影响若:塑胶与螺母选择上无问题,螺母埋入塑胶后标准状态如图(一)所示若:螺母尺寸太小,塑胶BOSS孔太大,螺母埋入塑胶后吃不到胶,会产生扭拉力不足现象如图(二)所示若:螺母尺寸太大,BOSS孔太小,会产生溢胶或者爆裂现象如图(三)所示如螺母尺寸与塑胶尺寸都没有问题,还有异常现象发生,那我们通常会考虑通过一些优化设计来改善;例1、塑胶BOSS孔深较浅,会产生扭拉力不足由于BOSS孔深度较浅,如选择双斜纹的螺母,在螺母各尺寸比例调配下,特别是压花上,压花段差较短,这样的螺母埋入塑胶后,压花吃胶面的塑胶太少,会产生扭拉力不足现象,所以一般建议,将BOSS孔深设在2.5mm以上,螺母尺寸长度一般建议做2.0mm以上。
螺母注塑模设计1

螺母注塑模设计设计题目产品名称:螺母注塑模 材料:ABS生产批量:大批量生产材料:塑件图毕业设计/论文说明书目录1绪论 (4)2模具工艺规程的制定 (6)3 注塑模的结构设计 (8)4 模具设计的有关计算 (13)5 模具加热与冷却系统的计算 (15)6结构与辅助零部件的设计 (18)7模具闭合高度的确定 (19)8注塑机有关参数的校核 (20)9模具的装配与调试 (16)10制模具总装配图和非标零件图 (24)11塑模主要零件加工工艺规程的编制 (25)12结论.................................................................... . (26)13致谢 (27)14参考文献 (28)插图清单图1-1 螺母零件图图1-2 分型面的选择图1-3 型腔的排列方式图1-4 导柱的形式图1-5 导套的形式图1-6 凸模结构图1-7 凹模结构卡1型芯加工工艺卡卡2型腔加工工艺卡绪论随着工业的发展,工业产品的品种和数量不断增加。
换型不断加快。
使模具的需要补断增加。
而对模具的质量要求越来越高。
模具技术在国民经济中的作用越来越显得更为重要。
模具是制造业的重要工艺基础,在我国,模具制造属于专用设备制造业。
中国虽然很早就开始制造模具和使用模具,但长期未形成产业。
直到20世纪80年代后期,中国模具工业才驶入发展的快车道。
近年,不仅国有模具企业有了很大发展,三资企业、乡镇(个体)模具企业的发展也相当迅速。
虽然中国模具工业发展迅速,但与需求相比,显然供不应求,其主要缺口集中于精密、大型、复杂、长寿命模具领域。
由于在模具精度、寿命、制造周期及生产能力等方面,中国与国际平均水平和发达国家仍有较大差距,因此,每年需要大量进口模具。
中国模具产业除了要继续提高生产能力,今后更要着重于行业内部结构的调整和技术发展水平的提高。
结构调整方面,主要是企业结构向专业化调整,产品结构向着中高档模具发展,向进出口结构的改进,中高档汽车覆盖件模具成形分析及结构改进、多功能复合模具和复合加工及激光技术在模具设计制造上的应用、高速切削、超精加工及抛光技术、信息化方向发展。
六角螺母注塑模设计

计算及说明备注六角螺母注塑模设计1. 塑件的成形工艺性分析:塑件如图1.1所示产品名称:六角螺母产品材料:增计算及说明备注强PA产品数量:大批量生产塑料尺寸:如图1.1所示塑件颜色:黑色塑料要求:塑料外侧表面光滑,下端外沿不允许有浇口痕迹。
图1.1(1)塑料材料特性①基本特征:计算及说明备注③确定分型面塑件分型面的选择应保证塑件的质量要求,因此采用如图所示分型面:④选择浇注系统塑件采用侧浇口系统,其浇注系统如图所示,侧浇口的宽度为1.5mm,侧浇口长度为0.5mm,分计算及说明备注1—定模座板2—轴3—中间板 4.10—导柱5.9—导套6.8—导柱7—动模座板⑦选择成型设备选用G—54—3240/400型卧式注射机,其有关参数:计算及说明备注4.模具的结构设计计算(1)型腔结构如图所示,型腔由定模板,定模镶件,滑块共三部分构成。
定模板和滑块构成塑件的侧壁,定模镶件成形塑件的顶部,而且侧浇口开在定模镶件上,这样使加工方便,有利于型腔的抛光,定模镶件可以更换,提高模具的使用寿命。
计算及说明备注2)模具中有侧向滑动结构时,尽量使其运动方向为水平方向。
3)当模具长度与宽度尺寸相差较大时,应尽可能使较长的边与水平方向平行。
4)模具带有液压油路接头,气路接头,热流道元件接线板时,尽可能放在非操作一侧,以免操作不方便。
模具在注射机上的固定多采用螺钉,压板的形式,如图4.1所示。
一般每侧4~8块压板,对称布置。
模具在注射机上之后,要进行循环调整,并且检查模上各运动机构是否可靠,灵活,定位装置是否能够有效使用。
注塑嵌装铜螺母的设计

注塑嵌装铜螺母的设计在很多塑件中,为了安装,联结等的需要,常常要在塑件中放置一些金属件或其他材质的零件,这些零件,统称为塑料制品中的嵌件。
图所示就是一些嵌件的典型形状(1) 嵌件的特点1) 嵌件多用金属制成,它可以增加塑件整体或某一部位的强度和刚度,如在手柄、箱攀上使用的金属骨杆嵌件,见图所示。
2) 壳以提高联结强度塑料的强度很低,要想把两个塑件联结在一起,如用螺钉联接,其强度要受到影响,而在塑件中事先安放带螺纹的嵌件,可使联结强度大为提高,且经久耐川,见图中所示。
3) 塑料是很好的绝缘体,而在塑件中安放一些金属片、线、板等,使得在电子、电器、电力元器件上大有用途,如图中等。
4) 塑料的硬度较低,抵抗外力的能力较差,在需要提高硬度和耐磨性的位置安放合适的金属嵌件,将有效地提高嵌件的硬度和耐磨性。
(2) 嵌件的材料制作嵌件的材料很多,金属材料和非金属材料均可制作嵌件,但多数以金属材料为主。
常用的金属材料有钢、铜、铝等。
