处理含锌铅钢铁厂粉尘的Inmetco工艺
回转窑处理钢铁厂含锌粉尘的工艺设计与实践
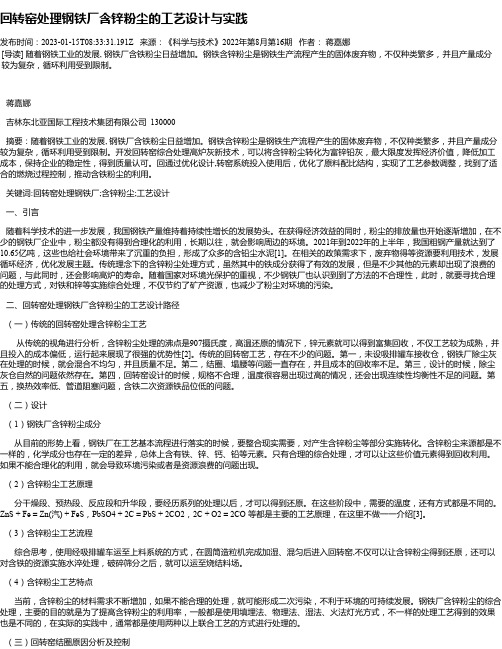
回转窑处理钢铁厂含锌粉尘的工艺设计与实践发布时间:2023-01-15T08:33:31.191Z 来源:《科学与技术》2022年第8月第16期作者:蒋嘉娜[导读] 随着钢铁工业的发展, 钢铁厂含铁粉尘日益增加。
钢铁含锌粉尘是钢铁生产流程产生的固体废弃物,不仅种类繁多,并且产量成分较为复杂,循环利用受到限制。
蒋嘉娜吉林东北亚国际工程技术集团有限公司 130000摘要:随着钢铁工业的发展, 钢铁厂含铁粉尘日益增加。
钢铁含锌粉尘是钢铁生产流程产生的固体废弃物,不仅种类繁多,并且产量成分较为复杂,循环利用受到限制。
开发回转窑综合处理高炉灰新技术,可以将含锌粉尘转化为富锌铅灰,最大限度发挥经济价值,降低加工成本,保持企业的稳定性,得到质量认可。
回通过优化设计,转窑系统投入使用后,优化了原料配比结构,实现了工艺参数调整,找到了适合的燃烧过程控制,推动含铁粉尘的利用。
关键词:回转窑处理钢铁厂;含锌粉尘;工艺设计一、引言随着科学技术的进一步发展,我国钢铁产量维持着持续性增长的发展势头。
在获得经济效益的同时,粉尘的排放量也开始逐渐增加,在不少的钢铁厂企业中,粉尘都没有得到合理化的利用,长期以往,就会影响周边的环境。
2021年到2022年的上半年,我国粗钢产量就达到了10.65亿吨,这些也给社会环境带来了沉重的负担,形成了众多的含铅尘水泥[1]。
在相关的政策需求下,废弃物得等资源要利用技术,发展循环经济,优化发展主题。
传统理念下的含锌粉尘处理方式,虽然其中的铁成分获得了有效的发展,但是不少其他的元素却出现了浪费的问题,与此同时,还会影响高炉的寿命。
随着国家对环境光保护的重视,不少钢铁厂也认识到到了方法的不合理性,此时,就要寻找合理的处理方式,对铁和锌等实施综合处理,不仅节约了矿产资源,也减少了粉尘对环境的污染。
二、回转窑处理钢铁厂含锌粉尘的工艺设计路径(一)传统的回转窑处理含锌粉尘工艺从传统的视角进行分析,含锌粉尘处理的沸点是907摄氏度,高温还原的情况下,锌元素就可以得到富集回收,不仅工艺较为成熟,并且投入的成本偏低,运行起来展现了很强的优势性[2]。
中冶京诚-回转窑处理钢铁企业含锌粉尘技术介绍

投资
太原钢铁公司 日照钢铁1X20;莱芜钢铁 德国:杜伊斯堡 2座85m3 1X30;马鞍山 1X20;沙 2用1备。 钢 1X30 处理20万吨/年:投 处理20万吨/年:投资2.3亿, 处理30万吨/年:投资约2 资1.2亿。 制块大于50%。 亿
较少
三、回转窑工艺介绍
该工艺主要目的是对高炉除尘灰的脱锌处理,实现高炉炉尘 的回收利用。利用回转窑对粉尘进行焙烧和还原处理,通过烟 气处理回收烟气中的锌等元素,实现高炉灰的再资源化;通过 对炉渣处理,可回收铁元素。
四、结语
钢铁联合企业产生的尘泥之中含有丰富的铁、碳、锌 及碱金属元素,如实现综合回收利用,不仅对钢厂炼铁 系统的生产操作有积极益处,同时在节约资源、保护环 境方面对社会和企业都有重要意义,因此,建设固废处 理设施实现钢铁企业“固废零排放”,越来越受到重视。 而选择何种工艺技术,需要与固废种类、产品规划、投 资、企业效益以及社会效益综合考虑,而回转窑工艺处 理含锌粉尘工艺是中小钢铁企业处理含锌粉尘的理想选 择之一。
谢
谢
处理含锌粉尘工艺技术比较
项目
原料 原料处理
DK小高炉
钢铁厂粉尘 混匀-烧结-破碎 原料:烧结矿 燃料:焦炭+喷煤 冶炼时间:5h >90% 铁水 —— 铸造、炼钢
OXICUP竖炉
