第二篇动平衡和转轴校直
电动机常见故障的分析和处理及维护和修理保养

电动机常见故障的分析和处理及维护和修理保养电动机常见故障的分析和处理随着电动机在工矿的广泛使用,电机的维护和修理和保养已经得到了各层领导和技术人员的高度重视,只有加强电动机的日常维护和修理和保养才能够经济、安全的为社会制造更多的财富。
下文来介绍下故障及维护和修理方法:一、电动机常见故障的分析和处理(一)接通后,电动机不能起动,但有嗡嗡声可能原因:(1)电源没有全部接通而形成缺相起动;(2)电动机过载;(3)被拖动机械卡住;(4)绕线式电动机转子回路开路成断线;(5)定子内部首端位置接错,或有断线、短路。
处理方法:(1)检查电源线,电动机引出线,熔断器,开关的各对触点,找出断路位置,予以排出;(2)卸载后空载或半载起动;(3)检查被拖动机械,排出故障;(4)检查电刷,滑环和起动电阻各个的接合情况;(5)重新判定三相的首尾端,并检查三相绕组是否有断线和短路。
(二)电动机起动困难,加额定负载后,转速较低可能原因:(1)电源电压较低;(2)原为角接误接成星接;(3)鼠笼型转子的笼条端脱焊,松动或断裂。
处理方法:(1)提高电压;(2)检查铭牌接线方法,改正定子绕组接线方式;(3)进行检查后并对症处理。
(三)电动机起动后发热超过温升标准或冒烟可能原因:(1)电源电压过低,电动机在额定负载下造成温升过高:(2)电动机通风不良或环境湿度过高;(3)电动机过载或单相运行;(4)电动机起动频繁或正反转次数过多;(5)定子和转子相擦。
处理方法:(1)测量空载和负载电压;(2)检查电动机风扇及清理通风道,加强通风降低环温;(3)用钳型电流表检查各相电流后,对症处理;(4)削减电动机正反转次数,或更换适应于频繁起动及正反转的电动机;(5)检查后对症处理。
(四)绝缘电阻低可能原因:(1)绕组受潮或淋水滴入电动机内部;(2)绕组上有粉尘,油圬;(3)定子绕组绝缘老化。
处理方法:(1)将定子、转子绕组加热烘干处理;(2)用汽油擦洗绕组端部烘干;(3)检查并恢复引出线绝缘或更换接线盒绝缘线板;(4)一般情况下需要更换全部绕组。
传动轴平衡机操作规程范文(三篇)

传动轴平衡机操作规程范文第一章总则第一条根据传动轴平衡机的工作特点和使用要求,制定本操作规程,规范传动轴平衡机的使用和操作,确保设备安全和工作效率。
第二条传动轴平衡机的操作人员应按照本操作规程的要求进行操作,严禁违章作业,确保操作安全。
第三条传动轴平衡机的操作人员应经过专门培训并持有相关操作证书,保证具备操作技能和知识。
第二章操作前的准备工作第四条操作人员应在上岗前对传动轴平衡机进行检查,确保设备的正常工作。
1.检查设备的机械运转部分是否有异常声音或异味。
2.检查设备的电气部分是否正常,电线是否松动、破损等。
3.检查设备的固定螺丝是否紧固,避免设备震动。
4.检查设备上的控制按钮和开关是否正常工作。
5.检查设备的润滑油和冷却液是否充足。
第五条操作人员应穿戴工作服和劳动防护用品,并戴好防护眼镜和耳塞,确保人员的安全。
第六条按照工作要求准备所需的传动轴,包括尺寸和材质要求。
第三章操作流程第七条将待测传动轴放置在传动轴平衡机上,在传动轴两端用夹具将其固定住,确保传动轴的稳定。
第八条操作人员需根据传动轴的尺寸和材质要求设置合适的测试参数。
第九条启动传动轴平衡机,调整传动轴的转速,使之达到设定值。
第十条在传动轴达到设定转速后,通过传感器采集传动轴的振动数据,并将数据传输到计算机进行分析和处理。
第十一条根据计算机分析的结果,判断传动轴是否需要进行平衡调整。
1.如果传动轴的平衡良好,计算机会显示为正常状态,操作人员可继续进行下一轴的测试。
2.如果传动轴的平衡不良,计算机会显示不平衡的程度和位置,操作人员需进行相应的调整。
第十二条在判定传动轴需要进行平衡调整时,操作人员需根据计算机显示的不平衡程度和位置,进行相应的修复。
1.对于小幅度的不平衡,可以通过增加或减少传动轴上的配重块来实现平衡调整。
2.对于较大幅度的不平衡,需要将传动轴取下并进行加工修整,然后再进行平衡调整。
第十三条在进行平衡调整时,操作人员需注意安全,并按照工艺要求进行操作。
传动轴平衡机操作规程(4篇)
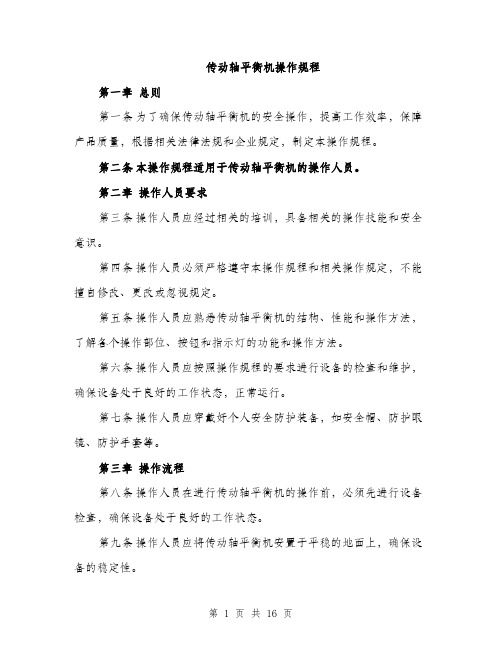
传动轴平衡机操作规程第一章总则第一条为了确保传动轴平衡机的安全操作,提高工作效率,保障产品质量,根据相关法律法规和企业规定,制定本操作规程。
第二条本操作规程适用于传动轴平衡机的操作人员。
第二章操作人员要求第三条操作人员应经过相关的培训,具备相关的操作技能和安全意识。
第四条操作人员必须严格遵守本操作规程和相关操作规定,不能擅自修改、更改或忽视规定。
第五条操作人员应熟悉传动轴平衡机的结构、性能和操作方法,了解各个操作部位、按钮和指示灯的功能和操作方法。
第六条操作人员应按照操作规程的要求进行设备的检查和维护,确保设备处于良好的工作状态,正常运行。
第七条操作人员应穿戴好个人安全防护装备,如安全帽、防护眼镜、防护手套等。
第三章操作流程第八条操作人员在进行传动轴平衡机的操作前,必须先进行设备检查,确保设备处于良好的工作状态。
第九条操作人员应将传动轴平衡机安置于平稳的地面上,确保设备的稳定性。
第十条操作人员应按照所需平衡参数进行设定,确保平衡精度和平衡时间的要求。
第十一条在操作时,操作人员应注意观察设备的运行情况,如发现异常情况应及时停机检查。
第十二条操作人员应严格按照传动轴平衡机的操作程序进行操作,不得擅自调整或改变操作参数。
