含缺陷压力管道的安全评定
压力管道的无损检测技术
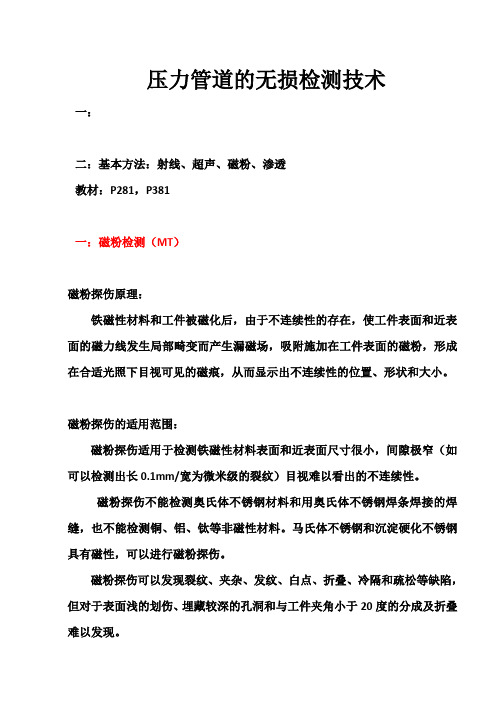
压力管道的无损检测技术一:二:基本方法:射线、超声、磁粉、渗透教材:P281,P381一:磁粉检测(MT)磁粉探伤原理:铁磁性材料和工件被磁化后,由于不连续性的存在,使工件表面和近表面的磁力线发生局部畸变而产生漏磁场,吸附施加在工件表面的磁粉,形成在合适光照下目视可见的磁痕,从而显示出不连续性的位置、形状和大小。
磁粉探伤的适用范围:磁粉探伤适用于检测铁磁性材料表面和近表面尺寸很小,间隙极窄(如可以检测出长0.1mm/宽为微米级的裂纹)目视难以看出的不连续性。
磁粉探伤不能检测奥氏体不锈钢材料和用奥氏体不锈钢焊条焊接的焊缝,也不能检测铜、铝、钛等非磁性材料。
马氏体不锈钢和沉淀硬化不锈钢具有磁性,可以进行磁粉探伤。
磁粉探伤可以发现裂纹、夹杂、发纹、白点、折叠、冷隔和疏松等缺陷,但对于表面浅的划伤、埋藏较深的孔洞和与工件夹角小于20度的分成及折叠难以发现。
磁粉探伤的基本操作步骤:1:预处理;2:磁化被检工件表面;3:施加磁粉和磁悬液;4:在合适的光照下观察和评定磁痕;5:退磁;6:后处理:思考题:1:叙述磁粉探伤的原理和适用范围。
2:写出磁粉探伤的基本操作步骤。
二:渗透探伤(PT)渗透探伤原理:渗透探伤是基于液体的毛细管作用(或毛细管现象)和固体染料在一定条件下的发光现象。
渗透探伤的工作原理是:被检工件在被施涂含有荧光染料或着色染料的渗透液后,在毛细管作用下,经过一定时间的渗透,渗透液可以渗进表面开口的缺陷中;经过去除被检工件表面多余的渗透液和干燥后,再在被检工件表面施涂吸附介质——显象剂;同样,在毛细管作用下,显象剂将吸附缺陷中的渗透液,使渗透液回渗到显象剂中;在一定光源下(黑光或白光),缺陷处之渗透液痕迹被显示(黄绿色荧光或鲜艳红色),从而检测处缺陷的形貌及分布状态。
渗透探伤可以检查金属和非金属材料的表面开口缺陷,例如:裂纹、疏松、气孔、夹渣、冷隔、折叠和氧化斑疤等。
这些表面开口缺陷,特别是细微的表面开口缺陷,一般情况下,目视检查难以发现。
压力管道焊接常见缺陷成因分析与预防措施
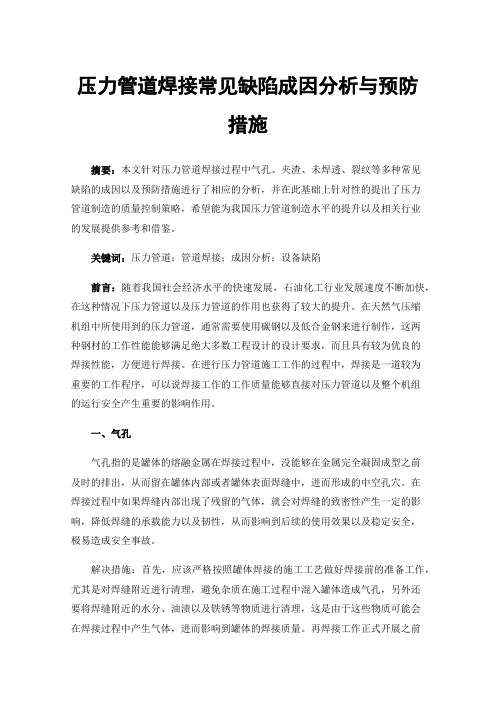
压力管道焊接常见缺陷成因分析与预防措施摘要:本文针对压力管道焊接过程中气孔、夹渣、未焊透、裂纹等多种常见缺陷的成因以及预防措施进行了相应的分析,并在此基础上针对性的提出了压力管道制造的质量控制策略,希望能为我国压力管道制造水平的提升以及相关行业的发展提供参考和借鉴。
关键词:压力管道;管道焊接;成因分析;设备缺陷前言:随着我国社会经济水平的快速发展,石油化工行业发展速度不断加快,在这种情况下压力管道以及压力管道的作用也获得了较大的提升。
在天然气压缩机组中所使用到的压力管道,通常需要使用碳钢以及低合金钢来进行制作,这两种钢材的工作性能能够满足绝大多数工程设计的设计要求,而且具有较为优良的焊接性能,方便进行焊接。
在进行压力管道施工工作的过程中,焊接是一道较为重要的工作程序,可以说焊接工作的工作质量能够直接对压力管道以及整个机组的运行安全产生重要的影响作用。
一、气孔气孔指的是罐体的熔融金属在焊接过程中,没能够在金属完全凝固成型之前及时的排出,从而留在罐体内部或者罐体表面焊缝中,进而形成的中空孔穴。
在焊接过程中如果焊缝内部出现了残留的气体,就会对焊缝的致密性产生一定的影响,降低焊缝的承载能力以及韧性,从而影响到后续的使用效果以及稳定安全,极易造成安全事故。
解决措施:首先,应该严格按照罐体焊接的施工工艺做好焊接前的准备工作,尤其是对焊缝附近进行清理,避免杂质在施工过程中混入罐体造成气孔,另外还要将焊缝附近的水分、油渍以及铁锈等物质进行清理,这是由于这些物质可能会在焊接过程中产生气体,进而影响到罐体的焊接质量。
再焊接工作正式开展之前还应该对准备好的焊条、焊剂等物品进行整理,确保其干燥无水分,并在焊接之前进行预热,减少施工过程中温度的变化速度,为气体排放留出预留空间和时间。
其次,在焊接过程中也应该多加注意,主要表现在四个方面。
首先是对电弧长度的控制,焊接工作人员在对罐体进行焊接的过程中应该尽可能地保持短弧操作,并且根据具体情况进行电弧长度的具体控制;其次,在进行焊条电弧焊的过程中,应该对焊接电流进行相应的控制,尽可能将电流大小控制在合理的区间范围之内,避免由于电流过大导致焊条的温度在短时间内迅速升高,进而导致药皮失去防护作用,而且在这个过程中还应该尽量避免产生磁偏吹现象;再次,还应该在使用气体保护焊技术的过程中,对气体流量进行控制;最后,在进行埋弧焊操作的过程中,应该对干伸长进行合理的选择和控制,并调节焊剂层的厚度,从而能够很好的减少气孔的出现。
TSG D7005-2018 压力管道定期检验规则—工业管道

前言2008年2月,国家质量监督检验检疫总局(以下简称国家质检总局)特种设备安全监察局(以下简称特种设备局)下达了在《在用工业管道定期检验规程(试行 )》(国质检锅【2003 ] 108号)基础上,制定《压力管道定期检验规则一一工业管道》的任务书。
2010年7月,中国特种设备检测研究院组织有关专家成立修订工作组,在南京召开第一次会议,讨论修订原则、重点内容以及主要问题,并就修订工作进行了具体分工,制定了修订工作时间表。
2013年8月,工作组在北京召开第二次会议,经过讨论,形成征求意见稿。
2014年7月,特种设备局以质检特末【2014 ] 21号文向有关部门、有关单位、专家及公民征求意见。
2015年8月,工作组召开第三次会议,对征求到的意见进行研究讨论,形成送审稿。
2015年10月,提交国家质检总局特种设备安全与节能技术委员会审议。
2018年1月26日,由国家质检总局批准颁布。
本次修订工作的基本原则与《4中华人民共和国特种设备安全法兴特种设备目录》《压力管道安全技术监察规程一一工业管道》(TSG D0001)一致。
根据实际使用情况以及行业发展,调整、完善不适用的内容,明确定期检验的性质、定位及检验周期的含义,统一检验结论及检验报告内容;在保证基本安全要求的基础上,建立基于损伤模式制定针对性检验方案的思想,突出检验项目的针对性、有效性和科学性;为新检验、检测技术和评定方法的应用给出渠道 ;吸纳基于风险的检验等成熟的科技成果,厘清与常规检验方法的关系; 落实企业安全主体责任,为企业安全与发展服务。
参加本规则修订工作的主要单位和人员如下:中国特种设备检测研究院谢国山”修长征”李光海乔涛史进国家质检总局特种设备局秦先勇合肥通用机械研究院王冰胡明东北京市质量技术监督局由涛上上海市质量技术监督局王善江南京市质量技术监督局染华上海市特种设备监督检验技术研究院罗晓明吉林市特种设备检验中心胡宝林中科(广东)炼化有限公司王光中国石油天然气股份有限公司独山子石化分公司”杨瑞平中国石油化工股份有限公司天津分公司装备研究院李春树目录1总则2 “定期检验( 4)3 ”安全状况等级评定.(11)4定期检验记录、报告及结论 (16)S 附则17)附件A,工业管道年度检查要求《18)附录a工业管道年度检查报告(23)附件B工业管道定期检验报告26)附件C特种设备定期检验意见通知书(30)压力管道定期检验规则一一工业管道1总则目的为规范在用工业管道定期检验工作,根据《中华人民共和国特种设备安全法》《特种设备目》及相关安全技术规范规定,制定本规则。
环焊缝含错边缺陷压力管道的极限载荷分析
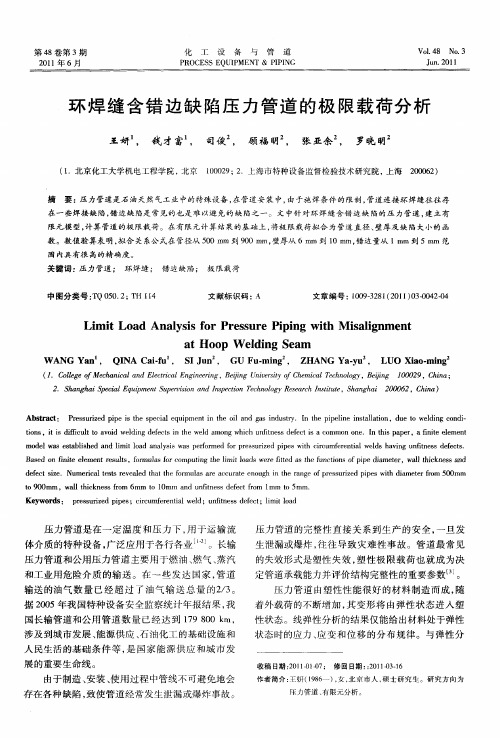
展 的重要生命 线 。 由于制造 、 安装 、 使用过 程 中管线不 可避免地会
存 在各 种缺 陷 , 致使 管道经 常发 生泄漏或爆 炸事 故 。
收 稿 日期 :0 10 4 2 1.1) 7; 修 回 日期 :2 1 431 :0 1 —6 )
作 者 简 介 : 妍 ( 96 ) 女 , 京 市 人 , 士 研 究 生 。 研 究 方 向为 王 18 一 , 北 硕
压力管道 的完整 性直 接关 系到生 产 的安 全 , 一旦 发
生泄漏或爆 炸 , 往 导致 灾 难性 事故 。管 道最 常 见 往
体介质 的特种 设备 , 泛应 用于各 行各业 ¨ 。长输 广
压 力管道 和公用 压力 管道 主要 用 于燃 油 、 气 、 燃 蒸汽 和工 业用 危险 介质 的输 送 。在一 些 发达 国家 , 管道
数 。数值验算表 明, 拟合关 系公 式在 管径从 5 0m 0 m到 90m 壁厚从 6m 0 m, m到 1 错边量从 lm 0mm, m到 5m m范
围 内具 有很 高 的精 确 度 。 关 键 词 :压 力 管道 ; 环 焊缝 ; 错 边 缺 陷 ; 极 限栽 荷
中 图分 类号 :Q0 0 2 T I T 5 . ; H I4
在本 文 研究 中 , 两 管道 的两端 面都施 加 了轴 对
向位 移约 束 , 中对 一 端 面 上 的所 有 节 点还 施 加 了 其 周 向位移 约束 。 管道有 限元模 型如 图 2所示 。
陷 的环 焊缝 接头处 的性 能对 整条 管线 的使 用寿 命及 安 全 可靠性起 着 至关重 要 的作用 。
输送 的油 气 数 量 已经 超 过 了油 气 输 送 总 量 的 2 3 /。
压力管道定期检验-无损检测
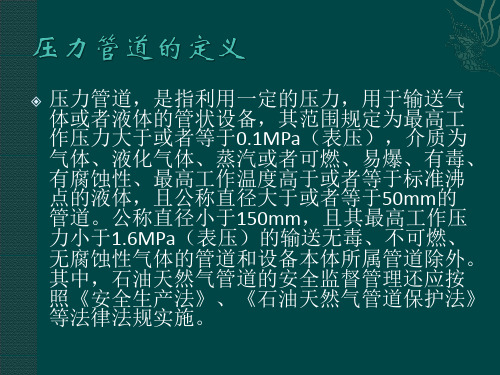
(2)在实际工况下,材料韧性良好,并且未出现材料 性能劣化以及劣化趋向;
(3)壁厚局部减薄以及其附近无其他表面缺陷或者埋 藏缺陷;
