Nitrendipine_39562-70-4_DataSheet_MedChemExpress
超米特电子有限公司产品说明书

1US Headquarters TEL +(1) 781-935-4850FAX +(1) 781-933-4318 • Europe TEL +(44) 1628 404000FAX +(44) 1628 404090Asia Pacific TEL +(852) 2 428 8008FAX +(852) 2 423 8253South America TEL +(55) 11 3917 1099FAX +(55) 11 3917 0817Superior elongation and tensilestrength help to prevent tearing in use due to mishandling. Typical properties for CHO-SEAL 1310 and 1273 materi-al are shown on pages 33 and 32respectively.High Shielding PerformanceCHO-SEAL 1310 material provides more than 80 dB of shielding effectiv-ness from 100 MHz to 10 GHz, while CHO-SEAL 1273 material provides more than 100 dB.Low Volume ResistivityBoth materials have exceptionally low volume resistivity, which makes them well suited for grounding appli-cations in which a flexible electrical contact is needed.Low Compression GasketSpacer gaskets are typicallydesigned to function under low deflec-tion forces. Chomerics uses design tools such as Finite Element Analysis (FEA) to accurately predict compres-sion-deflection behavior of various cross section options. Refer to page16.LCP Plastic SpacerLiquid crystal polymer (LCP)spacers, including those made with Vectra A130 material, provide aCHO-SEAL ®1310 or 1273Conductive ElastomersWith EMI spacer gaskets, shielding and grounding are provided by Chomerics’CHO-SEAL 1310 and 1273 conductive elastomers, specifi-cally formulated for custom shape molded parts. They provide excellent shielding and isolation against electro-magnetic interference (EMI), or act as a low impedance ground path between PCB traces and shielding media. Physically tough, these elas-tomers minimize the risk of gasket damage, in contrast to thin-walled extrusions or unsupported molded gaskets.Silicone-based CHO-SEAL 1310and 1273 materials offer excellent resistance to compression set over a wide temperature range, resulting in years of continuous service. CHO-SEAL 1310 material is filled with silver-plated-glass particles, while 1273 utilizes silver-plated-copper filler to provide higher levels of EMI shielding effectiveness.EMI Spacer GasketsThe unique design of Chomerics’EMI spacer gaskets features a thin plastic retainer frame onto which a conductive elastomer is molded. The elastomer can be located inside or outside the retainer frame, as well as on its top and bottom surface. EMI spacer gaskets provide a newapproach to designing EMI gaskets into handheld electronics such as dig-ital cellular phones. Board-to-board spacing is custom designed to fit broad application needs. Customized cross sections and spacer shapes allow for very low closure forcerequirements and a perfect fit in any design or device.Robotic InstallationSpacer gaskets can be installed quickly by robotic application. Integral locater pins in the plastic spacer help ensure accuratepositioning in both manual and pick-and-place assembly. Benefits include faster assembly and lower labor costs.The integrated conductive elastomer/plastic spacer gasket is a low cost,easily installed system for providing EMI shielding and grounding in small electronic enclosures.Figure 1Single Piece EMI Gasket/Locator PinsCHO-SEAL 1310 or 1273 Conductive Elastomer (Inside)Plastic Spacer Around Outsideor InsideApplications for EMI Spacer GasketsThe spacer gasket concept is especially suited to digital and dual board telephone handsets or other handheld electronic devices. It provides a low impedance path between peripheral ground traces on printed circuit boards and components such as:•the conductive coating on a plastic housing•another printed circuit board •the keypad assemblyTypical applications for EMI spacer gaskets include:•Digital cellular, handyphone and personal communications services (PCS) handsets •PCMCIA cards•Global Positioning Systems (GPS)•Radio receivers•Other handheld electronics, e.g.,personal digital assistants (PDAs)•Replacements for metal EMI shield-ing “fences” on printedcircuit boards in wireless tele-communications devicesstable platform for direct, highprecision molding of conductive elas-tomers. The Vectra A130 material described in Table 1 has excellent heat deflection temperature character-istics (489°F, 254°C). For weight con-siderations, the LCP has aspecific gravity of only 1.61. This plas-tic is also 100% recyclable.Typical EMI Spacer Gasket Design ParametersThe EMI spacer gasket concept can be considered using the design parameters shown in Table 2. Some typical spacer gasket profiles are shown below.Figure 2Typical Spacer Gasket Profiles3US Headquarters TEL +(1) 781-935-4850FAX +(1) 781-933-4318 • Europe TEL +(44) 1628 404000FAX +(44) 1628 404090Asia Pacific TEL +(852) 2 428 8008FAX +(852) 2 423 8253South America TEL +(55) 11 3917 1099FAX +(55) 11 3917 0817Finite Element AnalysisChomerics, a division of the Parker Hannifin Corporation’s Seal Group, is the headquarters of Parker Seal’s Elastomer Simulation Group. This unit specializes in elastomer finite element analysis (FEA) using MARC K6 series software as a foundation for FEA capability.Benefits of FEA include:•Quickly optimizing elastomer gasket designs•Allowing accurate predictions of alternate elastomer design concepts •Eliminating extensive trial and error prototype evaluationTypical use of FEA in EMI spacer gasket designs is to evaluate the force vs. deflection requirements of alternate designs.For example, onespacer design features a continuous bead of con-ductive elastomer molded onto a plastic spacer. An alternative designemploys an “interrupted bead,” where the interrup-tions (gaps left on the plastic frame) are sized to maintain the requiredlevel of EMI shielding. Figure 4illustrates these alternative designs.Gasket DeflectionFigure 5 compares the effect of continuous and interrupted elastomer gasket designs in terms of the force required to deflect the conductive elastomer. This actual cellular handset application required a spacer gasket with interrupted bead to meet desired deflection forces.Chomerics Designand Application ServicesChomerics will custom design a spacer for your application. Advice,analysis and design assistance will be provided by Chomerics Applications and Design engineers at no additional fee. Contact Chomerics directlyat the locations listed at the bottom of the page.Figure 3FEA Example of an EMISpacer Gasket Cross SectionFigure 4Continuous (top) and InterruptedElastomer GasketsFigure 5Typical Spacer Gasket Deflection。
供应日本田村助焊剂

TAMURA无铅焊锡丝SAC305/BH204/BH211/BH306/BH601
AIM焊锡条SN100C
AIM无铅焊锡条SN100C
AIM无铅焊锡丝SN100C
AIM无铅焊锡棒SN100C (3)TAMURA日本田村喷涂设备:TAP40-12F
(4)TAMURA日本田村氮气产生装置:KN4
7、TAMURA日本田村设备维修服务
8、TAMURA无铅焊锡条
TAMURA日本田村无铅锡条SAC305/BH 204/BH 211/BH 306/BH 601
TAMURA田村SAC305/BH204/BH211/BH306/BH601
TAMURA关键词:
TAMURA日本田村
1、无铅锡膏:
(1)TAMURA日本田村无卤锡膏:TLF-204-NH
(2)TAMURA日本田村常温存储无铅锡膏:TLF-204-SIS、TLF-204-SMY
(3)TAMURA日本田村常规锡膏:TLF-401-11、TLF-204-MDS、TLF-204-111、TLF-204-111A、TLF-204-111M、TLF-204-93、TLF-204-93IVT、TLF-204-93K、TLF-204-93S、TLF-204-93F、 TLF-204-19A、、TLF-204-19B 、TLF-204-151、TLF-204-153/210、TLF-204-49、TLF-204-21、TLF-204-29M-2、TLF-204-41、TLF-204-43、TLF-204-49FC、TLF-204-75、TLF-204F-111ST、TLF-204F-NHS、TLF-204-107、TLF-204-107(SH)、TLF-801-17、TLF-204-19B、TLF-204-43
TekVPI Interface Adapter TPA-BNC 数据手册说明书

TekVPI™Interface AdapterTPA-BNC DataSheetFeatures &Bene fitsEnables Existing TekProbe ®Products to Connect to the TekVPI™Probe Interface of the New DPO7000and DPO4000Series Oscilloscopes An Easy-to-use Plug-in Adapter to the Oscilloscope’s TekVPI Interface Provides Necessary Power,Communication,and Offset Control as Needed by the Attached TekProbe ProductProvides Overcurrent and Thermal Overload Protection for the Attached TekProbe ProductProvides an LED Probe Status Indicator which Identi fies that the Probe has Powered-up SuccessfullyApplicationsAdapts Existing TekProbe ®Probe Types for Application with TekVPI™OscilloscopesTekVPI™Interface AdapterTPA-BNC Adapter enables existing TekProbe ®interface products(active,differential,high-voltage,current,and optical probes)to be used with Tektronix’newest generation of DPO7000and DPO4000SeriesOscilloscopes which feature the new TekVPI™probe interface architecture.Existing TekProbe-BNC probe types simply plug into the TPA-BNC adapter which is then plugged directly into any TekVPI probe channel of the DPO7000and DPO4000Series oscilloscopes.The TPA-BNC adapter recognizes and supplies the necessary power and serial communication and offset control as used by the connected TekProbe product accessory.Note:Tektronix probe types using a BNC connection,or a BNC connection with a single analog encoding pin for attenuation factor detection connect directly to the oscilloscope’s TekVPI probe interface and do not require a TPA-BNC adapter.TekProbe ®InterfaceTekProbe is a probe interface architecture introduced in 1986,and used on many earlier models of Tektronix oscilloscopes including the TDS300,TDS400,TDS500,TDS600,TDS700,TDS3000/B,TDS5000/B,and TDS7000Series.In addition to coupling the signal from the probe to the oscilloscope,the TekProbe interface provides power and offset control to active probes.It also allows the oscilloscope to sense the probe’s attenuation scale factor and/or probetype.Data SheetCharacteristicsBandwidth–DC to>3GHz.VSWR–<1.23:1up to3GHz.RF Insertion Loss–<0.25dB.Delay Time–245ps.Maximum Input Signal Voltage–42V pk-pk,30V RMS,60VDC.Physical CharacteristicsDimensions mm in.Height43 1.694Width30.5 1.200 Length62.2 2.449Weight kg lb. Shipping0.451Power RequirementsTPA-BNC is powered directly from DPO7000and DPO4000Series Oscilloscopes,using TekVPI probe interface.EnvironmentalTemperatureOperating–0°C to+50°C.Nonoperating–-40°C to+75°C.HumidityOperating–5%to95%Relative Humidity(RH)up to+30°C;5%to85%RH above +30°C up to+50°C,noncondensing.Nonoperating–5%to95%Relative Humidity(RH)up to+30°C;5%to85%RH above+30°C up to+75°C,noncondensing.AltitudeOperating–Up to3,000m(10,000ft.).Nonoperating–Up to15,240m(50,000ft.).RegulatoryCompliance Labeling–WEEE(European Union).Standard WarrantyOne year parts and labor.Recommended OscilloscopesDPO7000and DPO4000Series Oscilloscopes with TekVPI probe interface. Ordering InformationTPA-BNCTekVPI™Interface Adapter to TekProbe-BNC ProbesIncludes:User manual(071-1689-xx).Service OptionsOpt.C3–Calibration Service3years(initial certification,plus2calibrations). Opt.C5–Calibration Service5years(initial certification,plus4calibrations). Opt.D3–Test Data on delivery and with future calibrations.Must be ordered with Opt.C3.Opt.D5–Test Data on delivery and with future calibrations.Must be ordered with Opt.C5.Opt.R3–Repair Service.Repair warranty extended to cover3years.Opt.R5–Repair Service.Repair warranty extended to cover3years.Product(s)are manufactured in ISO registered facilities.TekVPI™Interface Adapter—TPA-BNC3Data Sheet Contact Tektronix:ASEAN/Australasia(65)63563900Austria+41526753777Balkans,Israel,South Africa and other ISE Countries+41526753777Belgium078160166Brazil+55(11)40669400Canada1(800)661-5625Central East Europe,Ukraine,and the Baltics+41526753777Central Europe&Greece+41526753777Denmark+4580881401Finland+41526753777France+33(0)169868181Germany+49(221)9477400Hong Kong(852)2585-6688India(91)80-42922600Italy+39(02)250861Japan81(3)6714-3010Luxembourg+44(0)1344392400Mexico,Central/South America&Caribbean52(55)54247900Middle East,Asia,and North Africa+41526753777The Netherlands09002021797Norway80016098People’s Republic of China86(10)62351230Poland+41526753777Portugal800812370Republic of Korea82(2)6917-5000Russia&CIS+7(495)7484900South Africa+27112068360Spain(+34)901988054Sweden020*******Switzerland+41526753777Taiwan886(2)2722-9622United Kingdom&Ireland+44(0)1344392400USA1(800)426-2200For other areas contact Tektronix,Inc at:1(503)627-7111Updated30October2008For Further Information.Tektronix maintains a comprehensive,constantly expandingcollection of application notes,technical briefs and other resources to help engineers workingon the cutting edge of technology.Please visit Copyright©Tektronix,Inc.All rights reserved.Tektronix products are covered by U.S.and foreign patents,issued and rmation in this publication supersedes that in all previously published material.Specification and price change privileges reserved.TEKTRONIX and TEK are registered trademarks ofTektronix,Inc.All other trade names referenced are the service marks,trademarks,or registered trademarksof their respective companies.05Jun200951W-19077-1。
超特克(Supertex)高压DC DC转换器应用注解说明书

Supertex inc.AN-H59Application NoteApplication CircuitHigh Voltage DC/DC Converter forSupertex Ultrasound Transmitter DemoboardsBy Afshaneh Brown, Applications Engineer,and Jimes Lei, Applications ManagerIntroductionThe Supertex AN-H59DB1 demoboard is a high voltage DC/DC converter. It can provide up to +90V voltage supply for V PP and -90V for V NN . It also provides +8.0 to +10V voltage supply for V DD , floating power supplies of V NN +8.0 to V NN +10V for V NF and V PP -8.0 to V PP -10V for V PF . The input supply voltage is 12V.The AN-H59DB1 circuitry consists of two high voltage PWM Current-Mode controllers, a DC/DC transformer driver, and three low dropout regulators. The Supertex AN-H59DB1 uses a high-voltage, current mode, PWM controller boost topology to generate +15 to +90V and a high-voltage current mode PWM controller buck-boost topology to generate -15 to -90V power supply voltage for Supertex HV738DB1 and HV748DB1 ultrasound transmitter demoboards.Each of the transmitter demoboards has slightly different operating voltages as summarized below.To accommodate all three demoboards, the AN-H59DB1 demoboard has adjustable V PP , V NN , V DD , V PF and V NF . The purpose of the AN-H59DB1 is to aid in the evaluation of the three transmitter demoboards. The intention of this application note is to provide a general circuit description on how each of the output voltages is generated.The VSUB pin on the HV738DB1 and HV748DB1 can either be connected to the most positive supply voltage on the demoboard, or can be left floating.To power up the AN-H59DB1, ensure that the 3.3V power supply will be powered up first, and then the 12V power supply. The sequences on the HV738DB1 and HV748DB1 took into consideration using the protection diodes on each power line.The circuit is shown in Figure 6, the component placement in Figure 5, and the bill of materials is at the end of thisapplication note.PP The circuit in Figure 1 shows U5, the Supertex high volt -age current mode PWM controller, being used to generate the high voltage power supply for V PP . The maximum output power for V PP was set for 10mA at 90V, which is 900mW. With an input voltage of 12V, a converter frequency of 110 kHz with a 100µH inductor was chosen to provide the de -sired output power.The converter frequency is set by an external resistor, R20, across OSC IN and OSC OUT pins of U5. A 154kΩ resistor will set the frequency to about 110 kHz. R24 is the current sense resistor. 