钢铁厂粉尘 混料-压块100~150mm
RHF转底炉
钢铁厂粉尘 烘干-混匀-造球8~20mm干燥
回转窑 (简化版)
钢铁厂粉尘 粉料入窑
回转窑处理钢铁企业含锌粉尘 技术介绍
炼铁与储运工程技术所 2015年1月11日
主要内容
1 2 3
粉尘处理背景
处理含锌粉尘工艺技术比较 回转窑工艺介绍 结语
钢铁厂含锌粉尘的处理工艺与技术

4. 对原料比较敏感,使工艺难以优化; 5. 处理过程中引入的硫、氯等易造成新的环境污染; 6. 与钢厂现有技术不配套;效率较低; 7. 与火法比,其能源消耗和设备投资要少一些。
高炉含锌粉尘处理工艺
1
2
3
物理法 处理工艺
带出比例 %
90 80 70 60 50 40 30 20 10
0
烧结矿 球团矿
块矿 达丰焦炭 禹王焦炭 旭阳焦炭
焦丁 喷吹煤粉
80 60 40 20
0
炉渣
重力灰
布袋灰
铁水 出铁厂灰
1.高炉系统中Zn元素:(收入项-支出项)/收入项为:9.81%;
2. 说明取样期间某钢厂高炉锌排出能力较差,富集较为明显。
二、技术发展的必然性
炼钢 空气
富氧
氧气
炼铁 空气
富氧
氧气
氧气高炉需解决的技术关键
关键问题 产生原因 带来的问题
上冷 下热
炉缸煤气量大 幅度减少
1、理论燃烧温 度提高; 2、煤气量大幅 度减少 。 3、 直接还原 度降低
炉料加热不足,严重阻 碍炉身还原,使间接还 原度大幅度下降。
理论燃烧温度过高, Si 及其它元素大量还原蒸 发,最终导致高炉燃料 比猛烈上升、炉况不顺
1、投资 低、运行 简单
2、原料 要求低
1、金属化
率低
住友12万
2、生产不 稳定
吨含铁尘 泥
料
其它热点问题
• 1 低碳冶金
炼铁、烧结、 各工序能耗 焦化工序占到钢铁
工序能耗的65%以
上;而且其能源构 成主要以煤炭为主;
钢铁厂粉尘回收利用工艺以及系统[发明专利]
![钢铁厂粉尘回收利用工艺以及系统[发明专利]](https://img.taocdn.com/s3/m/f252cd9b02768e9950e73842.png)
专利名称:钢铁厂粉尘回收利用工艺以及系统专利类型:发明专利
发明人:夏锋,周强,秦涔,谭玲玲,袁冬冬,张二雷申请号:CN201510865843.2
申请日:20151130
公开号:CN105441687A
公开日:
20160330
专利内容由知识产权出版社提供
摘要:本发明涉及粉尘回收,提供一种钢铁厂粉尘回收利用工艺,先将粉尘(或添加还原剂粉料)混匀制粒,与还原剂粉料混合后装入还原室内,采用燃烧室加热还原室,粉尘中的铁氧化物与锌氧化物分别生成海绵铁与锌蒸汽,收集海绵铁,锌蒸汽则在冷却后进行收集;还提供一种钢铁厂粉尘回收利用系统,包括燃烧室以及还原室,每一还原室均与燃烧室紧邻,且还原室与燃烧室之间采用炉墙分隔,还包括有冷凝装置,每一还原室均设置有排气口,且均设置有卸料口。
本发明的工艺中,采用隔焰加热的方式,不但可以在粉尘中回收金属铁与金属锌,且能够实现铁锌的高效分离,以得到高质量的海绵铁与液态锌,回收率非常高,且工作过程利于控制。
申请人:中冶南方工程技术有限公司
地址:430223 湖北省武汉市东湖新技术开发区大学园路33号
国籍:CN
代理机构:北京汇泽知识产权代理有限公司
更多信息请下载全文后查看。
适用于转底炉处置含铁、锌粉尘的消解工艺