第十三条在操作过程中,操作人员应注意设备运行的状态,确保设备正常运行,避免因操作不当引发事故。
第十四条操作人员在停机前,应将设备恢复到正常状态,清理现场并进行设备的保养工作。
第四章安全措施第十五条操作人员在进行传动轴平衡机的操作前,应了解设备的安全操作规程,并按照规程执行。
第十六条操作人员应加强对传动轴平衡机的安全保护措施,如加装安全防护网、安装急停按钮等。
第十七条操作人员在操作过程中应保持注意力集中,不得分散注意力。
禁止喧哗、闲聊等影响操作安全的行为。
第十八条操作人员应按照规定使用个人防护装备,并对装备进行定期检查和更换。
第十九条操作人员应将设备清理干净,清除杂物和油污,确保设备的干净整洁。
《机械设计基础》-题库

《机械设计基础》一.填空题:1.机械设计课程主要讨论通用机械零件和部件的设计计算理论和方法。
2.机械零件设计应遵循的基本准则:强度准则、刚度准则、耐磨性准则、震动稳定性准则。
3.强度:零件抵抗破裂(表面疲劳、压溃、整体断裂)及塑性变形的能力。
1.所谓机架是指机构中作为描述其他构件运动的参考坐标系的构件。
2.机构是机器中的用以传递与转换运动的单元体;构件是组成机构的运动单元;零件组成机械的制造单元。
3.两构件组成运动副必须具备的条件是两构件直接接触并保持一定的相对运动。
4.组成转动副的两个运动副元素的基本特征是圆柱面。
5.两构件通过面接触而形成的运动副称为低副,它引入2个约束,通过点线接触而构成的运动副称为高副,它引入1个约束。
6.机构的自由度数等于原动件数是机构具有确定运动的条件。
7.在机构运动简图上必须反映与机构运动情况有关的尺寸要素。
因此,应该正确标出运动副的中心距,移动副导路的方向,高副的轮廓形状。
1.铰链四杆机构若最短杆与最长杆长度之和小于等于其余两杆长度之和则可能存在曲柄。
其中若最短杆是连架杆,则为曲柄摇杆机构;若最短杆是连杆,则为双摇杆机构;若最短杆是机架,则为双曲柄机构;若最短杆与最长杆长度之和大于其余两杆长度之和则不存在曲柄(任何情况下均为双摇杆机构)2.最简单的平面连杆机构是两杆机构。
3.为保证连杆机构传力性能良好,设计时应使最小传动角γmin≥[γ]4.机构在死点位置时的传动角γ=0°.5.平面连杆机构中,从动件压力角α与机构传动角γ之间的关系是α+γ=90°.6.曲柄摇杆机构中,必然出现死点位置的原动件是摇杆。
7.曲柄滑块机构共有6个瞬心。
8.当连杆机构无急回运动特性时行程速比系数K=1.9.以曲柄为主动件的曲柄摇杆机构、曲柄滑块机构中,可能出现最小传动角的位置分别是曲柄与机架共线、曲柄两次垂直于滑块导路的瞬时位置,而导杆机构λ始终是90°1.凸轮的基圆半径是指凸轮转动中心至理论廓线的最小半径。
传动轴平衡机操作规程
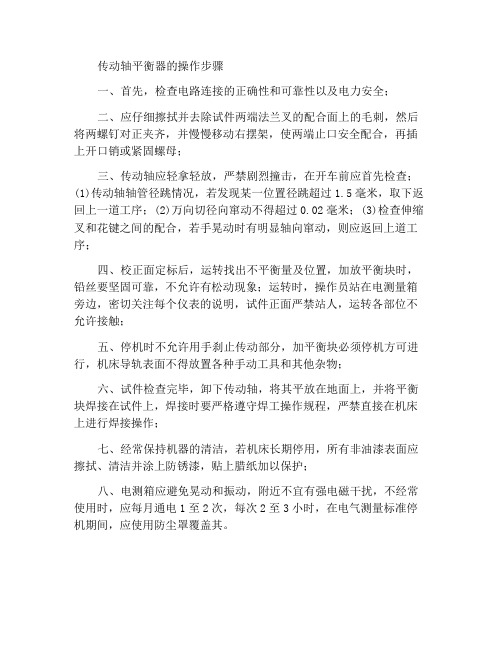
传动轴平衡器的操作步骤
一、首先,检查电路连接的正确性和可靠性以及电力安全;
二、应仔细擦拭并去除试件两端法兰叉的配合面上的毛刺,然后将两螺钉对正夹齐,并慢慢移动右摆架,使两端止口安全配合,再插上开口销或紧固螺母;
三、传动轴应轻拿轻放,严禁剧烈撞击,在开车前应首先检查;
(1)传动轴轴管径跳情况,若发现某一位置径跳超过1.5毫米,取下返回上一道工序;(2)万向切径向窜动不得超过0.02毫米;(3)检查伸缩叉和花键之间的配合,若手晃动时有明显轴向窜动,则应返回上道工序;
四、校正面定标后,运转找出不平衡量及位置,加放平衡块时,铅丝要坚固可靠,不允许有松动现象;运转时,操作员站在电测量箱旁边,密切关注每个仪表的说明,试件正面严禁站人,运转各部位不允许接触;
五、停机时不允许用手刹止传动部分,加平衡块必须停机方可进行,机床导轨表面不得放置各种手动工具和其他杂物;
六、试件检查完毕,卸下传动轴,将其平放在地面上,并将平衡块焊接在试件上,焊接时要严格遵守焊工操作规程,严禁直接在机床上进行焊接操作;
七、经常保持机器的清洁,若机床长期停用,所有非油漆表面应擦拭、清洁并涂上防锈漆,贴上腊纸加以保护;
八、电测箱应避免晃动和振动,附近不宜有强电磁干扰,不经常使用时,应每月通电1至2次,每次2至3小时,在电气测量标准停机期间,应使用防尘罩覆盖其。
发动机曲轴毕业论文

成都工业学院毕业设计(论文)设计(论文)题目:发动机曲轴工艺设计及钻中心孔夹具和钻斜油孔夹具设计系部名称:机电工程系专业:数控技术专业班级:09423学生姓名:学号:指导教师:二O一二年五月摘要曲轴是发动机上的一个重要的旋转机件,装上连杆后,可承接活塞的上下(往复)运动变成循环运动。
曲轴主要有两个重要加工部位:主轴颈和连杆颈。
主轴颈被安装在缸体上,连杆颈与连杆大头孔连接,连杆小头孔与汽缸活塞连接,是一个典型的曲柄滑块机构。
发动机工作过程就是:活塞经过混合压缩气的燃爆,推动活塞做直线运动,并通过连杆将力传给曲轴,由曲轴将直线运动转变为旋转运动。
而曲轴加工的好坏将直接影响着发动机整体性能的表现。
曲轴的材料一般为35、40、45钢或球墨铸铁QT600-2,曲轴有两个重要部位:主轴颈,连杆颈。
本次采用45钢,设计的主要就是这两方面的在数控机床的加工。
集合多种的曲轴加工后,深入分析了曲轴的加工工艺。