2.2Ω was used to set the maximum peak current limit to about 450mA. An RC filter, R23 and C15, is added between the current sense resistor and the current sense terminal pin 3 of U5. This reduces the leading edge spike on R24 from entering the current sense pin.Inductor L1 is being charged from the 12V input by M3. When M3 turns off, the energy in L1 is discharged into C16, which is the V PP output through D8. The V PP voltage is di-vided down by feedback resistors R25, R26, and R27. The wiper of R26 is connected to pin 14 of U5. The overall con -verter will regulate the voltage on pin 14 to 4.0V. Different V PP output voltages can be obtained by adjusting R26.When the wiper for R26 is set to the top, V PP can be calcu-lated as:where V FB is 4.0VWhen the wiper for R26 is set to the bottom, V PP can be calculated as:By adjusting potentiometer R26, V PP meets the adjustable target range of 15 to parator U6 will turn on LED D7 when the V PP output is out of regulation due to excessive load. During initial power up, C16 will be at 0V. D7 is therefore expected to be on until C16 is charged to the desired regulation voltage.Figure 1: Adjustable V PP Power SupplyV PPGNDV PP = 4.0V x ( 232k + 100k + 14.3k )= 12.1V 100k + 14.3k V PP= V FBx ( R25 + R26 + R27 )R26 + R27V PP = 4.0V x ( 232k + 100k + 14.3k )= 96.9V 14.3kV PP = V FBx ( R25 + R26 + R27 )R27NN The circuit in Figure 2 shows U7, the Supertex high voltage current mode PWM controller, being used to generate the high voltage power supply for V NN . The function of U7 is very similar to what was described in the V PP circuit description for U5. However, in this circuit a negative voltage is gener -ated from a positive input voltage source, therefore requir-ing a buck-boost topology. The maximum output power for V NN was set for -10mA at -90V which is 900mW. With an input voltage of 12V, a converter frequency of 110 kHz with a 100µH inductor was chosen to provide the desired output power.Inductor L2 is being charged from the 12V input by the par-allel combination of M6 and M7. When M6 and M7 turn off, the energy in L2 is discharged into C23, which is the V NNoutput through D10. M6 and M7 are high voltage P-channel MOSFETs. U7 is designed to drive a high voltage N-chan -nel MOSFET. The drive output for U7 therefore needs to be inverted. This is accomplished by M4 and M5.The feedback voltage that U7 detects on pin 14 is +4.0V. The V NN that needs to be sensed is a negative voltage. A cir-cuit is needed to make sure the feedback voltage is positive. This is consists of Q4, Q5, R33, R34, R35, R37, and R38. Q4 becomes a constant current sink set by the V NN voltageand R35. The same current will be flowing through R33 and R34.The voltage on the base of Q5 will be V IN minus the voltage drop across the sum of R33 and R34. By varying R34, the base voltage on Q5 will change. Q5 becomes a constant current source with a value set by its base voltage and R37. The current source of Q5 is going into R38, which creates a positive voltage that is now proportional to the magnitude of V NN .where V BE = 0.6V, V FB = 4.0V.When R34 is set to 100k, V NN is calculated to be:= -4.0VWhen R34 is set to 0k, V NN is calculated to be:= -97.4V By adjusting potentiometer R34, V NN meets the adjustable target range of -15 to parator U8 will turn on LED D9 when the V NN output isout of regulation due to excessive load. During initial power up, C23 will be at 0V. D9 is therefore expected to be on until C23 is charged to the desired regulation voltage.Figure 2: Adjustable V NN Power SupplyVNN-15V to -90V GNDV NN = V BE - ( R35 ) x (V BE + V FB x R37 ), R33 + R34 R38V NN = 0.6V - ( 273k) x (0.6V + 4.0V x 14.7k ) 4.99k + 100k 40.2k V NN = 0.6V - ( 273k ) x (0.6V + 4.0V x 14.7k )4.99k + 0k 40.2kVPF and VNF Circuit DescriptionThe three transmitter demoboards require two floating low voltage supplies, V PF and V NF . The floating supplies need to be adjustable to accommodate the different operating re-quirements for the three different boards. The V PF is 8.0 to 10V below the high voltage V PP positive supply. The V NF is 8.0 to 10V above the high voltage V NN negative supply. The two floating supplies are generated by using two isolated transformers, T1 and T2, and an isolated transformer driver, U1, as shown in Figure 4. Both outputs utilize adjustable low dropout linear regulators, U2 and U3, as shown in Figure 3. U2 and U3 are both Linear Technology LT1521, which has a reference voltage of 3.75V on the ADJ pin. For V PF , resistors R6, R7, and R8 set the output V PF voltage. R7 is a potentiom -eter for adjusting V PF . V PF can be calculated with the following equation:When R7 is set to 20kΩ, V PF becomes:When R7 is set to 0Ω, V PF becomes:Please note that the OUT pin on U2 is referenced to V PP , thereby setting V PF to be 8.0 to 10V below V PP . V NF can also be calculated in a similar manner using resistors R12, R13, and R14. Please note that the GND pin on U3 is referenced to V NN thereby setting V NF to be 8.0 to 10V above V NN .LED indicators, D5 and D11, start to turn on when the input current to U2 and U3 reaches an arbitrary value of 40mA. This is set by Q1 and R3 for V PF and Q2 and R9 for V NF . The input current can be calculated with the following equation: Input current = V EB = 0.5V = 41.3mA R 12.1Ω50mA current limits are added to protect against output shorts. The current limiter is consists of a depletion-mode MOSFET and a series source resistor. The resistor sets the current limit and can be estimated with the following equa -tion:R SERIES = V TH x ( √I LIM / I DSS - 1) where, I LIMV TH = pinch-off voltage for M1 and M2: -2.5V I LIM = desired current limit: 50mAI DSS = saturation current for M1 and M2: 1.1A R SERIES = 39.3Ω. A 40.2Ω resistor was used.Figure 3: Adjustable V PF and V NF Power SupplyV VNFVFPV PF = 3.75V x ( 45.3k + 20k + 24.9k )= 7.53V 20k + 24.9kV PF = 3.75V x ( 45.3k + 0k + 24.9k )= 10.6V 0 +24.9kV PF= V ADJx ( R6 + R7 + R8 )R7 + R8V DD Circuit DescriptionThe V DD output voltage utilizes an adjustable low dropout lin -ear regulator, U4 LT1521, as shown in Figure 4. The desiredadjustable output voltage range is 8.0 to 10V to accommo-date the different operating V DD voltages for the three differ-ent transmitter demoboards.The LT1521 has a reference voltage of 3.75V on the adj pin. Resistors R17, R18, and R19 set the output V DD voltage. R18 is a potentiometer for adjusting V DD . V DD can be calcu-lated with the following equation:When R18 is set to 20kΩ, V DD becomes:When R18 is set to 0Ω, V DD becomes:An LED indicator, D6, is included in case of excessive input,I IN, current. D6 is starts to turn on when the input currentreaches an arbitrary value of 20mA. This is set by Q3 and R15. When the emitter-base junction of Q3 is forward biased (0.5V), Q3 will start to turn on, thereby forward biasing D6.The I IN value to turn D6 on can be calculated with the follow -ing equation: I IN = V EB = 0.5V= 20.6mAR1524.3Ω 3.3V Input TerminalThe AN-H59DB1 has a 3.3V input terminal that is directly connected to the output terminal, V CC . There is no circuitry on this board that uses the 3.3V supply. It is only there as a convenient connection to the 8-pin header. V CC is the logic supply voltage for HV738DB1 and HV748DB1 and can oper-ate from 1.2 to 5V. However, most users will operate V CC at either 3.0 or 3.3V.Input and Output PowerThe output voltages from the AH-H59DB1 are all generated from the 12V input line. With no load on the outputs, the measured input current was about 70mA. This input current can vary from board to board due to variations in the isolated transformer.The maximum output power is:P OUT(MAX) = P VPP(MAX) + P VNN(MAX) + P VPF(MAX) + P VNF(MAX) + P VDD(MAX)P OUT(MAX) = 0.9W + 0.9W + 0.4W + 0.4W + 0.2W P OUT(MAX) = 2.8WUnder this condition, the 12V input current was measured to be 340mA. Input power is therefore 4.08W. This gives an approximate overall efficiency of 69% at full load.Figure 4: Adjustable V DD Power SupplyV IN = 12VVDD+8.0 to 10V GNDV DD = 3.75V x ( 45.3k + 20k + 24.9k )= 7.53V20k + 24.9kV DD = 3.75V x ( 45.3k + 0k + 24.9k )= 10.6V 0 + 24.9k V DD = V ADJ x ( R17 + R18 + R19 )R18 + R19VPF and VNF Output CurrentThe AN-H59DB1 can supply more than 40mA of current for the V PF and V NF outputs. The I NF and I PF input currents for the HV738 or the HV748 can be found in their respective datasheet but are summarized below:This is for continuous 5.0 MHz operation. For ultrasound, thehigh voltage transmitter is operating at very low duty cycles; 1% or lower. At a 1% duty cycle, the average current is ex -pected to be a 100 times lower. The 40mA output current ca -pability on the AN-H59DB1 is more than sufficient to power up the HV738 or the HV748.ConclusionThe main purpose of AN-H59DB1 power supply demoboard is to help the evaluation of the Supertex HV738DB1 and HV748DB1 demoboards by reducing the number of power supplies needed. The AN-H59DB1 was designed to operate from a single 12V input which should be commonly available in any engineering laboratory.The five on-board LEDs allow the user to quickly determine whether there is an overload condition on each of the supplylines. The five potentiometers allow the user to easily adjust each supply to meet their particular needs.Figure 5: AN-H59 Component PlacementFigure 6: AN-H59 Circuit SchematicVPPVPFVNFSupertex inc. does not recommend the use of its products in life support applications, and will not knowingly sell them for use in such applications unless it receives an adequate “product liability indemnification insurance agreement.” Supertex inc. does not assume responsibility for use of devices described, and limits its liability to the replacement of the devices determined defective due to workmanship. No responsibility is assumed for possible omissions and inaccuracies. Circuitry and specifications are subject to change without notice. For the latest product specifications refer to the Supertex inc. (website: http//)©2012 Supertex inc. All rights reserved. Unauthorized use or reproduction is prohibited.Supertex inc.1235 Bordeaux Drive, Sunnyvale, CA 94089。
top258pn

TOP252-262TOPSwitch-HX Family January 2009Enhanced EcoSmart ®, Integrated Off-Line Switcher with Advanced Feature Set and Extended Power Range®Product HighlightsLower System Cost, Higher Design FlexibilityMulti-mode operation maximizes efficiency at all loads New eSIP-7F and eSIP-7C packagesLow thermal impedance junction-to-case (2 °C per watt)Low height is ideal for adapters where space is limitedSimple mounting using a clip to aid low cost manufacturing Horizontal eSIP-7F package ideal for ultra low height adapter and monitor applicationsExtended package creepage distance from DRAIN pin to adjacent pin and to heat sinkNo heatsink required up to 35 W using P , G and M packages with universal input voltage and up to 48 W at 230 VACOutput overvoltage protection (OVP) is user programmable for latching/non-latching shutdown with fast AC reset Allows both primary and secondary sensingLine undervoltage (UV) detection prevents turn-off glitches Line overvoltage (OV) shutdown extends line surge limit Accurate programmable current limitOptimized line feed-forward for line ripple rejection132 kHz frequency (254Y-258Y and all E/L packages) reduces transformer and power supply sizeHalf frequency option for video applications Frequency jittering reduces EMI fi lter cost •••••••••••••••••Figure 1. Typical Flyback Application.Heatsink is connected to SOURCE for low EMIImproved auto-restart delivers <3% of maximum power in short circuit and open loop fault conditionsAccurate hysteretic thermal shutdown function automatically recovers without requiring a resetFully integrated soft-start for minimum start-up stress Extended creepage between DRAIN and all other pins improves fi eld reliability•••••Table 1.Output Power Table. (for notes see page 2).Rev. F 01/09EcoSmart ®– Energy Effi cientEnergy efficient over entire load range No-load consumptionLess than 200 mW at 230 VAC Standby power for 1 W input>600 mW output at 110 VAC input >500 mW output at 265 VAC inputDescriptionTOPSwitch-HX cost effectively incorporates a 700 V power MOSFET, high voltage switched current source, PWM control, oscillator, thermal shutdown circuit, fault protection and other control circuitry onto a monolithic device.••••••Figure 2. Typical Flyback Application TOP259YN, TOP260YN and TOP261YN.Y Package Option for TOP259-261In order to improve noise-immunity on large TOPSwitch-HX Y package parts, the F pin has been removed (TOP259-261YN are fi xed at 66 kHz switching frequency) and replaced with a SIGNAL GROUND (G) pin. This pin acts as a low noise path for the C pin capacitor and the X pin resistor. It is only required for the TOP259-261YN package parts.Notes for Table 1:1. Minimum continuous power in a typical non-ventilatedenclosed adapter measured at +50 °C ambient. Use of an external heat sink will increase power capability. 2. Minimum continuous power in an open frame design at+50 °C ambient.3. Peak power capability in any design at +50 °C ambient.4. 230 VAC or 110/115 VAC with doubler.5. Packages: P: DIP-8C, G: SMD-8C, M: SDIP-10C,Y: TO-220-7C, E: eSIP-7C, L: eSIP-7F .See part ordering information.6. TOP261 and TOP262 have the same current limit set point. Insome applications TOP262 may run cooler than TOP261 due to a lower R DS(ON) for the larger device.7. TOP256E package parts are available with Green (HalogenFree) mold compound. See Part Ordering Information on page 47. Parametrically green material encapsulated E package parts are identical to non-green parts. Section ListFunctional Block Diagram (4)Pin Functional Description (6)TOPSwitch-HX Family Functional Description (7)CONTROL (C) Pin Operation (8)Oscillator and Switching Frequency (8)Pulse Width Modulator (9)Maximum Load Cycle (9)ErrorAmplifier (9)On-Chip Current Limit with External Programmability (9)Line Under-Voltage Detection (UV) (10)Line Overvoltage Shutdown (OV) (11)Hysteretic or Latching Output Overvoltage Protection (OVP) (11)Line Feed-Forward with DCMAX Reduction (13)Remote ON/OFF and Synchronization (13)Soft-Start (13)Shutdown/Auto-Restart (13)Hysteretic Over-Temperature Protection (13)BandgapReference (13)High-Voltage Bias Current Source (13)Typical Uses of FREQUENCY (F) Pin (15)Typical Uses of VOLTAGE MONITOR (V) and EXTERNAL CURRENT LIMIT (X) Pins (16)Typical Uses of MULTI-FUNCTION (M) Pin (18)Application Examples (21)A High Effi ciency, 35 W, Dual Output – Universal Input Power Supply (21)A High Effi ciency, 1500 W, 250-380 VDC Input Power Supply (22)A High Effi ciency, 20 W Continuous – 80 W Peak, Universal Input Power Supply (23)A High Effi ciency, 65 W, Universal Input Power Supply (24)Key Application Considerations (25)TOPSwitch-HX vs.TOPSwitch-GX (25)TOPSwitch-HX Design Considerations (26)TOPSwitch-HX Layout Considerations (27)Quick Design Checklist (31)DesignTools (31)Product Specifi cations and Test Conditions (32)Typical Performance Characteristics (39)Package Outlines (43)Part Ordering Information (47)Rev. F 01/09Rev. F 01/09Figure 3a. Functional Block Diagram (P and G Packages).Figure 3b. Functional Block Diagram (M Package).Rev. F 01/09Figure 3c. Functional Block Diagram (TOP254-258 YN Package and all eSIP Packages).Figure 3d. Functional Block Diagram TOP259YN, TOP260YN, TOP261YN.Rev. F 01/09Pin Functional DescriptionDRAIN (D) Pin:High-voltage power MOSFET DRAIN pin. The internal start-up bias current is drawn from this pin through a switched high-voltage current source. Internal current limit sense point for drain current.CONTROL (C) Pin:Error amplifi er and feedback current input pin for duty cycle control. Internal shunt regulator connection to provide internal bias current during normal operation. It is also used as the connection point for the supply bypass and auto-restart/compensation capacitor.EXTERNAL CURRENT LIMIT (X) Pin (Y, M, E and L package):Input pin for external current limit adjustment and remote ON/OFF. A connection to SOURCE pin disables all functions on this pin.Figure 4. Pin Confi guration (Top View).P I -4711-021308Figure 5. TOP254-258 Y