(4)壁厚局部减薄处剩余壁厚大于2mm; (5)管道不承受疲劳载荷。
5、其他 一)RT检测时必须放置对比试块; 二)对比试块的高度需和需要和评级时需要对比
3、扩拍要求
抽查发现安全状况等级3级或者4级的缺 陷,应当增加抽查比例,增加的抽查比例 由检验人员与使用单位结合管道运行参数 和实际情况进行协商确定。
注:对于3级的缺陷尽量进行返修,否则下 次检验周期不一致,会增加企业定检压力。
4、缺陷描述
(一)咬边
GC1咬边深度不超过0.5mm,GC2、GC3咬边 深度不超过0.8mm,不影响定级,否则,应打磨 消除,并且按照局部减薄评级。(咬边缺陷描述: 深度,长度(打磨消除))
(五)未熔合
GC1级管道的单个焊接接头未熔合总长度不大
于焊接接头长度的50%时,按照表4-4定级,否则 定为4级;GC2级、GC3级管道未熔合的长度不限, 按照表4-4定级。 (未熔合缺陷描述:长度,自身 高度)
有效厚度
安全状况等级
压力管道的检验检测技术
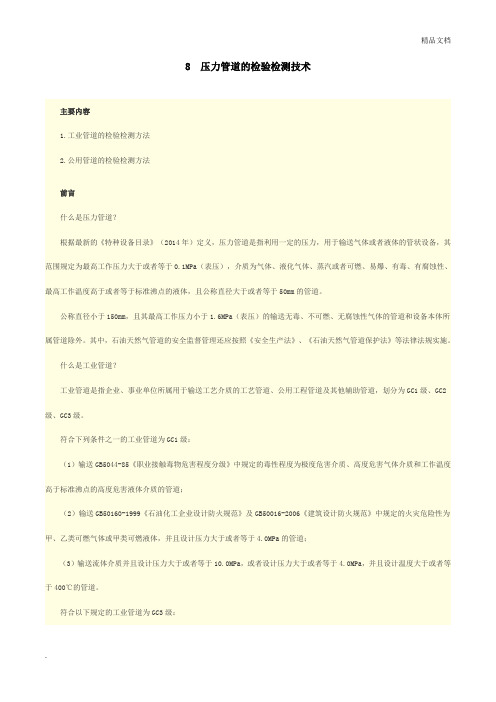
8 压力管道的检验检测技术主要内容1.工业管道的检验检测方法2.公用管道的检验检测方法前言什么是压力管道?根据最新的《特种设备目录》(2014年)定义,压力管道是指利用一定的压力,用于输送气体或者液体的管状设备,其范围规定为最高工作压力大于或者等于0.1MPa(表压),介质为气体、液化气体、蒸汽或者可燃、易爆、有毒、有腐蚀性、最高工作温度高于或者等于标准沸点的液体,且公称直径大于或者等于50mm的管道。
公称直径小于150mm,且其最高工作压力小于1.6MPa(表压)的输送无毒、不可燃、无腐蚀性气体的管道和设备本体所属管道除外。
其中,石油天然气管道的安全监督管理还应按照《安全生产法》、《石油天然气管道保护法》等法律法规实施。
什么是工业管道?工业管道是指企业、事业单位所属用于输送工艺介质的工艺管道、公用工程管道及其他辅助管道,划分为GC1级、GC2级、GC3级。
符合下列条件之一的工业管道为GC1级:(1)输送GB5044-85《职业接触毒物危害程度分级》中规定的毒性程度为极度危害介质、高度危害气体介质和工作温度高于标准沸点的高度危害液体介质的管道;(2)输送GB50160-1999《石油化工企业设计防火规范》及GB50016-2006《建筑设计防火规范》中规定的火灾危险性为甲、乙类可燃气体或甲类可燃液体,并且设计压力大于或者等于4.0MPa的管道;(3)输送流体介质并且设计压力大于或者等于10.0MPa,或者设计压力大于或者等于4.0MPa,并且设计温度大于或者等于400℃的管道。
符合以下规定的工业管道为GC3级:输送无毒、非可燃液体介质,设计压力小于或者等于1.0MPa,并且设计温度大于-20℃但是小于185℃的管道。
其余为GC2工业管道。
--1.工业管道的检验检测方法>>1.1.压力管道常见的缺陷>>1.2.检验检测方法>>1.3.工业管道的定期检验1.1.压力管道常见的缺陷(1)制造安装过程中产生的缺陷压力管道在制造安装的过程产生的缺陷包括管道材料冶炼、轧制、机加工、焊接、热处理等过程中产生的缺陷。
TSG D7005-2018压力管道定期检验规则-工业管道

TSG特种设备安全技术规范TSG D7005—2018压力管道定期检验规则——工业管道Periodic Inspection Regulation for Industrial Pressure Piping中华人民共和国国家质量监督检验检疫总局颁布2018年1月26日前 言2008年2月,国家质量监督检验检疫总局(以下简称国家质检总局)特种设备安全监察局(以下简称特种设备局)下达了在《在用工业管道定期检验规程(试行)》(国质检锅〔2003〕108号)基础上,制定《压力管道定期检验规则——工业管道》的任务书。
2010年7月,中国特种设备检测研究院组织有关专家成立修订工作组,在南京召开第一次会议,讨论修订原则、重点内容以及主要问题,并就修订工作进行了具体分工,制定了修订工作时间表。
2013年8月,工作组在北京召开第二次会议,经过讨论,形成征求意见稿。
2014年7月,特种设备局以质检特函〔2014〕21号文向有关部门、有关单位、专家及公民征求意见。
2015年8月,工作组召开第三次会议,对征求到的意见进行研究讨论,形成送审稿。
2015年10月,提交国家质检总局特种设备安全与节能技术委员会审议。
2018年1月26日,由国家质检总局批准颁布。
本次修订工作的基本原则与《中华人民共和国特种设备安全法》《特种设备目录》《压力管道安全技术监察规程——工业管道》(TSG D0001)一致。
根据实际使用情况以及行业发展,调整、完善不适用的内容,明确定期检验的性质、定位及检验周期的含义,统一检验结论及检验报告内容;在保证基本安全要求的基础上,建立基于损伤模式制定针对性检验方案的思想,突出检验项目的针对性、有效性和科学性;为新检验、检测技术和评定方法的应用给出渠道;吸纳基于风险的检验等成熟的科技成果,厘清与常规检验方法的关系;落实企业安全主体责任,为企业安全与发展服务。
参加本规则修订工作的主要单位和人员如下: 中国特种设备检测研究院 谢国山 修长征 李光海孟 涛 史 进 国家质检总局特种设备局 秦先勇 合肥通用机械研究院 王 冰 胡明东北京市质量技术监督局 由 涛 上海市质量技术监督局 王善江 南京市质量技术监督局梁 华 上海市特种设备监督检验技术研究院 罗晓明 吉林市特种设备检验中心 胡宝林 中科(广东)炼化有限公司王 光 中国石油天然气股份有限公司独山子石化分公司杨瑞平中国石油化工股份有限公司天津分公司装备研究院 李春树国家质量监督检验检疫总局 h t t p ://w w w .a q s i q .g o v .c n /目 录1 总则 .................................................................................................................................. (1) 2 定期检验 .......................................................................................................................... (4) 3 安全状况等级评定 ........................................................................................................ (11) 4 定期检验记录、报告及结论 ........................................................................................ (16) 5 附则 .. (17)附件A 工业管道年度检查要求 (18)附录a 工业管道年度检查报告 ............................................................................... (23) 附件B 工业管道定期检验报告 ...................................................................................... (26) 附件C 特种设备定期检验意见通知书 .. (30)国家质量监督检验检疫总局 h t t p ://w w w .a q s i q .g o v .c n /— 1 —压力管道定期检验规则——工业管道1 总 则1.1 目的为规范在用工业管道定期检验工作,根据《中华人民共和国特种设备安全法》 《特种设备目录》以及相关安全技术规范规定,制定本规则。
在用压力管道检测规定

在用工业管道定期检验规程第一章总则第一条为了加强压力管道安全监察,规范在用工业管道检验工作,确保在用工业管道的安全运行,保障公民生命和财产的安全,根据压力管道安全管理与监察规定的有关规定,制定本规程;第二条本规程是在用工业管道检验、安全状况等级划分方法见附件一评定和缺陷处理的基本要求,有关单位制定的实施细则,应满足本规程的要求;第三条本规程适用于压力管道安全管理与监察规定适用范围的在用工业管道及附属设施,但不包括下列管道:一公称直径≤25mm的管道;二非金属管道;三最高工作压力>42MPa或<的管道;第四条本规程适用范围内的在用工业管道的级别划分如下:一符合下列条件之一的工业管道为GCl级:1.输送现行国家标准职业接触毒物危害程度分级GB5044中规定的毒性程度为极度危害介质的管道;2.输送现行国家标准石油化工企业设计防火规范GB50160及建筑防火规范GBJ l6中规定的火灾危险性为甲、乙类可燃气体或甲类可燃液体,并且设计压力≥的管道;3.输送可燃流体介质、有毒流体介质,设计压力≥,并且设计温度≥400℃的管道;4.输送流体介质并且设计压力≥的管道;二符合下列条件之一的工业管道为GC2级:1.输送现行国家标准石油化工企业设计防火规范GB50160及建筑防火规范GBJ16中规定的火灾危险性为甲、乙类可燃气体或甲类可燃液体,并且设计压力<4.0MPa的管道;2.输送可燃流体介质、有毒流体介质,设计压力<4.0MPa,并且设计温度≥400℃的管道;3.输送非可燃流体介质、无毒流体介质,设计压力<10.OMPa,并且设计温度≥400℃的管道;4. 