脱氧方法对钢中氧含量的影响[1]
钢的脱氧程度
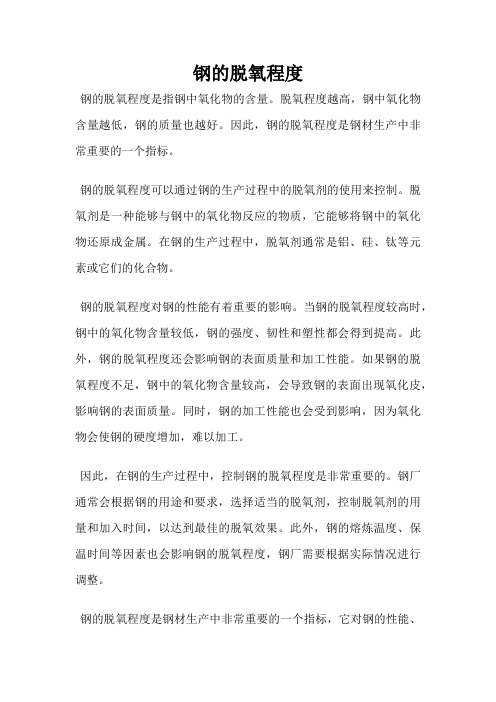
钢的脱氧程度
钢的脱氧程度是指钢中氧化物的含量。
脱氧程度越高,钢中氧化物含量越低,钢的质量也越好。
因此,钢的脱氧程度是钢材生产中非常重要的一个指标。
钢的脱氧程度可以通过钢的生产过程中的脱氧剂的使用来控制。
脱氧剂是一种能够与钢中的氧化物反应的物质,它能够将钢中的氧化物还原成金属。
在钢的生产过程中,脱氧剂通常是铝、硅、钛等元素或它们的化合物。
钢的脱氧程度对钢的性能有着重要的影响。
当钢的脱氧程度较高时,钢中的氧化物含量较低,钢的强度、韧性和塑性都会得到提高。
此外,钢的脱氧程度还会影响钢的表面质量和加工性能。
如果钢的脱氧程度不足,钢中的氧化物含量较高,会导致钢的表面出现氧化皮,影响钢的表面质量。
同时,钢的加工性能也会受到影响,因为氧化物会使钢的硬度增加,难以加工。
因此,在钢的生产过程中,控制钢的脱氧程度是非常重要的。
钢厂通常会根据钢的用途和要求,选择适当的脱氧剂,控制脱氧剂的用量和加入时间,以达到最佳的脱氧效果。
此外,钢的熔炼温度、保温时间等因素也会影响钢的脱氧程度,钢厂需要根据实际情况进行调整。
钢的脱氧程度是钢材生产中非常重要的一个指标,它对钢的性能、
表面质量和加工性能都有着重要的影响。
钢厂需要通过选择适当的脱氧剂、控制脱氧剂的用量和加入时间等措施,来控制钢的脱氧程度,以达到最佳的脱氧效果。
探讨炼钢生产中转炉炼钢脱氧工艺
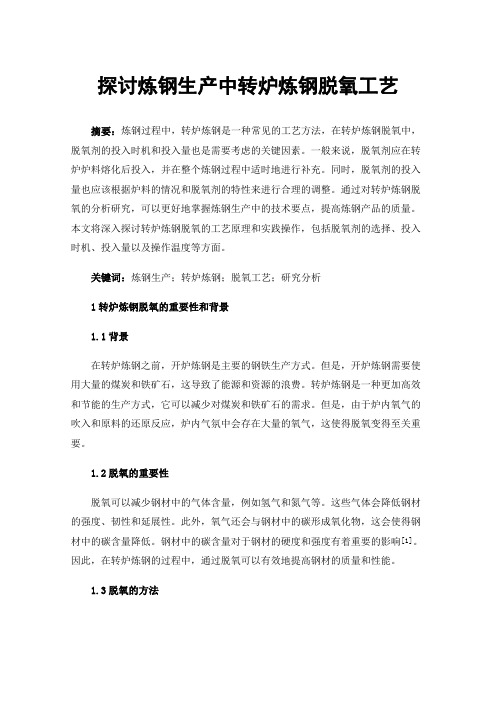
探讨炼钢生产中转炉炼钢脱氧工艺摘要:炼钢过程中,转炉炼钢是一种常见的工艺方法,在转炉炼钢脱氧中,脱氧剂的投入时机和投入量也是需要考虑的关键因素。
一般来说,脱氧剂应在转炉炉料熔化后投入,并在整个炼钢过程中适时地进行补充。
同时,脱氧剂的投入量也应该根据炉料的情况和脱氧剂的特性来进行合理的调整。
通过对转炉炼钢脱氧的分析研究,可以更好地掌握炼钢生产中的技术要点,提高炼钢产品的质量。
本文将深入探讨转炉炼钢脱氧的工艺原理和实践操作,包括脱氧剂的选择、投入时机、投入量以及操作温度等方面。
关键词:炼钢生产;转炉炼钢;脱氧工艺;研究分析1转炉炼钢脱氧的重要性和背景1.1背景在转炉炼钢之前,开炉炼钢是主要的钢铁生产方式。
但是,开炉炼钢需要使用大量的煤炭和铁矿石,这导致了能源和资源的浪费。
转炉炼钢是一种更加高效和节能的生产方式,它可以减少对煤炭和铁矿石的需求。
但是,由于炉内氧气的吹入和原料的还原反应,炉内气氛中会存在大量的氧气,这使得脱氧变得至关重要。
1.2脱氧的重要性脱氧可以减少钢材中的气体含量,例如氢气和氮气等。
这些气体会降低钢材的强度、韧性和延展性。
此外,氧气还会与钢材中的碳形成氧化物,这会使得钢材中的碳含量降低。
钢材中的碳含量对于钢材的硬度和强度有着重要的影响[1]。
因此,在转炉炼钢的过程中,通过脱氧可以有效地提高钢材的质量和性能。
1.3脱氧的方法转炉炼钢中有两种主要的脱氧方法,即硅脱氧和铝脱氧。
硅脱氧是最常用的方法,它通过在炉内加入硅来将氧气与硅反应,从而减少炉内氧气含量。
硅脱氧可以有效地减少氧气含量,但同时也会增加钢材中硅的含量。
铝脱氧则是一种更加高效的脱氧方法,它可以将氧气与铝反应,从而减少氧气含量,同时不会增加钢材中其他元素的含量。
铝脱氧可以生产出更加纯净的钢材。
2氧化铝脱氧法在转炉炼钢中的应用2.1背景在传统的转炉炼钢过程中,气氛中存在大量的氧气,这会使钢中存在过多的气体,如氮气、氧气和氢气等。
这些气体会导致钢中的气孔和夹杂物增多,从而降低钢的质量和性能。
钢中脱氧反应
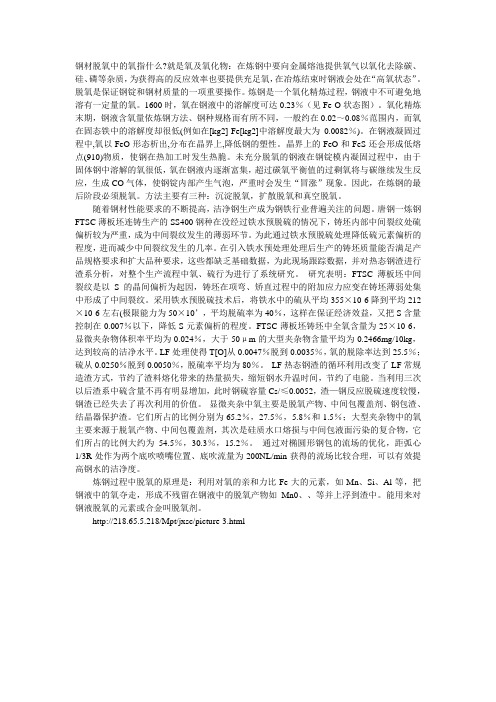
钢材脱氧中的氧指什么?就是氧及氧化物:在炼钢中要向金属熔池提供氧气以氧化去除碳、硅、磷等杂质,为获得高的反应效率也要提供充足氧,在冶炼结束时钢液会处在“高氧状态”。
脱氧是保证钢锭和钢材质量的一项重要操作。
炼钢是一个氧化精炼过程,钢液中不可避免地溶有一定量的氧。
1600时,氧在钢液中的溶解度可达0.23%(见Fe-O状态图)。
氧化精炼末期,钢液含氧量依炼钢方法、钢种规格而有所不同,一般约在0.02~0.08%范围内,而氧在固态铁中的溶解度却很低(例如在[kg2]-Fe[kg2]中溶解度最大为0.0082%)。