and All M/E/L Package Line Sense and Externally Set Current Limit.Figure 7. P/G Package Line Sense.P I -4983-021308Figure 6. TOP259-261 Y Package Line Sense and External Current Limit.VOLTAGE MONITOR (V) Pin (Y & M package only):Input for OV, UV, line feed forward with DC MAX reduction, output overvoltage protection (OVP), remote ON/OFF and device reset. A connection to the SOURCE pin disables all functions on this pin.MULTI-FUNCTION (M) Pin (P & G packages only):This pin combines the functions of the VOLTAGE MONITOR (V) and EXTERNAL CURRENT LIMIT (X) pins of the Y package into one pin. Input pin for OV, UV, line feed forward with DC MAXRev. F 01/09Figure 8. P/G Package Externally Set Current Limit.reduction, output overvoltage protection (OVP), external current limit adjustment, remote ON/OFF and device reset. Aconnection to SOURCE pin disables all functions on this pin and makes TOPSwitch-HX operate in simple three terminal mode (like TOPSwitch-II).FREQUENCY (F) Pin (TOP254-258Y, and all E and L packages):Input pin for selecting switching frequency 132 kHz if connected to SOURCE pin and 66 kHz if connected to CONTROL pin. The switching frequency is internally set for fi xed 66 kHzoperation in the P , G, M package and TOP259YN, TOP260YN and TOP261YN.SIGNAL GROUND (G) Pin (TOP259YN, TOP260YN & TOP261YN only):Return for C pin capacitor and X pin resistor.SOURCE (S) Pin:Output MOSFET source connection for high voltage power return. Primary side control circuit common and reference point.TOPSwitch-HX Family Functional DescriptionLike TOPSwitch-GX, TOPSwitch-HX is an integrated switched mode power supply chip that converts a current at the control input to a duty cycle at the open drain output of a high voltage power MOSFET. During normal operation the duty cycle of the power MOSFET decreases linearly with increasing CONTROL pin current as shown in Figure 9.In addition to the three terminal TOPSwitch features, such as the high voltage start-up, the cycle-by-cycle current limiting, loop compensation circuitry, auto-restart and thermalshutdown, the TOPSwitch-HX incorporates many additional functions that reduce system cost, increase power supply performance and design fl exibility. A patented high voltageCMOS technology allows both the high-voltage power MOSFET and all the low voltage control circuitry to be cost effectively integrated onto a single monolithic chip.Three terminals, FREQUENCY, VOLTAGE-MONITOR, andEXTERNAL CURRENT LIMIT (available in Y and E/L packages),two terminals, VOLTAGE-MONITOR and EXTERNAL CURRENT LIMIT (available in M package) or one terminal MULTI-FUNCTION (available in P and G package) have been used to implement some of the new functions. These terminals can be connected to the SOURCE pin to operate the TOPSwitch-HX in aTOPSwitch-like three terminal mode. However, even in this three terminal mode, the TOPSwitch-HX offers many transparent features that do not require any external components:A fully integrated 17 ms soft-start significantly reduces or eliminates output overshoot in most applications by sweeping both current limit and frequency from low to high to limit the peak currents and voltages during start-up.A maximum duty cycle (DC MAX ) of 78% allows smaller inputstorage capacitor, lower input voltage requirement and/or higher power capability.Multi-mode operation optimizes and improves the powersupply effi ciency over the entire load range while maintaining good cross regulation in multi-output supplies.1.2.3.Figure 9. Control Pin Characteristics (Multi-Mode Operation).Rev. F 01/09Switching frequency of 132 kHz reduces the transformer sizewith no noticeable impact on EMI.Frequency jittering reduces EMI in the full frequency mode athigh load condition.Hysteretic over-temperature shutdown ensures automaticrecovery from thermal fault. Large hysteresis prevents circuit board overheating.Packages with omitted pins and lead forming provide largedrain creepage distance.Reduction of the auto-restart duty cycle and frequency toimprove the protection of the power supply and load during open loop fault, short circuit, or loss of regulation.Tighter tolerances on I 2f power coeffi cient, current limitreduction, PWM gain and thermal shutdown threshold.The VOLTAGE-MONITOR (V) pin is usually used for line sensing by connecting a 4 M Ω resistor from this pin to the rectifi ed DC high voltage bus to implement line overvoltage (OV), under-voltage (UV) and dual-slope line feed-forward with DC MAXreduction. In this mode, the value of the resistor determines the OV/UV thresholds and the DC MAX is reduced linearly with a dual slope to improve line ripple rejection. In addition, it also provides another threshold to implement the latched and hysteretic output overvoltage protection (OVP). The pin can also be used as a remote ON/OFF using the I UV threshold.The EXTERNAL CURRENT LIMIT (X) pin can be used to reduce the current limit externally to a value close to the operating peak current, by connecting the pin to SOURCE through a resistor. This pin can also be used as a remote ON/OFF input.For the P and G package the VOLTAGE-MONITOR andEXTERNAL CURRENT LIMIT pin functions are combined on one MULTI-FUNCTION (M) pin. However, some of the functions become mutually exclusive.The FREQUENCY (F) pin in the TOP254-258 Y and E/L packages set the switching frequency in the full frequency PWM mode to the default value of 132 kHz when connected to SOURCE pin. A half frequency option of 66 kHz can be chosen by connecting this pin to the CONTROL pin instead. Leaving this pin open is not recommended. In the P , G and M packages and the TOP259-261 Y packages, the frequency is set internally at 66 kHz in the full frequency PWM mode.CONTROL (C) Pin OperationThe CONTROL pin is a low impedance node that is capable of receiving a combined supply and feedback current. During normal operation, a shunt regulator is used to separate thefeedback signal from the supply current. CONTROL pin voltage V C is the supply voltage for the control circuitry including the MOSFET gate driver. An external bypass capacitor closely connected between the CONTROL and SOURCE pins is required to supply the instantaneous gate drive current. The total amount of capacitance connected to this pin also sets the auto-restart timing as well as control loop compensation.When rectifi ed DC high voltage is applied to the DRAIN pin during start-up, the MOSFET is initially off, and the CONTROL pin capacitor is charged through a switched high voltage4.5.6.7.8.9.current source connected internally between the DRAIN and CONTROL pins. When the CONTROL pin voltage V C reaches approximately 5.8 V, the control circuitry is activated and the soft-start begins. The soft-start circuit gradually increases the drain peak current and switching frequency from a low starting value to the maximum drain peak current at the full frequency over approximately 17 ms. If no external feedback/supplycurrent is fed into the CONTROL pin by the end of the soft-start, the high voltage current source is turned off and the CONTROL pin will start discharging in response to the supply current drawn by the control circuitry. If the power supply is designed properly, and no fault condition such as open loop or shorted output exists, the feedback loop will close, providing external CONTROL pin current, before the CONTROL pin voltage has had a chance to discharge to the lower threshold voltage of approximately 4.8 V (internal supply undervoltage lockout threshold). When the externally fed current charges theCONTROL pin to the shunt regulator voltage of 5.8 V, current in excess of the consumption of the chip is shunted to SOURCE through an NMOS current mirror as shown in Figure 3. The output current of that NMOS current mirror controls the duty cycle of the power MOSFET to provide closed loop regulation. The shunt regulator has a fi nite low output impedance Z C that sets the gain of the error amplifi er when used in a primary feedback confi guration. The dynamic impedance Z C of the CONTROL pin together with the external CONTROL pin capacitance sets the dominant pole for the control loop.When a fault condition such as an open loop or shorted output prevents the fl ow of an external current into the CONTROL pin, the capacitor on the CONTROL pin discharges towards 4.8 V. At 4.8 V, auto-restart is activated, which turns the output MOSFET off and puts the control circuitry in a low current standby mode. The high-voltage current source turns on and charges the external capacitance again. A hysteretic internal supply undervoltage comparator keeps V C within a window of typically 4.8 V to 5.8 V by turning the high-voltage current source on and off as shown in Figure 11. The auto-restart circuit has a divide-by-sixteen counter, which prevents the output MOSFET from turning on again until sixteen discharge/charge cycles have elapsed. This is accomplished by enabling the output MOSFET only when the divide-by-sixteen counter reaches the full count (S15). The counter effectively limitsTOPSwitch-HX power dissipation by reducing the auto-restart duty cycle to typically 2%. Auto-restart mode continues until output voltage regulation is again achieved through closure of the feedback loop.Oscillator and Switching FrequencyThe internal oscillator linearly charges and discharges an internal capacitance between two voltage levels to create atriangular waveform for the timing of the pulse width modulator. This oscillator sets the pulse width modulator/current limit latch at the beginning of each cycle.The nominal full switching frequency of 132 kHz was chosen to minimize transformer size while keeping the fundamental EMI frequency below 150 kHz. The FREQUENCY pin (available only in TOP254-258 Y and E, L packages), when shorted to the CONTROL pin, lowers the full switching frequency to 66 kHzRev. F 01/09Figure 10. Switching Frequency Jitter (Idealized V DRAIN Waveforms).(half frequency), which may be preferable in some cases such as noise sensitive video applications or a high effi ciency standby mode. Otherwise, the FREQUENCY pin should be connected to the SOURCE pin for the default 132 kHz. In the M, P and G packages and the TOP259-261 Y package option, the full frequency PWM mode is set at 66 kHz, for higher effi ciency and increased output power in all applications.To further reduce the EMI level, the switching frequency in the full frequency PWM mode is jittered (frequency modulated) by approximately ±2.5 kHz for 66 kHz operation or ±5 kHz for 132 kHz operation at a 250 Hz (typical) rate as shown in Figure 10. The jitter is turned off gradually as the system is entering the variable frequency mode with a fi xed peak drain current.Pulse Width ModulatorThe pulse width modulator implements multi-mode control by driving the output MOSFET with a duty cycle inversely proportional to the current into the CONTROL pin that is in excess of the internal supply current of the chip (see Figure 9). The feedback error signal, in the form of the excess current, is fi ltered by an RC network with a typical corner frequency of 7 kHz to reduce the effect of switching noise in the chip supply current generated by the MOSFET gate driver.To optimize power supply effi ciency, four different control modes are implemented. At maximum load, the modulator operates in full frequency PWM mode; as load decreases, the modulator automatically transitions, fi rst to variable frequency PWM mode, then to low frequency PWM mode. At light load, the control operation switches from PWM control to multi-cycle-modulation control, and the modulator operates in multi-cycle-modulation mode. Although different modes operate differently to make transitions between modes smooth, the simple relationship between duty cycle and excess CONTROL pin current shown in Figure 9 is maintained through all three PWM modes. Please see the following sections for the details of the operation of each mode and the transitions between modes.Full Frequency PWM mode: The PWM modulator enters full frequency PWM mode when the CONTROL pin current (I C ) reaches I B . In this mode, the average switching frequency is kept constant at f OSC (66 kHz for P , G and M packages and TOP259-261 Y, pin selectable 132 kHz or 66 kHz for Y and E/Lpackages). Duty cycle is reduced from DC MAX through the reduction of the on-time when I C is increased beyond I B . This operation is identical to the PWM control of all other TOPSwitch families. TOPSwitch-HX only operates in this mode if the cycle-by-cycle peak drain current stays above k PS(UPPER)*I LIMIT (set), where k PS(UPPER) is 55% (typical) and I LIMIT (set) is the current limit externally set via the X or M pin.Variable Frequency PWM mode: When peak drain current is lowered to k PS(UPPER)* I LIMIT (set) as a result of power supply load reduction, the PWM modulator initiates the transition to variable frequency PWM mode, and gradually turns off frequency jitter. In this mode, peak drain current is held constant at k PS(UPPER)* I LIMIT (set) while switching frequency drops from the initial full frequency of f OSC (132 kHz or 66 kHz) towards the minimum frequency of f MCM(MIN) (30 kHz typical). Duty cycle reduction is accomplished by extending the off-time.Low Frequency PWM mode: When switching frequencyreaches f MCM(MIN) (30 kHz typical), the PWM modulator starts to transition to low frequency mode. In this mode, switchingfrequency is held constant at f MCM(MIN) and duty cycle is reduced, similar to the full frequency PWM mode, through the reduction of the on-time. Peak drain current decreases from the initial value of k PS(UPPER)* I LIMIT (set) towards the minimum value ofk PS(LOWER)*I LIMIT (set), where k PS(LOWER) is 25% (typical) and I LIMIT (set) is the current limit externally set via the X or M pin.Multi-Cycle-Modulation mode: When peak drain current is lowered to k PS(LOWER)*I LIMIT (set), the modulator transitions to multi-cycle-modulation mode. In this mode, at each turn-on, the modulator enables output switching for a period of T MCM(MIN) at the switching frequency of f MCM(MIN) (4 or 5 consecutive pulses at 30 kHz) with the peak drain current of k PS(LOWER)*I LIMIT (set), and stays off until the CONTROL pin current falls below I C(OFF). This mode of operation not only keeps peak drain current low but also minimizes harmonic frequencies between 6 kHz and30 kHz. By avoiding transformer resonant frequency this way, all potential transformer audible noises are greatly supressed.Maximum Duty CycleThe maximum duty cycle, DC MAX , is set at a default maximum value of 78% (typical). However, by connecting the VOLTAGE-MONITOR or MULTI-FUNCTION pin (depending on the package) to the rectifi ed DC high voltage bus through a resistor with appropriate value (4 M Ω typical), the maximum duty cycle can be made to decrease from 78% to 40% (typical) when input line voltage increases from 88 V to 380 V, with dual gain slopes.Error Amplifi erThe shunt regulator can also perform the function of an error amplifi er in primary side feedback applications. The shunt regulator voltage is accurately derived from a temperature-compensated bandgap reference. The CONTROL pin dynamic impedance Z C sets the gain of the error amplifi er. TheCONTROL pin clamps external circuit signals to the V C voltage level. The CONTROL pin current in excess of the supply current is separated by the shunt regulator and becomes the feedback current I fb for the pulse width modulator.Rev. F 01/09On-Chip Current Limit with External ProgrammabilityThe