输送流体介质,设计压力<lO.OMPa,并且设计温度<400℃的管道;三符合下列条件之一的GC2级工业管道划分为GC3级:1.输送可燃流体介质、有毒流体介质,设计压力<1.OMPa,并且设计温度<400℃的管道;2.输送非可燃流体介质、无毒流体介质,设计压力<4.0MPa并且设计温度<400℃的管道;其中穿跨越铁路干线、重要桥梁、住宅及工厂重要设施的输送火灾危险性为甲、乙类介质或毒性程度为中度危害以上介质的GC2、GC3级工业管道,其穿跨越部分按GCl级管道的检验要求进行检验;第五条在用工业管道定期检验分为在线检验和全面检验;第六条从事在用工业管道检验的单位和检验人员,应履行以下义务:一应在认可的资格范围内从事压力管道的检验工作; 二接受质量技术监督部门的监督检查和业务指导; 三保证检验质量,并对检验的结果负责;第二章在线检验第一节一般规定第七条在线检验是在运行条件下对在用工业管道进行的检验,在线检验每年至少一次;第八条在线检验工作由使用单位进行,使用单位也可将在线检验工作委托给具有压力管道检验资格的单位;使用单位应制定在线检验管理制度,从事在线检验工作的检验人员须经专业培训,并报省级或其授权的地市级质量技术监督部门备案;使用单位根据具体情况制定检验计划和方案,安排检验工作;第九条在线检验一般以宏观检查和安全保护装置检验为主,必要时进行测厚检查和电阻值测量;管道的下述部位一般为重点检查部位:一压缩机、泵的出口部位;二补偿器、三通、弯头弯管、大小头、支管连接及介质流动的死角等部位;三支吊架损坏部位附近的管道组成件以及焊接接头;四曾经出现过影响管道安全运行的问题的部位;五处于生产流程要害部位的管段以及与重要装置或设备相连接的管段;六工作条件苛刻及承受交变载荷的管段;第十条本章所规定的在线检验项目是在线检验的一般要求,检验人员可根据实际情况确定实际检验项目和内容,并进行检验工作;第二节检验项目及要求第十一条在线检验的一般程序见图1;第十二条在线检验开始前,使用单位应准备好与检验有关的管道平面布置图、管道工艺流程图、单线图、历次在线检验及全面检验报告、运行参数等技术资料,检验人员应在了解这些资料的基础上对管道运行记录、开停车记录、管道隐患监护措施实施情况记录、管道改造施工记录、检修报告、管道故障处理记录等进行检查,并根据实际情况制定检验方案;│││┌------------------------------------------------------------------------------┐┌—┈---┬----—-┬---┈-┬┈—----┬——--┈┬┈--┈┬------┬┈-—-┐┌—----—┼——----┐││图1 在线检验的一般程序第十三条宏观检查的主要检查项目和内容如下:一泄露检查主要检查管子及其他组成件泄漏情况;二绝热层、防腐层检查主要检查管道绝热层有无破损、脱落、跑冷等情况;防腐层是否完好; 三振动检查主要检查管道有无异常振动情况;四位置与变形检查1、管道位置是否符合安全技术规范和现行国家标准的要求;2.管道与管道、管道与相邻设备之间有无相互碰撞及摩擦情况;3.管道是否存在挠曲、下沉以及异常变形等;五支吊架检查1.支吊架是否脱落、变形、腐蚀损坏或焊接接头开裂;2.支架与管道接触处有无积水现象;3.恒力弹簧支吊架转体位移指示是否越限;4.变力弹簧支吊架是否异常变形、偏斜或失载;5.刚性支吊架状态是否异常;6.吊杆及连接配件是否损坏或异常;7.转导向支架间隙是否合适,有无卡涩现象;8.阻尼器、减振器位移是否异常,液压阻尼器液位是否正常;9.承载结构与支撑辅助钢结构是否明显变形,主要受力焊接接头是否有宏观裂纹;六阀门检查1.阀门表面是否存在腐蚀现象;2.阀体表面是否有裂纹、严重缩孔等缺陷;3.阀门连接螺栓是否松动;4.阀门操作是否灵活;七法兰检查1.法兰是否偏口,紧固件是否齐全并符合要求,有无松动和腐蚀现象;2. 法兰面是否发生异常翘曲、变形;八膨胀节检查1.波纹管膨胀节表面有无划痕、凹痕、腐蚀穿孔、开裂等现象;2.波纹管波间距是否正常、有无失稳现象;3.铰链型膨胀节的铰链、销轴有无变形、脱落等损坏现象;4.拉杆式膨胀节的拉杆、螺栓、连接支座有无异常现象;九阴极保护装置检查对有阴极保护装置的管道应检查其保护装置是否完好;十蠕胀测点检查对有蠕胀测点的管道应检查其蠕胀测点是否完好;十一管道标识检查检查管道标识是否符合现行国家标准的规定;十二检验员认为有必要的其他检查;第十四条对需重点管理的管道或有明显腐蚀和冲刷减薄的弯头、三通、管径突变部位及相邻直管部位应采取定点测厚或抽查的方式进行壁厚测定;第十五条对输送易燃、易爆介质的管道采取抽查的方式进行防静电接地电阻和法兰间的接触电阻值的测定;管道对地电阻不得大于100Ω,法兰间的接触电阻值应小于Ω;第十六条安全保护装置检验按本规程第五章的相关要求进行;第三节检验报告及问题处理第十七条在线检验的现场检验工作结束后,检验人员应根据检验情况,按照附件二在用工业管道在线检验报告书的规定,认真、准确填写在线检验报告;检验结论分为:可以使用、监控使用、停止使用;在线检验报告由使用单位存挡,以便备查;第十八条在线检验发现管道存在异常情况和问题时,使用单位应认真分析原因,及时采取整改措施;重大安全隐患应报省级质量技术监督部门安全监察机构或经授权的地市级质量技术监督部门安全监察机构备案;第三章全面检验第一节一般规定第十九条全面检验是按一定的检验周期在在用工业管道停车期间进行的较为全面的检验;安全状况等级为1级和2级的在用工业管道,其检验周期一般不超过6年;安全状况等级为3级的在用工业管道,其检验周期一般不超过3年;管道检验周期可根据下述情况适当延长或缩短;一经使用经验和检验证明可以超出上述规定期限安全运行的管道,使用单位向省级或其委托的地市级质量技术监督部门安全监察机构提出申请,经受理申请的安全监察机构委托的检验单位确认,检验周期可适当延长,但最长不得超过9年;二属于下列情况之一的管道,应适当缩短检验周期:1.新投用的管道首次检验周期;2.发现应力腐蚀或严重局部腐蚀的管道;3.承受交变载荷,,可能导致疲劳失效的管道;4.材料产生劣化的管道;5.在线检验中发现存在严重问题的管道;6.检验人员和使用单位认为应该缩短检验周期的管道;第二十条在用工业管道全面检验工作由已经获得质量技术监督部门资格认可的检验单位进行取得在用压力管道自检资格的使用单位可以检验本单位自有的在用压力管道,下同;从事全面检验工作的检验人员应按锅炉压力容器压力管道及特种设备检验人员资格考核规则的要求经考核合格,取得相应的检验人员资格证书具备全面检验人员资格即具备在线检验人员资格;检验单位和检验人员应做好检验的安全防护工作,严格遵守使用单位的安全生产制度;第二十一条使用单位负责制定在用工业管道全面检验计划,安排全面检验工作,按时向负责对其发放压力管道使用登记证的安全监察机构或其委托的检验单位申报全面检验计划和向检验单位申报全面检验;使用单位应进行全面检验的现场准备工作,确保所提供检验的管道处于适宜的待检验状态;提供安全的检验环境,负责检验所必需的辅助工作如拆除保温、搭脚手架、打磨除锈、配起重设置、提供检验用电、水、气等,并协助检验单位进行全面检验工作;第二十二条本章所规定的全面检验项目是全面检验的一般要求,检验人员可根据实际情况确定实际检验项目和内容,进行检验工作;第二节检验项目及要求第二十三条全面检验的一般程序见图2;│││││第二十四条检验单位和检验人员在检验前应做好资料审查和制定检验方案等检验准备工作,并达到以下要求:一对以下资料和资格证明进行审查:1、压力管道设计单位资格、设计图纸、安装施工图及有关计算书等;2、压力管道安装单位资格、竣工验收资料含安装竣工资料、材料检验等;3、管道组成件、管道支承件的质量证明文件;4、在线检验要求检查的各种记录;5、该检验周期内的历次在线检验报告;6、检验人员认为检验所需要的其他资料;二检验单位和检验人员应根据资料审查情况制定检验方案,并在检验前与使用单位落实检验方案;第二十五条检验中的安全事项应达到以下要求:一影响管道全面检验的附设部件或其他物体,应按检验要求进行清理或拆除;二为检验而搭设的脚手架、轻便梯等设施,必须安全牢固,便于进行检验和检测工作;三高温或低温条件下运行的压力管道,应按照操作规程的要求缓慢地降温或升温,防止造成损伤;四检验前,必须切断与管道或相邻设备有关的电源,拆除保险丝,并设置明显的安全标志;五如需现场射线检验时,应隔离出透照区,设置安全标志;六全面检验时,应符合下列条件:1.将管道内部介质排除干净,用盲板隔断所有液体、气体或蒸汽的来源,设置明显的隔离标志;2.对输送易燃、助燃、毒性或窒息性介质的管道,应进行置换、中和、消毒,清洗;对于输送易燃介质的管道,严禁用空气置换;3.进入管道内部检验所用的灯具和工具的电源电压应符合现行国家标准安全电压GB3805的规定;检验用的设备和器具,应在有效的检定期内,经检查和校验合格后方可使用;第二十六条无绝热层的非埋地管道一般应对整条管线进行外部宏观检查;有绝热层的非埋地管道应按一定的比例进行抽查;埋地敷设的管道应选择易发生损坏部位开挖抽查如有证据表明防腐情况良好,可免于开挖抽查;抽查的比例由检验人员和使用单位结合管道运行经验协商确定;外部宏观检查的项目和要求如下:一在线检验的宏观检查所包括的相关项目及要求;二管道结构检查:1.支吊架的间距是否合理;2.