关键词:曲轴主轴劲夹具连杆劲数控加工AbstractThe crankshaft is an important engine rotating parts, fitted with linking, you can undertake up and down the piston (reciprocating) motion into circular motion. The crankshaft main two important processing areas: the main journal and rod neck. Spindle neck to be installed on the cylinder block, connecting rod journal and connecting rod hole connection, connect the connecting rod small end hole and the cylinder piston, is a typical slider-crank mechanism. Engine working process: the piston after the blasting of the mixed compressed gas pushes the piston linear motion and force to the crankshaft through the connecting rod, the linear motion into rotary motion by the crankshaft. The crankshaft processing will directly affect the overall performance of the engine performance. The material of the crankshaft is made of carbon structural steel or ductile iron, there are two important areas: the main journal rod neck. This paper introduces the fixture design of the engine crankshaft process design of the two processes. Ensure product quality, increase productivity, reduce costs, make full use of the existing production conditions to ensure workers have designed under the premise of a good and safe working conditions. In process design, the author combines practical theory of design, traditional crankshaft production process improvements, optimizing processes and process equipment, production and processing more economical and reasonable so that the crankshaft. Fixture design part of the collection of processing machine tools, cutting tools and auxiliary tools and other relevant information used based on the workpiece material, structural features, technical requirements and process analysis, in accordance with the fixture design steps to design a line with the crankshaft production process and fixture manufacturing requirements of the fixture.目录摘要 (I)Abstract (II)目录..................................................................................................................................................... 第1章绪论.. (1)1.1 课题研究的意义及现状 (1)1.2 论文主要研究内容 (2)第2章发动机曲轴零件图分析 (3)2.1曲轴的作用分析 (3)2.2曲轴的结构及其特点 (3)2.3曲轴的主要技术要求分析 (4)2.4曲轴的材料和毛坯的确定 (4)第3章工艺规程设计 (5)3.1 计算生产纲领,确定生产类型 (5)3.2 选择毛坯 (5)3.3 工艺过程设计 (5)3.3.1定位基准的选择 (5)3.3.2加工阶段的划分与工序顺序的安排 (6)3.3.3制定工艺路线 (7)3.4 确定加工余量 (10)3.4.1确定机械加工余量 (11)3.4.2设计毛坯图(一)确定毛坯尺寸公差 (12)3.5重要工序设计 (15)3.5.1选择加工设备和工艺装备 (15)3.6 确定切削用量及基本工时 (17)3.6.1曲轴主要加工表面的工序安排 (17)3.6.2确定工时定额 (17)3.6.3粗磨第一主轴颈和齿轮轴颈 (19)3.6.4精车二、三、五、主轴颈、油封轴颈、法兰 (19)3.6.5切槽 (20)3.6.6精车第三主轴颈及过渡圆角 (20)第4章夹具设计 (24)4.1 机床夹具的分类、基本组成和功用 (24)4.2发动机曲轴夹具的设计思路 (24)4.2.1形状复杂 (24)4.2.2刚性差 (24)4.2.3技术要求高 (25)4.3铣曲轴两端面打中心孔夹具 (25)4.3.1零件的工艺性分析: (25)4.3.2零件机械加工工艺路线制定: (25)4.3.3夹具结构方案确定 (27)4.3.4其它装置和夹具体确定 (29)4.3.5定位误差分析计算 (31)4.3.6夹具结构及操作介绍 (33)4.3.7本设计的主要优缺点 (34)总结....................................................................................................................错误!未定义书签。
精品课件- 机械的平衡及调节
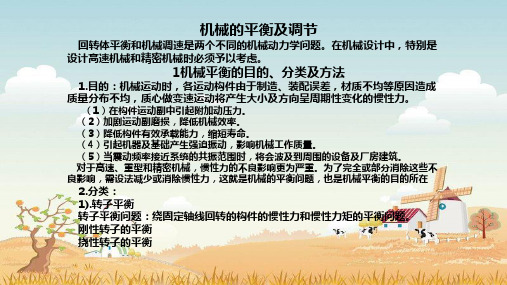
二、机械运转的平均速度和不均匀系数 若已知机械主轴角速度随时间变化的规律时,一个周期角速度的实现平均值 ωm为: ωm=(ωmin+ωmax)/2; δ=(ωmax-ωmin)/ωm
一定时,δ越小,表示机械运转越均匀,运转的平稳性越好。不同机械其运动平 稳性的要求不同,许用不均匀系数[δ]也不同。各种不同的机械对速度的波动有 不同的要求,即根据设计要求规定不同的不均匀系数δ的许用值。几种常见机械 的不均匀系数的取值范围见表7—2。
机构的平衡:为了减小或消除机构中各构件的惯性力和惯性力矩所引起的 振动、附加动压力和减小输入转矩波动而采用的改善质量分布、附加机构 等的措施,称为机构的平衡,如内燃机曲柄连杆机构等的平衡。
3.研究机械平衡的方法 计算法: 图解法与解析法。图解法简单方便;解析法计算结果准确,它们皆用在各 不平衡质量大小及质心位置已知的情况下。 试验法则适用于各平衡质量大小及质心位置未知的情况下或虽经计算法加 平衡配重平衡,但实际由于材质不衡之。 这里主要阐述图解法。
三、飞轮设计简介
1.飞轮设计的基本原理
飞轮的调速是利用它的储能作用,在机械系统出现盈功时,吸收储存多余能量
,而在出现亏功时释放其能量,以弥补能量的不足,从而使机械的角速度变化幅
度得以缓减,即达到调节作用。
当机械系统的等效构件上装加一个转动惯量为 J f的飞轮之后,需飞轮储存的
最大盈亏功为Wmax=Emax-Emin,其等效构件的速度不均匀系数则为 δ=
2.分类:根据转子不平衡质量的分布情况,转子的平衡可分为静平衡和动平衡。 1).静平衡
对于轴向尺寸较小的零件,也称为盘状零件(直径D与宽度L之比::D/ L≥5),如飞 轮、砂轮等,其质量分布可以近似认为在同一回转面内。当回转件匀速转动时,各质量所 产生的离心力构成同一平面内交于回转中心点的力系。如果该力系不平衡,则它们的合力 不等于零。为了使力系达到平衡,只需在同一平面内加上一个平衡质量,使其所产生的离 心力等于原离心力的合力且方向相反。这样,加上一个平衡质量后,由回转件上各质量所 产生的离心力组成的力系就达到平衡。这种平衡称静平衡。
动平衡与静平衡在选粉机中的选择
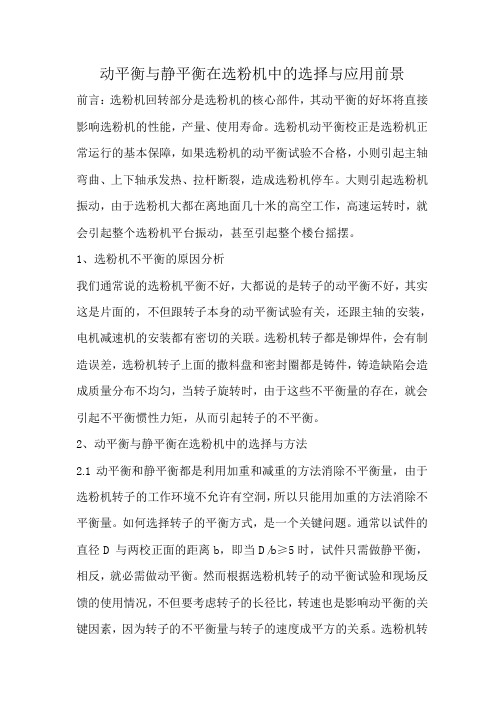
动平衡与静平衡在选粉机中的选择与应用前景前言:选粉机回转部分是选粉机的核心部件,其动平衡的好坏将直接影响选粉机的性能,产量、使用寿命。
选粉机动平衡校正是选粉机正常运行的基本保障,如果选粉机的动平衡试验不合格,小则引起主轴弯曲、上下轴承发热、拉杆断裂,造成选粉机停车。
大则引起选粉机振动,由于选粉机大都在离地面几十米的高空工作,高速运转时,就会引起整个选粉机平台振动,甚至引起整个楼台摇摆。
1、选粉机不平衡的原因分析我们通常说的选粉机平衡不好,大都说的是转子的动平衡不好,其实这是片面的,不但跟转子本身的动平衡试验有关,还跟主轴的安装,电机减速机的安装都有密切的关联。
选粉机转子都是铆焊件,会有制造误差,选粉机转子上面的撒料盘和密封圈都是铸件,铸造缺陷会造成质量分布不均匀,当转子旋转时,由于这些不平衡量的存在,就会引起不平衡惯性力矩,从而引起转子的不平衡。
2、动平衡与静平衡在选粉机中的选择与方法2.1动平衡和静平衡都是利用加重和减重的方法消除不平衡量,由于选粉机转子的工作环境不允许有空洞,所以只能用加重的方法消除不平衡量。
如何选择转子的平衡方式,是一个关键问题。
通常以试件的直径D与两校正面的距离b,即当D/b≥5时,试件只需做静平衡,相反,就必需做动平衡。
然而根据选粉机转子的动平衡试验和现场反馈的使用情况,不但要考虑转子的长径比,转速也是影响动平衡的关键因素,因为转子的不平衡量与转子的速度成平方的关系。
选粉机转子的直径大都从φ300至φ5500,高度从300至3000,转速从80r/min 至270r/min,当D/b≥5时,且转速低于120r/min时,可以做静平衡;当D/b<5时,或者转速≥120r/min时,必须做动平衡;当不平衡量很大时,需要先做静平衡,再做动平衡试验。
2.2静平衡方法:静平衡试验比较简单,在厂内做个旋转平台,试验时,将转子至于平台上,人工拨动转子旋转,当转子停止时,如果转子不平衡,则偏心引起的重力矩将使转子向一边倾斜,这时在转子倾斜的对面加适当的配重,再拨动转子重复试验,直到转子不再向一边倾斜为止。
第二篇 动平衡和转轴校直.