在钢液凝固过程中,氧以FeO形态析出,分布在晶界上,降低钢的塑性。
晶界上的FeO和FeS还会形成低熔点(910)物质,使钢在热加工时发生热脆。
未充分脱氧的钢液在钢锭模内凝固过程中,由于固体钢中溶解的氧很低,氧在钢液内逐渐富集,超过碳氧平衡值的过剩氧将与碳继续发生反应,生成CO气体,使钢锭内部产生气泡,严重时会发生“冒涨”现象。
因此,在炼钢的最后阶段必须脱氧。
方法主要有三种:沉淀脱氧,扩散脱氧和真空脱氧。
随着钢材性能要求的不断提高,洁净钢生产成为钢铁行业普遍关注的问题。
唐钢一炼钢FTSC薄板坯连铸生产的SS400钢种在没经过铁水预脱硫的情况下,铸坯内部中间裂纹处硫偏析较为严重,成为中间裂纹发生的薄弱环节。
为此通过铁水预脱硫处理降低硫元素偏析的程度,进而减少中间裂纹发生的几率。
在引入铁水预处理处理后生产的铸坯质量能否满足产品规格要求和扩大品种要求,这些都缺乏基础数据,为此现场跟踪数据,并对热态钢渣进行渣系分析,对整个生产流程中氧、硫行为进行了系统研究。
研究表明:FTSC薄板坯中间裂纹是以S的晶间偏析为起因,铸坯在项弯、矫直过程中的附加应力应变在铸坯薄弱处集中形成了中间裂纹。
采用铁水预脱硫技术后,将铁水中的硫从平均355×10-6降到平均212×10-6左右(极限能力为50×10’,平均脱硫率为40%,这样在保证经济效益,又把S含量控制在0.007%以下,降低S元素偏析的程度。
Q235钢的脱氧合金化方案优化探讨

Q235钢脱氧合金方案优化探讨摘要:改变以往的Si-Mn脱氧方式,改用Si-Mn-Al脱氧使钢液内的夹杂物能够尽量的变成液体夹杂而充分上浮排除,保证钢液内合适的Als含量以保证浇注过程不发生结流现象。
关键词:夹杂物的变性处理酸熔铝一、现状去年,是炼钢厂产量规模再上一个台阶、品种开发全面实施最为关键的一年,而炼钢工序作为保证集团公司顺利实施品种开发,拓宽产品结构最为关键的一环,对钢水纯净度的研究显得尤为重要。
根据对我厂板坯Q235生产各工序夹杂物含量分析,其中铸坯夹杂粒度在10~30um有相当数量,且多数为内部Al2O3、外部硅酸盐的复合型夹杂,这与我厂脱氧合金化方式有一定关系。
我厂通过加强转炉吹炼控制,强化氩站处理后,从测试所分析显示,经上精炼炉、保护浇注钢种对夹杂物控制有一定提高,夹杂物数量有一定减少,但球形夹杂物级别达2.5级,表明对夹杂物的上浮、吸附作得不够;而对于敞开浇注总氧含量则更高,严重影响钢材的最终轧制性能。
为此,炼钢厂特成立《降低钢中夹杂物、提高钢水纯净度攻关小组》,对影响夹杂各环节逐一分析、解决,以达到满足新产品质量要求的目的。
二、存在问题主要原因分析目前炼钢厂生产Q235钢时脱氧合金化方式为:开始出钢时先加入铝块8~10kg进行预脱氧,出钢至1/3时将硅铁、高锰和硅铝钡钙一同加入钢包中。
氩站处理完后自由氧平均含量为41ppm。
测试所金相分析结果为:此钢种夹杂物较多,夹杂物种类有硅酸盐、氧化铝及球状氧化物,其中硅酸盐类夹杂物较为严重,一般为1.5级以上,部分可达到5级。
首先分析硅酸盐夹杂的形成机理:根据相关资料介绍,Si/Mn脱氧时生成的夹杂物类型及形态与〔%Si〕/〔%Mn〕2有关。
当形成的脱氧产物为S iO2饱和时,必然有一个临界〔%Si〕/〔%Mn〕2比值,当高于此临界值,Mn实际上不能参加与硅的脱氧反应,生成的脱氧产物只能是固体SiO2;相反,钢液成分低于此临界值,脱氧产物必然为液态Mn-硅酸盐。
钢的脱氧
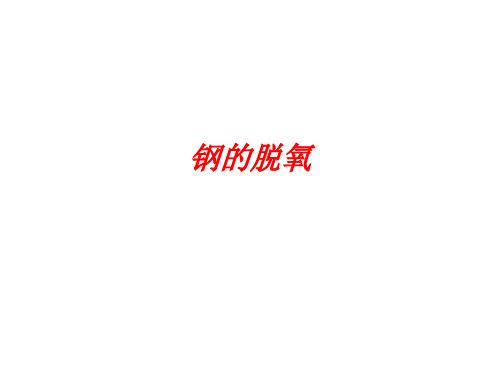
LFeO
(% FeO ) = = KC [%O ]
– 是一个常数,向渣中加入一定量的脱氧剂,使渣中(FeO) 是一个常数,向渣中加入一定量的脱氧剂,使渣中 降低, 不变, 降低,为了保证 LFeO 不变,钢中氧向渣中扩散 。
扩散脱氧
• 过程: 过程:
– 向熔池的渣面上投加粉状的脱氧剂如碳粉、Fe向熔池的渣面上投加粉状的脱氧剂如碳粉、 Si粉、Ca-Si合金粉、Al粉和石灰等,脱除渣中 合金粉、 粉和石灰等 粉和石灰等, 粉 合金粉 的氧,使渣中FeO含量降低至 含量降低至1.0%,利用 的氧,使渣中 含量降低至 , (FeO)=[Fe]+[O]存在平衡,当渣中 存在平衡, 存在平衡 当渣中FeO浓度降 浓度降 低时,平衡破坏, 低时,平衡破坏,为了保持在此温度下的分配 常数,钢中氧必然向渣中扩散, 常数,钢中氧必然向渣中扩散,从而降低了钢 中氧含量,达到脱氧目的。 中氧含量,达到脱氧目的。
