过共晶铝硅合金发动机活塞的挤压铸造工艺研究
内燃机活塞锻造成型技术

1 1 等 温模锻 工 艺的特 点 .
量
等 温模锻 工艺 是针 对传 统热 变形 的不 足而逐 渐
发展 起来 的一 种材 料 加 工 新 工 艺 , 等温 成 型 方 法 是
通过 模具 和坯 料在 变形 过程 中保 持 同一 温度 来实 现
的 , 有 如下 特点 : 具
收 稿 日期 :0 1— 1—2 21 0 7
性 的难 变形 材料 4 1 合金 活塞 “ 火 ” A1 铝 一 成型 成 为
可能 。
密 , 仅力 学性 能有所 提 高 , 不 导热 和抗 高压 能力 也 明 显 增 强 , 加 了活塞工 作 的可靠 性 。 增 发动机 的未来发 展方 向是 高动力 输 出和低 燃油 耗 。对 于 汽油 机活 塞 而 言 , 造铝 活 塞 是 未来 的发 锻 展方 向和 目标 , 而对 于 重 型 车 用 和大 功 率 内燃 机 车
柴油机 而 言 , 了适应 高爆 发压 力 ( 为 大于 2 a 的 0 MP ) 需要 , 锻钢 活塞 会逐渐 成 为设计 的 主流 。
() 3 锻件 质 量 好 。等 温 成 型 时 , 于坯 料 变 形 由
温度基 本保 持恒 定 , 料 内温度分 布 比较均 匀 , 良 坯 在 好 的润滑条 件下 , 可使 坯料 变形 均匀 , 因而锻 件组 织
接 影 响到整 个 发动 机 的性 能 。 目前 , 塞 的成 型 方 活 式 主要 有重 力铸 造 、 力铸 造 、 造等 。铸 造容 易产 压 锻 生疏 松 、 孔及偏 析 等缺 陷 。与 铸造 工艺 相 比 , 缩 锻造 活塞 经塑性 加工 成 型 , 粒 可 以得 到 细 化 且呈 流 线 晶 分布 , 材料 内部 孔 隙等 缺 陷 被焊 后 内部 组 织更 加 致
挤压铸造双金属复合材料成型工艺及性能分析

世界有色金属 2023年 5月上10冶金冶炼M etallurgical smelting挤压铸造双金属复合材料成型工艺及性能分析户 芳,高秀峰,叶 云(山西晋中理工学院,山西 晋中 030600)摘 要:双金属复合材料是一种具有高利用率、综合性能优于其它金属材料的新型浇铸材料,为此,本文对挤压铸造工艺和性能进行了分析。
首先,通过对双金属复合材料的模态结构的建模、固液复合度的控制、双金属材料的包覆温度和退温成型等方面的研究,而后对其成型过程进行了分析,最后再对其导电性、轻量化等方面作了较为深入的研究。
关键词:复合材料;性能分析;挤压铸造;成型工艺中图分类号:TG249.2 文献标识码:A 文章编号:1002-5065(2023)09-0010-3Forming Technology and Performance Analysis of Squeeze Casting Bimetal CompositesHU Fang, GAO Xiu-feng, YE Yun(Shanxi Jinzhong Institute of Technology,Jinzhong 030600,China)Abstract: Bimetal composite material is a new type of casting material with high utilization rate and better comprehensive performance than other metal materials. Therefore, the squeeze casting process and performance are analyzed in this paper. First of all, through the research on the modeling of the modal structure of the bimetallic composite, the control of the solid-liquid composite, the coating temperature of the bimetallic material and the annealing molding, the molding process is analyzed, and finally, the conductivity and lightweight of the bimetallic composite are further studied.Keywords: composite materials; Performance analysis; Squeeze casting; Forming process收稿日期:2023-03作者简介:户芳,女,生于1988年,汉族,山东曹县人,硕士研究生,助教,研究方向:材料成型。
复杂结构ADC12_铝合金汽车支架挤压铸造工艺参数优化

精 密 成 形 工 程第15卷 第11期132 JOURNAL OF NETSHAPE FORMING ENGINEERING2023年11月收稿日期:2023-05-16 Received :2023-05-16基金项目:国家重点研发计划(2019YFB2006503);黑龙江省科技重大专项(2021ZX05A02)Fund :National Key R&D Program of China (2019YFB2006503); Major Science and Technology Project of Heilongjiang Prov-ince (2021ZX05A02)引文格式:朴俊杰, 姜博, 胡茂良, 等. 复杂结构ADC12铝合金汽车支架挤压铸造工艺参数优化[J]. 精密成形工程, 2023, 15(11): 132-139.PIAO Jun-jie, JIANG Bo, HU Mao-liang, et al. Optimization of Squeeze Casting Process Parameters for ADC12 Aluminum Alloy Automobile Support with Complex Structure[J]. Journal of Netshape Forming Engineering, 2023, 15(11): 132-139. *通信作者(Corresponding author )复杂结构ADC12铝合金汽车支架挤压铸造工艺参数优化朴俊杰1a ,姜博1a,1b*,胡茂良1a ,王晔1a ,吉泽升1a,2,SUGIYAMA Sumio 3,许红雨1a ,王云龙2,张永冰2(1.哈尔滨理工大学 a.材料科学与化学工程学院 b.先进制造智能化技术教育部重点实验室,哈尔滨 150080;2.哈尔滨吉星机械工程有限公司,哈尔滨 150060;3.东京大学 生产技术研究所,东京 153-8505) 摘要:目的 解决ADC12铝合金汽车发动机支架在挤压铸造成形工艺下的缺陷问题。
不同压力下挤压铸造铝铜合金的组织与性能

铸造
李彦霞等:不同压力下挤压铸造铝铜合金的组织与性能
・ 765・
压速度为 0.03 "0.06 m/s,保压 30 s 左右至铸件完全凝 固。 将铸件切割并切削成圆棒试样 (GB/T228 !1976), 金相试样取样位置如图 1 所示。每个铸件取 3 个试样, 部分做热处理,固溶采用 ( 490 !5 ) # 保温 8 h,室温