现代冶金Modern Metallurgy第49卷第1期2021年2月Vol. 49 No. 1Feb. 2021适用于转底炉处置含铁、锌粉尘的消解工艺赵丹丹,吴传文(上海梅山工业民用工程设计研究院有限公司,江苏南京210039)摘要:转底炉处理含铁、锌尘泥技术为国内乃至国际上较前沿技术,具有非常高的经济和环保效益,为使生产线高效、稳定运行,须对含铁、锌粉尘进行针对性的预处理$对游离钙含量较高的粉尘进行消解处理的机理及工艺设施 进行介绍$关键词:转底炉;冶金粉尘;资源回收;润湿试验;消解工艺中图分类号:X7561概述钢铁企业生产过程中会产生大量有利用价值的各种含铁、锌的粉尘、污泥,主要是烧结除尘灰、高炉 除尘灰、电弧炉粉尘、转炉除尘灰等,同时含有部分锌、铅、钾、钠等有害元素%采用目前常规的利用方 式已经影响了设备使用寿命、工艺生产顺行,致使相当一部分粉尘只能采取弃置、填埋等处置。
循环、高 效的固废处理是当前国家重点鼓励发展的产业;转底炉直接还原技术,将含铁、锌尘泥进行资源循环处置,被广大的钢铁企业关注并实施。
由于钢铁企业 生产原料的不同、生产工艺的差异,含铁、锌尘泥的物理特性、化学成分具有差异性;针对不同的物料组合,选择适宜的预处理措施,是保证生产线正常运行 的先决条件%含铁、锌尘泥是钢铁工业种类最多、成分最杂的 废弃物,是钢铁企业在原料准备、烧结、球团、炼铁、表1 炼钢和轧钢等工艺过程中所排烟尘进行干法除尘、湿法除尘和废水处理后的固态废物%例如:高炉除 尘灰是高炉炼铁过程中矿槽、筛分、出铁场等除尘工艺收集到的粉尘;烧结除尘灰是烧结原料在转运、配 料、烧结过程中,除尘器收集下来的粉尘;转炉LT灰是转炉煤气干法净化回收的粉尘%这些除尘灰的 总铁含量(TFe )—般在20%-70%,还含有Zn,Ca ,Mg 及C,P,S 等元素%转底炉直接还原工艺是将含铁、锌尘泥配碳和粘结剂后混合造球,生球经烘干后置于转底炉内,当 转底炉转动时生球被加热,至1100 D 左右时ZnO 被还原,还原出的Zn 被蒸发并随烟气一起排出,经冷却系统时被氧化成ZnO 后沉积在除尘器收集后 销售,生产的直接还原铁(DRI )和余热回收的蒸汽可循环利用%通过含铁、锌粉尘化学成分的测定和润湿试验,为消解工艺路线的选择提供强有力的支撑。
钢铁厂含锌粉尘的危害与处理技术

钢铁厂含锌粉尘的危害与处理技术摘要:钢铁生产是国内非常重要的基础产业,其对于我国社会经济的发展有着非常重要的影响和意义,但是在钢铁工业生产过程中,不可避免地会产生一些含锌粉尘,这些粉尘对生态环境、烧结生产、高炉设备都会造成一定程度上的损害,因此需要工作人员对含锌粉尘的处理工作提高重视。
接下来笔者将围绕含锌粉尘这一主题从危害分析和处理技术两方面内容对其展开详细的阐述,希望这些意见和建议可以对相关钢铁生产企业有所裨益。
关键词:钢铁厂;含锌粉尘;危害与处理技术引言为了可以有效地降低钢铁厂内含锌粉尘的危害性,工作人员需要采取相应处理技术对其进行处理,常见的有湿法处理技术、威尔兹法处理技术、循环法处理技术、球团法处理技术、微波法处理技术、熔融法处理技术、氧化法处理技术等等,不同的处理技术各有利弊,工作人员可以根据钢铁厂内含锌粉尘的实际情况选择最合适的处理技术,以求达到最佳的处理效果,这也是笔者将要与大家进行重点探究的主要内容。
一、含锌粉尘危害分析钢铁厂在开展烧结、高炉、炼钢等工业生产作业时,不可避免地会产生大量的含锌粉尘,该类粉尘中所含有的锌元素通常是由含锌烧结矿、镀锌废钢等主要炼钢原材料经过高温煅烧而来,这些含锌粉尘的危害性较高,具体体现在以下几点。
(一)对生态环境的危害钢铁厂每年伴随着工业生产作业会产生大量的含锌粉尘,这些含锌粉尘的堆积会占据大量的土地。
由于含锌粉尘中含有大量的重金属元素以及其他具有强污染性和腐蚀性的物质,在其堆积过程中,会对土壤内部结构中的酸碱平衡性进行破坏,经过雨水的浸染深入地下土质层还有可能会对该地区的地下水资源造成污染[1]。