– 分配定律,即在一定温度下,氧在熔渣与钢液中的溶解达 分配定律,即在一定温度下, 到平衡时FeO在渣与钢中的浓度之比是个常数。 在渣与钢中的浓度之比是个常数。 到平衡时 在渣与钢中的浓度之比是个常数 – 当温度一定时,[Fe]+[O]=(FeO) 达到平衡时, 当温度一定时, 达到平衡时,
(% FeO ) KC = [% Fe][%O ]
真空脱氧
• 优点
– 脱氧产物是CO气体,不会残留于钢中沾污钢水 脱氧产物是 气体, 气体 – 随着 随着CO气泡上浮搅拌钢水,有效的去除钢中的有害气 气泡上浮搅拌钢水, 气泡上浮搅拌钢水 体和非金属夹杂物,有利于纯净钢水; 体和非金属夹杂物,有利于纯净钢水; – 真空脱氧采用碳脱氧不需用合金,节省了合金费用。 真空脱氧采用碳脱氧不需用合金,节省了合金费用。
对炼钢生产中转炉炼钢脱氧工艺的探讨

对炼钢生产中转炉炼钢脱氧工艺的探讨摘要:随着中国钢铁企业竞争的加剧,钢铁企业加强了成本和质量管理。
因此,如何利用新技术提高产品质量,降低投资成本,已成为现阶段中国钢铁企业提高产品竞争力的关键。
在转炉炼钢的实际制造过程中,氧气的大量存在是不可避免的,因此企业必须首先了解氧气对炼钢产品和钢铁生产的影响,同时了解有效的除氧方法,进而合理利用和改进除氧技术,在保证钢铁质量的前提下,进一步降低投资成本,更加安全有效地实现炼钢生产。
转炉炼钢脱氧工艺广泛应用于炼钢生产中,能有效提高钢材质量。
同时,为了保证应用效果,必须加强对该工艺的应用研究,特别是加强对转炉氧含量的控制。
关键词:炼钢生产;转炉炼钢;脱氧工艺;氧化处理引言:中国工业发展比较快,在冶炼钢铁材料时,对各种工艺和技术的应用有很高的要求。
转炉炼钢的脱氧处理是生产转炉炼钢产品过程中的关键环节,因为钢水脱氧的效率直接关系到炼铁生产和炼钢产品的质量。
如果钢液含氧量高,钢材的热成型性会减弱,内部气孔会扩大,组织疏松,容易形成热脆性,影响钢材的生产质量。
在转炉炼钢过程中,需要结合实际生产情况,提高对氧的危害性的认识。
通过脱氧技术的合理使用,可以有效提高钢材质量,有效提高钢厂生产能力,为钢厂持续稳定发展奠定坚实基础,加强转炉炼钢的脱氧管理已成为提高炼钢生产质量的关键原因。
目前,转炉炼钢脱氧工艺是我国最重要的炼钢技术,在应用中取得了良好的效果。
因为转炉炼钢形成的氧气会在一定程度上影响钢材质量,进而降低生产效率,制约和阻碍钢厂的经营和发展。
与其他炼钢技术相比,转炉炼钢自动化生产水平相对较高,可以提高生产质量和效率,因此,该技术在钢铁企业生产中得到了广泛应用。
但在工艺应用中仍存在一些不足,需要在现有工艺的基础上进行创新和优化,以提高综合生产水平。
1氧气在炼钢生产中的影响及危害分析在转炉炼钢中,需要分离生铁中的碳和杂质,通过氧化处理可以生产出强度更高、性能更好的材料。
在生产过程中,生铁中的碳和铁元素会反应生成碳化铁。
炼钢常用的脱氧方法
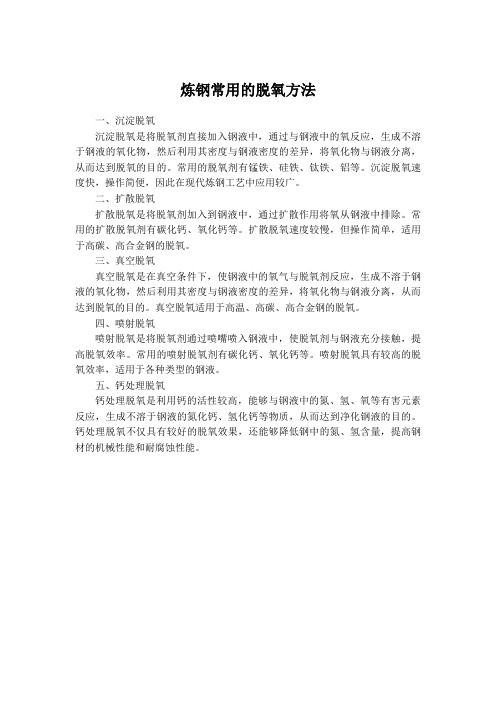
炼钢常用的脱氧方法
一、沉淀脱氧
沉淀脱氧是将脱氧剂直接加入钢液中,通过与钢液中的氧反应,生成不溶于钢液的氧化物,然后利用其密度与钢液密度的差异,将氧化物与钢液分离,从而达到脱氧的目的。
常用的脱氧剂有锰铁、硅铁、钛铁、铝等。
沉淀脱氧速度快,操作简便,因此在现代炼钢工艺中应用较广。
二、扩散脱氧
扩散脱氧是将脱氧剂加入到钢液中,通过扩散作用将氧从钢液中排除。
常用的扩散脱氧剂有碳化钙、氧化钙等。
扩散脱氧速度较慢,但操作简单,适用于高碳、高合金钢的脱氧。
三、真空脱氧
真空脱氧是在真空条件下,使钢液中的氧气与脱氧剂反应,生成不溶于钢液的氧化物,然后利用其密度与钢液密度的差异,将氧化物与钢液分离,从而达到脱氧的目的。
真空脱氧适用于高温、高碳、高合金钢的脱氧。
四、喷射脱氧
喷射脱氧是将脱氧剂通过喷嘴喷入钢液中,使脱氧剂与钢液充分接触,提高脱氧效率。
常用的喷射脱氧剂有碳化钙、氧化钙等。
喷射脱氧具有较高的脱氧效率,适用于各种类型的钢液。
五、钙处理脱氧