关键词:挤压铸造;铝铜合金;力学性能;显微组织 中图分类号:TG 249. 2;TG 291 文献标识码:A 文章编号:1001-4977 ( 2005 ) 08-0764-03
LI Ya n-xia , NGAI Tungwa i, ZHAO Ha i-dong, ZHANG We i-we n, LI Yua n-yua n (Adva nce d Me ta llic Ma te ria ls Re s e a rch a nd P roce s s ing Te chnology Ke y La bora tory of Gua ngdong P rovince , S outh China Unive rs ity of Te chnology, Gua ngzhou 510640, Gua ngdong, China ) S que e ze ca s ting proce s s wa s us e d to produce a ne wly de ve lope d high s tre ngth a nd high !"#$%&’ ( ) *+,-. / 01234 567 8 9:;< => ?@ AB C DEFGH I JK L MNOPQRSTU VW XYZ [\ ] ^_ ‘abcdefg hijk lmn o pqrstuv w xy z{| }~ ¡¢£ ¤ ¥¦§¨© ª«¬ ® ¯°± ²³´µ¶ ·¸ ¹º » ¼½¾¿ÀÁ  ÃÄ ÅÆÇ È É ÊËÌ Í Î Ï ÐÑ ÒÓ ÔÕ Ö ×ØÙÚÛ Ü ÝÞ ß àáâãäåæçèé êë ìí îï ðñòóô õö÷ øùúû üý þÿ !"# $ %&’ ()* +,- . / 0123 45 6 789: ; <=> ?@A B CDE FGHIJK LM NO PQ RST U VWX YZ[\] ^ _‘abc defg h ij klmn opq rs tuv w x yz{ | } ~ ca s tings incre a s e with the a pplie d pre s s ure a nd re a che d a ma ximum a t a pre s s ure of 50 MP a , re s pe ctive ly, but the ha rdne s s of the a lloy without s que e ze pre s s ure is highe r tha n tha t of thos e s que e ze ca s ts . The gra in s ize a nd the de ndrite a rm s pa cing de cre a s e a nd more de ndrite s a ppe a r with the incre a s e of a pplie d pre s s ure . s que e ze ca s ting; Al-Cu a lloy; me cha nica l prope rty; micros tructure
挤压铸造
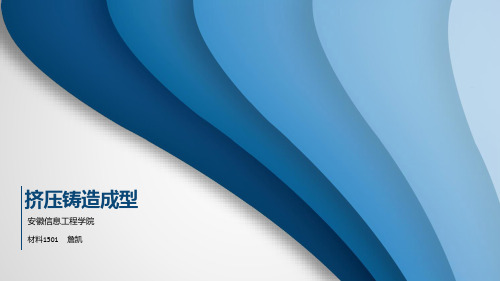
挤压铸造成型
3.在挤压铸造工艺中应用人工神经网络 挤压铸造工艺参数的确定主要靠经验,而且这些参数很难确定,人 工神经网络是一个比较新的学科,在非线性系统、错误诊断、预测、 自适应控制等方面已取得了很大成功。但我国才刚刚起步,应加强 对人工神经网络预测挤压铸造工艺参数的研究。
挤压铸造成型
应用实例:
挤压铸造成型
7.铸型涂料 为了防止铸件黏焊铸型,使铸件能顺利地从型腔中取出,以降低铸件表
面粗糙度,提高铸型的寿命,减缓金属液在加压前的结壳速度,以利于金 属液在压力下充型,在挤压铸型的表面一般都必须喷涂涂料。在挤压铸造 中不能采用涂料层来控制铸件的凝固,因为施加在金属液上的高压将使涂 料层剥落,引起铸件产生夹杂缺陷,为此,采用50μm左右的薄层涂料。。
挤压铸造成型
适用范围:
1、在材料种类方面适用性较广,可用于生产各种类型的合金,如铝合 金、锌合金、铜合金、灰铸铁、球墨铸铁、碳钢、不锈钢等。
2、对于一些复杂且性能上有一定要求的零件,采用挤压铸造合适。 因为挤压铸造既能容易成形,又能保证产品性能的要求。
3、在工件壁厚方面,一般来讲不能太薄,否则将给成形带来困难。
挤压铸造成型
1.工艺原理及特点 (1)工艺原理 将一定量的液体金属(或半固态金属)浇入金属
型腔内,通过冲头以高压(50〜100MPa)作用于液体金属上, 使之充型、成形和结晶凝固,并产生一定塑性形变,从而获得优 质铸件。
(a)熔化
(b)充型
(c)挤压
(d)顶出铸件
挤压铸造成型
(2)工艺特点 适用的材料范围较宽,不仅是普通铸造合金,也适用于高性能的变形合金,
挤压铸造成型
安徽信息工程学院 材料1501 詹凯
目录
挤压模具资料
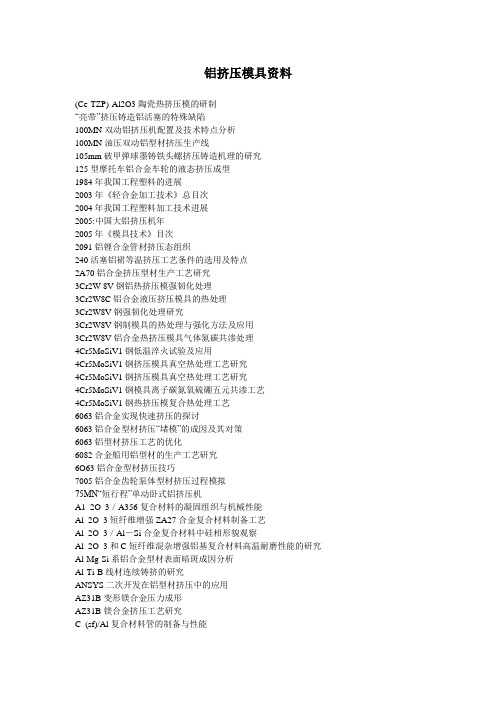
铝挤压模具资料(Ce-TZP)-Al2O3陶瓷热挤压模的研制“亮带”挤压铸造铝活塞的特殊缺陷100MN双动铝挤压机配置及技术特点分析100MN油压双动铝型材挤压生产线105mm破甲弹球墨铸铁头螺挤压铸造机理的研究125型摩托车铝合金车轮的液态挤压成型1984年我国工程塑料的进展2003年《轻合金加工技术》总目次2004年我国工程塑料加工技术进展2005:中国大铝挤压机年2005年《模具技术》目次2091铝锂合金管材挤压态组织240活塞铝裙等温挤压工艺条件的选用及特点2A70铝合金挤压型材生产工艺研究3Cr2W 8V钢铝热挤压模强韧化处理3Cr2W8C铝合金液压挤压模具的热处理3Cr2W8V钢强韧化处理研究3Cr2W8V钢制模具的热处理与强化方法及应用3Cr2W8V铝合金热挤压模具气体氮碳共渗处理4Cr5MoSiV1钢低温淬火试验及应用4Cr5MoSiV1钢挤压模具真空热处理工艺研究4Cr5MoSiV1钢挤压模具真空热处理工艺研究4Cr5MoSiV1钢模具离子碳氮氧硫硼五元共渗工艺4Cr5MoSiV1钢热挤压模复合热处理工艺6063铝合金实现快速挤压的探讨6063铝合金型材挤压“堵模”的成因及其对策6063铝型材挤压工艺的优化6082合金船用铝型材的生产工艺研究6O63铝合金型材挤压技巧7005铝合金齿轮泵体型材挤压过程模拟75MN“短行程”单动卧式铝挤压机A1_2O_3/A356复合材料的凝固组织与机械性能Al_2O_3 短纤维增强 ZA27 