中径计算公式
螺纹大径中径小径

螺纹大径中径小径一、螺纹基本概念介绍1.螺纹的定义螺纹是一种用于连接两个零件的螺旋形纹路。
它可以根据不同的用途和场合分为多种类型,如三角形螺纹、矩形螺纹、圆锥螺纹等。
2.螺纹的分类根据螺纹的形状,可分为三角形螺纹、矩形螺纹、梯形螺纹等。
根据螺纹的用途,可分为连接螺纹、传动螺纹、密封螺纹等。
3.螺纹的作用螺纹主要用于连接两个零件,传递力矩和运动。
通过螺纹的旋转,可以实现零件之间的紧固、拆卸、调整等操作。
二、螺纹的三种直径含义1.螺纹大径螺纹大径是指螺纹的外径,即螺纹的最大直径。
它决定了螺纹的尺寸和连接能力。
2.螺纹中径螺纹中径是指螺纹的平均直径,也称为螺纹的有效直径。
它是计算螺纹面积、强度等参数的重要依据。
3.螺纹小径螺纹小径是指螺纹的内径,即螺纹的最小直径。
它影响了螺纹的牢固程度和磨损性能。
三、螺纹尺寸的测量与计算1.螺纹大径的测量与计算螺纹大径的测量可以使用卡尺、测微计等工具。
计算公式为:螺纹大径= 外径- 2 × 螺纹三角高度。
2.螺纹中径的测量与计算螺纹中径的测量可以使用千分尺、光学测微计等高精度测量工具。
计算公式为:螺纹中径= 平均直径- 0.5 × 螺纹三角高度。
3.螺纹小径的测量与计算螺纹小径的测量可以使用内径千分尺、光学测微计等高精度测量工具。
计算公式为:螺纹小径= 内径- 2 × 螺纹三角高度。
四、螺纹应用领域及注意事项1.螺纹在工程领域的应用螺纹在工程领域广泛应用于建筑、桥梁、隧道等结构物的施工过程中,用于连接钢结构、混凝土结构等。
2.螺纹在机械领域的应用螺纹在机械领域主要用于传动、紧固、调整等作用。
如螺纹轴、螺纹联轴器、螺纹刀具等。
3.螺纹在使用过程中的注意事项(1)选用合适的螺纹规格和材质;(2)正确安装和紧固螺纹连接件;(3)定期检查和维护螺纹连接件,防止磨损、松动等现象;(4)在高温、高压、腐蚀等特殊环境下,选用特殊材质的螺纹连接件。
通过以上介绍,我们对螺纹有了更深入的了解。
螺纹大径、中径、小径计算公式-螺栓中经计算公式

紧固件生产中应用的相关计较公式之五兆芳芳创作一、 60°牙型的外螺纹中径计较及公役(国标GB 197/196)a. 中径根本尺寸计较: 螺纹中径的根本尺寸=螺纹大径-螺距×系数值公式暗示:d/D-P×0.6495例:外螺纹M8螺纹中径的计较8-1.25×0.6495=8-0.8119≈7.188b.经常使用的6h外螺纹中径公役(以螺距为基准) 上限值为”0” 下限值为P0.8-0.095 P1.00-0.112 P1.25-0.118 P1.5-0.132 P1.75-0.150 P2.0-0.16 P2.5-0.17 上限计较公式即根本尺寸,下限值计较公式d2-hes-Td2即中径根本尺寸-偏差-公役M8的6h级中径公役值:上限值7.188 下限值:7.188-0.118=7.07C经常使用的6g级外螺纹中径根本偏差: (以螺距为基准) P 0.80-0.024 P 1.00-0.026 P1.25-0.028 P1.5-0.032 P1.75-0.034 P2-0.038 P2.5-0.042 上限值计较公式d2-ges即根本尺寸-偏差下限值计较公式d2-ges-Td2即根本尺寸-偏差-公役例M8的6g级中径公役值:上限值7.188-0.028=7.16 下限值:7.188-0.028-0.118=7.042注:①以上的螺纹公役是以粗牙为准,对细牙的螺纹公役相应有些变更,但均只是公役变大,所以按此控制不会越出标准界限,故在上述中未一一标出.②螺纹的光杆坯径尺寸在生产实际中按照设计要求的精度和螺纹加工设备的挤压力的不合而相应比设计螺纹中径尺寸加大0.04—0.08之间,为螺纹光杆坯径值,例我们公司的M8外螺纹6g级的螺纹光杆坯径实在7.08—7.13即在此规模.③考虑到生产进程的需要外螺纹在实际生产的未进行热处理和概略处理的中径控制下限应尽量保持在6h级为准二、 60°内螺纹中径计较及公役(GB 197 /196)a. 6H级螺纹中径公役(以螺距为基准) 上限值: P0.8+0.125 P1.00+0.150 P1.25+0.16 P1.5+0.180 P1.25+0.00 P2.0+0.212 P2.5+0.224 下限值为”0”, 上限值计较公式2+TD2即根本尺寸+公役例M8-6H内螺纹中径为:7.188+0.160=7.348 上限值:7.188为下限值b. 内螺纹的中径根本尺寸计较公式与外螺纹相同即D2=D-P×0.6495即内螺纹中径螺纹大径-螺距×系数值c. 6G级螺纹中径根本偏差E1(以螺距为基准) P0.8+0.024 P1.00+0.026 P1.25+0.028 P1.5+0.032 P1.75+0.034 P1.00+0.026 P2.5+0.042 例:M8 6G级内螺纹中径上限值:7.188+0.026+0.16=7.374 下限值:7.188+0.026=7.214 上限值公式2+GE1+TD2即中径根本尺寸+偏差+公役下限值公式2+GE1即中径尺寸+偏差三、外螺纹大径的计较及公役(GB 197/196)a. 外螺纹的6h大径上限值即螺纹直径值例M8为φ8.00上限值公役为”0”b. 外螺纹的6h级大径下限值公役(以螺距为基准) P0.8-0.15 P1.00-0.18 P1.25-0.212 P1.5-0.236 P1.75-0.265 P2.0-0.28 P2.5-0.335 大径下限计较公式:d-Td 即螺纹大径根本尺寸-公役例:M8外螺纹6h大径尺寸:上限为φ8,下限为φ8-0.212=φ7.788c. 外螺纹6g级大径的计较与公役6g级外螺纹的基准偏差(以螺距为基准) P0.8-0.024 P1.00-0.026 P1.25-0.028 P1.5-0.032 P1.25-0.024 P1.75 –0.034 P2.0-0.038 P2.5-0.042 上限计较公式d-ges 即螺纹大径根本尺寸-基准偏差下限计较公式d-ges-Td 即螺纹大径根本尺寸-基准偏差-公役例: M8 外螺纹6g级大径上限值φ8-0.028=φ7.972 下限值φ8-0.028-0.212=φ7.76注:①螺纹的大径是由螺纹光杆坯径及搓丝板/滚丝轮的牙型磨损程度来决定的,并且其数值在同样毛坯及螺纹加工东西的根本上与螺纹中径成正比出现即中径小则大径大,反之中径大则大径小.②对需进行热处理和概略处理等加工的零件,考虑到加工进程的关系实际生产时应将螺纹大径控制在6h级的下限值加0.04mm以上,如M8的外螺纹在搓(滚)丝的大径应包管在φ7.83以上和7.95以下为宜.四、内螺纹小径的计较与公役a. 内螺纹小径的根本尺寸计较(D1) 螺纹小径根本尺寸=内螺纹根本尺寸-螺距×系数例:内螺纹M8的小径根本尺寸8-1.25×1.0825=6.646875≈6.647b. 内螺纹6H级的小径公役(以螺距为基准)及小径值计较P0.8 +0. 2 P1.0 +0. 236 P1.25 +0.265 P1.5 +0.3 P1.75 +0.335 P2.0 +0.375 P2.5 +0.48 内螺纹6H级的下限偏差公式D1+HE1即内螺纹小径根本尺寸+偏差注:6H级的下偏值为“0” 内螺纹6H级的上限值计较公式=D1+HE1+TD1即内螺纹小径根本尺寸+偏差+公役例:6H级M8内螺纹小径的上限值 6.647+0=6.647 6H级M8内螺纹小径的下限值6.647+0+0.265=6.912c. 内螺纹6G级的小径根本偏差(以螺距为基准)及小径值计较P0.8 +0.024 P1.0 +0.026 P1.25 +0.028 P1.5 +0.032 P1.75 +0.034 P2.0 +0.038 P2.5 +0.042 内螺纹6G级的小径下限值公式=D1+GE1即内螺纹根本尺寸+偏差例: 6G级M8内螺纹小径的下限值6.647+0.028=6.675 6G级M8内螺纹小径的上限值公式D1+GE1+TD1即内螺纹根本尺寸+偏差+公役例: 6G级M8内螺纹小径的上限值是6.647+0.028+0.265=6.94 注:①内螺纹的牙高直接关系到内螺纹的承载力矩的大小,故在毛坯生产中应尽量在其6H级上限值以内②在内螺纹的加工进程中,内螺纹小径越小会给加东西——丝锥的使用效益有所影响.从使用的角度讲是小径越小越好,但综合考虑时一般采取小径的在中限至上限值之间,如果是铸铁或铝件时应采取小径的下限值至中限值之间③内螺纹6G级的小径在毛坯生产中可按6H级执行,其精度等级主要考虑螺纹中径的镀层,故只在螺纹加工时考虑丝锥的中径尺寸而不必考虑光孔的小径.五、分度头单分度法计较单分度法计较公式:n=40/Z n:为分度头应转过的转数 Z:工件的等分数 40:分度头定数例:铣削六方的计较代入公式: n=40/6计较:①化简分数:找出最小约数2进行约分,行将份子分母同时除以2得20/3.分数的同时缩小其等分不变.②计较分数:此时要看份子与分母的数值而确定;如份子此分母大时进行计较. 20÷3=6(2/3)即n值,也即分度头应转过6(2/3)转.此时的分数已酿成带分数;带分数的整数部分6为分度头应转过6整圈.带分数的分数2/3则只能是转一圈的2/3,此时又须重新计较③分度板的选用计较:缺乏一圈的计较须借助分度头的分度板来实现.计较时第一步将分数2/3进行同时扩大.例:如果同时扩大14倍时的分数为28/42;如同时扩大10倍时,分数为20/30;如同时扩大13倍时的分数为26/39……扩大分门倍数的多少要按照分度板的孔数来选择.此时应注意:①选择分度板的孔数一定能被分母3整除.如前面举例中的42孔是3的14倍,30孔是3的10倍,39是3的13倍……②分数的扩大必须是份子分母同时扩大其等分不变,如举例中的28/42=2/3×14=(2×14)/(3×14);20/30=2/3×10=(2×10)/(3×10);26/39=2/3×13=(2×13)/(3×13) 28/42分母42即采取分度数的42孔进行分度;份子28即在上轮的定位孔上向前再转过28孔即29孔上为本轮的定位孔,20/30是在30孔分度板向前再转过10孔即11孔上为本轮的定位孔.26/39是在39孔的分度板向前再转26孔即27孔上为本轮的定位孔. 铣六方(六等分)时便可采取42孔,30孔,39孔等被3整除的孔作为分度:其操纵是手柄转整6圈后,再辨别在上轮的定位孔上向前再转28+1/ 10+1 / 26+!孔的29/11/27孔上作为本轮的定位孔例2:铣 15齿的齿轮计较代入公式: n=40/15 计较 n=2(2/3) 是转2整圈再选被3整除的分度孔如24,30,39,42.51.54.57,66等孔板上再向前转过16,20,26,28,34,36,38,44加1孔即17,21,27,29,35,37,39,45孔作为本轮的定位孔.例3: 铣 82齿的分度计较代入公式: n=40/82 计较 n=20/41 即:只要选41孔的分度板,在上轮定位孔上再转过20+1即21孔作为本轮的定位孔便是例4: 铣51齿的分度计较代入公式n=40/51由于此时分数无法计较则只能直接选孔,即选51孔的分度板,在上轮定位孔上再转过51+1即52孔作为本轮的定位孔便是例5 铣100齿的分度计较代入公式n=40/100 计较n=4/10=12/30 即选30孔的分度板,在上轮定位孔上再转过12+1即13孔作为本轮的定位孔便是如所有分度板无计较所需的孔数时则应采取复式分度法计较,不在本计较办法之列,实际生产时一般采取滚齿,因复式分度计较后的实际操纵极其便利六、圆内接六方形的计较公式:①圆D求六方对边(S面) S=0.866D 即直径×0.866(系数)②六方对边(S面)求圆(D)直径D=1.1547S 即对边×1.1547(系数)七、冷镦工序的六方对边与对角计较公式①外六角对边(S)求对角e e=1.13s 即对边×1.13②内六角对边(s)求对角(e) e=1.14s 即对边×1.14(系数)八、圆内接四方形的计较公式:①圆(D)求四方形对边(S面) S=0.7071D 即直径×0.7071②四方对边(S面)求圆(D) D =1.414S 即对边×1.414九、冷镦工序的四方对边与对角的计较公式①外四方对边(S)求对角(e) e=1.4s 即对边(s)×1.4参数十、六方体体积的计较公式① s20.866×H/m/k 即对边×对边×0.866×高或厚度十一、圆台(圆锥)体的体积计较公式0.262H(D2+d2+D×d)即0.262×高度×(大头直径×大头直径+小头直径×小头直径+大头直径×小头直径)十二、球缺体(例如半圆头)的体积计较公式3.1416h2(R-h/3) 即3.1416×高度×高度×(半径-高度÷3)十三、内螺纹用丝锥的加工尺寸计较1.丝锥大径D0的计较公式D0=D+(0.866025P/8)×(0.5~1.3)即丝锥大径螺纹根本尺寸+0.866025螺距÷8×0.5至1.3 注:0.5至1.3的多少选择应按照螺距的大小来确认,螺距值越大则应采取小一点系数,反之,螺距值越小而相应采取大一点系数2.丝锥中径(D2)的计较公式: D2=(3×0.866025P)/8即丝锥中径=3×0.866025×螺距÷83.丝锥小径(D1)的计较公式: D1=(5×0.866025P)/8即丝锥小径=5×0.866025×螺距÷8十四、各类形状冷镦成型用料长度计较已知:圆的体积公式是直径×直径×0.7854×长度或半径×半径×3.1416×长度即d2×0.7854×L或R2×3.1416×L 计较时将需要用料的体积X÷直径÷直径÷0.7854或X÷半径÷半径÷3.1416即为投料的长度列式=X/(3.1416R2)或X/0.7854d2 式中的X暗示需要用料体积数值L暗示实际投料的长度数值R/d暗示实际投料的半径或直径十五、滚齿轮机滚齿轮的挂轮计较a. 