钙处理脱氧是利用钙的活性较高,能够与钢液中的氮、氢、氧等有害元素反应,生成不溶于钢液的氮化钙、氢化钙等物质,从而达到净化钢液的目的。
钙处理脱氧不仅具有较好的脱氧效果,还能够降低钢中的氮、氢含量,提高钢材的机械性能和耐腐蚀性能。
炼钢生产中转炉炼钢脱氧工艺

炼钢生产中转炉炼钢脱氧工艺摘要:近些年来,随着炼钢企业的快速发展,很多先进的炼钢技术和设备被的应用和推广。
在具体的炼钢生产过程中,广泛的应用转炉炼钢脱氧方法,有利于提高钢产品的质量,相关技术人员需要对转炉中的氧气含量进行有效的控制,对提高岗产品质量具有重要的作用,也是整个炼钢生产过程中的重要环节。
由于炼钢生产过程中会产生一些氧气成分,作为生产管理人员应该明确炼钢生产过程中所产生的氧气对钢产品的质量有着重要的危害和影响,所以应该加强脱氧方法和技术的研究与创新,善于运用先进的脱氧工艺和脱氧技术不断提高脱氧效果,因此,文章对炼钢生产中转炉炼钢脱氧工艺的相关内容进行分析,为炼钢企业提高钢产品质量提出一些合理化建议。
关键词:炼钢;转炉炼钢;脱氧工艺前言:近些年来,炼钢企业竞争日趋激烈,所以企业管理者应该加强产品质量的重视,同时做到有效的成本控制,不断提高市场竞争力。
通过改善炼钢生产核心技术的方式,实现企业的长远发展[1-2]。
在具体的炼钢过程中,转炉炼钢是重要的生产环节,在转炉炼钢运行过程中会产生一定量的氧气,通过技术人员的分析和研究表明,转炉炼钢生产所产生的氧气对钢铁产品质量具有一定的影响[5],所以在生产过程中要求技术人员采用有效的脱氧方法,提升脱氧效果[3-4]。
在基础生产工艺的前提和基础上,对脱氧工作进行优化和完善,对提高钢铁产品质量具有重要的作用。
1转炉炼钢的含义转炉生产过程中,通过高温和高炉的作用下,对钢进行氧化处理,目的是降低生钢的碳元素含量,有利于保障产品的质量。
由于所冶炼的钢与铁材质上存在很大的差异,其中所富含的碳总量也存在不同,钢的碳含量一般在2%以下,比生铁熔点更高。
转炉炼钢生产过程中都广泛的运用低碳钢,这种钢材的材质和硬度相对不高,所以这类钢材在使用过程中具有一定的可塑性,在不同的生产与制造领域中得到了广泛的应用。
2炼钢过程中的影响因素分析在具体的炼钢工作中,相关人员应该注重炼钢设备与炼钢质量的有效控制,在不同的炼钢环节,科学合理的使用原材料,满足炼钢工作的质量要求,生产出符合要求的产品。
炼钢脱氧剂

炼钢脱氧剂前言炼钢脱氧剂是炼钢过程中的重要辅助剂,用于去除钢铁中的氧气,提高钢铁的纯度和质量。
本文将全面探讨炼钢脱氧剂的原理、种类、应用以及未来发展趋势。
原理在炼钢过程中,钢水中的氧气会对钢铁产生不利影响,其中最主要的问题是碳增加。
氧化碳会导致钢铁的碳含量升高,从而降低钢铁在冷加工及焊接过程中的可塑性和可焊性。
因此,炼钢过程中需要引入脱氧剂来与氧气反应形成稳定的化合物,以将氧气从钢水中去除。
常见的脱氧剂包括铝、硅、钛等元素。
这些元素与氧气反应时会生成相对稳定的氧化物,从而实现脱氧的效果。
脱氧剂的选择需要考虑到其对钢铁的影响,包括脱氧效果、添加量、产生的副产物等。
种类铝脱氧剂铝是一种常用的脱氧剂,其添加量较小且成本相对较低。
铝与氧气反应后生成的氧化铝具有良好的稳定性,能够有效地将氧气从钢水中脱除。
同时,铝的添加还能够细化钢铁的晶粒,提高机械性能和韧性。
硅脱氧剂硅也是一种常见的脱氧剂,其添加量相对较大。
硅与氧气反应后会生成二氧化硅,具有较高的熔点。
硅脱氧剂在炼钢过程中还能够提高钢铁的耐蚀性和抗氧化性能,适用于一些特殊要求的钢铁产品。
钛脱氧剂钛是一种高效的脱氧剂,其添加量较小但成本相对较高。
钛与氧气反应后会生成钛酸钙等氧化物,具有良好的热稳定性。
钛脱氧剂能够有效地降低钢铁中的氧含量,提高钢铁的纯度和质量。
其他脱氧剂除了上述常见的脱氧剂外,还有一些特殊情况下使用的脱氧剂。
例如,铌脱氧剂可用于耐热钢的生产,镁脱氧剂可用于铝杂质较高的钢铁制造。
应用炼钢脱氧剂广泛应用于钢铁制造过程中。
其主要作用是去除钢水中的氧气,从而提高钢铁的纯度和质量。
同时,脱氧剂的添加还能够改善钢铁的性能,提高其使用寿命和耐腐蚀性。
脱氧剂的选择需要考虑多个因素,包括钢铁的用途、成本、脱氧效果等。
不同的脱氧剂在不同钢铁制造过程中均有应用,具体选择需要依据实际情况进行。