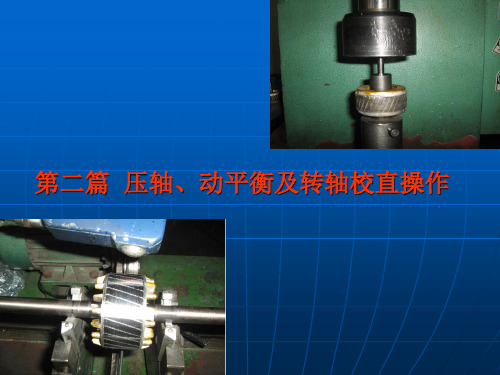
B、操作
1、将转轴一端放进铸铝转子铁芯孔后,一起放在底座的下 压头上,注意放正后,再放上压头;
2、用脚踩油压机脚踏开关,压机压头压下,将转轴压下到 位; 3、 压机压头回程后,按顺序取下上压头,转子,将转子放 在流转板上。 注:转子压转轴后,按图要求必须检测静压力(特殊客户 要求:300mm跌落试验)。
二、工艺规范
1.操作时不得损伤轴承档表面、轴头螺纹;
2.跳动合格与跳动不合格的转子不得混放; 3.跳动不合格的应放在红盘里;
4.测量点应控制在轴端5-20mm尺寸内(螺纹 段不包括在内); 5.操作前用油布将V型块支承面擦试干净。
三、工序质量控制内容
检查频次与控制手段 检查项目 精度范围 测量工具 首检 自检 互检 巡检
1. 2. 3. 4. 5. 6. 7. 8.
做前检查设备是否完好,并做好点检; 未经同意严禁擅自改动设备内部程序; 注意控制箱显示值,异常情况及时反馈; 读取显示器上的数值应为稳定值; 反光灯应能稳定取值; 平衡机支承架应锁紧; 平衡机每月用标准转子校准一次; 测量加工达到要求的转子用压缩空气去除铁 屑;
B、操作
1. 将转子置于平衡机上,根据转子外径大小 8395系列转子可采用皮带压转子图2;110-140 系列转子可采用转子压皮带。图3,并在转子的 右边任一圆周上贴反光纸;
2.启动电机,使转子旋转,同时将反光灯垂直对准 反光纸,灯距离转子一定尺寸,观察绿灯显示稳 定进入正常测试;
3.当显示器上显示数值后,停机,读出锁定的不平衡 量及相应的角度后,找准位置待去重或加重。
去掉飞边、铁屑, 涂上防锈油
5.加重法: ①根据不平衡的大小、位置在平衡柱上加上 1-2片专用铁片。加上铁片后需用榔头将 垫片铆住,不能有松动与脱落现象。注: 铆接时专用垫片不能超出转子外圆、不能 碰伤风叶。
三相异步电动机的启动方法 三相异步电动机常见问题解决方法
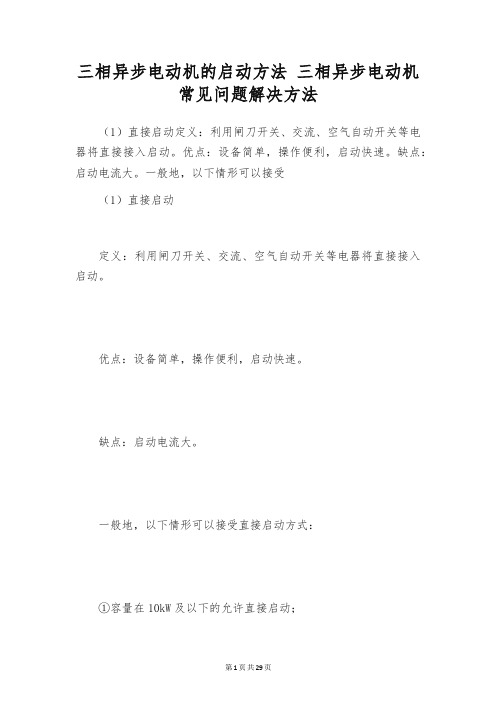
三相异步电动机的启动方法三相异步电动机常见问题解决方法(1)直接启动定义:利用闸刀开关、交流、空气自动开关等电器将直接接入启动。
优点:设备简单,操作便利,启动快速。
缺点:启动电流大。
一般地,以下情形可以接受(1)直接启动定义:利用闸刀开关、交流、空气自动开关等电器将直接接入启动。
优点:设备简单,操作便利,启动快速。
缺点:启动电流大。
一般地,以下情形可以接受直接启动方式:①容量在10kW及以下的允许直接启动;②启动时,电动机的启动电流在供电线路上引起的电压降不超过正常电压的,假如没有独立变压器(与照明共用),则不应超过;③用户有独立的变压器供电时,频繁启动的电动机容量小于变压器容量的时允许直接启动;不频繁启动时电动机容量小于变压器的时允许直接启动。
(2)降压启动当电动机的容量较大,电源容量不能充分直接启动要求时,为了减小,常用此法。
定义:利用启动设备,在启动时降低加在定子绕组上的电压,当电动机的转速接近额定转速时,再全电压(额定电压)运行。
适用于启动时负载转矩不大的情况。
—专业分析仪器服务平台,试验室仪器设备交易网,仪器行业专业网络宣扬媒体。
相关热词:等离子清洗机,反应釜,旋转蒸发仪,高精度温湿度计,露点仪,高效液相色谱仪价格,霉菌试验箱,跌落试验台,离子色谱仪价格,噪声计,高压灭菌器,集菌仪,接地电阻测试仪型号,柱温箱,旋涡混合仪,电热套,场强仪万能材料试验机价格,洗瓶机,匀浆机,耐候试验箱,熔融指数仪,透射电子显微镜。
三相异步电动机常见故障及处理方法一、电动机起动困难,额定负载时,电动机转速低于额定转速较多1、故障原因①电源电压过低;②三角形接法误接为Y;③笼型转子开焊或断裂;④绕线电动机的集电环与电刷接触不良,从而使接触电阻增大损耗增大,输出功率削减;⑤电源缺相;⑥电机过载;⑦绕线电动机转子回路串电阻过大。
2、故障排出①测量电源电压,设法改善;②矫正接法;③检查开焊和断点并修复;④调整电刷压力,用细砂布磨好电刷与集电环的接触面;⑤对于由于熔断器断路显现的断相运行,应先检查出原因,然后更换熔断器熔丝;⑥减载;⑦适当减小转子回路串接的变阻器阻值。
动平衡基本知识和操作经验
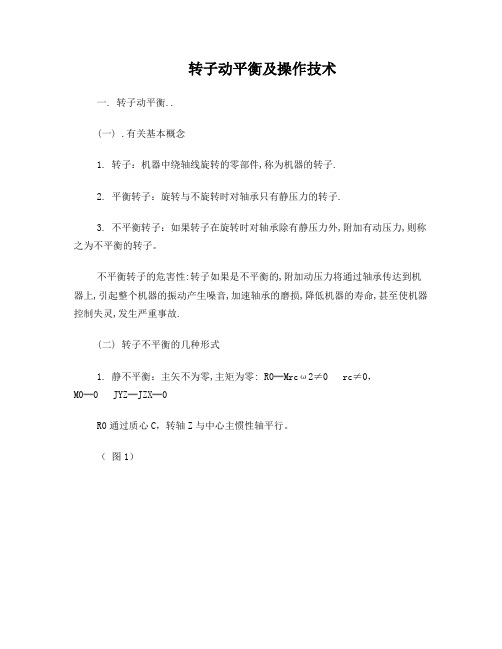