滚齿轮主轴定数24b. 滚齿轮挂轮计较是依照将数据分化即同时扩大或缩小其等分不变来实现的B1和b2示意图为复合变速,b3和b4示意图为直接变速c. 主轴参数24的分化c1直接分化可为2×12=24; 3×8=24; 4×6=24 c2扩大倍数后分化: 如扩大5倍24×5=120那么120就可分化为20×6; 3×40; 4×30; 6×20 如扩大8倍 24×8=192那么192就分化为2×91; 91×2; 48×4; 4×48; 3×64; 64×3; 8×24; 24×8; 32×6; 6×32在扩大倍数时应将加工零件的齿数同时扩大到直至以便于分化为止;d. 演算事例分化d.1设加工零件为15齿时的计较列式:24/15同时扩大10倍后240/150;分化同时清除公倍数3得(3×80)/(3×50)=80/50此时可采取 b.4示意图在中间装一任意介轮即在①处装80齿数齿轮②处装50齿数齿轮d.2设加工零件为77齿时的计较列式:24/77同时扩大90倍后2160/6930;分化(40×54)/(70/99)此时可采取 b.1示意图的装配齿轮,考虑到齿轮时的装配便利,1和3数可任意调换,2 和4也可任意调换但1与2或4及3与2或4位置不适调换反之4与1或3及2与1或3同不克不及调换d.3设加工零件为32齿时的计较列式: 24/32 同时扩大5倍后120/160;分化为(4×30)/(4×40)同时清除公倍数4后得30/40此时可采取b.3示意图在中间装任意介轮即在①处装30齿轮②处装40齿轮数齿轮d.4设加工零件为13齿时的计较列式: 24/13同时扩大100倍后2400/1300;分化力(30×80)/(20×65)此时可采取 b.2示意图进行装配,注:为什么2400时分化为30×80也可分化40×60,此时应看装配后齿轮的相互吻合而定,只要好吻合便可,本齿轮齿数也可将2400分化为20×120便可同6.4的示意图装配,。
螺纹大径、中径、小径计算公式-螺栓中经计算公式

紧固件生产中应用的相关计算公式之迟辟智美创作一、 60°牙型的外螺纹中径计算及公差(国标GB 197/196)a. 中径基本尺寸计算: 螺纹中径的基本尺寸=螺纹年夜径-螺距×系数值公式暗示:d/D-P×0.6495例:外螺纹M8螺纹中径的计算8-1.25×0.6495=8-0.8119≈7.188b.经常使用的6h外螺纹中径公差(以螺距为基准) 上限值为”0” 下限值为P0.8-0.095 P1.00-0.112 P1.25-0.118 P1.5-0.132 P1.75-0.150 P2.0-0.16 P2.5-0.17 上限计算公式即基本尺寸,下限值计算公式d2-hes-Td2即中径基本尺寸-偏差-公差M8的6h级中径公差值:上限值7.188 下限值:7.188-0.118=7.07C经常使用的6g级外螺纹中径基本偏差: (以螺距为基准) P 0.80-0.024 P 1.00-0.026 P1.25-0.028 P1.5-0.032 P1.75-0.034 P2-0.038 P2.5-0.042 上限值计算公式d2-ges即基本尺寸-偏差下限值计算公式d2-ges-Td2即基本尺寸-偏差-公差例M8的6g级中径公差值:上限值7.188-0.028=7.16 下限值:7.188-0.028-0.118=7.042注:①以上的螺纹公差是以粗牙为准,对细牙的螺纹公差相应有些变动,但均只是公差变年夜,所以按此控制不会越出规范界限,故在上述中未一一标出.②螺纹的光杆坯径尺寸在生产实际中根据设计要求的精度和螺纹加工设备的挤压力的分歧而相应比设计螺纹中径尺寸加年夜0.04—0.08之间,为螺纹光杆坯径值,例我们公司的M8外螺纹6g级的螺纹光杆坯径实在7.08—7.13即在此范围.③考虑到生产过程的需要外螺纹在实际生产的未进行热处置和概况处置的中径控制下限应尽量坚持在6h级为准二、 60°内螺纹中径计算及公差(GB 197 /196)a. 6H级螺纹中径公差(以螺距为基准) 上限值: P0.8+0.125 P1.00+0.150 P1.25+0.16 P1.5+0.180 P1.25+0.00 P2.0+0.212 P2.5+0.224 下限值为”0”, 上限值计算公式2+TD2即基本尺寸+公差例M8-6H内螺纹中径为:7.188+0.160=7.348 上限值:7.188为下限值b. 内螺纹的中径基本尺寸计算公式与外螺纹相同即D2=D-P×0.6495即内螺纹中径螺纹年夜径-螺距×系数值c. 6G级螺纹中径基本偏差E1(以螺距为基准) P0.8+0.024 P1.00+0.026 P1.25+0.028 P1.5+0.032 P1.75+0.034 P1.00+0.026 P2.5+0.042 例:M8 6G级内螺纹中径上限值:7.188+0.026+0.16=7.374 下限值:7.188+0.026=7.214 上限值公式2+GE1+TD2即中径基本尺寸+偏差+公差下限值公式2+GE1即中径尺寸+偏差三、外螺纹年夜径的计算及公差(GB 197/196)a. 外螺纹的6h年夜径上限值即螺纹直径值例M8为φ8.00上限值公差为”0”b. 外螺纹的6h级年夜径下限值公差(以螺距为基准) P0.8-0.15 P1.00-0.18 P1.25-0.212 P1.5-0.236 P1.75-0.265 P2.0-0.28 P2.5-0.335 年夜径下限计算公式:d-Td 即螺纹年夜径基本尺寸-公差例:M8外螺纹6h年夜径尺寸:上限为φ8,下限为φ8-0.212=φ7.788c. 外螺纹6g级年夜径的计算与公差 6g级外螺纹的基准偏差(以螺距为基准) P0.8-0.024 P1.00-0.026 P1.25-0.028 P1.5-0.032 P1.25-0.024 P1.75 –0.034 P2.0-0.038 P2.5-0.042 上限计算公式d-ges 即螺纹年夜径基本尺寸-基准偏差下限计算公式d-ges-Td 即螺纹年夜径基本尺寸-基准偏差-公差例: M8 外螺纹6g级年夜径上限值φ8-0.028=φ7.972 下限值φ8-0.028-0.212=φ7.76注:①螺纹的年夜径是由螺纹光杆坯径及搓丝板/滚丝轮的牙型磨损水平来决定的,而且其数值在同样毛坯及螺纹加工工具的基础上与螺纹中径成反比呈现即中径小则年夜径年夜,反之中径年夜则年夜径小.②对需进行热处置和概况处置等加工的零件,考虑到加工过程的关系实际生产时应将螺纹年夜径控制在6h级的下限值加0.04mm以上,如M8的外螺纹在搓(滚)丝的年夜径应保证在φ7.83以上和7.95以下为宜.四、内螺纹小径的计算与公差a. 内螺纹小径的基本尺寸计算(D1) 螺纹小径基本尺寸=内螺纹基本尺寸-螺距×系数例:内螺纹M8的小径基本尺寸8-1.25×1.0825=6.646875≈6.647b. 内螺纹6H级的小径公差(以螺距为基准)及小径值计算P0.8 +0. 2 P1.0 +0. 236 P1.25 +0.265 P1.5 +0.3 P1.75 +0.335 P2.0 +0.375 P2.5 +0.48 内螺纹6H级的下限偏差公式D1+HE1即内螺纹小径基本尺寸+偏差注:6H级的下偏值为“0” 内螺纹6H级的上限值计算公式=D1+HE1+TD1即内螺纹小径基本尺寸+偏差+公差例:6H级M8内螺纹小径的上限值 6.647+0=6.647 6H级M8内螺纹小径的下限值6.647+0+0.265=6.912c. 内螺纹6G级的小径基本偏差(以螺距为基准)及小径值计算P0.8 +0.024 P1.0 +0.026 P1.25 +0.028 P1.5 +0.032 P1.75 +0.034 P2.0 +0.038 P2.5 +0.042 内螺纹6G级的小径下限值公式=D1+GE1即内螺纹基本尺寸+偏差例: 6G级M8内螺纹小径的下限值6.647+0.028=6.675 6G级M8内螺纹小径的上限值公式D1+GE1+TD1即内螺纹基本尺寸+偏差+公差例: 6G级M8内螺纹小径的上限值是 6.647+0.028+0.265=6.94 注:①内螺纹的牙高直接关系到内螺纹的承载力矩的年夜小,故在毛坯生产中应尽量在其6H级上限值以内②在内螺纹的加工过程中,内螺纹小径越小会给加工具——丝锥的使用效益有所影响.从使用的角度讲是小径越小越好,但综合考虑时一般采纳小径的在中限至上限值之间,如果是铸铁或铝件时应采纳小径的下限值至中限值之间③内螺纹6G级的小径在毛坯生产中可按6H级执行,其精度品级主要考虑螺纹中径的镀层,故只在螺纹加工时考虑丝锥的中径尺寸而不用考虑光孔的小径.五、分度头单分度法计算单分度法计算公式:n=40/Z n:为分度头应转过的转数 Z:工件的等分数 40:分度头定命例:铣削六方的计算代入公式: n=40/6计算:①化简分数:找出最小约数2进行约分,即将分子分母同时除以2得20/3.分数的同时缩小其等分不变.②计算分数:此时要看分子与分母的数值而确定;如分子此分母年夜时进行计算. 20÷3=6(2/3)即n值,也即分度头应转过6(2/3)转.此时的分数已酿成带分数;带分数的整数部份6为分度头应转过6整圈.带分数的分数2/3则只能是转一圈的2/3,此时又须重新计算③分度板的选用计算:缺乏一圈的计算须借助分度头的分度板来实现.计算时第一步将分数2/3进行同时扩年夜.例:如果同时扩年夜14倍时的分数为28/42;如同时扩年夜10倍时,分数为20/30;如同时扩年夜13倍时的分数为26/39……扩年夜分门倍数的几多要根据分度板的孔数来选择.此时应注意:①选择分度板的孔数一定能被分母3整除.如前面举例中的42孔是3的14倍,30孔是3的10倍,39是3的13倍……②分数的扩年夜必需是分子分母同时扩年夜其等分不变,如举例中的28/42=2/3×14=(2×14)/(3×14);20/30=2/3×10=(2×10)/(3×10);26/39=2/3×13=(2×13)/(3×13) 28/42分母42即采纳分度数的42孔进行分度;分子28即在上轮的定位孔上向前再转过28孔即29孔上为本轮的定位孔,20/30是在30孔分度板向前再转过10孔即11孔上为本轮的定位孔.26/39是在39孔的分度板向前再转26孔即27孔上为本轮的定位孔. 铣六方(六等分)时即可采纳42孔,30孔,39孔等被3整除的孔作为分度:其把持是手柄转整6圈后,再分别在上轮的定位孔上向前再转28+1/ 10+1 / 26+!孔的29/11/27孔上作为本轮的定位孔例2:铣 15齿的齿轮计算代入公式: n=40/15 计算 n=2(2/3) 是转2整圈再选被3整除的分度孔如24,30,39,42.51.54.57,66等孔板上再向前转过16,20,26,28,34,36,38,44加1孔即17,21,27,29,35,37,39,45孔作为本轮的定位孔.例3: 铣 82齿的分度计算代入公式: n=40/82 计算 n=20/41 即:只要选41孔的分度板,在上轮定位孔上再转过20+1即21孔作为本轮的定位孔即是例4: 铣51齿的分度计算代入公式n=40/51由于此时分数无法计算则只能直接选孔,即选51孔的分度板,在上轮定位孔上再转过51+1即52孔作为本轮的定位孔即是例5 铣100齿的分度计算代入公式n=40/100 计算n=4/10=12/30 即选30孔的分度板,在上轮定位孔上再转过12+1即13孔作为本轮的定位孔即是如所有分度板无计算所需的孔数时则应采纳复式分度法计算,不在本计算方法之列,实际生产时一般采纳滚齿,因复式分度计算后的实际把持极为方便六、圆内接六方形的计算公式:①圆D求六方对边(S面) S=0.866D 即直径×0.866(系数)②六方对边(S面)求圆(D)直径D=1.1547S 即对边×1.1547(系数)七、冷镦工序的六方对边与对角计算公式①外六角对边(S)求对角e e=1.13s 即对边×1.13②内六角对边(s)求对角(e) e=1.14s 即对边×1.14(系数)八、圆内接四方形的计算公式:①圆(D)求四方形对边(S面) S=0.7071D 即直径×0.7071②四方对边(S面)求圆(D) D =1.414S 即对边×1.414九、冷镦工序的四方对边与对角的计算公式①外四方对边(S)求对角(e) e=1.4s 即对边(s)×1.4参数十、六方体体积的计算公式① s20.866×H/m/k 即对边×对边×0.866×高或厚度十一、圆台(圆锥)体的体积计算公式0.262H(D2+d2+D×d)即0.262×高度×(年夜头直径×年夜头直径+小头直径×小头直径+年夜头直径×小头直径)十二、球缺体(例如半圆头)的体积计算公式3.1416h2(R-h/3) 即3.1416×高度×高度×(半径-高度÷3)十三、内螺纹用丝锥的加工尺寸计算1.丝锥年夜径D0的计算公式 D0=D+(0.866025P/8)×(0.5~1.3)即丝锥年夜径螺纹基本尺寸+0.866025螺距÷8×0.5至 1.3 注:0.5至1.3的几多选择应根据螺距的年夜小来确认,螺距值越年夜则应采纳小一点系数,反之,螺距值越小而相应采纳年夜一点系数2.丝锥中径(D2)的计算公式: D2=(3×0.866025P)/8即丝锥中径=3×0.866025×螺距÷83.