对有柔性设计要求的管道,管道固定点或固定支吊架之间是否采用自然补偿或其它类型的补偿器结构;三检查管道组成件有无损坏,有无变形,表面有无裂纹、皱褶、重皮、碰伤等缺陷;四检查焊接接头包括热影响区是否存在宏观的表面裂纹;五检查焊接接头的咬边和错边量;六检查管道是否存在明显的腐蚀,管道与管架接触处等部位有无局部腐蚀;第二十七条管道材料的种类和牌号一般应查明,材质不明的,可根据具体情况,采用化学分析、光谱分析等方法予以确定;第二十八条对管道进行剩余厚度的抽查测定,一般采用超声波测厚的方法,测厚的位置应在单线图上标明;一弯头、三通和直径突变处的抽查比例见表1,对于上述被抽查的每个管件,测厚位置不得少于3处;上述被抽查管件与直管段相连的焊接接头的直管段一侧应进行厚度测量,测厚位置不得少于3处;检验人员认为必要时,对其余直管段进行厚度抽查;二发现管道壁厚有异常情况时,应在附近增加测点,并确定异常区域大小,必要时,可适当提高整条管线的厚度抽查比例;表1弯头、三通和直径突变处测厚抽查比例注:不锈钢管道、介质无腐蚀性的管道可适当减少测厚抽查比例;第二十九条表面无损检测:一宏观检查中发现裂纹或可疑情况的管道,应在相应部位进行表面无损检测;二绝热层破损或可能渗入雨水的奥氏体不锈钢管道,应在相应部位进行外表面渗透检测;三处于应力腐蚀环境中的管道,应进行表面无损检测抽查;四长期承受明显交变载荷的管道,应在焊接接头和容易造成应力集中的部位进行表面无损检测;五检验人员认为有必要时,应对支管角焊缝等部位进行表面无损检测抽查;第三十条GC1、GC2级管道的焊接接头一般应进行超声波或射线检测抽查; GC3级管道如未发现异常情况,一般不进行其焊接接头的超声波或射线检测抽查;超声波或射线检测抽查的比例与重点检测部位按下述原则确定:一GC1、GC2级管道焊接接头的超声波或射线检测抽查比例见表2;表2管道焊接接头超声波或射线检测抽查比例注:1.温度、压力循环变化和振动较大的管道的抽查比例应为表中数值的2倍;2.耐热钢管道的抽查比例应为表中数值的2倍;3.抽查的焊接接头进行全长度无损检测;抽查时若发现安全状况等级3级或4级的缺陷,应增加检查比例,增加量由检验人员与使用单位结合管道运行参数和运行经验协商确定;二抽查的部位应从下述重点检查部位中选定:1.制造、安装中返修过的焊接接头和安装时固定口的焊接接头;2.错边、咬边严重超标的焊接接头;3.表面检测发现裂纹的焊接接头;4.泵、压缩机进出口第一道焊接接头或相近的焊接接头;5.支吊架损坏部位附近的管道焊接接头;6.异种钢焊接接头;7.硬度检验中发现的硬度异常的焊接接头;8.使用中发生泄漏的部位附近的焊接接头;9.检验人员和使用单位认为需要抽查的其他焊接接头;当重点检查部位确需进行无损检测抽查,而表2所规定的抽查比例不能适应检查需要时,检验人员应与使用单位协商确定具体抽查比例;第三十一条下列管道一般应选择有代表性的部位进行金相和硬度检验抽查;一工作温度大于370℃的碳素钢和铁素体不锈钢管道;二工作温度大于450℃的钼钢和铬钼钢管道;三工作温度大于430℃的低合金钢和奥氏体不锈钢管道;四工作温度大于220℃的输送临氢介质的碳钢和低合金钢管道;第三十二条对于工作介质含湿HS或介质可能引起应力腐蚀的碳钢和低合金2钢管道,一般应选择有代表性的部位进行硬度检验;当焊接接头的硬度值超过HB200时,检验人员视具体情况扩大焊接接头内外部无损检测抽查比例;第三十三条对于使用寿命接近或已经超过设计寿命的管道,检验时应进行金相检验或硬度检验,必要时应取样进行力学性能试验或化学成分分析;第三十四条按本规程第五章的相关要求进行安全保护装置检验;第三十五条耐压强度校验和应力分析:一耐压强度校验管道的全面减薄量超过公称厚度的10%时应进行耐压强度校验;耐压强度校验参照现行国家标准工业金属管道设计规范GB50316的相关要求进行;二管道应力分析检验人员和使用单位认为必要时,对下列情况之一者,应进行管系应力分析;1.无强度计算书,并且t0≥D/6或P/σt>的管道;其中t0为管道设计壁厚mm,D为管道设计外径mm,P为设计压力MPa,σt为设计温度下材料的许用应力MPa;2.存在下列情况之一的管道:有较大变形、挠曲;法兰经常性泄漏、破坏;管段应设而未设置补偿器或补偿器失效;支吊架异常损坏;严重的全面减薄;第三节压力试验第三十六条在用工业管道应按一定的时间间隔进行压力试验,具体要求如下:一经全面检验的管道一般应进行压力试验;二管道有下列情况之一时,应进行压力试验:1.经重大修理改造的;2.使用条件变更的;3.停用2年以上重新投用的;对因使用条件变更而进行压力试验的管道,在压力试验前应经强度校核合格;三本条二款所述的管道,如果现场条件不允许使用液体或气体进行压力试验,经使用单位和检验单位同意,可同时采用下列方法代替:1.所有焊接接头和角焊缝包括附着件上的焊接接头和角焊缝,用液体渗透法或磁粉法进行表面无损检测;2.焊接接头用100%射线或超声检测,3.泄漏性试验;四不属于本条二款所述的管道,如果现场条件不允许使用液体或气体进行压力试验,经使用单位和检验单位同意,通过泄漏性试验的可以不进行压力试验;第三十七条进行压力试验时,应遵守下列规定:一压力试验一般应以液体为试验介质;当管道的设计压力小于或等于时,也可采用气体为试验介质,但应采取有效的安全措施;脆性材料管道严禁使用气体进行压力试验;二当进行压力试验时,应划定禁区,采取必要的安全保护措施,无关人员不得进入;三在管道上进行的修补,应在压力试验前完成;四压力试验合格后,应按本规程附件三规定的格式填写在用工业管道压力试验报告或泄漏性试验报告;第三十八条压力试验和泄漏性试验的具体规定按现行国家标准工业金属管道工程施工及验收规范B50235执行, 其中试验压力计算公式中的设计压力在此可以用最高工作压力代替;第四节检验报告第三十九条全面检验工作结束后,检验人员应根据检验情况和所进行的检验项目,按照附件三在用工业管道全面检验报告书的规定,认真、准确填写;安全状况等级按照第四章的要求评定;检验报告由检验员签署,加盖检验单位印章;检验报告一般在工业管道投入使用之前送交使用单位;第五节缺陷处理第四十条可以采用如下方法对在检验中发现的超标缺陷进行处理:一修复处理消除缺陷:二采用安全评定的方法,确认缺陷是否影响管道安全运行到下一检验周期;第四十一条缺陷修复前,使用单位应制定修复方案,相关文件记录应存档;缺陷的修复应按有关规范的要求进行;缺陷修复后,由原检验单位确认合格后,管道方可投入使用;第四十二条工业管道的缺陷安全评定必须由国家质量监督检验检疫总局锅炉压力容器安全监察局核准的单位进行,工业管道安全评定单位应对评定结果负责;第四章安全状况等级评定第四十三条在用工业管道的安全状况等级应根据全面检验的结果评定,并以其中各评定项目中等级最低者作为评判级别;第四十四条管道位置不当或不合理结构,安全状况等级划分如下:一位置不当1. 当管道与其他管道或相邻设备之间存在碰撞及摩擦时,应进行调整,调整后符合安全技术规范的,不影响定级;否则,可定为3级或4级;2.管道位置不符合安全技术规范和现行国家标准的要求,应进行调整;受条件限制,无法调整的,应根据具体情况定为2级或3级,如对管道安全运行影响较大,应定为4级;二不合理结构管道有不符合安全技术规范或者设计、安装标准的不合理结构时,应进行调整或修复,调整或修复完好后,不影响定级;如一时无法进行调整或修复,对于不承受明显交变载荷并且经全面检验未发现新生缺陷不包括正常的均匀腐蚀的,可定为2级或3级;否则,应对管道进行安全评定,经安全评定确认不影响安全使用的,则可定为2级,反之则可定为3级或4级;第四十五条管道组成件的材质,应符合设计和使用要求,如与原设计不符,材质不明或者材质劣化时,安全状况等级划分如下:一材质与原设计不符如材质清楚,可以满足使用要求,则不影响定级;否则定为4级;二材质不明材质不明,一般应进行材质检验,确定材质类别;如满足使用要求,可定为之级或3级;经检验确认不符合使用要求,则定为4级;三材料劣化和损伤材料的球化、石墨化、蠕变损伤、氢腐蚀、晶间腐蚀、应力腐蚀与疲劳损伤一般可按以下规定定级:1.材料发生轻度球化,可评为2级,当发生中度球化或更严重球化时则评为3级或4级;材料球化程度的评定参照现行行业标准火电厂用20号钢珠光体球化评级标准DL/ T 674、火电厂用12Cr1MoV钢球化评级标准DL/T 773的要求进行;2.材料发生轻度石墨化,可评为3级,当发生中度石墨化或更严重石墨化时,则评为4级;材料石墨化程度的评定参照现行行业标准碳钢石墨化检验及评级标准DL/T 78 6的要求进行;3.对蠕变损伤,如金相检验仅发现材料存在蠕变空洞时,可评为3级,当存在蠕变裂纹时,评为4级;4.对氢腐蚀,如仅发生氢腐蚀脱碳但未发现裂纹时,可评为3级,当出现氢腐蚀裂纹时评为4级;5.材料发生晶间腐蚀,但未发现裂纹,可按最大晶间腐蚀深度采用第四十四条的。
承压设备合于使用评价
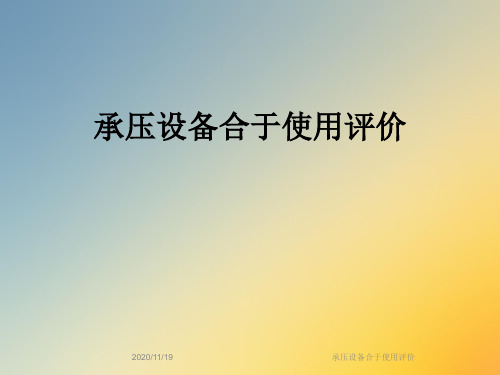
方法。
承压设备合于使用评价
国际上得到较好的工程验证并普遍采用的FFS标准/规范:
➢ API 579-1/ASME FFS-1 《合于使用评价》(2007年) ➢ R6《含缺陷结构完整性评定》(2001年,第四版)/R5《高温下结构相应
高参数化
复杂化
分析设计方法:JB4732、ASME VⅢ-2
基于塑性(极限载荷、安定性理论)与疲劳设计理论。
基本假设:材料均匀、连续、各向同性。
承压设备合于使用评价
概述
承压设备设计标准:质量控制
不足:① 建立在一定经验的基础上或建立在一定假设条件的
前提下; ② 设计时没有考虑承压设备存在缺陷的可能性。
承压设备合于使用评价
四、在用含缺陷压力容器安全评定
➢ 合于使用评价的主要内容:
• 评价对象的状况调查(历史、工况、环境等) • 缺陷检测、缺陷成因分析 • 失效模式判断 • 材料检验(性能、损伤与退化等) • 应力分析 • 必要的实验与计算 • 综合分析和评价
承压设备合于使用评价
四、在用含缺陷压力容器安全评定
定》的要求进行,承担压力容器合于使用评价的检验机构,应当根据缺 陷的性质、缺陷产生的原因,以及缺陷的发展预测在评价报告中给出明 确的评定结论,说明缺陷对压力容器安全使用的影响;
承压设备合于使用评价
二、法规标准和合于使用评价
➢ 《固定式压力容器安全技术监察规程 》
7.7 合于使用评价 ቤተ መጻሕፍቲ ባይዱ4)并且经过检验机构法定代表人或者技术负责人批准。承担压力容器合于
温度: -120℃
LNG 储罐
低温+大直径
压力管道缺陷产生原因及无损检测_1

压力管道缺陷产生原因及无损检测发布时间:2021-05-28T08:55:31.112Z 来源:《电力设备》2021年第2期作者:房爱伟[导读] 第三种是由于循环应力与腐蚀介质共同作用导致的腐蚀疲劳裂纹。
(国网新源控股有限公司检修分公司 100053)摘要:压力管道经过长期的高压运行后,会产生较多的缺陷问题,将会造成化工产业在经济和效率方面的损失,通过缺陷原因和无损检测技术的分析,能够有效促进压力管道缺陷问题的改善和防范,并加强无损检测技术的提高与发展,使化工产业的生产质量和效率得到更好的保障。
关键词:压力管道缺陷;产生原因;无损检测一、压力管道缺陷的产生原因(一)疲劳裂纹疲劳裂纹主要是由于压力管道的结构材料承受交变反复荷载,尤其是局部高应变区内的峰值应力已经远远超过材料所能承受的强度,会在晶粒之间形成滑移和错位等影响,最终导致微裂纹的产生,并随着荷载的增加而逐渐扩大成疲劳裂纹。
根据不同的形成原因,可以将疲劳裂纹分为常见的三种类型,第一种是由于交变工作荷载导致的疲劳裂纹,第二种是由于循环热应力导致的热疲劳裂纹,第三种是由于循环应力与腐蚀介质共同作用导致的腐蚀疲劳裂纹。
(二)应力腐蚀裂纹应力腐蚀裂纹就是金属材料受到特定腐蚀介质的拉应力影响所形成的裂纹,以奥氏体不锈钢压力管道中含有的氯离子最为常见。
(三)晶间腐蚀晶间腐蚀主要是受到特定介质的腐蚀影响,使结构的连续性受到严重损伤,以不锈钢管道的焊缝表面较为常见,尤其是熔合线和热影响区,其中最大的影响因素就在于晶间贫铬。
(四)局部腐蚀局部腐蚀以点腐蚀为主,主要是某些腐蚀性溶液与金属材料形成接触,导致局部腐蚀在金属材料表面逐渐形成,再随着腐蚀的不断进展而形成不断加深的蚀孔。
局部腐蚀中还常见磨损腐蚀,是指金属材料受到磨损和腐蚀的双重作用,会促进磨损和腐蚀的快速进展,导致金属材料的损伤速度和程度加剧。
二、压力管道无损的检测(一)无损检测技术的意义通过化工行业长期的发展经验,逐渐形成处理压力管道缺陷问题的多种措施,无损检测就是由长期的经验和实践总结而来。
在用含未焊透缺陷工业管道的安全评定
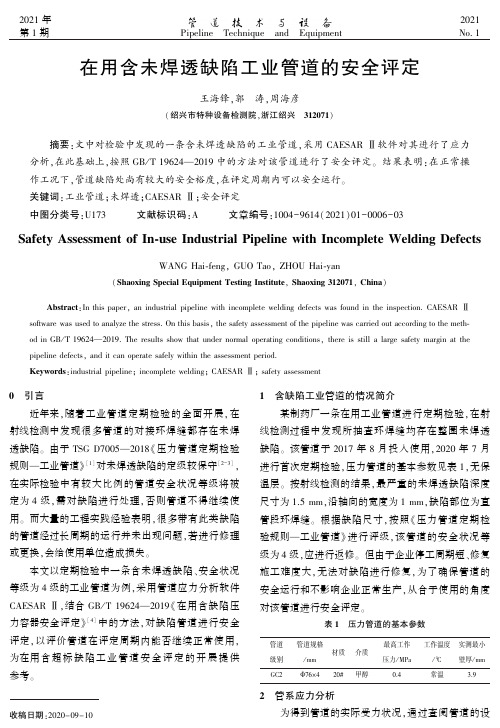
㊀2021年㊀第1期Pipeline㊀Technique㊀and㊀Equipment2021㊀No 1㊀收稿日期:2020-09-10在用含未焊透缺陷工业管道的安全评定王海锋,郭㊀涛,周海彦(绍兴市特种设备检测院,浙江绍兴㊀312071)㊀㊀摘要:文中对检验中发现的一条含未焊透缺陷的工业管道,采用CAESARⅡ软件对其进行了应力分析,在此基础上,按照GB/T19624—2019中的方法对该管道进行了安全评定㊂结果表明:在正常操作工况下,管道缺陷处尚有较大的安全裕度,在评定周期内可以安全运行㊂关键词:工业管道;未焊透;CAESARⅡ;安全评定中图分类号:U173㊀㊀㊀文献标识码:A㊀㊀㊀文章编号:1004-9614(2021)01-0006-03SafetyAssessmentofIn⁃useIndustrialPipelinewithIncompleteWeldingDefectsWANGHai⁃feng,GUOTao,ZHOUHai⁃yan(ShaoxingSpecialEquipmentTestingInstitute,Shaoxing312071,China)Abstract:Inthispaper,anindustrialpipelinewithincompleteweldingdefectswasfoundintheinspection.CAESARⅡsoftwarewasusedtoanalyzethestress.Onthisbasis,thesafetyassessmentofthepipelinewascarriedoutaccordingtothemeth⁃odinGB/T19624 2019.Theresultsshowthatundernormaloperatingconditions,thereisstillalargesafetymarginatthepipelinedefects,anditcanoperatesafelywithintheassessmentperiod.Keywords:industrialpipeline;incompletewelding;CAESARⅡ;safetyassessment0㊀引言近年来,随着工业管道定期检验的全面开展,在射线检测中发现很多管道的对接环焊缝都存在未焊透缺陷㊂由于TSGD7005 2018‘压力管道定期检验规则 工业管道“[1]对未焊透缺陷的定级较保守[2-3],在实际检验中有较大比例的管道安全状况等级将被定为4级,需对缺陷进行处理,否则管道不得继续使用㊂而大量的工程实践经验表明,很多带有此类缺陷的管道经过长周期的运行并未出现问题,若进行修理或更换,会给使用单位造成损失㊂本文以定期检验中一条含未焊透缺陷㊁安全状况等级为4级的工业管道为例,采用管道应力分析软件CAESARⅡ,结合GB/T19624 2019‘在用含缺陷压力容器安全评定“[4]中的方法,对缺陷管道进行安全评定,以评价管道在评定周期内能否继续正常使用,为在用含超标缺陷工业管道安全评定的开展提供参考㊂1㊀含缺陷工业管道的情况简介某制药厂一条在用工业管道进行定期检验,在射线检测过程中发现所抽查环焊缝均存在整圈未焊透缺陷㊂该管道于2017年8月投入使用,2020年7月进行首次定期检验,压力管道的基本参数见表1,无保温层㊂按射线检测的结果,最严重的未焊透缺陷深度尺寸为1.5mm,沿轴向的宽度为1mm,缺陷部位为直管段环焊缝㊂根据缺陷尺寸,按照‘压力管道定期检验规则 工业管道“进行评级,该管道的安全状况等级为4级,应进行返修㊂但由于企业停工周期短㊁修复施工难度大,无法对缺陷进行修复,为了确保管道的安全运行和不影响企业正常生产,从合于使用的角度对该管道进行安全评定㊂表1㊀压力管道的基本参数管道级别管道规格/mm材质介质最高工作压力/MPa工作温度/ħ实测最小壁厚/mmGC2Φ76ˑ420#甲醇0.4常温3.92㊀管系应力分析为得到管道的实际受力状况,通过查阅管道的设㊀㊀㊀㊀㊀第1期王海锋等:在用含未焊透缺陷工业管道的安全评定7㊀㊀计㊁安装和竣工资料,并对现场管道走向㊁支吊架位置等情况进行实际查勘,利用CAESARⅡ软件建立管道的整体应力分析模型,如图1所示㊂图1㊀管道应力分析模型由CAESARⅡ软件推荐的工况进行计算,得到管道一次应力校核时节点处的最大综合应力值为61.517MPa,应力比率为47.3%;二次应力校核时节点处的最大综合应力值为33.627MPa,应力比率为12.8%㊂按照ASMEB31.3规范的校核准则,管道一次㊁二次应力的校核均满足要求㊂根据未焊透缺陷在应力分析模型中的节点位置,由计算可知,在操作工况(OPE)下,最严重缺陷处管道横截面的弯矩载荷M=0.065kN㊃m㊂3㊀管道的安全评定受检管道材质为20#,在检验中未发现材料脆化倾向,可以按照GB/T19624 2019标准附录H给出的评定方法,对管道未焊透缺陷进行安全评定㊂3.1㊀缺陷部位管道尺寸的确定假设检验周期初定3a,管道实测最小壁厚为3.9mm,则周期性腐蚀量C2=(4-3.9)ˑ3/3=0.1mm,管道计算壁厚T=3.9-0.1=3.8mm㊂管道外径实测最大值Do=76mm,外半径Ro=Do/2=38mm,内半径Ri=Ro-T=34.2mm㊂3.2㊀缺陷的规则化及无量纲化处理由射线检测结果可知,缺陷性质为整圈未焊透,最严重缺陷处的深度为1.5mm,缺陷沿轴向的宽度为1mm㊂按图2所示进行规则化处理,则轴向半长A=0.5mm㊁环向半长B=πRi=107.39mm㊁深度C=1.5mm㊂缺陷尺寸的无量纲化处理如下:相对轴向长度a=A/RoT=0.5/38ˑ3.8=0.042,相对环向长度b=B/(πRi)=1,相对深度c=C/T=1.5/3.8=0.395㊂图2㊀未焊透缺陷表征示意图3.3㊀材料性能数据的确定按文献[5]确定在评定工况下材料的屈服强度σs=245MPa,抗拉强度σb=390MPa㊂则材料的流变应力:σᶄ=σs+σb2=245+3902=317.5MPa3.4㊀无缺陷管道在纯内压和纯弯矩下的塑性极限载荷的计算在纯内压下的塑性极限内压:PL0=23σᶄlnRoRi=23ˑ317.5ˑln3834.2=38.63MPa在纯弯矩下的塑性极限弯矩:ML0=4σᶄR3o-R3i3=4ˑ317.5ˑ383-34.233=6.295kN㊃m3.5㊀免于评定的判别未焊透缺陷若要免于评定,则须同时满足下列条件:(1)管道结构符合设计制造要求;(2)Pmax/PL0ɤ0.3;(3)未焊透缺陷的相对深度c0不超过表2规定的容限值,其中c0=[C+(T0-T)]/T0㊂表2㊀压力管道未焊透缺陷容限值缺陷的相对环向长度b容许的最大缺陷相对深度c0bɤ0.250.450.25<bɤ0.500.400.50<bɤ0.750.350.75<bɤ1.000.25㊀㊀受检管道结构符合设计制造要求,且Pmax/PL0=0.4/38.63=0.01<0.3,满足条件(1)和(2),但相对深度c0=[C+(T0-T)]/T0=[1.5+(4-3.8)]/4=0.425>㊀㊀㊀㊀㊀8㊀PipelineTechniqueandEquipmentJan 