其中,铜合金机械强度高,不生锈、易加工,是制作嵌件的常用材料;但是铜与塑料的热胀系数相差较大,结合牢固性较义;而铝,的热胀系数最大,与塑料的结合最牢固,也是常用材料,但强度较低。
(3) 嵌件的设计要点1) 金属嵌件嵌人塑料部分不能为尖角,应适当倒圆,以减少嵌件周围塑料冷却时产生的应力集中对塑件的影响,提高塑件强度2) 如嵌件设泎塑件上的凸起部位时,其嵌入深度应大于凸起部位的高度,以保证嵌入塑件的机械强度,见图所示3) 嵌件与塑件侧壁的间距一般不得小于0.6mm如塑件相对面都有嵌件, 则两嵌件间所隔塑料层厚不得少于3. 5mmo4) 对于内、外螺纹嵌件,其高度应稍低于型腔的成型高度0.05mm 左右,以免压坏嵌件和模腔,见图所示。
1) 嵌件底面距塑件底面间的塑料层应有一定厚度,一般不小于嵌件外径的1/6,若厚度过小,塑件在此位置易产生凹痕和裂纹等缺陷。
2) 外螺纹嵌件,应设置一段无螺纹区,以防止熔料渗入模具内,见图所示。
螺母注塑模设计

设计题目产品名称:螺母注塑模材料:ABS生产批量:大批量生产目录1绪论 (4)2模具工艺规程的制定 (6)3 注塑模的结构设计 (8)4 模具设计的有关计算 (13)5 模具加热与冷却系统的计算 (15)6结构与辅助零部件的设计 (18)7模具闭合高度的确定 (19)8注塑机有关参数的校核 (20)9模具的装配与调试...... .. (16)10制模具总装配图和非标零件图 (24)11塑模主要零件加工工艺规程的编制 (25)12结论.................................................................... . (26)13致谢 (27)14参考文献 (28)插图清单图1-1 螺母零件图图1-2 分型面的选择图1-3 型腔的排列方式图1-4 导柱的形式图1-5 导套的形式图1-6 凸模结构图1-7 凹模结构卡1型芯加工工艺卡卡2型腔加工工艺卡绪论随着工业的发展,工业产品的品种和数量不断增加。
换型不断加快。
使模具的需要补断增加。
而对模具的质量要求越来越高。
模具技术在国民经济中的作用越来越显得更为重要。
模具是制造业的重要工艺基础,在我国,模具制造属于专用设备制造业。
中国虽然很早就开始制造模具和使用模具,但长期未形成产业。
直到20世纪80年代后期,中国模具工业才驶入发展的快车道。
近年,不仅国有模具企业有了很大发展,三资企业、乡镇(个体)模具企业的发展也相当迅速。
虽然中国模具工业发展迅速,但与需求相比,显然供不应求,其主要缺口集中于精密、大型、复杂、长寿命模具领域。
由于在模具精度、寿命、制造周期及生产能力等方面,中国与国际平均水平和发达国家仍有较大差距,因此,每年需要大量进口模具。
中国模具产业除了要继续提高生产能力,今后更要着重于行业内部结构的调整和技术发展水平的提高。
结构调整方面,主要是企业结构向专业化调整,产品结构向着中高档模具发展,向进出口结构的改进,中高档汽车覆盖件模具成形分析及结构改进、多功能复合模具和复合加工及激光技术在模具设计制造上的应用、高速切削、超精加工及抛光技术、信息化方向发展。
职业学院机械制造与自动化毕业论文-塑料六角形螺母模具结构设计

职业学院机械制造与自动化毕业论文-塑料六角形螺母模具结构设计设计课题: 塑料六角形螺母模具结构设计院 (系): 机电工程系专业: 机械制造与自动化姓名: 杨昌华学号: 5801021201048 指导教师: 刘祥二〇一五年三月二十五日设计课题任务书5801021201048 杨昌华学生姓名学号专业机械制造与自动化机电工程系院(系)塑料六角形螺母模具结构设计设计课题刘祥职称讲师指导教师任务:进行塑料六角形螺母的模具结构设计工作1.查阅模具设计相关资料2.软件绘制模具相关结果三维、平面图要求:独立完成本设计任务,杜绝抄袭现象任务与要求1.格式规整,文字排版好2.论文内容充实,详略得当3.有自己设计内容和构思完成时间段 2014年 10 月 21 日至2015 年 3 月 28 日共 21 周院(系)审核意见年月日声明本人郑重声明:所呈交的毕业设计说明书,是在指导教师的指导下,进行独立工作取得的成果。
除了文中特别加以标注引用的内容外,本说明书中不包含任何其他个人或集体已经发表或撰写过的作品成果。
本人完全明确本声明的法律责任,对本说明书导致的所有问题承担全部责任。
学生签名:杨昌华日期:2015 年3月20日毕业设计说明注意事项1.毕业设计说明主要是针对学生们所设计的作品进行详细的阐述,包括五大部分:课题分析、调研分析、方案绘制与设计题案、课题总结、提交资料。
2.课题分析。
是学生对自己的作品前期的设计现状、设计背景及设计方向、设计思路、设计意图和当前社会的现状作出参照分析的一种阐述。
3.调研分析。
是学生对自己的作品在社会的趋势调查、处境调查、市场调查分析等做出详细的阐述。
4.方案绘制与设计题案。
是学生将设计定位、设计系列草图、展板图等做出说明及展示。
5.课题总结。
是学生通过本次设计获得结论,得到的启发,课题设计的优点与不足作出的阐述。
6.提交资料。
是学生完成课题设计后,需要提交的资料名称与资料内容,用于成绩评定与存档。
最新六角螺母注塑模设计
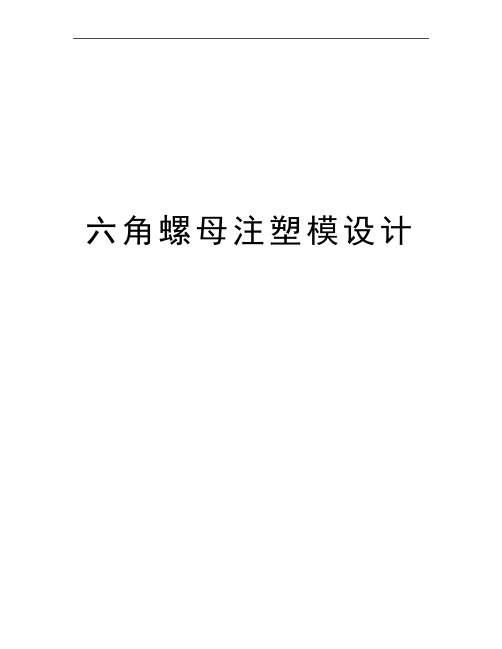
六角螺母注塑模设计精品好文档,推荐学习交流六角螺母注塑模设计1. 塑件的成形工艺性分析:塑件如图1.1所示产品名称:六角螺母产品材料:增强PA精品好文档,推荐学习交流产品数量:大批量生产塑料尺寸:如图1.1所示塑件颜色:黑色塑料要求:塑料外侧表面光滑,下端外沿不允许有浇口痕迹。