(二)对烧结生产的危害通常来说,含锌粉尘的粒径大部分在50μm以内,而正是由于含锌粉尘粒度过于细小,所以烧结生产作业中所产生的含锌粉尘会大幅度降低烧结层的通透性,从而进一步导致烧结作业的产量下降,影响钢铁厂的生产效率。
(三)对高炉设备的危害从技术的层面上来说,锌元素在高炉设备中的不断循环会加重高炉设备内锌元素的含量,长此以往会对高炉设备产生严重的损害,大幅度缩短其使用年限,具体如下:第一,含锌粉尘不仅含有大量的锌元素,还存在一定含量的碱金属,锌元素与碱金属在高温的环境中极易发生氧化反应,体积不断增加,对高炉设备内部的砖衬结构造成损坏,影响高炉设备的正常运行[2];第二,高炉设备内的液态锌有可能会与氧气发生反应形成氧化锌,其再与氧化硅、氧化铝等物质进行二次反应,最终会形成硅酸锌和锌尖晶石等难溶物质,而这些物质会随着高炉设备内的生产作业逐渐增大,最终形成“炉瘤”,影响工业生产的顺利进行。
钢铁厂含锌粉尘的处理工艺与技术

Coal
300kg
Oxygen 307Nm3
图 2.6 NKK氧气高炉流程
• 1986年NKK公司在3.9 m3试验高炉上进 行了两次试验,每次一个半月。试验 结果:
–煤比可以提高到320Kg; –焦比大大降低; –利用系数达到5.1t/m3•d; –铁水硅含量明显下降;
第一次试验证明了氧气高炉在技
原料配比—造球—入
炉冶炼—直接还原铁 1、以焦粉、无烟煤作 为造球内还原剂 2、天然气或焦炉煤气 作为转底炉的主要燃
料
1、金属 收得率高 2、还原 铁运输、
堆存方便
3、原料配比要求严格
1、不能处 理铁鳞、渣 铁 2、工厂固 定投资高, 占地面积大
新日铁15、 19、30万 吨
浦项20万 吨
马钢20万 吨
1、投资 低、运行 简单
2、原料 要求低
1、金属化
率低
住友12万
2、生产不 稳定
吨含铁尘 泥
料
其它热点问题
• 1 低碳冶金
炼铁、烧结、 各工序能耗 焦化工序占到钢铁
工序能耗的65%以
上;而且其能源构 成主要以煤炭为主;
炼铁 45.9%
因此低碳首先要研
究铁前工序的减碳
技术。
焦化 14.7%转炉 2.ຫໍສະໝຸດ %1锌在高炉中的行为
2
锌对高炉冶炼过程的影响
3
高炉中锌的分布
4
高炉含锌粉尘处理工艺概况
高炉含锌粉尘处理工艺
1
2
3
物理法 处理工艺
湿法 处理工艺
火法 处理工艺
含锌粉尘中的锌主要富集在磁性较弱,粒度较 小的粒子中,且含锌化合物颗粒与含铁颗粒在 密度和表面性质上有所差异。
钢铁厂含锌粉尘的处理方法

者低价出售,这样不仅污染环境,而且造成宝贵
资源的浪费。现在越来越多的钢厂已经认识到这
个问题,开始对含锌粉尘进行综合处理,提取金 属锌,既减少污染又节约资源。目前的主要处理
方法有以下:
过于耀眼,将星星直接踢入了黑暗,尽法。高锌和中
锌粉尘可采用湿法直接处理,而低锌粉尘应先富
法、宝钢 BSR 法。
过于耀眼,将星星直接踢入了黑暗,尽管如此,夕年依旧的恋着星
火法处理的优点:1)生产效率较高.设备 占地面积较小;2)多数工艺中的 Zn、Pb 等重金
属的去除彻底,可充分满足环保要求;伴生的铁
碳资源可以得到充分回收;3)在钢厂内部处理
粉尘,其还原剂、能源、动力的消耗较少。
3、湿法-火法联合工艺
目前比较成熟的联合工艺是先火法后湿法
过于耀眼,将星星直接踢入了黑暗,尽管如此,夕年依旧的恋着星
的 MRT(HST)工艺。该工艺先采用转底炉对含锌粉 尘等物料进行直接还原,使铁与锌、铅、镉等分
离,得到的直接还原铁产品可以返回电弧炉循环
利用。
含铅、镉、铜、银等金属的粗氧化锌产品则 送入含热氯化铵的浸出槽中进行浸出,然后对浸