cycle-by-cycle peak drain current limit circuit uses the output MOSFET ON-resistance as a sense resistor. A current limit comparator compares the output MOSFET on-state drain to source voltage V DS(ON) with a threshold voltage. High drain current causes V DS(ON) to exceed the threshold voltage and turns the output MOSFET off until the start of the next clock cycle. The current limit comparator threshold voltage is temperature compensated to minimize the variation of the current limit due to temperature related changes in R DS(ON) of the output MOSFET. The default current limit of TOPSwitch-HX is preset internally. However, with a resistor connected between EXTERNAL CURRENT LIMIT (X) pin (Y, E/L and M packages) or MULTI-FUNCTION (M) pin (P and G package) and SOURCE pin (for TOP259-261 Y, the X pin is connected to the SIGNAL GROUND (G) pin), current limit can be programmed externally to a lower level between 30% and 100% of the default current limit. By setting current limit low, a larger TOPSwitch-HX than necessary for the power required can be used to take advantage of the lower R DS(ON) for higher effi ciency/smaller heat sinkingrequirements. TOPSwitch-HX current limit reduction initial tolerance through the X pin (or M pin) has been improved signifi cantly compare with previous TOPSwitch-GX. With a second resistor connected between the EXTERNAL CURRENT LIMIT (X) pin (Y, E/L and M packages) or MULTI-FUNCTION (M) pin (P and G package) and the rectifi ed DC high voltage bus, the current limit is reduced with increasing line voltage, allowing a true power limiting operation against line variation to be implemented. When using an RCD clamp, this power limiting technique reduces maximum clamp voltage at high line. This allows for higher refl ected voltage designs as well as reducing clamp dissipation.The leading edge blanking circuit inhibits the current limitcomparator for a short time after the output MOSFET is turned on. The leading edge blanking time has been set so that, if a power supply is designed properly, current spikes caused by primary-side capacitances and secondary-side rectifi er reverse recovery time should not cause premature termination of the switching pulse.The current limit is lower for a short period after the leading edge blanking time. This is due to dynamic characteristics of the MOSFET. During startup and fault conditions the controller prevents excessive drain currents by reducing the switching frequency.Line Undervoltage Detection (UV)At power up, UV keeps TOPSwitch-HX off until the input line voltage reaches the undervoltage threshold. At power down, UV prevents auto-restart attempts after the output goes out of regulation. This eliminates power down glitches caused by slow discharge of the large input storage capacitor present in applications such as standby supplies. A single resistor connected from the VOLTAGE-MONITOR pin (Y, E/L and M packages) or MULTI-FUNCTION pin (P and G packages) to the rectifi ed DC high voltage bus sets UV threshold during power up. Once the power supply is successfully turned on, the UV threshold is lowered to 44% of the initial UV threshold to allow extended input voltage operating range (UV low threshold). If the UV low threshold is reached during operation without the power supply losing regulation, the device will turn off and stay off until UV (high threshold) has been reached again. If the power supply loses regulation before reaching the UV lowthreshold, the device will enter auto-restart. At the end of each auto-restart cycle (S15), the UV comparator is enabled. If the UV high threshold is not exceeded, the MOSFET will bedisabled during the next cycle (see Figure 11). The UV feature can be disabled independent of the OV feature.Figure 11. Typical Waveforms for (1) Power Up (2) Normal Operation (3) Auto-Restart (4) Power Down.Line Overvoltage Shutdown (OV)The same resistor used for UV also sets an overvoltage threshold, which, once exceeded, will force TOPSwitch-HX to stop switching instantaneously (after completion of the current switching cycle). If this condition lasts for at least 100 μs, the TOPSwitch-HX output will be forced into off state. Unlike with TOPSwitch-GX, however, when the line voltage is back to normal with a small amount of hysteresis provided on the OV threshold to prevent noise triggering, the state machine sets to S13 and forces TOPSwitch-HX to go through the entire auto-restart sequence before attempting to switch again. The ratio of OV and UV thresholds is preset at 4.5, as can be seen in Figure 12. When the MOSFET is off, the rectifi ed DC high voltage surge capability is increased to the voltage rating of the MOSFET (700 V), due to the absence of the refl ected voltage and leakage spikes on the drain. The OV feature can be disabled independent of the UV feature.In order to reduce the no-load input power of TOPSwitch-HX designs, the V-pin (or M-pin for P Package) operates at very low currents. This requires careful layout considerations when designing the PCB to avoid noise coupling. Traces and components connected to the V-pin should not be adjacent to any traces carrying switching currents. These include the drain, clamp network, bias winding return or power traces from otherconverters. If the line sensing features are used, then the senseresistors must be placed within 10 mm of the V-pin to minimizethe V-pin node area. The DC bus should then be routed to theline sense resistors. Note that external capacitance must notbe connected to the V-pin as this may cause misoperaton of theV pin related functions.Hysteretic or Latching Output Overvoltage Protection (OVP) The detection of the hysteretic or latching output overvoltageprotection (OVP) is through the trigger of the line overvoltagethreshold. The V-pin or M-pin voltage will drop by 0.5 V, andthe controller measures the external attached impedanceimmediately after this voltage drops. If IVor IMexceeds IOV(LS) (336 μA typical) longer than 100 μs, TOPSwitch-HX will latchinto a permanent off state for the latching OVP. It only can bereset if VVor VMgoes below 1 V or VCgoes below the power-up-reset threshold (VC(RESET)) and then back to normal.If IVor IMdoes not exceed IOV(LS)or exceeds no longer than100 μs, TOPSwitch-HX will initiate the line overvoltage and thehysteretic OVP. Their behavior will be identical to the line overvoltage shutdown (OV) that has been described in detail in the previous section.Voltage Monitor and External Current Limit Pin Table**This table is only a partial list of many VOLTAGE MONITOR and EXTERNAL CURRENT LIMIT Pin Confi gurations that are possible. Table 2. VOLTAGE MONITOR (V) Pin and EXTERNAL CURRENT LIMIT (X) Pin Confi guration Options.Multi-Function Pin Table**This table is only a partial list of many MULTI-FUNCTIONAL Pin Confi gurations that are possible.Table 3. MULTI-FUNCTION (M) Pin Confi guration Options.。
CommScope 617-894和1695-2690MHz多频段65° HPBW 12端口扇形抗干
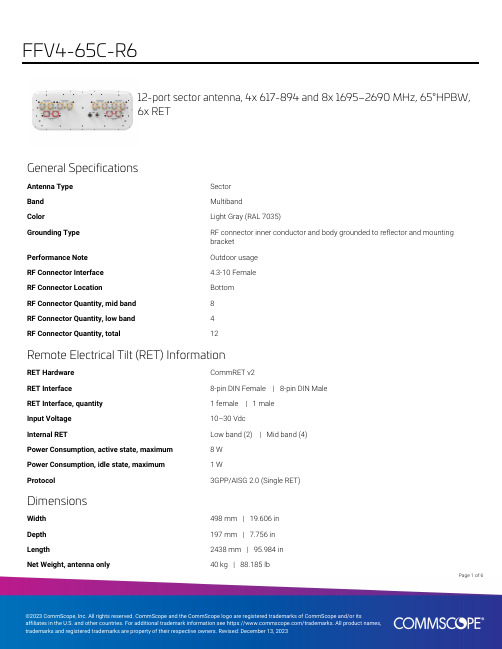
12-port sector antenna, 4x 617-894 and 8x 1695–2690 MHz, 65°HPBW,6x RETGeneral SpecificationsAntenna Type SectorBand MultibandColor Light Gray (RAL 7035)Grounding Type RF connector inner conductor and body grounded to reflector and mountingbracketPerformance Note Outdoor usageRF Connector Interface 4.3-10 FemaleRF Connector Location BottomRF Connector Quantity, mid band8RF Connector Quantity, low band4RF Connector Quantity, total12Remote Electrical Tilt (RET) InformationRET Hardware CommRET v2RET Interface8-pin DIN Female | 8-pin DIN MaleRET Interface, quantity 1 female | 1 maleInput Voltage10–30 VdcInternal RET Low band (2) | Mid band (4)Power Consumption, active state, maximum8 WPower Consumption, idle state, maximum 1 WProtocol3GPP/AISG 2.0 (Single RET)DimensionsWidth498 mm | 19.606 inDepth197 mm | 7.756 inLength2438 mm | 95.984 inNet Weight, antenna only40 kg | 88.185 lb16Page ofArray LayoutPort ConfigurationPage of26Page of 36Logo ImageElectrical Specifications50 ohmImpedance50 ohmOperating Frequency Band1695 – 2690 MHz | 617 – 894 MHzPolarization±45°Total Input Power, maximum1,400 W @ 50 °CElectrical SpecificationsR1,R2R1,R2Y1,Y2,Y3,Y4Y1,Y2,Y3,Y4Y1,Y2,Y3,Y4Y1,Y2,Y3,Y4Y1,Y2,Y3,Y4 Frequency Band, MHz617–698698–8941695–18801850–19901920–22002300–25002500–2690RF Port1,2,3,41,2,3,45,6,7,8,9,10,11,125,6,7,8,9,10,11,125,6,7,8,9,10,11,125,6,7,8,9,10,11,125,6,7,8,9,10,11,12 Gain, dBi1515.717.217.818.118.518.6Gain at Mid Tilt, dBi14.715.516.717.417.818.318.166566566645959 Beamwidth,Horizontal, degrees10.38.7 5.6 5.35 4.5 4.2 Beamwidth, Vertical,degreesBeam Tilt, degrees2–132–132–122–122–122–122–12USLS (First Lobe), dB18161922222221Front-to-Back Ratio at29313433333027180°, dB20222629272422Front-to-Back TotalPower at 180° ± 30°, dB25252525252525Isolation, CrossPolarization, dB25252525252525Isolation, Inter-band,dBVSWR | Return loss, dB 1.5 | 14.0 1.5 | 14.0 1.5 | 14.0 1.5 | 14.0 1.5 | 14.0 1.5 | 14.0 1.5 | 14.0PIM, 3rd Order, 2 x 20-150-150-150-150-150-150-150W, dBc250250200200200200200Input Power per Portat 50°C, maximum,wattsElectrical Specifications, BASTAFrequency Band, MHz617–698698–8941695–18801850–19901920–22002300–25002500–269014.515.216.617.317.718.118Gain by all Beam Tilts,average, dBiGain by all Beam Tilts±0.8±0.5±0.7±0.5±0.5±0.6±0.5 Tolerance, dBBeamwidth, Horizontal ±4±5±5±4±4±8±746Page ofTolerance, degreesBeamwidth, VerticalTolerance, degrees±0.7±1±0.3±0.2±0.3±0.3±0.3USLS, beampeak to20° above beampeak,dB17151617171716CPR at Boresight, dB20181919181413 CPR at Sector, dB10887755 Mechanical SpecificationsWind Loading @ Velocity, frontal829.0 N @ 150 km/h (186.4 lbf @ 150 km/h)Wind Loading @ Velocity, lateral217.0 N @ 150 km/h (48.8 lbf @ 150 km/h)Wind Loading @ Velocity, maximum1,102.0 N @ 150 km/h (247.7 lbf @ 150 km/h)Wind Loading @ Velocity, rear570.0 N @ 150 km/h (128.1 lbf @ 150 km/h)Wind Speed, maximum241 km/h (150 mph)Packaging and WeightsWidth, packed565 mm | 22.244 inDepth, packed309 mm | 12.165 inLength, packed2625 mm | 103.347 inWeight, gross53.3 kg | 117.506 lbRegulatory Compliance/CertificationsAgency ClassificationCHINA-ROHS Below maximum concentration valueISO 9001:2015Designed, manufactured and/or distributed under this quality management systemREACH-SVHC Compliant as per SVHC revision on /ProductComplianceROHS CompliantUK-ROHSCompliantIncluded ProductsBSAMNT-2F–Mounting bracket for cylindrical pipe installations (60-115mm pipe diameter) for fix mechanicaltilt applications.Page of56* FootnotesPerformance Note Severe environmental conditions may degrade optimum performance66Page of。
7777型号选择指南:Meredian II电极线性或浸湿装配说明书

51-52-16U-17Issue 29Page 1 of 3Series 7777Model Selection GuideMeredian® II ElectrodeIn-Line or Immersion MountingKEY NUMBERSelectionAvailabilityDescription7777 Electrode Mounting07777In-line mountingTee not includedTABLE II - Mounting, Leads, Instrument Connection, Part No.Meredian II Glass pH:Mounting Leads (Integral)Instrument Connection P/NIn-Line Quick Disconnect Direct Connection to:09c (Note 3)UDA2182, APT2000/4000Immersion20' Tinned c (6,10 meters)In-Line18c Immersion12' (6 pin preamp connector)03d (3,66 meters)In-Line14dORP Electrodes:Mounting LeadsTemp.In-LineQuick Disconnect11c (Note 3)12c Immersion 20' Tinned -5 to 110oC07c (6,10 meters) -5 to 110oC08c In-Line20' Tinned -5 to 110oC27c (6,10 meters) -5 to 110oC28c 50' Tinned 29c(15,25 meters)RESTRICTIONSRestrictionLetter Table Selection Tablec I 0d I3Note 1:For longer preamp to instrument cables, see Accessories and Spare Parts List.Note 2: Gold is generally used in applications containing cyanide; platinum is used for all others.Note 3:Please order corresponding Quick Disconnect sensor-to-instrument cable from accessory table.50027820-502 (gold)16Available Only With51451341-504 (gold) 51451326-50431074387-501 -5 to 110oC 51451340-505 (platinum)50027820-501Not Available With31074399-50151451340-503 (platinum) 51451340-504 (platinum) -5 to 110oC-5 to 110oC50027820-503 (platinum)Selection51451341-503 (gold) P/N (Note 2)Direct Connection to:51451326-503Preamp Connection UDA2182, APT2000/4000Series 7777Accessories andReplacement PartsDescription Part NumberDirections - Meredian II Mounting70-82-25-05Directions - Preamp (31075704-501 & 31075705-501)70-82-25-57Directions - Meredian II Electrode70-82-25-56pH Buffer Solutions4.0131103001-5016.8631103002-5019.1831103003-501Extension Cables for Sensors with Quick Disconnect Option:2m (6.56 Ft.)50024092-5013m (9.84 Ft.)50024092-5026m (19.69 Ft.)50024092-503Only Honeywell Extension Cables can be used.Cable - preamp to instrumentTable I = 3 - 20 feet (6,10 meters)31075723-501- 50 feet (15,25 meters)51309677-501Smooth Electrode Tip - In-Line Mounting31074331-501Guarded Electrode Tip - Immersion Mounting31074330-501Frit 0-Ring (for replacement tips)31074365-501Junction Box50034477-501Special CPVC pipe tee for 3/4" in-line mounting31120167-501Cable grip - for Meredian glass and preamp to instrument cables (3/4" NPT31074354-501 connection and 0.25" grommet hole)。
1752A Category 5e+ Patch Cable 商品说明书
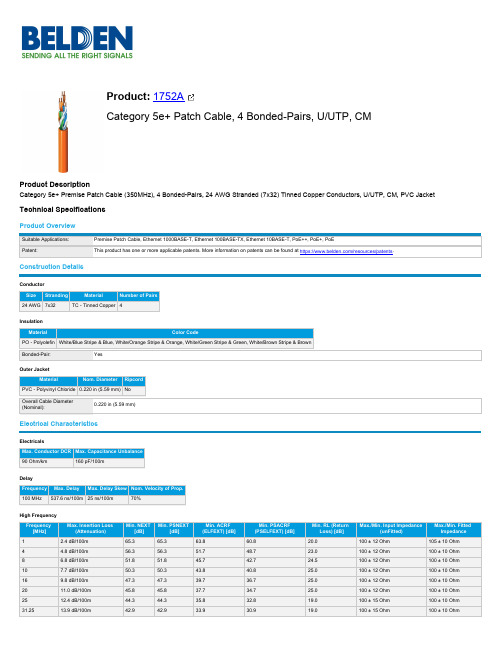
Product:1752ACategory 5e+ Patch Cable, 4 Bonded-Pairs, U/UTP, CMProduct DescriptionCategory 5e+ Premise Patch Cable (350MHz), 4 Bonded-Pairs, 24 AWG Stranded (7x32) Tinned Copper Conductors, U/UTP, CM, PVC Jacket Technical SpecificationsProduct OverviewConstruction DetailsConductorInsulationOuter JacketElectrical CharacteristicsElectricalsDelayHigh Frequency62.520.1 dB/100m38.438.427.824.819.0100 ± 15 Ohm100 ± 10 Ohm 10026.1 dB/100m35.335.323.820.819.0100 ± 15 Ohm100 ± 10 Ohm 15533.3 dB/100m32.532.519.916.919.0100 ± 18 Ohm100 ± 10 Ohm 20038.4 dB/100m30.830.817.714.719.0100 ± 18 Ohm100 ± 10 Ohm 25043.7 dB/100m29.329.315.812.818.0100 ± 20 Ohm100 ± 10 Ohm 30048.6 dB/100m28.228.214.211.218.0100 ± 20 Ohm100 ± 10 Ohm 31049.5 dB/100m27.927.913.910.918.0100 ± 20 Ohm100 ± 10 Ohm 35053.2 dB/100m27.227.212.99.917.0100 ± 22 Ohm100 ± 10 OhmVoltageUL Voltage Rating300 V (CM)Mechanical CharacteristicsTemperatureUL Temperature Operating Installation Storage75°C-20°C To +75°C0°C To +50°C-20°C To +75°CBend RadiusStationary Min.Installation Min.1.0 in (25 mm)2.2 in (56 mm)Max. Pull Tension:40 lbs (18 kg)Bulk Cable Weight:21 lbs/1000ftStandards and ComplianceEnvironmental Suitability:Indoor, IndoorSustainability:Product Lens™, Environmental Product Declaration (EPD) AvailableFlammability / Reaction to Fire:UL 1685 (UL 1581) Vertical Tray, FT1, FT1NEC / UL Compliance:Article 800, CMCEC / C(UL) Compliance:CMICEA Compliance:S-90-661-2012IEEE Compliance:IEEE 802.3bt Type 1, Type 2, Type 3NEMA Compliance:NEMA WC-63.1Data Category:Category 5eTIA/EIA Compliance:ANSI/TIA-568.2-D Category 5eThird Party PerformanceCategory 5e PatchVerification:ISO/IEC Compliance:ISO/IEC 11801-1, IEC 61156-6European DirectiveEU CE Mark, EU Directive 2015/863/EU (RoHS 2 amendment), REACH, EU Directive 2011/65/EU (RoHS 2), EU Directive 2012/19/EU (WEEE), REACH: 2020-01-16 Compliance:APAC Compliance:China RoHS II (GB/T 26572-2011)Product NotesNotes:Electrical values are expected performance based on cable testing and representative performance within a typical Belden system. Print Includes Descending Footage Markings.Conductor strands are bonded together.HistoryUpdate and Revision:Revision Number: 0.408 Revision Date: 12-15-2021VariantsItem #Color Putup Type Length UPC1752A 0101000Black Reel1,000 ft6128251222101752A 010U1000Black UnReel1,000 ft6128251222031752A 0061000Blue Reel1,000 ft6128251221731752A 006U1000Blue UnReel1,000 ft6128251221661752A F2V1000Gray Reel1,000 ft6128251220741752A F2VU1000Gray UnReel1,000 ft6128251220671752A 0051000Green Reel1,000 ft6128251221591752A 005U1000Green UnReel1,000 ft6128251221421752A 0031000Orange Reel1,000 ft6128251221111752A 003U1000Orange UnReel1,000 ft6128251221041752A 007U1000Purple UnReel1,000 ft6128251221801752A 0021000Red Reel1,000 ft6128251220981752A 002U1000Red UnReel1,000 ft6128251220811752A 0041000Yellow Reel1,000 ft6128251221351752A 004U1000Yellow UnReel1,000 ft612825122128© 2022 Belden, IncAll Rights Reserved.Although Belden makes every reasonable effort to ensure their accuracy at the time of this publication, information and specifications described here in are subject to error or omission and to change without notice, and the listing of such information and specifications does not ensure product availability.Belden provides the information and specifications herein on an "ASIS" basis, with no representations or warranties, whether express, statutory or implied. In no event will Belden be liable for any damages (including consequential, indirect, incidental, special, punitive, or exemplary damages) whatsoever, even if Belden has been advised of the possibility of such damages, whether in an action under contract, negligence or any other theory, arising out of or in connection with the use, or inability to use, the information or specifications described herein.All sales of Belden products are subject to Belden's standard terms and conditions of sale.Belden believes this product to be in compliance with all applicable environmental programs as listed in the data sheet. The information provided is correct to the best of Belden's knowledge, information and belief at the date of its publication. This information is designed only as a general guide for the safe handling, storage, and any other operation of the product itself or the one that it becomes a part of. The Product Disclosure is not to be considered a warranty or quality specification. Regulatory information is for guidance purposes only. Product users are responsible for determining the applicability of legislation and regulations based on their individual usage of the product.。