图1.1(1)塑料材料特性①基本特征:精品好文档,推荐学习交流PA塑料(聚酰胺)通称为尼龙(Nglon)尼龙是含有酰胺基的线型热塑性树脂,尼龙的这一类塑料的总称。
根据原料的不同,常见的尼龙品种有尼龙1010,尼龙610,尼龙66,尼龙6,尼龙9,尼龙11等。
②使用特性及用途:尼龙有优良的力学性能,抗拉,抗压,耐磨,经过拉伸定向处理的尼龙,其抗拉强度很高,接近于钢的水平,因尼龙的结晶性很高,表面硬度大,摩擦系数小,故具有十分突出的耐磨性和自润滑性,它的耐磨性高于一般用做轴承材料的铜,铜合金,普通钢等。
尼龙耐碱,弱酸,但强酸和氧化剂能侵蚀尼龙。
尼龙的缺点是吸水性能强,收缩率大,常常因吸水而引起尺寸变化,其稳定性较差,一般只能在80°c ~100°c之间使用。
为了进一步改善尼龙的性能,常在尼龙中加入减摩剂,稳定剂,润滑剂,玻璃纤维填料精品好文档,推荐学习交流等,以克服尼龙存在的一些缺点,提高机械强度。
尼龙广泛用于工业上制作各种机械,化学和电器零件。
如轴承,齿轮,辊轴,滚子,滑轮,泵叶轴,风扇叶片。
蜗轮,高压密封扣圈,垫片,输油管,储油容器,绳索,传动带,电池箱,电器线圈等零件,还可将粉状尼龙热喷到金属表面上,以提高耐磨性或作为修复磨损零件之用。
(2)塑料材料成形性能尼龙原料较易吸湿因此在成形加工前必须进行干燥处理,尼龙的热稳定性差,干燥时为避免材料高温时氧化,最好采用真空干燥法;尼龙的熔体黏度较低,流动性好,有利于组成强度特别好的薄壁塑件,但容易产生飞边,故模具必须使用最小间隙,熔融状态的尼龙热稳定性较差,易发生降解使塑料性能下降,因此不允许尼龙在高温料筒内停留过长时间,尼龙成形收缩率范围及收缩率大,方向性明显,易精品好文档,推荐学习交流产生缩孔,凹痕,变形等缺陷,因此应严格控制成形工艺条件。
注塑预埋螺母壁厚设计
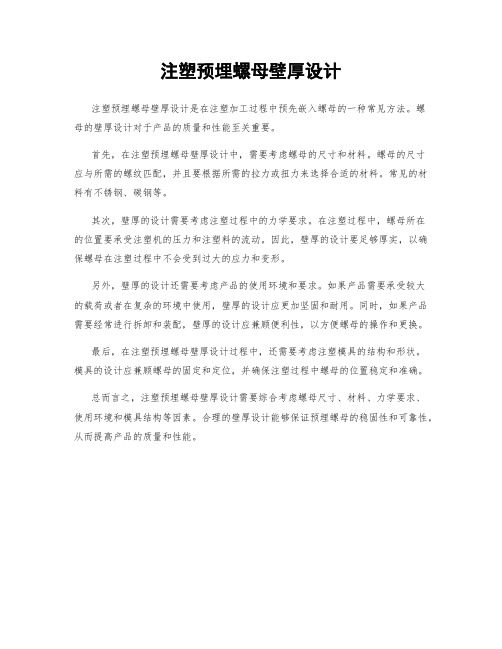
注塑预埋螺母壁厚设计
注塑预埋螺母壁厚设计是在注塑加工过程中预先嵌入螺母的一种常见方法。
螺
母的壁厚设计对于产品的质量和性能至关重要。
首先,在注塑预埋螺母壁厚设计中,需要考虑螺母的尺寸和材料。
螺母的尺寸
应与所需的螺纹匹配,并且要根据所需的拉力或扭力来选择合适的材料。
常见的材料有不锈钢、碳钢等。
其次,壁厚的设计需要考虑注塑过程中的力学要求。
在注塑过程中,螺母所在
的位置要承受注塑机的压力和注塑料的流动。
因此,壁厚的设计要足够厚实,以确保螺母在注塑过程中不会受到过大的应力和变形。
另外,壁厚的设计还需要考虑产品的使用环境和要求。
如果产品需要承受较大
的载荷或者在复杂的环境中使用,壁厚的设计应更加坚固和耐用。
同时,如果产品需要经常进行拆卸和装配,壁厚的设计应兼顾便利性,以方便螺母的操作和更换。
最后,在注塑预埋螺母壁厚设计过程中,还需要考虑注塑模具的结构和形状。
模具的设计应兼顾螺母的固定和定位,并确保注塑过程中螺母的位置稳定和准确。
总而言之,注塑预埋螺母壁厚设计需要综合考虑螺母尺寸、材料、力学要求、
使用环境和模具结构等因素。
合理的壁厚设计能够保证预埋螺母的稳固性和可靠性,从而提高产品的质量和性能。
塑料法兰螺母注射模设计

《模具工业》 !""#$ %& $ ’ 总 !("
! "#$%&’( )*+ ,#&-.#%& /0(#123%. 45 67 ,.8 67 9#:-3%& 7 "#$%&’( ;<<=>>7 4-#%$ ? !"#$%&’$ * +-@5(&- .-3 .3A-%5B5&#A$B $%$BC’#’ 5D .-3 1B$’.#A DB$%&3 %(. 1$@. 7 .-3 8#DD#A(B.C D5@ 83’#&%#%& .-3 25(B8 D5@ .-3 1$@. -$’ E33% D5(%8 5(. 6 F% #%.3@%$B A5@3G1(BB#%& ’.@(A.(@3 H#.- .H5G’.31 1$@.#%& #’ #%.@58(A38 6 +-#’ ’.@(A.(@3 A$% 3%’(@3 .-3 1@58(A.’ .5 D$BB D@33BC 7 .-(’ @3$B#:3 $(.52$.#A 1@5G 8(A.#5% 6 +-#’ 25(B8 ’.@(A.(@3 #’ ’#21B3 $%8 3$’C .5 2$%(D$A.(@3 6 I@$A.#A$B 1@58(A.#5% J3@#D#38 .-$. .-3 513@$.#5% 5D .-3 25(B8 #’ @3B#$EB3 $%8 8325(B8#%& 5D .-3 1B$’.#A 1$@.’ #’ ’255.- 6 ()*+,%-# * .H5G’.31 1$@.#%& K #%.3@%$B A5@3G1(BB#%& K D@33 D$BB K $(.52$.#A 1@58(A.#5% 6
螺丝注塑模具工程图绘制

2.1对Pro/E 转过来的图进行处理打开AUTOCAD,打开Pro/E 转过来的图,即DRW0001.DXF 文件,运行“带基点复制”命令,将图复制到一个新建的公制文件,点击“产品”层,将当前层设置为产品层,然后使用模具工具工具条中的“输入图元自动分层”,按图2-1所示设置。
将图元归为产品层。
图2-1复制一份,删除一些不必要的图元,留作接下来设计用。
如图2-2所示。
分完层后,还需检查一下产品的尺寸是否失真,和3D 模型是否对得上。
图2-22.2镜像、做产品基准、放缩水将前后模视图做镜像,侧视图不用做镜像。
可选取产品上特殊部位做镜像对称线 ,或者直接用模板对称中心线。
如图2-3所示。
图2-3把产品各个视图做成块,注意也要将整个块归入产品层;然后再放缩水,全部做完,要在图上打入标记进行区分。