丝锥小径(D1)的计算公式: D1=(5×0.866025P)/8即丝锥小径=5×0.866025×螺距÷8十四、各种形状冷镦成型用料长度计算已知:圆的体积公式是直径×直径×0.7854×长度或半径×半径×3.1416×长度即d2×0.7854×L或R2×3.1416×L 计算时将需要用料的体积X÷直径÷直径÷0.7854或X÷半径÷半径÷3.1416即为投料的长度列式=X/(3.1416R2)或X/0.7854d2 式中的X暗示需要用料体积数值L暗示实际投料的长度数值R/d暗示实际投料的半径或直径十五、滚齿轮机滚齿轮的挂轮计算a. 滚齿轮主轴定命24b. 滚齿轮挂轮计算是依照将数据分解即同时扩年夜或缩小其等分不变来实现的B1和b2示意图为复合变速,b3和b4示意图为直接变速c. 主轴参数24的分解c1直接分解可为2×12=24; 3×8=24; 4×6=24 c2扩年夜倍数后分解: 如扩年夜5倍24×5=120那么120就可分解为20×6; 3×40; 4×30; 6×20 如扩年夜8倍24×8=192那么192就分解为2×91; 91×2; 48×4; 4×48; 3×64; 64×3; 8×24; 24×8; 32×6; 6×32在扩年夜倍数时应将加工零件的齿数同时扩年夜到直至以便于分解为止;d. 演算事例分解d.1设加工零件为15齿时的计算列式:24/15同时扩年夜10倍后240/150;分解同时清除公倍数3得(3×80)/(3×50)=80/50此时可采纳 b.4示意图在中间装一任意介轮即在①处装80齿数齿轮②处装50齿数齿轮d.2设加工零件为77齿时的计算列式:24/77同时扩年夜90倍后2160/6930;分解(40×54)/(70/99)此时可采纳 b.1示意图的装配齿轮,考虑到齿轮时的装配方便,1和3数可任意调换,2 和4也可任意调换但1与2或4及3与2或4位置不适调换反之4与1或3及2与1或3同不能调换d.3设加工零件为32齿时的计算列式: 24/32 同时扩年夜5倍后120/160;分解为(4×30)/(4×40)同时清除公倍数4后得30/40此时可采纳b.3示意图在中间装任意介轮即在①处装30齿轮②处装40齿轮数齿轮d.4设加工零件为13齿时的计算列式: 24/13同时扩年夜100倍后2400/1300;分解力(30×80)/(20×65)此时可采纳 b.2示意图进行装配,注:为什么2400时分解为30×80也可分解40×60,此时应看装配后齿轮的互相吻合而定,只要好吻合即可,本齿轮齿数也可将2400分解为20×120即可同6.4的示意图装配,。
各种螺纹的计算公式

各种螺纹的计算公式一、 60°牙型的外螺纹中径计算及公差(国标GB 197/196)a. 中径基本尺寸计算:螺纹中径的基本尺寸=螺纹大径-螺距×系数值。
公式表示:d/D-P×0.6495例:外螺纹M8螺纹中径的计算8-1.25×0.6495=8-0.8119≈7.188b. 常用的6h外螺纹中径公差(以螺距为基准)。
上限值为“0”,下限值为P0.8-0.095、P1.00-0.112、P1.25-0.118、P1.5-0.132、P1.75-0.150、P2.0-0.16、P2.5-0.17上限计算公式即基本尺寸,下限值计算公式d2-hes-Td2即中径基本尺寸-偏差-公差。
M8的6h级中径公差值:上限值7.188;下限值:7.188-0.118=7.07。
C. 常用的6g级外螺纹中径基本偏差: (以螺距为基准)。
P0.80-0.024、P 1.00-0.026、P1.25-0.028、P1.5-0.032、P1.75-0.034、P2-0.038、P2.5-0.042上限值计算公式d2-ges即基本尺寸-偏差下限值计算公式d2-ges-Td2即基本尺寸-偏差-公差例M8的6g级中径公差值:上限值:7.188-0.028=7.16 下限值:7.188-0.028-0.118=7.042。
注:①以上的螺纹公差是以粗牙为准,对细牙的螺纹公差相应有些变化,但均只是公差变大,所以按此控制不会越出规范界限,故在上述中未一一标出。
②螺纹的光杆坯径尺寸在生产实际中根据设计要求的精度和螺纹加工设备的挤压力的不同而相应比设计螺纹中径尺寸加大0.04—0.08之间,为螺纹光杆坯径值,比如公司的M8外螺纹6g级的螺纹光杆坯径实在7.08—7.13即在此范围。
③考虑到生产过程的需要外螺纹在实际生产的未进行热处理和表面处理的中径控制下限应尽量保持在6h级为准。
二、 60°内螺纹中径计算及公差(GB 197 /196)a. 6H级螺纹中径公差(以螺距为基准)。
螺纹大径、中径、小径计算公式-螺栓中经计算公式

紧固件生产中应用得相关计算公式一、60°牙型得外螺纹中径计算及公差(国标GB 197/196)a、中径基本尺寸计算: 螺纹中径得基本尺寸=螺纹大径-螺距×系数值公式表示:d/D-P×0。
6495例:外螺纹M8螺纹中径得计算8-1.25×0、6495=8-0.8119≈7.188b、常用得6h外螺纹中径公差(以螺距为基准) 上限值为”0”下限值为P0、8-0、095 P1。
00—0、112P1、25-0。
118 P1、5—0、132 P1。
75—0。
150 P2、0—0、16P2、5-0.17 上限计算公式即基本尺寸,下限值计算公式d2-hes-Td2即中径基本尺寸-偏差-公差M8得6h级中径公差值:上限值7。
188下限值:7。
188-0、118=7、07C常用得6g级外螺纹中径基本偏差: (以螺距为基准) P 0.80—0、024P 1.00-0、026P 1.25-0、028 P1。
5-0、032 P1.75-0、034P2-0、038P2.5-0。
042 上限值计算公式d2-ges即基本尺寸-偏差下限值计算公式d2-ges-Td2即基本尺寸—偏差-公差例M8得6g级中径公差值:上限值7。
188—0.028=7、16 下限值:7。
188-0。
028-0.118=7。
042注:①以上得螺纹公差就是以粗牙为准,对细牙得螺纹公差相应有些变化,但均只就是公差变大,所以按此控制不会越出规范界限,故在上述中未一一标出。
②螺纹得光杆坯径尺寸在生产实际中根据设计要求得精度与螺纹加工设备得挤压力得不同而相应比设计螺纹中径尺寸加大0、04—0。
08之间,为螺纹光杆坯径值,例我们公司得M8外螺纹6g级得螺纹光杆坯径实在7。
08—7.13即在此范围。
③考虑到生产过程得需要外螺纹在实际生产得未进行热处理与表面处理得中径控制下限应尽量保持在6h级为准二、60°内螺纹中径计算及公差(GB197 /196)a。
螺纹大径、中径、小径计算公式[精华]
![螺纹大径、中径、小径计算公式[精华]](https://img.taocdn.com/s3/m/62c3a4d02dc58bd63186bceb19e8b8f67c1cef91.png)
紧固件生产中应用的相关计算公式0000一、60°牙型的外螺纹中径计算及公差(国标GB 197/196)0000a. 中径基本尺寸计算: 螺纹中径的基本尺寸=螺纹大径-螺距×系数值公式表示:d/D-P×0.6495 0000例:外螺纹M8螺纹中径的计算8-1.25×0.6495=8-0.8119≈7.188 0000b.常用的6h外螺纹中径公差(以螺距为基准) 上限值为”0”下限值为P0.8-0.095 P1.00-0.112 P1.25-0.118 P1.5-0.132 P1.75-0.150 P2.0-0.16 P2.5-0.17 上限计算公式即基本尺寸,下限值计算公式d2-hes-Td2即中径基本尺寸-偏差-公差M8的6h级中径公差值:上限值7.188 下限值:7.188-0.118=7.07 0000C常用的6g级外螺纹中径基本偏差: (以螺距为基准) P 0.80-0.024 P 1.00-0.026 P1.25-0.028 P1.5-0.032 P1.75-0.034 P2-0.038 P2.5-0.042 上限值计算公式d2-ges即基本尺寸-偏差下限值计算公式d2-ges-Td2即基本尺寸-偏差-公差例M8的6g级中径公差值:上限值7.188-0.028=7.16 下限值:7.188-0.028-0.118=7.042 0000注:①以上的螺纹公差是以粗牙为准,对细牙的螺纹公差相应有些变化,但均只是公差变大,所以按此控制不会越出规范界限,故在上述中未一一标出. 0000②螺纹的光杆坯径尺寸在生产实际中根据设计要求的精度和螺纹加工设备的挤压力的不同而相应比设计螺纹中径尺寸加大0.04—0.08之间,为螺纹光杆坯径值,例我们公司的M8外螺纹6g级的螺纹光杆坯径实在7.08—7.13即在此范围. 0000③考虑到生产过程的需要外螺纹在实际生产的未进行热处理和表面处理的中径控制下限应尽量保持在6h级为准0000二、60°内螺纹中径计算及公差(GB 197 /196) 0000a. 6H级螺纹中径公差(以螺距为基准) 上限值: P0.8+0.125 P1.00+0.150 P1.25+0.16 P1.5+0.180 P1.25+0.00 P2.0+0.212 P2.5+0.224 下限值为”0”, 上限值计算公式2+TD2即基本尺寸+公差例M8-6H内螺纹中径为:7.188+0.160=7.348 上限值:7.188为下限值0000b. 内螺纹的中径基本尺寸计算公式与外螺纹相同即D2=D-P×0.6495即内螺纹中径螺纹大径-螺距×系数值0000c. 6G级螺纹中径基本偏差E1(以螺距为基准) P0.8+0.024 P1.00+0.026 P1.25+0.028 P1.5+0.032 P1.75+0.034 P1.00+0.026 P2.5+0.042 例:M8 6G级内螺纹中径上限值:7.188+0.026+0.16=7.374 下限值:7.188+0.026=7.214 上限值公式2+GE1+TD2即中径基本尺寸+偏差+公差下限值公式2+GE1即中径尺寸+偏差0000三、外螺纹大径的计算及公差(GB 197/196) 0000a. 外螺纹的6h大径上限值即螺纹直径值例M8为φ8.00上限值公差为”0”0000b. 外螺纹的6h级大径下限值公差(以螺距为基准) P0.8-0.15 P1.00-0.18 P1.25-0.212 P1.5-0.236 P1.75-0.265 P2.0-0.28 P2.5-0.335 大径下限计算公式:d-Td 即螺纹大径基本尺寸-公差例:M8外螺纹6h大径尺寸:上限为φ8,下限为φ8-0.212=φ7.788 0000c. 外螺纹6g级大径的计算与公差6g级外螺纹的基准偏差(以螺距为基准) P0.8-0.024 P1.00-0.026 P1.25-0.028 P1.5-0.032 P1.25-0.024 P1.75 –0.034 P2.0-0.038 P2.5-0.042 上限计算公式d-ges 即螺纹大径基本尺寸-基准偏差下限计算公式d-ges-Td 即螺纹大径基本尺寸-基准偏差-公差例: M8 外螺纹6g级大径上限值φ8-0.028=φ7.972 下限值φ8-0.028-0.212=φ7.76 0000注:①螺纹的大径是由螺纹光杆坯径及搓丝板/滚丝轮的牙型磨损程度来决定的,而且其数值在同样毛坯及螺纹加工工具的基础上与螺纹中径成反比出现即中径小则大径大,反之中径大则大径小. 0000②对需进行热处理和表面处理等加工的零件,考虑到加工过程的关系实际生产时应将螺纹大径控制在6h级的下限值加0.04mm以上,如M8的外螺纹在搓(滚)丝的大径应保证在φ7.83以上和7.95以下为宜. 0000四、内螺纹小径的计算与公差0000a. 内螺纹小径的基本尺寸计算(D1) 螺纹小径基本尺寸=内螺纹基本尺寸-螺距×系数例:内螺纹M8的小径基本尺寸8-1.25×1.0825=6.646875≈6.647 0000b. 内螺纹6H级的小径公差(以螺距为基准)及小径值计算P0.8 +0. 2 P1.0 +0. 236 P1.25 +0.265 P1.5 +0.3 P1.75 +0.335 P2.0 +0.375 P2.5 +0.48 内螺纹6H级的下限偏差公式D1+HE1即内螺纹小径基本尺寸+偏差注:6H级的下偏值为“0”内螺纹6H级的上限值计算公式=D1+HE1+TD1即内螺纹小径基本尺寸+偏差+公差例:6H级M8内螺纹小径的上限值6.647+0=6.647 6H级M8内螺纹小径的下限值6.647+0+0.265=6.912 0000c. 内螺纹6G级的小径基本偏差(以螺距为基准)及小径值计算P0.8 +0.024 P1.0 +0.026 P1.25 +0.028 P1.5 +0.032 P1.75 +0.034 P2.0 +0.038 P2.5 +0.042 内螺纹6G级的小径下限值公式=D1+GE1即内螺纹基本尺寸+偏差例: 6G级M8内螺纹小径的下限值 6.647+0.028=6.675 6G 级M8内螺纹小径的上限值公式D1+GE1+TD1即内螺纹基本尺寸+偏差+公差例: 6G级M8内螺纹小径的上限值是6.647+0.028+0.265=6.94 注:①内螺纹的牙高直接关系到内螺纹的承载力矩的大小,故在毛坯生产中应尽量在其6H级上限值以内0000②在内螺纹的加工过程中,内螺纹小径越小会给加工具——丝锥的使用效益有所影响.从使用的角度讲是小径越小越好,但综合考虑时一般采用小径的在中限至上限值之间,如果是铸铁或铝件时应采用小径的下限值至中限值之间0000③内螺纹6G级的小径在毛坯生产中可按6H级执行,其精度等级主要考虑螺纹中径的镀层,故只在螺纹加工时考虑丝锥的中径尺寸而不必考虑光孔的小径。