合金复合材料制备工艺Al_2O_3/Al-Si合金复合材料中硅相形貌观察Al_2O_3和C短纤维混杂增强铝基复合材料高温耐磨性能的研究Al-Mg-Si系铝合金型材表面暗斑成因分析Al-Ti-B线材连续铸挤的研究ANSYS二次开发在铝型材挤压中的应用AZ31B变形镁合金压力成形AZ31B镁合金挤压工艺研究C_(sf)/Al复合材料管的制备与性能C~+和Ti~+注入铝型材热挤压模表面改性研究CAD/CAM系统在挤压模具设计与制造中的应用CONFORM包覆机工模具调整提高铝包钢丝结合力Conform的扩展挤压及多孔管生产Conform机在生产多孔扁铝管产品上的应用CONFORM连续挤压变形过程的实验研究与数值模拟CONFORM连续挤压的模具Conform连续挤压内螺纹铝管工艺研究Conform连续挤压内螺旋翅片管模具研究CONFORM连续挤压生产线超高压(63MPa)液压系统分析与改进Conform连续挤压原理与铜线挤压加工的影响因素CVD技术在模具上的应用ECAP等径角挤压变形参数的研究ECAP工艺细化铁基形状记忆合金研究ECAP挤压L2纯铝的微观组织演化规律ECAP条件下纯铝的应变行为模拟研究ECAP细晶机制及对纯铝显微组织和力学性能的影响H13钢模具的表面强化技术H13钢热挤压模具自保护膏剂稀土硼碳氮共渗的应用研究H13钢散热器挤压模具失效分析H13铝型材挤压模具早期开裂失效分析H13模具钢的热加工工艺研究H13热挤压模具的开裂原因分析H13热挤压模具型腔变形原因分析及改进措施H13热作模具钢的表面热处理HPb59—1黄铜热挤压工艺及模具H形型材挤压模具的设计K87火车窗铝型材尺寸偏差的控制KBE技术在铝型材挤压模具设计中的应用LD31挤压型材缺陷和工艺优化LD8铝屑重熔—150活塞挤压铸造工艺LY12法兰盘液态模锻锻件及模具设计LY12法兰盘整体加压挤压铸造工艺试验LY12硬铝支架冷挤压工艺及模具设计Ni-Al系金属间化合物基复合材料的研究进展Ⅰ制备方法NiTi合金等径弯角挤压工艺及晶粒细化P/M制备SiC_p/Al复合材料的研究现状PAMOCVD工艺研究及在铝型材挤压模上的应用PCVD模具强化技术应用研究PLC在铝型材挤压机上的应用PSA氮气用于铝挤压保护SiC_p/A1复合材料挤压成形的实验研究SiC_P/Al复合材料搅拌熔炼—液态模锻成型工艺研究SiC_w/Al-Li-Cu-Mg-Zr复合材料压铸工艺的研究SiC_w/Al复合材料热挤压模具设计及其对挤压棒材组织和性能的影响SiC_W/LD2复合材料管材的包覆挤压SiC_w和纳米SiC_p混杂增强铝基复合材料的制备与评价SiCw/Al-Li复合材料热挤压变形及其对组织和性能的影响SiC颗粒增强铝基复合材料的挤压铸造工艺研究SiC颗粒增强铝基复合材料的热挤压工艺研究UGⅡ软件在铝型材挤压分流组合模具设计中的应用WCML-2热作模具钢的研究ZL201曲面薄壁件挤压铸造工艺及模具设计ZnAl_(22)的超塑成形及其装备阿尔福姆合金有限公司在挤压新工艺方面的成就半固态成形的工艺概况与模具材料选用半固态挤压SiC_p/2024复合材料的组织性能研究及缺陷分析半固态挤压变形体传热有限元模型及动态仿真半固态加工技术在机车车辆制造业中的应用前景半固态金属流变成形模具失效与选材半固态扩展挤压A2017合金过程中金属流动的有限元分析半固态模锻及其工业应用前景展望包装废弃物综合治理研究(续完)扁挤压筒的挤压力及应力场的光弹性分析扁挤压筒设计变断面铝型材挤压模平磨胎具的改进变断面型材模具加工工艺的改进变形铝合金均匀化热处理的应用现状与研究进展变形铝合金可挤压性的分析与评价变形铝合金可挤压性的分析与评价表面镀铝及附着碳化硅微粒的高模碳纤维与铝的压铸复合特性表面强化技术与模具寿命冰箱后板成形模设计并行工程在铝型材产品开发中的应用研究玻璃钢拉挤模具设计薄壁铝型材挤压成形的一种有效模拟方法薄壁铝型材挤压有限体积分步模拟薄壁门窗型材挤压的有限体积分步模拟薄壁小铝管盘拉过程游动芯头稳定性的实验研究不连续碳纤维增强ZA-12合金基复合材料的制备工艺不同方式等通道转角挤压纯铝微结构分析不同路径等通道转角挤压镁合金的结构与力学性能不同压力下挤压铸造铝铜合金的组织与性能不锈钢棘轮的温热挤压模具材料加工·制造工程·冷压成形采用H13横向模块提高挤压模具寿命采用挤压铸造新工艺生产柴油机铝活塞试验采用径向挤压方法使废铝颗粒再生成材的试验研究侧向挤压陶瓷型芯模具设计与型芯质量评估超A级尺寸精度铝油堵的成形工艺超大型材生产经验超高分子量聚乙烯的成型技术现状及研究进展(Ⅱ)超高强铝合金强韧化的发展过程及方向超宽型材模具的几种设计方法超声振动压力加工的现状与展望超塑技术在模具制造中的应用超塑性挤压在金属塑性成形中的应用超塑性挤压在金属塑性成形中的应用超塑性锌铝共晶合金成形工艺的研究超塑性在压力加工中的应用超塑性增强合金及其注塑模具热挤压的应用探讨车辆铝合金大型材模具的设计与制造工艺研究车身覆盖件冲压成形动态仿真的研究进展衬套冷技工艺及模具尺寸驱动图元在挤压模具中的应用冲裁过程和冲裁间隙冲裁挤压成型模纯铝等径角挤技术(Ⅰ)——显微组织演化纯铝等径角挤技术(Ⅱ)——变形行为模拟纯铝和LY12铝合金微塑性成形性能评价试验研究纯铝铸件JB—1并沟线夹的挤压铸造工艺打火机壳挤压模具及工艺大壁厚铝型材分流模的设计大变形零件温挤压凹模型孔设计技巧大尺寸多层喷射沉积6066Al/SiC_p/Gr复合材料管坯的制备大间隙冲裁对模具寿命的影响大口径弹尾部零件挤压铸造工艺的研究大宽厚比薄壁异型材挤压多工艺参数优化研究大型工业铝合金型材的挤压生产工艺与关键技术(续)大型铝合金散热器挤压型材的模具设计大型双鼓形铝轮毂精密锻模设计与改进大悬臂半空心铝型材模具设计大悬臂挤压模变形机理分析大悬臂铝型材挤压模的设计与强度校核带翼内凸筋D形铝管连续挤压生产工艺的研究带翼内凸筋D形铝管连续挤压生产工艺的研究氮化硼粉末静电喷涂技术在铝型材挤压生产上的应用德国洪塞尔铝业公司44MM挤压机等截面侧挤压技术及其实验模具设计等截面通道角形挤压对高纯铝微观组织及力学性能的影响等径角挤压法制备超细晶的研究现状等径角挤压法制备块体超细晶材料的研究现状及展望等径角挤压模具对超细晶材料显微组织的影响等径角轧制AZ31镁合金板材的组织与性能等径通道挤压中晶粒细化影响因素的研究进展等径弯曲通道变形力的研究等离子体表面改性技术及其在模具中的应用等通道弯角多道次挤压工艺累积变形均匀性研究等通道弯角挤压变形机理模拟与工艺参数优化等通道转角挤压(ECAP)工艺的研究现状等通道转角挤压纯铝的组织结构等通道转角挤压对L2工业纯铝力学性能的影响等通道转角挤压对纯铝L2阻尼性能的影响等通道转角挤压工艺有限元分析等通道转角挤压过程有限元模拟等通道转角挤压铝硅合金组织的研究等通道转角挤压模具挤压力计算等通道转角挤压实验模具设计等温热反挤压工艺参数对SiCp/LY12复合材料超塑性的影响等效应变量对等径角挤压的2A12铝合金力学性能的影响低碳马氏体在模具中的应用低体积分数SiC_W/Al复合材料的制备低温渗硼提高模具的使用寿命地铁车辆铝型材用特种挤压模具制造技术分析地铁车辆用边梁型材GDX-14模具的设计地铁特宽空心型材模具设计与挤压工艺研究地铁型材模具的探讨地铁用铝合金型材挤压模具设计第八讲空心铝型材挤压模具优化设计(2)第二讲铝型材挤压模具的材料选择第二届全国液态模锻(挤压铸造)学术交流会论文摘要第九讲民用建筑铝型材挤压模具优化设计第六讲实心铝型材挤压模具优化设计(2)第七讲空心铝型材挤压模具优化设计(1)第三讲铝型材挤压模结构要素与设计原则第十讲工业铝型材模具优化设计(1)第十一讲工业铝型材模具优化设计(2)第四讲铝型材挤压模具的种类及组装形式第五讲挤压垫优化设计第五讲实心铝型材挤压摸具优化设计(1)第一讲挤压筒的优化设计(1)第一讲铝型材挤压模具概论电锤钻双键槽冷挤压成型新工艺电动机连接端盖拉伸精整模设计电加工技术在模具上的应用电解磨料喷射抛光工艺的试验研究电缆连续挤压包覆产品缺陷的分析电缆连续挤压包覆技术及设备电缆铝护套连续挤压包覆模具的设计电缆铝护套连续挤压包覆型腔设计的均压判定准则短碳纤维增强铝基复合材料的半固态加工短碳纤维增强铝基复合材料的挤压浸渗工艺短纤维氧化铝/铝复合材料液态浸渗后直接挤压的试验研究锻压模具的润滑对4Cr5MoSiV1热挤压模具钢加工工艺的研究对挤压模工作带的设计、加工、修正的研究对我国铝材挤压加工发展之管见对向式间接液态金属模锻对中国铝挤压工业若干问题的探讨对中国铝挤压工业若干问题的探讨多孔管、棒挤压模加工工艺的改进多坯料挤压及在铝/铝合金复合材料成形中的应用多腔室模具加热曲线及控制发射器用大型散