2.3 定模仁、调模架模仁是在分模阶段定下来的,尺寸及外形都是事先定好的在这里不在叙述。
因为是一模八腔,所以产品间距和流道空间都是经过仔细推算得出来的,分模时的模仁毛坯大小如图2-6所示如图2-6模架的尺寸可按模仁的尺寸单边取50mm来算,其中厚度尺寸,前模仁加25mm,后模仁加30mm。
理论上是这样算的,但是如果按这样的尺寸定下模架的话,在后续做滑块的时候遇到问题,就是滑块的侧抽距离较大,SL=15+(3-5)mm。
所以在导柱倾角18度不变的话,势必会引起B板尺寸加大,为了整体的协调性,A和C 板也要跟着发生相应变化。
综合考虑这些,本套模具的模架尺寸我是这样定的:模仁尺寸为80×130,单边加50mm后,再稍微变化一点,变为250×250;前模仁厚度为20,则A板可取50;后模仁厚度为20,则B板可取80;根据以上数据,可调用模架2525,也可以通过量取模仁X,Y来确定模架大小。
在“模具标准件”中点击模胚工具按钮,在弹出的模胚工具框中,按如下参数设置。
如图2-7所示。
设置好参数后,调入的模架如图2-8所示。
内六角螺钉注塑模具的标准零部件
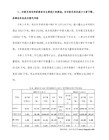
第4章 注塑模具的标准零部件
4.1 概 述 4.2 注塑模具标准模架
1 、 模 架 的 定 义 与 用 途
2、模架的组成结构及其称谓
3 、 模 架 的 分 类
4、模架规格的表示方法
第4章 注塑模具的标准零部件
4.2 注塑模具标准模架
1、模架的定义与用途 模架的定义:模架也称为模胚。由模板、导柱和 导套等零件组成,但型腔未加工的组合体。 型芯、型腔、定位环、浇口套、顶杆、滑块机构 等部件须安装到模架上才构成一套完整的模具。 模架的用途:保证了凸凹模在开合模时能正确对 准,起连接、固定、导向的作用。
第4章 注塑模具的标准零部件
细水口模架的八种形式 •定模部分:有水口推板与无水口推板
DA EA 第一个D DB EB DC EC DD ED A B C 有垫板,无推板 有垫板,有推板 无垫板,无推板
有水口推板
D
E 无水口推板
无垫板, 有推板
第4章 注塑模具的标准零部件
定模部分带水口推板(弹料板)
F
G
有水口推板
无水口推板
A
C
有垫板
无垫板
第4章 注塑模具的标准零部件
4、模架规格的表示方法
4045 DC I A板 80 B板 90 C板 150 300
第4章 注塑模具的标准零部件
4.3 注塑模具标准模架的选用
根据图4-7所示的塑料件,说明怎样选用模架。
影响选用模架的因素: • 塑件的尺寸大小、形状 • 模具设计师的设计风格 • 模具制造所具有的生产设备有关
• 产品较高,对型芯的包紧力较大 时,此时顶杆的推出力不够,无 法满足产品顶出的需要。 产品是透顶时,没有合适的位置 安排顶出杆。
PROE三维建模 六角螺母
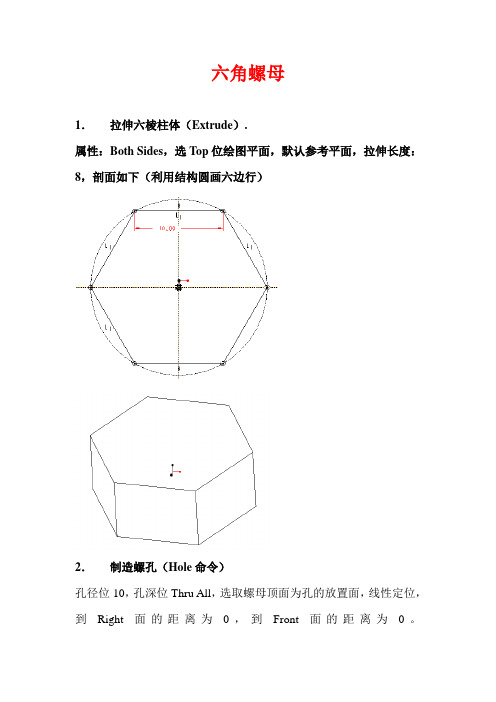
六角螺母
1.拉伸六棱柱体(Extrude).
属性:Both Sides,选Top位绘图平面,默认参考平面,拉伸长度:8,剖面如下(利用结构圆画六边行)
2.制造螺孔(Hole命令)
孔径位10,孔深位Thru All,选取螺母顶面为孔的放置面,线性定位,到Right面的距离为0,到Front面的距离为0。
3.制作旋转切面(Cut Revolve)
属性:OneSide,选择一个跨过对角的两条棱的面为绘图平面,选择Top在选零件顶面为参考平面。
旋转角度为360,剖面如下
4.复制旋转切面(Copy->Mirror)
5.倒角
45xd的倒角,边长为0.5,螺母内圆柱面的两端边。
6.制作螺纹(Advanced->Helical Swp)
属性用默认的,绘图平面为Right,选取螺母的轴线和圆柱的边界作为参考线。
做一条中心线过圆柱的轴线,做一条直线和圆柱的边重合和两端相连。
输入螺距为1.5。
绘制剖面。
六角头螺栓的成型工艺分析与成型模具设计

六角头螺栓的成型工艺分析与成型模具设计(,,, ,届) 本科毕业设计六角头螺栓的成型工艺分析与成型模具设计 I 摘要本次设计的课题是六角头螺栓的成型工艺分析与成型模具设计。
六角头螺栓属于紧固件,在各个领域都有广泛应用。
在设计过程中,通过查阅大量资料、手册、期刊等,结合教材上的知识对锻造模具有了系统的认识,拓宽了视野,丰富了知识,为将来独立完成模具设计积累了一定的经验。
设计过程包括设计准备、六角螺栓的制造工艺确定、模具设计、零件图的绘制和毕业设计论文的完成等五个环节。
其中,六角螺栓的制造工艺确定和模具设计是重要环节。
在六角头螺栓工艺的确定过程中,主要对螺栓的算料、下料,尤其是加热规范进行了详细的分析,并且对六角的成型工步进行了计算。
在整个模具设计过程中,使用一模三腔的形式,涉及到了锻件的结构设计、平锻机的选择、镦粗比的确定、分型面的确定及型槽分布,其中,对锻件的局部镦粗规则进行的详细的分析,从而更准确的制造出模具的形状。
在模具设计过程中主要运用了 UG 6.0 模块来完成整个设计工作,此外还利用了AutoCAD2004 软件进行装配图及零件图的绘制。