未来发展趋势随着钢铁工业的发展和技术进步,炼钢脱氧剂的应用也在不断创新和改进。
第6章钢液脱氧反应及钢中的非金属夹杂物
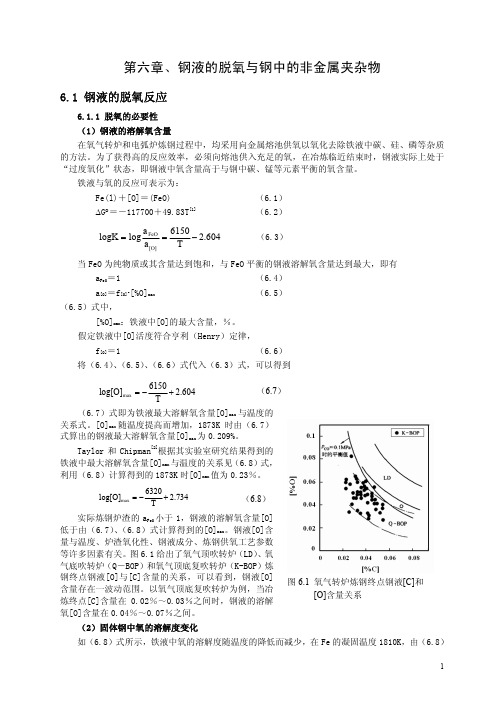
(6.1) (6.2) (6.3)
logK = log
a FeO 6150 = − 2.604 a [O] T
当 FeO 为纯物质或其含量达到饱和,与 FeO 平衡的钢液溶解氧含量达到最大,即有 aFeO=1 a[O]=f[O][%O]max (6.5)式中, [%O]max:铁液中[O]的最大含量,%。 假定铁液中[O]活度符合亨利(Henry)定律, f[O]=1 (6.6) 将(6.4) 、 (6.5) 、 (6.6)式代入(6.3)式,可以得到
3
表 6.1 脱氧常数和钢液有关组元活度相互作用系数 脱氧反应式 2[Al]+3[O]=Al2O3(s) 2[B]+3[O]=B2O3(l) [Ba]+[O]=BaO(s) [C]+[O]=CO [Ca]+[O]=CaO(s) 2[Ce]+3[O]=Ce2O3 2[Cr]+3[O]=Cr2O3 [Mn]+[O]=MnO(l) [Nb]+2[O]=NbO2(s) [Si]+2[O]=SiO2(s) 2[Ta]+5[O]=Ta2O5(s) 3[Ti]+5[O]=Ti3O5(s) 2[V]+3[O]=V2O3(s) ZrO2(s)=[Zr]+2[O] log K’ -64000/T+20.57 -10000/T-1.8 -1160/T-2.003
-0.189 -0.083 -0.71 -0.119 -1.2 -0.46 -12
0.00 0.00 0 0.103 0.11 0.041 0.022 0
(6.15)式可以进一步表示为:
K ' = ( f [ M ] ⋅ [% M ]) x ⋅ ( f [O ] ⋅ [%O ]) y
(6.16)
对[M]和[O]的活度,以亨利定律为基准,忽略活度相互作用系数高次项的影响,由(6.16)式 可以得到:
炼钢常用的脱氧方法 -回复

炼钢常用的脱氧方法-回复炼钢是将生铁或铸铁中的杂质含量降低,使其成为高纯度的钢的过程。
脱氧是炼钢过程中的一项重要措施,其目的是去除炼钢过程中产生的氧化物,以提高钢的质量。
下面将详细介绍炼钢常用的脱氧方法。
1. 炉内脱氧法炉内脱氧法是最常见的脱氧方法之一。
在炼钢炉中加入脱氧剂,通过与钢液中的氧化物反应,达到脱氧的目的。
常见的脱氧剂有铝、硅、钛等。
这些脱氧剂与氧化物反应生成气体,同时会加入钢液中,达到脱氧的效果。
炉内脱氧法具有操作简单、成本低等优势,广泛应用于炼钢生产中。
2. 真空脱氧法真空脱氧法是另一种常用的脱氧方法。
在真空条件下,通过热合金反应、电热反应或加热电弧炉等方式,将脱氧剂引入炉内与钢液反应。
真空脱氧法可以有效降低钢液中的氧含量,提高钢的纯度。
这种方法适用于高纯度钢的生产,如特殊钢、不锈钢等。
真空脱氧法复杂度较高,但可以得到更高纯度的钢产品。
3. 吹氩脱氧法吹氩脱氧法是通过吹氩将炉中的氧气置换为惰性气体,从而达到去除氧化物的目的。
吹氩脱氧法一般用于连铸炼钢过程中。
在钢液连续浇铸时,通过向钢液表面喷吹氩气,可以防止氧气进入钢液中,减少氧化物的生成。
这种方法操作简单、效果显著,常用于优质连铸钢的生产。
4. 磷脱氧法磷脱氧法是炼钢过程中的一种特殊脱氧方法。
在钢液中加入含磷化合物,通过与氧化物反应生成无氧化性的磷化物,达到脱氧的目的。
磷脱氧法可以有效降低炼钢过程中的钢液温度,减少炉渣的生成,提高钢的纯净度。
这种方法适用于高温操作条件下的钢液脱氧。
以上是炼钢常用的脱氧方法的介绍。
脱氧是炼钢过程中的一项关键环节,能够有效降低钢液中的氧含量,提高钢的纯净度。
不同的脱氧方法适用于不同的炼钢场景,选择合适的脱氧方法对于提高钢的质量具有重要意义。
随着炼钢技术的不断发展,脱氧方法也在不断创新,以满足对钢质量要求的不断提高。
钢液中脱氧以及非金属夹杂物
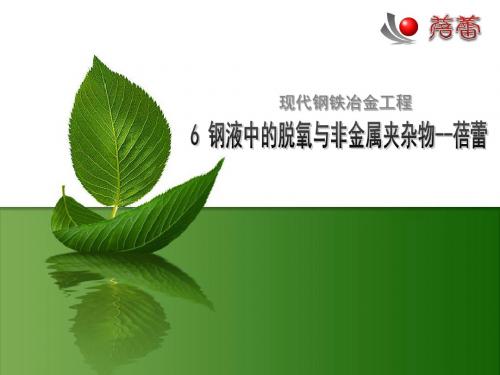
6.1.2 直接脱氧反应热力学--复合脱氧
在一定的温度下,当Si]/[Mn]2 比超过某一临界值时,锰不参加 脱氧反应,脱氧产物仅为固态的 SiO2。 图6.10为不同温度下[Si]/ [Mn]2比临界值的曲线图。当金属 中硅、锰成分位于曲线下面的区 域内时,脱氧产物为熔融的硅酸 锰;当硅、锰成分位于曲线上方 时,脱氧产物是固体SiO2。