出液进行固、液分离,过滤,得到的滤液进一步
处理,分离回收铅和镉,最后将溶液浓缩、沉淀、
过于耀眼,将星星直接踢入了黑暗,尽管如此,夕年依旧的恋着星
干燥,就可以得到高纯氧化锌。这种联合工艺得 到的产品回收率高,但流程较长,成本比较高。
1cs0f9c9b
集后才能用于湿法处理。
湿法包括酸洗和碱洗。主要流程为:浸出、
净化、沉积和电解。湿法工艺中的溶解是在扩散
过于耀眼,将星星直接踢入了黑暗,尽管如此,夕年依旧的恋着星
控制下进行的,所以要进行高强度搅拌。
转底炉处理含锌尘泥成套工艺装备技术
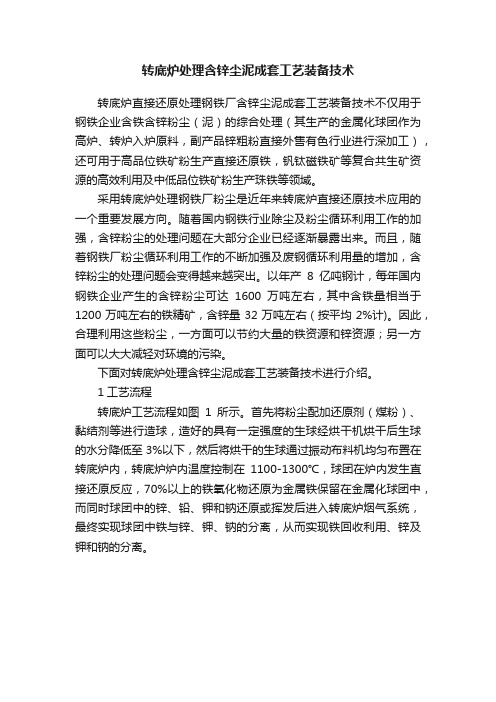
转底炉处理含锌尘泥成套工艺装备技术转底炉直接还原处理钢铁厂含锌尘泥成套工艺装备技术不仅用于钢铁企业含铁含锌粉尘(泥)的综合处理(其生产的金属化球团作为高炉、转炉入炉原料,副产品锌粗粉直接外售有色行业进行深加工),还可用于高品位铁矿粉生产直接还原铁,钒钛磁铁矿等复合共生矿资源的高效利用及中低品位铁矿粉生产珠铁等领域。
采用转底炉处理钢铁厂粉尘是近年来转底炉直接还原技术应用的一个重要发展方向。
随着国内钢铁行业除尘及粉尘循环利用工作的加强,含锌粉尘的处理问题在大部分企业已经逐渐暴露出来。
而且,随着钢铁厂粉尘循环利用工作的不断加强及废钢循环利用量的增加,含锌粉尘的处理问题会变得越来越突出。
以年产8亿吨钢计,每年国内钢铁企业产生的含锌粉尘可达1600万吨左右,其中含铁量相当于1200万吨左右的铁精矿,含锌量32万吨左右(按平均2%计)。
因此,合理利用这些粉尘,一方面可以节约大量的铁资源和锌资源;另一方面可以大大减轻对环境的污染。
下面对转底炉处理含锌尘泥成套工艺装备技术进行介绍。
1工艺流程转底炉工艺流程如图1所示。
首先将粉尘配加还原剂(煤粉)、黏结剂等进行造球,造好的具有一定强度的生球经烘干机烘干后生球的水分降低至3%以下,然后将烘干的生球通过振动布料机均匀布置在转底炉内,转底炉炉内温度控制在1100-1300℃,球团在炉内发生直接还原反应,70%以上的铁氧化物还原为金属铁保留在金属化球团中,而同时球团中的锌、铅、钾和钠还原或挥发后进入转底炉烟气系统,最终实现球团中铁与锌、钾、钠的分离,从而实现铁回收利用、锌及钾和钠的分离。
转底炉内发生的化学反应:Fe X O+C→Fe+COFe X O CO→Fe COZnO C=Zn(g) COZnO CO=Zn(g) CO22 关键技术1)转底炉本体热工调控技术◆基于数模计算的新型炉膛整体结构设计:五段式阶梯状炉膛结构和可移动式调压隔板。
减缓烟气聚集处的流速,将烟气流速与炉压合理匹配;◆转底炉温度、气氛调控结构设计:顶烧嘴、侧烧嘴喷嘴的结构。
工业烟气中铅_锌杂质的脱除技术浅析

2013年5月(下)[摘要]随着社会的发张和技术的进步,绿色与环保越来越受重视,工业生产中产生的废气处理方式方法引起人们的关注。
本文对去除工业烟气中铅、锌的处理方式进行了探讨,主要介绍了化学吸收法、物理吸收法、袋式除尘净化工艺、电除尘净化工艺,旨在促进工业烟气处理技术的进步,以及根据污染物排放情况、排放标准选择合适的处理方式。
[关键词]烟气净化技术;化学吸收法;物理吸收法;袋式除尘净化工艺;电除尘净化工艺工业烟气中铅、锌杂质的脱除技术浅析王广廷胡晓波金伟(林州市环境保护局,河南林州456550)铅、锌污染物主要由铅、锌冶炼及烧结过程中产生,烟气中铅、锌等杂质多以尘粒和烟的形式存在,对于粒径较大的尘粒(1~200μm ),一般采用袋式除尘器即可除去,对于粒径较小的铅、锌烟(0.01~1μm ),则可以采用静电除尘或者化学吸收法。