关键词:螺栓;加热规范 ;模锻;局部镦粗 II Hex head bolt forming process analysis and molddesign Abstract This subject of this design is about the molding process analysis ofthe hex head bolt and its mold design. Hexagon head bolts are fastenerswidely used in various fields. During the designing process throughaccessing to a large amount of data manuals and journals I have asystematic knowledge of forging combined with the textual knowledgewhich helps to broaden the horizon and enrich the related knowledge ofmold design. It enables me to accumulate some experience of mold designin order to accomplish independently the design in the future. There are totally five procedures including design preparation amanufacturing process to determine the hex bolts mold design partmapping and the completion of designing thesis. Among them in thehexagonal bolt manufacturing process the main operation is thecalculation of the bolt material cutting especially a detailed analysisof heating rules. Whats more the work of the hexagon formingstep werecalculated. In the entire mold design process by using a model with three cavitieswhich relates to the structural design of forging machine selection ofthe flat forging ratio determination of upsetting determination ofparting and distribution of groove. Moreover a more detailed analysisof the rules for forgings local upsetting is carriedout thus a morecorrect shape of the mold is acquired. In the mold design process the function of the UG 6.0 module is appliedto complete thewhole design. In addition the software called AutoCAD2004is used for assembly and part drawing.Keywords: Bolts;Heating Specifications ;Forging ;Upsetting III 目录摘要.................................................................. .........................................................IIAbstract ......................................................... ...............................................................III1 绪论...................................................................... (1)1.1 课题的来源...................................................................... ................................ 1 1.2 课题的意义...................................................................... ................................ 1 1.3 锻造工艺的相关研究的最新成果及动态...................................................... 2 1.4 课题研究的主要内容...................................................................... ................ 52 螺栓的成形工艺分析.................................................................. ............................... 6 2.1 六角头螺栓成形方案设计...................................................................... ....... 