转子动平衡及操作技术一. 转子动平衡..(一) .有关基本概念1. 转子:机器中绕轴线旋转的零部件,称为机器的转子.2. 平衡转子:旋转与不旋转时对轴承只有静压力的转子.3. 不平衡转子:如果转子在旋转时对轴承除有静压力外,附加有动压力,则称之为不平衡的转子。
不平衡转子的危害性:转子如果是不平衡的,附加动压力将通过轴承传达到机器上,引起整个机器的振动产生噪音,加速轴承的磨损,降低机器的寿命,甚至使机器控制失灵,发生严重事故.(二) 转子不平衡的几种形式1. 静不平衡:主矢不为零,主矩为零: R0═Mrcω2≠0rc≠0,M0═0JYZ═JZX═0R0通过质心C,转轴Z与中心主惯性轴平行。
(图1)2. 准静不平衡:主矢和主矩均不为零,但相互垂直R0═Mrcω2≠0,M0═0JYZ═JZX═0, R0不通过质心C,转轴Z与中心主惯性轴相交于某一点。
(图2)3. 偶不平衡:主矢为零,主矩不为零R0═0rc═0M0≠0JXZ≠0JYZ≠0(图3)4. 动不平衡:主矢和主矩均不为零且既不相交,又不平行.R0═Mrcω2≠0rc≠0M0≠0JXZ≠0JYZ≠0(图4)5.选择静平衡或动平衡的一般原则当转子外径D与长度L满足D/L≧5时,不论其工作转速高低都只需进行静平衡(如果L/l>2时)当D≤I时,n>1000r/min必须进行动平衡.(特殊要求除外)(三) 动平衡机的工作原理把刚性回转体安装在动平衡机的弹性支承上,使回转体转动.根椐支承的不同情况,(通过回转体的周期性机械振动信号变为电感信号)测量出支承的振动和支反力.用分离解算电路,计算出回转体的不平衡量,再对回转体进行加重或去重,直至平衡量达到要求.1. 软支承动平衡机的分离解算原理刚性回转体动平衡时,任一校正面的不平衡量都会使左,右二支承同时产生振动, α设校正面I上的不平衡量m1r1在左,右支承处引起的振幅分别用αL1mr1和αR1mr1表示;校正面Ⅱ上的不平衡量m2r2在左,右支承处引起的振幅分别用αL2mr2和αR2mr2表示.其中为一组与回转体重量,支承位置,校正面位置及回转体惯性矩等有关的动力影响系数,在实际操作中,可由试验确定.则左,右支承的振幅Vl,VR与不平衡量m1r1,m2r2的关系为:VL═αL1m1r1+αL2m2r2VR=αR1m1r1+αR2m2r2以下两式可联立解出得: m1r1=αR2 VL/?-αL2 VR/?m2r2=αL1VR/?-αR1 VL/?式中:△=αL1 αR2-αL2αR1由算式可知:只要知道四个影响系数,就可以从测得的支承振幅VL和VR算出不平衡量m1r1和m2r2,在动平衡机实际操作中,无需算出四个动力影响系数,只需通过调整电位器W1,W2,W3,W4即可求出m1r1和m2r2(见DRZ—1A)动平衡机操作显示屏示意图.(图5)2. 硬支承动平衡机的分离解算原理在硬支承动平衡机中,不平衡产生的离心力与支承振幅成正比,而且相位相同,因此,对于硬支承动平衡机是通过测量支承反力来确定二校正面上的不平衡量,若二校正面上的不平衡量产生的离心力为FL和FR,则左,右两支承的反力NL和NR,则左,右两支承的反力NL和NR.可由静力学的方法求出.硬支承平衡机的支承关系式如下:FL=fL+1/B(AfL-CfR) FR=fR-1/B(AfL-CfR)(图6)(1) FL=fL+1/B(AfL+CfR) FR=fR-1/B(AfL+CfR)(图7)(2) FL=fL-1/B(AfL+CfR) FR=fR+1/B(AfL+CfR) (图8),(图9)(3) FL=fL+1/B(AfL-CfR) FR=fR+1/B(AfL-CfR)(图10)图中的A,B,C为支承和校正面的位置尺寸.离心力FL和FR仅与支承反力NL和NR及尺寸A,B,C有关.不同的支承形式只改变支反力的运算符号,用传感器测出支反力NL,使用如软支承平衡机类似的分离解算电路,求出离心力FL和FR,再根椐回转体的工作角度ωω 算出左,右校正面上的不平衡量FL/ω和FR/ω(1)~(4)为通常将不平衡量分解到两个校正面上进行平衡校正的方法,而对于直径比(L/D)较小的园盘形回转体,进行两面高精度平衡或检查其单面平衡后的精度,或对装配式回转体(如带叶片轴)进行边装配边平衡则可用静/偶平衡法.3.软支承动平衡机与硬支承动平衡机的比较:(四) 动平衡精度1. 动平衡的定义:不平衡的转子经过测量其不平衡量和不平衡相位,并加以校正以消除其不平衡量,使转子在旋转时,不致产生不平衡离心力的平衡工艺叫做动平衡.2. 转子的平衡精度等级(1) 通过实验(工作状态下),积累资料,对未做规定的某些特殊要求的转子订出可行的平衡精度规范(2)根据eω=G(递减的常数)分级。