TC240 安装手册和操作说明说明书
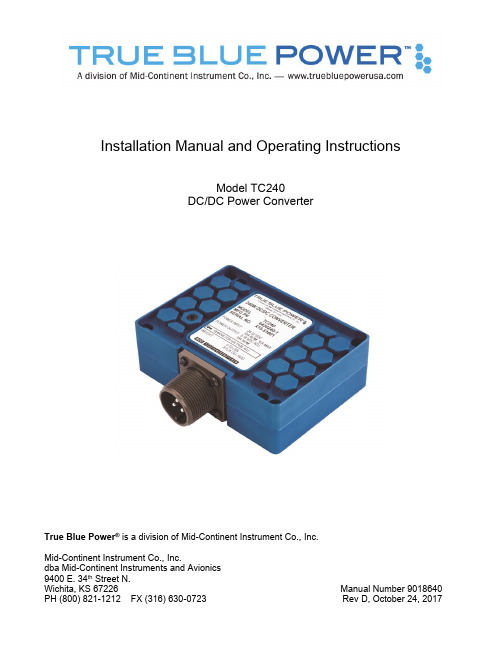
Installation Manual and Operating InstructionsModel TC240DC/DC Power ConverterTrue Blue Power®is a division of Mid-Continent Instrument Co., Inc.Mid-Continent Instrument Co., Inc.dba Mid-Continent Instruments and Avionics9400 E. 34th Street N.FOREWORDThis manual provides information intended for use by persons who, in accordance with current regulatory requirements, are qualified to install this equipment. If further information is required, please contact:True Blue Powerc/o Mid-Continent Instrument Co., Inc.Attn: Customer Service Dept.9400 E. 34th Street N.Wichita, KS 67226 USAPH (316) 630-0101FX (316) 630-0723We welcome your comments concerning this manual. Although every effort has been made to keep it free of errors, some may occur. When reporting a specific problem, please describe it briefly and include the manual part number, the paragraph/figure/table reference and the page number. Send your comments to:True Blue Powerc/o Mid-Continent Instrument Co., Inc.Attn: Technical Publications9400 E. 34th Street N.Wichita, KS 67226 USAPH (316) 630-0101FX (316) 630-0723All products produced by Mid-Continent Instrument, Co., Inc., including those identified as Mid-Continent Instruments and Avionics or True Blue Power, are designed and manufactured in Wichita, KS, USA.Copyright 2016Mid-Continent Instrument Co., Inc.REVISION DETAILRevision Date Approved DetailA 05/23/16 SHO Initial releaseB 06/22/16 KJW Corrected typo, page 12, 4.2.3, ‘maximum.’5.2 Environmental Qualification Statement:∙ Section 4, changed from F2 to F1;∙ Section 4.5.1 Operating Low Temp changed from -55C to -40C∙ Section 4.5.3 Operating High Temp changed from+70C to +55C.C 12/02/2016 KJW Corrected description, Figure 3.3. Revised theEnvironmental Qualification Statement table forTemperature and Altitude, Section 4.D 10/24/17 KJW Changed Environmental Qualification Statement to add helicopter vibe levels.TABLE OF CONTENTSSECTION 1 GENERAL DESCRIPTIONINTRODUCTION 51.1SPECIFICATIONS 5 TECHNICAL1.2SECTION 2 INSTALLATION CONSIDERATIONS2.1 COOLING 6LOCATION 62.2EQUIPMENT2.3 ROUTING OF CABLES 62.4LIMITATIONS 6SECTION 3 INSTALLATION PROCEDUREINFORMATION 7 GENERAL3.13.2 UNPACKING AND INSPECTING EQUIPMENT 73.3 CABLE HARNESS 7Selection 7 GaugeWire3.3.1Information 7 AssignmentPin3.3.2HarnessVerification 83.3.3Adjustment 8 VoltageOutput3.3.43.4 MOUNTING 103.5CAUTION 10 INSTALLATION10COMPLETIONINSTALLATION3.6SECTION 4 OPERATION11PERFORMANCEELECTRICAL4.1FEATURES 12 PROTECTIVE4.2On/Off 124.2.1Remote12Limit4.2.2VoltageInput12Over-Temperature4.2.3Over-Current 12 Circuitand4.2.4ShortSECTION 5 CONFORMANCE5.1 INSTRUCTIONS FOR CONTINUED AIRWORTHINESS 1313STATEMENT5.2ENVIRONMENTALQUALIFICATIONSECTION 1 GENERAL DESCRIPTION1.1 INTRODUCTIONThe model TC240 DC/DC Power Converter is a lightweight power converter that translates a direct current (DC) input of 28 volts to an adjustable 5 to 18 volt direct current (DC) output.The input operating voltage (24–32VDC) makes the TC240 suitable for nearly any common general, business, or commercial aviation application and provides an adjustable DC output voltage of 5 to18VDC. The unit is rated for a nominal output of 240 watts to power avionics, instrumentation, personal charging, lighting, and many other applications. The TC240 DC/DC Converter is FAA certified to TSO-C71 and tested to rigorous environmental standards and levels of RTCA DO-160G. The small size and light weight in conjunction with its installation flexibility (inside or outside the pressure vessel) make it an ideal choice for aircraft power needs while reducing the challenges associated with other similar products.Highlighted features include short circuit protection, overload capability, low input voltage shut-down, temperature monitoring, reverse polarity protection, a self-resettable over-temperature disable and an optional remote enable (on/off) feature.The TC240 DC/DC converter has a robust Military-rated circular connector and a rugged aluminum case which dissipates heat and provides excellent mechanical strength. It is engineered to require no external cooling and contains no internal fans or cooling methods, which saves energy, reduces weight and allows more flexible installation locations. At only 0.70 pounds, it is lighter and smaller than any other certified solution in the aviation market today.1.2 TECHNICALSPECIFICATIONSElectrical Attributes:Input Voltage: Rated 28VDC nominal, Operating 24 – 32VDC.Input Current (full load): 10 amps max at nominal input voltageOutput Voltage 5 – 18VDC adjustableOutput Power: 240 watts nominalEfficiency: 95%nominalTable 1.1Physical Attributes:Weight: 0.70 lbs (0.32 kg)Dimensions:(not including connector mate) 2.75 inches long x 3.75 inches wide x 1.29 inches high (69.9 mm long x 95.3 mm wide x 32.8 mm high)Mating Connector Kit: 6430240-1 MCIA P/N 9018654 6430240-2 MCIA P/N 9018655Mounting: Base mount – orientation not criticalTable 1.2Qualifications:Certification: FAATSO-C71Environmental Qualification: RTCA DO-160G Environmental Category; See Section 5.2 Altitude: -15,000 feet to +55,000 feetTemperature: -55°C to +70°C (-67°F to +158°F)Table 1.3SECTION 2 PRE-INSTALLATION CONSIDERATIONS2.1 COOLINGThe TC240 product does not require external cooling or contain internal active cooling. Cooling of the unit occurs exclusively through passive conduction through the base or radiated cooling across the metal case. Additional cooling can be realized through convection (exposure to free moving air) or conduction (mounting to a thermally conductive metal surface). These methods are not required to achieve rated performance but can help prevent potential overheating and extend life when the unit is operated at full power or during overload conditions. Specifically, mounting the unit to a metal surface is preferred, but not required.2.2 EQUIPMENTLOCATIONThe TC240 is designed for mounting flexibility, allowing for installation inside or outside the pressure vessel with no requirement for temperature control. In addition to altitude and temperature resistance, the unit is also designed to withstand high levels of condensing humidity. However, installation locations where the unit could be subject to standing or direct water exposure should be avoided. The unit can be mounted in any orientation. Clearance should be provided for the mating connector and may require as much as five inches past the unit connector to allow for back shell access to the connector.OFCABLES2.3 ROUTINGThe wires and cable bundle associated with the unit are heavy gauge wire and carry significant power. Be aware of routing cables near other electronics or with other wire bundles that may be susceptible to high energy flow.Avoid sharp bends in cabling and routing near aircraft control cables. Also avoid proximity and contact with aircraft structures, avionics equipment, or other obstructions that could chafe wires during flight and cause undesirable effects.2.4 LIMITATIONSThe conditions and tests for TSO approval of this article are minimum performance standards. Those installing this article, on or in a specific type or class of aircraft, must determine that the aircraft installation conditions are within the TSO standards. TSO articles must receive additional installation approval prior to being operated on each aircraft. The article may be installed only according to 14 CFR Part 43 or the applicable airworthiness requirements.The TC240 is designed to operate at full rated load (per Figure 4.1) throughout the specified environmental temperature range (per section 5.2). Note that when operating at full power, the unit case can be hot to the touch. Reference the following examples of selected conditions when operating at maximum rated load of 240 watts (stabilized after 20 minutes):∙At an ambient test temperature of +23°C when not mounted to a metal surface, the maximum case temperature can reach +62°C. (+42°C when mounted to a metal surface) ∙At an ambient test temperature of +70°C when not mounted to a metal surface, the maximum case temperature can reach +87°C. (+68°C when mounted to a metal surface)Caution and consideration should be taken with respect to aircraft installation and operation.SECTION 3 INSTALLATION PROCEDURESINFORMATION3.1 GENERALThis section contains interconnect diagrams, mounting dimensions and other information pertaining to the installation of the TC240 DC/DC Converter. After installation of cabling and before installation of the equipment, ensure that power is applied only to the pins specified in the interconnect diagram.The following two versions of the unit are available. See Section 4.2.1 for additional details of the remote enable (on/off) feature and installation details within Section 3.Part Number Remote On/Off6430240-1 No (output always enabled)6430240-2 Yes (enable signal required)3.2 UNPACKING AND INSPECTING EQUIPMENTWhen unpacking this equipment, make a visual inspection for evidence of any damage that may have occurred during shipment. The following parts should be included:a. DC/DC Converter MCIA P/N 6430240-( )b. Connector Kit1) 6430240-1 MCIA P/N 90186542) 6430240-2 MCIA P/N 9018655c. Installation Manual MCIA P/N 9018640Equipment not provided:a. Mounting Hardware Four 6-32 x 1” (min) pan head screws#6 lock washers (optional)b. Cable Harness Wire See Section 3.3 for specificationsHARNESS3.3 CABLEConstruct the cable harness with regards to the instructions below, and using Connector Pinout of Table 3.1 or 3.2 and referencing Typical Wiring Diagrams of Figures 3.3 or 3.4, as applicable.Refer to Section 2: Pre-Installation Considerations in regards to routing precautions.3.3.1 Wire Gauge SelectionUse of PTFE, ETFE, TFE, Teflon, or Tefzel insulated wire is recommended for aircraft use.Use the following wire gauges for each of the pins in the connector:Pins A and B – 16 AWG stranded or solidPins C – 14 AWG or 16 AWG stranded or solidPins D (for -2) – 24 AWG stranded or solid3.3.2 Pin Assignment InformationPositive DC input – (24-32 VDC). Connect pin B to aircraft positive 28 VDC bus.(20 Amp circuit breaker recommended)DC Output – Connect pin C as the positive output voltage (adjustable)DC Return – Connect pin A to input power return or aircraft ground.Enable – 6430240-1: Not available6430240-2: Pin D to be grounded to enable power output(via switch or other means. See section 4.2.1 and figure 3.4 for related details)Figure 3.1Table 3.1 Pinout View of 6430240-1 Unit Connector6430240-1 Connector PinoutFigure 3.2Table 3.2 Pinout View of 6430240-2 Unit Connector6430240-2 Connector Pinout3.3.3 Harness VerificationWith the TC 240 Static Converter disconnected, activate the aircraft power bus that suppliesthe unit and use a multi-meter to verify that aircraft power and ground with appropriatevoltage is on the pins within the mating harness.3.3.4 Output Voltage AdjustmentThe output voltage can be set to any value between 5 and 18VDC.NOTE: The default output voltage is initially set to approximately 13.8VDC at the factory.The output voltage can be adjusted while the TC240 DC/DC Power Converter is connected tothe mating harness and aircraft power, but disconnected from the output load. Use a multi-meter at the load end of the harness to measure output voltage.The adjustment trimmer can be accessed by removing the screw near the label as shown inFigure 3.5. After removing the screw, a flat screwdriver (2mm) will fit into the hole and thetrimmer. Turn the trimmer carefully either clockwise to increase voltage or counter-clockwiseto decrease voltage. Replace the screw after adjustment is complete. Connector PinoutA DC Power ReturnB DC Power InputC DC Power Output Connector Pinout A DC Power Return B DC Power Input C DC Power OutputD EnableFigure 3.3: Typical 6430240-1 Aircraft Wiring Installation – Constant OnFigure 3.4: Typical 6430240-2 Aircraft Wiring Installation – Remote On/Off3.4 MOUNTINGRefer to Section 2: Pre-Installation Considerations in regards to equipment location.The TC240 DC/DC Converter is designed for base mounting only. Four 6-32 mounting holes should be provided in the aircraft in accordance with Figure 3.5. Secure the unit with four 6-32 pan head screws, or equivalent. A lock washer under the head of each screw is recommended.4X Ø0.15 Mounting Holesfor #6-32 X 1.0" (min)MS3102A-16-10POutput voltage adjustmentMS3102A-16-9PFigure 3.5TC240 DC/DC Converter Outline Drawing3.5 INSTALLATION CAUTIONUnder no circumstances should the output of the Converter be connected to another power output source or damage will occur to the unit or the connected power source.3.6 INSTALLATION COMPLETIONPrior to operating the unit in the aircraft, it is recommended to verify the output and functionality of the unit. In order to prevent accidental damage to other systems, it is best not to attach the output to other equipment or power busses prior to verification. Verify the output of the unit at the terminating end of the cable with a multi-meter to ensure proper voltage and polarity. Once verified, installation can be completed and functionality of the remote on/off feature (if used) should be checked.SECTION 4 OPERATION4.1 ELECTRICAL PERFORMANCEThe TC240 is designed as a non-isolated, buck topology, solid-state switch-mode power supply. The unitconverts a direct current voltage (VDC) input to a regulated 5-18 VDC output. It is capable of providing