热器挤压模设计反向挤压技术及挤压设备反向挤压模具设计探讨反向挤压时的挤压力变化规律反应烧结氮化硅陶瓷模具材料的研究非对称空心铝型材模具设计的重要原则非牛顿特性下冷挤压流体动力润滑模型的建立分流挤压镁合金管材工艺研究分流模挤压紫铜电脑散热片实验研究分流模在挤压生产中的应用分流组合模挤压的有限元模拟与模具设计评价粉末冶金法制造SiCp/LY12复合材料及SiCp/LY12复合材料超塑性研究粉末冶金制备颗粒增强5052铝基复合材料的压力加工工艺研究风机生产模具及工艺装备造价的对比研究氟塑料加工复杂断面空心型材挤压模具的制作技术复杂盒形零件挤压金属非均匀流动控制研究复杂铝型材挤压成形有限体积仿真改进重载铝活塞的技术改善挤压性能,提高6063合金挤压速度钢铝层叠复合材料固态复合技术及应用钢铝复合导电轨制造技术的探讨高表面质量铝管冷挤成形及挤光工艺高纯铝等通道转角挤压引起的微观组织变化高光洁度大铝管冷挤成形及挤光工艺高精度铝合金挤压型材生产的新发展高铝青铜Cu-14%Al-X合金的气孔及消除方法高铝锌基合金ZA27液态模锻工艺参数研究高铝锌基合金挤压铸造的组织和性能的研究高铝锌基合金直齿圆锥齿轮的挤压铸造工艺高强超高精度7A04超硬铝合金导轨型材的研制高强度铝及铝-锂合金大型壁板和型材的生产高强韧冷作模具钢——LD钢的性能和应用高热强性热作模具钢的开发研制及模具寿命的提高高热强性热作模具钢的研制开发及模具寿命的提高高速锤热挤压增压器涡轮叶片高速列车用大型挤压铝型材工业铝型材挤压模具的设计工艺参数对铝型材挤压变形规律的影响工艺润滑材料的发展评述骨架表面改性对SiC/Al复合材料性能的影响关于挤压变形规律理论研究方法的一些探讨管材挤压工艺分析及实验研究管子钳铝合金钳柄体液态挤压工艺及模具罐用铝材的研究现状及存在的问题分析光塑性在连续挤压成形研究中的若干关键技术广东铝型材热挤压模具渗氮技术的发展广东热处理表面工程与市场经济广东省几家模具企业发展的启示硅酸铝短纤维增强铝硅合金复合材料热处理组织的研究硅线石/2024液态挤压成形件的摩擦学特性硅线石颗粒/LY12搅融混合后半固态挤压成形件组织与性能研究硅线石颗粒/铝搅融混合半固态挤压成材的试验研究硅线石颗粒与铝液混融后挤压下流动凝固的塑性变形特征轨道车辆大型铝合金型材模具的设计与制造技术轨道车辆用大型铝合金型材的开发评估及挤压工艺特点国内外挤压铸造技术发展概况国内外模具发展概况国外冲压与模具技术动向国外反应注塑成型技术的进展国外铝和铝合金挤压模具的发展国外铝挤压技术及其装备的进展国外铝加工技木新进展国外模具技术发展动态国外钛工业发展概况和加工工艺新发展(续)过共晶铝硅合金半固态挤压铸造近终成形技术研究过共晶铝硅合金活塞的挤压铸造过共晶铝合金汽缸体的挤压铸造航空用DQ3137型材舌型挤压模具的改进合理大间隙冲裁模的应用黑色压铸用铜合金模具材料活塞用碳纤维铝基复合材料的制备方案研究基于BP神经网络的铝型材挤压模具优化设计基于BP网络和遗传算法的铝型材挤压模工作带优化模型基于BP遗传算法的铝型材挤压模具优化设计基于UG平台构建三维铝型材挤压模具CAD系统基于VB6.0的轻合金带筋壁板挤压模具CAD系统开发基于多变性设计的回转体零件挤压模具结构智能设计方法研究基于多重优化设计的铝型材挤压工作带模型基于流函数法的铝型材挤压导流模合理设计基于热力耦合的热挤压模具结构参数优化设计基于数值模拟的铝型材挤压变形规律的研究(Ⅱ)基于数值模拟的铝型材挤压变形规律的研究(I)基于有限元分析的铝合金等温挤压工艺设计基于有限元技术的大型6061无缝管挤压温度变化规律研究基于有限元模拟的型材挤压专家系统基于知识的铝型材挤压模具集成设计系统极限变形程度下纯铝反挤压变形力的研究几种多腔工业铝型材挤压模具的设计几种具有优良性能的模具钢几种铝型材挤压模具的改良设计几种铝型材挤压模具的优化设计挤出吹塑模具设计挤出模损坏原因分析及改进办法挤压不锈钢用高铝青铜合金模具材料挤压成形技术在接插件端子模具设计中的应用挤压锭铸造新方法——气滑铸造挤压分流模CAD关键技术的研究挤压分流组合模的设计挤压工模具材料及其热处理与表面处理现状挤压工艺和模具对成品率的影响及措施挤压珩磨在模具研磨工艺上的应用挤压珩磨在模具制造中的应用挤压加工润滑剂的应用挤压加工新技术挤压浸渗法制备C_(sf)/Al复合材料的组织与性能挤压铝合金型材时牵引力的计算挤压铝型材表面“停止痕”缺陷的成因与对策挤压铝型材产品开发计算机辅助设计系统挤压铝型材出现“咬痕”的原因及预防措施挤压铝型材的悬臂模具设计挤压铝型材断面难度系数的探讨挤压模的寿命及提高实例挤压模具CAD应用程序开发技术挤压模具氮化工艺控制挤压模具电火花加工空刀新工艺挤压模具气体软氮化及废气处理新工艺挤压模具软氮化工艺实践挤压模具设计技术挤压模具设计综合数据库系统挤压模具使用寿命的主要影响因素挤压模具使用寿命影响因素的分析挤压模具早期失效起因与处理挤压模具制造工艺分析挤压模孔优化的CAD研究挤压渗流铸造泡沫铝合金的工艺因素探讨挤压式铝管外导体物理发泡射频同轴电缆的设计制造及铝管缺陷分析挤压筒锁紧面大帽的起因分析挤压温度对高硅铝合金材料组织与性能的影响挤压型材内腔加强筋的超声波探伤挤压硬铝时工艺条件对制品强度和粗晶环厚度的影响挤压铸件优质化技术进展挤压铸造CF/Al复合材料的工艺研究挤压铸造SiC_w/L3复合材料的热挤压挤压铸造SiC_w/L3复合材料液-固两相区包覆挤压挤压铸造代替锻铝的试验挤压铸造的应用与模具材料挤压铸造对过共晶铝硅合金活塞各部位含硅量分布的影响挤压铸造法制备(SiC/A1)/A1复合材料挤压铸造法制备可变形SiC_P/Al复合材料的组织与性能挤压铸造工艺参数对Al_2O_(3f)/Al-4.5%Cu复合材料凝固方式与组织的影响挤压铸造工艺参数对柱塞式大高径比ZA27合金铸件力学性能的影响挤压铸造技术的发展及应用挤压铸造铝合金车轮模具的结构与排气挤压铸造铝合金的材料研究挤压铸造铝基复合材料凝固偏析研究挤压铸造模具材料的选用及热处理挤压铸造模具三维运动仿真介绍挤压铸造模温对C/Mg复合材料组织和性能的影响挤压铸造硼酸铝晶须增强Al基复合材料浸渗过程理论分析挤压铸造汽车空压机铝连杆的试验研究挤压铸造汽车空压机铝连杆的研制与应用挤压铸造汽车制动主缸的研究与应用挤压铸造—烧结反应制备Al_2O_3/Ti_xAl_y复合材料新工艺挤压铸造碳纤维增强A356金属基复合材料凝固过程的研究挤压铸造条件下铝基复合材料铸造流动性研究挤压铸造条件下铝基复合材料铸造流动性研究挤压铸造无缩孔判据在有色金属中的验证挤压铸造用模具材料的选用技术改造推动了模具专业化发展加工过程对渗氮铝挤压模性能的影响加工制造过程对铝挤压模具寿命的影响加磷处理过共晶铝硅合金的挤压铸造夹头冷挤模设计间接挤压铸造模具编码系统研究减轻铝型材表面光泽条纹的措施检阅水平、交流技术、沟通渠道的一次盛会——参观“全国模具及模具加工机械展销会” 