6 2.2 六角头螺栓成型工艺………………………………………………………..6 2.2.1 材料的选择.................................................................. ....................... 7 2.2.2 算料.................................................................. ................................... 7 2.2.3 下料...................................................................... ............................... 9 2.2.4 坯料加热...................................................................... ..................... 11 2.2.5 锻造温度范围...................................................................... ............. 13 2.2.6 加热规范.................................................................. ......................... 143 锻模设计...................................................................... ............................................. 16 3.1 锻模选料...................................................................... .................................. 16 3.2 设备选择...................................................................... .................................. 16 3.3 局部镦粗规则...................................................................... .......................... 17 3.4 分型面确定...................................................................... .............................. 21 3.5 锻模设计...................................................................... .................................. 22 3.5.1 锻模模块选择...................................................................... ............. 22 3.5.2 型槽分布.................................................................. ......................... 23 3.5.3 模壁厚度...................................................................... ..................... 24 3.5.4 模块尺寸...................................................................... ..................... 25结论.................................................................. ............................................................ 27参考文献...................................................................... ................................................ 28致谢...................................................................... ........................................................ 29附录...................................................................... ........................................................ 30 IV 六角头螺栓的成型工艺分析与成型模具设计 1 绪论1.1 课题的来源我院与海盐诸多知名标准件生产企业建立了合作项目—浙江海盐标准间科技创新服务平台建设,本设计以此项目为依托,以典型标准件-六角螺栓为研究对象,分析确定成型工艺,设计成型用模具。