三针测量法

三针测量法用量针测量螺纹中径的方法称三针量法,测量时,在螺纹凹槽内放置具有同样直径D的三根量针,如图(e)示,然后用适当的量具(如千分尺等)来测量尺寸M的大小,以验证所加工的螺纹中径是否正确。
一.外螺纹中径的计算公式:D2=M-D(1+1/sin(α/2))+t/2*ctg(α/2)M:千分尺测量的数值(mm)、D:量针直径(mm)、α/2:牙形半角、t:工件螺距或蜗杆周节量针直径D的计算公式:D= 0.5t/cos(α/2)如果已知螺纹牙形角,也可用下面简化公式计算:29°: D2=M-4.994D+1.933t; D=0.516t;30°: D2=M-4.864D+1.866t; D=0.518t;40°: D2=M-3.924D+1.374t; D=0.533t; 侧面进刀量:F=0.5(D2-D2')tg(α/2) 55°: D2=M-3.166D+0.96t; D=0.564t;60°: D2=M-3D+0.866t; D=0.577t;或者29°: M=d2+4.994D-1.933t30° : M=d2+4.864D-1.866t40°: M=d2+3.924D-1.374t55° : M=d2+3.166D-0.960t60°: M=d2+3D-0.866t例3用三针量法测量M24*1.5的螺纹,已知D = 0.866mm,d2=23.026mm,求千分尺应测得的读数值?解∵α = 60°代入上式M = d2+3D-0.866t = 23.026+3*0.866-0.866*1.5=24.325mm图(e)二.内螺纹中径的计算公式:D2=M+D(1+SIN(α/2)+COS(α/2)ctg(α/2))-t/2*ctg(α/2)M:千分尺测量的数值(mm)、D:量针直径(mm)、α/2:牙形半角、t:工件螺距或蜗杆周节(mm)量针直径D的计算公式:D= 0.5t/cos(α/2)如果已知螺纹牙形角,也可用下面简化公式计算:29°: D2=M+4.994D-1.933t; D=0.516t;30°: D2=M+4.864D-1.866t; D=0.518t;40°: D2=M+3.924D-1.374t; D=0.533t; 侧面进刀量:F=0.5(D2-D2')tg(α/2) 55°: D2=M+3.166D-0.96t; D=0.564t;60°: D2=M+3D-0.866t; D=0.577t;或者29°: M=d2-4.994D+1.933t30°M=d2-4.864D+1.866t40°: M=d2-3.924D+1.374t55° : M=d2-3.166D+0.960t60°: M=d2-3D+0.866t。
螺纹大径、中径、小径计算公式

紧固件生产中应用的相关计算公式一、60°牙型的外螺纹中径计算及公差(国标GB 197/196)a. 中径基本尺寸计算: 螺纹中径的基本尺寸=螺纹大径-螺距×系数值公式表示:d/D-P×0.6495例:外螺纹M8螺纹中径的计算8-1.25×0.6495=8-0.8119≈7.188b.常用的6h外螺纹中径公差(以螺距为基准) 上限值为”0”下限值为P0.8-0.095 P1.00-0.112 P1.25-0.118 P1.5-0.132 P1.75-0.150 P2.0-0.16 P2.5-0.17 上限计算公式即基本尺寸,下限值计算公式d2-hes-Td2即中径基本尺寸-偏差-公差M8的6h级中径公差值:上限值7.188 下限值:7.188-0.118=7.07C常用的6g级外螺纹中径基本偏差: (以螺距为基准) P 0.80-0.024 P 1.00-0.026 P1.25-0.028 P1.5-0.032 P1.75-0.034 P2-0.038 P2.5-0.042 上限值计算公式d2-ges即基本尺寸-偏差下限值计算公式d2-ges-Td2即基本尺寸-偏差-公差例M8的6g级中径公差值:上限值7.188-0.028=7.16 下限值:7.188-0.028-0.118=7.042注:①以上的螺纹公差是以粗牙为准,对细牙的螺纹公差相应有些变化,但均只是公差变大,所以按此控制不会越出规范界限,故在上述中未一一标出.②螺纹的光杆坯径尺寸在生产实际中根据设计要求的精度和螺纹加工设备的挤压力的不同而相应比设计螺纹中径尺寸加大0.04—0.08之间,为螺纹光杆坯径值,例我们公司的M8外螺纹6g级的螺纹光杆坯径实在7.08—7.13即在此范围.③考虑到生产过程的需要外螺纹在实际生产的未进行热处理和表面处理的中径控制下限应尽量保持在6h级为准二、60°内螺纹中径计算及公差(GB 197 /196)a. 6H级螺纹中径公差(以螺距为基准) 上限值: P0.8+0.125 P1.00+0.150 P1.25+0.16 P1.5+0.180 P1.25+0.00 P2.0+0.212 P2.5+0.224 下限值为”0”, 上限值计算公式2+TD2即基本尺寸+公差例M8-6H内螺纹中径为:7.188+0.160=7.348 上限值:7.188为下限值b. 内螺纹的中径基本尺寸计算公式与外螺纹相同即D2=D-P×0.6495即内螺纹中径螺纹大径-螺距×系数值c. 6G级螺纹中径基本偏差E1(以螺距为基准) P0.8+0.024 P1.00+0.026 P1.25+0.028 P1.5+0.032 P1.75+0.034 P1.00+0.026 P2.5+0.042 例:M8 6G级内螺纹中径上限值:7.188+0.026+0.16=7.374 下限值:7.188+0.026=7.214 上限值公式2+GE1+TD2即中径基本尺寸+偏差+公差下限值公式2+GE1即中径尺寸+偏差三、外螺纹大径的计算及公差(GB 197/196)a. 外螺纹的6h大径上限值即螺纹直径值例M8为φ8.00上限值公差为”0”b. 外螺纹的6h级大径下限值公差(以螺距为基准) P0.8-0.15 P1.00-0.18 P1.25-0.212 P1.5-0.236 P1.75-0.265 P2.0-0.28 P2.5-0.335 大径下限计算公式:d-Td 即螺纹大径基本尺寸-公差例:M8外螺纹6h大径尺寸:上限为φ8,下限为φ8-0.212=φ7.788c. 外螺纹6g级大径的计算与公差6g级外螺纹的基准偏差(以螺距为基准) P0.8-0.024 P1.00-0.026 P1.25-0.028 P1.5-0.032 P1.25-0.024 P1.75 –0.034 P2.0-0.038 P2.5-0.042 上限计算公式d-ges 即螺纹大径基本尺寸-基准偏差下限计算公式d-ges-Td 即螺纹大径基本尺寸-基准偏差-公差例: M8 外螺纹6g级大径上限值φ8-0.028=φ7.972 下限值φ8-0.028-0.212=φ7.76注:①螺纹的大径是由螺纹光杆坯径及搓丝板/滚丝轮的牙型磨损程度来决定的,而且其数值在同样毛坯及螺纹加工工具的基础上与螺纹中径成反比出现即中径小则大径大,反之中径大则大径小.②对需进行热处理和表面处理等加工的零件,考虑到加工过程的关系实际生产时应将螺纹大径控制在6h级的下限值加0.04mm以上,如M8的外螺纹在搓(滚)丝的大径应保证在φ7.83以上和7.95以下为宜.四、内螺纹小径的计算与公差a. 内螺纹小径的基本尺寸计算(D1) 螺纹小径基本尺寸=内螺纹基本尺寸-螺距×系数例:内螺纹M8的小径基本尺寸8-1.25×1.0825=6.646875≈6.647b. 内螺纹6H级的小径公差(以螺距为基准)及小径值计算P0.8 +0. 2 P1.0 +0. 236 P1.25 +0.265 P1.5 +0.3 P1.75 +0.335 P2.0 +0.375 P2.5 +0.48 内螺纹6H级的下限偏差公式D1+HE1即内螺纹小径基本尺寸+偏差注:6H级的下偏值为“0”内螺纹6H级的上限值计算公式=D1+HE1+TD1即内螺纹小径基本尺寸+偏差+公差例:6H级M8内螺纹小径的上限值6.647+0=6.647 6H级M8内螺纹小径的下限值 6.647+0+0.265=6.912c. 内螺纹6G级的小径基本偏差(以螺距为基准)及小径值计算P0.8 +0.024 P1.0 +0.026 P1.25 +0.028 P1.5 +0.032 P1.75 +0.034 P2.0 +0.038 P2.5 +0.042 内螺纹6G级的小径下限值公式=D1+GE1即内螺纹基本尺寸+偏差例: 6G级M8内螺纹小径的下限值 6.647+0.028=6.675 6G 级M8内螺纹小径的上限值公式D1+GE1+TD1即内螺纹基本尺寸+偏差+公差例: 6G级M8内螺纹小径的上限值是 6.647+0.028+0.265=6.94 注:①内螺纹的牙高直接关系到内螺纹的承载力矩的大小,故在毛坯生产中应尽量在其6H级上限值以内②在内螺纹的加工过程中,内螺纹小径越小会给加工具——丝锥的使用效益有所影响.从使用的角度讲是小径越小越好,但综合考虑时一般采用小径的在中限至上限值之间,如果是铸铁或铝件时应采用小径的下限值至中限值之间③内螺纹6G级的小径在毛坯生产中可按6H级执行,其精度等级主要考虑螺纹中径的镀层,故只在螺纹加工时考虑丝锥的中径尺寸而不必考虑光孔的小径。
螺纹大径、中径、小径计算公式
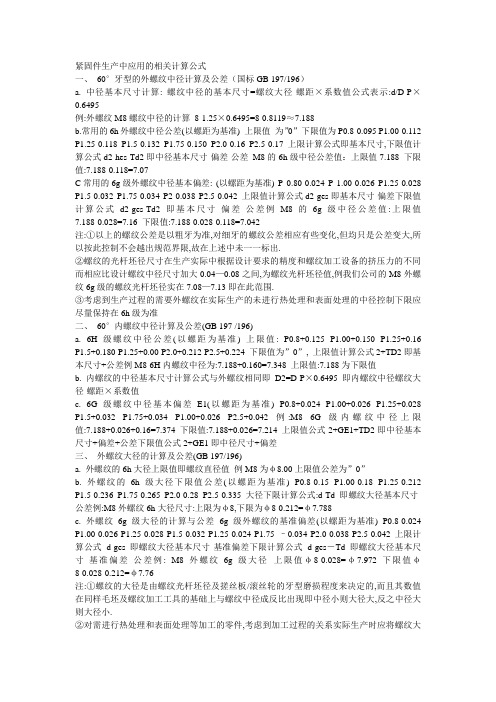
紧固件生产中应用的相关计算公式一、60°牙型的外螺纹中径计算及公差(国标GB 197/196)a. 中径基本尺寸计算: 螺纹中径的基本尺寸=螺纹大径-螺距×系数值公式表示:d/D-P×0.6495例:外螺纹M8螺纹中径的计算8-1.25×0.6495=8-0.8119≈7.188b.常用的6h外螺纹中径公差(以螺距为基准) 上限值为”0”下限值为P0.8-0.095 P1.00-0.112 P1.25-0.118 P1.5-0.132 P1.75-0.150 P2.0-0.16 P2.5-0.17 上限计算公式即基本尺寸,下限值计算公式d2-hes-Td2即中径基本尺寸-偏差-公差M8的6h级中径公差值:上限值7.188 下限值:7.188-0.118=7.07C常用的6g级外螺纹中径基本偏差: (以螺距为基准) P 0.80-0.024 P 1.00-0.026 P1.25-0.028 P1.5-0.032 P1.75-0.034 P2-0.038 P2.5-0.042 上限值计算公式d2-ges即基本尺寸-偏差下限值计算公式d2-ges-Td2即基本尺寸-偏差-公差例M8的6g级中径公差值:上限值7.188-0.028=7.16 下限值:7.188-0.028-0.118=7.042注:①以上的螺纹公差是以粗牙为准,对细牙的螺纹公差相应有些变化,但均只是公差变大,所以按此控制不会越出规范界限,故在上述中未一一标出.②螺纹的光杆坯径尺寸在生产实际中根据设计要求的精度和螺纹加工设备的挤压力的不同而相应比设计螺纹中径尺寸加大0.04—0.08之间,为螺纹光杆坯径值,例我们公司的M8外螺纹6g级的螺纹光杆坯径实在7.08—7.13即在此范围.③考虑到生产过程的需要外螺纹在实际生产的未进行热处理和表面处理的中径控制下限应尽量保持在6h级为准二、60°内螺纹中径计算及公差(GB 197 /196)a. 6H级螺纹中径公差(以螺距为基准) 上限值: P0.8+0.125 P1.00+0.150 P1.25+0.16 P1.5+0.180 P1.25+0.00 P2.0+0.212 P2.5+0.224 下限值为”0”, 上限值计算公式2+TD2即基本尺寸+公差例M8-6H内螺纹中径为:7.188+0.160=7.348 上限值:7.188为下限值b. 内螺纹的中径基本尺寸计算公式与外螺纹相同即D2=D-P×0.6495即内螺纹中径螺纹大径-螺距×系数值c. 6G级螺纹中径基本偏差E1(以螺距为基准) P0.8+0.024 P1.00+0.026 P1.25+0.028 P1.5+0.032 P1.75+0.034 P1.00+0.026 P2.5+0.042 例:M8 6G级内螺纹中径上限值:7.188+0.026+0.16=7.374 下限值:7.188+0.026=7.214 上限值公式2+GE1+TD2即中径基本尺寸+偏差+公差下限值公式2+GE1即中径尺寸+偏差三、外螺纹大径的计算及公差(GB 197/196)a. 外螺纹的6h大径上限值即螺纹直径值例M8为φ8.00上限值公差为”0”b. 外螺纹的6h级大径下限值公差(以螺距为基准) P0.8-0.15 P1.00-0.18 P1.25-0.212 P1.5-0.236 P1.75-0.265 P2.0-0.28 P2.5-0.335 大径下限计算公式:d-Td 即螺纹大径基本尺寸-公差例:M8外螺纹6h大径尺寸:上限为φ8,下限为φ8-0.212=φ7.788c. 外螺纹6g级大径的计算与公差6g级外螺纹的基准偏差(以螺距为基准) P0.8-0.024 P1.00-0.026 P1.25-0.028 P1.5-0.032 P1.25-0.024 P1.75 –0.034 P2.0-0.038 P2.5-0.042 上限计算公式d-ges 即螺纹大径基本尺寸-基准偏差下限计算公式d-ges-Td 即螺纹大径基本尺寸-基准偏差-公差例: M8 外螺纹6g级大径上限值φ8-0.028=φ7.972 下限值φ8-0.028-0.212=φ7.76注:①螺纹的大径是由螺纹光杆坯径及搓丝板/滚丝轮的牙型磨损程度来决定的,而且其数值在同样毛坯及螺纹加工工具的基础上与螺纹中径成反比出现即中径小则大径大,反之中径大则大径小.