1铅的危害铅(Pb )属重金属类污染物,中毒后导致人体贫血,出现头痛、眩晕、乏力、困倦、便秘和肢体酸痛等;有的口中有金属味,动脉硬化、消化道溃疡和眼底出血等症状也与铅污染有关。
小孩铅中毒则出现发育迟缓、食欲不振、行走不便和便秘、失眠,特别是儿童处于生长发育阶段,对铅比成年人更敏感,进入体内的铅对神经系统有很强的亲和力,故对铅的吸收量比成年人高好几倍,受害尤为严重。
2含铅、锌烟气净化技术2.1化学吸收法目前采用的吸收剂主要是稀醋酸或NaOH 溶液。
1)稀醋酸溶液净化含铅、锌烟废气在斜孔板塔中,用0.25%~0.3%的醋酸溶液作为吸收剂,使铅、锌烟中的和Pb/Zn 和PbO/ZnO 变成醋酸铅/醋酸锌:Pb+2CH 3COOH Pb (CH 3COO )2+H 2PbO+2CH 3COOH Pb (CH 3COO )2+H 2O Zn +2CH 3COOH Zn (CH 3COO )2+H 2ZnO+2CH 3COOHZn (CH 3COO )2+H 2O烧结烟气进塔之前,先做除尘预处理,除去较大的颗粒后,再进入吸收塔。
- 1、下载文档前请自行甄别文档内容的完整性,平台不提供额外的编辑、内容补充、找答案等附加服务。
- 2、"仅部分预览"的文档,不可在线预览部分如存在完整性等问题,可反馈申请退款(可完整预览的文档不适用该条件!)。
- 3、如文档侵犯您的权益,请联系客服反馈,我们会尽快为您处理(人工客服工作时间:9:00-18:30)。
粉尘堆密度及粒度组成分别用量筒法及水筛法 测定 ,其结果如表 2 所示
1997 年 6 月 第 15 卷 第 3 期
环 境 工 程 ENV IRONM EN TAL EN GIN EERIN G
J une ,1997 Vol. 15 ,No . 3
综
合 利
处理含锌铅钢铁厂粉尘的 Inmetco 工艺
用
王东彦
(东北大学钢铁冶金系 ,110006)
(陈北京伟科庆技 大周学荣冶章金系 林,10宗008彩3)
产出的大量含锌铅粉尘进行综合利用 ,不仅对钢铁 工业的环境保护和资源回收有重要意义 ,对有色金 属工业的发展也是有益的补充 。
对已开发出的各种钢铁厂含锌铅粉尘处理工艺 的比较分析表明 :环形炉工艺是比较适合目前我国 含锌铅钢铁厂粉尘中锌含量较低特点 ,符合今后该 类粉尘处理技术发展方向的工艺之一 。然而 ,该工 艺目前存在的问题是 :仅能处理锌含量小于 2 % ,全 铁含量在 50 %以上的粉尘[2 ] 。这一点大大限制了 该工艺的应用范围 。据调查 ,目前含锌铅钢铁厂粉 尘主要是电炉粉尘和我国南部地区钢铁厂产出的高 炉粉尘 。其中 ,电炉粉尘的平均含锌量在 5 % ,含铁 量在 40 % ;高炉粉尘的平均含锌量则更高 ,达 15 % , 而含铁量则较低 ,只有 10 % - 20 % ,将其与几乎不 含锌的转炉粉尘按产出比例混合成低锌粉尘后的平 均锌含量也在 5 % ,平均全铁含量在 40 %左右 。因 此 ,将此工艺的应用范围扩展到处理 5 %锌含量和 40 %左右含铁量的钢铁厂粉尘 ,对于能否应用环形 炉工艺对含锌铅钢铁厂粉尘进行经济有效的处理具
表 3 所示 :
粉尘 种类 转 炉 尘
高 炉 尘
尘泥料 水份 %
18 20 23 25
表 3 两种粉尘的动态成球性测定结果
动态成球性测定的粒度组成 %
< 215 mm 2. 5 - 5
5- 8
8 - 12
形核率 ( %)
6318
3315
1198
0180
3613
0124
5125
8815
6100
9918
1997 年 6 月 第 15 卷第 3 期
环 境 工 程
51
图 2 煤粉粒度与生球强度的关系
图 5 水玻璃对生球强度的影响