传动轴平衡机操作规程范文(二篇)
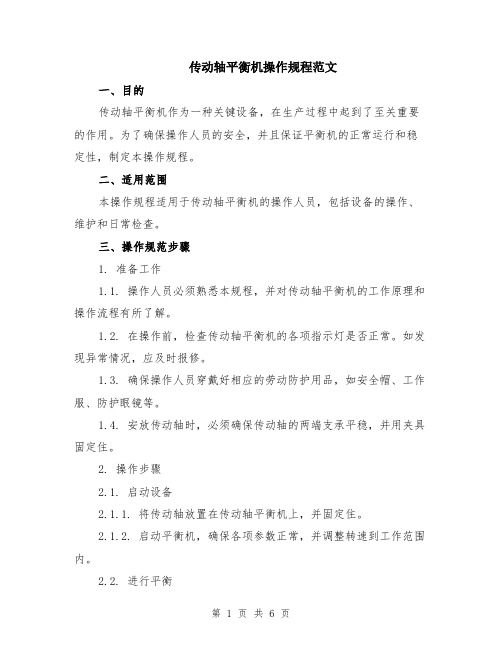
传动轴平衡机操作规程范文一、目的传动轴平衡机作为一种关键设备,在生产过程中起到了至关重要的作用。
为了确保操作人员的安全,并且保证平衡机的正常运行和稳定性,制定本操作规程。
二、适用范围本操作规程适用于传动轴平衡机的操作人员,包括设备的操作、维护和日常检查。
三、操作规范步骤1. 准备工作1.1. 操作人员必须熟悉本规程,并对传动轴平衡机的工作原理和操作流程有所了解。
1.2. 在操作前,检查传动轴平衡机的各项指示灯是否正常。
如发现异常情况,应及时报修。
1.3. 确保操作人员穿戴好相应的劳动防护用品,如安全帽、工作服、防护眼镜等。
1.4. 安放传动轴时,必须确保传动轴的两端支承平稳,并用夹具固定住。
2. 操作步骤2.1. 启动设备2.1.1. 将传动轴放置在传动轴平衡机上,并固定住。
2.1.2. 启动平衡机,确保各项参数正常,并调整转速到工作范围内。
2.2. 进行平衡2.2.1. 根据传动轴的尺寸和重量,调整平衡机的夹具和测量系统,确保能够准确测量传动轴的不平衡度。
2.2.2. 观察传动轴在转动过程中的不平衡情况,根据测量结果,进行动平衡校正。
2.2.3. 完成动平衡校正后,再次检查传动轴的不平衡度。
如仍有不平衡,应再次调整夹具和测量系统进行校正。
2.2.4. 反复操作,直到传动轴符合设定的平衡要求为止。
3. 维护与检查3.1. 操作结束后,关闭传动轴平衡机,切断电源。
3.2. 清理设备的工作区域,移除传动轴和夹具,并将设备恢复到清洁整齐的状态。
3.3. 定期对传动轴平衡机进行检查和维护,确保各项部件和设备的正常运行。
3.4. 特别注意传动轴平衡机的传动系统和润滑系统的保养,及时添加润滑剂和更换磨损的零部件。
四、注意事项和安全预防措施4.1. 操作人员必须按照规程进行操作,不得随意更改设备参数和操作流程。
4.2. 在操作传动轴平衡机过程中,严禁戴手套、长袖衣物和松散物品,以免危及安全。
4.3. 在进行平衡校正时,操作人员应留意设备的指示灯和声光报警器,确保操作的安全性。
机械的平衡及调节

第十四章机械的平衡及调节回转体平衡和机械调速是两个不同的机械动力学问题。
在机械设计中,特别是设计高速机械和精密机械时必须予以考虑。
§14—1机械平衡的目的、分类及方法1.目的:机械运动时,各运动构件由于制造、装配误差,材质不均等原因造成质量分布不均,质心做变速运动将产生大小及方向呈周期性变化的惯性力。
(1)在构件运动副中引起附加动压力。
(2)加剧运动副磨损,降低机械效率。
(3)降低构件有效承载能力,缩短寿命。
(4)引起机器及基础产生强迫振动,影响机械工作质量。
(5)当震动频率接近系统的共振范围时,将会波及到周围的设备及厂房建筑。
对于高速、重型和精密机械,惯性力的不良影响更为严重。
为了完全或部分消除这些不良影响,需设法减少或消除惯性力,这就是机械的平衡问题,也是机械平衡的目的所在2.分类:1).转子平衡转子平衡问题:绕固定轴线回转的构件的惯性力和惯性力矩的平衡问题。
刚性转子的平衡问题:转子转速低于一阶临界转速,挠曲线变形忽略挠性转子的平衡问题:转子转速高于一阶临界转速,其旋转轴线的挠曲线的变形不能忽略。
2).机构平衡机构的平衡问题:对整个机构而言,所有构件的惯性力和惯性力矩,可以合成为通过机构总重心的总惯性力和总惯性力矩。
它们可被部分或完全地平衡。
有关它们的平衡问题即为机构的平衡问题。
机构的平衡:为了减小或消除机构中各构件的惯性力和惯性力矩所引起的振动、附加动压力和减小输入转矩波动而采用的改善质量分布、附加机构等的措施,称为机构的平衡,如内燃机曲柄连杆机构等的平衡。
3.研究机械平衡的方法计算法:图解法与解析法。
图解法简单方便;解析法计算结果准确,它们皆用在各不平衡质量大小及质心位置已知的情况下。
试验法则适用于各平衡质量大小及质心位置未知的情况下或虽经计算法加平衡配重平衡,但实际由于材质不均匀、安装制造误差等原因,往往仍达不到预期的要求时,可用试验法平衡之。