②对需进行热处理和表面处理等加工的零件,考虑到加工过程的关系实际生产时应将螺纹大径控制在6h级的下限值加0.04mm以上,如M8的外螺纹在搓(滚)丝的大径应保证在φ7.83以上和7.95以下为宜.四、内螺纹小径的计算与公差a. 内螺纹小径的基本尺寸计算(D1) 螺纹小径基本尺寸=内螺纹基本尺寸-螺距×系数例:内螺纹M8的小径基本尺寸8-1.25×1.0825=6.646875≈6.647b. 内螺纹6H级的小径公差(以螺距为基准)及小径值计算P0.8 +0. 2 P1.0 +0. 236 P1.25 +0.265 P1.5 +0.3 P1.75 +0.335 P2.0 +0.375 P2.5 +0.48 内螺纹6H级的下限偏差公式D1+HE1即内螺纹小径基本尺寸+偏差注:6H级的下偏值为“0”内螺纹6H级的上限值计算公式=D1+HE1+TD1即内螺纹小径基本尺寸+偏差+公差例:6H级M8内螺纹小径的上限值6.647+0=6.647 6H级M8内螺纹小径的下限值6.647+0+0.265=6.912c. 内螺纹6G级的小径基本偏差(以螺距为基准)及小径值计算P0.8 +0.024 P1.0 +0.026 P1.25 +0.028 P1.5 +0.032 P1.75 +0.034 P2.0 +0.038 P2.5 +0.042 内螺纹6G级的小径下限值公式=D1+GE1即内螺纹基本尺寸+偏差例: 6G级M8内螺纹小径的下限值6.647+0.028=6.675 6G 级M8内螺纹小径的上限值公式D1+GE1+TD1即内螺纹基本尺寸+偏差+公差例: 6G级M8内螺纹小径的上限值是 6.647+0.028+0.265=6.94 注:①内螺纹的牙高直接关系到内螺纹的承载力矩的大小,故在毛坯生产中应尽量在其6H级上限值以内②在内螺纹的加工过程中,内螺纹小径越小会给加工具——丝锥的使用效益有所影响.从使用的角度讲是小径越小越好,但综合考虑时一般采用小径的在中限至上限值之间,如果是铸铁或铝件时应采用小径的下限值至中限值之间③内螺纹6G级的小径在毛坯生产中可按6H级执行,其精度等级主要考虑螺纹中径的镀层,故只在螺纹加工时考虑丝锥的中径尺寸而不必考虑光孔的小径。
螺纹大径、中径、小径计算公式-螺栓中经计算公式

紧固件生产中应用的相关计较公式之五兆芳芳创作一、 60°牙型的外螺纹中径计较及公役(国标GB 197/196)a. 中径根本尺寸计较: 螺纹中径的根本尺寸=螺纹大径-螺距×系数值公式暗示:d/D-P×0.6495×≈7.188b.经常使用的6h外螺纹中径公役(以螺距为基准) 上限值为”0”下限值为P0.8-0.095 P1.00-0.112 P1.25-0.118 P1.5-0.132 P1.75-0.150 P2.0-0.16 P2.5-0.17 上限计较公式即根本尺寸,下限值计较公式d2-hes-Td2即中径根本尺寸-偏差-公役 M8的6h级中径公役值:上限值7.188 下限值:7.188-0.118=7.07C经常使用的6g级外螺纹中径根本偏差: (以螺距为基准) P 0.80-0.024 P 1.00-0.026 P1.25-0.028 P1.5-0.032 P1.75-0.034 P2-0.038 P2.5-0.042 上限值计较公式d2-ges即根本尺寸-偏差下限值计较公式d2-ges-Td2即根本尺寸-偏差-公役例M8的6g级中径公役值:上限值7.188-0.028=7.16 下限值:7.188-0.028-0.118=7.042注:①以上的螺纹公役是以粗牙为准,对细牙的螺纹公役相应有些变更,但均只是公役变大,所以按此控制不会越出标准界限,故在上述中未一一标出.②——7.13即在此规模.③考虑到生产进程的需要外螺纹在实际生产的未进行热处理和概略处理的中径控制下限应尽量保持在6h级为准二、 60°内螺纹中径计较及公役(GB 197 /196)a. 6H级螺纹中径公役(以螺距为基准) 上限值: P0.8+0.125 P1.00+0.150 P1.25+0.16 P1.5+0.180 P1.25+0.00 P2.0+0.212 P2.5+0.224 下限值为”0”, 上限值计较公式2+TD2即根本尺寸+公役例M8-6H内螺纹中径为:7.188+0.160=7.348 上限值:7.188为下限值b. 内螺纹的中径根本尺寸计较公式与外螺纹相同即D2=D-P××系数值c. 6G级螺纹中径根本偏差E1(以螺距为基准) P0.8+0.024 P1.00+0.026 P1.25+0.028 P1.5+0.032 P1.75+0.034 P1.00+0.026 P2.5+0.042 例:M8 6G级内螺纹中径上限值:7.188+0.026+0.16=7.374 下限值:7.188+0.026=7.214 上限值公式2+GE1+TD2即中径根本尺寸+偏差+公役下限值公式2+GE1即中径尺寸+偏差三、外螺纹大径的计较及公役(GB 197/196)a. 外螺纹的6h大径上限值即螺纹直径值例M8为φ”0”b. 外螺纹的6h级大径下限值公役(以螺距为基准) P0.8-0.15 P1.00-0.18 P1.25-0.212 P1.5-0.236 P1.75-0.265 P2.0-0.28 P2.5-0.335 大径下限计较公式:d-Td 即螺纹大径根本尺寸-公役例:M8外螺纹6h大径尺寸:上限为φ8,下限为φ8-0.212=φ7.788c. 外螺纹6g级大径的计较与公役 6g级外螺纹的基准偏差(以螺距为基准) P0.8-0.024 P1.00-0.026 P1.25-0.028 P1.5-0.032 P1.25-0.024 P1.75 –0.034 P2.0-0.038 P2.5-0.042 上限计较公式 d-ges 即螺纹大径根本尺寸-基准偏差下限计较公式 d-ges-Td 即螺纹大径根本尺寸-基准偏差-公役例: M8 外螺纹6g级大径上限值φ8-0.028=φ7.972 下限值φ8-0.028-0.212=φ7.76注:①螺纹的大径是由螺纹光杆坯径及搓丝板/滚丝轮的牙型磨损程度来决定的,并且其数值在同样毛坯及螺纹加工东西的根本上与螺纹中径成正比出现即中径小则大径大,反之中径大则大径小.②对需进行热处理和概略处理等加工的零件,考虑到加工进程的关系实际生产时应将螺纹大径控制在6h级的下限值加0.04mm 以上,如M8的外螺纹在搓(滚)丝的大径应包管在φ7.83以上和7.95以下为宜.四、内螺纹小径的计较与公役a. 内螺纹小径的根本尺寸计较(D1) 螺纹小径根本尺寸=内螺纹根本尺寸-螺距××≈6.647b. 内螺纹6H级的小径公役(以螺距为基准)及小径值计较 P0.8 +0. 2 P1.0 +0. 236 P1.25 +0.265 P1.5 +0.3 P1.75 +0.335 P2.0 +0.375 P2.5 +0.48 内螺纹6H级的下限偏差公式D1+HE1即内螺纹小径根本尺寸+偏差注:6H级的下偏值为“0”65=6.912c. 内螺纹6G级的小径根本偏差(以螺距为基准)及小径值计较P0.8 +0.024 P1.0 +0.026 P1.25 +0.028 P1.5 +0.032 P1.75 +0.034 P2.0 +0.038 P2.5 +0.042 内螺纹6G级的小径下限值公式=D1+GE1即内螺纹根本尺寸+偏差例: 6G级M8内螺纹小径的下限值 6.647+0.028=6.675 6G级M8内螺纹小径的上限值公式D1+GE1+TD1即内螺纹根本尺寸+偏差+公役例: 6G级M8内螺纹小径的上限值是 6.647+0.028+0.265=6.94 注:①内螺纹的牙高直接关系到内螺纹的承载力矩的大小,故在毛坯生产中应尽量在其6H级上限值以内②在内螺纹的加工进程中,内螺纹小径越小会给加东西——丝锥的使用效益有所影响.从使用的角度讲是小径越小越好,但综合考虑时一般采取小径的在中限至上限值之间,如果是铸铁或铝件时应采取小径的下限值至中限值之间③内螺纹6G级的小径在毛坯生产中可按6H级执行,其精度等级主要考虑螺纹中径的镀层,故只在螺纹加工时考虑丝锥的中径尺寸而不必考虑光孔的小径.五、分度头单分度法计较单分度法计较公式:n=40/Z n:为分度头应转过的转数 Z:工件的等分数 40:分度头定数例:铣削六方的计较代入公式: n=40/6计较:①化简分数:找出最小约数2进行约分,行将份子分母同时除以2得20/3.分数的同时缩小其等分不变.②计较分数:此时要看份子与分母的数值而确定;如份子此分母大时进行计较. 20÷3=6(2/3)即n值,也即分度头应转过6(2/3)转.此时的分数已酿成带分数;带分数的整数部分6为分度头应转过6整圈.带分数的分数2/3则只能是转一圈的2/3,此时又须重新计较③分度板的选用计较:缺乏一圈的计较须借助分度头的分度板来实现.计较时第一步将分数2/3进行同时扩大.例:如果同时扩大14倍时的分数为28/42;如同时扩大10倍时,分数为20/30;如同时扩大13倍时的分数为26/39……扩大分门倍数的多少要按照分度板的孔数来选择.此时应注意:①选择分度板的孔数一定能被分母3整除.如前面举例中的42孔是3的14倍,30孔是3的10倍,39是3的13倍……②分数的扩大必须是份子分母同时扩大其等分不变,如举例中的28/42=2/3×14=(2×14)/(3×14);20/30=2/3×10=(2×10)/(3×10); 26/39=2/3×13=(2×13)/(3×13) 28/42分母42即采取分度数的42孔进行分度;份子28即在上轮的定位孔上向前再转过28孔即29孔上为本轮的定位孔,20/30是在30孔分度板向前再转过10孔即11孔上为本轮的定位孔.26/39是在39孔的分度板向前再转26孔即27孔上为本轮的定位孔. 铣六方(六等分)时便可采取42孔,30孔,39孔等被3整除的孔作为分度:其操纵是手柄转整6圈后,再辨别在上轮的定位孔上向前再转28+1/ 10+1 / 26+!孔的29/11/27孔上作为本轮的定位孔例2:铣 15齿的齿轮计较代入公式: n=40/15 计较 n=2(2/3) 是转2整圈再选被3整除的分度孔如24,30,39,42.51.54.57,66等孔板上再向前转过16,20,26,28,34,36,38,44加1孔即17,21,27,29,35,37,39,45孔作为本轮的定位孔.例3: 铣 82齿的分度计较代入公式: n=40/82 计较 n=20/41 即:只要选41孔的分度板,在上轮定位孔上再转过20+1即21孔作为本轮的定位孔便是例4: 铣51齿的分度计较代入公式n=40/51由于此时分数无法计较则只能直接选孔,即选51孔的分度板,在上轮定位孔上再转过51+1即52孔作为本轮的定位孔便是例 5 铣100齿的分度计较代入公式n=40/100 计较n=4/10=12/30 即选30孔的分度板,在上轮定位孔上再转过12+1即13孔作为本轮的定位孔便是如所有分度板无计较所需的孔数时则应采取复式分度法计较,不在本计较办法之列,实际生产时一般采取滚齿,因复式分度计较后的实际操纵极其便利六、圆内接六方形的计较公式:①圆D求六方对边(S面) S=0.866D 即直径×0.866(系数)②六方对边(S面)求圆(D)直径 D=1.1547S 即对边×1.1547(系数)七、冷镦工序的六方对边与对角计较公式①外六角对边(S)求对角e e=1.13s 即对边×1.13②内六角对边(s)求对角(e) e=1.14s 即对边×1.14(系数)③外六角对边(s)求对角(D)的头部用料直径,应按(6.2公式)六方对边(s面)求圆(D)直径并适量加大其偏移中心值即D≥八、圆内接四方形的计较公式:①圆(D)求四方形对边(S面) S=0.7071D 即直径×0.7071②四方对边(S面)求圆(D) D =1.414S 即对边×1.414九、冷镦工序的四方对边与对角的计较公式①外四方对边(S)求对角(e) e=1.4s 即对边(s)×1.4参数②内四方对边(s)求对角(e) e=1.45s 即对边(s)×十、六方体体积的计较公式①×H/m/k 即对边×对边××高或厚度十一、圆台(圆锥)体的体积计较公式 0.262H(D2+d2+D××高度×(大头直径×大头直径+小头直径×小头直径+大头直径×小头直径)×高度×高度×(半径-高度÷3)十三、内螺纹用丝锥的加工尺寸计较1.丝锥大径D0的计较公式 D0=D+(0.866025P/8)×÷8×0.5至1.3 注:0.5至1.3的多少选择应按照螺距的大小来确认,螺距值越大则应采取小一点系数,反之,螺距值越小而相应采取大一点系数2.丝锥中径(D2)的计较公式: D2=(3×0.866025P)/8即丝锥中径=3××螺距÷8 3.丝锥小径(D1)的计较公式: D1=(5×0.866025P)/8即丝锥小径=5××螺距÷8十四、各类形状冷镦成型用料长度计较已知:圆的体积公式是直径×直径××长度或半径×半径××长度即d2××L或 R2××L 计较时将需要用料的体积X÷直径÷直径÷÷半径÷半径÷3.1416即为投料的长度列式=X/(3.1416R2)或X/0.7854d2 式中的X暗示需要用料体积数值 L暗示实际投料的长度数值 R/d暗示实际投料的半径或直径十五、滚齿轮机滚齿轮的挂轮计较a. 滚齿轮主轴定数24b. 滚齿轮挂轮计较是依照将数据分化即同时扩大或缩小其等分不变来实现的 B1和b2示意图为复合变速,b3和b4示意图为直接变速c. 主轴参数24的分化 c1直接分化可为 2×12=24; 3×8=24; 4×6=24 c2扩大倍数后分化: 如扩大5倍24×5=120那么120就可分化为20×6; 3×40; 4×30; 6×20 如扩大8倍 24×8=192那么192就分化为2×91; 91×2; 48×4; 4×48; 3×64; 64×3; 8×24; 24×8; 32×6; 6×32在扩大倍数时应将加工零件的齿数同时扩大到直至以便于分化为止;d. 演算事例分化d.1设加工零件为15齿时的计较列式:24/15同时扩大10倍后240/150;分化同时清除公倍数3得(3×80)/(3×①处装80齿数齿轮②处装50齿数齿轮d.2设加工零件为77齿时的计较列式:24/77同时扩大90倍后2160/6930;分化(40×54)/(70/99)此时可采取 b.1示意图的装配齿轮,考虑到齿轮时的装配便利,1和3数可任意调换,2 和4也可任意调换但1与2或4及3与2或4位置不适调换反之4与1或3及2与1或3同不克不及调换 d.3设加工零件为32齿时的计较列式: 24/32 同时扩大5倍后120/160;分化为(4×30)/(4×①处装30齿轮②处装40齿轮数齿轮 d.4设加工零件为13齿时的计较列式: 24/13同时扩大100倍后2400/1300;分化力(30×80)/(20×65)此时可采取b.2示意图进行装配,注:为什么2400时分化为30×80也可分化40×60,此时应看装配后齿轮的相互吻合而定,只要好吻合便可,本齿轮齿数也可将2400分化为20×120便可同6.4的示意图装配,。