图 3 煤粉加入量与生球强度的关系 2 工艺可行性实验结果 211 造球过程
造球过程是环形炉工艺的前部关键工序 ,主要 为高温还原过程作准备 ,生球强度和生球爆裂温度 越高 ,则生球入炉还原操作过程中的生球破损率越 低 ,湿球的烘干效率越高 。 造球实验研究得出了如下结果 :在转炉尘与高 炉尘混合造球比为产出量之比 ,即 115/ 1 时 ,除造球 水分 、造球时间外 ,如图 2~6 所示 :湿球落下强度随
Wang Dongyan ( Ferrous Department of Nort h2east University ,110006)
Chen Weiqing ,Zhou Rongzhang ,Lin Zongcai (Metallurgical Dept . of University of Science & Technology ,Beijing ,100083) ABSTRACT The inmetco process is an important met hod ,wit h which t he in2plant Zn2Pb2bearing dust can be treated. Its reasonability and feasibility were expounded by tests and analysis of process principle. KEY WORDS in2plant Zn2Pb2bearing dust , Inmetco process ,metallic pellet removed zinc ,second dust rich in zinc and lead.
尘泥块干燥 破 碎 混 料 造 球 烘 干 环形炉还原
富 锌 粉 尘
金属化 球 团
图 1 环形炉处理粉尘工艺流程图
112 工艺流程及合理性分析
粒较多 (均在 54 %以上) ,因此 ,不必细磨 ,即可将其
工艺图表明 :环形炉工艺的主要步骤是造球和 直接用于造球 。此外 ,转炉尘堆密度较大 ,有利于增
图 6 皂土和水玻璃对湿球爆裂温度的影响
图 4 皂土对生球强度的影响
图 7 造球水分与生球强度的关系 外配煤粒度减少和煤量的增加而显著增加 。亦可显 著提高干球抗压强度和湿球爆裂温度 。因此 ,除适 当调整煤粒度和煤量改善生球强度外 ,皂土和水玻 璃也可作为生球强度的调整手段 。 如图 7 所示 :在适宜造球的水分范围内 ,生球抗 压强度随水分增加呈凸形 ,若将对应湿球抗压强度 最高 的 水 分 看 作 是 最 佳 水 分 , 则 最 佳 水 分 值 为
直接还原 。而上述尘泥原料分析的结果则为采用此 加还原后的金属化球团的强度 。(3) 由表 3 可知 ,
工艺处理含锌铅钢铁厂粉尘提供了以下的合理性 。 转炉尘的形核率较好 ,成球性较差 ,高炉尘则形核率
(1) 高炉粉尘中较高的碳可在还原过程中充当还原 较低 ,成球性较好 。两种尘泥混合造球 ,结合了各自
足不了高炉冶炼对脱锌金属化球团的要求 ,但单纯 为了提高强度而不顾金属化率的高低 ,也将使工艺 成本大大增加 ,不可能使其推广 。为此 ,本工作将在 实验的基础上 ,确定使锌铅挥发率 、金属化率和球团 抗压强度均达到较高水平的工艺参数 ,以满足还原 工艺对锌铅铁还原率和抗压强度的双重要求 。 实验结果表明 :还原温度 、还原时间及球团碱度 均对锌铅挥发率 、金属化率和抗压强度有显著影响 , 如图 9 所示 :球团的锌铅挥发率和金属化率均随温 度升高而显著增加 ,1300 ℃时 ,锌铅挥发率和铁的金 属化率均达 99 %以上 。抗压强度在 1 250 ℃以前单 调升高 ,但在 1 300 ℃时出现软化 、破碎现象 。