2021㊀0.25,不满足条件(3),故该缺陷不能免于评定,应对其进行安全评定㊂3.6㊀缺陷管道在纯内压和纯弯矩下的塑性极限载荷的计算在纯内压下的塑性极限内压:PLS=pLSˑPL0(1)式中:pLS=0.95-(0.85+0.013a/b)Ae=0.864,Ae=c(aebc)1/3=0.1007,ae=min(3.0,a)=0.042㊂将相关数据代入式(1),计算得PLS=33.38MPa㊂在纯弯矩下的塑性极限弯矩:MLS=mLSˑML0(2)式中:mLS=(1-c)sinπ(1-bc)2(1-c)éëêêùûúú+csin(πb)2=0.605㊂将相关数据代入式(2),计算得MLS=3.808kN㊃m㊂3.7㊀安全性评价若式(3)的判据成立,说明该缺陷是安全或可接受的;否则,说明管道在操作工况下不能保证安全或不可接受㊂PPLSæèçöø÷2+MMLSæèçöø÷2ɤ0.44(3)P取管道最高工作压力值0.4MPa,将计算出的PLS=33.38MPa㊁M=0.065kN㊃m㊁MLS=3.808kN㊃m代入式(3),计算可得:PPLSæèçöø÷2+MMLSæèçöø÷2=0.00043<0.44通过计算可知,在正常操作工况下,该含未焊透缺陷的管道在评定周期内是可以安全运行的㊂4㊀结论(1)本文对检验过程中发现的超标未焊透缺陷进行了安全评定分析,详细介绍了评定步骤及计算过程,给出了管道安全评价的结果㊂结果表明:在正常操作工况下,缺陷处尚有较大的安全裕度,在评定周期内可以安全运行,满足合于使用要求㊂(2)对部分含超标缺陷安全状况等级定为4级的工业管道,在企业由于各种原因无法及时进行返修的情况下,可以采用安全评定的方法对管道的安全状况进行评估,在保证管道安全运行的前提下,进一步发挥了在用含缺陷管道的使用经济性㊂参考文献:[1]㊀国家质量监督检验检疫总局.压力管道定期检验规程工业管道:TSGD7005 2018[S].北京:新华出版社,2018:13-15.[2]㊀梁文军,陈坡,盛水平,等.含未焊透缺陷压力管道极限载荷数值分析[J].轻工机械,2008,26(5):113-116.[3]㊀张叔自.对‘在用工业管道定期检验规程“(试行)几个问题的探讨[J].化工设备与管道,2005,42(1):21-23.[4]㊀国家市场监督管理总局.在用含缺陷压力容器安全评定:GB/T19624 2019[S].北京:中国标准出版社,2020:105-110.[5]㊀国家质量技术监督局.工业金属管道设计规范:GB50316 2000[S].北京:中国计划出版社,2008:104.作者简介:王海锋(1985 ),工程师,硕士研究生,主要从事承压类特种设备的检验检测工作㊂E⁃mail:sxwhf20@163.com。
含缺陷在用压力管道合于使用评价
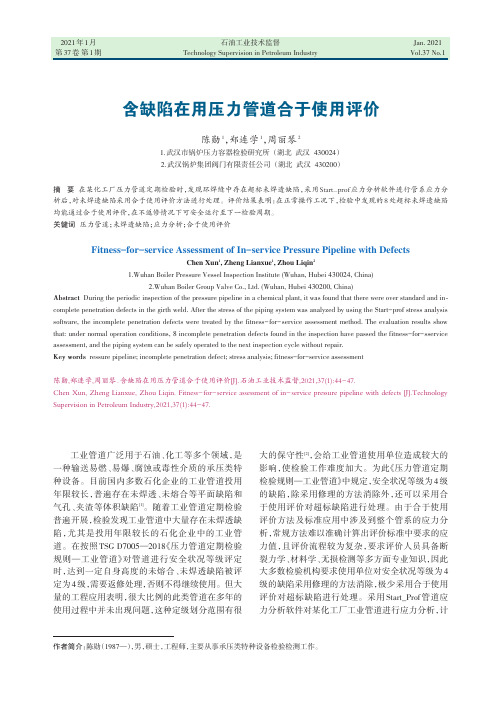
2020年10月第36卷第10期石油工业技术监督Technology Supervision in Petroleum IndustryOct.2020Vol.36No.102021年1月第37卷第1期Jan.2021Vol.37No.1作者简介:陈勋(1987—),男,硕士,工程师,主要从事承压类特种设备检验检测工作。
含缺陷在用压力管道合于使用评价陈勋1,郑连学1,周丽琴21.武汉市锅炉压力容器检验研究所(湖北武汉430024)2.武汉锅炉集团阀门有限责任公司(湖北武汉430200)摘要在某化工厂压力管道定期检验时,发现环焊缝中存在超标未焊透缺陷,采用Start _prof 应力分析软件进行管系应力分析后,对未焊透缺陷采用合于使用评价方法进行处理。
评价结果表明:在正常操作工况下,检验中发现的8处超标未焊透缺陷均能通过合于使用评价,在不返修情况下可安全运行至下一检验周期。
关键词压力管道;未焊透缺陷;应力分析;合于使用评价Fitness-for-service Assessment of In-service Pressure Pipeline with DefectsChen Xun 1,Zheng Lianxue 1,Zhou Liqin 21.Wuhan Boiler Pressure Vessel Inspection Institute (Wuhan,Hubei 430024,China)2.Wuhan Boiler Group Valve Co.,Ltd.(Wuhan,Hubei 430200,China)Abstract During the periodic inspection of the pressure pipeline in a chemical plant,it was found that there were over standard and in⁃complete penetration defects in the girth weld.After the stress of the piping system was analyzed by using the Start-prof stress analysis software,the incomplete penetration defects were treated by the fitness-for-service assessment method.The evaluation results show that:under normal operation conditions,8incomplete penetration defects found in the inspection have passed the fitness-for-sservice assessment,and the piping system can be safely operated to the next inspection cycle without repair.Key words ressure pipeline;incomplete penetration defect;stress analysis;fitness-for-service assessment 陈勋,郑连学,周丽琴.含缺陷在用压力管道合于使用评价[J].石油工业技术监督,2021,37(1):44-47.Chen Xun,Zheng Lianxue,Zhou Liqin.Fitness-for-service assessment of in-service pressure pipeline with defects [J].Technology Supervision in Petroleum Industry,2021,37(1):44-47.工业管道广泛用于石油、化工等多个领域,是一种输送易燃、易爆、腐蚀或毒性介质的承压类特种设备。
薄壁管未焊透缺陷安全评定

《装备维修技术》2021年第4期—97—薄壁管未焊透缺陷安全评定齐喜岑 王 钊 钱英豪(江苏省特种设备安全监督检验研究院,江苏 苏州 215031)在压力管道的定期检验过程中,80%的管道焊接缺陷为未焊透,根据TSG D7005-2018《压力管道定期检验规则—工业管道》,对于材料为20钢、Q345或奥氏体不锈钢的管道未焊透,可以按照局部减薄来定级。
而根据TSG D7005局部减薄超过制造或者验收标准所允许范围,同时满足以下条件的,可以定为2级或3级,否则,安全状况等级定为4级[1]: (1)管道结构符合设计规范或者管道应力分析结果满足有关安全技术规范要求;(2)在实际工况下,材料韧性良好,并且未出现材料性能劣化以及劣化趋向; (3)壁厚局部减薄以及其附近无其他表面缺陷或者埋藏缺陷;(4)壁厚局部减薄处剩余壁厚大于2mm;(5)管道不承受疲劳载荷。
因此,未焊透按照局部减薄来定级必须要满足局部减薄处剩余壁厚大于2mm。
那么对于实际检验中管子壁厚不足2mm,经RT检测,存在未焊透现象的压力管道,按照TSG D7005的要求只能定为4级,不得投入使用。
本文通过计算,采用安全评定的方式来探讨该类管道在一定条件下是否具有安全性。
1 安全评定技术压力管道焊缝的安全评定主要是基于合于使用的基本原则。
在焊接结构的发展初期,要求结构在制造和使用过程中不能有任何缺陷存在,否则就要返修甚至报废;英国焊接研究所首先提出了“合于使用”的概念。
目前很多国家已建立了使用于焊接结构的设计、制造和验收的“合于使用”原则的标准。
通常安全评定需要输入载荷、类型裂纹缺陷和断裂韧度三个参量。
对于未熔合、未焊透和其他类型裂纹缺陷,视为平面缺陷,气孔、夹渣和类似的焊接接线则视为体积缺陷,有时缺陷类型是难以区分的,如某些情况下咬肉可视为简单的应力集中,而在某些情况下又应视为类裂纹缺陷[2][3]。
在安全评定中,通常将各种缺陷模型化。
平面缺陷以包络它的矩形之高度予以理想化,并以此作为安全评定的缺陷尺寸。
浅析压力管道检验中发现的缺陷原因分析及处理措施