优 点:与单独元素的脱氧相比.在多数情况下,复合脱 氧能够提高脱氧元素的脱氧能力。
6.1.2 直接脱氧反应热力学--复合脱氧
[Mn]-[O]
[Si]-[O]
6.1.2 直接脱氧反应热力学--复合脱氧
6.1.2 直接脱氧反应热力学--复合脱氧
假定Si—Mn复合脱氧产 物中MnO和SiO2的摩尔分 数分别为55%和45%,由 图6.7可以查到:脱氧产物 中MnO的活度aMnO大约为 0.27,SiO2的话度aSiO2: 大约为0.55。将上述aMnO 和aSiO2的数值代人式(6.24), 可以得到以下关系式:
6.1.3 直接脱氧反应动力学——脱氧产物的形核
6.1.3 直接脱氧反应动力学——脱氧产物的形核
6.1.1 脱氧的必要性——氧对钢性能的影响
6.1.1.3 氧对钢性能的影响
氧是在钢的凝固过程中偏析倾向最严重的元素之一,其偏析 系数([O]固体钢/[O]钢液)仅为0.02。 在钢液的凝固和随后的冷却过程中,由于溶解度的急剧降低, 钢中原溶解的绝大部分氧由γ 或α 相中析出,并以铁氧化物、氧 硫化物等微细夹杂物的形式在γ 或α 晶界处富集存在。 这些微细夹杂物会造成晶界脆化,在钢的加工和使用过程中容 易成为晶界开裂的起点,并最终导致钢材发生脆性破坏。
6.1.3 直接脱氧反应动力学——脱氧剂的溶解与均匀化
铁粉做脱氧剂原理
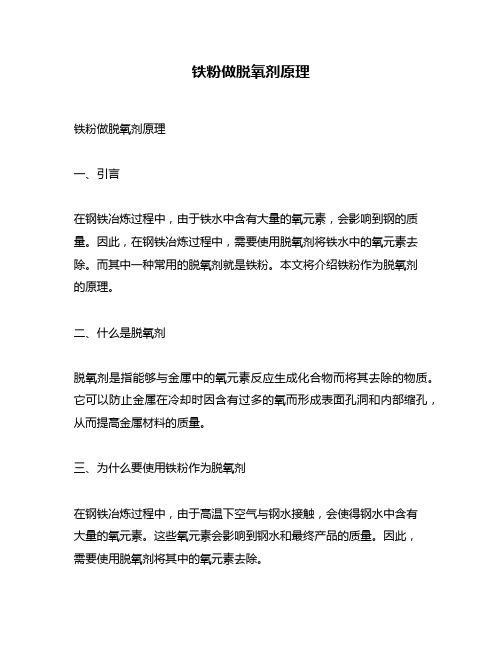
铁粉做脱氧剂原理铁粉做脱氧剂原理一、引言在钢铁冶炼过程中,由于铁水中含有大量的氧元素,会影响到钢的质量。
因此,在钢铁冶炼过程中,需要使用脱氧剂将铁水中的氧元素去除。
而其中一种常用的脱氧剂就是铁粉。
本文将介绍铁粉作为脱氧剂的原理。
二、什么是脱氧剂脱氧剂是指能够与金属中的氧元素反应生成化合物而将其去除的物质。
它可以防止金属在冷却时因含有过多的氧而形成表面孔洞和内部缩孔,从而提高金属材料的质量。
三、为什么要使用铁粉作为脱氧剂在钢铁冶炼过程中,由于高温下空气与钢水接触,会使得钢水中含有大量的氧元素。
这些氧元素会影响到钢水和最终产品的质量。
因此,需要使用脱氧剂将其中的氧元素去除。
与其他脱氧剂相比,铁粉具有以下优点:1.价格低廉:铁粉是一种廉价的原料,与其他脱氧剂相比,成本更低。
2.反应速度快:铁粉与钢水中的氧元素反应速度快,可以快速将其中的氧元素去除。
3.脱氧效果好:使用铁粉作为脱氧剂可以有效地将钢水中的氧元素去除。
同时,使用铁粉还可以减少其他杂质的含量,提高钢水的纯度。
四、铁粉作为脱氧剂的原理在钢铁冶炼过程中,将铁粉加入到钢水中后,会发生以下反应:Fe + O2 → FeO其中Fe表示铁粉,O2表示钢水中的氧元素,FeO表示生成的化合物。
这个反应是一个还原反应。
在这个反应中,铁粉会与钢水中的氧元素发生化学反应,并生成一种新化合物——FeO。
由于FeO具有较高的熔点和密度,在冷却时不会形成表面孔洞和内部缩孔。
因此,在使用铁粉作为脱氧剂时可以有效地防止金属材料在冷却时产生缺陷。
此外,铁粉还可以减少其他杂质的含量,提高钢水的纯度。
在反应过程中,铁粉会与钢水中的其他杂质发生化学反应,并将其去除。
五、铁粉作为脱氧剂的使用方法在钢铁冶炼过程中,使用铁粉作为脱氧剂的方法如下:1.将适量的铁粉放入加料斗中;2.在钢水温度达到一定温度时,将铁粉加入到钢水中;3.搅拌一段时间,使铁粉充分与钢水反应;4.待反应结束后,将产生的FeO等杂质从钢水中分离出来。
炼钢常用的脱氧方法
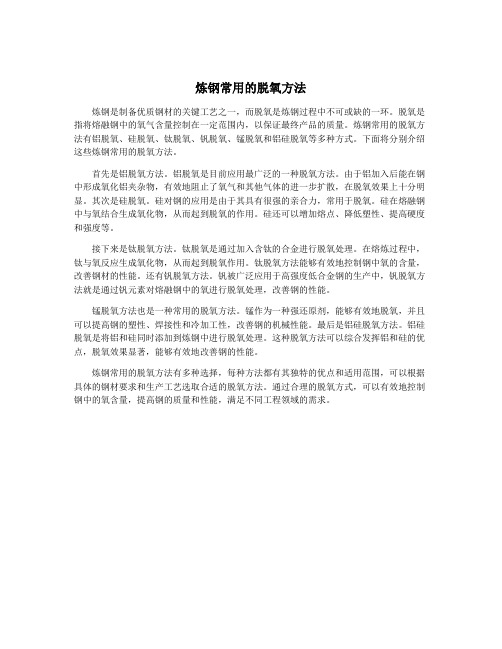
炼钢常用的脱氧方法炼钢是制备优质钢材的关键工艺之一,而脱氧是炼钢过程中不可或缺的一环。
脱氧是指将熔融钢中的氧气含量控制在一定范围内,以保证最终产品的质量。
炼钢常用的脱氧方法有铝脱氧、硅脱氧、钛脱氧、钒脱氧、锰脱氧和铝硅脱氧等多种方式。
下面将分别介绍这些炼钢常用的脱氧方法。
首先是铝脱氧方法。
铝脱氧是目前应用最广泛的一种脱氧方法。
由于铝加入后能在钢中形成氧化铝夹杂物,有效地阻止了氧气和其他气体的进一步扩散,在脱氧效果上十分明显。
其次是硅脱氧。