螺纹大径、中径、小径计算公式

紧固件生产中应用的相关计算公式一、60°牙型的外螺纹中径计算及公差(国标 GB 197/196 )a.中径基本尺寸计算:螺纹中径的基本尺寸=螺纹大径-螺距x系数值公式表示:d/D-P x0.6495例:外螺纹 M8螺纹中径的计算8-1.25 x 0.6495=8-0.8119〜7.188b.常用的6h外螺纹中径公差(以螺距为基准)上限值为”0”下限值为P0.8-0.095 P1.00-0.112P1.25-0.118 P1.5-0.132 P1.75-0.150 P2.0-0.16 P2.5-0.17 上限计算公式即基本尺寸,下限值计算公式d2-hes-Td2即中径基本尺寸-偏差-公差M8的6h级中径公差值:上限值 7.188下限值:7.188-0.118=7.07C常用的6g级外螺纹中径基本偏差:(以螺距为基准)P 0.80-0.024 P 1.00-0.026 P1.25-0.028P1.5-0.032 P1.75-0.034 P2-0.038 P2.5-0.042上限值计算公式 d2-ges即基本尺寸-偏差下限值计算公式d2-ges-Td2即基本尺寸-偏差-公差例 M8的6g级中径公差值:上限值 7.188-0.028=7.16 下限值:7.188-0.028-0.118=7.042注:①以上的螺纹公差是以粗牙为准,对细牙的螺纹公差相应有些变化,但均只是公差变大,所以按此控制不会越出规范界限,故在上述中未--- 标出.②螺纹的光杆坯径尺寸在生产实际中根据设计要求的精度和螺纹加工设备的挤压力的不同而相应比设计螺纹中径尺寸加大0.04— 0.08之间,为螺纹光杆坯径值,例我们公司的 M8外螺纹6g级的螺纹光杆坯径实在7.08 — 7.13即在此范围.③考虑到生产过程的需要外螺纹在实际生产的未进行热处理和表面处理的中径控制下限应尽量保持在6h级为准二、60°内螺纹中径计算及公差(GB 197 /196)a.6H 级螺纹中径公差(以螺距为基准)上限值:P0.8+0.125 P1.00+0.150 P1.25+0.16 P1.5+0.180 P1.25+0.00 P2.0+0.212 P2.5+0.224 下限值为” 0” ,上限值计算公式 2+TD2 即基本尺寸+公差例M8-6H内螺纹中径为:7.188+0.160=7.348上限值:7.188为下限值b.内螺纹的中径基本尺寸计算公式与外螺纹相同即D2=D-P x 0.6495即内螺纹中径螺纹大径-螺距X系数值c.6G 级螺纹中径基本偏差 E1(以螺距为基准)P0.8+0.024 P1.00+0.026 P1.25+0.028P1.5+0.032 P1.75+0.034 P1.00+0.026 P2.5+0.042 例:M8 6G 级内螺纹中径上限值:7.188+0.026+0.16=7.374 下限值:7.188+0.026=7.214 上限值公式 2+GE1+TD2 即中径基本尺寸+偏差+公差下限值公式 2+GE1即中径尺寸+偏差三、外螺纹大径的计算及公差(GB 197/196)a.外螺纹的6h大径上限值即螺纹直径值例M8为$ 8.00上限值公差为”0”b.外螺纹的 6h级大径下限值公差(以螺距为基准)P0.8-0.15 P1.00-0.18 P1.25-0.212 P1.5-0.236 P1.75-0.265 P2.0-0.28 P2.5-0.335大径下限计算公式:d-Td即螺纹大径基本尺寸- 公差例:M8外螺纹6h大径尺寸:上限为$ 8,下限为$ 8-0.212= $ 7.788c.外螺纹6g级大径的计算与公差6g级外螺纹的基准偏差(以螺距为基准)P0.8-0.024 P1.00-0.026 P1.25-0.028 P1.5-0.032 P1.25-0.024 P1.75 - 0.034 P2.0-0.038 P2.5-0.042 上限计算公式d-ges即螺纹大径基本尺寸-基准偏差下限计算公式d-ges- Td即螺纹大径基本尺寸-基准偏差-公差例:M8外螺纹6g级大径上限值$ 8-0.028= $ 7.972下限值$ 8-0.028-0.212= $ 7.76注:①螺纹的大径是由螺纹光杆坯径及搓丝板/滚丝轮的牙型磨损程度来决定的,而且其数值在同样毛坯及螺纹加工工具的基础上与螺纹中径成反比出现即中径小则大径大,反之中径大则大径小.②对需进行热处理和表面处理等加工的零件,考虑到加工过程的关系实际生产时应将螺纹大径控制在6h级的下限值加 0.04mm以上,如M8的外螺纹在搓(滚)丝的大径应保证在 $ 7.83 以上和7.95以下为宜.四、内螺纹小径的计算与公差a.内螺纹小径的基本尺寸计算(D1)螺纹小径基本尺寸 =内螺纹基本尺寸-螺距x系数例:内螺纹 M8的小径基本尺寸8-1.25 X 1.0825=6.646875〜6.647b.内螺纹6H级的小径公差(以螺距为基准)及小径值计算 P0.8 +0. 2 P1.0 +0. 236 P1.25 +0.265P1.5 +0.3 P1.75 +0.335 P2.0 +0.375 P2.5 +0.48 内螺纹 6H 级的下限偏差公式 D1+HE1 即内螺纹小径基本尺寸 +偏差注:6H级的下偏值为“ 0”内螺纹6H级的上限值计算公式=D1+HE1+TD1即内螺纹小径基本尺寸+偏差+公差例:6H级M8内螺纹小径的上限值6.647+0=6.647 6H 级 M8 内螺纹小径的下限值 6.647+0+0.265=6.912c.内螺纹6G级的小径基本偏差(以螺距为基准)及小径值计算 P0.8 +0.024 P1.0 +0.026 P1.25+0.028 P1.5 +0.032 P1.75 +0.034 P2.0 +0.038 P2.5 +0.042 内螺纹 6G 级的小径下限值公式=D1+GE1即内螺纹基本尺寸 +偏差例:6G级M8内螺纹小径的下限值 6.647+0.028=6.675 6G 级M8内螺纹小径的上限值公式D1+GE1+TD1即内螺纹基本尺寸+偏差+公差例:6G级M8内螺纹小径的上限值是 6.647+0.028+0.265=6.94注:①内螺纹的牙高直接关系到内螺纹的承载力矩的大小,故在毛坯生产中应尽量在其6H级上限值以内②在内螺纹的加工过程中,内螺纹小径越小会给加工具一一丝锥的使用效益有所影响.从使用的角度讲是小径越小越好,但综合考虑时一般采用小径的在中限至上限值之间,如果是铸铁或铝件时应采用小径的下限值至中限值之间③内螺纹6G级的小径在毛坯生产中可按6H级执行,其精度等级主要考虑螺纹中径的镀层, 故只在螺纹加工时考虑丝锥的中径尺寸而不必考虑光孔的小径。
螺纹大径、中径、小径计算公式-螺栓中经计算公式

紧固件生产中应用的相关计算公式之青柳念文创作一、60°牙型的外罗纹中径计算及公差(国标GB 197/196)a. 中径基本尺寸计算: 罗纹中径的基本尺寸=罗纹大径-螺距×系数值公式暗示:d/D-P×0.6495×≈7.188b.常常使用的6h外罗纹中径公差(以螺距为基准) 上限值为”0”下限值为P0.8-0.095 P1.00-0.112 P1.25-0.118 P1.5-0.132 P1.75-0.150 P2.0-0.16 P2.5-0.17 上限计算公式即基本尺寸,下限值计算公式d2-hes-Td2即中径基本尺寸-偏差-公差 M8的6h级中径公差值:上限值7.188 下限值:7.188-0.118=7.07C常常使用的6g级外罗纹中径基本偏差: (以螺距为基准) P 0.80-0.024 P 1.00-0.026 P1.25-0.028 P1.5-0.032 P1.75-0.034 P2-0.038 P2.5-0.042 上限值计算公式d2-ges即基本尺寸-偏差下限值计算公式d2-ges-Td2即基本尺寸-偏差-公差例M8的6g级中径公差值:上限值7.188-0.028=7.16 下限值:7.188-0.028-0.118=7.042注:①以上的罗纹公差是以粗牙为准,对细牙的罗纹公差相应有些变更,但均只是公差变大,所以按此节制不会越出规范边界,故在上述中未一一标出.②——7.13即在此范围.③思索到生产过程的需要外罗纹在实际生产的未停止热处理和概况处理的中径节制下限应尽可能坚持在6h级为准二、 60°内罗纹中径计算及公差(GB 197 /196)a. 6H级罗纹中径公差(以螺距为基准) 上限值: P0.8+0.125 P1.00+0.150 P1.25+0.16 P1.5+0.180 P1.25+0.00 P2.0+0.212 P2.5+0.224 下限值为”0”, 上限值计算公式2+TD2即基本尺寸+公差例M8-6H内罗纹中径为:7.188+0.160=7.348 上限值:7.188为下限值b. 内罗纹的中径基本尺寸计算公式与外罗纹相同即D2=D-P ××系数值c. 6G级罗纹中径基本偏差E1(以螺距为基准) P0.8+0.024 P1.00+0.026 P1.25+0.028 P1.5+0.032 P1.75+0.034 P1.00+0.026 P2.5+0.042 例:M8 6G级内罗纹中径上限值:7.188+0.026+0.16=7.374 下限值:7.188+0.026=7.214 上限值公式2+GE1+TD2即中径基本尺寸+偏差+公差下限值公式2+GE1即中径尺寸+偏差三、外罗纹大径的计算及公差(GB 197/196)a. 外罗纹的6h大径上限值即罗纹直径值例M8为φ”0”b. 外罗纹的6h级大径下限值公差(以螺距为基准) P0.8-0.15 P1.00-0.18 P1.25-0.212 P1.5-0.236 P1.75-0.265 P2.0-0.28 P2.5-0.335 大径下限计算公式:d-Td 即罗纹大径基本尺寸-公差例:M8外罗纹6h大径尺寸:上限为φ8,下限为φ8-0.212=φ7.788c. 外罗纹6g级大径的计算与公差 6g级外罗纹的基准偏差(以螺距为基准) P0.8-0.024 P1.00-0.026 P1.25-0.028 P1.5-0.032 P1.25-0.024 P1.75 –0.034 P2.0-0.038 P2.5-0.042 上限计算公式 d-ges 即罗纹大径基本尺寸-基准偏差下限计算公式 d-ges-Td 即罗纹大径基本尺寸-基准偏差-公差例: M8 外罗纹6g级大径上限值φ8-0.028=φ7.972 下限值φ8-0.028-0.212=φ7.76注:①罗纹的大径是由罗纹光杆坯径及搓丝板/滚丝轮的牙型磨损程度来决议的,而且其数值在同样毛坯及罗纹加工工具的基础上与罗纹中径成反比出现即中径小则大径大,反之中径大则大径小.②对需停止热处理和概况处理等加工的零件,思索到加工过程的关系实际生产时应将罗纹大径节制在6h级的下限值加0.04mm以上,如M8的外罗纹在搓(滚)丝的大径应包管在φ7.83以上和7.95以下为宜.四、内罗纹小径的计算与公差a. 内罗纹小径的基本尺寸计算(D1) 罗纹小径基本尺寸=内罗纹基本尺寸-螺距××≈6.647b. 内罗纹6H级的小径公差(以螺距为基准)及小径值计算P0.8 +0. 2 P1.0 +0. 236 P1.25 +0.265 P1.5 +0.3 P1.75 +0.335 P2.0 +0.375 P2.5 +0.48 内罗纹6H级的下限偏差公式D1+HE1即内罗纹小径基本尺寸+偏差注:6H级的下偏值为“0”65=6.912c. 