upto 240 watts of power to a variety of aircraft accessories including lights and onboard systems or portableconsumer product power. Rated output current, and thus power, is a function of the user-selected outputvoltage. See Figure 4.1 for maximum current vs. voltage.Figure 4.1TC240 Output Current Performance1012141618202224262857911131517O u t p u t C u r r e n t (A )Output Voltage (V)TC240 Output Current PerformanceMaximumContinuousFEATURES4.2 PROTECTIVE4.2.1 Remote On/OffThe TC240 DC/DC Converter (6430240-2 only) incorporates a remote on/off feature thatallows the user to enable or disable the output of the unit. By providing a ground on theappropriate pin, the user can enable the output of the unit via a remote mounted switch. (SeeFigure 3.4)4.2.2 Input Voltage LimitIf the input voltage exceeds the over-voltage threshold (34VDC), the output will be disabled.4.2.3 Over-TemperatureThe TC240 DC/DC Converter incorporates an internal temperature sensing device thatcontinually provides monitoring and feedback to the control circuits. When the unit senses aninternal condition that exceeds maximum temperature ratings, the output is disabled. TheConverter will continue to remain shut-down until the temperature returns to within acceptablelimits. This over-temperature reset occurs automatically without external interventionrequired.4.2.4 Short Circuit And Over-CurrentThe TC240 DC/DC Converter is capable of surviving a short circuit or over-current eventwithout permanent damage or effect to long-term reliability. The unit can provide over itsrated power output up to 277 watts for over 120 minutes (until over-temperature shutdownoccurs).The Converter monitors the DC output on a pulse-by-pulse scenario to determine a short -circuit or over-current situation. If detected, the output is limited by limiting the current outputto less than 20A. If the short-circuit or over-current situation is removed, the unit will return tonormal operation.SECTION 5 CONFORMANCE 5.1 INSTRUCTIONS FOR CONTINUED AIRWORTHINESSNo periodic scheduled maintenance or calibration is necessary for continued airworthiness of theTC240 DC/DC Converter. If the unit fails to perform to specifications, the unit must be removed andserviced by Mid-Continent Instruments and Avionics or their authorized designee.5.2 ENVIRONMENTAL QUALIFICATION STATEMENTPART NUMBER : 6430240MODEL NUMBER : TC240 NOMENCLATURE : DC/DC ConverterTSO NUMBER : C71MANUFACTURERS SPECIFICATIONS: Test Specification (TS) 688-P, Test Data Sheet (TDS) 688-PQUALIFICATION STANDARD : RTCA DO-160G, dated December 8, 2010CONDITIONS SECTION DESCRIPTION OF TESTTemperature and Altitude Low Temperature High Temperature Altitude Decompression Overpressure 4 4.5.2 4.5.4 4.6.1 4.6.2 4.6.3 Category F1 & F2Operating Low Temp = -40COperating High Temp = +70CAltitude = +55,000 ft.+8,000 to +55,000 ft.-15,000 ft.Temperature Variation 5 Category S2Humidity 6 Category B Operational Shock and Crash Safety7 Category B Vibration 8 Category R; Curve C, C1 [(RCC1)] Category U, Curve G [UG]Explosion 9 Category X Waterproofness 10 Category XFluids 11 Category X Sand and Dust 12 Category XFungus 13 Category F Salt Spray 14 Category XMagnetic Effect 15 Category ZPower Input 16 Category B(XX)Voltage Spike 17 Category BAudio Frequency Conducted Susceptibility18 Category R Induced Signal Susceptibility 19 Category XRadio Frequency Susceptibility 20 Category XEmission of Radio Freq Energy 21 Category MLightning Induced Transient Susceptibility22 Category X Lightning Direct Effects 23 Category XIcing 24 Category X ESD 25 Category A Flammability 26 Category X。
SimpliPhi Power产品连接指南说明书
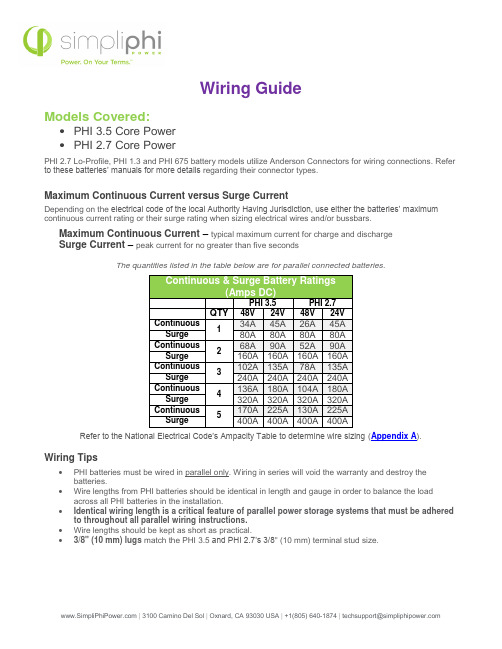
Wiring GuideModels Covered:•PHI 3.5 Core Power•PHI 2.7 Core PowerPHI 2.7 Lo-Profile, PHI 1.3 and PHI 675 battery models utilize Anderson Connectors for wiring connections. Refer to these batteries’ manuals for more details regarding their connector types.Maximum Continuous Current versus Surge CurrentDepending on the electrical code of the local Authority Having Jurisdiction, use either the batteries’ maximum continuous current rating or their surge rating when sizing electrical wires and/or bussbars.Maximum Continuous Current–typical maximum current for charge and dischargeSurge Current–peak current for no greater than five secondsThe quantities listed in the table below are for parallel connected batteries.Continuous & Surge Battery Ratings(Amps DC)PHI 3.5 PHI 2.7QTY48V 24V 48V 24VContinuous1 34A45A26A45ASurge 80A80A80A80AContinuous2 68A90A52A90ASurge 160A160A160A160AContinuous3 102A135A78A135ASurge 240A240A240A240AContinuous4 136A180A104A180ASurge 320A320A320A320AContinuous5 170A225A130A225ASurge 400A400A400A400ARefer to the National Electrical Code’s Ampacity Table to determine wire sizing(Appendix A).Wiring Tips•PHI batteries must be wired in parallel only. Wiring in series will void the warranty and destroy the batteries.•Wire lengths from PHI batteries should be identical in length and gauge in order to balance the load across all PHI batteries in the installation.•Identical wiring length is a critical feature of parallel power storage systems that must be adhered to throughout all parallel wiring instructions.•Wire lengths should be kept as short as practical.•3/8" (10 mm) lugs match the PHI 3.5 and PHI 2.7’s 3/8" (10 mm) terminal stud size.DC + bus DC – bus•Wiring from PHI batteries to DC busbars should be sized at 2 AWG or larger.•SimpliPhi recommends using Arctic Ultraflex Blue wire from Polarwire.•Energy supplied by the battery is reduced as electrical current moves through wire. For lengths of battery cable greater than ~10 ft/3 m, ensure that the voltage drop is no greater than 3%.•Wiring from the battery DC busbars to the equipment interface should be sized according to the interfacing equipment’s specifications and appropriate code requirements.Wiring Methods• 1 - 8 PHI batteries can be wired directly to DC busbars in an inverter’s power panelo See Appendix B for more details• 6 - 20 PHI batteries can be wired to a DC combiner or panelboardo See Appendix C for more details•20+ PHI batteries can be connected using common bussing directly on the batteries’ terminalsSourcing DC Combiner Boxes, Panelboards and Busbars•MidNite Solar produces the MNBCB 1000/50 Battery Combiner•Storm Power Components produces a variety of combiners and custom bussingFrom Magnum ’s Mini Magnum Panel Owner’s Manual :DC shuntDC – busDC+ bus Magnum’s Mini Magnum Panel (MMP) includes a battery positive busbar and a DC negative busbar, both rated to handle 120 Amps each. Each busbar includes seven total holes for screw type compression terminals (no ring lugs required): two holes are sized for #14 to #1/0 AWG wire and five are sized for #14 to #6 AWG wire.Note in the diagram above that the charge controller’s BAT NEG wire lands on the DC Negative Busbar, and a short wire connects the DC Negative Busbar to the top of the DC Shunt.If the DC Negat ive Busbar is utilized for battery paralleling, then the charge controller’s BAT NEG wire should instead land at the top of the DC Shunt (along with the inverter’s negative cable), and the short wire connecting the DC Negative Busbar to the DC Shunt should be moved so that the short wire lands at the bottom of the DC Shunt.From Schneider Electric’s Conext XW+ Installation Guide (975-0239-01-01_Rev M):DC – busDC+ busFrom Schneider Electric’s Conext XW+ MINI PDP Install Guide (975-0735-01-01_Rev-B):DC – busDC+ busFrom OutBack Power’s GS Load Center Installation Manual:The OutBack GS Load Center includes a single pre-installed 500Adc/50 mV shunt for landing negative battery cables. This shunt is located to the upper left of the main inverter disconnect. It is designed for several 3/8" (10 mm) ring lugs to be bolted to it. Up to two more shunts can be installed in the GS Load Center.The GS Load Center for the OutBack Radian 8048 and 8048A includes a DC positive wiring plate* for landing positive battery cables. This plate must be ordered separately from OutBack (Product Guide Catalog linked here). The plate can be installed directly beneath the main inverter disconnects. It has four 0.31" (8 mm) holes andthree 0.4" (10 mm) holes. It is intended for several ring lugs to be bolted to it.*The DC positive wiring plate is not included in the GS Load Center for the OutBack Radian 4048.The illustration below shows the placement of the shunt and the DC Positive Plate, as well as the hardware installation order on the shunt and the DC Positive Plate. Do not install hardware in a different order from the illustration. The battery cable lug(s) must be the first item(s) installed. The first cable lug must make solid contact with the surface.Hardware Connection to ShuntSize and Torque Requirements for Circuit Breakers and Bus BarsOutBack FLEXware 250, 500 and 1000 products can also be assembled to include DC busbars. These busbarsdo not come with the FLEXware; they must be ordered separately.Hardware Connection to DC + PlateAppendix CFor Technical Support:•Residential•Commercial HV•OEM-Interoperability。
ADP UHF 半导体方向性无线电天线(470-1075MHz)商品说明说明书

Passive directional antenna for use with Evolution Wireless Digital systems.The ADP UHF passive directional antenna is the perfect addition for enhancing the wireless performance of your Evolution Wireless Digital system. The ⅝" and ⅜" threads make it easy to mount on any mic stand. The ADP UHF can be connected to the EW-D EM receiver, the EW-D AB antenna booster or EW-D ASA antenna splitter.FEATURES• UHF transmission greatly enhances range, reliabilityand scalability • Built-in ⅝" and ⅜" threads allow for easy mic standmountingACCESSORIESEW-D AB (Q)Antenna Booster 470 - 550 MHz Art. no. 508873EW-D AB (R)Antenna Booster 520 - 608 MHz Art. no. 508874EW-D AB (S)Antenna Booster 606 - 694 MHz Art. no. 508875EW-D AB (U)Antenna Booster 823 - 865 MHz Art. no. 508876EW-D AB (V)Antenna Booster 902 - 960 MHz Art. no. 508877EW-D ASA (Q-R-S)Active Antenna Splitter 470 - 694 MHz Art. no. 508879EW-D ASA (T-U-V-W)Active Antenna Splitter 694 - 1075 MHz Art. no. 508880EW-D ASA CN/ANZ (Q-R-S)Active Antenna Splitter470 - 694 MHzArt. no. 508998ARTICLE INFORMATIONADP UHF (470 - 1075 MHz)Art. no. 508863SPECIFICATIONSFrequency range 470 – 1075 MHz Apex angle (-3 dB)approx. 100°Front-to-back ratio > 14 dB Gain typ. 5 dBi Impedance 50 ΩConnection BNC female, no DC path Threads for tripod mounting 3/8" and 5/8"Dimensions 319 x 310 mmWeightApprox. 1100 g (2.43 lbs)Operating temperature range-10 °C - +55 °C (14 °F - 131 °F)Storage temperature range-20 °C - +85 °C (-4 °F - 185 °F)Relative humiditymax. 95 % (non-condensing)POLAR PATTERN90°90°0°180°Sennheiser electronic GmbH & Co. KG · Am Labor 1 · 30900 Wedemark · Germany · DIMENSIONSPOSITIONING。
Fluke DSX-PLA004S CHA004S 10 Gigabit 永久连接 通道适配器用户指

PN 4329932 (English) May 2013, Rev. 2 6/20172013-2017 Fluke Corporation All product names are trademarks of their respective companies.DSX-PLA004S/CHA004S10 Gigabit Permanent Link/Channel AdaptersUsers GuideThe DSX-PLA004S/CHA004S are sets of two permanent link or two channel adapters for use with Fluke Networks DSX CableAnalyzer ™ modules. These adapters let you test and certify installed permanent links and channels to ANSI/TIA/EIA Cat 6A standards and verify that links will support 10 Gigabit Ethernet applications. The adapter’s minimal effect on test results ensures that your results exceed the accuracy and repeatability specifications given in the proposed TIA-568-B, ISO 11801, and IEEE 802.3an (10GBASE-T) standards.Symbols WWarning or Caution: Risk of damage or destruction to equipment or software. See explanations in the manuals.XWarning: Risk of fire, electric shock, or personal injury.~This product complies with the WEEE Directive marking requirements. Theaffixed label indicates that you must not discard this electrical/electronic product in domestic household waste. Product Category: With reference to the equipment types in the WEEE Directive Annex I, this product isclassed as category 9 "Monitoring and Control Instrumentation" product. Do not dispose of this product as unsorted municipal waste.To return unwanted products, contact the manufacturer’s web site shown on the product or your local sales office or distributor.40 year Environment Friendly Use Period (EFUP) under China Regulation - Administrative Measure on the Control of Pollution Caused by Electronic Information Products. This is the period of time before any of theidentified hazardous substances are likely to leak out, causing possible harm to health and the environment.W Safety InformationW Warning XTo prevent possible fire, electric shock, or personal injury, read the safety information in the documentation supplied with the CableAnalyzer modules and the Versiv™ units before you use the tester.W CautionTo prevent damage to the tester, adapters, and cables under test, to prevent data loss, and to make sure your test results are as accurate as possible:•Do not connect the adapters to telephone lines of any type, including ISDN lines.•For permanent link adapters, do not twist, pull on, pinch, crush, or make kinks in the cables. See Figure 1.Figure 1. How to Prevent Damage to the Permanent Link Adapter Cables 2How to Use the AdaptersFigures 2 and 3 show typical connections to a permanent link and a channel. Be sure to select the test standard that is applicable to the link under test. For more information on how to do tests, see the documentation supplied with your tester.NoteTo disconnect the permanent link adapter’s plug from a patch panel, pull onthe plug’s case as shown in Figure 1. It is not necessary to press on the latch todisconnect the plug.Figure 2. Permanent Link Connections3Figure 3. Channel ConnectionsMaintenance and ServiceClean the adapters with a soft cloth that is moist with water or water and a mild soap. Do not use abrasives, solvents, or alcohol.If an adapter does not operate correctly, look for damage to the connections in the adapter jack, plug, or socket. Make sure that the adapter is latched tightly to the tester. For permanent link adapters, look for damage to the adapters’ cable.For service on the adapters, speak to a Fluke Networks representative for information on service centers.For the most current test limits and features, keep your tester’s software up to date. The latest version of software is available on the Fluke Networks website.Tips and Latches on Permanent Link AdaptersReplace the RJ45 tips on permanent link adapters when test result margins start to shrink or if a tip shows damage. You can use the Autotest counter on the tester’s version information screen to monitor the number of insertions.The plug’s latch can also wear over time. The kit shown under "Replacement Parts" supplies replacement tips and latches.45Replacement PartsSpecificationsThe DSX-PLA004/CHA004 permanent link and channel adapters meet all measurement accuracy specifications for Level IV test equipment. For more information, visit the Fluke Networks website.Life of module contacts (typical): >5,000 cyclesDimensions (each adapter): 3.0 in x 2.1 in x 1.2 in (75 mm x 54 mm x 30 mm)Permanent link adapter has a 5ft (1.5 m) cable.Weight (each adapter):Channel adapter: 2.4 oz (68 g)Permanent link adapter: 11.7oz (332g)Contact Fluke NetworksFluke Networks operates in more than 50 countries worldwide. For more contact information, visit our website.Description Fluke NetworksModel NumberSet of 2 tips, 2 latches, 2 screws, and 2 conductive washersfor DSX-PLA004 Permanent Link AdaptersDTX-PLA002PRP **********************1-800-283-5853, +1-425-446-5500Fluke Networks6920 Seaway Boulevard, MS 143FEverett WA 98203 USALIMITED WARRANTY AND LIMITATION OF LIABILITYFluke Networks mainframe products will be free from defects in material and workmanship for one year from the date of purchase, unless stated otherwise herein. Parts, accessories, product repairs and services are warranted for 90 days, unless otherwise stated. Ni-Cad, Ni-MH and Li-Ion batteries, cables or other peripherals are all considered parts or accessories. This warranty does not cover damage from accident, neglect, misuse, alteration, contamination, or abnormal conditions of operation or handling. Resellers are not authorized to extend any other warranty on Fluke Networks’ behalf. To obtain service during the warranty period, contact your nearest Fluke Networks authorized service center to obtain return authorization information, then send your defective product to that Service Center with a description of the problem.For a list of authorized resellers, visit /wheretobuy.THIS WARRANTY IS YOUR ONLY REMEDY. NO OTHER WARRANTIES, SUCH AS FITNESS FOR A PARTICULAR PURPOSE, ARE EXPRESSED OR IMPLIED. FLUKE NETWORKS IS NOT LIABLE FOR ANY SPECIAL, INDIRECT, INCIDENTAL OR CONSEQUENTIAL DAMAGES OR LOSSES, ARISING FROM ANY CAUSE OR THEORY. Since some states or countries do not allow the exclusion or limitation of an implied warranty or of incidental or consequential damages, this limitation of liability may not apply to you.4/15Fluke NetworksPO Box 777Everett, WA 98206-0777USA6。