硅对钢的应用是由于其具有很强的亲合力,常用于脱氧。
硅在熔融钢中与氧结合生成氧化物,从而起到脱氧的作用。
硅还可以增加熔点、降低塑性、提高硬度和强度等。
接下来是钛脱氧方法。
钛脱氧是通过加入含钛的合金进行脱氧处理。
在熔炼过程中,钛与氧反应生成氧化物,从而起到脱氧作用。
钛脱氧方法能够有效地控制钢中氧的含量,改善钢材的性能。
还有钒脱氧方法。
钒被广泛应用于高强度低合金钢的生产中,钒脱氧方法就是通过钒元素对熔融钢中的氧进行脱氧处理,改善钢的性能。
锰脱氧方法也是一种常用的脱氧方法。
锰作为一种强还原剂,能够有效地脱氧,并且可以提高钢的塑性、焊接性和冷加工性,改善钢的机械性能。
最后是铝硅脱氧方法。
铝硅脱氧是将铝和硅同时添加到炼钢中进行脱氧处理。
这种脱氧方法可以综合发挥铝和硅的优点,脱氧效果显著,能够有效地改善钢的性能。
炼钢常用的脱氧方法有多种选择,每种方法都有其独特的优点和适用范围,可以根据具体的钢材要求和生产工艺选取合适的脱氧方法。
通过合理的脱氧方式,可以有效地控制钢中的氧含量,提高钢的质量和性能,满足不同工程领域的需求。
炼钢用铝脱氧剂-概述说明以及解释
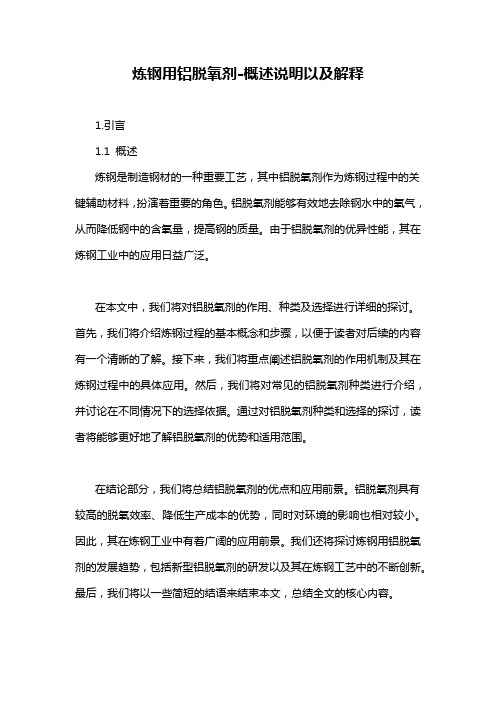
炼钢用铝脱氧剂-概述说明以及解释1.引言1.1 概述炼钢是制造钢材的一种重要工艺,其中铝脱氧剂作为炼钢过程中的关键辅助材料,扮演着重要的角色。
铝脱氧剂能够有效地去除钢水中的氧气,从而降低钢中的含氧量,提高钢的质量。
由于铝脱氧剂的优异性能,其在炼钢工业中的应用日益广泛。
在本文中,我们将对铝脱氧剂的作用、种类及选择进行详细的探讨。
首先,我们将介绍炼钢过程的基本概念和步骤,以便于读者对后续的内容有一个清晰的了解。
接下来,我们将重点阐述铝脱氧剂的作用机制及其在炼钢过程中的具体应用。
然后,我们将对常见的铝脱氧剂种类进行介绍,并讨论在不同情况下的选择依据。
通过对铝脱氧剂种类和选择的探讨,读者将能够更好地了解铝脱氧剂的优势和适用范围。
在结论部分,我们将总结铝脱氧剂的优点和应用前景。
铝脱氧剂具有较高的脱氧效率、降低生产成本的优势,同时对环境的影响也相对较小。
因此,其在炼钢工业中有着广阔的应用前景。
我们还将探讨炼钢用铝脱氧剂的发展趋势,包括新型铝脱氧剂的研发以及其在炼钢工艺中的不断创新。
最后,我们将以一些简短的结语来结束本文,总结全文的核心内容。
通过本文的阐述,读者将能够全面了解炼钢用铝脱氧剂的重要性及其在炼钢工业中的具体应用。
同时,读者也可以对铝脱氧剂的未来发展有一个更清晰的认识。
希望本文能够为相关领域的读者提供有价值的信息和思路。
1.2文章结构文章结构部分的内容应该是对整篇文章的框架进行介绍。
下面是对文章结构部分的一个参考范例:在本文中,我们将探讨炼钢过程中使用铝脱氧剂的重要性和应用。
本文将分为三个主要部分:引言、正文和结论。
在引言部分,我们首先会对炼钢过程进行概述,介绍其中的重要性和挑战。
随后,我们将阐明本文的文章结构和目的,为读者营造一个清晰的阅读框架。
在正文部分,我们将详细介绍炼钢过程的基本原理和步骤,并重点探讨铝脱氧剂在炼钢中的作用。
我们将讨论铝脱氧剂对钢材的脱氧效果、温度控制等方面的优势,并介绍不同种类的铝脱氧剂和如何选择适合的铝脱氧剂。
底吹转炉钢中脱氧剂的添加与利用
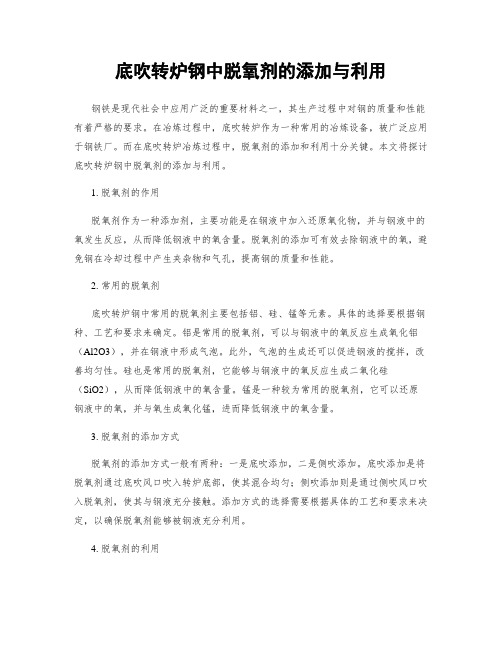
底吹转炉钢中脱氧剂的添加与利用钢铁是现代社会中应用广泛的重要材料之一,其生产过程中对钢的质量和性能有着严格的要求。
在冶炼过程中,底吹转炉作为一种常用的冶炼设备,被广泛应用于钢铁厂。
而在底吹转炉冶炼过程中,脱氧剂的添加和利用十分关键。
本文将探讨底吹转炉钢中脱氧剂的添加与利用。
1. 脱氧剂的作用脱氧剂作为一种添加剂,主要功能是在钢液中加入还原氧化物,并与钢液中的氧发生反应,从而降低钢液中的氧含量。
脱氧剂的添加可有效去除钢液中的氧,避免钢在冷却过程中产生夹杂物和气孔,提高钢的质量和性能。
2. 常用的脱氧剂底吹转炉钢中常用的脱氧剂主要包括铝、硅、锰等元素。
具体的选择要根据钢种、工艺和要求来确定。
铝是常用的脱氧剂,可以与钢液中的氧反应生成氧化铝(Al2O3),并在钢液中形成气泡。
此外,气泡的生成还可以促进钢液的搅拌,改善均匀性。