简易模具的制作及其应用(连载)——[Ⅰ]简易模具的基础知识角铝型材挤压过程的数值模拟接合型复合材料的成形界面对纤维增强铝硅合金复合材料耐磨性的影响金属表面的电火花强化法金属材料半固态挤压工艺的有限元分析金属材料的等通道转角挤压研究进展金属反向挤压技术的发展与应用前景金属复合线材成形工艺的研究开发概况金属挤压成形理论与技术发展的现状与趋势(1)金属挤压成形理论与技术发展的现状与趋势(2)金属挤压成形理论与技术发展的现状与趋势(3)金属连续铸挤包覆成型技术金属塑性成形模具的灵敏度分析金属微成形技术及其研究进展近代铝合金反向挤压技术近期国内液态模锻技术的一些研究进展九十年代模具技术的发展动向矩形钼管加工工艺研究具有较大舌比的半空心铝型材模具的设计聚苯乙烯泡沫塑料模的制造均匀流场在铝合金冷挤压中的应用(英文)颗粒增强金属基复合材料挤压性能的研究颗粒增强铝基复合材料的制备及应用颗粒增强铸造铝合金内燃机活塞材料的研究空调压缩机外壳的液态挤压成形空心铝铆钉冷挤压工艺及其模具的研究空心铝型材挤压成形过程的有限元数值模拟空心铝型材挤压过程计算机仿真系统空心铝型材挤压时金属流动的计算机辅助(CAD)分析空心型材分流组合挤压CAD/CAE模型的建立空心型材挤压模具模芯变形的有限元分析快速成型与快速模具制造技术快速模具制造技术的应用研究快速凝固/粉末冶金制备高硅铝合金材料的组织与力学性能快速凝固SiC_p/LY12复合材料的制造工艺和性能快速凝固高硅铝合金粉末的热挤压过程快速凝固过共晶铝硅合金材料的研究进展快速凝固铝锂合金粉末特性对其挤压村组织和性能的影响宽断面美格铝型材模具的设计宽截面铝型材挤压导流模应用研究宽展挤压模具正交试验研究扩音器话筒接头冷挤压模具设计冷冲模设计参考资料(三)冷挤工艺在圆形连接器中的应用冷挤铝手柄工艺及模具冷挤压凹模受力分析冷挤压锻铝的润滑剂冷挤压机载荷与缓冲参数关系的试验研究冷挤压技术的发展及模具冷挤压流体动力润滑模型的建立冷挤压散热片模具及工艺冷挤压通孔凹模受力分析与横向开裂冷挤压柱塞加工离子注入工模具材料表面改性及其展望力学分析在挤压模具调整方面的应用利用废旧模具生产优质电渣熔铸模具钢锭的新技术连续包覆(CONCLAD)模具优化的模拟实验连续变断面挤压成形方法的研究*连续变断面挤压工艺的开发连续挤压/包覆模具型腔CAD系统开发连续挤压D97多孔扁管组织性能的研究连续挤压包覆CATV同轴电缆芯线防灼伤系统研究连续挤压包覆技术在铝包钢丝生产上的应用连续挤压成形过程的计算机仿真连续挤压带翼内凸筋D型铝管模具研究连续挤压多通道铝扁管用硬质合金模具的研制连续挤压法介绍连续挤压工模具负载的计算机模拟连续挤压和连续包覆技术的理论研究与工程实践连续挤压铝管典型缺陷的原因分析及预防措施连续挤压模具的选材连续挤压模具型腔汇合室几何参数优化设计连续扩展挤压成形常见缺陷分析与预防连续铸挤成形技术的发展及应用连续铸挤成型技术及其发展连续铸挤生产铝管的力能计算与分析连续铸挤生产铝管的研究两种粒径颗粒混合增强铝基复合材料的导热性能流变法铸造石墨铝挤压铸造工艺参数的正交试验研究。
铸造工艺对ZL101铝合金铸件质量影响的研究

铸造工艺对ZL101铝合金铸件质量影响的研究作者:黎静妮冯丽江韦凤萍潘荣禄钟佳梅来源:《理论与创新》2021年第01期【摘要】利用传统的重力铸造方法制备ZL101铝合金,采用硬度测试、拉伸性能测试等实验方法研究铸造工艺对ZL101铝合金铸件质量影响。
研究结果表明:熔炼温度为720℃,合理的保温时间能有效细化合金组织,当保温时间为20min时,粗大α-Al初生树枝晶向细小胞状晶与球状晶转变,共晶硅的形态也得到较好的改善,合金表现出较好的力学性能,其中抗拉强度为260 MPa,断后伸长率为6%,布氏硬度值为70 HBS。
【关键词】ZL101铝合金;铸造工艺;力学性能引言铸造是一种古老的制造方法,在我国可以追溯到6000年前。
随着工业技术的發展,大型铸件的质量直接影响着产品的质量,因此,铸造在机械制造业中占有重要的地位。
铸造技术的发展也很迅速,特别是19世纪末和20世纪上半叶,出现了很多的新的铸造方法,如低压铸造、陶瓷铸造、连续铸造等,在20世纪下半叶得到完善和实用化。
铸造是将通过熔炼的金属液体浇注入铸型内,经冷却凝固获得所需形状和性能的零件的制作过程。
铸造是常用的制造方法,制造成本低,工艺灵活性大,可以获得复杂形状和大型的铸件,在机械制造中占有很大的比重,如机床占60~80%,汽车占25%,拖拉机占50~60%。
由于现今对铸造质量、铸造精度、铸造成本和铸造自动化等要求的提高,铸造技术向着精密化、大型化、高质量、自动化和清洁化的方向发展,例如我国这几年在精密铸造技术、连续铸造技术、特种铸造技术、铸造自动化和铸造成型模拟技术等方面发展迅速。
ZL101铝合金是一种通过铸造方式制备得到的研究和应用最为广泛的铝硅镁合金,该合金中Si元素的占比约为6.5~7.5%,其中还含有少量的Mg(0.25~0.45%),为亚共晶合金。
该合金具有强度高、韧性以及良好的耐蚀性等多项优异力学性能和物理性能,并且还可以通过适当的热处理使其加工性能、材料塑性以及合金表面性能都获得显著提升,能够有效满足汽车部件的轻量化要求。
铝活塞的挤压铸造(1)

铝活塞的挤压铸造闫汝辉,张屹林,王亚南,高占雨(山东滨州渤海活塞股份有限公司,山东滨州256602)摘要:概述了挤压铸造技术的发展情况。
重点评述了铝活塞挤压铸造工艺特点及其优势以及此技术在实际中的应用。
关键词:挤压铸造;铝活塞;复合材料中图分类号:TK403.3 文献标识码:B 文章编号:1000-6494(2006)03-0022-03The Squeeze Casting of Aluminium Alloy PistonYAN Ru -hui,Z HANG Yi -lin,W ANG Ya -nan,GAO Zhan -yu (Shandong Binzhou B ohai Piston C o.,Ltd.,Binzhou 256602,China)Abstract:The squeeze casting technical development is summarized in this paper.It focuses on introducing the aluminiu m piston squeeze casting technology characteristics and their superiori ty and its practical application .Key words:squeeze casting;alu minium alloy piston;compound material作者简介:闫汝辉(1970-),男,山东滨州人,高级工程师,主要从事铝活塞铸造工艺、计算机辅助设计与自动化设计的研究。
收稿日期:2005-11-211 概述1.1 铝活塞的热工成形技术活塞是汽车发动机中传递能量的一个重要的零件。
它的工作条件是高温高压及高应力状态,与活塞环、气缸壁之间不断产生摩擦,润滑条件较差,工作条件极其恶劣。
铝活塞传统上应用最多的生产工艺是金属型铸造,金属型铸造对活塞形状的选择自由度大,容易满足设计者对形状的要求,加工简单,生产成本较低,但容易产生缩孔、缩松等铸造缺陷,机械性能较低。
AlSi12Cu3Ni2Mg1活塞合金挤压铸造性能研究

2007 年中 国压 铸、挤 压铸 造、半固态 加工 学术 年会 专刊
A lSi12Cu3N i2M g1活塞合金挤压铸造性能研究
侯林冲1, 2 党惊知 1 高明灯 2 彭银江 2 沈建明 2 ( 1. 中北大学; 2. 中国兵器科学研究院宁波分院 )
摘 要 研究了挤压铸 造工艺条件下, 挤压铸造工艺参数对 A lSi12Cu3N i2Mg1活塞合金性能的影响。
[ 2] FRANKLIN J R, DAS A A. Squeeze cast ing: a review of the statu s[ J]. The Brit ish Foundry, 1984, 77( 3 ): 1502158.
[ 3] 刘达利, 齐丕骧. 新型铝活塞 [M ]. 北京: 国防工业出版社, 1999.