IT200 IntelliTone Pro 音调发生器和探测器用户手册说明书
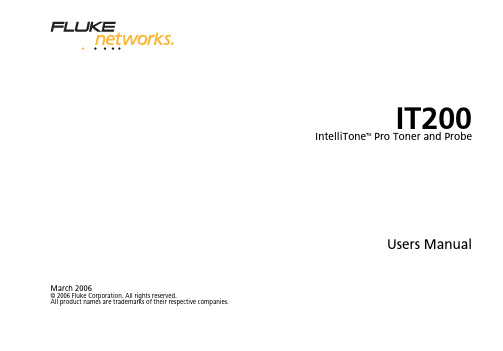
IT200IntelliTone Pro Toner and ProbeUsers ManualMarch 2006© 2006 Fluke Corporation. All rights reserved.All product names are trademarks of their respective companies.LIMITED WARRANTY AND LIMITATION OF LIABILITYEach Fluke Networks product is warranted to be free from defects in material and workmanship under normal use and service. The war-ranty period for the mainframe is one year and begins on the date of purchase. Parts, accessories, product repairs and services are war-ranted for 90 days, unless otherwise stated. Ni-Cad, Ni-MH and Li-Ion batteries, cables or other peripherals are all considered parts or acces-sories. The warranty extends only to the original buyer or end user customer of a Fluke Networks authorized reseller, and does not apply to any product which, in Fluke Networks’ opinion, has been misused, abused, altered, neglected, contaminated, or damaged by accident or abnormal conditions of operation or handling. Fluke Networks warrants that software will operate substantially in accordance with its func-tional specifications for 90 days and that it has been properly recorded on non-defective media. Fluke Networks does not warrant that software will be error free or operate without interruption.Fluke Networks authorized resellers shall extend this warranty on new and unused products to end-user customers only but have no author-ity to extend a greater or different warranty on behalf of Fluke Networks. Warranty support is available only if product is purchased through a Fluke Networks authorized sales outlet or Buyer has paid the applicable international price. Fluke Networks reserves the right to invoice Buyer for importation costs of repair/replacement parts when product purchased in one country is submitted for repair in another country.Fluke Networks warranty obligation is limited, at Fluke Networks option, to refund of the purchase price, free of charge repair, or replace-ment of a defective product which is returned to a Fluke Networks authorized service center within the warranty period.To obtain warranty service, contact your nearest Fluke Networks authorized service center to obtain return authorization information, then send the product to that service center, with a description of the difficulty, postage and insurance prepaid (FOB destination). Fluke Net-works assumes no risk for damage in transit. Following warranty repair, the product will be returned to Buyer, transportation prepaid (FOB destination). If Fluke Networks determines that failure was caused by neglect, misuse, contamination, alteration, accident or abnormal con-dition of operation or handling, or normal wear and tear of mechanical components, Fluke Networks will provide an estimate of repair costs and obtain authorization before commencing the work. Following repair, the product will be returned to the Buyer transportation prepaid and the Buyer will be billed for the repair and return transportation charges (FOB Shipping point).THIS WARRANTY IS BUYER’S SOLE AND EXCLUSIVE REMEDY AND IS IN LIEU OF ALL OTHER WARRANTIES, EXPRESS OR IMPLIED, INCLUDING BUT NOT LIMITED TO ANY IMPLIED WARRANTY OR MERCHANTABILITY OR FITNESS FOR A PARTICULAR PURPOSE. FLUKE NETWORKS SHALL NOT BE LIABLE FOR ANY SPECIAL, INDIRECT, INCIDENTAL OR CONSEQUENTIAL DAMAGES OR LOSSES, INCLUDING LOSS OF DATA, ARISING FROM ANY CAUSE OR THEORY.Since some countries or states do not allow limitation of the term of an implied warranty, or exclusion or limitation of incidental or conse-quential damages, the limitations and exclusions of this warranty may not apply to every buyer. If any provision of this Warranty is held invalid or unenforceable by a court or other decision-maker of competent jurisdiction, such holding will not affect the validity or enforce-ability of any other provision.4/04Fluke NetworksPO Box 777Everett, WA 98206-0777USATable of ContentsPage TitleOverview of Features (1)Registration (3)Contacting Fluke Networks (3)Unpacking (4)ITK200 IntelliTone Pro Kit (4)IT200 IntelliTone Pro Toner (4)IT200 IntelliTone Pro Probe (4)Safety Information (5)Battery Status (6)Auto Power Down (6)Locating and Isolating Terminated UTP/STP Cables with the IntelliTone (6)Isolating Individual Wire Pairs with the SmartTone Analog Function (9)SmartTone Positive Identification (9)Validating RJ11 and RJ45 Cable Maps (10)Validating the Cable’s Shield (12)Validating Telephone Service and Polarity (13)Validating Ethernet Service (14)iIT200Users ManualTesting for Continuity (15)Battery Life and Replacement (16)Accessories (17)Specifications (18)Environmental and Regulatory Specifications (18)IT200 Toner Electrical Specifications (19)IT200 Probe Electrical Specifications (19)Feature Compatibility (20)Certifications and Compliance (20)Dimensions (20)Weight (with battery) (20)iiIT200 IntelliTone Pro Toner IT200 IntelliTone Pro ProbeOverview of FeaturesThe IT200 IntelliTone Pro toner and probe let you locate, isolate, and validate twisted pair (UTP, Cat 5e, Cat 6), coax cables (RG6, RG59, and others for CATV/CCTV), bare wire (such as speaker wire and security network wire), and Cat 3 telephone cabling. The toner also lets you validate voice and data services.The toner and probe feature both digital and analog toning and detection. The digital IntelliTone tone is primarily used on data cables, and on active networks. In these environments, the digital signal eliminates cable misidentification due to signal bleed and radiated or ambient noise.The analog tone is primarily used on voice cables, and on bare wire. The SmartTone™ analog technology will change cadence when a pair is shorted at the far end. This makes exact pair identification easy and precise. The IntelliTone feature also lets you use the IT200 toner and probe to validate and troubleshoot wiring on RJ11 and RJ45 cables.The IT200 toner detects telephone and Ethernet service, indicates polarity and active line numbers on voice circuits, and indicates active pair number on Ethernet circuits.The IT200 toner and probe also provide standard functions such as visual and audible signal strength indication, digital toning/detection, SmartTone analog toning/detection, and continuity testing.1IT200Users ManualThe IntelliTone feature also lets you use the IT200 toner and probe to validate and troubleshoot wiring on RJ11 and RJ45 cables.The IT200 toner detects telephone and Ethernet service, indicates polarity and active line numbers on voice circuits, and indicates active pair number on Ethernet circuits. The IT200 toner and probe also provide standard functions such as visual and audible signal strength indication, digital toning/detection, SmartTone analog toning/detection, and continuity testing.2Registration3RegistrationRegistering your product with Fluke Networks gives you access to valuable information on product updates, troubleshooting tips, and other support services. Toregister, fill out the online registration form on the Fluke Networks website at /registration . If you do not have Internet access, print the registration form from the CD included with the product. Fill out the form, then mail or fax it to the appropriate address for your country.Contacting Fluke NetworksFor technical support, please contact us via *************************.************************* +1-425-446-4519• Australia: 61 (2) 8850-3333 or 61 (3) 9329-0244 • Beijing: 86 (10) 6512-3435 • Brazil: 11 3044 1277 • Canada: 1-800-363-5853• Europe: +44-(0)1923-281-300 • Hong Kong: 852 2721-3228 • Japan: 03-3434-0510 • Korea: 82 2 539-6311 • Singapore: 65 6799-5566 • Taiwan: (886) 2-227-83199 • USA: 1-800-283-5853Visit our website for a complete list of phone numbers.IT200Users Manual4UnpackingThe IT200 products come with the accessories listedbelow. If an accessory is damaged or missing, contact the place of purchase immediately.ITK200 IntelliTone Pro Kit• IT200 Toner with 9V battery • IT200 Probe with 9V battery • 2 RJ11 to RJ11 patch cords • 2 RJ45 to RJ45 patch cords• Test lead set, banana jacks to alligator clips • F connector adapter, female to female • Quick Reference Guide • Product Manuals CDIT200 IntelliTone Pro Toner• IT200 Toner with 9V battery • 1 RJ11 to RJ11 patch cord • 1 RJ45 to RJ45 patch cord• Test lead set, banana jacks to alligator clips • F connector adapter, female to female • Quick Reference Guide • Product Manuals CD IT200 IntelliTone Pro Probe• IT200 Probe with 9V battery • Quick Reference Guide • Product Manuals CDSafety Information5Safety InformationTable 1 describes the international electrical symbols used on the tester and in this manual.Table 1. International Electrical SymbolsWWarning: Risk of personal injury. See explanations in the manual.Caution: Risk of damage or destruction toequipment or software. See explanations in the manual.X Warning: Risk of electric shock.j This equipment not for connection to publiccommunications networks, such as activetelephone systems.~ Do not put circuit boards in the garbage. Dispose of circuit boards in accordance with localregulations.P ConformitéEuropéenne; N10140Meets C-Tick EMC standardWX Warning•Never use the toner or probe on circuits of more than 100V.•Never use the toner, probe, or test leads if they are damaged. Inspect the cases and test leads for damage before use.• Disconnect unused test leads and connectors from the toner when testing telephone circuits. • Never open the case except to change the battery; no user-serviceable parts are inside. • Turn off the toner or probe and disconnect all test leads before replacing the battery. • Use only a 9V battery, properly installed in the case, to power the toner and probe.•If this equipment is used in a manner not specified by the manufacturer, the protection provided by the equipment may be impaired.W Caution•Avoid touching the probe tip to patch panelconnections and using the tip to dig into cable bundles. Doing so regularly may damage the probe tip over time.•To avoid unreliable test results, replace the battery as soon as the low battery indication appears.IT200Users Manual6Battery StatusLEDs on the toner and probe light for 1 second at poweron to indicate the battery status:Toner battery status LED Probe battery status LEDGreen: Battery is good.Yellow: Battery is marginal. Red: Battery is low.See “Battery Life and Replacement” on page 16 for more information on the battery.Auto Power DownThe toner turns off automatically after approximately 2 ½ hours of inactivity. The probe turns off automatically after 1 hour of inactivity.To reactivate the toner or probe, turn the rotary switch to any position except OFF .Locating and Isolating Terminated UTP/STP Cables with the IntelliToneThe IntelliTone Pro toner provides two toning modes for locating and isolating cables; one digital tone M and one SmartTone 1kHz analog tone H .With the toner set to digital tone mode, the probe can be set to either locate M or isolate N .Both toning signals are available at all connectors on the toner.Locating and Isolating Terminated UTP/STP Cables with the IntelliToneThe digital tone M is optimized for 4 pair UTP data environments and the SmartTone analog tone H is optimized for two wire locating.To locate and isolate cables using the digital tone, do the following:1.Connect the IT200 toner to a jack or punch-downblock as shown in Figure 1.2.Turn the toner’s rotary switch to M.3.Turn the IT200 probe’s rotary switch to M(locate).e the probe to find the general location of thetone at a cable rack, patch panel, or behind a wall.The SYNC LED lights up green when the probe isreceiving the IntelliTone signal.In locating mode, the probe’s LEDs light up from 1 to8 as the signal strength increases. The higher thenumber, the stronger the signal.NoteIf you cannot locate the IntelliTone signal on2-conductor cables, the cable may be shorted.Use the cable map test (page 10) to test for shortson cables with RJ11 and RJ45 connectors. Use thecontinuity test (page 15) to check for shorts oncoax and non-terminated cables.5.Turn the probe’s rotary switch to N (isolate).e the probe to isolate the tone source in the cablebundle or at the patch panel. The SYNC LED lights up green when the probe is receiving the IntelliTonesignal.In isolating mode, the probes LEDs light up from 1 to8 as the signal strength increases.Users Manualash04f.epsFigure 1. Locating and Isolating CablesIsolating Individual Wire Pairs with the SmartTone Analog FunctionIsolating Individual Wire Pairs with the SmartTone Analog FunctionThe H position on the IT200 probe and toner lets you use the probe to trace using an analog 1kHz tone. SmartTone is intended for use on dry pairs of wires that are un-terminated at both ends of the run. It is not intended to be used on live wires with a DC power source (e.g., live telephone lines), nor will it work on wire pairs that are carrying AC signals. SmartTone works on many types of wire pairs including twisted pair, house wiring, and coax (the shield is one wire and the center conductor is the other wire of the pair). SmartTone Positive Identification1.The toner red lead must be connected to one ofthe wires of the pair, and the black lead must beconnected to the other wire of the pair.2.Put the toner and probe in the H position.3.At the far end of the cable run, place the probenear the wires you are tracing. Pick the pair thatgives the loudest signal in the toner speaker.4.Short and release the two wires of the pair. Ifyou hear a change in the pattern of the tone,then you have located the target pair of wires.If you don’t hear a change in the tone pattern,then pick a different pair and try again untilyou find the pair that causes the tone patternto change.Users ManualValidating RJ11 and RJ45 Cable Maps You can use the IT200 or IT100 toner and IT200 probe to validate the cable map on RJ11 and RJ45 connectors. The cable map function finds the most common wiring faults on twisted pair cabling: shorts, opens, and crossed pairs.1.Connect an IT200 or IT100 toner to a RJ11 or RJ45jack, as shown in Figure 1.2.Turn the toner’s rotary switch to M3.If necessary, use the IP200 probe to locate the correctconnector at the other end of the cabling, asdescribed in the previous section.4.Connect the IP200 probe to the RJ11 or RJ45 jack;then turn the probe’s rotary switch to CABLE MAP.5.The probe’s LEDs and beeper indicate the cable map,as follows:•The number of each LED corresponds to a pin on the connector. You can enable the SYNC LED tovalidate the shield. See “Validating the Cable’sShield” on page 12. •Each LED that corresponding to an active pin flashes briefly, then should light for about 1second. The brief flash shows which LED is nextin the sequence.