浅析压力管道检验中发现的缺陷原因分析及处理措施摘要:压力管道会受到外部作用和环境影响,导致压力管道在使用环节中容易出现腐蚀、破损、裂纹等缺陷问题,若不进行及时的修复管理,很容易导致压力管道存在缺陷,影响管道输送安全。
为此,应该严格开展压力管道检验工作,发现管道存在的缺陷,分析缺陷出现的原因,并做好处理工作。
关键词:压力管道;检验;缺陷原因;处理措施1压力管道检验常见缺陷1.1腐蚀缺陷一些压力管道露天铺设而且运行温差较大,导致压力管道的腐蚀严重,尤其运输介质和环境有较大的温差,腐蚀会更加严重。
很多压力管道受到雨水、大气腐蚀、母液的影响,还有一些在地沟内铺设,土中的水分也会影响管道,土壤中可能会含有一定量的腐蚀性物质,进而加速管道腐蚀。
出现腐蚀问题对管道影响较大,很容易导致管道出现断裂、变形,降低管道强度,因此,必须针对腐蚀问题做好防范工作。
对于架空管道和地面铺设管道,为避免管道受到外界腐蚀,需要涂抹防腐蚀层;地下管道则需要在管道外侧增加包裹层,同时增加阴极防护,提升管道的防护效果;若不同的金属管道需要捆扎在一起时,要使用绝缘件隔开,例如在管道支撑作业中,就需要做好事先的管道隔离。
管道的腐蚀情况可以直接通过外观进行检查,或者检查管道壁厚度。
检查管道的外观时,不仅要检查管道的情况,也要检查和管道连接的部件,比如管道支撑、管道紧固件等部位的腐蚀状况。
测定管道壁厚时,为了保证测量结果精确,要选择具有代表性的检测点,例如管道内壁容易腐蚀的位置,在制造时容易出现拉薄的位置等等,在此类部位检测时,需要结合管道内流体流动方式,确定受力最大的部位开展相应检测。
也要结合获得的实测数据,结合管道所处的环境分析管道受到腐蚀的规律,测量管道还具有的强度,结合测量结果确定防范措施。
针对腐蚀量较大的位置,还需要定期进行标记和检测。
1.2焊接缺陷分别针对夹渣缺陷以及未熔合缺陷的产生因素进行综合性分析。
首先,夹渣缺陷的发生原因主要有破口的角度以及焊接电流无法达标,焊接边缘有气泡,边缘清理不干净,存在氧化物,铁皮或者碳化物出现酸性焊条的情况,在电流或者运条不当的情况下,会形成复杂碱性焊条的情况下,电头过长以及极性不正确也会引发夹渣问题。
国家质量监督检验检疫总局关于印发《压力管道使用登记管理规则》(试行)的通知
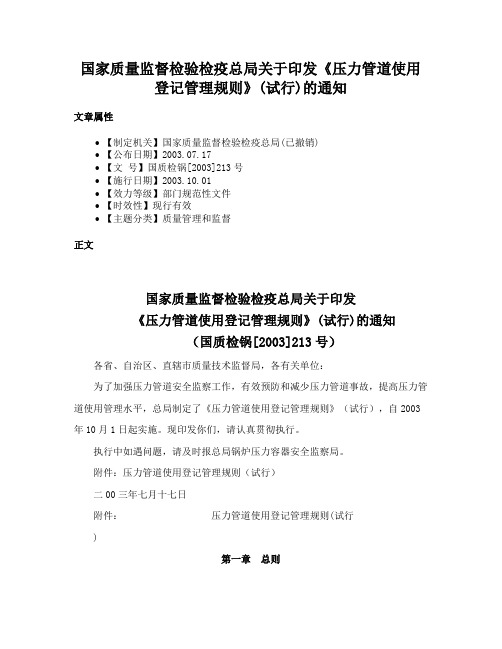
国家质量监督检验检疫总局关于印发《压力管道使用登记管理规则》(试行)的通知文章属性•【制定机关】国家质量监督检验检疫总局(已撤销)•【公布日期】2003.07.17•【文号】国质检锅[2003]213号•【施行日期】2003.10.01•【效力等级】部门规范性文件•【时效性】现行有效•【主题分类】质量管理和监督正文国家质量监督检验检疫总局关于印发《压力管道使用登记管理规则》(试行)的通知(国质检锅[2003]213号)各省、自治区、直辖市质量技术监督局,各有关单位:为了加强压力管道安全监察工作,有效预防和减少压力管道事故,提高压力管道使用管理水平,总局制定了《压力管道使用登记管理规则》(试行),自2003年10月1日起实施。
现印发你们,请认真贯彻执行。
执行中如遇问题,请及时报总局锅炉压力容器安全监察局。
附件:压力管道使用登记管理规则(试行)二00三年七月十七日附件:压力管道使用登记管理规则(试行)第一章总则第一条为了加强压力管道使用安全监察工作,规范压力管道使用登记行为,提高压力管道安全管理水平,根据《特种设备安全监察条例》、《压力管道安全管理与监察规定》以及国务院赋予国家质量监督检验检疫部门的职责等有关规定,制定本规则。
第二条本规则适用于《特种设备安全监察条例》规定范围内的压力管道及其安全保护装置和附属设施的使用登记管理。
第三条使用压力管道的单位和个人(以下统称使用单位),应当按照本规则的规定办理压力管道使用登记。
压力管道使用登记分为登记注册和登记发证(证书格式见附件一)两种形式。
使用登记证有效期为6年。
第四条国家质量监督检验检疫总局负责办理跨省(自治区、直辖市)的长输管道的使用登记;省级质量技术监督行政部门负责办理所辖行政区域内不跨省(自治区、直辖市)的长输管道的使用登记;省级质量技术监督行政部门或其授权的市(地级)级质量技术监督行政部门负责办理所辖行政区域内公用管道和工业管道的使用登记。
使用登记部门内设的负责压力管道安全监察的机构(以下简称安全监察机构),负责压力管道使用登记的受理、注册和发证工作。
压力管道安全使用要点(三篇)

压力管道安全使用要点压力管道的安全运行与使用关系极大,在用压力管道由于介质和环境的侵害、操作不当、维护不力,往往会引起材料性能的恶化、失效而降低其使用性能和周期,甚至发生事故。
要保证压力管道的安全运行,需掌握以下安全使用要点:1)强化工艺指标控制。
a.控制管道温度和压力不超过最高工作压力和极限工作温度,防止出现过低的操作温度。
b.避免频繁加压和卸压,避免过大压力及温度波动,力求平稳操作,有效的控制交变载荷的产生。
c.对压力管道内的腐蚀性介质含量及工况进行严格的监控措施,坚决制止介质超标等违反工艺规程、操作规程的行为。
2)坚持岗位责任制。
操作人员必须经过安全技术和岗位操作法的学习培训,经考核合格后方可上岗操作,明确规定其职责、权限,责任落实到人。
3)认真执行巡回检查。
操作和维修人员应按各自的责任和要求定期按巡回检查路线完成每个部位、每个项目的检查,并做好记录,检查中发现的异常情况应及时汇报和处理。
4)进行日常维护保养。
对检查及保养项目进行必要的日常维护保养。
5)加强定期检查和检验。
每年至少进行一次专业的外部检查,每六年至少进行一次全面检验。
压力管道的检验工作必须严格地按有关检验规程执行,检验中发现的有关超标缺陷要慎重对待,必要时要请失效评定权威机构进行安全评定,确定管道是否能安全工作,并提出必要的预防补救措施。
6)做好特护措施。
a.建立严格的介质定期采样制度,加强对压力管道腐蚀环境的监测和分析,并进行严格的控制。
b.必须建立定点、定时、定材料挂片测腐蚀速率的制度,建立全面的管道测厚系统。
c.对原材料性质经常发生变化的使用单位,一旦原料发生变化时,有关的工作要重复进行。
d.对部分存在隐患的压力管道,应强化管理,缩短定检周期,加强对特定或重要管道的检测、检验工作。
压力管道安全使用要点(二)压力管道是一种用于输送流体或气体的管道系统,它承受着很大的压力,因此在使用过程中需要注意安全。
以下是压力管道安全使用的要点:1. 设计和制造:压力管道的设计和制造必须符合相关的标准和规范,确保其承受能力和安全性。
2023年江苏省连云港市特种设备作业特种设备安全管理A模拟考试(含答案)
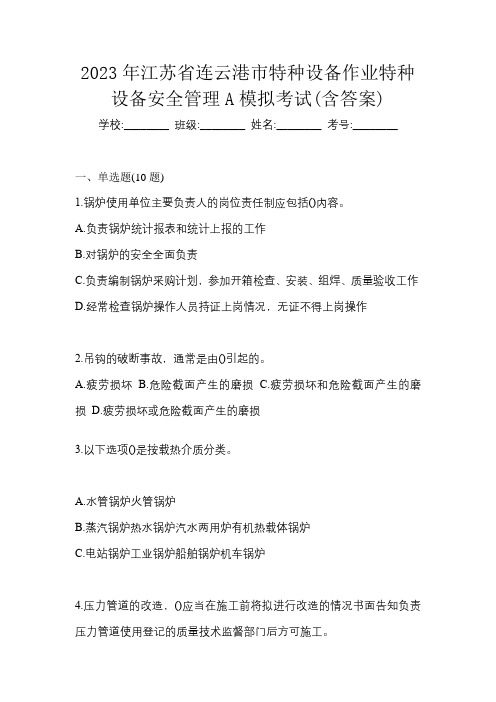
2023年江苏省连云港市特种设备作业特种设备安全管理A模拟考试(含答案) 学校:________ 班级:________ 姓名:________ 考号:________一、单选题(10题)1.锅炉使用单位主要负责人的岗位责任制应包括()内容。
A.负责锅炉统计报表和统计上报的工作B.对锅炉的安全全面负责C.负责编制锅炉采购计划,参加开箱检查、安装、组焊、质量验收工作D.经常检查锅炉操作人员持证上岗情况,无证不得上岗操作2.吊钩的破断事故,通常是由()引起的。
A.疲劳损坏B.危险截面产生的磨损C.疲劳损坏和危险截面产生的磨损D.疲劳损坏或危险截面产生的磨损3.以下选项()是按载热介质分类。
A.水管锅炉火管锅炉B.蒸汽锅炉热水锅炉汽水两用炉有机热载体锅炉C.电站锅炉工业锅炉船舶锅炉机车锅炉4.压力管道的改造,()应当在施工前将拟进行改造的情况书面告知负责压力管道使用登记的质量技术监督部门后方可施工。
A.设计单位B.安装单位C.监理单位D.检验单位5.《特种设备安全监察条例》规定最高工作压力()的压力管道属于监察的范围。
A.高于0.1MPaB.高于1MPaC.高于或者等于0.1MPa6.按锅炉安装许可等级分类中,级别为2级时,安装锅炉的范围是额定出口压力小于等于()Mpa的锅炉。
A.0.8B.1.6C.2.57.观光列车的牵引车头座位数不大于()人。
A.2B.4C.38.因技术不够完善或者设备自然损耗等原因引起并且是在人所不能预见或者不能避免的情况下所发生的事故属于()。
A.自然事故B.责任事故C.人为事故D.技术事故9.锅炉使用单位应当逐台建立安全技术档案,()不是安全技术档案要求的内容。
A.锅炉的出厂技术文件(含产品能效测试报告)B.锅炉安装改造修理技术资料C.锅炉定期检验报告D.相关作业人员资质证书10.泄漏试验压力应为()。
A.设计压力B.计算压力C.工作压力D.15倍设计压力二、单选题(10题)11.边运行边上下乘人的游乐设施,其运行速度应不大于()。
压力管道安全使用要点
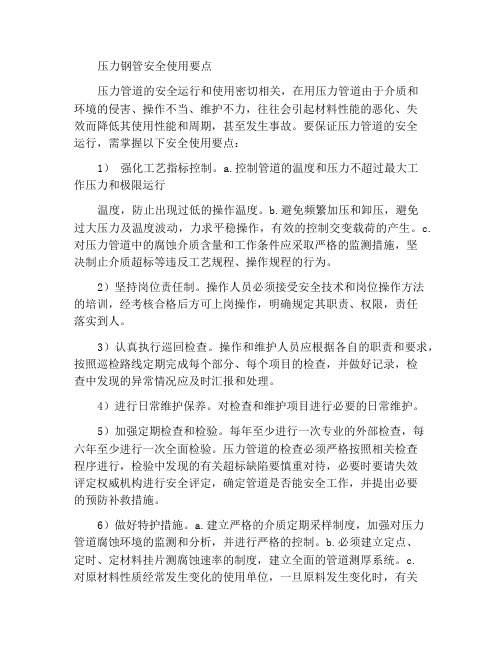
压力钢管安全使用要点压力管道的安全运行和使用密切相关,在用压力管道由于介质和环境的侵害、操作不当、维护不力,往往会引起材料性能的恶化、失效而降低其使用性能和周期,甚至发生事故。
要保证压力管道的安全运行,需掌握以下安全使用要点:1)强化工艺指标控制。
a.控制管道的温度和压力不超过最大工作压力和极限运行温度,防止出现过低的操作温度。
b.避免频繁加压和卸压,避免过大压力及温度波动,力求平稳操作,有效的控制交变载荷的产生。
c.对压力管道中的腐蚀介质含量和工作条件应采取严格的监测措施,坚决制止介质超标等违反工艺规程、操作规程的行为。
2)坚持岗位责任制。
操作人员必须接受安全技术和岗位操作方法的培训,经考核合格后方可上岗操作,明确规定其职责、权限,责任落实到人。