A2固溶体上分布着点状及短条状的共晶硅, 存在极少量 小块状初晶硅, 组织达到内燃机铸造铝活塞金相检验标 准 (GB6289- 2005) 1~ 2级。
3 分析
在传统 A l2Si合 金 ( ZL109) 的基础 上添加 少量的 铜、镍等元素能够提高合金的力学性能, 其中硅增加基 体的强度, 降低基体塑性; 铜元素大部分存在于铝固溶 体中, 对基体产生较大的强化作用, 这种作用受热处理 影响较少, 对基体高温强度有明显影响; 镍元素主要以 一系列深浸蚀的较粗大化合物存在, 由于铜和镍能形成 化合物, 对基体高温强度有明显影响。
素的含量, 改善了材料的韧度和高温强度, 满足了大功
率发动机活塞需要, 性能超越传统的 ZL109合金。
表 1 M a h le142合金主要化学 成分
%
Si 11~ 13
Cu 2. 6 ~ 4. 0
wB
文献综述——铝挤压

基于数值模拟研究铝合金管材挤压过程中的金属流动规律及模具优化设计文献综述1.铝合金分类及铝合金挤压现状纯铝的密度为ρ=2.7g/cm3,约是铁的1/3,熔点为660℃,铝是面心立方结构,故具有很高的塑性(δ:32~40%,ψ:70~90%),易于加工,可制成各种型材、板材,并且具有极好的抗腐蚀性能;但是纯铝的强度很低,退火状态σb 值约为8kgf/mm2,故不宜作结构材料。
通过长期的生产实践和科学实验,人们逐渐以加入合金元素及运用热处理等方法来强化铝,这就得到了一系列的铝合金。
添加一定元素形成的合金在保持纯铝质轻等优点的同时还能具有较高的强度,σb 值分别可达24~60kgf/mm2。
这样使得其“比强度”(强度与比重的比值σb/ρ)胜过很多合金钢,成为理想的结构材料,铝合金密度低,但强度比较高,接近或超过优质钢,塑性好,可加工成各种型材,具有优良的导电性、导热性和抗蚀性。
近几十年来发展十分迅速,在国民经济和人民生活各领域获得了十分广泛的应用,成为仅次于钢材的第二大金属材料。
2002~2010年间,全国铝合金产量如表1所示。
表1 2002-2010年中国铝合金产量及增长速度统计从表中可以看出,2002-2010年间,全国的铝合金产量呈上升趋势。
随着加工技术,产品性能的提高,铝合金的产量将继续增大,其应用必定会更加广泛。
1.1铝合金的分类铝合金分两大类:铸造铝合金,在铸态下使用;变形铝合金,能承受压力加工。
可加工成各种形态、规格的铝合金材。
主要用于制造航空器材、建筑用门窗等。
铝合金挤压所用的材料一般均为变形铝合金。
1.1.1铸造铝合金铸造铝合金(cast aluminium alloy)是指适于熔融状态下充填铸型获得一定形状和尺寸铸件毛坯的铝合金,可按成分中铝以外的主要元素硅、铜、镁、锌分为四类,代号编码分别为100、200、300、400。
(1)铝硅系合金,也叫“硅铝明”或“矽铝明”。
有良好铸造性能和耐磨性能,热胀系数小,在铸造铝合金中品种最多,用量最大的合金,含硅量在10%~25%。
汽车发动机铝合金前盖的压铸工艺优化

汽车发动机铝合金前盖的压铸工艺优化摘要:应用仿真软件,以某轿车发动机铝合金前罩为实例,进行了浇铸与溢流系统的模拟计算。
对仿真的结果进行了分析,并给出了压铸工艺的最佳设计;模拟了最佳浇注与固化工艺,对温度场、气压、凝固等参数的变化进行了仿真,验证该方法是否具有较好的合理性。
同时,由于铸件局部温度过高,冷却时间过长,可以使用一些方法来加速局部冷却,例如,高压点冷,从而改善铸件质量。
最后,对浇注系统及其它工艺设计进行了论证。
关键词:铝合金;汽车;前盖;发动机;压铸工艺在我国汽车工业迅速发展的今天,对轻质合金的需求日益增加。
铝合金,因其具有较低的致密、较低的热膨胀率和较好的摩擦力,广泛用于汽车发动机盖、变速箱壳体等铸件。
我国汽车铝合金铸件主要采用,Si含量为,属亚共晶型或共晶型,机械性能良好。
采用软件,对某汽车发动机铝合金前盖的充型、凝固过程进行了研究。
并对其进行了仿真计算,并给出了相应的优化设计,为同类产品的制造提供了借鉴。
一、铝液的处理为了改善铸件的机械性能,降低铸件的各类缺陷,对铝合金的熔融处理是十分重要的一环。
1.铝合金熔体的提纯和纯化由于对铝溶液的品质提出了更高的要求,所以,从精制原理上将其分成两大类:吸附提纯与不吸附提纯。
浮游法是最常用的精制方法,80年代后期,公司根据气泡浮游的原理,开发出一种,将惰性气体从铝液的底部吸入,使之分散为均匀的微小气泡,从而大大增加了与铝液的接触面积和时间。
同时,由于气泡表面吸附的杂质也会随之上升,从而实现脱氢除渣。
目前,该工艺主要是利用氮气进行脱气,在的条件下,吹管的转速在,在内进行。
2.铝合金熔体的变质和细化处理改进合金的铸态结构最好的办法是变质合金,常规的变质剂主要为钠变质和锶变质,变质更适于大规模、连续的生产。
普遍认为,的质量分数应该在之间,;铝锭中最好不要有Sr,由于铝锭中含,在中转铝时易被卷入氧化夹杂物;加Sr的添加时间为,后发生变质。
加入Sr可以消除宏观收缩,从而形成显微缩孔。
高功率密度柴油机铝活塞材料与铸造技术
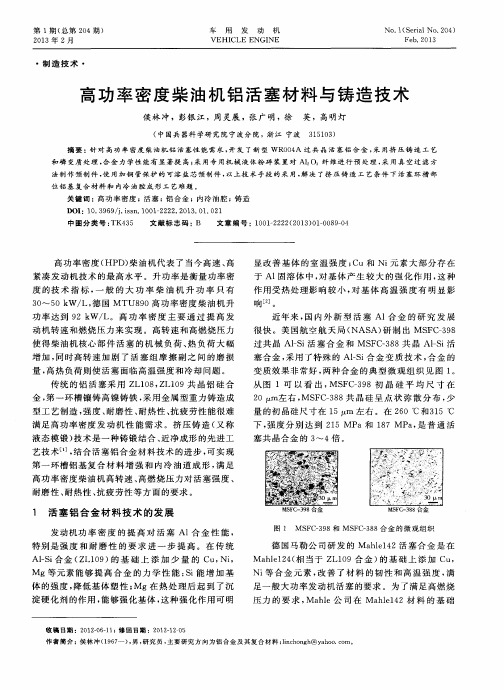
Mg等元 素能 够 提 高 合 金 的力 学 性 能 : S i 能增 加 基 体 的强度 , 降低 基体 塑 性 ; Mg在 热 处 理后 起 到 了沉 淀 硬 化剂 的作 用 , 能够 强化基 体 , 这种 强 化作用 可 明
Ni 等合金元素, 改 善 了 材 料 的韧 性 和 高 温 强 度 , 满 足 一般 大功 率 发动机 活 塞 的要 求 。为 了满 足高燃 烧 压 力 的要 求 , Ma h l e公 司 在 Ma h l e 1 4 2材 料 的 基 础
ቤተ መጻሕፍቲ ባይዱ
塞共 晶合 金 的 3 ~4倍 。
高 功率 密度 柴油 机高 转速 、 高燃 烧 压力对 活 塞强度 、 耐磨 性 、 耐热 性 、 抗 疲 劳性 等方 面 的要求 。
1 活 塞 铝 合 金 材 料 技 术 的 发 展
发动 机 功 率 密 度 的提 高 对 活 塞 Al 合金性 能, 特别 是强 度 和 耐 磨 性 的要 求 进 一 步 提 高 。在 传 统
第 1 期( 总第 2 0 4期 )
2 0 1 3年 2月
车
用
发
动
机
No . 1 ( S e r i a l No . 2 0 4 )
Fe b .2 01 3
VE H I CLE EN G I N E
・
制造 技术 ・
高 功 率 密 度 柴 油 机 铝 活 塞 材 料 与铸 造 技 术
满 足高 功率 密度 发 动 机 性 能 需求 。挤 压 铸造 ( 又 称
液 态模 锻) 技 术是 一种 铸锻 结合 、 近净成 形 的先进 工 艺技 术n ] , 结 合活 塞铝 合金 材料 技术 的进 步 , 可实 现 第 一环槽 铝 基复 合 材料 增 强 和 内冷 油 道 成 形 , 满 足
挤压铸造在汽车、摩托车上的应用

挤压铸造在汽车、摩托车上的应用
体,制动器缸体,离合器缸体,拔叉、摇臂、履带板、铝基复合材料制动毂清器支架、变
速箱体、多岐
管、燃料分配
器
体、涡旋盘;空压
机连杆、油泵壳
体、空气过滤器罐
体、罐盖
架、车摇架、车架
接头、把接头、方
向轴、曲柄,发动
机活塞
、作者的合作厂生产的汽车空调压缩机零件照片。
、作者的合作厂生产的摩托车零件照片。
汽车铝轮毂挤压铸造动作程序
)合模浇注,(b)压射缸摆正上升,(c)下冲头上升伸第一次挤压
)上冲头下行第二次挤压(e)上冲头下行冲孔并将料饼推出