52
环 境 工 程
1997 年 6 月 第 15 卷第 3 期
图 8 造球时间与生球强度的关系 21 % ,湿球落下强度随水分的变化也呈凸形 ,若将落
下强度最高值对应的水分作为落下强度的最佳水
分 ,则最佳水分为 22 %。
如图 8 所示 :生球抗压强度和落下强度均随造
球时间延长而有 较 显 著 的 提 高 , 但 在 超 过 20 min
后 ,其增加幅度变小 ,因此 ,延长造球时间可作为提
高生球强度的重要手段之一 ,但不宜超过 20 min 。
若以湿球抗压强度达到最大为标准选择造球条
件 ,则在不添加皂土和水玻璃的条件下 ,球团的最佳
造球条件为 : 造球时间 20 min ,造球水分 21 %。最
佳造球条件下的球团性能为 : 湿球抗压强度 1417
50
环 境 工 程
1997 年 6 月 第 15 卷第 3 期
有重要的意义 。 1 原料及工艺 111 原料选择及分析
工艺研究所用的含锌铅钢铁厂粉尘选用了有代 表性的柳州钢厂湿法除尘的高炉尘泥和转炉尘泥 。 对这两种尘泥所进行的化学分析 ,粒度分析和物相 分析的结果如下 :
表 1 尘泥化学成分
2210Βιβλιοθήκη 4419128114196
7810
≈0
≈0
5105
9510
≈1
成球率 ( %) 1110 5130 5100 9418
成球速度 / mm·min - 1
010088 010590 010600 019420
对两种尘泥进行 X 光衍射 、电子探针及显微镜 观察分析 ,得到的两种尘泥的物相结果为 : (1) 转炉 尘泥中的物相主要有 : Fe3O4 ,金属铁和 CaO 、MgO 、 SiO2 、Al2O3 组成的硅酸盐杂相 。高炉尘泥中的物相 有 :金 属 铁 、磁 铁 矿 、赤 铁 矿 、ZnO 、PbO 、SiO2 、方 解 石 ,白云石 ,焦碳 ,硅酸盐杂相 (Ca ,Mg ,Al ,Si) O 。(2)
表 2 两种粉尘的堆密度和粒度分布
名 称 堆密度/ kg·m - 3 20~100 目 100~200 目 200~360 目 - 360 目
高炉尘 转炉尘
776 1176
15193 19177
17153 15148
8149 10105
58107 54103
113 粉尘成球性能 采用动态成球性测定方法测得的动态成球性如
N/个 , 干 球 抗 压 强 度 为 24199 N/ 个 ; 爆 裂 温 度
210 ℃。与已有工艺给出的湿球抗压强度大于 918
N/ 个 ,干球抗压强度大于 1916 N/ 个和落下强度大
于 6 次/ 个的标准[4] ,相比 ,上述指标可以满足环形
炉工艺对生球性能的要求 。说明造球工艺是可行
的。
(4)
Pb (1) = Pb (g)
(5)
此过程要求球团还原率应尽可能高 ,即锌铅挥发的
尽可能完全 ,球团金属化率高 。此外 ,抗压强度应尽
可能高 ,从而使脱锌金属化球团能满足高炉冶炼的
要求 。并得到较多富锌铅的二次粉尘 。目前的环形
炉工艺仅局限在处理锌含量较低和全铁含量较高粉
尘的主要原因在于 :球团还原后的抗压强度较低 ,满
转炉尘泥中的氧化铁相以颗粒状分布在硅酸盐杂相 中 。高炉尘泥中的氧化锌大多数均匀附着在由 (Ca , Mg ,Al ,Si) O 和焦碳末形成的基底相上 。少部分附 着在其它物相上 。氧化铝除小部分以单一圆颗粒均 匀分布在高炉尘泥中外 ,大部分均匀附着在由 ( Ca , Mg ,Al ,Si) O 和焦碳末形成的基底相上 。还有少部 分附着在其它物相上 。