内罗纹6G级的小径基本偏差(以螺距为基准)及小径值计算P0.8 +0.024 P1.0 +0.026 P1.25 +0.028 P1.5 +0.032 P1.75 +0.034 P2.0 +0.038 P2.5 +0.042 内罗纹6G级的小径下限值公式=D1+GE1即内罗纹基本尺寸+偏差例: 6G级M8内罗纹小径的下限值 6.647+0.028=6.675 6G级M8内罗纹小径的上限值公式D1+GE1+TD1即内罗纹基本尺寸+偏差+公差例: 6G级M8内罗纹小径的上限值是6.647+0.028+0.265=6.94 注:①内罗纹的牙高直接关系到内罗纹的承载力矩的大小,故在毛坯生产中应尽可能在其6H 级上限值以内②在内罗纹的加工过程中,内罗纹小径越小会给加工具——丝锥的使用效益有所影响.从使用的角度讲是小径越小越好,但综合思索时一般采取小径的在中限至上限值之间,如果是铸铁或铝件时应采取小径的下限值至中限值之间③内罗纹6G级的小径在毛坯生产中可按6H级执行,其精度等级主要思索罗纹中径的镀层,故只在罗纹加工时思索丝锥的中径尺寸而不必思索光孔的小径.五、分度头单分度法计算单分度法计算公式:n=40/Z n:为分度头应转过的转数 Z:工件的等分数 40:分度头定数例:铣削六方的计算代入公式: n=40/6计算:①化简分数:找出最小约数2停止约分,即将分子分母同时除以2得20/3.分数的同时缩小其等分不变.②计算分数:此时要看分子与分母的数值而确定;如分子此分母大时停止计算. 20÷3=6(2/3)即n值,也即分度头应转过6(2/3)转.此时的分数已变成带分数;带分数的整数部分6为分度头应转过6整圈.带分数的分数2/3则只能是转一圈的2/3,此时又须重新计算③分度板的选用计算:缺乏一圈的计算须借助分度头的分度板来实现.计算时第一步将分数2/3停止同时扩展.例:如果同时扩展14倍时的分数为28/42;如同时扩展10倍时,分数为20/30;如同时扩展13倍时的分数为26/39……扩展分门倍数的多少要根据分度板的孔数来选择.此时应注意:①选择分度板的孔数一定能被分母3整除.如前面举例中的42孔是3的14倍,30孔是3的10倍,39是3的13倍……②分数的扩展必须是分子分母同时扩展其等分不变,如举例中的 28/42=2/3×14=(2×14)/(3×14);20/30=2/3×10=(2×10)/(3×10); 26/39=2/3×13=(2×13)/(3×13) 28/42分母42即采取分度数的42孔停止分度;分子28即在上轮的定位孔上向前再转过28孔即29孔上为本轮的定位孔,20/30是在30孔分度板向前再转过10孔即11孔上为本轮的定位孔.26/39是在39孔的分度板向前再转26孔即27孔上为本轮的定位孔. 铣六方(六等分)时即可采取42孔,30孔,39孔等被3整除的孔作为分度:其操纵是手柄转整6圈后,再分别在上轮的定位孔上向前再转28+1/ 10+1 / 26+!孔的29/11/27孔上作为本轮的定位孔例2:铣15齿的齿轮计算代入公式: n=40/15 计算n=2(2/3) 是转2整圈再选被3整除的分度孔如24,30,39,42.51.54.57,66等孔板上再向前转过16,20,26,28,34,36,38,44加1孔即17,21,27,29,35,37,39,45孔作为本轮的定位孔.例3: 铣82齿的分度计算代入公式: n=40/82 计算n=20/41 即:只要选41孔的分度板,在上轮定位孔上再转过20+1即21孔作为本轮的定位孔即是例4: 铣51齿的分度计算代入公式 n=40/51由于此时分数无法计算则只能直接选孔,即选51孔的分度板,在上轮定位孔上再转过51+1即52孔作为本轮的定位孔即是例5 铣 100齿的分度计算代入公式 n=40/100 计算 n=4/10=12/30 即选30孔的分度板,在上轮定位孔上再转过12+1即13孔作为本轮的定位孔即是如所有分度板无计算所需的孔数时则应采取复式分度法计算,不在本计算方法之列,实际生产时一般采取滚齿,因复式分度计算后的实际操纵极为方便六、圆内接六方形的计算公式:①圆D求六方对边(S面) S=0.866D 即直径×0.866(系数)②六方对边(S面)求圆(D)直径D=1.1547S 即对边×1.1547(系数)七、冷镦工序的六方对边与对角计算公式①外六角对边(S)求对角e e=1.13s 即对边×1.13②内六角对边(s)求对角(e) e=1.14s 即对边×1.14(系数)③外六角对边(s)求对角(D)的头部用料直径,应按(6.2公式)六方对边(s面)求圆(D)直径并适量加大其偏移中心值即D ≥八、圆内接四方形的计算公式:①圆(D)求四方形对边(S面) S=0.7071D 即直径×0.7071②四方对边(S面)求圆(D) D =1.414S 即对边×1.414九、冷镦工序的四方对边与对角的计算公式①外四方对边(S)求对角(e) e=1.4s 即对边(s)×1.4参数②内四方对边(s)求对角(e) e=1.45s 即对边(s)×十、六方体体积的计算公式①×H/m/k 即对边×对边××高或厚度十一、圆台(圆锥)体的体积计算公式 0.262H(D2+d2+D××高度×(大头直径×大头直径+小头直径×小头直径+大头直径×小头直径)×高度×高度×(半径-高度÷3)十三、内罗纹用丝锥的加工尺寸计算1.丝锥大径D0的计算公式 D0=D+(0.866025P/8)×÷8×0.5至1.3 注:0.5至1.3的多少选择应根据螺距的大小来确认,螺距值越大则应采取小一点系数,反之,螺距值越小而相应采取大一点系数2.丝锥中径(D2)的计算公式: D2=(3×0.866025P)/8即丝锥中径=3××螺距÷83.丝锥小径(D1)的计算公式: D1=(5×0.866025P)/8即丝锥小径=5××螺距÷8十四、各种形状冷镦成型用料长度计算已知:圆的体积公式是直径×直径××长度或半径×半径××长度即d2××L 或 R2××L 计算时将需要用料的体积X÷直径÷直径÷÷半径÷半径÷3.1416即为投料的长度列式=X/(3.1416R2)或X/0.7854d2 式中的X暗示需要用料体积数值 L暗示实际投料的长度数值 R/d暗示实际投料的半径或直径十五、滚齿轮机滚齿轮的挂轮计算a. 滚齿轮主轴定数24b. 滚齿轮挂轮计算是依照将数据分解即同时扩展或缩小其等分不变来实现的 B1和b2示意图为复合变速,b3和b4示意图为直接变速c. 主轴参数24的分解 c1直接分解可为 2×12=24; 3×8=24; 4×6=24 c2扩展倍数后分解: 如扩展5倍24×5=120那末120便可分解为20×6; 3×40; 4×30; 6×20 如扩展8倍 24×8=192那末192就分解为2×91; 91×2; 48×4; 4×48; 3×64; 64×3; 8×24; 24×8; 32×6; 6×32在扩展倍数时应将加工零件的齿数同时扩展到直至以便于分解为止;d. 演算事例分解d.1设加工零件为15齿时的计算列式:24/15同时扩展10倍后240/150;分解同时清除公倍数3得(3×80)/(3×①处装80齿数齿轮②处装50齿数齿轮d.2设加工零件为77齿时的计算列式:24/77同时扩展90倍后2160/6930;分解(40×54)/(70/99)此时可采取b.1示意图的装配齿轮,思索到齿轮时的装配方便,1和3数可任意调换,2 和4也可任意调换但1与2或4及3与2或4位置不适调换反之4与1或3及2与1或3同不克不及调换d.3设加工零件为32齿时的计算列式: 24/32 同时扩展5倍后120/160;分解为(4×30)/(4×①处装30齿轮②处装40齿轮数齿轮 d.4设加工零件为13齿时的计算列式: 24/13同时扩展100倍后2400/1300;分解力(30×80)/(20×65)此时可采取b.2示意图停止装配,注:为什么2400时分解为30×80也可分解40×60,此时应看装配后齿轮的互相吻合而定,只要好吻合即可,本齿轮齿数也可将2400分解为20×120即可同6.4的示意图装配,。
三针测中径计算公式
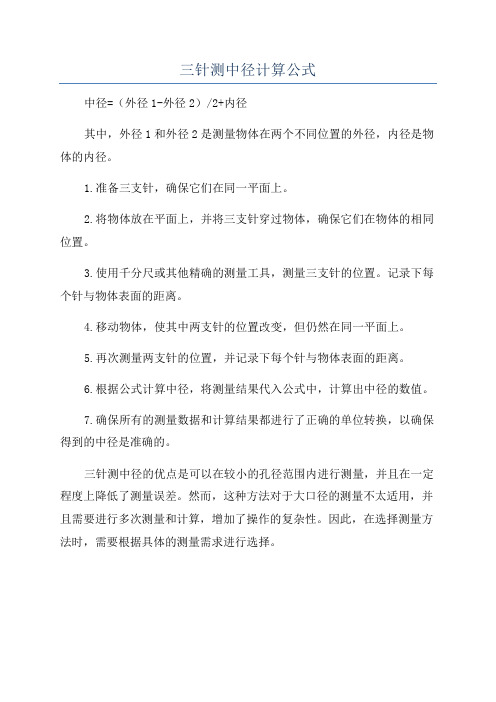
三针测中径计算公式
中径=(外径1-外径2)/2+内径
其中,外径1和外径2是测量物体在两个不同位置的外径,内径是物体的内径。
1.准备三支针,确保它们在同一平面上。
2.将物体放在平面上,并将三支针穿过物体,确保它们在物体的相同位置。
3.使用千分尺或其他精确的测量工具,测量三支针的位置。
记录下每个针与物体表面的距离。
4.移动物体,使其中两支针的位置改变,但仍然在同一平面上。
5.再次测量两支针的位置,并记录下每个针与物体表面的距离。
6.根据公式计算中径,将测量结果代入公式中,计算出中径的数值。
7.确保所有的测量数据和计算结果都进行了正确的单位转换,以确保得到的中径是准确的。
三针测中径的优点是可以在较小的孔径范围内进行测量,并且在一定程度上降低了测量误差。
然而,这种方法对于大口径的测量不太适用,并且需要进行多次测量和计算,增加了操作的复杂性。
因此,在选择测量方法时,需要根据具体的测量需求进行选择。
弯管中径曲率半径计算公式

弯管中径曲率半径计算公式弯管是一种常见的管道连接元件,用于改变管道的方向和角度。
在工程设计和制造过程中,需要对弯管的中径曲率半径进行计算,以确保管道连接的准确性和稳定性。
本文将介绍弯管中径曲率半径的计算公式及其应用。
弯管中径曲率半径是指弯管内侧曲线的曲率半径,它是弯管设计和制造的重要参数之一。
在实际工程中,弯管的中径曲率半径需要根据管道的设计要求和使用环境进行计算,以确保管道连接的牢固和稳定。
弯管中径曲率半径的计算公式如下:R = D/2 + T (T^2 + (L/2)^2)^(1/2)。
其中,R表示弯管的中径曲率半径,D表示弯管的直径,T表示弯管的壁厚,L 表示弯管的弯曲长度。
通过这个公式,可以很方便地计算出弯管的中径曲率半径,从而为弯管的设计和制造提供重要的参考数据。
在实际工程中,弯管的中径曲率半径计算公式可以应用于各种类型的管道连接设计和制造中。
例如,在石油化工、船舶、造船、航空航天等领域,都需要用到弯管连接,而弯管的中径曲率半径计算公式可以帮助工程师们准确地设计和制造弯管,确保管道连接的牢固和稳定。
此外,弯管的中径曲率半径计算公式还可以应用于管道安装和维护中。
在管道安装过程中,工程师们可以根据弯管的中径曲率半径计算公式,选择合适的弯管尺寸和材质,确保管道连接的质量和安全性。
在管道维护过程中,工程师们也可以根据这个公式,对弯管的曲率半径进行检测和评估,及时发现并解决弯管连接的问题,确保管道的正常运行。
总之,弯管中径曲率半径计算公式是管道连接设计、制造、安装和维护过程中的重要工具,它为工程师们提供了便捷和准确的计算方法,确保管道连接的质量和安全。
在未来的工程实践中,我们可以进一步完善和应用这个公式,为各种类型的管道连接提供更加可靠和高效的解决方案。
圆环中径公式

圆环中径公式好的,以下是为您生成的文章:在我们的数学世界里,有各种各样神奇的公式,就像一个个神秘的密码等待着我们去解开。
今天,咱们就来聊聊圆环中径公式这个有趣的家伙。
先来说说啥是圆环哈。
想象一下,你去游乐场玩,看到那种大大的摩天轮,那一个个的座舱就像是在一个大大的圆环上。
或者再想想你手上戴着的那种有装饰环的戒指,中间空了一块,这就是圆环啦。
圆环中径,简单来说,就是圆环中间那一圈的直径。
那怎么来计算它呢?圆环中径公式就是:中径 = (外圆直径 + 内圆直径)÷ 2 。
为了让大家更好地理解这个公式,我给大家讲一件我曾经遇到的事儿。
有一次,我带着一群小朋友去做手工,任务是用彩色纸做出圆环装饰。
小朋友们可积极啦,都想做出最漂亮的圆环。
其中有个叫小明的小朋友,特别聪明。
他拿到纸后,先量出了外面大圆的直径是 10 厘米,里面小圆的直径是 6 厘米。
可是他不知道怎么算出中间那一圈的直径,急得直挠头。
我就走过去告诉他圆环中径公式,让他把两个直径加起来除以 2 。
小明听了之后,眼睛一亮,赶紧拿起笔算了起来,(10 + 6)÷ 2 = 8 厘米。
算出结果的那一刻,他开心得跳了起来,然后按照这个中径尺寸剪出了漂亮的圆环装饰。
咱们再回到这个公式。
比如说,一个圆环,外圆的直径是20 厘米,内圆直径是 12 厘米。
那按照公式,中径就是(20 + 12)÷ 2 = 16 厘米。
是不是很简单?在实际生活中,圆环中径的计算也有很多用处呢。
比如工人师傅要做一个圆环形状的零件,就得先算出中径,才能确定尺寸,做出合适的零件。
还有啊,咱们家里的那种圆环形的灯罩,设计师在设计的时候也得用到这个公式,不然做出来的灯罩大小不合适,那可就不好看啦。
总之,圆环中径公式虽然看起来简单,但是用处可大着呢。
它就像是我们数学世界里的一把小钥匙,能帮我们打开很多有趣的问题的大门。
希望大家通过这次对圆环中径公式的了解,能更加喜欢数学,发现数学里更多的小秘密和乐趣!。
螺纹中径定义

螺纹中径定义
螺纹中径是指螺纹的内径和外径之间的平均直径。
在机械工程中,螺纹是一种常见的连接方式,它可以将两个零件牢固地连接在一起,并且能够承受一定的拉力和剪力。
而螺纹中径的定义则是在制造和加工螺纹时非常重要的一个参数。
螺纹中径的计算方法是通过螺纹的内径和外径之和除以2得到的。
由于螺纹是一种圆柱形的结构,因此螺纹的内径和外径是不同的,螺纹中径就是这两个直径的平均值。
螺纹中径的计算对于螺纹的加工和装配非常重要,因为它决定了螺纹连接的牢固程度和密封性能。
在机械设备的设计和制造过程中,螺纹连接是非常常见的。
因为螺纹连接可以方便地拆卸和装配,同时还能够保证连接的牢固性。
而螺纹中径的合理选择可以保证螺纹连接的质量,避免因为螺纹中径不合理而导致的连接松动或者漏气现象。