•The probe also beeps in different tones to indicate good wiring, miswires, shorts, andopens.•Miswire: If one LED flashes briefly, then another LED lights for one second, the wire for the firstLED is miswired to the pin for the second LED. •Short: If two LEDs turn on for 1 second at the same time, those two pins are shorted together.If more than 2 wires are shorted together, theLEDs for the shorted pins indicate opens. •Open: If an LED flashes briefly, then no LEDs turn on, that pin is open.Validating RJ11 and RJ45 Cable Mapsash05f.eps Figure 2. Validating Cable MapsUsers ManualValidating the Cable’s ShieldTo use the probe’s SYNC LED for shield validation during cable map tests, do the following:1.Remove the battery door and disconnect the batteryfrom the probe, as described under “Battery Life and Replacement” on page 16.1.Turn the probe’s rotary switch to CABLE MAP.Note: The battery must be disconnected from theprobe for at least 30 seconds.2.Replace the battery and battery door.The SYNC LED will now indicate a good, open, or shorted shield as described in the previous section. To disable shield validation via the probe’s SYNC LED, do the following:1.Remove the battery door and disconnect the batteryfrom the probe.2.Turn the probe’s rotary switch any position exceptCABLE MA P.Note: The battery must be disconnected from theprobe for at least 30 seconds.3.Replace the battery and battery door.Validating Telephone Service and PolarityPolarityThe toner detects telephone service and circuit polarity onits banana, RJ11, and RJ45 jacks.NoteThis test requires power from the Central Office.1.Turn off the toner.2.Connect the toner to the circuit as shown in Figure3.Disconnect unused test leads and connectors fromthe toner.3.Turn the toner’s rotary switch to SERVICE.4.The LEDs indicate telephone service and polarity asshown in Figure 3.The toner checks for continuity between the red andblack test leads and across the middle pair of theRJ45/RJ11 jack (line 1).ash01f.epsFigure 3. Validating Telephone Service and PolarityUsers ManualThe toner detects link pulses for 10BASE-T, 100BASE-TX,and 1000BASE-T Ethernet service on pins 1, 2 and 3, 6 ofits RJ45 jack.1.Turn off the toner.2.Connect the toner to the circuit as shown in Figure 4.3.Turn the toner’s rotary switch to SERVICE.4.The Ethernet LED indicates service on pins 1, 2 or 3, 6as shown in Figure 4.The toner checks for continuity between pins 4, 5.Continuity indicates the toner is connected to a networkdevice that is turned off.NoteIf the Ethernet LED alternates between red andgreen, the Ethernet service is Auto-MDIX.ash08f.epsFigure 4. Validating Ethernet ServiceTesting for ContinuityTesting for ContinuityYou can use the toner to test circuits and components for continuity.1.If you are testing a circuit, verify that it is notpowered. Use the toner’s continuity E function tocheck for continuity. Use a voltage meter to checkother types of circuits for power.2.Turn off the toner.3.Connect the toner to the circuit or component asshown in Figure 5.4.Turn the toner’s rotary switch to E.5.The A LED indicates an open or closed circuit asshown in Figure 5.ash09f.eps Figure 5. Continuity TestUsers ManualMaintenanceClean the case with a soft cloth dampened with water or a mild soap solution.W CautionTo avoid damaging the case, do not use solventsor abrasive cleansers.Battery Life and ReplacementThe toner and probe batteries last for about 20 hours of typical use.Figure 6 shows how to replace the battery in the toner and probe.NoteThe position of the probe’s rotary switch whenthe battery is replaced enables or disables shieldvalidation for cable map tests. See “Validatingthe Cable’s Shield” on page 12.WX WarningTo avoid possible electric shock or personalinjury:•Turn off the toner or probe and disconnect all test leads before replacing the battery. •Use only a 9V battery, properly installed in the case, to power the toner and probe.W CautionTo avoid unreliable test results, replace thebattery as soon as the low battery indicationappears. See “Battery Status” on page 6.Testing for Continuityash10f.eps Figure 6. Replacing the Battery AccessoriesTo order accessories (Table 2), contact Fluke Networks. For the latest list of IT200 accessories and other cable testers visit the Fluke Networks website at.Table 2. AccessoriesAccessoryFluke Networks Modelor Part Number Test lead set, banana jacks toalligator clipsMT-8203-22Test lead set, banana jacks toalligator clips with bed of nailsMT-8203-20Soft carrying case MT-8202-05Users ManualSpecificationsSpecifications apply at 23 o C (73 o F), unless otherwisenoted.Environmental and Regulatory SpecificationsOperating temperature 32 °F to 104 °F (0 o C to 40 o C) Storage temperature -4 °F to +140 °F (-20 o C to +60 o C)Operating relative humidity (% RH without condensation) 95 % (50 °F to 95 °F; 10 o C to 35 o C) 75 % (95 °F to 104 °F; 35 o C to 40 o C) uncontrolled < 50 °F (< 10 o C)Vibration Random, 2 g, 5 Hz-500 HzShock 1 m drop testSafety EN 61010-1 1st Edition + Amendments 1, 2 Altitude 3000 mEMC EN 61326-1SpecificationsIT200 Toner Electrical SpecificationsTalk battery voltage 6 V into 600 ΩOutput power 5 V p-pVoltage protection 100 VTone frequencies 1 digital tone 500 kHz1 analog tone 1 kHzBattery type and life 9V alkaline (NEDA 1604A or IEC 6LR61); 20 hours typicalAuto power down Turns off automatically after 4 hours of inactivityIT200 Probe Electrical SpecificationsTone detection Detects IntelliTone signal from IT100 or IT200 toner and 1 kHz signal from other toners. Battery type and life 9V alkaline (NEDA 1604A or IEC 6LR61); 20 hours typicalAuto power down Turns off automatically after 1 hour of inactivityUsers ManualFeature CompatibilityProduct CompatibilityIntelliTone Toner/Probe Feature IntelliTone Toner and Probe Works with Legacy Toner or Probe IntelliTone locate modeIntelliTone isolate modeCable map validation {Shield validation {Analog tone 1 kHzVisual / audible proximity indicators{Requires IntelliTone IP200 probe.Certifications and ComplianceP Conforms to relevant European Union directives.;N10140Meets C-Tick EMC standard. DimensionsToner: 5.54 in x 2.94 in x 1.25 in(14.1 cm x 7.5 cm x 3.2 cm) Probe: 8.73 in x 1.88 in x 1.26 in (22.2 cm x 4.8 cm x 3.2 cm) Weight (with battery) Toner: 6.0 oz (170 g)Probe: 4.7 oz (133 g)。
EKZH高寿命系列规格书NIPPON黑金刚

330 500 900 1,210 1,240 1,410 1,650 1,960 2,250 2,480 2,900 3,450 3,570 3,250 3,630 330 500 900 1,210 1,240 1,410 1,650 1,960 2,250 2,480 2,900 3,450 3,250 3,570 3,630 330 500 900 1,210 1,240 1,410 1,650 1,960
小型铝电解电容器
KZH 系列
低 Z 长寿命 RoHS2 适应品
● 因低电阻电解液的使用,实现了超低 ESR、超低阻抗。
● 额定电压范围 :6.3 ~ 35V、静电容量范围 :47 ~ 8,200μF。 ● 保证 105℃ 5,000 ~ 6,000 小时 ( 叠加纹波电流 )。 ● 请注意不属于基板清洗类型。
68 5×11 0.24 150 6.3×11 0.11 330 8×11.5 0.062 390 8×15 0.048 470 10×12.5 0.045 560 8×20 0.033 680 10×16 0.032 25 820 10×20 0.020 1,000 10×25 0.018 1,500 12.5×20 0.017 1,800 12.5×25 0.015 2,200 12.5×30 0.013 2,200 16×20 0.015 2,700 12.5×35 0.012 3,300 16×25 0.013
□□内为端子加工·编带代码。
阻抗
额定 纹波
WV Cap
尺寸 (Ωmax/100kHz) 电流
(Vdc) (μF) φD×(L mm)
(mArms/
105℃、 20℃ -10℃ 100kHz)
Frsky Taranis X9E 说明书
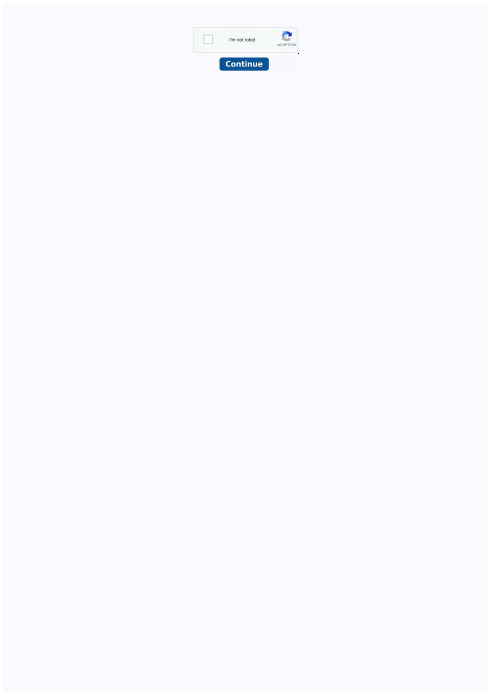
Tarani
Frsky taranis x9 lite firmware update. Frsky taranis x9d+.
FrSky Electronic Co., FrSky 2.4GHz ACCST Taranis X9E Manual FrSky Electronic Co., Cautions on handling antennaDo not touch the antenna during operation. Doing so could interfere with transmission, causing a crash.Do not carry the transmitter by the antenna. The antenna wire could break and prevent transmission.Do not pull the antenna forcefully. The antenna wire could break and prevent transmission.SpecificationsModel Name: Taranis X9ENumber of Channels: 16 Channels (extensible to 32 channels)Operating Voltage Range: 6~15V (2S, 3S Lipos are acceptable)Operating Current: 260mA maximum (both RF module and backlit are on)Operating Temperature: -10~60℃Backlight LCD Screen: 212*64Model Memories: 60 (ex
丰野耐指纹剂介绍

×~ △ × ~ △ ○
△~○
耐热性
导电性 后涂装性
● 备注:
2007/12/10
○ ~ ◎
◎ ◎~○
△~○
△~ × ○ ~ ◎
无机皮膜只在低皮膜量条件下就能确保性能。
×—差,△—不可, ○ —良,◎ —优
Eco-Conscious Products for Sustainable Growth
耐腐蚀性
耐碱性
涂装密着性 导电性
其它特性(耐黑、耐水性、耐热、耐溶剂等)
最佳化皮膜量范围
=0.40~0.80g/m2
0.30
0.40
0.50
0.60 0.70 皮膜量((g/m2)
0.80
0.90
1.00
2007/12/10
Eco-Conscious Products for Sustainable Growth
100% 无明显痕迹 无明显痕迹 无明显变化 △E=0.5 无色透明
METER)
*导电性测定用仪器 (ADVANTEST
2007/12/10
Eco-Conscious Products for Sustainable Growth
FY-WS-001
A.1.
无铬无机耐指纹处理剂
FYNC-NZW-007
2007/12/10
Eco-Conscious Products for Sustainable Growth
FY-WS-001
A.1.
无铬无机耐指纹处理剂
FYNC-NZW-007
无机皮膜特征
性能項目
皮膜量范围 耐溶剂性 耐碱 耐黑变性
无机皮膜
0.3~0.8 g/m2 ○~◎ ○~◎ ○~◎
VERTEX70_Bruker

Bruker OpticsThe VERTEX 70 series FT-IR spectrometers offer unmatched performance and versatil-ity for demanding analytical and research applications.RockSolid* interferometer2-channel 24-bit dynamic range ADC Remotely selectable 5 exit and 2 input beam portsEasy beamsplitter change without interferometer alignmentNear IR, visible and far IR/THz spectral range extensionsVacuum optics for VERTEX 70v Automated internal dual sourcesand dual detectors optionAutomatic optical components recognition VERTEX 70: Unmatched FT-IR Performance and Versatility The VERTEX 70 is a fully digital FT-IR spectrometer series for demanding R&D applications. Its innovative design results in the highest flexibility and highest performance. The data acquisition is based on two channel delta-sigma ADCs with 24-bit dynamic range, which are integrated into the detector preamplifier electronics. This advanced DigiTect* technology prevents external signal disturbance and guarantees the highest signal-to-noise ratio. Wide Spectral RangeThe VERTEX 70 series can be optionally equipped with optical compo-nents to cover the spectral range from 15cm-1 (10cm-1 for VERTEX 70v) in the far IR/THz, through the mid and near IR up to the visible/UV spectral range at 28,000cm-1. With its pre-aligned optical components and permanently aligned RockSolid* interferometer, range change is easy and maintenance free.BRAIN: Bruker Artificial Intelligence NetworkA network of intelligent functions such as recognition of sampling accessories and optical components, automatic set up and check of measurement parameters makes FT-IR spectroscopy easy, fast and reliable. In addition, the permanent online check of spectrometer com-ponents keeps fault diagnostics and maintenance simple. A full suite of software tools ensures this functionality.VERTEX 70 & 70v FT-IR SpectrometerBruker Optics Inc.Billerica, MA · USAPhone +1 (978) 439-9899Fax +1 (978) 663-9177info@Bruker Optik GmbH Ettlingen · GermanyPhone +49 (7243) 504-600Fax +49 (7243) 504-698info@brukeroptics.deBruker Optik Asia Pacific Ltd.Hong KongPhone +852 2796-6100Fax +852 2796-6109asiapacific@Bruker Optics is continually improving its products and reserves the right to change specifications without notice. © 2008 Bruker Optics BOPT-080122-1Automatic Component RecognitionThe sources, detectors and beam splitters on the VERTEX 70 - 70v are electronically coded to be recognized by the instrument and ap-propriate experimental parameters are auto-matically loaded. In addition, if two conflicting components are installed at the same time, the VERTEX 70 series will recognize this and inform about the mismatch.Vacuum OpticsWith the evacuable optics bench of the VERTEX 70v vacuum FT-IR spectrometer, PEAK sensitivity in the mid-, near and far IR/THz regions are obtained without the fear of masking very weak spectral features caused by water vapor or CO 2 absorptions. Outstand-ing results, e.g. in the area of nano-science research down to sub-monolayers, can be ob-tained with the new VERTEX 70v vacuum FT-IR spectrometer. The oil-free dry vacuum pump which is included in the instrument delivery pro-vides a vacuum level of less than 0.2hPa (mbar) within minutes.Plug & Play: Easy Set UpAll over the world, no matter where you are, plug in the power cord and the Ethernet connection, and the VERTEX 70 is ready for operation. The Ethernet connection to the VERTEX 70 also offers the possibility to control the spectrometer via your network or the World Wide Web.Spectral Resolutionthan 0.4cm-1 Versatilitythe HYPERION User-changeable components in the different compartments are easily accessible.RockSolid* interferometer used in the VERTEX 70 - 70v FT-IR spectrometer.* covered by one or more of the following patents:US 5,309,217; US 7034944; DE 4212143; DE 10159721Bruker Opticsis ISO 9001 certified.Laser class 2。
- 1、下载文档前请自行甄别文档内容的完整性,平台不提供额外的编辑、内容补充、找答案等附加服务。
- 2、"仅部分预览"的文档,不可在线预览部分如存在完整性等问题,可反馈申请退款(可完整预览的文档不适用该条件!)。
- 3、如文档侵犯您的权益,请联系客服反馈,我们会尽快为您处理(人工客服工作时间:9:00-18:30)。
Product Name:
Nitrendipine CAS No.:
39562-70-4C t N HY B0424Product Data Sheet
Cat. No.:
HY-B0424MWt:
360.36Formula:
C18H20N2O6Purity :>98%
DMSO 2/L W 1/
L
Solubility:Mechanisms:
Biological Activity:
Pathways:Membrane Tranporter/Ion Channel; Target:Calcium Channel DMSO 72 mg/mL; Water <1 mg/mL
Nitrendipine is a calcium channel blocker with marked vasodilator action.
Target: Calcium Channel Nitrendipine is a dihydropyridine calcium channel blocker. It is used in the treatment of primary hypertension to decrease blood pressure. Nitrendipine blocked Ca2+ currents very potently, with half-block by subnanomolar concentrations. The concentration dependence of block had the form expected for 1:1 binding, with an apparent dissociation constant (Kd) of 0.36 nM. In contrast, when cells were held at hyperpolarized potentials, nitrendipine blocked Ca2+ currents much less potently (Kd approximately equal to 700 nM) [1, 2]. Nitrendipine, a potent analogue of nifedipine, binds in a References:
[1]. Bean, B.P., Nitrendipine block of cardiac calcium channels: high-affinity binding to the
inactivated state. Proc Natl Acad Sci U S A, 1984. 81(20): p. 6388-92.[2]. Peterson, B.Z., T.N. Tanada, and W.A. Catterall, Molecular determinants of high affinity
dihydropyridine binding in L-type calcium channels J Biol Chem 1996271(10):p 5293-6reversible and saturable manner to partially purified guinea-pig heart membranes [3].
[3H]nitrendipine binding in smooth muscle is to a site which mediates the pharmacologic response
[4]. dihydropyridine binding in L type calcium channels. J Biol Chem, 1996. 271(10): p. 52936.[3]. Bellemann, P., et al., [3H]-Nitrendipine, a potent calcium antagonist, binds with high affinity to
cardiac membranes. Arzneimittelforschung, 1981. 31(12): p. 2064-7.[4]. Bolger, G.T., et al., Characterization of binding of the Ca++ channel antagonist, [3H]nitrendipine,
to guinea-pig ileal smooth muscle. J Pharmacol Exp Ther, 1983. 225(2): p. 291-309.Caution: Not fully tested. For research purposes only
Medchemexpress LLC
18 W i l k i n s o n W a y , P r i n c e t o n , N J 08540,U S A
E m a i l : i n f o @m e d c h e m e x p r e s s .c o m W e b : w w w .m e d c h e m e
x p r e s s .c o m。