硅也是常用的脱氧剂,它能够与钢液中的氧反应生成二氧化硅(SiO2),从而降低钢液中的氧含量。
锰是一种较为常用的脱氧剂,它可以还原钢液中的氧,并与氧生成氧化锰,进而降低钢液中的氧含量。
3. 脱氧剂的添加方式脱氧剂的添加方式一般有两种:一是底吹添加,二是侧吹添加。
底吹添加是将脱氧剂通过底吹风口吹入转炉底部,使其混合均匀;侧吹添加则是通过侧吹风口吹入脱氧剂,使其与钢液充分接触。
添加方式的选择需要根据具体的工艺和要求来决定,以确保脱氧剂能够被钢液充分利用。
4. 脱氧剂的利用脱氧剂的添加是为了使钢中的氧含量降到最低限度,提高钢的质量和性能。
为了充分利用脱氧剂,需要注意以下几点:(1)控制添加量:脱氧剂的添加量需要根据钢种和工艺来确定,过量的脱氧剂不仅会增加成本,还可能对钢液的性能产生不利影响。
(2)控制冶炼时间:在底吹转炉冶炼过程中,冶炼时间过长会造成脱氧剂的消耗过大,降低了其利用率。
(3)保持良好的搅拌条件:良好的搅拌条件可以使脱氧剂与钢液充分接触,提高其利用效率。
综上所述,底吹转炉钢中脱氧剂的添加与利用是钢铁冶炼过程中的重要环节。
转炉脱氧的作用

转炉脱氧的作用一、引言转炉脱氧是冶金工艺中的一种关键步骤,它在钢铁制造中发挥着重要的作用。
本文将探讨转炉脱氧的作用以及相关的工艺参数。
二、转炉脱氧的定义转炉脱氧是利用还原剂将炼钢过程中的氧气从炉中除去的过程。
通过脱氧作用,可以降低钢中的氧含量,提高钢的质量和可塑性。
三、转炉脱氧的作用机制脱氧剂在转炉中与钢水中的氧气反应,生成不挥发的氧化物,并沉淀于炉渣中。
同时,还原剂与氧气反应,生成可挥发的氧化物,从而有效地降低钢水中的氧含量。
四、转炉脱氧的重要性转炉脱氧的作用对钢铁制品的质量有着至关重要的影响。
4.1 提高钢的可塑性通过脱氧作用,钢中的氧含量降低,钢的韧性和可塑性得到改善。
这对于冷加工和热加工过程中的变形性能和成形性能至关重要。
4.2 降低钢的气体含量转炉脱氧除了能够去除氧气,还能够去除一些其他气体,如氮气,从而降低钢水中的气体含量。
这对于减少钢中的气孔和气泡,提高钢的致密性和机械性能非常重要。
4.3 提高钢的抗氧化能力钢经过转炉脱氧后,氧含量降低,钢的抵抗氧化的能力也得到提高。
这对于钢在高温和腐蚀环境中的使用具有重要意义。
4.4 降低钢的夹杂物含量转炉脱氧还能够有效降低钢中的夹杂物含量,改善钢的内在质量,提高钢材的强度和韧性。
五、转炉脱氧的工艺参数5.1 还原剂选择常用的还原剂有硅、铝、镁等。
不同的还原剂有不同的还原能力,选择合适的还原剂对于脱氧效果至关重要。
5.2 还原剂的加入方式还原剂的加入方式有点状加入、喷射加入等。
采用不同的加入方式可以达到不同的脱氧效果。
5.3 脱氧剂的选择常用的脱氧剂有硅、锰、铝、钛等。
不同的脱氧剂对于脱氧效果有着不同的影响,需要根据具体情况选择合适的脱氧剂。
5.4 脱氧剂的加入方式脱氧剂的加入方式有一次性加入、分次加入等。
加入方式的选择需要考虑如何充分发挥脱氧剂的作用。
六、转炉脱氧的工艺控制转炉脱氧的工艺控制对于脱氧效果的稳定性和一致性至关重要。
6.1 温度控制转炉脱氧的温度控制是关键的一步。
炼钢的氧化亚铁

在炼钢过程中,氧化亚铁(FeO)是一种重要的中间产物,它在高炉中铁矿石还原过程中形成,以及在转炉中过量的生铁与氧气反应生成。
氧化亚铁的存在对钢材质量有不利影响,因为它会导致钢中氧含量升高,从而增加夹杂物和缺陷,影响钢材的机械性能和耐腐蚀性。
为了去除炼钢过程中的氧化亚铁,通常采用以下方法:
1. 脱氧剂的使用:在钢液中加入脱氧剂,如硅铁、锰铁、铝或钙等。
这些脱氧剂与氧化亚铁反应,生成不溶于钢液的氧化物,并以渣的形式从钢液中分离出去。
2. 底吹和顶吹:在转炉炼钢过程中,可以通过底吹或顶吹氧气来氧化氧化亚铁及其他杂质元素,生成的氧化物随炉渣排出。
3. 真空脱气:在二次精炼阶段,通过降低炉内压力来去除溶解在钢液中的气体,包括由氧化亚铁分解产生的气体。
4. 渣洗:利用炉渣对钢液进行洗涤,通过渣与钢液的物理接触,将夹杂物从钢液中分离出去。
5. 电渣重熔:在某些特殊的钢材生产过程中,可以使用电渣重熔法进一步提纯钢液,去除氧化亚铁及其他不希望的元素。
通过以上方法,可以有效减少钢中的氧含量,改善钢材的整体质量。
氧化亚铁的去除是钢铁冶炼中不可缺少的一环,对于生产出高质量的钢材至关重要。