- 1、下载文档前请自行甄别文档内容的完整性,平台不提供额外的编辑、内容补充、找答案等附加服务。
- 2、"仅部分预览"的文档,不可在线预览部分如存在完整性等问题,可反馈申请退款(可完整预览的文档不适用该条件!)。
- 3、如文档侵犯您的权益,请联系客服反馈,我们会尽快为您处理(人工客服工作时间:9:00-18:30)。
六角螺母注塑模设计计算及说明备注六角螺母注塑模设计1. 塑件的成形工艺性分析:塑件如图1.1所示产品名称:六角螺母产品材计算及说明备注料:增强PA产品数量:大批量生产塑料尺寸:如图1.1所示塑件颜色:黑色塑料要求:塑料外侧表面光滑,下端外沿不允许有浇口痕迹。
图1.1(1)塑料材料特性①基本特征:计算及说明备注PA塑料(聚酰胺)通称为尼龙(Nglon)尼龙是含有酰胺基的线型热塑性树脂,尼龙的这一类塑料的总称。
根据原料的不同,常见的尼龙品种有尼龙1010,尼龙610,尼龙66,尼龙6,尼龙9,尼龙11等。
②使用特性及用途:尼龙有优良的力学性能,抗拉,抗压,耐磨,经过拉伸定向处理的尼龙,其抗拉强度很高,接近于钢的水平,因尼龙的结晶性很高,表面硬度大,摩擦系数小,故具有十分突出的耐磨性和自润滑性,它的耐磨性高于一般用做轴承材料的铜,铜合金,普通钢等。
尼龙耐碱,弱酸,但强酸和氧化剂能侵蚀尼龙。
尼龙的缺点是吸水性能强,收缩率大,常常因吸水而引起尺寸变化,其稳定性较差,一般只能在80°c~100°c之间使用。
计算及说明备注为了进一步改善尼龙的性能,常在尼龙中加入减摩剂,稳定剂,润滑剂,玻璃纤维填料等,以克服尼龙存在的一些缺点,提高机械强度。
尼龙广泛用于工业上制作各种机械,化学和电器零件。
如轴承,齿轮,辊轴,滚子,滑轮,泵叶轴,风扇叶片。
蜗轮,高压密封扣圈,垫片,输油管,储油容器,绳索,传动带,电池箱,电器线圈等零件,还可将粉状尼龙热喷到金属表面上,以提高耐磨性或作为修复磨损零件之用。
(2)塑料材料成形性能尼龙原料较易吸湿因此在成形加工前必须进行干燥处理,尼龙的热稳定性差,干燥时为避免材料高温时氧化,最好采用真空干燥法;尼龙的熔体黏度较低,流动性好,有利于组成强度特别好的薄壁塑件,但容易产生飞边,故模计算及说明备注具必须使用最小间隙,熔融状态的尼龙热稳定性较差,易发生降解使塑料性能下降,因此不允许尼龙在高温料筒内停留过长时间,尼龙成形收缩率范围及收缩率大,方向性明显,易产生缩孔,凹痕,变形等缺陷,因此应严格控制成形工艺条件。
2. 塑件的成形工艺参数确定查有关手册得到PA(增强)塑料的成形工艺参数如下:注射机类型:螺杆式螺杆转速20~40rpm密度 1.4 ~1.6g /cm³收缩率0.3%~0.5 %预热时间2~3h料筒温度后段210°c~225°c计算及说明备注中段230°C~250°c前段235°c~255°c喷嘴温度240°c~255°c模具温度(℃)50~80注射压力90~130Mpa烘干温度90°c~110°c烘干时间6~12h保压压力50~70 MPa成形时间注射时间15~40s保压时间0~5 s冷却时间20~150 s3.模具的基本结构及模架选择(1)模具的基本结构①确定成形方法计算及说明备注塑件采用注射成形法生产,为保证塑件表面质量,使用侧浇口成型,因此模具应为单分型面注射模。
②型腔分布塑件形状较简单,质量较小,生产批量大,所以应采用多型腔注射模具,此模具采用一模三腔平衡布置,这样吗尺寸较小,制造方便,生产率高,塑件成本低,其布置如图所示:③确定分型面塑件分型面的选择应保证塑件的质量要求,因计算及说明备注此采用如图所示分型面:④选择浇注系统塑件采用侧浇口系统,其浇注系统如图所示,侧浇口的宽度为1.5mm,侧浇口长度为0.5mm,分流道采用半圆截面流动,其半径R为3~3.5mm,主流道为圆锥形,上部直径与注射机喷嘴相配合,下部直径为φ6~φ8mm。
⑤确定推出方式由于塑件形状为六边形且壁厚较薄,使用推杆推出容易在塑件上留下推出痕迹,不宜采用,所以选模内自动脱螺纹机构,这种方法能尽量保证塑件在动模一侧推出力均匀,塑件在推出时变形小,推出可靠。
⑥模具的结构形式计算及说明备注模具结构为单分型面注射模,采用螺纹拉杆控制分型面 A.A的打开距离,其最大分型面应大于40mm,方便取出制件,模具分型面的打开顺序由螺纹拉杆控制。
计算及说明备注1—定模座板2—轴3—中间板 4.10—导柱5.9—导套6.8—导柱7—动模座板⑦选择成型设备选用G—54—3240/400型卧式注射机,其有关参数:额定注射量 200/400 m³注射压力109Mpa锁模力2540KN 最大注射面积645 cm³模具厚度165~406mm 最大开合模行程260mm喷嘴圆弧半径18mm 喷嘴孔直径4mm拉杆间距290mm×368mm(2)选择模距①模架的选择计算及说明备注模架的选择如图所示②模架安装尺寸校核模具外形尺寸为长300mm,宽120mm,高150mm,小于注射机拉杆间距和最大模具厚度,可以方便的安装在注射机上。
计算及说明备注4.模具的结构设计计算(1)型腔结构如图所示,型腔由定模板,定模镶件,滑块共三部分构成。
定模板和滑块构成塑件的侧壁,定模镶件成形塑件的顶部,而且侧浇口开在定模镶件上,这样使加工方便,有利于型腔的抛光,定模镶件可以更换,提高模具的使用寿命。
(2)型心结构如图所示,型芯是由动模板上的孔固定,型芯于推板采用锥面配合,以保证配合的紧密,防止塑件产生飞边。
另外锥面配合可以减少推件板在推件动时与型芯之间的磨损,型芯中心开有冷却水孔,用来冷却型芯。