另外,螺纹中径的定义也是对于螺纹加工工艺的重要要求。
在螺纹加工过程中,需要根据螺纹的规格和要求来选择合适的刀具和工艺参数,以保证螺纹的质量和精度。
而螺纹中径的计算则是确定螺纹加工工艺参数的重要依据,只有在合理选择螺纹中径的情况下,才能保证螺纹的加工质量。
总之,螺纹中径的定义是在机械工程中非常重要的一个参数。
它直接影响着螺纹连接的牢固性和密封性能,同时也是螺纹加工工艺的重要依据。
在实际的机械制造和加工过程中,合理选择螺纹中径是保证螺纹连接质量的关键。
螺纹大径、中径、小径计算公式-螺栓中经计算公式
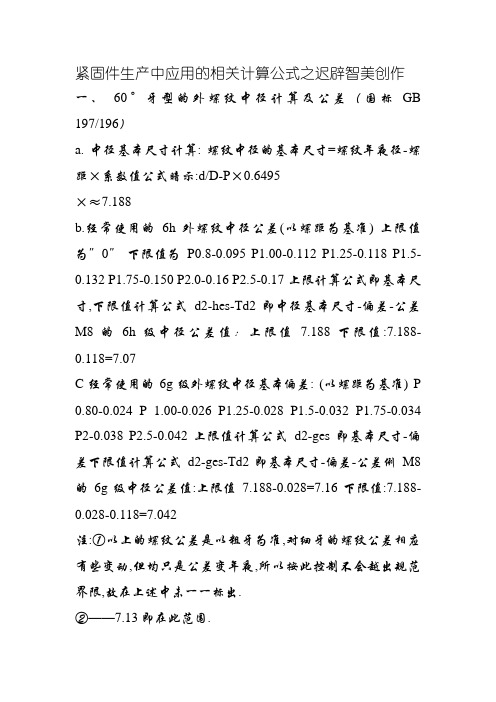
紧固件生产中应用的相关计算公式之迟辟智美创作一、60°牙型的外螺纹中径计算及公差(国标GB 197/196)a. 中径基本尺寸计算: 螺纹中径的基本尺寸=螺纹年夜径-螺距×系数值公式暗示:d/D-P×0.6495×≈7.188b.经常使用的6h外螺纹中径公差(以螺距为基准) 上限值为”0”下限值为P0.8-0.095 P1.00-0.112 P1.25-0.118 P1.5-0.132 P1.75-0.150 P2.0-0.16 P2.5-0.17 上限计算公式即基本尺寸,下限值计算公式d2-hes-Td2即中径基本尺寸-偏差-公差M8的6h级中径公差值:上限值7.188 下限值:7.188-0.118=7.07C经常使用的6g级外螺纹中径基本偏差: (以螺距为基准) P 0.80-0.024 P 1.00-0.026 P1.25-0.028 P1.5-0.032 P1.75-0.034 P2-0.038 P2.5-0.042 上限值计算公式d2-ges即基本尺寸-偏差下限值计算公式d2-ges-Td2即基本尺寸-偏差-公差例M8的6g级中径公差值:上限值7.188-0.028=7.16 下限值:7.188-0.028-0.118=7.042注:①以上的螺纹公差是以粗牙为准,对细牙的螺纹公差相应有些变动,但均只是公差变年夜,所以按此控制不会越出规范界限,故在上述中未一一标出.②——7.13即在此范围.③考虑到生产过程的需要外螺纹在实际生产的未进行热处置和概况处置的中径控制下限应尽量坚持在6h级为准二、 60°内螺纹中径计算及公差(GB 197 /196)a. 6H级螺纹中径公差(以螺距为基准) 上限值: P0.8+0.125 P1.00+0.150 P1.25+0.16 P1.5+0.180 P1.25+0.00 P2.0+0.212 P2.5+0.224 下限值为”0”, 上限值计算公式2+TD2即基本尺寸+公差例M8-6H内螺纹中径为:7.188+0.160=7.348 上限值:7.188为下限值b. 内螺纹的中径基本尺寸计算公式与外螺纹相同即D2=D-P ××系数值c. 6G级螺纹中径基本偏差E1(以螺距为基准) P0.8+0.024 P1.00+0.026 P1.25+0.028 P1.5+0.032 P1.75+0.034 P1.00+0.026 P2.5+0.042 例:M8 6G级内螺纹中径上限值:7.188+0.026+0.16=7.374 下限值:7.188+0.026=7.214 上限值公式2+GE1+TD2即中径基本尺寸+偏差+公差下限值公式2+GE1即中径尺寸+偏差三、外螺纹年夜径的计算及公差(GB 197/196)a. 外螺纹的6h年夜径上限值即螺纹直径值例M8为φ”0”b. 外螺纹的6h级年夜径下限值公差(以螺距为基准) P0.8-0.15 P1.00-0.18 P1.25-0.212 P1.5-0.236 P1.75-0.265 P2.0-0.28 P2.5-0.335 年夜径下限计算公式:d-Td 即螺纹年夜径基本尺寸-公差例:M8外螺纹6h年夜径尺寸:上限为φ8,下限为φ8-0.212=φ7.788c. 外螺纹6g级年夜径的计算与公差 6g级外螺纹的基准偏差(以螺距为基准) P0.8-0.024 P1.00-0.026 P1.25-0.028 P1.5-0.032 P1.25-0.024 P1.75 –0.034 P2.0-0.038 P2.5-0.042 上限计算公式d-ges 即螺纹年夜径基本尺寸-基准偏差下限计算公式d-ges-Td 即螺纹年夜径基本尺寸-基准偏差-公差例: M8 外螺纹6g级年夜径上限值φ8-0.028=φ7.972 下限值φ8-0.028-0.212=φ7.76注:①螺纹的年夜径是由螺纹光杆坯径及搓丝板/滚丝轮的牙型磨损水平来决定的,而且其数值在同样毛坯及螺纹加工工具的基础上与螺纹中径成反比呈现即中径小则年夜径年夜,反之中径年夜则年夜径小.②对需进行热处置和概况处置等加工的零件,考虑到加工过程的关系实际生产时应将螺纹年夜径控制在6h级的下限值加0.04mm以上,如M8的外螺纹在搓(滚)丝的年夜径应保证在φ7.83以上和7.95以下为宜.四、内螺纹小径的计算与公差a. 内螺纹小径的基本尺寸计算(D1) 螺纹小径基本尺寸=内螺纹基本尺寸-螺距××≈6.647b. 内螺纹6H级的小径公差(以螺距为基准)及小径值计算P0.8 +0. 2 P1.0 +0. 236 P1.25 +0.265 P1.5 +0.3 P1.75 +0.335P2.0 +0.375 P2.5 +0.48 内螺纹6H级的下限偏差公式D1+HE1即内螺纹小径基本尺寸+偏差注:6H级的下偏值为“0”65=6.912c. 内螺纹6G级的小径基本偏差(以螺距为基准)及小径值计算P0.8 +0.024 P1.0 +0.026 P1.25 +0.028 P1.5 +0.032 P1.75 +0.034 P2.0 +0.038 P2.5 +0.042 内螺纹6G级的小径下限值公式=D1+GE1即内螺纹基本尺寸+偏差例: 6G级M8内螺纹小径的下限值6.647+0.028=6.675 6G级M8内螺纹小径的上限值公式D1+GE1+TD1即内螺纹基本尺寸+偏差+公差例: 6G级M8内螺纹小径的上限值是6.647+0.028+0.265=6.94 注:①内螺纹的牙高直接关系到内螺纹的承载力矩的年夜小,故在毛坯生产中应尽量在其6H级上限值以内②在内螺纹的加工过程中,内螺纹小径越小会给加工具——丝锥的使用效益有所影响.从使用的角度讲是小径越小越好,但综合考虑时一般采纳小径的在中限至上限值之间,如果是铸铁或铝件时应采纳小径的下限值至中限值之间③内螺纹6G级的小径在毛坯生产中可按6H级执行,其精度品级主要考虑螺纹中径的镀层,故只在螺纹加工时考虑丝锥的中径尺寸而不用考虑光孔的小径.五、分度头单分度法计算单分度法计算公式:n=40/Z n:为分度头应转过的转数 Z:工件的等分数 40:分度头定命例:铣削六方的计算代入公式: n=40/6计算:①化简分数:找出最小约数2进行约分,即将分子分母同时除以2得20/3.分数的同时缩小其等分不变.②计算分数:此时要看分子与分母的数值而确定;如分子此分母年夜时进行计算. 20÷3=6(2/3)即n值,也即分度头应转过6(2/3)转.此时的分数已酿成带分数;带分数的整数部份6为分度头应转过6整圈.带分数的分数2/3则只能是转一圈的2/3,此时又须重新计算③分度板的选用计算:缺乏一圈的计算须借助分度头的分度板来实现.计算时第一步将分数2/3进行同时扩年夜.例:如果同时扩年夜14倍时的分数为28/42;如同时扩年夜10倍时,分数为20/30;如同时扩年夜13倍时的分数为26/39……扩年夜分门倍数的几多要根据分度板的孔数来选择.此时应注意:①选择分度板的孔数一定能被分母3整除.如前面举例中的42孔是3的14倍,30孔是3的10倍,39是3的13倍……②分数的扩年夜必需是分子分母同时扩年夜其等分不变,如举例中的28/42=2/3×14=(2×14)/(3×14);20/30=2/3×10=(2×10)/(3×10); 26/39=2/3×13=(2×13)/(3×13) 28/42分母42即采纳分度数的42孔进行分度;分子28即在上轮的定位孔上向前再转过28孔即29孔上为本轮的定位孔,20/30是在30孔分度板向前再转过10孔即11孔上为本轮的定位孔.26/39是在39孔的分度板向前再转26孔即27孔上为本轮的定位孔. 铣六方(六等分)时即可采纳42孔,30孔,39孔等被3整除的孔作为分度:其把持是手柄转整6圈后,再分别在上轮的定位孔上向前再转28+1/ 10+1 / 26+!孔的29/11/27孔上作为本轮的定位孔例2:铣 15齿的齿轮计算代入公式: n=40/15 计算 n=2(2/3) 是转2整圈再选被3整除的分度孔如24,30,39,42.51.54.57,66等孔板上再向前转过16,20,26,28,34,36,38,44加1孔即17,21,27,29,35,37,39,45孔作为本轮的定位孔.例3: 铣 82齿的分度计算代入公式: n=40/82 计算 n=20/41 即:只要选41孔的分度板,在上轮定位孔上再转过20+1即21孔作为本轮的定位孔即是例4: 铣51齿的分度计算代入公式n=40/51由于此时分数无法计算则只能直接选孔,即选51孔的分度板,在上轮定位孔上再转过51+1即52孔作为本轮的定位孔即是例5 铣100齿的分度计算代入公式n=40/100 计算n=4/10=12/30 即选30孔的分度板,在上轮定位孔上再转过12+1即13孔作为本轮的定位孔即是如所有分度板无计算所需的孔数时则应采纳复式分度法计算,不在本计算方法之列,实际生产时一般采纳滚齿,因复式分度计算后的实际把持极为方便六、圆内接六方形的计算公式:①圆D求六方对边(S面) S=0.866D 即直径×0.866(系数)②六方对边(S面)求圆(D)直径D=1.1547S 即对边×1.1547(系数)七、冷镦工序的六方对边与对角计算公式①外六角对边(S)求对角e e=1.13s 即对边×1.13②内六角对边(s)求对角(e) e=1.14s 即对边×1.14(系数)③外六角对边(s)求对角(D)的头部用料直径,应按(6.2公式)六方对边(s面)求圆(D)直径并适量加年夜其偏移中心值即D≥八、圆内接四方形的计算公式:①圆(D)求四方形对边(S面) S=0.7071D 即直径×0.7071②四方对边(S面)求圆(D) D =1.414S 即对边×1.414九、冷镦工序的四方对边与对角的计算公式①外四方对边(S)求对角(e) e=1.4s 即对边(s)×1.4参数②内四方对边(s)求对角(e) e=1.45s 即对边(s)×十、六方体体积的计算公式①×H/m/k 即对边×对边××高或厚度十一、圆台(圆锥)体的体积计算公式0.262H(D2+d2+D××高度×(年夜头直径×年夜头直径+小头直径×小头直径+年夜头直径×小头直径)×高度×高度×(半径-高度÷3)十三、内螺纹用丝锥的加工尺寸计算1.丝锥年夜径D0的计算公式D0=D+(0.866025P/8)×÷8×0.5至1.3 注:0.5至1.3的几多选择应根据螺距的年夜小来确认,螺距值越年夜则应采纳小一点系数,反之,螺距值越小而相应采纳年夜一点系数2.丝锥中径(D2)的计算公式: D2=(3×0.866025P)/8即丝锥中径=3××螺距÷83.丝锥小径(D1)的计算公式: D1=(5×0.866025P)/8即丝锥小径=5××螺距÷8十四、各种形状冷镦成型用料长度计算已知:圆的体积公式是直径×直径××长度或半径×半径××长度即d2××L 或R2××L 计算时将需要用料的体积X÷直径÷直径÷÷半径÷半径÷3.1416即为投料的长度列式=X/(3.1416R2)或X/0.7854d2 式中的X暗示需要用料体积数值L暗示实际投料的长度数值 R/d暗示实际投料的半径或直径十五、滚齿轮机滚齿轮的挂轮计算a. 滚齿轮主轴定命24b. 滚齿轮挂轮计算是依照将数据分解即同时扩年夜或缩小其等分不变来实现的B1和b2示意图为复合变速,b3和b4示意图为直接变速c. 主轴参数24的分解 c1直接分解可为 2×12=24; 3×8=24; 4×6=24 c2扩年夜倍数后分解: 如扩年夜5倍24×5=120那么120就可分解为20×6; 3×40; 4×30; 6×20 如扩年夜8倍 24×8=192那么192就分解为2×91; 91×2; 48×4; 4×48; 3×64; 64×3; 8×24; 24×8; 32×6; 6×32在扩年夜倍数时应将加工零件的齿数同时扩年夜到直至以便于分解为止;d. 演算事例分解d.1设加工零件为15齿时的计算列式:24/15同时扩年夜10倍后240/150;分解同时清除公倍数3得(3×80)/(3×①处装80齿数齿轮②处装50齿数齿轮d.2设加工零件为77齿时的计算列式:24/77同时扩年夜90倍后2160/6930;分解(40×54)/(70/99)此时可采纳b.1示意图的装配齿轮,考虑到齿轮时的装配方便,1和3数可任意调换,2 和4也可任意调换但1与2或4及3与2或4位置不适调换反之4与1或3及2与1或3同不能调换d.3设加工零件为32齿时的计算列式: 24/32 同时扩年夜5倍后120/160;分解为(4×30)/(4×①处装30齿轮②处装40齿轮数齿轮d.4设加工零件为13齿时的计算列式: 24/13同时扩年夜100倍后2400/1300;分解力(30×80)/(20×65)此时可采纳 b.2示意图进行装配,注:为什么2400时分解为30×80也可分解40×60,此时应看装配后齿轮的互相吻合而定,只要好吻合即可,本齿轮齿数也可将2400分解为20×120即可同6.4的示意图装配,。