挤压铸造工艺参数列于表2,不同铸造方法的铝轮毛坯的力学性能比较列于表,可见挤压铸造性能最好。
、解放牌汽车活塞挤压铸造模具图
2、连杆;
3、摆杆;
4、支架;
5、垫板;
6、活塞毛坯;
DHXV350型卧式挤压铸造机动作原理图
、铝液输送管 2、电磁泵 3、静模 4、动模 5、挤压头 6型缸体挤压铸造工艺参数
每次模浇冲头内浇低速内浇口处充型升压。
发动机铝合金活塞铸件的分析研究

发动机铝合金活塞铸件的分析研究摘要:针对汽车发动机铝合金活塞铸件进行缺陷分析,同时尝试借助实际试制浇铸及模拟分析软件相结合的方法,对铸件的成型情况进行相应的解析,从模具冷却结构改进方面入手对铸件缩松缺陷问题加以解决,借助模具设计结构的特点解决铸造缺陷,这对于金属重力铸造生产铸件的缺陷解决具有一定的借鉴意义。
关键词:缺陷分析;模拟分析;铸造工艺随着社会的不断进步以及科技的不断发展,汽车发动机活塞的轻量化程度也在逐渐提升,无论是其热负荷还是机械负荷都有了明显的增大,这样会致使活塞的工作环境更为严酷。
基于上述情况分析,活塞铸件的材料必须要具备下述功能特点:热膨胀系数小、密度小、热传导性好,除此之外铸件材料还要满足耐腐蚀、耐磨等需求。
这样看来,铝合金能够在较大程度上胜任活塞铸件的要求。
目前共晶铝硅合金是发动机活塞最长应用的材料之一,该材料中约含有11%~14%的硅,随着含硅量的不断增加,Al-Si系合金的抗拉性能也会有相应的提升,到共晶成分点时达到最大;之后持续增加硅含量,但是由于会产生粗大长针状初晶硅,其形状不太好进而也会导致合金的强度出现骤然下降的情况。
因而为了使得铝硅合金的原有特点不被破坏,又能保证力学性有很大程度的提升,进而可以使得这种合金的应用范围扩大,在近些年,无论是国内还是国外,都在对其开展研究,并采用了多种行之有效的措施。
1铸件结构与试制本篇文章所选用的汽油机活塞铸件其铝合金材料的牌号为KS1295的共晶铝硅合金,这种材料的优势众多,其具有膨胀系数小、密度小、耐磨、流动性好等诸多特点。
这个活塞铸件的造型相对来说复杂性较高,包括了多处深腔及薄壁区域。
这种活塞铸件在发动机工况下的力学性能要求:最大承载功率大于155kW(211ps,5500rpm),最大承载扭矩为350N·m(1200~4000rpm),材料的硬度不得低于HB140。
依据相应的设计标准以及浇筑需求,借助一模两腔重力铸造浇注机对活塞铸件尝试进行生产。
Al_Si活塞挤压铸造工艺研究
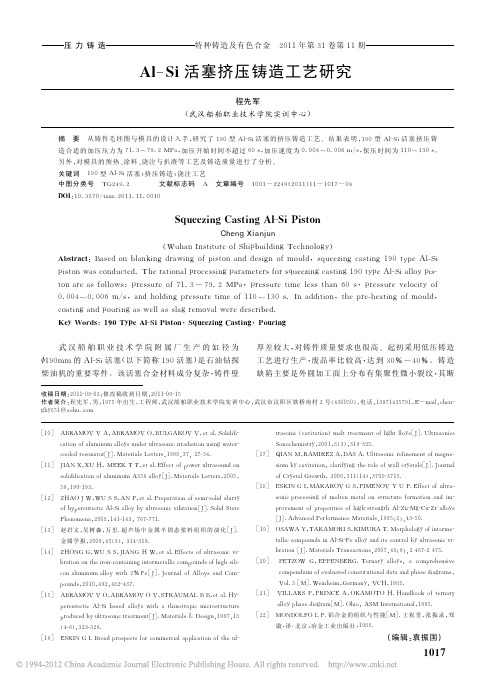
; 收稿日期 : 修改稿收到日期 : 2 0 1 1 0 8 0 2 2 0 1 1 0 9 1 5 - - - - ) , : 作者简介 : 程先军 , 男, 工程师 , 武汉船舶职业技术学院实训中心 , 武汉市汉阳区铁桥南村 2 号 ( 电话: 1 9 7 5 年出生 , 4 3 0 0 5 0 1 3 9 7 1 4 3 5 7 9 1, E-m a i l c h e n - o h u. c o m h 8 5 1@s g y
压 力 铸 造
特种铸造及有色合金 2 0 1 1 年第 3 1 卷第 1 1期
i活塞挤压铸造工艺研究 A l -S
程先军 ( 武汉船舶职业技术学院实训中心 )
摘 要 从铸件毛坯图与模具的设计入手 , 研究了 1 9 0型 A l S i活塞的挤压铸造工艺 。 结 果 表 明 , 1 9 0型 A l S i活 塞 挤 压 铸 - - , , / , 。 造合适的加压压力为 7 加压开始时间不超过 6 加压速度为 0. 保压时间为 1 1. 3~7 9. 2 MP a 0s 0 0 4~0. 0 0 6m s 1 0~1 3 0s 另外 , 对模具的预热 、 涂料 、 浇注与扒渣等工艺及铸造质量进行了分析 。 关键词 1 挤压铸造 ; 浇注工艺 9 0型 A l S i活塞 ; - ( ) 中图分类号 T G 2 4 9. 2 文献标志码 A 文章编号 1 0 0 1-2 2 4 9 2 0 1 1 1 1-1 0 1 7-0 4 : / D O I 1 0. 3 8 7 0 t z z z . 2 0 1 1. 1 1. 0 0 1 0
S u e e z i n C a s t i n A l S i P i s t o n - q g g
C h e n X i a n u n g j ( ) Wu h a n I n s t i t u t e o f S h i b u i l d i n T e c h n o l o p g g y : , A b s t r a c t B a s e d o n b l a n k i n d r a w i n o f i s t o n a n d d e s i n o f m o u l d s u e e z i n c a s t i n 1 9 0t e A l S i - g g p g q g g y p i s t o n w a s c o n d u c t e d . T h e r a t i o n a l r o c e s s i n a r a m e t e r s f o r s u e e z i n c a s t i n 1 9 0t e A l S i a l l o i s - - p p g p q g g y p y p : , , t o n a r e a s f o l l o w s r e s s u r e o f 7 1. 3~7 9. 2 MP a r e s s u r e t i m e l e s s t h a n 6 0s r e s s u r e v e l o c i t o f p p p y / , , , 0. 0 0 4~0. 0 0 6m s a n d h o l d i n r e s s u r e t i m e o f 1 1 0~1 3 0s . I n a d d i t i o n t h e r e h e a t i n o f m o u l d - g p p g o u r i n c o a t i n a n d a s w e l l a s s l a r e m o v a l w e r e d e s c r i b e d . p g g g : , , K e W o r d s1 9 0T e A l S i P i s t o n S u e e z i n C a s t i n o u r i n - y y p q g g P g 武 汉 船 舶 职 业 技 术 学 院 附 属 厂 生 产 的 缸 径 为 以下简称 1 是石油钻探 1 9 0 mm 的 A l S i活塞 ( 9 0 活塞 ) - 柴油机的重要零件 。 该活塞合金材料成分复杂 , 铸件壁 厚差较大 , 对铸件质量要求也很高 。 起初采用低压铸造 工艺进行生产 , 废品率比 较 高 , 达到3 0% ~4 0% 。 铸 造 缺陷主要是外圆加工面上分布有集聚性微小裂纹 , 其断
大型发电机组冷却系统用3003铝合金型材挤压工艺研究
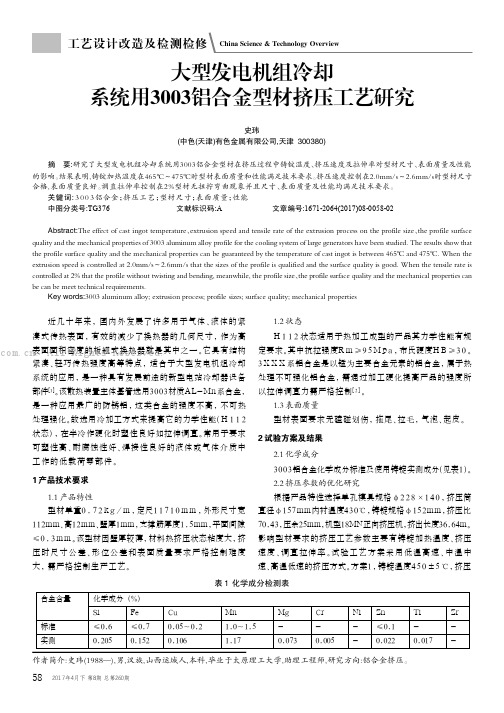
近几十年来, 国内外发展了许多用于气体 、液体的紧 凑式传热表面, 有效的减少了换热器的几何尺寸, 作为高
58 2017年4月下 第8期 总第260期
China Science & Technology Overview 工艺设计改造及检测检修