这里主要阐述图解法。
§14—2 转子的平衡一、转子平衡的分类1.概念:由于转子结构不对称、材质不均匀、制造和安装误差等原因,均会引起偏心(质心偏离形心)。
中型电机转轴热校直工艺研究
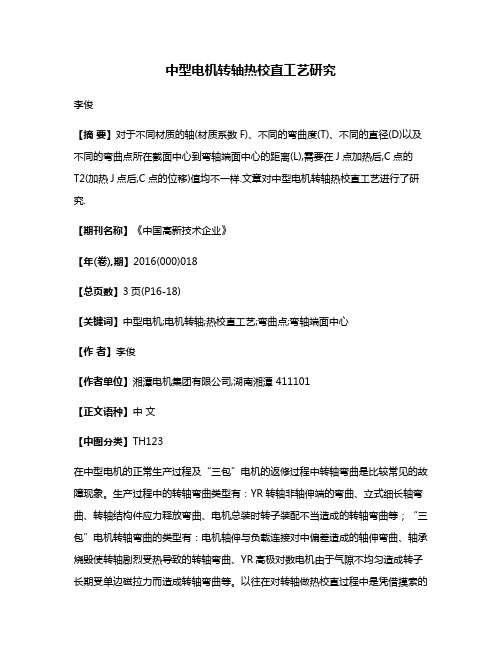
中型电机转轴热校直工艺研究李俊【摘要】对于不同材质的轴(材质系数F)、不同的弯曲度(T)、不同的直径(D)以及不同的弯曲点所在截面中心到弯轴端面中心的距离(L),需要在J点加热后,C点的T2(加热J点后,C点的位移)值均不一样.文章对中型电机转轴热校直工艺进行了研究.【期刊名称】《中国高新技术企业》【年(卷),期】2016(000)018【总页数】3页(P16-18)【关键词】中型电机;电机转轴;热校直工艺;弯曲点;弯轴端面中心【作者】李俊【作者单位】湘潭电机集团有限公司,湖南湘潭 411101【正文语种】中文【中图分类】TH123在中型电机的正常生产过程及“三包”电机的返修过程中转轴弯曲是比较常见的故障现象。
生产过程中的转轴弯曲类型有:YR转轴非轴伸端的弯曲、立式细长轴弯曲、转轴结构件应力释放弯曲、电机总装时转子装配不当造成的转轴弯曲等;“三包”电机转轴弯曲的类型有:电机轴伸与负载连接对中偏差造成的轴伸弯曲、轴承烧毁使转轴剧烈受热导致的转轴弯曲、YR高极对数电机由于气隙不均匀造成转子长期受单边磁拉力而造成转轴弯曲等。
以往在对转轴做热校直过程中是凭借摸索的经验,处理时间长且准确度差,如果有关于转轴热校直的系统指导资料加以参考,将在现场处理中起到多方的促进作用。
通过对2010年生产过程中的电机和“三包”电机转轴弯曲的统计数据来看,正常产品中:YR转轴弯曲的有5台,立式细长轴弯曲的有6台,由于转轴结构件应力释放导致转轴弯曲的有3台,装配不当(使用犁形吊装工具不当)造成转轴弯曲的有2台;“三包”问题中:由于电机与负载连接对中偏差造成转轴弯曲的有8台,烧轴承导致转轴弯曲的有6台。
共合计30台。
如图2所示,C点为百分表测量点,当百分表读数为负的最大值时,即C点为轴端面弯曲的最低点,做好标记。
将百分表向左移动(每次移动30mm),同样找到轴上的最低点,做记号,依次类推,直至百分表显示的跳动量逐渐减小至0.10mm以内,做好标记,该处标记即为加热点J:(1)将百分表打在C处,于J点用气焊枪加热(用外焰加热,不可损伤轴)。
双面动平衡操作步骤及模拟实验

双面动平衡操作步骤及模拟实验之前我们介绍了“单面动平衡操作步骤及模拟实验”,今天我们来做“双面动平衡操作步骤及模拟实验”。
测试环境不变,只需将画面中初始不平衡设定为动不平衡。
双面动平衡操作步骤如下:1、开机,测量初始不平衡。
2、停机,A面加试重,测量试重后A、B两面的振动值。
3、拆除A面试重,在B面加试重,测量试重后A、B两面的振动值。
3、根据YBD-3动平衡仪的计算功能,将初始振动值、两次试重及试重后A、B两面的振动值输入YBD-3动平衡仪,计算配重。
首先,我们测试转子的初始不平衡,可以观察到在动不平衡中,因为质心轴与几何中心轴相交,两侧轴承所测的相位角反相(相差180°)。
记录A面振动值7.05mm/s∠166°与B面振动值5.1mm/s∠344°。
如图1所示。
图1 动不平衡下初始振动值其次,在A面加试重,首先观察初始振动7.05mm/s∠166°,为了不使加试重后的振动量猛增,我们将相位角±180°做为试重的相位,重量首先定为20g,则加重为20g∠345°。
如果试重引起的振动幅值变化没有超过20%或相位变化超过30度,我们就需要调整试重的重量。
在图2中,我们观察到A面加试重后,A面振动值为5.77mm/s∠126°,B面振动值为6.14mm/s∠354°,振幅明显降了下来且振动幅值变化超过20%或相位变化超过30度,此次所加的试重是安全且有效的。
再次,拆除A面试重。
在B面加试重20g∠161°,加试重后A面振动值为9.11mm/s∠176°,B面振动值4.44mm/s∠271°,如图3所示。
图2 A面加试重后振动值图3 B面加试重后振动值最后,汇总YBD-3动平衡仪输入值如下表所示:表1将上表中数据输入YBD-3中进行计算,得到最终的校正质量与相位:A面配重36.78g∠295.02°;B面配重27.58g∠105.60°。