3)认真执行巡回检查。
操作和维护人员应根据各自的职责和要求,按照巡检路线定期完成每个部分、每个项目的检查,并做好记录,检查中发现的异常情况应及时汇报和处理。
4)进行日常维护保养。
对检查和维护项目进行必要的日常维护。
5)加强定期检查和检验。
每年至少进行一次专业的外部检查,每六年至少进行一次全面检验。
压力管道的检查必须严格按照相关检查程序进行,检验中发现的有关超标缺陷要慎重对待,必要时要请失效评定权威机构进行安全评定,确定管道是否能安全工作,并提出必要的预防补救措施。
6)做好特护措施。
a.建立严格的介质定期采样制度,加强对压力管道腐蚀环境的监测和分析,并进行严格的控制。
b.必须建立定点、定时、定材料挂片测腐蚀速率的制度,建立全面的管道测厚系统。
c.对原材料性质经常发生变化的使用单位,一旦原料发生变化时,有关的工作要重复进行。
d.对部分存在隐患的压力管道,应强化管理,缩短定检周期,加强对特定或重要管道的检测、检验工作。
- 1、下载文档前请自行甄别文档内容的完整性,平台不提供额外的编辑、内容补充、找答案等附加服务。
- 2、"仅部分预览"的文档,不可在线预览部分如存在完整性等问题,可反馈申请退款(可完整预览的文档不适用该条件!)。
- 3、如文档侵犯您的权益,请联系客服反馈,我们会尽快为您处理(人工客服工作时间:9:00-18:30)。
一、压力管道直管段体积缺陷安全评定方法 g、含缺陷管道在纯内压和纯弯矩下的塑性极限载荷确定
是 h>0.7B
否 是
否
c=a=h
输出a、c
表面裂纹表征示意图
是
否
是
否
否
是
是
否
输出a、c
埋藏裂纹表征示意图
输出c、a
穿透裂纹表征示意图 4)、斜裂纹
裂纹平面方向与主应力方向不垂直时,将裂纹投影到与主应力 方向垂直的平面内再进行表征。
两共面且位于同侧的表面裂纹表征示意图
否
否 按单个裂纹 进行表征
一、压力管道直管段体积缺陷安全评定方法 e、免于评定的判别
夹渣免于评定的判别条件: 如果夹渣自身高度或宽度不大于0.4T,则该夹 渣可免于评定
夹渣免于评定程序流程图:
夹渣
输入2a, 2c
min(2a,2c)<0.4T
否
继续评定程序
是
合格,免 于评定
一、压力管道直管段体积缺陷安全评定方法 e、免于评定的判别
环向平面缺陷的评定(U因子评定法)
输出
是
“安全”
输出“不能 保证安全”
否
否 U=1
是
U=U
压力管道直管段缺陷
平面缺陷 体积缺陷
塑性失效评定方法 疲劳失效评定方法 塑性失效评定方法 疲劳失效评定方法
压力管道直管段平面缺陷 的疲劳失效评定方法
1、缺陷的表征 (缺陷规则化并
确定a、c)
安全
7、安全性评价 (给出评定结论)
缺陷规则化尺寸的无量纲化处理:
一、压力管道直管段体积缺陷安全评定方法 1、评定总体流程: a、缺陷部位管道尺寸的确定 b、缺陷规则化 c、材料性能数据的确定 d、无缺陷管道在纯内压或纯弯矩下的塑性极限载荷的确定 e、免于评定的判别 f、典型工况载荷组合的确定与缺陷处弯矩的计算 g、含缺陷管道在纯内压和纯弯矩下的塑性极限载荷确定 h、安全性评价
III型:
如果S1< (a1+a2)且S2< (c1+c2), 则有效长度为2c=(2c1+2c2+s2)
一、压力管道直管段体积缺陷安全评定方法 b、缺陷规则化
3:气孔、夹渣缺陷的表征
<2>非共面夹渣
当两个非共面埋藏夹渣之间的最小距离S3 小于较小的夹渣的自身高度的一半时,则 这两个夹渣可以视为共面并按共面夹渣规 定进行复合。否则,均应逐个进行评定。
是 否 否 是
1、缺陷的表征 (缺陷规则化并
确定a、c)
安全
7、安全性评价 (给出评定结论)
七、安全性评价
压力管道直管段缺陷
平面缺陷 体积缺陷
塑性失效评定方法 疲劳失效评定方法 塑性失效评定方法 疲劳失效评定方法
一、压力管道直管段体积缺陷安全评定方法 1、评定总体流程: a、缺陷部位管道尺寸的确定 b、缺陷规则化 c、材料性能数据的确定 d、无缺陷管道在纯内压或纯弯矩下的塑性极限载荷的确定 e、免于评定的判别 f、典型工况载荷组合的确定与缺陷处弯矩的计算 g、含缺陷管道在纯内压和纯弯矩下的塑性极限载荷确定 h、安全性评价
否 分别评定
2c=max(2a, 2c1)
2a=2a1
输出2a, 2c
输出2c,2a
一、压力管道直管段体积缺陷安全评定方法
b、缺陷规则化
3:气孔、夹渣缺陷 的表征程序流程图
III型夹渣复合
输入:s1, s2, a1, a2, c1, c2
S1< (a1+a2) 是
否 分别评定
S2< (c1+c2) 是
A的取值
M的取值 3.35
3.0
对伴有解理或微孔聚合等具有更高 扩展速率的疲劳裂纹扩展机制
3.0
是 无效 否
是
否
否 是
1、缺陷的表征 (缺陷规则化并
确定a、c)
安全
7、安全性评价 (给出评定结论)
1、含长为2a的穿透裂纹的板壳(板宽2W,板长2L)
是
否
否
是
输出 “无效”
是
否
输出无 结果
是 否
确定a、c)
7、安全性评价 (给出评定结论)
是
否 是
否
输出“无效”
1
1 否
是
否
否 是
是
否 是
否 输出“无效”
输出G
是 否 1
1 是
否 是
否 是
否 否
是
否 是
输出 “失效”
否
是
输出G
是 否
否 是
是
否 是
1、缺陷的表征 (缺陷规则化并
确定a、c)
7、安全性评价 (给出评定结论)
是
否 输出“无 结果”
一、压力管道直管段体积缺陷安全评定方法 b、缺陷规则化 压力管道直管段缺陷的分类: 1:壁厚局部减薄 2:未焊透缺陷
3:气孔、夹渣缺陷
一、压力管道直管段体积缺陷安全评定方法 b、缺陷规则化 1:壁厚局部减薄缺陷的表征
深度:C 环向长度:2B
轴向长度:2A
一、压力管道直管段体积缺陷安全评定方法 b、缺陷规则化 2:未焊透缺陷表征
一、压力管道直管段体积缺陷安全评定方法
a、缺陷部位管道尺寸的确定
计算壁厚T: 实测壁厚与下一个检测周期 末的腐蚀量之差
外径R0
一、压力管道直管段体积缺陷安全评定方法 1、评定总体流程: a、缺陷部位管道尺寸的确定 b、缺陷规则化 c、材料性能数据的确定 d、无缺陷管道在纯内压或纯弯矩下的塑性极限载荷的确定 e、免于评定的判别 f、典型工况载荷组合的确定与缺陷处弯矩的计算 g、含缺陷管道在纯内压和纯弯矩下的塑性极限载荷确定 h、安全性评价
一、压力管道直管段体积缺陷安全评定方法
f、典型工况载荷组合的确定与缺陷处弯矩的计算
根据实际情况,确定需要进行缺陷评定的载 荷工况,给出相应的内压载荷P,并通过可靠 方法确定评定工况下缺陷处的弯矩载荷M。
一、压力管道直管段体积缺陷安全评定方法 1、评定总体流程: a、缺陷部位管道尺寸的确定 b、缺陷规则化 c、材料性能数据的确定 d、无缺陷管道在纯内压或纯弯矩下的塑性极限载荷的确定 e、免于评定的判别 f、典型工况载荷组合的确定与缺陷处弯矩的计算 g、含缺陷管道在纯内压和纯弯矩下的塑性极限载荷确定 h、安全性评价
1、缺陷的表征 (缺陷规则化并
确定a、c)
7、安全性评价 (给出评定结论)
通用失效评定图
压力管道直 管段缺陷
平面 缺陷
体积 缺陷
塑性失效评定方法 疲劳失效评定方法
轴向平面缺陷的评定 环向平面缺陷的评定
塑性失效评定方法 疲劳失效评定方法
压力管道直管段平面缺陷 的塑性失效评定方法
(环向平面缺陷的评定)
是 否
按单个裂纹 进行表征
否 否
是
是
1
2
1
2
否
各自进 行评定
是
则视为共面按共
面裂纹群的相应
程序进行评定
1、缺陷的表征 (缺陷规则化并
确定a、c)
7、安全性评价 (给出评定结论)
表面缺陷区域的应力线性化图示
埋藏缺陷区域的应力线性化图示
一次应力 二次应力
1、缺陷的表征 (缺陷规则化并
确定a、c)
否 分别评定
2c=(2c1+2c2+s2)
2a=(2a1+2a2+s1)
输出2c, 2a
一、压力管道直管段体积缺陷安全评定方法 b、缺陷规则化 3:气孔、夹渣缺陷的表征
环向长度:2B
轴向长度:2A
注意:若能够获得可靠的缺 陷自身高度H值,则C=H,否 则近似取C=2A
深度:C
一、压力管道直管段体积缺陷安全评定方法 b、缺陷规则化
局部减薄和未焊透免于评定的判别条件:
<1> 管道结构符合设计制造要求 <2>Pmax/PL0≤0.3 Pmax为最大容许工作压力(Mpa) <3> 局部减薄或未焊透相对深度c不超过下表的容限值
一、压力管道直管段体积缺陷安全评定方法
e、免于评定的判别
局部减薄 和未焊透
局部减薄和未焊透免于评
输入Pmax
7、安全性评价 (给出评定结论)
附:系数说明
1、缺陷的表征 (缺陷规则化并
确定a、c)
7、安全性评价 (给出评定结论)
1、含长为2a的穿透裂纹的板壳(板宽2W,板长2L)
是
否
否
是
输出 “无效”
是
否
输出无 结果
是 否
是 否
是
否
是
否 输出无 结果
是 否
是 否
是
否
1、缺陷的表征 (缺陷规则化并
是 h>0.7B
否 是
否 c=a=h
输出a、c
表面裂纹表征示意图
是 否
否 是
是 否
是
否
输出a、c
埋藏裂纹表征示意图
输出c、a
穿透裂纹表征示意图 4)、斜裂纹
裂纹平面方向与主应力方向不垂直时,将裂纹投影到与主应力 方向垂直的平面内再进行表征。
两共面且位于同侧的表面裂纹表征示意图
否
否 按单个裂纹 进行表征
是 否
是
输出a、c
两共面且位于同侧的表面裂纹表征示意图
否
否 按单个裂纹 进行表征
是 否
是
输出a、c
是 否
按单个裂纹 进行表征
否
否
是
是
1
2
1 否
是
2 否
是
输出a、c
一条埋藏裂纹、一条表面裂纹表征示意图