工艺设计改造及检测检修 China Science & Technology Overview
大型发电机组冷却 系统用3003铝合金型材挤压工艺研究
史玮 (中色(天津)有色金属有限公司,天津 300380)
摘 要:研究了大型发电机组冷却系统用3003铝合金型材在挤压过程中铸锭温度、挤压速度及拉伸率对型材尺寸、表面质量及性能
1 产品技术要求
1.1 产品特性 型材单重0 . 7 2 k g / m , 定尺1 1 7 1 0 m m , 外形尺寸宽 112mm、高12mm、壁厚1mm,支撑筋厚度1.5mm,平面间隙 ≤0 . 3 m m 。该型材因壁厚较薄, 材料热挤压状态粘度大, 挤 压时 尺 寸 公 差 、形 位 公 差 和表 面 质 量 要 求严 格 控 制 难度 大, 需严格控制生产工艺。
表 1 化学成分检测表
合金含量
标准 实测
化学成分(%)
Si
Fe
≤0.6 ≤0.7
0.205 52
Cu 0.05~0.2 0.106
Mn 1.0~1.5 1.17
Mg
Cr
Ni Zn
Ti
Zr
-
-
- 1、下载文档前请自行甄别文档内容的完整性,平台不提供额外的编辑、内容补充、找答案等附加服务。
- 2、"仅部分预览"的文档,不可在线预览部分如存在完整性等问题,可反馈申请退款(可完整预览的文档不适用该条件!)。
- 3、如文档侵犯您的权益,请联系客服反馈,我们会尽快为您处理(人工客服工作时间:9:00-18:30)。
❖ (3)取代锻造、 热挤压等工艺, 以降低成本, 简化工艺 。
实验总体工艺流程图
合金成分设计及配料
优化成分
熔化精炼
变质处理 挤压铸造 热处理 性能检测
硬 度 测 试
室 温 拉 伸
高 温 拉 伸
蠕 变 试 验
磨 损 试 验
❖ 过共晶铝硅合金热处理工艺参数 ❖ (1)固溶温度:固溶温度越接近共晶转变温
国内外发动机零件所用材料比较
气缸盖罩,铸铁或 部分使用亚/共晶
铝硅合金
气缸盖,铸铁或
部分使用亚/共晶 铝硅合金
气缸筒,铸铁
气缸体,铸铁或部分 是在亚共晶铝硅合金
镶嵌铸铁的气缸筒
国产活塞材料为ZL108、ZL109, 含 11~13%Si , 共 晶 铝 硅 合 金 ; 国 外使用过共晶铝硅合金制造,含 16~26%Si。
❖ 气缸是发动机中最重的零件,占发动机总重的30%以上, 国外50%的汽缸采用铝合金铸造。国内气缸大量使用灰 铸铁或少量使用亚共晶铝硅合金缸体镶铁缸套的复合工 艺,后者生产工艺复杂、生产成本高,影响气缸铝化的 进展。
❖ 国外的活塞用挤压铸造工艺(液态模锻)将熔体在高压下铸造 成活塞形状的毛坯,热处理后再将毛坯车加工成零件。挤压 铸造工艺能大幅度提高过共晶硅的性能、细化初生硅的尺寸。
线 膨 胀
金扫透能 相描射谱 观观观分 察察察析
组织分析
实验总体工艺流程图
DTA X-ray
主要研究内容
❖ 初晶硅长大的机理研究及初晶硅的尺寸控制 ❖ 特种铸造工艺的研究(低压铸造、挤压铸造) ❖ 特种铸造的工、模具设计 ❖ 热处理工艺研究
前期实验进程
❖ 铝铜磷变质剂 将铜磷合金粉与铝粉按一定比例进行球磨,
过共晶铝硅合金发动机活塞的挤压 铸造工艺研究
姓 名: 朱 君 罡 指导教师: 关 绍 康 教 授 专 业: 材 料 学
目录
❖ 选题意义 ❖ 挤压铸造的概念及开发方向 ❖ 实验总体工艺流程图 ❖ 主要研究内容 ❖ 前期实验进程 ❖ 后期实验内容及参数 ❖ 课题的预期目标
选题意义
❖ 在发动机中,用铝合金替代铸铁成为全球的发展趋势。 由于铝合金的质量轻,减少活塞往复的惯性力,能使发 动机的燃油效率提高3~5%;铝合金的密度只相当于钢的 1/3,汽车上每使用1kg铝,可降低自身重量的2.25kg,减 重效益高达125%;同时在汽车的整个使用寿命内,还可 减少废气排放20kg。
❖ 铝活塞挤压铸造参数 ❖ (1)挤压铸造铝液浇铸温度与金属模活塞浇注的温度基本
相同。 ❖ (2)不同活塞结构应用相应的压力,才可以完全消除铸造
缺陷。(所需压力的大小, 取决于合金的种类和性质及铸 件的大小、形状、高度等因素。) ❖ (3)保压时间主要取决于活塞铸件的壁厚,一般保压到完 全凝固。保压时间为15~35s,此时铸件质量较好。(短则 不易补缩,形成缩松;长则收缩应力大,表面质量差) ❖ (4)加压速度采用在空行程时以140mm/s快速下行,冲头 刚接触到液面时改变为慢速挤压,速度为40mm/s ,直至 压力升到保压压力,结晶凝固。(过快易卷入气体或喷液; 过慢会金属自由结壳过厚,影响加压效果。) ❖ (5)一般凹模取180~220℃,凸模取140~180℃较好。 (过低成形性差,晶粒粗大,缺陷多;过高则粘模且模具磨 损量大。)
❖ 国内多使用共晶铝硅合金ZL109,多用普通的金属模铸造, 铸造后通过进一步的锻造加工来提高合金的力学性能,然后 再热处理车制成活塞,这种工艺的成品率低,工序多,并且 锻造加工共晶铝硅相对于过共晶铝硅合金仍然存在耐热性、 耐磨性、膨胀系数和体积稳定性差等问题。
❖ 因此,有必要大力发展新型过共晶铝硅合金的挤压铸造工艺。
合模力8000KN 大杠内间距910×910mm 大杠直径180mm 最大合模距离760mm 模具最小厚度740mm 滑块距工作台最大距离1500mm 顶出力360KN 顶出行程180mm 压射力1000/1250 KN 压射距离850/900mm 压射速度30-110mm/s 料筒直径范围95-132/106-150mm 标准料筒直径105/130mm 铝液最大浇筑量7.3/10kg
然后压成小块,在保护气氛下进行烧结。
球磨机
德国 保护气氛 热处理炉
❖ 熔炼
熔化铝锭
添加合金元素
添加变质剂
除渣
除气
搅拌
熔体过热处理
静置
浇铸
铝合金实验炉
熔炼过程的局部工艺流程图
❖ 热处理 通过对该过共晶铝硅合金进行DTA分析,
确定其热处理温度,将铸锭在500 ℃保温3h。
热处理炉
❖ 金像
a)
b)
金相显微镜
A17
110
115
107
110.7
A18
132
130
120
127.3
A19
132
123
120
125
表1-2过共晶铝硅合金A12热处理前后维氏硬度
处理状态 热处理前
1
2
3
平均
92 102 105 99.6
热处理后
149 146 145 146.6
维 氏 硬 度 计
后期实验内容及参数
❖ 苏州三基立式挤压铸造机SCV-800
c)
d)
线切割后的合金 棒
a),b) 未变质的金相形貌 c),d) 1.5%AlCuP500 ℃烧结780变质的金相形貌
过共晶铝硅合金变质前后的晶铝硅合金随着变质剂烧结温度升高 的维氏硬度
样品型号 1
2
3
平均
A15
104
109
97
101.7
A16
114
107
119
113.3
挤压铸造的力学过程
❖ 铸件的三个区:
硬层区(塑性体) 固液区(脆性体) 液相区(黏性体)
❖ 挤压铸造时,铸件外壳产生塑性变形,固-液相产生
热裂,液态金属在等静压的作用下挤入微小裂纹中。
挤压铸造产品的开发方向
❖ (1)取代常规的压铸工艺, 使其有更致密的 组织,可固溶热处理,并提高其力学性能, 或 提高其耐磨性、抗渗漏性;
油底壳,铸铁或铝硅合 金
国外已成功研制过共晶铝硅合 金用低压铸造的方法一次成形 的全铝气缸,不用镶嵌铸铁的
气缸筒
挤压铸造的概念及开发方向
❖ 挤压铸造是一种使液态金属在高机械压力下 成型凝固的工艺方法。其具有减少或消除缩 松和缩孔,减轻偏析,细化晶粒,使铸件组 织致密,且有一次成型、缩短周期、成品率 高等优点。