(3)导柱、滑块结构如图装配图所示计 算 及 说 明 备 注(4) 模具的导向机构为了保证模具的闭合精度,模具的定模部分和动模部分采用导柱和导套导向定位,推件板上装有导套,推出推件时,导套在导柱上运动,保证了推件板的运动精度。
定模板上装有导柱,为浇口凝料推板和定模座板的运动导向。
5. 模具成形尺寸设计计算(1)取PA 的平均收缩率为0.4%,塑件未注公差按照STBT2中8级精度公差值选取。
a.型腔径向尺寸模具最大磨损量选取塑件公差的1/6,模具的制造公差3z δ∆=,取0.75x = ①0.02800.0283636.28+-→0(1)[(1)1]zz Lm S Ls x δδ-++=+-∆ 0.090[(10.4%)36.280.750.28]+=+⨯-⨯ 0.09050.68+=计 算 及 说 明 备 注 ②0.240.245 5.24R R +-→00(2)[(1)2]zz Lm S Ls x δδ-++=+-∆0.080[(10.4%) 5.240.750.24]+=+⨯-⨯ 0.0805.08+=b.型腔深度尺寸模具最大磨损量选取塑件公差的1/6,模具的制造公差3z δ∆=,取0.5x = 公式 00()[(1)]zz Hm S Hs x δδ-++=+-∆式中Hs —塑件的高度最大尺寸①0.280.284.540.28+-→ 00(1)[(1)]zz Hm S Hs x δδ-++=+-∆0.080[(10.4%)40780.50.28]+=+⨯-⨯0.0804.83+= ②0.280.286 6.28+-→00(2)[(1)]zz Hm S Hs x δδ-++=+-∆计 算 及 说 明 备 注 0.080[(10.4%) 6.280.50.28]+=+⨯-⨯0.08018.59+=c.型芯径向尺寸型芯径向尺寸计算公式为:()[(1)1]z z LS S Ls x δδ---=++∆ 式中Ls —塑件内形的最小尺寸,最大磨损量选取塑件公差的1/6,模具的制造公差3z δ∆=,取0.75x = 0.260.263030φφ++→()[(1)1]z z Ls S Ls x δδ---=++∆00.26[(10.4%)300.750.26]-=+⨯+⨯00.2630.39-=d.型芯高度尺寸型芯高度尺寸计算公式为:0()[(1)1]z z HS S Hs x δδ---=++∆ 式中Hs —塑件的内形深度最小尺寸,最大磨损量取塑件公差的1/6,模具的制造公差3z δ∆=,取0.5x =计 算 及 说 明 备 注 1.2 1.248.448.4++→()[(1)1]z z Hs S Hs x δδ---=++∆ 00.40[(10.4%)48.40.5 1.2]-=+⨯+⨯00.4049.29-=6.模具的加热、冷却系统① 模具加热一般生产PA 材料塑件的模具不需要外加热。
② 模具冷却为了循环模具成形的生产周期,需要对模具进行冷却,常用水对模具进行冷却,即在注塑完成后通循环水到靠近型腔的零件孔内,以便迅速使模具冷却,设计水道要注意到以下几点:冷却数量(水道)尽可能多,孔径尺寸能大,冷却水孔中心线与型腔壁的距离为冷却通道直径的1~2倍,冷却通道之间的中心距为水孔直径的3~5倍,通道直径一般在8mm 以上。
冷却水孔至型腔表面的距离,应尽可能相等,计算及说明备注当塑件厚壁均匀时,冷却水孔与型腔表面的距离应相等,塑件厚壁不均匀时,应在厚壁处强化冷却。
浇口处需强化冷却。
冷却水孔道不应穿过镶块或其接缝部分,以防漏水。
冷却水孔应避免设计在塑料的熔接痕处。
进出水口管接头的位置应尽可能设在模具的同一侧,通常设在注射机的背面。
7.型腔厚壁的确定型腔厚壁的确定从理论上讲是通过力学的刚度及强度公式进行计算的,刚度不足将产生过大的弹性变形而产生溢料间隙,强度不足将会产生塑料变形,并可能破裂。
由于塑件成形受温度压力,塑件特性及塑件复杂程度等因素的影响,所以理论计算并不能完全确定真实的反映结果,所以通常模具型腔厚壁不通过计算,通过经验确定。
8.冷料穴和拉料杆的确定冷料穴是浇注系统内的结构构成之一,冷料穴的作用是容纳浇注系统道中的前锋冷料,以免让冷计算及说明备注料注入型腔,多型腔模具分型面上有几个冷料穴。
9.排气方式设计(1)排气槽设计多种排气方式对于中型塑件的模具,对于本模具不必设计。
(2)行型面排气对于本模具可以加以利于(3)利于型芯,顶杆,镶拼块等间隙排气,本模具主要型芯,顶杆,镶件的间隙排气。
10.模具成形零件的结构(1)型芯的结构设计由于塑件结构复杂,尺寸较小,因此本模具的型芯由几个型芯镶块拼合组成,才能保证塑件的成形。
(2)镶块的设计镶块是组成型腔的一部分,镶块之间用楔块连接。
五.注射机参数的校核1.最大注塑量的校核M机≥M实/ α =(nM 塑+M浇)/ α计算及说明备注式中M机—注射机的最大注塑量M实—实际注塑量α—注塑系数,一般取为0.8n—型腔个数M 塑—每个塑件的质量M浇—浇注系统的质量当实际注塑量以注塑容量V实表示时,有M'实= ρ'V实式中M'实—注塑塑料密度为ρ'时的实际注塑量V实—实际注塑量ρ'—Cρ式中ρ—注塑塑件在常温下的密度C—塑化温度和压力下塑料密度变化的校正系数,对结晶型塑料,C=0.85,对于非结晶型塑料C=0.93.当实际注塑量以注塑量M实表示时,有M'实= M实(ρ/ Aρρ)式中Aρρ—聚酰胺在常温下的密度cmV机—200~400 3mm而 V塑—12×8.5=102 3计算及说明备注cmV浇—40 2cmV机—102+40/0.8=177.53cm,所以满而选定的注射机注塑量大于177.53足要求。